常用铸造工艺对比
重力浇铸和压铸的区别专业知识讲座

Page: 5
文档来源于网络,文档所提供的信息仅供参考之用,不能作为科学依据,请勿模仿。文档如有
低压铸造
不当之处,请联系本人或网站删除。
低压铸造的工艺过程为:在密封的坩埚(或密封罐)中,通入干燥的压缩空气,金属液在气体压 力的作用下,沿升液管进入直浇道上升,通过内浇道平稳地进入型腔,并保持坩埚内液面上的气 体压力。直到铸件完全凝固为止。然后解除液面上的气体压力,使升液管中未凝固的金属液流回 坩埚。 再开型并取出铸件。
Page: 3
文档来源于网络,文档所提供的信息仅供参考之用,不能作为科学依据,请勿模仿。文档如有
高压铸造
不当之处,请联系本人或网站删除。
压力铸造分为高压铸造和低压铸造两种。
高压铸造是一种将熔融合金液倒入压室内,以高速充填钢制模具的型腔,并使合金液在压力下凝 固而形成铸件的铸造方法。
高压压铸区别于其它铸造方法的主要特点是高压和高速。 ①金属液是在压力下填充型腔的,并在更高的压力下结晶凝固,常见的压力为 15—100MPa。 ②金属液以高速充填型腔,通常在 10—50米/秒,有的还可超过80米/秒,(通过内浇口导入型
优缺点对比艺 复杂
模具 模具 气孔 费用 寿命 率
高短 差
热处 加工 表面 适宜产品 生产效率 理 余量 光洁
不可 小 高 薄壁件 高
低压铸造 简单 低 长 好 重力浇铸 简单 低 长 好
可以 大 高 中
中
可以 大 低 厚壁件 低
在强度方面,由于所事宜的铝合金原材料不同,其强度差异也较大: 压铸产品由于在高压下成型,产品致密性高,其强度较高。比如 A380的压铸产品,其强度可达到 360MPa,而其延伸率只能达到 3.7%左右。 重力浇铸产品一般情况强度要较压铸低。其材料较好的 ZL101A,热处理后也只能达到有310MPa, 但其延伸率较高,能达到5-6%。也有强度能达到380MPa以上的材料,如ZL201A、ZL204A 。
铸造工艺对比.ppt

定义 差压铸造是在低压铸造 的基础上,铸型外罩个
密封罩,同时向坩埚和 罩内通入压缩空气,但 坩埚内的压力略高,坩 埚内的金属液在压力差
的作用下经升液管充填 铸型,并在压力下结晶 的一种铸造方法。
定义 低压铸造是液体金属在 压力作用下,完成充型 及凝固过程而获得铸件 的一种铸造方法。由于 作用的压力较低(一般 为20~60kPa),故称 为低压铸造。
工艺特点对比
铸造 方法
高压 铸造
重力 铸造
差压 铸造
低压 铸造
工艺 复杂 简单 简单 简单
模具 费用
高
低
低
低
模具 寿命
短
气孔率 热处理
差
不可
加工 余量
小
长
好
可以
大
长
好
可以
大
长
好
可以
大
表面 光洁
高
适宜 产品
薄壁件
生产 效率
高
低 厚壁件 低
高
中厚 壁件
中
中
中厚 壁件
中
力学性能对比
350
高
300性Leabharlann 能 可 重 减优缺点及应用
HPDC 高压铸造
