管道的应力腐蚀断裂(2021新版)
10 应力腐蚀开裂 氢致开裂
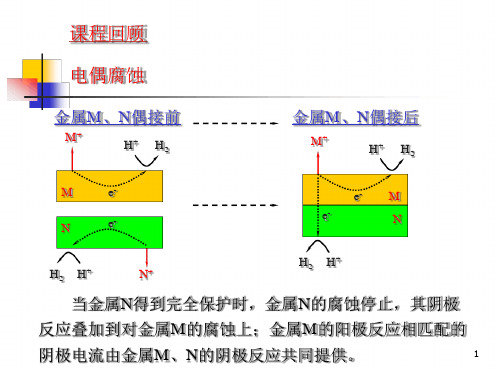
第二节 氢致开裂
一、氢致开裂的定义
? 氢致开裂:又称氢脆或氢损伤,原子氢在合金晶体结构 内的渗入和扩散所导致的脆性断裂的现象。
二、金属中的氢
1、金属中氢的来源 ? 内氢来源:如冶炼、 焊接、酸洗、阴极充氢等。 ? 外氢来源:如工业环境中吸收氢(如油井H2S)、水溶液中微电池
阴极产物 (部分析出, 部分渗入金属)、湿空气中金属( Al、Si、Ti、V) 催化水生成原子氢等。
溶解区重新进入钝态
位错再次开动、 膜破裂
产生穿晶型 SCC 开裂 (放大100倍)
说明:4~7图为放 大倍数为200000 倍的结果。
3、断裂
? 应力腐蚀裂纹扩展到临界尺寸,便会在机械力作用下发 生失稳快速断裂。 ? 氢致开裂型应力腐蚀: 特殊的应力腐蚀,阳极金属溶解 腐蚀所对应的阴极过程为析氢反应,且氢原子能扩散进入金 属并控制裂纹的形核和扩展。
A
A
阴极 1/2O2+H2O+2e- ? 2OH溶液
A区(裂纹两侧): 电流密度~ 10-5A/cm2
阴极 1/2O2+H2O+2e- ? 2OH-
A*区(裂纹尖端): 电流密度~ 0.5A/cm2
奥氏体不锈钢应力腐蚀破裂模型图
304不锈钢在沸腾45%MgCl 溶液中的穿晶裂纹
敏化304不锈钢在室温连多硫 酸溶液中的晶间裂纹
材料破裂与应力大小及时间的关系
9
2、环境特征
? 某一种金属材料只有在特定的环境中才能发生,对环境 的选择性形成了所谓“SCC 的材料―环境组合”。
如锅炉钢在碱性溶液中的碱脆 低碳钢在硝酸溶液中的硝脆 奥氏体不锈钢在含氯离子溶液中的氯脆 黄铜在氨气氛中的氨脆 高强度钢在酸性或中性 NaCl 中的氢脆
TP321厚壁管道焊接过程中的常见问题及应对措施

TP321厚壁管道焊接过程中的常见问题及应对措施摘要:TP321广泛应用于石化行业渣油加氢、连续重整、加氢裂化等装置的高压管道。
近年来,出现了TP321厚壁管道的焊后热处理后发生再热裂纹现象。
因此,本文结合中科炼化一体化项目440万吨/年渣油加氢脱硫装置,现场TP321管材焊缝稳定化热处理后部分焊缝表面出现裂纹,对焊缝裂纹原因进行了分析,制定的处理方案进行论述。
关键词:TP321管道;稳定化;热处理;应对措施TP321奥氏体不锈钢管,在制造时加入了Ti,碳含量很低,可以防止晶间腐蚀,利用形变强化提高强度,采用固溶热处理将钢加热至1050℃~1150℃,使碳化物充分溶解,然后进行水冷却,获得单项奥氏体组织,提高耐蚀性。
渣油加氢脱硫装置突出的特点是高温、高压,介质有氢气、硫化氢、环烷酸等临氢工况,所采用的TP321多为厚壁管道,为了防止在450℃~850℃的敏化温度范围内,碳从奥氏体中以碳化铬(Cr23C6)形式延晶界析出,使晶界附近的合金元素含铬量降低到耐腐蚀所需的最低含量(12%)以下,产生厚度数十纳米的贫铬区,尤其以650℃最危险。
近年来,随着设备的尺寸,TP321厚壁管道越来越多,最大厚度达88mm。
在多个炼化项目中对厚壁TP321管道的进行稳定化热处理后,热影响区、母材或焊缝出现再热裂纹,为解决这一问题,确保装置长期安全运行,为厚壁稳定性奥氏体不锈钢未来现场施工提供技术依据,研究了TP321奥氏体不锈钢管道稳定化热处理的可行性。
1 TP321焊接性分析A312 TP321属于18-8型铬镍奥氏体不锈钢,相当于我国的0Cr18Ni10Ti。
含18%的铬和10%的钛。
TP321具有优良的可焊性,与其他奥氏体不锈钢一样在焊接时容易发生晶间腐蚀、应力腐蚀开裂和焊接热裂纹,并且比其他奥氏体不锈钢更容易出现焊接热裂纹和再热裂纹。
如图1所示。
图1 可能出现晶间腐蚀的位置图2 晶间腐蚀1.1热裂纹产生原因及预防措施由于TP321奥氏体不锈钢焊缝中枝晶方向性很强,枝晶间低熔点杂质的偏析,加之TP321导热系数仅为低碳钢的1/2,而膨胀系数比低碳钢大50%左右,使焊缝区产生较大的温差和收缩内应力,所以焊缝中容易产生热裂纹。
化工压力管道缺陷产生原因及预防压力管道失效事故措施

化工压力管道缺陷产生原因及预防压力管道失效事故措施发布时间:2021-07-08T10:41:54.443Z 来源:《基层建设》2021年第11期作者:石瑞章李战华李贵利王利刚[导读] 摘要:随着我国化学工业的快速发展,大批化工装置在10多年前集中建成投运。
鹤壁宝发能源科技股份有限公司河南鹤壁 458000摘要:随着我国化学工业的快速发展,大批化工装置在10多年前集中建成投运。
现如今,一些装备已到了易失效阶段,尤其是设计寿命在10到15年的化工工艺管道。
近几年因压力管道失效,尤其是化工管道失效所造成的事故频发。
未来一段时间,如果企业不加强压力管道管理,还可能发生类似事故。
本文结合作者的工作环境,介绍了化工压力管道运行过程中易产生的缺陷及预防压力管道失效事故措施。
关键词:压力管道;缺陷;失效事故预防措施化工管道在化工生产中起到重要的作用,化工压力管道经过一段时间使用后,由于苛刻的运行条件,即使是原来设计和制造质量完全符合规范的要求,压力管道的质量也会发生变化,原来存在制造规范允许的小缺陷扩展开裂,可使压力管道中原来没有缺陷的地方产生新的缺陷,最终导致设备失效,无法正常运行甚至发生事故。
我们单位的压力管道属于化工及石化装置压力管道,采用的管道材质有碳钢、低合金钢和不锈钢,介质含有腐蚀性,有的介质含有氯离子。
