{TPM设备维护}现代设备TPM管理的理论与实践
TPM全面生产维护精益管理实战读书笔记
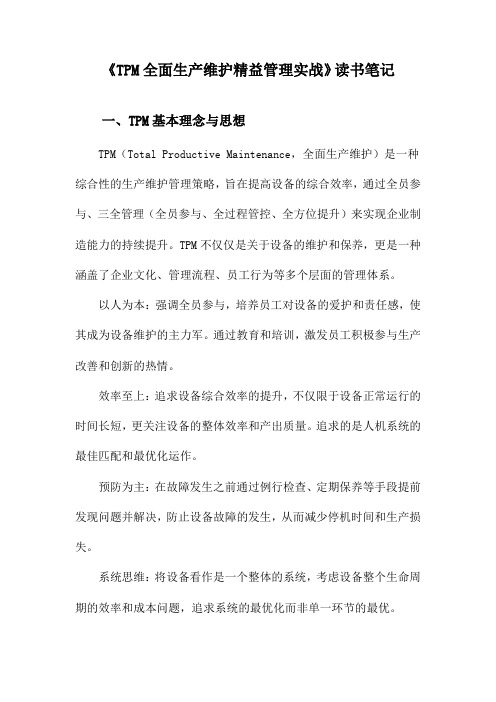
《TPM全面生产维护精益管理实战》读书笔记一、TPM基本理念与思想TPM(Total Productive Maintenance,全面生产维护)是一种综合性的生产维护管理策略,旨在提高设备的综合效率,通过全员参与、三全管理(全员参与、全过程管控、全方位提升)来实现企业制造能力的持续提升。
TPM不仅仅是关于设备的维护和保养,更是一种涵盖了企业文化、管理流程、员工行为等多个层面的管理体系。
以人为本:强调全员参与,培养员工对设备的爱护和责任感,使其成为设备维护的主力军。
通过教育和培训,激发员工积极参与生产改善和创新的热情。
效率至上:追求设备综合效率的提升,不仅限于设备正常运行的时间长短,更关注设备的整体效率和产出质量。
追求的是人机系统的最佳匹配和最优化运作。
预防为主:在故障发生之前通过例行检查、定期保养等手段提前发现问题并解决,防止设备故障的发生,从而减少停机时间和生产损失。
系统思维:将设备看作是一个整体的系统,考虑设备整个生命周期的效率和成本问题,追求系统的最优化而非单一环节的最优。
总效率的提升:不仅关注设备本身的效率,更关注整个生产流程的效率提升,包括生产准备、生产加工、质量控制等各个环节。
以自主管理为中心:倡导员工自主管理设备,通过日常点检、自主维修等手段,实现设备的自主维护管理。
开展小组活动:通过成立各种小组活动,如设备改善小组、创新小组等,鼓励员工积极参与设备的改善和创新工作。
构建企业文化:将TPM理念融入企业文化之中,使之成为企业共同的价值观和行动准则,从而推动企业的持续发展和进步。
1. TPM概述及发展历程TPM(Total Productive Maintenance,全面生产维护)是一种源于工业设备管理的思想和方法体系,它通过充分调动组织所有成员的积极性和创造性,提升设备的整体效能。
其主要目的在于将被动的事后维修变成主动的全过程维护,旨在实现设备的全面维护和生产效率的最大化。
TPM不仅仅是一种设备维护方法,更是一种管理理念和文化。
现代企业的设备管理-TPM的实施与培训
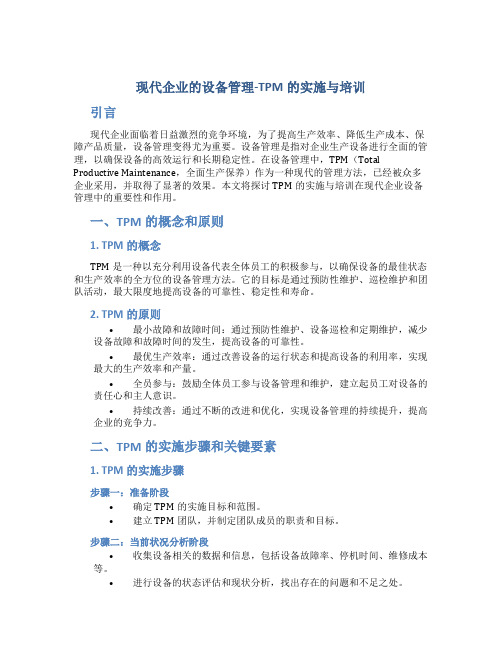
现代企业的设备管理-TPM的实施与培训引言现代企业面临着日益激烈的竞争环境,为了提高生产效率、降低生产成本、保障产品质量,设备管理变得尤为重要。
设备管理是指对企业生产设备进行全面的管理,以确保设备的高效运行和长期稳定性。
在设备管理中,TPM(Total Productive Maintenance,全面生产保养)作为一种现代的管理方法,已经被众多企业采用,并取得了显著的效果。
本文将探讨TPM的实施与培训在现代企业设备管理中的重要性和作用。
一、TPM的概念和原则1. TPM的概念TPM是一种以充分利用设备代表全体员工的积极参与,以确保设备的最佳状态和生产效率的全方位的设备管理方法。
它的目标是通过预防性维护、巡检维护和团队活动,最大限度地提高设备的可靠性、稳定性和寿命。
2. TPM的原则•最小故障和故障时间:通过预防性维护、设备巡检和定期维护,减少设备故障和故障时间的发生,提高设备的可靠性。
•最优生产效率:通过改善设备的运行状态和提高设备的利用率,实现最大的生产效率和产量。
•全员参与:鼓励全体员工参与设备管理和维护,建立起员工对设备的责任心和主人意识。
•持续改善:通过不断的改进和优化,实现设备管理的持续提升,提高企业的竞争力。
二、TPM的实施步骤和关键要素1. TPM的实施步骤步骤一:准备阶段•确定TPM的实施目标和范围。
•建立TPM团队,并制定团队成员的职责和目标。
步骤二:当前状况分析阶段•收集设备相关的数据和信息,包括设备故障率、停机时间、维修成本等。
•进行设备的状态评估和现状分析,找出存在的问题和不足之处。
步骤三:设备改善活动阶段•制定设备改善计划,包括改善目标、改善方法和改善时间表。
•实施设备改善活动,并记录改善效果。
步骤四:维护和巡检活动阶段•建立设备的维护计划和巡检计划。
•实施设备的预防性维护和巡检,并记录维护和巡检结果。
步骤五:员工培训和意识提升阶段•对员工进行TPM的培训,提高员工对设备管理的知识和技能。
关于TPM的理论及实例

04
TPM的效益与成果
提高设备综合效率(OEE)
总结词
通过全面预防性维护,TPM能够提高设备的整体效率,确保设备在最佳状态下运行。
详细描述
TPM采用预防性维护策略,定期检查、保养和维修设备,减少设备故障停机时间,提高设备运行效率,从而提升 整体生产效率。
降低维修成本
总结词
通过减少意外故障和预防性维护,TPM能够 降低维修成本,节约企业运营成本。
对设备发生的故障进行深入分析,找出 故障的根本原因,提出相应的改善措施 。
VS
技术改进
不断引进新技术和工艺,对设备进行技术 改进和升级,提高设备的性能和效率。
03
TPM实例分享
某制造企业的TPM实施案例
总结词
成功提升设备综合效率
详细描述
该制造企业通过推行TPM,实现了设备综 合效率的大幅提升。通过制定详细的TPM 推进计划,全员参与设备点检和保养,及时 发现并解决设备问题,确保设备稳定运行。 同时,加强员工培训和激励机制,提高员工 参与TPM的积极性和技能水平。经过一段 时间的实施,设备综合效率得到了显著提升, 生产成本大幅降低,产品质量也得到了有效 保障。
