化工企业生产装置泄漏
融汇化工“8·29”氯气泄漏事故调查报告(摘登)

案例分析•矣会•吨2021年第4期融汇化工“8 *29”氯气泄漏事故调查报告(摘登)2020年8月29日17时28分许,位于安徽省芜湖市鸠江区境内的芜湖融汇化工有限公司(以下简称“融汇化工”)液氯工段在对液氯槽车充装液氯过程中,发生氯气泄漏,造成19人 中毒,直接经济损失48万元。
1事故企业及相关情况1.1 事故企业基本情况融汇化工是香港融汇集团属下成员企业之一,于2003年11月由芜湖山江化学有限公司重组改制后成立的一家氯碱化工企业。
企业类型为有限责任公司。
企业注册资本3.5亿元人民币,总资产14亿人民币。
公司位于安徽省芜湖市长江北路243号,占地面积46.7万m2。
经营 范围:17万t/a烧碱(离子膜法),9万t/a液氯 (氟机冷却液下泵罐装法),7万t/a盐酸(合成 法),32000t/a次氯酸钠,4000t/a氯甲基甲醚(甲醛法),7万t/a氯乙烯(电石法),4万t/a三 氯乙烯,4万t/a四氯乙烷,1200t/a四氯乙烯,1.092万t/a盐酸等生产工艺系统(安全生产许可证有效期至2023年7月25日);氯化聚乙烯、聚氯乙烯生产和销售;食品添加剂的生产和销售;化工设备制造、安装、五金机械加工;化 工技术研宄、咨询,消毒剂生产和销售(危化品 除外)。
1.2 事故项目建设情况1.2.1 项目建设情况事故发生在第一事业部10万t/a离子膜烧碱液氯充装区域,该装置建设备案名称为10万t/a 离子膜烧碱改扩建工程。
设计单位:中国成达工程有限公司;施工单位:中国化学工程第十六建设有限公司;监理单位:浙江南方工程建设监理有限公司;2009年开始建设,2011年竣 工验收,相关手续齐全。
1.2.2 生产工艺简介来自上游装置的原料氯气经氯气缓冲罐进入氯气液化器,与自螺杆冷凝机组来的氟利昂换热后,约在-2.r c下,大部分氯气被液化。
出氯气液化器的液氯与不凝气(少量未被液化的氯气与其他杂质气体)进入液氯分离器,在液氯分 离器中进行气液分离,分离后的液氯流入液氯储槽,不凝气和没有液化的氯气进入尾气分配台后送往盐酸工序。
48.国家安监总局关于加强化工企业泄漏管理的指导意见
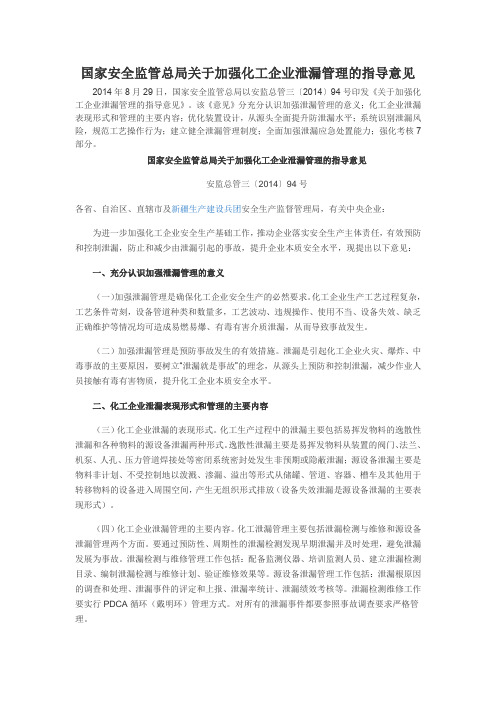
国家安全监管总局关于加强化工企业泄漏管理的指导意见2014年8月29日,国家安全监管总局以安监总管三〔2014〕94号印发《关于加强化工企业泄漏管理的指导意见》。
该《意见》分充分认识加强泄漏管理的意义;化工企业泄漏表现形式和管理的主要内容;优化装置设计,从源头全面提升防泄漏水平;系统识别泄漏风险,规范工艺操作行为;建立健全泄漏管理制度;全面加强泄漏应急处置能力;强化考核7部分。
国家安全监管总局关于加强化工企业泄漏管理的指导意见安监总管三〔2014〕94号各省、自治区、直辖市及新疆生产建设兵团安全生产监督管理局,有关中央企业:为进一步加强化工企业安全生产基础工作,推动企业落实安全生产主体责任,有效预防和控制泄漏,防止和减少由泄漏引起的事故,提升企业本质安全水平,现提出以下意见:一、充分认识加强泄漏管理的意义(一)加强泄漏管理是确保化工企业安全生产的必然要求。
