数控机床加工精度分析与应用.
数控机床的加工精度误差分析与精度校正技巧
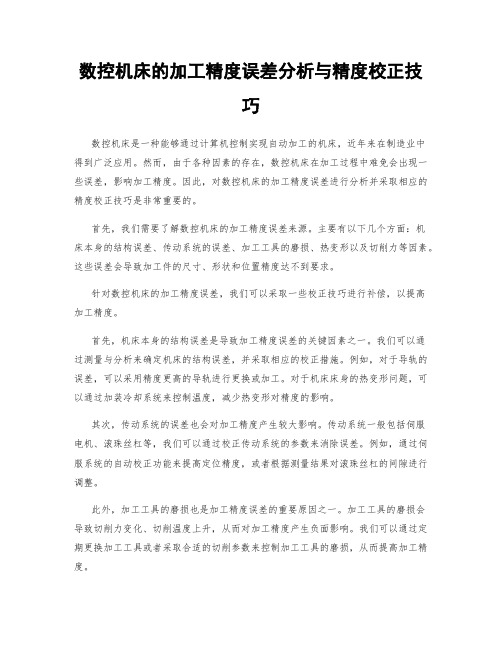
数控机床的加工精度误差分析与精度校正技巧数控机床是一种能够通过计算机控制实现自动加工的机床,近年来在制造业中得到广泛应用。
然而,由于各种因素的存在,数控机床在加工过程中难免会出现一些误差,影响加工精度。
因此,对数控机床的加工精度误差进行分析并采取相应的精度校正技巧是非常重要的。
首先,我们需要了解数控机床的加工精度误差来源。
主要有以下几个方面:机床本身的结构误差、传动系统的误差、加工工具的磨损、热变形以及切削力等因素。
这些误差会导致加工件的尺寸、形状和位置精度达不到要求。
针对数控机床的加工精度误差,我们可以采取一些校正技巧进行补偿,以提高加工精度。
首先,机床本身的结构误差是导致加工精度误差的关键因素之一。
我们可以通过测量与分析来确定机床的结构误差,并采取相应的校正措施。
例如,对于导轨的误差,可以采用精度更高的导轨进行更换或加工。
对于机床床身的热变形问题,可以通过加装冷却系统来控制温度,减少热变形对精度的影响。
其次,传动系统的误差也会对加工精度产生较大影响。
传动系统一般包括伺服电机、滚珠丝杠等,我们可以通过校正传动系统的参数来消除误差。
例如,通过伺服系统的自动校正功能来提高定位精度,或者根据测量结果对滚珠丝杠的间隙进行调整。
此外,加工工具的磨损也是加工精度误差的重要原因之一。
加工工具的磨损会导致切削力变化、切削温度上升,从而对加工精度产生负面影响。
我们可以通过定期更换加工工具或者采取合适的切削参数来控制加工工具的磨损,从而提高加工精度。
另外,热变形也是影响加工精度的重要因素。
随着机床的连续工作,温度会逐渐升高,导致机床的热变形。
我们可以通过在机床上安装温度传感器,监测温度的变化,然后根据变化的温度对加工精度进行校正。
此外,通过改进机床的散热系统,减少热量的积聚,也可以有效地降低热变形对加工精度的影响。
最后,我们还可以通过控制切削力来提高加工精度。
切削力对加工精度具有较大的影响,对切削力的控制可以通过调整切削参数(如切削速度、进给量等)来实现。
4--数控铣床的性能指标与功能
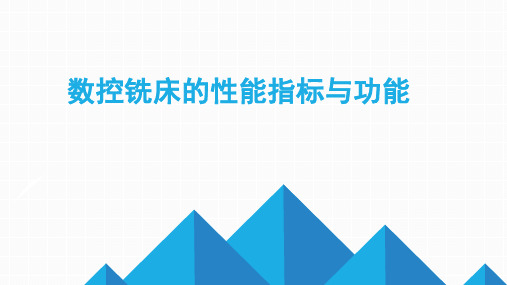
• 6、模态、非模态指令 模态指令也称续效指令,一经程序段中指 令,便一直有效,直到以后程序段中出现同组另一指令或被其它 指令取消是才失效。
• 三、程序编制的分类 • 1.编程的两大方法 • 1)手工编程:由操作者或程序员以人工方式完成整个加工程序编制工作的
方法。
• 2)自动编程:主要由计算机及其外围设备组成的自动编程系统完成加工程 序编制的方法。
• 3、坐标行程
• 数控机床坐标轴 X 、 Y 、 Z 的行程大小,构成数控机床的空间加工范围,即加 工零件的大小。
• 4、刀库容量和换刀时间
• 刀库容量是指刀库能存放加工所需要的刀具数量。目前常见的中小型加工中心多 为16~60把,大型加工中心达100 把以上。
• 换刀时间指有自动换刀系统的数控机床,将主轴上使用的刀具与装在刀库上的下 一工序需用的刀具进行交换所需要的时间。目前国内生产的数控机床的换刀时间可 达到4∽5s。
数控机床的加工精度误差分析与校正方法
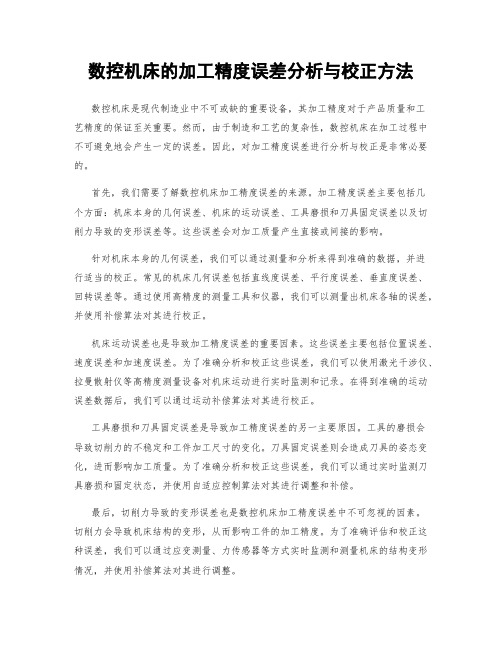
数控机床的加工精度误差分析与校正方法数控机床是现代制造业中不可或缺的重要设备,其加工精度对于产品质量和工艺精度的保证至关重要。
然而,由于制造和工艺的复杂性,数控机床在加工过程中不可避免地会产生一定的误差。
因此,对加工精度误差进行分析与校正是非常必要的。
首先,我们需要了解数控机床加工精度误差的来源。
加工精度误差主要包括几个方面:机床本身的几何误差、机床的运动误差、工具磨损和刀具固定误差以及切削力导致的变形误差等。
这些误差会对加工质量产生直接或间接的影响。
针对机床本身的几何误差,我们可以通过测量和分析来得到准确的数据,并进行适当的校正。
常见的机床几何误差包括直线度误差、平行度误差、垂直度误差、回转误差等。
通过使用高精度的测量工具和仪器,我们可以测量出机床各轴的误差,并使用补偿算法对其进行校正。
机床运动误差也是导致加工精度误差的重要因素。
这些误差主要包括位置误差、速度误差和加速度误差。
为了准确分析和校正这些误差,我们可以使用激光干涉仪、拉曼散射仪等高精度测量设备对机床运动进行实时监测和记录。
在得到准确的运动误差数据后,我们可以通过运动补偿算法对其进行校正。
工具磨损和刀具固定误差是导致加工精度误差的另一主要原因。
工具的磨损会导致切削力的不稳定和工件加工尺寸的变化。
刀具固定误差则会造成刀具的姿态变化,进而影响加工质量。
为了准确分析和校正这些误差,我们可以通过实时监测刀具磨损和固定状态,并使用自适应控制算法对其进行调整和补偿。
最后,切削力导致的变形误差也是数控机床加工精度误差中不可忽视的因素。
切削力会导致机床结构的变形,从而影响工件的加工精度。
为了准确评估和校正这种误差,我们可以通过应变测量、力传感器等方式实时监测和测量机床的结构变形情况,并使用补偿算法对其进行调整。
总结来说,数控机床的加工精度误差分析与校正是确保产品质量和工艺精度的关键步骤。
在这个过程中,我们需要准确地识别和分析加工精度误差的来源,并采取相应的校正措施。
数控机床的精度与应用范围
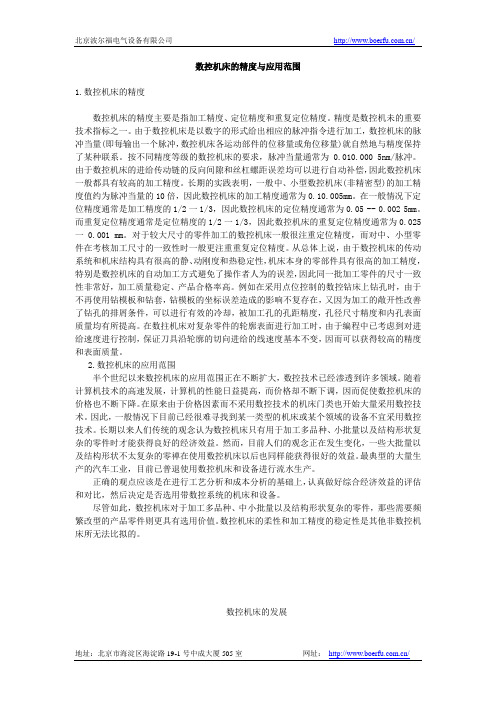
数控机床的精度与应用范围1.数控机床的精度数控机床的精度主要是指加工精度、定位精度和重复定位精度。
精度是数控机未的重要技术指标之一。
由于数控机床是以数字的形式给出相应的脉冲指令进行加工,数控机床的脉冲当量(即每输出一个脉冲,数控机床各运动部件的位移量或角位移量)就自然地与精度保持了某种联系。
按不同精度等级的数控机床的要求,脉冲当量通常为0.010.000 5nm/脉冲。
由于数控机床的进给传动链的反向间隙和丝杠螺距误差均可以进行自动补偿,因此数控机床一般都具有较高的加工精度。
长期的实践表明,一般中、小型数控机床(非精密型)的加工精度值约为脉冲当量的10倍,因此数控机床的加工精度通常为0.10.005mm。