减少安全事故
总结词
TPM的实施可以减少设备故障和生产事故,保障员工的 人身安全和企业的财产安全。
详细描述
TPM强调设备的定期检查和维护,及时发现和解决潜在 的安全隐患,降低设备故障引发的事故风险,确保生产 过程中的安全。
05
TPM的未来发展与趋势
数字化技术在TPM中的应用1 2数字化技术
利用计算机、传感器、通信和数据处理等技术, 实现设备运行数据的实时采集、传输和分析,提 高设备运行效率和可靠性。
关于TPM的理论及实例
TPM全面生产维护:精益设备管理
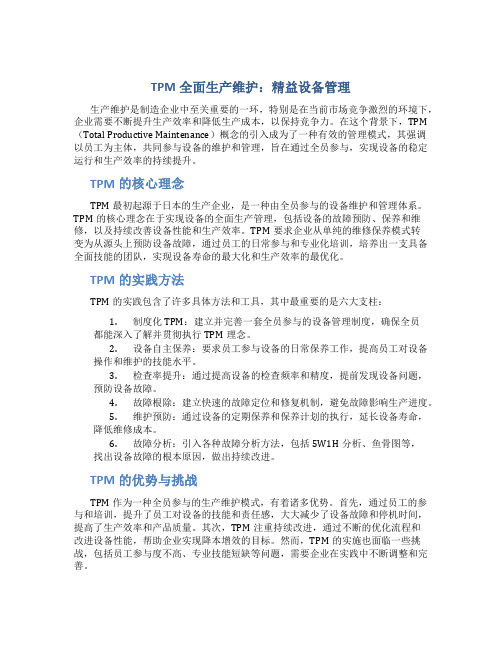
TPM全面生产维护:精益设备管理生产维护是制造企业中至关重要的一环,特别是在当前市场竞争激烈的环境下,企业需要不断提升生产效率和降低生产成本,以保持竞争力。
在这个背景下,TPM (Total Productive Maintenance)概念的引入成为了一种有效的管理模式,其强调以员工为主体,共同参与设备的维护和管理,旨在通过全员参与,实现设备的稳定运行和生产效率的持续提升。
TPM的核心理念TPM最初起源于日本的生产企业,是一种由全员参与的设备维护和管理体系。
TPM的核心理念在于实现设备的全面生产管理,包括设备的故障预防、保养和维修,以及持续改善设备性能和生产效率。
TPM要求企业从单纯的维修保养模式转变为从源头上预防设备故障,通过员工的日常参与和专业化培训,培养出一支具备全面技能的团队,实现设备寿命的最大化和生产效率的最优化。
TPM的实践方法TPM的实践包含了许多具体方法和工具,其中最重要的是六大支柱:1.制度化 TPM:建立并完善一套全员参与的设备管理制度,确保全员都能深入了解并贯彻执行TPM理念。
2.设备自主保养:要求员工参与设备的日常保养工作,提高员工对设备操作和维护的技能水平。
3.检查率提升:通过提高设备的检查频率和精度,提前发现设备问题,预防设备故障。
4.故障根除:建立快速的故障定位和修复机制,避免故障影响生产进度。
5.维护预防:通过设备的定期保养和保养计划的执行,延长设备寿命,降低维修成本。
6.故障分析:引入各种故障分析方法,包括5W1H分析、鱼骨图等,找出设备故障的根本原因,做出持续改进。
TPM的优势与挑战TPM作为一种全员参与的生产维护模式,有着诸多优势。
首先,通过员工的参与和培训,提升了员工对设备的技能和责任感,大大减少了设备故障和停机时间,提高了生产效率和产品质量。
其次,TPM注重持续改进,通过不断的优化流程和改进设备性能,帮助企业实现降本增效的目标。
然而,TPM的实施也面临一些挑战,包括员工参与度不高、专业技能短缺等问题,需要企业在实践中不断调整和完善。
TPM管理中的设备故障维修和质量控制

TPM管理中的设备故障维修和质量控制随着信息技术的迅猛发展,世界各国的经济和社会都已形成以电子、计算机、网络为核心的现代信息技术体系,使得现代工业已经向自动化、信息化方向快速发展,并大量使用各种现代工业设备,从而极大地提高了生产效率和生产质量。
为保证现代工业的稳定运行,设备故障维修和质量控制显得非常关键。
TPM(全称:Total Productive Maintenance,中文为全员生产保养)是日本企业普遍采用的一种维护管理技术。
一、TPM的基础理论和要素1、TPM的基础理论TPM是一种以保养、检修、诊断为主,以预防、预见机器故障为目的的维修管理计划,它强调设备故障维修和质量控制应由所有员工参与,把每台机器都看成是整个生产过程的一部分,在全员参与维护下可以最大限度地提高设备稳定性和产品质量。
2、TPM的要素TPM要素包括:企业理念、教育培训、员工参与、设备状态管理、全面预防维修、设备改进。
二、TPM管理中的设备故障维修和质量控制在TPM管理中,设备故障维修和质量控制是很重要的环节,它们对于提高设备稳定性和保证产品质量具有重要意义。
1、设备故障维修设备故障维修是TPM中很重要的一个方面,它可以帮助企业省去大量的维修成本,显著提高生产效率。
在设备故障维修中需要注意以下几点:(1) 定期进行设备巡检和保养,以减少设备故障的发生。
(2) 设备故障发生后,能够快速解决问题,减少停机时间。
(3) 根据设备故障的原因分析数据,采取相应措施进行改进,避免类似故障的再次发生。
(4) 在设备维修中,要注意保证安全,在维修人员进行维修时,必须严格遵守相关规定和安全制度。
2、质量控制质量控制是企业产品质量的保证,实施好质量控制可以提高产品的质量和公司的竞争力。
在TPM中,质量控制一般包括以下几种措施:(1) 使用可靠的设备和材料,确保产品的质量。
(2) 定期进行设备的检查和保养,尽量减少质量问题的发生。
(3) 实施质量改进活动,根据生产数据和反馈信息,优化生产过程,提高产品的质量和生产效率。
现代设备管理理论创新与实践(TPM TPEM TNPM)
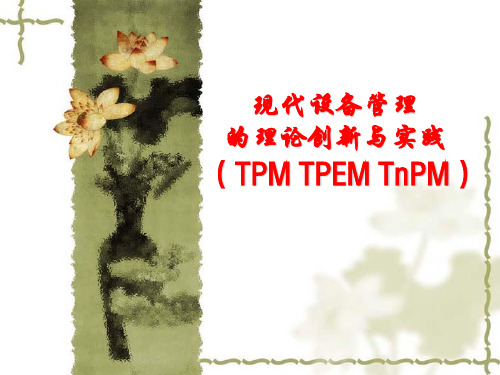
❖ 定义:为了实现组织的目标,所进行的计划、组 织、领导、控制和协调的诸过程。
❖ 管理的任务就是提高组织的效率和效能。 ❖ 有效管理的三要素: (1)管理意识 (2)管理方法 (3)员工的行动
2、什么是机制?
