铆焊车间实习报告
铆焊车间实习总结
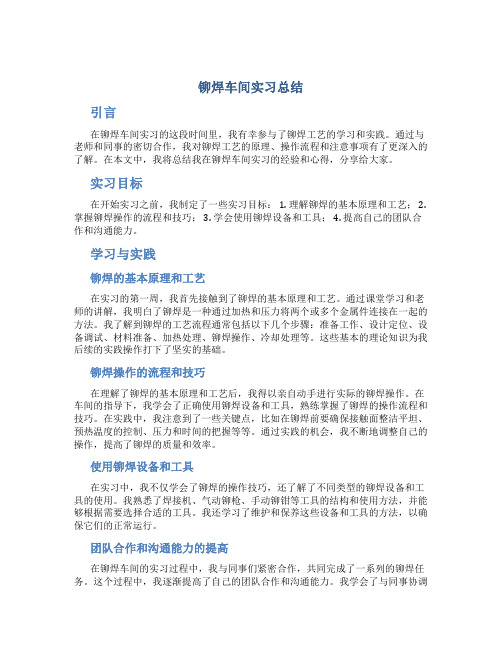
铆焊车间实习总结引言在铆焊车间实习的这段时间里,我有幸参与了铆焊工艺的学习和实践。
通过与老师和同事的密切合作,我对铆焊工艺的原理、操作流程和注意事项有了更深入的了解。
在本文中,我将总结我在铆焊车间实习的经验和心得,分享给大家。
实习目标在开始实习之前,我制定了一些实习目标: 1. 理解铆焊的基本原理和工艺; 2. 掌握铆焊操作的流程和技巧; 3. 学会使用铆焊设备和工具; 4. 提高自己的团队合作和沟通能力。
学习与实践铆焊的基本原理和工艺在实习的第一周,我首先接触到了铆焊的基本原理和工艺。
通过课堂学习和老师的讲解,我明白了铆焊是一种通过加热和压力将两个或多个金属件连接在一起的方法。
我了解到铆焊的工艺流程通常包括以下几个步骤:准备工作、设计定位、设备调试、材料准备、加热处理、铆焊操作、冷却处理等。
这些基本的理论知识为我后续的实践操作打下了坚实的基础。
铆焊操作的流程和技巧在理解了铆焊的基本原理和工艺后,我得以亲自动手进行实际的铆焊操作。
在车间的指导下,我学会了正确使用铆焊设备和工具,熟练掌握了铆焊的操作流程和技巧。
在实践中,我注意到了一些关键点,比如在铆焊前要确保接触面整洁平坦、预热温度的控制、压力和时间的把握等等。
通过实践的机会,我不断地调整自己的操作,提高了铆焊的质量和效率。
使用铆焊设备和工具在实习中,我不仅学会了铆焊的操作技巧,还了解了不同类型的铆焊设备和工具的使用。
我熟悉了焊接机、气动铆枪、手动铆钳等工具的结构和使用方法,并能够根据需要选择合适的工具。
我还学习了维护和保养这些设备和工具的方法,以确保它们的正常运行。
团队合作和沟通能力的提高在铆焊车间的实习过程中,我与同事们紧密合作,共同完成了一系列的铆焊任务。
这个过程中,我逐渐提高了自己的团队合作和沟通能力。
我学会了与同事协调工作,分工合作,及时沟通,以提高工作效率和质量。
同时,我也通过与同事们的交流,吸取了不少宝贵的经验和教训,进一步提升了自己的铆焊技能。
铆工实习报告
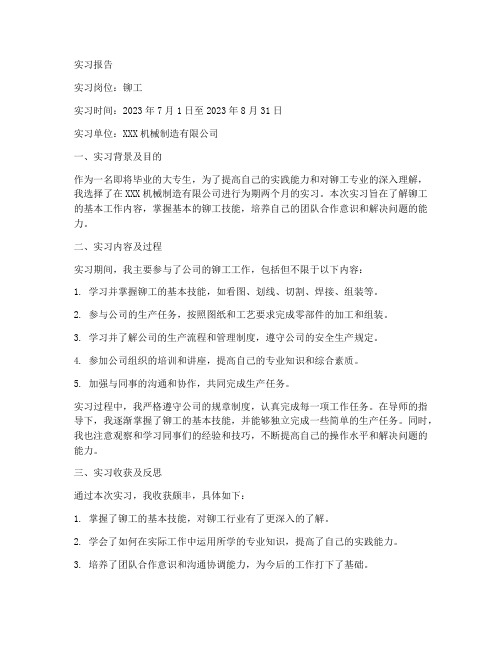
实习报告实习岗位:铆工实习时间:2023年7月1日至2023年8月31日实习单位:XXX机械制造有限公司一、实习背景及目的作为一名即将毕业的大专生,为了提高自己的实践能力和对铆工专业的深入理解,我选择了在XXX机械制造有限公司进行为期两个月的实习。
本次实习旨在了解铆工的基本工作内容,掌握基本的铆工技能,培养自己的团队合作意识和解决问题的能力。
二、实习内容及过程实习期间,我主要参与了公司的铆工工作,包括但不限于以下内容:1. 学习并掌握铆工的基本技能,如看图、划线、切割、焊接、组装等。
2. 参与公司的生产任务,按照图纸和工艺要求完成零部件的加工和组装。
3. 学习并了解公司的生产流程和管理制度,遵守公司的安全生产规定。
4. 参加公司组织的培训和讲座,提高自己的专业知识和综合素质。
5. 加强与同事的沟通和协作,共同完成生产任务。
实习过程中,我严格遵守公司的规章制度,认真完成每一项工作任务。
在导师的指导下,我逐渐掌握了铆工的基本技能,并能够独立完成一些简单的生产任务。
同时,我也注意观察和学习同事们的经验和技巧,不断提高自己的操作水平和解决问题的能力。
三、实习收获及反思通过本次实习,我收获颇丰,具体如下:1. 掌握了铆工的基本技能,对铆工行业有了更深入的了解。
2. 学会了如何在实际工作中运用所学的专业知识,提高了自己的实践能力。
3. 培养了团队合作意识和沟通协调能力,为今后的工作打下了基础。
4. 增强了自己的安全生产意识,熟悉了企业的生产流程和管理制度。
然而,在实习过程中,我也发现了自己的一些不足之处,如在实际操作中,有时会出现紧张、慌乱的情况,影响操作的准确性;在团队合作中,有时沟通不畅,导致工作效率降低。
针对这些问题,我将在今后的学习和工作中,不断提高自己的心理素质和沟通能力,努力提升自己的综合能力。
四、实习总结通过本次实习,我对铆工专业有了更深入的了解,收获了许多宝贵的实践经验。
同时,也认识到了自己的不足,明确了今后的发展方向。
关于铆焊的实习报告
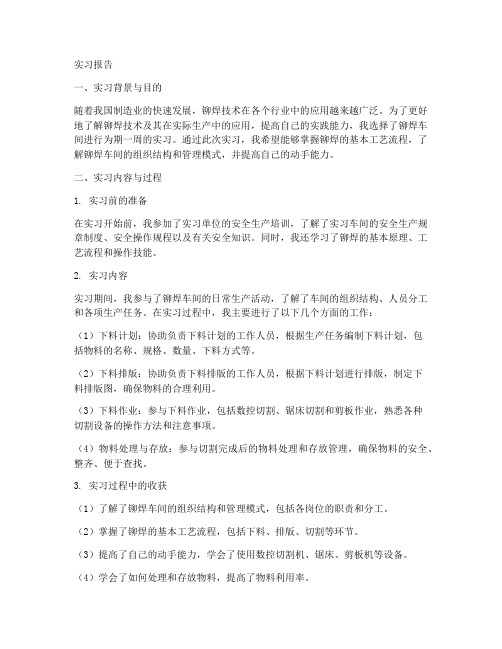
实习报告一、实习背景与目的随着我国制造业的快速发展,铆焊技术在各个行业中的应用越来越广泛。
为了更好地了解铆焊技术及其在实际生产中的应用,提高自己的实践能力,我选择了铆焊车间进行为期一周的实习。
通过此次实习,我希望能够掌握铆焊的基本工艺流程,了解铆焊车间的组织结构和管理模式,并提高自己的动手能力。
二、实习内容与过程1. 实习前的准备在实习开始前,我参加了实习单位的安全生产培训,了解了实习车间的安全生产规章制度、安全操作规程以及有关安全知识。
同时,我还学习了铆焊的基本原理、工艺流程和操作技能。
2. 实习内容实习期间,我参与了铆焊车间的日常生产活动,了解了车间的组织结构、人员分工和各项生产任务。
在实习过程中,我主要进行了以下几个方面的工作:(1)下料计划:协助负责下料计划的工作人员,根据生产任务编制下料计划,包括物料的名称、规格、数量、下料方式等。
(2)下料排版:协助负责下料排版的工作人员,根据下料计划进行排版,制定下料排版图,确保物料的合理利用。
(3)下料作业:参与下料作业,包括数控切割、锯床切割和剪板作业,熟悉各种切割设备的操作方法和注意事项。
(4)物料处理与存放:参与切割完成后的物料处理和存放管理,确保物料的安全、整齐、便于查找。
3. 实习过程中的收获(1)了解了铆焊车间的组织结构和管理模式,包括各岗位的职责和分工。
(2)掌握了铆焊的基本工艺流程,包括下料、排版、切割等环节。
