粉末冶金零件的金相制样
粉末特性-粉末冶金页PPT课件

铁粉性能的比较
Green strength (MPa)
生坯强度
0.6% Kenolube
40 35 30 25 20 15 10
5 200 300 400 500 600 700 800 900
压制压力(MPa)
MH80.23 NC100.24 SC100.26 ABC100.30 ASC100.29 AHC100.29
150-212 45-150 <45
铁粉性能的比较
g/cm3 s/50g
松比和流动性
3.5
40
3.0
35
2.5
30
25 2.0
20 1.5
15
1.0
10
0.5
5
0.0
0
ABC100.30
ASC100.29
AHC100.29
SC100.26
NC100.24
H80.23 M
松比 流动性
铁粉性能的比较
粉末性能
• 冶金性能
化学成分与杂质 显微结构 显微硬度
• 几何性能
颗粒尺寸分布 颗粒外部形状 颗粒内部结构(颗粒孔隙度)
• 机械性能
流动速率 松装密度 压缩性,生坯强度和弹性后效
性能间的相互关系
• 显微结构 化学成分 • 显微硬度 化学成分 • 压缩性 显微硬度, 孔隙度 • 压缩性 粒度 • 流动性 颗粒形状和尺寸 • 生坯强度 颗粒形状
Green density (g/cm3)
压缩性
润滑阴模
7.6 7.4 7.2 7.0 6.8 6.6 6.4 6.2 6.0 5.8 5.6
200 300 400 500 600 700 800 900
实验一-粉末冶金材料组织观察与硬度测试

实验一粉末冶金材料组织观察与硬度测试实验学时4h 实验性质综合实验要求必做所属课程粉末冶金一、实验目的掌握Fe基粉末冶金烧结材料的相图,根据相图及显微形貌(组织特征)识别材料的组织,理解组织与成分之间的关系;能够根据有关定律及公式计算烧结铁基合金组织组成物的相对含量。
熟悉布氏、洛氏及维氏硬度计的结构原理及特点。
掌握布氏、洛氏、维氏硬度试验方法,能独立进行操作;了解粉末冶金材料的组织特点及硬度之间的关系二、烧结Fe基合金组织特征概述粉末冶金一种冶金方法。
把金属粉末压制成型后再烧结成制品。
粉末冶金适用于高熔点、高硬度的金属或含有不互溶成分的合金制品的制造。
烧结铁基合金是目前应用非常广泛的粉末冶金工程材料,其基本相图为铁碳合金的平衡组织,是研究铁碳合金的性能及相变机理的基础。
因此认识和分析铁碳合金的平衡组织有十分重要的意义。
此外,观察和分析铁碳合金的平衡组织有助于帮助我们进一步借助相图来分析问题。
所谓平衡组织,是指符合平衡相图的组织,即在一定温度,一定成分和一定压力下合金处于最稳定状态的组织,要获得这样的组织,必须使合金发生的相变在非常缓慢的条件下进行,通常将缓冷(退火)后的铁碳合金组织看作为平衡组织。
不同成分Fe基合金的平衡组织都是由铁素体、渗碳体、珠光体、石墨、孔隙、夹杂等组成,其区别仅在于分布形态和数量不同。
根据各组成物的形态、分布和数量可以判断和识别组织及含碳量。
1、铁素体:是碳在α-Fe中的固溶体。
碳的浓度是可变的,在727℃时达到最大溶解度(0.0218%);常温下其碳浓度约为0.008%。
铁素体的硬度很低,塑性好,经4%硝酸酒精浸蚀后呈白亮色。
铁素体有两种形态和分布:一是呈游离状的不规则多边形。
二是与渗碳体呈层状相间排列,如珠光体中的铁素体。
2、渗碳体:是碳与铁的一种化合物,化学式为Fe3C,含碳量高达6.69%,坚硬而脆,抗浸蚀能力很强,经4%硝酸酒精浸蚀后成白亮色。
渗碳体的分布和形态有:①游离的直条状渗碳体,如过共晶生铁中的Fe3CⅠ;②作为基体,其中分布有孤立的珠光体,即莱氏体中的渗碳体;③沿奥氏体晶界呈网状分布,如过共析钢的Fe3CⅡ;④与铁素体呈片层状分布,即珠光体中的Fe3C;⑤沿铁素体晶界分布,即工业纯铁中的Fe3CⅢ。
国内外关于粉末冶金机械零件——技术标准

国内外关于粉末冶金机械零件材料的一些技术标准滑动轴承粉末冶金轴承技术条件(中华人民共和国国家标准GB2688-81)本标准适用于GB2685-81《粉末冶金筒形轴承型式、尺寸与公差》、GB2686-81《粉末冶金带挡边筒形轴承型式、尺寸与公差》及GB2687-81《粉末冶金球形轴承型式、尺寸与公差》所规定的粉末冶金铁基和钢基轴承(以下简称轴承)。
1.技术要求1.1轴承的材料按合金成分与密度分类规定于表1。
表1材料牌号标记实例铁基1类含油密度为5.7~6.28/cm3的粉末冶金轴承材料标记;1.2轴承化学成分与物理一机械性能应符合表2规定。
1.3轴承的机构型式、尺寸与公差应符合GB2685-81、GB2686-81及GB2687-81的规定。
1.4轴承外观应有均匀的金属光泽,不允许有裂纹、夹杂和锈蚀等缺陷。
1.5轴承成品应浸渍的润滑油。
一般浸渍GB443-64规定的HJ-20牌号机械油(铁基轴承允许加入防锈剂)。
如对于浸渍的润滑油另有要求,应在订货时提出。
1.6轴承应有良好的表面多孔性。
1.7对本标准未规定的特殊技术要求应在订货时提出。
2.验收规则2.1轴承成品应由制造厂按本标准检验合格后,并附有产品合格证方能出厂。
2.2轴承成品应按批交货验收。
批量大小应在订货时注册,如不注明则由制造厂规定。
2.3有必要时订货单位可对制造厂交货的成品按批抽样检验,其方法规定如下:2.3.1每批轴承成品任取2%,但不少于5件不多于50件,用肉眼按本标准规定检查外观质量。
