精馏过程的节能途径及新型的精馏技术
精馏过程的节能途径及新型的精馏技术
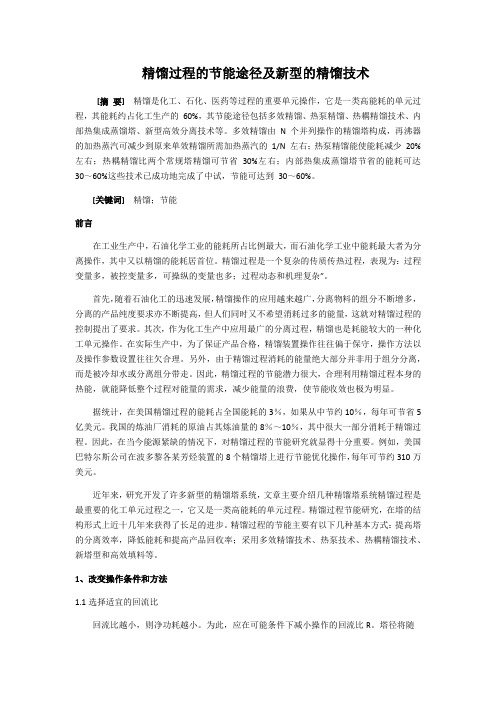
精馏过程的节能途径及新型的精馏技术[摘要]精馏是化工、石化、医药等过程的重要单元操作,它是一类高能耗的单元过程,其能耗约占化工生产的60%,其节能途径包括多效精馏、热泵精馏、热耦精馏技术、内部热集成蒸馏塔、新型高效分离技术等。
多效精馏由N 个并列操作的精馏塔构成,再沸器的加热蒸汽可减少到原来单效精馏所需加热蒸汽的1/N 左右;热泵精馏能使能耗减少20%左右;热耦精馏比两个常规塔精馏可节省30%左右;内部热集成蒸馏塔节省的能耗可达30~60%这些技术已成功地完成了中试,节能可达到30~60%。
[关键词]精馏;节能前言在工业生产中,石油化学工业的能耗所占比例最大,而石油化学工业中能耗最大者为分离操作,其中又以精馏的能耗居首位。
精馏过程是一个复杂的传质传热过程,表现为:过程变量多,被控变量多,可操纵的变量也多;过程动态和机理复杂”。
首先,随着石油化工的迅速发展,精馏操作的应用越来越广,分离物料的组分不断增多,分离的产品纯度要求亦不断提高,但人们同时又不希望消耗过多的能量,这就对精馏过程的控制提出了要求。
其次,作为化工生产中应用最广的分离过程,精馏也是耗能较大的一种化工单元操作。
在实际生产中,为了保证产品合格,精馏装置操作往往偏于保守,操作方法以及操作参数设置往往欠合理。
另外,由于精馏过程消耗的能量绝大部分并非用于组分分离,而是被冷却水或分离组分带走。
因此,精馏过程的节能潜力很大,合理利用精馏过程本身的热能,就能降低整个过程对能量的需求,减少能量的浪费,使节能收效也极为明显。
据统计,在美国精馏过程的能耗占全国能耗的3%,如果从中节约10%,每年可节省5亿美元。
我国的炼油厂消耗的原油占其炼油量的8%~10%,其中很大一部分消耗于精馏过程。
因此,在当今能源紧缺的情况下,对精馏过程的节能研究就显得十分重要。
例如,美国巴特尔斯公司在波多黎各某芳烃装置的8个精馏塔上进行节能优化操作,每年可节约310万美元。
近年来,研究开发了许多新型的精馏塔系统,文章主要介绍几种精馏塔系统精馏过程是最重要的化工单元过程之一,它又是一类高能耗的单元过程。
精馏过程节能技术综述

精馏过程节能技术综述现代工业生产过程中,精馏过程是十分常见的一种操作,用于从混合物中分离出不同组分。
然而,传统的精馏过程存在能源浪费的问题,因为它需要大量的能源来进行加热和冷却。
因此,如何降低精馏过程的能源消耗成为了一个重要的研究方向。
在过去的几十年里,研究人员提出了多种节能技术,以下综述了一些常见的节能技术。
首先,改进传统精馏塔的设计是一种简单但有效的节能方法。
例如,使用多级精馏塔可以增加分馏塔的效率,减少需加热和冷却的动力。
此外,增加塔内的换热面积也可以改善能量利用率。
此外,通过使用先进的塔内填料和分布器,可以提高物质的传质效率,从而减少所需的塔高和物料回流比例。
其次,热力耦合是另一种常用的节能技术。
该技术通过将不同温度的流体进行热交换,来降低能源消耗。
例如,实施热力耦合可以将进出精馏塔的气体进行热交换,从而降低所需的加热和冷却负荷。
此外,热力耦合还可以用于塔内热交换,例如通过使用塔内回流来预热进入精馏塔的物料。
另外,采用较低的工艺温度和压力也可以有效地减少精馏过程的能耗。
降低工艺温度可以减少所需的加热负荷,而降低工艺压力可以减少所需的冷却负荷。
因此,在设计和操作精馏过程时,应考虑选取较低的工艺温度和压力,以降低能源消耗。
此外,使用较低的辅助能源,如太阳能、余热等,也是一种常用的节能技术。
太阳能可以用于提供所需的加热或冷却能量,从而降低对传统能源的依赖。
余热是指在其他工艺过程中产生的废热,在精馏过程中可以被回收利用,用于提供所需的加热或冷却能源,进一步减少能源消耗。
最后,引入新的分离技术也是提高精馏过程能耗效率的一种途径。
例如,膜分离技术被广泛应用于分离混合物中的气体或液体组分,并且其能耗通常较低。
相比传统的蒸馏过程,膜分离技术不需要额外的加热和冷却能源,因此能够有效地节约能源。
总的来说,精馏过程节能技术的研究和应用对能源的合理利用具有重要意义。
通过改进传统精馏塔的设计、热力耦合、降低工艺温度和压力、使用低辅助能源和引入新的分离技术等方法,可以有效地降低精馏过程的能耗。
精馏过程的节能降耗

精馏过程的节能降耗精馏过程在化工产业中是一项重要的分离技术,但是它也是能耗较高的过程。
为了降低能耗,节能降耗已经成为精馏技术的一个重要研究方向。
本文将介绍几种精馏过程的节能降耗技术。
首先,提高精馏塔的热效率是提高精馏过程的一个关键。
一种常见的做法是引入换热器网络来最大程度地利用出塔冷凝液和进塔蒸汽之间的热量传递。
这种方法可以降低所需的蒸汽量,从而降低了能耗。
此外,还可以使用多效精馏、热泵或采用废热回收技术进一步提高热效率。
其次,提高精馏过程的物质效率也是节能降耗的一个重要途径。
物质效率是指在精馏过程中使用的干燥剂或者吸附剂能够更有效地去除杂质,从而减少能耗。
通过改进精馏塔的操作条件,如温度、压力和液体流速等参数,可以提高物质效率。
同时,使用高效的精馏填料或者塔板也能够提高分离效果,减少杂质的含量。
此外,使用先进的辅助技术可以进一步降低精馏过程的能耗。
例如,在精馏过程中引入膜分离技术可以减少能源消耗。
膜分离技术是一种基于材料表面或孔隙的选择性渗透性原理分离混合物的方法。
与传统的溶剂萃取或者蒸馏技术相比,膜分离技术具有能耗低、操作简单、体积小等优点。
通过将膜分离技术与精馏过程相结合,可以实现更高效的分离效果。
