炉外精炼各种方法
(六)炉外精炼

1、钢水脱氧 Al作脱氧剂:2Al+3[O]= Al2O3,兼有细化晶粒的作用 2、微合金化 通过钢包喂丝的方法来控制合金的加入量 如加B、Ti、Nb、V和Zr(在脱氧后加入) 3、夹杂物形态控制 用填充有CaSi粉的空心铝丝喂入钢水中,使团状的Al2O3变成球状的铝酸钙。 即可脱氧、细化晶粒,又可改善夹杂物的形态。
二、真空处理
真空处理:就是在浇注前或浇注过程中,利用抽真空的办法以降低钢水处理 容器中的气体压力,达到去除钢中气体和非金属夹杂物的目的 。 方法:液面脱气法 、钢流脱气法 、真空提升脱气法(DH法) 、 循环脱气法(RH法) 1、钢液脱气法(钢液真空滴流脱气法) 原理:将钢水注入真空室,由于压力急剧下降,使流股突然膨胀并散 开成一定角度以滴状降落,使脱气表面积大大增加,有利于气体逸出。 方法:倒包法、真空浇注法、出钢过程脱气法 缺点:钢水降温严重 措施:过热100℃
三、钢包精炼
真空脱气法是以提高钢的质量为主要目的发展起来的,钢包精炼法则 是在确保质量的同时,以提高生产效率和降低生产成本为目标发展起来的 . 以代替电炉的还原精炼(脱O、脱S、去夹杂及成分调整)。
钢包真空精炼法(ASEA-SKF) 真空吹氧脱碳法(VOD法) 钢包炉精炼法(LF法) VOD法适合精炼超低碳钢种及特殊钢 冶金反应动力学条件好,可适当补充 加热,防止温度降。
图13-6 VOD法示意图 1-氧枪;2-合金添加孔;3-氩气;4-抽气孔
四、氩氧精炼(氩气脱碳法。AOD法)
该方法是精炼不锈钢的一个有效方法。
1、原理:用Ar作为稀释气体以降低CO的分压, 使钢水中的碳优先氧化,抑制铬的氧化, 以达到脱碳保铬的目的。
2、生产不锈钢的过程: 电炉熔化(Cr、Ni调整) →调整温度1600~1650℃→扒渣脱硫 →出钢水至钢包 →AOD炉精炼(脱C、脱S、调整成分及温度)
炉外精炼
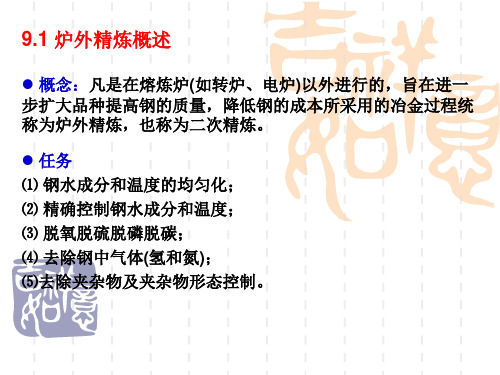
ASEA-SKF法的特点: 将炼钢过程分为两步:由初炼炉(如电炉、转炉)熔化钢铁料, 调整含碳量和温度;然后在钢包炉内,在电磁搅拌的条件 下,进行电弧加热、真空脱气、除渣和造新渣、脱硫、真 空脱氧和脱碳、调整成分与温度,最后吊出钢包进行浇注。
ASEA-SKF法的主要设备: ① 钢包由非磁性材料制成,有滑动水口,可直接用于浇注; ② 电磁感应搅拌器使钢水产生搅拌作用; ③ 真空炉顶及电气设备; ④ 电视—摄影及其他辅助设备如钢包移动装置,原料加入装 置和集尘装置等。
形式: ⑴ 底吹。是通过安装在钢包底部一定位置的透气砖(或 其他形式的喷口),将氩气吹入钢液。 ⑵ 顶吹。吹氩喷枪插入钢包内的钢液中,在接近包低 处将氩气吹入钢液。
最常见的有两种:CAS和CAS—OB。 ⑴ CAS 概念:采用强吹氩工艺将渣液面吹开后,将封闭的浸渍 钟罩内迅速形成氩气保护气氛,避免了钢水氧化的工艺 称为CAS法,又称SAB法。
9.1 炉外精炼概述
概念:凡是在熔炼炉(如转炉、电炉)以外进行的,旨在进一 步扩大品种提高钢的质量,降低钢的成本所采用的冶金过程统 称为炉外精炼,也称为二次精炼。
任务 ⑴ 钢水成分和温度的均匀化; ⑵ 精确控制钢水成分和温度; ⑶ 脱氧脱硫脱磷脱碳; ⑷ 去除钢中气体(氢和氮); ⑸去除夹杂物及夹杂物形态控制。
基本手段 (1) 渣洗;(合成渣渣洗) (2) 搅拌;(CAS钢包吹氩精炼) (3) 真空;(RH真空循环脱碳法) (4) 加热;(LF) (5) 喷吹。(WF喂丝法)
主要作用 ⑴ 提高质量扩大品种的主要手段; ⑵ 优化冶金生产流程,提高生产效率节能降耗降低成本 主要方法; ⑶ 炼钢—炉外精练—连铸—热装轧制工序衔接。
幻灯片 12
特点: ⑴ 除底部吹氩外,在钢包液面上加一沉入罩,罩内充有从钢 液中排出的或专门导人的氩气。 ⑵ 通过罩上方的加料口,可添加合成渣料和微调钢液成分用 的合金。 优点: ⑴ 均匀钢水成分和温度,且控制快速、准确,操作方便; ⑵ 提高合金收得率,且稳定; ⑶ 净化钢液,去除夹杂物,连铸坯质量提高; ⑷ 基建、设备投资少,操作费用低。
精选炉外精炼工艺
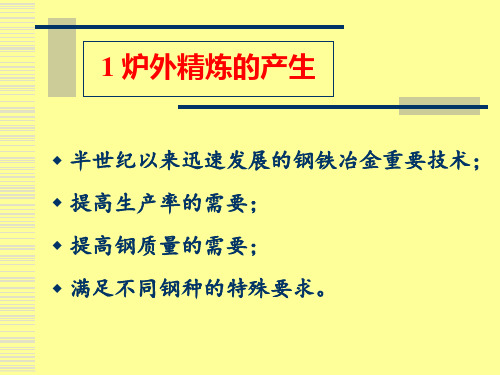
合成渣洗
根据要求将各种渣料配置成满足某种冶金功能 的合成炉渣;
通过在专门的炼渣炉中熔炼,出钢时钢液与炉 渣混合,实现脱硫及脱氧去夹杂功能;
不能去除钢中气体; 必须将原炉渣去除; 同炉渣洗、异炉渣洗。
真空处理
脱气的主要方法 提高真空度可将钢中C、H、O降低;
日本真空技术,真空度到1 torr; C<10ppm,H<1ppm,O<5ppm
3.3 VD/VOD 炉
VD 的功能仅是真空加搅拌, VOD 是Vacuum and stir and injection
