1 干法刻蚀和湿法刻蚀
刻蚀工艺和薄膜工艺(一)

刻蚀工艺和薄膜工艺(一)
刻蚀工艺和薄膜工艺
简介
•刻蚀工艺是一种常用的微纳加工技术,用于在半导体材料上制造微细结构。
•薄膜工艺是根据特定的要求在材料表面制备一层薄膜的技术。
刻蚀工艺
定义
•刻蚀工艺是通过化学反应或物理作用,将特定区域的材料制成所需形状或深度的工艺。
常见方法
1.干法刻蚀:使用高能离子束或高温等干燥条件进行刻蚀。
2.湿法刻蚀:利用酸碱溶液进行刻蚀,有较高的选择性和均匀性。
薄膜工艺
定义
•薄膜工艺是在材料表面制备一层具有特定功能的薄膜的工艺。
常见方法
1.物理气相沉积(PVD):利用物理方式将原子或分子沉积在基底
上。
2.化学气相沉积(CVD):利用化学反应在基底上生成薄膜。
刻蚀工艺和薄膜工艺的联系和区别
•刻蚀工艺和薄膜工艺都是微电子制造中常用的工艺。
•刻蚀工艺主要用于制造微细结构,而薄膜工艺主要用于制备功能性薄膜。
•刻蚀工艺和薄膜工艺可以结合使用,以实现更精确的微纳加工。
结论
•刻蚀工艺和薄膜工艺都是微电子制造中极为重要的工艺。
•了解刻蚀工艺和薄膜工艺的原理和方法,可以帮助提高微细结构制备和薄膜制备的技术水平。
脚标:该文章以一个资深创作者的视角,简要介绍了刻蚀工艺和薄膜工艺的定义、常见方法以及二者的联系和区别。
通过用标题和副标题的方式进行排版,提供了清晰易读的文章结构。
文章内容符合markdown格式的要求,没有出现html字符、网址、图片、电话号码等内容。
综述报告——刻蚀简介

微加工技术——刻蚀简介自从半导体诞生以来,很大程度上改变了人类的生产和生活。
半导体除了在计算机领域应用之外,还广泛地应用于通信、网络、自动遥控及国防科技领域。
本文主要介绍半导体制造工艺中的刻蚀工艺。
随着半导体制造大规模集成电路技术的发展,图形加工线条越来越细,硅片尺寸越来越大,对刻蚀工艺的要求也越来高。
因此,学习了解刻蚀工艺十分必要。
本文将主要从刻蚀简介、刻蚀参数及现象、干法刻蚀和湿法刻蚀四个方面进行论述。
1、刻蚀简介1.1 刻蚀定义及目的刻蚀就是用化学的、物理的或同时使用化学和物理的方法,有选择地把没有被抗蚀剂掩蔽的那一部分薄膜层除去,从而在薄膜上得到和抗蚀剂膜上完全一致的图形。
刻蚀的基本目的,是在涂光刻胶(或有掩膜)的硅片上正确的复制出掩膜图形[1]。
刻蚀,通常是在光刻工艺之后进行。
通过刻蚀,在光刻工艺之后,将想要的图形留在硅片上。
从这一角度而言,刻蚀可以被称之为最终的和最主要的图形转移工艺步骤。
在通常的刻蚀过程中,有图形的光刻胶层〔或掩膜层)将不受到腐蚀源显著的侵蚀或刻蚀,可作为掩蔽膜,保护硅片上的部分特殊区域,而未被光刻胶保护的区域,则被选择性的刻蚀掉。
其工艺流程示意图如下。
1.2 刻蚀的分类从工艺上分类的话,在半导体制造中有两种基本的刻蚀工艺:干法刻蚀和湿法腐蚀。
干法刻蚀,是利用气态中产生的等离子体,通过经光刻而开出的掩蔽层窗口,与暴露于等离子体中的硅片行物理和化学反应,刻蚀掉硅片上暴露的表面材料的一种工艺技术法[1]。
该工艺技术的突出优点在于,是各向异性刻蚀(侧向腐蚀速度远远小于纵向腐蚀速度,侧向几乎不被腐蚀),因此可以获得极其精确的特征图形。
超大规模集成电路的发展,要求微细化加工工艺能够严格的控制加工尺寸,要求在硅片上完成极其精确的图形转移。
任何偏离工艺要求的图形或尺寸,都可能直接影响产品性能或品质,给生产带来无法弥补的损害。
由于干法刻蚀技术在图形转移上的突出表现,己成为亚微米尺寸下器件刻蚀的最主要工艺方法。
干法刻蚀和湿法刻蚀

