加工中心高速切削参数表
加工中心硬质合金刀具切削参数表经典

0.06 -0.025--0.047 高速推荐侧刃切削
1500 -0.025--0.047 高速推荐侧刃切削
13000 -0.025--0.047 高速推荐侧刃切削
60 -0.025--0.047 高速推荐侧刃切削
0.81 -0.025--0.047 高速推荐侧刃切削
刀具直径
E6 E6 E6 E6 E6 E6 E8 E8 E8 E8 E8 E8 刀具直径
0.06 -0.025--0.047 高速推荐侧刃切削
1500 -0.025--0.047 高速推荐侧刃切削
13000 -0.025--0.047 高速推荐侧刃切削
60 -0.025--0.047 高速推荐侧刃切削
0.81 -0.025--0.047 高速推荐侧刃切削
高速切削 刀具精度
侧刃切削
15 -0.025--0.047 高速推荐侧刃切削
侧刃切削
0.2-0.3 4
1200 2950 50 0.783 0.2-0.3
6 1300 2800 50 0.783 侧刃切削
0.25-0.5 8
1500 1750 60 1.087 0.25-0.5 10 1500 2000 60
高速切削 刀具精度
侧刃切削
9
-0.025--0.047 高速推荐侧刃切削
0.06 -0.025--0.047 高速推荐侧刃切削
1500 -0.025--0.047 高速推荐侧刃切削
13000 -0.025--0.047 高速推荐侧刃切削
60 -0.025--0.047 高速推荐侧刃切削
0.81 -0.025--0.047 高速推荐侧刃切削
9
-0.025--0.047 高速推荐侧刃切削
三菱系统加工中心G和M指令
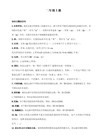
G84 固定循环(攻牙)
G85 固定循环(搪孔)
G86 固定循环(搪孔)
G87 固定循环(反搪孔)
G88 固定循环(搪孔)
G89 固定循环(搪孔)
G90 绝对值指令
G91 增量值指令
G92 机械坐标系设定
M10 吹气关闭 →
M09也能关吹气
M11《斗笠式》主轴夹刀
M12 主轴松刀
M13 主轴正转+切削液启动
M14 主轴反转+切削液启动
M15 主轴停止+切削液关闭
M16— M18没有
M19 主轴定位
M20 —— 没有
G61 正确停止检查模式
G61.1 高精度制御
G62 自动转角进给率调整
G63 攻牙模式
G63.1 同期攻牙模式(正攻牙)
G63.2 同期攻牙模式(逆攻牙)
G64 切削模式
G65 使用者巨集 单一呼叫
G66 使用者巨集 状态呼叫A
G74 固定循环(反向攻牙)
G75 使用者固定循环
G76 固定循环(精搪孔)
G77 使用者固定循环
G78 使用者固定循环
G79 使用者固定循环
G80 固定循环取消
G81 固定循环(钻孔/铅孔)
G82 固定循环(钻孔/计数式搪孔)
M86 工作台门开
M87 工作台门关
M88 —— M97 没有
M98 调用子程序
M99 子程序结束
三菱系统加工中心G指令M指令一览表
G00 快速定位
G01 直线补间切削
G02 圆弧补间切削
加工中心切削转速和进给速度计算方法及公式
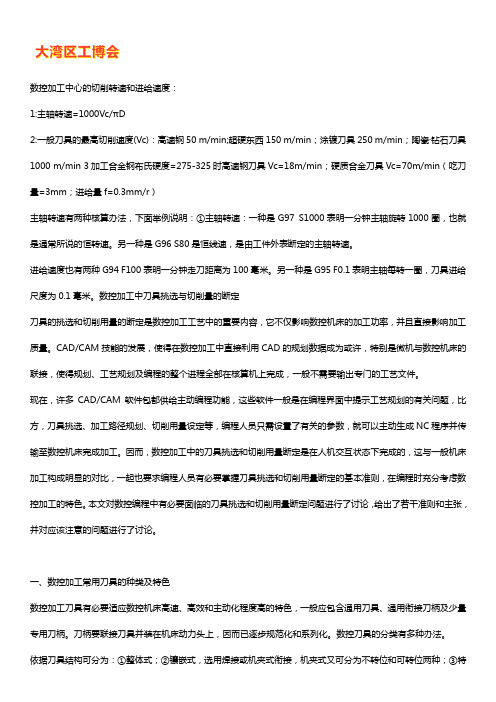
数控加工中心的切削转速和进给速度:1:主轴转速=1000Vc/πD2:一般刀具的最高切削速度(Vc):高速钢50 m/min;超硬东西150 m/min;涂镀刀具250 m/min;陶瓷·钻石刀具1000 m/min 3加工合金钢布氏硬度=275-325时高速钢刀具Vc=18m/min;硬质合金刀具Vc=70m/min(吃刀量=3mm;进给量f=0.3mm/r)主轴转速有两种核算办法,下面举例说明:①主轴转速:一种是G97 S1000表明一分钟主轴旋转1000圈,也就是通常所说的恒转速。
另一种是G96 S80是恒线速,是由工件外表断定的主轴转速。
进给速度也有两种G94 F100表明一分钟走刀距离为100毫米。
另一种是G95 F0.1表明主轴每转一圈,刀具进给尺度为0.1毫米。
数控加工中刀具挑选与切削量的断定刀具的挑选和切削用量的断定是数控加工工艺中的重要内容,它不仅影响数控机床的加工功率,并且直接影响加工质量。
CAD/CAM技能的发展,使得在数控加工中直接利用CAD的规划数据成为或许,特别是微机与数控机床的联接,使得规划、工艺规划及编程的整个进程全部在核算机上完成,一般不需要输出专门的工艺文件。
现在,许多CAD/CAM软件包都供给主动编程功能,这些软件一般是在编程界面中提示工艺规划的有关问题,比方,刀具挑选、加工路径规划、切削用量设定等,编程人员只需设置了有关的参数,就可以主动生成NC程序并传输至数控机床完成加工。
因而,数控加工中的刀具挑选和切削用量断定是在人机交互状态下完成的,这与一般机床加工构成明显的对比,一起也要求编程人员有必要掌握刀具挑选和切削用量断定的基本准则,在编程时充分考虑数控加工的特色。
本文对数控编程中有必要面临的刀具挑选和切削用量断定问题进行了讨论,给出了若干准则和主张,并对应该注意的问题进行了讨论。
一、数控加工常用刀具的种类及特色数控加工刀具有必要适应数控机床高速、高效和主动化程度高的特色,一般应包含通用刀具、通用衔接刀柄及少量专用刀柄。
FANUC高速、高精加工的参数调整

