神经网络优化理论研究及应用_第4章优化网络在板形模式识别中的应用_44_59
基于神经网络的分类算法优化与应用研究

基于神经网络的分类算法优化与应用研究随着大数据和人工智能的发展,机器学习算法越来越广泛地被应用到各个领域,其中分类算法是机器学习中的重要分支之一。
基于神经网络的分类算法因其良好的分类效果和不断优化的性能而受到了广泛关注。
本文将从优化神经网络、解决过拟合问题、实现数据预处理等方面阐述基于神经网络的分类算法优化与应用研究。
一、神经网络优化神经网络是一种对异质数据源进行建模和处理的有效工具,能够在具有多层连接的网络中实现非线性函数的高效表示,近年来,如何优化神经网络成为了机器学习领域的研究热点之一。
神经网络的优化主要包括以下几个方面:1.调整神经网络参数神经网络的性能主要依赖于网络结构和参数设置。
其中最重要的参数包括学习率、正则化系数和权重参数等。
适当的调整这些参数,可以大大提高神经网络的性能。
2.采用不同的随机化方法神经网络的初始化条件对性能影响很大,因此采用不同的随机化方法可以大大提高神经网络的分类效果。
3.采用不同的优化算法优化算法直接影响模型参数的优化效果。
目前,梯度下降算法被广泛应用于神经网络中的模型训练,不过随着深度神经网络的发展,其逐渐暴露出梯度弥散的问题。
为了解决这一问题,Adam、Adadelta等优化算法被提出,这些算法经过不断优化,取得了很好的效果。
二、解决过拟合问题在分类算法中,过拟合问题是一个普遍存在的问题。
当样本数据的数量远远小于特征向量的数量时,神经网络容易陷入过拟合状态,降低分类模型的精度。
如何解决神经网络的过拟合问题是一个亟需解决的难题。
1.增加训练数据增加训练数据是解决过拟合问题的一种常见方法。
增加训练数据可以增加神经网络对不同样本的学习能力,从而避免出现过拟合的状况。
2.使用正则化方法正则化方法是解决过拟合问题最常用的方法之一。
其中,L1和L2正则化最为常见。
采用正则化方法可以有效地抑制神经网络中的过拟合现象。
3.使用dropout技术Dropout技术是一种常见的神经网络正则化方法。
改进BP神经网络在模式识别中的应用及研究

背景知识
BP神经网络是一种反向传播神经网络,它通过不断地调整神经网络的权重和偏 置,最小化输出结果与实际结果之间的误差。在模式识别中,BP神经网络可以 用于对输入数据进行分类和识别,它具有以下优点:
1、自适应能力强:BP神经网络能够自适应地学习输入数据的特征,从而自动 地识别出不同的模式。
2、鲁棒性好:它对输入数据的噪声和干扰具有较强的适应性,能够有效地降 低误识别率。
改进BP神经网络在模式识别 中的应用及研究
01 引言
03 参考内容
目录
02 背景知识
引言
模式识别是指通过计算机算法对输入的数据进行分类和识别,从而自动地识别 出对象或现象的模式。它是领域中的一个重要研究方向,被广泛应用于图像识 别、语音识别、自然语言处理等领域。BP神经网络是模式识别中常用的一种算 法,它具有自学习和自适应的能力,能够通过对输入数据的训练,自动地识别 出不同的模式。BP神经网络也存在一些问题和不足,需要进一步改进和完善。
改进措施
针对BP神经网络在手写数字识别中的不足,本次演示提出以下改进措施:
1、使用动量项:在梯度下降过 程中
其中,v(t)表示时刻 t的速度,g(t)表示时刻 t的梯度,w(t)表示时刻 t的 权重,α是动量项系数。
2、使用自适应学习率:传统BP 神经网络的学习率是固定的
lr(t+1) = lr0 * (1 - exp(-β*t)) 其中,lr(t)表示时刻 t的学习率,lr0是初始学习率,β是学习率调整系数。
2、性能更优:通过加入动量项和卷积层,改进后的模型在手写数字识别任务 中具有更好的性能表现。实验结果表明,准确率提高了20%以上。
3、鲁棒性更好:改进后的模型对噪声和干扰的抵抗能力更强,能够更好地适 应实际应用中的复杂环境。
模式识别第4章 线性判别函数

w1。
44
4.3 判别函数值的鉴别意义、权空间及解空间 4.3.2 权空间、解矢量与解空间
(3) 解空间
w1
先看一个简
单的情况。设一
维数据1,2属于
w0
1, -1,-2属
于2 求将1和
2区分开的w0 ,
w1。
45
4.3 判别函数值的鉴别意义、权空间及解空间 4.3.2 权空间、解矢量与解空间
(3) 解空间
53
第四章 线性判别方法
4.1 用判别域界面方程分类的概念
有 4.2 线性判别函数 监 4.3 判别函数值的鉴别意义、权空间及解空间 督 4.4 Fisher线性判别 分 4.5 一次准则函数及梯度下降法 类 4.6 二次准则函数及其解法
4.7 广义线性判别函数
54
4.4 Fisher线性判别
这一工作是由R.A.Fisher在1936年的论文中 所提出的,因此称为Fisher线性判别方法。
0123456789
x1
d23(x)为正
d32(x)为正 d12(x)为正 d21(x)为正
i j两分法例题图示
24
25
3、第三种情况(续)
d1(xr) d2(xr)
1
2
d1(xr ) d3(xr )
3
d2 (xr ) d3(xr )
多类问题图例(第三种情况)
26
27
上述三种方法小结:
8
4.2 线性判别函数
9
10
11
d3(xr) 0
不确定区域
r
xr xrxr xr xr
x2
?
d1(x) 0
1
2
3
x1 d2(xr ) 0
神经网络理论及应用

神经网络理论及应用神经网络(neural network)是一种模仿人类神经系统工作方式而建立的数学模型,用于刻画输入、处理与输出间的复杂映射关系。
神经网络被广泛应用于机器学习、人工智能、数据挖掘、图像处理等领域,是目前深度学习技术的核心之一。
神经网络的基本原理是模仿人脑神经细胞——神经元。
神经元接收来自其他神经元的输入信号,并通过一个激活函数对所有输入信号进行加权求和,再传递到下一个神经元。
神经元之间的连接权重是神经网络的关键参数,决定了不同输入组合对输出结果的影响。
神经网络的分类可分为多层感知机、卷积神经网络、循环神经网络等等。
其中多层感知机(Multi-Layer Perceptron,MLP)是最基本的神经网络结构。
MLP由输入层、若干个隐藏层和输出层组成,每层包括多个神经元,各层之间被完全连接,每个神经元都接收来自上一层的输入信号并输出给下一层。
通过不断地训练神经网络,即对连接权重进行优化,神经网络能够准确地对所学习的模式进行分类、回归、识别、聚类等任务。
神经网络的应用非常广泛,涉及到各个领域。
在图像处理领域中,卷积神经网络(Convolutional Neural Network,CNN)是一种特殊的神经网络,主要应用于图像识别、图像分割等任务。
比如,在医疗领域中,CNN被用于对医学影像进行诊断,对疾病进行分类、定位和治疗建议的制定。
在语音处理领域中,循环神经网络(Recurrent Neural Network,RNN)因其能够处理序列数据而备受推崇,常用于文本生成、机器翻译等任务。
在自然语言处理领域中,基于预训练的语言模型(Pre-trained Language Models,PLM)在语言模型微调、文本分类和情感分析等方面表现出色。
尽管神经网络有诸多优点,但它也存在一些缺点。
其中最为突出的是过度拟合(overfitting),即模型过于复杂,为了适应训练集数据而使得泛化能力下降,遇到未知数据时准确率不高。
神经网络算法优化及应用

