冷挤压模结构设计
6.1冷挤压模具设计
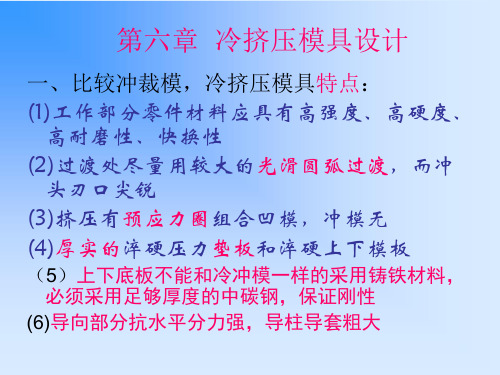
二、反挤压凸模高度确定
• 反挤纯铝时 l/d≤7-10 • 反挤紫铜时l/ d≤5—6; • 反挤黄铜时l/ d≤4—5; • 反挤低碳钢时l /d≤2.5—3 • 可用临界压杆 条件校核计算
三、反偏心方法、卸料方法
• 图12-26咬 住不变形区 减小失稳, 壁厚均匀; 图12-17工 作部分细长 过渡部分加 粗,加工卸 料槽;气孔 • 知识点:卸 料槽使用
六、反挤凸模与凹模制造尺寸与公差: 公差居中原则即入体原则
• 1.保证外径时图a
• 2.保证内径时图b
• Δ可选0.75、0.9系数 • 公差可选IT7-9级
例题1确定挤压凹模尺寸公差
• 原则:入体原则模具尺寸浮动 范围必须在挤压件尺寸公差允 许范围内 0.04 • 书本A100=(100-0.2) = 0 • 99.8 0.04 0 • 一般=(100-0.75*0.2) 1/ 4*0.2 0.05 0 • =99.85 0 • 简便=理想尺寸H7级公差 • =99.9 0.035 0 • 提问:如果挤压件是 φ100±0.2挤压凹模尺寸公差 如何? φ100±0.2= φ100.20-0.4表达不同而已 • 知识点:公差转化方法
0 +0.055
• 一般=(100-0.75*0.22)0+IT7=99.8350+0.035 • 简便=理想尺寸H7级公差=99.890+0.035 • 判断:三种算法的区别?哪个更合理?余量及胀 形影响
(三)反挤压顶杆设计 图6-18
• 设计要点: • 支承部分的直 径应放大, • 大R或斜锥过渡, 间隙0.1mm ,
0.3
0 解:书本T70=(70+0.18)0.036
例3如果是正挤压杆部直径φ100如何设 计正挤凹模工作带尺寸与公差?
冷挤压工艺分析及变薄拉深模具设计

Fig.8 Force-displacement graph of fluidic muscle
6 结语
气动肌腱作为一种新型的驱动器,由于其初拉 力大、利用进气压力可以精确控制其行程、结构简 单、尺寸小、重量轻的特点,从而在出力大行程小 的应用场合具有普通气缸所不可比拟的优越性。本 文中基于一根气动肌腱和斜楔与双铰链连杆机构组 合所提出的设计方法是一种传动简单、结构紧凑、 噪音小、增力比大且易于实现的小型压力机或台式 冲压机的新型设计思路,为进行挤压或锻造等工艺 的小型锻压设备的设计提供了一种新的驱动方式。
变形条件,挤压前对坯料进行磷化皂化,提供足够 的韧性,能经受重压而不致破坏的润滑层,以降低 工具载荷,减小磨损,延长模具寿命。同样,在变
万方数据
薄拉深之前也要进行磷化皂化处理。为了提高材料 的塑性,降低其硬度和变形抗力,以及消除冷作硬 化和内应力,原材料以及挤压后的工件都要进行软 化处理。热处理规范为:800℃保温6 h,随炉冷却 到350℃,处理后的硬度为110---125 HBS。由于变 薄拉深后工件的残余应力很大,拉深完成后也要进 行低温回火处理以消除之。
第32卷第3期 V01.32 No.3
锻 尼技 #
FORGING&STAMPING TECHNOLOGY
2007年6月 Jull. 2007
深杯形件冷挤压工艺分析及变薄拉深模具设计*
任国成h+。王广春2。徐淑波2。蔡元兴1 (1.山东建筑大学材料学院,山东济南250014;2.山东大学材料学院,山东济南250061)
考虑坯料制造误差和压力机行程下止点控制的 误差,在长度上加修整量4.5 mm。按零件图求得坯 料体积Vo-=401.43 mm3,坯料外径取do一9.5 mm, 以利于坯料在凹模模腔内定位。则毛坯高度为:
球头销冷挤压工艺及模具设计

球头销冷挤压工艺及模具设计万亚飞;吴淑芳【摘要】球头销是汽车中的重要零件之一,在工作过程中受力情况非常复杂,对其成形过程进行研究,寻求更加合理的成形方案,对提高球头销的质量有重要的意义.针对某载重汽车球头销的结构特点,结合球头销冷挤压成形工艺,为了进一步减小变形抗力、提高挤压件质量,在传统的两工步成形的基础上,提出了三工步冷挤压成形的工艺方案.设计了球头销尾部、锥体、球头的冷挤压模具,并运用大型有限元模拟软件DEFORM对球头销成形过程进行数值模拟,得到了模具填充情况、等效应力应变、载荷—行程曲线.模拟结果表明,该工艺方案的变形抗力大大减小,成形质量显著提高.【期刊名称】《模具制造》【年(卷),期】2014(014)002【总页数】5页(P52-56)【关键词】球头销;冷挤压;模具设计;数值模拟【作者】万亚飞;吴淑芳【作者单位】长春理工大学机电工程学院吉林长春 130022;长春理工大学机电工程学院吉林长春 130022【正文语种】中文【中图分类】TG3721 引言球头销是汽车转向拉杆联结部分的一个重要零件,在工作过程中,受力情况比较复杂,受拉、压、剪、扭、弯曲和冲击等多种载荷的作用,因此,要求其具有较高的疲劳强度和冲击韧性。