最后,优化精馏过程的操作策略也是节能降耗的一个重要途径。
通过优化参数设定和控制策略,可以使精馏过程更加稳定和高效。
例如,采用先进的控制算法,如模型预测控制或者模糊控制算法,可以实现对精馏过程的快速响应和精确控制,从而降低了能耗和运行成本。
总的来说,精馏过程的节能降耗是一个涉及多个方面的工程问题。
通过提高热效率、物质效率,使用先进的辅助技术和优化操作策略,可以有效地降低精馏过程的能耗。
这些节能降耗技术不仅可以减少环境污染,还可以提高精馏过程的经济效益。
因此,精馏过程的节能降耗在工业应用中具有重要的意义。
化工精馏高效节能技术的开发及应用

化工精馏高效节能技术的开发及应用化工精馏是一种将混合物分离成纯净组分的重要工艺。
传统的精馏过程需要大量的能源和设备投入,对环境造成了严重污染。
为了减少能源消耗和环境污染,近年来,许多高效节能的化工精馏技术得到了开发和应用。
过程集成是一种有效的高效节能技术。
通过在不同的精馏塔之间进行热、质量和能量的流动,可以有效地减少能源消耗。
过程集成不仅可以减少热量的需求,还可以减少外部操作材料的消耗和废物产生。
采用反向工程设计方法,将热质合适的塔纳入某一塔内,从而实现能量和物质的流动,提高精馏过程的能效。
新型的精馏塔设计也是高效节能的重要技术。
传统的精馏塔结构往往有许多内置的板式结构,这些板式结构会导致液体在塔内的阻力增大,从而增加了能量消耗。
目前,研究人员已经开发出了一种新型的精馏塔设计,即用填料代替板式结构。
填料结构不仅可以提供更大的表面积用于传递热量和物质,还可以减少液体在塔内的阻力,从而减少了能源消耗。
使用先进的控制技术也可以实现高效节能的化工精馏。
通过使用先进的模型预测和优化方法,可以实时调整操作条件和控制参数,以提高精馏过程的效率和能源利用率。
采用模型预测控制技术,可以根据实时测量数据和模型预测结果,调整进料流量、塔内温度和压力等操作参数,实现精确控制和节能。
使用先进的节能设备也可以实现高效节能的化工精馏。
采用高效换热器,可以实现余热的回收利用,从而减少能源消耗。
采用节能泵和节能压缩机,可以减少能源消耗和运行成本。
还可以使用先进的分离膜和吸附剂等技术,实现低温混合物的分离和提纯,减少能源消耗和废物产生。
开发和应用高效节能的化工精馏技术对于减少能源消耗和环境污染具有重要意义。
通过过程集成、新型精馏塔设计、先进的控制技术和节能设备的应用,可以实现精馏过程的高效节能,为化工行业的可持续发展做出贡献。
化工精馏高效节能技术的开发及应用
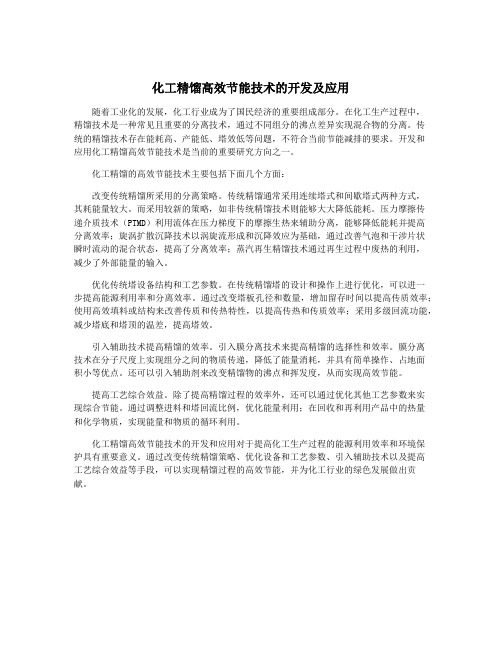
化工精馏高效节能技术的开发及应用随着工业化的发展,化工行业成为了国民经济的重要组成部分。
在化工生产过程中,精馏技术是一种常见且重要的分离技术,通过不同组分的沸点差异实现混合物的分离。
传统的精馏技术存在能耗高、产能低、塔效低等问题,不符合当前节能减排的要求。
开发和应用化工精馏高效节能技术是当前的重要研究方向之一。
化工精馏的高效节能技术主要包括下面几个方面:改变传统精馏所采用的分离策略。
传统精馏通常采用连续塔式和间歇塔式两种方式,其耗能量较大。
而采用较新的策略,如非传统精馏技术则能够大大降低能耗。
压力摩擦传递介质技术(PTMD)利用流体在压力梯度下的摩擦生热来辅助分离,能够降低能耗并提高分离效率;旋涡扩散沉降技术以涡旋流形成和沉降效应为基础,通过改善气泡和干涉片状瞬时流动的混合状态,提高了分离效率;蒸汽再生精馏技术通过再生过程中废热的利用,减少了外部能量的输入。
优化传统塔设备结构和工艺参数。
在传统精馏塔的设计和操作上进行优化,可以进一步提高能源利用率和分离效率。
通过改变塔板孔径和数量,增加留存时间以提高传质效率;使用高效填料或结构来改善传质和传热特性,以提高传热和传质效率;采用多级回流功能,减少塔底和塔顶的温差,提高塔效。
引入辅助技术提高精馏的效率。
引入膜分离技术来提高精馏的选择性和效率。
膜分离技术在分子尺度上实现组分之间的物质传递,降低了能量消耗,并具有简单操作、占地面积小等优点。
还可以引入辅助剂来改变精馏物的沸点和挥发度,从而实现高效节能。
提高工艺综合效益。
除了提高精馏过程的效率外,还可以通过优化其他工艺参数来实现综合节能。
通过调整进料和塔回流比例,优化能量利用;在回收和再利用产品中的热量和化学物质,实现能量和物质的循环利用。
化工精馏高效节能技术的开发和应用对于提高化工生产过程的能源利用效率和环境保护具有重要意义。
通过改变传统精馏策略、优化设备和工艺参数、引入辅助技术以及提高工艺综合效益等手段,可以实现精馏过程的高效节能,并为化工行业的绿色发展做出贡献。
化工精馏节能技术探讨

化工精馏节能技术探讨化工精馏是一种广泛的分离技术,广泛应用于炼油、化工、精细化工、制药等行业。
由于化工精馏的能耗和排放量较高,为了减少对环境的影响以及降低生产成本,探究化工精馏节能技术的应用显得十分重要。
一、精馏原理精馏是一种将混合物中的组分分离为一系列固定沸点组分的方法。
在一个精馏塔中,混合物在塔底蒸发后升往塔顶,通过多级板或者填料进一步蒸馏和分离。
不同沸点的组分会在不同的塔板或填料层凝结、液化分离出来。
经过多次分离,可以得到高纯度的分离产物。
二、节能措施1. 优化工艺参数通过客观分析和实验对化工精馏的工艺参数进行优化,可以达到节能的目的。
优化参数包括塔径、进料温度、进料速率、再沸点的选择等。
优化参数的主要目的是降低热量的损耗,提高再沸进料的回收,提高产品的纯度。
2. 应用热力学分析方法化工精馏通过热量供给来产生馏出性的分级蒸馏过程。