1 干法刻蚀和湿法刻蚀干法刻蚀是把硅片外表暴露于空气中产生的等离子体,等离子体通过光刻胶中开出的窗口,与硅片发生物理或化学反响,从而去掉暴露的外表材料。
湿法腐蚀是以液体化学试剂以化学方式去除硅片外表的材料。
2刻蚀速率是指在刻蚀过程中去除硅片外表材料的速度,通常用。
A/min表示刻蚀速率=T/t(。
A/min)其中T=去掉的材料厚度t=刻蚀所用的时间为了高的产量,希望有高的刻蚀速率。
3刻蚀选择比指的是同一刻蚀条件下一种材料与另一种刻蚀材料相比刻蚀速率快多少。
他定义为被刻蚀材料的刻蚀速率与另一种材料的刻蚀速率的比。
干法刻蚀的选择比低,通常不能提供对下一层材料足够高的刻蚀选择比。
高选择比意味着只刻除想要刻去的那层。
4干法刻蚀的主要目的完整的把掩膜图形复制到硅片外表上。
优点:刻蚀剖面是各向异性,具有非常好的侧壁剖面控制,好的CD控制最小的光刻胶脱落或粘附问题好的片内,片间,批次间的刻蚀均匀性较低的化学制品使用和处理费用缺乏:对下层材料的差的刻蚀选择比,等离子体带来的器件损伤和昂贵的设备。
5化学机理:等离子体产生的反响元素与硅片外表的物质发生反响,为了获得高的选择比,进入腔体的气体都经过了慎重选择。
等离子体化学刻蚀由于它是各向同性的,因而线宽控制差。
物理机理:等离子体产生的带能粒子在强电场下朝硅片外表加速,这些离子通过溅射刻蚀作用去除未被保护的硅片外表材料。
6根本部件:发生刻蚀反响的反响腔,一个产生等离子体的射频电源,气体流量控制系统,去除刻蚀生成物和气体的真空系统。
氟刻蚀二氧化硅,氯和氟刻蚀铝,氯,氟和溴刻蚀硅,氧去除光刻胶。
7z微波鼓励源来产生高密度等离子体。
ECR反响器的一个关键点是磁场平行于反映剂的流动方向,这使得自由电子由于磁力的作用做螺旋形运动。
当电子的盘旋频率等于所加的微波电场频率时,能有效把电能转移到等离子体中的电子上。
这种振荡增加了电子碰撞的可能性,从而产生高密度的等离子体,获得大的离子流。
1-干法刻蚀和湿法刻蚀

1 干法刻蚀和湿法刻蚀干法刻蚀是把硅片表面暴露于空气中产生的等离子体,等离子体通过光刻胶中开出的窗口,与硅片发生物理或化学反应,从而去掉暴露的表面材料。
湿法腐蚀是以液体化学试剂以化学方式去除硅片表面的材料。
2刻蚀速率是指在刻蚀过程中去除硅片表面材料的速度,通常用。
A/min表示刻蚀速率=T/t(。
A/min)其中T=去掉的材料厚度t=刻蚀所用的时间为了高的产量,希望有高的刻蚀速率。
3刻蚀选择比指的是同一刻蚀条件下一种材料与另一种刻蚀材料相比刻蚀速率快多少。
他定义为被刻蚀材料的刻蚀速率与另一种材料的刻蚀速率的比。
干法刻蚀的选择比低,通常不能提供对下一层材料足够高的刻蚀选择比。
高选择比意味着只刻除想要刻去的那层。
4干法刻蚀的主要目的完整的把掩膜图形复制到硅片表面上。
优点:刻蚀剖面是各向异性,具有非常好的侧壁剖面控制,好的CD控制最小的光刻胶脱落或粘附问题好的片内,片间,批次间的刻蚀均匀性较低的化学制品使用和处理费用不足:对下层材料的差的刻蚀选择比,等离子体带来的器件损伤和昂贵的设备。
5化学机理:等离子体产生的反应元素与硅片表面的物质发生反应,为了获得高的选择比,进入腔体的气体都经过了慎重选择。
等离子体化学刻蚀由于它是各向同性的,因而线宽控制差。
物理机理:等离子体产生的带能粒子在强电场下朝硅片表面加速,这些离子通过溅射刻蚀作用去除未被保护的硅片表面材料。
6基本部件:发生刻蚀反应的反应腔,一个产生等离子体的射频电源,气体流量控制系统,去除刻蚀生成物和气体的真空系统。
氟刻蚀二氧化硅,氯和氟刻蚀铝,氯,氟和溴刻蚀硅,氧去除光刻胶。
7z微波激励源来产生高密度等离子体。
ECR反应器的一个关键点是磁场平行于反映剂的流动方向,这使得自由电子由于磁力的作用做螺旋形运动。
当电子的回旋频率等于所加的微波电场频率时,能有效把电能转移到等离子体中的电子上。
这种振荡增加了电子碰撞的可能性,从而产生高密度的等离子体,获得大的离子流。
纳米刻蚀工艺中的干法刻蚀与湿法刻蚀比较