在一般情况下定位精度通常是加工精度的1/2一1/3,因此数控机床的定位精度通常为0.05 -- 0.002 5mm。
而重复定位精度通常是定位精度的1/2一1/3,因此数控机床的重复定位精度通常为0.025一0.001 mm。
对于较大尺寸的零件加工的数控机床一般很注重定位精度,而对中、小型零件在考核加工尺寸的一致性时一般更注重重复定位精度。
从总体上说,由于数控机床的传动系统和机床结构具有很高的静、动刚度和热稳定性,机床本身的零部件具有很高的加工精度,特别是数控机床的自动加工方式避免了操作者人为的误差,因此同一批加工零件的尺寸一致性非常好,加工质量稳定、产品合格率高。
例如在采用点位控制的数控钻床上钻孔时,由于不再使用钻模板和钻套,钻模板的坐标误差造成的影响不复存在,又因为加工的敞开性改善了钻孔的排屑条件,可以进行有效的冷却,被加工孔的孔距精度,孔径尺寸精度和内孔表面质量均有所提高。
在数拄机床对复杂零件的轮廓表面进行加工时,由于编程中已考虑到对进给速度进行控制,保证刀具沿轮廓的切向进给的线速度基本不变,因而可以获得较高的精度和表面质量。
2.数控机床的应用范围半个世纪以来数控机床的应用范围正在不断扩大,数控技术已经渗透到许多领域。
数控机床的加工精度达到多少

数控机床的加工精度达到多少数控机床加工精度是指零件加工后的实际几何参数(尺寸、形状和位置)与图纸规定的理想几何参数符合的程度。
这种相符合的程度越高,加工精度也越高。
加工精度高数控机床的加工精度一般可达0.050.1MM,数控机床是按数字信号形式控制的,数控装置每输出一脉冲信号,则机床移动部件移动一具脉冲当量(一般为0.001MM),而且机床进给传动链的反向间隙与丝杆螺距平均误差可由数控装置进行曲补偿,因此,数控机床定位精度比较高,不过目前各个数控机床的加工精度根据机床品牌,机床类型,数控机床操作人员技术等因素都会造成数控机床的加工精度差异。
数控机床的加工精度一般可达0.050.1MM,数控机床是按数字信号形式控制的,数控装置每输出一脉冲信号,则机床移动部件移动一具脉冲当量(一般为0.001MM),而且机床进给传动链的反向间隙与丝杆螺距平均误差可由数控装置进行曲补偿,因此,数控机床定位精度比较高。
数控机床在进行加工过程中难免会受到各种各样因素的影响,使得其加工精度产生一定的偏差,给生产生活带来一些不便。
怎样提高数控机床加工精度是工程师们很关心的事情。
数控机床加工中的位置误差对加工精度的影响位置误差是指加工后零件的实际表面、轴线或对称平面之间的相互位置相对于其理想位置的变动量或偏离程度,如垂直度、位置度、对称度等。
数控机床加工中的位置误差通常指死区误差,产生位置误差的原因主要在机床零件加工时由于传动时产生的间隙和弹性变形导致加工误差,以及在加工中,机床的刀头需要克服摩擦力等因素导致产生位置误差。
在开环系统中位置精度受到的影响是很大的,而在闭环随动系统中,则主要取决于位移检测装置的精度和系统的速度放大系数,一般影响较小。
数控机床加工中由于几何误差导致的加工精度误差数控机床加工中,由于刀具和夹具在受外力和加工中产生的热量等外界因素的影响下,机床的几何精度受到影响,机床上加工的零部件产生几何变形,从而导致产生几何误差。
解析数控车床加工精度的影响因素及提高措施
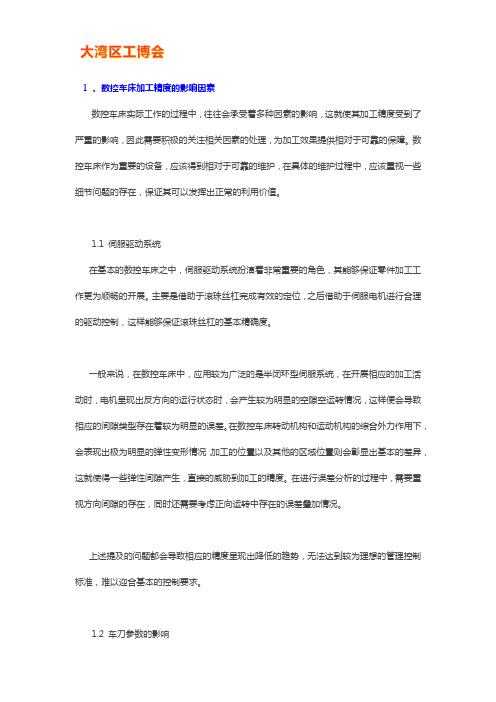
1 、数控车床加工精度的影响因素数控车床实际工作的过程中,往往会承受着多种因素的影响,这就使其加工精度受到了严重的影响,因此需要积极的关注相关因素的处理,为加工效果提供相对于可靠的保障。
数控车床作为重要的设备,应该得到相对于可靠的维护,在具体的维护过程中,应该重视一些细节问题的存在,保证其可以发挥出正常的利用价值。
1.1 伺服驱动系统在基本的数控车床之中,伺服驱动系统扮演着非常重要的角色,其能够保证零件加工工作更为顺畅的开展。
主要是借助于滚珠丝杠完成有效的定位,之后借助于伺服电机进行合理的驱动控制,这样能够保证滚珠丝杠的基本精确度。
一般来说,在数控车床中,应用较为广泛的是半闭环型伺服系统,在开展相应的加工活动时,电机呈现出反方向的运行状态时,会产生较为明显的空隙空运转情况,这样便会导致相应的间隙类型存在着较为明显的误差。
在数控车床转动机构和运动机构的综合外力作用下,会表现出极为明显的弹性变形情况,加工的位置以及其他的区域位置则会彰显出基本的差异,这就使得一些弹性间隙产生,直接的威胁到加工的精度。
在进行误差分析的过程中,需要重视方向间隙的存在,同时还需要考虑正向运转中存在的误差叠加情况。
上述提及的问题都会导致相应的精度呈现出降低的趋势,无法达到较为理想的管理控制标准,难以迎合基本的控制要求。
1.2 车刀参数的影响通常来讲,在数控车床的加工实践中,往往是借助于编程控制的基本手段落实车刀的调整,保证可以更加顺畅的开展零部件的切削工作,由此让其基本的形状符合相应的要求。
在车削加工的基本环节之中,车刀一般会反映出主偏角以及刀尖圆弧半径的基本数值,在对棒料进行适当的加工时,轴向的尺寸还是很容易产生一些误差问题,面对这样的情况应该做出合理的分析,判断这类误差和主偏角往往是呈现出一种反比的关系,当不断地增加相应的主偏角之后,相应的误差可以适当的降低,但是对比于刀尖圆弧半径来看,两者之间还是存在着正比的关联。
如果在具体加工的过程中车刀的参数发生了较为显著的变化,会使得相应的精度受到较为直接的影响。
CNC机床加工中的加工精度评估与标准
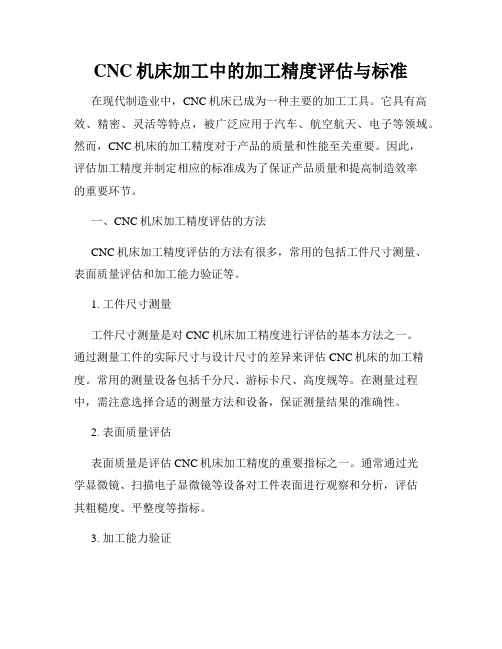
CNC机床加工中的加工精度评估与标准在现代制造业中,CNC机床已成为一种主要的加工工具。
它具有高效、精密、灵活等特点,被广泛应用于汽车、航空航天、电子等领域。
然而,CNC机床的加工精度对于产品的质量和性能至关重要。
因此,评估加工精度并制定相应的标准成为了保证产品质量和提高制造效率的重要环节。
一、CNC机床加工精度评估的方法CNC机床加工精度评估的方法有很多,常用的包括工件尺寸测量、表面质量评估和加工能力验证等。
1. 工件尺寸测量工件尺寸测量是对CNC机床加工精度进行评估的基本方法之一。
