机械加工工艺技术误差分析与控制
机械加工锥度误差的分析与控制

机械加工锥度误差的分析与控制在机械加工中,锥度误差是一个很常见的问题。
对于需要精度较高的零部件而言,锥度误差的存在会造成影响,甚至导致产品的失效。
因此,了解和掌握锥度误差的分析和控制方法十分关键。
一、锥度误差的定义及分类锥度误差指的是加工的零部件在锥面的直径或位置上出现的偏差。
按照偏差类型的不同,可以将锥度误差分为两类:一类是直徑误差,即端面锥度误差,另一类是位置误差,即轴向锥度误差。
两者的区别在于,前者指的是端面锥面上的偏差,后者则是指锥面与轴线偏离的偏差。
二、锥度误差分析方法1、观察法通过目测或使用专用的仪器来观察加工的零件,并测量几个关键点的尺寸,从而确定锥度误差的存在和大小。
这种方法的优点是简单易懂,但准确度受到操作者的经验和观察能力的限制。
2、放大法通过放大镜、投影仪等仪器,将零件放大并投影在屏幕上,然后对投影图进行观察和测量,以确定锥度误差的存在和影响程度。
这种方法的优点是准确度高,但需要专用的仪器和技术人员。
3、数字化测量法利用数字化测量仪器对加工的零件进行三维测量,然后通过软件对所得到的数据进行分析和处理,最终得到锥度误差的大小和位置。
这种方法的优点是精度高、可重复性好、速度快,但需要投资一定的成本。
三、锥度误差控制的方法1、选择适当的加工方式和工艺对于需要精度较高的零部件,应选择比较稳定可靠的加工方式和工艺,如磨削、慢走丝加工等。
同时,制定合理的加工方案,对加工过程进行监控和调整,保证加工质量的稳定性和可靠性。
2、严格控制加工参数对于不同的锥度误差类型和大小,要采取不同的加工参数措施。
例如,在轴向锥度误差较大时,应通过调整加工速度、切削深度、切削速率等参数,来达到控制误差的目的。
在直径误差较大时,则应采取使用更好的砂轮、切削液、工艺装备等手段,来提高加工质量和精度。
3、使用合适的检测仪器采用适当的检测仪器来检测加工出来的零部件的质量和精度,从而发现和纠正存在的误差。
常用的检测仪器包括光学测量仪、三坐标测量仪等。
在机械加工过程中的误差分析及数学建模研究

在机械加工过程中的误差分析及数学建模研究机械加工是制造过程中不可或缺的一环。
然而,在机械加工过程中,由于种种因素的影响,难免会出现误差。
误差的存在直接影响到零部件的质量和精度,因此对机械加工过程中的误差进行分析和数学建模研究具有重要的意义。
一、误差来源分析在机械加工过程中,误差可以来源于多个方面,包括:1.制造设备的误差:制造设备本身的精度会对加工零件的准确性产生影响。
例如,机床的刚性、热变形、传动系统的间隙等都会造成误差的产生。
2.切削力的变化:由于刀具的磨损或者加工条件的变化,切削力会发生变化,从而导致零件加工中出现误差。
3.工件的变形:加工过程中,工件可能会因为切削力等原因而发生变形,使得加工结果与设计要求不符。
4.加工过程中的振动:振动是机械加工中不可避免的现象,但过大的振动会引起工件位置的偏移,从而影响加工精度。
二、误差分析方法为了更好地理解机械加工过程中的误差,并对其进行建模研究,我们通常采用以下几种误差分析方法:1.测量方法:通过测量零件的几何属性,使用测量仪器和测量技术分析零件的误差情况。
常用的测量方法包括三坐标测量、投影仪测量等。
2.试验方法:通过设计一系列的试验,控制其他因素不变,仅改变某个因素,如切削速度、刀具刃磨状况等,来测量零件加工结果的误差。
通过对试验结果的分析,可以得到误差与各个因素之间的关系。
3.仿真模拟方法:利用计算机建立机械加工过程的仿真模型,通过对模型进行参数调整和试验,得到加工结果的误差。
仿真模拟方法可以节省时间和成本,并能够更好地在加工过程中控制误差。
三、数学建模研究数学建模是解决误差分析问题的重要方法之一。
在机械加工领域,数学建模可以针对不同的误差来源进行研究,建立与之相关的数学模型,从而帮助我们更加深入地理解误差的本质,并提供改善加工精度和质量的方法。
在误差分析中,常用的数学模型包括:1.误差传递模型:利用数学方法研究误差在加工过程中的传递规律,分析传递路径和影响因素,以便为误差的减小提供方向。
机械制造工艺学加工误差统计分析报告