神经网络算法优化及应用第一章神经网络基础知识随着人工智能技术的不断发展,神经网络算法被广泛应用于各种领域。
本章将介绍神经网络的基础知识,包括神经元、网络结构、前向传播与反向传播等概念。
1.神经元神经元是神经网络的基本单位,它接收输入信号并将其转化为输出信号。
神经元包括一个权值向量和一个激活函数。
输入信号与权值向量进行内积后,再经过激活函数得到神经元的输出信号。
2.网络结构神经网络的网络结构由若干个神经元组成,通常包括输入层、隐层和输出层。
每层包括若干个神经元,隐层和输出层的每个神经元都与前一层的所有神经元相连。
3.前向传播与反向传播前向传播是指从输入层开始,逐层计算神经元的输出信号,直到输出层。
反向传播是指根据网络的误差,从输出层开始逐层反向调整权值,以减小误差。
第二章神经网络算法的优化神经网络算法在应用中需要不断进行优化,以提高模型的精度和效率。
本章将介绍神经网络算法的优化方法,包括激活函数、网络结构、迭代次数和学习率等方面。
1.激活函数激活函数影响神经元输出信号的形态,进而影响整个网络的性能。
传统的激活函数包括sigmoid、tanh和ReLU等。
近年来,被广泛应用于深度学习成果的激活函数包括softmax、sigmoid和tanh等。
这些激活函数有不同的特性,需要根据具体应用场景进行选择。
2.网络结构神经网络的结构对性能有很大的影响。
目前广泛应用的网络结构包括卷积神经网络、循环神经网络、残差网络等。
其中,卷积神经网络在图像处理和语音识别等领域得到了广泛应用,循环神经网络在自然语言处理领域得到了广泛应用。
3.迭代次数和学习率在神经网络训练过程中,迭代次数和学习率是两个重要的超参数。
迭代次数影响模型的拟合程度,过少会导致模型欠拟合,过多会导致模型过拟合。
学习率影响模型的收敛速度,过大会导致震荡,过小会导致收敛速度过慢。
应根据具体应用场景进行选择优化。
第三章神经网络算法在图像处理中的应用神经网络算法在图像处理中有着广泛的应用,如图像分类、目标检测、图像分割等。
神经网络模式识别的改进及应用

神经网络模式识别的改进及应用神经网络是一种模拟人脑神经元结构和工作方式的计算模型,通过模拟神经元之间的连接和信息传递,可以实现模式识别和学习的功能。
在神经网络模式识别的应用领域中,人们不断改进神经网络的结构和算法,以提高其识别准确率和性能。
神经网络的结构改进是提高模式识别性能的重要手段之一。
传统的神经网络模型使用多层感知机结构,其中包含输入层、隐藏层和输出层,每个神经元层之间都完全连接。
这种结构在处理大规模数据时存在计算复杂度高和过拟合的问题。
研究者们提出了一些改进结构,如卷积神经网络(CNN)和循环神经网络(RNN)。
CNN通过共享权重和局部感受野的方式,减少参数数量和计算复杂度,并在图像处理中取得了很好的效果。
RNN则通过引入循环连接,使神经网络能够处理序列化的数据,如语音识别和自然语言处理。
神经网络的算法改进也对模式识别性能的提升起到了重要作用。
传统的神经网络训练算法是基于梯度下降的反向传播算法,但该算法容易陷入局部最优解。
为了解决这个问题,研究者们提出了一些改进算法,如具有自适应学习率的优化算法(如Adagrad、Adam)和正则化算法(如Dropout、Batch Normalization)。
这些算法能够加速收敛速度、提高泛化能力,并且对于大规模数据的训练也具有较好的效果。
神经网络在模式识别中的应用越来越广泛。
在图像识别领域,神经网络可以通过训练来自动学习图像中的特征,并实现图像分类、目标检测和图像生成等任务。
在语音识别领域,神经网络可以通过训练来建立声学模型,实现语音识别和语音合成等应用。
神经网络还可以用于自然语言处理、生物信息学、金融预测等领域。
神经网络模式识别的改进和应用是一个不断发展的领域。
通过改进神经网络的结构和算法,可以提高其模式识别性能,并在各种领域中得到广泛应用。
仍然有许多挑战需要克服,如如何提高网络的可解释性和鲁棒性。
随着深度学习和大数据的不断发展,相信神经网络模式识别在未来会有更加广阔的应用前景。
神经网络技术的理论和应用

神经网络技术的理论和应用随着科技的不断发展,神经网络技术成为人们研究和应用的热点之一。
它的出现改变了传统的学习和运算方式,为人们提供了更多解决问题的可能性。
一、理论基础神经网络技术是由多层神经元组成的复杂网络,其结构类似于人类大脑的神经系统。
在神经网络中,信息处理是通过模拟能力的不断迭代进行,最终实现对数据的分析和处理。
神经网络的核心是人类学习过程的模型,其训练和学习方式也很类似。
人们通过不断的学习,掌握和积累各种知识和技能,而神经网络的学习过程同样也是从一些简单的反馈中不断逐步地逐步获得技能和知识。
二、应用1. 语音识别神经网络技术在语音识别领域中有着广泛的应用,通过对大量的语音数据进行训练,神经网络可以快速准确地识别不同的语音信号。
这一技术对人们日常生活中的语音交互和文字转换具有极大帮助。
2. 图像处理图像处理是神经网络技术最受注目的应用领域之一。
利用神经网络的卷积层和池化层等结构,可以极大地提高图像的识别和分类能力。
随着图像处理领域的快速发展,神经网络技术已经成为图像处理领域不可或缺的技术手段。
3. 数据挖掘在商业、金融和医疗等领域,数据挖掘技术的应用越来越广泛。
而神经网络技术的出现为数据挖掘提供了更多的选择。
通过对大量的数据进行训练和学习,利用神经网络实现数据的分类和预测,为企业和机构提供更加准确、快速和智能的决策支持。
三、未来发展随着互联网和科技的不断发展,人们对于神经网络技术的需求也在日益上升。
未来,神经网络技术将会在更多领域中得到广泛应用和发展,如自动驾驶、智能家居和机器人等领域。
总之,神经网络技术的理论和应用正在改变我们的生活和工作方式。
通过对于神经网络技术的深入研究和不断创新,我们相信,神经网络技术将在未来给我们带来更多惊喜和想象力。
神经网络技术的研究与应用

