换热器一般设计要求
换热器的设计原则
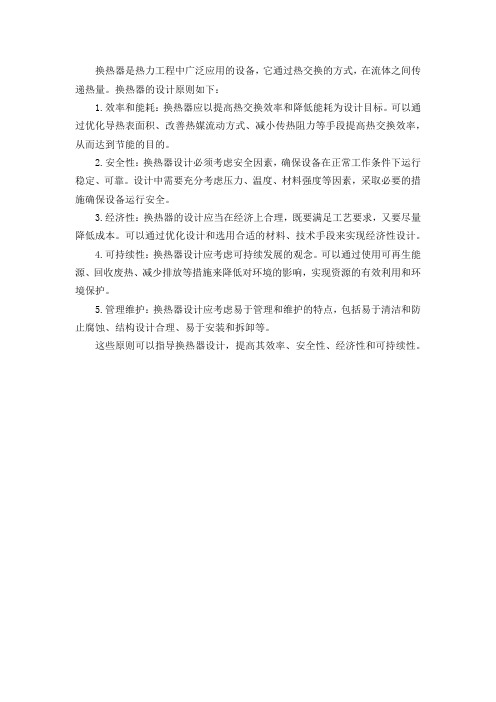
换热器是热力工程中广泛应用的设备,它通过热交换的方式,在流体之间传递热量。
换热器的设计原则如下:
1.效率和能耗:换热器应以提高热交换效率和降低能耗为设计目标。
可以通过优化导热表面积、改善热媒流动方式、减小传热阻力等手段提高热交换效率,从而达到节能的目的。
2.安全性:换热器设计必须考虑安全因素,确保设备在正常工作条件下运行稳定、可靠。
设计中需要充分考虑压力、温度、材料强度等因素,采取必要的措施确保设备运行安全。
3.经济性:换热器的设计应当在经济上合理,既要满足工艺要求,又要尽量降低成本。
可以通过优化设计和选用合适的材料、技术手段来实现经济性设计。
4.可持续性:换热器设计应考虑可持续发展的观念。
可以通过使用可再生能源、回收废热、减少排放等措施来降低对环境的影响,实现资源的有效利用和环境保护。
5.管理维护:换热器设计应考虑易于管理和维护的特点,包括易于清洁和防止腐蚀、结构设计合理、易于安装和拆卸等。
这些原则可以指导换热器设计,提高其效率、安全性、经济性和可持续性。
管壳式换热器的设计
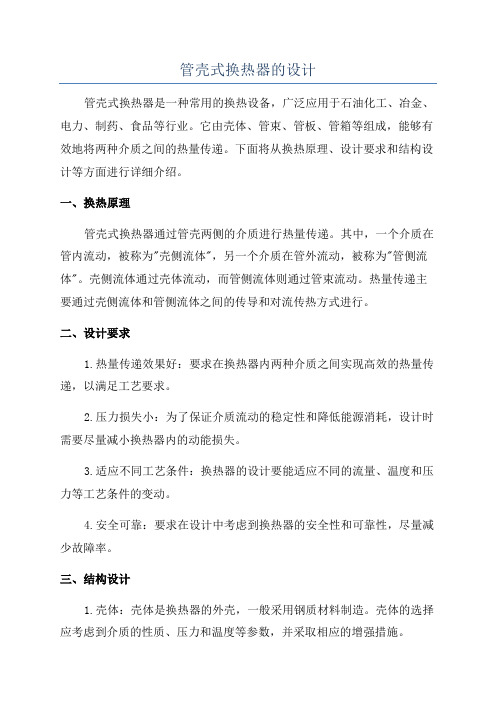
管壳式换热器的设计管壳式换热器是一种常用的换热设备,广泛应用于石油化工、冶金、电力、制药、食品等行业。
它由壳体、管束、管板、管箱等组成,能够有效地将两种介质之间的热量传递。
下面将从换热原理、设计要求和结构设计等方面进行详细介绍。
一、换热原理管壳式换热器通过管壳两侧的介质进行热量传递。
其中,一个介质在管内流动,被称为"壳侧流体",另一个介质在管外流动,被称为"管侧流体"。
壳侧流体通过壳体流动,而管侧流体则通过管束流动。
热量传递主要通过壳侧流体和管侧流体之间的传导和对流传热方式进行。
二、设计要求1.热量传递效果好:要求在换热器内两种介质之间实现高效的热量传递,以满足工艺要求。
2.压力损失小:为了保证介质流动的稳定性和降低能源消耗,设计时需要尽量减小换热器内的动能损失。
3.适应不同工艺条件:换热器的设计要能适应不同的流量、温度和压力等工艺条件的变动。
4.安全可靠:要求在设计中考虑到换热器的安全性和可靠性,尽量减少故障率。
三、结构设计1.壳体:壳体是换热器的外壳,一般采用钢质材料制造。
壳体的选择应考虑到介质的性质、压力和温度等参数,并采取相应的增强措施。
2.管束:管束是由多根管子组成的,一般采用金属材料或塑料制造。
管束的设计要考虑到介质对管材的腐蚀性、温度和压力等参数,同时也要考虑到换热面积的要求。
3.管板:管板位于管束两端,起到支撑和固定管束的作用,一般采用钢质材料制造。
管板的设计要考虑到壳侧和管侧流体的流动特性,并采用合适的孔洞布置,以保证流体的均匀流动。
4.管箱:管箱是安装在管板上的设施,主要用于集流壳侧流体并将其引导出换热器。
管箱的设计应考虑到壳侧流体的流动特性和流量等参数,以实现流体的顺畅流动。
在设计过程中,需要进行换热器的热力计算和结构力学计算,以确定壳体、管束和管板等部件的尺寸和选材。
同时,还需要根据不同工艺和使用条件的要求,进行热交换面积的计算和确定。
换热器的选型和设计指南全

换热器的选型和设计指南全
1.温度和压力要求:在进行换热器选型和设计之前,需要明确设备所
需的温度和压力要求。
根据这些要求,可以选择合适的材料和换热器类型。
2.热交换面积计算:根据需要传递的热量和温度差,可以计算得到所
需的热交换面积。
热交换面积的计算是选择换热器类型和尺寸的基础。
3.材料选择:换热器的材料选择要考虑到介质的化学性质、腐蚀性以
及温度和压力要求。
常用的材料包括不锈钢、铜合金、钛合金等。
4.流体流动方式:流体可以采用并行流、逆流或交叉流方式通过换热器。
在选择流体流动方式时,需要考虑换热效率和压降等因素。
5.清洁程度要求:根据介质的清洁程度,可以选择适当的换热器类型。
尽量选择结构简单、易于清洁的换热器,以保证长期稳定的换热效果。
6.管束和散热面积:根据热量传递的需要,可以选择合适的管束形式
和散热面积。
管束的选择要考虑到介质的流速和传热系数等因素。
7.防堵塞设计:在换热器设计中要考虑到防止堵塞的问题。
可以采用
增加管道直径、添加过滤装置等措施来减少堵塞的风险。
8.设备布局和管道设计:在进行换热器的设计时,需要考虑到设备的
布局和管道的连接。
合理布局可以减少管道阻力和热量损失。
9.热媒选择:热媒的选择要根据介质的性质以及工艺流程的要求来进行。
常用的热媒有水、蒸汽、有机液体等。
10.清洗和维护考虑:在进行换热器设计时,要考虑到清洗和维护的
便捷性。
合理的设计可以降低维护成本和停机时间。
板式换热器设计标准

板式换热器设计标准1. 引言板式换热器是一种常用的热交换设备,广泛应用于化工、石油、冶金、食品等行业。
板式换热器的设计标准对于确保设备的安全运行和高效传热至关重要。
本文将介绍板式换热器的设计标准及其要求。
2. 设计标准2.1 板式换热器的分类根据传热方式和结构特点,板式换热器可分为传统板式换热器、起泡器板式换热器、波纹板式换热器等几种类型。
不同类型的板式换热器具有不同的设计标准和要求。
2.2 设计原则板式换热器的设计应遵循以下原则:•确定换热器的传热面积和传热系数;•选择合适的流体流速;•确定板式换热器的结构参数,如板间距、板高度等;•确保换热器的压力临界条件;•确定板式换热器的材料和密封方式。
2.3 流体参数在板式换热器设计中,需明确各流体的流速、温度、压力等参数。