通过测量工件的实际尺寸与设计尺寸的差异来评估CNC机床的加工精度。
常用的测量设备包括千分尺、游标卡尺、高度规等。
在测量过程中,需注意选择合适的测量方法和设备,保证测量结果的准确性。
2. 表面质量评估表面质量是评估CNC机床加工精度的重要指标之一。
通常通过光学显微镜、扫描电子显微镜等设备对工件表面进行观察和分析,评估其粗糙度、平整度等指标。
3. 加工能力验证加工能力验证是评估CNC机床加工精度的定量方法之一。
通过制定一系列的加工试验,比如圆度试验、直线度试验等,得出CNC机床的实际加工能力。
加工能力验证可以帮助制定合理的加工参数和工艺流程,提高加工效率和加工精度。
二、CNC机床加工精度的评估标准为了确保CNC机床加工的稳定性和精度,制定相应的评估标准至关重要。
下面介绍几种常用的CNC机床加工精度评估标准。
1. 国家标准不同国家制定了相应的CNC机床加工精度评估标准。
例如中国的《数控机床精度检验标准》(GB/T 16672-2008)规定了CNC机床的加工精度分级与检验方法,包括几何精度、运动精度和位置精度等指标。
2. 行业标准各行业也制定了相应的CNC机床加工精度评估标准。
以航空航天行业为例,美国航空航天协会(AIA)制定了《航空航天产品精度与质量评估标准》(AIA NAS-970)。
该标准覆盖了航空航天产品的设计、制造和验收等方面,对CNC机床加工精度进行了详细的规定。
数控加工精度数控加工精度
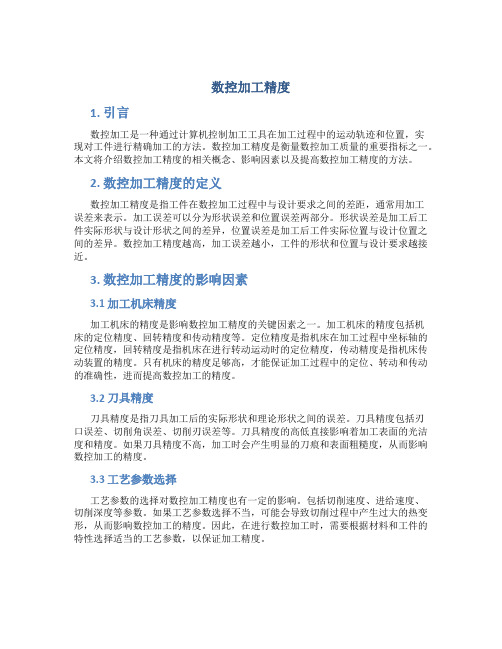
数控加工精度1. 引言数控加工是一种通过计算机控制加工工具在加工过程中的运动轨迹和位置,实现对工件进行精确加工的方法。
数控加工精度是衡量数控加工质量的重要指标之一。
本文将介绍数控加工精度的相关概念、影响因素以及提高数控加工精度的方法。
2. 数控加工精度的定义数控加工精度是指工件在数控加工过程中与设计要求之间的差距,通常用加工误差来表示。
加工误差可以分为形状误差和位置误差两部分。
形状误差是加工后工件实际形状与设计形状之间的差异,位置误差是加工后工件实际位置与设计位置之间的差异。
数控加工精度越高,加工误差越小,工件的形状和位置与设计要求越接近。
3. 数控加工精度的影响因素3.1 加工机床精度加工机床的精度是影响数控加工精度的关键因素之一。
加工机床的精度包括机床的定位精度、回转精度和传动精度等。
定位精度是指机床在加工过程中坐标轴的定位精度,回转精度是指机床在进行转动运动时的定位精度,传动精度是指机床传动装置的精度。
只有机床的精度足够高,才能保证加工过程中的定位、转动和传动的准确性,进而提高数控加工的精度。
3.2 刀具精度刀具精度是指刀具加工后的实际形状和理论形状之间的误差。
刀具精度包括刃口误差、切削角误差、切削刃误差等。
刀具精度的高低直接影响着加工表面的光洁度和精度。
如果刀具精度不高,加工时会产生明显的刀痕和表面粗糙度,从而影响数控加工的精度。
3.3 工艺参数选择工艺参数的选择对数控加工精度也有一定的影响。
包括切削速度、进给速度、切削深度等参数。
如果工艺参数选择不当,可能会导致切削过程中产生过大的热变形,从而影响数控加工的精度。
因此,在进行数控加工时,需要根据材料和工件的特性选择适当的工艺参数,以保证加工精度。
3.4 材料特性不同材料的特性也会对数控加工精度产生影响。
有些材料容易产生切削刃磨损,有些材料容易产生热变形,还有些材料容易产生划伤等问题。
在进行数控加工时,需要根据不同材料的特性选择合适的刀具和工艺参数,以提高数控加工的精度。
数控机床加工中的瑕疵分析与解决方法

数控机床加工中的瑕疵分析与解决方法随着科技的不断进步和发展,数控机床作为一种先进的加工设备,在各个行业中得到了广泛的应用。
然而,在数控机床加工过程中,瑕疵问题不可避免地出现。
本文将对数控机床加工中常见的瑕疵进行分析,并提供解决方法,以帮助读者更好地应对这些问题。
一、瑕疵分析1. 加工精度不高:数控机床的加工精度是影响产品质量的重要因素。
加工精度不高可能导致尺寸偏差、表面粗糙度不达标等问题。
2. 加工失真:加工失真主要是指加工过程中由于热变形、应力集中等原因导致加工形状与设计要求不符合。
3. 加工热损伤:由于数控机床加工过程中涉及高速切削、高温摩擦等因素,可能会导致零件表面出现热损伤,如烧伤、氧化等。
4. 加工表面质量不佳:数控机床加工表面质量是考验产品外观质量的重要指标,表面存在凹凸不平、毛刺、划痕等问题,会影响产品的档次和使用寿命。
二、解决方法1. 提高加工精度:首先应对数控机床进行维护保养,保证设备的正常工作状态。
其次,选择合适的刀具和切削参数,并按照加工标准进行程序的编写和调试,以确保加工精度的达标。
2. 预防加工失真:加工失真问题主要与材料的热变形和应力有关。
因此,在选择材料时要根据产品的要求选择合适的材料,避免出现热变形和应力集中的情况。
另外,在加工过程中,要控制加工温度,避免过高的温度对材料的影响。
3. 预防加工热损伤:数控机床在加工时会产生大量热量,主要集中在刀具和工件之间的切削区域。
为了预防加工热损伤,可以采用切削液冷却的方法,及时将热量带走,保持切削区域的温度在适宜范围内。
4. 改善加工表面质量:为了改善加工表面质量,可以采用一些方法,如切削参数的调整、切削工艺的优化、使用合适的刀具和刀具涂层等。
此外,还可以采用表面处理技术,如砂光、抛光、氮化等,来改善加工表面质量。
总结:数控机床加工中的瑕疵是无法避免的,但通过合理的分析和解决方法,可以有效地减少瑕疵的发生率,提高产品质量。
在实际应用中,需要根据具体情况选择相应的措施,并进行合理的调试和优化。
机床数控技术及其应用

第4章
1. 插补:在一条曲线的已知起点和终点之间进行“数据点的密化工作”。 2. 并行处理的实现方式:资源分时共享(单 CPU) ;资源重叠流水处理(多 CPU)
第5章