神经网络技术的研究与应用一、简介神经网络是一种模仿生物神经网络结构和功能的人工智能技术。
它由许多互相连接的处理单元组成,该技术可以对图像、音频、文本等多种数据进行识别、分类、预测等操作。
神经网络技术的研究和应用已经发展多年,并且逐渐在智能制造、人工智能医疗、智能金融等领域得到应用。
二、神经网络技术的研究神经网络技术的研究主要分为以下几个方面:1、网络结构的设计:神经网络能否有效地处理数据,主要取决于它的网络结构。
现有的神经网络结构包括前馈神经网络、循环神经网络、卷积神经网络等。
研究人员需要综合考虑各种因素,如数据的类型、数据的规模、处理的目标等来选择合适的结构。
2、训练算法的研究:神经网络的训练是指根据已知数据来调整网络的参数。
通常采用的方法是反向传播算法,但该算法存在着训练过程较慢、容易陷入局部最优等问题。
研究人员正在探索新的训练算法,如强化学习、进化计算等方法来提高神经网络训练效率和准确度。
3、深度学习的研究:深度学习是一种基于神经网络的机器学习方法,它是近年来发展的热点。
深度学习可以帮助神经网络学习更高层次的抽象特征,从而提升数据处理的准确性和效率。
目前,研究人员正在探索更深层次的神经网络结构和更优秀的算法来推动深度学习的发展。
三、神经网络技术的应用1、智能制造:神经网络在智能制造中有着广泛的应用。
例如,神经网络可以用来预测加工过程中的质量、识别产品的缺陷等。
近年来,随着工业互联网和数字化制造的发展,神经网络技术在智能制造中的应用将会越来越广泛。
2、人工智能医疗:神经网络技术可以用于医学图像处理、病理诊断、疾病预测等方面。
例如,在医学图像处理方面,神经网络可以帮助医生自动识别和分割出病变区域,从而帮助医生更好地评估患者的病情。
3、智能金融:基于大数据和机器学习技术,金融机构可以使用神经网络来进行风险评估、投资策略设计等方面。
例如,神经网络可以帮助银行自动识别信用卡欺诈行为、预测股价波动等。
神经网络优化算法的应用与研究进展

神经网络优化算法的应用与研究进展近年来,神经网络成为了计算机科学领域研究的热点之一。
它具有良好的自适应性、强大的计算能力和广泛的适应性。
神经网络优化算法是神经网络中的一个重要领域,它的研究成果被广泛应用于各个领域,并取得了显著的效果。
本文将探讨神经网络优化算法的应用和研究进展。
一、神经网络优化算法的应用神经网络优化算法广泛应用于模式识别、图像处理、语音处理、自然语言处理、机器人控制、金融预测等领域。
下面将介绍其中的几个应用领域。
1. 模式识别模式识别是指识别数据中的某个模式。
神经网络优化算法可以通过训练将大量的数据转换为特定的模式或类别,以实现对数据的有效分类和识别。
在生物医学领域,神经网络优化算法被广泛应用于癌症诊断和疾病治疗。
2. 图像处理图像处理是指对图像进行数字化处理。
神经网络优化算法可以从大量的图像数据中提取有用的特征,如边角、纹理等,以实现图像的匹配和分类。
这一应用领域包括图像识别、人脸识别等。
3. 语音处理语音处理是指对语音信号进行数字化处理。
神经网络优化算法可以将大量的语音数据转换为语音特征,以实现对语音信号的识别和分类。
这一应用领域包括语音识别、语音合成等。
4. 自然语言处理自然语言处理是指对自然语言进行数字化处理。
神经网络优化算法可以将大量的自然语言数据转换为特定的语法结构和语义表达,以为文本分析和语言翻译提供更好的基础。
这一应用领域包括机器翻译、语言理解等。
二、神经网络优化算法的研究进展神经网络优化算法的研究围绕着优化算法的设计和理论分析,以及算法的应用等方面展开。
下面将介绍其中的几个方面。
1. 神经网络优化算法的设计神经网络优化算法的设计是对算法的效率和可靠性进行优化的关键环节。
目前,人们主要研究神经网络优化算法的结构设计、参数设置、适应性操作等问题。
其中,进化算法、遗传算法、蚁群算法、粒子群算法、差分进化算法等被广泛应用。
2. 神经网络优化算法的理论分析神经网络优化算法的理论分析是指对算法效果进行理论分析,以发现其潜在机理,并提高算法的准确性和可靠性。
神经网络算法的应用与优化

神经网络算法的应用与优化近年来,随着计算机技术的飞速发展,人工智能引起了越来越多的关注。
神经网络算法作为人工智能领域的一项重要技术,被广泛应用于图像识别、语音处理、自然语言处理等方面。
本文将介绍神经网络算法的应用及其优化方法。
一、神经网络算法的应用神经网络算法可以模拟人脑的神经网络结构,通过大量的训练数据进行学习、识别和预测。
目前,神经网络算法已广泛应用于以下领域:1、图像识别神经网络算法在图像识别方面的应用非常广泛,几乎可以涵盖所有的物体识别、面部识别等视觉识别任务。
例如,人脸识别、车牌识别、商品识别等领域均已经成功应用了基于神经网络的算法。
同时,神经网络算法已经成为深度学习领域最为有效的算法之一,也成为了目前最为流行的人工智能技术之一。
2、语音处理神经网络算法在语音处理领域中的应用可以帮助我们实现语音识别、语音转换、语音合成等任务。
例如,商用的语音助手(Siri,Alexa等)中,语音识别部分就采用了神经网络算法。
此外,神经网络语音合成技术已经广泛应用于行业中。
3、自然语言处理自然语言处理是指计算机识别、理解和生成人类自然语言的技术。
神经网络算法在这方面的应用相当广泛,可以处理诸如机器翻译、情感分析、问答系统等任务。
例如,语音翻译功能中采用了基于神经网络的算法,此外基于神经网络的问答系统也在近些年中取得了杰出的成果。
二、神经网络算法的优化1、对网络模型进行优化在神经网络算法中,模型的设计和参数设置会对算法的性能产生很大的影响。
因此,通过对网络模型进行优化可以进一步提高神经网络算法的效率和泛化能力。
比如,常用的卷积神经网络(CNN)就是针对图像识别问题进行设计的,包括卷积层,池化层等特殊结构,同时在设计网络时需要考虑网络层数、卷积核的尺寸、池化方式等方面。
2、选择优化算法优化算法是指寻找最优解的方法,主要包括梯度下降、动量法、共轭梯度法等。
在机器学习领域,优化算法被广泛应用于模型训练过程中,它们主要的作用是在保证训练误差收敛的同时,尽可能缩短训练时间和提高训练精度。
神经网络在模式识别中的简单分析及应用参考Word

