1数控机床精度分析
数控机床的精度检测与调整方法

数控机床的精度检测与调整方法数控机床是现代制造业中不可或缺的一种设备,它的精度对于产品的质量和性能起着至关重要的作用。
本文将介绍数控机床的精度检测与调整方法,帮助读者更好地了解和应用这些技术。
一、精度检测方法1. 几何误差检测几何误差是数控机床精度的重要指标,包括直线度、平行度、垂直度、圆度等。
常用的几何误差检测方法有激光干涉仪、三坐标测量仪等。
通过这些设备,可以精确测量机床各个轴向的几何误差,并得出相应的数据。
2. 理论切削路径与实际切削路径对比在数控机床的加工过程中,理论切削路径与实际切削路径之间可能存在偏差。
通过对比理论切削路径与实际切削路径,可以判断数控机床的精度是否达标。
常用的方法是使用光学测量仪器,对切削路径进行高精度的测量和分析。
二、精度调整方法1. 机床结构调整数控机床的结构调整是提高其精度的重要手段。
首先,需要检查机床各个部件的紧固情况,确保机床的刚性和稳定性。
其次,根据几何误差的检测结果,对机床的导轨、滑块等部件进行调整,以减小误差。
2. 控制系统调整数控机床的控制系统对于其加工精度起着至关重要的作用。
通过调整控制系统的参数,可以改善机床的运动精度和定位精度。
常用的调整方法包括增加控制系统的采样频率、优化控制算法等。
3. 刀具与工件的匹配调整刀具与工件的匹配对于加工精度有很大影响。
在数控机床的加工过程中,需要根据工件的要求选择合适的刀具,并对刀具进行调整和校准。
同时,还需要对工件进行检测,确保其尺寸和形状与设计要求一致。
三、精度检测与调整的重要性数控机床的精度检测与调整是保证产品质量和性能的关键环节。
只有通过科学的检测方法,准确地了解机床的精度情况,才能及时采取相应的调整措施,提高机床的加工精度。
这对于提高生产效率、降低成本、提升产品竞争力具有重要意义。
四、未来发展趋势随着制造业的不断发展,数控机床的精度要求也越来越高。
未来,数控机床的精度检测与调整方法将更加精细化和智能化。
数控机床加工精度检测与校准方法

数控机床加工精度检测与校准方法在现代制造业中,数控机床是不可或缺的重要设备。
它的高效率、高精度和高稳定性使得加工过程更加精确和可靠。
然而,由于各种因素的影响,数控机床的加工精度可能会出现偏差。
因此,对数控机床的精度进行检测和校准是非常必要的。
一、加工精度检测方法1. 几何误差检测几何误差是数控机床加工精度的重要指标之一。
常见的几何误差包括直线度误差、平行度误差、垂直度误差和圆度误差等。
几何误差的检测可以使用光学测量仪器,如激光干涉仪、光学投影仪等。
通过将测量仪器与数控机床进行联动,可以实时监测数控机床的加工精度,并得出相应的误差数据。
2. 热误差检测热误差是数控机床加工精度的另一个重要指标。
由于加工过程中会产生热量,数控机床的温度会发生变化,从而导致加工精度的偏差。
为了检测热误差,可以使用温度传感器对数控机床进行监测。
通过实时记录数控机床的温度变化,并与加工精度进行对比,可以得出热误差的数据。
3. 振动误差检测振动误差是数控机床加工精度的另一个重要影响因素。
振动会导致数控机床的加工过程不稳定,从而影响加工精度。
为了检测振动误差,可以使用振动传感器对数控机床进行监测。
通过实时记录数控机床的振动情况,并与加工精度进行对比,可以得出振动误差的数据。
二、加工精度校准方法1. 机床调整机床调整是校准数控机床加工精度的常用方法之一。
通过调整数控机床的各项参数,如传动装置、导轨、滑块等,可以减小加工误差。
例如,可以通过调整导轨的平行度和垂直度来改善加工精度。
此外,还可以通过更换加工刀具、调整刀具固定方式等方式来提高加工精度。
2. 补偿技术补偿技术是校准数控机床加工精度的另一种常用方法。
通过对加工过程中的误差进行实时监测,并通过数学模型进行补偿,可以减小加工误差。
例如,可以通过在程序中添加补偿指令,根据误差数据进行补偿,从而提高加工精度。
3. 精度校准仪器精度校准仪器是校准数控机床加工精度的重要工具。
常见的精度校准仪器包括激光干涉仪、光学投影仪、三坐标测量机等。
数控机床工作台的定位精度检测与调整技巧

数控机床工作台的定位精度检测与调整技巧数控机床工作台是现代制造业中不可或缺的重要设备,其定位精度直接关系到加工零件的质量和精度。
本文将为大家介绍数控机床工作台的定位精度检测与调整技巧。
一、定位精度检测方法1. 平面定位精度检测:将工作台移动到机床最大行程的两端,将测量时的测头放置在工作台上,并对两个端点进行平面度测量。
根据测量结果,计算平均偏差,以评估工作台的平面定位精度。
2. 垂直定位精度检测:将工作台移动到最高点或最低点,将测量时的测头放置在工作台上,并对工作台进行垂直度测量。
根据测量结果,计算垂直度偏差,以评估工作台的垂直定位精度。
3. 水平定位精度检测:将工作台移动到机床最大行程的两端,将测量时的测头放置在工作台上,并对两个端点进行水平度测量。
根据测量结果,计算平均偏差,以评估工作台的水平定位精度。