在实际的使用中,我们发现,这些管道往往受到低温、高温,高压,腐蚀等环境,以及材质、工艺、焊接、安装等运行因素的影响极易产生腐蚀、疲劳、脆性、蠕变等破坏的形成,从而产生壁厚变薄、缺陷扩展、疲劳裂纹、应力腐蚀裂纹、晶间腐蚀及各种腐蚀缺陷,从而对管道的安全运行造成严重的危害,因此加强对各种缺陷产生原因的分析,并采取相应的压力管道失效事故预防措施对压力管道安全运行将起到积极作用。
一、常见管道失效模式1 低温管道低温金属管道广泛应用于石油化工生产装置,在化肥行业中经常会用到一些低温管道,如大型合成氨、甲醇装置低温甲醇洗工序中的管道等。
化工设备常见的应力腐蚀开裂与防护王斌

化工设备常见的应力腐蚀开裂与防护王斌发布时间:2022-03-15T10:49:12.732Z 来源:《中国科技信息》2021年11月下作者:王斌[导读] 在化工生产中,设备及管道的腐蚀很常见,具有不可预知性和突发性。
国投新疆罗布泊钾盐有限责任公司王斌 65220119891012****摘要:在化工生产中,设备及管道的腐蚀很常见,具有不可预知性和突发性。
若腐蚀引发事故,会导致直接经济损失、生产装置停工停产、打乱正常连续生产秩序、还可能造成生产装置着火、爆炸等恶性事故。
化工设备应力腐蚀开裂会造成突发性事故,且在各项腐蚀破坏中占比高,需引起设计和使用单位的重视。
关键词:化工设备;应力腐蚀开裂;防护措施;腐蚀监测1 前言应力腐蚀开裂,又叫“环境断裂”,是指金属材料在各项应力和腐蚀介质的交互作用下所引起的腐蚀开裂或断裂现象。
目前没有绝对精准的理论来解释应力腐蚀的机理,其腐蚀机理需用电化学与金属学、腐蚀环境、表面物理化学等方面来综合解释。
有鉴于此,本文将结合文献查阅以及自身多年工作实际经验情况下,针对化工设备常见的应力腐蚀开裂与防护展开探讨,以供参考。
2导致化工设备常见的应力腐蚀开裂因素2.1外加载荷化工设备及构件在工作条件下所承受的所有外加载荷,比如设备填装材料以后的承载力、设备运行中的各向应力。
外加载荷类型有:拉应力、压应力、扭转应力、弯曲应力等。
若设备及构件带有缺口或裂纹的,根据载荷和裂纹的取向不同划分为Ⅰ、Ⅱ、Ⅲ和混合型4种载荷。
2.2残余应力制造化工设备及构件的钢材会产生残余应力的环节很多:热处理和加工铸造过程、焊接和装配过程、表面处理过程等。
残余应力的类型:①热胀冷缩导致的热应力;②由组织体积变化导致的相变应力;③由形状变化导致的形变应力等。
2.3腐蚀产物设备及构件材料局部阳极溶解会与腐蚀介质中的氧、氢等反应,形成相对原金属体积较大的腐蚀产物。
大体积的腐蚀产物会在局部闭塞部位产生了楔入应力,该应力达到临界值后就会产生裂纹扩展。
油气管道常见腐蚀原因及防护措施应用
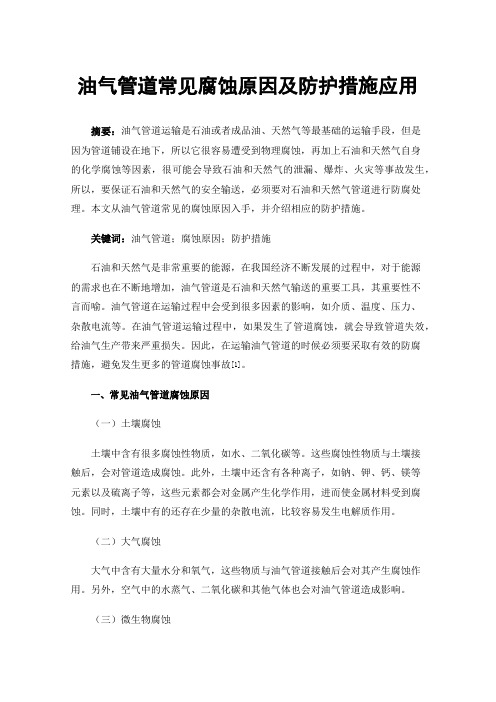
油气管道常见腐蚀原因及防护措施应用摘要:油气管道运输是石油或者成品油、天然气等最基础的运输手段,但是因为管道铺设在地下,所以它很容易遭受到物理腐蚀,再加上石油和天然气自身的化学腐蚀等因素,很可能会导致石油和天然气的泄漏、爆炸、火灾等事故发生,所以,要保证石油和天然气的安全输送,必须要对石油和天然气管道进行防腐处理。
本文从油气管道常见的腐蚀原因入手,并介绍相应的防护措施。
关键词:油气管道;腐蚀原因;防护措施石油和天然气是非常重要的能源,在我国经济不断发展的过程中,对于能源的需求也在不断地增加,油气管道是石油和天然气输送的重要工具,其重要性不言而喻。
油气管道在运输过程中会受到很多因素的影响,如介质、温度、压力、杂散电流等。
在油气管道运输过程中,如果发生了管道腐蚀,就会导致管道失效,给油气生产带来严重损失。
因此,在运输油气管道的时候必须要采取有效的防腐措施,避免发生更多的管道腐蚀事故[1]。
一、常见油气管道腐蚀原因(一)土壤腐蚀土壤中含有很多腐蚀性物质,如水、二氧化碳等。
这些腐蚀性物质与土壤接触后,会对管道造成腐蚀。
此外,土壤中还含有各种离子,如钠、钾、钙、镁等元素以及硫离子等,这些元素都会对金属产生化学作用,进而使金属材料受到腐蚀。
同时,土壤中有的还存在少量的杂散电流,比较容易发生电解质作用。
(二)大气腐蚀大气中含有大量水分和氧气,这些物质与油气管道接触后会对其产生腐蚀作用。
另外,空气中的水蒸气、二氧化碳和其他气体也会对油气管道造成影响。
(三)微生物腐蚀微生物腐蚀是指在各种原因(如温度、湿度等)的作用下,土壤中的微生物将金属材料或其他非金属材料分解的过程。
这些分解反应可能是化学反应(如氧化)或物理反应(如电化学反应),也可能是化学反应(如生物作用)。
(四)水腐蚀一些管道由于地域原因,会将其放置在海河当中,也会造成管道的腐蚀。
由于一些水的溶氧浓度、酸碱度、水的硬度、水流快慢、水的温度等等一系列因素都会影响管道的使用寿命。
应力腐蚀 美标-概述说明以及解释
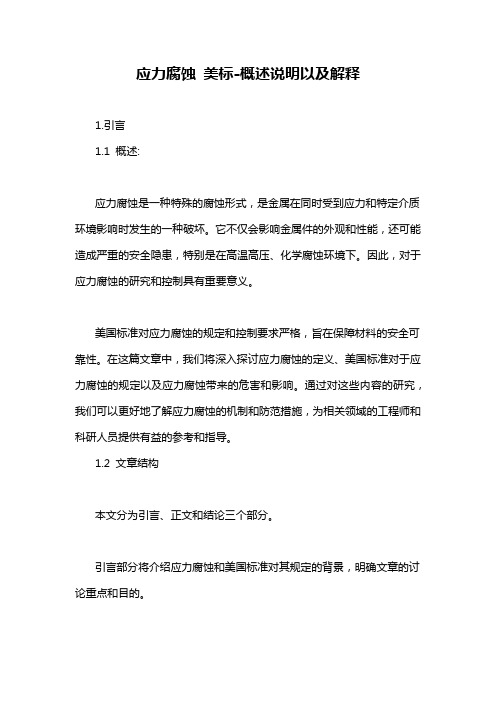
应力腐蚀美标-概述说明以及解释1.引言1.1 概述:应力腐蚀是一种特殊的腐蚀形式,是金属在同时受到应力和特定介质环境影响时发生的一种破坏。
它不仅会影响金属件的外观和性能,还可能造成严重的安全隐患,特别是在高温高压、化学腐蚀环境下。
因此,对于应力腐蚀的研究和控制具有重要意义。
美国标准对应力腐蚀的规定和控制要求严格,旨在保障材料的安全可靠性。
在这篇文章中,我们将深入探讨应力腐蚀的定义、美国标准对于应力腐蚀的规定以及应力腐蚀带来的危害和影响。
通过对这些内容的研究,我们可以更好地了解应力腐蚀的机制和防范措施,为相关领域的工程师和科研人员提供有益的参考和指导。
1.2 文章结构本文分为引言、正文和结论三个部分。
引言部分将介绍应力腐蚀和美国标准对其规定的背景,明确文章的讨论重点和目的。
正文部分将详细阐述应力腐蚀的定义、美国标准对应力腐蚀的规定以及应力腐蚀对材料的危害和影响。