1. 数据采样插补采用时间分割思想 2. 把加工一段直线或圆弧的整段时间细分为许多相等的时间间隔,称为插补周期 T; 插补周期 T 与采样周期 T 反馈可相同或不同,一般:T= T 反馈的整数倍。 3. 逐点比较法特点:运算直观,最大插补误差≤1 个脉冲当量,脉冲输出均匀,调节方便 4. 逐点比较法直线插补:令 为偏差判别函数,则有: 1)Fi,j≥0 时,向+X 方向进给一个脉冲当量,到达点 Pi+1,j,此时 xi+1=xi+1,则点 Pi+1,j 的 偏差判别函数 Fi+1,j 为
机床数控技术及其应用
第1章
1. 数控技术正在向高速度、高精度、智能化、网络化以及高可靠性等方向迅速发展 2. 机床数控技术由机床本体、数控系统和外围技术组成 3. CNC --- 计算机数控系统(Computer Numerical Control ) 4. 数控系统的核心是 CNC 装置
5. 闭环控制的位置检测装置安装在机床刀架或者工作台等执行部件上 6. 半闭环控制的位置检测装置安装在伺服电机上或丝杠的端部
第6章
1. 数控系统中的检测装置分为位移、速度和电流三种类型 安装的位置及耦合方式—直接测量和间接测量; 测量方法———————增量型和绝对型; 检测信号的类型————模拟式和数字式; 运动型式———————回转型和直线型; 信号转换的原理————光电效应、光栅效应、电磁感应原理、压电效应、压阻效应和磁 阻效应等 2. 旋转变压器是一种输出电压与角位移量成连续函数关系的感应式微电机,数控机床上常 见的角位移测量装置 3. 定尺节距ω2 即为检测周期 2τ是衡量感应同步器精度的主要参数。常取 2τ=2mm相位 。 360 4. 正弦绕组和余弦绕组在空间错开 1/4 定尺节距(相当于电角度错开π/2) 5. 当滑尺移动距离为 2,V 2 变化 2,当移动 x 时,则对应感应电压以余弦函数变化 角 度。可得: 6. 对于栅距 d 相等的指示光栅和标尺光栅,当两光栅尺沿线纹方向保持一个很小的夹角θ , 刻划面平行且有一个很小间隙(一般 0.05mm,0.1mm) ,在光源照射下,在与两光栅线纹 角θ的平分线相垂直的方向上,形成明暗相间条纹——莫尔条纹(横向莫尔条纹) , 两条亮 (暗)纹间的距离称莫尔条纹宽度 w 。 7. 莫尔条纹特性: (1)光学放大作用 放大比 k 为 :
CNC机床加工中的加工力学分析与优化

CNC机床加工中的加工力学分析与优化近年来,随着工业技术的快速发展,CNC(计算机数控)机床加工已经成为现代制造业中不可或缺的一环。
CNC机床加工的高精度和高效率使得许多企业在生产过程中寻求该技术的应用。
然而,要实现高精度加工,需要对加工力学进行深入的分析和优化。
本文将对CNC机床加工中的加工力学进行探讨,并提出优化的方法。
一、加工力学分析1.工件材料力学参数测定在进行加工力学分析之前,首先需要测定工件材料的力学参数。
工件材料的力学参数包括杨氏模量、泊松比等,它们对加工力学的分析具有重要影响。
可以通过材料测试仪器对工件材料进行力学参数测定,以获得准确的数据作为分析的基础。
2.切削力计算切削力是CNC机床加工中的重要参数之一。
切削力的大小直接影响到加工件表面的粗糙度和加工效率。
通常,可以通过理论计算或实验测量来得到切削力的数值。
理论计算需要考虑切削过程中的切削速度、进给速度、切削力系数等因素,并结合加工力学模型进行分析。
对于复杂的工件形状,可以通过试验手段进行切削力的实时测量。
3.表面粗糙度除了切削力,表面粗糙度也是CNC机床加工中一个重要的指标。
通过合理的加工力学分析,可以优化切削参数,从而改善表面质量。
常见的优化方法包括调整切削速度、进给速度、加工深度等,以达到最佳的加工效果。
二、加工力学优化1.切削参数优化CNC机床加工中的切削参数优化是提高加工质量和效率的关键。
通过实验和模拟分析,可以找到最佳的切削速度、进给速度和切削深度等参数。
同时,还可以考虑刀具材料和几何形状等因素,以进一步优化切削过程中的加工力学。
2.刀具设计优化刀具的设计对于CNC机床加工中的加工力学也具有重要意义。
通过合理的刀具设计,可以降低切削力和振动,提高加工质量和工具寿命。
因此,在CNC机床加工过程中应该选择适合的刀具类型和刀具材料,并进行刀具设计的优化。
3.机床刚度优化机床刚度对于加工力学分析和优化也起着重要的影响。
较高的机床刚度可以减少振动和变形,提高加工精度和表面质量。
数控机床加工定位精度误差及实例

服 因细 长轴挠度变形而形成的 定位精 度误 差和传递运动 滞后 的现象出现 ,可以大大提 高运 动部 件的定位精度和 反向速 度。
项 技术 因素 ,从而 能实现 应用 先进 的数控 设备 、合理
和优化 的加 工工 艺 ,来 充分保 证产 品的 质量和 数量 , 达 到产出的最大化。 决定 加工 产品精 度好 坏的 因素有 很 多 ,涉 及数控 机床本身有两项精度指标 :
式 中 代表数控机 床坐标轴的长 度。针对数控机 床
的定位 精度 来说 ,应该 是与机 床的 动态精 度有 着密切 的利 害关系。 目前数控设备运动轴传递 形式大约以6 m为界限 ,小
精 度误 差参数的补偿即螺7 <偿。在 加工产品时定位精 1b  ̄ 度决定产品的形位公差尺寸 ,但是 考核机床加工产品精 度另一 重要指标是重复定位精 度。特别是在加工同一轴
于该长度的大部分都采用滚珠丝杆传递运动 ( 见图1 , )
建议最好通过调整机械 系统的预紧力来消除。
图 1
数控 机 床在 实际应 用 中遇 到问题 和 发现加 工精 度
超差 ,不能满足工艺要求的情况和 种类有许 多,有时与 系统有关 ,只要通过 系统进 行参数补偿和漂移补偿就能
这种滚珠 丝杆的螺母可以调整预 紧力的结构 。大 干该长 度的基本都采用双 电动机双 齿轮 齿条消隙机构装置作为
现象:当数控外圆磨床砂轮架 轴在磨肖]件时, J f:
发现 磨削工件的尺寸有变化 ,难以控 制和掌握 。
诊断 :首先 用仪表 检查 机械机 构的进 给 系统 ,没 有发现砂轮架 轴 快进 液压油缸漂移和进给滚珠丝杆存
2停机后重起机床定位精度严重误差 .
现 象 :机床在 加工 工件后 ,停 机切断 电源 重新起 动 ,回 - 点发现与停机前最大 有2 rm 由 原 . 左右 不定的 3 a
机床数控技术及应用

伺服系统
伺服系统是数控机床的重要组成部分,负责接收数控装置 发出的运动指令,驱动机床的各个运动部件按照指令要求 进行运动。