化工企业生产工艺过程复杂,工艺条件苛刻,设备管道种类和数量多,工艺波动、违规操作、使用不当、设备失效、缺乏正确维护等情况均可造成易燃易爆、有毒有害介质泄漏,从而导致事故发生。
(二)加强泄漏管理是预防事故发生的有效措施。
泄漏是引起化工企业火灾、爆炸、中毒事故的主要原因,要树立“泄漏就是事故”的理念,从源头上预防和控制泄漏,减少作业人员接触有毒有害物质,提升化工企业本质安全水平。
二、化工企业泄漏表现形式和管理的主要内容(三)化工企业泄漏的表现形式。
化工生产过程中的泄漏主要包括易挥发物料的逸散性泄漏和各种物料的源设备泄漏两种形式。
逸散性泄漏主要是易挥发物料从装置的阀门、法兰、机泵、人孔、压力管道焊接处等密闭系统密封处发生非预期或隐蔽泄漏;源设备泄漏主要是物料非计划、不受控制地以泼溅、渗漏、溢出等形式从储罐、管道、容器、槽车及其他用于转移物料的设备进入周围空间,产生无组织形式排放(设备失效泄漏是源设备泄漏的主要表现形式)。
(四)化工企业泄漏管理的主要内容。
化工企业生产装置泄漏管理导则
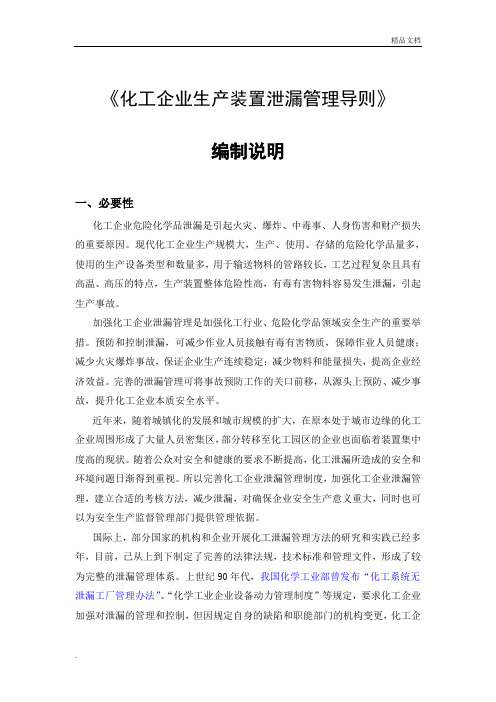
《化工企业生产装置泄漏管理导则》编制说明一、必要性化工企业危险化学品泄漏是引起火灾、爆炸、中毒事、人身伤害和财产损失的重要原因。
现代化工企业生产规模大,生产、使用、存储的危险化学品量多,使用的生产设备类型和数量多,用于输送物料的管路较长,工艺过程复杂且具有高温、高压的特点,生产装置整体危险性高,有毒有害物料容易发生泄漏,引起生产事故。
加强化工企业泄漏管理是加强化工行业、危险化学品领域安全生产的重要举措。
预防和控制泄漏,可减少作业人员接触有毒有害物质,保障作业人员健康;减少火灾爆炸事故,保证企业生产连续稳定;减少物料和能量损失,提高企业经济效益。
完善的泄漏管理可将事故预防工作的关口前移,从源头上预防、减少事故,提升化工企业本质安全水平。
近年来,随着城镇化的发展和城市规模的扩大,在原本处于城市边缘的化工企业周围形成了大量人员密集区,部分转移至化工园区的企业也面临着装置集中度高的现状。
随着公众对安全和健康的要求不断提高,化工泄漏所造成的安全和环境问题日渐得到重视。
所以完善化工企业泄漏管理制度,加强化工企业泄漏管理,建立合适的考核方法,减少泄漏,对确保企业安全生产意义重大,同时也可以为安全生产监督管理部门提供管理依据。
国际上,部分国家的机构和企业开展化工泄漏管理方法的研究和实践已经多年,目前,已从上到下制定了完善的法律法规,技术标准和管理文件,形成了较为完整的泄漏管理体系。
上世纪90年代,我国化学工业部曾发布“化工系统无泄漏工厂管理办法”、“化学工业企业设备动力管理制度”等规定,要求化工企业加强对泄漏的管理和控制,但因规定自身的缺陷和职能部门的机构变更,化工企业后续的泄漏管理工作没有得到应有的重视。
目前,我国化工企业整体泄漏控制的水平跟发达国家的化工企业相比差距较大。
