常用铸造方法
金属常见铸造工艺

金属常见铸造工艺一、砂型铸造砂型铸造是金属铸造中最常见的一种工艺。
它以砂为主要原料,通过制作砂型,将熔化的金属注入砂型中,冷却后取出成型的零件。
砂型铸造工艺具有成本低、适用范围广等优势。
在砂型铸造中,常用的砂型材料有石英砂、水玻璃砂和石膏砂等。
二、金属型铸造金属型铸造是一种将熔化金属倒入金属型中制造零件的工艺。
与砂型铸造相比,金属型铸造具有更高的表面光洁度和尺寸精度。
常见的金属型材料有铸铁、铸钢、铝合金等。
金属型铸造工艺适用于制造复杂形状、高精度要求的零件。
三、压力铸造压力铸造是一种将金属熔液通过高速喷射到模具中制造零件的工艺。
压力铸造具有生产效率高、零件表面质量好等优点。
在压力铸造中,常用的金属包括铝合金、锌合金、镁合金等。
压力铸造广泛应用于汽车、航空航天等领域。
四、失重铸造失重铸造是一种利用失重环境制造金属零件的工艺。
常见的失重铸造方法有真空铸造、离心铸造和低压铸造等。
失重铸造工艺可以获得高质量的零件,尤其适用于制造大型复杂的铸件。
五、连续铸造连续铸造是一种连续生产长条状铸件的工艺。
在连续铸造中,金属熔液通过连续流动的铸模,经过冷却和凝固,最终形成所需的长条状铸件。
连续铸造工艺适用于生产钢坯、铸铁坯等。
六、精密铸造精密铸造是一种制造高精度、高表面质量零件的工艺。
它通过采用精密模具和特殊工艺控制,实现零件尺寸、形状和表面质量的要求。
精密铸造广泛应用于航空航天、光电子等领域。
七、熔模铸造熔模铸造是一种以熔融模具为模具材料制造零件的工艺。
常见的熔模材料有蜡、塑料等。
熔模铸造工艺可以制造出具有复杂内部结构和高表面质量的零件,广泛应用于航空航天、汽车等领域。
八、低压铸造低压铸造是一种将金属熔液通过压力推入模具中制造零件的工艺。
低压铸造具有生产效率高、零件质量好等优点。
常见的低压铸造材料有铝合金、镁合金等。
九、注射铸造注射铸造是一种将金属熔液通过高速注射进入模具中制造零件的工艺。
注射铸造具有生产效率高、零件尺寸精度高等优点。
常用的铸造方法

常用的铸造方法宝子,今天咱来唠唠铸造方法呀。
砂型铸造可是最常见的一种呢。
就像是用沙子搭城堡一样,不过这可是很有技术含量的。
把砂弄成特定的形状,做出型腔,然后把熔化的金属倒进去,等金属冷却凝固,把砂型一拆,一个铸件就诞生啦。
砂型铸造成本低,对设备要求也不高,所以很多小厂或者做一些简单铸件的时候就爱用这个方法。
它就像一个低调又实用的小伙伴,虽然看起来不是那么高大上,但是超级靠谱。
熔模铸造也很有趣哦。
它就像是给金属做个蜡模替身。
先做出一个蜡模,这个蜡模可以做得很精细呢,就像做精致的小雕塑一样。
然后用特殊的材料把蜡模包裹起来,再把蜡化掉,就留下了一个型腔,再把金属液灌进去。
这样铸造出来的零件精度可高啦,表面还很光滑。
就像是给金属穿上了一件量身定制的漂亮衣服,特别适合那些对精度和表面质量要求高的小零件。
还有压铸呢。
这就像是给金属来一场快速的变身秀。
把金属加热熔化后,用很大的压力把金属液快速地压射到模具里。
这个过程特别快,就像闪电侠一样。
压铸出来的零件密度高,强度好,而且尺寸精度也不错。
不过呢,压铸的设备比较贵,就像一个傲娇的小公主,虽然有点难伺候,但是能做出很棒的铸件呢。
离心铸造也很独特。
想象一下,把金属液放在一个旋转的模具里,金属液就像被甩出去一样,靠着离心力均匀地分布在模具壁上。
这种方法铸造出来的圆筒形的铸件特别好,质量均匀,内部也不容易有缺陷。
就像是在游乐场里玩旋转木马一样,金属液在旋转中完成了自己的华丽变身。
铸造的方法各有各的妙处,就像不同性格的小伙伴,在不同的场合发挥着自己的特长,是不是很神奇呀?。
铸造常用的造型方法

铸造常用的造型方法“哎呀,这东西坏了,得重新做一个呀!”我不禁嘟囔着。
铸造,这可是一门相当有意思的工艺呢。
铸造常用的造型方法有好几种,且听我慢慢道来。
首先就是砂型铸造啦。
这就像是搭积木一样,先准备好型砂,然后把模样放在砂箱里,用型砂把模样埋起来,再把模样取出来,就留下了一个型腔。
步骤听起来简单,可做起来得特别细心呢!在这个过程中,要注意型砂的湿度和紧实度,太湿了或者太松了都不行,那可就容易出问题啦。
砂型铸造的应用场景那可多了去了,像一些大型的铸件,比如机床的底座啊,就经常用砂型铸造。
它的优势就是成本相对较低,而且能铸造出各种形状复杂的零件。
我记得有一次,我们要做一个发动机的缸体,就是用砂型铸造的方法。
大家齐心协力,先仔细地调配型砂,然后小心翼翼地把模样放进去,再一点一点地填砂、紧实。
当最后把铸件取出来的时候,哇,那种成就感简直爆棚!虽然过程中也遇到了一些小麻烦,比如有个地方型砂没填好出现了缺陷,但通过大家的努力都一一解决了。
还有金属型铸造呢。
这个就像是做蛋糕用的模具,把金属液倒进模具里,等冷却了就成型啦。
操作的时候要注意模具的预热和涂料的涂刷,这可关系到铸件的质量呢。
金属型铸造适用于大批量生产,它的优点是铸件的精度高、表面质量好。
就像上次我们做一批小零件,用的就是金属型铸造。
大家分工明确,有人负责预热模具,有人负责涂刷涂料,有人负责浇注金属液。
当看到那一个个亮晶晶的小零件从模具里出来的时候,大家都兴奋得不行。
另外,消失模铸造也很有趣呢。
