机械零件设计概论
机械设计基础第9章机械零件设计概论(六-1)

一)强度准则
强度准则是指零件中的应力不得超过许用值。
即: σ ≤ σlim
σlim ----材料的极限应力
脆性材料:σlim = σB (强度极限)
延伸率 < 5%
塑性材料:σlim = σS (屈服极限) 延伸率 > 5%
为了安全起见,引入安全系数S,得:
B
如齿轮、凸轮、滚动轴承等。
潘存云教授研制
潘存云教授研制
若两个零件在受载前是点接触或线接触。受载后,
由于变形其接触处为一小面积,通常此面积甚小而表
层产生的局部应力却很大,这种应力称为接触应力。
这时零件强度称为接触强度。
机械零件的接触应力通常是随时间作周期性变化的,在载荷重复作用下,首先在
表层内约20μm处产生初始疲劳裂纹,然后裂纹逐渐扩展(润滑油被挤迸裂纹中将
▲使用功能要求 ▲经济性要求 ▲劳动保护要求 ▲可靠性要求 ▲其它专用要求
机器的可靠度——指在规定的使用时间内和预定的环 境下机器能够正常工作的概率。
机器由于某种故障而不能完成预定的功能称为失 效,它是随机发生的,其原因是零件所受的载荷、环 境温度、零件本身物理和机械性能等因素是随机变化 的。为了提高零件的可靠性,就应当在工作条件和零 件性能两个方面使其变化尽可能小。
▲使用功能要求 ▲经济性要求 ▲劳动保护要求 ▲可靠性要求 ▲其它专用要求
其它专用要求——针对不同机器所特有的要求。例如: 1)对机床有长期保持精度的要求; 2)对飞机有质量小,飞行阻力小而运载能力大的要求;
3)对流动使用的机器有便于安装和拆卸的要求;
4)对大型机器有便于运输的要求等等。
机械零件设计概论

2. 塑料 塑料的比重小,易于制成形状复杂的零件, 而且各种不同塑料具有不同的特点,如耐蚀性、绝热 性、绝缘性、减摩性、摩擦系数大等,所以近年来在 机械制造中其应用日益广泛。 3.其它非金属材料:皮革、木材、纸板、棉、丝等。
各种材料的化学成分和力学性能可在相关国标、行标 和机械设计手册中查得。
选用原则: 优选碳素钢,其次是硅、锰、硼、钒类合金钢。
将零件的型式、规格、实验方法 、质量鉴定及标号等标准化,在 机械制造中具有重大意义。设计人员在设计时如无特殊要求,就应 当采用国家标准。
(二)机械零件设计中的标准化
零件的标准化,就是通过对零件的尺寸、结构要素、材料性能、检 验方法、设计方法、制图要求等,制定出各种各样的大家共同遵守 的标准。 1、标准化的内容 标准化工作包括三方面的内容,即标准化、系列化和通用化,简称 为机械产品的“三化”。 1)、标准化 是指对机械零件种类、尺寸、结构要素、材料性质、检验方法、公 差配合和制图规范等制定出相应的标准,供设计、制造时共同遵照 使用。 2)、系列化 将同一类产品的主要参数、型式、尺寸、基本结构等依次分档,制 成系列化产品,以较少的规格品种满足用户的广泛要求。 3)、通用化 将用途、结构相近的零部件(如轴承、螺栓等),经过统一后实现 互换。
(三)、我国标准化的分类
标准层次:国际标准、国家标准、行业标准、企业标准
代号为 ISO
GB J号) -××××(为 批准年代) 强制性国标必须严格遵照执行,否则就是违法。
推荐性国家标准:代号为GB/T ××××-××××,这类标准 占整个国标中的绝大多数。如无特殊理由和特殊需要,必须遵守这 些国标,以期取得事半功倍的效果。
1.退火 退火是将钢加热到一定温度,保温一段时间,然后工件随 炉温缓慢冷却。退火可消除因锻造、焊接等产生的内应力,降低硬 度以改善切削加工性能。
机械设计概论4机械零件的主要失效形式和计算准则一

5、零部件装配工艺性
6、零部件维修工艺性
机械零件设计中的标准化
标准化、系列化、通用化
机械设计
一、传统设计方法
第1 章
机械设计概论
12
1.7 机械设计方法及其新发展 1、理论设计 1)根据使用要求,选择零件的类型和结构。 2)根据机器的工作要求,计算作用在零件上的载荷。 3)选择适当的材料。 4)根据零件工作能力准则,确定零件的主要尺寸
机械设计
第1 章
机械设计概论
2
1.2 机器设计的一般程序 机械设计是一个创新与借鉴相结合的过程,一般程序如下:
计划阶段 方案设计 技术设计 试制、试验、鉴定、生产 信 息 反 馈 、 修 改
技术文件的编制
机械设计
第1 章
机械设计概论
3
减速器设计
机械设计
第1 章
机械设计概论
4
1.3 机械零件设计的基本要求及一般步骤
5)选用高效率设备,减少动力、燃料消耗。
机械设计
3、可靠性要求
第1 章
机械设计概论
1
机器的可靠度(R):在规定的工作期限内和规定的工 作条件下,无故障完成规定功能的概率。 提高机器可靠度的关键是提高其组成零部件的可靠度 4、劳动保护和环境保护要求 1)操作者的操作安全,减轻操作者的劳动强度 2)改善操作者及机器的环境 5、其它要求 产品的特殊要求、造型要求、清洁能源、材料等