首先,相应的标准还比较欠缺,很多企业做防泄漏工作,但是在执行层面方法各异,泄漏治理效果评估缺乏标准依据;其次,管理措施没有系统化,企业的管理方法有一定局限性,不如发达国家对危险化学品泄漏管理措施层次分明、内容全面。
化工泄漏点漏点分析报告
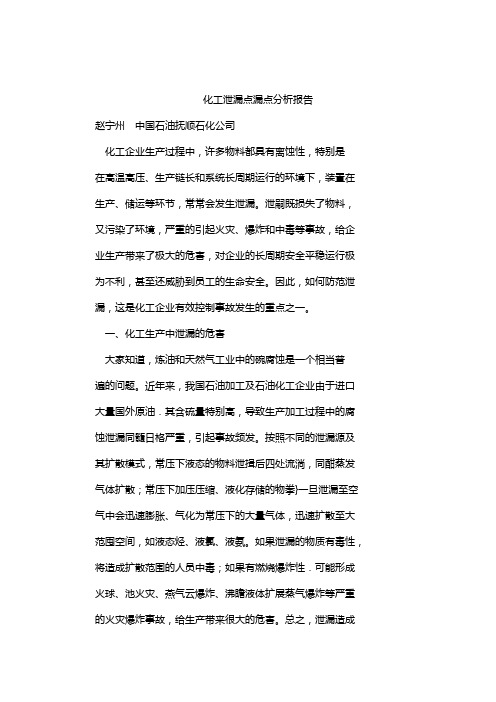
化工泄漏点漏点分析报告赵宁州中国石油抚顺石化公司化工企业生产过程中,许多物料都具有离蚀性,特别是在高温高压、生产链长和系统长周期运行的环境下,装置在生产、储运等环节,常常会发生泄漏。
泄嗣既损失了物料,又污染了环境,严重的引起火灾、爆炸和中毒等事故,给企业生产带来了极大的危害,对企业的长周期安全平稳运行极为不利,甚至还威胁到员工的生命安全。
因此,如何防范泄漏,这是化工企业有效控制事故发生的重点之一。
一、化工生产中泄漏的危害大家知道,炼油和天然气工业中的碗腐蚀是一个相当普遍的问题。
近年来,我国石油加工及石油化工企业由于进口大量国外原油.其含硫量特别高,导致生产加工过程中的腐蚀泄漏同髓日格严重,引起事故频发。
按照不同的泄漏源及其扩散模式,常压下液态的物料泄揖后四处流淌,同酣蒸发气体扩散;常压下加压压缩、液化存储的物拳}一旦泄漏至空气中会迅速膨胀、气化为常压下的大量气体,迅速扩散至大范囤空间,如液态烃、液氯、液氨。
如果泄漏的物质有毒性,将造成扩散范围的人员中毒;如果有燃烧爆炸性.可能形成火球、池火灾、燕气云爆炸、沸瞻液体扩展蒸气爆炸等严重的火灾爆炸事故,给生产带来很大的危害。
总之,泄漏造成的危害是巨大的,主要体现在以下几个方面:1.将料和能量损失泄漏首先流失了生产过程中有用的物料和能量,增加了物料消耗,使企业的生产成本上升,效益下降。
特别是价格昂啬的物料一日拊磊簖诰成的经济榀失重大.而使水,蕉汽境中的物质一般难以回收,严重污染了空气、水和土壤。
例如1986年儿月1日,瑞士巴塞尔市赞多兹化工厂危化品仓库发生火灾,约aOt农药和化工原料流人了莱菌河,使莱茵河受到磷酸和汞化物的严重污染.240多公里长的河道里漂起大量死鱼,河水不能使用,莱茵河漉域的居民在很长时间内都只能靠消防车和其它车辆从水库运水饮用。
有关专家曾经指出:这起事故将使菜茵河因污染治理工作而至少倒遇15年,并对河流生态造成长期的影响。
二、化工生产中泄漏产生的原因通过对建国以来我国化工系统发生的重大及典型泄厕事故的统计分析可以看出,化工泄漏事故主要有突发性强、危害性大、应急处理难度大的特点。
化工企业生产装置泄漏管理导则
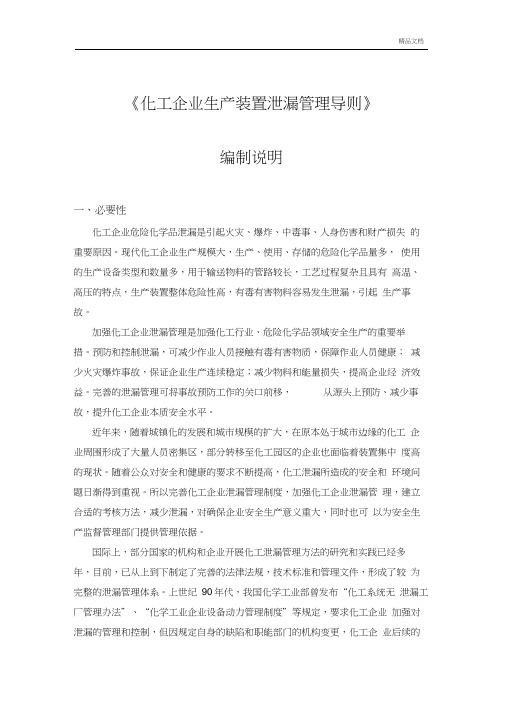
《化工企业生产装置泄漏管理导则》编制说明一、必要性化工企业危险化学品泄漏是引起火灾、爆炸、中毒事、人身伤害和财产损失的重要原因。
现代化工企业生产规模大,生产、使用、存储的危险化学品量多,使用的生产设备类型和数量多,用于输送物料的管路较长,工艺过程复杂且具有高温、高压的特点,生产装置整体危险性高,有毒有害物料容易发生泄漏,引起生产事故。