通过对应力腐蚀的机理、特点和影响因素的分析,使读者对该问题有更深入的了解。
结论部分将对全文的内容进行总结,提出预防应力腐蚀的措施并展望未来的研究方向。
通过对已有知识的总结和展望,为读者提供更加全面的视角和启发思考。
1.3 目的目的:本文旨在探讨应力腐蚀在工程领域中的重要性及其对设备和结构的危害,同时对美国标准在应力腐蚀方面的规定进行深入分析和解读。
通过深入了解应力腐蚀的定义、规定和危害,进一步加强工程师和相关从业人员对这一问题的认识,提高在工程设计和实施过程中对应力腐蚀问题的警惕性和预防能力,保障工程设备和结构的安全运行和可靠性。
同时,希望通过本文的研究,为今后改进和完善相关标准提供参考和借鉴,促进应力腐蚀防治技术的进步和发展。
2.正文2.1 应力腐蚀的定义应力腐蚀是一种在特定环境下由于材料受到外部应力作用而导致腐蚀的现象。
应力腐蚀是一种复合腐蚀形式,通常需要同时存在腐蚀环境和应力。
这种腐蚀形式常常发生在金属材料中,尤其是在高强度合金和不锈钢中。
压力容器压力管道检验中裂纹问题的解决措施
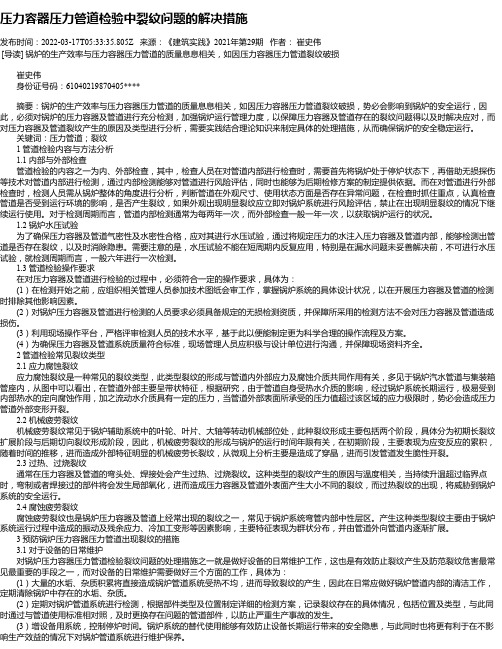
压力容器压力管道检验中裂纹问题的解决措施发布时间:2022-03-17T05:33:35.805Z 来源:《建筑实践》2021年第29期作者:崔史伟[导读] 锅炉的生产效率与压力容器压力管道的质量息息相关,如因压力容器压力管道裂纹破损崔史伟身份证号码:61040219870405****摘要:锅炉的生产效率与压力容器压力管道的质量息息相关,如因压力容器压力管道裂纹破损,势必会影响到锅炉的安全运行,因此,必须对锅炉的压力容器及管道进行充分检测,加强锅炉运行管理力度,以保障压力容器及管道存在的裂纹问题得以及时解决应对,而对压力容器及管道裂纹产生的原因及类型进行分析,需要实践结合理论知识来制定具体的处理措施,从而确保锅炉的安全稳定运行。
关键词:压力管道;裂纹1 管道检验内容与方法分析1.1 内部与外部检查管道检验的内容之一为内、外部检查,其中,检查人员在对管道内部进行检查时,需要首先将锅炉处于停炉状态下,再借助无损探伤等技术对管道内部进行检测,通过内部检测能够对管道进行风险评估,同时也能够为后期检修方案的制定提供依据。
而在对管道进行外部检查时,检测人员需从锅炉整体的角度进行分析,判断管道在外观尺寸、使用状态方面是否存在异常问题,在检查时抓住重点,认真检查管道是否受到运行环境的影响,是否产生裂纹,如果外观出现明显裂纹应立即对锅炉系统进行风险评估,禁止在出现明显裂纹的情况下继续运行使用。
对于检测周期而言,管道内部检测通常为每两年一次,而外部检查一般一年一次,以获取锅炉运行的状况。
1.2 锅炉水压试验为了确保压力容器及管道气密性及水密性合格,应对其进行水压试验,通过将规定压力的水注入压力容器及管道内部,能够检测出管道是否存在裂纹,以及时消除隐患。
需要注意的是,水压试验不能在短周期内反复应用,特别是在漏水问题未妥善解决前,不可进行水压试验,就检测周期而言,一般六年进行一次检测。
1.3 管道检验操作要求在对压力容器及管道进行检验的过程中,必须符合一定的操作要求,具体为: (1)在检测开始之前,应组织相关管理人员参加技术图纸会审工作,掌握锅炉系统的具体设计状况,以在开展压力容器及管道的检测时排除其他影响因素。
腐蚀学原理--第七章-应力作用下的腐蚀分析
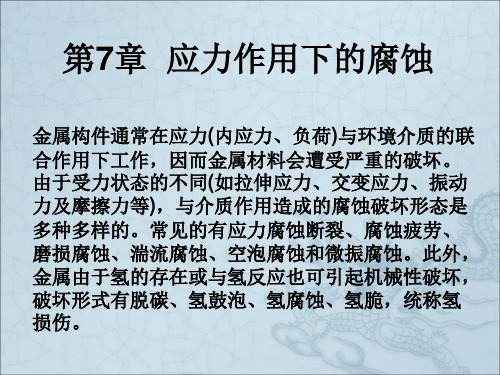
实例:中国版本的“黑Байду номын сангаас坠落”
7.1.3 防止应力腐蚀断裂的措施
1.降低或消除应力 (1) 改进结构设计,避免或减少局部应力集中。对应力腐蚀事故分析表明,由残余应力引起的比例最大,因此在加工、制造、装配中应尽量避免产生较大的残余应力。结构设计应尽量避免缝隙和可能造成腐蚀液残留的死角,防止有害物质(如Cl-、OH-)的浓缩。 (2) 消除应力处理:减少残余应力可采取热处理退火、过变形法、喷丸处理等方法。其中消除应力退火是减少残余应力的最重要手段,特别是对焊接件,退火处理尤为重要。 (3) 按照断裂力学进行结构设计:由于构件中不可避免地存在着宏观或微观裂纹和缺陷,因此用断裂力学进行设计比用传统力学方法具有更高的可靠性。在腐蚀环境下,预先确定材料的KISCC、da/dt等参数,根据使用条件确定构件允许的临界裂纹尺寸ac,具有重要的实际意义。
氢的存在形式
氢可以H-、H、H+、H2、金属氢化物、固溶体、碳氢化合物等形式存在于金属中,也可与位错结合形成气团(⊥H)而存在。当氢与碱金属(如Li、Na、K)或碱土金属作用时,可形成氢化物(如NaH)。在这类化合物中Na+和H-以离子键方式结合在一起,氢以H-形式存在。另一种观点认为,过渡族金属的d带没有填满,当氢原子进入金属后,分解为质子和电子,即H → H++e。氢的1s电子进入金属的d带,氢以质子状态存在于金属中。当金属d带填满后,多余的氢将以原子状态存在。也有观点认为,氢原子具有很小的原子半径(0.053nm),能处于点阵的间隙位置,如α—Fe的四面体间隙和γ—Fe的八面体间隙。最近,有的研究者又提出电子屏蔽概念。认为氢以原子态“H+e”存在于金属中,或者说氢以“屏蔽的离子”即穿有“电子外衣”的离子状态存在于金属中。 氢溶解在金属中可形成固溶体,氢在金属中的溶解度与温度和压力有关。氢在金属中如果超过固溶度,可形成分子氢(H2)、金属氢化物、氢原子气团三类化合物。
应力腐蚀裂纹的典型案例分析
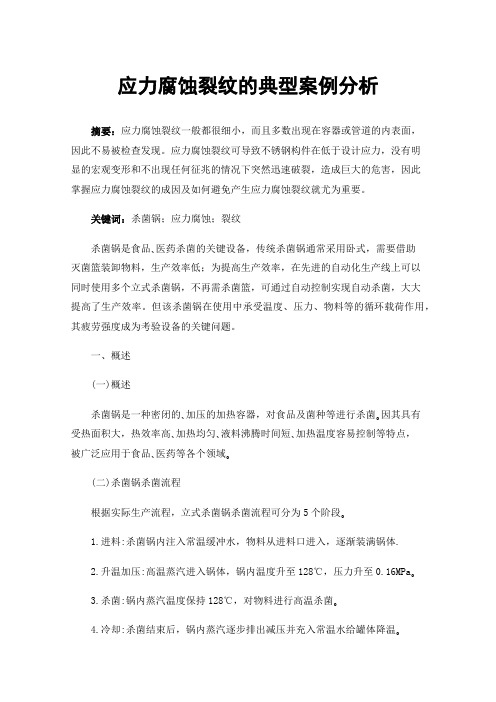