对于具有相同沸点的混合物,应用热力学分析方法来计算馏出程度,优化精馏条件,可达到节约热量、降低气体排放的目的。
3. 利用先进的装置技术采用先进的塔板、塔壳、填料技术,可以优化气液流动、充分利用热量,提高馏分的产量和质量。
例如,采用结构平面装置来提高塔顶的分馏效果,以及选用有效的填料来提高再沸孔的分馏效果等,都是有效的节能措施。
4. 优化回收系统采用高效的回收系统能够有效地提高化工精馏的再利用效益。
例如,实施热回收技术来回收热量和回收常温下的再沸馏分等都能达到节能的目的。
三、总结化工精馏在工业生产和人类生活中有着广泛的应用,同时其高耗能、高排放的特点也给环境带来了不小的影响。
为了减少对环境的影响,降低生产成本,我们需要探究化工精馏的节能降耗技术。
采取以上措施,能够有效地降低化工精馏的能耗和排放,提高生产效益,是企业可持续发展的重要措施。
精馏节能减耗总结

精馏节能减耗总结引言在许多化学工艺中,精馏作为一种常见的分离技术,广泛应用于石油化工、化学制药、能源等行业。
然而,传统的精馏过程存在能源消耗大的问题。
为了减少精馏过程中的能源消耗,提高能源利用率,许多节能减耗技术被引入并逐渐得到应用。
本文将对精馏节能减耗的相关技术进行总结,包括辅助加热装置、改进的精馏塔结构以及新型精馏塔填料等。
通过这些节能减耗技术的应用,精馏过程的能耗问题可以得到一定程度的改善,从而实现能源的可持续利用。
辅助加热装置传统的精馏过程中,常常需要大量的蒸汽或热能来提供塔底部的加热需求。
为了减少能源的消耗,引入一些辅助加热装置可以起到节能降耗的效果。
多效加热器多效加热器是一种高效的辅助加热装置,能够通过热传递的方式将高温废热回收利用。
其原理是在精馏塔的塔顶和塔底之间设置多级的加热器,利用顶部产生的低温蒸汽将底部的高温液体加热,从而实现能量的再利用。
热泵热泵是另一种常用的辅助加热装置,通过将低温的热能转移到高温区域,从而实现能量的传递和利用。
在精馏过程中,可以利用热泵将废热转化为可用的热能,供给精馏塔的加热需求。
这样不仅可以减少能源的消耗,还可以达到能源利用的最大化。
改进的精馏塔结构传统的精馏塔结构存在一些不利于能源节约的问题,如传质效率低、压力损失大等。
通过改进精馏塔的结构,可以减少能源的消耗,提高精馏效率。
塔板结构优化传统的精馏塔中,常见的结构是塔板结构,它的主要问题是传质效率低。
为了提高传质效率,可以引入一些新的塔板结构,如泡沫塔板、视窗塔板等。
这些新型塔板结构具有更大的表面积和更好的传质性能,能够有效地提高精馏效率,降低能源消耗。
塔内增加填料层除了改进塔板结构,也可以在精馏塔内部增加填料层,以增加界面面积,提高传质效果。
常见的填料包括金属填料、陶瓷填料、塑料填料等。
这些填料具有较大的表面积和较好的传质性能,能够增加相接触的机会,从而提高传质效率,减少能源消耗。
新型精馏塔填料塔填料作为精馏过程中的重要组成部分,对其传质效率和能源消耗有着直接的影响。
浅谈精馏操作的节能优化措施

浅谈精馏操作的节能优化措施摘要:石油化工是我国经济发展中的一个重要产业,数据显示,石油化工能耗约占全国工业总能耗的15%。
在能源消耗领域,分离工序占能源消耗的41%至71%,而蒸馏工序占能源消费的96%。
在热力学上,蒸馏是一种非常低效的能耗操作,具有很强的热力学不可逆性。
因此,作为蒸馏操作中的中间操作,蒸馏塔系统的整个操作过程都以产品质量合格和能耗最低为标准。
然而,优化蒸馏操作需要许多因素。
本文从以下几个方面分析了精馏操作的节能措施。
关键词:蒸馏;节能;发展趋势;技术分析前言蒸馏操作是化工生产中的一个重要操作单元,因其能耗高、节能效果好而备受关注。
降低市场产品生产过程中的生产能耗是降低成本、提高市场竞争力的关键,而蒸馏操作过程具有节能效果。
一、蒸馏的工作原理蒸馏是化学生产中分离不混溶液体混合物的典型单元操作。
其本质是多级蒸馏,利用不混溶液体混合物中每种成分在一定压力下的不同沸点或饱和蒸气压来蒸发轻组分(沸点较低或蒸气压较高的组分)。
经过多次部分液相蒸发和部分气相冷凝,气相中轻组分和液相中重组分的浓度逐渐增加,从而实现分离。
在此过程中,传热和传质过程同时进行,属于传质过程控制。
原料从塔中间合适的位置送入塔中,塔分为两段。
上段是没有进料的蒸馏段,下段包含作为保留段的进料板。
冷凝器从塔顶提供液相回流,再沸器从塔底提供气相回流。
气相和液相的回流是蒸馏的一个重要特征。
蒸馏塔是一种提供混合物气相和液相之间接触条件并实现传质过程的设备。
该设备可分为两类:一类是板式蒸馏塔,另一类是填料蒸馏塔。
二、精馏塔影响的因素1.回流比的影响影响蒸馏塔分离效果的主要原因是回流比,在实际操作和生产中通常通过改变回流比来控制回流比,以控制产品质量。
蒸馏段中操作线的斜率(蒸馏段中下降液体的摩尔流速与上升蒸汽的摩尔流速的比率)与回流比成正比,该段中的传质驱动力也与回流比直接成正比。
具体来说,在确定回收率的条件下,如果用增加回流比来提高分离度,则应满足以下要求:首先,由于蒸馏塔理论塔板数的限制,在规定的塔板数范围内,即使回流比增加到无穷大(总回流),分离度总是存在一个极限最大值;其次,由于整个塔中物料平衡的限制,分离极限为FxF/Dx (F为原料液中挥发性成分的摩尔分数)。
空分精馏节能技术的应用

空分精馏节能技术的应用
空分精馏是一种广泛应用于化工、石油、医药、电子、新能源等领域的重要分离技术。
传统的空分精馏过程需要大量的能源消耗,因此节能成为了一个重要的问题。
近年来,为
了降低能源消耗、提高生产效率,人们不断尝试采用各种新技术来改进空分精馏过程。
下