(3)提高了自己的动手能力,学会了使用数控切割机、锯床、剪板机等设备。
(4)学会了如何处理和存放物料,提高了物料利用率。
三、实习总结与展望通过一周的实习,我对铆焊技术有了更深入的了解,收获颇丰。
在实习过程中,我认识到了实践的重要性,理论联系实际,才能更好地掌握知识点。
同时,我也意识到自己在铆焊技术方面的不足,需要继续学习和提高。
展望未来,我将继续深入学习铆焊技术,提高自己的专业素养。
在实际工作中,充分发挥自己的优势,为我国制造业的发展贡献自己的力量。
机械铆焊及加工实训报告
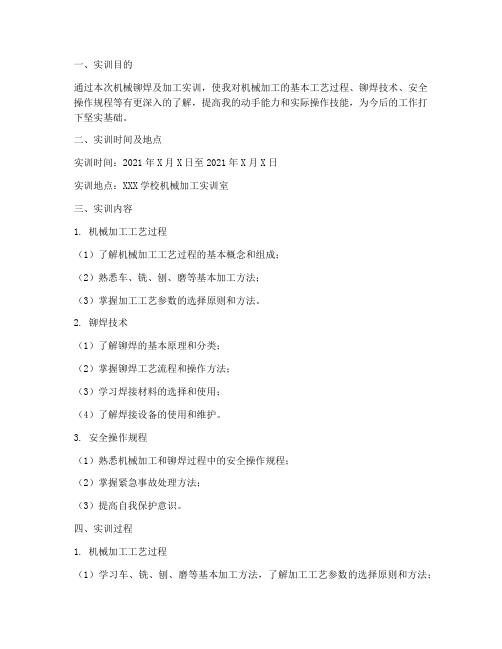
一、实训目的通过本次机械铆焊及加工实训,使我对机械加工的基本工艺过程、铆焊技术、安全操作规程等有更深入的了解,提高我的动手能力和实际操作技能,为今后的工作打下坚实基础。
二、实训时间及地点实训时间:2021年X月X日至2021年X月X日实训地点:XXX学校机械加工实训室三、实训内容1. 机械加工工艺过程(1)了解机械加工工艺过程的基本概念和组成;(2)熟悉车、铣、刨、磨等基本加工方法;(3)掌握加工工艺参数的选择原则和方法。
2. 铆焊技术(1)了解铆焊的基本原理和分类;(2)掌握铆焊工艺流程和操作方法;(3)学习焊接材料的选择和使用;(4)了解焊接设备的使用和维护。
3. 安全操作规程(1)熟悉机械加工和铆焊过程中的安全操作规程;(2)掌握紧急事故处理方法;(3)提高自我保护意识。
四、实训过程1. 机械加工工艺过程(1)学习车、铣、刨、磨等基本加工方法,了解加工工艺参数的选择原则和方法;(2)通过实际操作,掌握加工过程中的注意事项,提高加工质量;(3)完成规定数量的零件加工任务。
2. 铆焊技术(1)学习铆焊的基本原理和分类,了解焊接材料的选择和使用;(2)通过实际操作,掌握铆焊工艺流程和操作方法;(3)完成规定数量的焊接任务。
3. 安全操作规程(1)学习机械加工和铆焊过程中的安全操作规程;(2)通过模拟演练,掌握紧急事故处理方法;(3)提高自我保护意识。
五、实训成果1. 熟悉了机械加工的基本工艺过程和铆焊技术;2. 掌握了加工工艺参数的选择原则和方法;3. 提高了动手能力和实际操作技能;4. 增强了安全意识,提高了紧急事故处理能力。
六、实训体会1. 机械加工和铆焊技术是制造业的基础,掌握这些技术对于今后的工作具有重要意义;2. 实训过程中,要注重理论联系实际,提高自己的动手能力和实际操作技能;3. 安全操作规程是保证人身安全的重要措施,要时刻牢记在心;4. 通过本次实训,我深刻体会到团队合作的重要性,只有团结协作,才能完成高质量的实训任务。
铆工车间实习报告

实习报告实习岗位:铆工车间实习生实习时间:2021年6月1日至2021年8月31日实习单位:XX钢铁制造有限公司一、实习背景及目的作为一名机械工程专业的学生,为了将理论知识与实际生产相结合,提高自己的实践能力和职业技能,我选择了铆工车间作为实习岗位。
本次实习旨在了解铆工车间的生产流程、工艺技术,学习金属制品的制作方法,掌握焊接、铆接、螺栓连接等加工方法,培养自己的团队合作精神和劳动纪律意识。
二、实习内容与过程1. 实习前期,我在导师的指导下,学习了铆工的基本知识,包括识图和制图、金属材料及热处理、矫正变形较大或复合变形的原材料及一般结构件等。
同时,我还学会了使用维护剪床、气割、电焊机等设备。
2. 实习期间,我参与了车间内的生产任务,主要包括以下几个环节:(1)放样:根据图纸要求,将零部件的形状、尺寸、位置等参数标注在原材料上。
(2)号料:根据放样结果,对原材料进行切割、打孔等加工处理。
(3)下料:使用剪床、切割机等设备将号料后的原材料切割成所需形状和尺寸。
(4)成型:通过加热、弯曲、压制等方法,使原材料形成所需形状。
(5)制作:将成型后的零部件进行组装、焊接、铆接、螺纹连接等加工,制作成完整的金属制品。
(6)校正:对制作过程中的误差进行调整,确保零部件的尺寸、形状、位置等满足图纸要求。
(7)安装:将制作好的金属制品安装到指定的位置,进行下一步的组装或调试。
3. 实习期间,我还参与了车间的日常管理工作,学习了生产计划编制、生产进度跟踪、质量控制等方面的知识。
三、实习收获与反思1. 技能方面:通过实习,我掌握了铆工的基本技能,包括识图和制图、金属材料及热处理、矫正变形较大或复合变形的原材料及一般结构件等。
同时,我的实际操作能力、动手能力得到了很大提高。
2. 团队协作:在实习过程中,我充分体验到了团队合作的重要性。
与同事们一起解决问题、完成任务,使我更加明白了团队协作的意义。
3. 劳动纪律:实习期间,我严格遵守车间的各项规章制度和劳动纪律,培养了良好的职业道德和职业素质。
铆工的实习报告

为了更好地了解铆工这一职业,提升自己的专业技能,我于2023年7月至9月在XX公司进行了为期两个月的铆工实习。
XX公司是一家专业从事钢结构设计、制造和安装的企业,具有丰富的行业经验和技术实力。
通过这次实习,我对铆工工作有了更加深刻的认识,为今后的职业生涯奠定了基础。
二、实习内容实习期间,我主要参与了以下工作:1. 识图与制图:学习了如何读懂铆接图样,掌握了放样、号料、下料、成型等基本工艺流程,并能够根据图纸进行制图。
2. 金属材料的选用与加工:了解了常用金属材料的种类、性能和选用原则,掌握了板材、型材、线材、管材等金属材料的加工方法。
3. 铆接技术:学习了铆接的基本原理、工具和设备的使用方法,掌握了全位置定位焊、铆接、螺纹连接等技术。
4. 矫正与成形:掌握了矫正变形较大或复合变形的原材料及一般结构件的方法,能够制作成基本形体的展开图,计算展开料长。
5. 设备操作与维护:熟悉了剪床、气割、电焊机等设备的使用方法,并学会了设备的基本维护和保养。
6. 现场施工与安全管理:参与了现场施工,了解了施工流程和安全规范,掌握了现场施工的基本技能。
