主轴组件 1-2
第3章_典型部件设计(主轴、支承件、导轨)

3.1.4.1 主轴部件主支承常用滚动轴承 (1) 角接触球轴承(向心推力球轴承)
角接触球轴承极限转速较高;可以同时承受 径向和一个轴向的载荷,a越大,可承受的进给力 越大。主轴用的a一般取15o或25o。
传动件放在主轴的后悬伸端,较多用于带传 动,可便于传动带的更换,如磨床。
3.1.3.3 主轴传动件位置的合理布置 (2) 驱动主轴的传动轴位置的合理布置 ★在布置传动轴的位置时,应尽量使传动力
Q与切削力P两者引起的主轴轴端位移和轴承受力 的影响能互相抵消一部分。
3.1.3.4 主轴主要结构参数的确定 主轴的主要结构参数有:
3.1.4.1 主轴部件主支承常用滚动轴承 (1) 角接触球轴承 球轴承为点接触,刚度不高,为提高刚度,
同一支承处可多联组配。 组配方式有三种: 背靠背组合;面对面组合;同向组合。
3.1.4.1 主轴部件主支承常用滚动轴承 (2) 双列短圆柱滚子轴承 特点:内圈有1:12的锥孔,轴向移动内圈可
径向圆跳动
端面圆跳动
3.1.4 主轴滚动轴承
主轴轴承的类型、配置方式、精度、安装、 调整、润滑和冷却等都直接影响主轴部件的工作 性能。
常用主轴轴承有滚动轴承、液体动压轴承, 液体静压轴承、空气静压轴承等。
轴承的轴向承载能力和刚度,由强到弱依次 为:推力球轴承、推力角轴承、圆锥滚子轴承、 角接触球轴承;
以调整轴承的径向间隙和预紧; 轴承的滚子能承受较大的
径向载荷和转速; 轴承由两列滚子交叉排列,
数量较多,因此刚度很高; 不能承受轴向载荷。
3.1.4.1 主轴部件主支承常用滚动轴承 (3) 圆锥滚子轴承 特点:刚度和承载能力大,既可承受径向力,
lzc7第四篇三章主轴组件
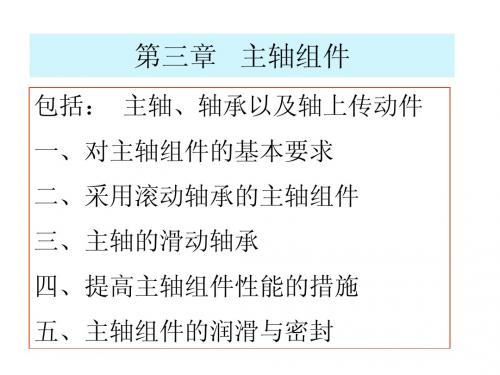
影响因素:
主轴、轴承、箱体孔的制造、装配和调整, 转速、支承设计,润滑剂,动平衡等
二、静刚度
静刚度:(刚度) 主轴组件抵抗静态外载荷变形的能力。 弯曲刚度K: 使主轴前端产生单位位移时,组位移方 向测量处所需施加的力。 即:K = F/δ (N/µm) ) 影响因素: 影响因素: 主轴尺寸形状 轴承型号数量 支承间距 传动件的布置方式 主轴前端悬伸量
车 床 主 轴 端 部
扭 定 矩 传 递 : 前 端 双 键 杆 从 后 端 拉 紧 孔 : 锥 位
铣 床 和 加 工 中 心 端 部
拉
7:24 7:24
短 锥 定 位 反 向 螺 母 锁 紧
外 圆 磨 床 主 轴 端 部
内圆磨床主轴 莫氏锥孔定位砂轮接杆并传递扭矩, 锥孔底部螺孔紧固接杆。
•
1.刚性支承、弹性主轴
L RB RA F a
δs
主轴前端受载F后,其挠度为: δs=( F a3 / 3 E I )(L/ a + 1 ) 柔度为:δs/ F=(a3 / 3 E I)(L/ a + 1 )
2. 刚性主轴、弹性支承
δk
RA
近似为线性变形 前后支承变形分别为δA 和 δB : δA =R A/KA δB =R B /K B 由于支承变形导致的主轴前端位移: δz =F/KA[(1+KA/KB)(a2/L2)+2a/L+1]
主轴结构之一:高刚度型
机床主轴结构之二:高速型
采用圆锥滚子轴承的主轴结构
多刀半自动车床主轴组件
磨床主轴
磨床主轴单元
内圆磨床主轴组件
第三节 主轴的滑动轴承
• 滑动轴承优点: 阻尼性能好 抗振性能好 • 分类: 液体滑动轴承 气体滑动轴承 支承刚度高 运动平稳 动压轴承 静压轴承
试谈数控机床_加工中心的结构设计
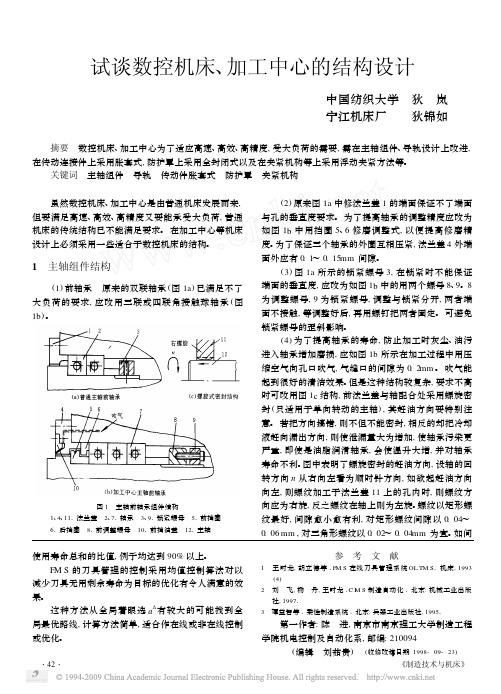
试谈数控机床、加工中心的结构设计中国纺织大学 狄 岚 宁江机床厂 狄锦如 摘要 数控机床、加工中心为了适应高速、高效、高精度,受大负荷的需要,需在主轴组件、导轨设计上改进,在传动连接件上采用胀套式,防护罩上采用全封闭式以及在夹紧机构等上采用浮动夹紧方法等。
关键词 主轴组件 导轨 传动件胀套式 防护罩 夹紧机构 虽然数控机床、加工中心是由普通机床发展而来,但要满足高速、高效、高精度又要能承受大负荷,普通机床的传统结构已不能满足要求。
在加工中心等机床设计上必须采用一些适合于数控机床的结构。
1 主轴组件结构 (1)前轴承 原来的双联轴承(图1a )已满足不了大负荷的要求,应改用三联或四联角接触球轴承(图1b )。
图1 主轴前轴承组件结构1、4、111法兰盖2、71轴承3、91锁紧螺母 51前挡圈61后挡圈 81前调整螺母 101前挡油盖 121主轴 (2)原来图1a 中修法兰盖1的端面保证不了端面与孔的垂直度要求。
