常用的锻造方法
2.3 锻造工艺解析

机械制造工艺基础——锻压工艺
5、平锻机上模锻:
• 平锻机的主要结构与曲柄压力机相同。只因 滑块是作水平运动,故称平锻机。
机械制造工艺基础——锻压工艺
5、平锻机上模锻:
•平锻机上模锻的特点: (1)有两个分模面,可以锻出其他模锻方 法无法锻出的锻件。 (2)生产率高,400-900件/小时。 (3)锻件尺寸精确,表面粗糙度低。 (4)材料利用率达85-95%。 (5)非回转体及中心不对称的锻件较难锻 造。平锻机造价高。 (6)适合于带头部的杆类和有孔零件的模 锻成型。
机械制造工艺基础——锻压工艺
补充: 典型零件模锻工艺过程: (1)零件图纸的分析
(2)选择分模面
(3)确定锻孔
(4)确定模锻工序
(5)绘制锻件图
(6) 锻模设计
机械制造工艺基础——锻压工艺
(1)零件图纸的分析
• 汽车后闸传动杆零件,上下端面、四个大孔、 20.3孔的端面和8孔需机械加工,其余均需模 锻锻出。
机械制造工艺基础——锻压工艺
1、模锻件图的绘制:
4)锻模圆角: •所有两表面交角处都应 有圆角。一般内圆角半 径(R)应大于其外圆半 径(r)。 5)留出冲孔连皮: •锻 件 上 直 径 小 于 25mm 的孔,一般不锻出,或 只压出球形凹穴。
机械制造工艺基础——锻压工艺
1、模锻件图的绘制:
• 大于25mm的通孔,也不能直接模锻出通孔, 而必须在孔内保留一层连皮。 • 冲孔连皮的厚度s与孔径d有关,当d =30~ 80mm时,s =4~8mm。
机械制造工艺基础——锻压工艺
3.摩擦压力机上模锻
④ 摩擦压力机承受偏心载荷能力差,通 常只适用于单膛锻模进行模锻。对于形 状复杂的锻件,需要在自由锻设备或其 它设备上制坯。 •应用: 适合于中小件的小批生产。如铆钉、 螺钉、螺母、气门、齿轮和三通阀体等。
锻造的基本方法

冶金备件锻造的基本方法
A自由锻造
自由锻造的操作方法主要有:(1)镦粗。
它是使毛坯断面增大而高度减小的锻造工序。
常用这种工序制造齿轮,法兰盘等锻件。
(2)镦延。
指被锻工件断面减小,长度增加的一种工序,亦称拔长工序。
用于制造轴类等长件。
(3)冲孔。
冶金备件把坯料冲出透孔或不透孔的工序。
用于扩孔的准备工作。
(4)截断。
截断是在热状态下用凿子进行。
先从一面截,然后翻转工件再断,用尖头凿子除去端部形成的飞刺。
(5)弯曲。
弯曲通常在弯曲机上进行。
坯料弯曲处的加热温度应比其他部位高,以避免弯曲处的截面减小。
(6) 扭转。
冶金备件扭转工序用于锻造实心零件。
零件先在一个平面内锻打,然后旋转一定的角度锻打,例如锻造曲轴。
B模型锻造
模型锻造通常分开式模锻和闭式模锻。
(1)开式模锻。
这种方法在模膛周围的分模面处有多余的金属形成飞边。
也正由于飞边的作用,才促使金属充满整个模膛。
开式模锻应用很广,一般用于锻造较复杂的锻件。
(2)闭式模锻。
在整个锻造过程中模膛是封闭的,其分模面间隙在锻造过程中保持不变。
只要坯料选取得当,所获锻件就很少有飞边或根本无飞边,因而大大节约金属,减少设备能耗。
因制取坯料相当复杂,故闭式模锻一般多用在形状简单的锻件上,如旋转体等。
锻件缺陷的主要特征及产生的原因

1锻造概述1.1锻造利用冲击力或静压力使加热后的坯料在锻压设备上、下砧之间产生塑性变形,以获得所需尺寸、形状和质量的锻件加工方法称为锻造。
常用的锻造方法为自由锻、模锻、胎模锻。
1.2自由锻利用冲击力或静压力使经过加热的金属在锻压设备的上、下砧间向四周自由流动产生塑性变形,获得所需锻件的加工方法称为自由锻。
自由锻分为手工锻造和机器锻造两种。
手工锻造只能生产小型锻件,机器锻造是自由锻。