应力腐蚀裂纹的典型案例分析摘要:应力腐蚀裂纹一般都很细小,而且多数出现在容器或管道的内表面,因此不易被检查发现。
应力腐蚀裂纹可导致不锈钢构件在低于设计应力,没有明显的宏观变形和不出现任何征兆的情况下突然迅速破裂,造成巨大的危害,因此掌握应力腐蚀裂纹的成因及如何避免产生应力腐蚀裂纹就尤为重要。
关键词:杀菌锅;应力腐蚀;裂纹杀菌锅是食品、医药杀菌的关键设备,传统杀菌锅通常采用卧式,需要借助灭菌篮装卸物料,生产效率低;为提高生产效率,在先进的自动化生产线上可以同时使用多个立式杀菌锅,不再需杀菌篮,可通过自动控制实现自动杀菌,大大提高了生产效率。
但该杀菌锅在使用中承受温度、压力、物料等的循环载荷作用,其疲劳强度成为考验设备的关键问题。
一、概述(一)概述杀菌锅是一种密闭的、加压的加热容器,对食品及菌种等进行杀菌。因其具有受热面积大,热效率高、加热均匀、液料沸腾时间短、加热温度容易控制等特点,被广泛应用于食品、医药等各个领域。(二)杀菌锅杀菌流程根据实际生产流程,立式杀菌锅杀菌流程可分为5个阶段。1.进料:杀菌锅内注入常温缓冲水,物料从进料口进入,逐渐装满锅体.2.升温加压:高温蒸汽进入锅体,锅内温度升至128℃,压力升至0.16MPa。3.杀菌:锅内蒸汽温度保持128℃,对物料进行高温杀菌。4.冷却:杀菌结束后,锅内蒸汽逐步排出减压并充入常温水给罐体降温。5.出料:初步冷却完毕,物料从底部出料口排出,经出料装置至下一生产工序.整个流程中有两个典型的受力阶段:杀菌时,锅体承受最大温度载荷128℃和压力载荷0.16MPa;一个杀菌周期有3种循环载荷:①水压循环载荷,缓冲水注出导致的水压变化,最大水压值;②进出料循环载荷,待杀菌物料进出的物料压力;③进出蒸汽与升降温循环载荷。采用Workbench基于静力学理论、瞬态传热和热—结构耦合等分析立式杀菌锅两个典型阶段的力学特性。二、使用情况介绍杀菌锅基本参数该杀菌锅为内蒙古XX生物科技有限公司使用,通过高温蒸汽加热,对微生物菌种和NaCL盐水进行灭菌,在进行宏观检验时发现容器内部不锈钢金属表面已失去金属光泽(图一),经过打磨后对接管角焊缝及纵环焊缝进行渗透检测,在压力测试口接管角焊缝周围和疏水口接管角焊缝周围发现大量细微裂纹存在,裂纹形态多呈树枝状(图二、图三),经与使用单位人员沟通得知,在对NaCL盐水进行杀菌时,将NaCL盐水装在玻璃试管内,用橡胶塞堵住试管口进行杀菌操作,在杀菌的过程中,玻璃试管在加压加热的作用下,将橡胶塞弹出,部分NaCL盐水喷射到容器内壁上,从而产生腐蚀裂纹。
应力腐蚀断裂
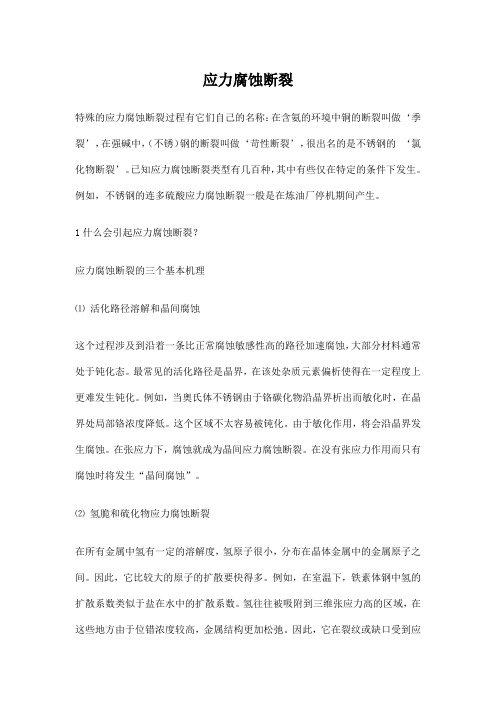
应力腐蚀断裂特殊的应力腐蚀断裂过程有它们自己的名称:在含氨的环境中铜的断裂叫做‘季裂’,在强碱中,(不锈)钢的断裂叫做‘苛性断裂’,很出名的是不锈钢的‘氯化物断裂’。
已知应力腐蚀断裂类型有几百种,其中有些仅在特定的条件下发生。
例如,不锈钢的连多硫酸应力腐蚀断裂一般是在炼油厂停机期间产生。
1什么会引起应力腐蚀断裂?应力腐蚀断裂的三个基本机理⑴活化路径溶解和晶间腐蚀这个过程涉及到沿着一条比正常腐蚀敏感性高的路径加速腐蚀,大部分材料通常处于钝化态。
最常见的活化路径是晶界,在该处杂质元素偏析使得在一定程度上更难发生钝化。
例如,当奥氏体不锈钢由于铬碳化物沿晶界析出而敏化时,在晶界处局部铬浓度降低。
这个区域不太容易被钝化。
由于敏化作用,将会沿晶界发生腐蚀。
在张应力下,腐蚀就成为晶间应力腐蚀断裂。
在没有张应力作用而只有腐蚀时将发生“晶间腐蚀”。
⑵氢脆和硫化物应力腐蚀断裂在所有金属中氢有一定的溶解度,氢原子很小,分布在晶体金属中的金属原子之间。
因此,它比较大的原子的扩散要快得多。
例如,在室温下,铁素体钢中氢的扩散系数类似于盐在水中的扩散系数。
氢往往被吸附到三维张应力高的区域,在这些地方由于位错浓度较高,金属结构更加松弛。
因此,它在裂纹或缺口受到应力作用之前就被吸附到这些区域。
此后,溶解的氢加速了金属的断裂,一方面使得开裂更容易,另一方面促进了局部塑性变形的迅速发展。
这些作用导致金属的脆化;断裂既可以在晶间也可以穿晶粒。
通常断裂扩展速度相当快,在最极端的情况下可达1mm/s。
铁素体的bcc(体心立方)晶体结构金属原子之间空隙相对小,但是这些空隙之间的通路相对宽。
因此氢在铁素体中的溶解度相对低,但扩散系数相对高。
相反,在fcc (面心立方)奥氏体晶格中空隙比较大,但它们之间的通路比较小,因此,像奥氏体不锈钢这样的材料,氢的溶解度比较高,扩散系数比较低。
所以,奥氏体不锈钢AISI 316L对氢脆几乎不敏感,而铁素体和双相不锈钢可能对这种现象敏感。
零件的脆性断裂(含疲劳、应力腐蚀、氢脆断裂等)失效分析
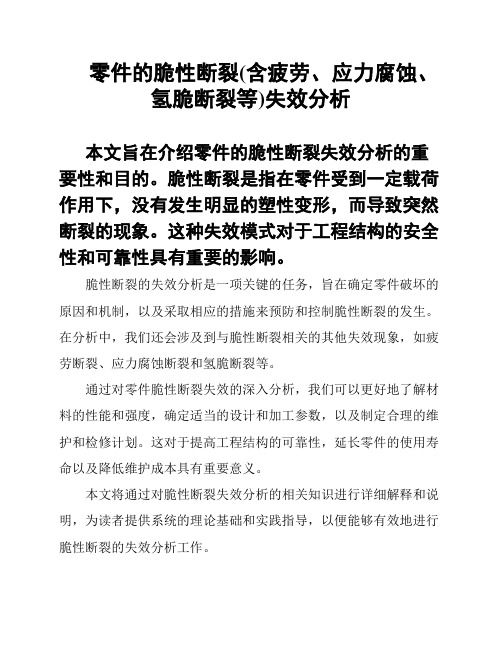
零件的脆性断裂(含疲劳、应力腐蚀、氢脆断裂等)失效分析本文旨在介绍零件的脆性断裂失效分析的重要性和目的。
脆性断裂是指在零件受到一定载荷作用下,没有发生明显的塑性变形,而导致突然断裂的现象。
这种失效模式对于工程结构的安全性和可靠性具有重要的影响。
脆性断裂的失效分析是一项关键的任务,旨在确定零件破坏的原因和机制,以及采取相应的措施来预防和控制脆性断裂的发生。
在分析中,我们还会涉及到与脆性断裂相关的其他失效现象,如疲劳断裂、应力腐蚀断裂和氢脆断裂等。
通过对零件脆性断裂失效的深入分析,我们可以更好地了解材料的性能和强度,确定适当的设计和加工参数,以及制定合理的维护和检修计划。
这对于提高工程结构的可靠性,延长零件的使用寿命以及降低维护成本具有重要意义。
本文将通过对脆性断裂失效分析的相关知识进行详细解释和说明,为读者提供系统的理论基础和实践指导,以便能够有效地进行脆性断裂的失效分析工作。
