数控机床主轴旋转精度及测量方法
五轴数控机床的运动精度检测

五轴数控机床的精度检测方法分析摘要:本文首先对五轴数控机床的精度检测技术做了一个简要概括,然后介绍数控机床精度检测的必要性,指出数控机床常见的精度要求及传统检测方法,并介绍先进检测方法和检测仪器、工具,以及各个检测方法的特点。
关键词:五轴数控机床;精度检测Precision analysis of detection method of five axis CNC machine toolsAbstract: Firstly,this paper introduces the precision detection technology of five axis NC machine tools, and then introduces the necessity of CNC machine tool accuracy detection accuracy requirements of CNC machine tools, points out the common and the traditional detection method, and introduce advanced detection method and detection instruments, tools, and the characteristics of each detection method.Key words: Five axis NC machine tool;Precision detection1 引言五轴联动数控机床目前已大量用于航空制造等高端制造领域。
由于机床复杂的机械结构及控制系统,五轴联动机床加工精度检测及优化一直是机械制造行业内研究的热点和难点,成为影响产品加工质量及效率的关键。
对企业来说,购买数控机床是一笔相当大的投资,特别是购买大型机床。
实践表明,大多数大型数控机床解体发运给用户安装时,必须在现场调试才能符合其技术指标,因此,在新机床检收时,要进行严格的检定,使机床一开始安装就能保证达到其枝术指标预期使用性能和生产效率。
简要叙述机床回转轴回转精度检测的实验方案
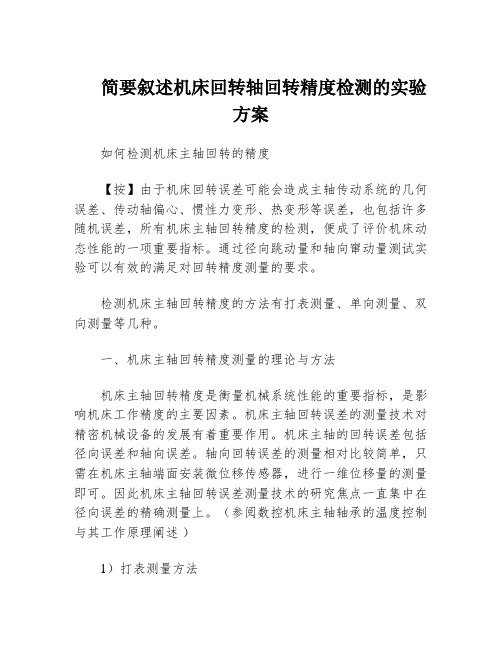
简要叙述机床回转轴回转精度检测的实验方案如何检测机床主轴回转的精度【按】由于机床回转误差可能会造成主轴传动系统的几何误差、传动轴偏心、惯性力变形、热变形等误差,也包括许多随机误差,所有机床主轴回转精度的检测,便成了评价机床动态性能的一项重要指标。
通过径向跳动量和轴向窜动量测试实验可以有效的满足对回转精度测量的要求。
检测机床主轴回转精度的方法有打表测量、单向测量、双向测量等几种。
一、机床主轴回转精度测量的理论与方法机床主轴回转精度是衡量机械系统性能的重要指标,是影响机床工作精度的主要因素。
机床主轴回转误差的测量技术对精密机械设备的发展有着重要作用。
机床主轴的回转误差包括径向误差和轴向误差。
轴向回转误差的测量相对比较简单,只需在机床主轴端面安装微位移传感器,进行一维位移量的测量即可。
因此机床主轴回转误差测量技术的研究焦点一直集中在径向误差的精确测量上。
(参阅数控机床主轴轴承的温度控制与其工作原理阐述)1)打表测量方法早期机床主轴回转精度不太高时,测量机床主轴误差的常用方法是将精密芯棒插入机床主轴锥孔,通过在芯棒的表面及端面放置千分表来进行测量。
这种测量方法简单易行,但却会引入锥孔的偏心误差,不能把性质不同的误差区分开,而且不能反映主轴在工作转速下的回转误差,更不能应用于高速、高精度的主轴回转精度测量。
除此之外也有采用测量试件来评定主轴的回转误差。
2)单向测量方法单向测量法又称为单传感器测量法。
由传感器拾得“敏感方向”的误差号,经测微仪放大、处理后,送入记录仪,以待进一步数据处理。
然后以主轴回转角作为自变量,将采集的位移量按主轴回转角度展开叠加到基圆上,形成圆图像。
误差运动的敏感方向是通过加工或测试的瞬时接触点并平行于工件理想加工的表面的法线方向,非敏感方向在垂直于第三方向的直线上。
单向测量法测量的主轴回转误差运动实质上只是一维主轴回转误差运动在敏感方向的分量。