机械设计
第1 章
机械设计概论
6
机械设计
二、设计准则
第1 章
机械设计概论
7
1、强度准则
强度:零件抵抗断裂、塑变、疲劳破坏的能力。 方法: 1) [ ] 或 [ ]
[ ]
杨可桢《机械设计基础》章节题库(机械零件设计概论)【圣才出品】

第9章机械零件设计概论一、选择题1.对于受循环变应力作用的零件,影响疲劳破坏的主要因素是()。
A.最大应力B.平均应力C.应力幅【答案】C2.由试验知,有效应力集中,绝对尺寸,表面质量和表面强化只对零件的()有影响。
A.应力幅B.平均应力C.应力幅和平均应力【答案】A3.零件的形状、尺寸、结构、精度和材料相同时,磨削加工的零件与精车加工的零件相比,其疲劳强度()。
A.较高B.较低C.相同【答案】A【解析】磨削加工与精车加工相比,后者的表面质量不如前者,而表面质量越高,零件的疲劳强度越高,因此,磨削加工的零件,其疲劳强度比精车加工高。
4.下列四种叙述中,()是正确的。
A.应变力只能由变载荷产生B.静载荷不能产生应变力C.变应力是由静载荷产生的D.变应力是由变载荷产生,也有可能由静载荷产生【答案】D【解析】例如,心轴工作时,受到径向静载荷作用,弯曲应力就是对称循环变化的变应力。
5.绘制塑性材料的简化的极限应力图时,所必需的已知数据是()。
A.B.C.D.【答案】A6.零件的工作安全系数为()。
A .零件的极限应力比许用应力B .零件的极限应力比零件的工作应力C .零件的工作应力比许用应力D .零件的工作盈利比零件的极限应力【答案】A【解析】lim []S σσ=。
7.影响零件疲劳强度的综合影响系数(K )D 或(Kr )D 与( )等因素有关。
A .零件的应力集中、加工方法、过载B .零件的应力循环特性、应力集中、加载状态C .零件的表面状态、绝对尺寸、应力集中D .零件的材料、热处理方法、绝对尺寸【答案】C【解析】由公式σσD σ()k k βε=或ττD τ()k k βε=可以得出结论。
σk 、τk 是有效应力集中系数,σε、τε是尺寸系数,β是表面状态系数。
8.已知45钢调质后的力学性能为:,等效系数σψ为( )。
A .1.6B .2.2C .0.24D .0.26【答案】C 【解析】根据等效系数计算公式:10σ02σσψσ--=。
机械零件设计概论
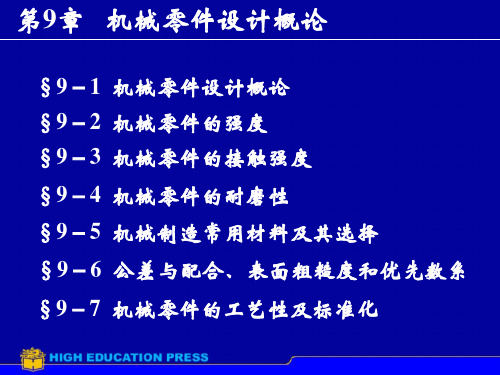
机械零件的失效: 机械零件曲于某种原因不能正常工作时,称为失效。
工作能力----在不发生失效的条件下,零件所能安全工
作的限度。通常此限度是对载荷而言,所以习惯上又
称为: 承载能力。
如轴、齿轮、轴瓦、轴颈、螺栓、带
断裂或塑性变形;
传动等。机械零件虽然有多种可能的 失效形式,归纳起来最主要的为
过大的弹性变形;
2
变应力的循环特性:
σ
-1 = r min 0
+1 max
T
σ
σa
σa
σmax σmin σm o
----对称循环变应力 ----脉动循环变应力
----静应力
静应力是变应力的特例
σ
r =+1
σmax
σmin to
σa σa
σ=常数
o
t
σ
σmax
σa
σa
σm
t o σmin
t
循环变应力
对称循环变应力 r =-1
材料
种类规格
相对价格
碳素结构钢Q235 (φ 33~42)
1
优质碳素钢 (φ 29~50)
热轧圆滚合钢动金轴结承构钢钢((φφ292~95~05)0)
合金工具钢(φ 29~50) 4Cr9Si2耐热钢(φ 29~50)
1.5~1.8 1.7~2.5
3 3~20
5
灰铸铁铸件 碳素铸钢件铸件
铜合金、铝合金铸件
磨损↑ →间隙↑、 精度↓、效率↓、振动↑、 冲击↑、噪音↑
据统计,约有80%的损坏零件是因磨损而报废的。
磨损的主要类型 :硬质颗粒或摩擦表面上硬的凸蜂,在摩擦过程中引起的材料脱落现象称为磨 粒磨损 。硬质颗粒可能是零件本身磨损造成的金属微粒,也可能是外来的尘 土杂质等。摩擦面间的硬粒,能使表面材料脱落而留下沟纹。
机械零件设计概论

机械零件设计概论9.1机械零件设计概述机械零件由于某种缘故不能正常工作时,称为失效。
在不发生失效的条件下,零件所能安全工作的限度,称为工作能力。
通常此限度对载荷而言,因此适应上又称为承载能力。
零件的失效可能由于:断裂或塑性变形;过大的弹性变形;工作表面的过度磨损或损害;发生强烈的振动;联接的放松;摩擦传动的打滑等。
机械零件尽管有多种可能的失效形式,但归纳起来最要紧的为强度、刚度、耐磨性、稳固性和温度的阻碍等几个方面的问题。
关于各种不同的失效形式,相应地有各种工作能力判定条件。
设计机械零件时,常依照一个或几个可能发生的要紧失效形式,运用相应的判定条件,确定零件的形状和要紧尺寸。
机械零件的设计常按下列步骤进行:1)拟定零件的运算简图。