4. 位移重复性检测:将工作台移动到同一个位置,并多次测量工作台的定位偏差。
根据测量结果,计算位移重复性误差,以评估工作台的定位精度。
二、定位精度调整技巧1. 调整导轨与滑块:导轨与滑块是数控机床工作台的关键部件,直接影响着定位精度。
通过调整导轨与滑块之间的间隙,减小摩擦力,可以提高定位精度。
调整时需仔细测量每个位置的间隙,并确保在规定范围内。
2. 调整传动系统:传动系统的精度也是影响工作台定位精度的重要因素。
可以通过调整传动装置的齿轮啮合间隙、传动带的张力以及传动链条的松紧度来提高定位精度。
3. 检查并更换磨损部件:长时间使用后,机床工作台的关键部件可能会出现磨损,导致定位精度下降。
及时检查并更换磨损的部件,可以恢复工作台的定位精度。
4. 调整液压系统:液压系统的稳定性对工作台的定位精度有重要影响。
可以通过调整液压泵的工作压力、检查液压缸的密封状况,保证液压系统的正常工作,提高工作台的定位精度。
5. 关注温度变化:温度变化也会对工作台的定位精度造成影响。
数控机床工作台应放置在稳定的温度环境中,并定期检查温度变化对定位精度的影响,必要时进行调整或采取温度补偿措施。
数控机床加工精度标准
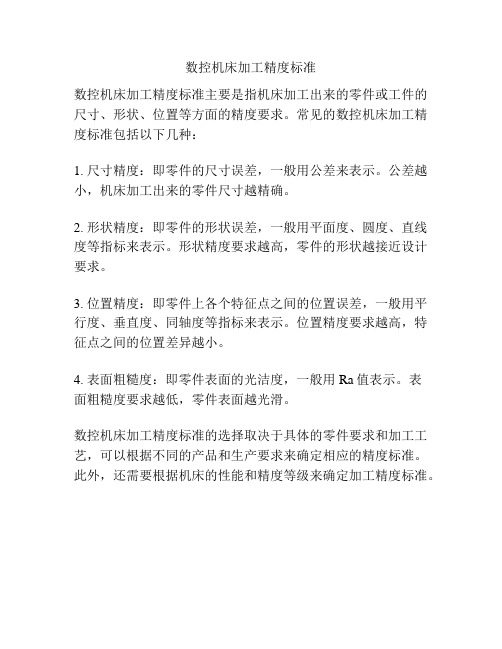
数控机床加工精度标准
数控机床加工精度标准主要是指机床加工出来的零件或工件的尺寸、形状、位置等方面的精度要求。
常见的数控机床加工精度标准包括以下几种:
1. 尺寸精度:即零件的尺寸误差,一般用公差来表示。
公差越小,机床加工出来的零件尺寸越精确。
2. 形状精度:即零件的形状误差,一般用平面度、圆度、直线度等指标来表示。
形状精度要求越高,零件的形状越接近设计要求。
3. 位置精度:即零件上各个特征点之间的位置误差,一般用平行度、垂直度、同轴度等指标来表示。
位置精度要求越高,特征点之间的位置差异越小。
4. 表面粗糙度:即零件表面的光洁度,一般用Ra值表示。
表
面粗糙度要求越低,零件表面越光滑。
数控机床加工精度标准的选择取决于具体的零件要求和加工工艺,可以根据不同的产品和生产要求来确定相应的精度标准。
此外,还需要根据机床的性能和精度等级来确定加工精度标准。
数控机床位置精度测试常用的测量方法及评定标准

4.4补偿实例 现以ZJK2532A数控铣钻床的X轴为例,该机床配置华中数控世纪星系统。测量方法为“步距规”测量;设某步距规实际尺寸为:
位置
P0
P1
P2
P3
P4
P5
实际尺寸mm
0
100.10
200.20
300.10
400.20
500.05
1、测试步骤如下: 。 在首次测量前,开机进入系统(华中数控HNC-2000或HNC-21M),依次按“F3参数”键、再按“F3输入权限”键进入下一子菜单,按F1数控厂家参数,输入数控厂家权限口令,初始口令为“NC”,回车,再按“F1参数索引”键,再按“F4轴补偿参数”键如图2-6所示,移动光标选择“0轴” 回车,即进入系统X轴补偿参数界面如图2-8所示,将系统的反向间隙、螺距补偿参数全部设置为零,按“Esc”键,界面出现对话框“是否保存修改参数?”,按“Y”键后保存修改后的参数。按“F10”键回到主界面,再按“Alt+X”,退出系统,进入DOS状态,按“N”回车进入系统;
图6步距规安装示意图
数控机床精度检验内容

数控机床精度检验内容数控机床是一种高精度、高效率的加工设备,其精度直接影响着加工零件的质量和精度。
因此,对数控机床的精度进行检验是非常重要的。
下面将介绍数控机床精度检验的内容。
首先,数控机床的精度检验包括几个方面,几何精度、运动精度和位置精度。
几何精度是指机床各轴线的几何误差,包括直线度、平行度、垂直度等;运动精度是指机床在运动过程中的动态精度,包括加工速度、加速度、减速度等;位置精度是指机床在停止状态下的定位精度,包括定位误差、重复定位精度等。
这些精度指标直接影响着数控机床加工零件的精度和表面质量。
其次,数控机床精度检验的方法主要包括几种,静态检验、动态检验和综合检验。
静态检验是指在机床停止状态下对各轴线的几何精度进行检测,可以通过测量仪器进行测量,如千分尺、角尺等;动态检验是指在机床运动状态下对运动精度进行检测,可以通过加工模拟零件进行加工,然后进行测量分析;综合检验是指将静态检验和动态检验相结合,对机床的整体精度进行评估。
另外,数控机床精度检验的标准主要包括国家标准和行业标准。
国家标准是指由国家相关部门颁布的针对数控机床精度的检验标准,如GB/T19001-2008《数控机床检验标准》等;行业标准是指由行业协会或企业制定的针对特定类型数控机床的检验标准,如《数控车床精度检验标准》等。
在进行数控机床精度检验时,需要严格按照相关标准进行检验,以确保检验结果的准确性和可靠性。
最后,数控机床精度检验的意义在于保证机床加工零件的精度和质量,提高加工效率和加工精度,降低加工成本,提高产品的竞争力。
通过定期对数控机床进行精度检验,可以及时发现机床的精度问题,进行调整和维护,确保机床的稳定性和可靠性,延长机床的使用寿命。