❖ 机制就是制度加方法或者制度化了的方法。 其含 义为“因为这个方法的存在,使得一件事不得不被 完成到最好” 。
现代设备管理 的理论创新与实践
(TPM TPEM TnPM)
目录
❖ 一、日本的TPM理论与实践 ❖ 二、欧美的TPEM理论与实践 ❖ 三、中国的TnPM理论与实践 ❖ 四、日本企业如何实施TPM ❖ 五、日本的启示与我们的差距 ❖ 六、中国企业的TPM之路
一、日本的TPM理论与实践
(一) TPM基础知识
❖ 1)对故障发生源进行有效的改善。
❖ 2)记录日常检查结果和发生故障的详细情况。
❖ 为了保证设备不出故障、不制造不良品,又出现 了“ 维 修预 防 ”(Maintenance Prevention , MP / 1961)。
❖ 从设备的设计阶段就开始对设备故障进行控制, 其最终目的是实现无故障和简便的日常维护。
❖ 1)设备购置时选型有误。过多地考虑技术储备,盲 目追求加工中心的兼容性,结果是在用精密机床加工 非精密、低附加值和低效率的零件,导致部分功能闲 置。
❖ 2)相关的工艺装备不配套。在刀具、夹具、量具、 软件、维修和环境等方面的投资不足,造成机床使用 的寿命和效率的低下。
❖ 3)工艺编排不合理。没有根据精益生产的“一个流” 去编排产品加工的工艺过程,只是根据设备的种类编 组,在某一工步或工序节省了部分时间,而没有从根 本上提高效率。
❖ MP是依据对设备的运行和维护情况的完整记录, 帮助设计人员对设备的结构进行改进。
现代设备TPM管理理论与实践

2019/4/8 12
作业时能够快速取用;
清扫:将作业场所中的灰尘、油污、垃圾清扫 干净,创造一个舒适的作业环境; 清洁:清除各类污染源(如废水、废气等), 杜绝各类跑、冒、滴、漏现象; 素养:员工应具有良好的职业素养,遵章守纪。 5S中的素养是核心。员工具有良好的素养,其 余四项就容易形成制度。
世界级企业对产品质量的要求已上升到“世纪级
质量”的标准,即世界最高水准的质量标准。这
些企业的产品合格品率通常都能达到98%左右的
水平,而美国通用电气公司实施的“6σ”管理,
容许产品的不合格率更是要求达到0.002ppm的十
亿分率的水平。而摩托罗拉公司通过6σ管理要求
所生产的产品合格品率达到99.9996%,也就是在
2019/4/8 4
目标则是减少维修费用,而这又是通过减少辅
助人员及提高生产效率加以实现的。
日本工程师学会为全员生产维修所下的
定义为: 以追求设备综合效率最高为目标; 建立以设备一生为目标的全系统的预防 维修;
与设备管理相关的所有部门的参与;
从企业最高管理层到一线员工的参与; 开展小组自主活动推进生产维修。
自主意识和团队精神,使员工自觉、自发地开展 TPM
管理中的各项活动,实现“生产设备非计划停机时间
2019/4/8 11
为零;由生产设备故障引发的产品缺陷为零;生产设
备的速度损失为零”的目标。
所谓“5S”活动的内容就是:
整理:将工作场所的各类物品有序地进行整理、 摆放,以便有条不紊地开展各项作业;
整顿:将要使用的各类物品根据定量、定位、使
2019/4/8 5
全员生产维修TPM特点是三全:全效率,全
试论现代企业设备管理理念以及TPM的有效应用

试论现代企业设备管理理念以及TPM的有效应用引言现代企业设备管理在企业运营中起着至关重要的作用。
合理的设备管理理念能够帮助企业提高生产效率、降低成本、改善产品质量和提升企业竞争力。
本文将首先介绍现代企业设备管理的基本理念,随后重点探讨TPM(全面生产维护)在设备管理中的有效应用,并针对实际案例进行分析和讨论。
现代企业设备管理理念现代企业设备管理理念包括预防性维护、设备的全面生命周期管理、故障排除和设备更新等。
下面将分别对这些理念进行详细阐述。
1. 预防性维护预防性维护是设备管理的基础,它通过定期检查、保养和维修设备,以预防设备故障和停机。
预防性维护的好处是显而易见的:它可以减少设备故障率,提高设备可靠性和稳定性,保证生产进程的顺利进行。
在实施预防性维护时,企业需要建立一套科学的维护计划,制定检修周期和维修工作内容,并且及时记录维修情况,为后续的维护提供数据支持。
2. 设备的全面生命周期管理现代企业设备管理不仅关注设备的日常维护,还需要在设备的整个生命周期内进行综合管理。
从设备的采购、配置、调试,到设备的使用、维护和淘汰,都需要有相应的管理措施和制度。
在设备的采购阶段,企业需要明确设备的功能需求、质量要求和性价比,并且进行供应商的评估和选择。
在设备的使用阶段,需要确保设备能够正常运行,并及时处理设备故障和异常情况。
在设备的淘汰阶段,需要根据设备的实际状况和性能表现,制定合理的更新计划,以及设备的处置方案。
3. 故障排除在设备管理过程中,难免会遇到各种故障和问题。
针对设备故障,企业需要建立一套完善的故障排除机制。
这包括及时报告故障、迅速定位故障原因、制定解决方案、及时修复故障等。
为了提高故障排除的效率,现代企业还可以利用先进的故障检测技术,如振动分析、红外热像仪和无损检测等,对设备进行全面的监测和诊断,以实现故障的早期发现和预警。
4. 设备更新设备更新是现代企业设备管理的重要环节。
对于旧化的设备,企业需要及时进行更新和升级,以适应市场需求的变化和技术的更新。
现代设备管理与全员生产维修TPM
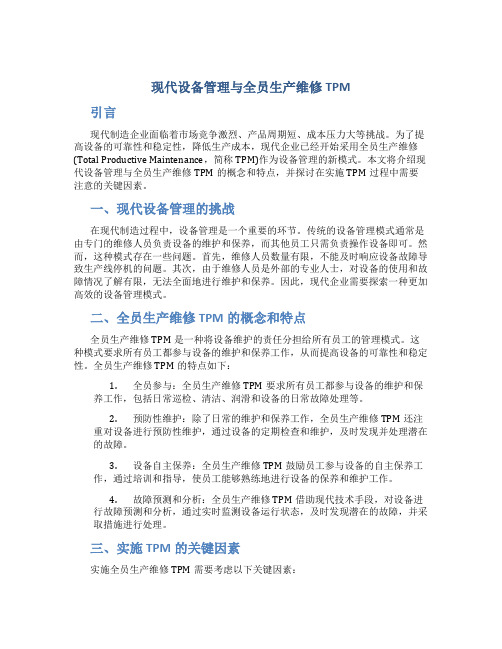
现代设备管理与全员生产维修TPM引言现代制造企业面临着市场竞争激烈、产品周期短、成本压力大等挑战。
为了提高设备的可靠性和稳定性,降低生产成本,现代企业已经开始采用全员生产维修(Total Productive Maintenance,简称TPM)作为设备管理的新模式。
本文将介绍现代设备管理与全员生产维修TPM的概念和特点,并探讨在实施TPM过程中需要注意的关键因素。
一、现代设备管理的挑战在现代制造过程中,设备管理是一个重要的环节。
传统的设备管理模式通常是由专门的维修人员负责设备的维护和保养,而其他员工只需负责操作设备即可。