因此单向测量法只适用于具有敏感方向的主轴回转精度的测量,例如工件回转型机床。
数控机床位置精度测试常用的测量方法及评定标准

4.4补偿实例 现以ZJK2532A数控铣钻床的X轴为例,该机床配置华中数控世纪星系统。测量方法为“步距规”测量;设某步距规实际尺寸为:
位置
P0
P1
P2
P3
P4
P5
实际尺寸mm
0
100.10
200.20
300.10
400.20
500.05
1、测试步骤如下: 。 在首次测量前,开机进入系统(华中数控HNC-2000或HNC-21M),依次按“F3参数”键、再按“F3输入权限”键进入下一子菜单,按F1数控厂家参数,输入数控厂家权限口令,初始口令为“NC”,回车,再按“F1参数索引”键,再按“F4轴补偿参数”键如图2-6所示,移动光标选择“0轴” 回车,即进入系统X轴补偿参数界面如图2-8所示,将系统的反向间隙、螺距补偿参数全部设置为零,按“Esc”键,界面出现对话框“是否保存修改参数?”,按“Y”键后保存修改后的参数。按“F10”键回到主界面,再按“Alt+X”,退出系统,进入DOS状态,按“N”回车进入系统;
图6步距规安装示意图
简述数控车床主轴主要几何精度检测项目

简述数控车床主轴主要几何精度检测项目摘要:一、数控车床主轴简介二、数控车床主轴主要几何精度检测项目1.轴向窜动2.径向跳动3.端面跳动4.轴向刚度5.径向刚度三、检测方法及注意事项四、提高数控车床主轴几何精度的措施正文:数控车床主轴是数控车床的核心部件,承担着加工过程中刀具的旋转、工件的输送以及切削力的传递等重要任务。
主轴几何精度是衡量数控车床性能的重要指标,它直接影响到加工零件的精度和质量。
本文将对数控车床主轴主要几何精度检测项目进行简述,以期为大家提供参考。
一、数控车床主轴简介数控车床主轴通常由高精度轴承、电机、变速装置、润滑系统等组成。
主轴在高速旋转过程中,需要具备高精度、高刚度、高平稳性等特点。
为了确保这些性能,对主轴的几何精度进行检测是十分必要的。
二、数控车床主轴主要几何精度检测项目1.轴向窜动:轴向窜动是指主轴在轴向方向上的位移。
过大的轴向窜动会导致加工过程中刀具与工件的相对位置发生变化,从而影响加工精度。
2.径向跳动:径向跳动是指主轴在径向方向上的振动。
径向跳动会影响刀具的切削稳定性和工件的加工精度。
3.端面跳动:端面跳动是指主轴端面在加工过程中产生的振动。
端面跳动会导致工件表面质量下降,影响加工精度。
4.轴向刚度:轴向刚度是指主轴在轴向载荷作用下的变形能力。
提高轴向刚度有利于保证加工过程中刀具与工件的相对稳定性。
5.径向刚度:径向刚度是指主轴在径向载荷作用下的变形能力。
提高径向刚度有助于保证加工过程中刀具的切削稳定性。
三、检测方法及注意事项1.检测方法:采用光学投影仪、测振仪、激光干涉仪等设备对主轴几何精度进行检测。
2.注意事项:检测过程中应确保主轴充分冷却,避免温度变化对检测结果产生影响。
同时,检测设备应定期校准,确保检测数据的准确性。
四、提高数控车床主轴几何精度的措施1.选用高精度轴承,提高主轴的旋转精度。
2.优化主轴变速装置,降低轴向窜动。
3.加强主轴润滑系统的维护,提高主轴的平稳性。
提高数控机床主轴组件旋转精度的方法探讨
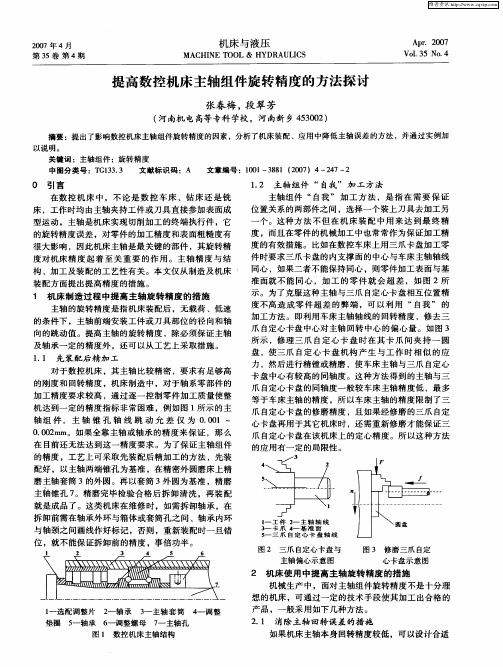
的应 用 有 一 定 的局 限 性 。
主轴锥孔 7 。精磨 完毕 检验合格后 拆卸 清洗 ,再装 配 就是成 品了。这类机床在维修 时 ,如需拆 卸轴 承 。在 拆卸前需在轴 承外 环与箱 体或套 筒孔之间 、轴承 内环 与轴 颈之 间画线作好标记 ,否则 ,重新装配时一旦错 位 ,就不 能保证拆卸前 的精 度 。事倍 功半。
6 一调整螺母
7 主轴孔 一
图 1 数控机床 主轴结 构
维普资讯
机床与液压
第3 5卷
的拨盘 ,使 传动 和定 位 分开 ,消除 主轴 径 向跳动 引 起 的误差 。如 图4所 示为主轴精 度不高的外圆磨床磨 削精度较高零件 的工作 图 ,采用拨 盘带 动零件 旋转 , 主轴顶尖不转动 ,这样主轴的误差不能影响到零件 。
12 主轴组 件 “自我 ” 加 工 方 法 .