纳米刻蚀工艺是纳米制造中的一项关键技术,它通过物理或化学方法去除材料,以达到制造纳米级别结构的目的。
在纳米刻蚀工艺中,干法刻蚀和湿法刻蚀是两种主要的刻蚀方法,它们各自具有不同的特点,也适用于不同的应用场景。
首先,让我们来看看干法刻蚀。
在干法刻蚀中,我们通常使用物理手段如离子刻蚀、反应离子刻蚀(RIE)、机械研磨等。
这些方法的主要优点是刻蚀速度快,对材料的兼容性好,能够处理各种不同类型的材料。
然而,这种方法也存在一些缺点。
首先,它对设备的要求较高,需要专门的设备和技术支持。
其次,由于其刻蚀过程中可能产生微小碎片,因此在处理敏感材料时需要特别小心。
此外,干法刻蚀对于深宽比的保持相对较差,即对同一尺寸的图形,干法刻蚀可能需要更大的实际面积。
接下来是湿法刻蚀,这种方法主要利用化学反应来去除材料。
常见的湿法刻蚀技术包括化学腐蚀、等离子体腐蚀等。
与干法刻蚀相比,湿法刻蚀对许多材料具有更强的兼容性,特别是在高分子材料和绝缘材料上。
此外,湿法刻蚀在处理大面积样品时更具优势,因为它不需要精确的定位和设备支持。
然而,湿法刻蚀也存在一些问题,如腐蚀液的选择和配比需要严格控制,以及对一些材料可能产生过敏反应的风险。
而且,湿法刻蚀的刻蚀深度较浅,对于深结构可能无法达到预期的刻蚀效果。
总的来说,干法刻蚀和湿法刻蚀各有优缺点,适用于不同的应用场景。
在选择使用哪种方法时,我们需要考虑待处理材料的性质、刻蚀速度的需求、设备的可用性以及成本等因素。
而且,随着技术的进步,我们期待在未来看到更多创新的纳米刻蚀方法出现,以满足更复杂、更高精度的纳米制造需求。
第二章干法刻蚀的介绍
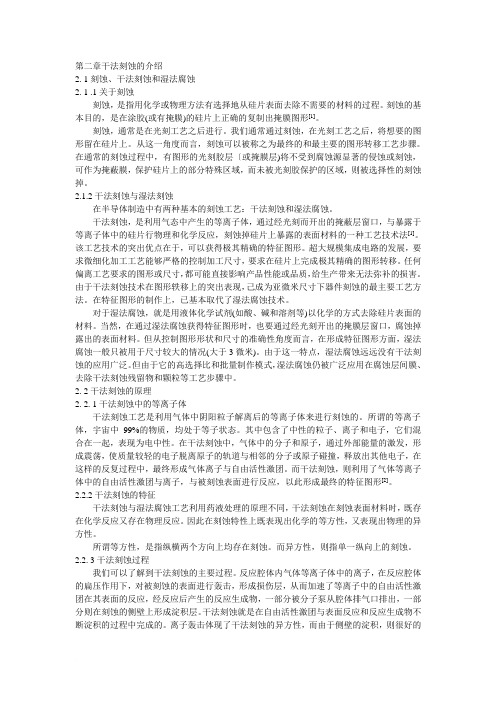
第二章干法刻蚀的介绍2. 1刻蚀、干法刻蚀和湿法腐蚀2. 1 .1关于刻蚀刻蚀,是指用化学或物理方法有选择地从硅片表面去除不需要的材料的过程。
刻蚀的基本目的,是在涂胶(或有掩膜)的硅片上正确的复制出掩膜图形[1]。
刻蚀,通常是在光刻工艺之后进行。
我们通常通过刻蚀,在光刻工艺之后,将想要的图形留在硅片上。
从这一角度而言,刻蚀可以被称之为最终的和最主要的图形转移工艺步骤。
在通常的刻蚀过程中,有图形的光刻胶层〔或掩膜层)将不受到腐蚀源显著的侵蚀或刻蚀,可作为掩蔽膜,保护硅片上的部分特殊区域,而未被光刻胶保护的区域,则被选择性的刻蚀掉。
2.1.2干法刻蚀与湿法刻蚀在半导体制造中有两种基本的刻蚀工艺:干法刻蚀和湿法腐蚀。
干法刻蚀,是利用气态中产生的等离子体,通过经光刻而开出的掩蔽层窗口,与暴露于等离子体中的硅片行物理和化学反应,刻蚀掉硅片上暴露的表面材料的一种工艺技术法[1]。
该工艺技术的突出优点在于,可以获得极其精确的特征图形。
超大规模集成电路的发展,要求微细化加工工艺能够严格的控制加工尺寸,要求在硅片上完成极其精确的图形转移。
任何偏离工艺要求的图形或尺寸,都可能直接影响产品性能或品质,给生产带来无法弥补的损害。
由于干法刻蚀技术在图形轶移上的突出表现,己成为亚微米尺寸下器件刻蚀的最主要工艺方法。
在特征图形的制作上,已基本取代了湿法腐蚀技术。
对于湿法腐蚀,就是用液体化学试剂(如酸、碱和溶剂等)以化学的方式去除硅片表面的材料。
当然,在通过湿法腐蚀获得特征图形时,也要通过经光刻开出的掩膜层窗口,腐蚀掉露出的表面材料。
但从控制图形形状和尺寸的准确性角度而言,在形成特征图形方面,湿法腐蚀一般只被用于尺寸较大的情况(大于3微米)。
由于这一特点,湿法腐蚀远远没有干法刻蚀的应用广泛。
但由于它的高选择比和批量制作模式,湿法腐蚀仍被广泛应用在腐蚀层间膜、去除干法刻蚀残留物和颗粒等工艺步骤中。
2. 2干法刻蚀的原理2. 2. 1干法刻蚀中的等离子体干法刻蚀工艺是利用气体中阴阳粒子解离后的等离子体来进行刻蚀的。
硅片刻蚀工艺

硅片刻蚀工艺
硅片刻蚀工艺是一种重要的半导体加工工艺,主要用于制造晶体管、集成电路等器件。
刻蚀是在硅片表面上进行化学或物理反应,将不需要的部分去除,从而形成所需的结构和元器件。
硅片刻蚀工艺主要包括湿法刻蚀和干法刻蚀两种。
湿法刻蚀是将硅片浸泡在化学溶液中,利用化学反应去除所需部分。
干法刻蚀则是在真空环境下,利用气体化学反应去除硅片表面的部分。
硅片刻蚀工艺的精度和效率对于器件的性能和质量有着重要影响,因此在半导体工业中具有广泛应用。
- 1 -。
两种基本的刻蚀工艺:干法刻蚀和湿法腐蚀

