零件热处理变形
热处理变形的原因

热处理变形的原因在实际生产中,热处理变形给后续工序,特别是机械加工增加了很多困难,影响了生产效率,因变形过大而导致报废,增加了成本。
变形是热处理比较难以解决的问题,要完全不变形是不可能的,一般是把变形量控制在一定范围内。
一、热处理变形产生的原因钢在热处理的加热、冷却过程中可能会产生变形,甚至开裂,其原因是由于淬火应力的存在。
淬火应力分为热应力和组织应力两种。
由于热应力和组织应力作用,使热处理后零件产生不同残留应力,可能引起变形。
当应力大于材料的屈服强度时变形就会产生,因此,淬火变形还与钢的屈服强度有关,材料塑性变形抗力越大,其变形程度越小。
1.热应力在加热和冷却时由于零件表里有温差存在造成热胀冷缩的不一致而产生热应力。
零件由高温冷却时表面散热快,温度低于心部,因此表面比心部有更大的体积收缩倾向,但受心部阻碍而使表面受拉应力,而心部则受压应力。
表里温差增大应力也增大。
2.组织应力组织应力是因为奥氏体与其转变产物的比容不同,零件的表面和心部或零件各部分之间的组织转变时间不同而产生的。
由于奥氏体比容最小,淬火冷却时必然发生体积增加。
淬火时表面先开始马氏体转变,体积增大,心部仍为奥氏体体积不变。
由于心部阻碍表面体积增大,表面产生压应力,心部产生拉应力。
二、减少和控制热处理变形的方法1.合理选材和提高硬度要求对于形状复杂,截面尺寸相差较大而又要求变形较小的零件,应选择淬透性较好的材料,以便使用较缓和的淬火冷却介质淬火。
对于薄板状精密零件,应选用双向轧制板材,使零件纤维方向对称。
对零件的硬度要求,在满足使用要求前提下,尽量选择下限硬度。
2.正确设计零件零件外形应尽量简单、均匀、结构对称,以免因冷却不均匀,使变形开裂倾向增大。
尽量避免截面尺寸突然变化,减少沟槽和薄边,不要有尖锐棱角。
避免较深的不通孔。
长形零件避免截面呈横梯形。
3.合理安排生产路线,协调冷热加工与热处理的关系对于形状复杂、精度要求高的零件,应在粗、精加工之间进行预先处理,如消除应力、退火等。
1j85热处理变形
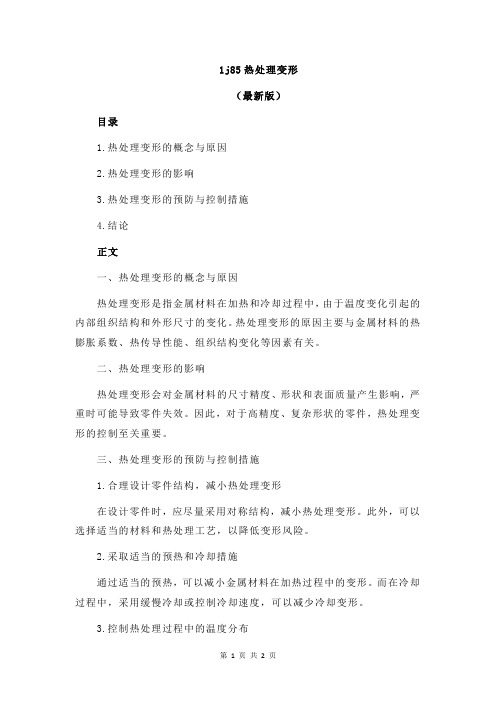
1j85热处理变形
(最新版)
目录
1.热处理变形的概念与原因
2.热处理变形的影响
3.热处理变形的预防与控制措施
4.结论
正文
一、热处理变形的概念与原因
热处理变形是指金属材料在加热和冷却过程中,由于温度变化引起的内部组织结构和外形尺寸的变化。
热处理变形的原因主要与金属材料的热膨胀系数、热传导性能、组织结构变化等因素有关。
二、热处理变形的影响
热处理变形会对金属材料的尺寸精度、形状和表面质量产生影响,严重时可能导致零件失效。
因此,对于高精度、复杂形状的零件,热处理变形的控制至关重要。
三、热处理变形的预防与控制措施
1.合理设计零件结构,减小热处理变形
在设计零件时,应尽量采用对称结构,减小热处理变形。
此外,可以选择适当的材料和热处理工艺,以降低变形风险。
2.采取适当的预热和冷却措施
通过适当的预热,可以减小金属材料在加热过程中的变形。
而在冷却过程中,采用缓慢冷却或控制冷却速度,可以减少冷却变形。
3.控制热处理过程中的温度分布
在热处理过程中,应尽量使金属材料各部分的温度分布均匀,以减少因温度差异引起的变形。
4.进行热处理后的加工
对于已经发生变形的零件,可以通过精加工来消除变形,确保零件尺寸精度和形状。
四、结论
热处理变形是金属材料在热处理过程中常见的问题,对零件的尺寸精度和形状产生影响。
通过采取合理的设计、预热和冷却措施,以及控制热处理过程中的温度分布,可以有效预防和控制热处理变形。
钢件热处理变形的原因总结

钢件热处理变形的原因总结一、材料特性:1.材料的塑性变形能力不同:不同类型的钢,具有不同的塑性特性。
一般来说,低碳钢和不锈钢等具有良好的塑性,因此容易出现变形。
而高碳钢、合金钢等则具有较差的塑性,不容易变形。
2.材料的尺寸和形状:钢件的形状和尺寸也会影响热处理的变形程度。
尺寸较大、形状复杂的钢件变形较严重,尤其是在加热和冷却不均匀的情况下。
3.各向异性:钢材具有各向异性,即材料在不同的方向上具有不同的物理性能。