主轴组 件 “ 自我 ” 加工 方 法 ,是 指 在 需要 保 证 位置关 系的两部件之 间 ,选择一 个装上 刀具去加工另 个 。这种 方法 不但 在 机床 装配 中用来 达 到最 终 精 度 ,而且在零件 的机械加工 中也 常常作 为保证加工精 度 的有效措施 。比如在数 控车床 上用三爪卡盘加工零 件时要求 三爪卡盘的内支撑面的中心与车床主轴轴线 同心 ,如果 二者不 能保持 同心 。则零 件加工表面与基 准面就不能 同 心 ,加工 的零件 就 会 超 差 ,如 图 2所 示。为了克服这种 主轴 与三爪 自定心卡盘相互位置精 度不 高造成 零 件超 差 的弊端 ,可 以利用 “ 自我 ” 的 加工 方法。即利用车床主轴轴线的 回转精度 ,修去三 爪 自定心卡盘 中心对主轴 回转 中心 的偏 心量 。如 图 3 所示 ,修理三 爪 自定心 卡 盘 时在其 卡 爪 间夹 持一 圆 盘 ,使三爪 自定心 卡 盘机 构产 生 与工 作 时相 似 的应 力 ,然后进行精镗或精磨 ,使车床主轴与三爪 自定心 卡盘 中心有较高的 同轴度 。这种方法得到 的主轴 与三 爪 自定心卡盘 的同轴度一般较车床 主轴精度低 ,最 多 等于车床主轴 的精度 ,所 以车床主轴 的精度 限制 了三 爪 自定心卡盘 的修磨精度 ,且如果经修磨 的三爪 自定 心卡盘再用于其它机床时 ,还需重新修磨才 能保证 三 爪 自定心卡盘在该机床上 的定心精度 。所 以这种方 法
五坐标数控机床旋转轴定位精度的校正方法

2019年 第5期图1 绕X 轴坐标的转动图中,C -P 1这一段以C 为中心绕X 坐标旋转了一个角度a ,这样C -P 1的末端从P 1移到了P 2。
当把这种概念用于机床时(可以认为C 点是转动主轴头的中心,P 1是刀具的中心),可以看到转动一个坐标的结果是使刀具中心在XYZ 坐标系中产生位移。
如果有RTCP 功能,数控系统将使刀具中心始终保持在一个固图2 无RTCP图3 有RTCP5.影响RTCP 精度的因素RT C P 精度是一个综合的空间精度,从RTCP 的运行状态,可以看到,RTCP 精度的好与差受到多种因素的影响。
这些因素包括机床的几何精度(如C 轴画圆精度等)、定位精度和重复定位精度、RTCP 的中心点长度、RTCP 机械偏心的补偿及回转坐标的绝对零点位置等。
图 4由于线性轴在RTCP 角度旋转时,如果角度旋转不大,如5 º,则移动距离只有40m m ,而机床的线性轴定位精度一般可以达到0.015mm/2 000mm ,所以线性轴的定位精度误差在旋转角度较小时对RTCP 精度的影响可以忽略不计(见图5)。
图 5在微小角度条件下,弧可以认为是垂直于一条边,并是一直线,由此我们可以得到:tan α=y /x α=arctan y /x由此,由于X (旋转轴旋转中心到刀具中心的距离)一般在700m m 以上,而Y (RT C P 精度值)一般很小,在0.1m m 以下,经计算,可以得到如果RTCP 变化2019年冷加工图 6图 7图 8图 9图 10图 11图 12成大先.机械设计手册[M]. 6版.北京:化学工业出版社,2016.(截稿日期:20190301)。
数控机床整机性能检测与调试4.2.2 主轴精度检测依据的国家标准

为了参考和修正方
便,应记录α值是小
于、等于还是大于
90°
主轴轴线和 0.015/30 平尺、专 5.5.1.2.3.2
Y轴轴线运 0
用支架和 如果可能, Z轴轴
动间的垂直
指示器 线锁紧。
度:
平尺应平行于Y轴
G14
轴线放置。
为了参考和修正方
便,应记录α值是小
于、等于还是大于
90°
期性轴向窜
5.6.2.2.2
动
应在机床的所
有工作主轴上进
行检验
序号
简图
检验项目
允差 mm
检验工具
检验方法
参照GB/T17421.1的有关 条文
主轴锥孔的径 a)
检验棒和 5.6.2.1.2和
向跳动:
0.007
指示器 5.6.1.2.3
a)靠近主轴端 b)
应在机床的所有
G11
部
0.015
工作主轴上进行
4.2.2 主轴精度检测依据的国家标准
检测依据