先做好一个泡沫模样,然后把它埋在型砂里,浇注的时候泡沫模样就会消失,金属液就会占据原来泡沫模样的位置。
这个方法特别适合做一些形状特别复杂的铸件。
在操作的时候要注意泡沫模样的制作精度和型砂的透气性。
我曾经参与过一个工艺品的铸造,用的就是消失模铸造。
看着那个精美的泡沫模样,我心里还真有点舍不得呢,不过一想到它会变成一个更漂亮的金属工艺品,又充满了期待。
当最后看到那个栩栩如生的工艺品出现在眼前时,那种惊喜真是难以言表。
手工砂型铸造常用的基本造型方法
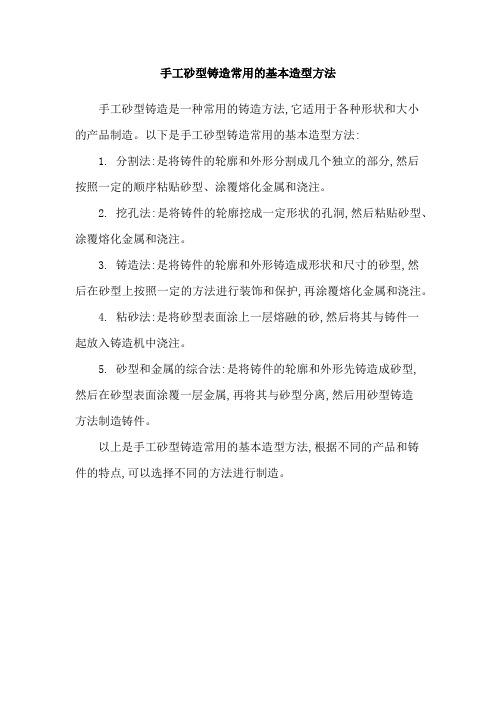
手工砂型铸造常用的基本造型方法
手工砂型铸造是一种常用的铸造方法,它适用于各种形状和大小
的产品制造。
以下是手工砂型铸造常用的基本造型方法:
1. 分割法:是将铸件的轮廓和外形分割成几个独立的部分,然后
按照一定的顺序粘贴砂型、涂覆熔化金属和浇注。
2. 挖孔法:是将铸件的轮廓挖成一定形状的孔洞,然后粘贴砂型、涂覆熔化金属和浇注。
3. 铸造法:是将铸件的轮廓和外形铸造成形状和尺寸的砂型,然
后在砂型上按照一定的方法进行装饰和保护,再涂覆熔化金属和浇注。
4. 粘砂法:是将砂型表面涂上一层熔融的砂,然后将其与铸件一
起放入铸造机中浇注。
5. 砂型和金属的综合法:是将铸件的轮廓和外形先铸造成砂型,
然后在砂型表面涂覆一层金属,再将其与砂型分离,然后用砂型铸造
方法制造铸件。
以上是手工砂型铸造常用的基本造型方法,根据不同的产品和铸
件的特点,可以选择不同的方法进行制造。
自己铸造铝件方法

自己铸造铝件方法
铸造铝件的方法可以分为两种:压力铸造和重力铸造。
以下是这两种方法的简要描述:
1. 压力铸造(压铸法):压力铸造是一种常用的铝铸造方法,适用于生产复杂形状的铝件。
主要步骤如下:
1) 设计和制作铸造模具:铸造模具根据铝件的形状和尺寸进行设计和制作。
2) 准备熔炉和铝合金:铝合金根据需要的成分比例,加入适量的合金元素,并在熔炉中加热至熔点。
3) 注入铝液:将预热好的模具放置在机器中,然后将熔化的铝液倒入模具中。
4) 施加压力:通过机器施加压力,使铝液填充整个模具并达到所需形状。
5) 冷却和固化:待铝液冷却后,铝件会固化成所需的形状。
6) 取出铝件和清洁:将模具分离,取出成品铝件,并进行清洁和表面处理。
2. 重力铸造(重铸法):重力铸造是一种相对简单且常用的铝铸造方法,适用于生产简单形状的铝件。
主要步骤如下:
1) 设计和制作铸造模具:铸造模具根据铝件的形状和尺寸进行设计和制作。
2) 准备熔炉和铝合金:按照需要的成分比例,加入适量的合金元素,并在熔炉中加热至熔点。
3) 注入铝液:将预热好的模具放置在垂直位置上,然后将熔化的铝液倒入模具中。
4) 冷却和固化:待铝液冷却后,铝件会固化成所需的形状。
5) 取出铝件和清洁:将模具分离,取出成品铝件,并进行清洁和表面处理。
需要注意的是,铸造过程中应遵循相关安全操作规程,确保操作者的安全并获得高质量的铝件。
此外,根据具体需求和要求,还可以采用其他铸造方法,如砂型铸造、低压铸造等。
常用的铸造方法有哪些

常用的铸造方法有哪些铸造是一种重要的金属加工工艺,它可以将熔化的金属或金属合金浇注到模具中形成所需的零件形状。
在工业生产中,铸造方法被广泛应用于制造各种金属零件,如汽车发动机零件、航空航天零件、建筑构件等。
下面介绍一些常用的铸造方法。
1.砂型铸造砂型铸造是最常见和最传统的铸造方法之一。
它以砂为模具材料,通过在砂型中浇注熔融金属来制造零件。
砂型铸造具有成本低、灵活性强、适应性广等优点,广泛应用于大型、中小型铸件的生产。
2.金属型铸造金属型铸造是利用金属模具来制造金属零件的铸造方法。
金属模具通常由铸铁、铸钢等金属材料制成,具有较高的热传导性和耐磨性。
金属型铸造适用于生产高精度、高要求的零件,如汽车发动机缸体、汽车制动鼓等。
3.压铸压铸是一种将熔融金属通过高压注射到模具中的铸造方法。
压铸通常使用压铸机进行操作,可以生产出形状复杂、尺寸精确的零件。
压铸适用于生产大批量的零件,如电子设备外壳、汽车零件等。
4.失蜡铸造失蜡铸造是一种利用蜡模进行铸造的方法。
首先,将蜡模涂覆在模具内,然后在加热的条件下蜡模燃烧脱掉,最后用熔融金属浇注到空腔中形成零件。
失蜡铸造适用于制造复杂形状和高精度的零件,如航空发动机叶片、珠宝等。
5.连铸连铸是一种连续浇注熔融金属的铸造方法。
在连铸过程中,熔融金属通过铸造机装置连续注入到冷却的铸坯模具中,以形成长条状的铸坯。
连铸常用于生产金属板、金属线材等。
6.壳模铸造壳模铸造是一种以薄壳层为模具的铸造方法。
在壳模铸造中,通过将涂覆在原型上的耐火材料经过多次处理形成薄壳层,然后将熔融金属浇注到薄壳层内形成零件。
壳模铸造适用于制造高精度和高表面质量要求的零件,如汽车零件、航空零件等。
7.压铸砂铸造压铸砂铸造是将熔融金属通过压力将座子压入砂型中的铸造方法。
压铸砂铸造可以用于生产加工复杂的金属零件,如汽车缸盖等,具有高生产效率和良好的表面质量。
8.低压铸造低压铸造是一种利用气压来推动熔融金属进入模具中的铸造方法。
常用的五种特种铸造方法

常用的五种特种铸造方法一、熔模铸造。
熔模铸造啊,又叫失蜡铸造。
它的过程还挺有趣的。
先得做个模样,这个模样可不是普通的,一般是用易熔材料,像蜡料啊之类的制成跟咱想要的铸件形状一模一样的东西。