2)确定作用在零件上的载荷。
3)选择合适的材料。
4)依照零件可能显现的失效形式,选用相应的判定条件,确定零件的形状和要紧尺寸。
应当注意,零件尺寸的运算值一·般并不是最终采纳的数值,设计者还要依照制造零件的工艺要求和标准、规格加以圆整。
5)绘制工作图并标注必要的技术条件。
以上所述为设计运算。
在实际工作中,也常采纳相反的方式─—校核运算,这时先参照实物(或图纸)和体会数据,初步拟定零件的结构和尺寸,然后再用有关的判定条件进行验算。
还应注意,在一样机器中,只有一部分零件是通过运算确定其形状和尺寸的,而其余的零件则仅依照工艺要求和结构要求进行设计。
9.2 机械零件的强度在理想的平稳工作条件下作用在零件上的载荷称为名义载荷。
然而在机器运转时,零件还会受到各种附加载荷,通常用引入载荷系数K(有时只考虑工作情形的阻碍,则用工作情形系数K A)的方法来估量这些因素的阻碍。
载荷系数与名义载荷的的乘积,称为运算载荷。
按照名义载荷用力学公式求得的应力,称为名义应力,按照运算载荷求得的应力,称为运算应力。
当机械零件按强度条件判定时,比较危险截面处的运算应力(σ、τ)是否小于零件材料的许用应力([σ]、[τ])。
机械设计基础课件第8章 机械零件设计概论
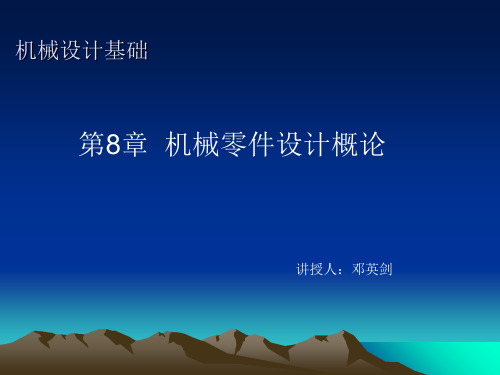
二、机械设计的一般程序 1、机器设计的一般程序
市场调 研
可行性 研究
设 计 任 务 书
原理 方案 设计
技术 设计
试制 试验
定
装配图、 样
出
零件图、 机
最
技术文
评
佳
件
价
方
改
案
进ቤተ መጻሕፍቲ ባይዱ
小批生 投 产试销 产
考核
产
工艺
品
性收
销
集用
售
户意
见
1、强度准则
零件在载荷作用下抵抗破坏的能力
2、刚度准则
[ ] lim S
[ ] lim St
B(B) 脆性材料 lim(lim)S (S )塑性材料
Y (Y )疲劳极限
零件在载荷作用下抵抗弹性变形的能力
y [y]
y——可以是挠度、偏转角或扭转角
3、耐磨性准则 作相对运动的零件其工作表面抵抗磨损的能力
p [p ] p v pv
4、振动和噪声准则
fp0.8f5,
fp1.1f5
机械设计基础
第8章 机械零件设计概论
讲授人:邓英剑
§8-1 机械设计的基本要求及设计程序
一、机械设计的基本要求
1、对机械设计的要求 a) 对机器使用功能方面的要求 b) 对机器经济性的要求
2、对机械零件设计的基本要求 a) 在预定工作期限内正常、可靠地工作,保证机器 的 各种功能 b) 要尽量降低零件的生产、制造成本
4、复合材料
二、机械零件材料选用的原则
1、使用要求 2、工艺要求 3、经济性要求
§8-4 机械零件的结构设计工艺性及标准化
一、机械零件的结构设计工艺性
第1章机械零件设计概论

§1.1 机械、机器、机构及其组成 §1.2 本课程的内容、性质的任务 §1.3 机械设计的基本要求和设计 过程 §1.4 机械零件的工作能力及其计算准则 §1.5 机械零件的载荷、应力和许用应力 §1.6 机械零件的材料的选用原则 §1.7 机械设计的新发展
1.1 机械、机器、机构及组成
1.6 机械制造常用材料及其选择
3、铜合金
青铜 — 含锡青铜、不含锡青铜 种类: 黄铜 — 铜锌合金,并含有少量的锰、铝、镍 轴承合金(巴氏合金) 特点:良好的塑性和液态流动性; 良好的减摩性和抗腐蚀性。 零件毛坯获取方法:辗压、铸造。 应用:应用范围广泛。
二、非金属材料
1、橡胶 橡胶富于弹性,能吸收较多的冲击能量。
4) 腐蚀磨损
在滚动或兼有滑动和滚动的高副申,如凸轮、齿轮等,受载时材料表层有很大的 接触应力。当载荷重复作用时,常会出现表层金属呈小片状剥落,而在零件表面 形成小坑,这种现象称为疲劳磨损或疲劳点蚀。 在摩擦过程申,与周围介质发生化学反应 或电化学反应的磨损,称为腐蚀磨
静应力是变应力的特例 1.5 机械零件的载荷、应力和许用应力
零件工作表面出现疲劳破坏或过度磨损 零件的弹性变形过大 零件发生强烈振动
2) 衡量零件工作能力的指标: 强度、刚度、抗磨性、耐热性、振动稳定性
1.4 机械零件的工作能力及其计算准则
三、机械零件的计算准则
强度计算准则 (整体强度和表面强度): [ ] 刚度计算准则; 抗磨性计算准则:
[ ]
1.1 机械、机器、机构及组成
机 器
进气阀3 制造角度:由若干个机械零件装配面成的 。 运动角度:由若干个可以相对运动的构件组装而成的。
结构角度:由机构组成的,而机构则是由一些能相对 独立运动的构件组成的。 排气阀4
机械零件设计概论
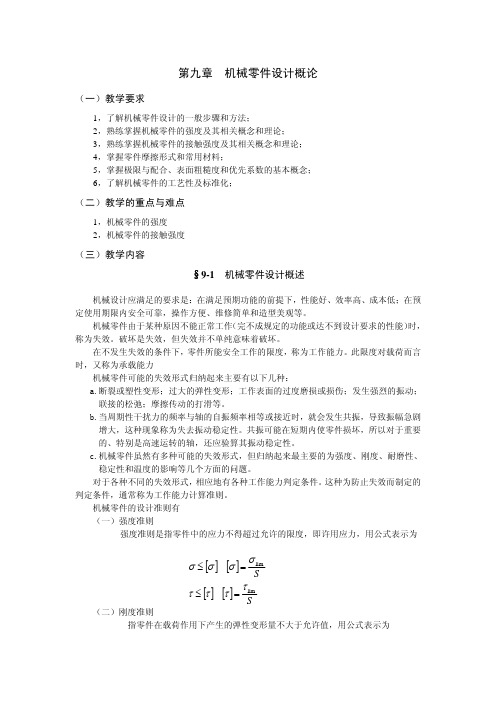
(2)粘着磨损
现象:表面微凸体接触,“高压、高温”粘着焊合,相对运动撕脱,材料转移