2.3.2每批轴承成品任取2%,但不少于5件不多于50件,按本标准规定检查尺寸与公差。
2.3.3每批轴承成品至少任取2件样品,经脱油处理后,取得不少于50克试样,按表2的规定分析化学成分。
2.3.4每批轴承成品任取5~10件(或由双方商定),按表2规定检查物理一机械性能。
2.3.5各类抽检结果中,如有一件不合格时,仍就不合格项目抽取2倍数量的成品复表2注:1.铁基各类轴承的化学成分中允许有<1%的硫2.化合碳含量允许用金相法评定。
金相制样 标准

金相制样标准全文共四篇示例,供读者参考第一篇示例:金相制样是金属材料分析的一种重要手段,通过金相制样可以观察和分析金属材料的组织结构及性能特征,为金属材料的性能评价和质量控制提供了重要依据。
金相制样的主要目的是通过金相显微镜观察材料的金相组织,从而了解金属材料的组织结构、相比例、晶粒度等信息,以评价材料的性能和质量。
金相制样的标准是指在金相制样的整个过程中所需遵循的规范和要求,包括样品的制备、金相显微镜观察、图像分析等方面。
金相制样标准的制定是为了确保金相分析的结果准确可靠,以及不同实验室之间的结果可以相互比较和验证。
下面将介绍一些金相制样的标准内容。
一、样品的制备1. 样品的切割:金相制样的第一步是对金属材料进行切割,通常使用金刚石切割机或者电火花切割机进行切割。
在切割过程中要避免造成金属材料的形变和损伤,确保后续金相制样的准确性。
2. 样品的研磨和抛光:切割后的金属样品需要研磨和抛光,使其表面平整光滑,去掉切割和研磨过程中产生的残留物和氧化层。
3. 样品的腐蚀:有些金属材料需要进行腐蚀处理,以去除表面的氧化层和其他污物,以确保金相显微镜观察时的清晰度。
二、金相显微镜观察1. 显微镜的使用:金相显微镜是金相制样的关键设备,其性能和调整对金相分析的结果有着重要影响。
金相显微镜的放大倍数、光源亮度、对比度等参数都需要进行合适的调整。
2. 图像的采集:金相显微镜观察到的金相组织图像需要进行合适的采集和保存,以便后续的图像分析和比对。
三、图像分析1. 图像处理:金相组织图像需要进行适当的处理,包括对比度增强、锐化、颜色反转等操作,以获得更清晰的金相组织信息。
2. 图像分析:金相组织图像可以通过图像分析软件进行颗粒度分析、相比例统计等操作,进一步了解金属材料的组织结构特征。
金相制样标准的制定和遵循对于金相分析的准确性和可靠性至关重要。
只有严格按照金相制样标准进行操作,才能获得准确可靠的金相分析结果,为金属材料的性能评价和质量控制提供有力的依据。
新型粉末冶金制取Al-Zn-Mg-Cu合金的金相评估
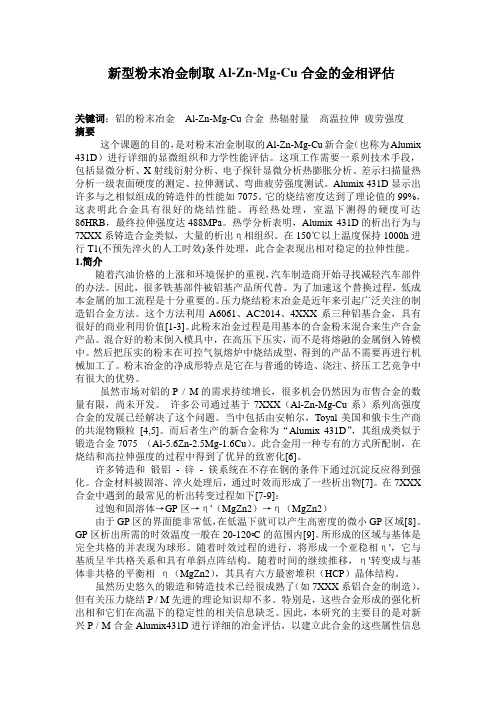
新型粉末冶金制取Al-Zn-Mg-Cu合金的金相评估关键词:铝的粉末冶金Al-Zn-Mg-Cu合金热辐射量高温拉伸疲劳强度摘要这个课题的目的,是对粉末冶金制取的Al-Zn-Mg-Cu新合金(也称为Alumix 431D)进行详细的显微组织和力学性能评估。
这项工作需要一系列技术手段,包括显微分析、X射线衍射分析、电子探针显微分析热膨胀分析、差示扫描量热分析一级表面硬度的测定、拉伸测试、弯曲疲劳强度测试。
Alumix 431D显示出许多与之相似组成的铸造件的性能如7075。
它的烧结密度达到了理论值的99%,这表明此合金具有很好的烧结性能。
再经热处理,室温下测得的硬度可达86HRB,最终拉伸强度达488MPa。
热学分析表明,Alumix 431D的析出行为与7XXX系铸造合金类似,大量的析出η相组织。
在150℃以上温度保持1000h进行T1(不预先淬火的人工时效)条件处理,此合金表现出相对稳定的拉伸性能。
1.简介随着汽油价格的上涨和环境保护的重视,汽车制造商开始寻找减轻汽车部件的办法。
因此,很多铁基部件被铝基产品所代替。
为了加速这个替换过程,低成本金属的加工流程是十分重要的。
压力烧结粉末冶金是近年来引起广泛关注的制造铝合金方法。
这个方法利用A6061、AC2014、4XXX系三种铝基合金,具有很好的商业利用价值[1-3]。
此粉末冶金过程是用基本的合金粉末混合来生产合金产品。
混合好的粉末倒入模具中,在高压下压实,而不是将熔融的金属倒入铸模中。
然后把压实的粉末在可控气氛熔炉中烧结成型,得到的产品不需要再进行机械加工了。
粉末冶金的净成形特点是它在与普通的铸造、浇注、挤压工艺竞争中有很大的优势。
虽然市场对铝的P / M的需求持续增长,很多机会仍然因为市售合金的数量有限,尚未开发。
许多公司通过基于7XXX(Al-Zn-Mg-Cu系)系列高强度合金的发展已经解决了这个问题。
当中包括由安帕尔,Toyal美国和俄卡生产商的共混物颗粒[4,5]。
新型粉末冶金制取Al-Zn-Mg-Cu合金的金相评估
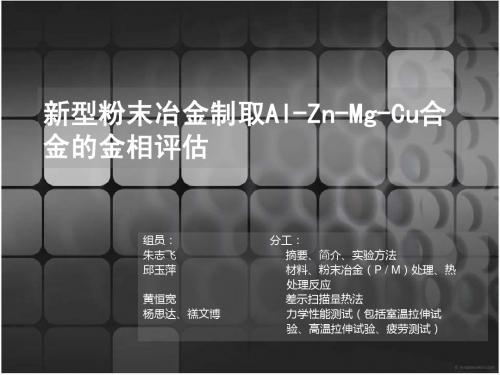
表所示的数据表明,Alumix431D与变形对应相比有50%的可 能性失败。烧结后的P / M合金的净疲劳寿命(18%)的减少 归因于残余毛孔(〜1%)。这些促进裂缝发生的应力集中, 随后,降低疲劳寿命的特性是已知的。
结论:
通过以上实验,我们可以得出这样的结论: 1.431D铝合金的烧结性能很好,而且在理论上能达到接近99%
粉末冶金在粉末冶金工艺过程中,利用电子探
针技术检测到在其进行烧结过程中其颗粒尺寸 的变化.