根据球头销种类、尺寸、形状等的不同,生产中常用的加工方法有车削加工、楔横轧、冷挤压等。
在车削加工球头销的过程中浪费了大量金属材料和机加工工时,增加了成本,而且机械性能也不理想。
楔横轧加工球头销对加工设备和模具设计要求较高。
而冷挤压作为一种近净成形的塑性成形技术在球头销的生产中得到了广泛的应用[1]。
冷挤压工艺是根据金属的塑性变形原理,利用装在压力机上的模具,在相当大的压力及一定的速度下,使金属在模腔内产生塑性变形,从而使毛坯变成所需形状、尺寸及一定性能的制件[2]。
冷挤压过程中,金属基本处于三向压应力状态,大大提高了金属的塑性变形能力,使金属在模具型腔内产生稳定的塑性流动,形成所需要的形状和尺寸,达到少无切削的目的。
冷挤压模具设计
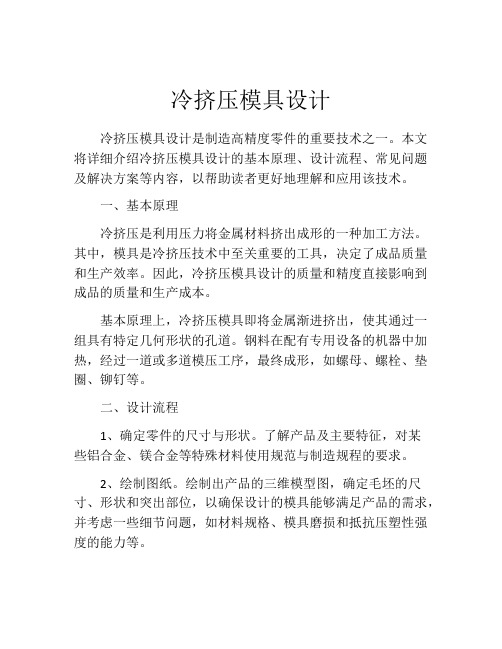
冷挤压模具设计冷挤压模具设计是制造高精度零件的重要技术之一。
本文将详细介绍冷挤压模具设计的基本原理、设计流程、常见问题及解决方案等内容,以帮助读者更好地理解和应用该技术。
一、基本原理冷挤压是利用压力将金属材料挤出成形的一种加工方法。
其中,模具是冷挤压技术中至关重要的工具,决定了成品质量和生产效率。
因此,冷挤压模具设计的质量和精度直接影响到成品的质量和生产成本。
基本原理上,冷挤压模具即将金属渐进挤出,使其通过一组具有特定几何形状的孔道。
钢料在配有专用设备的机器中加热,经过一道或多道模压工序,最终成形,如螺母、螺栓、垫圈、铆钉等。
二、设计流程1、确定零件的尺寸与形状。
了解产品及主要特征,对某些铝合金、镁合金等特殊材料使用规范与制造规程的要求。
2、绘制图纸。
绘制出产品的三维模型图,确定毛坯的尺寸、形状和突出部位,以确保设计的模具能够满足产品的需求,并考虑一些细节问题,如材料规格、模具磨损和抵抗压塑性强度的能力等。
3、确定模具类型。
根据产品的尺寸、形状和工艺要求,确定冷挤压模具的类型。
常用的冷挤压模具包括拉伸模、挤压模、钝化模、套筒模等。
4、设计模具的结构。
设计模具的结构时,需要考虑到模具主体的结构、腔体形状、孔形结构等几个方面,还需要根据压力、预压、挤出量等要素,确定可承受的载荷。
同时,还需要考虑一些实际运用中需要注意的问题,例如设定模具配合公差、调整模具的开合间隙、设定模具的定位和定向等。
5、制作模具样品。
样品制作过程中,需要考虑到模具结构的合理性,以及各种元素的配合度。
制作完成后,需要进行模具的调试、试胶、实验成型等环节,进行逐渐的调整和完善。
三、常见问题及解决方案1、模具寿命不够长。
在设计时应考虑模具的材质和硬度,通过表面热处理、高频淬火、氮化等方式进行强化处理,以延长模具的使用寿命。
2、模具容易出现磨损或变形。
在制作过程中,要合理设定模具的使用寿命,并且需要根据产品的多重要素,优化模具的设计结构,来提高其使用的稳定性。
冷挤压模具的结构分类与设计(

冷挤压模具的结构分类与设计(冷挤压模具是用于制造金属材料中凸台、凹槽、型材等形状的模具。
冷挤压是一种用压力将金属材料挤压成希望得到的形状的加工方法,其工艺和设备相对简单,成本低,可以制造出高强度和高精度的零部件,因此被广泛应用于汽车、航空航天、电子、军工等行业。
冷挤压模具的结构主要包括模具座、模具坯料导向器、模具上下模、模具磨床、模具中心销等几个部分。
模具座是支撑和固定模具的基础,其通常由底板和护板组成。
模具座上部设有导向器,用于引导坯料进入模具。
模具上下模是冷挤压模具的主要部分,通过在模具中心销的作用下上下开合,实现模具内坯料的挤压成型。
模具磨床主要用于修磨模具的工作面,并确保模具上下模的平行度。
模具中心销则是用于固定模具上下模的位置,以确保模具挤压工艺的精度。
1.封闭型模具:模具上下模的结构封闭,适用于对形状和尺寸要求较高的零部件的生产。
封闭型模具具有较高的工艺要求,但可以制造出更高精度的零部件。
2.开放型模具:模具上下模的结构相对开放,适用于要求不太高的形状的零部件的生产。
开放型模具结构相对简单,制造成本低,但精度相对较低。
3.多工位模具:模具上设有多个工作位置,可同时进行多个零件的挤压成型,提高生产效率。
多工位模具通常应用于批量生产的场合。
1.材料选择:模具材料应具有良好的耐磨性、强度和韧性,常见的模具材料有工具钢、硬质合金等。
根据具体的工艺要求,还可以进行表面硬化处理。
2.结构设计:结构设计应根据零件的形状和尺寸来确定。
模具的结构应尽量简单,以便于制造和维护,同时还需要考虑模具的强度和刚度。
3.工作面设计:工作面需要考虑零件的形状和尺寸,工作面的形状应尽量与零件的形状相匹配,以确保成型质量。
