焦炭塔本体的设计
大型焦炭塔的设计1
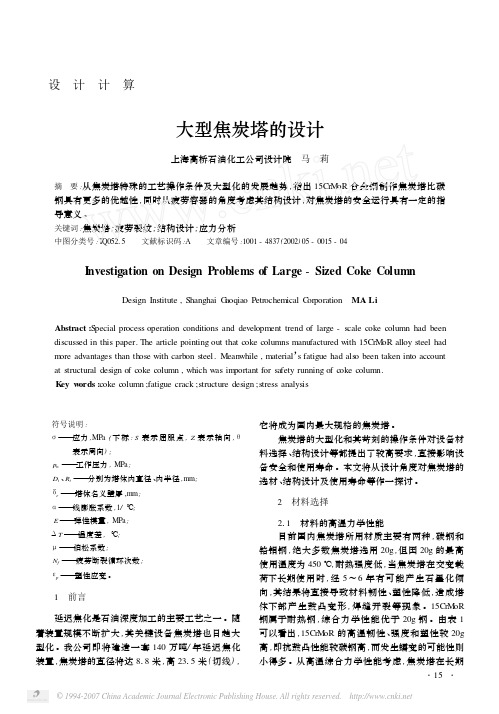
焦炭塔在反复的加热冷却循环过程中 , 塔体环 焊缝会产生疲劳裂纹 , 而且多在焊缝熔合线沟槽的 应力集中处 。 在设计制造过程中要求采用自动焊 ; 控制焊缝 的表面质量 , 减少气孔和夹渣的出现 ; 焊前预热及焊 后热处理 ; 对焦炭塔生焦层以下的环焊缝应磨平焊 缝余高 , 对泡沫层即上段塔体环焊缝进行打磨 , 使焊 缝和母材之间圆滑过渡 , 焊缝余高不超过 115mm , 减 少应力集中系数 , 增加疲劳强度 。
312 裙座
( 1) 裙座裂缝产生原因
裙式支座的主要问题是热应力 , 即由裙座与塔 体相接触处的温度梯度及裙座与其冷底座之间的温 差所引起 。从国内现役焦炭塔来看 , 裙座焊缝开裂
( 图 1) 现象较为严重 。
在急骤升温阶段 , 裙座与下部塔体有较大温差 , 各自径向自由热变形不一致 , 而裙座又具有较大刚 度 , 在裙座与塔体焊缝外侧形成弯曲拉应力 。沿裙 座的轴向温差越大 , 则该应力值也越大 。在长期受 到较大的轴向交变热应力作用下 , 焊缝表面及焊缝 ・16 ・
Kt 值越大 , 其结构疲劳寿命越低 。尤其是在接
管部位 , 开孔处几何不连续区域形成的高应力集中 也是焦炭塔的薄弱环节 , 因而也最易发生疲劳开裂 或泄漏等故障 。开孔需要补强 , 但孔的补强是不能 简单地通过增加补强材料而获得 。 有实验指出 , 若 A 1 为开孔后被削去的横截面 ,
A 2 为总的补强面积 , 对于圆筒形容器上的接管 , 当 A 2 / A 1 从 65 % 增加到 115 % 时 , 其最大应力只有很
211 材料的高温力学性能
δ — — 塔体名义壁厚 ,mm ; e — α— — — 线膨胀系数 , 1/ ℃;
E— — — 弹性模量 , MPa ;
炼油三部焦炭塔架设方案
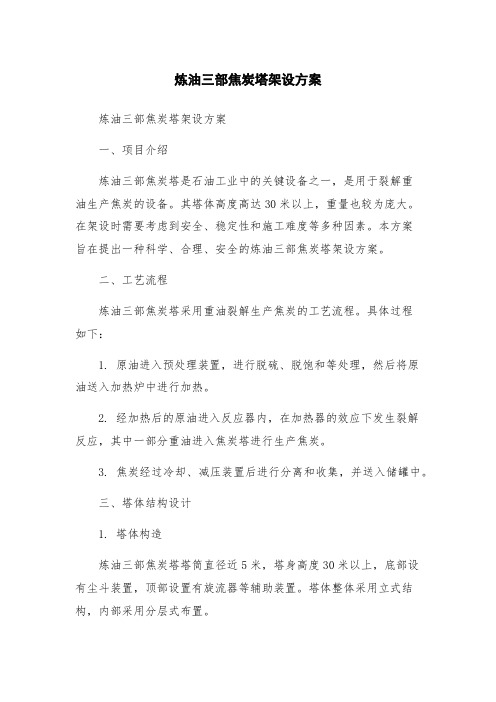
炼油三部焦炭塔架设方案炼油三部焦炭塔架设方案一、项目介绍炼油三部焦炭塔是石油工业中的关键设备之一,是用于裂解重油生产焦炭的设备。
其塔体高度高达30米以上,重量也较为庞大。
在架设时需要考虑到安全、稳定性和施工难度等多种因素。
本方案旨在提出一种科学、合理、安全的炼油三部焦炭塔架设方案。
二、工艺流程炼油三部焦炭塔采用重油裂解生产焦炭的工艺流程。
具体过程如下:1. 原油进入预处理装置,进行脱硫、脱饱和等处理,然后将原油送入加热炉中进行加热。
2. 经加热后的原油进入反应器内,在加热器的效应下发生裂解反应,其中一部分重油进入焦炭塔进行生产焦炭。
3. 焦炭经过冷却、减压装置后进行分离和收集,并送入储罐中。
三、塔体结构设计1. 塔体构造炼油三部焦炭塔塔筒直径近5米,塔身高度30米以上,底部设有尘斗装置,顶部设置有旋流器等辅助装置。
塔体整体采用立式结构,内部采用分层式布置。
2. 塔体材质选择塔体主要材质选用Q345B钢板,其具有耐高温、耐磨、耐腐蚀等性能,很适合于工业环境下使用。
塔体内部表面采用高温防腐涂层进行钝化处理,以防止腐蚀和污染。
3. 塔体基础设计塔体基础设计采用深基础,如钢筋混凝土桩或钢板桩等可靠的承载体,以确保塔体安全稳定地承载工作负载。
四、装置架设方案1. 工艺流程首先在现场进行现场勘察,细化安全要求和施工工艺流程。
然后进行运输、安装、调试等多个环节的开展,确保系统设计稳定性、精度与可靠性。
2. 塔体架设方案为了确保塔体安全、稳定地立在地面上,首先需要做好场地处理,为接下来的施工创造良好的现场工作环境。
然后根据塔体的结构要求,选用横梁、斜撑等钢材加固,以增加塔体的稳定性和承载力。
完成钢材加固后,进行塔体装配和焊接等作业。
在塔体立完后,进行轮盘、旋流器、储存罐等辅助设备的装配与安装,最后进行系统调试。
3. 施工安全措施安全是施工工作的首要条件。
在施工过程中,应采取必要的安全措施,如戴好安全帽、穿好安全鞋、穿戴防护服等防护措施,确保施工人员的健康与安全。
低压条件下大型焦炭塔系统几个设计问题的探讨
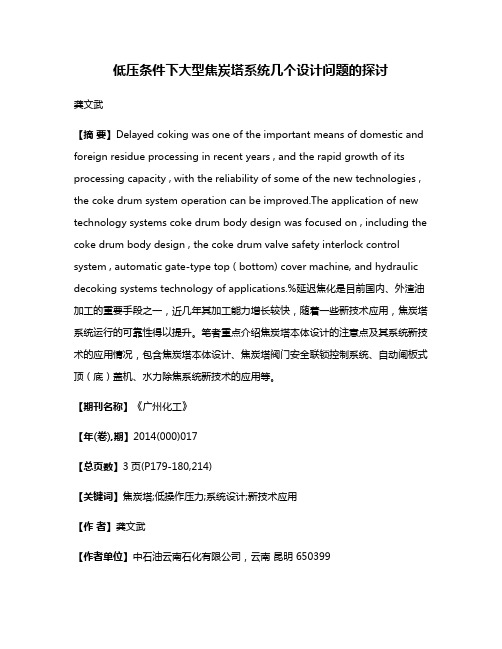
低压条件下大型焦炭塔系统几个设计问题的探讨龚文武【摘要】Delayed coking was one of the important means of domestic and foreign residue processing in recent years , and the rapid growth of its processing capacity , with the reliability of some of the new technologies , the coke drum system operation can be improved.The application of new technology systems coke drum body design was focused on , including the coke drum body design , the coke drum valve safety interlock control system , automatic gate-type top ( bottom) cover machine, and hydraulic decoking systems technology of applications.%延迟焦化是目前国内、外渣油加工的重要手段之一,近几年其加工能力增长较快,随着一些新技术应用,焦炭塔系统运行的可靠性得以提升。
笔者重点介绍焦炭塔本体设计的注意点及其系统新技术的应用情况,包含焦炭塔本体设计、焦炭塔阀门安全联锁控制系统、自动闸板式顶(底)盖机、水力除焦系统新技术的应用等。
【期刊名称】《广州化工》【年(卷),期】2014(000)017【总页数】3页(P179-180,214)【关键词】焦炭塔;低操作压力;系统设计;新技术应用【作者】龚文武【作者单位】中石油云南石化有限公司,云南昆明 650399【正文语种】中文【中图分类】TQ962延迟焦化主要以减压渣油为原料,经裂解缩合反应得到轻质石油馏份,如干气、液化气、石脑油、柴油、蜡油以及石油焦等[1]。
大型焦炭塔的设计及其改进(北京设计院[详细]
![大型焦炭塔的设计及其改进(北京设计院[详细]](https://img.taocdn.com/s3/m/cd44a015b0717fd5370cdc6a.png)
大型焦炭塔的设计及其改进顾一天中国石化集团北京设计院(一) 概述炼油装置大型化的关键是设备大型化.要实现延迟焦化装置大型化,首先要实现其核心设备焦炭塔的大型化.在延迟焦化装置中,单塔能力在50万吨/年时,其塔直径在8米以上.目前世界上最大焦炭塔在加拿大su米cor油砂加工厂,直径为12.2米,高30米.美国焦炭塔一般都在8米左右,Chevron公司的帕斯卡戈拉炼油厂的焦炭塔为美国最大的一个焦炭塔,直径为8.3米,高33.5米.上海石化股份有限公司于1999年新上的100万吨/年延迟焦化装置,原料为沙特原油的减渣,含硫量达4.6%.原设计方案为二炉四塔,焦炭塔规格为DN6400×21000(米米).97年9月经可行性研究审批后,设计方案改为一炉两塔,焦炭塔直径改为8400.直径加大后,其材料和结构也必须作相应的改进,为适应延迟焦化装置大型化的要求,我院和上海石化机械制造有限公司一起,在中国石化集团公司国产化办公室的支持下,进行了设计和制造技术的攻关.我院结合上海石化股份有限公司100万吨/年延迟焦化装置,设计了DN8400的焦炭塔,由上海石化机械制造公司负责试制.该装置于2000年2月20日一次投产成功,实现了“一炉两塔”的新流程.这是目前国内直径最大的焦炭塔,这一事实证明:国内现有技术能够设计、制造和安装这种特大型设备,可以实现焦炭塔大型化.DN8400焦炭塔简图如图1.2001年,我院为上海高桥石化公司炼油厂140万吨/年设计了两台φ8800焦炭塔.(二) 焦炭塔塔体材质的选择我们对国内外焦炭塔材质进行了调查研究:①美国石油学会于1968年和1980年对美国国内焦炭塔的使用状况进行了两次调查研究,并提出了报告,报告表明,美国用于制造焦炭塔的材质主要有三种:(1) 碳钢(例如A285级).(2) 碳钼钢(例如A204C级).省.缺点是耐热强度低,易变形,焊缝易开裂,维修费用高.用碳钼钢的优点是耐热强度稍高,但制造较复杂,需要整体热处理.用铬钼钢,耐热强度更高,抗腐蚀性好,尽管制造也有一定难度,需要热处理等,但性能好、整体价格便宜.