参考:JB/T 8771.2-1998 《加工中心检验条件》 第 2 部 分:立式加工中心 几何精度检验 的相关标准
序 号
简图
检验项目
允差 mm
检验工具
检验方法
参照GB/T17421.1的有关 条文
G10
主轴的周 0.005
指示器
5.6.2.1.1和
b)距主轴端部ຫໍສະໝຸດ 检验。300mm处
应至少旋转两整
圈进行检验
主轴轴线和 a)和b) 检验棒和 5.4.1.2.1和5.4.2.2.3
Z轴轴线运动 在300测 指示器 X轴轴线置于行程
间的平行度: 量长度上
数控机床精度检验
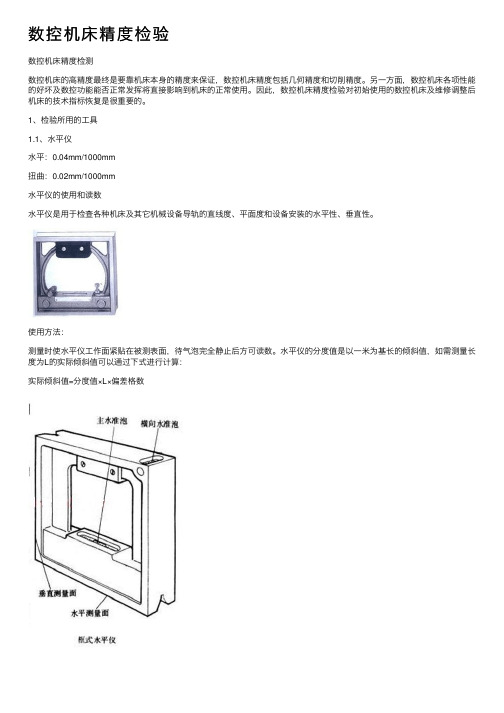
数控机床精度检验数控机床精度检测数控机床的⾼精度最终是要靠机床本⾝的精度来保证,数控机床精度包括⼏何精度和切削精度。
另⼀⽅⾯,数控机床各项性能的好坏及数控功能能否正常发挥将直接影响到机床的正常使⽤。
因此,数控机床精度检验对初始使⽤的数控机床及维修调整后机床的技术指标恢复是很重要的。
1、检验所⽤的⼯具1.1、⽔平仪⽔平:0.04mm/1000mm扭曲:0.02mm/1000mm⽔平仪的使⽤和读数⽔平仪是⽤于检查各种机床及其它机械设备导轨的直线度、平⾯度和设备安装的⽔平性、垂直性。
使⽤⽅法:测量时使⽔平仪⼯作⾯紧贴在被测表⾯,待⽓泡完全静⽌后⽅可读数。
⽔平仪的分度值是以⼀⽶为基长的倾斜值,如需测量长度为L的实际倾斜值可以通过下式进⾏计算:实际倾斜值=分度值×L×偏差格数1.2、千分表1.3、莫⽒检验棒2、检验内容2.1、相关标准(例)加⼯中⼼检验条件第2部分:⽴式加⼯中⼼⼏何精度检验JB/T8771.2-1998加⼯中⼼检验条件第7部分:精加⼯试件精度检验JB/T8771.7-1998加⼯中⼼检验条件第4部分:线性和回转轴线的定位精度和重复定位精度检验JB/T8771.4-1998机床检验通则第2部分:数控轴线的定位精度和重复定位精度的确定JB/T17421.2-2000加⼯中⼼技术条件JB/T8801-19982.2、检验内容精度检验内容主要包括数控机床的⼏何精度、定位精度和切削精度。
2.2.1、数控机床⼏何精度的检测机床的⼏何精度是指机床某些基础零件本⾝的⼏何形状精度、相互位置的⼏何精度及其相对运动的⼏何精度。
机床的⼏何精度是综合反映该设备的关键机械零部件和组装后⼏何形状误差。
数控机床的基本性能检验与普通机床的检验⽅法差不多,使⽤的检测⼯具和⽅法也相似,每⼀项要独⽴检验,但要求更⾼。
所使⽤的检测⼯具精度必须⽐所检测的精度⾼⼀级。
其检测项⽬主要有:直线度⼀条线在⼀个平⾯或空间内的直线度,如数控卧式车床床⾝导轨的直线度。
数控机床主轴旋转精度及测量方法

数控机床主轴旋转精度及测量方法来源:对钩网主轴是数控机床中的核心设备之一,担负着从机床电动机接受动力并将之传递给其他机床部件的重要责任。
工作中,要求主轴必须在承担着一定的荷载量,以及保持适当的旋转速度的前提条件下,带动在其控制范围之内的工件或者刀具,绕主轴旋转中心线进行精确、可靠而又稳定的旋转。
主轴的旋转精度直接决定了机床的加工精度。
主轴旋转精度的定义机床主轴精度大小是以其瞬时旋转中心线与理想旋转中心线的相对位置来决定的。
在正常工作旋转时,由于主轴、轴承等的制造精度和装配、调整精度,主轴的转速、轴承的设计和性能以及主轴部件的动态特征等机械原因,造成了主轴的瞬时旋转中心线往往会与理想旋转中心线在位置上产生一定的偏离,由此产生的误差就是主轴在旋转时的瞬时误差,也称为旋转误差。
而瞬时误差的范围大小,就代表主轴的旋转精度。
加工过程中,主轴可能会延与轴垂直的方向发生径向跳动,延轴方向发生轴向窜动或以轴上某点为中心,发生角度摆动,这些运动都会降低主轴的旋转精度。
实际生产中,人们常常用安装于主轴前端的刀具或工件部位的定位面发生的三种运动的运动幅度来衡量和描述主轴精度,这三种运动分别是径向跳动、端面跳动和轴向窜动。
主轴在工作转速时的旋转精度,也称为运动精度。
目前,我国已经制订并推行了国内统一的通用机床旋转精度检验标准,根据加工对象的精度要求确定不同的主轴精度标准。
主轴精度的测量和评定静态测量和评定法:这是一种在低速旋转环境下测定主轴旋转精度的方法,又称为打表法。