辅助装置
辅助装置包括润滑装置、冷却装置、排屑装置等,用于辅 助机床的正常运行。
机床数控系统的运行原理
零件程序的输入
通过输入输出装置将零件程序输入到数控 装置中。
检测反馈
在机床运动过程中,检测装置检测机床的 实际位置和速度,反馈给数控装置,数控 装置根据反馈信息进行误差补偿和控制。
数控车床在航天工业中的应用
在航天工业中,由于对零件的精度和可靠性要求极高,数控车床得到了广泛应用,能够加 工各种高精度的零件和复杂的结构件。
数控铣床的应用实例
数控铣床在模具制造中的应用
数控铣床可以加工各种复杂的模具型腔和型芯,如注塑模具、压铸模具等,能够大大提 高模具的制造精度和生产效率。
数控铣床在机械零件加工中的应用
机床数控技术及应用
目 录
• 引言 • 机床数控技术概述 • 机床数控技术的原理 • 机床数控技术的应用实例 • 机床数控技术的优势与挑战 • 结论
01 引言
主题简介
数控技术
数控技术是一种基于数字控制的 制造技术,通过计算机编程实现 机床的自动化加工。
应用领域
数控技术广泛应用于机械制造、 航空航天、汽车制造、模具加工 等领域。
维护成本。
数控机床在加工过程中 存在一定的安全风险, 需要加强安全防护措施。
机床数控技术的发展趋势
智能化发展
随着人工智能技术的发展,数控技术 将进一步实现智能化,提高加工精度 和效率。
复合化发展
未来数控机床将向复合加工方向发展, 实现多轴联动加工,提高加工效率和 精度。
数控技术在精密零件加工中的应用与优化研究

随着现代制造业的迅速发展,精密零件在各个领域中的重要性日益凸显。
而在精密零件的制造过程中,数控技术作为一种高效、精准的加工手段,为实现高质量、高精度的零件生产提供了强大支持。
数控技术以其灵活的加工方式、精确的控制能力以及自动化程度高的特点,已经在精密零件加工领域得到了广泛应用。
它不仅提高了零件的加工精度和生产效率,还为制造业转型升级、推动工业智能化提供了重要推动力。
本文旨在深入探讨数控技术在精密零件加工中的应用与优化研究,以期揭示数控技术在提升精密零件加工质量和效率方面的潜力。
数控技术在精密零件加工中的应用不仅极大地提高了零件加工的精度和效率,同时也为加工过程的控制提供了更高的灵活性和精确性。
通过数控技术,加工过程可以实现更精细的控制,从而确保零件的尺寸和形状符合设计要求。
首先,数控技术通过精密的运动控制系统,能够精确地控制加工工具在多个坐标轴上的运动轨迹和速度,实现复杂形状零件的加工[1]。
这种高度的运动控制能力使得加工过程更加稳定,减少了操作人员的操作误差,从而保障了零件的加工质量。
其次,数控技术可以实现加工过程的自动化和批量生产,大大提高了生产效率。
操作人员只需编写好加工程序并进行适当的设置,数控机床便可以自动地执行加工过程,不仅减少了人力投入,还降低了人为因素对加工精度的影响,从而确保了零件的稳定质量。
工艺参数优化首先涉及切削速度、进给速度和切削深度等参数的调整。
通过数控技术,这些参数可以进行精细的调节和控制,从而实现最佳的切削效果。
合理的工艺参数可以降低切削力和温度,减轻刀具磨损,从而延长刀具的使用寿命,并保证加工零件的尺寸精度和表面质量。
与此同时,工艺参数优化还包括材料选择和刀具设计方面的考虑。
数控技术可以根据不同材料的物理特性和切削要求,自动调整加工参数,以实现更佳的加工效果。
同时,针对不同形状和尺寸的精密零件,数控技术可以根据刀具的特性和加工路径,进行智能化的刀具设计,以确保加工过程的稳定性和一致性。
高精度数控技术的研究与应用

高精度数控技术的研究与应用一、引言高精度数控技术是目前在机械加工领域中备受关注的一个话题。
数控技术的应用已经成为了工业生产和科技发展的不可或缺的一部分。
高精度数控技术的出现则进一步改善了数控系统的精度,并促进了多个领域的创新。
本文将就高精度数控技术的研究和应用展开介绍。
二、高精度数控技术简介数控技术是利用计算机等现代科技手段来实现机器运动控制和加工的技术。
其优点是提高了加工精度和自动化水平,降低了人力消耗和加工时间,其中高精度数控技术即是数控技术中提高了精度的技术。
高精度数控技术包含很多方面的技术手段,包括优化误差补偿算法、高精度控制方法、高精度测量技术、机床结构设计等。
通过对上述技术进行改进和发展,将能使数控系统的精度达到亚微米级别,大大提高了加工的精度和效率。
三、高精度数控技术的研究高精度数控技术的研究是一个复杂且不断发展的领域。
以下将分别介绍误差补偿技术、控制系统设计、传感器技术等方面在高精度数控技术中的应用和发展。
1. 误差补偿技术误差补偿技术是提高精度的一个重要手段。
在实际加工中,往往会出现误差,这些误差可能是由于数控系统本身的误差或者外界因素引起的。
因此需要采用一些算法方法来对这些误差进行补偿,以提高系统的精度。
误差补偿技术主要包括传统误差补偿和自适应误差补偿技术。
传统误差补偿技术主要包括比例积分微分(PID)控制器、模型预测控制器(MPC)等方法。
自适应误差补偿技术则是根据实时误差进行自适应补偿。
这些技术能较好地补偿普通加工中的误差,但对于高精度加工则尚需进一步完善。
2. 控制系统设计控制系统是数控系统中的一个重要组成部分。
在高精度数控技术中,需要使用高精度控制器以及其他高精度传感器和执行器等元器件,以降低系统的干扰,提高系统的控制精度。
为了保证高精度数控系统的稳定性,需要对控制系统进行精细的设计和计算。
例如,有些加工工艺对于系统的动态响应要求很高,需要使用高精度控制器,并对控制系统中的采样周期、控制参数等进行合理的设计和调整。
数控机床技术中的工件质量问题分析与解决

数控机床技术中的工件质量问题分析与解决随着工业技术的发展和进步,数控机床已经成为现代制造业中不可或缺的设备之一。
数控机床以其高效、高精度的加工能力,广泛应用于各个领域,例如汽车制造、航空航天、船舶建造等。
然而,在数控机床加工过程中,工件质量问题往往会成为制约加工效果的关键,因此,对于工件质量问题的分析与解决显得尤为重要。
工件质量问题的分析是解决问题的关键之一。
数控机床加工过程中,常见的工件质量问题包括尺寸偏差、表面粗糙度、平行度、圆度等。
在分析这些问题时,首先应对数控机床本身进行评估,包括其结构、精度、控制系统等。