两种基本的刻蚀工艺:干法刻蚀和湿法腐蚀
在半导体制造中有两种基本的刻蚀工艺:干法刻蚀和湿法腐蚀。
干法刻蚀是把硅片表面曝露于气态中产生的等离子体,等离子体通过光刻胶中开出的窗口,与硅片发生物理或化学反应(或这两种反应),从而去掉曝露的表面材料。
干法刻蚀是亚微米尺寸下刻蚀器件的最重要方法。
而在湿法腐蚀中,液体化学试剂(如酸、碱和溶剂等)以化学方式去除硅片表面的材料。
湿法腐蚀一般只是用在尺寸较大的情况下(大于3微米)。
湿法腐蚀仍然用来腐蚀硅片上某些层或用来去除干法刻蚀后的残留物。
干法刻蚀也可以根据被刻蚀的材料类型来分类。
按材料来分,刻蚀主要分成三种:金属刻蚀、介质刻蚀、和硅刻蚀。
介质刻蚀是用于介质材料的刻蚀,如二氧化硅。
接触孔和通孔结构的制作需要刻蚀介质,从而在ILD中刻蚀出窗口,而具有高深宽比(窗口的深与宽的比值)的窗口刻蚀具有一定的挑战性。
硅刻蚀(包括多晶硅)应用于需要去除硅的场合,如刻蚀多晶硅晶体管栅和硅槽电容。
金属刻蚀主要是在金属层上去掉铝合金复合层,制作出互连线。
刻蚀也可以分成有图形刻蚀和无图形刻蚀。
有图形刻蚀采用掩蔽层(有图形的光刻胶)来定义要刻蚀掉的表面材料区域,只有硅片上被选择的这一部分在刻蚀过程中刻掉。
有图形刻蚀可用来在硅片上制作多种不同的特征图形,。
刻蚀相关知识点总结

刻蚀相关知识点总结刻蚀技术主要分为湿法刻蚀和干法刻蚀两种。
湿法刻蚀是在溶液中通过化学反应去除材料表面的工艺,而干法刻蚀是在气相中通过物理或化学反应去除材料表面的工艺。
下面将详细介绍刻蚀的相关知识点。
一、刻蚀的基本原理1. 湿法刻蚀原理湿法刻蚀是利用化学溶液对材料表面进行腐蚀或溶解的工艺。
湿法刻蚀的原理是在溶液中加入具有特定功能的化学试剂,使其与被刻蚀物质发生化学反应,从而去除材料表面的部分物质。
湿法刻蚀通常可以实现较高的刻蚀速率和较好的表面质量,但需要考虑溶液中的成分和温度对环境的影响。
2. 干法刻蚀原理干法刻蚀是利用气相中的等离子体或化学反应对材料表面进行腐蚀或清除的工艺。
干法刻蚀的原理是在高能离子束或化学气体的作用下,使被刻蚀物质表面发生物理或化学反应,从而去除材料表面的部分物质。
干法刻蚀通常可以实现更高的加工精度和更好的表面质量,但需要考虑设备的复杂性和成本的影响。
二、刻蚀的工艺参数1. 刻蚀速率刻蚀速率是刻蚀过程中单位时间内去除的材料厚度,通常以单位时间内去除的厚度为单位。
刻蚀速率的选择需要综合考虑刻蚀材料的性质、刻蚀条件、刻蚀设备和加工要求等因素。
2. 刻蚀选择性刻蚀选择性是指在多种材料叠加或混合结构中选择性地去除某一种材料的能力。
刻蚀选择性的选择需要考虑被刻蚀材料和其它材料之间的化学反应性和物理性质的差异,以实现精确的刻蚀。
3. 刻蚀均匀性刻蚀均匀性是指在整个刻蚀过程中去除材料的厚度分布情况。
刻蚀均匀性的选择需要考虑刻蚀设备和刻蚀条件对被刻蚀物质的影响,以实现均匀的刻蚀。
4. 刻蚀深度控制刻蚀深度控制是指在整个刻蚀过程中去除材料的深度分布情况。
刻蚀深度控制的选择需要综合考虑刻蚀设备和刻蚀条件对被刻蚀物质的影响,以实现精确的刻蚀深度。
5. 刻蚀环境控制刻蚀环境控制是指在整个刻蚀过程中对刻蚀环境(如溶液中的成分、气相中的气体、温度和压力等)的控制。
刻蚀环境控制的选择需要考虑被刻蚀材料的特性和加工的要求,以实现良好的刻蚀效果。
芯片刻蚀原理

芯片刻蚀原理
芯片刻蚀原理是指利用化学或物理方法,以去除或改变芯片表面部分材料的方式,实现对芯片结构的精确加工。
在芯片制造过程中,刻蚀是一个重要的工艺步骤,用于形成纳米级别的结构和通道。
芯片刻蚀可分为干法刻蚀和湿法刻蚀两种方法。
1. 干法刻蚀:
干法刻蚀是通过在真空或气氛中,引入特定的化学气体,在高频电场或射频场的作用下,产生等离子体。
等离子体中的高能粒子与芯片表面相互碰撞,将材料原子从表面去除。
干法刻蚀常用的气体有氟化物、氯化物等,它们可以与芯片表面的材料发生化学反应,形成易于去除的气体或溶解物。
干法刻蚀具有刻蚀速率快、刻蚀深度均匀、加工精度高等优点,适用于刻蚀深度较大的结构。
2. 湿法刻蚀:
湿法刻蚀是通过将芯片浸泡在特定的化学液体中,利用化学反应将芯片表面的材料蚀去。
湿法刻蚀可分为均匀蚀刻和选择性蚀刻两种方式。
- 均匀蚀刻:在均匀蚀刻过程中,芯片表面的材料被均匀蚀去,适用于要求芯片整体薄化或去除一致厚度的材料。
- 选择性蚀刻:在选择性蚀刻过程中,芯片中不同材料的蚀刻
速率不同,可以通过调整蚀刻液中的化学组成和温度等因素,实现不同材料的选择性蚀刻。
选择性蚀刻常用于形成井、孔等
空间结构,或是去除芯片中的残留材料。
总的来说,芯片刻蚀原理是通过控制化学或物理反应,实现对芯片表面材料的去除或改变,以实现芯片结构的加工和制造。
不同的刻蚀方法和参数选择,可以实现不同的刻蚀效果和加工要求。
刻蚀的工艺