为了提高轴承的调整精度应改为如图1b 中用挡圈5、6修磨调整式,以便提高修磨精度。
为了保证三个轴承的外圈互相压紧,法兰盖4外端面外应有0.1~0.15mm 间隙。
(3)图1a 所示的锁紧螺母3,在锁紧时不能保证端面的垂直度,应改为如图1b 中的用两个螺母8、9。
8为调整螺母,9为锁紧螺母,调整与锁紧分开,两者端面不接触,等调整好后,再用螺钉把两者固定。
可避免锁紧螺母的歪斜影响。
(4)为了提高轴承的寿命,防止加工时灰尘、油污进入轴承增加磨损,应如图1b 所示在加工过程中用压缩空气向孔口吹气,气缝口的间隙为0.2mm 。
吹气能起到很好的清洁效果。
但是这种结构较复杂,要求不高时可改用图1c 结构,前法兰盖与轴配合处采用螺旋密封(只适用于单向转动的主轴),其赶油方向要特别注意。
若把方向搞错,则不但不能密封,相反的却把冷却液赶向漏出方向,则使泄漏量大为增加,使轴承污染更严重,即使是油脂润滑轴承,会使温升大增,并对轴承寿命不利。
主轴组件

加工中心主轴组件分析报告一、主轴组件概述1.主轴组件定义加工中心主传动系统是由主轴电动机、主轴传动系统以及主轴组件组成,而主轴组件是加工中心的主传动部分的主要组成部分,在机床上,主轴主要作用是夹持工件或刀具旋转,提供足够的驱动功率或输出转矩,能在整个速度范围内提供切削所需功率和转矩,以满足机床强力切削时的要求,直接参加表面成形运动。
(应附图)主轴被比喻为“机床的心脏”,这是再恰当不过了,人们期望它输出更高的转速、更大的扭矩、更强劲的功率、更小的主轴跳动、更低的磨损率、更少的故障及更低的价格。
目前国内机床主轴的水平还未满足用户的要求。
2.国内外主轴现状比较在国外,主轴单元的设计大多是可以公开的,一些大轴承公司甚至公开出版书籍,教人们如何设计适合的主轴单元具体到使用什么轴承、轴承的精度等级、相应的配合公差、形位公差、主轴单元可以达到的精度、润滑方式、润滑油、密封方法、动平衡精度等,有的公司还会介绍如何装配,应在什么环境下装配等。
设计可以公开,但加工工艺就很少见诸文献。
大多数公司对工艺都严守秘密,好多出国考察的人士就反映主轴单元零件的精加工场所,甚至装配场所几乎都不允许参观。
因此很难叙述目前国外的工艺水平,只能从一些间接的现象来评估。
例如有时我们采用相同的设计、相同的材料、用同一轴承公司的型号、精度等级相同的轴承,而做不出相同精度或相同速度的主轴单元来。
对铣削加工中心,主轴跳动在1um已经是国内用户购买高精度机床的一个标淮,这对于国外的机床来说,也已经是一个非常普通的参数,甚至于价位很低的机床,反观我们国内的情况,还没有哪个厂家明确地在产品样本上标明主轴跳动为lum,而实际的情况更糟糕,机床的主轴指标往往是5um。
情况为什么会是这样呢?原因主要的还是主轴的结构设计、加工工艺、热处理工艺、装配工艺的问题。
这个也是以后开发主轴的技术难点。
此处至少应就主轴类技术指标、材料及热处理的差距列表,差距比较是表现技术水平高低的重要形式,必须有数据,国外在主轴方面的发展方向是什么,必须在文中有回答(并提供一些参考资料作为支持)二主轴组件的分类、功能、性能要求以下以铣加工中心作为例子介绍(1)主轴组件的分类:皮带式主轴、直结式主轴、内藏式主轴(电主轴)(应附图)三类主轴使用环境:皮带式主轴广泛用于小型机床上,并能满足机床对转矩特性的要求;直结式主轴虽然简化了主轴结构,有效地提高了主轴刚度,但主轴输出转矩小,电动机发热对主轴精度影响大;内藏式主轴是集皮带式主轴和直结式主轴优点,具有高速度,高精度,以及良好的稳定性能等多项优点,广泛用于数控钻铣设备,精密雕刻、雕铣、木工机械、精密磨床及其他数控高速机械。
JCS018A加工中心结构
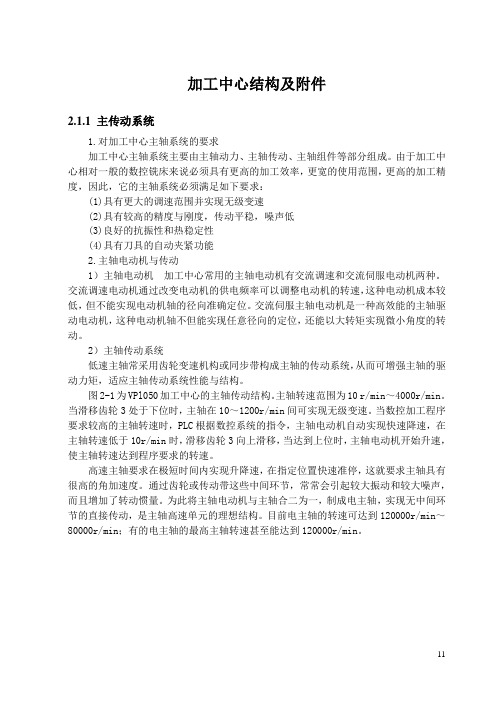
加工中心结构及附件2.1.1 主传动系统1.对加工中心主轴系统的要求加工中心主轴系统主要由主轴动力、主轴传动、主轴组件等部分组成。
由于加工中心相对一般的数控铣床来说必须具有更高的加工效率,更宽的使用范围,更高的加工精度,因此,它的主轴系统必须满足如下要求:(1)具有更大的调速范围并实现无级变速(2)具有较高的精度与刚度,传动平稳,噪声低(3)良好的抗振性和热稳定性(4)具有刀具的自动夹紧功能2.主轴电动机与传动1)主轴电动机加工中心常用的主轴电动机有交流调速和交流伺服电动机两种。
交流调速电动机通过改变电动机的供电频率可以调整电动机的转速,这种电动机成本较低,但不能实现电动机轴的径向准确定位。
交流伺服主轴电动机是一种高效能的主轴驱动电动机,这种电动机轴不但能实现任意径向的定位,还能以大转矩实现微小角度的转动。