同时,需要对原材料的质量进行检查,原材料的不合格可能会导致工件质量问题的出现。
此外,还应综合考虑工艺参数、刀具选择、切削液选用等因素对工件质量的影响。
通过综合分析这些因素,可以确定导致工件质量问题的原因,并进行相应的解决方案提出。
针对尺寸偏差这一常见的工件质量问题,可以从以下几个方面进行解决。
首先,提高数控机床的精度,包括提高加工台的刚性、改进润滑液系统等。
其次,优化刀具的选择和切削参数的设定,例如调整切削速度、切削深度等,以降低尺寸偏差。
此外,合理设计加工工艺,避免工件在加工过程中受到过大的热变形或力变形。
最后,在实际加工过程中,进行及时反馈和调整,通过测量工件实际尺寸与理论尺寸的差异,控制数控机床的准确性,确保工件的尺寸偏差控制在合理的范围内。
在解决工件质量问题中,表面粗糙度也是一个需要关注的因素。
为了降低表面粗糙度,可以采取以下措施。
首先,选择合适的刀具和切削参数,以减小刀具与工件之间的相互作用力,降低表面粗糙度。
其次,使用适当的切削液,以提供充分的润滑和冷却效果,减少热变形和切削力的影响。
同时,合理设计加工路径,避免切削过程中出现过大的重叠区域,减少表面粗糙度的产生。
最后,数控机床的定位精度也直接影响表面粗糙度,因此需要确保数控机床的精度和稳定性,降低因机床本身原因导致的表面粗糙度问题。
数控机床加工精度检测方法与控制

数控机床加工精度检测方法与控制数控机床作为现代制造业中重要的加工设备之一,其加工精度已经成为影响产品质量的重要因素之一。
为确保数控机床的加工精度,必须进行严格的检测和控制。
本文将介绍数控机床加工精度检测的方法和控制的重要性。
首先,数控机床加工精度的检测方法主要包括以下几种。
1.标准零件法:通过加工一组具有一定精度要求的标准零件,并测量其尺寸、形状和位置公差,来评估数控机床的加工精度。
2.零件配对法:将加工出的零件和标准零件进行配对,并通过测量其配对误差,来评估数控机床的加工精度。
3.物理检测法:采用测量仪器检测数控机床加工出的零件的尺寸、形状和位置公差,常用的物理检测方法包括三坐标测量和轮廓测量等。
4.工艺性能检测法:将数控机床加工出的零件进行装配,并结合装配工艺进行性能测试,通过测试结果的良品率和合格品率来评估数控机床的加工精度。
上述方法中,标准零件法和零件配对法是常用的定量评价数控机床加工精度的方法,可直观地反映出实际加工效果与设计要求之间的差距。
而物理检测法和工艺性能检测法则可以更加全面地评估加工精度和产品质量。
其次,控制数控机床加工精度的重要性不言而喻。
精度控制与加工质量密切相关,直接影响产品的性能、寿命和可靠性。
此外,高精度的加工也可以极大地提高产品的市场竞争力和附加值。
因此,为了确保数控机床的加工精度,必须采取有效的控制措施。
1.优化加工工艺:通过优化加工工艺的参数和流程,减小工序误差和插补误差,提高数控机床的加工精度。
2.精密的加工刀具选择:选择合适的刀具材料和几何形状,提高切削性能和加工质量。
3.数控系统的精度校正:定期对数控系统进行校正,修正机床轴向误差、传动间隙和系统误差,保证数控机床的加工精度。
4.质量控制体系的实施:建立完善的质量控制体系,包括质量管理、过程控制、检测监控等,确保数控机床加工精度的稳定性和一致性。
综上所述,数控机床加工精度的检测方法和控制措施对于保证产品质量和提高市场竞争力具有重要意义。
数控机床加工精度分析与调整方法
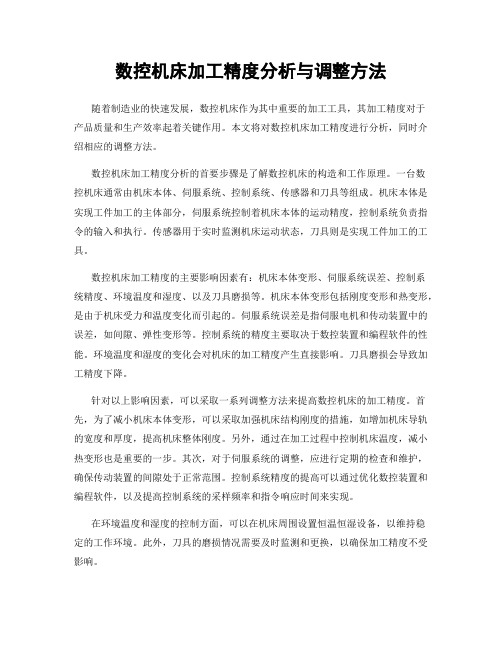
数控机床加工精度分析与调整方法随着制造业的快速发展,数控机床作为其中重要的加工工具,其加工精度对于产品质量和生产效率起着关键作用。
本文将对数控机床加工精度进行分析,同时介绍相应的调整方法。
数控机床加工精度分析的首要步骤是了解数控机床的构造和工作原理。
一台数控机床通常由机床本体、伺服系统、控制系统、传感器和刀具等组成。
机床本体是实现工件加工的主体部分,伺服系统控制着机床本体的运动精度,控制系统负责指令的输入和执行。
传感器用于实时监测机床运动状态,刀具则是实现工件加工的工具。
数控机床加工精度的主要影响因素有:机床本体变形、伺服系统误差、控制系统精度、环境温度和湿度、以及刀具磨损等。
机床本体变形包括刚度变形和热变形,是由于机床受力和温度变化而引起的。
伺服系统误差是指伺服电机和传动装置中的误差,如间隙、弹性变形等。
控制系统的精度主要取决于数控装置和编程软件的性能。
环境温度和湿度的变化会对机床的加工精度产生直接影响。
刀具磨损会导致加工精度下降。
针对以上影响因素,可以采取一系列调整方法来提高数控机床的加工精度。
首先,为了减小机床本体变形,可以采取加强机床结构刚度的措施,如增加机床导轨的宽度和厚度,提高机床整体刚度。
另外,通过在加工过程中控制机床温度,减小热变形也是重要的一步。
其次,对于伺服系统的调整,应进行定期的检查和维护,确保传动装置的间隙处于正常范围。
控制系统精度的提高可以通过优化数控装置和编程软件,以及提高控制系统的采样频率和指令响应时间来实现。
在环境温度和湿度的控制方面,可以在机床周围设置恒温恒湿设备,以维持稳定的工作环境。
此外,刀具的磨损情况需要及时监测和更换,以确保加工精度不受影响。
除了上述调整方法外,还可以采取一些辅助措施来提高数控机床的加工精度。
例如,使用稳定的切削参数和合适的刀具路径,避免过大的进给速率和切削深度。
同时,定期对机床和刀具进行维护保养,保持其正常运行和良好状态。
另外,及时进行加工质量的检测和评估,对加工结果进行分析,并根据实际情况进行调整和改进。
浅析数控车床的加工精度

浅析数控车床的加工精度摘要:数控车床作为一种重要的加工设备,其加工精度直接影响到工件的质量和精度要求。
本文通过对数控车床的加工精度进行浅析,探讨了影响加工精度的因素,并提出了提高加工精度的方法与措施。
旨在为数控车床的加工精度提升提供一定的理论支持和实践指导。
关键词:数控车床;加工精度随着制造业的发展,数控车床作为一种高效、精确的加工设备,被广泛应用于各个领域。
而加工精度作为衡量数控车床性能的重要指标,对于满足工件的精度要求具有关键意义。