1.3锻造特点1.3.1自由锻造所用工具和设备简单,通用性好,成本低。
同铸造毛坯相比,自由锻消除了缩孔、缩松、气孔等缺陷,使毛坯具有更高的力学性能。
锻件形状简单,操作灵活。
1.3.2锻件和铸件相比锻件的优点1.3.2.1金属经过锻造加工后能改善其组织结构和力学性能。
铸造组织经过锻造方法热加工变形后由于金属的变形和再结晶,使原来的粗大枝晶和柱状晶粒变为晶粒较细、大小均匀的等轴再结晶组织,使钢锭内原有的偏析、疏松、气孔、夹渣等压实和焊合,其组织变得更加紧密,提高了金属的塑性和力学性能。
1.3.2.2铸件的力学性能低于同材质的锻件力学性能。
此外,锻造加工能保证金属纤维组织的连续性,使锻件的纤维组织与锻件外形保持一致,金属流线完整,可保证零件具有良好的力学性能与长的使用寿命采用精密模锻、冷挤压、温挤压等工艺生产的锻件,都是铸件所无法比拟的。
1.3.2.3锻件是金属被施加压力,通过塑性变形塑造要求的形状或合适的压缩力的物件。
这种力量典型的通过使用铁锤或压力来实现。
铸件过程建造了精致的颗粒结构,并改进了金属的物理属性。
在零部件的现实使用中,一个正确的设计能使颗粒流在主压力的方向。
铸件是用各种铸造方法获得的金属成型物件,即把冶炼好的液态金属,用浇注、压射、吸入或其它浇铸方法注入预先准备好的铸型中,冷却后经落砂、清理和后处理等,所得到的具有一定形状,尺寸和性能的物件。
因此,它在重型机器及重要零件的制造上有特别重要的意义。
1.4应用领域自由锻造是靠人工操作来控制锻件的形状和尺寸的,所以锻件精度低,加工余量大,劳动强度大,生产率也不高,因此它主要应用于单件、小批量生产。
锻造的原理及应用方法论文

锻造的原理及应用方法论文引言锻造是一种通过施加压力和热量的方式对金属材料进行变形加工的方法。
这种加工方法在制造业中得到广泛应用,可以用于生产各种复杂形状的金属制品。
本文将介绍锻造的原理、应用领域和方法论,以帮助读者更好地了解和运用这一加工技术。
锻造的原理锻造的原理基于金属材料在高温下具有可塑性的特性。
通过施加压力和热量,原始金属材料可以被塑造成所需的形状。
锻造可以分为冷锻和热锻两种方式。
冷锻冷锻是在室温下进行的金属锻造过程。
这种方法适用于某些金属材料,比如铝和铜,因为它们在室温下具有较好的可塑性。
冷锻可以用于制造一些细小和高精度的零件,例如螺栓和钉子。
热锻热锻是在高温下进行的金属锻造过程。
通过加热金属材料,使其达到较高的塑性,从而可以更容易地进行形状变化。
热锻适用于大多数金属材料,包括钢、铁和合金。
热锻广泛应用于汽车、航空航天和能源行业,可以制造大型零件和复杂结构。
锻造的应用领域锻造在许多行业中都得到了广泛应用。
以下是一些常见的应用领域:•汽车工业:锻造用于制造汽车发动机零件、传动系统和悬挂部件等。
通过锻造,这些零件可以具有更高的强度和耐久性。
•航空航天工业:锻造用于制造飞机发动机零件、飞行器结构和涡轮机叶片等。
这些零件需要具备优异的性能,以确保航空航天系统的安全性和可靠性。
•能源行业:锻造用于制造石油和天然气开采设备、核电站部件和风力发电设备等。
这些设备需要承受极端条件下的高压和高温,因此对材料的强度和耐腐蚀性要求较高。
•建筑业:锻造用于制造建筑结构和桥梁等。
通过锻造,可以制造出更坚固和耐久的金属构件,以确保建筑物的结构稳定性和安全性。
锻造的应用方法论在进行锻造加工时,需要遵循一定的应用方法论。
以下是一些常用的锻造方法论:1.设计合理的模具:根据所需的零件形状和尺寸,设计适合的模具。
模具的设计应考虑到材料的流动性和纹理。
2.控制合适的工艺参数:确定合适的锻造温度、压力和速度等工艺参数。
这些参数的选择影响着材料的塑性和最终产品的质量。