铣床、加工中心高速、高精加工的参数调整(北京发那科机电有限公司王玉琪)使用铣床或加工中心机床加工高精度零件(如模具)时,应根据实际机床的机械性能对CNC系统(包括伺服)进行调整。
在FANUC的AC 电机的参数说明书中叙述了一般调整方法。
本文是参数说明书中相关部分的翻译稿,最后的“补充说明”叙述了一些实际调试经验和注意事项,仅供大家参考。
对于数控车床,可以参考此调整方法。
但是车床CNC系统无G08和G05功能,故车床加工精度(如车螺纹等)不佳时,只能调整HRV参数和伺服参数。
Cs控制时还可调整主轴的控制参数。
目录使用αi电机…………………………………………………P 2使用α电机……………………………………………………P22补充说明………………………………………………………P241使用αi电机伺服HRV控制的调整步骤⑴概述i系列CNC(15i/16i/18i)的伺服因为使用了HRV2和HRV3控制(21i为选择功能),改善了电流回路的响应,因此可使速度回路和位置回路设定较高而稳定的增益值。
图使用伺服HRV控制后的效果速度回路和位置回路的高增益,可以改善伺服系统的响应和刚性。
因此可以减小机床的加工形状误差,提高定位速度。
由于这一效果,使得伺服调整简化。
HRV2控制可以改善整个系统的伺服性能。
伺服用HRV2调整后,可以用HRV3改善高速电流控制,因此可进行高精度的机械加工。
若伺服HRV控制与CNC的预读(Look-ahead)控制,AI轮廓控制,AI纳米轮廓控制和高精度轮廓控制相结合,会大大改善加工性能。
关于这方面的详细叙述,请见节“高速、高精加工的伺服参数调整”。
2图伺服HRV控制的效果实例⑵适用的伺服软件系列号及版本号90B0/A(01)及其以后的版本(用于15i,16i,18i和21i,但必须使用320C5410伺服卡)。
⑶调整步骤概况HRV2和HRV3控制的调整与设定大致用以下步骤:①设定电流回路的周期和电流回路的增益(图中的*1 )电流回路的周期从以前的250μs降为125μs。
加工中心切削参数表

1450 -0.025--0.047 高速推荐侧刃切削
E10
高速涂层 4 S(转/min) 不提倡底刃切削 1750
7950 -0.025--0.047 高速推荐侧刃切削
E10
高速涂层 4 寿命(min) 不提倡底刃切削
60
60 -0.025--0.047 高速推荐侧刃切削
E10
高速涂层 4 金属去除率 不提倡底刃切削 1.087
1500 -0.025--0.047 高速推荐侧刃切削
E2
高速涂层 4 S(转/min) 不提倡底刃切削 5500
13000 -0.025--0.047 高速推荐侧刃切削
E2
高速涂层 4 寿命(min) 不提倡底刃切削
50
60 -0.025--0.047 高速推荐侧刃切削
E2
高速涂层 4 金属去除率 不提倡底刃切削 0.783
E12
高速涂层 4 S(转/min) 不提倡底刃切削 2000
E12
高速涂层 4 寿命(min) 不提倡底刃切削
60
E12
高速涂层 4 金属去除率 不提倡底刃切削 1.566
1450 6600 60 6.26
-0.032--0.059 高速推荐侧刃切削 -0.032--0.059 高速推荐侧刃切削 -0.032--0.059 高速推荐侧刃切削 -0.032--0.059 高速推荐侧刃切削
4.35 -0.025--0.047 高速推荐侧刃切削
E12
高速涂层 4 aa(mm)
不提倡底刃切削 0.25-0.5
18 -0.032--0.059 高速推荐侧刃切削
E12
高速涂层 4 ar(mm)
不提倡底刃切削
加工中心刀具切削用量表

线速度(米/分钟) 铝 高速钢铣刀 镀层硬质合金铣刀 硬质合金铣刀
加工中心刀具切削用量表
45# 60 100~300 100~300
淬硬钢 15~20
60
铸铁 15~20
30
15~20 60 30
S(转速)=线速度×1000/(直径×3.14) F(进给量)=刃数×每刃切削量×转速
每刃切削量 粗加 ~ 0.05
例:20MM硬质合金4刃铣刀精铣45#钢,线速度取60。每刃切0.05。则转速=60×1000/(20×3.14) =955,进给量=4×0.05×955=191。
以上是比较笼统的概括,适用于大多数铣刀、钻头、镗刀(不包括绞刀)加工工艺的计算。在实 际加工中还要针对不同实际情况做出调整。如:工件形状、余量大小、冷却条件、刀具磨损等。
每刃切削量参数的选择:如果太小小于0.02,那不是在切削,是在磨刀,如果太大大于0.2,那也 不是切削,是在撞击。所以并非转速越高,进给量越小越好切削,刀具必须处在一个合理的运动 状态下,才是均质、稳定的切削。
刀具加工中,对刀具寿命影响最大的是线速度,刀具商提供刀具的同时,应该会提供一份刀具针 对各种材料的线速度表,但刀具供应商的参数是在理想状态下得到的,在实际加工中,得打个 7~8折的。
钨钢铣刀切削参数表【免费下载】

钨钢(硬质合金)具有硬度高、耐磨、强度和韧性较好、耐热、耐腐蚀等一系列优良性能,特别是它的高硬度和耐磨性,即使在500℃的温度下也基本保持不变,在1000℃时仍有很高的硬度。
钨钢铣刀常常被用于数控加工中心、CNC雕刻机,这种刀具硬度为维氏10K,仅次于钻石,但是即使再坚硬的刀具也是不可避免的会被磨损,从而导致使用寿命缩短,所以掌握钨钢铣刀切削参数对于加工厂来说很重要。