就好比你要做个小摆件,那就先得用蜡做出这个小摆件的样子来。
然后把这个蜡模样沾上一层耐火材料,就像给它穿了一层“铠甲”,等这层“铠甲”干了之后呢,再重复沾几次,让这“铠甲”更厚实坚固。
接下来就是关键的一步啦,把这个带“铠甲”的蜡模样加热,让里面的蜡熔化流出来,这样就留下了一个跟蜡模样形状一样的空腔。
最后把熔化的金属液浇进去,等它冷却凝固后,把外面的“铠甲”去掉,一个精美的铸件就诞生啦。
熔模铸造的优点可不少哦。
它能铸造出形状很复杂的零件,不管是有各种弯弯绕绕的,还是有一些精细结构的,它都能搞定。
而且铸件的尺寸精度比较高,表面质量也很好,后续加工量就少啦,能省不少事儿呢。
不过呢,它也有缺点,成本相对高一些,生产周期也比较长。
二、金属型铸造。
金属型铸造就是用金属制成的铸型来进行铸造。
想象一下,有一个坚固的金属模具,把熔化的金属液倒进去,就像把水倒进杯子里一样,等它冷却凝固,就得到铸件啦。
这种铸造方法的优点那也是杠杠的。
因为金属型可以反复使用,所以能提高生产效率,降低成本。
而且金属型的导热性好,能让铸件冷却得更快,这样铸件的晶粒就比较细小,力学性能也就更好啦。
比如说一些铝合金的汽车零部件,用金属型铸造出来质量就很不错。
但是呢,金属型铸造也有它的小麻烦。
金属型没有退让性,就是说铸件在冷却收缩的时候,金属型不会像砂型那样可以稍微变形给铸件腾出点空间,所以铸件容易产生裂纹。
而且金属型的制造成本比较高,不太适合小批量生产。
三、压力铸造。
压力铸造啊,简单说就是在高压的作用下把金属液快速地压入铸型型腔中。
这就好比给金属液来了个“大力助推”,让它以很快的速度充满型腔。
压力铸造的优点超多的。
它的生产效率那叫一个高,能在很短的时间内就生产出一个铸件。
铸造常用的成型工艺

主要有砂型铸造和特种铸造2大类。
1 普通砂型铸造,利用砂作为铸模材料,又称砂铸,翻砂,包括湿砂型、干砂型和化学硬化砂型3类,但并非所有砂均可用以铸造。
好处是成本较低,因为铸模所使用的沙可重复使用;缺点是铸模制作耗时,铸模本身不能被重复使用,须破坏后才能取得成品。
1.1 砂型(芯)铸造方法:湿型砂型、树脂自硬砂型、水玻璃砂型、干型和表干型、实型铸造、负压造型。
1.2 砂芯制造方法:是根据砂芯尺寸、形状、生产批量及具体生产条件进行选择的。
在生产中,从总体上可分为手工制芯和机器制芯。
2特种铸造,按造型材料又可分为以天然矿产砂石为主要造型材料的特种铸造(如熔模铸造、泥型铸造、壳型铸造、负压铸造、实型铸造、陶瓷型铸造等)和以金属为主要铸型材料的特种铸造(如金属型铸造、压力铸造、连续铸造、低压铸造、离心铸造等)两类。
2.1 金属模铸造法利用熔点较原料高的金属制作铸模。
其中细分为重力铸造法、低压铸造法和高压铸造法。
受制于铸模的熔点,可被铸造的金属也有所限制。
2.2 脱蜡铸造法这方法可以为外膜铸造法和固体铸造法。
先以蜡复制所需要铸造的物件,然后浸入含陶瓷(或硅溶胶)的池中并待乾,使以蜡制的复制品覆上一层陶瓷外膜,一直重复步骤直到外膜足以支持铸造过程(约1/4寸到1/8寸),然后熔解模中的蜡,并抽离铸模。
其后铸模需要多次加以高温,增强硬度后方可用以铸造。
此方法具有良好的准确性,更可用作高熔点金属(如钛)的铸造。
但由于陶瓷价格颇高,而且制作需要多次加热和复杂,故成本颇为昂贵。
成型工艺1.重力浇铸:砂铸,硬模铸造。
依靠金属自身重力将熔融金属液浇入型腔。
2.压力铸造:低压浇铸,高压铸造。
依靠额外增加的压力将熔融金属液瞬间压入铸造型腔。
铸造常用的手工造型方法

铸造常用的手工造型方法铸造是一种传统的制造工艺,在现代工业生产中得到广泛应用。
铸造是指将熔化的金属或合金倒入模型中,冷却后形成所需的零件或产品的过程。
手工造型是铸造过程中最重要的环节之一,它决定了铸造品质的好坏。
本文将介绍铸造常用的手工造型方法。
一、石膏造型法石膏造型法是一种常用的手工造型方法,它的优点是操作简单,成本低廉。
具体步骤如下:1.准备模板:根据产品的尺寸和形状,制作出木质或塑料的模板。
2.制作石膏模型:将石膏粉加入水中,搅拌均匀,倒入模板中,待其凝固后取出。
3.修整模型:用刀具将多余的石膏切除,修整成所需的形状。
4.涂抹脱模剂:在模型表面涂抹一层脱模剂,以便于将铸造品从模型中取出。
5.铸造:将熔化的金属或合金倒入模型中,待其冷却后取出铸造品。
二、砂型造型法砂型造型法是一种常用的手工造型方法,它的优点是适用于各种形状的产品,且可以重复使用。
具体步骤如下:1.准备砂型:将干砂和粘结剂混合均匀,倒入模板中,压实成型。
2.制作芯子:根据产品的形状,制作出芯子,用于制造内部空腔或空洞的零件。
3.涂抹脱模剂:在砂型表面和芯子表面涂抹一层脱模剂,以便于将铸造品从模型中取出。
4.铸造:将熔化的金属或合金倒入砂型中,待其冷却后取出铸造品。
5.处理砂型:将铸造品从砂型中取出,清理砂型,以便于下一次使用。
三、蜡模造型法蜡模造型法是一种较为复杂的手工造型方法,它的优点是可以制造出高精度、高复杂度的铸造品。
具体步骤如下:1.制作蜡模:将蜡模料加热至液态,倒入模板中,冷却后取出蜡模。
2.组装蜡模:将多个蜡模组装成一个完整的零件,用于制造复杂的铸造品。