机械制造加工误差的统计分析一、实验目的:1.通过实验掌握加工精度统计分析的基本原理和方法,运用此方法综合分析零件尺寸的变化规律。
2.掌握样本数据的采集与处理方法,正确的绘制加工误差的实验分布曲线和x-R图并能对其进行正确地分析。
3.通过实验结果,分析影响加工零件精度的原因提出解决问题的方法,改进工艺规程,以达到提高零件加工精度的目的,进一步掌握统计分析在全面质量管理中的应用。
二、实验用材料、工具、设备1.50个被测工件;2.千分尺一只(量程25~50);3.记录用纸和计算器。
三、实验原理:生产实际中影响加工误差的因素是复杂的,因此不能以单个工件的检测得出结论,因为单个工件不能暴露出误差的性质和变化规律,单个工件的误差大小也不能代表整批工件的误差大小。
在一批工件的加工过程中,即有系统性误差因素,也有随机性误差因素。
在连续加工一批零件时,系统性误差的大小和方向或是保持不变或是按一定的规律而变化,前者称为常值系统误差,如原理误差、一次调整误差。
机床、刀具、夹具、量具的制造误差、工艺系统的静力变形系统性误差。
如机床的热变形、刀具的磨损等都属于此,他们都是随着加工顺序(即加工时间)而规律的变化着。
在加工中提高加工精度。
常用的统计分析有点图法和分布曲线法。
批零件时,误差的大小和方向如果是无规律的变化,则称为随机性误差。
如毛坯误差的复映、定位误差、加紧误差、多次调整误差、内应力引起的变形误差等都属于随机性误差。
鉴于以上分析,要提高加工精度,就应以生产现场内对许多工件进行检查的结果为基础,运行数理统计分析的方法去处理这些结果,进而找出规律性的东西,用以找出解决问题的途径,改进加工工艺,提高加工精度。
四、实验步骤:1.对工件预先编号(1~50)。
2.用千分尺对50个工件按序对其直径进行测量,3. 把测量结果填入表并将测量数据计入表1。
表内的实测值为测量值与零件标准值之差,单位取µm五、 数据处理并画出分布分析图:组 距: 44.59)35(1411min max =--=--=-=k x x k Rd µm 5.5=d µm 各组组界: ),,3,2,1(2)1(min k j dd j x =±-+ 各组中值: d j x )1(min -+16.1111-==∑=ni i x n x µm 28.12)(1112=--=∑=ni i x x n σ六、 误差分析1.加工误差性质样本数据分布与正态分布基本相符,加工过程系统误差影响很小。
机械零件装配过程中的误差分析与控制

机械零件装配过程中的误差分析与控制在机械制造领域中,装配是一个至关重要的环节。
装配过程中的误差会直接影响到机械的性能和精度。
因此,对于机械零件装配过程中的误差进行分析与控制是非常重要的。
一、误差分析在机械装配过程中,误差的来源可以分为多种类型。
首先是零件本身的尺寸误差。
由于加工工艺的限制,零件的尺寸无法完全做到精确。
其次是人为因素引起的误差,如操作工人的技术水平和专注度等。
还有一些误差是由装配工艺决定的,比如装配顺序和工艺参数等。
针对以上误差来源,我们可以通过一些方法进行误差分析。
首先是对零件尺寸进行测量与分析,了解其误差范围和分布情况。
其次是对装配过程进行实时监控,例如使用传感器等装置对关键节点进行监测,以便及时发现和纠正误差。
最后是通过统计学方法对误差进行分析,找到误差的主要来源和影响因素,为下一步的误差控制提供依据。
二、误差控制误差控制是指通过一系列的措施和方法,减小和控制机械零件装配过程中的误差。
首先是优化零件加工工艺,提高零件的精度和一致性。
这可以通过改进加工设备和工艺参数,提高机械加工过程的稳定性和准确度,从而减小零件尺寸误差。
其次是加强对装配工人的培训与管理,提高其技术水平和专注度。
专业的培训可以帮助工人了解装配过程中的误差来源和控制方法,从而减小人为误差的发生概率。
同时,建立一套完善的工艺标准和质量控制体系,对装配过程进行规范和监控,可以进一步减小装配误差。
此外,使用先进的装配设备和技术也是误差控制的重要手段。
例如,可以采用自动化装配线,减少人为操作的不确定性。
还可以利用机器视觉系统和机器人技术来实现高精度的零件配对和装配,从而提高装配的准确度和效率。
最后,建立完善的质量检测系统也是误差控制的关键环节。
通过对装配完成的机械进行全面的质量检测,可以及时发现和纠正装配过程中的误差,确保机械的性能和精度。
三、结论机械零件装配过程中的误差分析与控制是保证机械性能和精度的关键步骤。
通过对误差来源进行分析和控制,可以有效减小装配误差的发生概率。
机械加工工艺的技术误差问题及对策分析

机械加工工艺的技术误差问题及对策分析机械加工工艺是制造业中非常重要的一个环节,而技术误差问题是在机械加工过程中经常会遇到的一个难题。
技术误差问题一旦出现,不仅会影响产品的质量和精度,还会导致生产周期延长和成本增加。
对于机械加工工艺的技术误差问题及对策分析,是非常值得关注和深入研究的话题。
一、技术误差问题概述在机械加工过程中,技术误差是很难完全避免的。
技术误差主要表现为尺寸、形位和表面粗糙度方面的误差。
这些误差会直接影响产品的质量和精度,严重影响产品的使用性能和寿命。
技术误差问题不仅仅是机械加工工艺本身的问题,更是机械加工人员是否具备高水平的技术素养和严格的操作规范。
1. 设计误差:如果产品的设计尺寸、形位公差设置不合理,也会直接导致技术误差的产生。
2. 材料误差:材料的成分、硬度、力学性能等参数不符合要求,也会对机械加工产生影响。
3. 加工设备精度不足:机床、刀具、夹具等加工设备的精度不足,也会直接导致技术误差的产生。
4. 操作不当:加工人员操作不当,比如刀具磨损严重、刀具切削速度过快或过慢、切削进给量不合理等,都会引起技术误差。
5. 环境因素:加工环境的温度、湿度、灰尘等因素也会对机械加工产生影响,导致技术误差的产生。
三、对策分析1. 严格的产品设计与工艺标准产品设计的合理性和工艺标准的严格性是避免技术误差的关键。
产品设计要合理设置公差,严格控制尺寸、形位和表面粗糙度等要求,避免设计误差的产生。
工艺标准也要明确相关参数,确保每道工序的加工技术要求得到满足。
2. 材料的严格把控材料的选用直接影响机械加工的质量和精度,在材料的选用方面要严格把控,确保材料的质量和性能符合要求。
3. 加工设备的精度保证加工设备的精度是保证机械加工质量和精度的基础。
在购买、维护和保养加工设备时,要严格把控设备的精度,确保设备的正常运行和高效加工。
4. 加工人员的素质提升加工人员的技术水平和操作规范直接影响机械加工的质量和精度。
精密机械加工中的加工误差分析与控制研究