措施:选材料副匹配(避免同种金属配对),提高表面光洁度、合理润滑、控制压强、温度
(3)疲劳磨损(点蚀)
现象:交变接触应力反复作用、局部微裂纹扩展材料脱落形成麻点、微坑
措施:降低表面粗糙度、提高表面硬度、配对材料保持合理硬度差
增大,这种现象称为失去振动稳定性。共振可能在短期内使零件损坏,所以对于重要 的、特别是高速运转的轴,还应验算其振动稳定性。 c.机械零件虽然有多种可能的失效形式,但归纳起来最主要的为强度、刚度、耐磨性、 稳定性和温度的影响等几个方面的问题。 对于各种不同的失效形式,相应地有各种工作能力判定条件。这种为防止失效而制定的 判定条件,通常称为工作能力计算准则。 机械零件的设计准则有 (一)强度准则
零件发生疲劳点蚀后,减小了接触面积,损坏了零件的光滑表面,因而也降低了承载能 力,并引起振动和噪声。
两个轴线平行的圆柱体相互接触并受压时,接触应力分布如图 9-8 所示,最大接触应力 发生在接触区中线上,其值由赫兹(H.Hertz)公式计算
σH =
1±1 Fn ρ1 ρ2
πb 1− μ12 + 1− μ22
许用应力)的表格。使用时可以从中查表选取所需的安全系数(或许用应力)。 当没有专门的表格时,可参考下述原则选择安全系数: 1) 静应力下,塑性材料以屈服极限为极限应力。由于塑性材料可以缓和过大的局部应 力,故可取安全系数 S=1.2~1.5;对于塑性较差的材料或铸钢件可取 S=1.5~2.5。 2) 静应力下,脆性材料以强度极限为极限应力,这时应取较大的安全系数。例如,对 于高强度钢或铸铁件可取 S=3~4。
[ ] 而 σ H
= σ H lim SH
西工大机械原理第9章机械零件设计概论

3.疲劳磨损,即疲劳点蚀 是高副(点、线接触)机械零件的常见磨损形式。
§9-4 机械零件的耐磨性
4. 腐蚀磨损 摩擦表面在摩擦过程中,伴随有表面材料被腐蚀 的现象,这种情况下产生的磨损即为腐蚀磨损。 除了上述四种基本磨损类型以外,还有侵蚀磨损、 微动磨损等其他形式。
确定零件的形状和主要尺寸。 应当注意,零件尺寸的计算值一般并不是最终采用的
数值,设计者还要根据制造零件的工艺要求和标准、 规格加以圆整。 5) 绘制工作图并标注必要的技术条件。
§9-2 机械零件的强度
一、载荷 1. 载荷:进行强度计算所依据的、作用于零件上的 外力F、弯矩M、扭矩T以及冲击能量等,统称为 载荷。 2. 机械零件实际承受的载荷: ① 静载荷:大小、作用位置和方向不随时间变化 或变化缓慢的载荷。 ② 变载荷:大小、作用位置或方向随时间变化的 载荷。 ③ 动载荷:由于运动中产生的惯性力和冲击等引 起的载荷。
§9-3 机械零件的接触强度
3. 两个轴线平行的圆柱体相互接触并受压时,最大接触应力发 生在接触区中线上,其值由赫兹(H.Hertz)公式计算:
H
11
Fn
1 2
b 1 12 1 22
E1
E2
令
1 1 1 1 2
及 1 1 21,
E1 E2 E
对于钢或铸铁,取μ1=μ2 =μ=0.3,则上式简化为:
H
1 Fn E
2(1 2)b
0.418
Fn E
b
§9-3 机械零件的接触强度
4. 零件受接触变应力作用时接触强度条件为 σH≤[σH] 而[σH] = σHlim/SH
机械设计概论

机械设计概论【摘要】在机械设计当中有许多知识是需要掌握的,要求设计理念了解,对设计当中的每一个环节都要进行校核,不要出现零件最终生产出来时废品,这样在设计时候要考虑好材料,设计参数,最后的校核,每一个步骤都是不可缺少的。
【关键词】理念;寿命;校核1.设计理念要了解设计机械零件应满足的基本要求:1.1设计机械零件的基本要求刚度方面满足设计要求,同时也要考虑寿命,在这些要求满足下要兼顾经济,也不要讲零件设计的比较笨重。
例如在机床的主轴箱设计上,就要综合考虑什么因素能直接影响主轴、轴承,主轴箱体应该具体满足怎样的强度、刚度以及抗震性,同时还要考虑主轴箱的制造方法是铸造还是焊接:(1)铸造工艺,优点就是强度及刚度大、吸振性好,可以大批大量生产,但是制造成本高、周期长。
(2)焊接工艺,优点为制造成本低,周期短,缺点就是焊缝有应力集中,强度有所下降。
1.2机械设计方法通过书本上的理论设计,通过前人的经验设计,通过做实验来设计。
1.3机械设计的一般步骤(1)动向预测(2)方案设计(3)技术设计(4)施工设计(5)试生产(4)掌握常用现代设计方法的类型、基本思想。
1.4现代设计理念有限元分析方法:一种以计算机为基础的分析方法,它是将研究对象变换成一个计算机模型,将这个模型通过一系列的求解,最终得到相应的参数。
优化设计方法:使得在解决复杂设计问题时,能从众多的设计方案中寻到尽可能完善的或最适宜的设计方案。
计算机辅助设计:计算机辅助设计(Computer Aided Design—CAD):它的出现使机械设计简化的很多,它可以辅助设计人员就行分析、绘图,节省了设计时间。