三、实习收获1. 专业技能的提升:通过实习,我掌握了铆工的基本技能,包括识图、制图、金属材料的加工、铆接技术、矫正与成形、设备操作与维护等。
2. 实践经验积累:在实习过程中,我亲身参与了现场施工,积累了宝贵的实践经验,为今后的工作打下了基础。
3. 团队协作能力:在实习过程中,我与同事们共同完成了各项任务,学会了团队协作,提高了沟通能力。
4. 职业道德修养:在实习过程中,我严格遵守公司规章制度,认真完成工作任务,培养了良好的职业道德。
1. 理论与实践相结合:实习让我深刻体会到,理论知识是基础,但只有将理论知识与实际操作相结合,才能真正掌握一门技能。
2. 实践是检验真理的唯一标准:在实习过程中,我遇到了许多实际问题,通过不断尝试和摸索,找到了解决问题的方法,使我更加坚信实践是检验真理的唯一标准。
铆焊车间实习报告
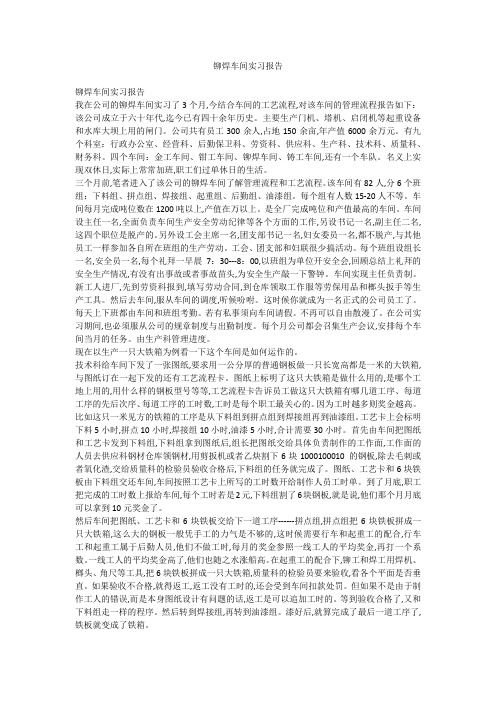
铆焊车间实习报告铆焊车间实习报告我在公司的铆焊车间实习了3个月,今结合车间的工艺流程,对该车间的管理流程报告如下:该公司成立于六十年代,迄今已有四十余年历史。
主要生产门机、塔机、启闭机等起重设备和水库大坝上用的闸门。
公司共有员工300余人,占地150余亩,年产值6000余万元。
有九个科室:行政办公室、经营科、后勤保卫科、劳资科、供应科、生产科、技术科、质量科、财务科。
四个车间:金工车间、钳工车间、铆焊车间、铸工车间,还有一个车队。
名义上实现双休日,实际上常常加班,职工们过单休日的生活。
三个月前,笔者进入了该公司的铆焊车间了解管理流程和工艺流程。
该车间有82人,分6个班组:下料组、拼点组、焊接组、起重组、后勤组、油漆组。
每个组有人数15-20人不等。
车间每月完成吨位数在1200吨以上,产值在万以上。
是全厂完成吨位和产值最高的车间。
车间设主任一名,全面负责车间生产安全劳动纪律等各个方面的工作,另设书记一名,副主任二名,这四个职位是脱产的。
另外设工会主席一名,团支部书记一名,妇女委员一名,都不脱产,与其他员工一样参加各自所在班组的生产劳动。
工会、团支部和妇联很少搞活动。
每个班组设组长一名,安全员一名,每个礼拜一早晨7:30---8:00,以班组为单位开安全会,回顾总结上礼拜的安全生产情况,有没有出事故或者事故苗头,为安全生产敲一下警钟。
车间实现主任负责制。
新工人进厂,先到劳资科报到,填写劳动合同,到仓库领取工作服等劳保用品和榔头扳手等生产工具。
然后去车间,服从车间的调度,听候吩咐。
这时候你就成为一名正式的公司员工了。
每天上下班都由车间和班组考勤。
若有私事须向车间请假。
不再可以自由散漫了。
在公司实习期间,也必须服从公司的规章制度与出勤制度。
每个月公司都会召集生产会议,安排每个车间当月的任务。
由生产科管理进度。
现在以生产一只大铁箱为例看一下这个车间是如何运作的。
技术科给车间下发了一张图纸,要求用一公分厚的普通钢板做一只长宽高都是一米的大铁箱,与图纸订在一起下发的还有工艺流程卡。
工厂铆工实习报告

工厂铆工实习报告一、实习背景及目的随着我国经济的快速发展,工业化进程不断加快,铆工这一职业在建筑、机械制造等领域发挥着越来越重要的作用。
为了更好地了解铆工行业,提高自己的实践能力,我选择了工厂铆工实习,希望通过实习对铆工工作有更深入的了解。
本次实习的主要目的是:学习铆工的基本技能,掌握铆工的操作流程,提高自己的动手能力;了解工厂的生产组织与管理,培养自己的团队协作精神;通过实践检验所学理论知识,提高自己的综合素质。
二、实习内容与过程1. 实习前的准备在实习开始前,我们参加了实习培训,了解了铆工的基本知识、安全操作规程以及实习要求。
培训内容包括:铆工的基本概念、常用工具和设备、焊接技术、切割技术等。
通过培训,我们对铆工有了初步的认识,为实习打下了基础。
2. 实习过程中的学习与实践实习过程中,我们跟随导师学习了铆工的基本技能,如焊接、切割、打磨等。
在实际操作中,我们严格遵守安全规程,认真观察、学习导师的操作技巧,不断提高自己的动手能力。
同时,我们还学习了工厂的生产组织与管理,了解了一系列生产流程。
3. 实习中的困难与解决办法在实习过程中,我们遇到了一些困难。
例如,刚开始操作时,对工具的使用不熟悉,导致操作不规范;在焊接过程中,掌握了焊接技巧,但焊接质量不稳定。
针对这些困难,我们通过请教导师、与同学交流经验、反复练习等方式,不断改进操作技巧,提高焊接质量。
三、实习收获与反思1. 实习收获通过本次实习,我们掌握了铆工的基本技能,了解了工厂的生产组织与管理,提高了自己的动手能力和团队协作精神。
同时,在实践中发现了自己的不足,如理论知识不扎实、动手能力较弱等,为今后的学习和工作指明了方向。
2. 实习反思实习过程中,我们认识到理论知识与实践操作的重要性。
只有掌握了扎实的理论知识,才能在实际操作中游刃有余。
同时,我们也要注重团队协作,发挥集体智慧,共同完成任务。
此外,我们还应学会总结经验,不断改进自己的不足,提高自己的综合素质。
铆工顶岗实习报告三千字
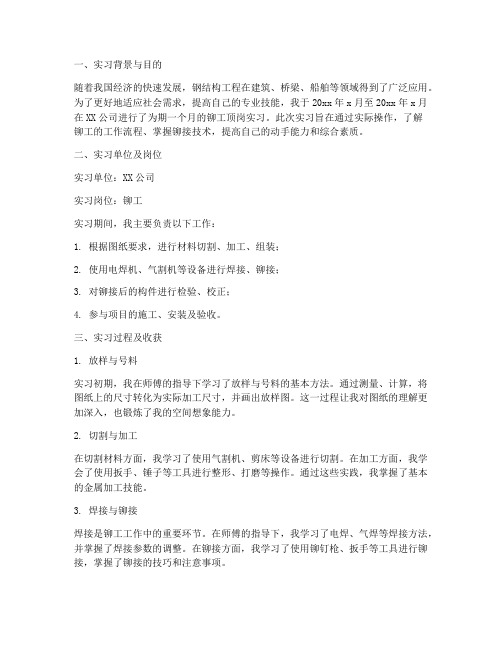
一、实习背景与目的随着我国经济的快速发展,钢结构工程在建筑、桥梁、船舶等领域得到了广泛应用。
为了更好地适应社会需求,提高自己的专业技能,我于20xx年x月至20xx年x月在XX公司进行了为期一个月的铆工顶岗实习。
此次实习旨在通过实际操作,了解铆工的工作流程、掌握铆接技术,提高自己的动手能力和综合素质。
二、实习单位及岗位实习单位:XX公司实习岗位:铆工实习期间,我主要负责以下工作:1. 根据图纸要求,进行材料切割、加工、组装;2. 使用电焊机、气割机等设备进行焊接、铆接;3. 对铆接后的构件进行检验、校正;4. 参与项目的施工、安装及验收。