一、数控车床的加工精度概述数控车床加工精度是指在数控车床上进行加工过程中,工件达到的尺寸、形状和位置的精确程度。
它是衡量数控车床加工质量的重要指标之一。
随着工业技术的不断发展,数控车床在各个领域得到了广泛应用,而加工精度的提高也成为了人们关注的焦点。
首先,尺寸精度是数控车床加工中的一个重要方面。
在工件加工过程中,尺寸精度的高低直接影响着工件能否符合设计要求。
要提高尺寸精度,可以通过控制切削量、刀具和刀具夹持方式、工件夹紧方式等来实现。
只有确保这些因素的合理选择和控制,才能保证工件加工后的尺寸与设计要求之间的偏差尽可能小。
其次,形状精度也是数控车床加工中不可忽视的一点。
在实际应用中,工件的形状往往要求具备一定的几何精度,例如平面度、圆度、圆柱度等。
为了提高形状精度,可以采取优化工艺参数、选择合适的刀具和夹具、控制加工温度等措施。
通过这些方式,能够有效减小工件加工后形状与设计要求之间的偏差,确保工件的几何形状达到精确的要求。
此外,位置精度也是影响数控车床加工精度的重要因素之一。
位置精度主要指工件上各个特定点之间的相对位置精度,例如平行度、垂直度、同轴度等。
要提高位置精度,可以通过优化工艺参数、提高机床刚性、加强夹紧与定位等来实现。
只有确保工件在加工过程中的稳定性和精度,才能保证位置精度的提升。
最后,表面粗糙度也是数控车床加工精度的重要方面之一。
工件表面的光洁程度对于某些特定工件的功能和装配要求有着重要影响。
- 1、下载文档前请自行甄别文档内容的完整性,平台不提供额外的编辑、内容补充、找答案等附加服务。
- 2、"仅部分预览"的文档,不可在线预览部分如存在完整性等问题,可反馈申请退款(可完整预览的文档不适用该条件!)。
- 3、如文档侵犯您的权益,请联系客服反馈,我们会尽快为您处理(人工客服工作时间:9:00-18:30)。
数控机床加工精度分析与应用王美姣(河南职业技术学院机电系,河南郑州450046摘要:数控机床是一种高精度、高效率、高柔性、高技术的现代化机电设备,其应用越来越普及。
提高机床效率、保证加工精度、确保产品品质是生产所必需。
关键词:数控机床;加工精度;应用中图分类号:TG659文献标识码:B文章编号:167125276(20040320025204Application and analysis of manufacturing precision of NC machinesWAN G Mei2jiao(Henan Vocational&Technical College,Zhengzhou Henan450046,ChinaAbstract:A NC machine tool is a modern mechatronic equipment which has advantage of high precision,high efficiency,high flexibility and advanced technologies.NC machines are being used in more and more fields.It is needed in production to improve efficiency,ensure precision and quality of products.K ey w ords:NC machine tool;manufacturing precision;application数控机床是按照加工程序自动加工零件,它具有加工精度高、生产效率高、产品品质稳定、加工过程柔性好、加工功能强等特点。
加工过程中,只要改变加工程序就能达到加工不同形状、不同精度零件的目的。
但并不是每个数控操作人员都能在规定的时间内保证工件的加工精度,提高机床效率,确保产品合格。
本文总结长期以来的实践经验,结合理论分析,从以下几方面提出几点粗浅看法。
1工件坐标系设定对加工精度的影响工件坐标系是编程人员在编写程序时,在工件上建立的坐标系,其原点即为工件原点(也称工件零点或编程原点。
理论上是由编程人员任意设定的,但实际上,它是编程人员根据零件特点为了编程方便以及尺寸的直观性而设定的。
选择工件坐标系时一般应遵循如下原则:a尽可能将工件原点选择在工艺定位基准上,这样有利于加工精度的提高;b尽量将工件原点选择在零件的尺寸基准上,这样便于坐标值的计算,减少错误率(当尺寸基准与工艺基准不重合时,则要考虑由基准不重合产生的误差;c尽量选在精度较高的工件表面上,以提高被加工零件的加工精度;d对于对称零件,应设在对称中心上,一般零件应设在工件轮廓某一角上,且Z轴方向上原点一般设在工件表面;e对于卧式加工中心最好把工件原点设在回转中心上,即设置在工作台回转中心与Z轴连线的适当位置上;f应将刀具起点和编程原点设在同一处,这样可以简化程序,便于计算,提高加工精度;对一般零件,仅按上述原则确定工件坐标系,即能保证其加工精度。
但对于复杂、特殊零件,就要综合考虑各种因素对加工精度的影响。
111在立式加工中心上加工畸形工件根据畸形工件的结构特点,往往在一个零件上要选择两个或两个以上的坐标系,这时就要根据零件的形状特征、夹紧方式及各加工部位的精度高低等因素综合考虑:a建立几个坐标系;b先加工哪个坐标系的哪个表面才能提高整个零件的加工精度;c坐标系间定位尺寸的精度对各部位加工精度的影响(某些定位基准可能不在工件上。
112在卧式加工中心上加工箱体类零件根据箱体类零件的结构特点,不仅除上下底面之外的四个侧面需要分别建立四个定位坐标系,而且每一侧面上有时还需建立几个坐标系,这时就必须考虑各加工精度如何保证。
如:a机床回转中心坐标精度对零件相对两侧面坐标系的建立来说,它直接影响两相对侧面通孔的同轴度;b每一侧面上几个坐标系建立时,加工工序的设计对加工精度的影响;c以底面为基准的的装夹精度,直接影响孔轴线相对端面的垂直度;d基准底面精度对孔的中心高精度的影响。
当然,零件结构不同,精度要求不同,坐标系的建立也不一样,不管何种情况都应详细分析优先选用哪一原则或同时兼顾哪几项原则,才能有利于保证零件加工精度、提高工作效率,降低加工成本。
2指令选择对加工精度的影响以下分析皆以加工中心为例aG92指令与G54~G59的选择。