精密机械加工中的加工误差分析与控制研究序言:精密机械加工是现代制造业中不可或缺的关键技术之一,其准确度和精细度的要求越来越高。
在这个过程中,加工误差是无法避免的,因此对加工误差的分析与控制成为了研究的焦点之一。
一、加工误差的来源1. 设备精度精密机械加工设备是保证加工精度的基础,高精度的设备可以提供更好的加工效果,降低加工误差的发生。
如果设备精度达不到要求,加工误差难以控制。
2. 切削力与刚性在精密机械加工中,切削力对工件的影响极大。
切削力过大或者设备刚度不足会导致加工误差的增加。
因此,切削力的控制和提高设备刚性是减小加工误差的重要因素。
3. 刀具磨损由于刀具长时间使用或者加工材料硬度较高,刀具会出现磨损。
刀具磨损会导致加工力的变化,进而影响加工质量。
因此,及时更换刀具以保持加工质量是必要的。
二、加工误差的类型1. 圆度误差圆度误差是指加工出来的圆形工件与理论圆形工件间的最大偏差。
圆度误差是精密机械加工中常见且重要的误差类型,其大小直接影响到机械零件的质量与性能。
2. 直线度误差直线度误差是指加工出来的直线与理论直线之间的最大偏差。
直线度误差会影响机械零件在运动中的平稳度和精度。
3. 角度误差角度误差是指加工出来的工件角度与理论角度之间的最大偏差。
角度误差会直接影响到机械零件间的连接和传动,进而影响结构的稳定性与工作效果。
三、加工误差的分析方法1. 测量方法精密加工误差的准确分析需要依赖精密的测量方法。
常用的测量方法包括二维测量仪、三维测量仪、光学测量仪等。
这些测量仪器可以提供具有亚微米精度的测量结果。
2. 数据处理与分析对加工误差数据的处理与分析是为了更好地理解误差的产生原因。
常用的分析方法有数据拟合、统计分析、频谱分析等。
通过这些方法,可以找出引起加工误差的关键因素。
四、加工误差的控制方法1. 工艺参数优化工艺参数的优化对于控制加工误差至关重要。
通过调整切削速度、进给速度、切削深度等工艺参数,可以减小加工误差的发生。
浅谈机械加工误差的分析

浅谈机械加工误差的分析机械加工误差是指实际加工零件的尺寸、形状、位置、表面质量等与设计要求或测量结果之间的偏差。
在机械加工中, 误差是不可避免的, 因此对机械加工误差进行分析是非常重要的。
本文将详细分析机械加工误差的产生原因、种类以及对策措施,希望能够对读者有所帮助。
一、机械加工误差的产生原因1. 加工设备问题加工设备是机械加工的基础,设备的精度、稳定性和可靠性直接影响着加工零件的质量。
设备的老化、磨损和维护不当是导致机械加工误差的重要原因之一。
2. 工艺因素在机械加工中,工艺参数的选择直接关系到零件的加工质量。
切削速度、进给量、切削深度等技术参数的合理选择能够有效减小误差的产生。
3. 材料因素不同材料的物理性质不同,机械加工对材料的硬度、韧性、拉伸性等性能要求也不同,如果材料的性能不符合要求,会导致机械加工误差的产生。
4. 操作人员技术水平操作人员的技术水平直接影响着加工零件的质量,操作人员对设备的熟练程度、对工艺参数的把握能力、对材料性能的了解程度等都是直接影响误差产生的因素。
1. 尺寸误差尺寸误差是指零件的实际尺寸与设计要求的尺寸之间的偏差,通常包括线性尺寸误差和非线性尺寸误差。
2. 形状误差形状误差是指零件的实际形状与设计要求的形状之间的偏差,通常包括平面度、圆度、圆柱度、并行度、垂直度等。
1. 加强设备维护定期对加工设备进行维护保养、及时更换老化磨损的零部件,以保证设备的精度、稳定性和可靠性。
3. 严格控制材料质量在零件加工过程中,选用合格的优质材料,并对材料进行必要的热处理,以确保材料的性能符合加工要求。
5. 使用适当的检测手段在机械加工过程中,使用适当的检测手段对零件进行检验,及时发现误差并采取措施进行调整和修正。
除了上述措施之外,还可以通过优化加工工艺、提高加工精度和改进加工工艺等方法来减小机械加工误差。
机械加工误差是在机械加工过程中难以避免的问题,了解误差产生的原因和种类,采取相应的对策措施是保证零件加工质量的关键。
机械制造工艺中的加工误差分析与优化

机械制造工艺中的加工误差分析与优化近年来,随着制造业的快速发展,机械制造工艺中的加工误差问题变得越来越重要。
加工误差不仅会影响产品的质量,还会导致产品的性能下降甚至无法使用。
因此,对于机械制造工艺中的加工误差进行深入分析和优化是至关重要的。
一、加工误差的来源在机械制造过程中,加工误差主要来源于材料、设备和操作等方面。
首先,材料的不均匀性和内在应力会导致加工过程中的变形和误差。
其次,设备的精度和稳定性也会直接影响加工的准确性。
最后,操作人员的技术水平和操作规范也是造成加工误差的重要因素。
二、加工误差的类型加工误差可以表现为几何误差、尺寸误差和形位误差等多种类型。
几何误差是指在加工过程中由于切削力和热力等因素引起的材料形状和尺寸的偏差。
尺寸误差是指实际尺寸与设计尺寸之间的差异。
形位误差是指工件表面形态的误差,如平面度、圆度、垂直度等。
三、加工误差的影响加工误差对产品的影响主要体现在以下几个方面。
首先,加工误差会导致产品尺寸偏差,影响产品的装配性能和使用寿命。
其次,加工误差还会影响产品的运动精度和运行稳定性,降低产品的工作效率。
最后,加工误差还可能导致产品的严重故障和事故,对人身安全和财产造成巨大损失。
四、加工误差的分析方法针对机械制造工艺中的加工误差,可以采用多种方法进行分析和测试。
首先,可以利用三坐标测量机等设备对工件进行测量,得到具体的误差数据。
其次,可以利用数学统计学的方法对误差数据进行处理和分析,得到误差的分布规律和特点。
最后,可以利用有限元分析等计算机辅助工具对加工过程进行模拟和分析,找出加工误差的源头和优化方向。
五、加工误差的优化方法为了减少机械制造工艺中的加工误差,可以从材料、设备和操作等方面入手进行优化。
首先,可以选择具有较好材料均匀性的原材料,减少材料的内在应力。
其次,可以对设备进行精度检测和调整,确保设备的准确性和稳定性。
最后,可以对操作人员进行培训和规范,提高其技术水平和操作意识。
机械加工误差产生的原因及措施