oxygen; VD主要应用于轴承钢脱氧; VOD 主要用于不锈钢冶炼;
V D / VOD
VD工艺
以轴承钢冶炼为例
轴承钢最重要的性能指标是疲劳寿命。
影响轴承钢寿命的重要指标是钢中氧含量,钢 中[O]控制在10ppm为好。
3.5 CAS、CAS-OB精炼工 艺
工艺优点: • 钢液升温和精确控制钢水温度 • 促进夹杂物上浮,提高钢水纯净度 • 精确控制钢液成分,实现窄成分控制 • 均匀钢水成分和温度 • 与喂线配合,可进行夹杂物的变性处理 • 冶炼节奏快,适合转炉的冶炼节奏。
CAS和CAS-OB
O2
CAS-OB的冶炼效果
加热;升温速度5-6℃/min; 钢液成分:吹氧前后变化不大; 钢水洁净度:[O]基本不变,可降低
[N]含量。
3.6 喷粉工艺
效果最好投资及使用成本最低也是最不好掌握的 技术;可脱硫、脱磷、合金化、夹杂变性;
工艺参数: 喷枪插入深度;h=H(钢液深)-hc(喷入深); 喷吹压力:大于钢液、炉渣及大气压; 喷吹时间:喷粉设备及钢液容纳粉剂的能力; 供料速度:设备能力及钢液化学反应速度; 载气能力与粉气比。
炉外精炼教程
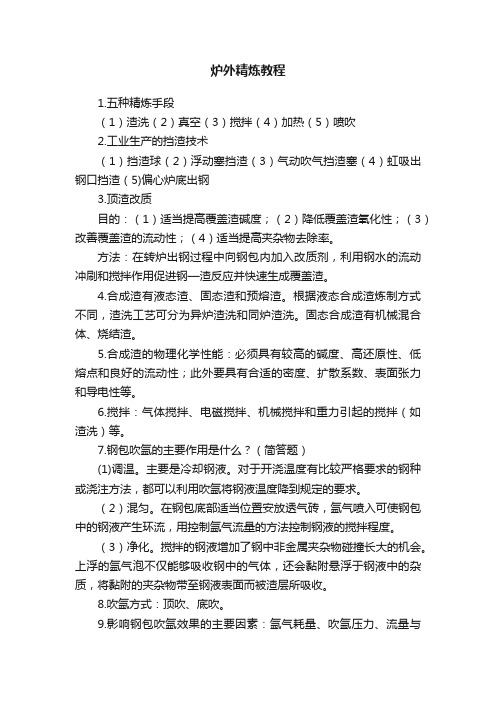
炉外精炼教程1.五种精炼手段(1)渣洗(2)真空(3)搅拌(4)加热(5)喷吹2.工业生产的挡渣技术(1)挡渣球(2)浮动塞挡渣(3)气动吹气挡渣塞(4)虹吸出钢口挡渣(5)偏心炉底出钢3.顶渣改质目的:(1)适当提高覆盖渣碱度;(2)降低覆盖渣氧化性;(3)改善覆盖渣的流动性;(4)适当提高夹杂物去除率。
方法:在转炉出钢过程中向钢包内加入改质剂,利用钢水的流动冲刷和搅拌作用促进钢—渣反应并快速生成覆盖渣。
4.合成渣有液态渣、固态渣和预熔渣。
根据液态合成渣炼制方式不同,渣洗工艺可分为异炉渣洗和同炉渣洗。
固态合成渣有机械混合体、烧结渣。
5.合成渣的物理化学性能:必须具有较高的碱度、高还原性、低熔点和良好的流动性;此外要具有合适的密度、扩散系数、表面张力和导电性等。
6.搅拌:气体搅拌、电磁搅拌、机械搅拌和重力引起的搅拌(如渣洗)等。
7.钢包吹氩的主要作用是什么?(简答题)(1)调温。
主要是冷却钢液。
对于开浇温度有比较严格要求的钢种或浇注方法,都可以利用吹氩将钢液温度降到规定的要求。
(2)混匀。
在钢包底部适当位置安放透气砖,氩气喷入可使钢包中的钢液产生环流,用控制氩气流量的方法控制钢液的搅拌程度。
(3)净化。
搅拌的钢液增加了钢中非金属夹杂物碰撞长大的机会。
上浮的氩气泡不仅能够吸收钢中的气体,还会黏附悬浮于钢液中的杂质,将黏附的夹杂物带至钢液表面而被渣层所吸收。
8.吹氩方式:顶吹、底吹。
9.影响钢包吹氩效果的主要因素:氩气耗量、吹氩压力、流量与吹氩时间及气泡大小等。
10.能量耗散速率(比搅拌功率):单位时间内,向1t钢液提供的搅拌能量作为描述搅拌特征和质量的指标。
11.常用的加热方法主要是电弧加热,化学加热(化学热法)、燃料燃烧加热、电阻加热等12.燃料燃烧加热存在哪些不足?(1)由于燃烧的火焰是氧化性的,而炉外精炼时总是希望钢液处在还原性气氛下,这样钢液加热时,必然会使钢液和覆盖在钢液面上的精炼渣的氧势提高,不利于脱硫、脱氧这样一些精炼反应的进行。
炉外精炼工艺技术
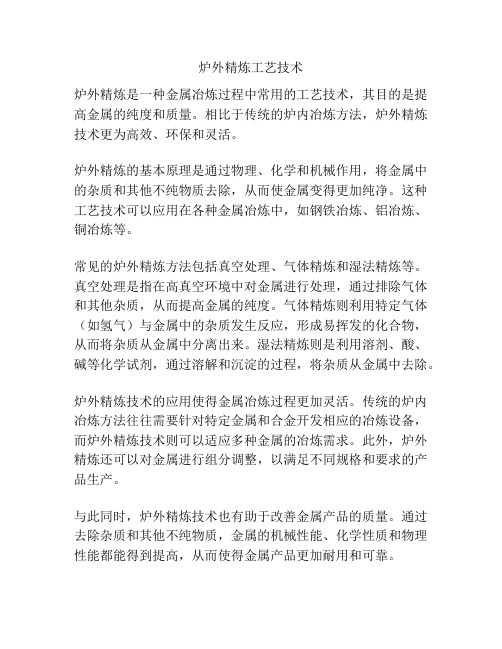
炉外精炼工艺技术炉外精炼是一种金属冶炼过程中常用的工艺技术,其目的是提高金属的纯度和质量。
相比于传统的炉内冶炼方法,炉外精炼技术更为高效、环保和灵活。
炉外精炼的基本原理是通过物理、化学和机械作用,将金属中的杂质和其他不纯物质去除,从而使金属变得更加纯净。
这种工艺技术可以应用在各种金属冶炼中,如钢铁冶炼、铝冶炼、铜冶炼等。
常见的炉外精炼方法包括真空处理、气体精炼和湿法精炼等。
真空处理是指在高真空环境中对金属进行处理,通过排除气体和其他杂质,从而提高金属的纯度。
气体精炼则利用特定气体(如氢气)与金属中的杂质发生反应,形成易挥发的化合物,从而将杂质从金属中分离出来。
湿法精炼则是利用溶剂、酸、碱等化学试剂,通过溶解和沉淀的过程,将杂质从金属中去除。
炉外精炼技术的应用使得金属冶炼过程更加灵活。
传统的炉内冶炼方法往往需要针对特定金属和合金开发相应的冶炼设备,而炉外精炼技术则可以适应多种金属的冶炼需求。
此外,炉外精炼还可以对金属进行组分调整,以满足不同规格和要求的产品生产。
与此同时,炉外精炼技术也有助于改善金属产品的质量。
通过去除杂质和其他不纯物质,金属的机械性能、化学性质和物理性能都能得到提高,从而使得金属产品更加耐用和可靠。
除了提高金属产品的质量外,炉外精炼技术还可以减少环境污染。
传统的炉内冶炼方法往往会产生大量的废气、废水和废渣,对环境造成严重的污染。