不同方向上的热膨胀系数不同,会导致热处理时钢件的不均匀膨胀和收缩,从而引起变形。
二、加热冷却方式:1.加热方式:钢件的加热方式会影响变形的严重程度。
例如,采用局部加热时,钢件的局部温度差异会导致表面和内部的温度差异,进而引起不均匀的膨胀和收缩。
2.加热速率和温度:加热速率和温度的选择也会对变形产生影响。
加热速率过快会导致钢材的内外温度差异增大,形成应力集中,易引发变形。
加热温度过高或过低也会导致钢件的不均匀热膨胀和变形。
三、操作参数:1.冷却速率:冷却速率的选择会直接影响钢件的变形。
冷却速率过快,会导致表面和内部温度差异增大,进而加剧变形。
冷却速率过慢,会使钢件的内部组织结构不均匀,产生不良的热处理效果。
2.冷却介质:冷却介质的选择也与变形有关。
不同的冷却介质冷却速率不同,从而影响变形的严重程度。
例如,水冷速度较快,容易引发变形;而油冷速度较慢,变形相对较小。
3.外部约束:外部约束也是导致钢件变形的重要因素。
外力的作用会导致钢件产生应力,从而引发变形。
因此,操作过程中要合理设置约束以避免变形的发生。
综上所述,钢件热处理变形是由于材料特性、加热冷却方式和操作参数的影响导致的。
合理选择加热冷却方式和操作参数,并根据钢材的特性进行调整,可以最大限度地减少钢件热处理变形的程度,确保热处理效果的稳定性和一致性。
关于热处理零件变形的解决措施探讨

关于热处理零件变形的解决措施探讨零件结构对热处理后的变形影响极大,严重时会出现裂纹等缺陷。
因此在设计零件时,应在满足使用性能的条件下,从热处理的工艺角度出发,适当修改零件结构来改善热处理操作难度。
本文对热处理零件变形的解决措施进行了分析。
标签:热处理;零件变形;措施热处理变形是指零件经热处理后其变形量超过了图样公差要求的一种物理现象。
设计人员设计零件的主要任务是确定零件的几何形状、机械性能要求、尺寸精度和选定材料牌号等等。
热处理目的是使零件获得所要求的机械性能和力学性能。
当热处理零件出现破损、弯曲、变形、发裂等现象时,人们常从材料的质量、热处理工艺使用不当或其他实际情况寻找发生变形的原因;除此之外,还应该从设计人员开始设计零件时的零件结构设计、材料选择、制定热处理技术要求等方面寻找原因,减少热处理的困难,和造成废品、反修品和零件在使用中的失效的情况。
因此设计人员必须在零件设计之初充分考虑零件结构在热处理中会不会引起变形或开裂等因素。
一、零件的结构分析变形和开裂是由热应力与组织应力共同作用的结果。
热应力是由于工件在加热和冷却时各部热胀冷缩不一致而产生;工件在加热时厚度大的传热较慢热胀也就慢,冷却时,厚度大的冷却也较慢冷缩也就慢,因此厚度大的结构限制了厚度薄的结构的热胀和冷缩。
组织应力是由于加热和冷却时组织转变不同时而产生。
同理,由于工件厚薄的差异,厚度较大的结构无论加热或冷却组织转变都滞后厚度较薄的结构,因此,引起体积膨胀或收缩也不一致。
同样厚度较大的结构限制了其它结构的组织转变。
明确了应力产生的原因与工件的结构有直接关系,零件设计,编制加工与工件的热处理变形有很大的关系,在零件设计时注意工件的截面积不宜过于悬殊,且截面形状尽量对称。
如设计时无法调整,在工件热处理前采用工艺调整的方法预留较大的加工余量或预留工艺台,在热处理后去除预留结构;在工件结构较薄处加副结构。
二、从设计方面考虑2.1合理选用材料。
薄壁件热处理变形
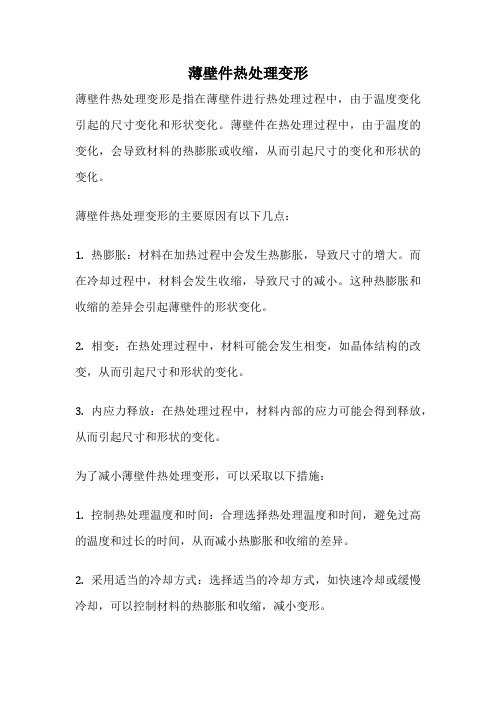
薄壁件热处理变形
薄壁件热处理变形是指在薄壁件进行热处理过程中,由于温度变化引起的尺寸变化和形状变化。
薄壁件在热处理过程中,由于温度的变化,会导致材料的热膨胀或收缩,从而引起尺寸的变化和形状的变化。
薄壁件热处理变形的主要原因有以下几点:
1. 热膨胀:材料在加热过程中会发生热膨胀,导致尺寸的增大。
而在冷却过程中,材料会发生收缩,导致尺寸的减小。
这种热膨胀和收缩的差异会引起薄壁件的形状变化。
2. 相变:在热处理过程中,材料可能会发生相变,如晶体结构的改变,从而引起尺寸和形状的变化。
3. 内应力释放:在热处理过程中,材料内部的应力可能会得到释放,从而引起尺寸和形状的变化。