面将重点介绍空分精馏节能技术的应用情况。
1. 热积分技术(HIP)
热积分技术是一种应用于空分精馏中的先进节能技术。
该技术采用循环热交换的方式
使高温精馏侧的排放热能够在低温侧得到回收,从而达到节能的目的。
2. 极低温气体分离技术(VLG)
极低温气体分离技术(VLG)是一种利用Clausius-Clapeyron方程,通过控制温度和
压力调节气体的相对挥发度来实现气体分离的新技术,标志着空分精馏技术的进一步革命。
相对于传统的空分精馏技术,VLG技术能够在更低的温度和压力下实现气体的分离,同时
使能源消耗大幅降低。
3. 旋转蒸发式空分精馏技术
旋转蒸发式空分精馏技术利用比传统空分精馏更高效的离心力对混合气体进行分离,
使得分离的过程更快,更具有规模化的可能。
这种技术可以大大减少能耗同时提高生产效率,使空分精馏产品的纯度和质量更稳定,同时还可以有效地保护环境。
总体而言,随着科技的不断进步,各种新型空分精馏节能技术的应用得以不断拓展。
这些新技术不仅使空分精馏的能源消耗大幅降低,同时也大大提高了生产效率,使得空分
精馏技术更加普及和成熟。
未来,我们有理由相信,空分精馏节能技术将继续以更加高效
和绿色的方式为我们带来更好的生产和生活。
浅析化工精馏高效节能技术开发及应用

浅析化工精馏高效节能技术开发及应用化工精馏是一种重要的分离技术,广泛应用于石油、煤化工、化肥、化学工程等领域。
传统的化工精馏过程存在能耗高、设备庞大、冷却塔效率低等问题,因此如何开发和应用高效节能的精馏技术成为了当前化工行业的研究热点之一。
一种常见的高效节能精馏技术是利用精馏塔内部多个板段进行分离操作。
通过在板段上设置理论塔板,可以有效增加提馏料和回流液之间的接触面积,提高分离效率。
还可以采用提馏料侧进料、回流液裂解等技术来提高精馏塔的分离效率。
在操作参数方面,通过调整塔内的温度、压力、流量等参数,可以进一步优化精馏过程,提高能量利用率。
另一种高效节能精馏技术是采用精馏塔内增容技术。
传统精馏塔通常只有一个塔体,通过增加塔体或引入新的分离层,可以使分离效率进一步提高。
在传统精馏塔上增设有限接触塔、萃取塔等增容设备,可以实现多级分离,提高分离效率。
还可以利用新型填料来提高精馏塔的分离效率。
采用高效填料,可以增加气液交换的面积,提高分离效果。
通过优化填料的形状和材料,可以减少压降,降低能耗。
除了上述技术,还可以采用先进的控制策略来提高精馏过程的效率。
通过合理控制馏出液的流量、温度、压力等参数,可以实现最优操作,提高能量利用率。
在实际应用中,化工精馏高效节能技术可以广泛应用于各行业。
在石油炼制工艺中,可以应用于原油分馏、汽车汽油制备等过程中。
在化肥工程中,可以应用于氨水脱碳、尿素生产等过程中。
在化学工程中,可以应用于有机合成、溶剂回收等过程中。
化工精馏高效节能技术的开发和应用对于提高工业生产效率、降低能源消耗、减少环境污染具有重要意义。
未来,随着科技的不断进步和发展,相信会出现更多创新的精馏技术,为化工行业的可持续发展做出更大贡献。
化工精馏高效节能技术的开发及应用
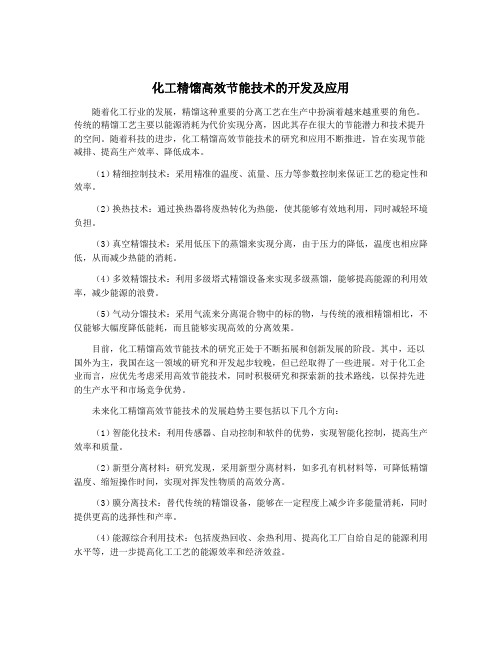
化工精馏高效节能技术的开发及应用随着化工行业的发展,精馏这种重要的分离工艺在生产中扮演着越来越重要的角色。
传统的精馏工艺主要以能源消耗为代价实现分离,因此其存在很大的节能潜力和技术提升的空间。
随着科技的进步,化工精馏高效节能技术的研究和应用不断推进,旨在实现节能减排、提高生产效率、降低成本。
(1)精细控制技术:采用精准的温度、流量、压力等参数控制来保证工艺的稳定性和效率。
(2)换热技术:通过换热器将废热转化为热能,使其能够有效地利用,同时减轻环境负担。
(3)真空精馏技术:采用低压下的蒸馏来实现分离,由于压力的降低,温度也相应降低,从而减少热能的消耗。
(4)多效精馏技术:利用多级塔式精馏设备来实现多级蒸馏,能够提高能源的利用效率,减少能源的浪费。
(5)气动分馏技术:采用气流来分离混合物中的标的物,与传统的液相精馏相比,不仅能够大幅度降低能耗,而且能够实现高效的分离效果。
目前,化工精馏高效节能技术的研究正处于不断拓展和创新发展的阶段。
其中,还以国外为主,我国在这一领域的研究和开发起步较晚,但已经取得了一些进展。
对于化工企业而言,应优先考虑采用高效节能技术,同时积极研究和探索新的技术路线,以保持先进的生产水平和市场竞争优势。
未来化工精馏高效节能技术的发展趋势主要包括以下几个方向:(1)智能化技术:利用传感器、自动控制和软件的优势,实现智能化控制,提高生产效率和质量。
(2)新型分离材料:研究发现,采用新型分离材料,如多孔有机材料等,可降低精馏温度、缩短操作时间,实现对挥发性物质的高效分离。
(3)膜分离技术:替代传统的精馏设备,能够在一定程度上减少许多能量消耗,同时提供更高的选择性和产率。
(4)能源综合利用技术:包括废热回收、余热利用、提高化工厂自给自足的能源利用水平等,进一步提高化工工艺的能源效率和经济效益。
总的来说,化工精馏高效节能技术的研究与应用是化工行业发展的重要方向之一。
持续不断的技术创新,将为化工企业带来更加可持续、高效、环境友好的生产模式,也是应对未来一系列环境和经济压力的必要手段之一。
新型精馏技术

1 反应精馏反应精馏作为一种新型特殊精馏,因其具有独特的优势而在化学工业中日益受到重视。
由于反应段固体催化剂的选择及装填方式对该工艺起关键作用,故国内外在注重工艺开发的同时,也需要在催化剂及填料上多做研究,以取得更大突破。
目前,反应精馏技术已在多个领域实现了产业化,对某些新领域的开发也取得了一定进展。