而炉外精炼技术则通过控制冶炼过程中的气体、液体和固体排放,使得废气减少、废水得到处理和回收、废渣变废为宝,从而实现了资源的循环利用和环境保护。
总之,炉外精炼工艺技术是一种高效、环保和灵活的金属冶炼方法。
它通过利用物理、化学和机械作用,对金属中的杂质和其他不纯物质进行去除,从而提高金属的纯度和质量。
这种技术的应用不仅可以改善金属产品的质量,还可以减少环境污染,实现资源的循环利用。
炉外精炼工艺技术是金属冶炼领域中的一项重要技术手段,它能够在金属冶炼过程中去除杂质和不纯物质,提高金属的纯度和质量。
炉外精炼的工艺设计

炉外精炼的工艺设计炉外精炼是一种对金属合金进行深度精炼的工艺,在金属冶炼过程中起到非常重要的作用。
炉外精炼技术可以通过减小金属杂质含量、提高合金成分均匀性、调整合金中的内应力和改善合金物理性能等多个方面对合金进行改善和调整。
本文将详细介绍炉外精炼的工艺设计。
1.炉外精炼工艺选择-操作方式:炉外精炼可以采用化学或物理方式进行,例如溶剂抽取、真空除气、电渣重熔等。
根据合金材料和工艺要求选择最合适的精炼方式。
-精炼介质:选择合适的精炼介质,例如惰性气体、真空、溶剂等,根据材料特性和成分要求进行选择。
-精炼设备:根据工艺要求选择合适的设备,例如真空炉、溶剂萃取设备、电渣炉等。
2.炉外精炼的关键参数控制-温度:精确控制精炼温度,根据不同的材料和要求进行调整,确保炉外精炼的效果。
-压力:根据材料的气体溶解度和精炼介质的选择,调整精炼过程中的压力,确保溶质向介质中迁移。
-时间:根据精炼过程的要求,确定精炼的时间,在一段时间内实现对杂质去除、合金调整和分相等的目标。
-速度:根据炉外精炼的工艺要求,确定精炼过程中的速度,例如溶质迁移速度、溶剂流动速度等。
3.炉外精炼的工艺步骤-准备工作:包括材料的预处理、精炼设备的准备、精炼介质的选择等。
-进料:将需要精炼的材料进料到精炼设备中,并根据要求确定进料方式和进料量。
-精炼操作:根据工艺要求进行精炼操作,例如加热、真空抽取、溶剂萃取等。
-过程监测:通过监测精炼过程中的温度、压力、溶质浓度等参数,控制精炼过程的效果,并及时调整工艺参数。
-精炼结束:根据工艺要求,判断精炼过程是否达到预期目标,如果达到预期目标,则结束精炼过程。
-产品处理:对精炼后的产品进行处理,例如冷却、干燥、分析检测等。
4.炉外精炼的优点和应用炉外精炼技术具有以下优点:-可以有效地去除金属杂质,改善合金的纯度和均匀性。
-可以调整合金的成分和物理性能,满足不同的应用要求。
-可以减小合金中的内应力,提高材料的延展性和抗拉强度。
炉外精炼
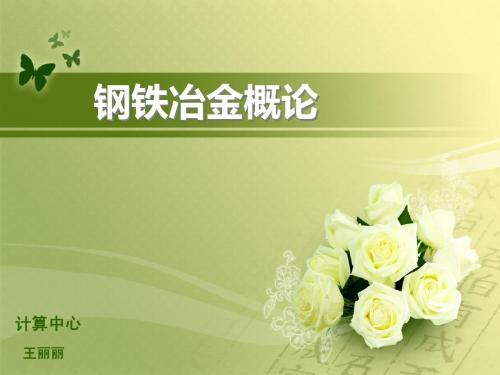
LF法 9.1 LF法
LF LF LLeabharlann LF炉精炼
原
理
2、LF的精炼操作 LF的精炼操作 将石灰、萤石按不同比例分批加入钢包中, 将石灰、萤石按不同比例分批加入钢包中,加入量为 钢水量的1 2%,造高碱度合成渣脱硫,然后用硅铁粉、 钢水量的1-2%,造高碱度合成渣脱硫,然后用硅铁粉、 硅钙粉和铝粉或炭粉按一定比例混合直接加入钢水面或 采取喷吹的方法加入钢水中形成流动性良好的炉渣。 采取喷吹的方法加入钢水中形成流动性良好的炉渣。
3)可进行吹氧脱碳和二次燃烧进行热补偿,减少处理 可进行吹氧脱碳和二次燃烧进行热补偿, 温降; 温降; 可进行喷粉脱硫,生产[S]≤5 10- 的超低硫钢。 [S]≤5× 4)可进行喷粉脱硫,生产[S]≤5×10-6的超低硫钢。 RH真空工艺过程 2、 RH真空工艺过程 出钢后,钢包测温取样; 1)出钢后,钢包测温取样; 下降真空室,插入深度为150 200mm; 1502)下降真空室,插入深度为150-200mm; 起动真空泵,一根插入管输入驱动气体; 3)起动真空泵,一根插入管输入驱动气体;真空室的 压力降到26 10kpa后 循环加剧; 26- 压力降到26-10kpa后,循环加剧;钢水上升速度为 5m/s、下降速度为1 2m/s; 5m/s、下降速度为1-2m/s; 气泡在钢液中将气体及夹杂带出。 4)气泡在钢液中将气体及夹杂带出。 如此反复循环3 次后达到脱气要求, 5)如此反复循环3-4次后达到脱气要求,处理时间约 20分钟 分钟。 为20分钟。
VD/VOD炉 9.2 VD/VOD炉
VD 的功能仅是真空加搅拌, 的功能仅是真空加搅拌, VOD 是真空吹氧精炼法; 是真空吹氧精炼法; VD主要应用于轴承钢脱氧; 主要应用于轴承钢脱氧; 主要应用于轴承钢脱氧 VOD 主要用于不锈钢冶炼; 主要用于不锈钢冶炼;
转炉炼钢炉外精炼与连铸工艺
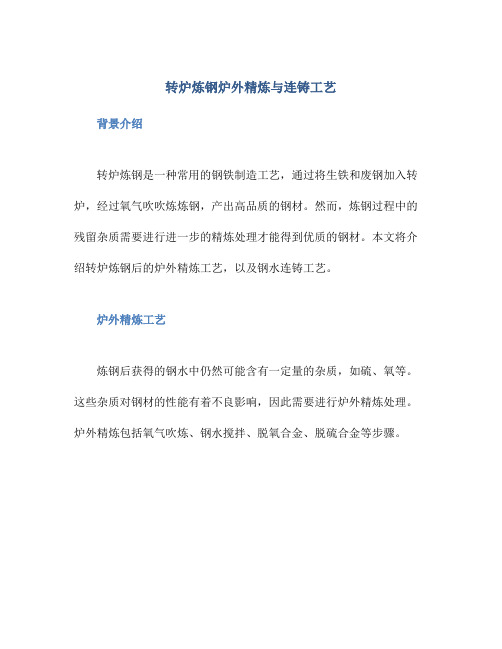
转炉炼钢炉外精炼与连铸工艺背景介绍转炉炼钢是一种常用的钢铁制造工艺,通过将生铁和废钢加入转炉,经过氧气吹吹炼炼钢,产出高品质的钢材。