3.涂抹陶瓷涂料:在蜡模表面涂抹一层陶瓷涂料,待其干燥后再涂抹多层。
4.烧结:将涂抹好陶瓷涂料的蜡模放入高温炉中烧结,使其成为坚硬的陶瓷模。
5.铸造:将熔化的金属或合金倒入陶瓷模中,待其冷却后取出铸造品。
6.处理陶瓷模:将铸造品从陶瓷模中取出,清理陶瓷模,以便于下一次使用。
(完整版)第二节常用的铸造方法

第二节常用的铸造方法(五)离心铸造离心铸造是将金属液浇入绕水平、倾斜或立轴旋转的铸型,在离心力的作用下凝固的铸造方法。
铸件的轴线与旋转铸型的轴线重合。
铸型可用金属型、砂型、陶瓷型、熔模壳型等。
1.离心铸造机离心铸造机是离心铸造所用的设备,按其旋转轴空间位置的不同分为立式、卧式二种。
立式离心铸造机的铸型是绕垂直轴旋转(图2-2-41a),由于金属液的重力作用,铸件的内表面呈抛物线形,故铸件不易过高,它主要用于铸造高度小于直径的环类、套类及成形铸件。
卧式离心铸造机的铸型是绕水平轴旋转(图2-2-41b),铸件的壁厚较均匀,主要用长度大于直径的管类、套类铸件。
图2-2-41 离心铸造示意图图 2-2-9 离心铸造2.离心铸造的特点和应用与其它铸造方法相比,离心铸造的优点是:(1)优点1)铸件组织致密,无缩孔、缩松、气孔、夹渣等缺陷,力学性能好。
2)铸造圆形中空铸件时,不用型芯和浇注系统,简化了工艺过程,降低了金属消耗。
3)提高了金属液的充型能力,改善了充型条件,可用于浇注流动性较差的合金及薄壁铸件。
4)可生产双金属铸件,如钢套内镶铜轴承等,其结合面牢固、耐磨,又可节约贵重金属材料。
5)离心铸造适应性较广,铸造合金的种类几乎不受限制。
既合适于铸造中空件,又可以铸造成形铸件。
中空铸件的内径通常为8~3000mm;铸件长度可达8000mm;质量可由几克至十几吨。
但离心铸造不宜生产易偏析的合金(如铅青铜等),铸件内表面较粗糙,尺寸不易控制。
(2)应用离心铸造主要用于生产各种管、套、环类铸件,如铸铁管、铜套、滑动轴承、缸套、双金属钢背铜套等铸件,也可用于生产齿轮、叶轮、涡轮等成形铸件。
(六)熔模铸造熔模铸造是指在易熔(如蜡料)制成的模样上包覆若干层耐火涂料,待其干燥硬化后熔出模样而制成型壳,型壳经高温培烧后即可浇注的铸造方法。
熔模铸造是精密铸造方法之一。
1.熔模铸造的工艺过程熔模铸造的工艺过程如动画2-2-7所示。
常用金属的铸造技术

常用金属的铸造技术铸造是一种重要的金属加工方法,广泛应用于制造业中。
常用金属的铸造技术涉及到铸造工艺、铸型材料、熔炼技术等多个方面。
本文将就常用金属的铸造技术进行介绍。
一、铸造工艺铸造工艺是指通过熔融金属注入铸型中,并在铸型中冷却凝固形成所需形状的加工方法。
常用的铸造工艺包括砂型铸造、金属型铸造和压力铸造等。
1. 砂型铸造:砂型铸造是一种常见的铸造工艺,其工艺流程包括制模、浇注、冷却、脱模和清理等。
制模阶段通过将砂型材料填充到铸型中,形成所需的形状。
浇注阶段将熔融金属注入砂型中,待冷却凝固后,进行脱模和清理,最终得到铸件。
2. 金属型铸造:金属型铸造是指使用金属材料制作铸型的铸造工艺。
常用的金属型材料有铸铁和铸钢等。
金属型铸造具有高精度和高表面质量的优点,广泛应用于汽车和机械制造等行业。
3. 压力铸造:压力铸造是通过在熔融金属中施加压力,将金属充填到铸型中的铸造工艺。
常用的压力铸造方法有压力重力铸造和压力差异铸造等。
压力铸造具有高效率和高密度的特点,适用于生产大批量的零件。
二、铸型材料铸型材料是指用于制作铸型的材料,常用的铸型材料包括砂型、金属型和陶瓷型等。
1. 砂型:砂型是一种常见的铸型材料,其主要成分是砂粒和粘结剂。
砂型具有成本低、易于制作和回收利用的优点,适用于大型和复杂铸件的制作。
2. 金属型:金属型是一种使用金属材料制作的铸型。
金属型具有高热导率和高强度的特点,适用于高温和高压力的铸造工艺。
3. 陶瓷型:陶瓷型是一种使用陶瓷材料制作的铸型。
陶瓷型具有高耐火性和化学稳定性,适用于高温合金和特殊材料的铸造。
三、熔炼技术熔炼技术是指将金属熔化成液态,并进行净化和调合的过程。
常用的熔炼技术包括电弧炉熔炼、感应炉熔炼和氩弧炉熔炼等。
1. 电弧炉熔炼:电弧炉熔炼是一种利用电弧加热金属材料并使其熔化的熔炼技术。
电弧炉熔炼具有温度高、熔炼速度快和操作灵活的特点,广泛应用于不同类型的金属熔炼。
2. 感应炉熔炼:感应炉熔炼是一种利用感应加热金属材料并使其熔化的熔炼技术。
铸造常用的成型工艺
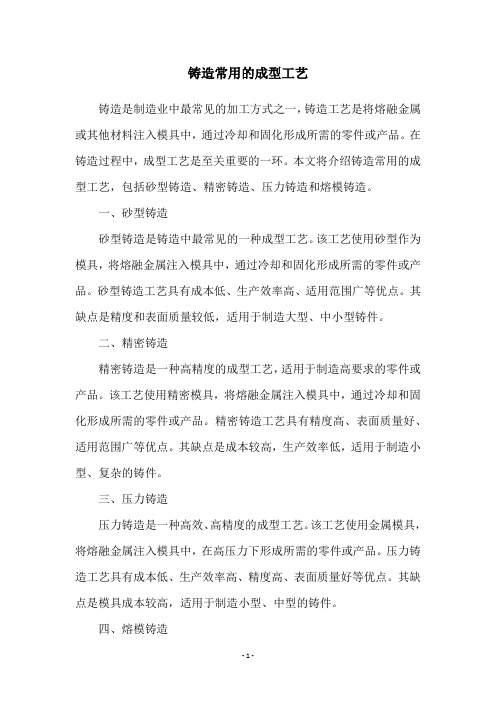
铸造常用的成型工艺铸造是制造业中最常见的加工方式之一,铸造工艺是将熔融金属或其他材料注入模具中,通过冷却和固化形成所需的零件或产品。
在铸造过程中,成型工艺是至关重要的一环。
本文将介绍铸造常用的成型工艺,包括砂型铸造、精密铸造、压力铸造和熔模铸造。
一、砂型铸造砂型铸造是铸造中最常见的一种成型工艺。
该工艺使用砂型作为模具,将熔融金属注入模具中,通过冷却和固化形成所需的零件或产品。
砂型铸造工艺具有成本低、生产效率高、适用范围广等优点。
其缺点是精度和表面质量较低,适用于制造大型、中小型铸件。
二、精密铸造精密铸造是一种高精度的成型工艺,适用于制造高要求的零件或产品。
该工艺使用精密模具,将熔融金属注入模具中,通过冷却和固化形成所需的零件或产品。