切削材料模具钢料(30≤硬度HRC≤40)刃径(d) 转速(S) 进刀(F) 切削量(H)1 16000 500 0.022 13000 1500-1800 0.044 12000 2500-2800 0.066 9000-10000 3000 0.088 8000 3000 0.110 6000 3000 0.112 5000 3500 0.12-0.15切削材料黄铜(硬度HRC≤30 铍铜硬度HRC35-42)刃径(d) 转速(S) 进刀(F) 切削量(H)1 16000 800-1000 0.03-0.052 14000 1800-2000 0.07-0.084 13000 2500 0.1-0.156 12000 2800-3000 0.38 8000 3000-3500 0.310 7000 3500 0.412 6500-7000 3500 0.4注解:1、以上参数是以高速加工中(主轴转速最高20000)的钨钢铣刀为准,它的表面硬度一般是HRC45-55(洛氏硬度)左右。
2 、平铣刀和圆铣刀(球刀)切削参数差不多,都可以参考上表。
3 、高速加工中一般用来加工一些比较小的零件和产品,所以它使用的刀具比较小,而且很少使用“飞刀”,也即合金铣刀。
4 、高速加工的理念就是:转速高,切削快,切削量少。
5、平时所说的钨钢一般指的就是硬质合金。
钨钢,又称为硬质合金,是指至少含有一种金属碳化物组成的烧结复合材料。
碳化钨,碳化钴,碳化铌、碳化钛,碳化钽是钨钢的常见组份。
FANUC高速、高精加工的参数调整
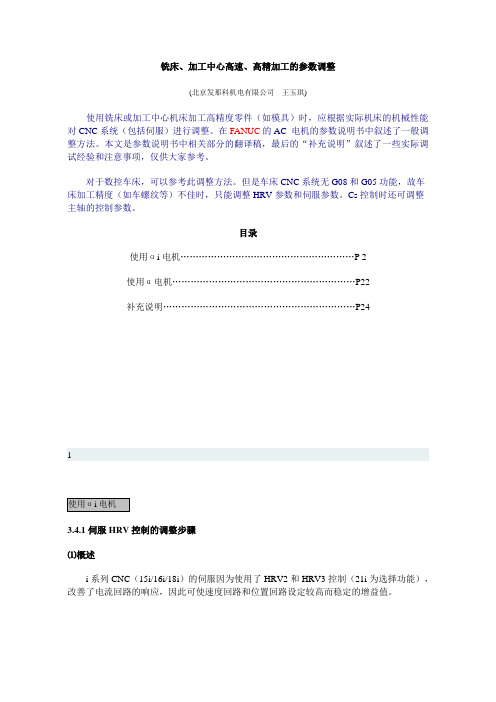
铣床、加工中心高速、高精加工的参数调整(北京发那科机电有限公司王玉琪)使用铣床或加工中心机床加工高精度零件(如模具)时,应根据实际机床的机械性能对CNC系统(包括伺服)进行调整。
在FANUC的AC 电机的参数说明书中叙述了一般调整方法。
本文是参数说明书中相关部分的翻译稿,最后的“补充说明”叙述了一些实际调试经验和注意事项,仅供大家参考。
对于数控车床,可以参考此调整方法。
但是车床CNC系统无G08和G05功能,故车床加工精度(如车螺纹等)不佳时,只能调整HRV参数和伺服参数。
Cs控制时还可调整主轴的控制参数。
目录使用αi电机…………………………………………………P 2使用α电机……………………………………………………P22补充说明………………………………………………………P2413.4.1伺服HRV控制的调整步骤⑴概述i系列CNC(15i/16i/18i)的伺服因为使用了HRV2和HRV3控制(21i为选择功能),改善了电流回路的响应,因此可使速度回路和位置回路设定较高而稳定的增益值。
图 3.4.1(a) 使用伺服HRV控制后的效果速度回路和位置回路的高增益,可以改善伺服系统的响应和刚性。
因此可以减小机床的加工形状误差,提高定位速度。
由于这一效果,使得伺服调整简化。
HRV2控制可以改善整个系统的伺服性能。
伺服用HRV2调整后,可以用HRV3改善高速电流控制,因此可进行高精度的机械加工。
若伺服HRV控制与CNC的预读(Look-ahead)控制,AI轮廓控制,AI纳米轮廓控制和高精度轮廓控制相结合,会大大改善加工性能。
关于这方面的详细叙述,请见3.4.3节“高速、高精加工的伺服参数调整”。
2图3.4.1(b) 伺服HRV控制的效果实例⑵适用的伺服软件系列号及版本号90B0/A(01)及其以后的版本(用于15i,16i,18i和21i,但必须使用320C5410伺服卡)。
⑶调整步骤概况HRV2和HRV3控制的调整与设定大致用以下步骤:①设定电流回路的周期和电流回路的增益(图3.4.3(c)中的*1 )电流回路的周期从以前的250μs降为125μs。
(完整版)加工中心新刀具常用切削参数参照表1
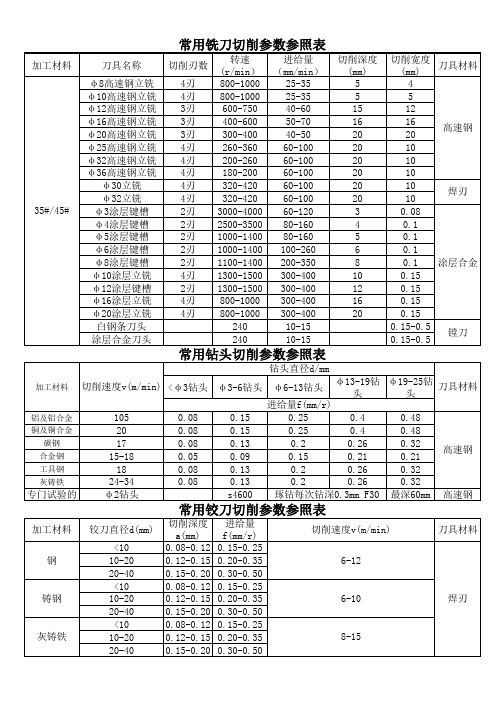
常用圆鼻刀切削参数参照表
加工材料 ZG275-485H
35#/45#
刀具名称
φ16圆鼻刀 φ20圆鼻刀 φ25圆鼻刀 φ25圆鼻刀 φ40圆鼻刀 φ40圆鼻刀 φ63圆鼻刀 φ63圆鼻刀 φ25圆鼻刀 φ32圆鼻刀 φ40圆鼻刀
用途
精加工 精加工 粗加工 精加工 粗加工 精加工 粗加工 精加工 粗加工 粗加工 粗加工
专门试验的
φ2钻头
s4600 琢钻每次钻深0.3mm F30 最深60mm 高速钢
常用铰刀切削参数参照表
加工材料 钢
铰刀直径d(mm)
<10 10-20
切削深度 进给量 a(mm) f(mm/r)
0.08-0.12 0.15-0.25 0.12-0.15 0.20-0.35
切削速度v(m/min) 6-12
2刃 1100-1400 200-350
8
0.1 0.1 涂层合金
φ10涂层立铣
4刃 1300-1500 300-400
10
0.15
φ12涂层键槽
2刃 1300-1500 300-400
12
0.15
φ16涂层立铣
4刃 800-1000 300-400
16
0.15
φ20涂层立铣
4刃 800-1000 300-400
800
60
800
20
700
50
400
60
400
80
120
40-50
120
40-50
用途
钻孔 扩孔 钻孔 钻孔 扩孔 精铰孔 精铰孔
切削宽度 (mm)
刀具材料
高速钢 合金 高速钢 高速钢 高速钢 合金 焊刃
加工中心钻直径12的孔,高速钢钻头,工件材料锡青铜,30厚,请问合理的转速,进给是多少?