综上所述,数控机床精度检验内容包括几何精度、运动精度和位置精度,检验方法包括静态检验、动态检验和综合检验,检验标准包括国家标准和行业标准。
通过精度检验可以保证机床的加工精度和质量,提高产品的竞争力,具有重要的意义和价值。
数控机床的精度检测方法与标准
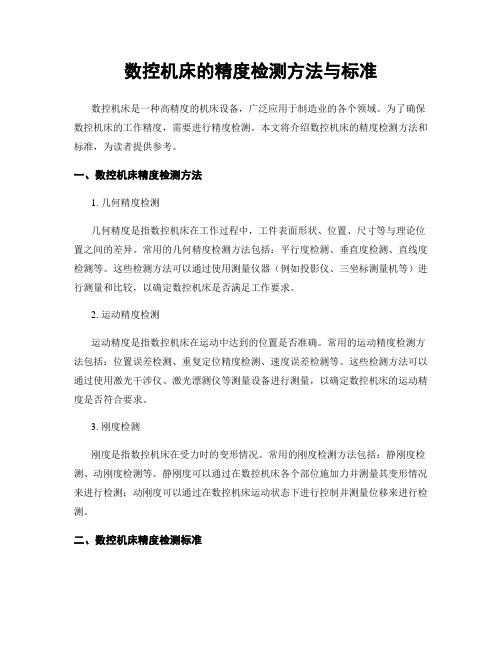
数控机床的精度检测方法与标准数控机床是一种高精度的机床设备,广泛应用于制造业的各个领域。
为了确保数控机床的工作精度,需要进行精度检测。
本文将介绍数控机床的精度检测方法和标准,为读者提供参考。
一、数控机床精度检测方法1. 几何精度检测几何精度是指数控机床在工作过程中,工件表面形状、位置、尺寸等与理论位置之间的差异。
常用的几何精度检测方法包括:平行度检测、垂直度检测、直线度检测等。
这些检测方法可以通过使用测量仪器(例如投影仪、三坐标测量机等)进行测量和比较,以确定数控机床是否满足工作要求。
2. 运动精度检测运动精度是指数控机床在运动中达到的位置是否准确。
常用的运动精度检测方法包括:位置误差检测、重复定位精度检测、速度误差检测等。
这些检测方法可以通过使用激光干涉仪、激光漂测仪等测量设备进行测量,以确定数控机床的运动精度是否符合要求。
3. 刚度检测刚度是指数控机床在受力时的变形情况。
常用的刚度检测方法包括:静刚度检测、动刚度检测等。
静刚度可以通过在数控机床各个部位施加力并测量其变形情况来进行检测;动刚度可以通过在数控机床运动状态下进行控制并测量位移来进行检测。
二、数控机床精度检测标准为了统一数控机床的精度检测标准,国内外制定了相应的标准,其中最有代表性的是国家标准GB/T16857-1997《数控机床精度检验方法》。
该标准规定了数控机床的几何精度、运动精度和刚度等指标的检测方法和要求。
以几何精度为例,该标准包括对工件表面形状、位置、尺寸等几何误差的检测,在该标准中,提供了一系列的测量方法,包括投影法、三坐标法、机床内检测法等。
此外,该标准还规定了几何误差的允许值,即数控机床在工作过程中允许存在的误差范围。
除了国家标准,国际标准也对数控机床的精度检测进行了规范,例如ISO 230-1和ISO 230-2等,这些标准主要用于指导和规范制造商以及使用单位在数控机床精度检测方面的操作。
近年来,随着数控机床技术的不断发展,对精度的要求也越来越高。
数控机床的加工精度误差分析与校正方法
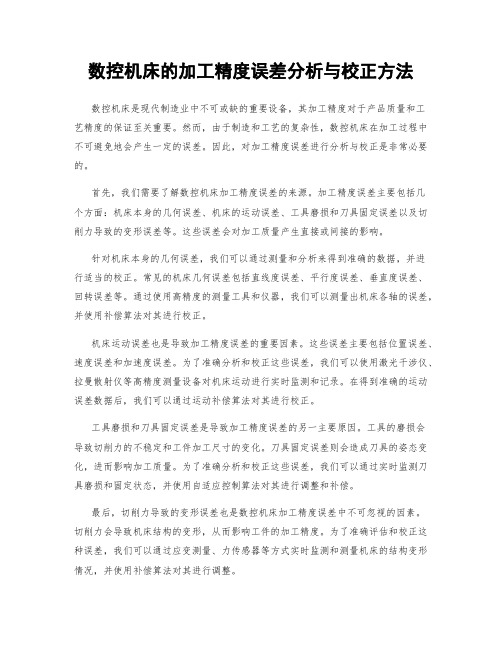
数控机床的加工精度误差分析与校正方法数控机床是现代制造业中不可或缺的重要设备,其加工精度对于产品质量和工艺精度的保证至关重要。
然而,由于制造和工艺的复杂性,数控机床在加工过程中不可避免地会产生一定的误差。
因此,对加工精度误差进行分析与校正是非常必要的。
首先,我们需要了解数控机床加工精度误差的来源。
加工精度误差主要包括几个方面:机床本身的几何误差、机床的运动误差、工具磨损和刀具固定误差以及切削力导致的变形误差等。
这些误差会对加工质量产生直接或间接的影响。
针对机床本身的几何误差,我们可以通过测量和分析来得到准确的数据,并进行适当的校正。
常见的机床几何误差包括直线度误差、平行度误差、垂直度误差、回转误差等。
通过使用高精度的测量工具和仪器,我们可以测量出机床各轴的误差,并使用补偿算法对其进行校正。
机床运动误差也是导致加工精度误差的重要因素。
这些误差主要包括位置误差、速度误差和加速度误差。
为了准确分析和校正这些误差,我们可以使用激光干涉仪、拉曼散射仪等高精度测量设备对机床运动进行实时监测和记录。
在得到准确的运动误差数据后,我们可以通过运动补偿算法对其进行校正。
工具磨损和刀具固定误差是导致加工精度误差的另一主要原因。
工具的磨损会导致切削力的不稳定和工件加工尺寸的变化。
刀具固定误差则会造成刀具的姿态变化,进而影响加工质量。
为了准确分析和校正这些误差,我们可以通过实时监测刀具磨损和固定状态,并使用自适应控制算法对其进行调整和补偿。
最后,切削力导致的变形误差也是数控机床加工精度误差中不可忽视的因素。
切削力会导致机床结构的变形,从而影响工件的加工精度。
为了准确评估和校正这种误差,我们可以通过应变测量、力传感器等方式实时监测和测量机床的结构变形情况,并使用补偿算法对其进行调整。
总结来说,数控机床的加工精度误差分析与校正是确保产品质量和工艺精度的关键步骤。
在这个过程中,我们需要准确地识别和分析加工精度误差的来源,并采取相应的校正措施。
数控机床加工精度的影响因素及提高方法

数控机床加工精度的影响因素及提高方法数控机床加工精度是衡量机床性能和加工质量的重要指标之一。
机床加工精度的高低直接影响到加工零件的尺寸精度和表面质量。
正确理解数控机床加工精度的影响因素及提高方法,可以有效提高机床加工精度,满足不同的加工要求。
一、影响因素1. 机床本身的精度:机床加工精度的高低取决于机床本身精度的高低。