解释脆性断裂是指在应力作用下,当零件发生断裂时没有明显的塑性变形。
详细讨论导致脆性断裂的各种原因,包括疲劳、应力腐蚀、氢脆断裂等。
脆性断裂是指材料在受力作用下发生的突然断裂,常常发生在零件长时间受重复负载或特定环境下受力情况下。
脆性断裂的原因多种多样,下面将对其中的疲劳、应力腐蚀和氢脆断裂进行详细讨论。
疲劳断裂:疲劳断裂是由于零件在长时间受到变化的载荷作用下产生的。
当重复载荷作用于零件时,如果应力超过了材料的疲劳极限,就会发生疲劳断裂。
疲劳断裂是零件的高频失效模式,常见于机械装置和结构中。
应力腐蚀断裂:应力腐蚀断裂是指在特定环境中,材料受到应力和腐蚀介质共同作用时突然断裂。
应力腐蚀断裂的发生是由于腐蚀介质在零件表面引起局部腐蚀,而应力则产生了裂纹的扩展。
应力腐蚀断裂是一个复杂的断裂形式,常见于化工设备和海洋装备等领域。
氢脆断裂:氢脆断裂是由于材料在存在氢的环境中发生的断裂。
氢脆断裂的主要机制是氢的扩散和积聚在材料中,导致材料的力学性能降低,从而引起断裂。
黄铜管道部件应力腐蚀失效分析

黄铜管道部件应力腐蚀失效分析许雯【摘要】通过2个在一定腐蚀环境下工作的黄铜管道部件失效断裂的案例,分析黄铜管道部件的特点及失效原因,有助于提高黄铜管道的运行水平.结果表明:失效件均在承受一定应力的腐蚀环境中服役,从而引发应力腐蚀开裂.【期刊名称】《热处理技术与装备》【年(卷),期】2019(040)003【总页数】7页(P60-66)【关键词】黄铜管道;应力腐蚀;断裂;失效分析【作者】许雯【作者单位】上海轨道交通检测技术有限公司,上海200434【正文语种】中文【中图分类】TG113.23+1;TG146.1+1黄铜是以锌为主要合金元素的铜合金,由于其具有良好的工艺性能、力学性能和耐蚀性能,同时,合金的导电导热性也高,所以它是铜合金中应用最广泛的合金材料之一[1]。
为了改善黄铜的某些性能,在铜-锌二元普通黄铜基础上加入其它合金元素,称为复杂黄铜。
如铅黄铜,在基体中存在的铅质点既有润滑作用又能改善材料的切削性能等。
本文主要阐明铅黄铜作为管道阀门器件在应力作用下的腐蚀失效的案例。
由于工业管道常为压力系统,管道部件的失效一般常会造成事故。
因此,通过分析2个案例找出黄铜管道件特点及失效原因,会有助于提高黄铜管道的运行水平。
1 气动管路中气堵螺栓断裂案例分析1.1 断裂螺栓概况该螺栓用于机车顶部的受电弓气路中的三通的一端,工作环境恶劣,长期经受高电压负载、日晒雨淋、冷热变化等,气堵螺栓装配示意和外形见图1,总长约38 mm,螺纹段为(0.5~18)×15 mm;中间段外径约为φ10 mm,长约11.5 mm,该段的中间(偏六角头)有一约为φ3.8 mm的通孔;同时,螺栓有从螺纹段起始的φ6 mm×26 mm盲孔。
气堵螺栓材质为HPb62-3铅黄铜。
该螺栓在服役中发生断裂。
1.2 宏观检测断裂发生在中心通孔邻近螺纹段一侧,在中心通孔区裂纹均呈V字形,其V字尖端一侧穿过孔,见图2-1;另一侧指向孔,见图2-3;两V字的两臂止于螺纹段起始端转角,并沿转角周向发展,裂缝周边均未见机械损伤及变形现象。
压力管道缺陷产生原因及无损检测_1

压力管道缺陷产生原因及无损检测发布时间:2021-05-28T08:55:31.112Z 来源:《电力设备》2021年第2期作者:房爱伟[导读] 第三种是由于循环应力与腐蚀介质共同作用导致的腐蚀疲劳裂纹。
(国网新源控股有限公司检修分公司 100053)摘要:压力管道经过长期的高压运行后,会产生较多的缺陷问题,将会造成化工产业在经济和效率方面的损失,通过缺陷原因和无损检测技术的分析,能够有效促进压力管道缺陷问题的改善和防范,并加强无损检测技术的提高与发展,使化工产业的生产质量和效率得到更好的保障。
关键词:压力管道缺陷;产生原因;无损检测一、压力管道缺陷的产生原因(一)疲劳裂纹疲劳裂纹主要是由于压力管道的结构材料承受交变反复荷载,尤其是局部高应变区内的峰值应力已经远远超过材料所能承受的强度,会在晶粒之间形成滑移和错位等影响,最终导致微裂纹的产生,并随着荷载的增加而逐渐扩大成疲劳裂纹。
根据不同的形成原因,可以将疲劳裂纹分为常见的三种类型,第一种是由于交变工作荷载导致的疲劳裂纹,第二种是由于循环热应力导致的热疲劳裂纹,第三种是由于循环应力与腐蚀介质共同作用导致的腐蚀疲劳裂纹。
(二)应力腐蚀裂纹应力腐蚀裂纹就是金属材料受到特定腐蚀介质的拉应力影响所形成的裂纹,以奥氏体不锈钢压力管道中含有的氯离子最为常见。
(三)晶间腐蚀晶间腐蚀主要是受到特定介质的腐蚀影响,使结构的连续性受到严重损伤,以不锈钢管道的焊缝表面较为常见,尤其是熔合线和热影响区,其中最大的影响因素就在于晶间贫铬。
(四)局部腐蚀局部腐蚀以点腐蚀为主,主要是某些腐蚀性溶液与金属材料形成接触,导致局部腐蚀在金属材料表面逐渐形成,再随着腐蚀的不断进展而形成不断加深的蚀孔。
局部腐蚀中还常见磨损腐蚀,是指金属材料受到磨损和腐蚀的双重作用,会促进磨损和腐蚀的快速进展,导致金属材料的损伤速度和程度加剧。
二、压力管道无损的检测(一)无损检测技术的意义通过化工行业长期的发展经验,逐渐形成处理压力管道缺陷问题的多种措施,无损检测就是由长期的经验和实践总结而来。
TP347H锅炉钢管失效机理研究进展

D()I:10.11973/jxgccl202102002TP347H锅炉钢管失效机理研究进展MATERIALS FO R MECHANICAL ENGINEERING_________________________________________________2021 年2 月第45 卷第2 期Vo 丨.45 No. 2 Feb. 2021张骏,郑准备,杨占君,孙兴新,李梦阳,张建伟(中国大唐集团科学技术研究院有限公司西北电力试验研究院,西安710021)摘要:TP347H奥氏体耐热钢广泛应用于火电机组锅炉受热面管。