加强化工企业泄漏管理是加强化工行业、危险化学品领域安全生产的重要举措。
预防和控制泄漏,可减少作业人员接触有毒有害物质,保障作业人员健康;减少火灾爆炸事故,保证企业生产连续稳定;减少物料和能量损失,提高企业经济效益。
完善的泄漏管理可将事故预防工作的关口前移,从源头上预防、减少事故,提升化工企业本质安全水平。
近年来,随着城镇化的发展和城市规模的扩大,在原本处于城市边缘的化工企业周围形成了大量人员密集区,部分转移至化工园区的企业也面临着装置集中度高的现状。
随着公众对安全和健康的要求不断提高,化工泄漏所造成的安全和环境问题日渐得到重视。
所以完善化工企业泄漏管理制度,加强化工企业泄漏管理,建立合适的考核方法,减少泄漏,对确保企业安全生产意义重大,同时也可以为安全生产监督管理部门提供管理依据。
国际上,部分国家的机构和企业开展化工泄漏管理方法的研究和实践已经多年,目前,已从上到下制定了完善的法律法规,技术标准和管理文件,形成了较为完整的泄漏管理体系。
上世纪90年代,我国化学工业部曾发布“化工系统无泄漏工厂管理办法”、“化学工业企业设备动力管理制度”等规定,要求化工企业加强对泄漏的管理和控制,但因规定自身的缺陷和职能部门的机构变更,化工企业后续的泄漏管理工作没有得到应有的重视。
目前,我国化工企业整体泄漏控制的水平跟发达国家的化工企业相比差距较大。
首先,相应的标准还比较欠缺,很多企业做防泄漏工作,但是在执行层面方法各异,泄漏治理效果评估缺乏标准依据;其次,管理措施没有系统化,企业的管理方法有一定局限性,不如发达国家对危险化学品泄漏管理措施层次分明、内容全面。
国家安全监管总局关于 加强化工企业泄漏管理的指导意见

国家安全监管总局关于加强化工企业泄漏管理的指导意见安监总管三〔2014〕94号各省、自治区、直辖市及新疆生产建设兵团安全生产监督管理局,有关中央企业:为进一步加强化工企业安全生产基础工作,推动企业落实安全生产主体责任,有效预防和控制泄漏,防止和减少由泄漏引起的事故,提升企业本质安全水平,现提出以下意见:一、充分认识加强泄漏管理的意义(一)加强泄漏管理是确保化工企业安全生产的必然要求。
化工企业生产工艺过程复杂,工艺条件苛刻,设备管道种类和数量多,工艺波动、违规操作、使用不当、设备失效、缺乏正确维护等情况均可造成易燃易爆、有毒有害介质泄漏,从而导致事故发生。
(二)加强泄漏管理是预防事故发生的有效措施。
泄漏是引起化工企业火灾、爆炸、中毒事故的主要原因,要树立“泄漏就是事故”的理念,从源头上预防和控制泄漏,减少作业人员接触有毒有害物质,提升化工企业本质安全水平。
二、化工企业泄漏表现形式和管理的主要内容(三)化工企业泄漏的表现形式。
化工生产过程中的泄漏主要包括易挥发物料的逸散性泄漏和各种物料的源设备泄漏两种形式。
逸散性泄漏主要是易挥发物料从装置的阀门、法兰、机泵、人孔、压力管道焊接处等密闭系统密封处发生非预期或隐蔽泄漏;源设备泄漏主要是物料非计划、不受控制地以泼溅、渗漏、溢出等形式从储罐、管道、容器、槽车及其他用于转移物料的设备进入周围空间,产生无组织形式排放(设备失效泄漏是源设备泄漏的主要表现形式)。