包括机床的机械结构精度、控制系统精度以及加工刀具等。
2. 工件加工材料的性质:工件的材料的硬度、韧性、温度等都会影响加工时的切削力、振动、温度变化等,从而影响机床加工精度。
3. 切削工艺参数:如切削速度、进给量、切削深度和切削方向等,都会对零件的尺寸和形状精度产生影响。
4. 加工环境:加工环境的湿度、温度、气压等也会对机床加工精度产生影响。
特别是在高温、潮湿的环境中长时间工作,会导致机床部件热膨胀和受潮,进而影响机床加工精度。
二、提高方法1. 优化机床结构:通过提高机床的机械结构精度,例如采用高刚性材料,优化结构设计,优化装配工艺等,以提高机床加工精度和稳定性。
2. 提高控制系统精度:控制系统是数控机床的重要组成部分。
通过对机床控制系统进行优化,提高控制精度、数据传输速率和控制方式等。
例如采用高精度伺服电机、编码器、传感器等辅助检测设备,提高机床的动态响应能力和精度。
3. 优化加工工艺:根据工件材料的特性,优化加工刀具的选型、切削工艺参数等,以确保加工过程中的稳定性和精度。
4. 控制加工环境:通过控制加工环境的温度、湿度、气压等条件,提高机床加工精度和稳定性。
综上所述,数控机床加工精度的影响因素和提高方法是相互关联的。
只有综合考虑机床结构、控制系统、加工工艺和加工环境等各个方面因素,才能最大限度的提高机床加工精度和稳定性,从而满足不同的加工要求。
数控机床的精度与应用范围
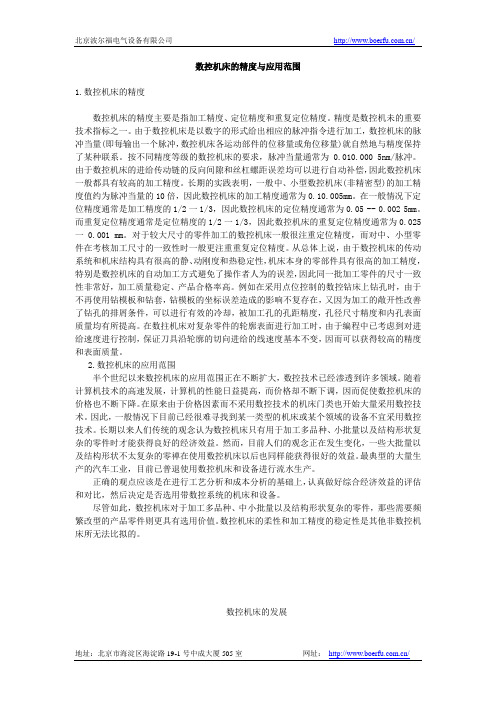
数控机床的精度与应用范围1.数控机床的精度数控机床的精度主要是指加工精度、定位精度和重复定位精度。
精度是数控机未的重要技术指标之一。
由于数控机床是以数字的形式给出相应的脉冲指令进行加工,数控机床的脉冲当量(即每输出一个脉冲,数控机床各运动部件的位移量或角位移量)就自然地与精度保持了某种联系。
按不同精度等级的数控机床的要求,脉冲当量通常为0.010.000 5nm/脉冲。
由于数控机床的进给传动链的反向间隙和丝杠螺距误差均可以进行自动补偿,因此数控机床一般都具有较高的加工精度。
长期的实践表明,一般中、小型数控机床(非精密型)的加工精度值约为脉冲当量的10倍,因此数控机床的加工精度通常为0.10.005mm。
在一般情况下定位精度通常是加工精度的1/2一1/3,因此数控机床的定位精度通常为0.05 -- 0.002 5mm。
而重复定位精度通常是定位精度的1/2一1/3,因此数控机床的重复定位精度通常为0.025一0.001 mm。
对于较大尺寸的零件加工的数控机床一般很注重定位精度,而对中、小型零件在考核加工尺寸的一致性时一般更注重重复定位精度。
从总体上说,由于数控机床的传动系统和机床结构具有很高的静、动刚度和热稳定性,机床本身的零部件具有很高的加工精度,特别是数控机床的自动加工方式避免了操作者人为的误差,因此同一批加工零件的尺寸一致性非常好,加工质量稳定、产品合格率高。
例如在采用点位控制的数控钻床上钻孔时,由于不再使用钻模板和钻套,钻模板的坐标误差造成的影响不复存在,又因为加工的敞开性改善了钻孔的排屑条件,可以进行有效的冷却,被加工孔的孔距精度,孔径尺寸精度和内孔表面质量均有所提高。
在数拄机床对复杂零件的轮廓表面进行加工时,由于编程中已考虑到对进给速度进行控制,保证刀具沿轮廓的切向进给的线速度基本不变,因而可以获得较高的精度和表面质量。
2.数控机床的应用范围半个世纪以来数控机床的应用范围正在不断扩大,数控技术已经渗透到许多领域。
数控车床工作精度验证

工件图
允差
尺寸 ﹤100 ﹤150 ﹤250 ﹤350 ﹤500
﹤750
范围1 0.008 0.010 0.015 — — — 0.010 0.003
范围2 — — — 0.020 0.025 0.035 0.020 0.005
谢谢观看/欢迎下载
BY FAITH I MEAN A VISION OF GOOD ONE CHERISHES AND THE ENTHUSIASM THAT PUSHES ONE TO SEEK ITS FULFILLMENT REGARDLESS OF OBSTACLES. BY FAITH I BY FAITH
轮廓的偏差检验方式
• 在数字控制下用一把单刃车刀车削试件的 轮廓。
工件图
• 所示的尺寸只适应于范围2:最大为 500。
• 对于范围1:最大为250机床的尺寸可 以由制造厂按比例缩小。
允差
• 范围1:最大为250的情况:0.030 • 范围2:最大为500的情况:0.045
基准半径的轮廓变化、直径的尺寸、 圆度误差检验方式
机床工作精度验证意义
• 数控机床完成以上的检验和调试后,实际 上已经基本完成独立各项指标的相关检验, 但是也并没有完全充分的体现出机床整体 的、在实际加工条件下的综合性能,而且 用户往往也非常关心整体的综合的性能指 标。所以还要完成工作精度的检验,以下 分别介绍数控车床的相关工作精度检验。
• 对于数控车床,根据GB/T 16462----1996 《数控卧式车床 精度检验》国家标准进行