流体参数的选择应基于设备的工作条件、传热要求和流体特性。
2.4 热平衡板式换热器的设计应满足热平衡要求,即传热面积上的热量输入等于输出。
为了确保热平衡,设计中需考虑传热系数、流速、管道布局等因素。
3. 设计要求3.1 板式换热器的传热效率板式换热器的传热效率是评估设备性能的重要指标。
设计时,需保证传热效率达到要求,并有效避免传热表面的堆积和腐蚀。
3.2 设备的安全运行板式换热器的设计应保证设备在正常工况下的安全运行。
设计中需考虑压力、温度、流速等因素,以确保设备的安全稳定运行。
3.3 板式换热器的清洁和维护为了保证板式换热器的正常运行,设计时应考虑清洁和维护的便捷性。
合理的板间距设计和换热板结构可以减少杂质的积聚,便于清理和维护。
3.4 设备的节能性在板式换热器设计中,节能是一个重要目标。
合理选择流体参数、优化换热结构和提高传热系数等措施可以提高设备的节能性能。
4. 结论板式换热器的设计标准包括设备分类、设计原则、流体参数、热平衡等要求。
合理的设计标准可以提高设备的传热效率、安全稳定运行、清洁维护和节能性能。
在实际应用中,设计者应根据具体情况,综合考虑各种因素,确保设计符合相关的规范和标准,以达到预期的效果。
换热器设计方案
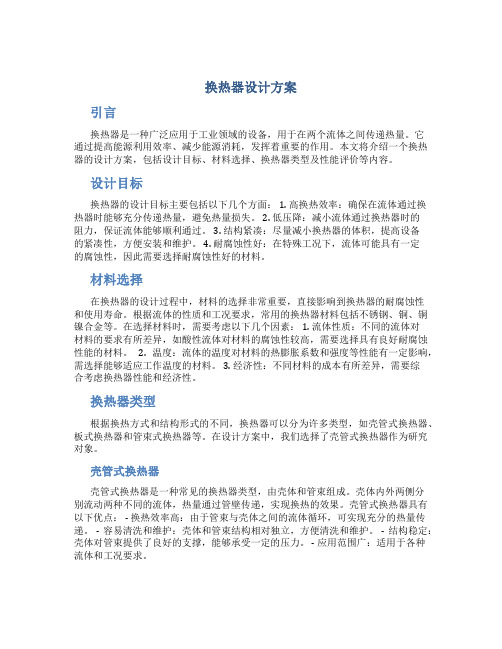
换热器设计方案引言换热器是一种广泛应用于工业领域的设备,用于在两个流体之间传递热量。
它通过提高能源利用效率、减少能源消耗,发挥着重要的作用。
本文将介绍一个换热器的设计方案,包括设计目标、材料选择、换热器类型及性能评价等内容。
设计目标换热器的设计目标主要包括以下几个方面: 1. 高换热效率:确保在流体通过换热器时能够充分传递热量,避免热量损失。
2. 低压降:减小流体通过换热器时的阻力,保证流体能够顺利通过。
3. 结构紧凑:尽量减小换热器的体积,提高设备的紧凑性,方便安装和维护。
4. 耐腐蚀性好:在特殊工况下,流体可能具有一定的腐蚀性,因此需要选择耐腐蚀性好的材料。
材料选择在换热器的设计过程中,材料的选择非常重要,直接影响到换热器的耐腐蚀性和使用寿命。
根据流体的性质和工况要求,常用的换热器材料包括不锈钢、铜、铜镍合金等。
在选择材料时,需要考虑以下几个因素: 1. 流体性质:不同的流体对材料的要求有所差异,如酸性流体对材料的腐蚀性较高,需要选择具有良好耐腐蚀性能的材料。
2. 温度:流体的温度对材料的热膨胀系数和强度等性能有一定影响,需选择能够适应工作温度的材料。
3. 经济性:不同材料的成本有所差异,需要综合考虑换热器性能和经济性。
换热器类型根据换热方式和结构形式的不同,换热器可以分为许多类型,如壳管式换热器、板式换热器和管束式换热器等。
在设计方案中,我们选择了壳管式换热器作为研究对象。
壳管式换热器壳管式换热器是一种常见的换热器类型,由壳体和管束组成。
壳体内外两侧分别流动两种不同的流体,热量通过管壁传递,实现换热的效果。
壳管式换热器具有以下优点: - 换热效率高:由于管束与壳体之间的流体循环,可实现充分的热量传递。
- 容易清洗和维护:壳体和管束结构相对独立,方便清洗和维护。
- 结构稳定:壳体对管束提供了良好的支撑,能够承受一定的压力。
- 应用范围广:适用于各种流体和工况要求。
性能评价换热器的性能评价主要包括换热效率和压降。
换热器的设计方案

换热器的设计方案1. 简介换热器是工业生产过程中常用的设备之一,用于在不同介质之间进行热量的传递和交换。
本文将介绍换热器的设计方案,包括选择材料、确定换热面积和流体参数等关键步骤。
2. 材料选择在进行换热器设计时,材料的选择是非常重要的。
一般来说,常用的换热器材料包括不锈钢、碳钢、铜、铝等。
选择材料时需要考虑以下几个因素:•耐腐蚀性:根据介质的性质选择能够抵抗腐蚀的材料,以确保换热器的使用寿命。
•导热性:选择具有良好导热性的材料,以提高换热效率。
•强度和硬度:根据工作条件确定材料的强度和硬度,以保证换热器的安全和可靠性。
3. 换热面积的确定换热面积是设计换热器时的关键参数,它直接影响换热器的热效率。
换热面积的确定需要考虑以下因素:•热传导:根据介质的热传导性质和需要传热的热量确定换热面积的大小。
•流体速度:流体速度越大,传热效果越好,因此需要根据流体速度确定换热面积。
•温差:温差越大,换热器的传热效果越好,因此需要根据温差确定换热面积。
4. 流体参数的确定在设计换热器时,需要确定流体的参数,包括流体的流速、流量和温度等。
这些参数直接影响换热器的性能和效果。
•流速:流体的流速越大,传热效果越好,因此需要根据具体情况确定流速。
•流量:根据需要传热的热量和换热器的热传导能力,确定流体的流量。
•温度:根据介质的温度要求和换热器的传热效果,确定流体的进出口温度。
5. 换热器类型的选择根据不同的工艺要求和介质特性,可以选择不同类型的换热器。
常见的换热器类型包括壳管换热器、板式换热器、管束换热器等。
在选择换热器类型时,需要考虑以下几个因素:•空间限制:根据工作场所的空间限制选择合适的换热器类型。
•介质性质:根据介质的流动性质和热传导性质选择合适的换热器类型。
•温度和压力:根据工艺要求和介质的温度和压力选择适应的换热器类型。
6. 换热器的安装和维护在设计换热器方案时,还需要考虑换热器的安装和维护问题。
换热器的安装需要确保换热器与管道的连接紧密可靠,以免出现泄漏等问题。
煤油换热器的设计方案

煤油换热器的设计方案一、引言二、设计要求与参数在设计煤油换热器之前,首先需要明确设计要求和相关参数。