精密铸造工艺具有精度高、表面质量好、适用范围广等优点。
其缺点是成本较高,生产效率低,适用于制造小型、复杂的铸件。
三、压力铸造压力铸造是一种高效、高精度的成型工艺。
该工艺使用金属模具,将熔融金属注入模具中,在高压力下形成所需的零件或产品。
压力铸造工艺具有成本低、生产效率高、精度高、表面质量好等优点。
其缺点是模具成本较高,适用于制造小型、中型的铸件。
四、熔模铸造熔模铸造是一种高精度、高表面质量的成型工艺。
该工艺使用陶瓷模具,将熔融金属注入模具中,在高温下形成所需的零件或产品。
熔模铸造工艺具有精度高、表面质量好、适用范围广等优点。
其缺点是成本较高,生产效率低,适用于制造小型、复杂的铸件。
总之,铸造常用的成型工艺包括砂型铸造、精密铸造、压力铸造和熔模铸造。
每种成型工艺都有其优点和缺点,根据所需的零件或产品的要求来选择合适的成型工艺是非常重要的。
钛合金铸造技术及其应用
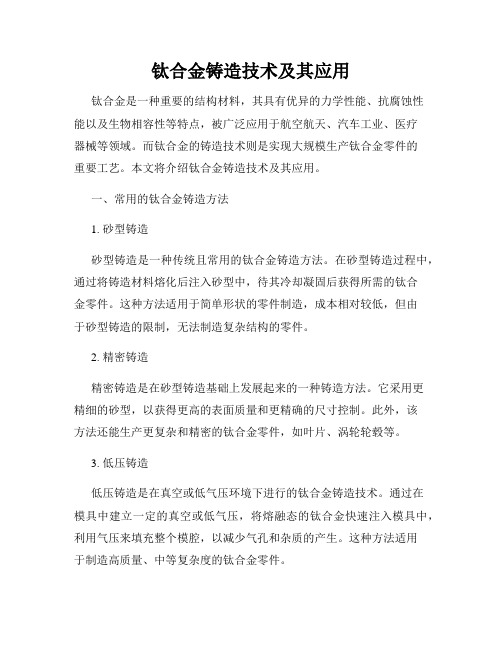
钛合金铸造技术及其应用钛合金是一种重要的结构材料,其具有优异的力学性能、抗腐蚀性能以及生物相容性等特点,被广泛应用于航空航天、汽车工业、医疗器械等领域。
而钛合金的铸造技术则是实现大规模生产钛合金零件的重要工艺。
本文将介绍钛合金铸造技术及其应用。
一、常用的钛合金铸造方法1. 砂型铸造砂型铸造是一种传统且常用的钛合金铸造方法。
在砂型铸造过程中,通过将铸造材料熔化后注入砂型中,待其冷却凝固后获得所需的钛合金零件。
这种方法适用于简单形状的零件制造,成本相对较低,但由于砂型铸造的限制,无法制造复杂结构的零件。
2. 精密铸造精密铸造是在砂型铸造基础上发展起来的一种铸造方法。
它采用更精细的砂型,以获得更高的表面质量和更精确的尺寸控制。
此外,该方法还能生产更复杂和精密的钛合金零件,如叶片、涡轮轮毂等。
3. 低压铸造低压铸造是在真空或低气压环境下进行的钛合金铸造技术。
通过在模具中建立一定的真空或低气压,将熔融态的钛合金快速注入模具中,利用气压来填充整个模腔,以减少气孔和杂质的产生。
这种方法适用于制造高质量、中等复杂度的钛合金零件。
4. 熔模铸造熔模铸造是一种通过直接将熔模注入模具中进行铸造的方法。
熔模铸造的优点是可以制造出高精度、高质量的钛合金零件,尤其适用于制造复杂结构和薄壁的零件。
然而,该方法的成本较高,且模具制备时间较长。
二、钛合金铸造技术的应用1. 航空航天领域钛合金在航空航天领域中具有非常重要的地位。
通过钛合金铸造技术,可以制造出航空发动机零件、地面支撑设备以及飞行器结构等。
钛合金的高强度、低密度和耐腐蚀性能使其成为飞机和航天器的理想材料。
2. 汽车工业钛合金在汽车工业中的应用也越来越广泛。
通过钛合金铸造技术,可以制造出汽车发动机中的活塞、连杆和阀门等零件,其中钛合金零件的应用可以减轻发动机重量,提高燃油效率,且具有良好的耐磨性和耐高温性。
3. 医疗器械由于钛合金具有生物相容性和抗腐蚀性能,因此广泛应用于医疗器械制造领域。
常见铸造工艺
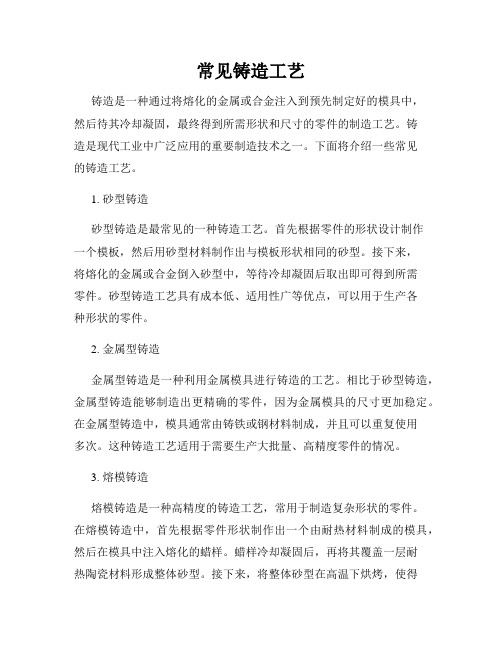
常见铸造工艺铸造是一种通过将熔化的金属或合金注入到预先制定好的模具中,然后待其冷却凝固,最终得到所需形状和尺寸的零件的制造工艺。
铸造是现代工业中广泛应用的重要制造技术之一。
下面将介绍一些常见的铸造工艺。
1. 砂型铸造砂型铸造是最常见的一种铸造工艺。
首先根据零件的形状设计制作一个模板,然后用砂型材料制作出与模板形状相同的砂型。
接下来,将熔化的金属或合金倒入砂型中,等待冷却凝固后取出即可得到所需零件。
砂型铸造工艺具有成本低、适用性广等优点,可以用于生产各种形状的零件。
2. 金属型铸造金属型铸造是一种利用金属模具进行铸造的工艺。
相比于砂型铸造,金属型铸造能够制造出更精确的零件,因为金属模具的尺寸更加稳定。
在金属型铸造中,模具通常由铸铁或钢材料制成,并且可以重复使用多次。
这种铸造工艺适用于需要生产大批量、高精度零件的情况。
3. 熔模铸造熔模铸造是一种高精度的铸造工艺,常用于制造复杂形状的零件。
在熔模铸造中,首先根据零件形状制作出一个由耐热材料制成的模具,然后在模具中注入熔化的蜡样。
蜡样冷却凝固后,再将其覆盖一层耐热陶瓷材料形成整体砂型。
接下来,将整体砂型在高温下烘烤,使得蜡样完全熔化并排出,留下蜡样的形状空腔。
最后,将熔化的金属或合金注入形状空腔中,等待冷却凝固后取出模具,就得到了所需的零件。
4. 连铸工艺连铸工艺是一种快速、连续、高效的铸造工艺,常用于制造长条状或板状的铸件,如钢坯、铸铁等。
在连铸工艺中,熔化的金属通过连续浇注到一个长而窄的铸模中,然后通过冷却、凝固、轧制等步骤得到所需尺寸和形状的铸件。
这种工艺能够实现连续生产,提高生产效率和产品质量。
以上是一些常见的铸造工艺。
每种铸造工艺都有其适用的领域和特点,可以根据具体需求选择合适的工艺来实现所需零件的制造。
铸造工艺的不断发展和创新将为各行各业提供更多高品质、高效率的零部件制造解决方案。
铸造种类和特点

铸造种类和特点铸造是制造工程领域中最常用的成形工艺之一,广泛应用于各个行业,如汽车、航空航天、机械制造等。
它以熔化金属液态材料,通过铸型成形,获得所需形状和尺寸的工件。