2.机械设计的强度校核在机械设计当中有许多设计环节需要进行校核,在这些校核当中轴的校核、轴承的校核、键的校核。
2.1轴的校核在设计当中我们要知道轴的结构和支点及轴上零件的力作用点,对轴进行受力分析、绘制弯矩图、扭矩图及当量弯矩图,要对轴上的危险截面进行校核,如果轴的直径不够大,可以进行增大。
机械设计概论
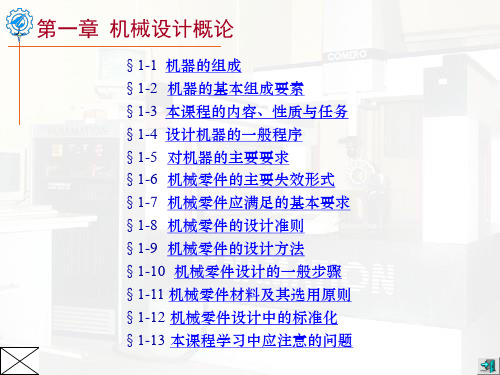
牛头刨床
起重机
起重机
内燃机
内燃机
内燃机工作原理
燃气由进气管通过进气 阀3被下行的活塞2吸入气缸, 然后3关闭,2上行压缩燃气, 点火使燃气在气缸中燃烧, 膨胀产生压力,推动2下行, 通过连杆5带动曲柄6转动向 外输出机械能。当2再次上 行时,排气阀4打开,废气 由排气管排出。图中,凸轮 7和顶杆8是用来启、闭进气 阀的;齿轮9,9’,10是用 来保证进气阀、排气阀和活 塞之间形成一定规律的运动。 以上各部分的协同配合动作, 便能把燃气燃烧时的热能变 为曲轴转动时的机械能。
本课程所涉及的先修课程有: 工程制图:设计的图形表达。 工程材料:非金属材料,金属材料及热处理。 机械制造基础:冷加工工艺,热加工工艺。 公差配合与技术测量:解决精度设计问题。 理论力学:解决力分析与动力计算。 材料力学:解决强度分析问题。 机械原理:解决机械的方案设计。
§1-3 本课程的内容、性质与任务
§1-2 机器的基本组成要素
一台机器虽然通常包含机械、电气、液压、气动、润滑、控制、监测等系统,
但机器的主体是机械系统,如传动部分、执行部分。
机器的机械系统总是由一些机构组成的,每个机构又是由许多零件组成的。 机器的基本组成要素是机械零件。 在各种机器中经常都能用到的零件,称之为通用零件; 在特定类型的机器中才能用到的零件,称之为专用零件。
强度准则 :确保零件不发生断裂破坏或过大的塑性变形,是最基 本的设计准则。
刚度准则 :确保零件不发生过大的弹性变形。 寿命准则 :通常与零件的疲劳、磨损、腐蚀相关。 振动稳定性准则 :高速运转机械的设计应注重此项准则。 可靠性准则 :当计及随机因素影响时,仍应确保上述各项准则。
第9章 机械零件设计概论

图 9.4 材料和零件的极限应力图 由于零件尺寸及几何形状变化,加工质量及强化处理等因素的影响,使得零件的疲劳 极限小于材料试件的疲劳极限。要注意,零件尺寸越大,内部的缺陷就越多,疲劳强度极限
值反而更低。在实际计算中,以弯曲疲劳极限的综合影响系数 k 表示材料对称循环弯曲疲
劳极限与零件对称循环弯曲疲劳极限的比值,实验表明,综合影响系数只影响应力幅而不影 响平均应力。当一个截面有多处应力源时,则分别求出其有效应力集中系数,从中取最大值。
如图 9.4 所示的 A’D’C’曲线。在此曲线内的任何一点所代表的最大应力(即平均应力和 应力幅之和)都低于材料的最大极限应力,是安全的。在此曲线之外的点则是不安全的,最 大应力大于材料的极限应力。曲线上的点表示应力的临界状态。对于塑性材料通常简化为图
中的 A’D’G’C 折线。其中,几个特征点的坐标为:A’(0, 1 ),D’( 0 / 2, 0 / 2) )和 C( S ,0)。
(3) 最小应力为常数 min c
如图 9.6 中应力点 S 的纵横坐标分别代表零件的应力幅和平均应力,求在 min c 状况
下零件的极限应力,则经过 S 点作与横坐标夹 45O 射线,和 AGC 线段交于 S1 点,则该点的 纵横坐标分别代表极限应力点的应力幅和平均应力。
图 9.6 零件的极限应力求法 用极限应力点的纵横坐标之和除以应力点的纵横坐标只和就得零件的安全系数。如果 求出的极限应力点在 AG 段,则零件在安全系数不够的情况下会发生疲劳破坏,如极限应力 点在 GC 段,则零件在安全系数不够的情况下会发生静应力破坏。例如图 9.6 中,在 M,N 点 的应力状况下,零件的失效形式是疲劳破坏,而 S 点的应力状况下会发生静应力破坏,与 综合影响系数的大小无关。读者也可用解析法确定强度,在应力比为常数时,安全系数为:
机械零件设计概论及原理
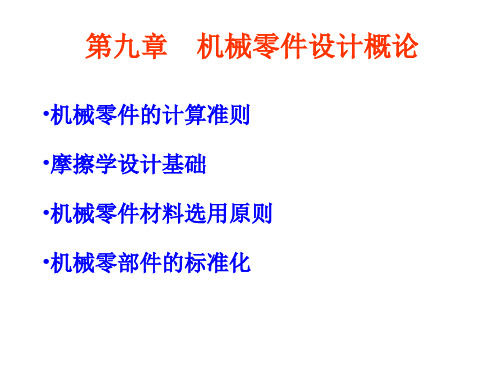
表层萌生疲劳磨损:表层萌生疲劳磨损造成扇形疲劳坑,磨屑多为扇形颗粒,故又称其为点蚀 表面萌生疲劳磨损:表面萌生疲劳磨损造成浅而大的疲劳凹坑,磨屑呈片状,故又称其为剥落。
接触疲劳准则
σHmax≤4τs 最大接触应力;剪切屈服点。
五、润滑剂及其特性
凡能降低摩擦阻力、且人为加入摩擦副的介质都称为润滑剂。
1.润滑剂的基本类型
液体润滑剂:矿物油、有机油、矿物油、合成油等 润滑脂:皂基脂、无机脂、烃基脂和有机脂 固体润滑剂:软金属,如Pb、Au、Ag、Sn、In等;无机化合物
2.润滑油