为了减小薄壁件热处理变形,可以采取以下措施:
1. 控制热处理温度和时间:合理选择热处理温度和时间,避免过高的温度和过长的时间,从而减小热膨胀和收缩的差异。
2. 采用适当的冷却方式:选择适当的冷却方式,如快速冷却或缓慢冷却,可以控制材料的热膨胀和收缩,减小变形。
3. 采用适当的工艺参数:调整热处理的工艺参数,如加热速度、冷却速度等,可以减小薄壁件的变形。
4. 采用适当的夹具和支撑:在热处理过程中,使用适当的夹具和支撑,可以控制薄壁件的形状变化,减小变形。
薄壁件热处理变形是一个复杂的问题,需要综合考虑材料的性质、热处理工艺参数等因素,采取合适的措施来减小变形。
钢件热处理容易变形的温度
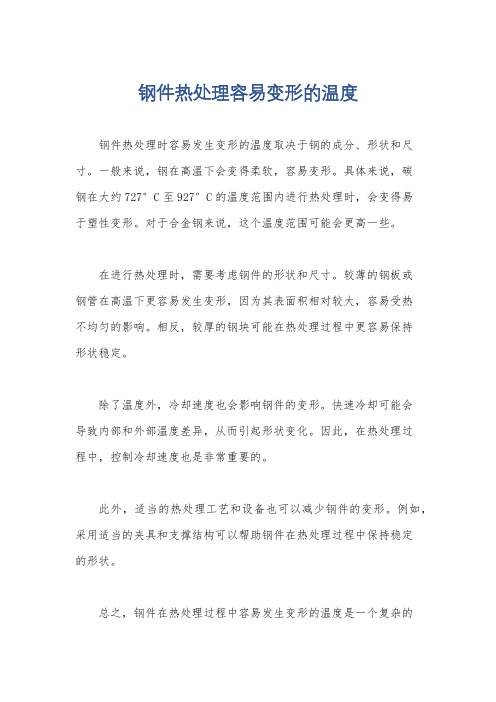
钢件热处理容易变形的温度
钢件热处理时容易发生变形的温度取决于钢的成分、形状和尺寸。
一般来说,钢在高温下会变得柔软,容易变形。
具体来说,碳
钢在大约727°C至927°C的温度范围内进行热处理时,会变得易
于塑性变形。
对于合金钢来说,这个温度范围可能会更高一些。
在进行热处理时,需要考虑钢件的形状和尺寸。
较薄的钢板或
钢管在高温下更容易发生变形,因为其表面积相对较大,容易受热
不均匀的影响。
相反,较厚的钢块可能在热处理过程中更容易保持
形状稳定。
除了温度外,冷却速度也会影响钢件的变形。
快速冷却可能会
导致内部和外部温度差异,从而引起形状变化。
因此,在热处理过
程中,控制冷却速度也是非常重要的。
此外,适当的热处理工艺和设备也可以减少钢件的变形。
例如,采用适当的夹具和支撑结构可以帮助钢件在热处理过程中保持稳定
的形状。
总之,钢件在热处理过程中容易发生变形的温度是一个复杂的
问题,需要综合考虑钢的成分、形状、尺寸以及热处理工艺等因素。
在实际操作中,需要根据具体情况采取合适的措施来减少变形的发生。
解决热处理零件变形的几个措施

结构在热 处理 中会不 会引起 变形或 开裂等 因素 。
一
、
从设计 方面考虑
裂或变 形 ,截 面变化 超过 1 的工件不 宜在水 中淬火 , : 4 应
1合理选 用材料 。零 件 的材料是实 现热处 理 目的的 .
重要条件 希望 所选用 的材料具 备达到所 需性 能要求 , 与
此 同时还 要具备 与热处理工 艺相适 应的能力 。即能 够承 受热处理 操作 。 () 1尺寸效 应 , 同一化 学成分 在同一情 况进行 热处 即
理状态下 的钢 ,由于钢 的淬透 性影 响和钢 的结 构尺 寸增
大 , 的 内部组 织产 生冶金缺 陷 ( 偏析 、 钢 如 疏松 、 非金 属夹
选择和热处理工艺有关 , 但零件结构设计是否设计合理 也是产生淬火变形和裂纹的重要原因。目 前尚无标准为
; i
设计提 供充足 的数 据 ,但设 计者应尽 可能做到 零件形状 ÷ 和尺寸 精度 的合 理化 , 以改善其 零件 的热 处理工艺性 。 U- z. l - , 5 零 件 的结构 应力求 简单 、 对称 . 以减少 变形 和翘 曲 ,
件 上 的 尖 角 和 棱 角 在 淬 火 加 热 时 容 易 过 热 ,容 易 产 生 应 力集 中 , 成淬火 裂纹 。 形
曛
辽辽
丁 丁
解决 热处理零 件变形 的几个措施
李 斐 石 玉 生 2
经经
济济 职 管
业理
技 干 术部 学学 院院
( . 宁 经 济 管理 干 部 学 院 , 宁 沈 阳 1 0 2 ; 1辽 辽 1 1 2 2沈 阳金 杯 车辆 制 造 有 限公 司 , 宁 沈 阳 10 1 ) . 辽 10 5
热处理变形的原因
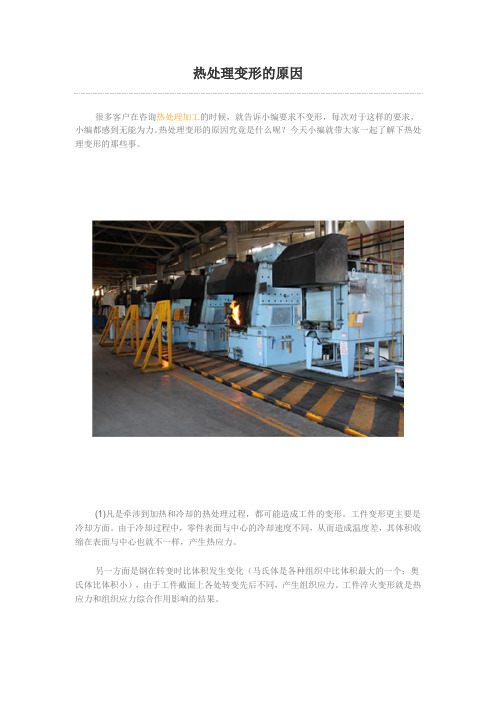
很多客户在咨询热处理加工的时候,就告诉小编要求不变形,每次对于这样的要求,小编都感到无能为力。
热处理变形的原因究竟是什么呢?今天小编就带大家一起了解下热处理变形的那些事。
(1)凡是牵涉到加热和冷却的热处理过程,都可能造成工件的变形。
工件变形更主要是冷却方面。
由于冷却过程中,零件表面与中心的冷却速度不同,从而造成温度差,其体积收缩在表面与中心也就不一样,产生热应力。