随着节能和环保要求日益提高,该技术与先进的计算机模拟软件相结合,在未来几十年将会发挥更大作用,同时会有更好的发展。
1.1 反应精馏技术基本原理反应精馏是在进行反应的同时用精馏方法分离出产物的过程。
其基本原理为;对于可逆反应,当某一产物的挥发度大于反应物时,如果将产物从液相中蒸出,则可破坏原有的平衡,使反应继续向生成物的方向进行,因而可提高单程转化率,在一定程度上变可逆反应为不可逆反应。
1.2 反应精馏技术特点(1) 反应和精馏在同一设备中进行,简化了流程,使设备费和操作费同时下降。
(2) 对于放热反应过程,反应热全部提供为精馏过程所需热量的一部分,节省了能耗。
(3) 对于可逆反应过程中,由于产物的不断分离,可使系统远离平衡状态,增大过程的转化率。
可使最终转化率大大超过平衡转化率,减轻后续分离工序的负荷。
(4) 对于目的产物具有关二次副反应的情形,通过某一反应物的不断分离,从而抑制了副反应,提高了选择性。
(5) 在反应精馏塔内,各反应物的浓度不同于进料浓度。
因此,进料可按反应配比要求,而塔板上造成某种反应物的过量,可使反应后期的反应速度大大提高、同时又达到完全反应;或造成主副反应速率的差异,达到较高的选择性。
这样,对于传统工艺中某些反应物过量从而需要分离回收的情况,能使原料消耗和能量消耗得到较大节省。
(6) 在反应精馏塔内,各组份的浓度分布主要由相对挥发度决定,与进料组成关系不大,因而反应精馏塔可采用低纯度的原料作为进料。
这一特点可使某些系统内循环物流不经分离提纯直接得到利用。
(7) 有时反应物的存在能改变系统各组份的相对挥发度,或绕过其共沸组成,实现沸点相近或具有恒沸组成的混合物之间的完全分离。
化工行业精馏高效节能技术的开发及应用
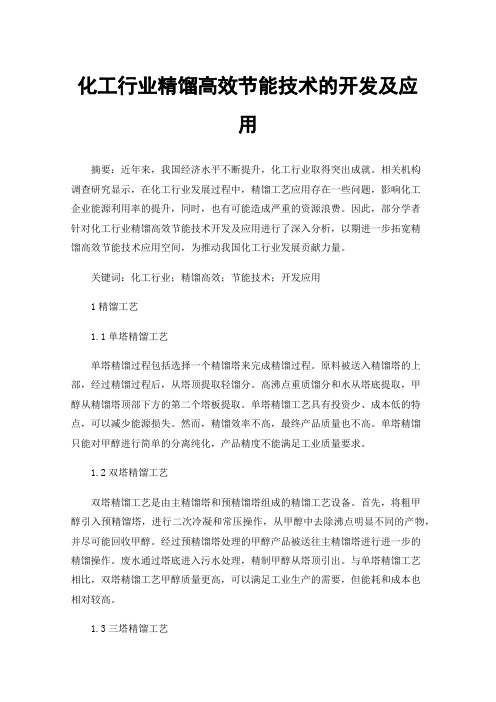
化工行业精馏高效节能技术的开发及应用摘要:近年来,我国经济水平不断提升,化工行业取得突出成就。
相关机构调查研究显示,在化工行业发展过程中,精馏工艺应用存在一些问题,影响化工企业能源利用率的提升,同时,也有可能造成严重的资源浪费。
因此,部分学者针对化工行业精馏高效节能技术开发及应用进行了深入分析,以期进一步拓宽精馏高效节能技术应用空间,为推动我国化工行业发展贡献力量。
关键词:化工行业;精馏高效;节能技术;开发应用1精馏工艺1.1单塔精馏工艺单塔精馏过程包括选择一个精馏塔来完成精馏过程。
原料被送入精馏塔的上部,经过精馏过程后,从塔顶提取轻馏分。
高沸点重质馏分和水从塔底提取,甲醇从精馏塔顶部下方的第二个塔板提取。
单塔精馏工艺具有投资少、成本低的特点,可以减少能源损失。
然而,精馏效率不高,最终产品质量也不高。
单塔精馏只能对甲醇进行简单的分离纯化,产品精度不能满足工业质量要求。
1.2双塔精馏工艺双塔精馏工艺是由主精馏塔和预精馏塔组成的精馏工艺设备。
首先,将粗甲醇引入预精馏塔,进行二次冷凝和常压操作,从甲醇中去除沸点明显不同的产物,并尽可能回收甲醇。
经过预精馏塔处理的甲醇产品被送往主精馏塔进行进一步的精馏操作。
废水通过塔底进入污水处理,精制甲醇从塔顶引出。
与单塔精馏工艺相比,双塔精馏工艺甲醇质量更高,可以满足工业生产的需要,但能耗和成本也相对较高。
1.3三塔精馏工艺自20世纪70年代以来,能源价格飞涨,传统的甲醇精馏工艺能耗高,甲醇纯度逐渐无法满足工艺生产的需要,逐渐被三塔精馏工艺所取代。
三塔精馏工艺主要由预精馏塔、加压精馏塔和常压精馏塔组成。
预精馏塔的功能与双塔精馏过程的功能相同。
经过预精馏塔的甲醇蒸汽进入加压塔的冷凝器进行冷却,然后送往常压精馏塔进行精馏。
三塔精馏工艺可以利用甲醇蒸汽作为加热源,从而节约能源。
三塔精馏工艺可以实现双效精馏效果,满足节能环保的要求。
生产的甲醇产品精度高。
2化工行业精馏高效节能技术的开发及应用2.1多效精馏技术介绍为进一步提升化工精馏工艺应用效果,同时降低不必要的能源损耗,应考虑提升蒸汽热量循环使用效率,促进能量供给成本的不断降低。
化工原理_34精馏过程的节能途径

馏出液的 平均组成
一、恒 R 下间歇精馏的计算
5.每批精馏所需的时间
每批操 作的馏 出量 kmol
每批操作的汽化量
nV ( R 1)nD
每批操作所需的时间
nV qn,V
汽化速率 kmol/h
二、恒 xD 下间歇精馏的计算
1.确定理论塔板层数 计算基准:终态 最小回流比 操作回流比 馏出液组成 xD 釜液组成 xWe
间歇精馏曲线作用
指导试车和生产 对精馏过程进行分析
四、间歇精馏与连续精馏的比较
多组分( n 个组分)混合物分离 比较项目 塔数 塔径 流程 能耗 劳动强度 间歇精馏 1 大 短 高 大 连续精馏 n-1 小 长 低 小
第九章 蒸 馏
9.5 两组分连续精馏的计算 9.6 间歇精馏 9.6.1 间歇精馏概述 9.6.2 间歇精馏计算
二、精馏过程的节能途径
2.降低塔釜操作温度 塔压降△P 示例
~ 釜温tW
~
能耗
采用高效塔填料代替原有塔板,降低塔压降
二、精馏过程的节能途径
3.热泵精馏 将塔顶蒸汽绝热压缩升温,作为再沸器的热源, 将再沸器中的液体部分汽化,而压缩气体本身冷凝 成液体,经节流阀后一部分作为塔顶产品采出,另 一部分作为塔顶回流液。
4.每批精馏所需的时间
确定xW和 R 的关系
积分求出 nV 则
nV qn,V
汽化速率 kmol/h
练 习 题 目
思考题 1.精馏过程有哪些节能途径? 2.影响精馏操作有哪些主要因素? 3.馏出液组成恒定的间歇精馏有何特点,其理论 板层数如何确定? 4.回流比恒定的间歇精馏有何特点,其理论板层 数如何确定?