粘度 表征流体流动的阻力,在流体动力和静力润滑状态,粘度与油膜厚度、摩擦阻力直接相关。
强度准则
一、静强度
在静应力下工作的零件,其可能的失效形式是塑性变形或断裂。材料种类不同,所取极限应力也不同。
塑性材料
单向应力状态下:
,
复合应力状态下:
按第三或第四强度理论计算当量应力。
脆性材料
单向应力状态下:
,
复合应力状态下: 按第一强度理论计算当量应力。
对于塑性材料和组织不均匀的材料(如灰铸铁),在计算静强度时,可不考虑应力集中的影响。 对于组织均匀的低塑性材料(如淬火钢),在计算静强度时,应考虑应力集中的影响。
工作能力——机械零件具有足够的抵抗失效的能力
计算准则——以防止产生各种可能失效为目的而拟定的零件工作能力计算依据的基本原则
因为失效类型不同,所以机械零件的工作能力类型也不同,故机械零件的计算准则也不同
载荷和应力
1、载荷
动载荷:由于运动中产生的惯性力和冲击等引起的载荷
静载荷
变载荷
按是否随时间变化,载荷
第9章 机械设计零件概论习题

机械设计零件概论习题9-1.设计铸件时,在垂直于分型面的表面应有适当的铸造斜度,这是为了_________。
A.使零件外型美观B.减轻零件重量C.减少零件加工面积D.便于起模9-2.在进行疲劳强度计算时,其极限应力应为材料的__________.A.屈服点B.疲劳极限C.强度极限D.弹性极限9-3.碳钢和合金钢是按__________来区分的。
A.用途不同B.材料的强度C.材料的塑性D.材料的化学成分9-4.循环特性r=-1的变应力是____________变应力。
A.非稳定B.脉动循环C.非对称循环D.对称循环9-5.循环特性r=0 的变应力是____________变应力。
A.非稳定B.脉动循环C.非对称循环D.对称循环9-6.在静应力作用下,脆性材料的极限应力为____________。
A.σb B.σsC.σ0 D.σ—19-6.在静应力作用下,塑性材料的极限应力为____________。
A.σb B.σsC.σ0 D.σ—19-7.在变应力下,材料以___________为极限应力。
A.屈服极限B.强度极限C.疲劳极限D.静应力9-8.齿轮、滚动轴承的主要失效形式是_________。
A.磨粒磨损B.胶合C.点蚀D.磨蚀磨损9-9.在循环变应力作用下,影响疲劳强度的主要因素是__________。
A.最大应力B.平均应力C.最小应力D.应力幅9-10.零件的工作安全系数为__________________。
A.零件的极限应力比许用应力B.零件的极限应力比零件的工作应力C.零件的工作应力比许用应力D.零件的工作应力比零件的极限应力9-11.含碳量小于______的铁碳合金称为钢,含碳量大于该值的称为铸铁。
A.2%B. 2.5%C.3%D.4%9-12.在静应力作用下选取安全系数时,脆性材料应比塑性材料大一些。
()9-13.由于变应力作用下疲劳极限应力较小,选取安全系数时应较静应力作用时大得多。
机械设计教材电子版机械设计教材电子版第七版考研

扬州大学专用
作者: 潘存云教授
§2-1 机器的组成
人们为了满足生产和生活的需要,研制了类型繁多、 功能各异的机器。尤其是蒸汽机出现之后,使机器具有 了完整的形态。
一台完整的机器的组成如下:
润滑、显示、照明等辅助部分
原动机部分 传感器
传潘存动云教部授分研制
执行部分
传感器
传感器
扬州大学专用
控制系统
作者: 潘存云教授
这是主要失效原因。
扬州大学专用
作者: 潘存云教授
§2-5 设计机械零件时应满足的基本要求
机器是由各种各样的零部件组成的,要使所设计 的机器满足基本要求,就必须使组成机器的零件满足 以下要求:
▲ 避免在预定寿命期内失效的要求 ▲ 结构工艺性要求 ▲ 经济性要求
▲ 质量小的要求
▲ 可靠性要求
一、避免在预定寿命期内失效的要求 应保证零件有足够的强度、刚度、寿命。
(3)对流动使用的机器有便于安装和拆卸的要求;
(4)对大型机器有便于运输的要求等等。
扬州大学专用
作者: 潘存云教授
§2-4 机械零件的主要失效形式
机械零件的失效: 机械零件由于某种原因不能正常工作时,称为失效。
工作能力——在不发生失效的条件下,零件所能安全
工作的限度。通常此限度是对载荷而言,所以习惯上
零件在工作时的弹性变形不能超过允许的范围称 为零件的刚度要求。
扬州大学专用
作者: 潘存云教授
提高零件刚度的措施有 ▲增大零件的截面尺寸或增大惯性矩; ▲缩短支承的跨距或采用多点支承。
3. 寿命要求 影响零件寿命的主要因素有
疲劳破坏 腐蚀 磨损
大部分零件工作在变应力下,故疲劳破坏是引 起零件破坏的主要原因。影响疲劳强度的因素有
机械设计概论习题

第9章 机械零件设计概论一、填空题[1]变载荷一定产生_________应力。
[2]应力幅与平均应力之和等于______________________。