(P / M)处理:
在烧结过程中,其目的是开发强的颗粒间键, 合金元素的均匀分布,并降低孔隙率。
获得进一步观察Alumix431DT1出现的相组织,准备 材料,进行x射线衍射。图4包含T1的XRD谱系统占 主导地位的阶段被发现的六方晶胞品种(平衡) 是铝和MgZη 2。
Alumix 431D在热处理T6回火下的成分模式图像
差示扫描量热法:确定热处理Alumix 431D 的析出的一种手段
T6 Alumix 431 d热处理的XRD谱
第一峰(A)是发生 在81℃的温度下吸 热的特性 在烧结后室温下时效 后一个吸热峰在(B) 发生。 在C点的第二区域开 始被认为是η的连续 形成,而且η大量形 成。 在250◦C(D)的下 一个放热峰被认为是 η生长的结果 Alumix 431D-t1样品以10◦C/miη的速度从室温加热到525◦C的DSC图
文献的难点及疑点: 英语水平不高,翻译成中文很吃力 专业术语太多,对其理解不深,导致翻译不到位 文章中提到的测试技术、方法没有太多的了解, 如差示扫描量热所以对文章理解不深。
THE END Thanks!
Alumix 431D成分与7xxx 系铝合金相同。 这项工作需要一系列技术手段,包括显 微分析、X射线衍射分析、电子探针 显微分析热膨胀分析、差示扫描量热 分析、拉伸测试、弯曲疲劳强度测试。
铁基粉末冶金零件常见生产缺陷的金相分析
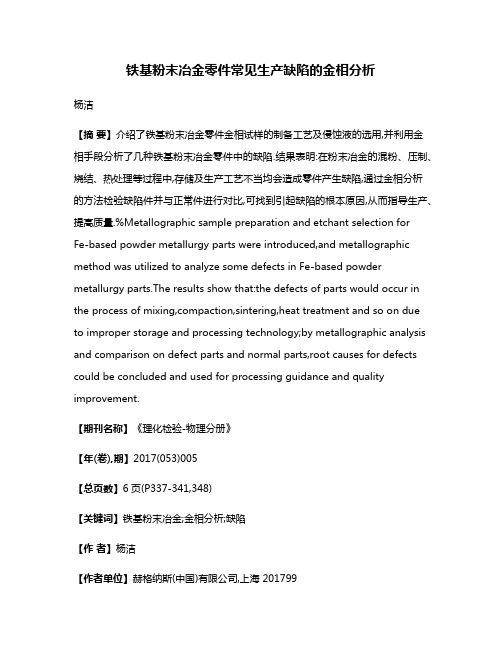
铁基粉末冶金零件常见生产缺陷的金相分析杨洁【摘要】介绍了铁基粉末冶金零件金相试样的制备工艺及侵蚀液的选用,并利用金相手段分析了几种铁基粉末冶金零件中的缺陷.结果表明:在粉末冶金的混粉、压制、烧结、热处理等过程中,存储及生产工艺不当均会造成零件产生缺陷,通过金相分析的方法检验缺陷件并与正常件进行对比,可找到引起缺陷的根本原因,从而指导生产、提高质量.%Metallographic sample preparation and etchant selection forFe-based powder metallurgy parts were introduced,and metallographic method was utilized to analyze some defects in Fe-based powder metallurgy parts.The results show that:the defects of parts would occur in the process of mixing,compaction,sintering,heat treatment and so on dueto improper storage and processing technology;by metallographic analysis and comparison on defect parts and normal parts,root causes for defects could be concluded and used for processing guidance and quality improvement.【期刊名称】《理化检验-物理分册》【年(卷),期】2017(053)005【总页数】6页(P337-341,348)【关键词】铁基粉末冶金;金相分析;缺陷【作者】杨洁【作者单位】赫格纳斯(中国)有限公司,上海 201799【正文语种】中文【中图分类】TG115.2作为一种绿色环保、近净成型技术,粉末冶金近年来得到迅速发展,在家电、汽车、电动工具等领域都有广泛应用[1]。
铁铜合金粉末烧结物相分析
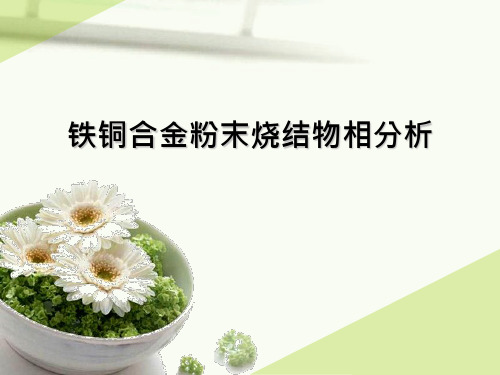
7
化率较高但塑性较低。为了获得适当晶粒度的材料和研究形变的微观机制及断 裂物理防止形变引起的断裂,必须测定晶粒粗细以及点阵完整程度。 若多晶材料的晶粒无畸变、足够大。理论上其粉末衍射花样的谱线应特别锋利 ,但在实际实验中,这种谱线无法看到。这是因为仪器因素和物理因素等的综 合影响,使纯衍射谱线增宽了。纯谱线的形状和宽度由试样的平均晶粒尺寸、 尺寸分布以及晶体点阵中的主要缺陷决定,故对线形作适当分析,原则上可以 得到上述影响因素的性质和尺度等方面的信息。
5
二、本材料作X射线衍射分析的目的
材料分析是通过对表征材料的物理性质或物理化学性质参数及其变化( 称为测量信息或特征信息)的检测实现的。采用各种不同的测量信号(相应 地具有与材料的不同特征关系)形成了各种不同的材料分析方法。晶胞内原 子的位置不同,X射线强度将发生变化。定量表征原子排列以及原子种类对 衍射强度影响规律的参数称为结构因子,即晶体结构对衍射强度的影响因 子。通过X射线在一个电子、原子、晶胞上的散射强度可以加强对结构因子 本质上的理解。
10
四、本材料测试试样的制备方法
我组选择的是德国布鲁克公司的D8型Advance型X射线衍射仪,粉末衍射仪 要求样品试片具有一个十分平整的平面,而且对平面中的晶粒的取向常常要求 是完全无序的,不存在择优取向。