2)主轴传动系统低速主轴常采用齿轮变速机构或同步带构成主轴的传动系统,从而可增强主轴的驱动力矩,适应主轴传动系统性能与结构。
图2-1为VPl050加工中心的主轴传动结构。
主轴转速范围为10 r/min~4000r/min。
当滑移齿轮3处于下位时,主轴在10~1200r/min间可实现无级变速。
当数控加工程序要求较高的主轴转速时,PLC根据数控系统的指令,主轴电动机自动实现快速降速,在主轴转速低于10r/min时,滑移齿轮3向上滑移,当达到上位时,主轴电动机开始升速,使主轴转速达到程序要求的转速。
高速主轴要求在极短时间内实现升降速,在指定位置快速准停,这就要求主轴具有很高的角加速度。
通过齿轮或传动带这些中间环节,常常会引起较大振动和较大噪声,而且增加了转动惯量。
为此将主轴电动机与主轴合二为一,制成电主轴,实现无中间环节的直接传动,是主轴高速单元的理想结构。
目前电主轴的转速可达到120000r/min~80000r/min;有的电主轴的最高主轴转速甚至能达到120000r/min。
图2-1 VP1050加工中心的主轴传动机构1-主轴驱动电动机 2、5-主轴齿轮 3-滑移齿轮 4、6-从动齿轮3.加工中心主轴组件加工中心主轴组件包括主轴、主轴轴承、传动件、密封件、自动夹紧装置、主轴定向装置和主轴锥孔清理装置等结构。
第10章 主轴组件PPT课件

金属切削机床
第三节 主 轴
主轴的结构 主轴材料与热处理方法 主轴技术要求
21
金属切削机床 主轴的结构 为了便于装配和满足轴承、传动件等轴向定位的需 要,主轴一般是阶梯形的轴。 有些主轴是空心的,如车床、铣床、加工中心等的 主轴。中孔用以通过棒料等。 d/D=0.7时,惯性矩下降约24%。为了不致使主轴 的刚度受太大的影响,孔径不宜超过外径的70%。
金属切削机床
a)
b)
常与双列圆柱滚子轴承配套使用
主轴轴承常用 轻系列、特轻系列、超轻系列
15
金属切削机床
主轴滚动轴承的精度 向心轴承: 0、6、5、4、2; 圆锥滚子轴承:0、6x、5、4、2; 推力轴承: 0、6、5、4
SP级和UP级作为补充;
旋转精度,相当于P4级和P2级;
(高)
内外圈的尺寸精度,则相当于P5级和P4级 (低)
轴承的工作精度主要决定于旋转精度
“成套轴承的内圈径向跳动”----Kia “成套轴承的外圈径向跳动”----Kea “轴圈滚道对底面的变动量”---Si(用于推力轴承)16
金属切削机床
表10-3
机床精度等级 前 轴 承
后轴承
普通精度级 精密级 高精度级
P5 或 P4(SP) P5 或 P4(SP)
主轴轴承在最高转速空转、连续运转至热稳态时允许温升为:
ቤተ መጻሕፍቲ ባይዱ
高精度机床 精密机床和数控机床 普通机床
810 ℃ 1520 ℃ 3040 ℃
滚动轴承温度不得超过 滑动轴承温度不得超过
70 ℃ 60 ℃
影响因素:
轴承间隙和预紧力的大小;润滑方式、散热条件等8
金属切削机床 5)耐磨性
长期保持原始精度的能力,即精度的保持性。 磨损后对精度有影响的部位首先是轴承。其次是安 装夹具、刀具或工件的定位面和锥孔, 还有如钻、镗床 的移动式主轴的内、外导向表面。
第3章 主轴组件设计
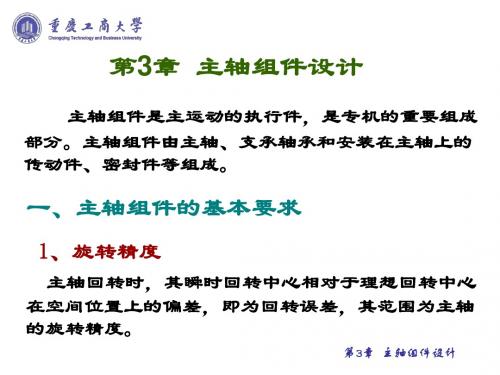
第3章 主轴组件设计
主轴前直径可根据电动机功率并参考 同类设备确定, 同类设备确定,后轴颈可参考前轴颈 直径确定。通常,D ( 直径确定。通常 2=(0.7~0.85)D1
第3章 主轴组件设计
(2)主轴内孔直径的确定 首先,内孔 的大小 的大小, 首先,内孔d的大小,应在满足主轴刚度的前 提下,尽量取大值;其次,内孔d大小的确定与 提下,尽量取大值;其次,内孔 大小的确定与 用途有关,通常不小于主轴平均直径55%~60%。 用途有关,通常不小于主轴平均直径 。 (3)主轴前端悬伸量的确定 前端悬伸量是指主轴组件前支承径向反力 作用点到前端受力作用点之间的距离。 作用点到前端受力作用点之间的距离。 前端悬伸量a的确定主要取决于主轴端部的结 前端悬伸量 的确定主要取决于主轴端部的结 前支承轴承配置和密封装置的型式和尺寸, 构、前支承轴承配置和密封装置的型式和尺寸, 由结构设计确定。 由结构设计确定。 第3章 主轴组件设计
第3章 主轴组件设计
上图所示,瞬时回转中心线相对于理想旋转中心线 上图所示 瞬时回转中心线相对于理想旋转中心线 在空间位置上的偏差被称为回转误差; 在空间位置上的偏差被称为回转误差;两线在空间位 置上的符合程度被称为回( 转精度。 置上的符合程度被称为回(旋)转精度
第3章 主轴组件设计
2、静刚度
第3章 主轴组件设计 章