二、恒 xD 下间歇精馏的计算
精馏过程的节能研究
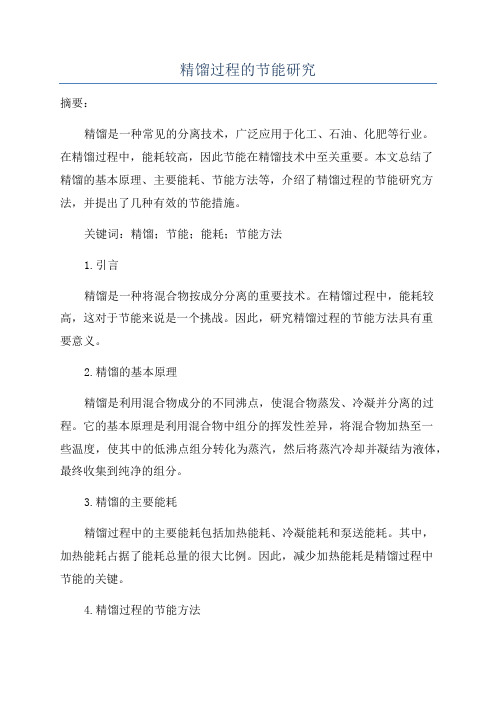
精馏过程的节能研究摘要:精馏是一种常见的分离技术,广泛应用于化工、石油、化肥等行业。
在精馏过程中,能耗较高,因此节能在精馏技术中至关重要。
本文总结了精馏的基本原理、主要能耗、节能方法等,介绍了精馏过程的节能研究方法,并提出了几种有效的节能措施。
关键词:精馏;节能;能耗;节能方法1.引言精馏是一种将混合物按成分分离的重要技术。
在精馏过程中,能耗较高,这对于节能来说是一个挑战。
因此,研究精馏过程的节能方法具有重要意义。
2.精馏的基本原理精馏是利用混合物成分的不同沸点,使混合物蒸发、冷凝并分离的过程。
它的基本原理是利用混合物中组分的挥发性差异,将混合物加热至一些温度,使其中的低沸点组分转化为蒸汽,然后将蒸汽冷却并凝结为液体,最终收集到纯净的组分。
3.精馏的主要能耗精馏过程中的主要能耗包括加热能耗、冷凝能耗和泵送能耗。
其中,加热能耗占据了能耗总量的很大比例。
因此,减少加热能耗是精馏过程中节能的关键。
4.精馏过程的节能方法(1)改善设备结构:优化精馏塔的结构,减少内部分布的不均匀性,提高传质效率和分离效果。
在塔体设计上,可以采用结构紧凑的塔板,增加塔板间隙,减小压降,提高塔板效率。
(2)改进传热方式:采用高效的传热方式,如采用波纹板式换热器、加快传热介质的速度等,提高传热效率,减少能耗。
(3)优化操作条件:合理选择操作条件,如适当降低温度、降低进料浓度等,以减少能耗。
此外,可合理控制回流比、调整塔压和温度等操作参数,以提高精馏的效果。
(4)采用节能设备:在精馏过程中,采用一些节能设备,如多级补热、换热器、回收利用部分废热等,来降低能耗。
5.精馏过程的节能研究方法(1)实验研究:通过实验对比不同条件下的能耗指标,分析各种因素对能耗的影响,优化操作条件,并提出相应的改进方法。
(2)模拟仿真:利用模拟软件对精馏过程进行仿真,探究不同操作条件下的能耗情况,并通过改变操作参数等方式来降低能耗。
(3)优化设计:通过数学方法建立精馏过程的数学模型,结合优化算法进行优化设计,以降低能耗为目标,寻找最优操作条件。
精馏的节能技术

国外新型填料有阶梯环填料(Cascade) (Mini-Ring)、英特洛克斯金属填料(Intalox metal)、网版格子填料(Perform Grid)和苏 尔采波纹填料(sulzer)。这些填料在国内也 有研究和试制。最近的发展趋向是代替鲍尔环 拉西环、鞍型填料和部分塔板,以节省精馏操 作能耗。
精馏作为化工、石化、医药、食品、冶金 等行业生产过程的重要单元操作,其能耗约 占化工生产的40%-70%。 故采取措施降低蒸馏过程中的能耗日益重 要,成为研究的重点所在。
1、操作线的改进 ⑴选择最优回流比 影响精馏过程能量消耗最主要的因素是回 流比,精馏塔的能耗随回流比几乎成正比增 加。所以应选择完成给定的分离任务所需要 的操作费和设备费的总和为最小值的回流比。 适宜回流比:与最少总费用相对应的回流比 称为适宜回流比或操作回流比。
3、热能的充分利用 (1)热交换系统 精馏系统是由塔体和热交换器组成。在再 沸器、冷凝器、进料顶热器和成晶冷却器系 统中, 热交换器最佳化是节能的重要环节, 因 为它决馏系统是由若 干压力不同的精馏塔构成 ,而且依据压力高低的顺 序,相邻两个塔的高压塔 塔顶蒸汽作用为低压塔再 沸器的热源,换言之,高 压塔塔顶蒸汽的冷凝潜热 均被精馏系统自身回收利 用,使热能得到充分有效 地利用。
热泵精馏
常用的三种热泵流程: (1)用外部制冷剂的热泵
将外部制冷剂用于塔顶冷凝器和再沸器所构成 的封闭循环中,冷凝器作为制冷剂的蒸发器,再沸 器作为制冷剂的冷凝器。
左图为该类热泵循环用 于分离丙烯-丙烷系统的 流程。 用丙烷作为外部制冷 剂 , 使 它 在 1.67℃ 下 蒸 发,并在43.33℃下冷凝 ,可使分凝器和再沸器 所需的热负荷完全匹配 。因此不用冷却水和加 热蒸汽,只耗电1173kW (假定制冷剂的压缩过 程是等熵的。
化工精馏高效节能技术的开发及应用
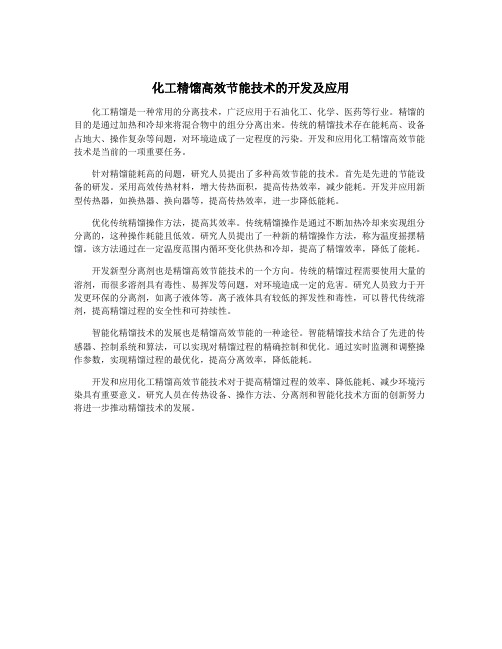
化工精馏高效节能技术的开发及应用化工精馏是一种常用的分离技术,广泛应用于石油化工、化学、医药等行业。
精馏的目的是通过加热和冷却来将混合物中的组分分离出来。
传统的精馏技术存在能耗高、设备占地大、操作复杂等问题,对环境造成了一定程度的污染。
开发和应用化工精馏高效节能技术是当前的一项重要任务。
针对精馏能耗高的问题,研究人员提出了多种高效节能的技术。
首先是先进的节能设备的研发。
采用高效传热材料,增大传热面积,提高传热效率,减少能耗。
开发并应用新型传热器,如换热器、换向器等,提高传热效率,进一步降低能耗。
优化传统精馏操作方法,提高其效率。
传统精馏操作是通过不断加热冷却来实现组分分离的,这种操作耗能且低效。
研究人员提出了一种新的精馏操作方法,称为温度摇摆精馏。
该方法通过在一定温度范围内循环变化供热和冷却,提高了精馏效率,降低了能耗。
开发新型分离剂也是精馏高效节能技术的一个方向。
传统的精馏过程需要使用大量的溶剂,而很多溶剂具有毒性、易挥发等问题,对环境造成一定的危害。
研究人员致力于开发更环保的分离剂,如离子液体等。
离子液体具有较低的挥发性和毒性,可以替代传统溶剂,提高精馏过程的安全性和可持续性。
智能化精馏技术的发展也是精馏高效节能的一种途径。
智能精馏技术结合了先进的传感器、控制系统和算法,可以实现对精馏过程的精确控制和优化。
通过实时监测和调整操作参数,实现精馏过程的最优化,提高分离效率,降低能耗。
开发和应用化工精馏高效节能技术对于提高精馏过程的效率、降低能耗、减少环境污染具有重要意义。
研究人员在传热设备、操作方法、分离剂和智能化技术方面的创新努力将进一步推动精馏技术的发展。
浅析化工精馏高效节能技术开发及应用

浅析化工精馏高效节能技术开发及应用
化工精馏过程是在化工生产中非常重要的一项技术。
根据精馏操作的不同,化工精馏
主要被用于物质的分离、纯化、浓缩、脱除杂质等操作。