工件图
范围1:最大为250 范围2:最大为500 Dmin=0.3L
允差
• 范围1:最大为250的情况:
– 圆度:0.003 – 切削加工直径的一致性:300长度上为0.020
数控机床精度检测报告
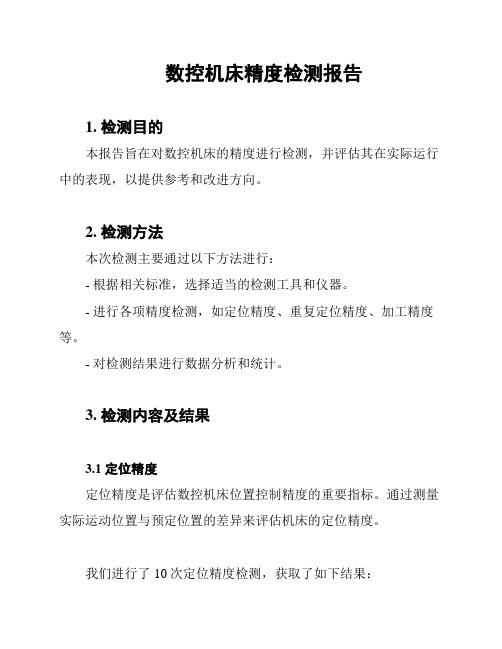
数控机床精度检测报告1. 检测目的本报告旨在对数控机床的精度进行检测,并评估其在实际运行中的表现,以提供参考和改进方向。
2. 检测方法本次检测主要通过以下方法进行:- 根据相关标准,选择适当的检测工具和仪器。
- 进行各项精度检测,如定位精度、重复定位精度、加工精度等。
- 对检测结果进行数据分析和统计。
3. 检测内容及结果3.1 定位精度定位精度是评估数控机床位置控制精度的重要指标。
通过测量实际运动位置与预定位置的差异来评估机床的定位精度。
我们进行了10次定位精度检测,获取了如下结果:- 平均偏差:0.02mm- 最大偏差:0.05mm3.2 重复定位精度重复定位精度是评估数控机床重复执行同一指令时的位置精度。
通过多次执行同一指令,并测量各次运动位置的偏差来评估重复定位精度。
我们进行了10次重复定位精度检测,获取了如下结果:- 平均偏差:0.03mm- 最大偏差:0.07mm3.3 加工精度加工精度是评估数控机床在实际加工过程中能够达到的精度水平。
通过进行实际加工并测量加工件的尺寸来评估加工精度。
我们进行了多个加工件的尺寸检测,并得出如下结果:- 加工件1:尺寸偏差±0.05mm- 加工件2:尺寸偏差±0.08mm- 加工件3:尺寸偏差±0.06mm4. 数据分析与评估基于以上检测结果,我们对数控机床的精度进行了评估。
4.1 优势数控机床在定位精度和重复定位精度方面表现良好,平均偏差较小,最大偏差也在可接受范围内。
4.2 不足数控机床在加工精度方面存在一定的改进空间,加工件的尺寸偏差较大,需要优化加工工艺和控制系统。
5. 改进方向基于上述评估结果,我们提出如下改进方向:- 进一步优化数控机床的控制算法,提高加工精度。
- 定期对数控机床进行维护和校准,确保其精度稳定性。
- 在加工过程中加强对工件尺寸的实时监测,及时进行调整和纠正。
6. 结论通过本次精度检测和评估,我们认为数控机床在定位精度和重复定位精度方面表现良好,但在加工精度方面仍有改进空间。
数控机床位置精度及标准

数控机床位置精度及标准数控机床是现代制造业中不可或缺的的设备,广泛应用于汽车、航空、医疗、工程机械等领域。
所谓数控机床位置精度,就是指数控机床在工作过程中所能达到的加工精度水平。
优秀的数控机床位置精度能够提高生产效率、提高质量保障以及节约成本。
一、数控机床位置精度的定义和分类机床精度是机床本身特性指标,机床加工精度则是机床的加工能力指标。
数控机床位置精度是指数控机床在工作过程中所能达到的加工精度水平。
根据加工对象的特点,数控机床加工的位置精度可以分为内外圆直径精度、平面度精度、位置精度和直线度精度等。
其中,内外圆直径精度是常见的量测指标,是个综合性的参数,直接关系到加工轴线的精度和轮廓的准确性;平面度精度则是指工件表面与基准面的平面度差值;位置精度是在绝对位置下测量,与工件的绝对位置有关;直线度精度是指在工作台坐标系上的误差。
二、数控机床位置精度的影响因素数控机床位置精度的影响因素很多,包括机床自身结构、控制系统、加工刀具与工件材料等。
具体影响因素如下:(1)机床结构。
机床的结构对数控机床位置精度的影响最为显著。
一般来说,机床的刚性越高,抗震性能越强,位置精度就越高。
在机床设计时,应考虑减小机床结构的自由度,对关键部位进行加强。
(2)控制系统。
数控机床的数控系统是机床能否达到指定精度的关键。
控制系统负责机床的运动控制,包括运动算法研究、算法设计、编程调试、自动补偿等方面。
数控机床应选择高精度、高速度、高稳定性的数控系统,以保证位置精度的稳定性。
(3)加工刀具。
加工刀具的优劣与数控机床位置精度也有着较大的关系。
良好的刀具可以确保工件轮廓的准确度、表面光洁度及加工精度,同时可以降低机床切削力、温度及振动,从而提高机床的稳定性及加工效果。
(4)工件材料。
加工对工件材料也有一定的要求。
不同工件材料表现出不同的加工特性,因此选择合适的工件材料也是保证数控机床位置精度的一条有效路径。
三、数控机床位置精度的检测和标准为了保证数控机床位置精度的优异表现,须定期对其进行检测。
数控机床精度检验
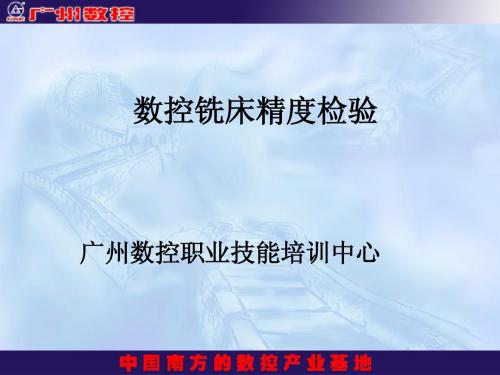
广州数控职业技能培训中心
§1 数控机床精度检验的必要性
数控机床的高精度最终是要靠机床本身的精度来 保证,数控机床精度包括几何精度和切削精度。另一 方面,数控机床各项性能的好坏及数控功能能否正常 发挥将直接影响到机床的正常使用。因此,数控机床 精度检验对初始使用的数控机床及维修调整后机床的 技术指标恢复是很重要的。