这些参数通常包括:1、热流体(煤油)和冷流体的进出口温度、流量。
2、工作压力和允许压降。
3、换热器的使用环境和安装条件。
假设我们的设计参数如下:热流体(煤油)入口温度为 200°C,出口温度为 150°C,流量为1000 kg/h。
冷流体入口温度为 30°C,出口温度为 100°C,流量为 1500 kg/h。
工作压力为 16 MPa,允许压降为 01 MPa。
三、换热器类型选择常见的换热器类型有管壳式、板式、螺旋板式等。
考虑到煤油的性质和设计要求,管壳式换热器是较为合适的选择。
管壳式换热器具有结构坚固、适应性强、处理量大等优点,能够满足高温、高压和大流量的工况。
四、材料选择1、管材由于煤油具有一定的腐蚀性,因此选用不锈钢作为换热管的材料,如 304 不锈钢或 316L 不锈钢,以保证换热器的使用寿命和可靠性。
2、壳体材料壳体通常采用碳钢,如 Q235B 或 Q345R,以降低成本。
3、封头和管板封头和管板可选用与壳体相同的材料。
五、换热管布置1、管径和管长根据经验和传热计算,选择管径为 25mm,管长为 6m。
2、排列方式采用正三角形排列,以提高传热效率和紧凑度。
3、管间距管间距的选择应考虑清洗和传热效果,通常管间距为 32mm。
六、壳程结构设计1、壳体直径根据换热管的排列和数量,计算出壳体的直径。
2、折流板为了提高壳程流体的传热效果,设置折流板。
折流板间距根据壳程流体的流速和压降要求确定,一般为 300 500mm。
折流板的形状采用弓形,缺口高度为壳体内径的 20% 40%。
七、传热计算1、总传热系数计算根据所选的换热器类型、材料和流体的物性参数,计算总传热系数。
2、传热面积计算根据热负荷和总传热系数,计算所需的传热面积。
3、校核对计算得到的传热面积进行校核,确保满足设计要求。
换热器工装设计标准
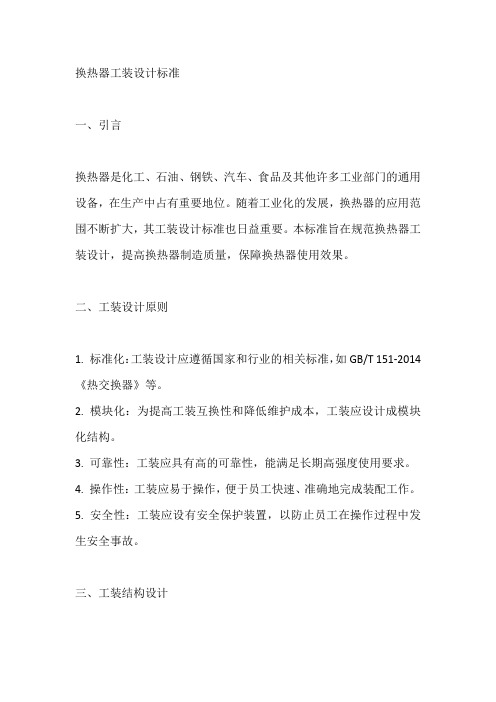
换热器工装设计标准一、引言换热器是化工、石油、钢铁、汽车、食品及其他许多工业部门的通用设备,在生产中占有重要地位。
随着工业化的发展,换热器的应用范围不断扩大,其工装设计标准也日益重要。
本标准旨在规范换热器工装设计,提高换热器制造质量,保障换热器使用效果。
二、工装设计原则1. 标准化:工装设计应遵循国家和行业的相关标准,如GB/T 151-2014《热交换器》等。
2. 模块化:为提高工装互换性和降低维护成本,工装应设计成模块化结构。
3. 可靠性:工装应具有高的可靠性,能满足长期高强度使用要求。
4. 操作性:工装应易于操作,便于员工快速、准确地完成装配工作。
5. 安全性:工装应设有安全保护装置,以防止员工在操作过程中发生安全事故。
三、工装结构设计1. 定位装置:工装应设有精确的定位装置,以确保换热器零部件的定位精度。
2. 夹紧装置:工装应设有可靠的夹紧装置,以保持换热器零部件的位置稳定。
3. 导向装置:对于需要导向的装配过程,工装应设有导向装置,以帮助员工准确、快速地完成装配。
4. 支撑装置:对于重量较大或形状复杂的换热器零部件,工装应设有支撑装置,以方便员工操作。
5. 防护装置:工装应设有防护装置,以防止换热器零部件在装配过程中受损。
四、工装材料选择1. 耐腐蚀性:工装材料应具有较好的耐腐蚀性,以适应换热器工作环境中的腐蚀性物质。
2. 强度:工装材料应具有足够的强度,以承受换热器零部件的重量和压力。
3. 耐磨性:工装材料应具有较好的耐磨性,以抵抗换热器长时间使用造成的磨损。
4. 易加工性:工装材料应具有较好的易加工性,以方便制造和维修。
五、工装制造工艺1. 加工精度:工装的加工精度应符合国家和行业的相关标准,以保证换热器零部件的装配精度。
2. 表面处理:工装的表面处理应符合国家和行业的相关标准,以保证工装的耐腐蚀性和美观度。
3. 装配调试:工装在出厂前应进行装配调试,以确保工装的完整性和准确性。
六、工装检验与维护1. 检验:工装应定期进行检验,以确保其符合国家和行业的相关标准。
换热器设备规范标准最新
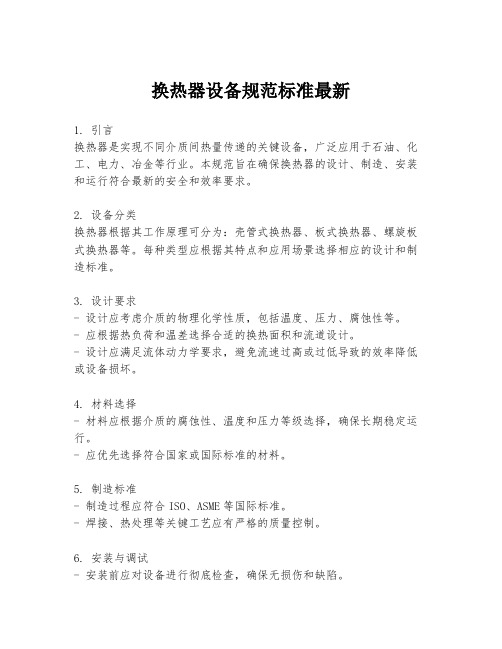
换热器设备规范标准最新1. 引言换热器是实现不同介质间热量传递的关键设备,广泛应用于石油、化工、电力、冶金等行业。
本规范旨在确保换热器的设计、制造、安装和运行符合最新的安全和效率要求。
2. 设备分类换热器根据其工作原理可分为:壳管式换热器、板式换热器、螺旋板式换热器等。
每种类型应根据其特点和应用场景选择相应的设计和制造标准。
3. 设计要求- 设计应考虑介质的物理化学性质,包括温度、压力、腐蚀性等。
- 应根据热负荷和温差选择合适的换热面积和流道设计。
- 设计应满足流体动力学要求,避免流速过高或过低导致的效率降低或设备损坏。
4. 材料选择- 材料应根据介质的腐蚀性、温度和压力等级选择,确保长期稳定运行。
- 应优先选择符合国家或国际标准的材料。
5. 制造标准- 制造过程应符合ISO、ASME等国际标准。
- 焊接、热处理等关键工艺应有严格的质量控制。
6. 安装与调试- 安装前应对设备进行彻底检查,确保无损伤和缺陷。
- 安装应严格按照设计图纸和制造商指导进行。
- 调试过程中应监测设备运行参数,确保达到设计要求。
7. 安全与环保- 设备应配备必要的安全装置,如压力释放阀、温度监控器等。
- 应采取措施减少噪音和振动,符合环保要求。
8. 运行与维护- 制定详细的操作规程,确保操作人员正确使用设备。
- 定期对设备进行检查和维护,及时发现并解决问题。