(四)化工企业泄漏管理的主要内容。
化工泄漏管理主要包括泄漏检测与维修和源设备泄漏管理两个方面。
要通过预防性、周期性的泄漏检测发现早期泄漏并及时处理,避免泄漏发展为事故。
泄漏检测与维修管理工作包括:配备监测仪器、培训监测人员、建立泄漏检测目录、编制泄漏检测与维修计划、验证维修效果等。
源设备泄漏管理工作包括:泄漏根原因的调查和处理、泄漏事件的评定和上报、泄漏率统计、泄漏绩效考核等。
泄漏检测维修工作要实行PDCA循环(戴明环)管理方式。
化工企业泄漏应急处置程序

泄漏应急处置程序1、应急处置人员应佩戴正压式空气呼吸器,穿防静电、防化服装,然后才能进入事故现场,完成侦检、堵漏、救援等任务。
根据泄露物质的理化性质、爆炸特性、毒性及现场监测结果设定初始隔离区,紧急疏散转移隔离区所有无关人员,由警卫人员把守重要出入口。
实时监测空气中有毒、易燃易爆气体的浓度,及时调整隔离区围。
消除事故现场所有点火源,防止燃烧和爆炸。
如果可能,应关闭前置阀门,切断泄漏源。
也可尝试将易燃易爆气体引入紧急泄漏压系统进行无害化处理;液体应进入倒罐处置。
2、根据现场情况,若易燃气体和液体泄漏,立即研究抢险及堵漏方案,所有堵漏行为必须采取防爆防毒措施,确保安全。
泄露形成的液体也可以用泡沫覆盖,防止挥发出易燃或有毒蒸汽,然后采用防爆泵进行收集。
可用雾状水稀释空气中的易燃气体,但应避免高压直流水冲击液体泄漏物,防止产生静电,引发二次事故。
收集后剩余的少量残液,用干砂土、水泥粉、干粉等吸附处置。
对于遇水反应或溶于水的物质,可以用大量水冲洗,污水应放入废水系统,经处理后可直接排放。
3、事故处理过程中,应避免泄漏物进入下水道等限制性空间。
整个泄漏处置过程中,均应有事故现场监视人员,一旦出现爆炸征兆时,所有应急人员均及时撤离事故现场,尽量降低人员伤亡。
在危险区和安全区交界处设立洗消站,对中毒人员、现场应急人员、医护人员、器具等进行洗消。
洗消污水的排放应力求符合环保要求,以防造成次生灾害。
附二燃烧、爆炸事故应急处置程序1、根据事故现场情况,消防、堵漏、搜救、侦检等应急处置人员应佩戴个人防护装备(正压式空气呼吸器、防火服、照明联络工具等)。
组织人员搜救隔离区的受伤和中毒人员,由警卫人员紧急疏散转移隔离区所有无关人员。
通过侦检、明确事故现场情况,包括事故物质的种类、理化性质和主要危险特性、容器储量、燃烧时间、部位、火势围、不同的着火点相互影响情况、对周围的储罐和生产装置的影响情况、次生灾害肯可能波及的区域、现场消防设施情况等。
化工泄露点处置方案

化工泄露点处置方案背景化工企业常因操作失误、设备磨损、意外事故等原因导致化工品泄露,可能会造成严重后果,如燃烧爆炸、环境污染、人员伤亡等。
因此,化工泄露事故的应急处置方案至关重要。