(完整版)锻造工试题及答案

锻造工注意事项:1.答卷前将装订线左边的项目填写清楚。
2.答卷必须用蓝色或黑色钢笔圆珠笔,不许用铅笔或红笔。
3.本份试卷共 5道大题,满分 100 分,考试时间90 分钟。
一、填空题(请将正确答案填在横线空白处,每空1分,共10题20分)1.钢坯加热温度超过其始锻温度会产生 、 等缺陷。
2.锻件必须有合理的锻造流线分布,设计锻件时应尽量使零件工作时的正应力与流线方向相 ,而使切应力与流线方向相 ,并且使锻造流线的分布与零件的外轮廓相符合而不被切断。
3.常用的锻造方法有 , ,特种锻造等。
4.冲压的基本工序有冲裁,弯曲, , 等.5.锻造加热时的常见缺陷有过热,过烧,脱碳,氧化,开裂等,其中,过热和 是难以避免的,而过热和 是无法挽回的。
6.锻造前金属坯料加热的目的是为了降低其 和增加其 从而可用较小热的变形获得较大冷的变形。
7.在再结晶温度以上的变形是 变形,变形后金属坯料具有 组织,而无加工硬化痕迹。
8.冷变形后金属的强度、硬度提高,塑性、 下降,这种现象叫 。
9.金属坯料经热变形后会形成再结晶组织,且变形程度愈大,这种组织愈 ,它使金属的机械性能能带来 ,这种组织是用热处理来消除的。
10.金属在变形过程中承受的压应力愈多,其塑性越 ,变形抗力也越 。
二、选择题(请将正确答案的代号填入括号内,每题2分,共10题20分)1.下列是模锻特点的是 A成本低B效率低C尺寸精度高2.锻造前对金属进行加热,目的是 A提高塑性 B 降低塑性 C 增加变形抗力3.空气锤的动力是 A 空气B电动机 C 活塞4.为防止坯料在镦粗时产生弯曲,坯料原始高度应小于其直径 A1倍 B 2倍C 2.5倍5.镦粗时,坯料端面、应平整并与轴线 A垂直B平行 C 可歪斜6.自由锻件是 ,使坯料产生变形而获得所需的几何形状及内部质量的锻件。
A: 只用简单的通用性工具,或在锻造设备的上、下砧间直接对坯料施加外力,B: 用热挤压的方法C: 在棒料的一端进行锻造,7.锻造比是锻造时变形程度的一种表示方法, 。
锻造实训题库及答案解析

锻造实训题库及答案解析一、单项选择题1. 锻造过程中,金属材料的塑性变形主要发生在()。
A. 初始阶段B. 中间阶段C. 终了阶段D. 全过程答案:B2. 锻造工艺中,为了提高金属的塑性,通常采用()。
A. 降低温度B. 提高温度C. 保持室温D. 交替温度答案:B3. 在锻造过程中,金属材料的变形抗力随着温度的升高而()。
A. 增加B. 减少C. 不变D. 先增加后减少答案:B4. 下列哪项不是锻造的基本工序之一?A. 镦粗B. 拔长C. 切割D. 冲孔答案:C5. 锻造过程中,金属材料的变形量通常用()来表示。
A. 长度B. 宽度C. 厚度D. 真应变答案:D二、多项选择题6. 锻造工艺中,常用的加热设备包括()。
A. 电炉B. 燃气炉C. 感应炉D. 空气炉答案:A, B, C7. 锻造中,金属材料的塑性变形可以通过()来实现。
A. 压力B. 温度C. 速度D. 化学成分答案:A, B8. 锻造过程中,金属材料的变形抗力受哪些因素影响?A. 材料的化学成分B. 材料的初始温度C. 变形速度D. 变形程度答案:A, B, C, D三、判断题9. 锻造过程中,金属材料的塑性变形总是伴随着硬度的增加。
()答案:正确10. 锻造过程中,金属材料的塑性变形可以通过增加变形速度来实现。
()答案:错误四、简答题11. 简述锻造工艺中常见的几种锻造方法及其特点。
答案:锻造工艺中常见的锻造方法包括自由锻造、模锻、锤锻和压力机锻造。
自由锻造适用于形状简单的零件,操作灵活;模锻适用于形状复杂、精度要求高的零件,生产效率高;锤锻适用于中小批量生产,设备简单;压力机锻造适用于大批量生产,精度高,生产效率高。