9、主轴旋转轴线对工作台(或立柱,或滑枕)横向移 动 的平行度 10、工作台中央或基准T形槽的直线度 11、主轴旋转轴线对工作台中央或基准T形槽的垂直 度(仅适用于卧式床身铣床) 12、中央或基准T形槽对工作台纵向移动的平行度 13、工作台(或立柱,或滑枕)横向移动对工作台纵 向移动的垂直度 14、直线运动坐标的定位精度 15、直线运动坐标的重复定位精度 16、直线运动坐标的平均反向值 (二)工件试切的精度:要求加工一个工件有圆、正 方形、六边形、球面。
• 1、参照GB/T17421.1,尤其是精度检验前的安装、 主轴及其部件的空运转升温和检验方法 • 2、参照GB/T17421.1--1998中3.1的规定,调整 机床安装水平。
机床水平调整安装要求:
• (1) 十字工作台型铣床调整安装水平时,将工 作台、滑座和主轴箱等移动部件分别置于行程的 中间位置,在工作台中央位置放置水平仪,水平 仪在纵向和横向的读数均不得超过 0.030/1000mm 。 • (2) 立柱移动型和滑枕移动型铣床调整安装水平 时,在床身导轨上放置圆检验棒(对V形导轨) 或板桥(对平导轨),圆检验棒和板桥上垂直于 床身导轨放一平尺。在圆检验棒、板桥和平尺上 各放一个水平仪:水平仪a和导轨平行,水平仪和 导轨垂直。调整导轨水平,水平仪a和b的读数均 不得超过0.03/1000。
数控机床的定位精度
浅析数控车床的加工精度

浅析数控车床的加工精度摘要:数控车床作为一种重要的加工设备,其加工精度直接影响到工件的质量和精度要求。
本文通过对数控车床的加工精度进行浅析,探讨了影响加工精度的因素,并提出了提高加工精度的方法与措施。
旨在为数控车床的加工精度提升提供一定的理论支持和实践指导。
关键词:数控车床;加工精度随着制造业的发展,数控车床作为一种高效、精确的加工设备,被广泛应用于各个领域。
而加工精度作为衡量数控车床性能的重要指标,对于满足工件的精度要求具有关键意义。
一、数控车床的加工精度概述数控车床加工精度是指在数控车床上进行加工过程中,工件达到的尺寸、形状和位置的精确程度。
它是衡量数控车床加工质量的重要指标之一。
随着工业技术的不断发展,数控车床在各个领域得到了广泛应用,而加工精度的提高也成为了人们关注的焦点。
首先,尺寸精度是数控车床加工中的一个重要方面。
在工件加工过程中,尺寸精度的高低直接影响着工件能否符合设计要求。
要提高尺寸精度,可以通过控制切削量、刀具和刀具夹持方式、工件夹紧方式等来实现。
只有确保这些因素的合理选择和控制,才能保证工件加工后的尺寸与设计要求之间的偏差尽可能小。
其次,形状精度也是数控车床加工中不可忽视的一点。
在实际应用中,工件的形状往往要求具备一定的几何精度,例如平面度、圆度、圆柱度等。
为了提高形状精度,可以采取优化工艺参数、选择合适的刀具和夹具、控制加工温度等措施。
通过这些方式,能够有效减小工件加工后形状与设计要求之间的偏差,确保工件的几何形状达到精确的要求。
此外,位置精度也是影响数控车床加工精度的重要因素之一。
位置精度主要指工件上各个特定点之间的相对位置精度,例如平行度、垂直度、同轴度等。
要提高位置精度,可以通过优化工艺参数、提高机床刚性、加强夹紧与定位等来实现。
只有确保工件在加工过程中的稳定性和精度,才能保证位置精度的提升。
最后,表面粗糙度也是数控车床加工精度的重要方面之一。
工件表面的光洁程度对于某些特定工件的功能和装配要求有着重要影响。
一、数控机床的精度检验

一、数控机床的精度检验一、数控机床的精度检验一、数控机床的精度检验数控机床的高精度最终是要靠机床本身的精度来保证,数控机床精度包括几何精度和切削精度。
另一方面,数控机床各项性能和性能检验对初始使用的数控机床及维修调整后机床的技术指标恢复是很重要的。
1. 几何精度检验几何精度检验,又称静态精度检验,是综合反映机床关键零部件经组装后的综合几何形状误差。
数控机床精度的检验工具和检验方法类似于普通机床,但检测要求更高。
几何精度检测必须在地基完全稳定、地脚螺栓处于压紧状态下进行。
考虑到地基可能随时间而变化,一般要求机床使用半年后,再复校一次几何精度。
在几何精度检测时,应注意测量方法及测量工具应用不当所引起的误差。
在检测时,应按国家标准规定,即机床接通电源后,在预热状态下,机床各坐标轴往复运动几次,主轴按中等转速运转十多分钟后进行。
常用的检测工具有精密水平仪、精密方箱、直角尺、平尺、平行光管、千分表、测微仪及高精度主轴心棒等。
检测工具的精度必须比所设的几何精度高一个等级。
以卧式加工中心为例,要对下列几何精度进行检验:1)X、Y、Z坐标轴的相互垂直度;2)工作台面的平行度;3)X、Z轴移动时工作台面的平行度;4)主轴回转轴线对工作台面的平行度;5)主轴在Z轴方向移动的直线度;6)X轴移动时工作台边界与定位基准的平行度;7)主轴轴向及孔径跳动;8)回转工作台精度。
2. 定位精度的检验数控机床的定位精度是表明所测量的机床各运动部位在数控装置控制下,运动所能达到的精度。