机械加工误差产生的原因及措施汇报人:2024-01-01•机械加工误差产生的原因•减小机械加工误差的措施•机械加工误差的补偿措施目录•提高机械加工精度的途径01机械加工误差产生的原因原理误差总结词原理误差是由于加工原理的不完善而导致的误差。
详细描述原理误差主要表现在机床或刀具的转动和移动过程中,由于设计原理或机构原理的限制,导致加工出的零件与理论值存在偏差。
例如,齿轮加工中,由于齿轮的齿廓理论是完美的,但在实际加工中,由于机床和刀具的精度限制,无法完全复制理想的齿廓形状,从而产生原理误差。
工具、夹具与机床的制造误差总结词工具、夹具与机床的制造误差是由于这些设备的制造精度不足而导致的误差。
详细描述工具、夹具和机床是机械加工中的重要组成部分,它们的制造精度直接影响着零件的加工精度。
例如,刀具的制造误差会导致加工表面的粗糙度不均匀,夹具的定位精度不高会导致零件的位置精度偏差,机床的主轴回转误差则会影响零件的圆度等。
调整误差是由于加工过程中的调整不准确而导致的误差。
详细描述在机械加工过程中,需要对工具、夹具和机床进行多次调整,如刀具的更换、夹具的定位、机床的校准等。
由于调整过程中的人为操作和设备本身的特性,往往会产生一定的调整误差。
例如,刀具的安装角度偏差会影响切削深度和表面粗糙度,夹具的调整不当会导致零件的定位不准确。
总结词VS总结词测量误差是由于测量设备的精度限制和测量方法的不完善而导致的误差。
要点一要点二详细描述测量是机械加工中不可或缺的一环,但由于测量设备的精度限制和测量方法的不完善,往往会产生测量误差。
例如,使用卡尺测量时,由于卡尺的刻度精度有限,会导致测量结果存在误差;同时,测量方法的不正确也会导致误差的产生。
如测量时没有保证工件与卡尺之间的平行度或垂直度,就会产生测量误差。
02减小机械加工误差的措施直接减小或消除误差法直接减小或消除误差法是通过直接减少或消除原始误差来降低加工误差的方法。
例如,通过提高机床的几何精度、减小刀具和夹具的制造误差、提高工件的定位精度等措施,可以有效地减小加工误差。
机械加工工艺的技术误差问题及对策

机械加工工艺的技术误差问题及对策机械加工工艺的技术误差是指在加工过程中由于工艺、设备、操作等因素导致的加工尺寸与设计要求之间的偏差。
这些误差会对零件的质量和性能造成不利影响,因此需采取相应的对策来减小误差。
本文将从设备选型、工艺参数控制、工艺改进等方面探讨机械加工工艺的技术误差问题及对策。
一、设备选型方面的对策设备选型是机械加工工艺误差控制的重要方面。
在选购加工设备时,应确保设备的精度、稳定性、刚性等方面符合加工要求,以减小误差的产生。
1.选择精度更高的设备对于要求加工高精度零件的工艺,应选择精度更高的加工设备,如高精度数控机床等,以提高加工精度,并减小误差的产生。
2.选用稳定性较好的设备设备的稳定性对加工精度影响很大。
选用稳定性较好的设备可以减小外界因素(如温度、振动等)对加工精度的影响,降低误差的发生率。
3.考虑设备的刚性刚性是指设备在加工过程中承受载荷时变形程度的能力。
设备刚性好,能够更好地抵抗加工过程中的振动和变形,从而提高加工精度,降低误差的发生。
二、工艺参数控制方面的对策控制合理的工艺参数是减小机械加工工艺误差的关键,下面将从切削速度、进给量、切削深度等角度分析工艺参数的控制对策。
1.合理控制切削速度切削速度是指加工过程中工件与刀具相对运动的速度。
切削速度的选择要根据加工材料的硬度、材料的切削性能以及机床和刀具的性能等因素综合考虑。
如果切削速度过快,容易导致刀具寿命下降,加工表面质量下降,误差增大;而切削速度过慢,则不仅会影响生产效率,还容易产生负载过重等问题。
在实际加工过程中要根据具体情况调整切削速度,以确保加工精度。
三、工艺改进方面的对策工艺改进是减小机械加工工艺误差的重要手段。
通过改进现有的工艺流程、技术手段来减小误差的产生,提高加工精度。
1.优化工艺流程通过优化加工工艺流程,合理安排加工顺序,避免二次调整导致误差的累积。
合理的工艺流程有助于提高加工效率,降低误差的发生率。
2.改进工艺技术手段利用先进的数控技术、自动化技术以及传感技术等,改进加工工艺技术手段,提高机床的加工精度,减小误差的产生。
机械加工工艺技术的误差分析及策略探讨