9. 质量保证- 制造商应提供完整的质量保证体系,包括材料证明、工艺流程记录、出厂检验报告等。
10. 附录- 附录包括换热器的典型设计参数、计算方法、故障排除指南等。
11. 结语本规范标准旨在指导换热器的设计、制造、安装和运行,以确保设备的安全、可靠和高效。
建议用户根据具体应用场景和最新技术发展,对本规范进行适当调整和更新。
请注意,上述内容为示例文本,实际的换热器设备规范标准应根据具体的行业标准和法规进行制定。
换热器设计要求
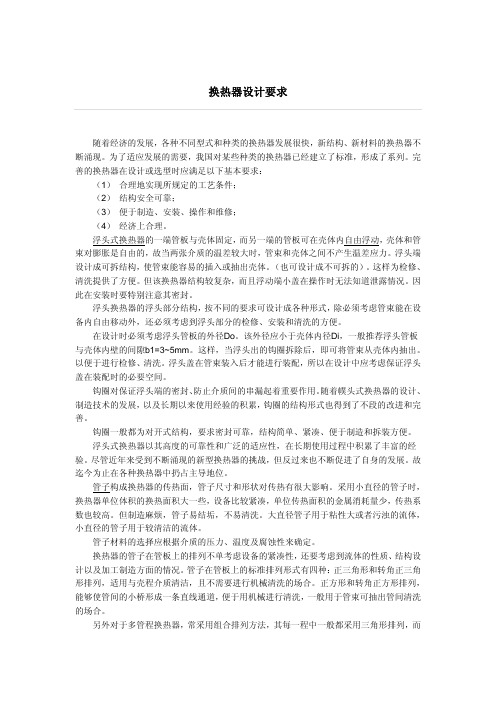
换热器设计要求随着经济的发展,各种不同型式和种类的换热器发展很快,新结构、新材料的换热器不断涌现。
为了适应发展的需要,我国对某些种类的换热器已经建立了标准,形成了系列。
完善的换热器在设计或选型时应满足以下基本要求:(1)合理地实现所规定的工艺条件;(2)结构安全可靠;(3)便于制造、安装、操作和维修;(4)经济上合理。
浮头式换热器的一端管板与壳体固定,而另一端的管板可在壳体内自由浮动,壳体和管束对膨胀是自由的,故当两张介质的温差较大时,管束和壳体之间不产生温差应力。
浮头端设计成可拆结构,使管束能容易的插入或抽出壳体。
(也可设计成不可拆的)。
这样为检修、清洗提供了方便。
但该换热器结构较复杂,而且浮动端小盖在操作时无法知道泄露情况。
因此在安装时要特别注意其密封。
浮头换热器的浮头部分结构,按不同的要求可设计成各种形式,除必须考虑管束能在设备内自由移动外,还必须考虑到浮头部分的检修、安装和清洗的方便。
在设计时必须考虑浮头管板的外径Do。
该外径应小于壳体内径Di,一般推荐浮头管板与壳体内壁的间隙b1=3~5mm。
这样,当浮头出的钩圈拆除后,即可将管束从壳体内抽出。
以便于进行检修、清洗。
浮头盖在管束装入后才能进行装配,所以在设计中应考虑保证浮头盖在装配时的必要空间。
钩圈对保证浮头端的密封、防止介质间的串漏起着重要作用。
随着幞头式换热器的设计、制造技术的发展,以及长期以来使用经验的积累,钩圈的结构形式也得到了不段的改进和完善。
钩圈一般都为对开式结构,要求密封可靠,结构简单、紧凑、便于制造和拆装方便。
浮头式换热器以其高度的可靠性和广泛的适应性,在长期使用过程中积累了丰富的经验。
尽管近年来受到不断涌现的新型换热器的挑战,但反过来也不断促进了自身的发展。
故迄今为止在各种换热器中扔占主导地位。
管子构成换热器的传热面,管子尺寸和形状对传热有很大影响。
采用小直径的管子时,换热器单位体积的换热面积大一些,设备比较紧凑,单位传热面积的金属消耗量少,传热系数也较高。
换热器设计相关标准
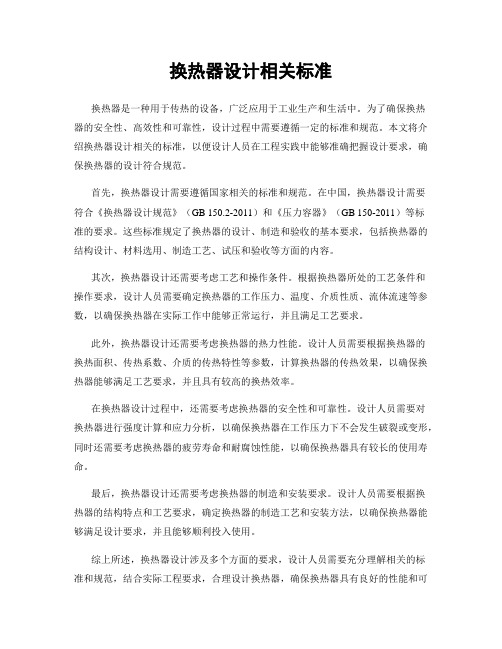
换热器设计相关标准换热器是一种用于传热的设备,广泛应用于工业生产和生活中。
为了确保换热器的安全性、高效性和可靠性,设计过程中需要遵循一定的标准和规范。
本文将介绍换热器设计相关的标准,以便设计人员在工程实践中能够准确把握设计要求,确保换热器的设计符合规范。
首先,换热器设计需要遵循国家相关的标准和规范。
在中国,换热器设计需要符合《换热器设计规范》(GB 150.2-2011)和《压力容器》(GB 150-2011)等标准的要求。
这些标准规定了换热器的设计、制造和验收的基本要求,包括换热器的结构设计、材料选用、制造工艺、试压和验收等方面的内容。
其次,换热器设计还需要考虑工艺和操作条件。
根据换热器所处的工艺条件和操作要求,设计人员需要确定换热器的工作压力、温度、介质性质、流体流速等参数,以确保换热器在实际工作中能够正常运行,并且满足工艺要求。
此外,换热器设计还需要考虑换热器的热力性能。
设计人员需要根据换热器的换热面积、传热系数、介质的传热特性等参数,计算换热器的传热效果,以确保换热器能够满足工艺要求,并且具有较高的换热效率。
在换热器设计过程中,还需要考虑换热器的安全性和可靠性。
设计人员需要对换热器进行强度计算和应力分析,以确保换热器在工作压力下不会发生破裂或变形,同时还需要考虑换热器的疲劳寿命和耐腐蚀性能,以确保换热器具有较长的使用寿命。
最后,换热器设计还需要考虑换热器的制造和安装要求。
设计人员需要根据换热器的结构特点和工艺要求,确定换热器的制造工艺和安装方法,以确保换热器能够满足设计要求,并且能够顺利投入使用。
综上所述,换热器设计涉及多个方面的要求,设计人员需要充分理解相关的标准和规范,结合实际工程要求,合理设计换热器,确保换热器具有良好的性能和可靠的运行。
只有在严格遵循相关标准和规范的前提下,换热器设计才能够达到预期的效果,为工业生产和生活提供可靠的换热服务。
换热器设计规范
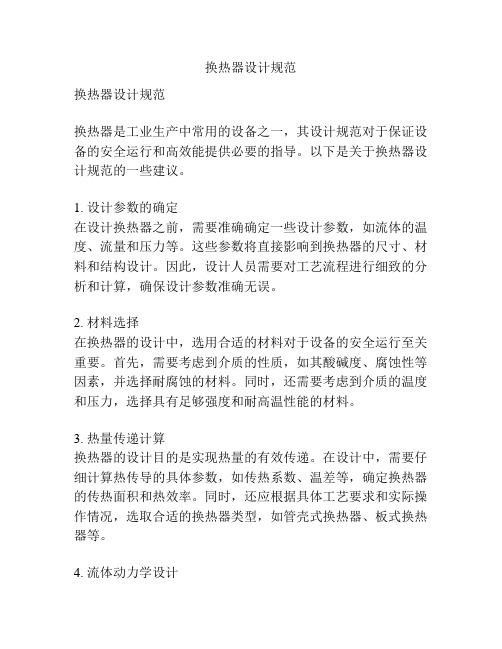
换热器设计规范换热器设计规范换热器是工业生产中常用的设备之一,其设计规范对于保证设备的安全运行和高效能提供必要的指导。
以下是关于换热器设计规范的一些建议。
1. 设计参数的确定在设计换热器之前,需要准确确定一些设计参数,如流体的温度、流量和压力等。
这些参数将直接影响到换热器的尺寸、材料和结构设计。
因此,设计人员需要对工艺流程进行细致的分析和计算,确保设计参数准确无误。
2. 材料选择在换热器的设计中,选用合适的材料对于设备的安全运行至关重要。
首先,需要考虑到介质的性质,如其酸碱度、腐蚀性等因素,并选择耐腐蚀的材料。
同时,还需要考虑到介质的温度和压力,选择具有足够强度和耐高温性能的材料。
3. 热量传递计算换热器的设计目的是实现热量的有效传递。