主轴组件是主运动的执行件, 主轴组件是主运动的执行件,是专机的重要组成 部分。主轴组件由主轴、 部分。主轴组件由主轴、支承轴承和安装在主轴上的 传动件、密封件等组成。 传动件、密封件等组成。
一、主轴组件的基本要求
1、旋转精度
主轴回转时, 主轴回转时,其瞬时回转中心相对于理想回转中心 在空间位置上的偏差,即为回转误差, 在空间位置上的偏差,即为回转误差,其范围为主轴 的旋转精度。 的旋转精度。
CA6140型普通卧式车床结构剖析——实验指导书2019.11.05

CA6140型普通卧式车床结构剖析——实验指导书2019.11.05CA6140型普通卧式车床结构剖析实验指导书课程名称:⾦属切削机床所在学院:核技术与⾃动化⼯程学院教师姓名:郝兴安授课专业:机械⼯程编写⽇期:2018.11.16⼀、实验⽬的1.了解CA6140型普通卧式车床的⽤途、总体布局,以及主要技术性能。
2.掌握CA6140型普通卧式车床的传动原理和路线。
3.掌握CA6140型普通卧式车床主轴箱、进给箱的构造和⼯作原理。
4.了解CA6140型普通卧式车床溜板箱、⼑架、尾座的构造和⼯作原理。
5.本实验项⽬为验证性实验,要求同学认真预习有关课程知识。
⼆、实验设备、仪器及⼯具1.CA6140型普通卧式车床1台2.TYKJ—6140型透明教学车床1台3.CA6140型普通卧式车床的结构挂图4.15⼨活络扳⼿⼀把、内六⾓扳⼿1套、300mm的⼀字旋具把三、注意事项1.关闭电源后,⽅可观察机床内部结构。
2.操作应符合基本操作规范。
3.实验时必须严格遵守实验设备和仪器的各项操作规程,在指导教师的指导下进⾏实验。
四、实验原理了解和分析CA6140型普通卧式车床的主要零部件的构造、功⽤和⼯作原理。
五、实验内容与步骤1.观察CA6140卧式车床的外观,了解卧式车床的⽤途、布局、各操纵⼿柄的作⽤及其操作⽅法。
2.揭开主轴箱盖,根据CA6140卧式车床的传动系统图和主轴箱展开图,看清实现主轴各级转速传动路线及有关传动件的构造。
(1)看懂标牌上符号的意义,明确主轴箱各操纵⼿柄的作⽤。
(2)分析主传动系统的传动路线,主轴的正转、反转、⾼速、低速的各条传动路线是如何调整实现的。
(3)结合现教学挂图,分析摩擦离合器的结构原理及其调整原理和操纵动作的过程,摩擦离合器与制动器的操纵动作的配合关系。
(4)操纵有关⼿柄使Ⅱ—Ⅲ轴上两个沿移齿轮移动,操纵有关⼿柄使Ⅳ轴上的两个滑移齿轮及Ⅵ轴上的⼀个滑移齿轮移动,注意它们的动作过程和啮合位置。
第三章-主轴部件

切
动压轴承和静压轴承两类。按照流体介质不同可分为
削
液体滑动轴承和气体滑动轴承。
机
(一)动压轴承
床
动压轴承按油楔数分为单油楔和多油楔。多油楔轴承
设
的轴心位置稳定性好,抗振动和冲击性能好。故多采
计
用多油楔轴承。
多油楔轴承有固定多油楔和活动多油楔两类。
返回本节
下一页
返回主页
退出
3.1.5 主轴滑动轴承
第 三
床
支承,中间支承为辅助支承,参见图2‐23; 也可以前、中支承为主要支承,后支承为
设 计
辅助支承,见图2‐29。且后者应用较多。
返回本节
下一页
返回主页
退出
图2‐23 卧式车床主轴箱展开图
中间支承为辅助支承 前后支承为主支承
图2‐29 加工中心主轴箱展开图
第 三
章
金 属 切 削 机 床 设 计
后支承为辅助支承 前中支承为主支承
《机械制造装备设计》
第三章 典型部件设计
主讲:王焱清
机械学院工业与制造工程系
3.1 主轴部件设计
退出
第
一、主轴部件应满足的基本要求
三 章
二、主轴部件的传动方式
金 属
切
三、主轴部件结构设计
削
机
四、主轴滚动轴承
床 设
计
五、主轴滑动轴承
返回本章
上一页
返
回
下一页
主
页
3.1.1 主轴部件应满足的基本要求
第 三
章
金 属 切 削 机
床
设
计
放在两个支承间靠近支承,受力情况良好, 最为常前见。
3.1.3 主轴部件结构设计
第三章 主轴组件设计解析
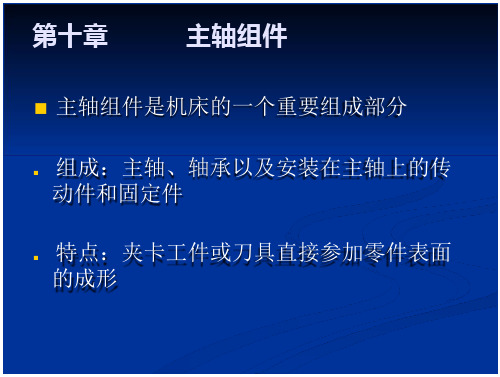
■ δa1、 δa2 可根据δa 计算得到 ■ 同 理 δb1、 δb2 也可根据δb计算得到
■ 一般情况下δ1等于δa1、δb1、δc1的均方根值 ■ δ2等于δa2、δb2、 δc2的均方根值
■ 据此,可算出δc1和δc2
■ 主轴的第⑶项公差就是根据2倍的δc1、 δc2 值
确定的
■ 4、短锥C对轴径A、B的径向圆跳动 ■ 短锥C是卡盘的定心轴颈。精度检验标准规
■ 二、轴承精度
■ 主轴轴承的精度主要采用P2、P4、P5 级
■ (B、C、D)相当于ISO 2、4、5 级