泄露点处置流程一般情况下,化工泄漏事故的应急处置流程主要分为以下几个步骤:1.确认泄漏情况,包括泄漏物质名称、泄漏量、泄漏位置、泄漏途径等信息,以便采取相应的紧急处理措施;2.向现场人员发出紧急疏散指令,并保障人员安全;3.组织专业人员对泄露现场进行技术评估,确定化学品泄漏的性质和危害程度,及其可能造成的后果;4.根据泄漏物质的性质和状态,选择合适的处理方法;5.针对情况进行现场气体监测和环境污染控制;6.进行泄漏物质的收集、中和、稀释等处置;7.清除污染区域和其他有可能感染的区域,并进行消毒处理;8.跟踪监测污染物质的扩散路径和范围,如果有必要进行善后处理;9.对处理情况进行汇报和记录,以便后期评估和总结。
针对不同泄露情况的处理方法不同泄漏情况需要采取不同的处理方法,以下是各种泄漏情况的处理方法:1.废气泄露对于废气泄漏,必须采取气体监测措施,分析废气的成分和浓度,然后选择适当的处理措施,如:静电保持措施、水喷淋措施等。
2.液体泄漏液态化学品泄漏时,应尽快堵塞点位、卸下设备,并找到泄漏根源。
此外,应选择合适的吸收剂(如石棉、沥青、膨润土等)或者防污染设备进行清除。
3.固体泄露若是固体化学品泄露时,只需将泄漏的固体收集后,置于合适的容器中,以便日后专门处理。
处置后的注意事项化工泄露事故处理完成后,还需要注意以下一些事项:1.记录化工泄露事故的情况,要求完整、准确;2.严格按照相应的规定进行分类处置;3.把处置后的废物及处理方案交由环保部门检验处理;4.安排专人负责处置区域的清扫和消毒工作;5.做好餐饮卫生检查和消防检查。
总结化工泄露点处置方案是化工企业应急管理中非常重要的一环。
在处置过程中,针对不同的泄漏情况需采用不同的处理方法,只有掌握了必要的技能、知识和经验,并合理利用现有的工具、设备和工艺,才能最大程度地降低化工泄漏事故所带来的后果和隐患,保障生产和人民群众的安全。
化工厂泄露处置方案

化工厂泄露处置方案背景化工厂是生产化学品和化学制品的工厂,这类工厂经常使用各种有毒有害的化学品。
在生产过程中,由于设备老化、技术操作失误、交通意外等原因,化学品可能会泄露,集装箱、管道等设备也可能遭受损坏。
一旦化学品泄露,将会对人和环境造成巨大的危害。
当化工厂发生泄露事故时,化工厂应即时采取措施进行处置,以降低危害和损失。
本文将介绍化工厂泄露处置方案。
泄露处置方案第一步:确定泄露污染物种类当化工厂发生泄漏事故时,应立即查明泄漏污染物的种类和规模,以便采取针对性的应急处置措施。
根据泄漏污染物种类不同,应采取不同的应急处置方法。
第二步:制定应急处置方案根据泄漏污染物种类和程度,制定应急处置方案,包括紧急止泄、人员疏散、保护措施、污染地点封锁、物资调度等措施,并切实落实好处置方案。
第三步:紧急止泄泄漏危险物品时,应立即实施止泄措施。
如果泄漏是源头迅速切断管路等设备,降低泄漏污染物外溢;如果泄漏已经形成污染团,则应及时投入适量的泄漏物质专用控制剂进行吸附或中和,避免危害物质进一步扩散。
第四步:保护人员和环境当化学品泄露或其他突发事件威胁到人员安全时,要立即疏散人员。
同时,应在周边区域设置适当的隔离带,并进行生态环境监测,确保人员和环境的安全。
第五步:清理污染物出现泄漏后,应采取措施避免污染物质进一步进入地下、地表水以及其他自然资源。