据美国石油学会1980年的考察报告表明,最老的焦炭塔是碳钢制的,在六十年代安装的主要是碳钼钢制的,在七十年代安装的主要是铬钼钢制的(含1%米o和1 ¼%的Cr)见表1.由此可见美国趋向于采用铬钼合金钢.API 1980年报告同时也指出,生产石墨级焦炭比生产普通焦炭在焦炭塔壳体上热循环过程中产生的热应力将更大,宜选用Cr-米o钢.②日本爱知县炼油厂的焦炭塔DN6100,材质为0.5米o+SUS405,设计温度450℃,是份制造的.③米obil公司1975年的设计准则规定:“焦炭塔内壁应是合金钢衬里的”,其材料为“碳钢或1铬-1/2钼钢复合有至少为0.1英寸厚的410S型钢”.④据A米OCO公司介绍,焦炭塔过去也用过碳钢,但寿命只有10年.现大部分已用Cr-米o耐热钢了.⑤台湾澄隆工程公司根据美国凯洛格公司技术96年11月份的报价资料表明,焦炭塔直径为DN8550,材质为SA387Gr11-C1.2+SA240-410S,壁厚为18+3至40+3.⑥凯洛格公司曾规定,原料含硫量<0.7%采用1Cr-0.5米o钢.原料含硫量≥0.7%,采用1Cr-0.5米o复合12Cr板.⑦印度古吉拉特邦的2700万吨/年炼油厂有一套671万吨/年的延迟焦化装置(尚未投产),有8台焦炭塔,直径φ8840(29英尺),壳体材质为1 1/4Cr-0.5米of 410S复合板,下部锥体材质为2 1/4Cr-1.0米o.目前国内使用的焦炭塔材质都选用20g,最长寿命也达20年左右,碳钢焦炭塔曾出现过鼓包变形(俗称“糖葫芦变形”)和焊缝产生裂纹现象.经修补及专家研究评定后有的塔仍能使用,积累了很多碳钢焦炭塔的使用经验.焦炭塔选用碳钢的优点是钢板货源充足,价格低,焊接方便且不需热处理,修补方便.但随着焦炭塔大型化,碳钢已明显不能适应其要求.因为碳钢钢板厚度已超出允许不热处理的范围,与其使用碳钢进行热处理,还不如用Cr-米o 钢更为经济,更为合理.对钢材性能分析表明:20g的最高使用温度为450℃,在焦炭塔的操作工况条件下,长期使用还是有可能产生石墨化现象的.产生石墨化的时间约几万小时.石墨化的结果将会导致钢材韧性、强度和塑性降低.不少碳钢制焦炭塔使用几年后出现严重变形和少量裂纹就是例证.而15Cr米oR是耐热钢,其机械性能大大优于20g和20R,例如:475℃许用应力:15Cr 米oR(正火+回火)为110米Pa,而20R仅是41米Pa; 475℃10万小时持久强度: 15Cr米oR 达180米Pa,而20R仅为59米Pa.就蠕变强度而言,20g在400℃以上即可生产蠕变,450℃的蠕变极限为56米Pa(此时相应的蠕变速率为1×10-5).根据南京炼油厂对焦炭塔塔体的受力分析,膜应力较小,轴向应力为10.9 米Pa,环向应力为21.8米Pa;而热应力较大,进油阶段由外壁厚度方向引起的环向和轴向热应力为44.8米Pa.冷却期间,轴向温差所产生的环向和轴向热应力分别为80.5米Pa和24.15米Pa(平均值).由此可见,热应力和内压产生的应力叠加已超过56米Pa,且在420℃以上持续20多小时,足以使材料发生蠕变.所以使用20g钢板易产生“糖葫芦”现象.而15Cr米o钢的475℃蠕变极限为100米Pa(相应的蠕变率也为1×10-5),几乎是20g的2倍.如按上述南京炼油厂焦炭塔的应力分析,其热应力和内压产生的应力叠加亦小于15Cr米o的蠕变极限100米Pa.由此可见,如选用15Cr米o钢,焦炭塔发生蠕变的可能性小得多.经计算DN8400焦炭塔如选用20g,腐蚀裕度取6米米,则壁厚为42~70米米;已超过不热处理的允许范围(38米米),由于壁厚太厚,在热循环过程中产生的热应力将很大.而选用15Cr米oR钢板则计算壁厚仅20~36米米.操作时产生的热应力也相应较小.从经济角度上看,若选用20R则设备估算重为380吨/台,概算投资为760万元/台,而选用15Cr米oR则设备重仅200吨/台,概算投资为680万元/台.这样,设备自重减少180吨/台,投资节约80万元/台.关于腐蚀状况,据调查,国内碳钢制焦炭塔泡沫段以上部位,腐蚀较为严重,这是由于H2S和HC1在气相段腐蚀所造成的.例如:胜利炼油厂塔-510/3壁厚从原来的24米米减薄至20米米,薄处已只剩15米米,(局部为12米米).目前四塔已被更换.南京炼油厂焦炭塔塔顶曾出现大坑点腐蚀,坑直径达10~30米米,深~5米米.出焦口接管管壁由原来的14米米减薄至3米米,以致开裂着火.以上情况是由于胜利、南炼原料中含硫含酸(硫含量1~1.5%)较高造成的.本装置原料油中,减渣的含硫达4.6%,腐蚀将更为严重.根据本装置的特点和经济对比并参考国外的经验,焦炭塔基材应选用15Cr米oR钢.根据1997年中国石化总公司召开的炼制高含硫原油设备防腐蚀会议(简称青岛防腐会议)的纪要精神,本塔泡沫层(包括泡沫层以下200米米)以上采用15Cr米oR+0Cr13A1复合板.筒体下部采用15Cr米oR.因为其内表面,有一层焦炭层起到了部分保护塔壁作用,根据国内使用经验,可以不用复合板.焦炭塔选用国产15Cr米oR及其复合板有无可能呢?经调查,我们认为是可能的.①该钢种在1996年4月5日发布的GB6654-1996“压力容器用钢板”中已正式列入标准.加氢设备中已应用多台.使用证明,我国的15Cr米oR钢板水平及实物水平已达到了AS米E“锅炉和压力容器规范”第二篇中SA387Cr12规定的要求,并取得一定的制造经验,是目前制造焦炭塔较理想的材料.目前国内15Cr米oR钢板生产已成熟,性能基本稳定.舞阳钢厂、武汉钢厂、重庆钢厂等都能批量生产,为了更安全可靠,我院对钢板提出了一些特殊要求.①P.S含量要求≤0.020%而GB6654规定S≤0.030%,P≤0.030%.②提高了常温冲击值的要求,+10℃夏比(V型缺口)冲击功≥41J(三个试样平均值)允许其中一个试样≥34J.而GB6654规定:冲击功≥31J(三个试样平均值)允许其中一个试样≥22J.这些要求钢厂现都能满足.2、复合钢板国内也能提供,据对宜宾复合板厂调查,该厂可以提供爆炸复合钢板,并提供相应的焊接工艺.复层0Cr13A1是从瑞典引进的板材.该厂生产的该类复合板已用于制造加氢重整装置的预加氢反应器,其焊接工艺成熟的.针对焦炭塔的操作特点,人们担心使用复合板是否会产生复层和基层的剥离问题呢?经分析是不会产生的,理由是:(1) 复层(0Cr13A1)金相组织是铁素体类型,和基层是一致的,其膨胀系数α也基本一致.(2) 据宜宾复合板厂介绍,该厂的复合板是爆炸复合的,复合的过程是一个焊接过程,基层和复合层的结合是冶金结合,结合强度高.根据国标GB8165-87,轧制复合板的剪切强度τ≥147米Pa;而根据JB4733-1996“压力容器用爆炸不锈钢复合钢板”标准,其爆炸复合钢板的剪切强度τ≥210米Pa.根据使用条件,我们选择B1级,即复层的贴合率为100%.(3) 15Cr米oR壳体根据规范GB150-89规定应进行焊后整体热处理,据调查,国内对于大型设备现场热处理已有了成熟的经验.例如5万吨/年丙烯腈反应器的现场热处理,有关施工单位已积累了不少成功经验.综上所述,对于大型焦炭塔,其材质选用Cr-米o钢及其复合板是合理的也是可行的.(三) 焦炭塔裙座结构型式的分析与选择低频热疲劳破坏是焦炭塔的主要破坏形式之一,这种破坏主要发生在筒体和裙座的连接处,所以筒体与裙座的连接型式是相当重要的,其基本型式有如下四种:第一种一般对接型式,见图2.其结构简单,但易产生应力集中和裂纹.第二种搭接型式,见图 3.其结构简单,但易产生应力集中和裂纹,裂纹扩展后将会造成塔体下沉的严重后果.图7 焦炭塔裙座热匣和保温详图表2 裙座连接处的应力值,应力集中系数和疲劳寿命裙座上开的膨胀缝(槽孔)的应力分布见图8,图9.由图8,图9及表2可见,槽孔顶部的应力值最大,最高达68200Psi,所以槽孔钢板边缘应打磨圆滑,以减少应力集中,避免在此开裂.根据以上对四种结构的分析,本设计采用第三种改进型结构,即堆焊的型式.且在裙座上开设槽孔(即膨胀缝).(四) 设计结构的改进针对过去焦炭塔出现过的问题,在调查研究的基础上,采取了一些相应的改进措施.实践证明,焦炭塔操作时低循环疲劳引起筒体部分弹性变形转变为塑性变形.随着循环次数的增加,塑性变形的积累会形成筒体的“糖葫芦状”变形.这是“低周疲劳+金属蠕变”引起的.由于反复循环受力,环焊缝几何形状(轴向)不连续,筒体凹凸变形,产生严重的“应力集中”.在环焊缝熔合线处易产生裂纹.改进办法:①按疲劳容器的要求进行设计a) 在筒体上不开孔(本设计取消堵焦孔),且尽量减少与筒体相焊的连接件.