116M achining and Application机械加工与应用机械加工工艺技术的误差分析及策略探讨于东义(凤城市职业教育中心,辽宁 丹东 118100)摘 要:随着我国经济的不断发展,为科学技术的进步奠定了良好的基础,而且工业生产也正在向机械化生产方面转变,在此背景下形成了完善的机械生产流程,以此提高了机械生产效率,从根本上促进了我国机械行业的全面发展。
但是,由于我国机械加工工艺技术还处在正在发展的阶段,其应用到机械工业生产过程中时肯定还存在着一些问题,这样一来也是在很大程度上影响到了我国机械工业的发展。
基于这种现状,机械加工工艺技术的误差问题必须引起高度重视,为了提高加工质量,确保零件的使用性能,本文从实践中总结经验,不断改善机械加工技术,完善机械加工工艺体系,来确立误差的种类,并深入分析改善机械加工工艺技术误差控制策略,以此提高机械加工行业的发展水平。
关键词:机械行业;加工工艺技术;误差;策略中图分类号:TH16 文献标识码:A 文章编号:11-5004(2021)12-0116-2收稿日期:2021-06作者简介:于东义,男,生于 1969年,满族,辽宁凤城人,本科,车工一级实习指导教师,研究方向:机械加工工艺技术。
工业行业中机械加工工艺主要是指按照设计图纸,并采用机械加工的方法,改变毛坯的形状、尺寸和表面质量等,使其成为零件的过程。
机械加工工艺的每一个环节都会关系到零件的质量,若是某一工艺流程出现了问题,则会影响零件的使用性能,导致成为废品。
因此为了保证零件的质量,需要采取有效的措施和方法,从根本上提高机械加工工艺技术,进而减少零件发生误差问题,全面优化机械加工工艺流程。
1 机械加工工艺技术的概述从一般情况下看,机械加工工艺技术水平的高低会在很大程度上影响着机械加工的质量,在实际的机械加工过程中,除了要重视机械加工工艺技术的实施,更需要重视产品的规格和数量,也需要整合实际的工艺实施情况,在工业实施过程中配备好工艺设备和施工人才。
机械加工工艺技术的误差分析及策略分析

机械加工工艺技术的误差分析及策略分析摘要:随着中国经济的高速发展,机械产品逐渐走入社会公众的日常生产生活,其产品种类以及制作工艺都得到了极大地提升。
在此背景下,机械产品的加工工艺技术也随之发展,由于不同产品所需要的零部件型号以及类型不同,因此机械产品及其零部件的加工势必要经过多重工序,应用不同的机械加工工艺。
该文从机械加工工艺技术的误差分析出发,对目前机械加工工艺技术的误差分析进行简要论述,并对如何解决机械加工工艺技术误差进行分析研究。
关键词:机械加工;误差分析引言基于社会公众对精密度高、产品质量高的机械产品的需求,该文从机械加工工艺技术的误差分析出发,对目前机械加工工艺技术的误差分析进行简要论述,并对如何解决机械加工工艺技术误差进行分析研究。
1.机械加工基本原理首先对基准面进行处理,然后再对基准面进行进一步的处理工作,可以称之为基准面处理。
第二,先孔后面。
对于连杆、箱体在加工工艺层,应注意嵌入这一原则,以保证孔和平闸门的精度,进而便于后续操作[3]。
再次,结合不同设备的不同加工要求,在粗加工过程中,对产品精度的实际要求相对较小。
因此,必须选择精度低、功率大的机床。
精加工时对产品的整体精度要求较高。
因此,必须尝试选择高精度的机器。
2.机械加工工艺技术的误差分析2.1定位误差执行加工过程中,使用加工技术,定位是指工件的固定以及机床的加工,使工件与刀具紧密结合,以保证定位精度。
提高整体定位精度,保证加工生产效率[5]。
定位误差主要表现为基准点不重合和定位副产品不精确。
首先是工件几何元素的选择,反映了定位精度。
后者用于定位元件和二次定位制造没有体现精度。
2.2机床制造产生的误差机床误差主要包括传动链误差、回转误差、导轨误差等,回转误差主要在机床轴线上,在不同的情况下,通过所研究的回转轴线回转。
由此产生的误差将对加工或加工全精密机械产品产生严重的不良影响,同轴电缆轴承、60°同轴电缆内衬生产的主要机械因素,通过传动链,可以传递机床运行所需的能量。
机械加工工艺的技术误差问题及对策分析

机械加工工艺的技术误差问题及对策分析一、引言机械加工工艺是制造行业中非常重要的一环,其质量直接影响到产品的性能和质量。
在机械加工过程中难免会出现技术误差,导致产品不符合设计要求,甚至影响到产品的使用效果。
对于机械加工工艺中的技术误差问题需要进行深入的分析,并提出相应的对策,以保证产品质量和生产效率。
二、机械加工工艺中的技术误差问题在机械加工过程中,技术误差是不可避免的。
技术误差主要包括以下几个方面:1. 设备精度误差机械加工设备的精度直接影响到产品加工的精度。
如果设备本身存在精度误差,那么加工出的产品也会存在相应的误差。
数控机床的定位精度、刀具的磨损、传动件的松动等都会导致产品加工精度下降。
2. 刀具磨损在机械加工中,刀具是直接与工件接触的工具,其磨损会直接影响到产品的加工精度。
如果刀具磨损严重,就会导致产品表面粗糙、尺寸偏差等问题。
3. 工序误差机械加工通常是由多道工序组成的,每个工序都会对产品加工精度产生影响。
如果某个工序出现误差,就会传导到整个加工过程中,导致产品精度下降。
4. 材料性能误差在机械加工中,材料的硬度、韧性、延展性等性能会直接影响到产品的加工精度。
如果材料性能不稳定,就会导致产品加工精度难以保证。
以上这些技术误差问题都会影响到产品的加工精度和质量,甚至导致产品无法使用。
对于这些技术误差问题需要有针对性地进行分析,并提出相应的对策分析。
三、对策分析针对机械加工工艺中的技术误差问题,可以采取以下对策进行解决:1. 提高设备精度首先要解决的是设备精度误差问题。
可以通过定期对设备进行维护和保养,及时更换损坏的零部件,来保证设备的精度。
现代化的数控机床可以通过自动补偿来修正设备误差,提高加工精度。
2. 优化刀具管理刀具的磨损是导致产品加工精度下降的重要原因之一。
可以通过建立刀具管理制度,定期检查刀具的磨损情况,及时更换磨损严重的刀具,以保证产品加工精度。
3. 加强工序管理针对工序误差问题,可以通过加强工序管理来减少误差的传导。
机械加工精度的误差分析与优化