然而,这种模式存在一些问题。
首先,维修人员数量有限,不能及时响应设备故障导致生产线停机的问题。
其次,由于维修人员是外部的专业人士,对设备的使用和故障情况了解有限,无法全面地进行维护和保养。
因此,现代企业需要探索一种更加高效的设备管理模式。
二、全员生产维修TPM的概念和特点全员生产维修TPM是一种将设备维护的责任分担给所有员工的管理模式。
这种模式要求所有员工都参与设备的维护和保养工作,从而提高设备的可靠性和稳定性。
全员生产维修TPM的特点如下:1.全员参与:全员生产维修TPM要求所有员工都参与设备的维护和保养工作,包括日常巡检、清洁、润滑和设备的日常故障处理等。
2.预防性维护:除了日常的维护和保养工作,全员生产维修TPM还注重对设备进行预防性维护,通过设备的定期检查和维护,及时发现并处理潜在的故障。
3.设备自主保养:全员生产维修TPM鼓励员工参与设备的自主保养工作,通过培训和指导,使员工能够熟练地进行设备的保养和维护工作。
4.故障预测和分析:全员生产维修TPM借助现代技术手段,对设备进行故障预测和分析,通过实时监测设备运行状态,及时发现潜在的故障,并采取措施进行处理。
三、实施TPM的关键因素实施全员生产维修TPM需要考虑以下关键因素:1.培训和教育:实施TPM前,必须对所有员工进行相关培训和教育,使其了解TPM的概念和原则,掌握设备的基本维护和保养知识。
TPM-全员设备管理与维护

TPM-全员设备管理与维护引言TPM(全员设备管理)是一种旨在改善设备管理和维护效率的方法。
它要求每个员工都有责任保护和维护公司的设备,以确保设备的正常运行和寿命。
本文将介绍TPM的基本概念和原则,以及如何实施TPM来提高设备管理和维护效率。
什么是TPM?TPM是Total Productive Maintenance(全员生产维护)的缩写,是一种由日本引入的管理方法。
它的目标是通过全员参与设备管理和维护,最大限度地减少设备故障和停机时间,提高设备的生产效率。
TPM强调的是预防性维护和日常保养,每个员工都有责任保持设备的运行状态良好。
通过养成良好的维护习惯,可以有效地减少设备故障和停机时间,提高设备的效率和寿命。
TPM的原则TPM基于以下几个基本原则:1.全员参与:TPM要求每个员工都参与设备管理和维护,包括机器操作员、维修人员、管理人员等。
每个员工都应该对设备的正常运行负责,并且能够及时发现和解决设备故障。
2.预防性维护:TPM注重预防设备故障而不是修复故障。
通过进行定期的保养和检查,可以提前发现设备问题并采取相应的措施,以减少故障和停机时间。
3.持续改进:TPM强调持续改进,通过不断地优化设备管理和维护流程,提高设备的效率和可靠性。
每个员工都应该提出改进建议,并参与改善活动。
4.操作员的自主性:TPM鼓励机器操作员参与设备管理和维护,使他们能够及时识别和解决设备故障。
操作员应该接受培训,具备一定的维修和故障排除能力。
TPM的实施步骤要实施TPM,可以按照以下步骤进行:1.培训和意识提高:为所有员工提供TPM培训,使他们了解TPM的概念和原则,以及他们在设备管理和维护中的角色和责任。
同时,提高员工对设备管理和维护的重要性的意识。
2.制定设备管理计划:与设备管理团队合作,制定设备管理计划,包括设备的保养计划、检查标准、操作规程等。
确保计划能够实施,并进行定期的检查和评估。
3.建立设备管理团队:成立设备管理团队,包括设备操作员、维修人员和管理人员等。
TPM管理中的预防维护实践
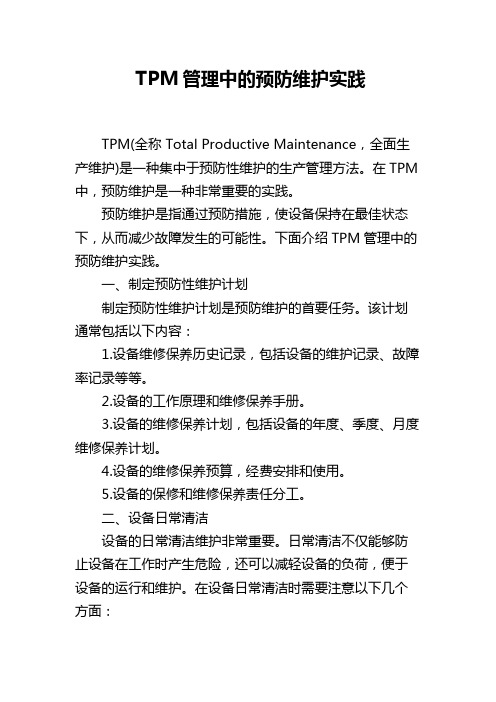
TPM管理中的预防维护实践TPM(全称 Total Productive Maintenance,全面生产维护)是一种集中于预防性维护的生产管理方法。
在TPM 中,预防维护是一种非常重要的实践。
预防维护是指通过预防措施,使设备保持在最佳状态下,从而减少故障发生的可能性。
下面介绍TPM管理中的预防维护实践。
一、制定预防性维护计划制定预防性维护计划是预防维护的首要任务。
该计划通常包括以下内容:1.设备维修保养历史记录,包括设备的维护记录、故障率记录等等。
2.设备的工作原理和维修保养手册。
3.设备的维修保养计划,包括设备的年度、季度、月度维修保养计划。
4.设备的维修保养预算,经费安排和使用。
5.设备的保修和维修保养责任分工。
二、设备日常清洁设备的日常清洁维护非常重要。
日常清洁不仅能够防止设备在工作时产生危险,还可以减轻设备的负荷,便于设备的运行和维护。
在设备日常清洁时需要注意以下几个方面:1.理清设备的使用路线,按照清洗步骤逐一清洗每个部位。
2.选择合适的清洗工具和清洗液。
3.严格控制水用量。
4.对于设备上较难到达的部位需要采用手工清洗等方式。
三、设备润滑对于大多数设备而言,润滑也是预防维护的重点之一。
设备润滑需注意以下几个方面:1.设备使用受力部位的润滑必须保证正常工作。
2.润滑方式要符合设备使用流程。
3.选用润滑剂时需要按照设备的使用环境和外在因素进一步选择考虑。
4.严格按照润滑剂的使用说明进行涂抹,润滑剂的余量不要过高。
5.定期更换润滑剂,根据设备的使用情况来确定更换周期。
四、设备状态监测设备状态监测是预防维护的重要工作之一,通过对设备运行状态进行监测,有助于及早发现设备的问题并能够及时解决。
设备状态监测主要包括以下几个方面:1.通过设备的声音、震动、电流等数据来监测设备状态。
2.定期对设备的关键部位进行检查和维护。
3.对设备的润滑剂、机油、制冷剂等物质进行定期检查,并进行更换。
4.对于设备的工作环境进行检查,防止环境对设备的影响。
TPM管理中的设备维修和维护技术转移实践

TPM管理中的设备维修和维护技术转移实践随着TPM(全员参与的生产设备管理)越来越被重视,设备维修和维护技术转移也成为了企业中不可避免的问题。
本文将从TPM的角度出发,探讨如何做好设备维修和维护技术转移的实践。
一、设备维修和维护技术转移的意义设备是生产的基础,设备维修和维护是保证设备正常运转的重要环节。