具体操作流程是,在无载荷条件下手动缓慢转动主轴,或控制主轴进行低速转动,利用千分表进行测量,测出最大度数和最小读数,计算出二者之差,即为主轴的旋转精度。
由于静态测量是在低速旋转环境下,而不是在主轴实际工作速度下进行的测量,因此并不能够反映出真正的主轴旋转精度。
动态测量和评定法:这是一种在主轴实际的工作转速之下,采用非接触式测量装置,测出主轴旋转运动精度误差的方法,包括主轴振动及高速旋转时的运动精度误差。
数控机床精度要求与测量方法

千分表 主轴检棒 大理石三角尺 水平仪 球杆仪 激光干涉仪
1.机床水平检测 2.主轴跳动检测 3.工作台运动与X轴 Y轴平行度 4.主轴中心线垂直度 X向 Y向 5.X轴运动与Y轴运动垂直度 6.Z轴运动与X轴 Y轴运动的垂直度 7.工作台运动x向与T型槽侧面平行度 8.主轴旋转与工作台面的垂直度(360) 9.反向间隙检测 10定位精度检测 11.重复定位精度检测
X轴平 行度
Y轴平 行度
①确保大理石与工作台面无碰伤油污。 ②调整大理石与轴平行。 ③ 移动工作台,千分表读数的最大差值为测定值。 ④允许值≤0.02/500
①确保主轴锥孔,主轴测试棒无碰伤油污。 ②千分表表尖相抵主轴测试棒直径处。 ③移动Z轴,千分表读数的最大差值作为测定值。 ④X轴允许值≤0.015/300, Y轴允许值≤0.015/300.
①工作台平面修整,表面清理干净。
②千分表表尖相抵工作台表面,以主轴为中心旋转千分表画 直径300的圆。 ③允许值≤0.02/300。
反向间隙是指:数控机床轴在移动过程中换向丝杆和螺母副 之间的间隙。
①回参考点。 ②用切削进给移动到测定点。 如:G01 X100. F1000 ③安装千分表使刻度对0
重复定位精度是指:数控机床反复执行同一个移动运行程 序代码,多次运行同位置的检测数据一致性,就是重复定 位精度。
重复定位精度可以参照反向间隙测量方法。 经过多次测量,测量数据最大值与最小差值就是重复定位
精度。
允许值≤0.0039
抹
油
布
石
砂 纸
防
锈 油
无
清
尘
探讨数控机床五轴精度快速校准方法

探讨数控机床五轴精度快速校准方法
Q253=1000;(预定位进给速度)
Q380=0;(参考角)
Q411=-90;(A轴起始角,为第一次测量时的角度)
Q412=+110;(A轴终止角,为最后一次测量时的角度)Q413=0;(A轴仰角,为测量其他旋转轴时的角度)
Q414=3;(A轴探测测量点数,值为0时不测量该轴)Q415=-90;(B轴起始角,为第一次测量时的角度)
Q416=+90;(B轴终止角,为最后一次测量时的角度)Q417=0;(B轴仰角,为测量其他旋转轴时的角度)Q418=0;(B轴探测测量点数,值为0时不测量该轴)
Q419=-210;(C轴起始角,为第一次测量时的角度)
Q420=+220;(C轴终止角,为最后一次测量时的角度)Q421=0;(C轴仰角,为测量其他旋转轴时的角度)
Q422=2;(C轴探测测量点数,值为0时不测量该轴)
Q423=4;(TNC用一个平面的4点还是3点测量基准球)Q432=1;(预设点)
图4KinematicsOpt功能
机床执行以上测量循环Cycle451,全自动地测量旋转轴A、C,计算测量值并将结果自动保存在机床相应运动特性表中,快速调整和优化数控机床五轴精度。
3.结语
使用iTNC530控制系统的KinematicsOpt功能,测量过程只需要一个接触式探头和校准
球,操作人员只需执行一个测量循环,就能在机床上校准五轴头精度,而不再必须由专门的技术人员来完成,给使用用户带来极大方便,同时大大提高了生产效率和加工精度。
数控机床精度检验
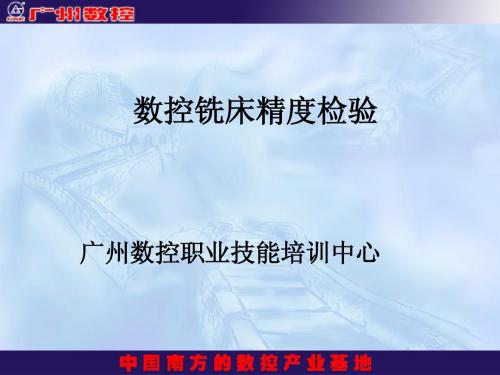
广州数控职业技能培训中心
§1 数控机床精度检验的必要性
数控机床的高精度最终是要靠机床本身的精度来 保证,数控机床精度包括几何精度和切削精度。另一 方面,数控机床各项性能的好坏及数控功能能否正常 发挥将直接影响到机床的正常使用。因此,数控机床 精度检验对初始使用的数控机床及维修调整后机床的 技术指标恢复是很重要的。