优点 1) 产品质量好。由于压铸型导热快,金属冷却迅速,同时在压力下结晶,铸件具有细的晶粒组织,表面坚 实,提高了铸件的强度和硬度,此外铸件尺寸稳定,互换性好,可生产出薄壁复杂零件; 2) 生产率高,压铸模使用次数多; 3) 经济效益良好。压铸件的加工余量小,一般只需精加工和铰孔便可使用,从而节省了大量的原材料、加 工设备及工时。 缺点 1) 模具结构复杂,制造费用高,准备周期长,所以,只适用于定型产品的大量生产; 2) 压铸速度高,型腔中的气体很难完全排出,加之金属型在型中凝固快,补缩可能性小,致使铸件容易产 生细小的气孔和缩松,铸件壁越厚,这种缺陷越严重,因此,压铸一般只适合于壁厚在6mm以下的铸件; 3) 压铸件的塑性低,不宜在冲击载荷及有震动的情况下工作; 4) 另外,高熔点合金压铸时,铸型寿命低,影响压铸生产的扩大应用。 应用 1)圆盘、圆盖、圆环类—泵壳罩壳 、轴承保持器、方向盘等; 2)筒体类—凸缘外套、导管、壳体形状的罩壳盖、上盖、仪表盖、探控仪表罩、等; 3)多孔缸体、壳体类—汽缸体、汽缸盖及油泵体等多腔的结构较为复杂的壳体等动力总成件; 4)特殊形状类—叶轮,喇叭、字体由筋条组成的装饰性压铸件等。
不同铸造工艺下含镁合金的显微组织

02 铸造工艺简介
砂型铸造
定义
砂型铸造是一种使用砂型模具进 行铸造的方法,通过将熔融的金 属倒入模具中,冷却后形成铸件
。
特点
砂型铸造工艺简单、成本低,适用 于生产各种形状和尺寸的铸件。
应用
广泛应用于汽车、机械、航空航天 等领域。
金属型铸造
定义
金属型铸造是一种使用金属模具进行铸造的方法 ,模具通常由耐热钢材或铝合金制成。
铸造压力对含镁合金显微组织的影响较为复杂。
详细描述
在一定范围内,增加铸造压力可以促进镁合金的致密化,减少孔隙和疏松,从而 改善显微组织。但过高的铸造压力可能导致晶粒破碎,反而影响显微组织的结构 。
模具材料对显微组织的影响
总结词
模具材料的性质和热传导性对含镁合 金的显微组织有一定影响。
详细描述
模具材料的热传导性越好,合金在冷 却过程中的温度梯度越小,从而减少 显微组织的各向异性。另外,模具表 面的粗糙度也会影响合金的凝固和显 微组织的形成。
由于砂型透气性较差,容易产生气孔和夹杂物。
力学性能
由于组织不够细密,砂型铸造的镁合金力学性能相对较低。
金属型铸造显微组织特点
1 2
晶粒细化
金属型散热性好,能够促进晶粒细化,提高组织 能产生气孔和 夹杂物。
3
力学性能
由于晶粒细化,金属型铸造的镁合金力学性能相 对较高。
不同铸造工艺下含镁 合金的显微组织
目录
CONTENTS
• 引言 • 铸造工艺简介 • 不同铸造工艺下含镁合金的显微组织特
点 • 铸造工艺对含镁合金显微组织的影响 • 实验方法与结果分析 • 结论与展望
01 引言
研究背景与意义
随着工业的快速发展,对轻质、高强度的材料需求日益增加 。镁合金作为一种具有优良性能的金属材料,在汽车、航空 航天、电子等领域得到广泛应用。
三种熔炼铸造工艺的对比研究