然而,炼钢过程中的残留杂质需要进行进一步的精炼处理才能得到优质的钢材。
本文将介绍转炉炼钢后的炉外精炼工艺,以及钢水连铸工艺。
炉外精炼工艺炼钢后获得的钢水中仍然可能含有一定量的杂质,如硫、氧等。
这些杂质对钢材的性能有着不良影响,因此需要进行炉外精炼处理。
炉外精炼包括氧气吹炼、钢水搅拌、脱氧合金、脱硫合金等步骤。
氧气吹炼是炼钢后必不可少的处理步骤之一。
通过将氧气通入钢水中,可以氧化钢水中的杂质,提高钢水的纯度。
同时,氧气吹炼还可以促进钢水的温度均匀性,减少气泡等缺陷。
钢水搅拌钢水搅拌是通过机械手等设备对炉外的钢水进行搅拌,促使钢水中的气泡和杂质向上浮动,有助于去除杂质并提高钢水的均匀性。
脱氧合金脱氧合金是指向钢水中添加具有强还原性的合金元素,如硅、铝等。
这些合金元素可以与钢水中氧化铁等氧化物结合,减少钢水中氧的含量,提高钢水的纯度。
脱硫合金是指向钢水中添加具有高硫亲和性的合金元素,如镁、钙等。
这些合金元素可以与钢水中的硫结合,从而降低钢水中的硫含量,提高钢材的质量。
钢水连铸工艺钢水连铸是钢材生产中的一项重要工艺,通过将炉外精炼处理后的钢水连续铸造成坯料、板材等形状的半成品。
钢水连铸可以有效提高生产效率,减少钢材的能耗和生产成本。
连铸机连铸机是实现钢水连铸的设备,通常由结晶器、浇铸机、冷却装置等组成。
在连铸机中,经过炉外精炼处理的钢水被连续铸造成各种形状的半成品,如板材、方坯等。
在连铸过程中,钢水经过结晶器冷却凝固,逐渐形成坯料,然后通过浇铸机进行切割成指定长度的板材。
冷却装置可以控制板材的温度和结晶组织,保证最终产品的质量。
连铸优势钢水连铸具有生产周期短、成品质量高、生产过程环保等优势。
同时,连铸还可以减少人工操作,提高生产效率,是现代钢铁制造中不可或缺的工艺。
结语通过炉外精炼和钢水连铸工艺,钢铁制造厂可以生产出高品质、高效率的钢材产品,满足市场需求。
工业硅炉外精炼的方法

工业硅炉外精炼的方法
工业硅炉外精炼是一种用于提高硅材料纯度和质量的关键工艺。
它通常是在硅
炉内部冶炼过程之后进行的,以去除残留的杂质和提高硅的纯净度。
以下是常用的工业硅炉外精炼方法:
1. 酸洗法:酸洗法是一种常见的精炼方法,通过将硅材料浸泡在酸性溶液中,
如盐酸或氢氟酸中,可以去除杂质。
酸洗的过程需要在恰当的温度和浸泡时间下进行,以确保杂质被充分溶解并去除。
2. 碱洗法:碱洗法是另一种常用的精炼方法。
硅材料可以被浸泡在碱性溶液中,如氢氧化钠或氨水中。
碱性条件可以使一些杂质在溶液中发生沉淀或化学反应,从而去除它们。
3. 氧化法:氧化是一种常用于硅材料精炼的方法。
在高温下,硅材料可以与氧
气反应形成氧化硅,并与部分杂质形成易于分离的氧化物。
这种方法可以去除硅材料中的一些杂质,提高纯度。
4. 熔炼法:熔炼法是将硅材料在高温下熔化,并使用不同的附加剂来吸附或反
应掉杂质的方法。
这些附加剂可以是金属、气体或其他高反应性物质。
这种方法可以去除大部分杂质,提高硅的纯度。
需要注意的是,工业硅炉外精炼方法的选择要根据具体的杂质种类和硅材料的
要求来确定。
不同的方法可能对不同的杂质有不同的效果。
此外,精炼过程需要控制温度、时间和化学条件,以确保精炼效果和硅材料的质量。
总之,在工业硅生产中,硅炉外精炼是一个重要的工艺步骤,可以提高硅材料
的纯度和质量。
通过选择适当的方法和调整精炼条件,我们能够去除杂质并获得高纯度的硅材料。
炉外精炼各种方法

节流量50-80NL/min,同时测温、取样,加入 硅石2 kg/mm,调整炉渣碱度R=1 .2-1 .5。 • 测温、取样后VD加盖密封,抽真空。 • 真空泵启动期间,调整氩气流量保持30 - 40NL/min。
CAS工艺操作过程
RH钢液循环脱气法
• 主要冶炼高质量产品,如轴承钢、LF钢、硅钢、 不锈钢、齿轮钢等。
• 特点:①反应速度快,表观脱碳速度常数kC可达
到3.5min-1。处理周期短,生产效率高,常与转 炉配套使用。②反应效率高,钢水直接在真空室 内进行反应,可生产H≤0.5×10-6,N≤25×10-6, C≤10×10-6的超纯净钢。③可进行吹氧脱碳和二 次燃烧进行热补偿,减少处理温降;④可进行喷粉 脱硫,生产[S]≤5×10-6的超低硫钢。
VD工艺
• 真空保持时间:真空启动后,工作压力达到67 Pa时,保持时间≥15min。
• 真空保持期间调整氩气流量 70NL/min左右,并 通过观察孔观察钢水沸腾情况,及时调整,保持 均匀沸腾。
• 终脱氧后解除真空、开盖、测温,软吹15- 25min,氩气流量 70-100NL/min左右,控制 渣面微动为宜。
拌,进一步脱碳, 钢液温度达到1670-1750之间. • 6.加合金,微调成分,加铝吹氩搅拌几分 后,破真空浇铸.