毕业论文神经网络在模式识别中的简单分析及应用模式识别就是机器识别、计算机识别或者机器自动化识别,目的在于让机器自动识别事物,使机器能做以前只能由人类才能做的事,具备人所具有的对各种事物与现象进行分析、描述与判断的部分能力。
它研究的目的就是利用计算机对物理对象进行分类,在错误概率最小的条件下,使识别的结果尽量与客观事物相符合。
随着人们对人工神经网络的不断地认识,神经网络是指用大量的简单计算单元构成的非线性系统,它在一定程度和层次上模仿了人脑神经系统的信息处理、存储及检索功能,因而具有学习、记忆和计算等智能处理功能。
这样人们利用人工神经网络具有高度的并行性,高度的非线性全局作用以及良好的容错性与联想记忆功能,并且具有良好的自适应、自学习功能等突出特点,可运用MATLAB神经网络工具箱中的神经网络模型,对经过训练的神经网络可以有效地提取信号、语音、图像等感知模式的特征,并能解决现有启发式模式识别系统不能很好解决的不变量探测、抽象和概括等问题。
这样神经网络可应用于模式识别的特征提取、聚类分析、边缘检测、信号增强以及噪声抑制、数据压缩等各个环节。
使用机器来进行模式的识别是一项非常有用的工作,能够辨别符号等系列的机器是很有价值的。
目前,模式识别技术可以应用指纹识别、IC卡技术应用、字符识别等实例。
模式识别成为人工神经网络特别适宜求解的一类问题。
因此,神经网络技术在模式识别中也得到广泛应用与发展。
关键词:模式识别;人工神经网络;神经网络模型;神经网络技术Pattern Recognition is the machine identification, computer identification or identification of machine automation, machine aimed at automatic identification of things to do before the machine can only be made by man can do, with people with all kinds of things and on an analysis of the phenomenon, described with the ability to determine the part. It is the purpose of the study of the physical object to use the computer for classification, the probability of the smallest in the wrong conditions, so that the results of recognition as far as possible in line with objective things.As artificial neural network to recognize the continuing, neural network refers to a large number of simple calculation unit consisting of non-linear system, which to some extent and level system to imitate the human brain's information processing, storage and retrieval functions, which has learning, memory and computing functions such as intelligent processing. Such people to use artificial neural network with a high degree of parallelism, the overall role of a high degree of non-linear and good fault tolerance and associative memory function, and have good self-adaptive, self-learning function, such as prominent features, the availability of MATLAB neural network toolbox The neural network model trained neural network can effectively extract the signal, voice, video and other features of perceptual patterns and heuristics to solve the existing pattern recognition systems are not well resolved invariant detection, such as abstract and summary issues. This neural network pattern recognition can be applied to feature extraction, clustering analysis, edge detection, signal enhancement and noise suppression, data compression, such as various links. The use of machines for pattern recognition is a very useful work, such as series of symbols to identify the machines are of great value. At present, the pattern recognition technology can be applied to fingerprint identification, IC card technology applications, such as examples of character recognition. Artificial neural network pattern recognition has become especially suitable for solving a class of problem. Therefore, the neural network pattern recognition technology is also widely used and development.Key words:pattern recognition;artificial neural network;neural network model;neural network technology毕业设计(论文)原创性声明和使用授权说明原创性声明本人郑重承诺:所呈交的毕业设计(论文),是我个人在指导教师的指导下进行的研究工作及取得的成果。
神经网络模式识别的改进及应用

神经网络模式识别的改进及应用神经网络模式识别是一种利用神经网络进行模式识别的方法。
随着计算机科学和人工智能技术的不断进步,神经网络模式识别技术也在不断发展和改进。
目前,在语音识别、图像识别、自然语言处理等领域都有广泛的应用。
一方面,神经网络模式识别技术的改进主要体现在模型的优化方面。
当前,神经网络模型分为前馈网络、反馈网络和卷积神经网络等多种形式。
其中,卷积神经网络是目前最为流行的神经网络之一,因其参数量少、计算速度快、准确率高等特点而受到广泛关注。
此外,还有深度监督学习、递归神经网络和长短时记忆网络等新型的神经网络结构,它们的出现为神经网络模式识别技术带来了更加优异的性能和更稳定的表现。
另一方面,神经网络模式识别技术的应用在不断扩展,如人脸识别、目标跟踪、医学影像识别等领域。
在人脸识别方面,神经网络模式识别技术可以通过学习一张人脸图像的编码,进而识别其他人脸图像。
在目标跟踪方面,可以使用神经网络识别目标并进行跟踪。
在医学影像识别领域,神经网络模式识别技术可以对医学影像进行分类,识别不同类型的肿瘤、疾病和器官。
需要注意的是,神经网络模式识别技术也存在一些应用问题。
第一,神经网络模式识别算法仍然无法解决有些模式分类问题。
第二,神经网络模式识别技术需要大量的计算资源和数据来支持其训练和推理。
第三,神经网络模式识别技术可能会存在一些漏洞和缺陷,导致其在对抗攻击等方面存在一定的脆弱性。
总之,神经网络模式识别技术的改进和应用在不断提高其性能和成果。
在未来,神经网络模式识别技术将得到更广泛的应用和发展,并成为人类智能服务和机器学习应用的核心技术之一。
神经网络算法的应用与优化

神经网络算法的应用与优化神经网络是一种模拟人脑神经系统的计算模型,通过网络结构和学习算法实现对数据的分类、识别等任务,并在各个领域得到了广泛的应用。
本文将从神经网络算法的应用和优化两个方面,探讨神经网络的发展趋势和未来发展方向。
一、神经网络算法的应用神经网络算法在人工智能、图像处理、自然语言处理、生命科学等领域得到了广泛的应用,下面分别介绍一下其在这些领域的具体应用:1.人工智能在人工智能领域,神经网络算法被广泛应用于机器学习、深度学习、大数据分析等方面。
例如,语音识别、人脸识别、自然语言处理、机器翻译等都是通过神经网络算法来实现的。
此外,随着深度学习算法的不断发展,不少科研机构和企业也开始使用神经网络算法来做一些创新性的工作,比如 AlphaGo 人工智能围棋系统,它通过神经网络算法进行大量的训练,成功地战胜了该领域最顶级的人类选手。
2.图像处理图像处理领域也是神经网络算法应用很广的领域。
以图像识别为例,几年前如果你想要识别一张猫的图像,还需要让计算机事先知道什么是猫,然后给出一系列规则,让计算机去寻找那些具有猫特征的像素点,这种方法显然存在很多限制。
而神经网络算法可以直接让计算机通过对大量数据学习,自动识别图片中的物体。
3.自然语言处理自然语言处理(NLP)领域的发展,绝大部分依赖于深度学习技术。
目前的大部分NLP 模型都是基于神经网络模型的基础之上,例如,语义分析、情感分析、关键字提取、自动问答等。
4.生命科学在生命科学领域,神经网络算法一般用于数据挖掘及模式识别。
例如基因组分析、药物发现、蛋白质结构预测等。
二、神经网络算法的优化尽管神经网络模型具备了很多优秀的特性,但是其自身也存在着很多问题。
例如模型训练困难、过拟合、收敛速度慢等。
下面分别介绍针对这些问题的优化方案:1.模型训练神经网络的训练是一个环环相扣的过程,不同的算法会对神经网络的训练速度和效果产生不同的影响。
比如,在梯度下降算法的基础之上,出现了各种优化方法,如动量优化算法(Momentum)和自适应学习率优化算法(AdaGrad)等。
神经网络理论及应用