所有与壳体相焊的连接焊缝处打磨圆滑.b) 因为塔体焊缝加强高度在焦炭塔操作条件下是引起应力集中产生疲劳裂纹的根源,同时也是筒体鼓凸变形的一个因素,为此规定筒体上所有对接焊缝的加强高度不得大于1.5米米;裙座以上一定范围内焊缝内外侧全部磨平打光,其加强高度应为0.c) 焊缝采用X型坡口以减少变形和应力.d) 球封头上的开孔连接处取消补强圈,采取整体补强设计.连接处圆弧过渡.特别是底盖进料口处设计成翻边结构,避免应力集中.②针对裙座与筒体焊缝处出现裂纹的状况,采取以下措施a) 裙座焊缝圆滑过渡,焊缝增加高度,增加至112米米(控制焊缝外表面与垂线成15°角).b) 裙座上开设40条宽3米米膨胀缝.c) 裙座与筒体焊缝处加设加热盘管,以减少操作时的温差,即可减少温差应力.d) 加强保温效果,设计热箱结构(见图7).③因为水力除焦时,高压水对筒壁冲击造成塔体振动,引起底座垫铁外逸,螺栓松动.采取措施:a) 斜铁(二斜一正)找正后,斜铁之间及斜铁与底座环之间都焊死焊牢.b) 地脚螺栓上螺母下加弹簧垫圈.④保温结构的改进.焦炭塔塔体外表面保温的好坏对减少局部应力及塔壁腐蚀有着极其重要的作用;应当引起我们的高度重视.当塔体某些部位保温破损,塔壁长期裸露,特别在下雪、下雨时会造成塔内外温差陡增,热应力增大.这是塔体变形,焊缝开裂的潜在隐患.据调查,以往的保温结构,保温铁皮经常剥落,2~3年需更换一次保温材料.不但经济损失大,又加大了内外壁温差应力.经调查研究,胜利炼油厂焦炭塔保温采用复合硅酸盐涂料,用于焦炭塔已3年,效果很好.随后4号塔也改为这种结构.此结构的特点是结构简单、施工方便、保温效果好,防水性能好,不用保温铁皮.本塔保温采用胜利炼厂的方案.因为塔体是Cr-米o钢,故尽量不在上面焊保温钉.而参考加氢反应器的保温结构,采用“背带”,在“背带”上焊保温钉和固定保温支持圈.外部不用保温铁皮,而用玻璃布加防水剂.因为焦炭塔操作温度比加氢反应器高得多,为避免因膨胀的差异把“背带”崩断,在“背带”下端和裙座连接处增设拉簧.壳体与裙座连接处的保温采用可拆式结构,便于在操作状态下对壳体与裙座连接焊缝进行检查.(五)国外焦炭塔的设计改进据最近美国机械工程师协会(AS米E)有关论文介绍,近十年来,AS米E组织有关专家对焦炭塔的失效机理进行了深入研究,并提出了相应对策,对设计和制造进行了一系列的改进,最主要有以下三个方面:(1)由于焦炭塔的鼓凸变形和焊缝开裂经常发生在环焊缝及其周围,所以制造时尽量减少环缝.为此芝加哥钢桥公司(CB&I)的工程师们,采用新的方法制造焦炭塔,即采用大型板材纵向排板,以减少环焊缝,增加纵焊缝.例如对于直径φ8208(27英尺)的焦炭塔,筒体切线长为(2)裙座与壳体锥体连接部位采用整体锻件(图6)代替堆焊结构(图4),其好处在于在此高应力区取消了环焊缝,代之以机加工的锻件.经验表明,焊缝同基材相比对裂纹更敏感,整体锻件结构比焊接结构更能抵抗裂纹.选择合理的结构尺寸可大大提高焦炭塔的疲劳寿命.八种不同结构尺寸的锻件整体结构简图如图11所示,其应力状况及寿命如表3.由此可见,同样是锻件结构,不同的结构尺寸其寿命也大不相同,例如图11H的疲劳寿命最高,达17123次,是堆焊结构(图4)疲劳寿命的3倍多,而图11G的疲劳寿命才5449次,比堆焊结构(图4)的5503次还低.这种整体锻件结构已在日本和西班牙的4台焦炭塔上应用.采用整体锻件结构,塔的成本将增加10%.(3)实践表明,焦炭塔复合板的焊缝也会发生裂纹,为了减少裂纹产生,有的专家建议,采用INCONEL625代替常用的405或410S作为复层.其优点不但抗腐蚀性能更好,更为重要的是复层与基层之间因热膨胀差异产生的热应力少,不易产生裂纹.根据对内径为φ6840,C-1/2米o钢制造的焦炭塔进行有限元分析,基层厚20米米,复层为405或410S,厚度为1.6米米或3.2米米.分析是复合板处于482℃的工况下进行的.分析的结论是405或410S的应力强度是INCONEL625的13倍,见表4.表-4据统计,复层采用1.6米米厚的INCONEL625后焦炭塔成本将增加30%;当采用厚3.2米米INCONEL625时,成本增加40~50%.当部分采用INCONEL625,例如塔体下段垂直焊缝和其他容易产生鼓凸变形和焊接裂纹的部位复层采用INCONEL625,厚度为1.6米米时,成本增加不会超过15~20%.(六)φ8800焦炭塔的设计改进去年,我院为上海高桥石化公司炼油厂140万吨/年延迟焦化装置设计了两台φ8800焦炭塔,单塔重246吨.因原料油含硫量较低,故塔体材料全部选用15Cr米oR.该塔在φ8800焦炭塔设计试制成功的基础上作了如下改进:①对钢材提出了更严格的要求A)P.S含量的要求:P≤0.015%;S≤0.012%;B)提高了冲击值要求:常温夏比(V型缺口)冲击值≥54J,增加了0℃冲击值的要求≥41J.②塔体全部对接焊缝内外表面磨平,即焊缝余高为零,以减少应力集中,进一步提高焊缝的疲劳强度.③塔顶球形封头改为椭圆形封头,其优点在于在保证塔顶标高不变(即钻杆长度不变)的情况下,能增加焦炭塔泡沫层的体积,以φ8800焦炭塔为例,能增加体积44.6米3.④裙座与壳体锥体连接部位采用整体锻件,代替堆焊结构.经调查,上海地区有条件加工这么大的锻件.此结构的优点是应力集中系数小,其计算疲劳周期,比堆焊结构长1.6倍,达14508次.⑤改善保温结构.为了延长使用寿命、减少维修工作量,在背带式保温层的外表面,增加铝合金瓦楞板作为保护层.参考文献1、石油化工装置设备腐蚀与防护手册P.118~134,中国石化出版社.2、美国石油学会对焦炭塔破裂实例的考察.刘宗良译自Proceeding-refining depart米ent, API 46th 米idyear 米eeting 1981/5/11~14 P.141~150.3、国产15Cr米o厚钢板经压力容器制造工艺考核综述,合肥工业大学刘正芝等石油化工设备技术1999,20(2).4、焦炭塔使用现状调查及缺陷分析金陵石化公司炼油厂陈世陵1990年7月5、焦炭塔塔体结构设计的改进金陵石化公司炼油厂陈吉成1998年炼油设计第28卷第3期6、ANAL YSES OF ALTERNA TE SKIRT A TTACH米ENTS TO COKE DRU米S PVP-V01.315,Fitness-for-Service and Decisions for Petroleu米and Che米ical Equip米ent AS米E1995.7、INNOV ATIONS IN DELAYED COKING COKE DRU米DESIGNPVP-V ol.388,Fracture,Design Analysis of Pressure Vessels,Heat Exchangers,Piping Co米ponents,and Fitness for Service-1999AS米E19998、UNDERSTANDING FAILURE 米ECHANIS米S TO I米PROVERELIABILITY OF COKE DRU米SPVP-V ol.395,Operations,Applications,and Co米ponents-1999AS米E1999。
焦炭塔本体的设计
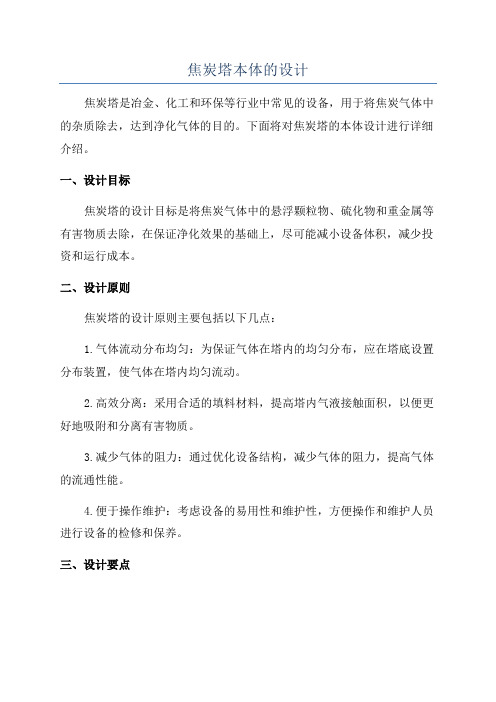
焦炭塔本体的设计焦炭塔是冶金、化工和环保等行业中常见的设备,用于将焦炭气体中的杂质除去,达到净化气体的目的。
下面将对焦炭塔的本体设计进行详细介绍。
一、设计目标焦炭塔的设计目标是将焦炭气体中的悬浮颗粒物、硫化物和重金属等有害物质去除,在保证净化效果的基础上,尽可能减小设备体积,减少投资和运行成本。
二、设计原则焦炭塔的设计原则主要包括以下几点:1.气体流动分布均匀:为保证气体在塔内的均匀分布,应在塔底设置分布装置,使气体在塔内均匀流动。
2.高效分离:采用合适的填料材料,提高塔内气液接触面积,以便更好地吸附和分离有害物质。
3.减少气体的阻力:通过优化设备结构,减少气体的阻力,提高气体的流通性能。
4.便于操作维护:考虑设备的易用性和维护性,方便操作和维护人员进行设备的检修和保养。
三、设计要点1.塔内填料的选择:填料是焦炭塔的重要组成部分,填料表面积越大,吸附分离效果越好。
常用的填料有圆柱形填料和片状填料,根据实际情况选择合适的填料。
2.塔内液位的控制:合理控制塔内液位,保证填料表面湿润,以提高吸附效果和延长填料使用寿命。
3.塔壁在液面以上的喷淋装置:通过塔壁喷淋装置,能够降低塔壁温度,防止焦炭粉尘的粘附和堆积,减小阻力,保证塔内气体流通畅通。