同时,在污染区域做好危险品容器拆卸、污染物的转移、清理和处理工作。
如果发现大面积的土地和水体被污染,则必须进行土地和水体的专业修复。
结论化工厂泄露污染事故不可避免,相应的应急处置措施必不可少。
如果化工厂可以按照上述步骤制定应急处置方案,并在污染事故时及时采取紧急处置措施,可以降低污染事故的风险和对环境的影响。
XXX公司设备泄漏挂牌管理
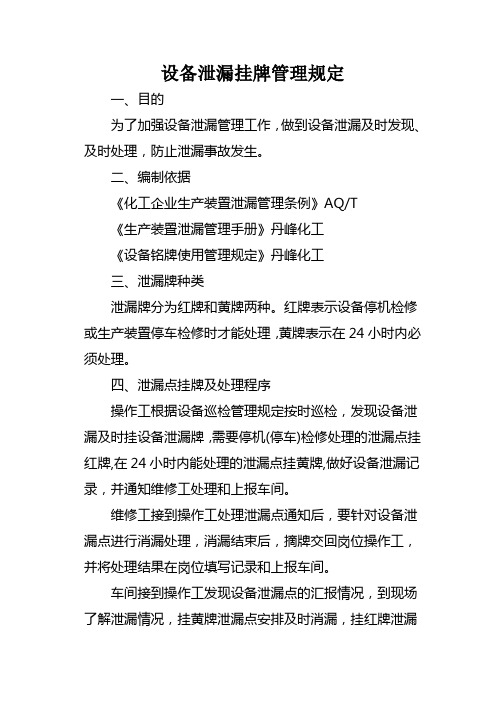
设备泄漏挂牌管理规定
一、目的
为了加强设备泄漏管理工作,做到设备泄漏及时发现、及时处理,防止泄漏事故发生。
二、编制依据
《化工企业生产装置泄漏管理条例》AQ/T
《生产装置泄漏管理手册》丹峰化工
《设备铭牌使用管理规定》丹峰化工
三、泄漏牌种类
泄漏牌分为红牌和黄牌两种。
红牌表示设备停机检修或生产装置停车检修时才能处理,黄牌表示在24小时内必须处理。
四、泄漏点挂牌及处理程序
操作工根据设备巡检管理规定按时巡检,发现设备泄漏及时挂设备泄漏牌,需要停机(停车)检修处理的泄漏点挂红牌,在24小时内能处理的泄漏点挂黄牌,做好设备泄漏记录,并通知维修工处理和上报车间。
维修工接到操作工处理泄漏点通知后,要针对设备泄漏点进行消漏处理,消漏结束后,摘牌交回岗位操作工,并将处理结果在岗位填写记录和上报车间。
车间接到操作工发现设备泄漏点的汇报情况,到现场了解泄漏情况,挂黄牌泄漏点安排及时消漏,挂红牌泄漏
点制定设备泄漏安全措施和检修计划,上报设备科便于公司统一安排计划检修,根据检修计划按时完成消漏工作,并做好设备泄漏点处理结果记录台账。
设备科根据车间上报的设备泄漏情况,登记台账,编制检修计划,安排停车(停机)处理,记录处理结果。
五、其它
1、设备泄漏挂牌的作用是说明此处设备已经泄漏,在本岗位操作和作业人员要高度警戒,防止发生泄漏事故,并要及时消漏。
所以,员工对设备泄漏挂牌工作要高度重视,做到巡检认真,挂牌及时。
2、设备泄漏点记录要按时填写,认真及时,班班交接。
3、设备泄漏牌要加强管理,做到挂牌及时、到位,摘牌按时回收,牌面保持干净、摆放整齐。
(附密封点泄漏挂牌管理程序图)。
关于加强化工企业泄漏管理的指导意见
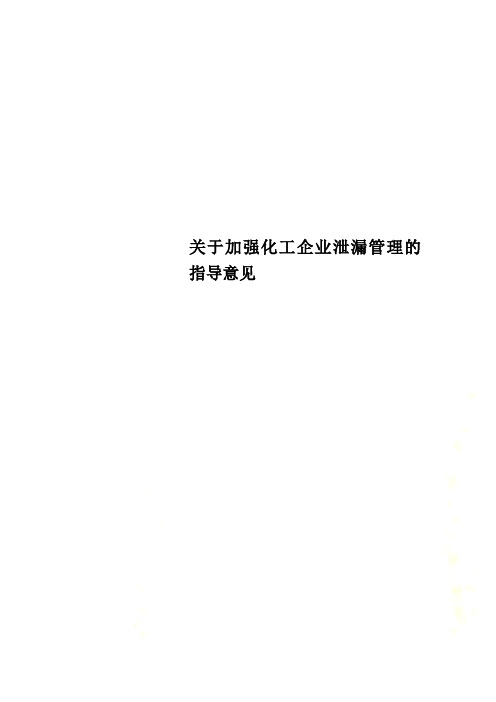
关于加强化工企业泄漏管理的指导意见国家安全监管总局关于加强化工企业泄漏管理的指导意见安监总管三〔2014〕94号各省、自治区、直辖市及新疆生产建设兵团安全生产监督管理局,有关中央企业:为进一步加强化工企业安全生产基础工作,推动企业落实安全生产主体责任,有效预防和控制泄漏,防止和减少由泄漏引起的事故,提升企业本质安全水平,现提出以下意见:一、充分认识加强泄漏管理的意义(一)加强泄漏管理是确保化工企业安全生产的必然要求。
化工企业生产工艺过程复杂,工艺条件苛刻,设备管道种类和数量多,工艺波动、违规操作、使用不当、设备失效、缺乏正确维护等情况均可造成易燃易爆、有毒有害介质泄漏,从而导致事故发生。
(二)加强泄漏管理是预防事故发生的有效措施。