制作合乎要求的衍射仪试片常用的方法:通常很细的样品粉末(手摸无 颗粒感)。如无显著的各相异性且在空气中又稳定,则可以用”压片法”来制 作试片。此法所需样品粉末量较多,约需0.4cm3。“涂片法”所需的样品量 最少。
金相标准样品1

48
高磷铸铁
铸造
珠光体+石墨及磷共晶
色呈花斑状,其上有黑色小点的为磷化合 物共晶
49
球墨铸铁
铸态
球状石墨+珠光体+铁素体
白色晶粒为铁素体,层状组织为珠光体, 黑色球状为石墨 白色为 α 相,晶界处暗色组织为共析体
50
铝青铜
铸态
α 相+共析体+FeAL 3
(α+γ2) , 晶内暗色为 FeAL 3 (试样未腐蚀 的照片)
高速钢 高速钢 不锈钢
淬火及回火 退火 固溶处理
29 30 31 32
20 钢 T8 钢 45 钢
铸态
低碳铸钢组织
白色网状、针状、块状组织为铁素体,黑 色部分为珠光体 表层脱碳后这亚共析钢,黑色为珠光体, 白色为铁素体,心部为粗片状珠光体。 白色晶粒为铁素体,黑色条状为珠光体, 呈明显的带状分布 黑色指纹状为珠光体,少量白色块状为铁 素体,分散的小黑点为疏松的含油孔
20 钢 45 钢 65 钢 T8 钢 T12 钢
退火 退火 退火
低碳钢平衡组织 中碳钢平衡组织 高碳钢平衡组织
退火
共析钢平衡组织
退火
过共析钢平衡组织
亚共晶 白口铁 铸态
变态莱氏体+珠光体 变态莱氏体
共 晶 白口铁 铸态
过共晶 白口铁 铸态
变态莱氏体+渗碳体
(二)钢的热处理组织 14 种 10 T8 钢 正火 索氏体 索氏体是细珠光体,片层间距小 屈氏体为极细珠光体,光学显微镜下难以 11 T8 钢 快冷正火 屈氏体 分辨其层状结构,灰白色块状、针状为淬 火马氏体。 12 13 14 15 16 17 18 19 20 21 65Mn 65Mn 20 钢 T12 45 钢 T10 钢 GCr15 GCr15 T12 15 钢 等温淬火 上贝氏体 羽毛球为上贝氏体,基体为索氏体或淬火 马氏体和残余奥氏体。 黑色针状为下贝氏体,白色基体为淬火马 氏体和残余奥氏体。 成束的板条状为低碳马氏体 深色针片状组织为马氏体,白色为残余奥 氏体 黑色针叶状互成 120 度夹角的针状马氏 体,其余为板条状马氏体 基体为铁素体,白色颗粒状为渗碳体。 黑色点状,颗粒状为碳化物,其余为有一 定饱和碳的铁素体。 颗粒状为碳化物,其余这铁素体 白色呈针状、细网络状分布的为渗碳体, 其余为片层状珠光体。 表层为过共析组织 (网状渗碳体+珠光体) , 由表向内含碳量逐渐减少,铁素体增多。退火脱碳源自表层脱碳组织锻造后退火
粉末冶金结构零件讲解

力学关系:
寸
△模冲/△阴模=3L/D
公 差
D表示阴模型腔的平均径向尺寸,
L表示模冲总长度。
如 何 消 减 尺 寸
公
用精整可改善零件的尺寸公 差,精整是将烧结零件装于 阴模中用模冲施压,即于精 整模具中进行复压。精整的 主要目的是校正烧结时产生 的扭曲变形。
差
粉末冶金结构零件的切削加工
☀ 采用粉末冶金零件的主要目的在于实现少 切削、无切削加工,节能,省材,降低零 件生产成本。粉末冶金零件不像相应的常 规金属零件那样容易切削加工。由于材料 组织中的孔隙导致的断续切削作用,刀具 寿命较短,零件表面粗糙度较差。
粉末冶金结构零件
粉末冶金结构零件
定义:用粉末冶金方法制造的具有一定尺寸精度 并能承受拉伸、压缩、扭曲等载荷 或在摩擦磨 损条件下工作的烧结零件,又称烧结结构零件 。
方法:在室温,于单轴向刚性模具中压制成形 与随后烧结的零件。
应用:粉末冶金结构零件主要应用 在汽车工业,未来有较好的应用领 用。
粉末冶金结构零件的主要优点
粉末冶金零件材料密度的影响
在粉末冶金结构零件生产中,往往采用复压和二次 烧结来提高零件的材料密度,依照压制——一次烧 结——复压——二次烧结的工艺路线生产结构零件。 用复压与二次烧结、温压可将零件材料密度提高到 普通铁的95﹪左右。
复压与精整相似,复压时施加较高的 压力仅仅是为了增高零件的整体密度, 二次烧结是指复压后再次进行烧结。 经复压与二次烧结的结构零件,由于 材料密度较高,可提高结构零件材料 的强度与韧性。
测定粉末冶金的切削性的标准: 用测定可钻削的孔数来确定切削 性。规定1045钢的值为100,切 削性额定值可由以下公式确定,
切削性额定值=烧结刚钻的孔数∕1045 钢钻的孔数×100
金相制样方法范文

金相制样方法范文金相制样是金相分析的重要环节之一,它是通过将金属试样制备成金相试件,然后经过打磨、腐蚀、酸洗等处理,最终在显微镜下观察和分析其显微结构和组织成分的一种方法。
本文将详细介绍金相制样方法的步骤和操作技巧。
一、试样的选择和准备金相试样的选取要依据实际需要进行,例如金属材料的硬度、表面状态等因素。
通常情况下,金相试样的形状为柱状、片状或环状。
二、试样的粗磨1.初磨将试样用金刚石砂轮或磨料纸配合砂轮机进行初次磨削。
砂轮机的转速一般为150-300r/min。
初磨时,要使试样均匀磨削,并保持试样温度不超过60℃。
2.粗磨用粗磨机进行粗磨,磨削的目的是去除初磨过程中残留的碳化物、氧化物等杂质,使试样表面平整、光洁。