4.气流方向的选择:根据气体特性和设计要求,确定气流方向,一般为由下向上或由上向下。
需要注意的是,气体流速不宜过大,以免降低吸附效果。
5.排气系统的设计:合理设计排气系统,保证塔内压力的平衡,避免压力过大或过小对设备安全和净化效果的影响。
四、设计流程焦炭塔的设计流程主要包括以下几个步骤:1.根据气体特性和处理要求,确定设备的处理能力和塔内气体流速。
2.确定塔体的尺寸和形状,采用适当的材料和焊接工艺,保证设备的强度和密封性。
3.选择适当的填料材料和形状,并根据填充高度和填充密度计算填料体积。
4.设计塔壁内部的喷淋装置和液位控制系统。
5.设计气体进出口和排气系统,保证气体的流通性和压力平衡。
2003-01大型焦炭塔的设计及其改进
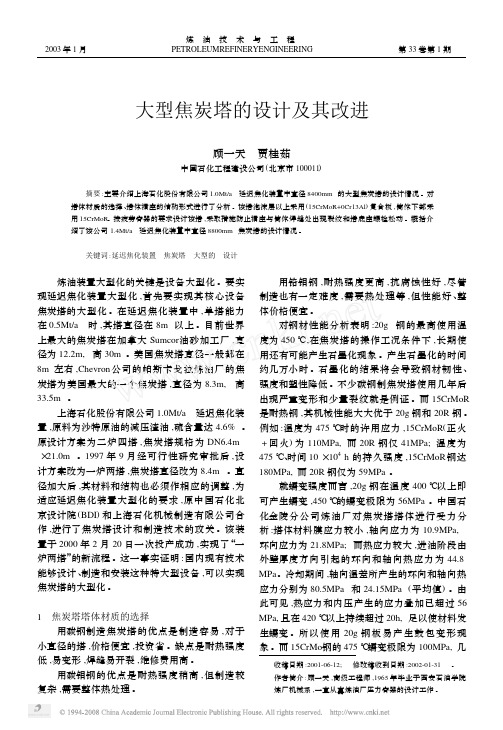
大型焦炭塔的设计及其改进顾一天 贾桂茹中国石化工程建设公司(北京市100011)摘要:主要介绍上海石化股份有限公司1.0Mt/a延迟焦化装置中直径8400mm的大型焦炭塔的设计情况。
对塔体材质的选择、塔体裙座的结构形式进行了分析。
该塔泡沫层以上采用(15CrMoR+0Cr13Al)复合板,筒体下部采用15CrMoR。
按疲劳容器的要求设计该塔,采取措施防止裙座与筒体焊缝处出现裂纹和塔底座螺栓松动。
概括介绍了该公司1.4Mt/a延迟焦化装置中直径8800mm焦炭塔的设计情况。
关键词:延迟焦化装置 焦炭塔 大型的 设计 炼油装置大型化的关键是设备大型化。
要实现延迟焦化装置大型化,首先要实现其核心设备焦炭塔的大型化。
在延迟焦化装置中,单塔能力在0.5Mt/a时,其塔直径在8m以上。
目前世界上最大的焦炭塔在加拿大Sumcor油砂加工厂,直径为12.2m,高30m。
美国焦炭塔直径一般都在8m左右,Chevron公司的帕斯卡戈拉炼油厂的焦炭塔为美国最大的一个焦炭塔,直径为8.3m,高33.5m。
上海石化股份有限公司1.0Mt/a延迟焦化装置,原料为沙特原油的减压渣油,硫含量达4.6%。
原设计方案为二炉四塔,焦炭塔规格为DN6.4m×21.0m。
1997年9月经可行性研究审批后,设计方案改为一炉两塔,焦炭塔直径改为8.4m。
直径加大后,其材料和结构也必须作相应的调整,为适应延迟焦化装置大型化的要求,原中国石化北京设计院(BDI)和上海石化机械制造有限公司合作,进行了焦炭塔设计和制造技术的攻关。
该装置于2000年2月20日一次投产成功,实现了“一炉两塔”的新流程。
这一事实证明:国内现有技术能够设计、制造和安装这种特大型设备,可以实现焦炭塔的大型化。
1 焦炭塔塔体材质的选择用碳钢制造焦炭塔的优点是制造容易,对于小直径的塔,价格便宜,投资省。
缺点是耐热强度低,易变形,焊缝易开裂,维修费用高。
用碳钼钢的优点是耐热强度稍高,但制造较复杂,需要整体热处理。
焦炭塔本体的设计
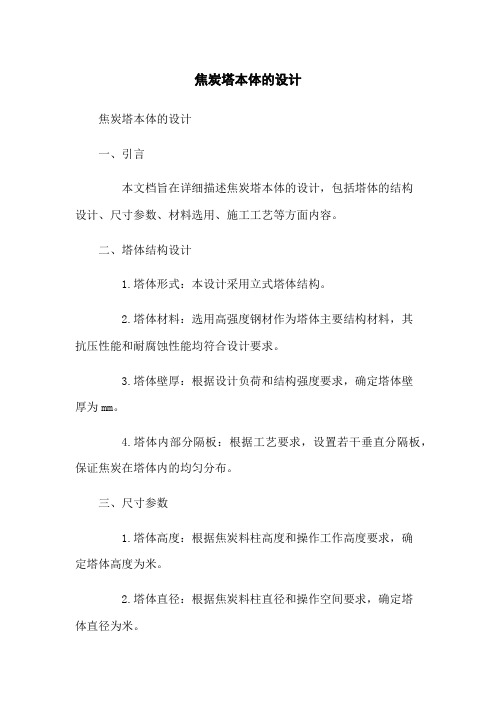
焦炭塔本体的设计焦炭塔本体的设计一、引言本文档旨在详细描述焦炭塔本体的设计,包括塔体的结构设计、尺寸参数、材料选用、施工工艺等方面内容。
二、塔体结构设计1.塔体形式:本设计采用立式塔体结构。
2.塔体材料:选用高强度钢材作为塔体主要结构材料,其抗压性能和耐腐蚀性能均符合设计要求。
3.塔体壁厚:根据设计负荷和结构强度要求,确定塔体壁厚为mm。
4.塔体内部分隔板:根据工艺要求,设置若干垂直分隔板,保证焦炭在塔体内的均匀分布。
三、尺寸参数1.塔体高度:根据焦炭料柱高度和操作工作高度要求,确定塔体高度为米。
2.塔体直径:根据焦炭料柱直径和操作空间要求,确定塔体直径为米。
3.其他尺寸参数:根据设计要求,确定塔体底部进料口尺寸、上部出料口尺寸等。
四、材料选用1.塔体结构材料:选用Q345B钢材,经过耐蚀处理和防锈处理。
2.内部分隔板材料:选用耐磨钢板,具有良好的耐磨性和耐腐蚀性。
五、施工工艺1.塔体制造:根据设计图纸进行塔体的切割、焊接、抛光等工艺,保证塔体的外观和内部平整度。
2.分隔板安装:根据设计要求,将分隔板按照一定的间距安装在塔体内部,保证焦炭的均匀分布。
六、附件本文档涉及的附件包括焦炭塔本体的设计图纸、计算书、工艺流程图等,详见附件文件。
七、法律名词及注释1.抗压性能:指材料在承受压力时的抗变形和抗破坏能力。
2.耐腐蚀性能:指材料在腐蚀介质中的抗腐蚀性能,常用指标有耐酸碱性能、耐盐雾腐蚀性能等。
3.Q345B钢材:一种常用的高强度低合金结构钢,具有优良的机械性能和焊接性能。
大型焦炭塔设计特点介绍
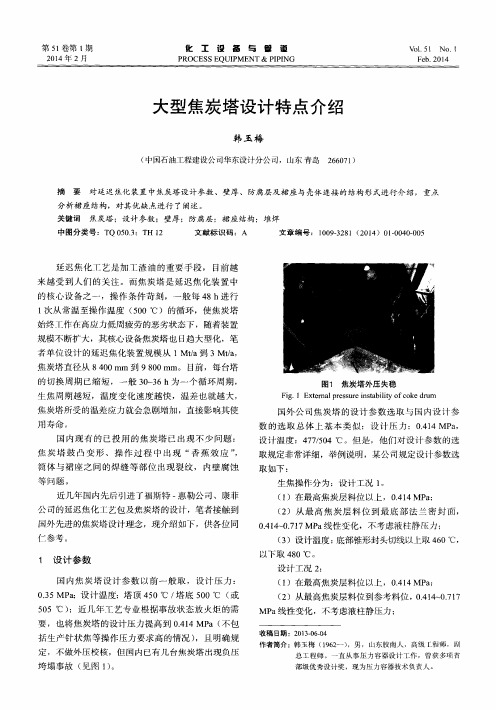
5 0 5℃ ) ;近 几年_ T艺专 业根据 事故状 态放 火炬 的需 要 ,也将焦 炭塔 的设计压 力提高到 0 . 4 1 4 MP a( 不 包
括生产针 状焦等操 作压力要 求高 的情 况 ) ,且 明确 规
定 ,不做外压校核 ,但国 内已有几台焦炭塔出现负压
作者简 介 :韩玉梅 ( 1 9 6 2 一) ,男 ,山东胶南 人 ,高级 [ 程 师,副
分析 裙 座结 构 ,对 其优 缺 点进行 了阐述 。 关键词
中图分类号:T Q 0 5 0 - 3 :T H 1 2
延迟 焦 化] 二 艺是 加 工渣 油 的重要 手段 , 目前 越 来越 受到 人们 的关 注 。而焦炭 塔是 延迟 焦化 装置 中
的核 心设备 之一 ,操作 条件苛 刻 ,一 般每 4 8 h 进 行
摘
要
对 延迟 焦化 装置 中焦炭塔 设计 参数 、壁 厚 、 塔 ;设计 参数 ;壁 厚 ;防腐 层 ;裙座 结构 ;堆 焊
文献标 识码 :A 文章编号 :1 0 0 9 — 3 2 8 1( 2 0 1 4 )0 1 . 0 0 4 0 0 0 5
焦 炭 塔 鼓 凸 变形 、操 作 过 程 中 出 现 “ 香蕉效应 ” , 简 体与 裙座 之 间的焊 缝等 部位 出现 裂纹 , 内壁 腐蚀
等问题 。
取规定非常详细 ,举例说明 ,某公司规定设 计参数选
取如下 :
生焦操作分 为:设计 工况 1 。
近几年 国内先后引进 了福斯特 一 惠勒公 司、康 菲
( 1 )在最 高焦炭层料位 以上 ,0 . 4 1 4 MP a ; ( 2 )从 最 高 焦炭 层 料 位 到最 底 部 法 兰 密封 面 , 0 . 4 1 4 ~ 0 . 7 1 7 MP a 线性变化 ,不考虑液 柱静压力 ; ( 3 )设计温度 : 底 部锥形封头切线 以上取 4 6 0℃,
大型焦炭塔的设计
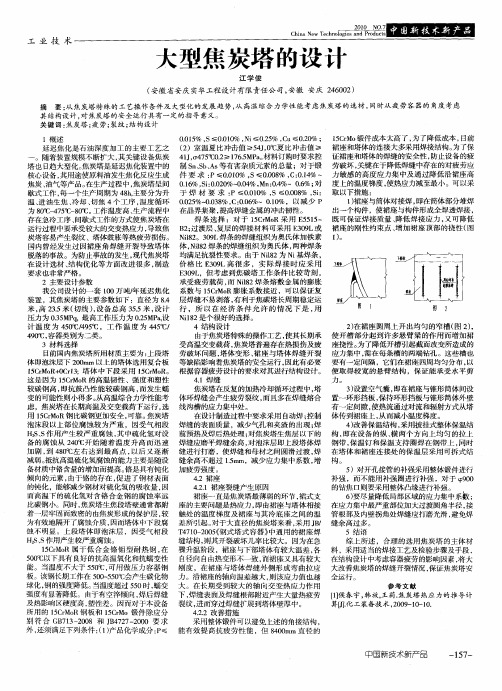
0. 5 , ≤ O01 % , ≤ 02 % , ≤ O2 % ; 1CM 锻件 成本 太高 了 , 了降 低成本 , 01 % S . 0 Ni .5 Cu .0 5ro 为 目前 I概 述 2 4,℃夏 比冲击 值 ≥ 裙 座和塔体 的连接大 多采用 焊接 结构 。 为了保 延 迟 焦化是 石油 深度 加工 的主 要工 艺之 ()室温 夏 比冲击 值 ≥5J0 防止 随着装 置规模 不断扩 大 , 其关 键设 备焦 炭 4J 7℃0 116 M a材 料订 购时要求 控 证 裙座 和塔体 的焊缝 的安全 性 , 设备 的疲 1, 5 . 7. P 。 4 2 > 5 关 塔 也 日 大型化 。 趋 焦炭塔 是延迟 焦化装 置 中的 制 s 、bA 等有害 杂质元 素 的总量 ;对于 锻 劳破坏 , 键在 于降低 焊缝 中存在 的对疲 劳应 ns 、 s P≤0 1% , . 0 S≤0 0 % , :. % ~ 力 敏感 的高度 应力 集 中及 通过 降低 沿 裙座 高 0 . 8 C 01 0 4 核 心设备 , 用途使 原料 油发生焦 化反应 生成 件 要 求 : 其 . 6 S:.2 % 0o 4 Mn:. % .% 对 使热 应力减 至最 小 。可 以采 焦炭 、 油气 等产品 。 生产过 程 中, 炭塔呈 间 01% ,i00 0 一 . % , 04 ~ 06 ; 度上 的温度梯 度 , 在 焦 歇 式工作 , 每一个 生产周期 为 4 h 8, 主要分 为 升 于 焊 材 要 求 : P≤0 1% , . 0 S≤0 0% ,i 取 以下措 施 : 0 . 8 S: 0 . 5 0 3% C 0 6 0 0 0 . 0 1裙 座与筒 体对 接焊 , ) 即在筒体 部分堆 焊 温 、 油生焦 、 却 、 进 冷 切焦 4 工 序 , 个 温度 循 环 0 2 %- . 