另一方面是钢在转变时比体积发生变化(马氏体是各种组织中比体积最大的一个;奥氏体比体积小),由于工件截面上各处转变先后不同,产生组织应力。
工件淬火变形就是热应力和组织应力综合作用影响的结果。
(2)工件的结构形状、原材料质量、热处理前的加工状态、工件的自重以及工件在炉中加热和冷却时的支承或夹持不当,冷却投入方向、方法和冷却时在冷却中的动作不当等也能引起变形。
加热温度高,冷却速快,故淬火变形最为严重。
(3)工件热处理后的不稳定组织和不稳定的应力状态,在常温和零下温度长时间放置或使用过程中,逐渐发生转变而趋于稳定,也会伴随引起工件的变形,这种变形称为时效变形。
时效变形虽然不大,但是对于精密零件和标准量具也不许的。
实际生产中必须予以防止。
(4)热处理过程中产生的内应力有
热应力和相变应力,它们的形成原因和作用是不同的。
这种应力在热处理过程中对变形影响是主要的原因。
钢件热处理变形的原因总结

钢件热处理变形的原因总结
引起热处理变形的因素颇多,总括起来,基本上有三点:
1、固态相变时,各相质量体积的变化必然引起体积的变化,造成零件的胀与缩的尺寸变化;
2、热应力,包括急热热应力和急冷热应力,当它们超过零件在该温度下所具有的屈服极限时,将使零件产生塑性变形,造成零件的形状变化,即歪扭,或称为畸变;
3、组织应力也会引起形状的改变,即畸变。
一般说,淬火工件的变形总是由于以上的两种或三种因素综合作用的结果,但究竟哪一个因素对变形的影响较大,则需要具体情况作具体的分析。
总的来说,体积变化是由相变时比容的改变而引起的。
马氏体的质量体积比钢的其他组成相的质量体积要大,热处理时钢由其他组成相转化为马氏体时,必然引起体积的增加。
而奥氏体的质量体积要比钢的其他组织质量体积要小,在热处理时由其他组成相转变为奥氏体时,则引起体积的减小。
关于形状的变化,歪扭或称为畸变,主要是由于内应力或者外加应力作用的结果。
在加热、冷却过程中,因工件各个部位的温度有差别,相变在时间上有先后,有时发生的组织转变也不一致,而造成内应力。
这种内应力一旦超过了该温度下材料的屈服极限,就产生塑性变形,引起形状的改变。
此外工件内的冷加工残余应力在加热过程中的松弛,以及由于加热时受到较大的外加应力也会引起形状的变化。
在热处理时可能引起体积变化和形状变化的原因见下表。
表中“体积变化原因” 一栏未列入钢因热胀冷缩现象而产生的体积变化,钢由淬火加热温度到零下温度进行冷处理,均随温度的变化而有相应的体积变化,因热胀冷缩而引起的体积变化不均匀乃是热应力产生的原因,而且对变形有相当的影响。
热处理可能引起体积变化和形状变化的原因。
7个减小热处理变形的方法

7个减小热处理变形的方法热处理是通过加热和冷却金属材料来改变其性质的过程。
在进行热处理过程中,材料会发生变形,这是由于温度和应力的变化引起的。
为了减小热处理过程中的变形,可以采取以下7种方法:1.加工前热处理:在材料进行初次加工之前,可以进行热处理以减小后续加工过程中的变形。
这样可以通过改变材料的晶体结构和分布来改变其屈服强度和塑性,从而减小变形。
2.采用复合材料:复合材料由两种或多种不同的材料组成,其中一个材料具有较高的强度和刚性,而另一个材料具有较高的韧性和延展性。
通过使用复合材料,可以在一定程度上减小热处理过程中的变形。
3.控制变形工艺参数:在进行热处理过程中,可以通过控制加热温度、冷却速率和时间等参数来减小变形。
例如,降低加热温度和冷却速率可以减少变形量。
4.施加局部应力:在进行热处理过程中,可以在材料上施加一定的局部应力来减小整体的变形。
这可以通过冷却或加热过程中施加压力实现,从而使材料变形更加均匀。
这种方法可以大大降低材料的变形量。
5.使用支撑装置:在进行热处理过程中,可以使用支撑装置或夹具来固定材料,以减小变形。
这些支撑装置可以帮助保持材料的形状和尺寸,从而降低变形。
6.采用适当的冷却介质:在进行热处理过程中,选择适当的冷却介质可以减小变形。
不同的冷却介质具有不同的冷却速率,可以根据需要选择合适的冷却介质,以减小变形。
7.进行后续时效处理:在进行热处理后,可以进行后续的时效处理以减小变形。