三、实习过程及收获1. 放样与号料实习初期,我在师傅的指导下学习了放样与号料的基本方法。
通过测量、计算,将图纸上的尺寸转化为实际加工尺寸,并画出放样图。
这一过程让我对图纸的理解更加深入,也锻炼了我的空间想象能力。
2. 切割与加工在切割材料方面,我学习了使用气割机、剪床等设备进行切割。
在加工方面,我学会了使用扳手、锤子等工具进行整形、打磨等操作。
通过这些实践,我掌握了基本的金属加工技能。
3. 焊接与铆接焊接是铆工工作中的重要环节。
在师傅的指导下,我学习了电焊、气焊等焊接方法,并掌握了焊接参数的调整。
在铆接方面,我学习了使用铆钉枪、扳手等工具进行铆接,掌握了铆接的技巧和注意事项。
4. 检验与校正在检验方面,我学会了使用量具对构件的尺寸、形状、位置等进行检验。
在校正方面,我学会了使用扳手、锤子等工具对变形的构件进行校正。
5. 项目参与在实习期间,我参与了多个项目的施工、安装及验收。
通过这些项目,我了解了施工现场的管理、协调及施工工艺,提高了自己的团队协作能力。
四、实习体会与感悟1. 实践出真知通过这次实习,我深刻体会到“实践出真知”的道理。
在课堂上学习的理论知识,只有通过实际操作才能转化为自己的技能。
2. 团队合作的重要性在项目施工过程中,我深刻体会到团队合作的重要性。
铆工实习报告
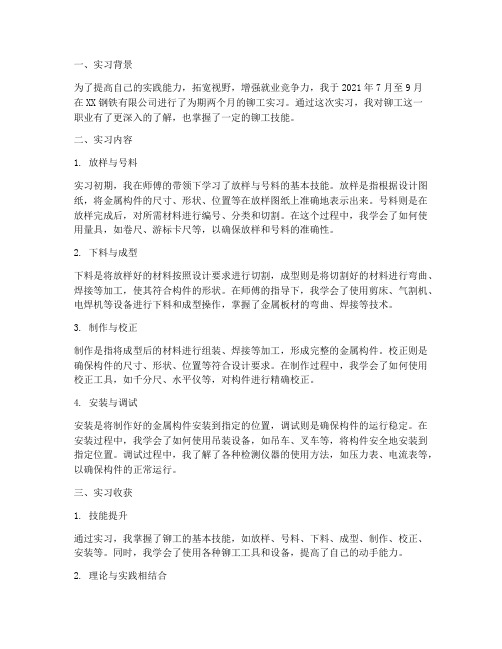
一、实习背景为了提高自己的实践能力,拓宽视野,增强就业竞争力,我于2021年7月至9月在XX钢铁有限公司进行了为期两个月的铆工实习。
通过这次实习,我对铆工这一职业有了更深入的了解,也掌握了一定的铆工技能。
二、实习内容1. 放样与号料实习初期,我在师傅的带领下学习了放样与号料的基本技能。
放样是指根据设计图纸,将金属构件的尺寸、形状、位置等在放样图纸上准确地表示出来。
号料则是在放样完成后,对所需材料进行编号、分类和切割。
在这个过程中,我学会了如何使用量具,如卷尺、游标卡尺等,以确保放样和号料的准确性。
2. 下料与成型下料是将放样好的材料按照设计要求进行切割,成型则是将切割好的材料进行弯曲、焊接等加工,使其符合构件的形状。
在师傅的指导下,我学会了使用剪床、气割机、电焊机等设备进行下料和成型操作,掌握了金属板材的弯曲、焊接等技术。
3. 制作与校正制作是指将成型后的材料进行组装、焊接等加工,形成完整的金属构件。
校正则是确保构件的尺寸、形状、位置等符合设计要求。
在制作过程中,我学会了如何使用校正工具,如千分尺、水平仪等,对构件进行精确校正。
4. 安装与调试安装是将制作好的金属构件安装到指定的位置,调试则是确保构件的运行稳定。
在安装过程中,我学会了如何使用吊装设备,如吊车、叉车等,将构件安全地安装到指定位置。
调试过程中,我了解了各种检测仪器的使用方法,如压力表、电流表等,以确保构件的正常运行。
三、实习收获1. 技能提升通过实习,我掌握了铆工的基本技能,如放样、号料、下料、成型、制作、校正、安装等。
同时,我学会了使用各种铆工工具和设备,提高了自己的动手能力。
2. 理论与实践相结合实习过程中,我将所学理论知识与实际操作相结合,加深了对铆工工艺的理解。
同时,通过解决实际问题,提高了自己的问题解决能力。
3. 团队合作意识在实习过程中,我与同事们相互协作,共同完成各项任务。
这使我认识到团队合作的重要性,提高了自己的沟通能力和团队协作能力。
铆工的实习报告
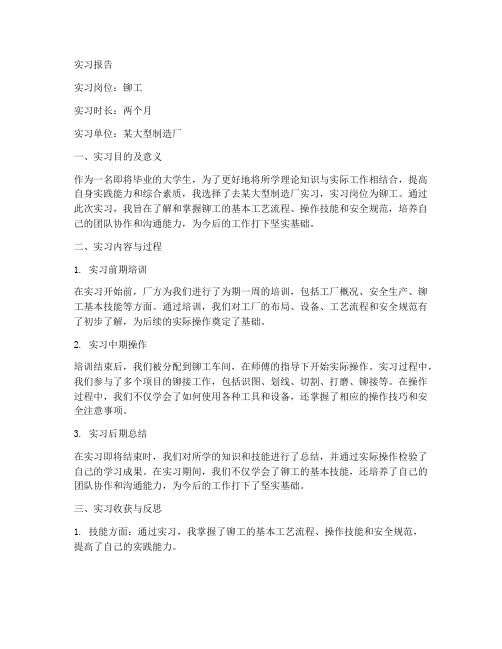
实习报告实习岗位:铆工实习时长:两个月实习单位:某大型制造厂一、实习目的及意义作为一名即将毕业的大学生,为了更好地将所学理论知识与实际工作相结合,提高自身实践能力和综合素质,我选择了去某大型制造厂实习,实习岗位为铆工。
通过此次实习,我旨在了解和掌握铆工的基本工艺流程、操作技能和安全规范,培养自己的团队协作和沟通能力,为今后的工作打下坚实基础。
二、实习内容与过程1. 实习前期培训在实习开始前,厂方为我们进行了为期一周的培训,包括工厂概况、安全生产、铆工基本技能等方面。
通过培训,我们对工厂的布局、设备、工艺流程和安全规范有了初步了解,为后续的实际操作奠定了基础。
2. 实习中期操作培训结束后,我们被分配到铆工车间,在师傅的指导下开始实际操作。
实习过程中,我们参与了多个项目的铆接工作,包括识图、划线、切割、打磨、铆接等。
在操作过程中,我们不仅学会了如何使用各种工具和设备,还掌握了相应的操作技巧和安全注意事项。
3. 实习后期总结在实习即将结束时,我们对所学的知识和技能进行了总结,并通过实际操作检验了自己的学习成果。
在实习期间,我们不仅学会了铆工的基本技能,还培养了自己的团队协作和沟通能力,为今后的工作打下了坚实基础。
三、实习收获与反思1. 技能方面:通过实习,我掌握了铆工的基本工艺流程、操作技能和安全规范,提高了自己的实践能力。
2. 团队协作:在实习过程中,我学会了与同事共同分担工作,相互协作,共同完成任务。
3. 沟通能力:在实际操作中,我与师傅、同事进行了充分沟通,提高了自己的沟通能力。
4. 安全意识:实习期间,我深刻认识到安全生产的重要性,时刻保持警惕,确保自己和同事的安全。
反思:在实习过程中,我发现自己在理论知识方面还有不足,需要在今后的学习中加强巩固。
同时,我要不断提高自己的团队协作和沟通能力,为将来的工作做好准备。
四、实习总结通过两个月的铆工实习,我不仅掌握了铆工的基本技能,还培养了自己的团队协作和沟通能力。
铆工实习报告周志

一、实习背景为了提高自己的实践能力,丰富专业经验,我选择了在某知名铆焊公司进行为期四周的铆工实习。
铆焊行业作为制造业的重要组成部分,对于机械加工、航空航天、汽车制造等领域都有着广泛的应用。