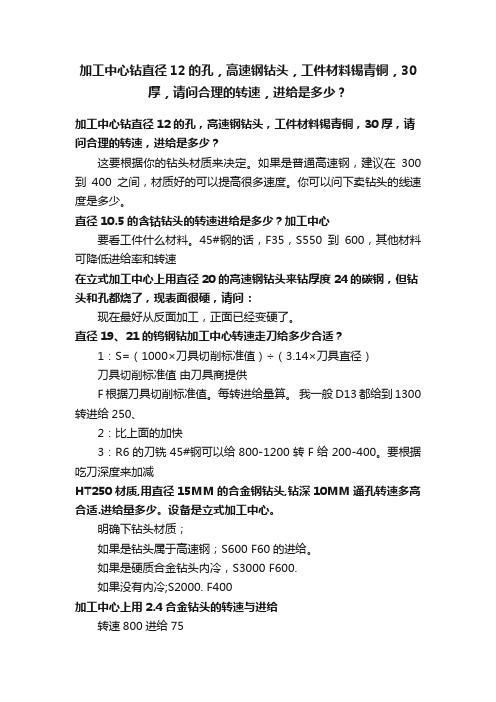
加工中心钻直径12的孔,高速钢钻头,工件材料锡青铜,30厚,请问合理的转速,进给是多少?加工中心钻直径12的孔,高速钢钻头,工件材料锡青铜,30厚,请问合理的转速,进给是多少?这要根据你的钻头材质来决定。
如果是普通高速钢,建议在300到400之间,材质好的可以提高很多速度。
你可以问下卖钻头的线速度是多少。
直径10.5的含钴钻头的转速进给是多少?加工中心要看工件什么材料。
45#钢的话,F35,S550到600,其他材料可降低进给率和转速在立式加工中心上用直径20的高速钢钻头来钻厚度24的碳钢,但钻头和孔都烧了,现表面很硬,请问:现在最好从反面加工,正面已经变硬了。
直径19、21的钨钢钻加工中心转速走刀给多少合适?1:S=(1000×刀具切削标准值)÷(3.14×刀具直径)刀具切削标准值由刀具商提供F根据刀具切削标准值。
每转进给量算。
我一般D13都给到1300转进给250、2:比上面的加快3:R6的刀铣45#钢可以给800-1200转F给200-400。
要根据吃刀深度来加减HT250材质,用直径15MM的合金钢钻头,钻深10MM通孔转速多高合适.进给量多少。
设备是立式加工中心。
明确下钻头材质;如果是钻头属于高速钢;S600 F60的进给。
如果是硬质合金钻头内冷,S3000 F600.如果没有内冷;S2000. F400加工中心上用2.4合金钻头的转速与进给转速800进给75用钻工中心,1.45的钻头钻孔,材料是紫铜,进给和转速,Q值给多少啊!请参考一下数值:Q值给0.1~0.3,F值150~220钻头直径(Dc)=1.45切削速度(vc)=50主轴转速(n)=10976每转进给(fn)=0.02在加工中心8.5麻花钻头转速与进给?40Cr材料选择切削参数的依据为:刀具材料、被加工材料、加工要求、加工环境。
其中刀具材料、被加工材料为主要因素,你缺刀具材料条件。
工件转,钻头不转,打侧孔,钻头直径3.1,转速和进给怎么算啊3.1的钻头可用2500-3000转以内——也就是在这个数值以下都行。
FANUC高速高精加工的参数调整

F A N U C高速高精加工的参数调整This manuscript was revised by the office on December 22, 2012铣床、加工中心高速、高精加工的参数调整(北京发那科机电有限公司王玉琪)使用铣床或加工中心机床加工高精度零件(如模具)时,应根据实际机床的机械性能对CNC系统(包括伺服)进行调整。
在FANUC的AC 电机的参数说明书中叙述了一般调整方法。
本文是参数说明书中相关部分的翻译稿,最后的“补充说明”叙述了一些实际调试经验和注意事项,仅供大家参考。
对于数控车床,可以参考此调整方法。
但是车床CNC系统无G08和G05功能,故车床加工精度(如车螺纹等)不佳时,只能调整HRV参数和伺服参数。
Cs控制时还可调整主轴的控制参数。
目录1伺服HRV控制的调整步骤⑴概述i系列CNC(15i/16i/18i)的伺服因为使用了HRV2和HRV3控制(21i为选择功能),改善了电流回路的响应,因此可使速度回路和位置回路设定较高而稳定的增益值。
图使用伺服HRV控制后的效果速度回路和位置回路的高增益,可以改善伺服系统的响应和刚性。
因此可以减小机床的加工形状误差,提高定位速度。
由于这一效果,使得伺服调整简化。
HRV2控制可以改善整个系统的伺服性能。
伺服用HRV2调整后,可以用HRV3改善高速电流控制,因此可进行高精度的机械加工。
若伺服HRV控制与CNC的预读(Look-ahead)控制,AI轮廓控制,AI纳米轮廓控制和高精度轮廓控制相结合,会大大改善加工性能。
关于这方面的详细叙述,请见节“高速、高精加工的伺服参数调整”。
2图伺服HRV控制的效果实例⑵适用的伺服软件系列号及版本号90B0/A(01)及其以后的版本(用于15i,16i,18i和21i,但必须使用320C5410伺服卡)。
⑶调整步骤概况HRV2和HRV3控制的调整与设定大致用以下步骤:①设定电流回路的周期和电流回路的增益(图中的*1 )电流回路的周期从以前的250μs降为125μs。
加工中心钻头钻孔参数【免费下载】

以下为加工中心钻头钻孔参数,一起来了解一下吧。
扩展资料:加工中心高效钻孔:相对于数控加工中心的表面加工,孔加工要复杂的多,加工孔也要比加工内外表面更为困难。
虽然如此,钻孔加工依然是数控加工中心最为常用的加工方式之一。
采购加工中心作为加工设备的话,孔加工的方法技巧一定要烂熟于心。
数控加工中心常见的孔加工方式主要有:钻孔、绞孔、镗孔、拉孔等,其中钻孔和铰孔最为常用,这两种工艺几乎每个制造车间,生产厂家都可以应用到。
以小型高精的vmc650加工中心为例,钻孔、铰孔的工艺技巧需要重点掌握。
钻孔:钻孔之所以最为常用,那是因为这是在实心材料上加工孔的第一道工序。
钻孔加工有两种方式:一种是钻头旋转;另一种是工件旋转。
钻孔直径一般小于80mm,精度和准确度要求较高。
而两种钻孔方式产生的误差是不相同的。
在钻头旋转的钻孔方式中,由于切削刃不对称和钻头刚性不足而使钻头引偏时,被加工孔的中心线会发生偏斜或不直,但孔径基本不变;而在工件旋转的钻孔方式中则相反,钻头引偏会引起孔径变化,而孔中心线仍然是直的。
常用钻孔刀具有:麻花钻、中心钻、深孔钻等,VMC850加工中心最配备的是麻花钻。
铰孔:铰孔是孔的精加工方法之一,在生产中应用很广。
铰孔余量对铰孔质量的影响很大,余量太大,铰刀的负荷大,切削刃很快被磨钝,不易获得光洁的加工表面,尺寸公差也不易保证;余量太小,不能去掉上工序留下的刀痕,自然也就没有改善孔加工质量的作用。
一般粗铰余量取为0.35~0.15mm,精铰取为01.5~0.05mm。
铰孔时必须用适当的切削液进行冷却、润滑和清洗,以防止产生积屑瘤并及时清除切屑。
与磨孔和镗孔相比,铰孔生产率高,容易保证孔的精度;但铰孔不能校正孔轴线的位置误差,孔的位置精度应由前工序保证。
VMC850加工中心具有完备的切削冷却系统可以完美解决铰孔工艺,但是铰孔不宜加工阶梯孔和盲孔。
t-v850加工中心的主要技术参数