刻蚀的工艺
刻蚀是一种常用的微纳加工工艺,通过将化学蚀刻剂作用于材料表面,使其在预定区域发生化学反应而被蚀刻掉,从而实现对材料的精确加工和形状控制。
刻蚀工艺广泛应用于半导体制造、光学元件制造、微纳米器件制造等领域。
刻蚀工艺通常分为湿法刻蚀和干法刻蚀两种。
1. 湿法刻蚀:湿法刻蚀是指将材料置入含有化学蚀刻剂的溶液中,通过溶液中的化学反应来蚀刻材料表面。
湿法刻蚀具有高蚀刻速率、高选择性和较低的成本等特点。
常见的湿法刻蚀包括酸性刻蚀、碱性刻蚀、氧化物刻蚀等。
2. 干法刻蚀:干法刻蚀是指将材料置入低压或大气压等特定环境中,通过气体或等离子体的物理作用或化学反应来蚀刻材料表面。
干法刻蚀通常具有更高的加工精度和更好的表面质量,但蚀刻速率较慢。
常见的干法刻蚀包括物理刻蚀(如离子束刻蚀、电子束刻蚀)和化学气相刻蚀等。
刻蚀工艺是一项复杂的加工技术,需要根据具体材料和加工要求选择合适的刻蚀工艺和工艺参数,以获得所需的形状和尺寸。
同时,刻蚀还要考虑蚀刻剂的选择、工艺控制、蚀刻均匀性等方面,以保证加工质量和一致性。
构想一些硅片加工的实验方法

构想一些硅片加工的实验方法
要进行硅片加工,可以考虑以下几个实验方法:
1. 激光刻蚀法:使用激光束照射硅片表面,控制激光功率、聚焦,通过物理或化学反应使硅片表面产生物理或化学变化,从而实现刻蚀加工。
2. 干法刻蚀法:使用气体等非液体介质,将其注入刻蚀室,依靠化学反应将硅片表面物质移除,实现刻蚀加工。
3. 湿法刻蚀法:使用酸性或碱性溶液,将硅片浸泡在溶液中,通过化学反应将硅片表面物质溶解或转化为其它物质,实现刻蚀加工。
4. 离子注入法:利用精密控制的离子束,将高能离子注入到硅片表面,改变硅片结构和性质,实现刻蚀加工。
5. 硅片薄膜沉积法:利用化学气相沉积或物理气相沉积等技术,将需要的材料薄膜覆盖在硅片表面,实现薄膜加工。
请注意,具体的实验方法可能需要根据具体的硅片加工需求和设备情况进行调整。
在进行实验之前,确保使用安全操作,遵循相关安全规范和法律要求。
刻蚀的原理

刻蚀的原理刻蚀是一种通过化学或物理的方式,在材料表面上制造微米或纳米级别的微细结构的加工技术。
它在半导体、光学、医学、微纳米加工等领域具有重要的应用价值。
刻蚀的原理主要包括化学刻蚀和物理刻蚀两种方式。
化学刻蚀利用化学试剂对材料表面发生化学反应,溶解或氧化表面材料来达到刻蚀的效果。
这种方法通常用于刻蚀金属、半导体、玻璃和陶瓷等材料。
其中最常用的化学刻蚀方法包括湿法刻蚀和干法刻蚀。
湿法刻蚀是指将材料放入酸性或碱性的溶液中,通过溶液中的化学试剂对材料表面进行化学反应而达到刻蚀的目的。
常用的湿法刻蚀试剂包括氢氟酸、氢氧化钠、硝酸、氢氧化铵等。
这些试剂能够与材料表面发生反应,溶解或氧化掉材料表面从而实现刻蚀的效果。
干法刻蚀是指在气相中利用化学气相刻蚀试剂对材料进行刻蚀。
常用的干法刻蚀气相试剂包括氯气、氟气、氩气、氧气等。
通过将这些气体与材料表面产生化学反应,溶解或氧化掉材料表面来实现刻蚀效果。
另一种刻蚀的方式是物理刻蚀,物理刻蚀是指利用能量粒子(如离子、电子、中性维、光子等)对材料进行直接轰击,通过在材料表面形成缺陷或者改变表面状态来实现刻蚀。
离子刻蚀是物理刻蚀中常见的一种方法,利用加速到高速度的离子束对材料表面进行轰击,使材料表面发生缺陷或者扭曲,从而实现刻蚀效果。
离子束的枪在处理头中生成目标离子(如氮、氖、氩、氖等)通过转向和侧推定位设备聚焦到微米或者更小的针对区域上,降低精确刻蚀目标物的实际需求。
电子束刻蚀是利用高能电子束对材料进行直接轰击,使材料表面的原子或分子发生移动或者排列变化,从而实现刻蚀效果。
这种方法对于光刻技术中的微米或纳米级别的加工非常有效。
光刻技术是一种利用光对材料表面进行刻蚀的方法,通过在光刻胶上投放光源,并根据需要的图案的轮廓聚集在光刻胶表面上,形成均匀的光图案,然后将这些图案传送到光敏化的硅片表面,然后进行暴露通过化学处理的方式,得到图案化的硅片表面。
刻蚀技术是当前微纳米加工中非常重要的一种工艺手段,它能够实现对材料表面微细结构的精确加工,具有很强的可控性和精确性。
芯片的刻蚀工艺