粗磨的粒度为150-180目,磨削时间根据试样的大小和硬度决定,大致为10-30分钟。
三、试样的镜面磨削1.镜面磨削在磨削液中加入适量的金刚石砂轮粉末,然后用镜面磨削机对试样进行磨削,直到试样表面出现光泽。
镜面磨削的时间一般为10-30分钟。
2.镜面抛光将试样放置在抛光台上,涂抹上抛光液。
然后,用抛光布沿着一个方向进行抛光,直到试样表面出现光泽。
抛光的时间一般为5-10分钟。
四、试样的腐蚀和酸洗1.腐蚀将试样放置在腐蚀剂中,根据试样的组织结构和需要的结果选择适当的腐蚀剂。
腐蚀时间一般为几秒至几分钟不等。
2.酸洗用稀硝酸或其他酸性溶液对试样进行酸洗,去除腐蚀产物并清洗试样表面。
酸洗的时间一般为1-2分钟。
五、试样的显微观察和分析将试样放置在显微镜下进行观察和分析,根据试样的组织结构和成分进行相应的判断和分析。
总结:金相制样是金相分析的重要环节,正确的制样方法可以保证分析结果的准确性和可靠性。
制样过程中需要注意的是控制试样的温度、磨削的速度和时间等因素,以及选择合适的腐蚀剂和酸洗溶液。
制样完成后,通过显微观察和分析,可以对试样的组织结构和成分进行细致地了解和分析。
金相制样工艺流程
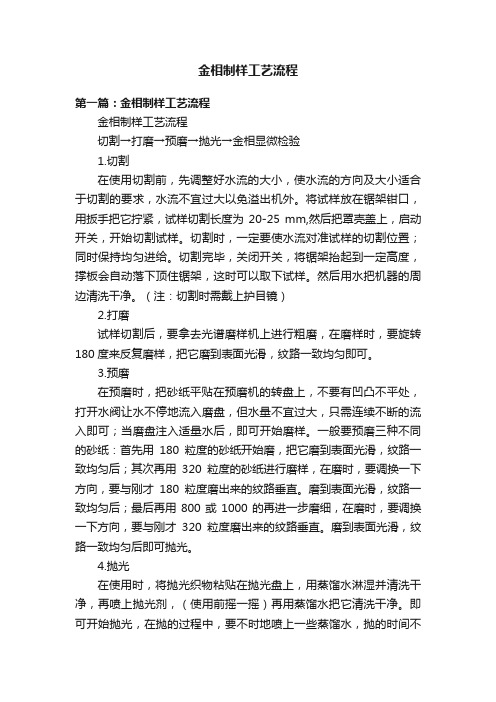
金相制样工艺流程第一篇:金相制样工艺流程金相制样工艺流程切割→打磨→预磨→抛光→金相显微检验1.切割在使用切割前,先调整好水流的大小,使水流的方向及大小适合于切割的要求,水流不宜过大以免溢出机外。
将试样放在锯架钳口,用扳手把它拧紧,试样切割长度为20-25 mm,然后把罩壳盖上,启动开关,开始切割试样。
切割时,一定要使水流对准试样的切割位置;同时保持均匀进给。
切割完毕,关闭开关,将锯架抬起到一定高度,撑板会自动落下顶住锯架,这时可以取下试样。
然后用水把机器的周边清洗干净。
(注:切割时需戴上护目镜)2.打磨试样切割后,要拿去光谱磨样机上进行粗磨,在磨样时,要旋转180度来反复磨样,把它磨到表面光滑,纹路一致均匀即可。
3.预磨在预磨时,把砂纸平贴在预磨机的转盘上,不要有凹凸不平处,打开水阀让水不停地流入磨盘,但水量不宜过大,只需连续不断的流入即可;当磨盘注入适量水后,即可开始磨样。
一般要预磨三种不同的砂纸:首先用180粒度的砂纸开始磨,把它磨到表面光滑,纹路一致均匀后;其次再用320粒度的砂纸进行磨样,在磨时,要调换一下方向,要与刚才180粒度磨出来的纹路垂直。
磨到表面光滑,纹路一致均匀后;最后再用800或1000的再进一步磨细,在磨时,要调换一下方向,要与刚才320粒度磨出来的纹路垂直。
磨到表面光滑,纹路一致均匀后即可抛光。
4.抛光在使用时,将抛光织物粘贴在抛光盘上,用蒸馏水淋湿并清洗干净,再喷上抛光剂,(使用前摇一摇)再用蒸馏水把它清洗干净。
即可开始抛光,在抛的过程中,要不时地喷上一些蒸馏水,抛的时间不宜太长,只要看着表面光滑,亮如镜面即可。
抛光完毕后,要用蒸馏水把抛光织物清洗干净,在不使用时应将盖盖上,以免灰尘或其它异物落入抛光织物上而影响以后的抛光效果。
5.金相显微检验1用未浸蚀的试样检查石墨○将抛光好的试样酒精清洗干净,再用风机把它吹干即可放在显微镜上观察石墨组织形态。
2用浸蚀之后试样检查金属基体○用少量的3%硝酸酒精试剂浸蚀,注意在浸蚀时抛光面不能接触到容器,浸蚀一定时间后,再用酒精把它清洗干净,用风机吹干后,即可放在显微镜上观察试样的基体组织。
4粉末冶金成形讲解
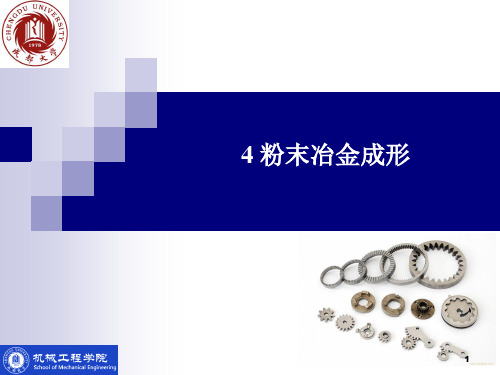
4 粉末冶金成形
13
✓(3)物理方法,常用蒸汽冷凝法 ✓(4)化学方法,常用还原法 碳还原法(制铁粉)
Fe2O3+C→Fe3O4+CO Fe3O4+C→FeO+CO FeO+C→Fe+CO
气体还原法(Fe,Ni,Cu,W)
MXOY+H2→M+ H2O
4 粉末冶金成形
14
4 粉末冶金成形
难熔化合物粉末制取
4 粉末冶金成形
29
16
➢ 2、成形 ✓ (1)粉末预处理
(1)粉末还原退火 (2)粉末筛分 (3)粉末混合
4 粉末冶金成形
17
✓(2)压制成形
单向压实 双向压制 浮动模压制 引下法
4 粉末冶金成形
单向压实
•粉末的结合力:机械咬合,冷焊
18
4 粉末冶金成形
➢ 改善压坯密度不均匀性的措施:
✓(1)减小粉末与模具内壁的摩擦力。
➢碳化物 MeO+C→MeC+CO ➢硼化物 MeO+B4C+C→MeB+CO ➢硅化物 MeO+Si→MeSi+SiO(蒸馏) ➢氮化物 MeO+N2+NH3+C→MeN+CO+H2O+H2
15
4 粉末冶金成形 ✓ (5)化学方法,(Cu, Ni, Ag, Sn, Cr, Mn) ➢ 法拉第定律 对于同一物质来说,阳极和阴极上溶解和析出的 物质与通过电解质溶液的电量成正比。
4 粉末冶金成形
1
4 粉末冶金成形
粉末冶金
一种制取金属粉末以及采用金属粉末(或金属粉末与非金 属粉末的混合物)为原料,经过成形和烧结工艺获得零件 制品的工艺技术。
金相图谱内容说明