神经网络理论及应用神经网络是模拟人类大脑和神经系统工作的计算机系统。
神经网络学习数据之间的关系,从而能够识别和分类数据。
神经网络已广泛应用于图像识别、语音识别、自然语言处理、机器翻译等领域。
本文将对神经网络的理论与应用进行探讨。
一、神经网络的理论1.神经元模型神经元是神经网络的基本元素,它有一个或多个输入和一个输出。
神经元通常用一个函数来描述,称为激活函数。
常用的激活函数有sigmoid函数、ReLU函数等。
sigmoid函数将输入变量映射到0和1之间,ReLU函数将负输入映射为0。
2.前馈神经网络前馈神经网络是最基本的神经网络类型。
它由输入层、若干个隐藏层和输出层组成。
输入层接收输入数据,然后通过隐藏层进行处理,最终输出结果。
隐藏层可以有多个,每个隐藏层的神经元数可以不同。
前馈神经网络的训练通常采用反向传播算法。
3.卷积神经网络卷积神经网络是一种特殊的神经网络,设计用于处理具有网格结构的数据,如图像和语音。
它的主要特点是参数共享和卷积运算。
参数共享是指卷积层的每个神经元都使用相同的卷积核进行计算。
这种方法可以减少计算量和参数量,但也可能导致信息的损失。
4.循环神经网络循环神经网络是一种能够处理序列数据的神经网络。
它通过反馈机制来处理当前时刻的输入和前一时刻的状态。
循环神经网络通常采用长短时记忆网络(LSTM)或门控循环单元(GRU)来处理长序列数据。
二、神经网络的应用1.图像识别图像识别是神经网络最常见的应用之一。
卷积神经网络是用于图像识别的最佳工具,它能够学习特征、识别物体并将其分类。
深度学习在图像识别领域的应用已经取得了显著的成果,如GoogleNet、VGGNet、ResNet等。
2.语音识别语音识别是另一个重要的应用,它可以将语音信号转换为相应的文本或命令。
循环神经网络是一个常用的语音识别工具,它能够使用基于声音特征的声学模型,并将其与语言模型相结合,以实现更准确的语音识别。
3.自然语言处理自然语言处理是指计算机处理自然语言的能力,包括文本分类、情感分析、语言翻译等。
几类神经网络的分析与优化及其应用研究

几类神经网络的分析与优化及其应用研究一、本文概述随着技术的快速发展,神经网络作为其中的核心组成部分,已经在诸多领域取得了显著的成果。
本文旨在探讨几类常见的神经网络模型,包括前馈神经网络、卷积神经网络、循环神经网络等,并分析它们的特性、优势以及存在的问题。
在此基础上,我们将深入研究神经网络的优化方法,包括参数优化、结构优化等方面,以提升网络的性能。
我们还将关注神经网络在不同领域的应用,如计算机视觉、自然语言处理、语音识别等,并探讨如何将神经网络的理论研究与实际应用相结合,推动技术的发展。
通过本文的研究,我们希望能够为神经网络的研究者和实践者提供一些有益的参考和启示,推动神经网络技术的进一步发展。
二、神经网络基本原理与分类神经网络是一种模拟人脑神经元结构的计算模型,其基本原理在于通过构建复杂的网络结构,模拟人脑对信息的处理过程。
神经网络由大量的神经元(或称为节点、单元)相互连接而成,每个神经元接收来自其他神经元的输入信号,并根据自身的权重和激活函数进行处理,产生输出信号。
整个神经网络通过不断地调整权重,使得输出信号与期望结果之间的误差最小,从而实现对输入信息的识别、分类、预测等功能。
神经网络的分类多种多样,根据其结构特点和应用场景,可以分为前馈神经网络、反馈神经网络、卷积神经网络、循环神经网络等。
前馈神经网络是最基本的神经网络类型,信息在网络中单向传递,没有反馈回路。
卷积神经网络则特别适用于处理图像数据,通过卷积层、池化层等结构,能够提取图像中的特征并进行分类。
循环神经网络则适用于处理序列数据,如自然语言、时间序列等,其内部的循环结构使得网络能够记住之前的信息,从而更好地处理序列数据。
除了以上几种常见的神经网络类型,还有许多其他特殊的神经网络结构,如长短期记忆网络(LSTM)、生成对抗网络(GAN)等,这些网络结构在特定的应用领域中取得了显著的成果。
例如,LSTM网络在处理自然语言、语音识别等领域中表现出色,而GAN网络则在图像生成、超分辨率等领域中取得了显著的突破。
神经网络模式识别的改进及应用

神经网络模式识别的改进及应用神经网络模式识别是一种通过神经网络模型对输入数据进行分析和分类的方法,已经在许多领域取得了显著的成功。
目前的神经网络模式识别仍存在一些改进的空间,这些改进可以进一步提高模型的性能和应用的效果。
神经网络模式识别可以通过改进网络结构和参数优化方法来提高性能。
目前常用的神经网络结构包括多层感知器、卷积神经网络和循环神经网络等,可以根据不同任务的特点选择最合适的网络结构。
优化算法如梯度下降、遗传算法和模拟退火算法等也可以用于调整神经网络参数,进一步提高识别准确率。
神经网络模式识别可以通过引入更多的样本和特征来改进。
样本的多样性和数量对模型的训练和泛化性能有重要影响,因此可以通过收集更多的数据来扩充样本集。
特征的选择和提取也是模式识别的关键环节,可以通过改进特征提取算法和引入更多的特征来改善模型的性能。
神经网络模式识别还可以借鉴其他领域的方法和思想进行改进。
可以引入深度学习和迁移学习的思想,将神经网络扩展为深度神经网络,并利用预训练的模型参数进行迁移学习,从而提高模型的泛化能力和适应性。
可以探索结合其他模式识别方法如支持向量机、隐马尔可夫模型和贝叶斯网络等,通过多个模型的集成和融合来提高模式识别的性能。
神经网络模式识别已经在许多领域得到应用,如图像分类、语音识别、文本挖掘和生物信息学等。
改进神经网络模式识别算法可以进一步提高这些应用的效果。
在图像分类中,可以通过改进卷积神经网络结构和训练算法来提高分类精度;在语音识别中,可以利用循环神经网络模型和迁移学习方法来提高语音识别的准确率;在文本挖掘中,可以利用深度学习和注意力机制来提取文本特征,从而提高分类和聚类的效果;在生物信息学中,可以利用神经网络模型来预测蛋白质结构和基因功能,从而促进生物学研究的进展。
通过改进神经网络模式识别的网络结构、参数优化、样本和特征的扩充以及借鉴其他领域的方法和思想,可以进一步提高模式识别的性能和应用效果,推动相关领域的发展和应用。
如何优化神经网络性能
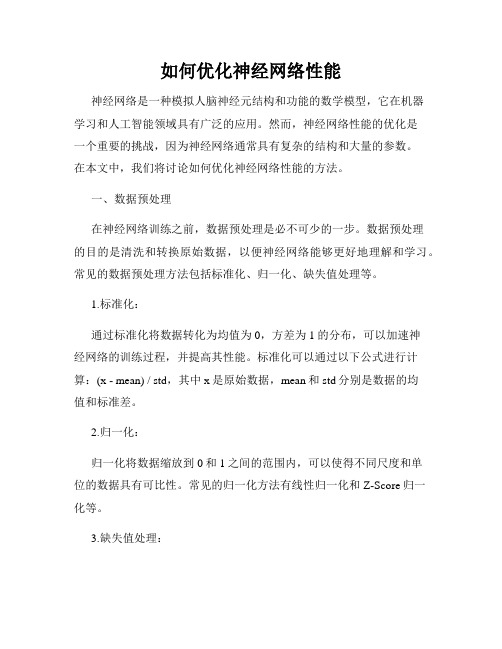
如何优化神经网络性能神经网络是一种模拟人脑神经元结构和功能的数学模型,它在机器学习和人工智能领域具有广泛的应用。
然而,神经网络性能的优化是一个重要的挑战,因为神经网络通常具有复杂的结构和大量的参数。
在本文中,我们将讨论如何优化神经网络性能的方法。
一、数据预处理在神经网络训练之前,数据预处理是必不可少的一步。
数据预处理的目的是清洗和转换原始数据,以便神经网络能够更好地理解和学习。
常见的数据预处理方法包括标准化、归一化、缺失值处理等。
1.标准化:通过标准化将数据转化为均值为0,方差为1的分布,可以加速神经网络的训练过程,并提高其性能。
标准化可以通过以下公式进行计算:(x - mean) / std,其中x是原始数据,mean和std分别是数据的均值和标准差。
2.归一化:归一化将数据缩放到0和1之间的范围内,可以使得不同尺度和单位的数据具有可比性。
常见的归一化方法有线性归一化和Z-Score归一化等。
3.缺失值处理:在实际的数据集中,常常存在缺失值的情况。
对于缺失值,可以选择删除对应的样本或者插补缺失值。
常用的插补方法有均值插补、中位数插补以及回归插补等。
二、选择合适的激活函数激活函数在神经网络中起到了非常重要的作用,它可以引入非线性,帮助神经网络更好地进行拟合。
在选择激活函数时,需要考虑其导数可导性、饱和区间、计算效率等因素。
1. ReLU函数:ReLU函数是常用的激活函数之一,它在x大于0时输出为x,小于0时输出为0。
ReLU函数具有非常好的收敛性和非线性表达能力,在深层神经网络中广泛应用。
2. Sigmoid函数:Sigmoid函数在x无限趋近于正无穷和负无穷时,分别趋近于1和0。
然而,Sigmoid函数在梯度消失和梯度爆炸的问题上表现较差,因此在深层神经网络中使用较少。
3. Tanh函数:Tanh函数是Sigmoid函数的一种变体,它在x无限趋近于正无穷和负无穷时,分别趋近于1和-1。
Tanh函数相较于Sigmoid函数来说,基本解决了梯度消失的问题,但仍可能存在梯度爆炸的问题。
神经网络模型优化及其在分类问题中的应用