然而,传统精馏技术在生产过
程中存在着很多问题,例如能耗高、设备维护成本高、产品质量不稳定等。
因此,开发和
应用化工精馏高效节能技术成为了当今化工行业必须重视和关注的问题。
一般来说,化工精馏高效节能技术主要包括以下方面:
1. 优化精馏塔内部设备结构。
根据操作需求,合理选择不同的塔板和填料结构等设
备元件,以减少气液阻力,提高传质效率和增加物料受热面积,同时提高物料与介质交换
效果,从而实现精馏过程的高效节能。
2. 引入新型能源节约技术。
通过采用热泵技术、废热回收技术、换热器等技术手段,对于化工精馏过程中高温高压、高沸点物质进行节能和回收,以减轻能源消耗,避免对环
境造成二次污染。
3. 结合自动控制技术。
采用精密自动控制技术,通过调节正负反馈,及时调整操作
参数,实现局部或全局的优化控制和节能降耗的目标。
4. 引入高级传感器和远程监控系统。
在化工精馏生产过程中,引入先进的传感器和
监控系统,能够实现实时掌握生产情况,及时发现并解决问题,有效提高设备运行率和产
品质量。
综上所述,化工精馏高效节能技术开发及应用,是化工行业中不可忽视的一个重要方向。
针对不同的化工生产行业,我们需要结合具体的工艺工程特点,选择合适的节能技术,努力探索适合自己企业的高效节能措施,以最大限度地降低能源的消耗,提高企业的经济
效益和社会效益。
- 1、下载文档前请自行甄别文档内容的完整性,平台不提供额外的编辑、内容补充、找答案等附加服务。
- 2、"仅部分预览"的文档,不可在线预览部分如存在完整性等问题,可反馈申请退款(可完整预览的文档不适用该条件!)。
- 3、如文档侵犯您的权益,请联系客服反馈,我们会尽快为您处理(人工客服工作时间:9:00-18:30)。
精馏过程的节能途径及新型的精馏技术[摘要]精馏是化工、石化、医药等过程的重要单元操作,它是一类高能耗的单元过程,其能耗约占化工生产的60%,其节能途径包括多效精馏、热泵精馏、热耦精馏技术、内部热集成蒸馏塔、新型高效分离技术等。
多效精馏由N 个并列操作的精馏塔构成,再沸器的加热蒸汽可减少到原来单效精馏所需加热蒸汽的1/N 左右;热泵精馏能使能耗减少20%左右;热耦精馏比两个常规塔精馏可节省30%左右;内部热集成蒸馏塔节省的能耗可达30~60%这些技术已成功地完成了中试,节能可达到30~60%。
[关键词]精馏;节能前言在工业生产中,石油化学工业的能耗所占比例最大,而石油化学工业中能耗最大者为分离操作,其中又以精馏的能耗居首位。
精馏过程是一个复杂的传质传热过程,表现为:过程变量多,被控变量多,可操纵的变量也多;过程动态和机理复杂”。
首先,随着石油化工的迅速发展,精馏操作的应用越来越广,分离物料的组分不断增多,分离的产品纯度要求亦不断提高,但人们同时又不希望消耗过多的能量,这就对精馏过程的控制提出了要求。
其次,作为化工生产中应用最广的分离过程,精馏也是耗能较大的一种化工单元操作。
在实际生产中,为了保证产品合格,精馏装置操作往往偏于保守,操作方法以及操作参数设置往往欠合理。
另外,由于精馏过程消耗的能量绝大部分并非用于组分分离,而是被冷却水或分离组分带走。
因此,精馏过程的节能潜力很大,合理利用精馏过程本身的热能,就能降低整个过程对能量的需求,减少能量的浪费,使节能收效也极为明显。
据统计,在美国精馏过程的能耗占全国能耗的3%,如果从中节约10%,每年可节省5亿美元。
我国的炼油厂消耗的原油占其炼油量的8%~10%,其中很大一部分消耗于精馏过程。
因此,在当今能源紧缺的情况下,对精馏过程的节能研究就显得十分重要。
例如,美国巴特尔斯公司在波多黎各某芳烃装置的8个精馏塔上进行节能优化操作,每年可节约310万美元。
近年来,研究开发了许多新型的精馏塔系统,文章主要介绍几种精馏塔系统精馏过程是最重要的化工单元过程之一,它又是一类高能耗的单元过程。
精馏过程节能研究,在塔的结构形式上近十几年来获得了长足的进步。
精馏过程的节能主要有以下几种基本方式:提高塔的分离效率,降低能耗和提高产品回收率;采用多效精馏技术、热泵技术、热耦精馏技术、新塔型和高效填料等。
1、改变操作条件和方法1.1选择适宜的回流比回流比越小,则净功耗越小。
为此,应在可能条件下减小操作的回流比R。
塔径将随回流比的增加而加大。
因此,最优回流比反映了设备费用与操作费用之间的最佳权衡。
据报道,曾对70个不同的烃类精馏塔统计计算,最优回流比R opt都在最小回流比的1.11~1.24倍之间,一般在分离物系具有较大的相对挥发度或分离要求不很高的情况下,相反若物系的相对挥发度接近于l或分离要求很高,则采用的R opt要显著地高于R min。
在一般情况下,若在R opt 下操作,总费用大部分是加热蒸汽的费用,约占70%,而冷却水的费用只占百分之几。
但当塔项冷凝器温度低于大气温度时,即在低温冷凝时,冷冻费用便是主要的了。
对于已定的精馏塔和分离物系,回流比和产品纯度密切相关。
为了确保得到纯度合格的产品,设计时有一定的回流余量,余量越大,能耗越高。
对于回流设置较大的精馏塔,在不降低产品质量等级的条件下,只要降低回流量,即可降低塔底再沸器的能耗。
1.2选择适宜的操作压力加压精馏有利于采用廉价加热介质和冷凝介质,如蒸汽和水。
一方面,加压精馏可以减少单位产品的能源消耗。
加压精馏实质上是提高被分离物系自身的饱和蒸汽压。
系统内蒸汽压力升高,被分离物系的温度也相应增高。
另一方面,加压精馏可充分利用廉价资源,由于精馏塔内饱和蒸汽压的提高,相应的馏出物的露点也随着增高,这就为使用廉价循环冷却水或低温水作为冷却介质创造了条件,在很大程度上减少了使用冰盐水或更高档次冷却介质的可能性。
采用水作为冷却介质可较大限度降低单位产品的投资和操作费用,同时由于减少了冰盐水的使用量,而相应降低了能耗。
减压精馏可以使许多高沸点化合物在分离过程中避免使用高价值的加热介质,如热油等。
采用蒸汽加热使用方便,价格低,同时由于传热系数大,有利于减少传热面积、节省投资;同时减压精馏可以避免热敏化合物的分解或聚合,减少物料的损失而降低消耗。
1.3选择适宜的进料板位置和进料状态若进塔的物料成分与加料板的成分差别较大,则应更换进料位置(一般塔都有几个进料口可供调节)。