t-v850加工中心的主要技术参数一、机床性能参数1. X/Y/Z轴行程:850/500/500mm2. 主轴转速:xxxrpm3. 主轴功率:15kW4. 主轴锥度:BT405. 工作台尺寸:1000*500mm6. 最大工件负载:700kg7. 快速进给速度:36/36/36m/min8. 切削进给速度:1-xxxmm/min9. 定位精度:±0.005/300mm10. 重复定位精度:±0.002mm二、主要标准配置1. 三轴直线导轨2. 三轴高速伺服马达3. 铸铁机床床身4. 安装在刚性机床床身上的高速主轴5. 宽大工作台6. 加强型刀库7. 宽大的工作台8. 台湾PMI滚珠丝杠与直线导轨三、可选配置1. 4轴/5轴转台2. 数控旋转头3. 高速刚性刀库4. 冷却系统5. 刀具长度检测装置6. 高压冷却系统7. 自动工件测量系统四、适用行业1. 适用于模具制造2. 适用于汽车零部件加工3. 适用于航空航天零部件加工4. 适用于通用工程机械零部件加工5. 适用于3C电子零部件加工五、机床优势1. 采用铸铁机床床身,刚性好,稳定性强2. 高速主轴可满足精密加工需求3. 宽大的工作台适用于大型工件加工4. 可选配置丰富,满足不同加工需求5. 适用行业广泛,市场需求大六、使用效果1. 高速主轴与高速伺服马达配合,加工效率高2. X/Y/Z三轴行程大,适用范围广3. 定位精度高,加工精度高4. 机床稳定性强,使用寿命长5. 高效率、高精度、稳定可靠七、结语t-v850加工中心作为一款高性能、高稳定性的数控加工设备,具有较为优秀的加工能力和适用范围。
其主要技术参数的稳定可靠性能,可靠的刚性机床床身和高速主轴的优势,使其在模具制造、汽车零部件加工、航空航天零部件加工等行业得到了广泛的应用。
在未来的市场竞争中,t-v850加工中心有着广阔的发展前景,有望成为行业内的领先产品。
t-v850加工中心是一款性能优异、稳定可靠的数控加工设备,具有出色的加工能力和广泛的适用范围。
加工中心切削参数

加工中心.数控铣床.刀具名称.转速进给、下刀量例:立铣刀必备知识(按照加工45号钢材)刀具名称、转速(/min)、进给(mm/min)、下刀量(mm) 63R6(刀片) 600 2500-3000 0.6-150R6(刀片) 650-850 2500-3000 0.55-0.7 25R5(刀片) 1200 2000-2500 0.45-0.55 32R6(刀片) 700-1200 2000-2500 0.5-0.65 16R0.8(刀片) 2000-2500 2000-3000 0.25-0.35 16R4(刀片) 2200-2500 2200-3000 0.3-0.4 16(球头刀 2000-2500 2000 0.25-0.35 12(球头刀 2200-2500 2000-3000 0.2510(球头刀 2500 1800-2000 0.2-0.25 8(球头刀 2500-2800 1500-1800 0.26(球头刀 4000 1500-1800 0.1-0.2 4(球头刀 5000-6000 1800 0.13(球头刀 7000 1500-1800 0.05-0.08 2(球头刀 12000 1500-2000 0.05-0.08 1.5(球头刀 16000 1200-1500 0.051(球头刀 20000 1200 0.050.5(球头刀 20000 500 0.023.175(球头刀 7000 1500 0.0830R5(平底立铣) 720-1000 2000-3000 0.3-0.540(平底立铣) 300-600 2000-2500 1.0-2.020(平底立铣) 600-1000 2000-2500 1.0-2.016(平底立铣) 1600 2000-2500 0.3-0.412(平底立铣) 2000-2200 2000-2500 0.25-0.3510(平底立铣) 2200-2500 2000-2500 0.25-0.38(平底立铣) 2500 1500-2000 0.2-0.36(平底立铣) 3000 1500-2000 0.15-0.24(平底立铣) 3500-4000 1500-2000 0.13(平底立铣) 6000 1500-1800 0.08-0.12(平底立铣) 9000 1500 0.05-0.081.5(平底立铣) 12000 1200-1500 0.05-0.081(平底立铣) 18000 1000-1500 0.03-0.05铣刀大体上分为:1.平头铣刀.进行粗铣.去除大量毛坯.小面积水平平面或者轮廓精铣2.球头铣刀.进行曲面半精铣和精铣.小刀可以精铣陡峭面/直壁的小倒角。
切削量实验报告结果(3篇)

第1篇一、实验目的本次实验旨在探究切削参数(切削深度、进给量、切削速度)对切削量(切削力、切削温度、表面粗糙度)的影响,为实际生产中切削参数的优化提供理论依据。
二、实验内容与方法1. 实验设备:高速切削实验台、电主轴、刀具、测力仪、温度计、表面粗糙度仪等。
2. 实验材料:45号钢。
3. 实验参数:- 切削深度:0.5mm、1.0mm、1.5mm- 进给量:0.2mm/r、0.4mm/r、0.6mm/r- 切削速度:300m/min、400m/min、500m/min4. 实验方法:- 将45号钢材料固定在高速切削实验台上,调整切削参数。
- 使用刀具进行切削实验,记录切削力、切削温度、表面粗糙度等数据。
- 对比不同切削参数下切削量的变化规律。
三、实验结果与分析1. 切削力:实验结果表明,切削力随切削深度、进给量的增加而增大,随切削速度的增加而减小。
在相同切削参数下,切削深度对切削力的影响最为显著。
2. 切削温度:实验结果表明,切削温度随切削深度、进给量的增加而升高,随切削速度的增加而降低。
在相同切削参数下,切削深度对切削温度的影响最为显著。
3. 表面粗糙度:实验结果表明,表面粗糙度随切削深度、进给量的增加而增大,随切削速度的增加而减小。
在相同切削参数下,切削速度对表面粗糙度的影响最为显著。
四、结论1. 切削力、切削温度、表面粗糙度均受到切削参数的影响,其中切削深度的影响最为显著。
2. 在实际生产中,应根据工件材料、加工要求等因素,合理选择切削参数,以获得最佳的切削效果。
3. 高速切削技术具有切削速度高、切削力小、切削温度低等优点,有利于提高加工效率、降低生产成本。
五、实验总结本次实验通过探究切削参数对切削量的影响,为实际生产中切削参数的优化提供了理论依据。
实验结果表明,切削深度、进给量、切削速度对切削力、切削温度、表面粗糙度具有显著影响。
在实际生产中,应根据工件材料、加工要求等因素,合理选择切削参数,以获得最佳的切削效果。
加工中心新刀具常用切削参数参照表1

8 8
120-150 120-150
20-30 20-25
半精铣T型 粗精槽铣T型
槽
焊刃 焊刃
φ68-72/T型刀
8
120-150
20-25 粗铣T型槽
焊刃
铸铁/滑块 φ68-72/T型刀 φ68-72/T型刀
8 8
120-150 120-150
30-45 30-40
半精铣T型 粗精槽铣T型
槽
焊刃 焊刃
400-600 300-400
50-70 40-50
16 20
16 20
高速钢