机械加工精度的误差分析与优化机械加工在现代制造业中占据着重要地位,而加工精度的误差成为了制约产品质量和性能的重要因素。
因此,对机械加工精度的误差进行分析与优化显得尤为重要。
本文将从误差的来源、误差分析的方法以及优化策略等方面进行论述。
一、误差的来源机械加工的误差来源主要包括设备误差、刀具误差、加工工艺误差以及材料误差等多个方面。
设备误差是指机床、夹具、测量装置等在设计、制造、装配等过程中产生的误差。
例如,机床的动力系统、传动系统、控制系统等都会引起误差,而夹具的刚度、精度也会对加工精度产生影响。
刀具误差是指刀具在制造、磨削、使用过程中产生的误差。
刀具的材质、几何形状、刃口磨削质量等都会对加工精度造成一定的影响。
加工工艺误差是指加工过程中由于操作不当、设备调试不当等原因引起的误差。
例如,切割速度、进给速度、径向切宽等参数的选择和调整不当,都可能导致加工误差的增加。
材料误差是指工件的形状、尺寸、物理性能等方面的误差。
材料的不均匀性、热膨胀系数、热导率等特性都会对加工误差产生一定的影响。
二、误差分析的方法误差分析是指通过对机械加工误差的定位、测量、分析等手段,揭示误差产生的原因和机理,以便进行误差补偿和改进的过程。
常用的误差分析方法包括测量法、数学模型法和统计分析法等。
测量法是通过使用测量仪器对加工件进行测量,获取几何形状和尺寸方面的数据,然后与设计要求进行比较,从而得出误差的大小和方向。
测量法可以通过直接测量、间接测量以及三坐标测量等方式进行。
数学模型法是通过建立机床、夹具、刀具、工艺等的数学模型,通过计算和仿真等手段,预测和分析误差的产生和传递路径。
数学模型法可以通过有限元法、多体系统理论等进行。
统计分析法是通过对多个加工件加工数据的收集和分析,利用统计学方法对误差进行分析和判别。
统计分析法可以通过卡尔曼滤波、方差分析等进行。
三、优化策略根据误差分析的结果,我们可以采取一系列的优化策略来降低机械加工精度误差。
机械加工工艺技术误差及改进分析

机械加工工艺技术误差及改进分析谢良雄湖南省涟源市工贸职业中等专业学校 湖南娄底 417100摘要:为了有效改进机械加工过程中存在的误差问题,研究以某个零件加工案例为对象,对机械加工技术加工过程中存在的问题展开研究分析,深入探讨了机械加工技术的误差以及改进方法。
先对零件加工过程中存在的变形问题、残余盈利以及磨削刚性误差以及装夹不合理等问题展开研究,从机械加工机床精度、刀具刃口以及工件装夹方法等方面为切入点,详细对机械加工工艺技术的误差展开探究,并提出了相应的改进方法。
最后,经验证结果证明,改进后的机械加工工艺具有良好的效果,不仅能够有效提高加工的精度和效率,还能够为相关工作提供参考。
关键词:机械制造 加工工艺技术 误差分析 改进方法中图分类号:TH16文献标识码:A 文章编号:1672-3791(2024)03-0089-03Analysis of Errors and Improvements of Machining ProcessTechnologyXIE LiangxiongLianyuan Industry and Trade Vocational Secondary School, Loudi, Hunan Province, 417100 China Abstract:In order to effectively improve the error problem in the machining process, this study takes a certain part processing case as the object, studies and analyzes the problems of machining technology in the machining process, and deeply explores the errors and improvement methods of machining technology. Firstly, this paper studies the problems of deformation, residual stress, grinding rigidity errors and unreasonable clamping during the machining process of parts. Then, it takes the accuracy of machining machines, the cutting edge of tools and the clamping methods of workpieces as starting points, explores the error of machining process technology in detail, and proposes corresponding improvement methods. Finally, the verified results have shown that the improved machining process technology has good effects, which can not only effectively improve the accuracy and efficiency of machining, but also provide reference for related work.Key Words: Mechanical manufacturing; Process technology; Error analysis; Improvement method制造领域中机械加工工艺技术具有不可替代的作用,而加工精度作为机械加工的重要指标,在加工过程中如何有效降低加工误差,合理对机械加工精度进行控制,是提高机械加工工艺技术质量的一个重要问题。
机械加工工艺的技术误差问题及对策分析
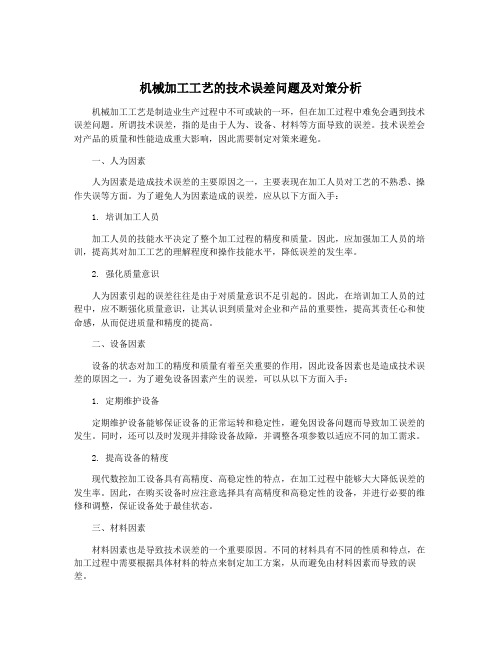
机械加工工艺的技术误差问题及对策分析机械加工工艺是制造业生产过程中不可或缺的一环,但在加工过程中难免会遇到技术误差问题。
所谓技术误差,指的是由于人为、设备、材料等方面导致的误差。
技术误差会对产品的质量和性能造成重大影响,因此需要制定对策来避免。
一、人为因素人为因素是造成技术误差的主要原因之一,主要表现在加工人员对工艺的不熟悉、操作失误等方面。
为了避免人为因素造成的误差,应从以下方面入手:1. 培训加工人员加工人员的技能水平决定了整个加工过程的精度和质量。
因此,应加强加工人员的培训,提高其对加工工艺的理解程度和操作技能水平,降低误差的发生率。
2. 强化质量意识人为因素引起的误差往往是由于对质量意识不足引起的。
因此,在培训加工人员的过程中,应不断强化质量意识,让其认识到质量对企业和产品的重要性,提高其责任心和使命感,从而促进质量和精度的提高。
二、设备因素设备的状态对加工的精度和质量有着至关重要的作用,因此设备因素也是造成技术误差的原因之一。
为了避免设备因素产生的误差,可以从以下方面入手:1. 定期维护设备定期维护设备能够保证设备的正常运转和稳定性,避免因设备问题而导致加工误差的发生。
同时,还可以及时发现并排除设备故障,并调整各项参数以适应不同的加工需求。
2. 提高设备的精度现代数控加工设备具有高精度、高稳定性的特点,在加工过程中能够大大降低误差的发生率。
因此,在购买设备时应注意选择具有高精度和高稳定性的设备,并进行必要的维修和调整,保证设备处于最佳状态。
三、材料因素材料因素也是导致技术误差的一个重要原因。
不同的材料具有不同的性质和特点,在加工过程中需要根据具体材料的特点来制定加工方案,从而避免由材料因素而导致的误差。
1. 调整加工方案不同材料在加工过程中需要采取不同的加工方案。
因此,在加工前应充分了解材料的性质和特点,制定适合材料特点的加工方案,从而提高加工的精度和质量。
2. 选择优质材料优质的材料能够在加工过程中更好地保证产品质量和精度。
机械加工工艺技术误差分析及对装配质量的影响