计 算 依 据 如下 [: 1 铸 件 工 艺 出 品率 按 7 %, 地 价 为 1 0 征 7万 , ; 亩 冲天 炉 焦 铁 比为 11 , :0 焦炭 价 为 2 0 5 0元 / ; 吨 石 灰 石 占焦炭 比例 3 %, 灰 石 10元 / ; 0 石 6 吨 脱 硫 剂 占铁液 含 量 2 , % 脱硫 剂 10 60元 / ; 吨 焦 炭 损 失 按 5 ; 冲 天 炉 每 吨 铁 液 风 机 用 电 量 %
短 流 程 用 电 量 :0 0 / ×10 k / = 0 ×1 300 t a 0 Wh 30 t 4 0
k h/ W a。
以上 费用 合 计 :4 9元 / 48 吨铸 件 () 2 中频 感 应 炉熔 炼 时 , 化 1吨铁 液需 要 8 0 Wh 熔 0k ,
运 行 费用 如 下 :
生铁 价 40 0 0元 / ; 吨
4 0力 兀 , 风 除 1 0 0 通 5 0刀 兀 风 1 0 j , 风 通 0 0了 兀 通
l 设 备
尘 系统费用
10万 元 8
除尘系统费用
4 O万 元
除尘 系统费用
4 0万 元
每 吨铁 液 冲 天 炉 修炉 费用 为 3元 , 电炉 修 炉 费 用 为 1
表 2是 以年产 4万 吨 H 2 0铸 件 的专 业 铸造 企 业 。 T5
表 2 生 产 运 行 费用 比较 表 序号 项目 冲天炉 中频感应 电炉 铸造短 流程
显 著 。 因此 铸 造 结 合 短 流 程 直 接 浇 铸 已成 为 发 达 国家 铸
造 技 术 改 进 的 展 的 今 天 , 选用 什 么
冲 天炉 用 电量 :0 0 / ×1 Wht 4 0 0 Wh ; 30 0 t a 5k / = 5 0 0k / a
精密铸造4种制壳工艺特点分析及改进方向探讨
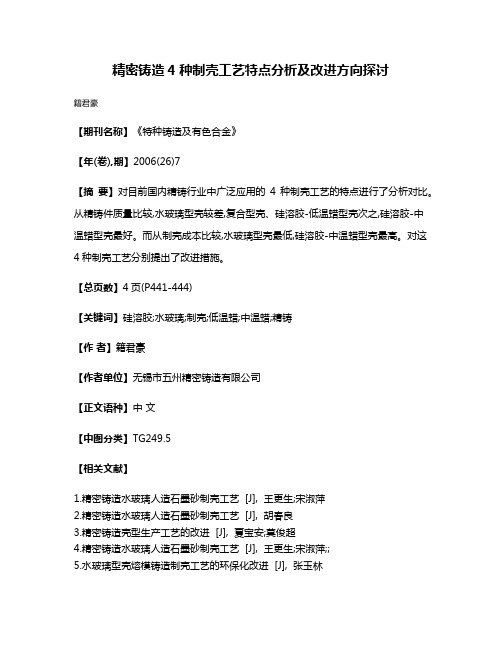
精密铸造4种制壳工艺特点分析及改进方向探讨
籍君豪
【期刊名称】《特种铸造及有色合金》
【年(卷),期】2006(26)7
【摘要】对目前国内精铸行业中广泛应用的4种制壳工艺的特点进行了分析对比。
从精铸件质量比较,水玻璃型壳较差,复合型壳、硅溶胶-低温蜡型壳次之,硅溶胶-中温蜡型壳最好。
而从制壳成本比较,水玻璃型壳最低,硅溶胶-中温蜡型壳最高。
对这4种制壳工艺分别提出了改进措施。
【总页数】4页(P441-444)
【关键词】硅溶胶;水玻璃;制壳;低温蜡;中温蜡;精铸
【作者】籍君豪
【作者单位】无锡市五州精密铸造有限公司
【正文语种】中文
【中图分类】TG249.5
【相关文献】
1.精密铸造水玻璃人造石墨砂制壳工艺 [J], 王更生;宋淑萍
2.精密铸造水玻璃人造石墨砂制壳工艺 [J], 胡春良
3.精密铸造壳型生产工艺的改进 [J], 夏宝安;莫俊超
4.精密铸造水玻璃人造石墨砂制壳工艺 [J], 王更生;宋淑萍;;
5.水玻璃型壳熔模铸造制壳工艺的环保化改进 [J], 张玉林
因版权原因,仅展示原文概要,查看原文内容请购买。
铸造工艺与轧制工艺-概述说明以及解释
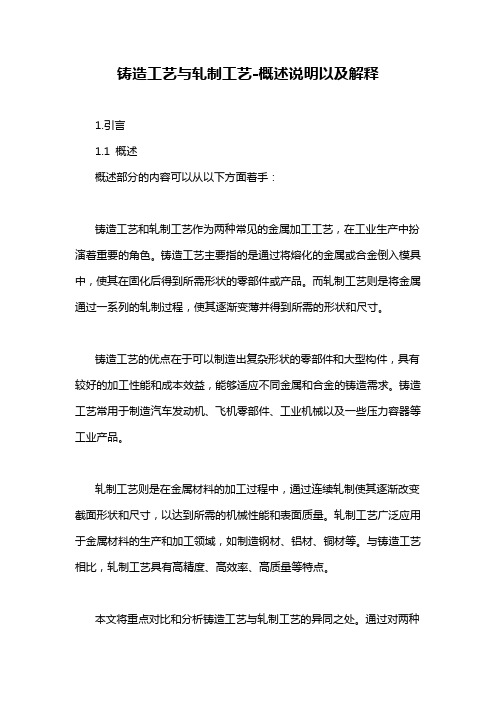