时效处理是通过在一定时间内将材料保持在一定的温度下,使其继续发生晶体结构和性质的变化。
这样可以通过改变材料的结构和性质来减小变形。
热处理变形产生的原因及控制方法
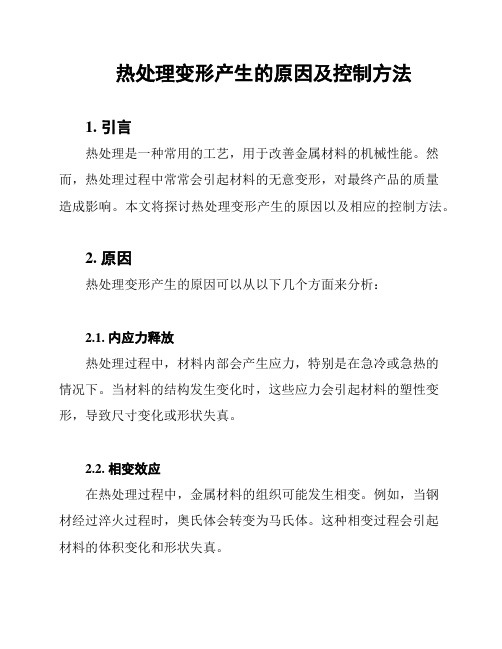
热处理变形产生的原因及控制方法1. 引言热处理是一种常用的工艺,用于改善金属材料的机械性能。
然而,热处理过程中常常会引起材料的无意变形,对最终产品的质量造成影响。
本文将探讨热处理变形产生的原因以及相应的控制方法。
2. 原因热处理变形产生的原因可以从以下几个方面来分析:2.1. 内应力释放热处理过程中,材料内部会产生应力,特别是在急冷或急热的情况下。
当材料的结构发生变化时,这些应力会引起材料的塑性变形,导致尺寸变化或形状失真。
2.2. 相变效应在热处理过程中,金属材料的组织可能发生相变。
例如,当钢材经过淬火过程时,奥氏体会转变为马氏体。
这种相变过程会引起材料的体积变化和形状失真。
2.3. 不均匀加热或冷却如果热处理过程中加热或冷却不均匀,材料的局部温度会存在差异。
这种温度差异会导致材料的非均匀膨胀或收缩,从而引起变形。
3. 控制方法为了减少热处理产生的变形,可以采取以下控制方法:3.1. 控制加热和冷却速率合理控制加热和冷却速率,避免过快或过慢,可以减少材料的变形。
在进行急冷或急热处理时,可以采取预先控制的温度梯度,以缓解内应力的释放。
3.2. 优化工艺参数通过调整热处理过程中的工艺参数,如温度、时间和冷却介质等,可以最大限度地减少材料的变形。
合理选择工艺参数,可以提高材料的均匀性和稳定性。
3.3. 采用合适的支撑结构对于形状复杂的工件,可以采用合适的支撑结构来减少变形。
支撑结构可以提供一定的约束,防止材料发生不受控制的变形。
4. 结论热处理变形是热处理过程中常见的问题,但通过合理的控制方法可以有效减少其影响。
合理控制加热和冷却速率、优化工艺参数以及采用合适的支撑结构都是减少热处理变形的有效途径。
这些控制方法可以提高最终产品的质量和性能。
---以上是关于热处理变形产生的原因及控制方法的内容。
请基于以上内容,进一步完善和添加具体细节,使文档达到800字以上的要求。
零件过盈压装后变形原因

零件过盈压装后变形原因零件变形的影响因素有:1、内力作用导致零件加工精度改变机床加工时,通常是利用向心力的作用,用车床的三爪或者四爪卡盘,把零件卡紧,然后对机械零件进行加工。
同时,为了确保零件在受力时不松动、减小内径向力的作用,必须要使夹紧力大于机械的切削力。
夹紧力随着切削力的增大而增大,随之减小而减小。
这样的操作才能使机械零件在加工过程中受力稳定。
但是,在三爪或者四爪卡盘松开后,加工出来的机械零件就会与原来的相差甚远,有的呈现多边形,有的呈现椭圆形,出现较大偏差。
2、热处理加工后容易产生变形问题对于薄片类的机械零件,由于其长径非常大,在对其进行热处理后容易出现草帽弯曲的状况。
一方面会出现中间鼓出的现象,平面偏差增大,另一方面由于各种外界因素的影响,使零件产生弯曲现象。
这些变形问题的产生不仅是由于热处理后的零件内应力发生了变化,还有操作人员的专业知识不扎实,不太了解零件的结构稳定性,从而增大了零件变形的概率。
3、外力作用下引起的弹性变形在机械加工中零件出现弹性形变的原因主要有几个方面。
(1)是一些零件的内部构造中如果含有薄片,就会对操作方法有更高要求,否则在操作人员在对零件进行定位和装夹时,不能和图纸的设计之间进行对应,容易导致弹性形变的产生。
(2)是车床和夹具的不平整,使零件在进行固定时两侧的受力不均匀,导致切割时受力作用小的一边在力的作用下就会出现平移出现零件变形。
(3)是在加工过程中零件的定位不合理,使零件的刚性强度降低。
(4)是切削力的存在也是引起零件弹性形变的原因之一。
这些不同的原因导致的弹性形变,都说明外力作用对机械零件加工质量的影响。
机械加工中,由于受环境,人为,夹具,机床的因素等等,做出来的工件会出现弯曲也就是说变形,在加工过程中最常见的就是加10mm厚度以下的工件变形最为常见,有些工件由于有平面度,平行度要求,那么工件变形就会导致这些位置尺寸达不到要求,从而直接影响产品质量,那么常见的引起变形的因素有哪些呢,我就以自己的加工经验告诉你们。