4.导向装置:导向装置用于引导坯料进入模具,并确保上下模的相对位置的准确性。
导向装置应结构简单,操作方便。
5.挤压力的确定:挤压力的大小直接影响到成型质量和模具的寿命。
挤压力的确定需要考虑零件的形状和尺寸,以及材料的性能。
冷挤压对模具设计的影响

冷挤压对模具设计的影响为了消除上述两个因素带来的不利影响,将模具方案进行了更改:第1步为冷挤;第2步为整形;第3步为复合落料。
此方案目前已经得到了量产的验证,第1步挤压高度可达5.8~6mm(超过6mm,在凸缘内孔底部上方1mm处出现材料颈缩现象),制件外形光亮带满足要求,模具寿命(由冷挤凸模寿命决定)在每次刃磨后达到15,000次。
1模具结构图2为排样图,图3为模具结构图。
模具工作过程:当导板和凹模框压紧材料后,冷挤凸模首先接触材料。
当冷挤凸模深入材料3.2mm左右,冷挤顶件器12通过反顶缸对冷挤凸模挤出的材料施加反向压应力,使材料在三向受压的状态下一方面继续向下流动,另一方面因为冷挤顶件器的特殊形状,进一步提供原材料的流动空间。
当冷挤顶件器到达下垫板时,冷挤凸模可以继续向下运动,通过减少冷挤凸模和冷挤顶件器之间的材料厚度,来增高挤压高度。
当挤压高度到达5.8mm左右,在冷挤凸模和冷挤顶件器之间的原材料厚度减薄至1.2~1.3mm。
2生产中注意的问题(1)冷挤凸模和冷挤顶件器的形状。
为了便于材料流动,冷挤凸模需制造5°左右的斜度和R,如图4所示。
同样冷挤顶件器需要制造30°左右的斜度和R角,如图5所示。
同时根据制件高度要求制造0.8mm的流动高度。
生产过程中因油压、原材料批次等因素的影响,建议将冷挤顶件器一分为二,在中间增减垫片来调整制件的冷挤高度。
(2)冷挤凸模的材质要求。
因冷挤凸模在成形即将结束的过程中,压应力出现陡增。
为了避免凸模镦粗失效,需要采用钨钢材料,同时热处理硬度在64~66HRC是合适的。
3结束语该类型精冲模结构紧凑,制件质量稳定。
避免了国产材料在局部受拉应力容易产生各类失效的缺陷。
提高了生产效率,也为同类型的制件成形提供了借鉴。
冷挤压对模具设计的影响。
冷挤压成形设计

冷挤压课程作业结构分析:冷挤压件图如下图所示:分析可知,挤压零件结构简单,为典型单向多台阶阶梯轴,并且除55Φ处有较大直径突变外,其余的直径变化均较小,且为倾斜台阶面过渡。
工艺设计:根据零件结构特征,55Φ处台阶需要通过镦粗成形,其余台阶面可采用减径挤压方式,所以采用减径挤压和镦粗相结合的方式,具体选取以下两种方案对比分析:1.镦挤复合,加工出55Φ,27.5Φ圆柱面,减径挤压出30.4Φ。
工步图如下:2.镦粗出55Φ圆柱面,依次减径挤压出30.4Φ,27.5Φ圆柱面。
工步图如下:坯料设计及挤压前处理:坯料设计:1.坯料形状和尺寸:根据零件结构分析采用棒状坯料如图a 所示:0P X V V V =+,取0.04X P V V =由冷挤压件图可知P V =.64813mm ,则0=V .83mm ,取坯料直径为d=36mm 由体积不变原则可得坯料尺寸为36262.1mm Φ⨯。
坯料如下所示:2.坯料制备方法:毛坯直径较大且长,为保证毛坯的尺寸精度及形状精度,采用锯切下料。
材料:20Cr ,(合金结构钢):前处理如下:1.软化处理:球化退火(加热到860°C ,保温14h ,随炉冷至300°C 后空冷)2.表面处理:磷化处理(具体过程为化学去油(85℃)→流动冷水洗→酸洗去锈(65~75℃)→流动冷水洗→热水洗→磷化处理(85~95℃)→流动冷水洗→中和处理。
)3.润滑处理:皂化处理(工业皂片)成形力计算及设备选择:对于实心圆柱件,断面减缩率0`101000000100100A A A D D A D ε--=*=*,式中,A0为挤压变形前毛坯的横断面积,A1为挤压变形后工件的横断面积,D0为挤压变形前毛坯的横断直径,D1为挤压变形后工件的横断直径,根据图算法求得单位挤压力P ,代入公式F=P*A0(()2002A D π=∙)求得减径挤压的挤压力如下表所示。
D0/mm D1/mm 断面减缩率 单位挤压力p/MPa 挤压力/kN 36 30.4 28.7% 620 631.1 36 27.5 41.6% 800 812.9 30.427.518.2%430304.9冷镦力计算根据零件尺寸计算D=55.5,H=75mm ,A=2419 2mm ;则冷镦力F=2482.1kN3.总成形吨位为F=1.3*(631.1+304.9|+2482.1)=3418.14.由计算选择400吨的机械压力机模具结构设计:模具材料选用硬质合金钢,冷挤压单位压力小于1100MPa,采用整体式凸模、两层组合式凹模形式。
冷挤压工艺及模具设计课件

对修复后的模具进行全面检测 和调试,确保其性能达到要求 。
05
冷挤压工艺与模具 设计的未来发展