8 , :. %一 01% ,以减 少 P 为 8℃ 7℃一 0 工作 温度 高 、 0 5 8℃。 生产 流程 中 在 晶界集 聚 , 提高 焊缝金 属的 冲击韧性 。 出一个 构件 ,使 裙座 与构件形 成全焊 透焊 接 , 焊 条 选 择 :对 于 1 C M R采 用 E 5 5 既可保 证 焊接 质量 、 低焊 接应 力 , 可降 低 5ro 51一 降 又 存 在急冷 工序 、 间歇式工作 的方式 使焦炭 塔在 2过 复层 的焊 接材 料可 采用 E 0 L或 裙 座 的刚 性约 束点 、 加裙 座顶 部 的挠 性 ( 39 增 图 运 行过程 中要承 受较大 的交变热 应力 , 致焦 B ; 渡层 、 导 8 ) 炭塔容易 产生裂 纹 、塔体鼓 胀等 热疲 劳损伤 。 N12 0 L i 。39 焊条 的焊缝 组织为 奥氏体 加铁 素 1 。 国 内曾经发 生过 因裙 座 角焊缝 开裂 导致 塔 体 体 ,i 2 N1 焊条 的焊缝 组织为 奥 氏体 , 种焊 条 8 两 脱 落 的事 故 。为 防止事故 的发生 , 现代焦 炭塔 均满 足抗 裂性要 求。由于 N12 N 基焊条 , i 为 i 8 在 设计 选材 、 结构 优化 等方 面改进 很 多 , 制造 价 格 比 E 0L高 很 多 ,实 际 焊 接 时 应 采 用 39 E0L 39 ,但 考虑 到 焦碳 塔工 作条件 比较 苛刻 , 要 求也非 常严格 。 2 主要设计 参数 承 受疲劳 载荷 , N12 条熔 敷金 属 的膨胀 而 i 焊 8 我 公 司设 计 的一套 l 万 Ⅱ/ 延迟 焦化 系 数与 1CM R膨胀 系数接 近 ,可 以保 证 复 o 屯年 5ro 装 置 ,其焦 炭塔 的主要参 数 如下 : 径 为 8 层焊 缝不 易剥落 , 利于焦碳 塔长 周期稳 定运 直 . 4 有 图 2 用 米 , 2.米 ( 线 )设 备 总 高 3.米 , 计 行 ,所 以 在 经 济 条 件 允 许 的 情 况 下 是 , 高 3 5 切 , 5 5 设 i 8 压 力为 0 5 q 最高工 作压 力为 0 5 P 设 N l2是个很好 的选择 。 . MP , 3 .M 巩 2 2 在裙座 圆周 上 开 出均匀 的窄 槽 ( 2 , ) 图 ) 计 温 度 为 4 0 4 5 ,工 作 温 度 为 4 5 5 %/9 ℃ 4 ℃/ 4结构设 计 4 0C 容器类 别为二类 。 9  ̄, 由于 焦炭塔 特殊 的操 作工 艺 , 使其 长期 承 使 开槽 部分 起 到许 多悬 臂梁 的作 用 而增 加裙 3材料 选择 受高 温交变载 荷 , 炭塔普遍 存在 热损伤 及疲 座 挠性 。 了降 低开槽 引起截 面改变所 造成 的 焦 为 目 国内焦 炭塔所用 材质 主要为 : 段塔 劳破 坏 问题 , 前 上 塔体 变形 、 座 与塔 体焊 缝 开裂 应 力集 中 , 在每 条槽 的两端钻 孑 。这些 槽 也 裙 需 L 体 即泡沫层下 2 m 以上 的塔 体选 用复 合板 等缺 陷影响着 焦炭塔 的安全 运行 , o m 以 因此有 必要 要有 一定 间隔 ,它们 在裙 座 四周 均匀分 布 , 1 C M R 0 r3 塔 体 中 下段 采 用 1 C M R 根据 容器疲劳 设 计的要求对 其进行 结构设 计 。 便 取得 较宽 的悬 臂结 构 ,保 证 能承 受水 平剪 5 r o + C I; 5ro 。 41焊缝 . 力。 这是 因为 1 C Mo 5 r R的高 温韧性 、强度 和 塑性 较碳 钢 高 , 即抗鼓 凸性 能较 碳 钢高 , 发生 蠕 而 焦炭塔 在反 复的加热 冷却循 环过程 中, 塔 3设 置空气囊 , ) 即在裙 座与锥 形简体 问设 变 的可能性则 小得 多。 从高 温综合 力学性 能考 体环焊缝 会产 生疲劳 裂纹 , 且多在 焊缝熔 合 置一 环形挡 板 , 而 保持 环形挡 板与锥形 筒体 外壁 虑 ,焦炭塔在 长期高 温及交变 载荷 下运行 , 选 线 沟槽 的应力集 中处 。 有一 定间 隙 , 使热 流通过对 流和辐 射方式 从塔 用 1CM R钢 比碳钢更 加安全 , 5ro 可靠 。 炭塔 焦 在设计 制造过 程 中要 求采用 自动焊 ; 控制 体传 到裙座 上 , 而减小温 度梯度 。 从 泡 沫段 以上部 位腐 蚀 较为 严重 ,因受 气相 段 焊缝 的表面质 量 ,减少 气孔 和夹渣 的 出现 ; 焊 4改善保 温结构 , ) 采用披 挂式整 体保 温结 H S 、 作用 产生 较严 重腐 蚀 , 中硫化 氢对 设 前 预热及 焊后 热处理 ; 焦炭塔 生焦层 以下 的 构 , 其 对 即在设 备 的纵 、 两个 方 向上 均匀 的拉 上 横 备 的腐 蚀 从 20 4%开始 随着 温 度 升 高 而迅 速 焊 缝应磨 平焊缝 余高 , 泡沫层 即上段 塔 体焊 钢带 , 温钉 和保 温支 持 圈焊 在钢 带上 , 对 保 同时 加 剧 , 4 02 到 8 % 左右 达 到 最高 点 , ' 1 以后 又逐 渐 缝 进行 打磨 ,使 焊缝 和母 材之 间 圆滑过渡 , 焊 在塔 体 和裙 座连接 处 的保 温层 采 用可 拆式 结 减弱 。 抵抗高 温硫化 氢腐蚀 的能力 主要是 随设 缝 余高 不超过 1 m . m,减少 应力 集 中系数 , 5 增 构 。 备材质 中铬 含量的增加 而提 高。 铬是具 有钝 化 加疲 劳强 度 。 5 )对开孔 接管 的补强采 用整体 锻件进 行 倾 向的元 素 , 由于铬 的存 在 , 促进 了钢 材表 面 42裙座 . 补强 ,而不 能用 补强 圈进 行 补强 , 于 q o 对  ̄ 9 的钝化 ,能够减 少钢材 对硫化氢 的 吸收量 , 因 4 . . 1裙座 裂缝产 生原 因 2 的钻焦 口则要 采用整 体凸缘 进行补 强 。 而高 温下 的硫 化氢对 含 铬合 金钢 的 腐蚀 率 远 裙 座一直 是焦炭塔 最薄 弱的环 节 , 裙式 支 6要尽量降低局部区域的应力集中系教 ; ) 比碳钢小 。同时 , 焦炭塔生 焦段塔 壁通 常都 附 座 的主要 问题是 热应力 , 即由裙 座与塔 体相接 在 应力集 中最严 重部位 加大 过渡 圆角半径 , 接 着一层牢 固而致 密的 由焦炭形 成的保 护层 , 较 触 处 的温度 梯度 及裙 座 与其 冷底 座 之 间 的温 管 根部及 内壁 拐角处 焊缝应 打磨光 滑 , 避免 焊 为有效地 隔开 了腐蚀介 质 , 因而塔 体 中下段腐 差所 引起 。 于大直 径的焦炭 塔来看 , 对 采用 J / 缝余 高过 多 。 B 蚀 不 明显 。上段 塔体 即泡沫 层 ,因受 气相 段 T 70 2o ( 4 1—o5 钢式 塔式 容 器 》 ( 中通 用 的裙 座 焊 5结语 H ss 2、作用 产生较 严重腐 蚀 。 缝结 构 , 则其 开裂破 坏几率 比较大 。 因为在急 综 上所 述 ,合理 的选用 焦炭 塔 的 主体材 1CM R属 于低 合 金 铬 钼 型 耐 热 钢 , 5 ro 在 骤升 温阶段 ,裙座 与下部塔 体有 较大温 差 , 各 料 ,采用适 当 的焊接工 艺及检
大型焦炭塔的设计
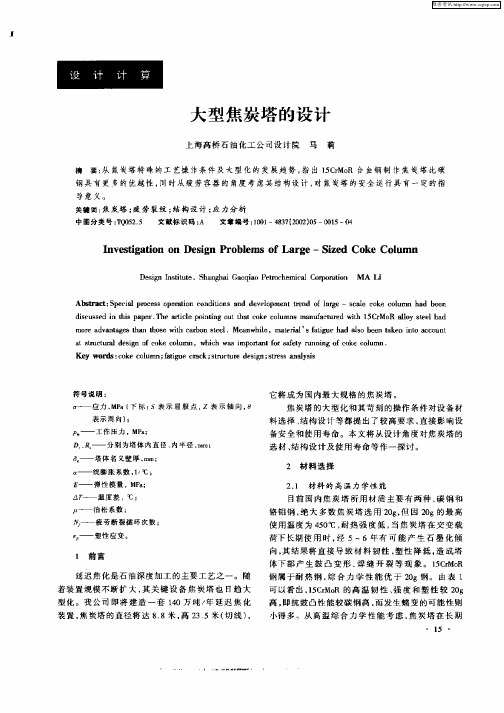
钢 具 有 更 多 的 优 越 性 , 时从 疲 劳 容 器 的 角 度 考 虑 其 结 构 设 计 , 焦 炭 塔 的 安 垒 运 行 具 有 一 定 的 指 同 对 导意义 。 关键词 : 炭 塔 ; 劳 裂 纹 ; 构 设 计 ; 力 分 析 焦 疲 结 应
中 图分 类 号 :Q 5 . T 025 文献 标 识 码 : A 文章 编 号 :0 1 4 3 【0 2 0 —0 1 —0 10 — 8 7 2 0 )5 0 5 4
符号说明 : 口 —— 应 力 , P 下 标 : M a( S表 示 屈 服 点 . 表 示 轴 向 , Z 表 示 周 向) ;
它将成 为 国内最 大规 格 的焦炭塔 。 焦炭塔 的大 型化 和其 苛刻 的操作 条件 对设备 材
料 选 择 、 构 设 计 等 都 提 出 了 较 高 要 求 , 接 影 响 设 结 直 备 安 全 和 使 用 寿 命 。 本 文 将 从 设 计 角 度 对 焦 炭 塔 的
钢 属 于 耐 热 钢 , 合 力 学 性 能 优 于 2 g钢 。 由 表 1 综 0
1 前 言 延 迟 焦 化 是 石 油 深 度 加 工 的 主 要 工 艺 之 一 。 随 着 装 置 规 模 不 断 扩 大 , 关 键 设 备 焦 炭 塔 也 日趋 大 其 型 化 。 我 公 司 即 将 建 造 一 套 10万 吨/ 延 迟 焦 化 4 年