■ 此外,又规定了SP级和UP级作为补充
■ 结构对精度的影响:
■ a、向心轴承用于切削力方向固定的主轴, 对径向旋转精度影响最大的是“成套轴承的 内圈径向跳动” Kia
■ b、如用于切削力方向随主轴旋转而变化的 主轴,对轴承径向旋转精度影响最大的是 “成套轴承的外圈径向跳动” Kea
■ 轴瓦除了径向摆动外,也可轴向摆动
■ 轴瓦与球头螺钉接触面积要大于 80% 以保 证接触刚度
■ 轴承间隙靠螺钉调整 ■ 缺点是综合刚度低于固定多油楔轴承
■ 二、液体静压轴承
■ 静压轴承的油膜压 强由外界液压泵供 给
■ 油膜厚度对轴径和 轴承孔的圆度误差 起均化作用
■ 1、工作原理
■ 如图
■ 2、节流器
■ 型号:NN3000K(3182100) ■ NNU4900K(4382900)
■ 特点:内孔为 1:12 的锥 孔与主轴的锥形轴颈相配 合,只承受径向力
■ 间隙的调整: ■ 轴向移动内圈 ■ 适用场合: ■ 载荷较大、刚度要求较高,
中等转速
■ 2、双向推力角接触球轴承 ■ 型号:234400(2268100) ■ 特点:可承受双向的轴向载荷 ■ 它与双列圆柱滚子轴承配套使用
主轴组件图库
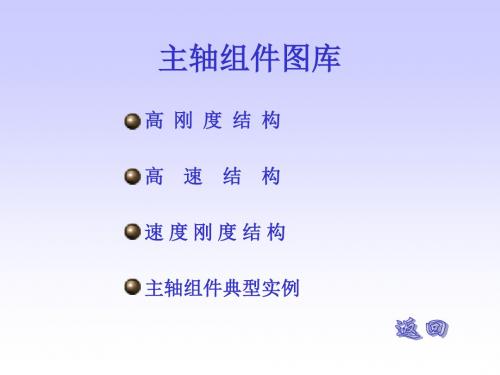
角接触球轴承具有良好的高速性能,但它 的承载能力较小,因而适用于高速轻载或精密 机床,如高速镗削单元、高速CNC车床等。
• 返回
典型高速结构
MNC 300
SKF 1
SS 125
NDM-40
76_300
返回
• MNC 300 该高速CNC车床主轴前后轴承都采用两 联角接触球轴承,具有较高的转速。
速度刚度结构
FNR 140 FNC 200 H2_077 SAG 101 BTA_B
HF2
SDNC 560
TNC 131
TS_15
返回
• FNR 140 返回
• FNC 200 返回
• H2_077
返回
• SAG 101
返回
• BTA_B返回• Fra bibliotekF2返回
• SDNC 560 返回
• TNC 131
主轴组件图库
高刚度结构 高速结构 速度刚度结构 主轴组件典型实例
高刚度结构
• 前支承用双列圆柱滚子轴承承受径向载 荷和60°角接触双列向心推力球轴承承 受轴向载荷,后支承采用双列短圆柱滚 子轴承。
这种轴承配置的主轴部件,适用于
中等转速和切削负载较大,要求刚度高 的机床。如数控车床主轴、镗削主轴单 元等。
返回
• TS_15
返回
机床主轴实例
• 返回
该图为具有一级转速的变速箱展开
图。最下面的轴是电动机轴或运动输入 轴,最上面的轴是机床主轴,主轴的位 置主要由车床的中心高确定。
• 返回
该图是采用圆锥滚子轴承的主轴部件,结 构比采用双列短援助滚子轴承简化,承载能力 和刚度比角接触球轴承高。但是因为圆锥滚子 轴承发热大、温升高,允许的极限转速要低些。 适用于载荷较大、转速不太高的普通精度的机 床主轴。
《变速箱工作原理》PPT课件

缺点: a.中性转向或稍有不足转向特性; b.轴距较长、传动轴较长需要加辅助支撑; c.整车装备质量大; d.传动轴限制了轿车地板的降低。
3.2前置发动机前轮驱动(前置前驱FF)
优点: a.机构紧凑,内部空间大; b.整车装备质量小8%左右; c.轴距小10%左右; d.降低成本; e.方向稳定性好,高速行驶安全性好; 这种布置形式应用于微型、普通级和中级轿车
两轴式变速器与离合器、主减速器的壳 体连成一体,且主减速器器的主动齿轮就 装在变速器第二周的输出端。
16
一轴 中间轴 图3:3轴式变速器
二轴
17
2.2 三轴式变速器
如图3所示结构:第一、二轴同心并与中间轴平行。 第一轴的前端用轴承支撑与 发动机飞轮中心,并 经花键与离合器从动盘相连;第二轴的后端经用 花键连接的突缘装有中央制动鼓和传动轴的千万 向节。第一轴的后端与其成一体的长啮合齿轮及 第二轴的各档齿轮分别与中间轴相应的齿轮啮合。
特点: a.除直接档外,其它各档的传动效率有所降低; b.在齿轮中心距较小的情况下,仍然可以获得大
的一档传动比。
18
下面是我部门开发的5T17变速箱齿轮与轴的安排 1-五倒档同步器 2-主轴五档齿轮 3-主轴四档齿轮
4-三/四同步器 5-主轴三档齿轮 6-主轴 7-副轴 8副轴一档齿轮 9-一/二档同步器 10-副轴二档齿轮 红色箭头为一档传动路线 黄色箭头为二档传动路线 绿色箭头为三档传动路线 蓝色箭头为四档传动路线 紫色箭头为五档传动路线
空调、灯光、雨刮,以及其他为满足
舒适性、安全性需要而设置的部件。
2
1.离合器 2.变速器 3.万向节 4.驱动桥 5.差速器 6.半轴 7.主减速器 8.传动轴