铸造工艺与轧制工艺-概述说明以及解释1.引言1.1 概述概述部分的内容可以从以下方面着手:铸造工艺和轧制工艺作为两种常见的金属加工工艺,在工业生产中扮演着重要的角色。
铸造工艺主要指的是通过将熔化的金属或合金倒入模具中,使其在固化后得到所需形状的零部件或产品。
而轧制工艺则是将金属通过一系列的轧制过程,使其逐渐变薄并得到所需的形状和尺寸。
铸造工艺的优点在于可以制造出复杂形状的零部件和大型构件,具有较好的加工性能和成本效益,能够适应不同金属和合金的铸造需求。
铸造工艺常用于制造汽车发动机、飞机零部件、工业机械以及一些压力容器等工业产品。
轧制工艺则是在金属材料的加工过程中,通过连续轧制使其逐渐改变截面形状和尺寸,以达到所需的机械性能和表面质量。
轧制工艺广泛应用于金属材料的生产和加工领域,如制造钢材、铝材、铜材等。
与铸造工艺相比,轧制工艺具有高精度、高效率、高质量等特点。
本文将重点对比和分析铸造工艺与轧制工艺的异同之处。
通过对两种工艺的概述以及关键要点的介绍,可以更好地了解它们在金属加工中的应用和优缺点。
最后,结合当前技术的发展趋势,展望铸造工艺和轧制工艺在未来的发展前景,以期为相关行业的科研和生产提供参考和借鉴。
1.2文章结构1.2 文章结构本文主要对比和探讨了铸造工艺与轧制工艺两个相关领域的工艺技术。
文章分为四个主要部分,包括引言、铸造工艺、轧制工艺和结论。
引言部分首先对整篇文章进行了简要的概述,介绍了铸造工艺和轧制工艺的基本概念和应用领域。
接着,文章说明了本文的文章结构和内容安排,给读者提供了整体的导引。
铸造工艺部分主要介绍了铸造工艺的概述,并阐述了铸造工艺的一些关键要点。
其中,铸造工艺要点1详细介绍了铸造工艺的原理和基本流程,包括模具制备、熔炼、浇注和冷却等工序。
铸造工艺要点2则讨论了不同类型的铸造工艺,比如压力铸造、砂型铸造和投掷铸造等,并分析了它们各自的优势和适用范围。
最后,铸造工艺要点3探讨了铸造工艺的一些常见问题和挑战,如气孔、缩孔和热裂纹等,并提出了相应的解决方案。
压铸工艺对比

NG
铝液
离型剂 压铸机 压铸机 压铸机
除气处理
旋转除气工艺,氮气净化(除气) 用片剂做溶液处理
除气动作为实施 除气动作为实施(不适合机边处理)
除气其他要求
最低要求使用带挡板的 行持续除气
旋转除气机进
除气动作为实施
晶体处理 铝合金晶体变质
目前未进行晶体建议
杂质过滤 溶液的机械式过滤
杂质净化
8、可按客户要求制作
9.所有生产用模具和模架必须用钢材 9、瑞振大模具用铸铁模架小模用钢模
制成,包括备用模架和镶块
;备用镶块都使用SKD61
1. 供应商现场必须要有三坐标检测必 须有自动模式。有记录功能的测量
1.瑞振拥有1台可全自动运行的三座标 测量机,可对检测结果进行打印、储 存。
2.供应商要有用于三坐标检测的点图/ 2.项目检讨时与客户确认测量方法及 图纸,检测点要供应商和SGM达成协议 坐标。
现有测漏机可进行
OK
3.在进行气泄露之前,铸件必须要完 全干燥,通常需要使用在线干燥机
现有测漏机可进行
OK
4.一些铸件同时要求进行 100% 流量