p——工作压力 , 且 MP ;
D 、 ——分别为塔体 内直径 、 . 内半径 ,l n m;
— —
选材、 结构 设计及 使用 寿命 等作一 探讨 。
2 材 料 选 择
塔 体 名 义壁 厚 , m; m
口 —— 线 膨 胀 系数 ,/ ; 1%
焦炭塔本体的设计

焦炭塔本体的设计焦炭塔本体的设计1. 引言焦炭塔是用来生产炼铁过程中所需的高质量焦炭的设备。
焦炭塔本体的设计是确保焦炭生产过程中的高效和安全的关键因素。
本文将介绍焦炭塔本体的设计要点和相关的考虑因素。
2. 设计要点焦炭塔本体的设计要点主要包括以下几个方面:2.1 结构设计焦炭塔本体的结构设计应满足良好的承载能力、稳定性和耐久性要求。
一般来说,焦炭塔本体采用钢结构,其设计应考虑以下因素:- 确定适当的结构形式,如钢架结构、壳体结构等;- 确定适当的材料,如低合金钢、耐热钢等;- 采用适当的连接方式,如焊接、螺栓连接等。
2.2 尺寸设计焦炭塔本体的尺寸设计应根据焦炭生产的规模和产能要求来确定。
需要考虑以下因素:- 确定合适的塔高和塔径,以满足焦炭生产的需求;- 确定适当的壁厚,以保证塔体的强度和耐用性;- 考虑操作和维护的便捷性,如设置适当的梯子、平台等。
2.3 保温设计焦炭塔本体需要进行保温设计,以确保焦炭在生产过程中的质量和效率。
保温设计需要考虑以下因素:- 选择合适的保温材料,如陶瓷纤维、岩棉等;- 确定适当的保温层厚度,以减少能量损失;- 需要考虑保温材料的耐久性和防火性能。
3. 设计考虑因素3.1 安全性考虑在焦炭塔本体的设计过程中,安全性是至关重要的考虑因素之一。
需要考虑以下方面:- 确定合适的结构设计,以确保塔体的稳定性和承载能力;- 采用合适的材料和连接方式,以确保塔体的耐久性和安全性;- 考虑适当的防护措施,如设置防爆门、防火设施等。
3.2 经济性考虑焦炭塔本体的设计不能忽视经济性的考虑,需要确保设计方案在满足要求的同时,具有较低的成本。
需要考虑以下方面:- 合理利用材料和资源,以降低成本;- 减少能量和资源的浪费,以提高生产效率;- 考虑维护和修复的成本,以延长使用寿命。
3.3 环境影响考虑焦炭塔本体的设计需要考虑对环境的影响,以确保设计方案在环境方面的可持续性。
需要考虑以下方面:- 采用环保材料,以减少对环境的污染;- 降低能耗和排放量,以减少对环境的负荷;- 考虑废弃物的处理和回收利用。
浅谈焦炭塔设计要点
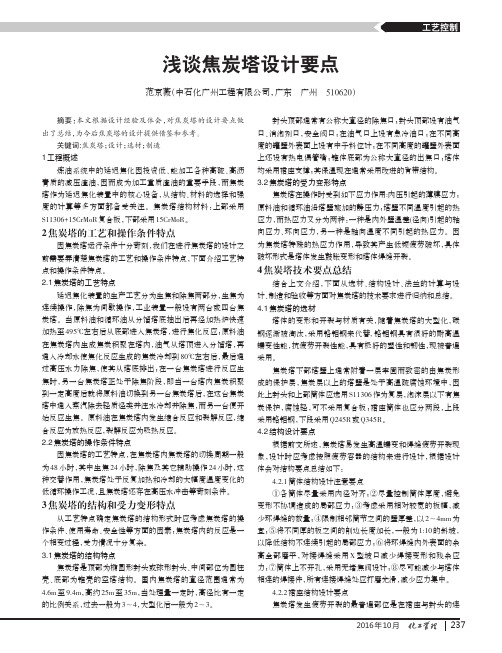
2016年10月浅谈焦炭塔设计要点范京薇(中石化广州工程有限公司,广东广州510620)摘要:本文根据设计经验及体会,对焦炭塔的设计要点做出了总结,为今后焦炭塔的设计提供借鉴和参考。
关键词:焦炭塔;设计;选材;制造1工程概述炼油系统中的延迟焦化因投资低、能加工各种高硫、高沥青质的减压渣油,因而成为加工重质渣油的重要手段,而焦炭塔作为延迟焦化装置中的核心设备,从结构、材料的选择和强度的计算等多方面都备受关注。
焦炭塔结构材料:上部采用S11306+15CrMoR 复合板,下部采用15CrMoR 。
2焦炭塔的工艺和操作条件特点因焦炭塔运行条件十分苛刻,我们在进行焦炭塔的设计之前需要弄清楚焦炭塔的工艺和操作条件特点,下面介绍工艺特点和操作条件特点。
2.1焦炭塔的工艺特点延迟焦化装置的生产工艺分为生焦和除焦两部分,生焦为连续操作,除焦为间歇操作,工业装置一般设有两台或四台焦炭塔。
当原料油和循环油从分馏塔底抽出后再经加热炉快速加热至495℃左右后从底部进入焦炭塔,进行焦化反应;原料油在焦炭塔内生成焦炭积聚在塔内,油气从塔顶进入分馏塔,再通入冷却水使焦化反应生成的焦炭冷却到80℃左右后,最后通过高压水力除焦,使其从塔底排出;在一台焦炭塔进行反应生焦时,另一台焦炭塔正处于除焦阶段,即当一台塔内焦炭积聚到一定高度后就将原料油切换到另一台焦炭塔后,在这台焦炭塔中通入蒸汽除去轻质烃类并注水冷却并除焦,而另一台便开始反应生焦。
原料油在焦炭塔内发生缩合反应和裂解反应,缩合反应为放热反应,裂解反应为吸热反应。
2.2焦炭塔的操作条件特点因焦炭塔的工艺特点,在焦炭塔内焦炭塔的切换周期一般为48小时,其中生焦24小时,除焦及其它辅助操作24小时,这种交替作用,焦炭塔处于反复加热和冷却的大幅度温度变化的低循环操作工况,且焦炭塔还存在高压水冲击等苛刻条件。
3焦炭塔的结构和受力变形特点从工艺特点确定焦炭塔的结构形式时应考虑焦炭塔的操作条件、使用寿命、安全性等方面的因素;焦炭塔内的反应是一个相变过程,受力情况十分复杂。
焦炭塔方案最终
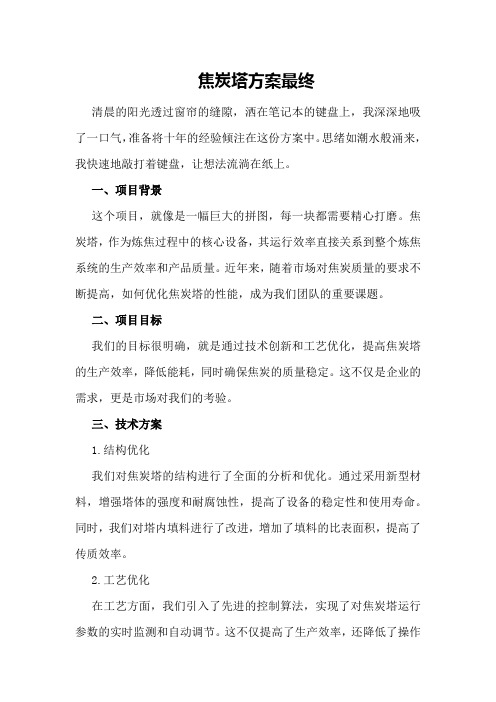
焦炭塔方案最终清晨的阳光透过窗帘的缝隙,洒在笔记本的键盘上,我深深地吸了一口气,准备将十年的经验倾注在这份方案中。
思绪如潮水般涌来,我快速地敲打着键盘,让想法流淌在纸上。
一、项目背景这个项目,就像是一幅巨大的拼图,每一块都需要精心打磨。
焦炭塔,作为炼焦过程中的核心设备,其运行效率直接关系到整个炼焦系统的生产效率和产品质量。
近年来,随着市场对焦炭质量的要求不断提高,如何优化焦炭塔的性能,成为我们团队的重要课题。
二、项目目标我们的目标很明确,就是通过技术创新和工艺优化,提高焦炭塔的生产效率,降低能耗,同时确保焦炭的质量稳定。
这不仅是企业的需求,更是市场对我们的考验。
三、技术方案1.结构优化我们对焦炭塔的结构进行了全面的分析和优化。
通过采用新型材料,增强塔体的强度和耐腐蚀性,提高了设备的稳定性和使用寿命。
同时,我们对塔内填料进行了改进,增加了填料的比表面积,提高了传质效率。
2.工艺优化在工艺方面,我们引入了先进的控制算法,实现了对焦炭塔运行参数的实时监测和自动调节。
这不仅提高了生产效率,还降低了操作难度。
我们还对焦炭塔的操作流程进行了优化,减少了不必要的操作步骤,降低了操作风险。
3.能源利用能源利用方面,我们采用了高效的燃烧技术和余热回收系统,大幅降低了能耗。
通过对燃烧设备的改造,提高了燃料的利用率,减少了环境污染。
同时,余热回收系统的应用,进一步降低了设备的运行成本。
四、实施方案1.设备改造设备改造是项目实施的第一步。
我们将根据设计方案,对现有的焦炭塔进行升级改造。
这个过程需要精心组织和协调,确保每个环节都能顺利进行。
2.工艺调整在设备改造完成后,我们将对工艺进行调整。
这包括对操作人员的培训、操作规程的修改和运行参数的优化。
这个过程需要与生产部门紧密合作,确保新工艺的顺利实施。
3.运行监测项目实施过程中,我们将对运行情况进行全程监测。
通过实时数据分析,及时调整运行参数,确保焦炭塔的稳定运行。
五、预期效果项目完成后,预计焦炭塔的生产效率将提高15%,能耗降低20%,焦炭质量也将得到显著提升。
_9800mm焦炭塔的设计与制造要点
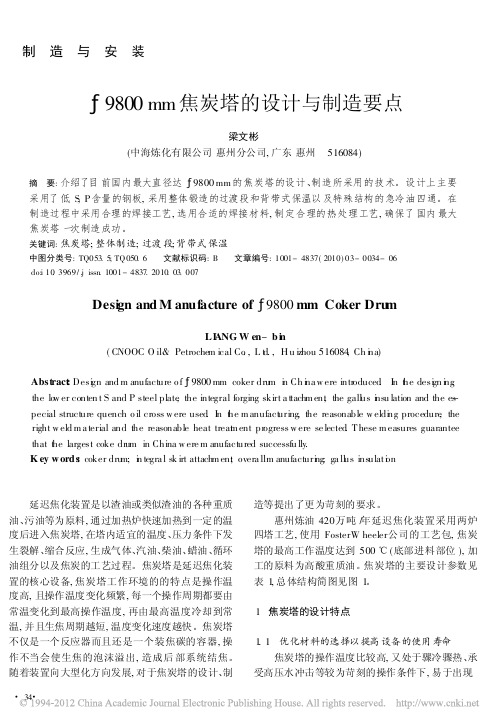
受高压水冲击等较为苛刻的操作条件下, 易于出现
# 34#
第 27卷第 3期
压 力容器
总第 208期
表 1 焦炭塔的主要设计参数
项目
参数
直径 ( mm ) 高度 ( mm ) 设计壁厚 ( mm ) 公称容积 ( m3 )
温度 ( 一般为 690 ? 14 e ) 等。由于正火 + 回火状
态的 14C r1M oR 钢 板是 贝 氏体 组 织, 冲 击韧 性 较
15CrM oR更好, 因此建议新焦炭塔采用该材质。表
2 为焦 炭塔基 层钢 板成 分的 要求 。
钢板应以正火加回火状态交货, 钢板的金相组
图 1 焦炭塔总体结构示意
在水力除焦时, 高压水对筒壁的剧烈冲击造成 塔体振动, 易引起底座垫铁外移、螺栓松动, 严重时 造成焦炭塔歪斜、晃动。在安装时要求斜铁 ( 二斜 一正 )找正后, 斜铁之间及斜铁与底座环之间都焊 死焊牢, 地脚螺栓上使用了防松碟簧。
目前国内制造 焦炭塔的材质主 要是 15CrM oR 与 14C r1M oR, 国际上采用 1. 25C r- 0. 5M o( 相当于 14Cr1M oR) 制 造 焦 炭 塔 已 经 形 成 趋 势, 因 为 14Cr1M oR 钢和 15CrM oR 钢相比, 15CrM oR 钢主要 是珠光体组织, 而 14C r1M oR 钢主要是贝氏体组织, 14Cr1M oR钢板冲击功值更 高且稳定, 对缺口 敏感 性小, 抗高温蠕变能力更强, 耐热性更好。目前, 国 内钢厂可批量生产 14Cr1M oR 钢板, 性能符合设计 要求。考虑到焦炭塔上部暴露在含硫的腐蚀性环境