热处理变形校正方法

热处理变形校正方法在金属加工行业中,热处理是一个至关重要的环节,它能够改善材料的性能,为产品提供必要的强度和硬度。
然而,热处理过程中往往伴随着变形的问题,这给产品质量带来了挑战。
本文将详细介绍热处理变形校正的方法,帮助读者更好地理解和应对这一工艺难题。
一、热处理变形的原因热处理变形主要是由于材料在加热和冷却过程中,内部应力重新分布所导致的。
当材料暴露在高温环境下,其晶体结构会发生改变,冷却后,这些改变会导致尺寸变化和形状变形。
二、热处理变形校正方法1.预防措施:- 选择合适的材料:不同材料的热处理变形程度不同,选择变形较小的材料是预防变形的有效手段。
- 优化热处理工艺:通过调整加热速度、保温时间、冷却速度等参数,降低热处理变形的风险。
2.变形校正方法:- 机械校正:通过机械力对变形部位进行校正,如锤击、拉伸等,但这种方法仅适用于轻微变形。
- 热校正:利用材料在高温下的塑性变形,对变形部位进行加热至适当温度后进行校正。
这种方法对操作技术要求较高,需防止过度加热导致新的变形。
- 液体校正:将变形部位浸入高温液体中,利用液体的压力和温度对变形进行校正。
此方法适用于复杂形状的零件。
3.数控加工校正:- 采用数控加工技术,根据变形量对零件进行精确加工,以消除变形影响。
这种方法适用于高精度要求的零件。
4.表面处理:- 对变形部位进行表面处理,如喷漆、氧化等,以掩盖或补偿变形。
三、总结热处理变形是金属加工中不可避免的问题,但通过合理的预防措施和校正方法,可以最大限度地降低变形对产品质量的影响。
在实际操作中,应根据具体情况选择合适的校正方法,确保产品达到预期的性能和质量要求。
1j85热处理变形
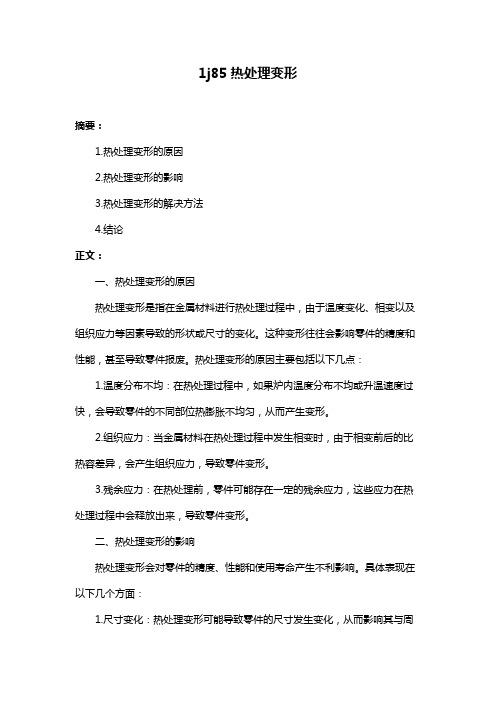
1j85热处理变形摘要:1.热处理变形的原因2.热处理变形的影响3.热处理变形的解决方法4.结论正文:一、热处理变形的原因热处理变形是指在金属材料进行热处理过程中,由于温度变化、相变以及组织应力等因素导致的形状或尺寸的变化。
这种变形往往会影响零件的精度和性能,甚至导致零件报废。
热处理变形的原因主要包括以下几点:1.温度分布不均:在热处理过程中,如果炉内温度分布不均或升温速度过快,会导致零件的不同部位热膨胀不均匀,从而产生变形。
2.组织应力:当金属材料在热处理过程中发生相变时,由于相变前后的比热容差异,会产生组织应力,导致零件变形。
3.残余应力:在热处理前,零件可能存在一定的残余应力,这些应力在热处理过程中会释放出来,导致零件变形。
二、热处理变形的影响热处理变形会对零件的精度、性能和使用寿命产生不利影响。
具体表现在以下几个方面:1.尺寸变化:热处理变形可能导致零件的尺寸发生变化,从而影响其与周边零件的配合精度,降低整机的工作性能。
2.形状翘曲:热处理过程中产生的变形可能导致零件形状翘曲,影响其外观和功能。
3.裂纹产生:严重变形可能导致零件产生裂纹,从而降低其使用寿命和可靠性。
4.加工难度增加:热处理变形可能使零件的加工精度降低,导致后续加工难度增加,提高生产成本。
三、热处理变形的解决方法为了避免或减小热处理变形,可以采取以下措施:1.合理设计零件:在设计阶段考虑热处理变形的影响,采用适当的结构和材料,以减小变形的可能性。
2.控制热处理过程:严格控制热处理过程中的温度、时间和冷却速度等参数,保证温度分布均匀,避免过快升温和降温。
3.采取预处理措施:在热处理前进行预处理,如退火、正火等,以消除残余应力,减小热处理变形。
4.调整加工顺序:对于较小、形状复杂的零件,可以先进行半精加工,热处理后再进行精加工,以减小热处理变形对加工精度的影响。
四、结论综上所述,热处理变形对零件的精度和性能有很大影响,需要采取合理措施进行控制。
各种热处理工艺造成变形的原因总结

各种热处理工艺造成变形的原因总结引言:热处理工艺是一种常见的金属加工方法,它通过对金属材料进行加热和冷却来改变其结构和性能。
然而,热处理过程中往往会导致材料发生变形,这对于一些精密零件的加工和制造带来一定的困扰。