图谱文字说明第一部分金相图谱一.铁碳合金平衡组织图1 名称铁素体( 工业纯铁退火)组织铁素体说明等轴多边形晶粒为铁素体,黑色线条为晶界图2 名称奥氏体(T8钢950℃加热)组织 奥氏体说明 白色多边形晶粒为奥氏体,黑色线条为晶界。
高温下部分晶粒已合并长大,形成了混合晶粒图3 名称 渗碳体(从珠光体中电化学分离出来的滲碳体片)组织 渗碳体片说明 从珠光体中分离出来的渗碳体片,其形状是不规则的,一侧鸡冠似的形状,某些部位有孔图4 名称 亚共析钢组织( 20钢退火)组织 铁素体+珠光体说明 白色块状为铁素体,因放大倍数低,层状结构未能显示出来,珠光体呈黑色块状图5 名称 亚共析钢组织( 45钢退火)组织 铁素体+珠光体说明 白色块状为铁素体,黑色块状为珠光体图6 名称 亚共析钢组织( 60钢退火)组织 铁素体+珠光体说明 白色网状分布的为铁素体,珠光体呈黑色块状图7 名称 共析钢组织(T8钢退火)组织 层状珠光体说明 层状珠光体是铁素体和滲碳体的层状组织,因放大倍数较低,且分辨率小于滲碳体层片厚度,故只能看到白色基体的铁素体和黑色线条的滲碳体图8 名称 共析钢电镜组织(T8钢退火)组织 层状珠光体说明 深灰色基体为铁素体,白色条状为滲碳体图9 名称 过共析钢组织(T12钢完全退火)组织 层状珠光体+二次滲碳体说明 基体为层状珠光体,晶界上的白色网络为二次滲碳体图10 名称 亚共晶白口铸铁铸态组织组织 珠光体+变态莱氏体+二次滲碳体说明 变态莱氏体呈黑白相间的基体,大黑块为珠光体,大黑块珠光体外围的白色滲碳体为二次滲碳体图11 名称 共晶白口铸铁铸态组织组织 变态莱氏体说明 变态莱氏体中白色基体为滲碳体(共晶滲碳体和二次滲碳体),黑色圆状及条状为珠光体图12 名称 过共晶口铸铁铸态组织组织 一次滲碳体+变态莱氏体说明 基体为黑白相间分布的变态莱氏体,白色条状为一次滲碳体二.钢经热处理后组织图13 名称 索氏体(T8钢正火)组织 索氏体说明 索氏体是细珠光体,其层状结构只有在高倍金相显微镜下才可分辩图14 名称 索氏体电镜形貌(T8钢正火)组织 索氏体说明 浅灰色基体为铁素体,白色条状为滲碳体图15 名称 托氏体(45钢860℃油淬,试样心部)组织 托氏体+马氏体说明 托氏体是极细珠光体,在光学金相显微镜下呈黑色团絮状。
铁基粉末冶金零件常见生产缺陷的金相分析
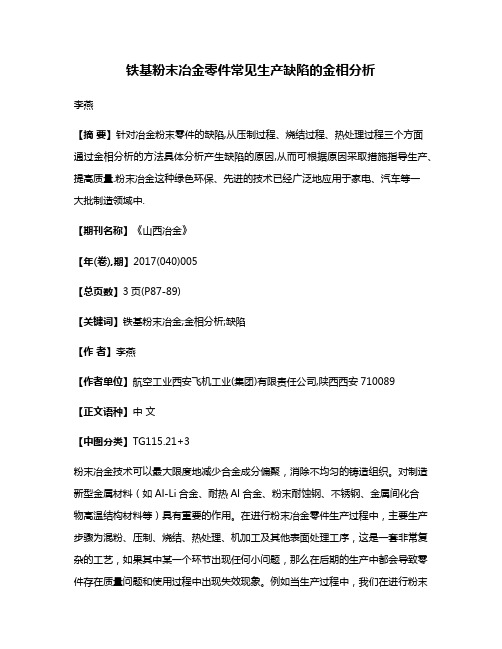
铁基粉末冶金零件常见生产缺陷的金相分析李燕【摘要】针对冶金粉末零件的缺陷,从压制过程、烧结过程、热处理过程三个方面通过金相分析的方法具体分析产生缺陷的原因,从而可根据原因采取措施指导生产、提高质量.粉末冶金这种绿色环保、先进的技术已经广泛地应用于家电、汽车等一大批制造领域中.【期刊名称】《山西冶金》【年(卷),期】2017(040)005【总页数】3页(P87-89)【关键词】铁基粉末冶金;金相分析;缺陷【作者】李燕【作者单位】航空工业西安飞机工业(集团)有限责任公司,陕西西安710089【正文语种】中文【中图分类】TG115.21+3粉末冶金技术可以最大限度地减少合金成分偏聚,消除不均匀的铸造组织。
对制造新型金属材料(如Al-Li合金、耐热Al合金、粉末耐蚀钢、不锈钢、金属间化合物高温结构材料等)具有重要的作用。
在进行粉末冶金零件生产过程中,主要生产步骤为混粉、压制、烧结、热处理、机加工及其他表面处理工序,这是一套非常复杂的工艺,如果其中某一个环节出现任何小问题,那么在后期的生产中都会导致零件存在质量问题和使用过程中出现失效现象。
例如当生产过程中,我们在进行粉末冶金的混粉施工工艺过程中,为了能够避免由于工艺不当造成的合金元素的偏析,必须要在进行轧制时使合金的参数保持在正常的范围内,防止零件在生产中出现裂纹、裂缝等现象;同时,注意生产过程中由于合金元素的偏析造成的零件脱碳、渗碳,以及氧化和冷却速率的异常,这样就能够避免在后期的热处理过程中防止由于出现渗碳造成的零件材料质地变硬,或者是由于处理时的温度没有达到标准温度出现零件硬度过低的现象。
但是,利用金相分析可以通过显微镜来观察组织评估,从而找到零件失效的主要原因,进而寻求一种解决办法改善生产工艺技术,金相分析是一种非常直观并有效的检测手段[1]。
英国冶金学家索比最早在1885年,利用光学显微镜应用直射光源,从而清晰地观察到珠光体的片层结构,并且其预测片层结构中厚的地方为纯铁,薄的片层为渗碳体组织。
- 1、下载文档前请自行甄别文档内容的完整性,平台不提供额外的编辑、内容补充、找答案等附加服务。
- 2、"仅部分预览"的文档,不可在线预览部分如存在完整性等问题,可反馈申请退款(可完整预览的文档不适用该条件!)。
- 3、如文档侵犯您的权益,请联系客服反馈,我们会尽快为您处理(人工客服工作时间:9:00-18:30)。
粉末冶金零件的金相制样除铸造、机械成形与机械加工等技术外,粉末冶金(P/M)技术也是制造金属零件的重要方法之一。
该技术可极大减少钢锭金属的不良性能,通过混合不同金属粉末、或金属与非金属粉末,可以达到预期理想的金属性能,而采用其它方法,这些金属通常不易熔成合金。
粉末加工、将其压制为有用形状、以及烧结的过程费用很高,但与锻件或铸件相比,采用这种方法最终制成的零件具有某些无可比拟的优点。