因此,根据实测的定位精度数值,可以判断出机床自动加工过程中能达到的最好的工件加工精度。
(1)定位精度检测的主要内容机床定位精度主要检测内容如下:1)直线运动定位精度(包括X、Y、Z、U、V、W轴);2)直线运动重复定位精度;3) 直线运动轴机械原点的返回精度;4) 直线运动失动量的测定;5) 直线运动定位精度(转台A 、B 、C 轴);6) 回转运动重复定位精度;7) 回转轴原点的返回精度;8) 回转运动矢动量的测定。
- 1、下载文档前请自行甄别文档内容的完整性,平台不提供额外的编辑、内容补充、找答案等附加服务。
- 2、"仅部分预览"的文档,不可在线预览部分如存在完整性等问题,可反馈申请退款(可完整预览的文档不适用该条件!)。
- 3、如文档侵犯您的权益,请联系客服反馈,我们会尽快为您处理(人工客服工作时间:9:00-18:30)。
1数控机床精度分析。
根据GB/T16462-2007《数控车床和车削中心检验条件》,卧式数控车床精度检验主要有3大项:几何精度检验(GB/T16462.1-2007);线性轴定位精度和重复定位精度检验(GB/T16462.4-2007)即位置精度检验;精加工试件精度检验(GB/T16462.6-2007)即工作精度检验。
数控车床几何精度主要包括主轴回转运动精度,线性轴直线运动精度。
主轴回转时,其回转轴线的空间位置应该固定不变,但实际上由于主轴部件中轴承,轴颈,轴承座孔等的制造误差和配合质量,润滑条件的影响,主轴实际回转轴线对其理想回转轴线呈现周期性飘移,即为主轴回转误差,表现为径向圆跳动和轴向窜动。
主轴轴承精度等级,主轴支承轴颈的圆度误差,主轴前后支承的同轴度误差,主轴箱体与主轴轴承系统的刚性,主轴及随其回转的零件的不平衡,主轴箱装配质量及主轴回转过程中热变形等因素影响了主轴的几何精度。
机床床身底座刚性和动态特性-负荷切削下机床抗变形能力,导轨布置形式,导轨自身的几何精度,导轨润滑条件等因素影响了线性轴直线运动精度。
GB/T16462.4-2007之线性轴定位精度是指在该轴行程内任意1个点定位时的误差范围,它综合反映了机床存在的几何误差,运动误差,热变形误差等,它与机床的几何精度共同对机床切削精度产生重要的影响,是数控车床最关键的技术指标。
线性轴重复定位精度,反映了该轴在行程内任意定位点的定位稳定性,这是衡量该轴能否稳定可靠工作的基本指标。
影响数控车床位置精度主要有丝杠的导程误差,传动链的反向间隙误差,导轨的摩擦阻尼,滚珠丝杠轴系的装配精度,伺服电机的惯量匹配等因素。
数控车床的电机,液压泵,卡盘油缸等连续运转的部件在运动过程中摩擦产生的热量会引起机床结构件的温度产生波动。
一方面,这些结构件会因温度变化产生线性尺寸的膨胀或收缩;另一方面,由于零件结构的不对称性,在内部热应力的作用下,必然出现结构的扭曲变形。
结构件热变形也是影响数控车床位置精度的一个重要因素。
只有提高数控车床的几何精度和位置精度,其工作精度才有可能得到保证。
数控车床工作精度不仅与机床自身静态精度有关,还与伺服系统跟踪误差,位置检测误差,刀具系统的位置误差,工件装夹误差有关。
另外,加工工艺的合理性,操作者的编程水平也影响到零件加工的稳定性。
因此,数控车床工作精度是一个综合影响的结果。
2提高数控车床精度保持性的技术措施。
数控车床已有数十年的发展历史,已积累形成了一系列成熟的先进技术。
生产1台性能稳定良好的机床,不是在于对每个零件提出很高要求,也不是在于选择使用高精度的配套件,而应在数控车床精度分析的基础上,掌握规律,从设计,制造开始就要进行全过程控制。
2.1做好数控车床的总体设计。
当前多数机床制造企业采取主机结构自行设计,功能部件外购的策略。
机床
整体设计遵循等刚度原则,把机床的变形均匀分配到力传递的每个部件上,避免刚度不均引起局部结构变形过大,出现刚度薄弱的部件。
机床机构重心对其动态特性性能影响很大,降低重心高度,可以有效提高摆动的模态频率。
在满足结构静刚度条件下,尽可能减少上部结构的材料使用量,使其重心下移。
主轴系统热态特性优化设计对数控车床加工精度及精度保持性尤为重要,一旦机床批量生产后发现热误差缺陷,机床在结构布局上很难改进。
主轴系统设计通常根据"热对称面"理论,即把最影响加工精度的零件配置在热对称面上,也就是说把通过数控车床主轴中心并垂直于床身底座的主轴箱安装面作为热对称面,主轴箱体两侧结构对称设计。
这样就能消除主轴中心因箱体发热产生的零点飘移现象,大大改善热变形所引起的加工精度不良的状况。
2.2提高主轴箱系统及床身导轨的几何精度的措施。
对数控车床来说,其加工精度保持性在很大程度上取决于主轴箱系统的几何精度。
设计人员要根据机床的加工精度要求和切削负荷类型,合理地确定主轴,轴承和主轴箱体的精度,选择合适的轴承类型,确定预加载荷形式。
因为轴承的内外圈均为薄壁件,主轴轴颈和箱体孔的形状和位置误差很容易引起轴承滚道变形,以至影响轴承的旋转精度。
因此在加工过程中要严格按照主轴前后轴颈的同轴度要求,特别是要控制好主轴箱体前后轴承孔的圆柱度和同轴度。