新材料的应用
高强度轻质材料
随着新材料技术的不断发展,高强度轻质材料如钛合金、铝合金等在冷挤压工 艺中的应用将更加广泛,能够满足产品轻量化、高性能的要求。
复合材料
复合材料的出现为冷挤压工艺提供了更多的可能性,通过将不同材料组合在一 起,可以实现单一材料无法达到的性能,提高产品性能和降低成本。
合理布局
根据产品特点和工艺要求,合 理布置模具结构,确保产品成
型和出模顺利。
优化流道设计
优化模具流道设计,减少流动 阻力,降低成型难度和压力。
增强刚性和稳定性
为确保模具在使用过程中不易 变形和损坏,应加强模具的刚 性和稳定性设计。
易于维修和更换
模具结构应便于维修和更换损 坏或磨损的部件,降低维护成
本。
冷挤压特点
冷挤压工艺具有高效率、高精度、低 成本等优点,能够加工出形状复杂、 精度要求高的零件,广泛应用于汽车 、家电、电子、航空航天等领域。
冷挤压的应用范围
汽车零件制造
家用电器制造
冷挤压工艺可以用于制造汽车发动机、底 盘、电气系统等零部件,如活塞、连杆、 气瓶等。
家用电器中的金属零部件,如空调压缩机 、冰箱压缩机、洗衣机电机等,也广泛采 用冷挤压工艺制造。
模具的制造工艺
选择合适的加工方法
根据模具材料和结构特点,选择合适的加工方法,确保模具精度 和表面质量。
控制加工参数
合理控制加工参数,如切削速度、进给量等,以提高加工效率和模 具质量。
热处理和表面处理
根据需要,对模具进行热处理和表面处理,提高其硬度和耐久性。
03
第 6章 冷挤压工艺与模具 设计
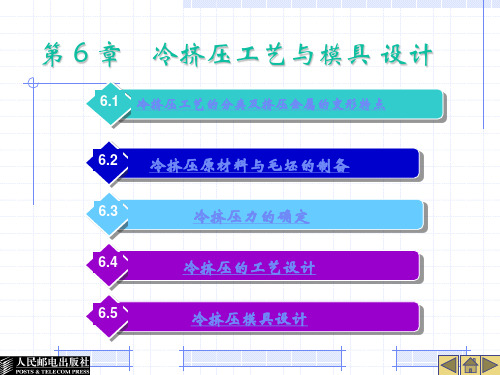
4)最好有超载保险装置。
5)最好在压力机上备有顶出装置。
P 850 MPa
⑶ 考虑到 h0 / d 0 1.5, 90 0 上述单位挤压力需要修 正,因此可根据图③中相应的曲线,查得修正的单位挤 压力:
P 1050 MPa
⑷根据毛坯直径 d 0 和修正的单位压力 p 从图④中查得总 挤压力:
P 4500 MPa
6.3.4冷挤压力机的选用
图6.4.3 断面的合理过渡
图6.4.4 锥形件的冷挤压
图6.4.5 实心阶梯形件
图6.4.6 空心阶梯形件
图6.4.7 挤压缩孔
图6.4.8 阶梯轴的冷锻 a)一次正挤 b)正挤——镦头
图6.4.9 有阶梯内孔件的挤压工序
图6.4.10 深孔薄壁件的挤压工序 图6.4.12 双向挤压深孔件
图6.4.11 无底筒形件的挤压工序
图6.4.13 考虑成品局部形状的半成品设计(挤压“山”形件) a)毛坯 b)半成品 c)成品
图6.4.14 冷挤压花键齿形截面图
图6.4.15 挤压凹模的轮廓形状
6.5 冷挤压模具设计
6.5.1、典型的冷挤压模具
正挤压模具(如图6.5.1) 反挤压模具(如图6.5.2)
3)挤压件可达精度和表面粗糙度 它有一定限度。增加修 整工序可提高挤压件精度。 4)挤压件的材料 材料影响挤压难度、许用变形程度。 5)挤压件费用 一般包含材料费、备料费、工具及模具制 造费、冷挤压加工费及后续工序加工费等。这是一项综合 指标,往往是决定工艺方案是否合理、可行的关键因素。 6)挤压件的批量 批量大时可以使总的成本降低。
390 JH70摩托车主轴坯冷镦成形模具设计

题目:JH70 摩托车主轴坯冷镦成形模具设计目 录摘要 (Ⅰ)Abstract (Ⅱ)1.绪论 (1)1.1概述 (1)1.2冷挤压技术的分类及简介 (1)1.3冷挤压技术的特点 (2)1.3.1冷挤压的优点 (2)1.3.1冷挤压的缺点 (3)1.4冷挤压技术现状及发展方向 (4)1.5本课题要求 (5)1.6预期目标及效果 (5)2.冷挤压零件 (6)2.1零件基本尺寸及三维模型 (6)2.2毛坯零件的选择及其性能指标 (7)2.3零件加工前准备 (8)2.4毛坯变形程度 (9)3.冷挤压模具设计 (11)3.1冷挤压模架整体结构设计 (11)3.2 模具主要零部件的设计 (13)3.2.1上模板的设计 (13)3.2.2上模座的设计 (14)3.2.3垫板的设计 (15)3.2.4下模座的设计 (15)3.2.5下模预应力圈的设计 (16)3.2.6下模板的设计 (17)3.2.7模圈导向套的设计 (18)4.组合凹模设计 (19)4.1组合凹模结构形式的确定 (20)4.2组合凹模各圈直径的确定 (20)4.3组合凹模径向过盈量及轴向压合量的确定 (21)5.模具及其零部件的三维建模 (23)5.1冷镦模具装配体三维模型 (23)5.2非标准零部件三维模型 (24)6.总结 (30)7.致谢 (31)参考文献 (32)摘要本文主要针对 JH70 摩托车主轴坯冷镦成形模具的设计。
本课题研究的核心 问题是冷挤压组合凹模的设计。