主要优点包括:- 可生成精细均质晶粒结构- 可形成复杂形状,尺寸公差精密- 制成品表面光洁度性能优良与其它成形方法相比,花费很高的机械加工过程可得以缩减或直接除去,于是减小了碎屑损失。
因此,对于小型、形状复杂,和精密零件(如齿轮、链环等)的大批量生产而言,粉末冶金技术是最经济有效的方法。
而且,通过该加工技术,可制造大量特种合金,这些合金具有完全不同材料性能,如高温刚度与硬度。
由碳化钨粉末烧结而成的高速切割刀具正是这样一个实例:采用粉末冶金加工技术获得许多独特的金属性能。
烧结压制零件的密度影响强度、韧性、硬度等重要性能,因此,达到特定的孔隙度至关重要。
为了进行工艺流程控制,需应用金相学知识以检验孔隙度、非金属杂质、以及交叉污染等。
在研究与失效分析中,金相学也是一个主要工具,用于开发新产品,改进加工工艺。
除化学分析外,质量控制还包括一些物理方法,以检验密度、尺寸变化、流率等。
金相制样困难之处研磨与抛光下图表示正确、典型孔隙度。
解决方案:足够长时间抛光粉末冶金零件制备制造为了达到粉末金属零件的理想构造与近净成形,需对以下生产程序进行严格工艺流程控制:- 制备粉末- 将粉末与添加剂(如:润滑剂、碳、和合金元素)混合- 在硬质合金模具中压制粉末- 在保护性气体环境下高温烧结(1100℃-1200℃)化学方法与雾化法是粉末制备中两种最常用的方法。
化学方法将金属在低于熔点的温度下从矿石氧化物直接转变为金属粉末。
例如,铁粉末制备如下:首先,直接从铁矿中提炼出海绵铁,然后,通过机械加工,将海绵铁压碎为粉末,再通过降低温度退火进一步精炼得到纯铁粉末。
这种方法适宜于合金与低密度金属应用场合,如轴承。
在雾化加工过程中,合金熔融金属液体流经一个喷嘴,并经高压水流或气体喷流冲击。
于是形成微滴,固化后,形成粒状物。
与机械碎化粉末相比,雾化粉末可得到更高的金属密度,因此,所有的钢粉末都是通过雾化法加工的。
铜粉末通过雾化法或电解法进行制备。
碳化钨粉末通过在钨粉末中加入一定控制量的碳,并在1400-2650℃高温下渗碳得到。
粉末制备与混合是一个非常专业、复杂的工艺加工过程,通过该过程,可定制粉末达到设计性能,以满足特定应用需求。
粉末混合良好不仅可实现特种合金所需的性能,而且,对于方便下一步粉末处理、压制与烧结也非常有必要。
例如:粉末的易流动性、及其与其它粉末的均匀混合性对于粉末在压制之前均匀分布非常重要,确保最终制作完成的零件内部结构保持均质一致。
零件加工时,混合粉末首先在高压下硬质合金模具中压制成形。
在此阶段,零件具有最终产品的几何形状,但没有达到其强度要求,因而被称之为“绿色”部件。
为了改进材料的机械与物理性能,需通过在烧结炉中高温烧结进行冶金结合。
冶金结合通过相邻晶粒之间扩散得以实现。
为了避免氧化作用(氧化作用将影响晶粒间的结合),烧结过程应在保护性气体环境下进行。
冶金结合增加了零件密度,经压制与烧结后的粉末金属零件通常含有5-25%的残余孔隙。
根据应用需要,一些零件还需另外经过热均衡压制以使尺寸更为精确,或经过表面抛光、油浸渗等工艺过程。
然后,进行终处理,如表面硬化、电镀、或涂层等。
粉末冶金零件金相制样困难之处硬质合金的烧结通过真空烧结工艺流程进行。
碳粉末与3-25%质量分数的钴混合,并加入微量的钛与碳化钽以抑制晶粒生长。
然后对该混合物进行压制与烧结。
在1280-1350℃高温下,钴发生液化作用,并形成类似共晶体状的WC/Co。
温度稍低后开始发生固化,并在液化之后很快达到理论上100%。
在液化过程中,零件体积缩减达40%之多。
应用粉末冶金零件主要用于以下领域:- 机械与结构零件,主要是铁基,也有铜、黄铜、青铜、与铝等。
粉末冶金(P/M)零件的最大用户是汽车工业领域。
零件供应商应用该技术制造连杆、同步接合套、链轮、凸轮、齿轮等。
- 耐高温金属,因其熔点很高,通过熔化、铸造很难制造。
- 多孔材料,其中孔隙度经过控制以作特殊用途,如自润滑轴承。
- 不形成合金的复合材料,如用于电触点的铜/钨、硬质合金切割工具(图3)、制动衬片与离合器衬片材料、金刚石切割工具、或金属基复合材料等。
- 特种重型合金,如用于喷气式发动机零件的镍钴基超合金;以及高速工具钢,其碳分布均匀,并具有各向同性性能(图4、5)。
此外,还生产用于热喷涂涂层的各种粉末与粉末混合物,并经金相质量控制。
金相制样的主要挑战在于:在研磨与抛光后显示真实的孔隙度。
根据材料的硬度不同,成功程度也不尽相同。
在软金属研磨过程中,磨掉的金属被压入孔中,然后通过抛光去除。
混合有硬材料与软材料的零件样品具有显著离隙。
因“绿色”零件易碎,其制样尤其需要谨慎与耐心。
粉末冶金零件制样建议切割要对特种金属与合金的粉末冶金零件进行切割,用户可根据推荐的表格与准则选择合适的切割砂轮。
对于混合材料,建议选用的切割砂轮应能适宜于对零件主要组成材料进行切割。
对于烧结硬质合金,建议使用树脂粘合的金刚石切割砂轮(24TRE,25EXO)。
“绿色”零件在切割前需镶嵌在冷埋树脂中(请参见“镶嵌”章节),以避免夹紧时被压碎。