TPM要求所有员工都参与设备管理,要求员工有维修和维护的能力。
设备维修和维护技术转移的意义在于:1.提高员工技能:通过技术转移,员工可以学习到更多的维修和维护知识,提高自己的技能水平。
2.提高设备可靠性:设备维修和维护技术转移能够保证设备得到及时的维修和维护,提高设备的可靠性,减少停机时间。
3.降低维修成本:通过技术转移,员工可以自己修复一些简单的故障,减少维修成本。
4.增强团队合作:技术转移需要员工之间相互合作,增强团队合作精神。
二、设备维修和维护技术转移实践设备维修和维护技术转移的实践包括以下几个方面:1.制定技术转移计划技术转移计划是设备维修和维护技术转移的基础。
企业制定技术转移计划时要将技术转移的内容、流程、时间、人员等因素考虑全面,确保计划可行。
计划制定完成后,要向员工宣传,提高员工对技术转移的认识和意识,让员工知道技术转移的意义和必要性。
2.培训教育技术转移是需要技能的支撑的,因此需要进行培训教育。
培训教育包括理论培训和实际操作培训。
理论培训主要是针对员工的基础知识和理论知识进行培训;实际操作培训则是利用实际设备进行操作,通过维修和维护实践,提高技能水平。
3.设立技术中心技术中心是技术转移的重要场所,企业要根据技术转移的实际情况,设立技术中心。
技术中心要配备必要的设备和工具,并培养一定的技术人员,确保技术中心能够有效开展技术转移工作。
4.建立维修和维护手册维修和维护手册是技术转移的重要依据,企业要根据设备具体情况,建立维修和维护手册。
维修和维护手册要详细说明设备的维修和维护方法、步骤、注意事项等内容,为员工提供操作指导和技术支持。
现代设备TPM管理的理论与实践

6
TPM的全系统生产维修体系
基础保养
生产维修
日常清洁、保养、 定期点检、润
点检
滑
2024/6/30
发现异常
事后维修
判断决策
突发故障
自主维修
维修计划
维修实施
设备分类
预防维修 维修计划 维修准备 维修实施
改善维修 分析论证 改善方案 方案实施
记录
总结
评价
建议
反馈
维修预防
制造厂设计改进
20
公司已经对供应商提出了精益制造的要求。 精益生产方式的核心思想在于“清除浪费,强调精简
组织结构”和“不断改善”。前者指的是从组织管理到生 产 过程,侧重分析“产品流”、“物资流”和“信息流”,
2024/6/30
及时暴 露问题,删繁就简,杜绝浪费,从而使“价值流”连续流 动 起来。后者则强调充分发挥人的潜能,力争精益求精,尽 善尽美,彻底消除浪费,体现出精益生产方式的精髓。
7
全员:操作者的自主维修。涉及设备寿命 周期各环节的所有部门及员工均应参加设备的 综合管理。全员管理包括两个层面:
纵向的全员:从企业高层管理到第一线的 操作工人参与TPM;2024/6/30
横向的全员:要求企业中生产、工艺、能 源动力、质检、设计、供应、物流以及环保等 所有部门都要参与TPM管理。
整顿:将要使用的各类物品根据定量、定位、使 用频率大小、标记化的原则,合理地加以布置,以便
11
作业时能够快速取用; 清扫:将作业场所中的灰尘、油污、垃圾清扫
干净,创造一个舒适的作业环境; 清洁:清除各类污20染24/6源/30 (如废水、废气等),
杜绝各类跑、冒、滴、漏现象; 素养:员工应具有良好的职业素养,遵章守纪。 5S中的素养是核心。员工具有良好的素养,其
浅析tpm设备管理理论实践与点检实施

区域治理
浅析tpm设备管理理论实践与点检实施
谢亮 陕西延长石油延安能源化工有限责任公司,陕西 延安727500
摘要:随着现代企业的发展,设备管理在企业中占着重要位置。目前tpm设备管理模式是全员参加为特征的生产维修体制,也是 一种高效的设备管理模式。陕西延长石油延安能源化工公司已展开tpm设备管理,转变了员工对设备管理的观念。员工积极开展自主 管理,不断提升自主管理能力。设备管理已从幕后维护转向了提前预防,从而可以降低设备维修费用,实现全员参与设备维护保养。
3 tpm设备管理模式在实行中所体现 的精神实质
lpm设备管理模式的精神实质是提高 质量,实现手段的实质是利益的重新划分。 tpm设备管理模式的核心思想是预防维修 为主,变事后维修为预防维修,变被动为 主动:目的是节约成本,消除了可避免的 成本,减缓、减少和控制了不可避免的成 本支出:目标是提高产品质量。其实现手 段的核心是“不间断的小集团活动”,其 他“支柱”均围绕实现小集团活动为宗旨。
关键词:tprn;设备;管理;应用
一、tpm设备管理模式简介 1 tpm的含义 tpm是total productivemaintenance 的英文缩写,中文译作“全员生产维修”。 tpm确切的定义是:全体人员,包括企业 领导、生产现场工人以及办公室人员参加 的生产维修、维护体制。而后其重新被定 义为:“以最有效的设备利用为目标,以 维修预防、预防维修、改善维修和事后维 修综合构成生产维修为总运行体制。由设 备的计划、使用、维修等所有有关人员, 从最高经营管理者到第一线作业人员全体 参与。以自主的小组活动来推行tpm,使 损失为零”。tpm活动是以改善设备状况, 改进人的观念、精神面貌及改良现场工作 环境的方式来革新企业的体制,创建轻松 活泼的工作氛围,使企业不断发展进步。 2 fpm管理活动的八大支柱和两大基石 八大支柱包括人才培养、自主管理、 专业保全、课题改善、事务改善、初始改善、 安全管理和品质保全。人才培养是tpm 的基础支柱之一。自主管理要求全员参与 进行彻底的自主管理,它是tpm的中流 砥柱。专业保全即将设备管理的职能进行 细分:课题改善主要针对突出的问题,在 tpm小组活动里按主题活动的方式开展课 题活动。事务改善把各项业务及流程进行 标准化和规范化,使获得的信息进行彻底 共享化实现效率最大化。初始改善即是指 在短期内消除初期故障。安全管理是万事 之本。品质保全即是事前管理活动,是以 提高产品品质为根本目的。两大基石是指 5s活动和不间断的小集团活动。5s活动 是现场改善的基石。5s包括整理、整顿、 清扫、清洁、素养五个项目,是以现场和 设备为中心去除周围能见到的混乱及浪费 现象的一种基本活动,是推行tpm阶段 活动前的必不可少的准备工作和前提,在 tpm里将5s称为tpm“0”阶段活动。 不问断的小集团活动是tpm的基石。小