在设计中,需要仔细计算热传导的具体参数,如传热系数、温差等,确定换热器的传热面积和热效率。
同时,还应根据具体工艺要求和实际操作情况,选取合适的换热器类型,如管壳式换热器、板式换热器等。
4. 流体动力学设计换热器中的流体流动状态对于换热效果有着重要影响。
设计人员需要准确计算流体的流速、流量以及流动方式,合理设计换热器内部的流体通道,确保流体能够充分接触并实现高效传热。
5. 温度控制和安全设计在换热器的设计中,温度的控制是至关重要的因素。
设计人员应根据实际需求,合理选择和设计温度控制装置,确保介质的温度处于安全运行范围内。
同时,还应考虑到换热器在运行过程中可能出现的异常情况,如堵塞、泄漏等,合理设计安全防护装置,确保换热器的安全性和可靠性。
6. 维护和清洗设计换热器是一个长期运行的设备,为了保证其长期运行的效果,设计人员应考虑到设备的维护和清洗问题。
合理的设计可以方便维护人员进行设备的检修和清洗,延长设备的使用寿命。
总之,换热器的设计规范对于确保设备的安全运行和高效能提供了必要的指导。
设计人员应根据具体的工艺要求和实际操作情况,认真分析和计算设计参数,合理选择材料和设备类型,并考虑到温度控制、安全设计和维护等方面,确保换热器的设计符合要求。
换热器技术要求
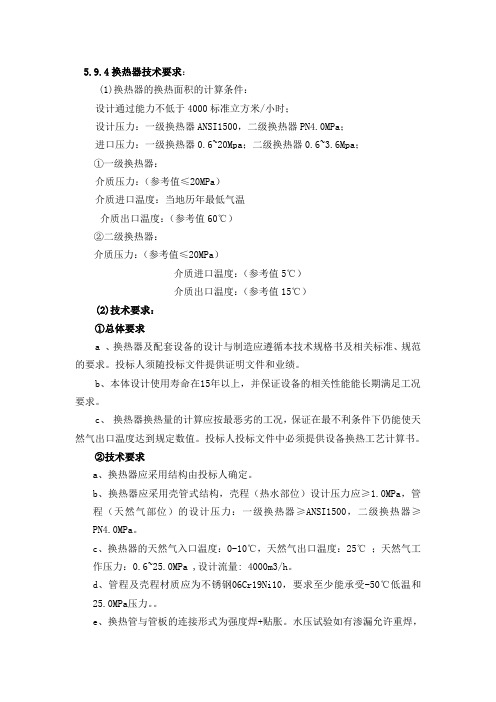
5.9.4换热器技术要求:(1)换热器的换热面积的计算条件:设计通过能力不低于4000标准立方米/小时;设计压力:一级换热器ANSI1500,二级换热器PN4.0MPa;进口压力:一级换热器0.6~20Mpa;二级换热器0.6~3.6Mpa;①一级换热器:介质压力:(参考值≤20MPa)介质进口温度:当地历年最低气温介质出口温度:(参考值60℃)②二级换热器:介质压力:(参考值≤20MPa)介质进口温度:(参考值5℃)介质出口温度:(参考值15℃)(2)技术要求:①总体要求a 、换热器及配套设备的设计与制造应遵循本技术规格书及相关标准、规范的要求。
投标人须随投标文件提供证明文件和业绩。
b、本体设计使用寿命在15年以上,并保证设备的相关性能能长期满足工况要求。
c、换热器换热量的计算应按最恶劣的工况,保证在最不利条件下仍能使天然气出口温度达到规定数值。
投标人投标文件中必须提供设备换热工艺计算书。
②技术要求a、换热器应采用结构由投标人确定。
b、换热器应采用壳管式结构,壳程(热水部位)设计压力应≥1.0MPa,管程(天然气部位)的设计压力:一级换热器≥ANSI1500,二级换热器≥PN4.0MPa。
c、换热器的天然气入口温度:0-10℃,天然气出口温度:25℃;天然气工作压力:0.6~25.0MPa ,设计流量: 4000m3/h。
d、管程及壳程材质应为不锈钢06Cr19Ni10,要求至少能承受-50℃低温和25.0MPa压力。
e、换热管与管板的连接形式为强度焊+贴胀。
水压试验如有渗漏允许重焊,但重焊后需重胀。
f、换热器与管道采用法兰连接,法兰标准ANSIB16.5 CLASS 1500。
换热器与热水供回水管道连接采用钢制对焊凸面法兰,法兰执行标准JB/T81-94。
g、设备制造完毕后,管程、壳程以1.5 倍设计压力进行水压试验,试压合格后壳程再按HG20584-1998 附录A 中的B 法进行氨渗透试验。
换热器设计的基本原则

换热器设计的基本原则
一、温度
⑴.设计温度高于最高工作温度15℃;
⑵.工艺换热时低端差≥20℃;
⑶.冷却水出口温度≤60℃;
⑷.冷却时高端温度差≥20℃;
⑸.冷却时低端温度差≥5℃;
⑹.冷却冷凝时冷却介质人口温度应高于工艺物料中冰点温度5℃;
⑺.冷凝有惰性气体存在时,冷却介质出口温度应低于物料露点温度5℃;
⑻.反应物料冷却时反应物与冷却介质温差≥10℃;
二、压力降
⑴.真空≤0.01MPa
⑵.0.1~0.17MPa 0.004~0.034
⑶.≥0.17MPa ≥0.034MPa
三、流速
⑴.水一般1~2.5m/s
⑵.气体一般8~30m/s
四、折流板间距
⑴.最小间距壳体内径的1/3~1/2
⑵.最大间距 171d00.74 (d0--管外径)
五、物料走向
⑴.温度高温物料走管程
⑵.压力高压力物料走管程
⑶.粘度高粘度物料走管程
⑷.腐蚀性高腐蚀性物料走管程
⑸.流速流速小的物料走壳程
⑹.结垢易结垢较脏的物料走管程
若易结垢较脏的物料必须走壳程,应调整换热管排列方式为四方形,或把换热器的结构形式改为U型管式、浮头式、填料函式等易拆结构。
⑺.导热系数导热系数小的走壳程,如:气体。
换热器设计的基本原则
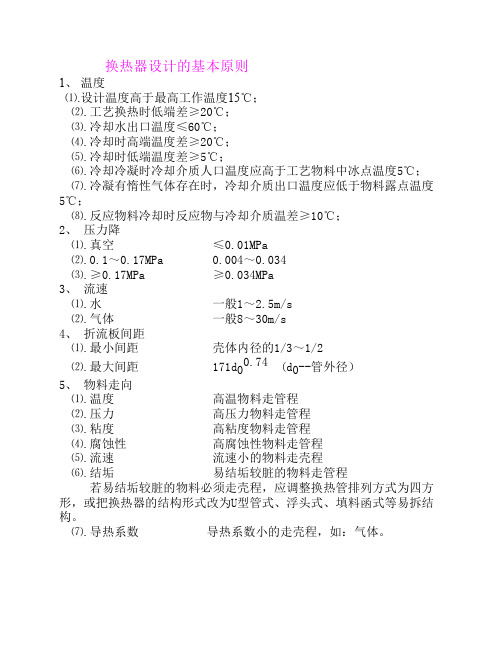
换热器设计的基本原则
1、温度
⑴.设计温度高于最高工作温度15℃;
⑵.工艺换热时低端差≥20℃;
⑶.冷却水出口温度≤60℃;
⑷.冷却时高端温度差≥20℃;
⑸.冷却时低端温度差≥5℃;
⑹.冷却冷凝时冷却介质人口温度应高于工艺物料中冰点温度5℃;
⑺.冷凝有惰性气体存在时,冷却介质出口温度应低于物料露点温度5℃;
⑻.反应物料冷却时反应物与冷却介质温差≥10℃;
2、 压力降
⑴.真空 ≤0.01MPa
⑵.0.1~0.17MPa 0.004~0.034
⑶.≥0.17MPa ≥0.034MPa
3、 流速
⑴.水 一般1~2.5m/s
⑵.气体 一般8~30m/s
4、 折流板间距
⑴.最小间距 壳体内径的1/3~1/2
⑵.最大间距 171d00.74 (d0--管外径)
5、 物料走向
⑴.温度 高温物料走管程