在保证产品同一质量品质的前提下,进料中重组分增加,可降低进料口位置,减小提馏段可降低塔釜加热热量。
如果被分离的物料来源不同,各组分的含量差异较大,可将各种物料混合后进行单塔处理或一塔多股进料。
实际证实多股进料完成相同的分离任务,能耗较低。
这是因为混合过程是增熵的过程,各组分不同的几股进料的混合,增加了过程的不可逆性,必然增加精馏过程的能耗。
进料状态将直接影响精馏塔的能耗q变小,使操作线更接近于气液平衡线,使提馏段塔板数减少,提馏蒸汽负荷减少,从而可节省蒸汽。
q增大,蒸汽量增加,但分离效果得到改善。
2、多效精馏多效精馏由N 个并列操作的精馏塔构成,操作压力由左至右逐效降低。
前面较高压力塔的塔顶蒸汽作为后面较低压力的塔底再沸器的加热介质,在其中冷凝。
如果相邻两塔的冷凝器和再沸器的热负荷平衡,则只有第一塔的再沸器需要加热蒸汽,最后一塔的冷凝器需要冷却介质。
采用N 效蒸馏后,再沸器所需的加热蒸汽可减少到原来单效精馏所需加热蒸汽的1/N 左右。
实践证明,两效精馏操作所需热量与单效精馏比较,可减少30~40%。
3、低温热泵精馏当塔顶冷凝器采用致冷剂冷却时称为低温精馏。
低温精馏可用较低的压力。
同时由于低温时相对挥发度较大,可采用较小的回流比,以减小冷凝器和再沸器的热负荷。
使用单效精馏并用热泵将热量从冷凝器泵送至再沸器的低温精馏,称为热泵精馏。
热泵精馏能使能耗减少。
为了使塔顶蒸汽冷凝时所放出的热能提供给再沸器作为气化室的热源,使用了膨胀阀和压缩机,以改变冷凝或沸腾的温度。
图2 为最简单的热泵精馏,在塔顶冷凝器和塔底再沸器之间联上一股闭路循环的外加致冷剂,致冷剂在塔顶冷凝器中蒸发时吸收热量,然后经压缩机压缩,塔釜再沸器冷凝并放出热量,再经节流阀减压至塔顶冷凝器中蒸发。
如此反复,不断将热量从温度较低的冷凝器泵送至温度较高的再沸器[2]。
4、热耦精馏技术热耦精馏是20 世纪60 年代提出的一种复杂蒸馏技术,主要用于三元混合物的分离。
该类型塔已在1989 年由德国BASF 公司率先实现了工业化,与常规蒸馏塔相比热耦蒸馏可以节省能耗达30%左右。
可以用一个全塔和一个副塔代替两个完整的精馏塔,从全塔内引出一股液相物流直接作为副塔塔顶的液相回流,引出一股气相物流直接作为副塔塔底的气相回流,使副塔避免使用冷凝器和再沸器,实现了热量的耦合,称为热耦精馏。
热耦精馏在热力学上是最理想的系统结构,既可节省设备投资,又可节省能耗。
计算表明,热耦精馏比两个常规塔精馏可节省能耗30%左右。
日本的住友重工株式会社和Krupp Uhde建成了工业化的热耦蒸馏塔,美国UOP 公司在提纯粗庚烷装置中采用了立式隔板蒸馏塔(热耦蒸馏塔的一种)。
它采用多股进料技术,并包括了吸收过程。
从近年来的发展趋势看,热耦蒸馏的工业应用有良好的前景。
Agrawal 和Fidkowski从热力学效率角度出发,分析了分离三元理想饱和液体时热耦蒸馏与常规序列的差异。
Schultz 等[4]提出了选用热耦蒸馏的一些经验法则,认为选用热耦蒸馏的情况是:进料中间组分的含量比较多,轻关键组分与中间组分之间的相对挥发度和中间组分与重关键组分之间的相对挥发度较接近。
吕向红、陆恩锡[5]采用蒸馏计算的严格模型,模拟研究三组分混合物分离的热耦蒸馏塔和常规简单蒸馏序列的能耗,分析热耦蒸馏塔应用的前提条件,从而提出热耦蒸馏塔选用的原则:(1)当分离指数ESI<1 时,如果中间组分的含量较低,则不宜于选用热耦蒸馏的方案;当其摩尔分数超过60%后,选用热耦蒸馏方案则比常规简单方案减少能耗10%。
(2)当ESI 在0.9~1.1 时,无论中间组分的含量高或低,选用热耦蒸馏方案都优于常规方案,既减少能耗,又节省设备投资。
(3)当ESI >1时,不宜于选用热耦蒸馏方案。
(4)如常规蒸馏2 塔操作压力差较大,亦不宜选用热耦蒸馏方案。
5、内部热集成蒸馏塔内部热集成蒸馏塔,指同一塔本身的精馏段和提馏段进行热量集成。
它是通过蒸馏塔精馏段和提馏段的热集成实现蒸馏塔的无冷凝器和再沸器操作,从而大幅度降低能耗,与常规蒸馏塔相比节省的能耗可达30~60%;这是迄今所知节能幅度最大、最先进的蒸馏塔型式。
这一设想最早于20 世纪60 年代由Freshwatert 提出,其后不断有学者发表研究成果。
日本学者M.Nakaiwa 等在完成实验研究的基础上,已于2000 年通过了该塔的中试,目前正朝着工业化的方向进展。
内部热集成塔和传统的蒸馏塔有着相当大的区别:传统蒸馏塔必不可少的塔顶冷凝器和塔釜再沸器已不再需要,原有的一个蒸馏塔被分成精馏和提馏2 个塔,精馏塔放置在提馏塔内部。
由于实施了内部热集成,故该类塔具有非常高的热力学效率。
6、采用新型高效分离技术分离技术是通过塔设备实现的。
对常规板式塔改造,采用高效导向筛板,可降低能耗,提高生产能力[7]。
6.1 高效导向筛板高效导向筛板是北京化工大学在对包括筛板塔板在内的各种塔板进行深入细致研究的基础,发挥筛板塔结构简单、造价低廉的特点,克服其漏点高、效率低的缺点,并且通过对各种塔板进行深入研究、综合比较,结合塔板上流体力学和传质学的研究开发的一种新型高效塔板,其工作原理如图6 所示。
高效导向筛板是在高效导向筛板上开设了大量筛孔及少部分导向孔,通过筛孔的气体在塔板上与液体错流,穿过液层垂直上升,通过导向筛板的气体沿塔板水平前进,将动量传递给塔板上水平流动的液体,从而推动液体在塔板上均匀稳定前进,克服了原来塔板上的液面落差和液相返混,提高了生产能力和板效率,解决了堵塔、夜泛等问题。
另外,在传统塔板上,由于液面梯度,在塔板的上游总存在个非活化区,在此区域内气流无法穿过液层而上升鼓泡。
实验测定,非活化区的面积约占塔截面积的1/3 左右。
高效导向筛板在液流入口处增加了向上凸成斜台状的鼓泡促进器,促使液体一进入塔板就能产生鼓泡,带来了良好的气液接触与传质。
高效导向筛板具有以下特点:(1)生产能力大;(2)效率高;(3)压降低;(4)抗堵能力强;(5)结构简单,造价低廉。
6.2 板填复合塔板板填复合塔板是北京化工大学对板式塔与填料塔进行深入研究的基础上,充分利用板式塔中塔板间距的空隙,设置高效填料,以降低雾沫夹带、提高气体在塔内的流速和塔的生产能力。