机械加工工艺技术误差分析及对装配质量的影响发布时间:2022-08-17T08:29:58.619Z 来源:《福光技术》2022年17期作者:邓海博[导读] 时代在变化,人民的生活质量是不断提升的状态,人民对于产品的质量也是愈发重视,与机械加工工艺技术如果出现误差,必然会对产品加工精度、生产质量等方面造成影响,甚至对企业健康、有序发展带来不利影响。
误差是由多方面因素导致的,彻底消除是一件非常困难的事情,需要应用科学方法与手段有效减少误差。
一重集团(黑龙江)重工有限公司黑龙江齐齐哈尔 161000摘要:时代在变化,人民的生活质量是不断提升的状态,人民对于产品的质量也是愈发重视,与机械加工工艺技术如果出现误差,必然会对产品加工精度、生产质量等方面造成影响,甚至对企业健康、有序发展带来不利影响。
误差是由多方面因素导致的,彻底消除是一件非常困难的事情,需要应用科学方法与手段有效减少误差。
相关单位与工作人员一定要对误差加强关注与重视,并且通过应用相关的机械加工工艺技术流程,制定完善的误差控制方法,有效延长机械使用时间,为保证产品质量打下良好的基础。
本文对机械加工工艺技术误差分析及对装配质量的影响进行探究,以供参考。
关键词:机械加工;工艺技术;误差分析;装配质量引言:就机械产品的所有性能来说,耐久性与可靠性主要是由机械加工工艺技术决定的。
所以,要想精准地把握机械加工过程中加工工艺对产品质量的影响规律,那么,就需要对机械加工误差出现的原因、加工过程中需要遵循的原则以及如何使得加工精度得到有效提高等层面展开深入研究。
如此一来,还可以应用这些相关规律来实现对加工过程的有效控制,为产品性能的提高提供基础保障。
1 机械加工工艺技术影响机械加工水平的主要因素多在于机械加工工艺技术的发展水平。
为确保零部件具有相应的精度,需要根据实际要求制定相应的工艺规范。
由于不同生产车间对零部件的规格及精度有不同要求,因而在零部件的具体加工过程中存在一定差别。
机械装配过程中的装配误差分析与优化

机械装配过程中的装配误差分析与优化引言:机械装配是制造业中常见的生产过程,其质量直接影响产品的性能和寿命。
然而,在机械装配过程中,难免会存在装配误差,这些误差有时会导致装配件无法完全匹配,影响装配的精度和效果。
因此,对机械装配过程中的装配误差进行分析与优化,是提高装配质量的重要措施。
1. 装配误差的产生原因1.1 零件加工误差在机械制造过程中,零件的加工误差是装配误差产生的主要原因之一。
由于加工设备、刀具磨损、操作技术等方面的限制,会导致零件的尺寸、形状和位置产生一定的偏差,从而影响装配的精度。
1.2 装配工艺控制不当在机械装配过程中,工艺控制不当也是装配误差产生的重要原因。
例如,装配工人的技术水平、工艺规范执行情况、装配过程中的操作失误等都可能导致装配误差的产生。
1.3 温度变化温度的变化也会对机械装配产生一定的影响。
由于温度膨胀系数不同,当零件在不同温度条件下进行装配时,会导致装配件的尺寸发生变化,从而产生装配误差。
2. 装配误差的分析方法2.1 设计分析法设计分析法是通过对设计图纸和工艺流程进行仔细分析,找出可能存在的装配误差及其原因。
通过对装配零件的尺寸、形状和位置进行比对,确定装配误差的来源,为优化装配过程提供依据。
2.2 几何测量法几何测量法是通过使用各类几何测量仪器,对装配件的尺寸和形状进行测量并分析。
例如,利用光学测量仪器、三坐标测量仪等,可以测量装配零件的直径、长度、平行度、垂直度等参数,从而得到装配误差的具体数值。
2.3 数值模拟方法数值模拟方法是通过计算机辅助工程软件,建立装配过程的数学模型,通过仿真计算来分析装配误差和其对产品性能的影响。
通过多次优化设计,可以确定减小误差的方法和方案。
3. 优化装配过程的方法3.1 加强质量控制在装配过程中,加强质量控制是提高装配质量的关键。
通过建立严格的工艺规范和操作流程,制定相应的质量检验标准,以确保每个环节的装配误差得到精确控制。
同时,进行质量培训,提高装配工人的技术水平和操作规范。
机械加工误差分析以及解决措施