神经网络模型优化及其在分类问题中的应用神经网络是人工智能领域中的一种重要的算法,它通过模拟人类神经系统的工作方式,实现对输入数据进行自动处理和学习。
在计算机视觉、语音识别、自然语言处理等领域,神经网络模型已经取得了诸多成功应用。
但是,在实际应用中,神经网络模型的训练和优化仍然面临着许多挑战和难题。
本文将着重探讨神经网络模型的优化方法以及在分类问题中的应用。
一、神经网络模型的训练与优化神经网络的训练过程是指通过给定的输入数据和相应的标签,利用反向传播算法对神经网络的权重和偏置进行一定的调整,从而实现神经网络的自适应调整和优化的过程。
1.梯度下降算法:梯度下降法是一种基于梯度的优化算法,其基本思想是通过不断地迭代调整参数,使得模型误差最小化。
梯度下降算法有两种基本形式:批量梯度下降和随机梯度下降。
2.动量法:动量法是一种基于动量的优化算法,它可以在梯度下降算法的基础上增加一个动量项,从而在更新参数时加快算法的收敛速度。
3.自适应学习率算法:自适应学习率算法是一种基于梯度方差的优化算法,它可以根据实际的梯度变化情况自适应地调整学习率,从而在收敛速度和精度方面取得更好的效果。
二、神经网络模型在分类问题中的应用神经网络模型在分类问题中的应用已经得到了广泛的应用,其基本思想是将特征向量作为输入,通过神经网络模型学习分类规则,从而实现对输入数据的分类。
1.手写数字识别:手写数字识别是神经网络在分类问题中的一个典型应用。
神经网络模型可以通过训练大量的手写数字图像数据来学习分类规则,从而实现对未知手写数字的识别。
2.图像分类:在图像分类问题中,神经网络模型可以通过训练大量的图像样本数据来学习图像特征,从而实现对输入图像的自动分类和识别。
3.文本分类:在自然语言处理中,文本分类是一个重要的问题。
神经网络模型可以通过学习单词和短语的分布规律,实现对文本数据的自动分类和识别。
总结神经网络模型优化及其在分类问题中的应用是人工智能领域的一个重要研究方向。
算法优化在深度神经网络中的应用研究

算法优化在深度神经网络中的应用研究深度学习已经成为先进技术领域中最热门、最具突破性的领域之一。
尤其是深度神经网络,随着硬件设备的不断升级和GPU等专门处理器的普及,深度学习已成为其中一个比较优秀的算法,其中深度神经网络是其中的佼佼者。
然而,深度神经网络虽然在实践中表现优异,但是其模型本质上仍有缺陷。
很难保证在每次训练中均可以得到高效的结果。
因此,研究如何优化深度神经网络的算法以提高训练准确率和速度变得异常重要。
本文将从算法优化的角度,探讨算法优化在深度神经网络中的实际应用和研究。
一、算法优化是什么算法优化是一种重要的技术,可以帮助我们改善深度神经网络在训练过程中所面临的一些问题。
在深度学习中,算法优化主要是针对误差反向传播算法进行的优化,目的是减少训练时间并提高准确性。
在算法优化的过程中,开发者需要考虑以下几个方面:1. 激活函数激活函数是神经元的数学函数,它将输入信号转化为输出信号。
常见的激活函数包括sigmoid、ReLU等。
算法优化中需要考虑如何选择合适的激活函数,以提高深度神经网络的性能。
2. 权重初始化权重初始化是指初始化训练网络中的权重值。
正确的权重初始化可以使神经网络正常训练,而不会使结果发生偏移。
在算法优化中,正确地初始化权重是非常关键的。
3. 学习率在深度学习中,学习率是指在误差反向传播过程中权重的变化速度。
学习率的变化影响着神经网络的训练速度和精度。
在算法优化中,需要选择适当的学习率,使深度神经网络在训练过程中得到更好的结果。
二、深度神经网络的训练问题深度神经网络优化算法的主要目的是解决深度神经网络训练过程中的一些问题。
这些问题通常涉及到“梯度消失”、“过拟合”、“优化”等问题。
1. 梯度消失梯度消失,指神经网络在反向传播中,由于链式法则的存在,梯度逐层变化,当误差逆传时,梯度值越来越小,直到接近于0,导致网络无法继续学习更新。
这种情况在深度神经网络中更加常见。
在深度神经网络优化算法中,需要解决梯度消失的问题,以确保神经网络的正常训练。
神经网络模型优化与应用研究