⑵.压力 高压力物料走管程
⑶.粘度 高粘度物料走管程
⑷.腐蚀性 高腐蚀性物料走管程
⑸.流速 流速小的物料走壳程
⑹.结垢 易结垢较脏的物料走管程
若易结垢较脏的物料必须走壳程,应调整换热管排列方式为四方形,或把换热器的结构形式改为U型管式、浮头式、填料函式等易拆结构。
⑺.导热系数 导热系数小的走壳程,如:气体。
换热器一般设计要求
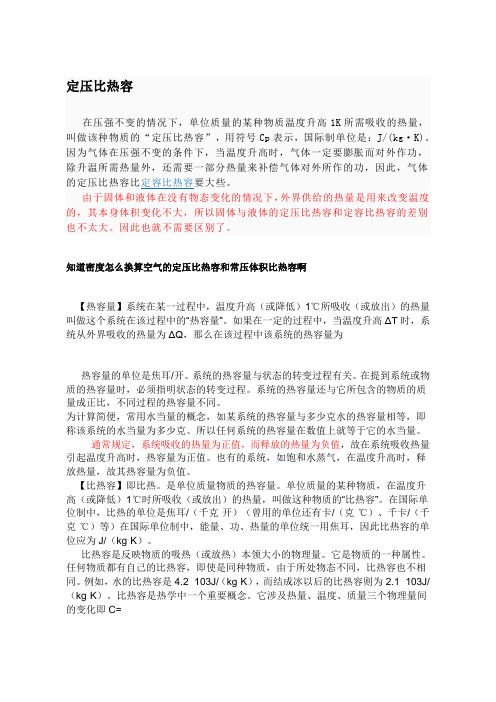
定压比热容在压强不变的情况下,单位质量的某种物质温度升高1K所需吸收的热量,叫做该种物质的“定压比热容”,用符号Cp表示,国际制单位是:J/(kg·K)。
因为气体在压强不变的条件下,当温度升高时,气体一定要膨胀而对外作功,除升温所需热量外,还需要一部分热量来补偿气体对外所作的功,因此,气体的定压比热容比定容比热容要大些。
由于固体和液体在没有物态变化的情况下,外界供给的热量是用来改变温度的,其本身体积变化不大,所以固体与液体的定压比热容和定容比热容的差别也不太大。
因此也就不需要区别了。
知道密度怎么换算空气的定压比热容和常压体积比热容啊【热容量】系统在某一过程中,温度升高(或降低)1℃所吸收(或放出)的热量叫做这个系统在该过程中的“热容量”。
如果在一定的过程中,当温度升高ΔT时,系统从外界吸收的热量为ΔQ,那么在该过程中该系统的热容量为热容量的单位是焦耳/开。
系统的热容量与状态的转变过程有关。
在提到系统或物质的热容量时,必须指明状态的转变过程。
系统的热容量还与它所包含的物质的质量成正比,不同过程的热容量不同。
为计算简便,常用水当量的概念,如某系统的热容量与多少克水的热容量相等,即称该系统的水当量为多少克。
所以任何系统的热容量在数值上就等于它的水当量。
通常规定,系统吸收的热量为正值,而释放的热量为负值,故在系统吸收热量引起温度升高时,热容量为正值。
也有的系统,如饱和水蒸气,在温度升高时,释放热量,故其热容量为负值。
【比热容】即比热。
是单位质量物质的热容量。
单位质量的某种物质,在温度升高(或降低)1℃时所吸收(或放出)的热量,叫做这种物质的“比热容”。
在国际单位制中,比热的单位是焦耳/(千克·开)(曾用的单位还有卡/(克·℃)、千卡/(千克·℃)等)在国际单位制中,能量、功、热量的单位统一用焦耳,因此比热容的单位应为J/(kg·K)。
比热容是反映物质的吸热(或放热)本领大小的物理量。
固定管板式换热器设计说明书

固定管板式换热器设计说明书一、设计背景与要求二、设计原理固定管板式换热器由固定的管束和管板组成,通过管束内的流体和管板外的流体之间的传热,实现热能转移。
其主要设计原理为热量的对流传递和热量的传导传递。
设计时需要根据流体的性质和要求确定换热系数和传导热阻,并通过计算和优化得出合理的设计。
三、操作参数1.温度:设计时需要确定换热器的设计工作温度范围,包括入口和出口温度,以及最大温度差。
2.压力:设计时需要确定换热器的设计工作压力范围,包括入口和出口压力,以及最大压力差。
3.流量:设计时需要确定流体的流量和流速,以便计算换热器的传热能力。
4.材料:选择合适的材料以满足操作参数和流体性质的要求。
四、结构特点1.管束:固定管束的结构形式多种多样,包括普通绕管式、螺旋绕管式、折流板绕管式等。
设计时需要根据传热效果和结构特点选择合适的管束类型。
2.管板:固定管束通过管板支撑和固定,管板的结构形式多样,包括单管板和多管板。
设计时需要考虑流体的流动和换热效果,选择合适的管板形式。
3.密封:固定管板式换热器的密封性能直接影响其工作效果,设计时需要充分考虑密封结构和材料,确保换热器的可靠性和密封性。
4.清洗:固定管板式换热器的管束和管板之间的间隙较小,难以进行清洗和维护。
设计时需要充分考虑清洗装置和维护便利性,保证换热器的正常运行。
五、设计方案1.确定操作参数:根据实际应用需求和流体性质,确定换热器的操作参数,包括温度、压力、流量等。
2.选择管束类型:根据传热效果和结构特点,选择合适的管束类型,包括普通绕管式、螺旋绕管式、折流板绕管式等。
3.设计管板形式:根据流体的流动和换热效果,选择合适的管板形式,包括单管板和多管板。
4.确定密封结构:根据换热器的工作要求,选择合适的密封结构和材料,确保换热器的可靠性和密封性。
5.考虑清洗装置:充分考虑清洗装置和维护便利性,确保换热器的清洗和维护工作能够顺利进行。
六、施工与使用1.施工流程:根据设计方案,进行换热器的制造和安装,确保施工质量和进度。
换热器的工艺设计参数
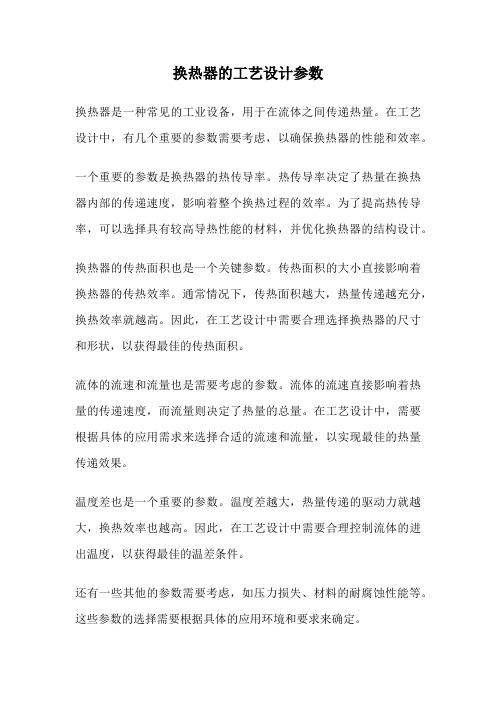
换热器的工艺设计参数
换热器是一种常见的工业设备,用于在流体之间传递热量。
在工艺设计中,有几个重要的参数需要考虑,以确保换热器的性能和效率。
一个重要的参数是换热器的热传导率。
热传导率决定了热量在换热器内部的传递速度,影响着整个换热过程的效率。
为了提高热传导率,可以选择具有较高导热性能的材料,并优化换热器的结构设计。
换热器的传热面积也是一个关键参数。
传热面积的大小直接影响着换热器的传热效率。
通常情况下,传热面积越大,热量传递越充分,换热效率就越高。
因此,在工艺设计中需要合理选择换热器的尺寸和形状,以获得最佳的传热面积。
流体的流速和流量也是需要考虑的参数。
流体的流速直接影响着热量的传递速度,而流量则决定了热量的总量。
在工艺设计中,需要根据具体的应用需求来选择合适的流速和流量,以实现最佳的热量传递效果。
温度差也是一个重要的参数。