芯片的刻蚀工艺
芯片的刻蚀工艺是制造芯片过程中的一项关键步骤,用于将薄膜层从芯片表面或者芯片区域刻蚀掉,以形成所需的结构和元件。
刻蚀工艺主要分为湿法刻蚀和干法刻蚀两种。
1. 湿法刻蚀:
湿法刻蚀是通过在蚀刻液中浸泡芯片来溶解薄膜层。
具体步骤包括:
- 准备蚀刻液:根据所需刻蚀的材料种类,选择相应的化学品制备蚀刻液,如酸、碱等。
- 芯片表面处理:在刻蚀前,通常需要先进行表面处理,如去胶、清洗等,以保证刻蚀的质量和效果。
- 蚀刻过程:把芯片浸泡在蚀刻液中,使蚀刻液与薄膜层接触,蚀刻液中的化学物质与薄膜层发生反应,导致薄膜层溶解掉。
蚀刻时间和温度通常根据蚀刻液的配方和需要的蚀刻深度来确定。
2. 干法刻蚀:
干法刻蚀是通过将芯片暴露在含有反应气体的环境中,利用化学反应或物理作用使薄膜层刻蚀。
具体步骤包括:
- 准备反应气体:根据刻蚀材料的需求,选择相应的气体,如氟化氢气体等。
- 芯片表面处理:与湿法刻蚀类似,在刻蚀前需要对芯片表面进行处理,如去胶、清洗等。
- 刻蚀过程:将芯片放置在刻蚀系统中,控制好温度和压力等刻蚀参数,通过引入反应气体和离子束等方式使薄膜层刻蚀。
刻蚀速度和深度通常根据刻蚀参数来控制和调节。
以上是芯片刻蚀工艺的一般步骤和原理,具体的刻蚀工艺流程和参数设定会根据具体的芯片设计和生产工艺而有所差异。
常见半导体材料的刻蚀工艺
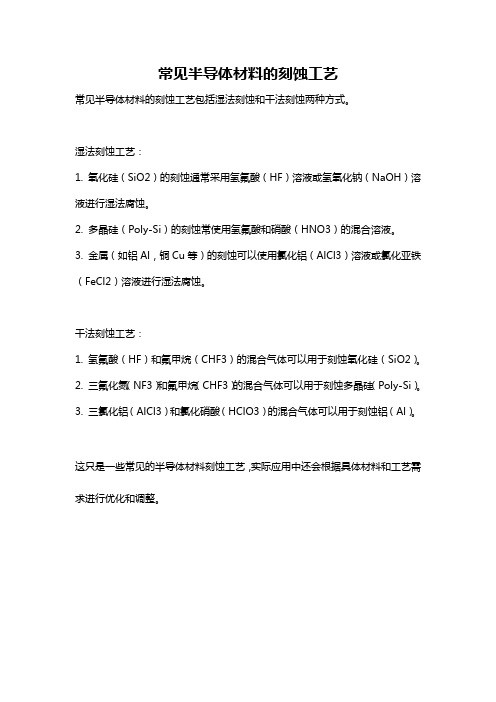
常见半导体材料的刻蚀工艺
常见半导体材料的刻蚀工艺包括湿法刻蚀和干法刻蚀两种方式。
湿法刻蚀工艺:
1. 氧化硅(SiO2)的刻蚀通常采用氢氟酸(HF)溶液或氢氧化钠(NaOH)溶液进行湿法腐蚀。
2. 多晶硅(Poly-Si)的刻蚀常使用氢氟酸和硝酸(HNO3)的混合溶液。
3. 金属(如铝Al,铜Cu等)的刻蚀可以使用氯化铝(AlCl3)溶液或氯化亚铁(FeCl2)溶液进行湿法腐蚀。
干法刻蚀工艺:
1. 氢氟酸(HF)和氟甲烷(CHF3)的混合气体可以用于刻蚀氧化硅(SiO2)。
2. 三氟化氮(NF3)和氟甲烷(CHF3)的混合气体可以用于刻蚀多晶硅(Poly-Si)。
3. 三氯化铝(AlCl3)和氯化硝酸(HClO3)的混合气体可以用于刻蚀铝(Al)。
这只是一些常见的半导体材料刻蚀工艺,实际应用中还会根据具体材料和工艺需求进行优化和调整。
第二章干法刻蚀的介绍
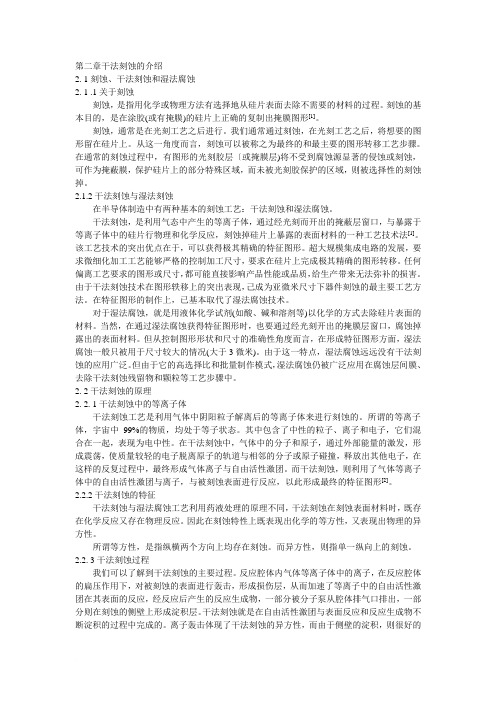
第二章干法刻蚀的介绍2. 1刻蚀、干法刻蚀和湿法腐蚀2. 1 .1关于刻蚀刻蚀,是指用化学或物理方法有选择地从硅片表面去除不需要的材料的过程。
刻蚀的基本目的,是在涂胶(或有掩膜)的硅片上正确的复制出掩膜图形[1]。
刻蚀,通常是在光刻工艺之后进行。
我们通常通过刻蚀,在光刻工艺之后,将想要的图形留在硅片上。
从这一角度而言,刻蚀可以被称之为最终的和最主要的图形转移工艺步骤。
在通常的刻蚀过程中,有图形的光刻胶层〔或掩膜层)将不受到腐蚀源显著的侵蚀或刻蚀,可作为掩蔽膜,保护硅片上的部分特殊区域,而未被光刻胶保护的区域,则被选择性的刻蚀掉。
2.1.2干法刻蚀与湿法刻蚀在半导体制造中有两种基本的刻蚀工艺:干法刻蚀和湿法腐蚀。
干法刻蚀,是利用气态中产生的等离子体,通过经光刻而开出的掩蔽层窗口,与暴露于等离子体中的硅片行物理和化学反应,刻蚀掉硅片上暴露的表面材料的一种工艺技术法[1]。
该工艺技术的突出优点在于,可以获得极其精确的特征图形。
超大规模集成电路的发展,要求微细化加工工艺能够严格的控制加工尺寸,要求在硅片上完成极其精确的图形转移。
任何偏离工艺要求的图形或尺寸,都可能直接影响产品性能或品质,给生产带来无法弥补的损害。
由于干法刻蚀技术在图形轶移上的突出表现,己成为亚微米尺寸下器件刻蚀的最主要工艺方法。
在特征图形的制作上,已基本取代了湿法腐蚀技术。
对于湿法腐蚀,就是用液体化学试剂(如酸、碱和溶剂等)以化学的方式去除硅片表面的材料。
当然,在通过湿法腐蚀获得特征图形时,也要通过经光刻开出的掩膜层窗口,腐蚀掉露出的表面材料。
但从控制图形形状和尺寸的准确性角度而言,在形成特征图形方面,湿法腐蚀一般只被用于尺寸较大的情况(大于3微米)。
由于这一特点,湿法腐蚀远远没有干法刻蚀的应用广泛。
但由于它的高选择比和批量制作模式,湿法腐蚀仍被广泛应用在腐蚀层间膜、去除干法刻蚀残留物和颗粒等工艺步骤中。
2. 2干法刻蚀的原理2. 2. 1干法刻蚀中的等离子体干法刻蚀工艺是利用气体中阴阳粒子解离后的等离子体来进行刻蚀的。
深硅刻蚀工艺原理