根据铸造方法和材料的不同,可以将铸造分为几种不同的类型。
本文将为大家介绍一些常见的铸造种类及其特点。
1. 砂型铸造砂型铸造是最常见和最基本的铸造方法之一。
它使用砂型作为铸造模具,在高温下,将熔化金属注入模具中,冷却后获得所需工件。
砂型铸造具有成本低、灵活性高等特点,适用于大多数金属材料的铸造,尤其适用于复杂形状的工件。
2. 金属型铸造金属型铸造是使用金属型作为模具进行铸造的方法。
金属型通常由铜合金或钢制成,可重复使用多次,具有较高的精度和表面质量。
金属型铸造适用于生产高精度、高表面质量要求的工件,如发动机缸体、汽车零件等。
3. 熔模铸造熔模铸造是一种精密铸造方法,也被称为“失蜡法”。
该方法首先制作模具,然后在模具中注入蜡模,形成整个铸件的空腔结构。
蜡模覆盖有特殊的耐火涂料,形成熔模。
在熔模中倒入熔化金属,蜡模被熔化和燃烧,金属充满模腔后冷却凝固,得到最终的铸件。
熔模铸造具有较高的精度和表面质量,适用于生产复杂形状、高精度的工件。
4. 压铸压铸是一种以高压下将熔化金属注入金属模具中的方法。
它具有高生产效率和较高的表面质量,适用于大批量生产复杂形状的工件。
压铸可用于铝合金、镁合金和锌合金等材料的铸造。
5. 真空铸造真空铸造是在真空环境下进行的一种特殊铸造方法。
在真空中铸造,可有效防止金属氧化和气孔的产生,提高铸件的密度和质量。
真空铸造适用于高温合金、精密合金等材料的铸造,广泛用于航空航天领域。
每种铸造方法都有其适用的范围和特点。
在实际生产中,根据所需工件的形状、尺寸、材料和数量等要求,选择合适的铸造方法非常重要。
总结:铸造作为一种传统工艺,在现代制造业中仍然扮演着重要的角色。
通过不同的铸造方法可以生产出各种形状、材料和尺寸的工件,满足各种行业的需求。
常用的特种铸造方法

常用的特种铸造方法常用的特种铸造方法有很多种,以下是其中几种比较常见和广泛应用的特种铸造方法。
1. 砂模铸造:砂模铸造是最常见和传统的铸造方法之一。
它利用砂模作为铸型,通过将熔融金属浇铸到砂模中,待金属凝固后取出,最终得到所需的铸件。
砂模铸造方法简单、成本低,并且适用于各种金属和合金的铸造,因此广泛应用于铸造行业。
2. 熔模铸造:熔模铸造是一种高精度的铸造方法,用于生产复杂形状和高品质的铸件。
它使用可熔的模具材料制作出铸型,将熔融金属浇铸到模型中,待金属凝固后融化模型材料,最终得到形状精确的铸件。
熔模铸造方法适用于生产涡轮叶片、发动机缸体等高温、高压零件。
3. 高压铸造:高压铸造也被称为压力铸造或压铸,是一种常用的特种铸造方法。
它利用高压将熔融金属迫使进入金属模具中,待金属凝固后取出铸件。
高压铸造方法适用于生产复杂形状和高精度的铸件,广泛应用于汽车制造、航空航天和电子产品等行业。
4. 重力铸造:重力铸造也称为重铸,是一种主要利用重力作用的铸造方法,通过重力迫使熔融金属填充铸型。
重力铸造方法简单、成本低,适用于生产大型铸件和毛坯,广泛应用于机械制造和钢铁工业。
5. 低压铸造:低压铸造是一种将熔融金属浇注到真空状态下的铸造方法。
它通过在铸型上施加一定的正压力,使熔融金属进入铸型,并且在凝固期间保持压力。
低压铸造方法适用于生产中小型铸件和高品质铸件,广泛应用于航空航天和汽车制造等高端领域。
6. 氩气铸造:氩气铸造是一种利用惰性气体氩气防止熔融金属中气孔形成的铸造方法。
在铸造过程中,通过在熔融金属中通入氩气,它会与金属中的氧、氢等杂质反应,从而防止气孔形成。
氩气铸造方法能够提高铸件的密度和强度,广泛应用于汽车零部件铸造。
总之,以上是常用的一些特种铸造方法,每种方法在不同的情况下有其特定的优势和适用范围。
铸造技术作为一项传统且重要的制造工艺,在各个工业领域中扮演着重要的角色。
随着科技的不断发展,特种铸造方法也在不断创新和改进,以满足越来越高的工艺要求和产品质量需求。
常用铸造方法

挤压铸造
先在铸型的下型中浇入定量的液体金属,迅速合型, 大批生产以非铁合金为主的形状
并在压力下凝固。铸件组织致密,无气孔,但设备 简单,内部质量要求高或轮廓尺
较复杂。挤压钢铁合金时模具寿命短
寸大的薄壁零件
石墨型铸造
用石墨材料制成铸型,重力浇铸成型、铸件组织致 成批生产铜合金螺旋桨等形状不
密,尺寸精确,生产率高,但铸型质脆,易碎,手 太复杂的中小型零件,也可用于
3. 融模铸件设计注意事项
五.金属型铸造 将金属液浇注到金属铸型中,待其冷却后获得铸件的方法叫金属型铸造。由于金属型
能反复使用很多次,又叫永久型铸造。 1. 金属型的结构
一般的,金属型用铸铁和铸钢制成。铸件的内腔既可用金属芯、也可用砂芯。金属型 的结构有多种,如水平分型、重直分型及复合分型。如图 5.1 所示。其中垂直分型便于开 设内浇口和取出铸件;水平分型多用来生产薄壁轮状铸件;复合分型的上半型是由垂直分 型的两半型采用铰链连结而成,下半型为固定不动的水平底板,主要应用于较复杂铸件的 铸造。