[3]根据是否随时间变化,将载荷分为____________________和_________________两类。
[4]r = -1的变应力称为___________________变应力。
[5]根据是否随时间变化,将应力分为_______________________和____________________两大类。
[6]当r =+1时称为_________________应力。
[7]r = 0的变应力称为_________________变应力。
[8]静应力是由_____________载荷产生的。
[9]应力幅与平均应力之差等于_________________________。
[10]最小应力与最大应力之比称为_______________________。
[11]机械零件由于某种原因不能正常工作时,称为_____________________。
二、判断题[1]循环特性r=-1的变应力为非对称循环变应力。
( )[2]静载荷也可能产生变应力。
( )[3]静应力可看作r =+1时的变应力。
( )[4]静应力也可能由变载荷产生。
( )[5]变载荷一定产生变应力。
( )[6]变应力只能由变载荷产生。
( )三、选择题[1]下列四种叙述中,( )是正确的。
A 、变应力只能由变载荷产生B 、变应力只能由静载荷产生C 、静载荷不能产生变应力D 、变应力也可能由静载荷产生[2]机械零件的强度条件可以写成________。
A 、σ≤][σ,τ≤][τB 、σ≥][σ,τ≥][τC 、σ≥][σ,τ≤][τD 、σ≤][σ,τ≥][τ[3]循环特性r=0的变应力称为( )应力。
A 、对称循环B 、脉动循环C 、静D 、非对称循环[4]循环特性r=+1的变应力称为( )。
- 1、下载文档前请自行甄别文档内容的完整性,平台不提供额外的编辑、内容补充、找答案等附加服务。
- 2、"仅部分预览"的文档,不可在线预览部分如存在完整性等问题,可反馈申请退款(可完整预览的文档不适用该条件!)。
- 3、如文档侵犯您的权益,请联系客服反馈,我们会尽快为您处理(人工客服工作时间:9:00-18:30)。
微裂纹常起始于应力最大的端口周边上,断口有明显的两个区域: 1)变应力重复作用下裂纹两边相互摩擦形成的光滑表面区; 2)最终发生脆性断裂的粗粒状区。如图。 1、疲劳曲线 表示应力σ与应力循环次 数N之间关系的曲线。
可知: 1)应力越小,所能经受的循环次 数越多。 2)循环次数超过数值N0后,趋于 水平。
3)疲劳磨损(疲劳点蚀) 在滚动或兼有滑动和滚动的高副申,如凸轮、齿轮等,受 载时材料表层有很大的接触应力。当载荷重复作用时,常会出 现表层金属呈小片状剥落,而在零件表面形成小坑,这种现象 称为疲劳磨损或疲劳点蚀。 4) 腐蚀磨损 在摩擦过程申,与周围介质发生化学反应或电化学反应 的磨损,称为腐蚀磨损。 实用耐磨计算是限制运动副的压强p,即:
应力幅: a
max min
2
2
max min
三、变应力下的许用应力
变应力下,零件的损坏形式是疲劳断裂。具有以下特征:
1)疲劳断裂的最大应力远比静应力下材料的强度极限低,甚至 比屈服极限低; 2)不管脆性材料或塑性材料,疲劳断口均表现为无明显塑性变形 的脆性突然断裂;
Fn
ρ1 ρ2 σH σH b
1 Fn E Fn E H 0.418 2 2 (1 ) b b
对于钢或铸铁取泊松比: μ1=μ2=μ=0.3 , 则有简化公式。 上述公式称为赫兹(H· Hertz)公式
“+”用于外接触, “-”用于内接触。
H
Fn E 0.418 b
σlim、τ lim -----极限应力,由实验方法测定。
1.分类
静应力→不随时间变化 变应力→随时间变化
•当σmax、σmin均维持常数→稳定交变应力 •当σmax和σmin的数值随时间而改变→不稳定的变应力
2.交变应力的特征及典型的交变应力 交变应力-随时间作周期性变化的应力
平均应力: m
拟定零件的计算简图 参照实物(图纸) 和经验数据 拟定零件的结构和尺寸 选用相应判定条件
确定作用在零件上的载荷
选择合适的材料
选用相应判定条件
确定零件形状和主要尺寸 绘制工作图,标注技术条件 验算零件结构和尺寸
验算,修改零件
设计计算法
校核计算法
§9-2
机械零件的强度
强度→ 零件承受载荷后,抵抗发生断裂或超过容许限度的 残余变形的能力→与载荷及应力有关 零件设计中的载荷及其分类 名义载荷:在理想的平稳工作条件下作用在零件上的载荷。 名义载荷:按名义载荷计算所得之应力。 载荷系数K:考虑各种附加载荷因素的影响。 计算载荷:载荷系数与名义载荷的乘积。 载荷可分为静载荷和变载荷两类。 静载荷:不随时间变化或变化缓慢的载荷. 变载荷:随时间作周期性或非周期性变化的载荷.