9、主轴旋转轴线对工作台(或立柱,或滑枕)横向移 动 的平行度 10、工作台中央或基准T形槽的直线度 11、主轴旋转轴线对工作台中央或基准T形槽的垂直 度(仅适用于卧式床身铣床) 12、中央或基准T形槽对工作台纵向移动的平行度 13、工作台(或立柱,或滑枕)横向移动对工作台纵 向移动的垂直度 14、直线运动坐标的定位精度 15、直线运动坐标的重复定位精度 16、直线运动坐标的平均反向值 (二)工件试切的精度:要求加工一个工件有圆、正 方形、六边形、球面。
• 1、参照GB/T17421.1,尤其是精度检验前的安装、 主轴及其部件的空运转升温和检验方法 • 2、参照GB/T17421.1--1998中3.1的规定,调整 机床安装水平。
机床水平调整安装要求:
• (1) 十字工作台型铣床调整安装水平时,将工 作台、滑座和主轴箱等移动部件分别置于行程的 中间位置,在工作台中央位置放置水平仪,水平 仪在纵向和横向的读数均不得超过 0.030/1000mm 。 • (2) 立柱移动型和滑枕移动型铣床调整安装水平 时,在床身导轨上放置圆检验棒(对V形导轨) 或板桥(对平导轨),圆检验棒和板桥上垂直于 床身导轨放一平尺。在圆检验棒、板桥和平尺上 各放一个水平仪:水平仪a和导轨平行,水平仪和 导轨垂直。调整导轨水平,水平仪a和b的读数均 不得超过0.03/1000。
数控机床的定位精度
数控机床几何精度检测工具及使用方法
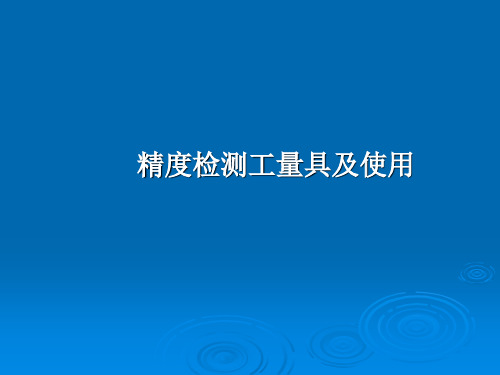
数控机床几何精度检验具有重要的实际 意义,不仅需要精密水平仪、平尺、角尺 、检验棒、指示表(如千分表、百分表、 杠杆表)和激光干涉仪等,还需要一些调 整工具。为完成数控机床调平和几何精度 检验,现介绍常用的工具、量具和检具。
一、常用工具
常用工具有扳手类、螺钉旋具、钳子、 锤子、铜棒、铝棒、千斤顶、油壶、油枪、 撬棍等,其中扳手包括活扳手、呆扳手、梅 花扳手、内六角扳手、扭力扳手、成套手动 套筒扳手和钩型扳手等,常用的螺钉旋具有 一字槽螺钉旋具和十字槽螺钉旋具,其实物 和功能见表1-1。
图1-4 自准直仪原理
图1-5 十字标线
自准直仪的光学系统是由光源发出的光经分划板、半透反射镜和物镜后射 到反射镜上。如反射镜倾斜,则反射回来的十字标线像偏离分划板上的零 位,如图1-5所示。
(2)使用方法 以自准直仪与多面棱镜联合使用检验数控转台分度误差为例, 说明其使用方法,见图1-6。
检验数控转台分度误差时,先清洁数控转台和多面棱镜座相关部位,安装多面棱镜座 并对其打表找正,使其与转台同轴(0.005mm内),将多面棱镜安装在镜座上,并对 其进行紧固,然后安装自准直仪支架,将自准直仪置于支架上,并且将自准直仪电源 线接好,调整水平和角度,完成对光。转动数控转台,通过目镜转动手轮,使其指示 的黑线在亮十字像中间,依次记录数据,用公式计算出数控转台分度误差。
图1-6 自准直仪检验数控转台分度误差
5.水平仪
(1)工作原理 水平仪原理是利用气泡在玻璃管内,气泡保持在最高位 置,如图1-7所示,表明该平面左端高于右端。
图1-7 精密水平仪气泡
1)水平仪刻度示值。实训室的水平仪灵敏度是0.02mm/m,此刻度示值 是以1米为基长的倾斜值为0.02mm/1000mm,如图1-8所示。
主轴动态精度测试方法【教程】
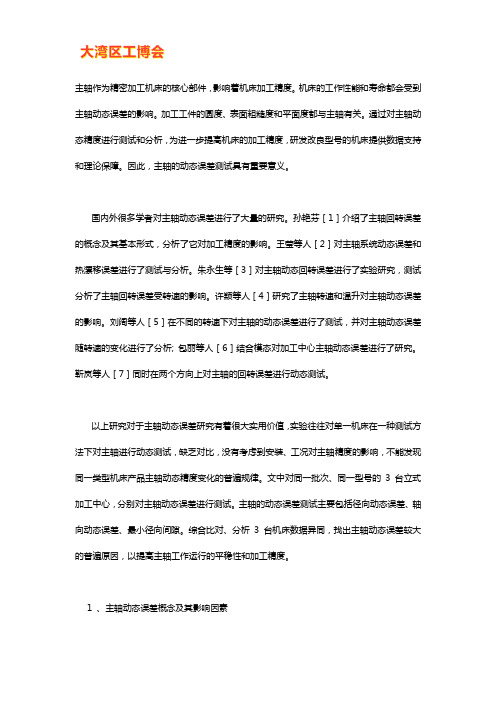
主轴作为精密加工机床的核心部件,影响着机床加工精度。
机床的工作性能和寿命都会受到主轴动态误差的影响。
加工工件的圆度、表面粗糙度和平面度都与主轴有关。
通过对主轴动态精度进行测试和分析,为进一步提高机床的加工精度,研发改良型号的机床提供数据支持和理论保障。
因此,主轴的动态误差测试具有重要意义。
国内外很多学者对主轴动态误差进行了大量的研究。
孙艳芬[1]介绍了主轴回转误差的概念及其基本形式,分析了它对加工精度的影响。
王莹等人[2]对主轴系统动态误差和热漂移误差进行了测试与分析。
朱永生等[3]对主轴动态回转误差进行了实验研究,测试分析了主轴回转误差受转速的影响。