各种生产批量以碳钢合金钢为主的各种合金和难于加工的高熔点合金复杂零件为宜铸件质量一般小于10kg金属型铸造用金属铸型在重力下浇铸成型对非铁合金铸件有细化组织的作用灰铸铁件易出现白口生产率高无粉尘设备费用教高手工操作时劳动条成批大量生产以非铁合金为主也可用于铸钢铸铁的厚壁简单或中等复杂的中小铸件低压铸造用金属型石墨型砂型在气体压力下充型及结晶凝固铸件致密金属利用率高设备简单单件小批或大批生产以非铁合金的中大薄壁铸件陶瓷型铸造采用高精度模样用自硬耐火浆料灌注成型重力浇铸铸件精度高表面粗糙度细但陶瓷浆料价单件小批生产中小型壁厚中等复杂铸件特别宜作金属型模板热芯盒及各种热锻模具离心铸造用金属型或砂型在离心力作用下浇铸成型铸件组织致密设备简单成本低生产率高但机械加工量大单件成批大量生产铁管铜套金属轴瓦汽缸套等旋转体型铸实型铸造用泡沫聚苯乙烯塑料模局部或全部代替木模或金属模造型在浇铸时烧失
常用的铸造造型方法

常用的铸造造型方法
1. 砂型铸造:使用砂模具来制造铸件形状的铸造方法。
2. 铸造模铸造:使用铸模来制造铸件形状的铸造方法。
3. 压铸:将金属熔化后,注入金属模具中,用高压使金属充满模具,待冷却固化后即可取出成型件。
4. 低压铸造:在铸造前将模具密封,在恒底压力和真空环境下进行铸造。
5. 真空铸造:在铸造前将模具密封,在低压和真空环境下进行铸造。
6. 熔模铸造:将固态金属铸造成具有模拟形状的铸造方法。
7. 铸造模压制成型法:将铸造模具中的铸造材料加压成型,再进行烧结结晶,得到铸造件。
8. 水玻璃铸造法:将石墨、铁或其他金属制成模具,再将水玻璃与石英砂混合后倒入模具中,待凝固后取出成型件。
9. 泥模铸造法:用泥土制成模具,再把铁或铜水倒入模具中,待凝固后取出铸件。
- 1、下载文档前请自行甄别文档内容的完整性,平台不提供额外的编辑、内容补充、找答案等附加服务。
- 2、"仅部分预览"的文档,不可在线预览部分如存在完整性等问题,可反馈申请退款(可完整预览的文档不适用该条件!)。
- 3、如文档侵犯您的权益,请联系客服反馈,我们会尽快为您处理(人工客服工作时间:9:00-18:30)。
液态合金中金 属密度大,而非金 属杂质、气体等密 度小,易于上浮。 铸件上表面易于产 生砂眼、气孔、夹 渣等缺陷。
图2.2.3 锥齿轮铸件的浇注位置
b.铸件大平面应朝下
图2.2.4 夹砂示意图
c.铸件的薄壁 应朝下,厚 壁应朝上
图2.2.5 大平面浇注位置 图2.2.6 壳体铸件浇注位置
②分型面的选择
零件图
铸型砂
造型 熔炼金属
浇注
铸型装配图
制造芯盒
合型
铸造工艺卡
造芯 制备芯砂
落砂
清理
检验 去应力退火 入库
2.铸件的生产
某工厂铸造车间生产端盖铸件, 材质为HT150,生产100件,采用砂
(1)铸件工艺设计
型铸造。零件图如下图所示 :
1)砂型的选择
2)造型方法的选择
4.生产报告
1.砂型铸造工艺简介
下面以连接盘零件为例,介绍一下砂型铸造的主 要工艺过程。
零件砂型铸造的主要工艺过程
生产铸件
首先技术人员根据零件的使用性能要求,设计零件的结 构,绘制零件图;然后铸造技术人员根据铸件的零件图、技 术要求、生产批量等进行工艺设计;而后投入生产。
一个铸件的生产过程大致如下:
3)浇注位置与分型面的选择
4)确定工艺参数
5)绘制铸造工艺图
(2)铸件的生产
1)模样和芯盒 2)造型材料 3)造型 4)浇注
5)落砂与清理
图2.2.1 端盖零件图
1)砂型的选择
砂型的选择应根据零件结构、质量要求、 生产批量和车间生产条件等加以选择。 表2.2.1列出了常用砂型的特点和适用范围。
端盖铸件形状简单。生产批量小,所用 材料灰铸铁具有良好的铸造性能。因此,从 表2.2.1可知,可以使用湿砂型。
表2.2.7 砂型铸造时模样外表面的起模斜度(摘自GB/T5105—91)
起模斜度≤
测量面高度 H/mm
金属模样、塑料模样
木模样
≤10 >10~40 >40~100 >100~160 >160~250 >250~400 >400~630 >630~1000
α
2º20′ 1º10′ 0º30′ 0º25′ 0º20′ 0º20′ 0º20′ 0º15′
0.4 0.7 0.9 1.3 1.4 2.5 3.5 5 7 10
0.5 0.8 1.1 1.5 2.2 3 4 6 9 12
0.6 0.9 1.2 1.8 2.5 3.5 5 7 10 14
注:①最终机械加工后铸件的最大轮廓尺寸。②等级A和B仅用于特殊场 合。
表2.2.5 毛坯铸件典型的机械加工余量等级
端盖铸件属于单 件,小批量生产,选 用手工造型比较合理。 端盖铸件最大截面在 一端,且为平面,由 表2.2.2可知,适合用 整模造型。
图2.2.2 模板
3)浇注位置与分型面的选择
浇注位置是浇注时铸件在铸型内所处的位置。 分型面是铸型砂箱间的结合面。
①浇注位置的选择 通常遵循以下原则:
a.铸件的重要加工面或主要工作面应处于底面或侧面
设备投资较少;铸件精度高、表面光滑;落砂方 便,旧砂处理简便;能耗和环境污染较小。但生 产效率较低,形状复杂覆膜较困难。适用于单件、 小批量生产形状不大复杂的铸件
气冲造型
气冲造型和负压造型是近年来发展很快的造型方 法。
气冲造型:
用蒸气或压 缩空气或爆炸产 生的气体瞬间膨 胀,所产生的压 力波紧实型砂的 造型方法。
表2.2.6 砂型铸造时铸件线收缩率
合金种类
铸件线收缩率/%
自由收缩
受阻收缩
中小件
1.0
0.9
普通灰铸铁
大中件
0.9
0.8
特大件
0.8
0.7
孕育铸铁
1.0~1.5
0.8~1.0
碳素铸钢
1.6~2.0
1.3~1.7
铝硅合金