现代设备管理模式--TPM全员生产维护

现代设备治理模式——TPM(全员生产维护)SUNNY译二零零一年元月名目一、什么是全员生产维护二、全员生产维护的历史三、如何样进行全员生产维护1.OEE——设备总体效率2.造成损失的六种要紧缘故3.组成全员生产维护的五个基石四、解决要紧咨询题1.解决要紧咨询题的七个步骤2. 解决咨询题的方法五、自发的设备治理1.自发设备治理的七个步骤2.自发设备治理的检查监督六、有方案的设备治理导进有方案的设备治理的七个步骤七、设备治理预防1.设备治理预防的七个步骤2.设备治理预防的方法八、教育及培训九、推举读物一、什么是全员生产维护如何在生产中落低本钞票一直是多年来企业界的一个重要目标。
因此其中有许多碍事因素,然而如何有效地利用工厂里的各种生产设备却是其中最重要的因素之一。
TPM〔全员生产维护〕是一种有助于特不有效地使用生产设备的理论。
那个地点有效使用的含义是指使设备无故障地运行并生产出无质量缺陷的产品,而且使其不至于因方案外故障而停机。
TPM所涉及到的不仅仅是设备,而是人、设备和工作环境的有机整体。
这种整体联系不仅要求设备不产生功能故障,而且其它方面如较少的工装和调整时刻、较高的加工稳定性以及操作和维修的方便性等也特殊重要。
因此,设备一定要保养好,要不断查出设备的薄弱部位,寻出缘故并排除之。
这些工作不能仅由设备治理人员担当,设备操作人员也必须大力、积极地参与。
TPM理论中最重要的一点确实是根基不断地革新和完善的思想,也确实是根基讲:为了提高人、设备和工作环境这一有机整体的效率,TPM决不应该停止。
为了长期富有成效地提高设备效率,除了全员生产维护外,我们还应该注重以下几点:●应完整地考虑生产设备的生命周期,从方案购置一直到停产报废;●所有职员都必须参与,从生产工人到车间主任;●企业的所有部门都必须参与〔例如,生产、设备、质量、方案部门等〕;●要特不重视小组〔团队〕工作,而且领导要给予支持。
二、全员生产维护的历史1951年日本引进了预防型的设备治理,这开始了设备治理的现代化进程。
TPM的理论与实例

TPM的理论与实例什么是TPM?TPM(Total Productive Maintenance,全面生产维护)是一种通过全员参与,实现设备全寿命周期管理的维护方法。
TPM着重于预防性维护,目标是通过减少故障和停机时间来提高设备的利用率和生产效率。
TPM的理论基础主要包括以下几个方面:1. 6大损失TPM将生产中的损失分为6大类,包括设备停机损失、设备速度损失、次品品率损失、调整和调试损失、物料更换损失以及员工安全和环境损失。
通过对这些损失的分析和解决,可以提高设备的生产效率。
2. OEE(Overall Equipment Efficiency)OEE是衡量设备绩效的指标,它是设备利用率、生产效率和产品质量的综合指标。
OEE的计算包括设备的稼动时间、产量以及良品率等因素。
TPM的目标是提高设备的OEE,以实现更高的生产效率。
3. 自律性维护自律性维护是指将维护的责任下放到操作工人,并鼓励工人进行日常设备维护和保养。
自律性维护的目的是提高设备的可靠性,并培养工人对设备维护的责任心和自我管理能力。
TPM的实例以下是两个TPM实例,分别涉及设备保养和故障预防。
实例一:设备保养在一个制造企业中,管理层决定引入TPM来提高设备的可靠性和生产效率。
首先,他们成立了一个跨职能的团队,包括生产、工程和维护等部门的代表。
这个团队开始对设备进行全面的评估和保养计划的制定。
团队首先分析设备产生的故障原因,并根据故障的频率和影响程度排序。
然后,他们制定了设备的保养计划,包括日常巡检、定期保养和维护计划。
这些计划由设备操作人员和设备维修人员共同执行。
此外,团队还组织了培训课程,培训设备操作人员进行日常设备保养和故障排除。
通过培训,工人们学会了如何进行设备的基础保养,并及时发现和解决设备故障。
这不仅提高了设备的可靠性,还培养了工人的技能和责任心。
在实施TPM后,该企业的设备的生产效率显著提高,设备故障率降低,生产线的停机时间减少,从而大大提高了生产效率和产品质量。
现代企业的设备管理TPM的实施与培训

(CS)多功能的综合人才 人是企业的最大财富,对固有技术的理论
教育,向实践技能教育转变。
4 设备保全
计划保全与保全技术提 恢复本色、维持本色、预防衰老、计划保
升
全。
5 品质保全
扑灭慢性不良与 QA合格 日常管理、异常管理、变化管理、机种差
率100%
异管理、履历管理
务效率化
职能提升与高效化
并改善。
第28页/共30页
谢 谢!
第29页/共30页
感谢您的观看!
第30页/共30页
第24页/共30页
从减少6大损失扩展到减少16大损失
1.设备故障
2.安装调整
设备效率8大损失
3.更换刀具、夹具 4.开工 5.其它停机(清理,检查,安排,质量认可)
★停机损失
6.短暂停机与闲置
★操作损失
7.速度损失
16
8.废品与返工
★质量缺陷损失
大
损 失
9.管理损失(等待指示或材料)
★生产工时损失
以设备维护人员为中心的 PM,通过对设 备设计、制作和保全方法的改善,追求极 限设备效率,并不追求对涉及到设备使用 方法的极限综合生产效率
手 段 方 法
TPM主要靠员工的自主管理(自己设备自 己维护)。如日常管理业务(清扫、注油、 紧固、点检等)由操作人员负责,设备检 查诊断修理由保全人员负责
PM中,操作人员只管理生产,日常的管理 业务、检查、修理等保全工作由保全人员 全权负责
4S(Service) 服务
第19页/共30页
整理 把要和不要的东西加以分开处理
1 、工作的地方是否零乱? 2、工具、文件是否有条理? 3、你是否把纸张、杂物、工具放在地板上? 4、经常使用和很少使用的工具、文件分开了吗? 5、灭火器和消防器的位置合适?