神经网络模型优化与应用研究第一章:引言近年来,神经网络技术在图像、语音、自然语言处理等领域中得到越来越广泛的应用,其中深度学习作为神经网络的一种重要应用形式,已经成为了人工智能主要研究领域之一。
然而,在处理复杂问题时,神经网络模型往往存在着过拟合、欠拟合等问题,因此对神经网络模型的优化研究是十分必要的。
本文将围绕神经网络模型的优化与应用展开详细阐述。
第二章:神经网络模型的优化2.1 参数初始化方法神经网络的参数初始化是在训练之前必须进行的一步,不同的初始化方法会对模型的训练和收敛性能产生不同的影响。
常见的初始化方法有随机初始化、Xavier初始化、He初始化等,其中Xavier初始化适用于tanh、sigmoid等饱和非线性函数,而He初始化适用于ReLu等非饱和非线性函数。
2.2 激活函数的选择激活函数是神经网络中的重要组成部分,其主要作用是引入非线性因素,增强网络的表达能力。
常见的非线性激活函数主要包括sigmoid、tanh、ReLU等,其中ReLU是目前应用最广泛的激活函数之一,其具有计算简单、训练速度快等特点。
2.3 梯度下降法在神经网络的训练中,梯度下降算法是最常用的一种优化方法,其主要思路是在每次迭代中根据损失函数对参数求解梯度,并根据梯度方向更新参数。
常见的梯度下降算法主要包括批梯度下降、随机梯度下降、小批量梯度下降等,其中小批量梯度下降算法在实践中应用最为广泛。
2.4 正则化方法正则化方法是用来避免神经网络模型出现过拟合问题的一种常见方法。
常见的正则化方法包括L1正则化、L2正则化、dropout 等,其中dropout是一种比较有效的正则化方法,其主要思想是在每次训练迭代中随机将一部分神经元设置为0。
第三章:神经网络模型在自然语言处理中的应用3.1 词向量的表示神经网络在自然语言处理领域中的应用主要体现在对文本进行表示学习,其中词向量表示是关键。
Word2Vec是一种常用的词向量表示方法,其主要思想是通过神经网络来学习每个词的向量表示,可以有效地处理同义词、近义词等问题。
- 1、下载文档前请自行甄别文档内容的完整性,平台不提供额外的编辑、内容补充、找答案等附加服务。
- 2、"仅部分预览"的文档,不可在线预览部分如存在完整性等问题,可反馈申请退款(可完整预览的文档不适用该条件!)。
- 3、如文档侵犯您的权益,请联系客服反馈,我们会尽快为您处理(人工客服工作时间:9:00-18:30)。
第4章优化网络在板形模式识别中的应用4.1 引言 板形是表征板带材横向质量的,它包含两重意义:一重意义是指板带材的横向厚差;另一重意义是指板带材的横向张力差。
前者主要对中厚板起作用;后者对薄板起作用,用平直度来标定[45,46]。
对冷轧带钢来说,“板形”的概念通常指平直度,平直度是指不平直的程度,亦即对一平坦平面的偏离程度,平直度也就是这种偏离程度的计量。
“板形”就其实质而言,是指带钢内部残余应力的分布程度[47]。
通常冷轧带钢产品不允许有明显的浪形与瓢曲等板形缺陷存在,因为板形不良将影响用户的使用。
如带钢在长度方向在水平面上向一边弯曲,会影响用户放样下料、自动进料或材料的利用率,更为严重的是切不成材,无法使用。
因此板形是冷轧带钢产品标准的保证项目之一。
在板形闭环控制策略中,板形缺陷识别和控制策略优化是彼此相关的两个重要环节。
为制定合理的控制策略,须通过对实测的一组板形应力信σ(i=1,2,…,n)进行模式识别,并以约定的参数定量的提供给下一控制号i环节,这即为板形缺陷模式识别。
在实际板形控制系统中,轧机出口带材的板形信息可以通过板形仪在线测量获得。
众所周知,轧机不同的执行机构控制不同类型的板形缺陷,而由板形仪测得的板形数据是一个综合板形缺陷,无法直接应用到板形控制系统中。
只有通过适当的方法进行模式分解,提取出控制系统各回路的控制量,才能达到控制板形的目的。
因此,实测板形的模式分解是板形控制系统中必不可少的一个环节,也是板形控制中的一个热点。
板形模式识别的主要任务是把在线检测到的(或理论计算得到的)一组张力分布离散值,经过一定的数学方法,映射为较少的几个特征参数,并且具有如下性质[48]:(1)尽可能少的状态变量,数学表达简练;(2)不丢失必要的信息,特征参数能够完全反映原应力分布值所决定的带钢板形质量状态;(3)特征参数便于计算机处理,满足控制上的要求。
对于处理这组离散的板形应力值,目前采用较多的是基于多项式的最小二乘法拟合原理的普通多项式回归方法和正交多项式回归分解法[49,50]。
基于多项式的板形模式识别方法,虽然能够有效地分解实测板形数据,但是其弱点在于,板形缺陷模式较复杂,数学描述及作为控制参数使用均不方便[51~53],抗干扰能力差,已不能满足新一代高技术板带轧机的在线板形控制的需要[54]。
为此根据被控轧机的技术、工艺实况及控制要求,定义N种简单的板形缺陷模式作为基本模式,则识别结果就是其中某一种基本模式或几种基本模式的组合,该识别方法数学表达简练,便于描述;能正确反映原应力分布所决定的板形状况;可直接输入后续控制环节,满足控制要求。
目前人工智能技术在轧制中的应用取得了较大的进展[55,56],在板形识别中使用较多的有两种新方法:模糊分类原理模式识别法和人工神经网络原理板形识别法[57~63]。
两种新方法完成一次识别所需时间都很短;在预先以工艺原则选择基本模式时能考虑轧机的各种板形调控能力。
人工神经网络原理板形识别法对实测信号具有一定的容错能力,而且由此导致的对主要模式成分的夸大和对次要模式成分的缩小,相当于一种智能调节器的作用。
与之相比较,模糊分类原理板形模式识别法的识别能力和精度不如前者,但它的模型简单实用,快速有效,能给出稳定的定量识别结果。
文献[57,61]中,提出的神经网络识别方法,网络输出均为6个,即对应6种标准的板形缺陷模式,6个输出均介于0~1之间,仅仅反映待识别板形偏差信号的缺陷类型,而不能定量反映每种板形缺陷的实际数值,这样就无法为板形控制提供可靠的依据;隐节点数量是随机选取的,存在一定的盲目性;还有一个关键问题是板形标准模式的选取不满足板形值自相平衡即沿横向的积分为零的条件。
这是上述识别方法的不足之处。
4.2 优化网络在板形模式识别中的应用本节在分析现有板形识别方法存在问题的基础上,根据文献[48]提出的基于勒让德多项式系板形模式识别方法,将第3章所述前向网络优化设计方法用于板形缺陷模式的识别,建立了6输入、3输出的识别网络。
将待测板形信号与6个标准板形模式的欧氏距离作为网络输入,板形模式的3个特征值作为网络输出。
基于遗传算法的网络优化设计方法的应用,使识别网络在训练过程中,始终保持最优的网络结构和映射关系,避免了以往神经网络识别方法中,隐节点及隐层作用函数选取的盲目性,能够快速、准确的表达板形缺陷的模式信息及数值大小,为后续板形控制调节量的设定提供了可靠依据,满足高精度、实时板形控制的要求。