镶嵌为了确保镶嵌树脂与样品材料之间具有很好的粘性,有必要在镶嵌之前采用丙酮、甲苯、或合成异构烷油 C*等,彻底清除样品油渍(处理溶剂时,请遵循安全使用操作规程)。
烧结零件可热镶嵌在树脂中,树脂与样品材料的硬度一致,可采用酚醛树脂( M u l t i F a s t )或增强树脂(DuroFast,IsoFast)。
“绿色”零件在切割后需在真空环境下用冷埋环氧树脂(CaldoFix,EpoFix,SpeciFix-40)重新浸渗。
可通过将少量(约1/2茶匙)粉末与慢凝环氧树脂混合,并将其倒入埋杯容器的方法,对粉末进行镶嵌。
在8小时凝固过程中,微粒在杯底沉淀,形成层状物。
硬金属粉末可通过与一量匙微粒镶嵌树脂IsoFast混合的方法,进行热镶嵌。
然后,将混合物倒入镶样机圆筒中,并用酚醛树脂封顶。
研磨与抛光粉末金属的研磨与抛光遵循相同的程序,即制备相同材料钢锭样品的程序。
大批量材料硬度>150HV的样品粗磨可在氧化铝磨石、或金刚石研磨盘(MDPiano)上进行。
材料硬度<150HV,可在碳化硅砂纸上粗磨。
对于金刚石精磨而言,精磨盘MD-Al legro适用于材料硬度>150HV的样品,而MD-Largo适用于材料硬度<150HV的样品。
然后用3μm金刚石悬浮液进行完全抛光,并用1μm悬浮液、或氧化抛光悬浮液进行短暂终抛光,粉末冶金零件制样的主要目标之一是显示真实的孔隙度,因此,金刚石抛光步骤应足够长以达到该目标(参见图6-9),这一点非常重要。
对于大型零件、或软金属零件制样,金刚石抛光需长达10-15分钟,以去除研磨过程中压入孔中的残余金属,并显示真实的孔隙度。
对于软金属而言,不应无谓拖长终抛光时间,因这将导致孔边缘磨圆。
从500#或800#开始,“绿色”零件将在碳化硅砂纸上手工研磨至4000#。
如有必要,表面需重新浸渗。
对于单个零件制样,抛光可在半自动抛光机上进行。
为了确定特种合金与零件的正确抛光时间,建议在抛光过程中每隔两分钟用显微镜检验其金相结构一次,只有当全部残余金属都从孔中去除后,才能进行下一步抛光程序。
一般而言,建议使用多晶金刚石悬浮液对粉末金属进行抛光。
如抛光过程过长,可使用Diapro金刚石悬浮液来代替。
清洗与干燥抛光后,有必要用水/清洁剂混合液对样品进行清洗,以去除孔中残余的抛光悬浮液与润滑剂。
然后再用水清洗,随后,用异丙醇溶液进行彻底清洗;将样品放在一个合适的角度,用温热空气流进行干燥。
请勿从顶部直接将空气流吹向样品表面,因为这样将迫使液流从孔中排出,从而在表面上留下污渍(图10)。
使用高品质乙醇进行清洗,以最小程度减小污渍,这一点非常重要。
粉末冶金(P/M)铜的制样方法浸蚀建议首先检验未浸蚀的样品,以查核密度、孔形状尺寸、氧化与杂质状况、烧结凹槽与游离石墨(参见图11、12)等。
掌握理论密度,以与孔隙度相比较,这一点非常重要。
经过这样的初步检验后,建议对样品即刻进行浸蚀以避免污渍干燥(当清洗与干燥液流从孔中逐渐排出时,即发生干燥)。
与具有定量孔隙度的其它粉末金属相较,对于非常致密的硬质合金而言,这一点就不那么重要。
为了显示内部结构,可使用文献中提及的常用化学腐蚀溶液,用于金属及其合金的腐蚀。
浸蚀程序如下:用异丙醇润湿表面,将样品表面朝上,浸入浸蚀剂中,并微幅搅动。
当达到一定的浸蚀时间后,将样品从浸蚀剂中取出,根据选用的浸蚀剂(参见下图),用异丙醇或水进行清洗,并用热气流进行干燥。
干燥后,应立即制作文字说明文档与照片文档。
粉末冶金(P/M)钢的制样方法烧结硬质合金的制样方法浸蚀时间取决于合金材料,时间选定需要经验。
如浸蚀时间过短,不同相之间的对比度就不够。
如浸蚀时间过长,则很难对不同相进行区分鉴别(参见图15-17)。
如对某些不熟悉的材料进行浸蚀,建议缩短浸蚀时间,并先用显微镜检验浸蚀结果。
如有必要,可再进一步浸蚀;而如果样品被过度浸蚀,则只有重新抛光。
以下是一些常用的浸蚀剂。
混合或使用化学试剂时,请遵循标准安全使用规程。
铜与铜合金:1. 100ml水 20ml盐酸溶液 5g三氯化铁 10-20秒先用水清洗,然后用异丙醇溶液清洗2. 100ml水 10g过硫酸铵溶液。
仅可使用新鲜未用的溶液!先用水清洗,然后用异丙醇溶液清洗钢:1. 1-3%硝酸乙醇腐蚀液,用于铁碳合金、铁碳铜合金、及预熔铁钼合金100ml乙醇1-3ml硝酸10-60秒,取决于碳含量用异丙醇溶液清洗(图14)2. 使用苦味酸乙醇溶液,区分马氏体与奥氏体100ml乙醇 4g苦味酸 10-60秒,取决于碳含量。
先用水清洗,然后用异丙醇溶液清洗(图13) 3. 区分珠光体、贝氏体、与马氏体:200ml乙醇 4g苦味酸 1-2ml硝酸 20-100秒,取决于碳含量及合金成分先用水清洗,然后用异丙醇溶液清洗不锈钢:Vllella试剂:45ml甘油15ml硝酸30ml盐酸30秒至5分钟先用水彻底清洗,然后用异丙醇溶液清洗烧结碳化钨:Murakami试剂100ml水10g氢氧化钠或氢氧化钾10g铁氰化钾通过浸泡进行浸蚀,或擦洗浸蚀先用水彻底清洗,然后用异丙醇溶液清洗小结:粉末冶金是零件制造的方法之一,适宜于通常不易熔成合金的金属零件制备,或结合了金属与非金属各自优点的复合材料零件制备。