AOD炉
AOD炉 主要是冶炼高质量的不锈 钢(C<20ppm,S,P<50ppm)使用更廉 价的原料(采用高碳铬代替低碳铬) 60%-70%的不锈钢产量 炉料:废钢,不锈钢返回料,高碳铬 铁,高碳镍铁 吹炼过程就是温度及氩氧比的控制 T=1680 O2:Ar=4:1(3:1)C下降为0.2% T=1700 O2:Ar=2;1 C下降为0.1% T=1730 O2:Ar=1;2 C下降为0.02% T=1750 O2:Ar=1:3 C下降为0.001%
钢铁冶金概论炉外精炼

钢铁冶金概论炉外精炼炉外精炼是现代钢铁冶金中一个非常重要的工艺阶段,它能够对已经经过高炉冶炼出来的熔融铁液进行进一步的处理和提纯,以得到更高品质的钢材。
本文将详细介绍炉外精炼的过程、方法以及其在钢铁冶金中的重要性。
炉外精炼的过程主要包括除氧、脱硫、还原剂控制等步骤。
首先是除氧过程,其目的是通过添加合适的除氧剂,将铁液中的氧气去除,以减少氧化和损耗。
通常使用的除氧剂有铝、硅及铝硅合金等。
除氧剂能与铁液中的氧气反应生成气体,如气体呈气泡状排出,并生成含铝或含硅的化合物,从而减少氧含量。
接下来是脱硫过程,铁液中的硫是一种有害的杂质,会导致钢材成品的脆化和性能下降。
因此,脱硫是炉外精炼过程中非常重要的一步。
常见的脱硫方法有氧化法和还原法。
氧化法主要是通过向铁液中添加氧化剂,使硫与氧化剂反应生成气体,如硫化氢,从而排出铁液中的硫。
还原法则是通过添加还原剂,通常是含碳的物质,使其与硫反应生成硫化物,再由硫化物降解和沉淀,从而实现脱硫目的。
此外,还需要对还原剂进行控制。
还原剂的控制是为了保持炉外精炼环境的还原性,从而有利于脱硫、除氧等反应的进行。
一般来说,还原剂的添加量应该合理,过多会导致过量还原,出现大量一氧化碳和游离碳的气体产生,而过少则会导致还原不充分,无法完全去除硫。
炉外精炼在钢铁冶金中的重要性不言而喻。
通过炉外精炼,可以进一步提高钢材的质量。
首先,炉外精炼可以去除铁液中的氧和硫等有害元素,减少钢材的夹杂物含量,提高了钢材的纯度和机械性能。
其次,炉外精炼还能调整钢液的成分,包括碳含量、合金元素含量等,使得钢材具有更好的性能和应用范围。
另外,炉外精炼中的控制参数对钢材的性能也有很大影响,合理地控制还原剂的添加量、操作温度、反应时间等,将会进一步提高钢材的质量。
总之,炉外精炼是现代钢铁冶金过程中一项非常重要的工艺阶段。
通过除氧、脱硫和还原剂控制等步骤,可以对铁液进行进一步的处理和提纯,最终得到高品质的钢材。
炉外精炼

LF炉
最常用的精炼方法 取代电炉还原期 解决了转炉冶炼优钢问题 具有加热及搅拌功能 脱氧、脱硫、合金化
LF炉工艺操作
电炉EBT出钢,出钢过程加合金、加渣料(石灰、 萤石等2%),底吹氩、通电升温、化渣,10分钟 取样分析,加渣料(1%),测温取样,加合金看 脱氧,准备出钢。
炉外精炼技术
郭海生主讲
炉外精炼
炉外精炼就是将转炉或电炉初炼的钢 水移到另一反应器进行精炼的过程,也称 二次精炼 太钢的二次精炼设备主要有:AOD、LF、 VOD、K-、惰性气氛或可控气氛的条件 下进行深脱碳、脱硫、脱氧、除气、调整 成分(微合金化)和调整温度并使其均匀化, 去除夹杂物,改变夹杂物形态和组成等。 钢水炉外精炼是为适应钢的品种质量的提 高,生产新钢种以及生产过程合理化,为 连铸对钢水成分、温度、纯净度和时间等 衔接的严格要求,不可缺少的工序,成为 现代炼钢、连铸生产中的重要环节。
AOD工艺过程
炉料:废钢、不锈钢返回料、高碳铬铁、高碳镍 铁 吹炼过程温度及氩氧比的控制 分不同温度及碳含量控制吹炼氩氧比: O2:Ar=4:1(3:1),C下降为0.2%、T=1680℃; O2:Ar=2:1, C下降为0.1%、T=1700℃; O2:Ar=1:2, C下降为0.02%、T=1730℃; O2:Ar=1:3, C下降为0.01%、T=1750℃;
CLU
GOR
底部
底部
O2、H2O(蒸汽)、N2、 O2、N2、Ar Ar
O2、N2、Ar、碳氢 化合物 O2、N2、Ar
1
1.3~1.5
AOD-VCR
VOD/SSVOD
侧部
底部
O2、N2、Ar
O2、Ar O2
炉外精炼

平炉: 平炉炼钢自1864年法国人P..马丁利用有蓄热室 的火焰炉 , 用废钢、生铁成功地炼出钢 液起,直到1960年一直是世 界上的主要炼钢方法 ,从60 年代起平炉逐渐被氧气转炉 和电炉炼钢所代替。
1.2 炉外精炼的任务
1)降低钢中氧、硫、氢、氮和非金属夹杂物含量,改变夹 杂物形态,以提高钢的纯净度,改善钢的力学性能。 2)深脱碳,满足低碳或超低碳钢的要求。 3)微调合金成分,把合金成分控制在很窄的范围内,并使其 分布均匀,尽量降低合金的消耗,以提高合金收得率。 4)调整钢液温度到浇注所要求的温度范围内,最大限度地 减小包内钢液的温度梯度。 5)作为炼钢与连铸间的缓冲,提高炼钢车间整体效率。
固态渣: 将固体的合成渣料在出钢前或在出钢过程中 加入钢包中。 固态渣分为: 机械混合渣、烧结渣
机械混合渣:直接将一定比例和粒度原材料 进行人工或机械混合,或者直接将原材料按 比例加入钢包内。 有点:便宜,方便 缺点:熔化速度慢、成分不均匀、易吸潮。
烧结渣: 将原来按一定比例和粒度混合后,在低于原 料熔点的情况下加热,使原料烧结在一起的 过程。 优点:混合均匀、稳定 缺点:密度小,气孔多,易吸气。