五、计算题12. 若某金属材料在锻造过程中的真应变为2,求其变形量。
答案:真应变定义为ε = ln(Lf/Li),其中Lf为最终长度,Li为初始长度。
当ε=2时,Lf = Li * e^2。
变形量为Lf - Li,即Li* (e^2 - 1)。
常用的锻造方法
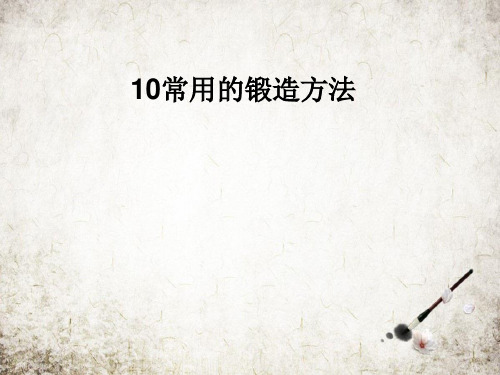
2武20汉20理/1工0/1大6学金工学部
2武30汉20理/1工0/1大6学金工学部 确定模锻件的机械加工余量及公差 机械加工余量一般为1~4 mm, 锻造公差一般取在±0.3~3 mm之间。
标注模锻斜度 当模膛宽度b小而深度h大时,
模锻斜度要取大些。内壁斜度要略大 于外壁斜度(a 2> a 1)。
2武0汉20理/1工0/1大6学金工学部
3.3.3.1 模锻件图的制定
选择模锻件的分模面
分模面即是上下锻模在模锻件上的分界面。 制订模锻锻件图时,必须按以下原则确定分模面位置: ➢要保证模锻件能从模膛中取出,分模面应选在模锻件最大 尺寸的截面上。 ➢按选定的分模面制成锻模后,应使上下两模沿分模面的模 膛轮廓一致,以便在安装锻模和生产中容易发现错模现象, 及时调整锻模位置。 ➢最好把分模面选在模膛深度最浅的位置处。这样可使金属 很容易充满模膛,便于取出锻件,并有利于锻模的制造。 ➢选定的分模面应使零件上所加的敷料最少。 ➢最好使分模面为一个平面,使上下锻模的模膛深度基本一 致,差别不宜过大,以便于制造锻模。
当镦粗的高径比 H / D > 2.5~3 时:
拔长:使坯料横截面面积减小,长度增加的锻造工序。适用于锻制长
轴类工件。拔长时将坯料沿轴向送进连续锻压,一次变形量为: 3/4方坯边长或0.4-0.8砧宽
规则:拔长矩形坯料时,要不断将坯料翻转90°,以免偏心与弯曲;
拔长园形坯料时,最好使用V形垫铁。
2武60汉20理/1工0/1大6学金工学部
弯曲模结构示意图
2武160汉20理/1工0/1大6学金工学部
3.3.2.2 固定模膛成型工艺的分类及设备
固定模膛成型工艺主要分为 锤上模膛成型工艺和压力机上模 膛成型工艺。
常用锻造方法的综合比较

常用锻造方法的综合比较一、自由锻造自由锻造是指将金属坯料加热至一定温度后,采用锤击或压力机等设备施加力,使其在自由形态下改变形状的一种锻造方法。
该方法操作简便,适用于小批量和单件生产。
优点:1.1 适应性强,可以锻造各种形状和尺寸的工件。
1.2 工艺灵活,易于调整工艺参数,适应不同的材料和产品需求。
1.3 适合加工复杂形状的零件,尤其是非标准件和特殊用途部件。
缺点:2.1 生产效率较低,适合小批量生产,不适合大规模生产。
2.2 成品的一致性和精度较低,难以保证每件工件的尺寸和性能完全一致。
2.3 工艺控制要求高,需要技术熟练的操作工。
二、模锻模锻是将金属坯料加热至适当温度后,置于特定的模具中,通过模具的挤压或冲击力使金属在模具中成形的一种锻造方法。
模锻适用于大批量生产,并且具有较高的生产效率。
优点:1.1 能够实现大批量生产,生产效率高。
1.2 工件尺寸精度高,表面光洁度好。
1.3 由于使用模具,产品的一致性较好,可以保证生产的每一件产品具有相同的质量和性能。
缺点:2.1 模具成本高,适合于批量生产,对小批量生产不经济。
2.2 模具设计和制造难度大,前期投入大。
2.3 对材料的要求较高,需要对材料的流动性和填充性进行精确控制。
三、闭模锻造闭模锻造是指在模具内施加压力,使金属在闭合的模具内成形。
闭模锻造可以提供更高的尺寸精度和表面质量,适用于复杂形状的工件。