结合奥氏体耐热钢管服役 性能和TP347H钢管爆管失效案例,综述了 TP347H钢制受热面管在锅炉服役运行中常见的6种 失效机理,包括晶间腐蚀、应力腐蚀开裂、组织老化、氧化腐蚀、原始缺陷和马氏体转变,并介绍了失 效特征、分析方法和预防措施。
关键词:火电机组;奥氏体耐热钢;TP347H钢;失效分析;失效机理中图分类号:T G142.25文献标志码:A文章编号:1000-3738(2021)02-0007-08Research Progress on Failure Mechanisms of TP347H Boiler Steel TubeZHANG Jun, ZHENG Zhunbei, YANG Zhanjun, SUN Xingxin, LI Mengyang, ZHANG Jianwei (N o r thwest P o w e r Te c h n o l o g y Research Institute, China D a t a n g G r o u p Science andT e c h n o l o g y Research Institute C o.,Ltd.,X i’an 710021,China)Abstract :T h e austenitic heat-resistant steel T P347H is widely used in heating tubes of thermal p o w e r unit boilers. C o m b i n i n g the service performance of austenitic heat-resistant steel tubes and the failure cases of T P347H steel tube bursts, the six c o m m o n failure m e c h a n i s m s,including intergranular corrosion, stress corrosion cracking, microstructure aging, oxidative corrosion, original defects and martensite transformation, of T P347H steel heating tubes during boiler operation are reviewed. T h e failure characteristics, analysis m e t h o d s and preventive measures are described.Key words:thermal p o w e r unit;austenitic heat-resistant steel;T P347H steel;failure analysis;failure m e c h a n i s m〇引言TP347H钢(国产牌号07Crl8N illN b)是在 18Cr-10N i合金钢的基础上添加稳定化元素铌(质 量分数约0.8%),并经固溶处理(热轧钢管固溶处 理温度不低于1 050 °C,冷拔钢管固溶处理温度不 低于1 095 °C)后,具有NbC型第二相析出强化基 体以及良好弯曲和焊接性能的粗晶奥氏体耐热钢[1,3]。
压力管道全面检验与内检测规范内容分析

2021年第 1期 特 种 设 备 安 全 技 术 · 19·压力管道全面检验与内检测规范内容分析韦永金 吴文林 秦 硕 候智强 陈立可摘 要根据管道相关规范内容, 对管道全面检验与内检测的关系、 检验周期确定原则的差异以及完整性评价与合于使用评价的关系等问题, 使用对比分析、 逻辑分析方法, 研究规范的内容, 进一步解读规范, 对规范之间的异同点进行阐 述, 同时为规范修订提出建议。
关键词管道完整性管理 全面检验 内检测 规范研究分析1 引 言特种设备法定检验是给设备看病, 是一种基本安全服 务, 是强制性的, 主要实行属地化管理, 只要企业提出申 请, 检验机构就应当提供这种服务, 同时, 一个企业购买了 法定检验这种安全服务后, 不仅保障了自身设备的安全, 也保障了周围人、 物和环境的安全 [1]。
“检验” 经常与 “检测” 相混淆, 实际二者有本质区别, 检测强调的是测试某项具体技术性能, 而检验强调的是验 证与相关要求的符合性; 特种设备行业的法定检验一般是 指检验机构依据 《特种设备安全法》 开展的检验, 目前法定 检验没有明确的定义, 是一个集合概念, 可以概括为: 经特 种设备监管部门核准的检验机构, 依据 《特种设备安全法》 开展的监督检验、 定期检验以及设计文件鉴定和型式试验 等强制性检验 [1]。
对于管道使用单位而言, 由于法定检验没有明确的定 义, 在保证管道安全前提下各种特种设备相关规范规定的 管道 “体检” 类型较多。
本文对管道全面检验与内检测、 外 检测等检测方式涉及到的现有规范内容进行分析、 讨论, 同时给出修改建议。
2 全面检验周期的规定2.1D7003规范内容分析根据TSG D7003-2010《压力管道定期检验规则长输 (油气) 管道》(以下简称D7003) 第三条:“管道的定期检验 通常包括年度检査、 全面检验和合于使用评价。