2)浮动塞挡渣 将挡渣物制成上为倒锥体下为棒状的塞。由 于其形状接近于漏斗形,可配合出钢时的钢 水流,故比挡渣球效率高。出钢时用专用机 械将挡渣塞吊置在出钢口上方,缓缓加到钢 水面上。挡渣塞能堵住出钢口而阻挡炉渣流 出。
3)气动吹气挡渣塞 4)虹吸出港口挡渣 5)偏心炉底出钢 优点: 1)可实现无渣出钢,易与炉外精炼配合 2)钢流短,无散流,缩短出钢时间,减少了钢水 二次氧化 3)减少了耐火材料的消耗
炉外精炼--钢包炉精炼法
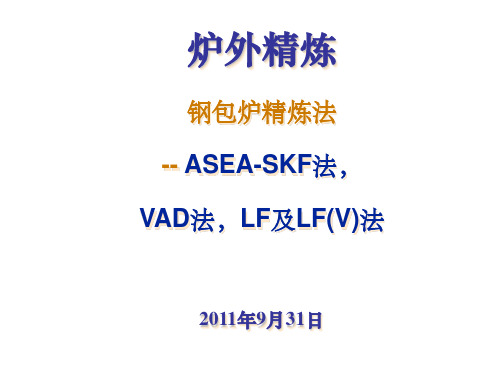
6.3 钢包炉精炼法(LF(V)法)
LF(V):Ladle Furnace (Vacuum)。 是钢包炉的缩写。
无真空工位的叫LF法,带有真空工位的叫LFV法。
LFV法是在ASEA-SKF法和VD法等方法基础上的改 进设备,这三种方法统称为钢包精炼炉。此法是把电
弧炉的还原精炼原样移到钢水包中操作。将电弧埋入
College of Metallurgy & Energy
6.3 钢包炉精炼法(LF(V)法)
LF钢包精炼炉按加热方式可分为交流钢包炉、直 流钢包炉以及等离子枪加热钢包炉。 等离子枪加热钢包炉:
三相交流等离子钢包炉,由于没有电极造成的增碳,
有利于生产高洁净度的极低碳钢。新日铁广烟制铁 所使用的是三相交流等离子的PLF法。
合金与渣料加料系统、底吹氩搅拌系统、喂线系统、炉盖 及冷却水系统(有的没有冷却系统)、除尘系统、测温取样 系统、钢包车控制系统等,如图6-9所示。按照供电方式 分为交流钢包炉和直流钢包炉,目前国内多数炉是使用交 流钢包炉。
College of Metallurgy & Energy
1-电极; 2-合金料仓;3-透气转;4-滑动水口 图6-9 LF设备示意图
a-炉盖旋转式;b-钢包移动式 1-钢包;2-搅拌器;3-电极盖;4-真空盖 图6-3 ASEA-SKF炉布置方式
College of Metallurgy & Energy
6.1钢包加热电磁搅拌精炼法(ASEA-SKF法)
电磁感应搅拌器
图6-4 搅拌器位置和钢液流动状态示意图
College of Metallurgy & Energy
非真空处理用的钢包,自由空间的高度小一些,对非真空
炉外精炼课件
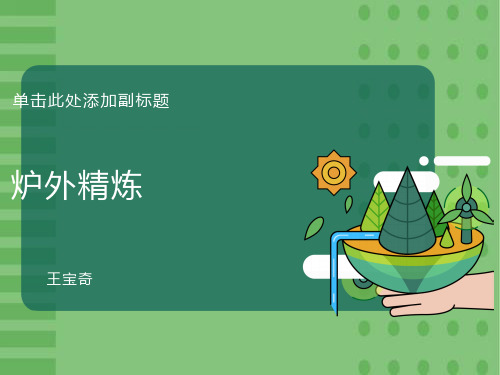
合金的喂入与喷粉 工艺示意图
加热
钢液在进行炉外精炼时,有热量损失,会造成温度下降。若炉外精炼方法 具有加热升温功能,可避免高温出钢和保证钢液正常浇铸,增加炉外精炼 工艺的灵活性,在精炼剂用量,钢液处理最终温度和处理时间均可自由选 择,以获得最佳的精炼效果。
常用的加热方法有电加热和化学加热。
采用专门的真空装置,将钢液置于真空环境中精炼,可以降低钢 中气体、碳及氧含量。
三.添加精炼剂
炉外精炼中金属液的精炼剂一类为以钙的化合物 (CaO或CaC2)为基的粉剂或合成渣,另一类为合金 元素如Ca、Mg、Al、Si及稀土元素等。
将这些精炼剂加入钢液中,可起到脱硫、脱氧、去除 夹杂物、夹杂物变性处理以及合金成分调整的作用。
电加热是将电能转变成热能来加热钢液的。这种加热方式主要有电弧加热 和感应加热。
化学加热是利用放热反应产生的化学热来加热钢液的。常用的方法有硅热 法、铝热法和CO二次燃烧法。化学加热需吹入氧气,与硅、铝、CO反应, 才能产生热量。
钢包加热系统工艺示意图
1 炉外精炼概述
过滤:随着技术的进步出现的一种新的精炼手段,如利用 陶瓷过滤器将中间包内钢液中的氧化物夹杂等过滤掉。
○ EAF(EBT)(或BOF)—LF炉—RH—连铸
4. 不锈钢:EAF或BOF—VOD—(LF炉)—连铸
○ EAF或BOF—AOD—(LF炉)—连铸 ○ EAF或BOF—AOD —VOD—(LF炉)—连铸
常用的炉外精炼方法
2 真空处理的作用
钢液的真空处理的作用 钢液真空处理的目的是去除钢液内的气体和氧、夹杂物,是提高钢水质量
1 炉外精炼概述
一.3炉外处理的基本手段
炉外精炼的手段包括:搅拌、真空、添加精炼剂、 加热(调温)以及过滤。通过这几种精炼手段的 不同组合,为完成某种精炼任务创造最佳热力学 和动力学条件,构成功能不同的炉外精炼设备。
炉外精炼主要工艺
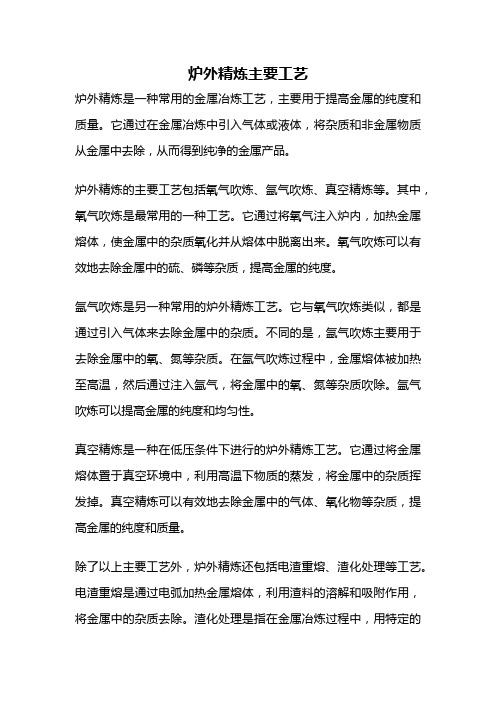
炉外精炼主要工艺炉外精炼是一种常用的金属冶炼工艺,主要用于提高金属的纯度和质量。
它通过在金属冶炼中引入气体或液体,将杂质和非金属物质从金属中去除,从而得到纯净的金属产品。
炉外精炼的主要工艺包括氧气吹炼、氩气吹炼、真空精炼等。
其中,氧气吹炼是最常用的一种工艺。
它通过将氧气注入炉内,加热金属熔体,使金属中的杂质氧化并从熔体中脱离出来。
氧气吹炼可以有效地去除金属中的硫、磷等杂质,提高金属的纯度。
氩气吹炼是另一种常用的炉外精炼工艺。
它与氧气吹炼类似,都是通过引入气体来去除金属中的杂质。
不同的是,氩气吹炼主要用于去除金属中的氧、氮等杂质。
在氩气吹炼过程中,金属熔体被加热至高温,然后通过注入氩气,将金属中的氧、氮等杂质吹除。
氩气吹炼可以提高金属的纯度和均匀性。
真空精炼是一种在低压条件下进行的炉外精炼工艺。
它通过将金属熔体置于真空环境中,利用高温下物质的蒸发,将金属中的杂质挥发掉。