通过这次实习,我希望能够深入了解铆焊工艺,提高自己的动手能力和团队合作精神。
二、实习内容1. 学习铆焊基础知识实习的第一周,我在公司技术部老师的带领下,学习了铆焊的基础知识。
了解了铆焊的定义、原理、工艺流程以及常用铆钉的种类。
同时,还学习了铆焊设备的使用方法和操作规范。
2. 实践操作技能实习的第二、三周,我开始了实际操作技能的学习。
在师傅的指导下,我学习了铆接、焊接、切割等基本操作。
通过不断练习,我逐渐掌握了铆焊的基本技能,如铆钉的安装、焊接火焰的调节、切割技巧等。
3. 参与项目实践实习的第四周,我参与了公司一个实际项目的铆焊工作。
在师傅的带领下,我与团队成员一起完成了铆焊任务。
在这个过程中,我不仅锻炼了自己的操作技能,还学会了与团队成员沟通协作,共同解决问题。
三、实习收获1. 提高动手能力通过这次实习,我的动手能力得到了很大提高。
从最初的不知所措,到后来能够熟练地完成各项操作,我深刻体会到了实践的重要性。
2. 增强团队合作精神在实习过程中,我与团队成员共同完成了多个项目。
这使我明白了团队合作的重要性,学会了如何在团队中发挥自己的作用。
3. 深入了解铆焊工艺通过实习,我对铆焊工艺有了更加深入的了解,为今后从事相关行业打下了坚实的基础。
四、实习体会1. 实践是检验真理的唯一标准在实习过程中,我深刻体会到了这句话的含义。
理论知识固然重要,但只有通过实践,才能真正掌握技能。
2. 学会沟通与协作在团队中,沟通与协作至关重要。
通过这次实习,我学会了如何与团队成员沟通,共同解决问题。
3. 严谨的工作态度铆焊工作需要严谨的工作态度,一丝不苟。
在实习过程中,我逐渐养成了严谨的工作习惯。
总之,这次铆工实习让我受益匪浅。
在今后的学习和工作中,我会继续努力,不断提高自己的实践能力和综合素质。
铆工实习报告三篇

铆工实习报告三篇铆工实习报告范文三篇篇一:铆工实习报告所谓铆工就是把板材、型材、线材、管材等通过焊接、铆接、螺栓连接等加工方法制作成钢结构的一种制作工艺。
铆工是金属构件施工中的指挥者。
按加工工艺又分为:放样、号料、下料、成型、制作、校正、安装等。
铆工既根据要求作出相应的金属制品,主要有识图和制图的学问;常用金属材料及热处理学问;能矫正变形较大或复合变形的原材料及一般结构件,能作成基本形体的展开图,计算展开料长;能使用维护剪床、气割、电焊机等设备;能读懂并装配桁架类、梁柱类、箱壳类、箱门类和低中压容器等图样,并进行全位置定位焊、铆接、螺纹连接,检验尺寸、样子位置。
时间过得真快,就一晃眼铆工实习结束了,但通过这次实习让我们把握了铆工的基本技能,为我们在以后的工作道路上铺平了道路,让我们学习到书本上的和非书本的学问将永久留在我记忆里,也毫无疑问,它们将使我在以后的职场道路上受益许多。
从当时的跃跃欲试,到疲乏到叫苦连天,到胜利时的无比喜悦,都已成为过去式,也将成为奇妙的回忆。
篇二:铆工实习心得铆工实习心得1、阅历是从实践中得来的。
(以铆工工种为例)书本上的理论精通不是真正意义上的对技术的精通,技术最终要应用于生产,就避开不了要解决很多实践中才遇到的问题,而这些待解决的问题远比我们想象中的要多。
例如初钻孔偏心,可以通过转变我气钻的方向使其回到中心,等等2.每步必留神〔以钳工为例〕很多东西一不留神错了就要花上双倍的时间去修改,甚至从头再来,又甚至是连重来的机会都没有了。
因此,步步留神,步步留神,步步三思就显得特殊重要了。
当然了,也不能说走极端的,做什么都畏手畏脚的,那也成不了事的。
例如,在使用牛头刨床时确定要把工件夹紧了,夹前确定要先敲敲工件,以保证工件是水平放置的。
要是到了刨完几个面才觉察问题的话,那就可以预备第二块工件重新来过了,因为这个时候所产生的误差已相当大,根本无法弥补了。
又例如在做钳工时,在工件上转孔时确定要留神,确定要先划好位置,要错了的话,那工件又报废了。
铆焊车间实习报告
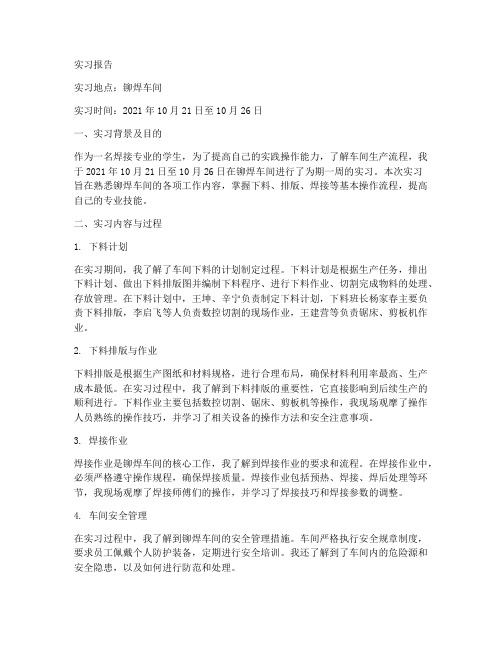
实习报告实习地点:铆焊车间实习时间:2021年10月21日至10月26日一、实习背景及目的作为一名焊接专业的学生,为了提高自己的实践操作能力,了解车间生产流程,我于2021年10月21日至10月26日在铆焊车间进行了为期一周的实习。
本次实习旨在熟悉铆焊车间的各项工作内容,掌握下料、排版、焊接等基本操作流程,提高自己的专业技能。
二、实习内容与过程1. 下料计划在实习期间,我了解了车间下料的计划制定过程。
下料计划是根据生产任务,排出下料计划、做出下料排版图并编制下料程序、进行下料作业、切割完成物料的处理、存放管理。
在下料计划中,王坤、辛宁负责制定下料计划,下料班长杨家春主要负责下料排版,李启飞等人负责数控切割的现场作业,王建营等负责锯床、剪板机作业。
2. 下料排版与作业下料排版是根据生产图纸和材料规格,进行合理布局,确保材料利用率最高、生产成本最低。
在实习过程中,我了解到下料排版的重要性,它直接影响到后续生产的顺利进行。
下料作业主要包括数控切割、锯床、剪板机等操作,我现场观摩了操作人员熟练的操作技巧,并学习了相关设备的操作方法和安全注意事项。
3. 焊接作业焊接作业是铆焊车间的核心工作,我了解到焊接作业的要求和流程。
在焊接作业中,必须严格遵守操作规程,确保焊接质量。
焊接作业包括预热、焊接、焊后处理等环节,我现场观摩了焊接师傅们的操作,并学习了焊接技巧和焊接参数的调整。
4. 车间安全管理在实习过程中,我了解到铆焊车间的安全管理措施。
车间严格执行安全规章制度,要求员工佩戴个人防护装备,定期进行安全培训。
我还了解到了车间内的危险源和安全隐患,以及如何进行防范和处理。
三、实习收获与反思通过本次实习,我对铆焊车间的各项工作有了更深入的了解,掌握了下料、排版、焊接等基本操作流程。