φ25高速钢立铣 4刃
260-360
60-100
20
10
φ32高速钢立铣 4刃
200-260
60-100
20
10
φ36高速钢立铣 4刃
180-200
60-100
20
10
φ30立铣
4刃
320-420
60-100
20
φ32立铣
专门试验的
φ2钻头
s4600 琢钻每次钻深0.3mm F30 最深60mm 高速钢
常用铰刀切削参数参照表
加工材料 钢
铰刀直径d(mm)
<10 10-20
切削深度 进给量 a(mm) f(mm/r)
0.08-0.12 0.15-0.25 0.12-0.15 0.20-0.35
切削速度v(m/min) 6-12
800
60
800
20
700
50
400
60
400
80
120
40-50
120
40-50
用途
钻孔 扩孔 钻孔 钻孔 扩孔 精铰孔 精铰孔
FANUC发那科+高速、高精加工的参数调整

高速、高精加工的参数调整使用αi电机3.4.1伺服HRV控制的调整步骤⑴ 概述i系列CNC(15i/16i/18i)的伺服因为使用了HRV2和HRV3控制(21i为选择功能),改善了电流回路的响应,因此可使速度回路和位置回路设定较高而稳定的增益值。
图 3.4.1(a) 使用伺服HRV控制后的效果速度回路和位置回路的高增益,可以改善伺服系统的响应和刚性。
因此可以减小机床的加工形状误差,提高定位速度。
由于这一效果,使得伺服调整简化。
HRV2控制可以改善整个系统的伺服性能。
伺服用HRV2调整后,可以用HRV3改善高速电流控制,因此可进行高精度的机械加工。
若伺服HRV控制与CNC的预读(Look-ahead)控制,AI轮廓控制,AI纳米轮廓控制和高精度轮廓控制相结合,会大大改善加工性能。
关于这方面的详细叙述,请见3.4.3节“高速、高精加工的伺服参数调整”。
图 3.4.1(b) 伺服HRV控制的效果实例⑵ 适用的伺服软件系列号及版本号90B0/A(01)及其以后的版本(用于15i,16i,18i和21i,但必须使用320C5410伺服卡)。
⑶ 调整步骤概况HRV2和HRV3控制的调整与设定大致用以下步骤:①设定电流回路的周期和电流回路的增益(图 3.4.3(c)中的*1 )电流回路的周期从以前的250μs降为125μs。
电流响应的改善是伺服性能改善的基础。
②速度回路增益的设定(图3.4.3(c)中的*2 )进行速度回路增益的调整时,对于速度回路的高速部分,应该使用速度环比例项的高速处理功能。
电流环控制周期时间的降低使电流响应得以改善,使用振荡抑制滤波器使可消除机械的谐振,这样可提高速度回路的振荡极限。
③ 消振滤波器的调整(图3.4.3(c)中的*3)机床可在某个频率下产生谐振。
此时,用消振滤波器消除某一频率下的振荡是非常有效的。
④ 精细加/减速的设定(图3.4.3(c)中的*4)当伺服系统的响应较高时,可能会出现加工的形状误差取决于CNC指令的扰动周期的现象。
三菱系统加工中心G指令M指令一览表

G00 快速定位G01直线补间切削G02 圆弧补间切削CW(顺时针)G03圆弧补间切削C CW(逆时针)G02.3 指数函数补间正转G03.3指数函数补间逆转G04暂停G05 高速高精度制御1G05.1 高速高精度制御2G06~G08没有G07.1/107 圆筒补间G09正确停止检查G10 程式参数输入/补正输入G11 程式参数输入取消G12 整圆切削CWG13 整圆切削CCWG12.1/112 极坐标补间有效G13.1/113 极坐标补间取消G14没有G15极坐标指令取消G16 极坐标指令有效G17 平面选择X-YG18 平面选择 Y-ZG19平面选择 X-ZG20英制指令G21 公制指令G22-G26没有G27参考原点检查G28 参考原点复归G29 开始点复归G30第2~4参考点复归G30.1复归刀具位置1G30.2 复归刀具位置2G30.3 复归刀具位置3G30.4复归刀具位置4G30.5 复归刀具位置5G30.6复归刀具位置6G31跳跃机能G31.1 跳跃机能1G31.2 跳跃机能2G31.3 跳跃机能3G32没有G33 螺纹切削G34特别固定循环(圆周孔循环)G35 特别固定循环(角度直线孔循环)G36特别固定循环(圆弧)G37 自动刀具长测定G37.1特别固定循环(棋盘孔循环)G38刀具径补正向量指定G39 刀具径补正转角圆弧补正G40 刀具径补正取消G41 刀具径补正左G42刀具径补正右G40.1法线制御取消G41.1法线制御左有效G42.1 法线制御右有效G43刀具长设定(+)G44 刀具长设定(—)G43.1第1主轴制御有效G44.1 第2主轴制御有效G45 刀具位置设定(扩张)G46刀具位置设定(缩小)G47 刀具位置设定(二倍)G48 刀具位置设定(减半)G47.1 2主轴同时制御有效G49 刀具长设定取消G50 比例缩放取消G51比例缩放有效G50.1 G指令镜象取消G51.1G指令镜象有效G52局部坐标系设定G53机械坐标系选择G54工件坐标系选择1G55工件坐标系选择2G56 工件坐标系选择3G57 工件坐标系选择4G58 工件坐标系选择5G59工件坐标系选择6G54.1 工件坐标系选择扩张48组G60 单方向定位G61正确停止检查模式G61.1 高精度制御G62自动转角进给率调整G63 攻牙模式G63.1 同期攻牙模式(正攻牙)G63.2 同期攻牙模式(逆攻牙)G64 切削模式G65 使用者巨集单一呼叫G66使用者巨集状态呼叫AG66.1 使用者巨集状态呼叫BG67使用者巨集状态呼叫取消G68 坐标回转有效G69坐标回转取消G70 使用者固定循环G71 使用者固定循环G72 使用者固定循环G73 固定循环(步进循环)G74 固定循环(反向攻牙)G75使用者固定循环G76固定循环(精搪孔)G77 使用者固定循环G78 使用者固定循环G79 使用者固定循环G80 固定循环取消G81固定循环(钻孔/铅孔)G82固定循环(钻孔/计数式搪孔)G83 固定循环(深钻孔)G84 固定循环(攻牙)G85固定循环(搪孔)G86固定循环(搪孔)G87 固定循环(反搪孔)G88 固定循环(搪孔)G89固定循环(搪孔)G90绝对值指令G91 增量值指令G92 机械坐标系设定G93 逆时间进给G94非同期进给(每分进给)G95 同期进给(每回转进给)G96 周速一定制御有效G97周速一定至于取消G98 固定循环起始点复归G99固定循环 R点复归G114.1 主轴同期制御G100~225 使用者巨集(G码呼叫)最大10个M00 程式停止(暂停)M01 程式选择性停止/选择性套用 M02程序结束M03 主轴正转M04 主轴反转M05主轴停止M06 自动刀具交换M07 吹气启动M08 切削液启动M09切削液关闭M10 