TPM全员参与设备维护管理理论与实际概论
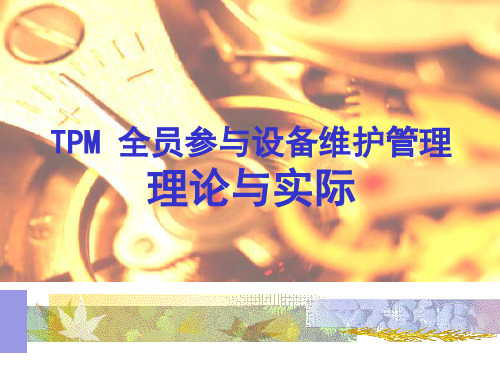
活动目标
◆ TPM活动: 4次/月.组 ◆ STEP诊断: 2次/年.组 ◆ 提案件数(实施): 4件/月.人 ◆ 故障件数(A级): 减半(全年对比)
TPM推进体系图
21C 世界 超一流 企業
最高의 競爭力을 갖춘 MAN,MACHINE SYSTEM構築
个别改善 主题活动
⑤树立对策:对每个原因分析,重点原因树立对策 ⑥实施对策:利用自主制作室 simulation(假制作) 1、2、3次循环改善 ⑦效果分析:把握P、Q、C、D、S、M成果
区分 STEP指标 成果指标 效果指标
内
容
In – out 指标
设备综合效率、MTBF、MTTR、lead time等
功能 ⑦不合理层别:把握活动的重点(Point) ⑧疑问点list:把握异常和正常(确定不合理) ⑨10分钟教育(OPL):改善事例、故障事例、不良事例
个人别、Know – How 等 ⑩改善前后比较:实施期间成果(P、Q、C、D、S、M,缩短时间、
降低库存等)
个别改善 主题活动
①选定主题:从不合理项目中找出改善案(发生源、困难部位、故障、 不良等) 经理指示事项 TPI个别对策项目 当前课题
3. M (Maintenance 维护)
面向生产SYSTEM的LIFE CYCLE整体 用效率极限追求维持生产经营体的‘理想状态’ 的活动。
TPM
TPM的定义
1. 对生产 System效率化(综合效率化), 构筑企业体制改善作为目标 ;
2. 生产System全过程作为活动对象的, 灾害 ”0”, 不良 “0”, 故障 “0” 等, 在现场·现物构筑防止 全 浪费(Loss)的体制;
现代设备管理的理论及实践

现代设备管理的理论与实践一、TPM理论的发展1、TPM的基础全面生产维修TPM(Total Productive Maintenance )是一个在世界范围内为维护、生产及企业管理者所关注并试图学习和了解的话题。
一些世界级企业都将TPM视为一种最新和最好的现代管理模式,如戴姆勒·克莱斯勒、大众、福特、宝马、邓禄普、摩托罗拉、卡夫、柯达、博世、西门子及其它一些世界级企业已经或正在建立TPM管理系统并取得了很好的成效。
TPM似乎将成为现代企业中一种最具发展潜力的管理模式。
20世纪50年代初日本引进了通用电气公司创建的预防维修体制。
如同质量管理与零故障管理的引进一样,日本人改进和发展了预防维修模式,使之更加适应日本企业的实际。
日本设备维修协会副主席中岛青一在全日本积极推动TPM,被称为TPM之父,他就TPM题材所写成的著作也被日本和许多国家认为是维护和生产管理领域内的圣经。
中岛青一首先在Nippondenso公司开展了涉及日常维修工作的TPM的试点并为此打下了较好的基础。
虽然中岛青一的书是针对日本企业的特点写的,但是TPM模式已被视为20世纪一种最为有效的设备管理手段,为提高自身的设备管理水平,许多国家的企业纷纷从日本引进TPM模式。
目前,日本人已在这一领域占据了无可争议的优势。
在日本,企业广泛地开展了TPM活动。
一个大型企业的董事长选择自己企业供货商的前提就是必须建立TPM管理系统,而这些供货商又同样要求自己的员工必须掌握TPM方法。
TPM模式实际上反映的是一种企业文化,而这种企业文化的核心就是团队精神,强调的是协作。
因此,建立TPM模式,必须首先为全体员工制订适合本企业实际情况的TPM计划,在此基础上根据不同部门的需求再规划出TPM实施进程。
按照日本人的观点, TPM模式的引进需要大量的时间、精力和金钱,因而必须取得企业高层的支持才能成功。
必须清醒地认识到,在TPM模式取得成效之前,不仅在时间、金钱方面的消耗是巨大的,而且企业文化也将发生变化。
TPM管理中的设备维修和维护技术转移实践

TPM管理中的设备维修和维护技术转移实践随着信息化的发展,信息安全越来越受到人们的关注,而TPM技术作为一种能够保障信息安全的关键技术,其应用越来越广泛。
对于TPM设备的维修和维护,技术转移是非常重要的一环,只有做好技术转移,才能保证设备的正常使用和运行,下面将从设备维修和维护技术转移的角度来探讨。
一、设备维修TPM设备出现故障是不可避免的,因此TPM设备的维修也是必要的,而设备维修需要掌握一定的技术,以下是设备维修的技术要点:1、维修前要做好准备TPM设备维修前,应彻底了解设备的状况,了解故障表现以及可能引起故障的原因,这样可以更加准确地进行修复工作。
同时要做好安全措施,避免因操作不当而导致的事故。
2、掌握常见故障的修复技术常见的TPM设备故障包括电源故障、硬盘损坏、主板故障等,对于这些故障,需要掌握相应的修复技术,例如更换损坏的零部件,修复硬件连接,更新固件等。
3、防止对设备造成二次损害在进行维修时,要避免因操作不当导致的二次损坏,例如在操作设备时不能过度用力,不能使用不当的工具进行维修。
二、设备维护设备的定期维护是保证TPM设备正常运行的关键,只有进行良好的设备维护,才能保证设备的长期使用,以下是设备维护的技术要点:1、根据维护计划进行维护TPM设备的维护需要有相应的维护计划,根据计划进行定期维护,这样可以预防设备出现故障,并且可以保证设备的使用寿命。
2、做好系统备份在进行设备维护的过程中,要做好系统备份工作,以免在维护过程中出现数据丢失等问题。
3、注意设备安全在进行设备维护时,需要注意设备的安全,例如在维护过程中需要避免数据被盗窃、篡改,同时要防止设备与其他设备发生不必要的接触。
三、技术转移随着企业业务的发展,可能需要将TPM设备迁移至不同的地点,或者进行更换。
在设备迁移或更换的过程中,需要进行技术转移,以保证设备的正常运行。
以下是技术转移的要点:1、提前准备在进行技术转移前,需要提前进行充分的准备,例如制定详细的计划,确定技术转移的步骤,确保设备的信息得以完全记录。
- 1、下载文档前请自行甄别文档内容的完整性,平台不提供额外的编辑、内容补充、找答案等附加服务。
- 2、"仅部分预览"的文档,不可在线预览部分如存在完整性等问题,可反馈申请退款(可完整预览的文档不适用该条件!)。
- 3、如文档侵犯您的权益,请联系客服反馈,我们会尽快为您处理(人工客服工作时间:9:00-18:30)。