通过被加工零件的尺寸以及变形程度确定冷挤压 的单位挤压力,从而确定冷挤压组合凹模的结构形式以及各圈直径,最后确定组 合凹模的径向过盈量以及轴向压合量。
再通过组合凹模的尺寸、形状确定冷镦模 架其它零部件的形状及尺寸,从而最终确定整个模架结构、尺寸以及组合形式等 要素。
通过查阅设计手册确定各个模架零部件的材料。
本模具采用模口导向的形 式保证在上、下模合模过程中的同轴度。
本文还对整个冷挤压模具进行了三维建 模,以便直观的表达冷挤压模具零部件的外形以及零件之间装配关系,方便读者 对整个模具的工作原理及过程有一个清晰的了解。
煤粉机用辊套嵌板挤压模毕业设计

摘要冷挤压是精密塑性体积成型技术中的一个重要组成部分。
冷挤压是指在冷态下将金属毛坯放入模具模腔内,在强大的压力下和一定的速度作用下,迫使金属从模具中挤出,从而获得所需的形状、尺寸以及具有一定力学性能的挤压件。
显然,冷挤压加工是靠模具来控制金属流动,考金属体积的大量转移来形成零件的。
本设计介绍了30万辊套网格零件结构分析、挤压工艺过程、挤压设备选择、模具结构的设计、凹凸模设计、挤压件质量分析、30万辊套网格模芯的结构、凸模加工工艺及模具各部件造型进行论述。
与常规的辊套网格加工工艺相比,冷挤压成型的辊套网格具有强度高、网格尺寸精度高、表面耐磨度高、材料利用率高、生产效率高、设备投资少等优势。
关键词:冷挤压;辊套网格;正挤压;凸缘AbstractCold extrusion molding technology precise plastic volume is one of the important component. Cold extrusion is to point to in the cold metal blank in the mold cavity inside, in strong pressure and a certain speed function, forced out of metal from a mold, and obtain the shape, size and has some mechanical properties of extrusion parts. Obviously, cold extrusion processing is to rely on the mold to control the flow, take an examination of a large volume of metal parts of the transfer to form. This paper introduced the design of roller set of grid structure parts, extrusion process analysis process, extrusion equipment selection, die structure design, mold design, extrusion bump a quality analysis, 300000 roller set of grid punch structure, the punch processing technology and die parts modelling is described. And the conventional roller set of grid than processing technology, cold extrusion of roller set of grid has high strength, mesh size high precision, high degree of exterior wear-resisting, material utilization high, high production efficiency, equipment less investment and other advantages.Keywords: Cold extrusion,Roller set of grid,Are squeezing,flange目录摘要 (I)Abstract ......................................................................................................................................................... I I 目录. (I)1、冷挤压的概述 (1)1.1冷挤压的概念 (1)1.1.1冷挤压加工的特点 (1)1.1.2冷挤压模具的基本结构 (1)1.1.3冷挤压模具分类 (2)2、工艺分析及模具结构设计 (2)2.1制件的工艺性分析及工艺计算 (2)2.1.1工艺分析 (2)3、模具总体设计及主要部件设计 (2)3.1径向尺寸算法 (2)3.2模板尺寸的确定 (4)3.2.1择模板材料 (4)3.2.2确定模板尺寸 (5)3.2.3挤压凸模与凸凹模结构尺寸确定 (5)3.3凸模刚度(细长杆失稳)校核 (6)3.4模具总体结构设计 (6)3.4.1送料定位机构设计 (7)3.4.2压块的卸除 (7)3.4.3模具主要零件的一般要求 (7)4、压力机的规格 (7)5、模具结构细节 (8)5.1设计构思 (8)5.2螺钉的安装 (8)5.3干涉检验 (8)6、模具装配图 (8)致谢 (10)参考文献 (11)1、冷挤压概述1.1冷挤压的概念1.1.1冷挤压加工的特点冷挤压就是把金属毛坯放在冷挤压模腔中,在室温下,通过压力机上固定的凸模向毛坯施加压力,使金属毛坯产生塑性变形而制得零件的加工方法。
冷冲压模具及结构.ppt

亚 奇 拉 科 技 (苏州) 有 限 公 司
四、冷冲压的模具类型
1.单工程模
在冲压的一次行程过程中,只能完成一个冲压工序 的模具。
单工程模-适合冲制外形尺寸较大,形状简单、复杂(复杂 的工件可分多套模具)的工件。
2020/3/25
冲压模具
17
亚 奇 拉 科 技 (苏州) 有 限 公 司
四、冷冲压的模具类型
三、冷冲压的基本工序
1.分离工序
指冲压过程中使冲压件与板料沿一定的轮廓 相互分离的工序。
2020/3/25
冲压模具
10
亚 奇 拉 科 技 (苏州) 有 限 公 司
三、冷冲压的基本工序
1.分离工序
分离基本工艺:冲孔、落料、切断、切口、切边、剖切、整 修等。
冲孔、落料
冲孔、剖切
2020/3/25
冲压模具
2020/3/25
冲压模具
7
亚 奇 拉 科 技 (苏州) 有 限 公 司
二、冷冲压模具的发展与应用
2.冷冲压模具的发展:
随着工业产品质量的不断提高,冲压产品生产正呈现多 品种、少批量,复杂、大型、精密,更新换代速度快的变化 特点,冲压模具正向高效、精密、长寿命、大型化方向发展。 为适应市场变化,随着计算机技术和制造技术的迅速发展, 冲压模具设计与制造技术正由手工、依靠人工经验和常规机 械加工技术向以计算机辅助设计(CAD)、数控切削加工、 数控电加工为核心的计算机辅助设计与制造(CAD/CAM) 技术转变
2020/3/25
冲压模具
5
亚 奇 拉 科 技 (苏州) 有 限 公 司
一、冷冲压的概念 4.冷冲压的特性:
1.冲压生产率高和 材料利用率高;
2.生产的制件精度 高、复杂程度高、 一致性高;
冷挤压 模具结构 分类 工艺 -回复

冷挤压模具结构分类工艺-回复冷挤压是一种常用的金属加工工艺,广泛应用于汽车、电子、航空航天等领域。
在冷挤压过程中,金属材料经过模具受到压力作用,从而形成所需的形状和尺寸。
模具的结构和分类对于冷挤压的工艺和成品质量起着至关重要的作用。
本文将一步一步回答关于冷挤压模具结构分类和工艺的问题。
一、冷挤压模具的结构冷挤压模具主要由模具坯料、模具座、模具芯和导向装置等组成。
1. 模具坯料:模具坯料是冷挤压模具的主体部分,通常使用的是高强度合金钢材料。
根据冷挤压的应用领域和具体要求,可以选择不同材质的模具坯料。
2. 模具座:模具座是支撑模具坯料的基础结构,具有足够的刚性和稳定性。
模具座通常由钢板焊接而成,并通过螺栓或焊接与装备机床的工作台连接。
3. 模具芯:模具芯是模具的主要成型部分,它可直接影响到成品的形状和尺寸精度。
模具芯通常采用等离子喷涂或硬质合金喷涂材料进行表面处理,以提高其硬度和耐磨性。
4. 导向装置:导向装置用于指导金属材料在冷挤压过程中的运动轨迹,防止金属材料偏离所需的成型轨迹。
常用的导向装置包括滑移导向和滚动导向等。
二、冷挤压模具的分类冷挤压模具可根据不同的分类标准进行划分,常见的分类方式有以下几种:1. 按形状和结构特点划分:按照成品的形状和结构特点,冷挤压模具可以分为直压型、弯曲型、挤压型和复杂型等。
直压型模具主要用于轴类零件的冷挤压成形,弯曲型模具适用于冷挤压成形曲面较多的零件,挤压型模具常用于制造大型、薄壁、空腔或横截面形状复杂的零件,而复杂型模具则适用于形状和结构较为复杂的零件。
2. 按工艺和生产方式划分:按照冷挤压的工艺和生产方式,冷挤压模具可分为单工位模具、多工位模具、连续冷挤压模具和摇臂冷挤压模具等。
单工位模具适用于小批量生产,多工位模具适用于大批量生产,连续冷挤压模具适用于连续生产线上的大批量生产,摇臂冷挤压模具适用于生产复杂形状的零件。
3. 按应用行业划分:按照冷挤压模具的应用行业,可分为汽车冷挤压模具、电子冷挤压模具、航空航天冷挤压模具等。
铰链管冷挤压工艺及模具设计

冷挤压模具设计
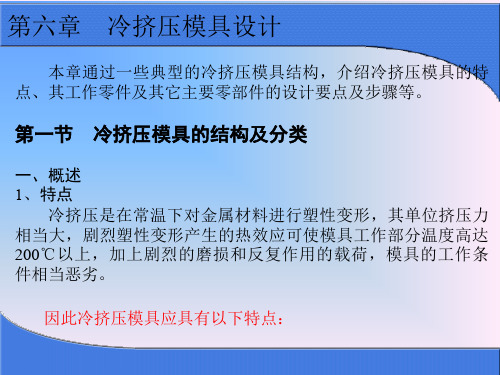