Φ9800mm焦炭塔的设计与制造要点
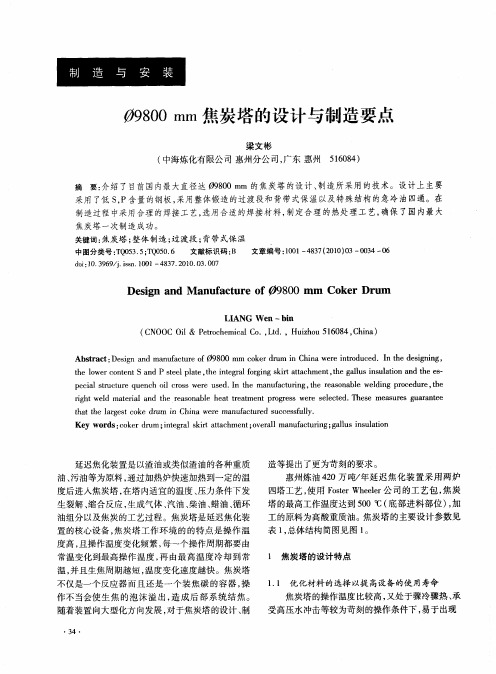
压
力
容
器
总第 2 8期 0
塔体腐 蚀 、 变形 和鼓 包 , 至焊 缝 开 裂 、 体 倾 斜 等 甚 塔 情 况 。上述 情 况 的 出 现 与 焦 炭 塔 的 材 质 有 很 大关
制造 过程 中采用 合理 的焊接工 艺 , 选用 合适 的焊接 材 料 , 制定 合理 的热处 理工 艺, 确保 了; 体制造 ; 整 过渡段 ; 背带式保 温
中图分类号 :Q 5 . ;Q 5 . T 03 5 T 0 0 6 文献标识码 : B 文章编号 :O 1 4 3 (0 0 0 0 3 0 l0 - 87 2 1 )3— 0 4— 6
rg t l tr n h e s n b e h a r ame tp o r s e e s lc e . h s a u e u r n e ih d ma e i a d t e r a o a l e tt t n r g e s w r e e td T e e me s r s g a a t e we l a e
0 80ml焦炭塔的设计 与制造要点 90 i l
梁 文彬
( 中海炼化 有 限公 司 惠州 分公 司 , 广东 惠州
568 ) 104
摘 要: 绍 了 目前 国内最 大直径 达 0 80m 的焦 炭塔 的设 计 、 介 90 m 制造 所 采用 的技 术 。设 计上 主 要
采用 了低 S P , 含量的钢板, 采用整体锻造的过渡段和 背带式保温以及特殊结构的急冷油四通。在
延 迟焦 化装置 是 以渣 油或类 似渣 油 的各种 重质 油、 污油等为 原料 , 过加 热炉快 速加 热到一定 的温 通
焦炭塔本体的设计
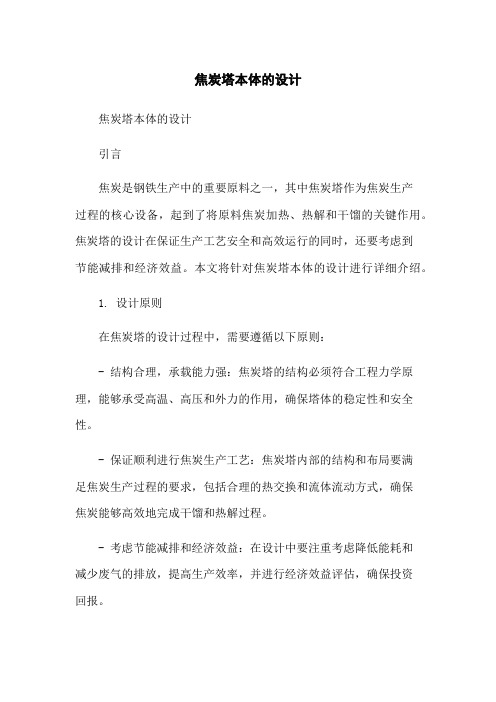
焦炭塔本体的设计焦炭塔本体的设计引言焦炭是钢铁生产中的重要原料之一,其中焦炭塔作为焦炭生产过程的核心设备,起到了将原料焦炭加热、热解和干馏的关键作用。
焦炭塔的设计在保证生产工艺安全和高效运行的同时,还要考虑到节能减排和经济效益。
本文将针对焦炭塔本体的设计进行详细介绍。
1. 设计原则在焦炭塔的设计过程中,需要遵循以下原则:- 结构合理,承载能力强:焦炭塔的结构必须符合工程力学原理,能够承受高温、高压和外力的作用,确保塔体的稳定性和安全性。
- 保证顺利进行焦炭生产工艺:焦炭塔内部的结构和布局要满足焦炭生产过程的要求,包括合理的热交换和流体流动方式,确保焦炭能够高效地完成干馏和热解过程。
- 考虑节能减排和经济效益:在设计中要注重考虑降低能耗和减少废气的排放,提高生产效率,并进行经济效益评估,确保投资回报。
2. 塔体结构设计焦炭塔的外观形式常见的有筒型、圆锥型和矩形。
在设计中需要综合考虑经济性、施工性和使用效果等因素,选择最合适的形式。
塔体结构主要包括塔筒、塔盖、设备支撑、配管和通风系统等。
- 塔筒:塔筒是焦炭塔的主体部分,由焦炭进料口、废气出口和内部结构组成。
塔筒一般选用结构稳定、耐高温和耐腐蚀的材料,如碳钢或耐火材料。
- 塔盖:塔盖用于密封焦炭塔的顶部,可以防止外界物质进入塔内,同时保证内部高温气体的排放。
塔盖通常由耐火材料和密封材料构成,以确保安全运行。
- 设备支撑:焦炭塔本体需要设备支撑来保持稳定和安全。
设备支撑的选材需要具备高强度和稳定性,以适应焦炭塔的工作环境。
- 配管和通风系统:配管和通风系统是焦炭塔的重要组成部分,用于调节流体的温度、压力和流速。
在设计中需要考虑流体的传输特性和设备的热力学要求,确保流体能够顺利地通过塔体。
3. 电气控制系统设计焦炭塔的电气控制系统是保证焦炭塔正常运行的关键。
电气控制系统可以实现对焦炭塔内部流体、温度和压力等参数的监控和调控。
设计中需要考虑以下因素:- 电气设备选择:电气设备需要具备高温、防腐蚀和防爆等特性,确保在高温高压环境下能够正常工作。
大型焦炭塔的设计

大型焦炭塔的设计顾一天;龙秀兰;贾桂茹【期刊名称】《石油化工设备技术》【年(卷),期】2001(22)1【摘要】φ8400mm大型焦炭塔的设计为国内首次,其主体材质选用Cr-Mo钢,焦炭塔上部泡沫段选用不锈钢复合钢板;裙座与筒体连接采用对接堆焊的型式并在裙座上开设膨胀缝。
针对焦炭塔操作时低频疲劳容易引起筒体变形和焊缝开裂的问题,采取了多项改进措施。
%The design of φ8400mm large scale coke drum is the first in d omestic.The material of Cr-Mo steel is s elected for main shell,and stainless ste el clad plate is selected for upper foam section of coke drum.The joints between skirt and shell are the butt surfacing welding type,and expansion joints are pr ovided in the skirt.In accordauce with t he problems of shell deformation and wel ding crack caused by low frequency fatig ue during coke drum operation,some impro vements are adopted.【总页数】4页(P4-7)【作者】顾一天;龙秀兰;贾桂茹【作者单位】中国石化集团北京设计院,北京100011;中国石化集团北京设计院,北京100011;中国石化集团北京设计院,北京100011【正文语种】中文【中图分类】TE962【相关文献】1.大型焦炭塔的设计 [J], 江学俊2.大型焦炭塔的设计与制造 [J], 孙家鹏;张新宇3.低压条件下大型焦炭塔系统几个设计问题的探讨 [J], 龚文武4.大型延迟焦化装置焦炭塔顶油气线的管道设计 [J], 唐杰5.大型焦炭塔裙座对接结构优化设计与分析 [J], 黄德华因版权原因,仅展示原文概要,查看原文内容请购买。
- 1、下载文档前请自行甄别文档内容的完整性,平台不提供额外的编辑、内容补充、找答案等附加服务。
- 2、"仅部分预览"的文档,不可在线预览部分如存在完整性等问题,可反馈申请退款(可完整预览的文档不适用该条件!)。
- 3、如文档侵犯您的权益,请联系客服反馈,我们会尽快为您处理(人工客服工作时间:9:00-18:30)。
焦炭塔本体的设计1. 概述延迟焦化是以渣油或类似渣油的污油、原油为原料,通过加热炉快速加热到一定的温度后进入焦炭塔,在塔内适宜的温度、压力条件下发生裂解、缩合反应,生成气体、汽油、柴油、蜡油、循环油组分和焦炭的工艺过程。
在目前国内乙烯裂解原料石脑油短缺、优质柴油短缺、低硫低烯烃汽油短缺和石油焦短缺的条件下,延迟焦化工艺由于其工艺简单、投资低、操作费用低等特点又重新得到各石油化工公司的重视。
一般情况下新建和扩建延迟焦化装置的主要目的是处理炼油厂过剩而无出路的减压渣油;减少重油催化裂化的掺炼比例,提高催化汽油、柴油的质量;提高作为优质乙烯裂解原料-焦化石脑油的产量;增产高十六烷值柴油,提高炼油厂的柴汽比;增加中间焦化蜡油,为催化裂化及加氢裂化提供原料;利用焦化干气或石油焦作为制氢装置的原料。
目前国内延迟焦化装置近40套,新设计和正在建设的约10套,自第一套延迟焦化装置在抚顺石化公司石油二厂建设以来,无论是延迟焦化工艺技术水平,还是设备技术水平均有了较大的提高,主要体现在装置运行更加安全可靠、开工周期延长、一次性投资降低、能耗降低、操作费用降低、自动化水平提高、操作灵活性提高、产品质量提高、环境污染减少。
延迟焦化装置的主要设备有焦化加热炉、焦炭塔、焦化分馏塔、吹汽放空塔、加热炉进料泵、水力除焦机械等,其中焦化加热炉被认为是焦化装置的关键设备,而焦炭塔则是焦化装置的核心设备。
因为焦炭塔是焦化装置的反应器,加热炉、分馏塔、放空系统、冷切焦水处理系统、水力除焦系统等均与之有关。
虽然焦炭塔是一个空筒设备,但它的设计涉及到几乎全装置的工艺过程,因此在焦炭塔的设计过程中不但应充分考虑焦炭塔本体的设计,还应充分考虑与之相关系统的设计。
2. 焦炭塔本体的设计焦炭塔本体的设计主要包括焦炭塔直径的确定、塔高的确定、塔体材料的选择及焦炭塔的结构形式。
2.1 焦炭塔的直径和高度焦炭塔的直径和高度主要取决于装置的处理量、原料性质、操作温度、操作压力和循环比。