同时,我也认识到了自己在专业技能方面的不足,需要在今后的学习中加强练习,提高自己的操作能力。
此外,我还深刻体会到了安全意识的重要性。
在实际操作过程中,必须时刻保持警惕,遵守操作规程,确保生产安全和人身安全。
2024焊装车间实习报告6篇

2024焊装车间实习报告2024焊装车间实习报告精选6篇(一)2024年焊装车间实习报告尊敬的企业领导:您好!我是来自A大学机械专业的学生小明,在2024年暑期参加了贵公司焊装车间的实习。
通过这次实习,我对焊接工艺、生产操作流程以及团队协作能力有了进一步的了解。
一、实习目标和工作内容在这次焊装车间的实习中,我的主要目标是熟悉焊接工艺和相关设备的操作,并能够独立完成一些简单的焊接任务。
实习期间,我主要参与了以下工作内容:1.观察和学习焊接工艺:我首先通过与工人的交流和观察,学习了不同焊接工艺的原理与应用范围,包括气体保护焊、手工电弧焊以及激光焊接等。
2.操作焊接设备:在掌握了一定的理论知识后,我开始实际操作焊接设备。
通过实习,我学会了操作氩弧焊设备、电弧焊设备以及自动焊接机器人等。
3.参与焊接任务:在熟悉了焊接工艺和设备操作后,我有机会参与一些小型焊接任务。
我与其他实习生和工人一起合作,完成了一些简单的焊接工作,并得到了一些肯定与鼓励。
二、实习收获通过这次焊装车间的实习,我获益良多。
主要有以下几点:1.增强了焊接技能:通过实际操作焊接设备,我对焊接的操作流程、注意事项和技巧有了更深刻的了解,并且提升了我的焊接技能。
2.了解了生产操作流程:在实习期间,我不仅参与了焊接任务,还有机会观察和学习了生产操作流程。
我了解到了焊装车间的生产过程,并对整个生产流程有了更全面的认识。
3.锻炼了团队合作能力:实习期间,我与其他实习生和工人一起合作完成了一些焊接任务。
在团队合作中,我学会了与他人有效沟通、协调合作,并意识到每个人的努力和贡献对于整个团队的重要性。
三、实习心得和建议通过这次焊装车间的实习,我对焊接工艺和生产流程有了更深入的了解,也提高了我的实际操作能力。
感谢企业给予我这次宝贵的实习机会。
在实习过程中,我感到焊装车间的工作环境非常重要。
一方面,焊接工作需要一定的专注力和安全意识,因此工作场所的安全设施和管理措施应该得到重视。
铆工顶岗实习报告

一、实习背景为了提高自己的专业技能和实际操作能力,我选择了铆工这一职业进行顶岗实习。
铆工是金属构件施工中的关键工种,主要负责将板材、型材、线材、管材等通过焊接、铆接、螺栓连接等加工方法制作成钢结构。
在实习期间,我深刻体会到了铆工工作的重要性和挑战性。
二、实习目的1. 了解铆工行业的发展现状和前景,为今后的职业规划提供依据。
2. 掌握铆工的基本技能,提高自己的动手操作能力。
3. 学习识图、制图、金属材料及热处理等理论知识,为实际工作打下坚实基础。
三、实习时间及单位实习时间:20xx年x月x日至20xx年x月x日实习单位:XX市XX钢结构有限公司四、实习内容及收获1. 了解铆工行业在实习期间,我了解到铆工行业在我国近年来得到了快速发展,尤其在基础设施建设、船舶制造、航空航天等领域有着广泛的应用。
随着我国经济的持续增长,铆工行业的发展前景十分广阔。
2. 掌握铆工基本技能(1)放样:在实习过程中,我学会了如何根据图纸进行放样,包括确定放样比例、绘制放样图、计算放样尺寸等。
(2)号料:掌握了如何根据放样图进行号料,包括选择合适的材料、计算号料尺寸、绘制号料图等。
(3)下料:学会了使用切割设备进行下料,包括剪床、气割、等离子切割等。
(4)成型:掌握了各种金属材料的成型方法,如弯曲、拉伸、冲压等。
(5)制作:学会了组装、焊接、铆接等加工方法,制作出符合要求的金属构件。
(6)校正:掌握了金属构件的校正方法,确保其尺寸、形状、位置符合要求。
(7)安装:学会了金属构件的安装方法,包括定位、固定、调整等。
3. 学习理论知识在实习过程中,我学习了识图、制图、金属材料及热处理等理论知识,为实际工作打下了坚实基础。
4. 实践操作经验通过实习,我积累了丰富的实践经验,掌握了铆工工作的各个环节,提高了自己的动手操作能力。
五、实习心得1. 理论与实践相结合:在实习过程中,我深刻体会到理论与实践相结合的重要性。
只有将理论知识运用到实际工作中,才能提高自己的技能水平。
铆工个人实习报告
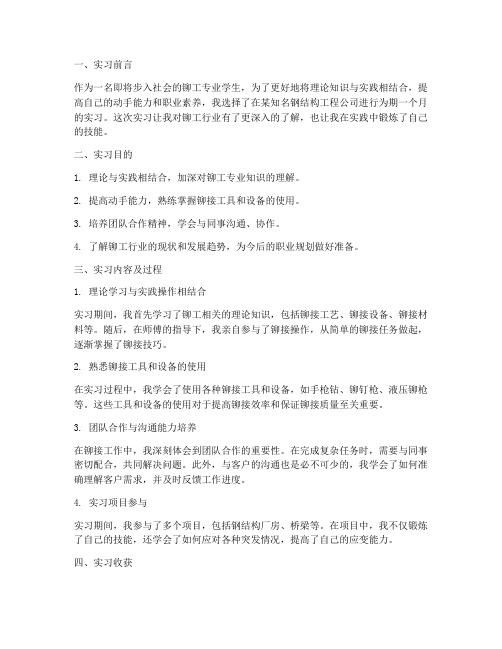
一、实习前言作为一名即将步入社会的铆工专业学生,为了更好地将理论知识与实践相结合,提高自己的动手能力和职业素养,我选择了在某知名钢结构工程公司进行为期一个月的实习。
这次实习让我对铆工行业有了更深入的了解,也让我在实践中锻炼了自己的技能。
二、实习目的1. 理论与实践相结合,加深对铆工专业知识的理解。
2. 提高动手能力,熟练掌握铆接工具和设备的使用。
3. 培养团队合作精神,学会与同事沟通、协作。
4. 了解铆工行业的现状和发展趋势,为今后的职业规划做好准备。
三、实习内容及过程1. 理论学习与实践操作相结合实习期间,我首先学习了铆工相关的理论知识,包括铆接工艺、铆接设备、铆接材料等。
随后,在师傅的指导下,我亲自参与了铆接操作,从简单的铆接任务做起,逐渐掌握了铆接技巧。
2. 熟悉铆接工具和设备的使用在实习过程中,我学会了使用各种铆接工具和设备,如手枪钻、铆钉枪、液压铆枪等。
这些工具和设备的使用对于提高铆接效率和保证铆接质量至关重要。
3. 团队合作与沟通能力培养在铆接工作中,我深刻体会到团队合作的重要性。
在完成复杂任务时,需要与同事密切配合,共同解决问题。
此外,与客户的沟通也是必不可少的,我学会了如何准确理解客户需求,并及时反馈工作进度。
4. 实习项目参与实习期间,我参与了多个项目,包括钢结构厂房、桥梁等。
在项目中,我不仅锻炼了自己的技能,还学会了如何应对各种突发情况,提高了自己的应变能力。