” D7003第 三条第 (二) 款: “首次全面检验之后的全面检验周期按照 本规则第二十三条确定” ; 第二十三条: “应当结合全面检 验和合于使用评价结果, 确定下次全面检验日期, 其全面 检验周期不能大于表1的规定, 并且最长不能超过预测的 管道剩余寿命的一半。
- 1、下载文档前请自行甄别文档内容的完整性,平台不提供额外的编辑、内容补充、找答案等附加服务。
- 2、"仅部分预览"的文档,不可在线预览部分如存在完整性等问题,可反馈申请退款(可完整预览的文档不适用该条件!)。
- 3、如文档侵犯您的权益,请联系客服反馈,我们会尽快为您处理(人工客服工作时间:9:00-18:30)。
Safety is the goal, prevention is the means, and achieving or realizing the goal of safety is the basic connotation of safety prevention.(安全管理)单位:___________________姓名:___________________日期:___________________管道的应力腐蚀断裂(2021新版)管道的应力腐蚀断裂(2021新版)导语:做好准备和保护,以应付攻击或者避免受害,从而使被保护对象处于没有危险、不受侵害、不出现事故的安全状态。
显而易见,安全是目的,防范是手段,通过防范的手段达到或实现安全的目的,就是安全防范的基本内涵。
四川省的天然气管线由于介质未处理好,在被输送的天然气中H2 S大大超过规定的含量,曾发生多次爆破事故。
据国外文献介绍,美国1955年第一次发生由于氢脆而产生的氢应力破坏,六十年代出现了其他形式的应力腐蚀断裂,以后随着时间的延续,这类破坏事故越来越多,而应力腐蚀断裂也越来越多地为管道工作者所关注,并成为研究的课题。
应力腐蚀断裂简称为SCC,这系由英文名词StressCorrosionCrac King而来的,其定义为:在应力和介质联合作用下,裂纹的形成和扩展的过程叫做应力腐蚀,由于应力腐蚀而产生的断裂称为应力腐蚀断裂。
当原始缺陷的长度2a小时临界裂纹长度2ac时,管线是不会断裂的,但由于疲劳或(和)环境的作用,裂纹长度可以增长,当原始缺陷长度逐渐增长,最后达到2ac时,则管道产生断裂。
这里只将讨论后者,即在环境和应力相互作用下引起的应力腐蚀断裂。
一、应力腐蚀的机理为说明应力腐蚀需先简单的介绍腐蚀反应。
大家知道,钢铁放在潮湿的空气中,就会生锈,锈不断脱落,就会导致截面减小和重量减轻,这称为钢铁受到了腐蚀。
腐蚀是一种电化学过程,它又可分为阳极过程和阴极过程,这二者是共存的。
金属原子是由带正电的金属离子,对钢来说,就是二价的铁离子F2+和周围带负电的电子云(用e-来表示)构成的,如下所示:Fe→Fe2++2e-上式是一个可逆反应。
当铁遇到水,铁离子Fe2+和水化合的倾向比Fe2+与e-结合成金属的倾向还要强,因此金属铁遇到水后就会发生如下反应:上式放出电子e-,故称为阳极反应。
阳极反应所放出的电子必须通过阴极过程(即吸收电子的过程)被取走,式的反应才能继续存在,否则该式将是可逆的。
一种常见吸收电子的阴极过程是吸氧过程,见下式:O2+2H2O+4e-→4OH-氢氧根OH-和铁离子Fe2+结合,就会产生铁锈,即Fe2O32Fe2++60H-→Fe2O3·3H2O综合阳极过程和阴极过程,即联合上两式,可写出下式:4Fe+nH2O+3O2→2Fe2O3·nH2O由上式可以看出,钢管生锈的条件为第一要接触水(或潮湿的空气),第二要接触空气,以提供O2前者是阳极过程,后者是阴极过程。
实验表明,和腐蚀介质相接触的阳极金属介面上会形成一层致密的复层,即纯化膜,它能阻碍阳极金属进一步溶解。
但金属构件,如钢管受到一定大小的拉伸应力作用时,由于应力集中,在裂纹尖端附近存在很高的拉伸应力场,它能阻碍裂纹尖端表面形成纯化膜,从而把新鲜的金属暴露在腐蚀介质面前,并造成裂纹的扩展,这就是应力腐蚀。
如果作用在构件上的是压应力或是拉应力,但数值很小时,这就无法使裂纹尖端的纯化膜膜破裂,因此裂纹也就不会扩展,故应力腐蚀除腐蚀所需要的条件之外,还得存在一定大小的拉伸应力。
正由于阳极溶解过程中除裂纹尖端表面外,其余部分全被纯化覆盖,故应力腐蚀时,仅是裂纹尖端向前扩展。
应力腐蚀中一个重要的分枝,即氢应力腐蚀,简写为HSC,系由英文HydrogenStressCracKing而来。
吸收电子的阴极过程除了吸氧反应外,还有放氢过程,如:在阴极形成的氢原子[H]有两条去路,一是原子氢结合成分子氢,并放出来:[H]+[H]→H2↑另一条去路是氢原子通过扩散进入金属内部,进入金属内部的[H]使金属原子的结合力下降,基体脆化,这种以阴极放氢导致的破坏称为氢脆。
氢的来源除上述的阴极放氢反应外,对于管道来说,主要来自输送介质,如H2S气体。
近若干年来的研究表明,对管道的阴极保护也会在金属的外表面产生[H]。
氢应力腐蚀象其他应力腐蚀一样,除有腐蚀性介质外,还有另一重要条件,即必须受到一定大小的拉应力。
二、KIscc及da/dtKIscc为应力腐蚀临界强度因子。
由本书的第三章可知,当原始裂纹长度为2a,由于内压而引起的应力为σ时,在管线中裂纹尖端的应力强度因子为:当KI<Kc,不会起裂当KI≥Kc,起裂如果原始缺陷长度为a0,应力为σ1,求出的应力强度因子为[KI]1,而[KI]1<Kc,故不会产生断裂;若管线在腐触环境中工作,由于应力腐蚀作用,a值逐渐增加,随之(KI)1,也逐渐增长,最后当应力强度应子达到Kc时,而产生破裂,请参见图2-5-10。
K1B1曲线(用虚线绘出)为随着时间的流逝,a值不断扩大,随之[KI ]1也不断扩大的曲线,由a0增长至ac或由[KI]1,增长至Kc所需的时间为t1。