真空精炼可以有效地去除金属中的气体、氧化物等杂质,提高金属的纯度和质量。
除了以上主要工艺外,炉外精炼还包括电渣重熔、渣化处理等工艺。
电渣重熔是通过电弧加热金属熔体,利用渣料的溶解和吸附作用,将金属中的杂质去除。
渣化处理是指在金属冶炼过程中,用特定的渣料对金属熔体进行处理,使杂质和非金属物质结合成渣,并将其从金属中分离出来。
炉外精炼工艺的应用范围广泛。
它可以用于钢铁冶炼、铜冶炼、铝冶炼等金属冶炼过程中。
在钢铁冶炼中,炉外精炼可以去除钢中的硫、磷、氧等杂质,提高钢的纯度和质量。
在铜冶炼中,炉外精炼可以去除铜中的氧、硫等杂质,提高铜的纯度和导电性能。
在铝冶炼中,炉外精炼可以去除铝中的气体、氧化物等杂质,提高铝的纯度和塑性。
炉外精炼是一种重要的金属冶炼工艺,可以提高金属的纯度和质量。
它的主要工艺包括氧气吹炼、氩气吹炼、真空精炼等。
这些工艺通过引入气体或液体,将金属中的杂质和非金属物质去除,从而得到纯净的金属产品。
炉外精炼广泛应用于钢铁、铜、铝等金属冶炼过程中,对提高金属的纯度和质量起到重要作用。
炉外精炼(炼钢工艺)

3)合成渣洗 4)喷粉精炼 5)钢水加热 电弧加热 化学加热(铝热法、硅热发、CO燃烧法 燃烧法) 化学加热(铝热法、硅热发、CO燃烧法)
钢包加热系统工艺示意图
合金的喂入与喷粉工艺示意图
分类
真空精炼法 惰性气体稀释法 渣洗精炼法
AOD
CLU
8.2 炉外精炼方法及冶金效果
AOD
VCR
利用真空和吹 氩,进一步脱 碳
AOD-VCR
8.3 炉外精炼技术发展趋势
1.钢水百分之百地进行处理; 1.钢水百分之百地进行处理; 钢水百分之百地进行处理 2.促使钢铁工业有粗放型向集约型发展 促使钢铁工业有粗放型向集约型发展; 2.促使钢铁工业有粗放型向集约型发展; 3.向组合 多功能化方向发展; 向组合、 3.向组合、多功能化方向发展; 4.对不同规模、不同产品配备不同精炼技术: 4.对不同规模、不同产品配备不同精炼技术: 对不同规模 生产板带钢材企业,应配备CAS OB和RH精炼站 CAS精炼站。 1)生产板带钢材企业,应配备CAS-OB和RH精炼站。 生产棒材的企业,应配备LF炉和喂线手段。 LF炉和喂线手段 2)生产棒材的企业,应配备LF炉和喂线手段。 3)对电弧炉特殊钢厂 生产不锈钢采用EF→AOD→VCR工艺; EF→AOD→VCR工艺 生产不锈钢采用EF→AOD→VCR工艺; 生产轴承钢采用EF→LF→RH→CC工艺; EF→LF→RH→CC工艺 生产轴承钢采用EF→LF→RH→CC工艺; 生产超纯结构钢采用EF→VAR工艺。 EF→VAR工艺 生产超纯结构钢采用EF→VAR工艺。
8.2 炉外精炼方法及冶金效果
四、循环真空脱气法
RH-KTB RH
RH-OB
8.2 炉外精炼方法及冶金效果
五、真空钢包处理
炉外精炼

1、炉外精炼的内容脱氧、脱硫;去气、去除夹杂;调整钢液成分及温度。
2、炉外精炼的手段渣洗:最简单的精炼手段;真空:目前应用的高质量钢的精炼手段;搅拌:最基本的精炼手段;喷吹:将反应剂直接加入熔体的手段;调温:加热是调节温度的一项常用手段。
3、主要的精炼工艺LF(Ladle Furnace process);AOD(Argon-oxygen decaburizition process );VOD (Vacuum oxygen decrease process) ;RH (Ruhrstahl Heraeus process);CAS-OB( Composition adjustments by sealed argon -oxygen blowing process) ;喂线(Insert thread) ;钢包吹氩搅拌(Ladle argon stirring);喷粉( powder injection )。
LF炉LF炉指一种利用钢包对钢水进行炉外精炼的设备!!!LF炉(LADLE FURNACE)即钢包精炼炉,是钢铁生产中主要的炉外精炼设备。
它的主要任务是:①脱硫②温度调节③精确的成分微调④改善钢水纯净度⑤造渣在LF炉生产中建立过程控制计算机系统,主要用来解决以下问题:①实时接收生产计划,按照计划动态组织生产。
②按照炉次对LF炉生产进行实时的数据跟踪。
③通过冶金模型的计算,实现作业过程的优化,同时并向操作人员提供操作指导。
④向下工序提供LF炉作业数据。
⑤向工艺人员提供生产数据的历史追溯.LF炉一般指钢铁行业中的精炼炉。
实际就是电弧炉的一种特殊形式。
最常用的精炼方法;取代电炉还原期;解决了转炉冶炼优钢问题;具有加热及搅拌功能;脱氧、脱硫、合金化LF 精炼炉LF钢包精炼炉可供初炼炉(电炉、中频炉、AOD炉、转炉)钢水精炼、保温之用。
是满足优钢、特钢生产和连铸、连轧的重要冶金设备。
具有常压电弧加热、脱氧去气、吹氩搅拌、加料调整成分、测温、取样、脱磷脱硫等功能。
- 1、下载文档前请自行甄别文档内容的完整性,平台不提供额外的编辑、内容补充、找答案等附加服务。
- 2、"仅部分预览"的文档,不可在线预览部分如存在完整性等问题,可反馈申请退款(可完整预览的文档不适用该条件!)。
- 3、如文档侵犯您的权益,请联系客服反馈,我们会尽快为您处理(人工客服工作时间:9:00-18:30)。
LF
• LF埋弧加热吹氩法是最常用的精炼方法, 能取代电炉还原期,解决了转炉冶炼优钢 问题,具有加热及搅拌功能.