吹气关闭→M09也能关吹气M11《斗笠式》主轴夹刀M12主轴松刀M13 主轴正转+切削液启动M14主轴反转+切削液启动M15 主轴停止+切削液关闭M16— M18没有 M19主轴定位M20 ——没有 M21 X轴镜象启动M22 Y轴镜象启动M23 镜象取消 M24第四轴镜象启动 M25第四轴夹紧M26 第四轴松开M27分度盘功能M28 没有 M29刚性攻牙M30 程式结束/自动断电M31 —— M47没有 M48深钻孔启动M49 —— M51没有M52 刀库右移M53刀库左移M54 —— M69没有 M70自动刀具建立M71 刀套向下M72换刀臂60° M73主轴松刀M74 换刀臂180°M75 主轴夹刀M76 换刀臂0°M77 刀臂向上M78 —— M80没有 M81工作台交换确认 M82工作台上M83 工作台下M84 工作台伸出M85 工作台缩回 M86工作台门开M87 工作台门关M88——M97 没有M98 调用子程序M99子程序结束。
数控加工参数表

数控加工参数表 The manuscript was revised on the evening of 2021一、主轴转速n(r/min)主轴转速一般根据切削速度V来选定,计算公式为:n=1000V/(π×d)式中,d为刀具直径(mm),V为刀具切削速度(m/min)。
对于球头铣刀,工作直径要小于刀具直径,故其实际转速应大于计算转速n。
表1铣刀的切削速度V(单位:m/min)二、进给速度V f (mm/min)Vf = fz×z×n式中n为主轴转速,z为铣刀齿数,f z为每齿进给量(mm/齿).每齿进给量fz的选取主要取决于工件材料的力学性能、刀具材料、工件表面粗糙度等因素。
工件材料的强度和硬度越高,f z越小;反之则越大。
硬质合金铣刀的每齿进给量高于同类高速钢铣刀。
工件表面粗糙度要求越高,f z就越小。
1.铣削加工表2 铣刀每齿进给量f z (单位:mm/齿)2.镗削加工表3 镗孔切削用量3、攻螺纹攻螺纹前底孔直径的确定:攻米制螺纹螺距P<1mm:d0=d-PP>1mm:d0=d-(~)P式中P —螺距(mm)d0 —钻头直径(mm)d—螺纹公称直径(mm)攻不通孔螺纹钻孔深度=所需螺孔深度- d表4 攻普通螺纹前的底孔直径表5 攻英制螺纹前的底孔直径表6 攻螺纹切削速度(单位:m/min)4、钻孔加工表7 用高速钢钻头钻孔切削用量(f单位:mm/r)5、铰孔加工铰孔属于精加工工序,加工过程中应合理选择铰刀的类型及材质,高速钢铰刀属于通用铰刀,硬质合金铰刀一般用于加工钢、铸钢、灰铸铁和冷硬铸铁。
为了达到较高的孔径精度和表面质量,应采用较低的切削速度和进给量并合理选择切削液。
铰孔前应留有铰削余量,一般为~底孔直径=铰刀直径-(~)mm铰削加工时切削速度V取3~15m/min进给量f取~r注意:在正式加工之前应试铰,并检验孔径及粗糙度是否符合要求。
三、切削液的选择注:以上各表是加工中心和数控铣床常用的加工参数,供参考。
- 1、下载文档前请自行甄别文档内容的完整性,平台不提供额外的编辑、内容补充、找答案等附加服务。
- 2、"仅部分预览"的文档,不可在线预览部分如存在完整性等问题,可反馈申请退款(可完整预览的文档不适用该条件!)。
- 3、如文档侵犯您的权益,请联系客服反馈,我们会尽快为您处理(人工客服工作时间:9:00-18:30)。
刀具直径 E63R6 E63R6 E63R6 E63R6 E63R6 E63R6 E63R6 E63R6 E63R6 E63R6 E63R6 E63R6 E63R6 E63R6 E63R6 E63R6 E63R6 E63R6
种类 飞刀 飞刀 飞刀 飞刀 飞刀 飞刀 飞刀 飞刀 飞刀 飞刀 飞刀 飞刀 飞刀 飞刀 飞刀 飞刀 飞刀 飞刀
粗加工 0.8-2 36 1800 700-1000 4800 72 0.6 36 1800 1000 4800 72 0.5 36 800 1000 4800 72
精加工 0.3 0.5 1400 1400 600 0.225 0.3 0.5 1400 1200 600 0.225 0.3 0.5 1000 1200 0.225
种类 飞刀 飞刀 飞刀 飞刀 飞刀 飞刀 飞刀 飞刀 飞刀 飞刀 飞刀 飞刀 飞刀 飞刀 飞刀 飞刀 飞刀 飞刀 飞刀 飞刀 飞刀 飞刀 飞刀 飞刀
参数 2 2 2 2 2 2 2 2 2 2 2 2 2 2 2 2 2 2 普通 普通 普通 普通 普通 普通
切削参数 aa(mm) ar(mm) F(mm/min) S(转/min) 寿命(min) 金属去除率 aa(mm) ar(mm) F(mm/min) S(转/min) 寿命(min) 金属去除率 aa(mm) ar(mm) F(mm/min) S(转/min) 寿命(min) 金属去除率 aa(mm) ar(mm) F(mm/min) S(转/min) 寿命(min) 金属去除率
刀具直径 E25R0.8 E25R0.8 E25R0.8 E25R0.8 E25R0.8 E25R0.8 E32R0.8 E32R0.8 E32R0.8 E32R0.8 E32R0.8 E32R0.8 E25R5 E25R5 E25R5 E25R5 E25R5 E25R5 E32R6 E32R6 E32R6 E32R6 E32R6 E32R6
粗加工参数指材料 硬度在HRC30-86, 对于低于此硬度的 材料,切深可增大
粗加工参数指材料 硬度在HRC30-50, 对于低于此硬度的 材料,切深可增大
刀具悬伸长度 刀长在150以下 刀长在150以下 刀长在150以下 刀长在150以下 刀长在150以下 刀长在150以下 刀长在200以下 刀长在200以下 刀长在200以下 刀长在200以下 刀长在200以下 刀长在200以下 刀长在100以下 刀长在100以下 刀长在100以下 刀长在100以下 刀长在100以下 刀长在100以下 刀长在150以下 刀长在150以下 刀长在150以下 刀长在150以下 刀长在150以下 刀长在150以下
粗加工 0.5 8 1000 3200 60 \ 0.5 10 1000 3000 60 \ 0.5 13 900 2500 60 \ 0.5 17 1000 2200 60 \
精加工 0.2 0.2 1000 3200 \ \ 0.2 0.2 1000 3000 120 \ 0.2 0.2 1800 3000 120 \ 0.2 0.2 1800 2500 120 \
粗加工参数指材料 硬度在HRC30-50, 对于低于此硬度的 材料,切深可增大
粗加工参数指材料 硬度在HRC30-50, 对于低于此硬度的 材料,切深可增大