2020/9/27
11
作业时能够快速取用;
清扫:将作业场所中的灰尘、油污、垃圾清扫
干净,创造一个舒适的作业环境;
清洁:清除各类污染源(如废水、废气等),
杜绝各类跑、冒、滴、漏现象;
素养:员工应具有良好的职业素养,遵章守纪。
5S中的素养是核心。员工具有良好的素养,其
余四项就容易形成制度。
2020/9/27
计,进行设备的维修预防;使用阶段实施预防
2020/9/27
5
维修;对重复故障采取改善维修。建立以设备一生
为对象的生产维修机制。另一方面对设备实施全空 间的管理:TPM管理涉及到设备的每一个零部件、
也涉及到设备的机械、电气、仪器仪表、等各个子 系统,TPM还要求设备周边的环境、生产现场乃
至办公区域实施清洁化、定置化、目视化和文明化
纵向和横向的全员管理是由完善的TPM加
以组织推动的。
2020/9/27
8
TPM管理的八大支柱:
TPM管理的八大支柱涉及个别改善、自
主维修、专业维修、初期管理、质量改善、安
全及环境卫生改善、事物改善以及教育培训。
与企业各部门之间的关系如下表所示:
个别改善 自主维修 专业维修 初期管理 质量改善 环境改善 事物改善 教育培训
段,而是以生产系统的寿命周期全过程为对象的
活动。全员生产维修在日本已由生产部门逐渐
推广到整个企业, 形成全企业TPM的格局。
2020/9/27
14
2020/9/27
15
全 面 生 产 维 修 TPM( Total Productive
Maintenance )是一个在世界范围内为维护、
生产及企业管理者所关注并试图学习和了解的 话题。一些世界级企业都将TPEM视为一种最
现代设备管理 的理论创新与实践
2020/9/27
1
一、现代设备管理理论的创新
( 全面生产设备管理 TPEM )
2020/9/27
2
全员生产维修TPM
20世纪70年代初, 日本在学习、推广设备综 合工程学及预防维修、生产维修的基础上, 提出 了“全员生产维修”的概念。全员生产维修是全 面质量管理概念的扩充,即质量意识和无故障规 划在维修领域内的体现。全员生产维修的首要目 标是通过减少计划外设备停机时间和废品数量以 提高设备的有效利用时间,同时通过满足不断变 化的需求以延缓生产设备的使用年限;其第二个
根据新的解释,TPM 中的“三全”指的是生产系统
的综合效率化、生产系统的寿命周期全过程以及
2020/9/27
13
包括生产、开发、经营、管理的所有部门和全
体成员。追求生产系统的最高效率则是使“灾 害为零, 废品为零, 故障为零”,而不单是追求
生产效率最高。新的观点也为“维修”赋予了广
义的解释,使其不单指生产系统的使用、维修阶
2020/9/27
3
目标则是减少维修费用,而这又是通过减少辅 助人员及提高生产效率加以实现的。
日本工程师学会为全员生产维修所下的 定义为:
以追求设备综合效率最高为目标; 建立以设备一生为目标的全系统的预防 维修; 与设备管理相关的所有部门的参与; 从企业最高管理层到一线员工的参与; 开展小组自主活动推进生产维修。
新和最好的现代管理模式,如戴姆勒·克莱斯
勒、大众、福特、宝马、邓禄普、摩托罗拉、
卡夫、柯达、博世、西门子及其它一些世界级 企业已经或正在建立TPEM管理系统并取得了
很好的成效。TPM似乎将成为现代企业中一种
最具发展潜力的管理模式。
2020/9/27
16
20世纪50年代初日本引进了通用电气公司创
建的预防维修体制。如同质量管理与零故障管理
建议
反馈
维修预防
制造厂设计改进
2020/9/27
7
全员:操作者的自主维修。涉及设备寿命
周期各环节的所有部门及员工均应参加设备的
综合管理。全员管理包括两ห้องสมุดไป่ตู้层面:
纵向的全员:从企业高层管理到第一线的
操作工人参与TPM;
横向的全员:要求企业中生产、工艺、能
源动力、质检、设计、供应、物流以及环保等 所有部门都要参与TPM管理。
生产、设备部 ● ● ●
● ●
设计、技术部 ●
● ● ● ●
●
●
质量管理部 ●
● ● ●
其他管理部门 ●
● ● ● ●
2020/9/27
9
TPM模式实际上反映的是一种企业文化,而这
种企业文化的核心就是团队精神,强调的是协作。小 组自主活动、5S活动、设备点检制等都是具有鲜明“
全员”特色的管理模式。
的引进一样,日本人改进和发展了预防维修模式,
使之更加适应日本企业的实际。日本设备维修协 会副主席中岛青一在全日本积极推动TPM,被称
为TPM之父,他就TPM题材所写成的著作也被日
小组自主活动的目的通过各种激励手段是员工的
自主意识和团队精神,使员工自觉、自发地开展TPM
管理中的各项活动,实现“生产设备非计划停机时间
2020/9/27
10
为零;由生产设备故障引发的产品缺陷为零;生产设 备的速度损失为零”的目标。
所谓“5S”活动的内容就是: 整理:将工作场所的各类物品有序地进行整理、 摆放,以便有条不紊地开展各项作业; 整顿:将要使用的各类物品根据定量、定位、使 用频率大小、标记化的原则,合理地加以布置,以便
12
自1971年日本推广全员生产维修以来, 情况发 生了很多变化, 内容也不断充实和完善。
其主导思想是将局限于生产部门的TPM推广到
包括开发、经营、管理等所有部门的遍及全工厂的
TPM, 以此追求整个生产系统的最高效率。与此对
应,TPM的目标、研究对象都由“设备”推广到“整
个”生产系统, 这就赋于了TPM以更广泛的意义。
的管理。 TPM的全系统结构如图所示:
2020/9/27
6
TPM的全系统生产维修体系
基础保养
生产维修
日常清洁、保养、 定期点检、润
点检
滑
设备分类
发现异常 判断决策 自主维修
事后维修 突发故障 维修计划 维修实施
预防维修 维修计划 维修准备 维修实施
改善维修 分析论证 改善方案 方案实施
记录
总结
评价
2020/9/27
4
全员生产维修TPM特点是三全:全效率,全
系统,全员。 全效率:又称综合效率。以提高综合效率为
目标,追求设备运行的经济性。 TPM管理追求生产系统整体综合效率最大化,
而设备综合效率最大化是实现这一目标的最根本
的措施。
全系统:全系统包括两个层面。对设备的全
过程管理:设备设计阶段采用可靠性、维修性设