图 1 传动系机构图
章节自测题及答案

机械制造装备习题及解答第一章金属切削机床1-1指出下列机床型号的含义:CM6132,CM1107,Y5132,Y3150E,M1432A,Y7132A。
答:CM6132:最大加工直径为320mm的精度车床。
CM1107:最大棒料直径为7mm的精密单轴纵切自动车床。
Y5132:最大加工直径为320mm的插齿机。
Y3150E:最大加工直径为500mm经过第五次重大改进的滚齿机。
M1432A:最大磨削直径为320mm经过第一次重大改进的万能外圆磨床。
Y7132A:最大加工直径为320mm经过第一次重大改进的锥形砂轮磨齿机。
1-2.何谓简单的成形运动?何谓复合的成形运动?答:如果一个独立的成形运动,是由单独的旋转运动或直线运动构成,则此成形运动为简单的成形运动。
如果一个独立的成形运动,是由两个或者两个以上的单元运动(旋转或直线)按照某种确定的关系组合而成,并且相互依存,这种成形运动成为复合的成形运动。
1-3母线和导线的形成方法及所需要的运动。
答:母线和导线统称发生线,形成发生线的方法有四种(1)轨迹法发生线形成方法:刀刃为切削点,它按照一定的规律做轨迹运动。
只需要一个独立的成形运动。
(2)成形法发生线形成方法:刀刃为一条切削线,它的形状和长短与所需要成型的发生线一致运动:不需要专门的成形运动(3)相切法发生线形成的方法:刀刃为切削点,它是旋转刀具刀刃上的点,切削刀具的需安装中心按一定规律轨迹运动,切削点运动轨迹的包络线(相切线)就是发生线。
运动:需要两个独立的成形运动,即刀具的旋转运动和刀具的回转中心的轨迹运动。
(4)展成法发生线形成的方法:刀刃为一条切削线,但他与需要形成的发生线不相吻合,在形成发生线的过程中,展成运动使切削刃与发生线相切并煮点接触而形成与他共轭的发生线,即发生线是切削点的包络线。
运动:需要一个独立的成形运动,即展成运动。
1-4用成形车刀车削成形回转表面。
答:母线—曲线,由成形法形成,不需要成形运动。
数控车床主轴的组件结构及平衡校正[精]
![数控车床主轴的组件结构及平衡校正[精]](https://img.taocdn.com/s3/m/93f98ae1680203d8ce2f2483.png)
序号 1 2 3 4
5
刚性转子动平衡工艺过程
名称
操作过程
安装调整
转子装上动平衡机,与动平衡机调整中心 调整水平,然后与联轴器联接
测原始 不平衡量
试加重量
起动动平衡机,升速至平衡转速,在仪表 上显示并记录转子的不平衡量
按测得原始不平衡量进行标定、计算,并 得出在校正平面上试加的重量
将转子或装上工艺轴的圆盘状转子放在静平衡台上, 使其沿水平方向来回自由滚动。滚动停止后,在通 过中心的铅垂线上半部某一选定半径处,试加重量, 直至转子在任何角度均能静止;取下试加的重量, 用等效法去重或加重后,再校平衡,即达到静平衡。
经过静平衡的转子,可确定其剩余不平衡量。即在 校正平面上将圆周八等分,在各等分线处于水平位 置时试加重量,逐个测出8个开始转动的重量,取 最大试重与最小试重之差的1/2,即为静平衡后的 剩余不平衡量。
谢谢
数控机床机械部件装调
数控车床主轴的组件结构 及平衡校正
一、数控车床主轴结构
斜床身的 数控车床
二、主轴的平衡校正
平衡校正:
机械设备中作回转运动的部件,如盘状体、曲轴等, 一般统称为转子。由于转子材质不均、结构不对称、 加工和装配误差及运行后的变形等多种因素的影响, 会导致转子重心偏离其旋转中心(即存在不平衡 量),使机器运行时产生振动和噪声。从实用价值 和经济效果两方面考虑,不同的机器只能允许转子 有一定的不平衡量存在。平衡校正的目的就是通过 一定的方法和手段,降低转子的不平衡量,保证机 器运转时,产生的振动和噪声在允许范围内,以改 善工作环境和机器使用寿命。
为防止动平衡机支承系统受到超载或超速的损害, 动平衡机制造厂对外形对称的转子,规定一个 “质量-速度”限值mn²(m为转子质量,n为选定 的动平衡机转速)。对外形不对称的转子则要换 算成等效质量。
- 1、下载文档前请自行甄别文档内容的完整性,平台不提供额外的编辑、内容补充、找答案等附加服务。
- 2、"仅部分预览"的文档,不可在线预览部分如存在完整性等问题,可反馈申请退款(可完整预览的文档不适用该条件!)。
- 3、如文档侵犯您的权益,请联系客服反馈,我们会尽快为您处理(人工客服工作时间:9:00-18:30)。
形成工件表面。所以.一台机床的加工质且在很 大程度上决定于主轴组件的质量。
主轴要传递扭矩,直接承受切削力,而且还要
满足通用机床、专用机床、数控机床各自不同的 要求。