机械加工误差分析以及解决措施摘要:在机械加工中,工件上某一尺寸的加工误差,可能是由多项系统误差和多项随机误差共同作用的综合结果。
由于在加工每一尺寸时,作用在其上的偶然因素的组合都不一样,因此,即使是同一设备、同一操作工人加工出的同一批工件,其实际尺寸也是变化的,这就是尺寸分散现象。
一批工件的尺寸分散范围若在公差范围之内,则合格;反之,若尺寸分散范围超出公差范围,则超出的部分工件为不合格品。
本文主要针对机械加工误差分析以及解决措施进行简要分析。
关键词:机械加工;误差;解决措施1机械加工精度及误差的含义所谓机械加工精度,指的是机械产品在进行机械加工之后,其实际的几何参数与图纸中所规定的数值的符合程度,符合程度越大,则证明机械加工精度越高,反之,则证明机械加工精度较低,加工后机械产品的实际几何参数与图纸中规定的数值之间的差值,就是机械加工误差,加工误差越小,说明机械产品的质量越好,加工误差永恒存在,不可消除,但如何控制加工误差,是一个亟待解决的问题。
2机械加工精度的具体内容机械加工精度主要包括三方面内容,分别是尺寸精度、几何形状精度以及相互位置精度,衡量机械加工精度的高低,要从这三方面人手。
尺寸精指的就是机械产品零件的实际尺寸与图纸中所标注的尺寸的符合程度。
几何形状精度指的是机械产品零件表面实际的宏观形状与图纸中所绘制的宏观形状的符合程度。
相互位置精度指的则是机械零件与基准之间的相互位置与图纸中所要求的相互位置的符合程度。
3机械加工误差产生的原因3.1原理误差在加工的过程中没办法采用理想的加工运动方式而采用了近似的加工运动方式,由此产生的加工误差称为原理误差。
从实际的情况考虑,如果采用理论中的加工原理对工件进行加工,那么就需要十分复杂的加工机构来实现这一目标,这会造成资源的极大浪费。
机械加工企业只需要将加工件的误差控制在一定范围内,能够满足功能需求即可,并不需要提高成本来彻底消除误差。
因此,在实际加工中原始误差是一定会存在的,这就会给加工件的加工精度带来影响。
- 1、下载文档前请自行甄别文档内容的完整性,平台不提供额外的编辑、内容补充、找答案等附加服务。
- 2、"仅部分预览"的文档,不可在线预览部分如存在完整性等问题,可反馈申请退款(可完整预览的文档不适用该条件!)。
- 3、如文档侵犯您的权益,请联系客服反馈,我们会尽快为您处理(人工客服工作时间:9:00-18:30)。
机械加工工艺技术误差分析与控制
机械加工工艺技术是制造业的一项基础技术,其精度与质量直接影响着产品的性能和使用寿命。
然而,在机械加工过程中,由于各种原因,往往会产生一些误差,影响加工结果的精度和质量。
因此,针对机械加工过程中出现的误差,进行误差分析和控制,是提高加工精度和质量的关键。
误差来源
机械加工过程中,误差来源很多,主要包括以下几种:
1.工艺系统误差:是由于各种加工设备和工艺参数的不同,导致加工结果的差异。
这种误差很难排除,只能通过不断提高加工设备的精度和稳定性来减小。
2.装夹误差:是由于工件在加工过程中固定不牢造成的误差。
对于铣削等加工过程中需要多次拆卸、装夹的情况,这种误差尤为明显。
3.刀具误差:是由于刀具的磨损或形状不正确导致的误差。
这种误差可以通过及时更换刀具或校正刀具形状来减小。
4.测量误差:是由于测量仪器本身误差或使用不当导致的误差。
解决这种误差需要科学选用合适的测量仪器,并且在使用过程中要注意正确操作。
误差控制方法
误差控制是指通过一系列方法,减小或最小化机械加工过程中产生的误差,提高加工精度和质量。
常用的误差控制方法包括以下几种:
1.工艺规范化:制订合理的工艺方案和技术标准,明确加工过程中各个环节的要求和限制。
这样可以使得整个加工过程更加可控,减少误差。
2.质量控制:对于每一个工件,都要进行严格的质量检验和控制。
避免出现低质量的产品混入市场。
3.自动化控制:使用先进的自动化控制技术,可以减少人为因素的干扰和误差。
从而提高加工精度和稳定性。
4.人机交互:通过合理的界面设计和操作方式,使得人机交互更加准确、清晰。
这样可以有效减少人为因素带来的误差。
1.试验法:通过对机械加工过程进行模拟试验,测量误差大小和分布规律,来确定误差来源和解决方法。
2.观察法:对机械加工过程进行全程观察,发现并记录误差产生的环节和原因,然后
针对性地进行调整和改进。
综上所述,机械加工工艺技术误差分析与控制是提高加工精度和质量的关键技术之一。
只有通过有效的误差分析和控制方法,才能准确地发现误差的来源,从而采取针对性的措
施进行改进和提高。