4.2.1 待识别板形的归一化处理由于板形仪检测的板形数据是带材的前张应力数值,而板形是指带钢内部残余应力的分布,因此须在前张应力分布值中消除平均前张应力的影响,即可得到轧后带材残余应力分布值,也就是板形值。
设板形仪测得带材前张应力为q σ,则其实测板形值为2/))](,([)()(i x trapz i i q q m σσσ−= (i =1,2,…,n ) (4-1)式中 m σ——板形仪测得的实际板形q σ——板形仪测得的带材前张应力x ——检测辊各测量段中心到带材中心处的坐标,]1,1[−∈x n ——n 为被带材覆盖的板形仪的测量区段数trapz ——Matlab 工具箱中的积分函数,用以求出平均前张力 设目标板形残余应力为t σ,则板形调节偏差为)()()(i i i t m σσσ−=∆ (i =1,2,…,n ) (4-2)式中 t σ——选定的目标板形由于BP 网络中S 型非线性函数f (x )随着x 的增大,梯度下降并趋于零,不利于权值的调整,因此希望x 工作在较小的区域。
故将网络输入做归一化处理,使实测数据转换为()0.1,0范围内的变量,然后作为网络输入。
板形偏差的最大值为)}({max 1max i ni σσ∆=∆= (i =1,2,…,n ) (4-3)由式(4-2)、(4-3),可求得板形偏差的归一化处理结果max)()(σσσ∆∆=′∆i i (i =1,2,…,n ) (4-4)4.2.2 标准板形的归一化处理从冷轧板带轧制工艺过程来看,轧后板形曲线即是轧后带材残余应力偏差沿横向(板宽方向)的分布曲线。
板形残余应力应满足其自相平衡即沿带宽横向积分为零的约束条件,所以板形基本模式曲线选为勒让德多项式系更接近实际。
所谓板形模式识别,就是识别板形的缺陷模式,然后根据识别结果,采取相应的控制方案,对板形进行自动控制。
由于轧机的执行机构只能消除左边浪、右边浪、中间浪、双边浪、边中浪和四分浪六种基本的全局板形缺陷,而更复杂的局部板形缺陷,需要通过轧辊分段冷却控制。
所以设置板形标准模式时,只需设置上述六种基本模式即可,这些基本模式构成了标准样本,每一个标准样本都有n 个参数,n 为被带材覆盖的板形仪的测量区段数。
六种基本板形缺陷模式)](,),2(),1([n k k k k σσσσL L =,(k =1,2,…,6),其标准归一化方程为左边浪 x x =)(1σ (4-5) 右边浪 x x −=)(2σ (4-6) 中间浪 2123)(23−=x x σ (4-7) 双边浪 2123()(24−−=x x σ (4-8)四分浪 )33035(81)(245+−=x x x σ (4-9)边中浪 )33035(81)(246+−−=x x x σ (4-10)x 是检测辊各测量段中心到带材中心处的坐标,归一化后]1,1[−∈x ,即对应带材两端的坐标分别为-1,1。
板形信号的基本模式如图4-1所示。
-0.5-0.5四分浪边中浪-0.50.50.5-0.5图4-1 板形信号的基本模式 Fig.4-1 Basic patterns of shape signal由式(4-5)~(4-10)可看出,六种标准模式中,左边浪和右边浪,中浪和双边浪,四分浪和边中浪互为互反的模式对。
由于带材板形模式是复合板形,且根据轧机执行机构的要求,识别出的板形模式中不能同时存在左边浪和右边浪、中间浪和双边浪、四分浪和边中浪,所以可将带材板形拟合成基本板形模式的多项式形式,如下式表示:)()()()()(4332211x P x P a x P a x P a x +++=σ (4-11)式中P 1(x )=x (4-12) 2123)(22−=x x P (4-13) )33035(81)(243+−=x x x P (4-14)P 1(x )——一次板形缺陷模式,即左边浪和右边浪,由倾辊来消除 P 2(x )——二次板形缺陷模式,即中间浪和双边浪,由弯辊消除P 3(x )——四次板形缺陷模式,即四分浪和边中浪,由弯辊和中间辊横移来消除P 4(x )——高次板形缺陷,由局部冷却来消除a 1、a 2、a 3——板形特征参数,其符号代表板形所属的模式类型,当a 1、a 2、a 3为正数时,代表的是左边浪、中间浪、四分浪,否则为负数时,代表的则是右边浪、双边浪和边中浪;其数值则精确反映了残余应力含有该板形缺陷的程度板形特征参数a i (i =1,2,3),既可反映实测板形残余应力与6种板形标准模式的归属关系,又可反映实测残余应力含有6种板形标准模式的精确数量关系。
4.2.3 神经网络结构及样本的选取已知归一化处理后的待识别板形为)](,),2(),1([n σσσσ′∆′∆′∆=′∆L 第k 个基本模式为)](,),2(),1([n k k k k σσσσ∆∆∆=∆L (k =1,2,…6) 采用欧氏距离形式求出σ′∆与k σ∆之间的距离D k ,然后将此距离做归一化处理,取为(0-1)之间的值DD k ,作为网络的输入。
∑=∆−′∆=∆−′∆=ni k k k i i D 12/12]))()(([σσσσ (4-15)∑=k k k D D DD / (k =1,2,…6) (4-16)DD k 反映了待识别板形与标准板形模式的相似程度,DD k 越接近于0,说明σ′∆与k σ∆越相似。
由于BP 网络中,增加隐层数可以降低误差,提高精度,但同时也使网络复杂化,而误差精度的提高也可以通过增加隐含层中的神经元数目来获得,所以,采用单隐层的BP 网络,输入节点为6个,分别为待测板形与六种板形基本模式的归一化距离DD k ;输出节点取为3个,即归一化后板形模式的特征值,用u 1,u 2,u 3表示。
由于板形基本模式的个数是固定的(k m =6),所以网络的输入节点和输出节点个数是固定的,不论板宽如何变化,识别网络的结构可以不变,始终是6-H -3(H 是隐层节点个数)。
网络训练时,标准样本的选取,如表4-1所示。
表4-1 GA-BP 网络标准输入输出样本 Table 4-1 I/O Samples of GA-BP network输入样本DD k (k =1,2, (6)输出样本u k (k =1,2,3)[0 * * * * *] [1 0 0] [* 0 * * * *] [-1 0 0] [* * 0 * * *] [0 1 0] [* * * 0 * *] [0 -1 0] [* * * * 0 *] [0 0 1] [* * * * * 0][0 0 -1]*为0~1之间的任意非0值,表示待识别板形缺陷与基本板形模式的归一化欧氏距离4.2.4 板形识别网络的优化设计根据第3章提出的BP 网络优化设计方法,对板形识别网络进行优化设计,先由遗传算法优化出网络结构、隐层作用函数和初始权、阈值,再由BP 算法继续训练,从而寻得最优的识别网络。