这些要求包括:
一、旋转精度
主轴组件的旋转精度定义:是指装配后,
在无载荷、低速转动的条件下,主轴前端 安装工件或刀具部位的径向跳动和轴向跳 动。
影响主轴组件的旋转精度的因素:主要取
决于各主要件,如主轴、轴承、箱体孔等 的制造、
二、静刚度
主轴组件的弯曲刚度K定义:使主轴前端产生单
位位移时,在位移方向测量处所需施加的力 (如 图4.3-1) ,即
K F / (N / m) K F/δ (N/m)
影响主轴组件的弯曲刚度的因素:如主轴的尺寸
(2)其端部的定心锥面、定心轴颈和锥孔等部位,应高 频淬硬至50HRC~55HRC。
(3)若采用滑动轴承,则轴颈处也需淬硬,硬度同上。
(4)精密机床主轴希望淬火变形和应力小些,可选用 40Cr或低碳合金钢20Cr、16MnCr5、12CrNi2A等渗碳 淬硬至 HRC≥60。
(5)采用滑动轴承的高精度磨床砂轮主轴,镗床、坐标 镗床、加工中心的主轴,要求有很高的耐磨性,这时可 用 渗 氮 钢 ( 如 38CrMoAlA) 经 渗 氮 处 理 , 表 面 硬 度 可 达 1100HV~1200HV(相当于69HRC一72HRC)。
一、主轴滚动轴承的类型
(1)主轴轴承选择:根据精度、刚度和转速选择。 (2)为了提高精度和刚度,主轴轴承的间隙应该是
可调的。这是它的主要特点。 (3)线接触的滚子轴承比点接触的球轴承刚度高,
但它在一定温升下允许的转速比球轴承低。 (4)因为一般机床主轴尺寸都较大,相对地讲轴承
负载较轻,轴承的承载能力和疲劳寿命不是选择主 轴轴承的主要指标。
和形状,滚动轴承的型号、数量、配置形式和预 紧,滑动轴承的类型和油膜刚度,前后支承间的 主轴前端的悬伸量,传动轴的布置方式,主轴主 件制造和装配质量等。
图4.3-1
三、抗振性
主轴组件产生振动的危害:降低工件的表
面质量和刀具耐用度,缩短主轴轴承寿命, 还会产生噪声影响环境。
振动表现形式:主要有强迫振动和自激振
第二节 采用滚动轴承的主轴组件
滚动轴承和滑动轴承都可用于机床主轴,都能满
足旋转精度的要求。相比之下滚动轴承有下述优 点:①在转速和载荷变化范围很大的情况下滚动 轴承仍能稳定工作,②滚动轴承能在零间隙、甚 至负间隙(预紧到 有一定过盈量)的条件下工作, 对提高旋转精度和刚度有利;③滚动摩擦系数小, 发热少;④滚动轴承容易润滑,可以用脂润滑, 装填一次用到修理时才更换,若用油时所需油量 也远比滑动轴承小;⑤滚动轴承为标准件,可以
图4.3-2
图e为钻、镗床主轴端部: (1)刀杆或刀具靠莫氏锥孔 定位; (2)前面扁孔传递扭矩; (3)后部扁孔拆卸刀具。
图4.3-2
图f为组合机床主轴端部: (1)圆柱孔用来安装接杆; (2)刀具则安装在接杆的 莫氏锥孔内; (3)前端圆螺母用来调整 刀具的轴向位置; (4)平键用来传递扭矩。
图4.3-2
图c为外圆磨床砂轮主轴端部: (1)法兰盘靠前端1:5的圆锥 面定位; (2)用螺母固定; (3)螺母的螺纹旋向必须与砂轮 的旋转方向相反,以防止启动时 因砂轮惯性而导致松脱。
图4.3-2
图d为内圆磨床砂轮主轴端部: (1)砂轮的接杆靠莫氏锥孔 定位并传递扭矩; (2)同时用锥孔底部螺孔紧 固接杆。
六、主轴的结构
1)为了提高刚度,主轴的直径应尽量大些。前轴 承至主轴前端面的距离(称悬伸量)应尽可能小些。 为了便于装配,主轴常做成阶梯形的。主轴的结 构与形状和主轴上所安装的传动件、轴承等零件 的类型、数量、位置和安装方法有直接的关系。
2)为了便于在主轴上安装各种标准刀具或夹具,主 轴前端部已标准化了。各类机床主轴前端结ห้องสมุดไป่ตู้形 状(如图4.3-2)
其主要技术要求如下(单位为mm):
现以一车床主轴为例,说明制定技术要求的原则。
图4.3-3
(1)轴颈A和B的圆度 A=0.003,B=0.0025 (2)莫氏锥孔和A、B面用涂色法检查接触率≥70% (3)莫氏锥孔对轴颈A、B的径向圆跳动
近轴端 0.005 , 300mm处 0.010 (4)短锥C对轴颈A、B的径向圆跳动0.005。 (5)端面D对轴颈A、B的端面圆跳动 0.010 以上技术条件可分为三类:
3.角接触球轴承(如图 e、f 所示) 这种轴承既可承受径向载荷,又可
承受轴向载荷,接触角度通常为α= 15º和α=25º两种,它的编号为 7000C(旧编号36100)和 7000AC(旧编号46100)系列。
15º接触角的轴承多用于轴向力较小、转速较高的地 方,如磨床主轴;25º接触角的多用于轴向力较大的 地方,如车床和加工中心主轴。这种轴承调隙(预紧) 时只需使内、外圈产生相对轴向位移即可。这种轴承 多用于高速主轴。目前,国内外在数控机床上采用最 多。