优点:1.1 精度高,工件的尺寸和形状稳定。
1.2 表面质量好,减少了后续加工的需求。
1.3 能够生产出复杂形状的工件,提高了锻造产品的附加值。
缺点:2.1 模具成本和维护费用高。
2.2 工艺复杂,对设备的要求较高。
2.3 模具的设计和制造周期长,前期准备工作较多。
四、热模锻造优点:1.1 适用于高强度材料和大尺寸锻件,材料流动性好。
1.2 能够改善金属的力学性能,如提高强度和韧性。
1.3 对材料的加工性能要求低,可以加工难以锻造的材料。
缺点:2.1 热能消耗大,生产成本较高。
- 1、下载文档前请自行甄别文档内容的完整性,平台不提供额外的编辑、内容补充、找答案等附加服务。
- 2、"仅部分预览"的文档,不可在线预览部分如存在完整性等问题,可反馈申请退款(可完整预览的文档不适用该条件!)。
- 3、如文档侵犯您的权益,请联系客服反馈,我们会尽快为您处理(人工客服工作时间:9:00-18:30)。
• Beginning temperature(始锻温度)—as high as possible • For carbon steel,the beginning temperature is 150~250℃ below the AE line. • Ending temperature(终锻温度)—as low as possible(ensure enough ductility)
(1)饼块类和空心类锻件 通常采用镦粗法,坯料的高径比应为H/D≤2.5~3 坯料的直径或边长可按下式计算: 圆截面坯料:D计 ≥0.8(V坯)1/3 方截面坯料:A计≥0.74(V坯)1/3 D计—圆截面坯料计算直径, A计—方截面坯料的计算 边长 (2)轴类锻件: 通常采用拔长法,拔长后的最大截面应达到规定的 锻造比要求。 F坯≥y· Fmax F坯—坯料的截面积, Fmax—拔长后的最大截面积 圆截面坯料:D计 ≥(y)1/2Dmax
• 二、工艺规程的制定
• 1、Draw up a forging drawing(绘制锻件图) • 以零件图为基础并考虑下列因素绘制而成的: • (1)余块—为简化锻件形状、便于锻造而增加的 一部分金属。 • (2)Machining allowance(锻件余量)—为后 续切削加工而留的加工余量。 • (3)Forging tolerance(锻件公差)—锻件名义 尺寸的允许偏差。 • 锻件图的画法: • 如图2-34 ,以粗实线表示锻件的形状、双点划线 表示零件的基本形状;零件尺寸注在锻件相应尺 寸下面的括号内。
• 2.blocking die cavity(预锻模膛 ):使坯料变形到 接近于锻件的形状和尺寸。 • 特点:预锻模膛的圆角和斜度较大 ,且没有飞边槽。 • 3.blank making die cavity(制坯模膛):使坯料形 状基本接近于锻件的形状。 • 根据锻件复杂程度的不同,锻模分为: • 单膛锻模:在一副锻模上只有一个终锻模膛。 • 多膛锻模:在一副锻模上具有两个或以上的模膛 。
2、The choice of forging operations(选择变形工 步) • 根据工步的特点及锻件的形状、尺寸、技术要求和 生产批量等来确定。 • 包括确定锻件成形所需的基本工序、辅助工序和精 整工序的工步,以及所需的工具,确定工步的顺序 及变形尺寸等。 • 各类自由锻件的基本变形工步方案见表2-4。 • 3、The calculation of blank`s quantity and size (计算坯料重量和尺寸) • 锻造用的坯料有两类:钢材和钢坯,用于中、小型 锻件;另一类为铸锭,用于大、中型锻件。