许颖等人[4]研究了主轴转速和温升对主轴动态误差的影响。
刘阔等人[5]在不同的转速下对主轴的动态误差进行了测试,并对主轴动态误差随转速的变化进行了分析; 包丽等人[6]结合模态对加工中心主轴动态误差进行了研究。
靳岚等人[7]同时在两个方向上对主轴的回转误差进行动态测试。
以上研究对于主轴动态误差研究有着很大实用价值,实验往往对单一机床在一种测试方法下对主轴进行动态测试,缺乏对比,没有考虑到安装、工况对主轴精度的影响,不能发现同一类型机床产品主轴动态精度变化的普遍规律。
文中对同一批次、同一型号的3 台立式加工中心,分别对主轴动态误差进行测试。
主轴的动态误差测试主要包括径向动态误差、轴向动态误差、最小径向间隙。
综合比对、分析3 台机床数据异同,找出主轴动态误差较大的普遍原因,以提高主轴工作运行的平稳性和加工精度。
1 、主轴动态误差概念及其影响因素主轴动态误差就是主轴在一定转速工作下的回转误差,机床主轴回转是机床最基本的成型运动,是决定工件圆度的主要因素之一。
主轴回转精度可以定义为: 主轴回转线在回转时相对于其平均周线的变动量在误差敏感方向的最大位移[8]。
它可以是径向跳动、轴向跳动或摆动,如图1 所示。
一般情况下3 种误差同时存在,并相互叠加,影响主轴精度。
主轴动态回转精度测试介绍

主轴动态回转精度测试介绍一、前言数控机床主轴组件的精度包含以下两个方面:1.几何精度-主轴组件的几何精度,是指装配后,在无负载低速转动(用手转动或低速机械转速)的条件下,主轴轴线和主轴前端安装工件或刀具部位的径向和轴向跳动,以及主轴对某参考系统(如刀架或工作台的纵、横移动方向)的位置精度,如平行度和垂直度等;2.回转精度-指的是主轴在以正常工作转速做回转运动时,轴线位置的变化。
二、主轴回转精度的定义主轴在作转动运动时,在同一瞬间,主轴上线速度为零的点的联机,称为主轴在该瞬间的回转中心线,在理想状况下,主轴在每一瞬间的回转中心线的空间位置,相对于某一固定的参考系统(例如:刀架、主轴箱体或数控机床的工作台面)来说,应该是固定不变的。
但实际上,由于主轴的轴颈支承在轴承上,轴承又安装在主轴箱体孔内,主轴上还有齿轮或其它传动件,由于轴颈的不圆、轴承的缺陷、支承端面对轴颈中心线的不垂直,主轴的挠曲和数控机床结构的共振等原因,主轴回转中心线的空间位置,在每一瞬时都是变动的。
把回转主轴的这些瞬间回转中心线的平均空间位置定义为主轴的理想回转中心线,而且与固定的参考坐标系统联系在一起。
这样,主轴瞬间回转中心线的空间位置相对于理想中心线的空间位置的偏离就是回转主轴在该瞬间的误差运动。
这些瞬间误差运动的轨迹,就是回转主轴误差运动的轨迹。
主轴误差运动的范围,就是所谓的「主轴回转精度」。
由此可见,主轴的回转精度,说明回转主轴中心线空间位置的稳定性特点。
三、主轴回转精度量测3.1 主轴回转误差运动的测量与研究目的对主轴回转误差运动的测量和研究有两方面的目的:(1).从设计、制造的角度出发,希望通过测量研究找出设计、制造因素与主轴误差运动的关系,及如何根据误差运动的特点,评定主轴系统的设计和制造质量,同时找出产生误差运动的主要原因,以便做进一步改善。
(2).从使用的角度出发,希望找出主轴运动与加工精度和表面粗糙度的关系,及如何根据误差运动的特点,预测出数控机床在理想条件下所能加工出的工件几何与表面粗糙度,给选用数控机床及设计数控机床提出依据。
一、数控机床的精度检验

一、数控机床的精度检验一、数控机床的精度检验一、数控机床的精度检验数控机床的高精度最终是要靠机床本身的精度来保证,数控机床精度包括几何精度和切削精度。
另一方面,数控机床各项性能和性能检验对初始使用的数控机床及维修调整后机床的技术指标恢复是很重要的。
1. 几何精度检验几何精度检验,又称静态精度检验,是综合反映机床关键零部件经组装后的综合几何形状误差。
数控机床精度的检验工具和检验方法类似于普通机床,但检测要求更高。
几何精度检测必须在地基完全稳定、地脚螺栓处于压紧状态下进行。
考虑到地基可能随时间而变化,一般要求机床使用半年后,再复校一次几何精度。
在几何精度检测时,应注意测量方法及测量工具应用不当所引起的误差。