1.0~1.2
0.8~1.0
锡青铜
1.4
1.2
端盖是小型普通灰铸铁件,且结构简单,查表得线收缩率为1%。
c.应尽量减少型芯活块的数量。
d.主要型芯应尽量放在下半铸型中。
端盖浇注位置和分型面的选择:
上
下
上
下
方案一
方案二
图2.2.10 端盖分型面选择
4)确定工艺参数
为了绘制铸造工艺图,在铸造方案确定后, 还需要选定如下工艺参数。
① 机械加工余量 ② 收缩率 ③ 铸造圆角 ④ 起模斜度 ⑤ 最小铸出孔、槽尺寸 ⑥ 型芯头
表2.2.2 常用手工造型方法的特点和应用范围
造型方法
特点
应用范围
整模造型
整体模,分型面为平面,铸型简单,铸件不会 铸件最大截面在一端,且为平
产生错型缺陷
面
分模造型 挖砂造型 假箱造型 活块造型 刮板造型 三箱造型 (也可两箱)
地坑造型
模样沿最大截面分为两半,型腔位于上、下两 最大截面在中部,一般为对称
造型是砂型铸造的重要工序,造型方法 有手工造型和机器造型两类。
① 手工造型 指紧砂与起模是由人来完成的。
常用于单件和小批量生产。 常用手工造型方法的 特点和应用范围见表2.2.2。
② 机器造型 指用机器全部完成或至少完成紧砂
和起模操作的造型工序。 适用于中、小型铸件的成批、大量生产。常用的
机器造型方法的主要特点和适用范围见表2.2.3。
经过烘干的高粘土含量 ( 粘 土 质 量 分 数 为 12% ~ 14%)的砂型
铸型强度和透气性较高,发 单件,小批量生
气量小,故铸造缺陷较少; 但生产周期长,设备投资大, 能耗较高,且难于实现机械
产质量要求较高, 结构复杂的中、
化与自动化
大型铸件
表面烘干 型
浇注前用适当方法将型腔 表层(厚15~20mm)进行 干燥的砂型
表2.2.4 机械加工余量
最大尺寸①
大于
至
—
40
40
63
63
100
10
160
160
250
250
400
400
630
630 1000
要求的机械加工余量等级
A② B②
C
D
E
F
G
H
J
K
0.1 0.1 0.2 0.3 0.4 0.5 0.5 0.7 1 1.4 0.1 0.2 0.3 0.3 0.4 0.5 0.7 1 1.4 2 0.2 0.3 0.4 0.5 0.7 1 1.4 2 2.8 4 0.3 0.4 0.5 0.8 1.1 1.5 2.2 3 4 6 0.3 0.5 0.7 1 1.4 2 2.8 4 5.5 8
a.芯头高(或长)度和斜度 b.芯头装配间隙
①机械加工余量
机械加工余量是铸件上为切削加工而加大的 尺寸。
大量生产时余量可减小;单件小批量生产时,余量 应加大;
表面粗糙时,余量应加大(如铸钢); 非铁金属表面光洁且材料价格昂贵,余量应减小; 铸件尺寸越大,加工余量越大; 加工面与基准面距离越大,加工余量越大。 要求的机械加工余量RMA等级有10级,称之为A、B、 C、D、E、 F、G、H、J和K级(见表2.2.4)。推荐用于 各种铸造合金和铸造方法的RMA等级列在表2.2.5中。
微震压实造 型
在高频率、小振幅振动下,利用 型砂的惯性紧实作用并同时或随 后加压紧实型砂
抛砂造型
利用离心力抛出型砂,使型砂在 惯性作用下完成填砂和紧实
气冲造型
用蒸气或压缩空气瞬间膨胀所产 生的压力波紧实型砂
型砂不含粘结剂,被密封于砂箱
负压造型 与塑料膜之间,抽真空使干砂紧
实
设备结构简单,造价低,效率较高,紧实度 较均匀;但紧实度较低,噪声大。适用于成 批大量生产中小型铸件
③铸造圆角
设计制作模样时,相邻两壁之间的交角都应做成圆弧过渡的 铸造圆角。一般中、小型铸件的铸造圆角半径为3~5mm 。端盖 属小型铸件,未注铸造圆角均为R3~5mm 。
④起模斜度
为便于取模, 在模样或芯盒壁 上平行于起模方 向的表面所设计 的斜度。
起模斜度
JB/T5105—1991铸件模样起模斜度规定了砂型铸造 所用的起模斜度,如表2.2.7所示。
2.2 常用的铸造方法
2.2.1砂型铸造及产品生产检验(实训教学内容) 2.2.2 少、无切削的铸造方法(特种铸造) 2.2.3 常用铸造方法比较
2.2.1 砂型铸造及产品的生产检验
砂型铸造是指用型砂紧实成型的铸造 方法。是工业生产中应用最广泛的一种铸 造方法。
1.砂型铸造工艺简介
2.铸件的生产
3.铸件的检验
单件小批量生产具有二个分型 面的铸件
生产批量不大的大、中型质量 要求不高的铸件可节省下箱
整模造型
分 模 造 型
挖砂造型
假箱造型
活块造型
刮板造型
三箱造型
地坑造型
表2.2.3 常用的机器造型方法的主要特点和适用范围
造型方法
原理
主要特点和适用范围
震压造型
先以机械震击紧实型砂,再 用较低的比压(0.15~ 0.4MPa)压实
兼有湿砂型和干砂型 的优点
单件、小批量生 产中、大型铝合 金铸件和铸铁件
自硬砂型
常用水玻璃或合成树脂做 粘结剂,原型砂自身的化 学反应硬化,一般不需要 烘烤,或只经低温烘烤
铸型强度高,能耗低,生产 效率高,粉尘少;但成本较 高,有时易产生粘砂等缺陷
单件或批量生产 各类铸件,尤其 是大、中型铸件
2)造型方法选择
便于造型起模,造型和制作模样都麻烦
的铸件
用特制的刮板代替实体模样造型,可显著降低 单件小批量生产等截面或回转 模样成本。但操作复杂,要求工人技术水平高 体大、中型铸件