• 电炉EBT出钢,出钢过程加合金,加渣料 (石灰和萤石2%),底吹氩,通电升温,化 渣,10分钟取样分析加渣料1%,测温取样, 加合金看脱氧,准备出钢,一般30-50分钟, 电耗50-80kwh/t,是现代转炉,电炉与连 铸联系的纽带
RH真空工艺过程
• 出钢后,钢包测温取样; • 下降真空室,插入深度为
150-200mm; • 起动真空泵,一根插入管
输入驱动气体; • 当真空室的压力降到26-
10kpa后,循环加剧; • 钢水上升速度为5m/s、
下降速度为1-2m/s; • 气泡在钢液中将气体及夹
杂带出。
VD工艺
• VD(真空馆内钢包脱氧)以轴承钢为例. • 轴承钢最重要的性能指标是疲劳寿命。 • 影响轴承钢寿命的重要指标是钢中氧含量,钢中
RH工艺参数
• 处理容量:大炉子比小炉子好(50t以上); • 处理时间:钢包在真空位的停留时间τ;
τ=Tc/Vt Tc允许温降, Vt平均温降℃/min; • 循环因数:C=ω(t/min).t(min)/Q (ton) ω 循环流量、 t脱气时间、 Q处理容量 • 循环流量ω:主要由上升管与驱动气体流量决定; • 真空度:60-100pa; • 抽气能力。
VD工艺
• 真空保持时间:真空启动后,工作压力达到67 Pa时,保持时间≥15min。
• 真空保持期间调整氩气流量 70NL/min左右,并 通过观察孔观察钢水沸腾情况,及时调整,保持 均匀沸腾。
• 终脱氧后解除真空、开盖、测温,软吹15- 25min,氩气流量 70-100NL/min左右,控制 渣面微动为宜。
LF 的工艺有点
VOD
• VOD(真空吹氧脱碳)主要用于不锈钢冶炼 • 1.初炼炉将碳控制在0.2-0.5%,P<0.03% 以下钢液温度为
1630. • 2.初炉除渣后,将VOD包吊如真空室,接底 吹氩,开始抽真
空,此时温度为1550- 1580之间. • 3.当真空度达到13-20kpa时,开始吹氧脱 碳. • 4.碳含量降低的同时,提高真空度保铬不 氧化. • 5.当碳合格时,停止吹氧,加大真空到 100pa以下,并加大搅
炉外精炼
炉外精炼的六种方法
➢一 合成渣精炼 ➢二 钢包吹氩精炼 ➢三 真空脱气 ➢四 带有加热装置的钢包精炼 ➢五 不锈钢精炼 ➢六 喷煤及特殊添加精炼
一.合成渣精炼
CAS封闭式吹氩微调
工艺优点: • 钢液升温和精确控制钢水温度 • 促进夹杂物上浮,提高钢水纯净度 • 精确控制钢液成分,实现窄成分控制 • 均匀钢水成分和温度 • 与喂线配合,可进行夹杂物的变性处理 • 冶炼节奏快,适合转炉的冶炼节奏。
CAS工艺操作过程
RH钢液循环脱气法
• 主要冶炼高质量产品,如轴承钢、LF钢、硅钢、 不锈钢、齿轮钢等。
• 特点:①反应速度快,表观脱碳速度常数kC可达
到3.5min-1。处理周期短,生产效率高,常与转 炉配套使用。②反应效率高,钢水直接在真空室 内进行反应,可生产H≤0.5×10-6,N≤25×10-6, C≤10×10-6的超纯净钢。③可进行吹氧脱碳和二 次燃烧进行热补偿,减少处理温降;④可进行喷粉 脱硫,生产[S]≤5×10-6的超低硫钢。
拌,进一步脱碳, 钢液温度达到1670-1750之间. • 6.加合金,微调成分,加铝吹氩搅拌几分 后,破真空浇铸.
AOD炉
AOD炉 主要是冶炼高质量的不锈 钢(C<20ppm,S,P<50ppm)使用更廉 价的原料(采用高碳铬代替低碳铬) 60%-70%的不锈钢产量 炉料:废钢,不锈钢返回料,高碳铬 铁,高碳镍铁 吹炼过程就是温度及氩氧比的控制 T=1680 O2:Ar=4:1(3:1)C下降为0.2% T=1700 O2:Ar=2;1 C下降为0.1% T=1730 O2:Ar=1;2 C下降为0.02% T=1750 O2:Ar=1:3 C下降为0.001%
[O]控制在10ppm为好。 最好水平[O] =3-5ppm。国内10ppm左右。 • 控制钢中非金属夹杂物和碳化物级别。 • GCr15是最常用轴承钢: %C:0.95-1.05 %Mn: 0.9-1.20 %Si:0.40-0.65 %Cr: 1.30-1.65 S,P<0.020
VD工艺
冶炼工艺:UHP+LF+VD(或RH)+CC: • LF出钢后,扒渣(倒渣)2/3,渣层厚度应保持
喷吹工艺
40-70mm,扒渣时间<3min。 • 扒渣完毕LF钢包入VD处理工位,接通氩气,调
节流量50-80NL/min,同时测温、取样,加入 硅石2 kg/mm,调整炉渣碱度R=1 .2-1 .5。 • 测温、取样后VD加盖密封,抽真空。 • 真空泵启动期间,调整氩气流量保持30 - 40NL/min。