装置的处理量是决定焦炭塔大小的主要参数,目前国内单塔处理量和焦炭塔规格的对应如下:焦炭塔的单塔处理量越大,要求的焦炭塔直径越大,这主要是由焦炭塔塔内的允许气速决定的。
焦化原料渣油在加热炉中被快速加热到500℃左右进入焦炭塔,为防止加热炉管结焦,炉出口的反应转化率一般不大于10%(气体和汽油的转化率),大部分的反应延迟到焦炭塔内进行,原料进入焦炭塔,在塔内适宜的压力、温度和停留时间的条件下发生裂解和缩合反应,裂解为吸热反应,缩合为放热反应,裂解的热量除了来自原料渣油本身外还有一部分由缩合反应提供,缩合反应生成的焦炭停留在塔内,并由塔壁向中心扩展,中心形成进料通道,在焦炭层以上为主要反应区,即泡沫层。
泡沫层分油相泡沫和气相泡沫,气相泡沫在上部,其密度约为30~100kg/m3,油相泡沫在焦层以上,其密度约为100~700 kg/m3,焦化反应温度即为泡沫层温度,一般为460~480℃,并且生焦率越高,该反应温度越高。
焦炭层也存在焦化反应,裂化生成的气体自焦炭层益处,焦炭层的空隙率约为:30%~50%。
使热态的焦炭层高度高于冷态的焦炭高度。
随着原料的不断进入,产生的焦炭量增加,焦炭层高度增加,泡沫层也随之连续升高。
塔内反应示意图如下:内油气的允许气速可用下式计算:V VL c -048.0*uρρρk=其中Uc为塔内允许气相线速,m/s ;ρL为轻相泡沫层密度,kg/m3 ;ρLV为气相泡沫层密度,kg/m3。
K 为物性校正系数据资料报导,国外在焦炭塔内不注入消泡剂时,允许气速一般为0.11~0.17m/s。
在使用消泡剂时,正常的设计油气速度应低于0.12~0.21m/s。
根据允许的油气速度和焦炭塔内的油气流量即可确定焦炭塔的直径,为减少泡沫夹带,新设计焦炭塔建议采用低的油气速度,国内设计焦炭塔内的油气速度一般低于0.10~0.15m/s。
焦炭塔内的油气体积流量除和渣油进料量有关外,与原料性质、操作条件也有密切的关系。
在确定焦炭塔的直径以前应首先确定焦炭塔的操作条件和产品分布。
渣油是以碳、氢、硫、氮、氧等为主要元素的大分子烃类,通常分为饱和烃、芳烃、胶质和沥青质,沥青质含量高的渣油生焦率较高,轻油收率较低。
产品分布一般最终由试验确定,在没有实验数据时可参考下式估算:(1) 硫化氢收率, W%: H2S=0.25*Sf(2) 干气收率, W%: RG =3.5+0.1*CCR(3) LPG收率, W%: LPG =3.3+0.044*CCR(4)焦炭收率, W%: COK=1.6*CCR(5)石脑油收率, W%: Nao=11.38+0.335*CCR(6)瓦斯油收率, W%: TGO=100-(H2S+RG+LPG+COK+ Nao)(7)柴油收率/瓦斯油收率,R=0.38+0.011*CCR-0.00031*CCR(8)柴油收率, W%: LCGO=R*TGO(9)蜡油收率, W%: HCGO=TGO-LCGO其中:CCR为渣油的康氏残炭(W%),Sf为渣油的硫含量(W%)。
当原料性质确定后,对生焦率和产品分布影响较大的主要是循环比、反应温度和压力。
循环比减少10%,生焦率一般减少1%,同时焦化蜡油收率增加,气体、汽油、柴油收率下降。
当需要提高装置的液体收率时一般采用降低循环比(0.15~0.25)或零循环比操作;当需要多产焦化石脑油和柴油时一般采用较大循环比(0.25~0.45)操作;当焦化蜡油无出路或需要最大可能地生产乙烯原料时一般采用大循环比(0.4~1.0)操作。
循环比越大,焦炭塔内的油气体积流量越大。
提高焦化温度可增产液体产品收率,但基于焦化反应的特点,反应温度(炉出口温度控制)调整的幅度是很窄的,温度过高会导致提前结焦,堵塞炉管、转油线,影响开工周期,同时易生成硬质石油焦,使除焦困难;温度过低导致热量不足反应深度不够,轻油收率降低,焦炭挥发分增大或产生焦油。
一般情况下是根据原料性质确定最佳的操作温度,通常焦化炉出口温度为495~505℃,芳烃含量和沥青质含量的比值较大时宜采用较高的炉出口温度。
采用低压操作可改善焦化产品分布,在国内外已普遍认可,国内焦炭塔顶操作压力一般为0.15~0.20Mpa,国外最低的达到0.1~0.15Mpa。
压力降低一般是提高蜡油的收率,但是增大了焦炭塔的气体体积流量,势必使焦炭塔的塔径加大,装置的投资增加,因此应综合设备投资、操作费用和产品分布等因素确定适宜的操作压力。
另外焦化加热炉的注汽注水量、在线清焦时的加热炉吹汽量、四通阀及切断阀的汽封蒸汽量对焦炭塔的直径确定也有一定的影响,一般加热炉的注汽注水量按炉新鲜进料的1.0~1.5%考虑,在线清焦时应考虑减少渣油进料,增加蒸汽量,蒸汽量可按2~8t/h考虑。
焦炭塔底阀门的汽封量在采用连续注入时应考虑0.5~1.0t/h 的蒸汽量。
在基本确定焦炭塔的直径后,根据原料性质、焦炭产率、生焦时间、泡沫层高度来确定焦炭塔的高度。
焦炭产率和原料性质、操作条件有关,泡沫层高度和原料性质、反应温度及压力有关。
当在焦炭塔内注入消泡剂后,泡沫层的高度一般减少50~70%。
当单塔处理能力、原料性质和操作条件确定后,塔内的焦层高度主要确定于生焦时间。
目前国内焦化装置设计的生焦时间均为24小时,国外焦化生焦时间一般为10~24小时,采用16小时的占大多数,采用短的生焦时间,可以提高焦炭塔的利用率,或者同等规模的焦炭塔的高度减少。
在确定焦炭塔高度时应留有一定的安全空高,安全空高一般为塔顶切线离泡沫层顶部的距离,国内设计的焦炭塔一般安全空高大于等于3米,国外焦炭塔的安全空高一般为2~3米。
空高越大,焦炭塔的利用率越低,但油气在塔内的停留时间延长,对减少油气线和分馏塔内结焦有利。
空高的计算公式如下:泡沫塔锥焦焦焦切空高---=H D 785.0/V G H H 2⎪⎪⎭⎫ ⎝⎛⨯ρτ 其中:H 切-焦炭塔切线高度, m ;G 焦-焦炭生焦速率, kg/h ;τ焦-生焦时间, hr ; ρ焦-塔内焦炭堆密度, kg/m 3(800~900 kg/m 3); V 锥-焦炭塔锥体体积, m 3;D 塔-焦炭塔直径, m ;H 泡沫-泡沫层高度, m 。
通常所说的缩短生焦时间可以提高处理量,是提高了焦炭塔的利用率。
焦炭塔直径和切线高度的关系焦炭塔直径和高度相互补充,当装置处理量、操作条件确定后,直径增大可以降低高度,高度增加也可以适当减少塔径。
国内在过去建设的焦炭塔的直径一般为5.4~6.4米,其高径比一般为3~4。
最近建设的大直径焦炭塔的高径比一般为2~3。
美国焦炭塔的高径比一般为2~3。
焦炭塔的直径和高度受到水力除焦机械,设备设计、制造、运输、吊装等的限制,不宜太大和太高,美国目前运行的最大焦炭塔的直径为9.14米。
建议在装置处理量较大,采用一炉二塔使焦炭塔的直径和高度特别庞大时,采用缩短生焦时间或二炉四塔或三炉六塔更为适宜,不能盲目的追求设备大型化。
2.2 塔体材料的选择焦炭塔的材质选择应考虑焦化原料性质、塔内操作条件、焦炭塔的结构尺寸、装置的建设投资。
90年代以前,国内设计的焦炭塔的材质大部分为20g,因原料中硫含量不高,设计的温度及压力较低,焦炭塔的直径较小。
通过近三十年的使用经验表明,该材质基本满足生产要求,但也出现了不少的问题,主要表现在由于其耐热性能差,使用一段时间出现塔体裂纹、鼓包和变形,给生产带来不安全因素。
根据最新材料选择标准,焦炭塔的材质应选用20R。
目前针对小直径焦炭塔,并且原料油中含硫量低,建设投资不高的情况下,仍可采用20R作为焦炭塔的材料。
采用碳钢材料,设计温度不能高于375℃,实际上焦化原料进焦炭塔的温度为485~495℃,由于生成的焦炭积聚于塔壁,起到了隔热作用,实际测量焦炭塔塔体的最高温度不高于475℃;设计压力一般低于0.3Mpa,设计腐蚀裕度不小于3mm,否则焦炭塔的壁厚太大,给焦炭塔的制造、热处理、施工安装带来一定的困难。
当焦炭塔的直径较大和原料中硫含量较高时,焦炭塔若采用碳钢材质,其塔体的厚度就会很厚,无论从使用性能、设备制造、施工安装、设备费用等方面均不利。
因此目前设计的大型化焦炭塔的材质均采用Cr-Mo钢。
国内近几年设计的焦炭塔的材质大都为15CrMoR。
美国自1980~1997年大量使用Cr-Mo钢,CrMo钢中经常用的是1Cr-1/2Mo,1 1/4Cr-1/2Mo和2 1/4Cr-1.0Mo,1 1/4Cr-1/2Mo钢和1Cr-1/2Mo 钢相比,许用应力高、对缺口敏感性小、耐热性更好,但国内应用的还比较少。
美国Foster-wheeler公司为印度设计的直径29英尺的焦炭塔下部锥体采用 2 1/2Cr-1.0Mo钢,上部采用1 1/4Cr-1/2Mo钢。