温度差越大,热量传递的驱动力就越大,换热效率也越高。
因此,在工艺设计中需要合理控制流体的进出温度,以获得最佳的温差条件。
还有一些其他的参数需要考虑,如压力损失、材料的耐腐蚀性能等。
这些参数的选择需要根据具体的应用环境和要求来确定。
总的来说,换热器的工艺设计参数是多方面的,涉及到材料、结构、流体等多个方面的考虑。
通过合理选择这些参数,可以实现换热器的高效运行,提高热量传递效率,满足工业生产的需求。
板式换热器技术标准
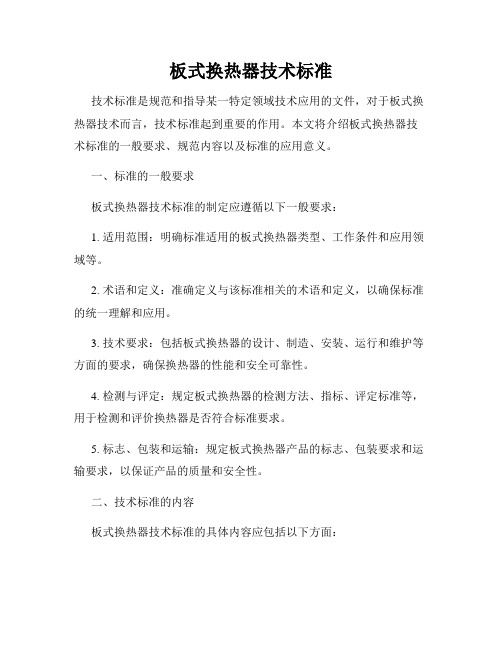
板式换热器技术标准技术标准是规范和指导某一特定领域技术应用的文件,对于板式换热器技术而言,技术标准起到重要的作用。
本文将介绍板式换热器技术标准的一般要求、规范内容以及标准的应用意义。
一、标准的一般要求板式换热器技术标准的制定应遵循以下一般要求:1. 适用范围:明确标准适用的板式换热器类型、工作条件和应用领域等。
2. 术语和定义:准确定义与该标准相关的术语和定义,以确保标准的统一理解和应用。
3. 技术要求:包括板式换热器的设计、制造、安装、运行和维护等方面的要求,确保换热器的性能和安全可靠性。
4. 检测与评定:规定板式换热器的检测方法、指标、评定标准等,用于检测和评价换热器是否符合标准要求。
5. 标志、包装和运输:规定板式换热器产品的标志、包装要求和运输要求,以保证产品的质量和安全性。
二、技术标准的内容板式换热器技术标准的具体内容应包括以下方面:1. 材料选择:明确板式换热器所使用的材料要求,包括板材、密封垫片、焊接材料等。
2. 设计要求:规定板式换热器的结构设计、换热面积计算、流体分隔和流体分配等方面的要求。
3. 制造要求:包括板式换热器的制造工艺、组装质量控制、清洗和检漏等制造过程的要求。
4. 安装要求:规定板式换热器的安装位置、布置方式、连接方式和管道支撑等安装细节要求。
5. 运行和维护要求:明确板式换热器的运行参数、操作要点、维护周期及方法等要求,确保换热器的正常运行和维护管理。
三、标准的应用意义制定和遵守板式换热器技术标准具有以下应用意义:1. 保证换热器性能:通过遵循技术标准,确保板式换热器具有良好的换热性能和传热效率,满足工艺要求。
2. 确保产品质量:标准的应用能够提高换热器的制造质量,确保产品具备良好的密封性、强度和耐腐蚀性,延长使用寿命。
3. 促进技术进步:技术标准是对行业技术的总结和规范,通过标准的制定和推广应用,可以促进技术的进步和创新。
4. 统一市场规范:技术标准的应用可以统一市场行为,避免低劣产品流入市场,保障用户的权益。
- 1、下载文档前请自行甄别文档内容的完整性,平台不提供额外的编辑、内容补充、找答案等附加服务。
- 2、"仅部分预览"的文档,不可在线预览部分如存在完整性等问题,可反馈申请退款(可完整预览的文档不适用该条件!)。
- 3、如文档侵犯您的权益,请联系客服反馈,我们会尽快为您处理(人工客服工作时间:9:00-18:30)。
定压比热容
在压强不变的情况下,单位质量的某种物质温度升高1K所需吸收的热量,叫做该种物质的“定压比热容”,用符号Cp表示,国际制单位是:J/(kg·K)。
因为气体在压强不变的条件下,当温度升高时,气体一定要膨胀而对外作功,除升温所需热量外,还需要一部分热量来补偿气体对外所作的功,因此,气体的定压比热容比定容比热容要大些。
由于固体和液体在没有物态变化的情况下,外界供给的热量是用来改变温度的,其本身体积变化不大,所以固体与液体的定压比热容和定容比热容的差别也不太大。
因此也就不需要区别了。
知道密度怎么换算空气的定压比热容和常压体积比热容啊
【热容量】系统在某一过程中,温度升高(或降低)1℃所吸收(或放出)的热量叫做这个系统在该过程中的“热容量”。
如果在一定的过程中,当温度升高ΔT时,系统从外界吸收的热量为ΔQ,那么在该过程中该系统的热容量为
热容量的单位是焦耳/开。
系统的热容量与状态的转变过程有关。
在提到系统或物质的热容量时,必须指明状态的转变过程。
系统的热容量还与它所包含的物质的质量成正比,不同过程的热容量不同。
为计算简便,常用水当量的概念,如某系统的热容量与多少克水的热容量相等,即称该系统的水当量为多少克。
所以任何系统的热容量在数值上就等于它的水当量。
通常规定,系统吸收的热量为正值,而释放的热量为负值,故在系统吸收热量引起温度升高时,热容量为正值。
也有的系统,如饱和水蒸气,在温度升高时,释放热量,故其热容量为负值。
【比热容】即比热。
是单位质量物质的热容量。
单位质量的某种物质,在温度升高(或降低)1℃时所吸收(或放出)的热量,叫做这种物质的“比热容”。
在国际单位制中,比热的单位是焦耳/(千克·开)(曾用的单位还有卡/(克·℃)、千卡/(千克·℃)等)在国际单位制中,能量、功、热量的单位统一用焦耳,因此比热容的单位应为J/(kg·K)。
比热容是反映物质的吸热(或放热)本领大小的物理量。
它是物质的一种属性。
任何物质都有自己的比热容,即使是同种物质,由于所处物态不同,比热容也不相同。
例如,水的比热容是4.2×103J/(kg·K),而结成冰以后的比热容则为2.1×103J/(kg·K)。
比热容是热学中一个重要概念。
它涉及热量、温度、质量三个物理量间的变化即C=
压强和体积的变化,而有所不同。
水的比热容,只有当温度从14.5℃上升到15.5℃时,它的比热容才等于4.2×103J/(kg·K),在其他温度间隔,水的比热容不一定等于4.2×103J/(kg·K)但由于差别很小,可不加考虑。
其他物质在温度改变时,比热容也有很小的变化。