如原始缺陷长度仍为a0,但应力为σ0,且σ2<σ1,故[KI]2<[KI]1,在图2-5-10中[KI]2在[KI]1,的下方,如在同一腐蚀环境下工作,由于应力下降,裂纹增长速度da/dt缓慢,a0达到ac的时间为t2,t2t1。
随着外加应力不断下降,KI也随之下降,由a0增长至ac所需要的时间也越长,当KI低于某一临界值称为应力腐蚀临界强度因子,用KIscc表示。
图2—5—10KI—t曲线见图2—5—11,在A0的应力强度应子为Kc,此时对应的断裂时间t=0,[KI]1与B1的交点为C1,[KI]2与B2的交点为C2,以此类推,连接A0,C1、C2、…得出一条曲线(为图中的实线),该曲线为KI 与断裂时间的关系曲线,KIscc为该曲线的渐近线。
当应力腐蚀裂纹前端的KI>KIscc时,裂纹就随时间而变大,单位时间内裂纹由于应力腐蚀而产生的扩展量称为应力腐蚀扩展速率,用da/dt表示。
da/dt与多种因素有关。
下面将作详细论述:da/dt与KIscc的关系大致如图2—5—11所示,由图看出,da/dt与KIscc关系可分为三个阶段:第Ⅰ阶段,KI刚超过KIscc裂纹经过一段孕育期,突然加速发展;第Ⅱ阶段,da/dt与KI 的关系不大,第Ⅲ阶段,裂纹长度已接近临界尺寸,da/dt又明显依赖于KI。
国外近若干年来,有些管道研究工作者倾向于用σth代替KIscc来表示应力腐蚀的应力界限值,σth的定义为:“当钢管中的应力高于此应力时,则可能产生SCC,低于此应力值时,则不可能产生SCC,此应力界线值称为应力腐蚀拉应力的界线值,或称门槛值,用σth表示”th为英文“thresholdstress”前面的两个字母。
所以选用σth有以下原因:(1)σth值易于由试验中取得;(2)σth与内压P直接相关联,似乎更有实际意义。
当σth求出后,可求出在具体条件下的KIscc值。
研究表明,以下诸因素影响σth值:(一)腐蚀介质对σth的影响不同的腐蚀介质及不同的介质浓度均对σth有影响。
图2—5—12为X52管材在NaNO3及NH4NO3水溶液中不同重量浓度对σth的影响,由图看出,浓度越高σth值越低,不同腐蚀介质对σth也有很大影响。
(二)管子与土壤间的电化学电位对σth的影响对任何已知环境,应力腐蚀只在很窄的一段电化学电位范围内才能产生,而且在这一范围内的σth,也是随电位而变化的。
见图2—5—13。
图2—5—12不同介质及浓度对σth的影响图5—2—13为X52管材在4.8%Ca2CO3和7.6%CaHCO3水溶液中,不同电位对盯σth的影响,由图看出,在这一特定情况下,电位为-0.70伏时,σth最低,亦即最易产生应力腐蚀,向两侧偏离σth迅速提高。
(三)应力状态对σth的影响应力的波动对σth有很大影响,见图2—5—14。
图2—5—14为X52管材,在Ca2 CO3浓度为4.8%,CaHCO3浓度为7.6%的水溶液中的情况,在静荷载下,σth≈1.25(SMYS),但应力波动时,σth有所降低,波动幅度为±1.5%,由此看出,波动的频率越低,σth降低值也越大。
如果波动频率为每三天一个循环,应力变化幅度为±1.5%~±5%,这时σth值只有静荷载时%值的60%。
图2—5—13电化学电位对σth的影响图2—5—14应力波动对σth的影响(四)人工时效对σth的影响钢材使之产生永久变形以后,再加热至某一温度,并维持一定时间的这一过程称为人工时效。
钢管在制造过程中先压成U形,再进一步压成O形,焊接后,再经过涨管整形,在整个制造过程中钢材经历了永久变形。
对于螺旋钢管,在制造过程和滚卷过程中,亦产生永久变形。
钢管在加设外涂层或(和)操作过程中,有可能需要加热,这样就形成了人工时效。
见图2—5—12,该图为X52钢管,在14℃下维持一小时,形成了人工时效,实践为经历了人工时效的情况,虚线为未经人工时效的情况(虽有永久变形,但未加热),由图看出,在2%永久变形时,σth 值最低。
除以上因素外,还有一些其他因素也影响σth值,如钢材在热轧过程中,表面脱炭可使σth有所下降,管材表面径喷丸处理后,又使σth有所上升。
总之,影响σth的因素是很多的,为了准确事先估计σth值也是十分困难的。
图2—5—15时效的影响三、氢应力腐蚀(氢脆)1955年就曾经发生过由于氢应力腐蚀(简称HSC)而产生管道断裂的事故,此后曾经进行过大量的研究工作,但至今仍有许多理论问题未曾搞清楚,而且研究工作者在这一领域内的许多认识还是互相矛盾的。
但是,以下几点是大家共同肯定的:(1)钢材的强度极限高于某一数值时,才可能产生HSC现象,通常这一数值被认为是7000~7700kg/cm2(100~110×103lb/in2);(2)钢材必须承受拉应力,且该拉应力必须高于某一确定的临界值时(该临界值与钢材的强度等级有关)才可能产生HSC;(3)原子氢必须溶解于钢材中,且必须达到一定的浓度时,才能产生HSC。
换句话说,只有同时满足以上三个条件,才有可能产生HSC。
有时人们常把HSC与其他的SCC现象相同混淆。
HSC与其它SCC 相比,有以下特点:(1)由HSC产生的破裂面上无沉积物,一般呈白色,而其它SCC的破裂面上有明显的黑色沉积物,其成分常为Fe3O4和PeCO3;(2)从外表看,HSC裂纹扩展比较平滑,而其它SCC裂纹扩展呈锯齿形;(3)HSC裂纹一般无分枝,而其它SCC为多分枝的;(4)HSC裂源处的金属金相组织为马氏体,而其它SCC裂源处的金相组织多为铁素体和珠光体;(5)HSC所产生的断裂一般为脆性断裂,且多为穿晶破坏,其它SCC 断裂则不一定。