(6)模具工作部分与上下模板之间要设置淬硬压力垫板,以扩大承压 面积,减小上下模板的单位压力,防止压坏上下模板;
(7)上下模板应有足够的厚度,以保证模板具有较高的强度和刚度。
第六章 冷挤压模具设计
2、组成 典型的冷挤压模具由以下几部分组成: 1) 工作部分:如凸模、凹模、顶出杆等; 2) 传力部分:如上、下压力垫板; 3) 顶出部分:如顶杆、反拉杆、顶板等; 4) 卸料部分:如卸料板、卸料环、拉杆、弹簧等; 5) 导向部分:如导柱,导套、模口、导筒等; 6) 紧固部分:如上、下模板、凸模固定圈、固定板、压板、模柄、 螺钉等。
第六章 冷挤压模具设计
二、冷挤压模具分类
冷挤压模具有多种结构形式,可根据冷挤压件的形状、尺寸 精度及材料来选择合适的模具结构形式。 (一) 按工艺性质分类
正挤压模:
反挤压模:
复合挤压模:
镦挤压模:
第六章 冷挤压模具设计
1、正挤压模
图6-1为实心 件正挤压模。
第六章 冷挤压模具设计
图6-2为空心件正挤压模(坯料为黑色金属)。
图e为浮动式凸模,其在芯棒上部放一弹簧,在挤压中芯棒受拉,弹簧被压缩, 可以克服更大的拉力,能有效地防止芯棒拉断。这种凸模可以用于材料硬度和摩 擦力比较大的黑色金属挤压。
为了防止芯棒拉断及卸料方便,芯棒一般做出10’~30’的斜度。
第六章 冷挤压模具设计
2、正挤压凸模尺寸参数设计 凸模各部分尺寸参数见表6-1。
第六章 冷挤压模具设计
第二节 模具工作部分的设计
冷挤压模具工作部分是指凸模、凹模、顶杆等在挤压时直接 参与挤压过程的一些零件。 一、正挤压模具工作部分零件设计 (一) 正挤压凸模
冷挤压模具设计及其成形过程毕业论文

目录目录 (1)冷挤压模具设计及其成形过程 (3)第一章绪论 (3)1.1冷挤压成形技术发展概况 (4)1.2选题依据和设计主要内容 (6)1.2.1毕业设计(论文)的内容 (6)1.2.2 毕业设计(论文)的要求 (6)第二章冷挤压工艺设计 (7)2.1挤压工艺步骤 (7)2.2工艺设计步骤 (9)2.2.1计算毛坯的体积 (9)2.2.2确定坯料尺寸 (10)2.2.3计算冷挤压变形程度 (11)2.2.4确定挤压件的基本数据 (13)2.2.5确定挤压次数 (13)2.2.6工序设计 (13)2.2.7工艺方案确定 (19)2.2.8各主要工序工作特点进一步分析 (21)第三章压力设备选择 (24)3.1各主要工序所需镦挤力 (24)3.2主要设备选用 (25)第四章模具设计 (26)4.1冷挤压模具设计要求 (27)4.2凸模设计依据 (28)4.3冷挤压组合凹模设计依据 (29)4.4凸模设计 (34)4.4.1镦平凸模设计 (34)4.4.2凹模设计 (36)4.5预成形模具设计 (37)4.5.1预成形凸模设计 (38)4.5.2预成形凹模设计 (39)4.6终成形模具设计 (41)4.6.1终成形凸模设计 (41)4.6.2终成形凹模设计 (42)4.7冷挤压模架设计 (43)4.7.1冷挤压模架设计的基本原则 (43)4.7.2模架的设计 (44)4.7.3其它零件设计 (46)第五章挤压模具零件加工工艺的编制 (51)5.1加工工艺编制原则 (51)5.2加工工艺的编制 (51)第六章总结及课题展望 (54)6.1本文工作总结 (54)6.2课题展望 (54)参考文献 (55)谢辞 (56)附录一:英文科技文献翻译 (57)英文翻译: (62)附录二毕业设计任务书 (66)冷挤压模具设计及其成形过程机械与电气工程学院机械设计制造及其自动化专业06城建机械乔红娇指导老师雷声第一章绪论挤压就是零件金属毛坯放在挤压模腔中,在一定温度下,通过压力机上固定的凸模或凹模向毛坯施加压力,使金属毛坯产生塑性变形而制得零件的加工方法。
- 1、下载文档前请自行甄别文档内容的完整性,平台不提供额外的编辑、内容补充、找答案等附加服务。
- 2、"仅部分预览"的文档,不可在线预览部分如存在完整性等问题,可反馈申请退款(可完整预览的文档不适用该条件!)。
- 3、如文档侵犯您的权益,请联系客服反馈,我们会尽快为您处理(人工客服工作时间:9:00-18:30)。
冷挤压模结构设计(一)
上下模板是冷挤压压力的主要支承部分,由于冷挤压的单位压力较高,上下模板不能采用铸铁材料。
上下模板加导柱、导套就组成有导向的冷挤压模架,无导柱、导套者则为无导向模架
图1为在导柱、导套导向通用反挤压模具。
卸年亦有导向,其导向的基准仍为模架的导柱。
反挤压时挤压件的端面往往是不平的,缺件时使凸模受力不均匀,可能造成凸模偏移而折断。
缺件有强有力的导向时,提高了凸模的稳定性,这是因为卸件板与凸划亦有导向的缘故。
反挤压适用模架兼作为下挤压及复合挤压使用。
图2为有导柱导套导向正挤压通用模具。
图3为镦挤复合模具。