比热容表中所给的数值都是这些物质的平均值。
气体的比热容和气体的热膨胀有密切关系,在体积恒定与压强恒定时不同,故有定容比热容和定压比热容两个概念。
但对固体和液体,二者差别很小,一般就不再加以区分。
【定容比热容】在物体体积不变的情况下,单位质量的某种物质温度升高1℃所需吸收的热量,叫做该种物质的“定容比热容”。
【定压比热容】在压强不变的情况下,单位质量的某种物质温度升高1℃所需吸收的热量,叫做该种物质的“定压比热容”。
因为气体在压强不变的条件下,当温度升高时,气体一定要膨胀而对外作功,除升温所需热量外,还需要一部分热量来补偿气体对外所作的功,因此,气体的定压比热容比定容比热容要大些。
换热器管程及壳程的流动阻力,常常控制在一定允许范围内。
若计算结果超过允许值时,则应修改设计参数或重新选择其他规格的换热器。
按一般经验,对于液体常控制在104~105Pa范围内,对于气体则以103~104Pa为宜。
此外,也可依据操作压力不同而有所差别,参考下表。
换热器的合理压力降:较高的压降值导致较高的流速,因此会导致较小的设备和较少的投资,但运行费用会增高,较低的允许压降值则与此相反。
所以,应该在投资和运行费用之间进行一个经济技术比较。
在下表中给出了常用的换热器的压降值,可供计算时参考。
管壳式换热器、空冷器和套管式换热器
板翅式换热器
其实不用这么复杂,一般换热器的压降要求是0.35公斤,如果介质为润滑油压降要求为1-2公斤,其余特殊的压降要求业主方技术人员会提出的
对容器而言,压降是在同一腔体内的压力差,压差一般指不同腔体间的压力差
换热器压力降参考值表
操作压力P(MPa) 压力降ΔP(MPa)
0~0.1(绝压) P/10
0~0.07(表压,下同) P/2
0.07~1.0 0.035
1.0~3.0 0.035~0.18
3.0~8.0 0.07~0.25
不管什么形式换热器,在传热的过程中,因为介质流过换热器的时候必然会有一定的阻力,所以介质出口压力肯定低于原来的进口压力,进出口介质的压力差即为换热器的压降;但是为了强化传热,我们会在流动通道内设置一些扰流元件,从而增加湍动程度,进而达到强化传热,那么在强化的过程中,压力降就更大,所需的动力就更大,所以绝对不能让压降太大,为了考虑成本和效益以及能量的损失,就提出了允许压降,把压力降限制在某个范围内。
当然,这没有什么绝对的,有时
必须有取舍。
容许压降往往是整个工艺要求的而不是换热器本身要求的,举例:
压力为0.13 kPa(A)的液体,经过换热器后要进入蒸馏塔。
蒸馏塔的压力是0.11 MPa (A),那么换热器的压降就不能高于0.02 MPa(A),否则换热后流体压力低,进不了塔,要设泵,增加了设备不是很麻烦?尽量避免。
压降低于0.02 MPa(A),就是这个换热器设计的硬性要求。
这种要求在工业设计中比比皆是,设计人员是从工艺全局看问题,提要求。
设备人员一般看不了这么远。
管壳式换热器允许压力降范围,按化工设备设计全书《换热器》的P18表2-2如下换热器的操作压力Pa 允许的压力降Pa
p<10^5(a) Δp=0.1xp
p=0~10^5(g) Δp=0.05xp
p=>10^5(g) Δp<5x10^4 p
这只给出的是大概范围,重要的是工艺计算来确定合理的满足单元操作的压力降。
根据钱颂文老师主编《换热器设计手册》,管壳式换热器的压降一般是控制:
工艺物流的压力MPa 允许压力降ΔP MPa
真空 0.01
0.1-0.17 0.004-0.034
>0.17 ≥0.034
(1)敏化处理:18-8钢系列的奥氏体不锈钢在450℃~850℃(此区间常称为敏化温度)短时间加热,使其具有晶间腐蚀倾向。
这是因为碳在奥氏体不锈钢中的溶解度与温度有很大影响。
奥氏体不锈钢在经400℃~850℃的温度范围内(敏化温度区域)时,会有高铬碳化物(Cr23C6)析出,当铬含量降至耐腐蚀性界限之下,此时存在晶界贫铬,会产生晶间腐蚀,严重时材料能变成粉末。
该方法一般只在不锈钢晶间腐蚀试验时采用。
(2)固溶热处理:将奥氏体不锈钢加热到1100℃左右,使碳化物相全部或基本溶解,碳固溶于奥氏体中,然后快速冷却至室温,使碳达到过饱和状态(碳已经稳定了,没有能力和机会与铬形成高铬碳化物)。
(3)稳定化处理:为避免碳与铬形成高铬碳化物,在奥氏体钢中加入稳定化元素(如Ti和Nb),在加热到875℃以上温度时,能形成稳定的碳化物。
这是因为Ti(或Nb)能优先与碳结合,形成TiC(或NbC),从而大大降低了奥氏体中固溶碳的浓度(含量),起到了牺牲Ti(或Nb)保护Cr的目的。
含Ti(或Nb)的奥氏体不锈钢(如:
1Cr18Ni9Ti,1Cr18Ni9Nb)经稳定化处理后比进行固溶热处理更具有良好的综合机械性能。
(4)所以,有晶间腐蚀倾向的奥氏体不锈钢应进行固溶热处理或稳定化处理。
;
从温度上来说
固溶处理>敏化处理>稳定化处理
三者热处理的目的也不一样!
通常采用316L的情况是由于有较高的耐蚀性要求和耐高温要求,为了节省材料降低成本,所以会选择采用复合板材料。
复合板的消应理论上应按照基层的材料要求进行,但是由于介质有较高的耐蚀性要求,所以为了避免材料在使用过程中发生晶间腐蚀,通常采用降低热处理温度,延长保温时间的办法来消除应力,一般在410-430度,这样就可以避开其敏化区间。
当然,如果介质没有腐蚀性,那热处理就按照基层材料的要求进行。
哈氏B-2合金存在对抗晶间腐蚀性能有相当大影响的两个敏化区:1200~1300℃的高温区和550~900℃的中温区。