第二章 主轴组件
主轴组件是机床的一个重要组成部分。
它包括主轴、轴承以及安装在主轴上的传 动件。
机床工作时,主轴要夹持着工件或刀具
共同完成表面成形运动,所以,主轴组件 的工作性能将直接影响加工工件的质量和 机床生产率。
第一节 对主轴组件的基本要求
与一般传动轴一样,主轴也要在一定的转速下
传递一定的扭矩。
三类技术条件:
(1)与工作和测量基准有关的项目; (2)与机床精度检验直接有关的项目; (3)其它各项。
下面分析前两类。
(—)与工作和测量基服有关的项目
(1)主轴中心线是指前后两轴颈A和B的圆心连
线,它是技术要求(3)一(5)项的测量基准,又是主 轴莫氏锥孔的工艺基准。因此,必须首先保证这 两轴颈的圆度。因为若轴颈截面不圆,就不会有 稳定的圆心。
为了提高轴承高度和承载能力,可将多个角接触球 轴承组合使用。
图4.3-5a、b、c为3种基本组合方式。这3 种 组合方式是两个轴承共同承担径向载荷。图a 和b可承受双向轴向载荷,图c则只能承受一个 方向的轴向载荷,但承受能力较大,轴向刚度 较高。这种轴承还可以三联(图4.3-5d)、四 联组合。
主轴要承受弯矩,因而希望轴承上产生一
(2)必须保证这两个轴颈锥度与滚动轴承锥孔的
一致性。用标准镊度规靠涂色法检查接触率(>70 %)来保证银角的准确性。这是第(2)项要求。
(二)与机床精度检验有关的项目
机床是以锥孔的轴线来代表主轴中心线的。主 轴部件装配后,在锥孔内插入一根长300mm以上 的检验棒。
卧式车床精度检验标准规定了检验棒的径向跳 动检验方法和数值。
八、主轴的技术要求
1. 主轴轴颈、支承孔的直径公差和形状公差
现以一车床主轴为例,说明制定技术要求的原则。
图4.3-3
现以一车床主轴为例,说明制定技术要求的原则。
图4.3-3
图中A、B处是安装轴承的轴颈,直径分别 为105mm、75mm,1:12锥面;前后轴承 精度均为P5级;C、D是安装卡盘的定心锥面 和端面。
外购。
第二节 采用滚动轴承的主轴组件
滚动轴承的缺点是:①滚动体的数目有限,所以滚动轴
承在旋转中的径向刚度是变化的,易产生振动;②滚动体 与内外圈是刚性接触,而滑动轴承的油膜形成粘性阻尼层, 故滚动轴承的阻尼较滑动轴承要低;③滚动轴承的径向尺 寸比滑动轴承大。
由上分析可知,在一般情况下尽量采用滚动轴承,尤其
接触球轴承,它由外圈2、内圈 1和4,以及隔套3等组成,接 触角α为60º。
修磨隔套3的厚度即可消除间隙并预紧。 它的公称外径与同孔径的双列圆柱滚子轴承相 同,但外径为负公差,与箱体孔间有间隙,因而 不承受径向载荷。 外圈2上开有油槽和油孔,以利于润滑油进入 轴承。其编号为234400(旧编号2268100)。
这种轴承的特点之一是接 触角α大,钢球直径小而数量 多,轴承承载能力和精度较 高,允许的极限转速高于一 般推力轴承,常用于高速、 较精密的机床主轴。
瑞典SKF公司还有(1)α=40º的246800型轴 承,形状与234400相同;(2)窄形的双向推力 角接触球轴承,其内外圈宽度相等,内径、外径 和公差都与234400相同(3)α=40º,特称 BTA-B系列。
主轴滚动轴承的类型主要包括:
1.双列圆柱滚子轴承 2.双向推力角接触轴承 3.角接触球轴承 4.圆锥滚子轴承 5.深沟球轴承
其图如下:
图4.3-4
分别讨论如下:
1.双列圆柱滚子轴承 图4.3—4a为NN3000K(旧编号
3182100)系列轴承,是特轻型: (1)内圈有1:12的锥孔与主轴的锥形轴 颈相配,通过轴向移动内圈,靠弹性变形 使内圈胀来消除间隙或预紧。 (2)两列直径和长度相等的短圆柱滚子 交错排列,且滚于数目多,载荷均布,承 载能力大。 (3)这种轴承的特点是径向刚度和承裁 能力都大,旋转精度高。但它不能承受轴 向载荷,内圈薄且开有两条滚道,厚薄不 匀,调间隙时内圈滚道易发生畸变。为避 免这一缺陷,出现了下页所示的轴承:
此外: (1)主轴中孔用于通过棒料、拉杆或 其它工具; (2)为了能通过更组的棒料,车床的 中孔直径希望大些,但受刚度条件的限 制,孔径不宜超过外径的70%。
七、材料和热处理
主轴材料的选择主要根据耐磨性和热处理变形来考 虑。
(1)普通机床主轴,可用45号或60号优质中碳钢,调质 到220HBS一250HBS。
动两种形式。
影响抗振性的因素:主要有主轴组件的静
刚度、质量分布和阻尼(特别是主轴前轴承 的阻尼)。
四、温升和热变形
主轴组件工作时因各相对运动处的摩擦 和搅油等而发热,产生温升,从而使主轴 组件的形状和位置发生变化(热变形)。