本文将从各种热处理工艺的角度,总结造成变形的原因,并探讨相应的解决方法。
一、淬火过程中的变形原因淬火是一种通过快速冷却来使金属材料达到高强度和硬度的热处理工艺。
然而,淬火过程中常常会出现变形现象。
造成淬火变形的主要原因有以下几点:1. 冷却速度不均匀:淬火过程中,材料表面和内部的冷却速度不一致,导致应力不均匀分布,从而引起变形。
2. 材料内部组织不均匀:金属材料内部的组织不均匀,如晶粒尺寸、相含量等差异,会导致淬火时的收缩和变形不一致。
3. 冷却介质选择不当:不同的冷却介质对材料的冷却速度有不同的影响,选择不当可能导致应力集中和变形。
解决方法:针对淬火过程中的变形问题,可以采取以下措施:1. 控制冷却速度:通过优化冷却介质的选择和控制冷却速度,使材料表面和内部的冷却速度尽可能一致,减少应力的不均匀分布。
2. 优化材料组织:通过调整材料的化学成分和热处理工艺,使材料内部的组织更加均匀,减少淬火时的收缩和变形差异。
3. 采用适当的淬火工艺:根据材料的特性和要求,选择适当的淬火工艺,控制冷却速度和温度,减少变形的发生。
二、退火过程中的变形原因退火是一种通过加热和缓慢冷却来改善材料的性能和结构的热处理工艺。
然而,退火过程中同样存在变形的问题。
造成退火变形的主要原因有以下几点:1. 温度不均匀:退火过程中,材料的温度分布不均匀,导致应力分布不均匀,从而引起变形。
2. 冷却速度过快:退火结束后,如果冷却速度过快,会导致材料内部的残余应力无法得到充分释放,从而引起变形。
3. 材料内部缺陷:金属材料内部存在各种缺陷,如气孔、夹杂物等,这些缺陷在退火过程中会扩散和移动,导致变形的发生。
解决方法:针对退火过程中的变形问题,可以采取以下措施:1. 控制温度均匀性:通过合理设计加热设备和工艺参数,确保材料的温度分布均匀,减少应力的不均匀分布。
套类零件热处理变形的几个规律
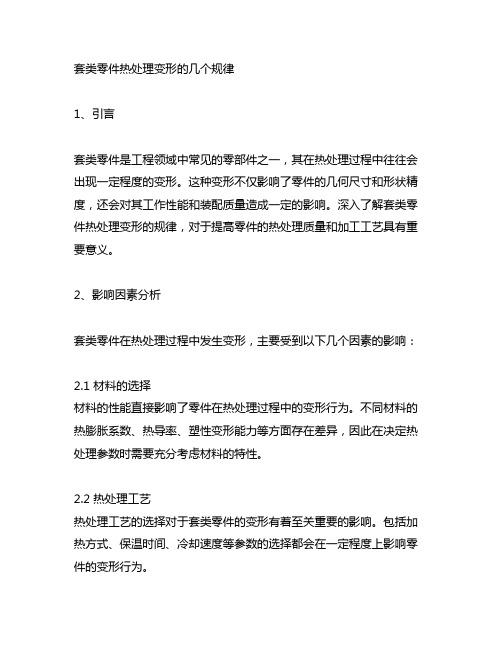
套类零件热处理变形的几个规律1、引言套类零件是工程领域中常见的零部件之一,其在热处理过程中往往会出现一定程度的变形。
这种变形不仅影响了零件的几何尺寸和形状精度,还会对其工作性能和装配质量造成一定的影响。
深入了解套类零件热处理变形的规律,对于提高零件的热处理质量和加工工艺具有重要意义。
2、影响因素分析套类零件在热处理过程中发生变形,主要受到以下几个因素的影响:2.1 材料的选择材料的性能直接影响了零件在热处理过程中的变形行为。
不同材料的热膨胀系数、热导率、塑性变形能力等方面存在差异,因此在决定热处理参数时需要充分考虑材料的特性。
2.2 热处理工艺热处理工艺的选择对于套类零件的变形有着至关重要的影响。
包括加热方式、保温时间、冷却速度等参数的选择都会在一定程度上影响零件的变形行为。
2.3 几何形状零件本身的几何形状也是影响其热处理变形的重要因素。
壁厚不均匀、孔的分布密度、壁厚、几何形状等都会影响套类零件在热处理中的变形行为。
3、变形规律分析根据对上述影响因素的分析,套类零件在热处理过程中的变形存在一定的规律性,主要包括以下几个方面:3.1 热处理收缩在套类零件的热处理过程中,由于材料的热膨胀系数不同,可能会导致零件在冷却过程中发生一定程度的收缩。
这种收缩一般会导致套类零件的几何尺寸发生变化,需要在设计和加工过程中进行合理的补偿。
3.2 内外端温差引起的变形在热处理过程中,套类零件的内外壁温度分布存在差异,会导致内外端产生不同程度的收缩,从而引起零件的不均匀变形。
因此在热处理工艺设计时需要充分考虑内外端温差的影响。
3.3 孔的收缩变形套类零件中的孔在热处理过程中往往会出现收缩变形的情况。
孔的收缩对于套类零件的组装质量和工作性能都会产生一定的影响,因此需要针对孔的收缩变形进行合理的处理和补偿。
4、个人观点和总结套类零件在热处理过程中的变形是一个复杂的过程,受到材料、热处理工艺和几何形状等多方面因素的影响。
薄壁件热处理变形
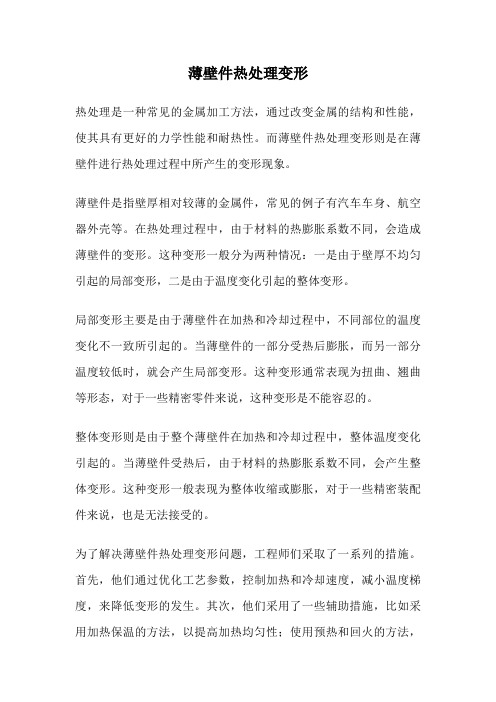
薄壁件热处理变形热处理是一种常见的金属加工方法,通过改变金属的结构和性能,使其具有更好的力学性能和耐热性。