在检测时,应按国家标准规定,即机床接通电源后,在预热状态下,机床各坐标轴往复运动几次,主轴按中等转速运转十多分钟后进行。
常用的检测工具有精密水平仪、精密方箱、直角尺、平尺、平行光管、千分表、测微仪及高精度主轴心棒等。
检测工具的精度必须比所设的几何精度高一个等级。
以卧式加工中心为例,要对下列几何精度进行检验:1)X、Y、Z坐标轴的相互垂直度;2)工作台面的平行度;3)X、Z轴移动时工作台面的平行度;4)主轴回转轴线对工作台面的平行度;5)主轴在Z轴方向移动的直线度;6)X轴移动时工作台边界与定位基准的平行度;7)主轴轴向及孔径跳动;8)回转工作台精度。
2. 定位精度的检验数控机床的定位精度是表明所测量的机床各运动部位在数控装置控制下,运动所能达到的精度。
因此,根据实测的定位精度数值,可以判断出机床自动加工过程中能达到的最好的工件加工精度。
(1)定位精度检测的主要内容机床定位精度主要检测内容如下:1)直线运动定位精度(包括X、Y、Z、U、V、W轴);2)直线运动重复定位精度;3) 直线运动轴机械原点的返回精度;4) 直线运动失动量的测定;5) 直线运动定位精度(转台A 、B 、C 轴);6) 回转运动重复定位精度;7) 回转轴原点的返回精度;8) 回转运动矢动量的测定。
- 1、下载文档前请自行甄别文档内容的完整性,平台不提供额外的编辑、内容补充、找答案等附加服务。
- 2、"仅部分预览"的文档,不可在线预览部分如存在完整性等问题,可反馈申请退款(可完整预览的文档不适用该条件!)。
- 3、如文档侵犯您的权益,请联系客服反馈,我们会尽快为您处理(人工客服工作时间:9:00-18:30)。
数控机床主轴旋转精度及测量方法
来源:对钩网
主轴是数控机床中的核心设备之一,担负着从机床电动机接受动力并将之传递给其他机床部件的重要责任。
工作中,要求主轴必须在承担着一定的荷载量,以及保持适当的旋转速度的前提条件下,带动在其控制范围之内的工件或者刀具,绕主轴旋转中心线进行精确、可靠而又稳定的旋转。
主轴的旋转精度直接决定了机床的加工精度。
主轴旋转精度的定义
机床主轴精度大小是以其瞬时旋转中心线与理想旋转中心线的相对位置来决定的。
在正常工作旋转时,由于主轴、轴承等的制造精度和装配、调整精度,主轴的转速、轴承的设计和性能以及主轴部件的动态特征等机械原因,造成了主轴的瞬时旋转中心线往往会与理想旋转中心线在位置上产生一定的偏离,由此产生的误差就是主轴在旋转时的瞬时误差,也称为旋转误差。
而瞬时误差的范围大小,就代表主轴的旋转精度。
加工过程中,主轴可能会延与轴垂直的方向发生径向跳动,延轴方向发生轴向窜动或以轴上某点为中心,发生角度摆动,这些运动都会降低主轴的旋转精度。
实际生产中,人们常常用安装于主轴前端的刀具或工件部位的定位面发生的三种运动的运动幅度来衡量和描述主轴精度,这三种运动分别是径向跳动、端面跳动和轴向窜动。
主轴在工作转速时的旋转精度,也称为运动精度。
目前,我国已经制订并推行了国内统一的通用机床旋转精度检验标准,根据加工对象的精度要求确定不同的主轴精度标准。
主轴精度的测量和评定
静态测量和评定法:这是一种在低速旋转环境下测定主轴旋转精度的方法,又称为打表法。
具体操作流程是,在无载荷条件下手动缓慢转动主轴,或控制主轴进行低速转动,利用千分表进行测量,测出最大度数和最小读数,计算出二者之差,即为主轴的旋转精度。
由于静态测量是在低速旋转环境下,而不是在主轴实际工作速度下进行的测量,因此并不能够反映出真正的主轴旋转精度。
动态测量和评定法:这是一种在主轴实际的工作转速之下,采用非接触式测量装置,测出主轴旋转运动精度误差的方法,包括主轴振动及高速旋转时的运动精度误差。
这种测量方法能够比较真实、全面地反映主轴的旋转精度情况。
目前已普遍采用的测量方法是:将一个标准圆球安装在主轴上,再将两个位移传感器以互成直角的方式,安装在主轴运动的两个敏感方向上。
主轴旋转时,两个位移
传感器同时测量回旋轴在不同敏感方向上的误差信息。
测量信号经放大后,由信号分析仪器或电子计算机进行处理,将结果输出到示波器上,或绘制出相应的误差图形曲线。