• (二)Technological process of closed die forging(模锻件图的制定)
• 1.Parting plane(分模面):上、下锻模在模锻件 上的分界面。 • Several rules • (1)分模面应选在锻件最大尺寸的截面上; • (2)为便于发现错模现象,应使上、下模的模膛外形 一致; • (3)为便于金属充满模膛,便于取出锻件和锻模的制 造,最好把分模面选在使模膛具有最浅的方向上; • (4)使零件所加的余块最少; • (5)使分模面为平面,上、下模膛的深浅基本一致。
• (4)选定设备吨位 • 参照表2-7 ,此锻件属圆环类,选择0.5吨的自由 锻锤。
四、自由锻零件的结构工艺性(Structural design for open die forgings) • 1.应避免锻件上有圆锥体或斜面的结构。
• 2.圆柱体与圆柱体的交接处锻造很困难,应改成平 面与圆柱或平面与平面相连;
• 3 .加强筋与表面凸台难以用自由段的方法锻出,工 字形截面或空间曲线形表面,也应避免; • 4 .横截面有急剧变化或形状复杂的零件,应分成几 个易锻造的简单部分,再用焊接或机械连接的方法 组合成整体。
• 3.4、模锻( Closed die forging) • 模锻是将加热后的坯料放入锻模的模膛内锻压成型 的方法。 • 其特点是坯料变形时,金属的流动受到模膛的限制 和引导,因此获得与模膛形状一致的锻件。
• 根据计算的坯料直径或边长后,参照有关标准,确 定坯料的实际直径或边长,然后计算出坯料的长度。
• 热轧圆钢的标准直径见表2-6。 • 采用钢锭为坯料的大型锻件,可根据实际经验估算 钢锭重量。
• 锻件的钢锭利用率约为0.50~0.65,锻造比通常取 2.5~5。
• 4、选择锻造设备 • 根据锻件的材料、尺寸和重量,并考虑实际生产的 条件。按表2-7选择。 • 5、确定锻造温度范围
• 锤上模锻能完成镦粗、拔长、滚挤、弯曲、成形、 预锻和终锻等变形工步的操作,锤击力量和锤击频 率可自由控制和变换,可完成各种长轴类和短轴类 锻件的模锻。
• 其适用性较好,设备费用相对较低,是目前用得最 多的一种模锻方法。 • 缺点是:振动和噪音大、劳动条件差、机械化程度 不够高,生产率也不太高,在大批量生产中有被压 力机模锻取代的趋势。
• 三、工艺规程举例
• 图2-35齿轮坯自由锻工艺: • (1)绘制锻件图: • 齿轮上的轮齿、小的凹槽、凸肩以及轮辐上的8个φ30的孔, 自由锻难以锻出,需加余块; • 查表2-2的锻件的加工余量和公差为a=10±4, b= 9±3, c= 13±5, 绘出锻件图。
• (2)确定变形工步
• 参照表2-4,主要变形工步是镦粗和冲孔和扩孔, • 凸肩采用垫环局部镦粗,内孔较大,应用冲子扩孔。 • 注意:冲孔和扩孔时,金属会沿径向流动,并沿凸 肩高度方向产生拉缩现象,因此,局部镦粗后的径 向尺寸要小些、凸肩的高度要大些。
• (3) Hydraulic press (液压机或水压机)
• 利用高压水的压力代替锻锤的冲击力。其吨位用压 力表示,可锻造<300吨的铸锭,且锻透深度较大, 但设备投资较大。
• 3.自由锻的工序(Forging operations) • 1.Basic operations(基本工序)—使金属材料产 生一定的塑性变形,以达到所需形状和尺寸的工艺 过程。包括镦粗、拔长、冲孔、弯曲、扭转、错移 等。 • 2.Assistant operations(辅助工序)—为方便基 本工序操作而进行的预变形,如倒棱、压肩等。
• •
• •
空气锤
• (2)Steam-air -operated hammer(蒸气-空气 锤)