影响疲劳强度的主要因素2
在变应力,取材料的疲劳极限作为极限应力。同时还应考虑 零件的切口和沟槽等截面突变、绝对尺寸和表面状态等影晌。 当应力是对称循环变化时,许用应力为: [ 1 ]
1
k S
当应力是脉动循环变化时,许用应力为: [ ] 0 0
k S
σ0 为材料的脉动循环疲劳极限,S为安全系数。以上各系数均 可机械设计手册中查得。以上所述为“无限寿命” 。
H [ H ],
H lim 而[ H ] SH
提高表面接触强度的主要措施 ——增大接触表面的综合曲率半径。 ——将外接触改为内接触。 ——将点接触改为线接触。 ——采用粘度较高的润滑油。 ——提高接触表面的加工质量。 ——提高零件表面硬度。
降低计算应 力 提高许用应力
§9-4 机械零件的耐磨性
§9-3 机械零件的接触强度
若两个零件在受载前是点接触或线接触。受载后,由于变 形其接触处为一小面积,通常此面积甚小而表层产生的局部应力 却很大,这种应力称为接触应力。这时零件强度称为接触强度。
如齿轮、凸轮、滚动轴承等。 失效形式常表现为: 疲劳点蚀
机械零件的接触应力通常是随时间作周期性变化的, 在载荷重复作用下,首先在表层内约 20μm 处产生初 始疲劳裂纹,然后裂纹逐渐扩展 ( 润滑油被挤迸裂纹 中将产生高压,使裂纹加快扩展,终于使表层金属呈 小片状剥落下来,而在零件表面形成一些小坑 ,这种 现象称为疲劳点蚀。
Fn
σH -------最大接触应力或赫兹应力; b -------接触长度; Fn -------作用在圆柱体上的载荷;
b
1 2 -----综合曲率半径; 1 2
E 2 E1 E2 -----综合弹性模量; E1、 E2 分别为两 E1 E2 圆柱体的弹性模量。
接触疲劳强度的判定条件为:
一、应力的种类
名义应力——按名义载荷计算所得之应力:
计算应力-----按计算载荷计算所得之应力: 强度判 定条件:
[ ] [ ]
其中
[ ]
S lim [ ] S
S-----安全系数
lim
[σ] 、[τ]-----许用应力
p ≤ [p] [p]由实验或同类机器使用经验确定
相对运动速度较高时,还应考虑运动副单位时间单位接触面积
的发热量 f p v 。在摩擦系数一定的情况下,可将 p v 值与许用
的 [p v] 值进行比较。即: p v ≤ [p v ]
§9-5 机械制造常用材料及其选择
机械制造中最常用的材料是钢和铸铁,其次是有色金属合 金。非金属材料如塑料、橡胶等 。 一、金属材料 铸铁 含碳量>2% 铁碳合金 常用金属 钢 含碳量≤ 2% 材料 铜合金 1.铸铁:灰铸铁、球墨铸铁、可锻铸铁、合金铸铁等。 特点:良好的液态流动性,可铸造成形状复杂的零件。较好的减 震性、耐磨性、切削性(指灰铸铁)、成本低廉。 应用:应用范围广。其中灰铸铁最广、球墨铸铁次之。 2.钢:结构钢、工具钢、特殊钢(不锈钢、耐热钢、耐酸钢等)、 碳素结构钢、合金结构钢、铸钢等。
§2-3影响疲劳强度的因素
机械零件上的应力集中会加快疲劳裂纹的形成和扩展。从而导致 零件的疲劳强度下降。 常用有效应力集中系数 表示疲劳强度的真正降低程度。
-1 ( -1) k
-1和( -1) 力集中试样的疲劳极限 。 k : 无应力集中试样和有应
注:当同一剖面上同时有几个应力集中源时,应采用其中最大的疲 有效应力集中系数进行计算。
(2)绝对尺寸的影响
零件的尺寸越大,其疲劳强度降低。
( -1) d = 用绝对尺寸系数 ( ) 表示。 -1 d 0
(3)表面状态的影响
包括表面粗糙度和表面处理的情况。零件表面光滑或经过 各种强化处理课提高零件的疲劳强度。 ( -1) 用表面状态系数β表示: = ( -1) 0 3、许用应力
§9-1 机械零件设计概述
(一)机械设计应满足的要求
在满足预期功能的前提下,性能好、效率高、成本低,在预 定使用期限内安全可靠,操作方便、维修简单和造型美观等。
(二)设计机械零件应满足的要求
* 避免在预定寿命周期内失效
既要可靠, 又要成本低
失效 -机械零件由于某种原因不能正常工作 工作能力 在不发生失效的条件下,零件所能安全工作的限度 承载能力 →对载荷而言
有限寿命区
无限寿命区
σ
的弯曲疲劳极限。
m m N 1 N0 C 当N<N0 时, 有近似公式: 1N
对应于N 的弯曲疲劳极限:
-1N -1
m
N0 N -1 N
2、影响零件疲劳强度的主要因素 (1)应力集中的影响
2)粘着磨损(胶合磨损)
加工后的零件表面总有一定的粗糙度。摩擦表面受载时,实际上只有部 分峰顶接触,接触处压强很高,能使材料产生塑性流动。若接触处发生 粘着,滑动时会使接触表面材料由一个表面转移到另一个表面,这种现 象称为粘着磨损(胶合磨损)。所谓材料转移是指接触表面擦伤和撕脱, 严重时摩擦表面能相互咬死。
失效形式 1. 整 体 强 度 静 应 →整体 力 破坏 整体断裂(脆性材料) 计算准则
B S
S S
r S
过大的残余变形 (塑性材料)
静 强 度 疲劳 强度
变应力 →疲劳破坏 →疲劳断裂 (塑、脆性材料)
2. 表面磨损 : p ≤[ p ] (比压、压强)→耐磨性 表 面 表面压溃 : σ p≤ [σp] (挤压应力) →挤压强度 强 接触疲劳: σ H≤ [σH] (接触应力) →接触强度(点蚀) 度
有限寿命时,用σ-1N代入得: [ 1 ]
1N
k S
m
N0 N
由于σ-1N> σ-1,所以可得到较大的许用应力,从而减小零件 的体积和重量。
四、安全系数
S↑ → 零件尺寸大,结构笨重。 S↓ → 可能不安全。 典型机械的 S 可通过查表求得。 无表可查时,按以下 原则取: 1)静应力下,塑性材料的零件:S =1.2~1.5 铸钢件:S =1.5~2.5 2)静应力下,脆性材料,如高强度钢或铸铁: S =3~4 3)变应力下, S =1.3~1.7 材料不均匀,或计算不准时取: S =1.7~2.5
前
言
机械零件设计概述
机械零件的强度
机械制造中常用材料及其选择
公差与配合、表面粗糙度和优先数列
机械零件的工艺性及标准化
(一) 机械零件的简介:
机构←构件→运动的单元 研究对象 构件←零件→制造的单元 例: 机构→齿轮机构(三个构件) 齿轮1 、齿轮2、机架3 3
1
2
构件1← (小齿轮) 齿轮 →传动件 轴、轴承、套筒等 →轴系零件 键 →联接件
后果:减少了接触面积、损坏了零件的光滑表面、降低了 承载能力、引起振动和噪音。
由弹性力学可知,应力为:
Fn
ρ1
σH σH ρ2 b
1
H
Fn 1 2 2 b 1 12 1 2 E1 E2