四、实习收获1. 技能提升通过实习,我的铆接技能得到了很大提升,能够独立完成各种铆接任务。
2. 职业素养提高在实习过程中,我学会了遵守职业道德,尊重同事,注重团队协作。
3. 对铆工行业的认识通过实习,我对铆工行业有了更深入的了解,认识到铆工行业的发展前景和市场需求。
五、实习总结这次实习让我受益匪浅,不仅提高了自己的技能,还锻炼了自己的职业素养。
在今后的工作中,我将继续努力,不断提升自己的能力,为铆工行业的发展贡献自己的力量。
- 1、下载文档前请自行甄别文档内容的完整性,平台不提供额外的编辑、内容补充、找答案等附加服务。
- 2、"仅部分预览"的文档,不可在线预览部分如存在完整性等问题,可反馈申请退款(可完整预览的文档不适用该条件!)。
- 3、如文档侵犯您的权益,请联系客服反馈,我们会尽快为您处理(人工客服工作时间:9:00-18:30)。
铆焊车间实习报告篇一:铆焊实习报告铆焊实习总结实习地点:铆焊车间实习时间:经过三周的实习,我掌握了公司生产运行的流程,技术部、工艺部、采购部、仓库、生产管理部、制造部等职能部门的具体职责,对车间的日常生产也有了细致的了解。
各职能部门技术部:产品图纸的设计,物料采购的申报。
工艺部:生产工艺、工时的制定。
采购部:生产原料的采购。
仓库:生产物料存放、发放的管理。
生产管理部:生产计划的制定与下达,公司内部生产运作、外协运作等工作的协调。
生产调度:李文龙,负责CSB 产品。
于奎龙、王振全负责泥浆泵。
制造部:公司内部生产制造、外协制造的管理。
外协调度:曹晓辉、王显。
我分别在夏亮亮、栾许志、张超群班组实习,下面是实习期间班组主要负责的产品:夏亮亮班组主要负责产品:泥浆泵。
栾许志班组主要负责产品:1.双动力鼠洞。
泥浆泵连杆。
、1600、XX、2200泥浆泵的压力表连接座、安全阀座。
张超群班组主要负责产品:泥浆泵。
绞车。
伸缩臂。
伸缩臂。
导轨。
三周的实习工作,我更加了解作为一个车间调度的职责与定位,做好生产保障工作、生产进度的跟进、异常情况的解决、质量的控制、现场的管理与安全。
让生产更加高效,质量更加优质,现场更加规范,安全更加到位,下面是我从生产保障、安全生产、铆焊作业、现场管理、团队建设几个方面做的实习总结。
1.生产保障技术工艺技术与工艺作为生产制造的主要依据,必须做到合理性、及时性,合理的工艺是经过正确的设计与反复的试验来确定的,正确合理的工艺可以使生产更高效更优质。
在我们公司技术的图纸会进行改动,那么就需要及时的通知各部门改变原有计划。
因为原有下料计划与改动后的图纸尺寸不符,新的计划没人制定与下达,导致原有计划所下的物料无法使用影响生产,加强技术与生产管理部的工作衔接,做到及时修改并下达下料计划。
技术图纸上的物料没有及时准确的申报采购,导致没有采购需要的物料影响生产,往往通过代料或者加急采购来解决,最好的办法是在一开始的时候做细采购申请避免遗漏。
在以后的工作中我要及时反馈出现的问题与技术工艺一起解决。
1.2物料保障我们公司生产中所需要的物料非常依赖外协加工,现在外协来料不及时已经成为一种常态,而且还会出现质量问题,严重影响到了生产的进度,增加了生产的难度。
我们公司外协是由生产调度转给外协调度,由外协调度负责与外协厂家之间的工作。
在这个过程中有时会出现漏转、入库遗失的现象。
漏转情况可以及时联系外协进行加工,入库遗失,甚至找不到也无人负责,应该由库管负起责任。
这方面工作需要生产调度、外协调度、仓库管理共同协作加强沟通以确保外协物料的及时性。
另外外协物料的质量非常重要,悬臂梁滑移的筋板大小不一、双鼠洞导轨的加工、连杆大头的平面度不达标等问题增加了生产难度,影响了生产进度。
应该加强对外协物料的质量控制,以减轻生产压力。
对于外协物料的质量问题应该建立反馈机制,加强与外协厂家的信息沟通。
可以赋予车间拒绝接受不合格物料的权利。
车间内部领料混乱,在下料实习总结已经提到。
出现已下物料丢失的情况,应该严格实施领料签单、发料明细的制度,规范铆工的作业习惯杜绝用物料当工装,减少物料丢失并能找到丢失的原因。
领料的时候遇到这种情况,仓库很忙没时间给你配送,我们只能去等待。
我觉得可以给我们车间配备一辆叉车供我们自己使用调配,可以解决这种被动等待的情况。
以后我需要运用ERP系统并积极的跟生产管理部、仓库同事的沟通与协作把我们生产所需要的每一样物料落到实处确保生产的顺利进行。
2.安全生产安全重于泰山。
安全是生产的前提,一切生产活动必须在安全的前提去进行。
车间同事日常劳保用品的佩戴不齐全,不带眼镜、不挂帽带、不带耳塞的有很多,吊具的违规使用,安全通道的常态占用,高空作业的防护不到位等。
安全意识比较薄弱,很多危险意识不到。
应加强员工的安全教育,树立牢固的安全意识。
在适当的位置做好安全标语及警示。
3.铆焊作业车间工人工作能力与态度都很好,有着积极的工作态度与过硬的技术。
大家都井然有序的工作着,缺少了最基本的沟通交流。
我想这是我们要去改变的,怎么样让大家快快乐乐篇二:铆焊车间下料工序实习报告铆焊车间下料工序实习报告实习地点:铆焊车间实习时间:经过五天的下料实习,我了解了车间下料的流程:作业指导、作业方式以及流程的控制方法。
现对这一周的实习工作做总结。
车间下料主要有下料计划,下料排版,下料作业(数控切割,锯,剪板)。
王坤、辛宁负责下料计划,下料班长杨家春主要负责下料排版,李启飞等人负责数控切割的现场作业,王建营等负责锯床、剪板机作业。
车间下料是根据生产任务,排出下料计划、做出下料排版图并编制下料程序、进行下料作业、切割完成物料的处理、存放管理。
一、下料计划生产计划是生产管理的核心工作,好的生产计划可以让生产有条不紊的进行,可以很好的提高生产的效率,从而降低运行成本。
下料作为生产的准备前序是非常重要的。