深硅刻蚀工艺原理深硅刻蚀(Silicon Deep Etching)是一种用于微纳加工的关键工艺。
它可以在硅片上进行高精度、高深度的刻蚀,用以制造微纳米器件,如微机电系统(MEMS)、传感器、光子器件等。
深硅刻蚀工艺的原理基于湿法刻蚀和干法刻蚀两种方法。
湿法刻蚀是深硅刻蚀的主要原理之一、湿法刻蚀使用一种含有刻蚀剂的溶液,通过溶液与硅表面发生化学反应来刻蚀硅。
湿法刻蚀的刻蚀速度取决于刻蚀剂的浓度、温度、流速等因素。
深硅刻蚀中常用的刻蚀剂有氢氟酸(HF)、氢氧化钾(KOH)和氢氟酸和硝酸(HNO3)的混合物。
在湿法刻蚀过程中,硅表面上的氧化物层会起到保护作用,防止刻蚀剂直接与硅接触。
刻蚀剂通过破坏氧化物层将硅暴露出来,然后溶解硅。
由于刻蚀剂是从硅片的正面和背面进行刻蚀,因此可以实现较大的深度刻蚀。
干法刻蚀是另一种深硅刻蚀的重要原理。
干法刻蚀与湿法刻蚀不同,它不使用溶液来刻蚀硅表面,而是通过气相刻蚀来进行。
干法刻蚀常用的刻蚀气体有氢氟酸、氯化氢和氧化硅等。
干法刻蚀通常利用高能离子束轰击硅表面,将硅表面的原子击碎并氧化,然后通过氧化物在高温下与离子反应生成气体,将离子弹射离开硅表面,从而实现刻蚀作用。
干法刻蚀具有高速度、高精度和高均匀性等优点。
深硅刻蚀的工艺流程一般包括掩膜定义、刻蚀准备、刻蚀、刻蚀终结和清洗等步骤。
首先,通过光刻技术在硅片上定义出掩膜,掩膜上有所需刻蚀的结构。
然后,在刻蚀准备中,对硅片进行表面处理,以去除氧化层和其他杂质。
接下来,进行刻蚀过程,可以采用湿法刻蚀或干法刻蚀,根据需要选择刻蚀剂和刻蚀条件。
刻蚀终结后,通过清洗去除残留的刻蚀剂和刻蚀产物,以便进行下一步的加工或测试。
深硅刻蚀工艺的应用非常广泛。
它可以制造微纳米的光学元件,如光纤阵列、波导、光栅等。
它还广泛用于制造MEMS器件,如惯性传感器、声波传感器、加速度计等。
此外,深硅刻蚀还可以制造微电子器件、太阳能电池组件、生物芯片等。
氮化硅刻蚀工艺