精加工后的主轴箱最后要研磨轴承孔,如图1所示,主轴箱垂直放置,研磨棒通过芯棒和工艺套保证与后轴承孔同轴,径向尺寸可调的研磨棒通过调整尺寸,逐步改善轴承孔形状,最后按照主轴轴承要求选配间隙。
在主轴箱部件装配时应注意以下几点:保持轴承清洁度,按照轴承手册要求加适量锂基润滑脂,控制好润滑脂的量就可以达到有效抑制主轴温升的效果。
用扭矩扳手控制主轴轴承预加载荷(根据轴承手册提供的参数),以消除轴承的轴向游隙,提高轴承的刚度和主轴的旋转精度。
主轴组的动平衡质量直接影响主轴高速回转时的振动,从而影响加工精度。
因此要按照主轴最高转速及精度要求,选择合适的动平衡等级。
数控车床一直在向高速,高负荷,高精度方向发展,对机床床身底座,导轨结构设计以及其刚度,抗振性和摩擦特性都提出了更高的要求。
全功能数控车床一般采用斜床身形式,床身尽量设计成封闭筒形结构,使得木模及铸造工艺简单,减轻铸件质量。
筒形结构相对增加了斜床身的抗弯和抗扭刚度,使机床在复杂的切削负荷条件下保持良好的精度。
在一定的伺服刚度条件下,运动副的摩擦特性直接影响数控车床的加工精度和工作稳定性。
基于移动速度较快,机床导轨应首选负载能力较大的圆柱滚子直线导轨。
对于经常用于高负荷切削的数控车床来说,为保证机床有较高的刚性和良好的精度保持性,常采用镶钢滑动导轨副结构。
经淬硬和磨削后的钢制滑动导轨用
螺钉安装在经导轨磨床磨削的安装面上,钢导轨与底座上导轨键之间用注塑材料固化后消除间隙,最后再在导轨磨床上整体磨削,以确保导轨获得最佳的几何精度。
滑动导轨与移动元件(拖板,十字拖板)接触面积比较大,拖板要作快速微量进给,需要克服移动部件的惯量,极易产生爬行现象,滑动面之间应选择优良的摩擦材料。
注塑材料因其静,动摩擦因数差值小,抗爬行性能好,在大,重型机床上应用比较多。
但注塑工艺比较复杂,加工成本高,随着机床以聚四氟乙烯为基材的导轨贴塑软带性能的不断改良,贴塑导轨也得到了广泛应用。
在数控车床的使用过程中应保持良好的润滑条件,减小导轨的摩擦阻力,避免低速重载下发生爬行现象,减小导轨磨损,保证精度持久性。
2.3提高数控车床位置精度的措施。
在伺服系统设计过程中应注意惯量匹配及力矩匹配,增加机械刚性和降低系统的惯性,减少机械传动部位的响应时间。
负载惯量JL由拖板及上面安装的刀架,滚珠丝杠,联轴器等直线和旋转运动件的惯量折合到伺服电机轴上的惯量组成,JL随切削负载改变而变化。
JM为伺服电机转子惯量。
要根据伺服电机的特性,控制JM与JL的比值。
在滚珠丝杠装配过程中应注意以下几点:丝杠两端轴承座固定后,确保丝杠上母线及侧母线分别与数控车床导轨主平面和次平面平行;确保丝杠螺母座轴线与丝杠轴线重合(修磨调整垫片);确保丝杠螺母座安装端面与丝杠轴线垂直。
丝杠是细长杆件,平行度偏差导致丝杠挠曲,直接影响定位精度。
丝杠螺母与丝杠螺母座安装端面不垂直会导致螺母受力不均,丝杠摩擦发热严重,引起丝杠热变形,将影响重复定位精度。
为保证丝杠有良好的刚性和动态特性,丝杠装配时必须做预拉伸,以补偿因温升所产生的热变形。
同时要控制丝杠两端的锁紧螺母的锁紧力矩和滚珠丝杠与伺服电机的联接刚度,否则会对机床的传动精度有影响。
应提高数控车床导轨的防护罩的性能和质量,钢制防护罩壳自身较重,其中间1层或几层护板是跟随拖板一起移动的,防护罩壳需要轻松,平稳的运行,不能有干涉现象,否则也会影响机床的定位精度。
2.4提高数控车床精度保持性的共性措施。
数控车床的床身底座,主轴箱,十字拖板等大结构件,在生产过程因铸造,热处理,机械加工产生的内应力残留在零件中,带有内应力的零件总是处于一种不稳定的状态。
为消除内应力引起零件的结构变形和几何精度变化,应选用合适的时效方法来消除内应力,如自然时效,热处理时效或者振动时效;其次,合理安排加工工艺,包括粗,精加工的次序和加工余量的分配,时效的次数和时间,在精加工之前尽可能消除零件内部的残余应力。
在数控车床装配过程中,刀架与上拖板,主轴箱和底座的固定结合面,滚珠丝杠的螺母座和轴承座与其固定结合面一定要进行刮研并作着色检验,确保部件结合面的接触刚度,这也是提高机床精度保持性的措施之一。
数控车床切削过程发热量大,为控制并减小机床的热变形,要进行冷却处理,并且要能够自动及时地排屑;对于发热大的部位,应加大其散热面积,改善散热或采取隔热处理。
还应该做好来工厂验收机床的用户培训,使用户正确,合理使用机床,定期保养机床,这对提高数控车床精度保持性非常重要。
3结语。
目前用户对国内生产的高精度数控车床信赖度低,主要原因在于国产高精度数控车床的可靠性,精度保持性与境外先进产品还有差距。
为了提高精度保持性,不仅要提高数控车床的设计水平,提高配套件技术含量,更应提高机床大件的制造工艺水平和装配综合调试水平,这需要大批优秀的专业工程师和技师。
数控车床作为一个高技术集成产品,要想做好需要多年的技术和人才积累,不应急功近利。
作为机床生产厂决不能只追求产品出厂时的良好精度指标,要对机床精度的持久性负责,要为用户持续创造价值提供可靠保证。