测试。如果要求流量测试,必须使用 自动设备。使用滚球或者 探头的方式
现有测漏机可进行泄漏量检测
OK
需要单独评估风险
5.气泄漏测试机控制单元要求具有自
动温度测量和补偿功能,或者放在有 测漏机摆放位置不满足要求
不了解要求是什么 不了解要求是什么 不了解要求是什么
4.如果由供应商设计铸件图纸,图纸 必须要由 PATAC DRE批准
NG
公司暂无设计产品能力
要求-铸件设计
5.如果供应商在铸件图的其他图纸之
铸造工艺对比

定义 差压铸造是在低压铸造 的基础上,铸型外罩个 密封罩,同时向坩埚和 罩内通入压缩空气,但 坩埚内的压力略高,坩 埚内的金属液在压力差 的作用下经升液管充填 铸型,并在压力下结晶 的一种铸造方法。
定义 低压铸造是液体金属在 压力作用下,完成充型 及凝固过程而获得铸件 的一种铸造方法。由于 作用的压力较低(一般 为20~60kPa),故称 为低压铸造。
生产工艺
HPDC高压铸造
GDC重力铸造
CPC差压铸造
LPDC低压铸造
定义 高压铸造是在压铸机的 压室内,浇入液态的金 属或合金,使它在高压 和高速下充填型腔,并 且在高压下成型和结晶 而获得铸件的一种铸造 方法。
定义 重力铸造是利用地球重 力将液态金属浇入金属 材质的铸型中,并在重 力的作用下结晶凝固而 形成铸件的一种铸造方 法。
优缺点及应用 LPDC低压铸造
优点 1)充型速度可以准确控制,以获得最佳充型速度,液体金属充型比较平稳; 2)提高了金属的利用率,可减小冒口的尺寸或不设冒口,因此可以大幅度降低材料费和加工工时; 3)劳动强度低,劳动条件好,设备简易,易实现机械化和自动化,不受操作者熟练程度的影响; 4)采用底注式充型,金属液充型平稳,无飞溅现象,可避免卷入气体及对型壁和型芯的冲刷,提高了铸件 的合格率; 5)容易形成顺序性凝固,内部缺陷少;气体、杂物的卷入少;铸件致密度高。 缺点 1)浇口方案的自由度小,因而限制了产品; 2)铸造周期长,生产性差,为了维持顺序性凝固和金属液流动性,模温较高,凝固速度慢。 应用 适用于中等壁厚类且性能要求较高的产品,如车轮等底盘安全件。
工艺特点对比
铸造 方法 高压 铸造 重力 铸造 差压 铸造 低压 铸造
工艺
模具 费用
模具 寿命
- 1、下载文档前请自行甄别文档内容的完整性,平台不提供额外的编辑、内容补充、找答案等附加服务。
- 2、"仅部分预览"的文档,不可在线预览部分如存在完整性等问题,可反馈申请退款(可完整预览的文档不适用该条件!)。
- 3、如文档侵犯您的权益,请联系客服反馈,我们会尽快为您处理(人工客服工作时间:9:00-18:30)。
眼等铸造缺陷。
湿砂型铸造
粗糙度(Ra/μm): 可达25(一般50-400) 精度等级(CT): 8-10 适用产品:重量在500公斤以下的薄壁铸铁件。
消失模铸造
消失模铸造通常用泡沫塑料(EPS 、STMMA或EPMMA)制 作成与产品结构、尺寸完全一样的实型模型,经过浸涂耐火 涂料并烘干后,埋在干石英砂中振动造型,在负压状态下浇 入熔化的金属液,使泡沫塑料模型气化,被液体金属取代, 冷却凝固后形成的一次性成型铸造工艺。