氮化硅刻蚀工艺
氮化硅刻蚀工艺是指通过化学反应的方式将氮化硅材料上的某些部分去除,以达到所需的形状和尺寸。
氮化硅刻蚀常用的方法主要有湿法刻蚀和干法刻蚀两种。
湿法刻蚀是指在湿润环境中使用化学溶液,如酸或碱溶液,对氮化硅材料进行刻蚀。
其中,酸性溶液常用的有浓硝酸、硫酸和氢氟酸等,碱性溶液常用的有氢氧化钠和氢氧化铵等。
湿法刻蚀具有刻蚀速度快、刻蚀均匀等优点,但也存在腐蚀性强、对环境要求高等缺点。
干法刻蚀是指在干燥环境中使用化学气体或等离子体对氮化硅材料进行刻蚀。
常用的干法刻蚀方法有反应离子刻蚀(RIE)和高密度等离子体刻蚀(DRIE)等。
干法刻蚀具有刻蚀速度可控、刻蚀深度均匀、对材料损伤小等优点,但也存在设备复杂、工艺参数调节难等缺点。
在实际应用中,氮化硅刻蚀工艺可以根据具体需求选择合适的刻蚀方法和工艺参数,以实现对氮化硅材料的精确加工和制造。
- 1、下载文档前请自行甄别文档内容的完整性,平台不提供额外的编辑、内容补充、找答案等附加服务。
- 2、"仅部分预览"的文档,不可在线预览部分如存在完整性等问题,可反馈申请退款(可完整预览的文档不适用该条件!)。
- 3、如文档侵犯您的权益,请联系客服反馈,我们会尽快为您处理(人工客服工作时间:9:00-18:30)。
1 干法刻蚀和湿法刻蚀
干法刻蚀是把硅片表面暴露于空气中产生的等离子体,等离子体通过光刻胶中开出的窗口,与硅片发生物理或化学反应,从而去掉暴露的表面材料。
湿法腐蚀是以液体化学试剂以化学方式去除硅片表面的材料。
2刻蚀速率是指在刻蚀过程中去除硅片表面材料的速度,通常用。
A/min表示
刻蚀速率=T/t(。
A/min)
其中T=去掉的材料厚度
t=刻蚀所用的时间
为了高的产量,希望有高的刻蚀速率。
3刻蚀选择比指的是同一刻蚀条件下一种材料与另一种刻蚀材料相比刻蚀速率快多少。
他定义为被刻蚀材料的刻蚀速率与另一种材料的刻蚀速率的比。
干法刻蚀的选择比低,通常不能提供对下一层材料足够高的刻蚀选择比。
高选择比意味着只刻除想要刻去的那层。
4干法刻蚀的主要目的完整的把掩膜图形复制到硅片表面上。
优点:刻蚀剖面是各向异性,具有非常好的侧壁剖面控制,
好的CD控制
最小的光刻胶脱落或粘附问题
好的片内,片间,批次间的刻蚀均匀性
较低的化学制品使用和处理费用
不足:对下层材料的差的刻蚀选择比,等离子体带来的器件损伤和昂贵的设备。
5化学机理:等离子体产生的反应元素与硅片表面的物质发生反应,为了获得高的选择比,进入腔体的气体都经过了慎重选择。
等离子体化学刻蚀由于它是各向同性的,因而线宽控制差。
物理机理:等离子体产生的带能粒子在强电场下朝硅片表面加速,这些离子通过溅射刻蚀作用去除未被保护的硅片表面材料。
6基本部件:发生刻蚀反应的反应腔,一个产生等离子体的射频电源,气体流量控制系统,去除刻蚀生成物和气体的真空系统。
氟刻蚀二氧化硅,氯和氟刻蚀铝,氯,氟和溴刻蚀硅,氧去除光刻胶。
7 ECR反应器在1-10毫托的工作压力下产生很密的等离子体,他在磁场环境中采用2.45GHz 微波激励源来产生高密度等离子体。
ECR反应器的一个关键点是磁场平行于反映剂的流动方向,这使得自由电子由于磁力的作用做螺旋形运动。
当电子的回旋频率等于所加的微波电场频率时,能有效把电能转移到等离子体中的电子上。
这种振荡增加了电子碰撞的可能性,从而产生高密度的等离子体,获得大的离子流。
8氟基气体
三个步骤:1,预刻蚀,用于去除自然氧化层,硬的掩蔽层和表面污染物来获得均匀的刻蚀2,刻至终点的主刻蚀,用来刻蚀大部分的多晶硅膜,并不损伤栅氧化层和获得理想的各向异性的侧壁剖面。
3,过刻蚀,用于去除刻蚀残留物和剩余多晶硅,并保证对栅氧层的高选择比。
9 氮化硅掩蔽层是用热磷酸进行湿法化学剥离的,这种酸槽一般维持在160摄氏度左右并对露出的氧化硅具有所希望的高选择比,通过使用检控样片进行定时操作。
在暴露的氮化硅上会形成一层氮氧化硅,在去除前,需要在氢氟酸中进行短时间的处理。