而薄壁件热处理变形则是在薄壁件进行热处理过程中所产生的变形现象。
薄壁件是指壁厚相对较薄的金属件,常见的例子有汽车车身、航空器外壳等。
在热处理过程中,由于材料的热膨胀系数不同,会造成薄壁件的变形。
这种变形一般分为两种情况:一是由于壁厚不均匀引起的局部变形,二是由于温度变化引起的整体变形。
局部变形主要是由于薄壁件在加热和冷却过程中,不同部位的温度变化不一致所引起的。
当薄壁件的一部分受热后膨胀,而另一部分温度较低时,就会产生局部变形。
这种变形通常表现为扭曲、翘曲等形态,对于一些精密零件来说,这种变形是不能容忍的。
整体变形则是由于整个薄壁件在加热和冷却过程中,整体温度变化引起的。
当薄壁件受热后,由于材料的热膨胀系数不同,会产生整体变形。
这种变形一般表现为整体收缩或膨胀,对于一些精密装配件来说,也是无法接受的。
为了解决薄壁件热处理变形问题,工程师们采取了一系列的措施。
首先,他们通过优化工艺参数,控制加热和冷却速度,减小温度梯度,来降低变形的发生。
其次,他们采用了一些辅助措施,比如采用加热保温的方法,以提高加热均匀性;使用预热和回火的方法,来缓解应力和变形。
工程师们还不断研发新的材料和工艺,以降低薄壁件热处理变形的发生。
比如,他们研究了一种具有低热膨胀系数的新材料,以减小变形的程度;他们还研究了一种新的热处理工艺,以提高薄壁件的热稳定性。
薄壁件热处理变形是一个复杂的问题,需要综合考虑材料的热膨胀系数、壁厚和加热冷却过程等因素。
工程师们通过优化工艺参数、采用辅助措施和研发新材料工艺等手段,不断寻求解决方案,以降低薄壁件热处理变形的发生,提高产品的质量和性能。
- 1、下载文档前请自行甄别文档内容的完整性,平台不提供额外的编辑、内容补充、找答案等附加服务。
- 2、"仅部分预览"的文档,不可在线预览部分如存在完整性等问题,可反馈申请退款(可完整预览的文档不适用该条件!)。
- 3、如文档侵犯您的权益,请联系客服反馈,我们会尽快为您处理(人工客服工作时间:9:00-18:30)。
零件热处理变形
一、引言
零件热处理是一种重要的材料加工技术,它能够改善材料的性能和延长使用寿命。
然而,在零件热处理过程中,由于温度和应力的影响,零件可能会发生变形。
这种变形会对零件的尺寸和形状造成影响,从而影响其功能和性能。
因此,了解零件热处理变形的原因和控制方法对于保证零件质量和稳定性具有重要意义。
二、零件热处理变形原因
1.温度梯度引起的变形
在热处理过程中,由于加热和冷却速度不同,导致不同部位温度存在梯度差异。
这种温度梯度会引起材料内部应力分布不均匀,从而导致变形。
2.相变引起的变形
在一些特殊的材料中,在热处理过程中会发生相变现象。
相变时产生的体积变化会导致材料产生应力分布不均匀,从而导致变形。
3.机械加工残余应力引起的变形
在机械加工过程中,由于切削和加工等原因,零件内部会产生残余应力。
在进行热处理时,残余应力会被释放,从而导致变形。
4.材料的热膨胀引起的变形
在热处理过程中,由于材料温度升高,导致材料发生热膨胀。
这种膨
胀会导致材料产生应力分布不均匀,从而导致变形。
三、零件热处理变形控制方法
1.优化加热和冷却方式
在进行零件热处理时,可以通过优化加热和冷却方式来减少温度梯度
的影响。
例如,在加热过程中采用均匀加热方式,在冷却过程中采用
缓慢冷却方式等。
2.控制相变过程
在进行特殊材料的热处理时,需要控制相变过程来减少变形。
例如,
在进行淬火处理时可以采用间歇淬火或油淬等方式来控制相变速率。
3.预处理机械加工残余应力
在进行零件热处理前,可以通过预处理机械加工残余应力来减少变形。
例如,在机械加工后进行热处理前可以进行退火处理来释放残余应力。
4.控制材料的热膨胀
在进行零件热处理时,可以通过控制材料的热膨胀来减少变形。
例如,在加热过程中可以采用局部加热或多次加热等方式来控制材料的膨胀。
四、结论
零件热处理变形是一个复杂的问题,其产生原因和控制方法需要综合考虑。
在实际应用中,需要根据具体情况选择合适的控制方法来减少变形。
通过合理的控制方法,可以提高零件质量和稳定性,从而满足不同领域对零件性能的要求。