我们的下料综合明细表包括了作业方式、人员等信息、托盘编号等,托盘编号这一点我觉得非常好,应该是为了方便找料设计的,但缺少下料完成时间,综合明细表上有接收人、接收时间、质检的签字等项目,但好像都没有这么做,没有起到一个跟进控制流程的作用。
按照车间的下料计划,下料进度应该是满足了生产进行,现场托盘上有很多已完成的物料,这几天来领料的师傅们也都找到了需要的物料。
而且我觉得堆料有点多,这样不方便现场的管理,作为下料单位来说太多的库存也反应出一定的问题,是不是下料产能与下工序产能的不协调。
可以主动的把下好的物料发放到下一工序,如果让整个车间去分担下料场地的问题,料场会管理的更好。
二、排版编程合理的排版可以减少板材的浪费。
根据生产计划进行每天的排版与编程,我们的排版图做的很紧凑,做到了合理利用板材减少浪费,都标注了图号、材质以及件数等。
在这里我提一点建议,规则的物料可以标注一下它们的尺寸,比如100X100;不规格的物料可以附上它们的简易图纸并标注尺寸。
因为在大批量的下料作业中是需要对首件进行自检的,他们既不参与编程也没有图纸根本没有自检这一控制环节,一旦出现问题就是一批物料。
三、下料作业下料作业中我们的员工基本都有很强的主观能动性,积极主动的做好自己的工作,即使没有人员安排也都在有序的工作着,切割成型的火焰切口光洁平整,氧化铁易于清除,材检号的移植,图号、材质、数量的标识都做到了,剩余的边角余料都存放起来用于以后再次利用。
工作中缺少交流沟通,这几天我感觉不是很好融入。
在下料作业过程中还是有很多细节做的不好,吊板材的过程中有时候,需要用手扶的时候有的同事会习惯性的把手伸到板材下方;吊车师傅有时候会很自发的去做一些起落的操作,吊车可以拒绝违规指挥,但是绝对不能去自发的去操作;吊板材需要垫东西的时候手是不能伸进去的只能扔东西进去。
这些日常工作中的习惯是非常危险的。
四、切割后处理切割完成后的处理是下料工序作业的最后一步,所以得符合下一工序使用要求,懂得铆焊工序都会对物料哪些方面有什么样的要求,用最少的资源做到最大的效果。
切割后氧化铁都非常仔细的剔除、打磨,切割导致的缺陷也都进行了打磨补焊再打磨,甚至切割不平整的表面会进行打磨,这些处理都非常到位,但是有些作业是可以省略的。
氧化铁主要是会对焊接质量产生影响,容易产生缺陷。
因为我们的车间加工的都是比较厚的板材,这几天我见到的最薄也15mm以上,按照行业默认的规范6-8mm以上的就需要进行破口加工的,不管平接或者角接,当然还是需要根据设计要求考虑焊接强度,我们车间的铆焊基本上都是需要破口的加工再进行焊接,而且焊接以后进行的探伤检验也都是MT磁粉探伤,只能探测表面的缺陷和近表面的缺陷,应该焊接的要求也不是很高,所以我觉得没有必要对切割后的表面进行如此细致的打磨,一方面可能开破口切掉,另一方面不会对焊接质量造成影响。
五、存放管理处理好的物料进行有序的存放,做好标识方便查找与领用。
车间物料的存放是根据产品对应托盘进行存放的,托盘上有产品的编号、名称,可是托盘上具体有什么料有多少,这一个产品还少什么料少多少就不清楚了,由于我们存料比较多,而且不可能根据产品一台一台的下,要根据工序需要按需要的次序完成,所以不能一个托盘一整套产品的用料一次领走。
我觉得可以做一个托盘物料明细,这个托盘什么产品、需要什么物料、各需要多少、完成了多少、什么时候完成、已领走等明细表与之前的下料综合明细对应起来方便我们对存料的管理。
锯床和剪板机实习的时间较少,只要平时做好规范操作,设备保养就没什么问题。
六、增加派工单与领料单整体的下料流程很熟练,在整个生产的控制过程中一开始少了派工单,在下达生产计划的同时应该也有派工单,派工单和生产计划是匹配的,是生产的基本凭证,不仅有开始生产的指令,还是控制生产数量、进度、核算生产成本的凭证;在进行生产的过程中应该做好综合明细表中的每一项签字确认,让每一个环节落到实处;下料结束发放给生产时我们车间缺少物料发放单,主要作用是记录控制物料的发放,内容应该包括用料产品的用途(产品编号、名称、图号具体点还以加入项目编号),发料的明细,接收物料的单位、时间,发料人员的确认,最主要的是车间领导的签字,这样不仅有效的规范了领料,方便了物料的管理,更可以让车间领导通过领料单了解车间各班组生产进度。
七、现场管理最后是现场的管理方面,关与6S:整理、整顿、清扫、清洁、素养、安全。
其实就是对现场人机料法的一种有效管理,是一种坚持养成习惯,持续改进员工素养,从而提高整体工作质量的目的。
我们车间的场地有限确实的进行6S现场管理有很大困难,只能尽我们的努力做到最好。
托盘上的物料标识完善一下(最上面一块最起码应该有图号、名称、材质、数量),托盘明细做好,做好不管是谁都能第一时间找到需要的物料。
切割后处理氧化铁的工作场地常常被堆的很乱,根本没有地方下脚,很容易绊倒或者磕倒人,可以尽可能的堆在一边留出一条允许通过的道路。
我们设备下面的氧化铁、熔渣等应该很久没有清理了,这样的设计也不方便清理,我觉得可以把整个设备垫起几块,让垃圾掉落下来以后我们可以从中间扫到侧面,这样每天都坚持做也不会积累这么多。
让员工在工作中养成一些很好的习惯,比如用完工具就放回规定的地点不要随手乱扔,电焊机上不要放置水杯子,每次使用磁力吊一定扣上保险,不要用量具去碰没有吹掉的熔渣,保持工具箱的合理规划和整洁等等,从而提高员工的作业素养,那么安全也就顺理成章了。
八、其他在工作过程中,车间的磁力吊不是很好用。
这几天也没看到车间的检查对完成的物料进行检查,还有我觉得钻床可以合并到下料,车间基本没有需要铆工组对好了进行配钻的作业,那么直接从下料转到钻床进行钻孔可以更有效。
实习的五天,每一天的感受都在变,因为毕竟这里不是我以前工作的地方,这里的制度和方式方法也是适合这里的,但是我觉得生产运行的管理就是不断的去发现问题去解决问题,是一个不断改善的过程。