等现象; 2、生产低碳合金钢时易增碳,不利于热处理。
消失模铸造
粗糙度(Ra/μm): 可达12.5(一般25-200)
精度等级(CT): 7-9
适用产品:适宜做壁厚均匀、结构复杂的箱体、壳类铸件。
适用材质排序:灰铸铁——非铁合金——普通碳素钢——球 墨铸铁——低碳钢及合金钢
覆膜砂铸造
覆膜砂铸造采用优质精选天然砂为砂基,经覆膜技术将 特殊性能的树脂覆与砂基表面,再将砂基制成薄壳(芯), 合箱后浇入熔化的金属液,冷却凝固形成的一次性成型铸造 工艺。
铸造
常
湿砂型铸造(翻砂)
用 消失模铸造
铸
造
覆膜砂铸造
工 水玻璃工艺
艺
熔模铸造
硅溶胶工艺
湿砂型铸造
湿砂型铸造是以型砂和芯砂为造型材料制成铸型,液态 金属在重力下充填铸型来生产铸件的铸造方法。
湿砂型铸造
优点: 砂型(芯)无需烘干、成本低、效率高,使用广泛、方
便,大约占所有砂型使用量的60~70%。
常用铸造工艺对比
——郭晓明
铸造
铸造是人类掌握比较早的一种金属热加工工艺,已有约 6000年的历史。中国约在公元前1700~前1000年之间已进入 青铜铸件的全盛期,工艺上已达到相当高的水平。被铸金属 有:铜、铁、铝、锡、铅等。
铸造
铸造——制作铸型,并将熔融金属浇入铸型,凝固后获 得具有一定形状、尺寸和性能金属零件毛坯的成型方法。
缺点: 1、工艺复杂且不易控制; 2、消耗材料较贵; 3、不适于大件的生产,一般不超过25kg。
熔模铸造
粗糙度(Ra/μm): 水玻璃工艺可达 6.3(一般12.5-25) 硅溶胶工艺可达 1.6 (一般6.3-12.5)
精度等级(CT):用于形状复杂、精度要求高、或很难进行其它 加工的小型零件,如涡轮发动机的叶片等。
熔模铸造
熔模铸造——用易熔材料制成与产品一样的模型,在模 型表面包覆若干层耐火材料制成型壳,再将模型熔化排出型 壳,从而获得无分型面的铸型,经高温焙烧后即可填砂浇注 的铸造方案。由于模型广泛采用蜡质材料来制造,故熔模铸 造又称为“失蜡铸造”。
熔模铸造
优点: 1、精度高; 2、可铸造形状复杂零件; 3、铸件最小壁厚可达0.5mm; 4、可生产碳素钢、合金钢、不锈钢、铜合金、铝合金等。
消失模铸造
优点: 1、无分型面,消除了因合箱、取模造成的缺陷; 2、可在理想位置设置合理浇冒口,减少了铸件内部缺陷; 3、负压浇铸,提高了组织致密度; 4、铸件无毛边毛刺; 5、可组合浇铸,提高生产效率; 6、可生产铸铁、铸钢、铸铜、铸铝等; 7、模具维护费用低。
消失模铸造
缺点: 1、生产厚大铸件时泡沫夹渣不易排出,导致使用中断裂
覆膜砂铸造
优点: 1、可浇铸薄壁产品; 2、废品率低; 3、生产效率高; 4、可生产铸铁、铸钢、铸铜、铸铝等;
缺点: 1、耗能多,成本高; 2、混砂工艺复杂; 3、大件铸造困难。
覆膜砂铸造
粗糙度(Ra/μm): 可达6.3(一般12.5-25) 精度等级(CT): 7-8 适用产品:广泛用于汽车发动机、柴油机、液压件等。