• 利用蒸气或压缩空气带动锤头工作,它的吨位稍大, 最大锻件质量<1500Kg, 但需要一套辅助设备(蒸 气锅炉或空气压缩机)。
• 主要组成部分有工作气缸1、落下部分2、机架3、 砧座4和操作手柄5等。
• 2.Machining allowance, tolerance (加工余量和公差)
• 三.锤上模锻工艺( ( drop forging technology) • (一)The procedures and die cavities • 模锻的变形工步分为制坯工步(preforming)和模锻工步(die foring) • 制坯工步使坯料初步成形,模锻工步完成锻件的最终成形。 • 相应的模锻模膛分为制坯模膛 、预锻模膛和终锻模膛。 • 1.finishing die cavity(终锻模膛):使坯料最后变形到锻 件所需的形状和尺寸。 • 特点: • (1)形状与锻件相同, • (2)尺寸放大一个收缩量,钢件取1.5% • (3)沿模膛四周有飞边槽(flash gutter), 其作用: • (a)增加金属从模膛中流出的阻力; • (b)容纳多余的金属; • (c)减缓上、下模的冲击。
• (3)计算坯料的重量和尺寸 • G锻=V锻· =17.8kg • 冲孔芯料的重量:取d=60mm, H=65mm, K2=1.3 (见表2-5) • G芯= K2 d2H=0.3kg • 烧损重量:需加热两次,系数K1=0.035 • G烧= G锻K1=0.6kg • G坯= G锻+ G芯+ G烧=18.7kg • 坯料的计算直径:D计 ≥0.8(V坯)1/3 • D计 =0.9(V坯)1/3=0.9(18.7/7.85)1/3=120mm • 查表2-6,选择坯料直径120mm • 坯料长度= V坯/A=210mm • 因此确定坯料的尺寸为φ120×210mm
• 3-3..自由锻(Open die forging)
• • • • 一General introduction 1、分类: Manual hammering and machine 机器自由锻根据锻造设备的不同,分为锤上自由锻 和水压机自由锻。 2、Equipments The hammer and the press are the two general types of forging equipments.The commonly used equipment in open die forging is : (1)Air-lift hammer(空气锤) 工作原理:电动机通过传动机构带动压缩缸内的压 缩活塞做往复运动。其吨位较小(50~750 Kg), 最 大锻件质量<100Kg
• Advantages: • (1) 使用工具简单,不需昂贵的模具; • (2)可以锻造各种重量的锻件,大型锻件,它 几乎是唯一的方法; • (3)所需的设备吨位较低。 Disadvantages: • (1)锻件的尺寸精度较低,加工余量大; • (2)锻件的形状受到一定的限制(比较简单); • (3)生产率较低,劳动强度大。 • 应用:单件小批量生产。
• 一.The comparison between closed die forging and open die forging • Advantages: • 1.high production rates • 2.higher dimensional accuracy • 3.more complicated shapes can be produced. • 4.save materials, lower cost in mass production.