刀具悬伸长度 刀长在50以下 刀长在50以下 刀长在50以下 刀长在50以下 刀长在50以下 刀长在50以下 刀长在60以下 刀长在60以下 刀长在60以下 刀长在60以下 刀长在60以下 刀长在60以下 刀长在90以下 刀长在90以下 刀长在90以下 刀长在90以下 刀长在90以下 刀长在90以下 刀长在130以下 刀长在130以下 刀长在130以下 刀长在130以下 刀长在130以下 刀长在130以下
刀具直径 E10R0.8 E10R0.8 E10R0.8 E10R0.8 E10R0.8 E10R0.8 E12R0.8 E12R0.8 E12R0.8 E12R0.8 E12R0.8 E12R0.8 E16R0.8 E16R0.8 E16R0.8 E16R0.8 E16R0.8 E16R0.8 E20R0.8 E20R0.8 E20R0.8 E20R0.8 E20R0.8 E20R0.8
粗加工 0.5 22 1200 2000 60 \ 0.5 29 1500 2000 60 \ 0.4 14 2000 2000 11.2 0.8 25 2000 2000 480 64
精加工 0.2 0.2 1800 2300 120 \ 0.2 0.2 2000 2200 120 \ 0.25 0.3 2000 2200 240 \ 0.1-0.5 0.1-0.5 2000 2200 0.21
刀具悬伸长度 刀长在160以下 刀长在160以下 刀长在160以下 刀长在160以下 刀长在160以下 刀长在160以下 刀长160-250 刀长160-250 刀长160-250 刀长160-250 刀长160-250 刀长160-250 刀长250-350 刀长250-350 刀长250-350 刀长250-350 刀长250-350 刀长250-350
粗加工参数指材料 硬度在HRC30-50, 对于低于此硬度的 材料,切深可增大
粗加工参数指材料 硬度在HRC30-50, 对于低于此硬度的 材料,切深可增大
刀具悬伸长度 刀长在200以下 刀长在200以下 刀长在200以下 刀长在200以下 刀长在200以下 刀长在200以下 刀长在160以下 刀长在160以下 刀长在160以下 刀长在160以下 刀长在160以下 刀长在160以下 刀长160-250 刀长160-250 刀长160-250 刀长160-250 刀长160-250 刀长160-250 刀长250-350 刀长250-350 刀长250-350 刀长250-350 刀长250-350 刀长250-350
平面加工 0.2 50 500 1200 \ \ 0.2 50 500 1200 \ \ 0.2 50 500 1200 \ \
备注
粗加工参数指材料 硬度在HRC30-50, 对于低于此硬度的 材料,切深可增大
粗加工参数指材料 硬度在HRC30-50, 对于低于此硬度的 材料,切深可增大
粗加工参数指材料 硬度在HRC30-50, 对于低于此硬度的 材料,切深可增大
参数 普通 普通 普通 普通 普通 普通 普通 普通 普通 普通 普通 普通 普通 普通 普通 普通 普通 普通 普通 普通 普通 普通 普通 普通
切削参数 aa(mm) ar(mm) F(mm/min) S(转/min) 寿命(min) 金属去除率 aa(mm) ar(mm) F(mm/min) S(转/min) 寿命(min) 金属去除率 aa(mm) ar(mm) F(mm/min) S(转/min) 寿命(min) 金属去除率 aa(mm) ar(mm) F(mm/min) S(转/min) 寿命(min) 金属去除率
平面加工 0.2 32 800 1800 \ \ 0.2 40 500 1400 \ \ 0.2 40 500 1400 \ \ 0.2 40 500 1400 \ \
备注
粗加工参数指材料 硬度在HRC30-50, 对于低于此硬度的 材料,切深可增大
粗加工参数指材料 硬度在HRC30-50, 对于低于此硬度的 材料,切深可增大
平面加工 0.2 22 1000 2300 60 \ 0.2 29 1000 2200 60 \ 0.2 14 500 2000 \ \ 0.2 25 700 2000 \ \
备注
粗加工参数指材料 硬度在HRC30-50, 对于低于此硬度的 材料,切深可增大
粗加工参数指材料 硬度在HRC30-50, 对于低于此硬度的 材料,切深可增大
粗加工 0.8 33 2000 2000 480 64 0.8-2 30 2000 800-950 480 64 0.6 30 1800 950 480 64 0.5 36.4 1200 950 480 64
精加工 0.1-0.5 0.1-0.5 2000 2000 0.21 0.3 0.5 1400 1200 0.21 0.3 0.5 1600 1400 600 0.24 0.3 0.5 1600 1400 600 0.24
种类 飞刀 飞刀 飞刀 飞刀 飞刀 飞刀 飞刀 飞刀 飞刀 飞刀 飞刀 飞刀 飞刀 飞刀 飞刀 飞刀 飞刀 飞刀 飞刀 飞刀 飞刀 飞刀 飞刀 飞刀
参数 2 2 2 2 2 2 2 2 2 2 2 2 2 2 2 2 2 2 2 2 2 2 2 2
切削参数 aa(mm) ar(mm) F(mm/min) S(转/min) 寿命(min) 金属去除率 aa(mm) ar(mm) F(mm/min) S(转/min) 寿命(min) 金属去除率 aa(mm) ar(mm) F(mm/min) S(转/min) 寿命(min) 金属去除率 aa(mm) ar(mm) F(mm/min) S(转/min) 寿命(min) 金属去除率
参数 普通 普通 普通 普通 普通 普通 普通 普通 普通 普通 普通 普通 普通 普通 普通 普通 普通 普通
切削参数 aa(mm) ar(mm) F(mm/min) S(转/min) 寿命(min) 金属去除率 aa(mm) ar(mm) F(mm/min) S(转/min) 寿命(min) 金属去除率 aa(mm) ar(mm) F(mm/min) S(转/min) 寿命(min) 金属去除率
刀具直径 E40R6 E40R6 E40R6 E40R6 E40R6 E40R6 E52R6 E52R6 E52R6 E52R6 E52R6 E52R6 E52R6 E52R6 E52R6 E52R6 E52R6 E52R6 E52R6 E52R6 E52R6 E52R6 E52R6 E52R6
种类 飞刀 飞刀 飞刀 飞刀 飞刀 飞刀 飞刀 飞刀 飞刀 飞刀 飞刀 飞刀 飞刀 飞刀 飞刀 飞刀 飞刀 飞刀 飞刀 飞刀 飞刀 飞刀 飞刀 飞刀