通用反挤、正挤和镦挤复合模架中的组合凹模在相同吨位的压力机上都设计成可以互换的,提高了模具的使用范围。
模架精度可分为三级,其技术指标见表1,用于不同挤压件选用,常用的为Ⅱ级。
卸件板与顶件杆:挤压有时粘在凸模上,有时粘在凹模中,有此部件,能将打主挤压件取出。
卸件板与顶件杆都是用于制件脱模的零件。
凸模与凹模垫板:通用冷挤压模具中,采用了多层垫板。
为了防止高的挤压单位压力直接传递给模板而造成局部凹陷或变形,必须在凹模底端加上垫板,以便把加工压力均匀分散传递,起到缓冲作用。
凸模固定器及定位环:凸模固定器是将凸模安装在上模上,而定位环则可考虑挤压件的不同直径快速交换,提高了模具的通用性能。
凸模与凹模:冷挤压模具的工作部件,在设计时必须认真对待。
应选用具一定韧性的高强度钢材制造。
凸模与凹模承受了最大的冷挤压单位压力。
为了加强凹模的强度,通常采用预应力组合凹模,可以用二层或三层组合而成。
表1
图1
图2
图3
在冷挤压模具中,凸模是最关键的零件之一。
凸模在冷挤压过程中,承受的单位挤压力最大,极易磨损与破坏。
为此凸模的设计和加工就显得特别重要。
1.反挤压凸模
图1是用于黑色金属冷挤压的几种凸模。
A、b两种凸模效果较好,在生产中尽量使用。
C的平端面工作部分的凸模,由于冷挤压件需要平的底部,在生产中也常用,但单位挤压力比锥形带平底的凸模约高20%。
无平台的锥形凸模α一般为5°~9°,也有用到27°的。
但不要超过27°。
角α过大,会因为毛坯端面不平面导致杯形件的壁厚差过大,使凸模受到很大的侧向力,在挤压过程中折断。
反挤压凸模工作高度及凸模后隙直径见公式1。
图2为纯铝等有色金属反挤压凸模工作部分的几种型式。
其设计原则与上述基本一致。
纯铝的塑性较好,强度较低,其反挤压杯压形件往往是薄壁深孔件,应尽可能减小凸模工作带的高度。
一般取g=0.5~1.5mm。
角
α=12°~25°。
有色金属反挤压凸模工作带高度一般是均匀的,如果在挤压变形不均的杯形件时,凸模工作带的高度在变形程度大的部位和变形阻力较大的部位,应适当减小凸模工作带的高度,即制造成不等的凸模工作带。
对于纯铝的反挤压细长凸模,为了增加其纵向稳定性,可以在工作端面上作出工艺凹槽(图3)。
凸模借工艺凹槽在开始挤压的瞬间将毛坯'咬住'而提高其稳定性。
凹槽的形状须对称于凸模中心,保持良好的同心度,否则反而会在挤压时发生偏移,造成凸模折断。
工艺凹槽的槽宽一般取0.3~0.8mm,深0.3~0.6mm。
工艺凹槽顶部应用小圆弧光滑相连。
2.正挤压凸模
在黑色金属冷挤压中,反挤压凸模的长径比一般较小,而正挤压的凸模长径比就往往较大。
为了不使凸模纵向失稳,有进还需加上凸模保护套。
图4是正挤压所用凸模的几种型式。
实心凸模可按型式a设计,在各台阶
相接处应用光滑弧连接,不允许有加工刀痕存在。
对于正挤压纯铝空心件的凸模,可采用型式b设计,凸模与芯轴制作成整体。
挤压黑色金属空心件,整体式凸模就不宜采用,在凸模本体与芯轴的直径急剧过渡区就很易断裂。
应当采用型式c与型式d的组合式,使凸模本体与芯轴组合而成。
组合芯轴分固定式c与活动式d。
固定用于芯轴直径较大,而活动式用于芯轴直径较小的环形件。
活动芯轴可随变形金属同时向下滑动一锻距离,从而改善了芯轴的受拉情况,防止芯轴被拉断。
图5为下挤压凸模顶端形状的又一种型式。
此型式有下列特点:
(1)端面有0.5°~1°斜角,其作用是保证凸模的稳定性。
特别是毛坯二端不平时尤为重要。
(2)同凹模配合的有效长度为3~5mm,而不是全直筒式的。
凸模在高的单位挤压力作用下,有时会使凸模直径胀大,增加了凸模下移的阻力。
仅有3~5mm有效长度,就能确保凸模的使用精度。
(3)后角3°的存在,采用小圆弧相联,具有较低的应力集中系数,保证凸模具有较高的寿命。
为此,这种型式的凸模亦广为采用。
公式1
图1
图2
图3
图4
图5
1.反挤压凹模
图1是常见的反挤压凹模结构型式。
A、b、c、d四种凹模主要用于不需要顶出装置的挤压件。
反挤压有色金属薄壁件可以采用这些型式凹模。
整体凹模结构筒单,制造方便,但在R转角处极易开裂,故不常用。
为防止整体凹模在底部R转角处因应力集中而开裂,对凹模采用横向分割型式d型及纵向佞割型(如c、e型)。
反挤压凹模的模膛深度:见公式1。
2.正挤压凹模
图2为几种常见的正挤压凹模的结构,型式a为整体结构,凹模容易发生横向开裂。
其余的凹模型式为横向分割型和纵向分割型。
图3为一般的正挤压凹模结构。
凹模入口角:α=90°~120°
工作带高:
g=1.0~3.0mm,有色金属。
g=2.0~4.0mm,黑色金属。
后隙:b=0.05~0.1mm
凹模模膛深度:见公式2。
凹模工作带以下高度:0.7倍的模膛直径。
带矫正的正挤压凹模结构见图4。
多台阶的正挤压凹模结构见图5。
公式1。