G92指令设定工件坐标系是在程序中,用程序段直接给出,指令中的坐标值,并不使机床产生运动,仅代表当前刀具的刀位点在工件坐标系中的坐标值。
因此,操作者在使用写有坐标系设定指令的程序时,必须在工件安装后检查或调整刀具的刀位点与工件坐标系之间的关系,保证机床处于加工起始点(对刀点,以确保在机床上设定的工件坐标系,与编程时在零件上规定的工件坐标系在位置上重合一致,否则将降低零件加工精度。
并且G92X Y Z各坐标轴不可省略,否则未被设定的坐标轴将按以前的记忆执行,这样刀具在运动时,可能到达不了预期的位置,甚至造成事故。
G54~G59指令设置工件坐标系时,首先必须通过偏置页面,预先将G54~G59设置在寄存器中,编程中再用程序选择,操作者安装工件后,通过测量来确定工件原点与机床原点偏移量。
目前的CNC系统一般都配有测量头,手动操作能准确测量该偏移量,其测量误差对工件的加工精度影响很小,可以忽略不计,用MDI方式存入到G54~G59的原点寄存器中,其后系统在执行程序中,就可以按照工件坐标系中的坐标值来运动了。
并且同一工件上能同时设定六个坐标系,特别是加工复杂零件更显示其优越性,事实证明,实际加工中不管何种零件,选用G54~G59指令省时准确又方便,且出错率极低。
bG40、G41、G42的选择。
G40、G41、G42为刀具半径补偿指令,G40是刀具半径补偿功能撤消指令、G41、G42分别是左偏、右偏指令。
如果机床没有刀具半径补偿功能,那么当刀具因更换、磨损或重磨而改变半径,或因粗加工时的余量不同等原因,而改变了刀具中心偏移量时,都要按刀具中心轨迹重新编制加工程序,这将是极其繁琐,并且影响生产的正常进行。
为解决此问题,数控系统一般都具有半径自动补偿功能。
在编程时不需要计算刀具中心运动轨迹,而可按工件的轮廓直接编程,刀具半径改变时在控制面板上用手工输入方式改变刀具半径补偿值即可,而不必修改程序,极大的方便了编程和加工。
据此该指令的应用将会大大提高加工效率,但在工厂的应用并非如此,如若选择使用不当,不仅会降低工件的加工精度,严重还会使工件报废,并且在某些情况下根据零件的具体结构并不总是按照零件轮廓进行编程。
举例如下:如图1为毛胚工件,D30孔已加工,现需加工长方孔。
建立坐标系如图,刀具为D16立铣刀;方法一:选用G40、G42指令程序如下:N10G90G00G54X0Y0;N20Z10.S300M03;N30G01Z-5.F1000;N40G42X-23.D31F100;N50Y17.5;N60X23.;N70Y-17.5;N80X-23.;N90Y17,5;N100G0Z50.;N110G40G91G28Z0Y0M05; N120M30;图1零件工序图方法二:选用G40、G41指令只对部分程序加以修改,其余相同N40G41X-23.D31F100;N50Y-17.5;N60X23.;N70Y17.5;N80X -23.N90Y0;方法一运行结果:1最后铣刀停留在B 点,虽说是按零件轮廓编程,但很明显多铣一个刀具半径,工件报废。
2加工表面粗糙度不理想。
3两尺寸精度通过半径补偿完全保证。
方法二运行结果:尺寸精度及表面粗糙度都完全保证。
分析:两种方法的差异就在于分别采用了G42(刀径右补、G41(刀径左补,从而决定了顺铣、逆铣的选择。
逆铣时(如图2(a ,切削厚度从零开始逐渐增大,当实际前角出现负值时,刀齿在加工表面上挤压、滑行,不能切除切屑,既增大了后刀面的磨损,又使工件表面产生较严重的冷硬层。
当下一个刀齿切入时,又在冷硬层表面上挤压、滑行,更加剧了铣刀的磨损,使工件加工后的表面粗糙度值也较大。
从力学角度分析,铣刀作用于工件上的纵向分力(图2(a 中F e ,总是与工作台的进给方向相反,即使机床进给机构有间隙,也始终能保持良好的接触,从而使进给运动平稳;但垂直分力(图2(a 中F v 的大小和方向是变化的,并且当刀齿切离工件时,F v 向上,有挑起工件的趋势,引起工作台的振动,从而影响工件表面的粗糙度。
所以当工件表面有硬皮,机床的进给机构有间隙时应选用逆铣。
图2顺铣与逆铣的受力分析顺铣时(如图2(b ,刀齿的切削厚度从最大开始,避免了挤压、滑行现象;并且垂直分力F u 始终压向工作台,从而使切削平稳,提高铣刀耐用度和加工表面质量;但纵向分力F e 与进给运动方向相同,如果进给机构有间隙,会造成工作台窜动,使铣削进给量不均匀,严重时会打刀,但一般数控机床,特别是加工中心,进给机构间隙很小,造成的影响可以忽略不计。
因此,当工件表面无硬皮时,应选用顺铣,特别是精铣,当工件材料为铝镁合金、钛合金或耐热合金时更应尽量采用顺铣。
由上述分析可知,选择刀径补G41和G42时应注意:1结合零件材料、机床特点及加工精度,适当选择G41和G42。
2使用G41和G42指令时,应仔细分析刀具运动轨迹,以免多切(长方形孔或少切(通槽。
3需要改变刀径补偿数值大小时,切忌改错方向,造成废品。
3气温及工艺系统热变形对加工精度的影响311气温分析物体,特别是金属材料具有热胀冷缩性质,温度的变化会引起零件尺寸的改变。
虽然零件的尺寸变化微小,但对于数控机床(很多数控车间并不能保证标准室温条件加工的高精度零件却不容忽视,否则会出现在某一温度条件下加工的零件合格,而在另一温度条件下测量就不合格。
如一精度要求较高的尺寸,在夏季加工与冬季加工就不一样,夏季因温度较高,机床工艺系统、刀具、工件变形较大,为保证零件在其他温度条件下也合格,加工好测量时就应使实际偏差靠近上偏差,这样即使在冬季测量时,就不会因温度较低尺寸变小而超差。
同理,冬季加工零件时,就应使实际偏差靠近下偏差,春秋季节应使实际偏差靠近上下偏差的中间位置,孔或轴类零件高精度尺寸皆应如此。
312工艺系统热变形分析在机械加工过程中,由于切削热、摩擦热等影响,使工艺系统各部分的温度升高不等,产生复杂的变形,从而改变了工件、刀具及机床之间的相互位置,破坏了工件和刀具之间相对运动的准确性,改变了已调整好的加工尺寸,严重影响了零件的加工精度。
据此,数控机床在设计制造时已考虑了这些因素的影响,使数控设备的传动系统和机床结构都具有很高的刚度和热稳定性,并对反向间隙与丝杠螺距误差等由计算机软件实现自动补偿,大大提高了加工精度。