泄漏是引起化工企业火灾、爆炸、中毒事故的主要原因,要树立“泄漏就是事故”的理念,从源头上预防和控制泄漏,减少作业人员接触有毒有害物质,提升化工企业本质安全水平。
二、化工企业泄漏表现形式和管理的主要内容(三)化工企业泄漏的表现形式。
化工生产过程中的泄漏主要包括易挥发物料的逸散性泄漏和各种物料的源设备泄漏两种形式。
逸散性泄漏主要是易挥发物料从装置的阀门、法兰、机泵、人孔、压力管道焊接处等密闭系统密封处发生非预期或隐蔽泄漏;源设备泄漏主要是物料非计划、不受控制地以泼溅、渗漏、溢出等形式从储罐、管道、容器、槽车及其他用于转移物料的设备进入周围空间,产生无组织形式排放(设备失效泄漏是源设备泄漏的主要表现形式)。
(四)化工企业泄漏管理的主要内容。
化工泄漏管理主要包括泄漏检测与维修和源设备泄漏管理两个方面。
要通过预防性、周期性的泄漏检测发现早期泄漏并及时处理,避免泄漏发展为事故。
泄漏检测与维修管理工作包括:配备监测仪器、培训监测人员、建立泄漏检测目录、编制泄漏检测与维修计划、验证维修效果等。
源设备泄漏管理工作包括:泄漏根原因的调查和处理、泄漏事件的评定和上报、泄漏率统计、泄漏绩效考核等。
化工企业生产装置泄漏检查表

压缩机、大型储罐、压力容器等关键设备在日常使用过程中要注意定期检查,可使
现场核查
序号
检杳项目
检杳内容
检杳方法
检杳情况
备注
用包括放射性、红外、磁感、电流、视觉在内的多种无损检测技术手段对设备的完整性和性能进行检测,及早发现设备缺陷,并进行更换和维修。
正确执行工艺操作规程,工艺操作的参数和操作步骤应该尽量能保证工艺平稳,避免产生较大工艺波动,保障设备稳定运行,各项安全控制指标不得超过操作设计值。工艺取样应严格按照取样规范,使用专用采样装置取样。
经泄漏测试合格后,可投入生产运行。
现场核查
试车应加强开停车的计划方案审核、泄漏防护和响应。
现场核查
开车过程中应严格按规程,避免设备承受较大应力。
现场核查
3
使用
压力容器在使用前,应取得设备所在地质量技术监督部门颁发的注册登记证书,并依照有关标准对承压、密封等泄漏相关的性能进行检验并取得检验报告。部分髙泄漏风险的容器可参考压力容器进行管理,
联动试车阶段,管道系统应吹扫、气密、
压力试验后方可投入生产运行。
现场核查
投料试车时,应该使用泄漏检测仪对泄漏风险较髙的压缩机、机泵、反应容器、储运容器、工业炉、换热器等主要设备的密封进行全面泄漏测试,对髙泄漏风险的管
现场核查
序号
检杳项目
检杳内容
检杳方法
检杳情况
备注
道系统的阀门、法兰等组件的密封件也应进行泄漏测试。
现场核查
序号
检杳项目
检杳内容
检杳方法
检杳情况
备注
定期检验、维护。
泄漏风险髙的设备投用前应组织进行风险评估,根据评估结果部署防护措施提髙设备的防护等级,对于储罐、容器类设备应借助液位计、压力表、温度表等仪表系统实时监控工艺参数,避免液位超髙、压力超压、温度过髙等物理因素超标导致设备本体破损或内部物料溢出、喷射,也可通过增加外保护壳、围堰等被动防护措施提升防护等级。
关于加强化工企业泄漏管理的指导意见
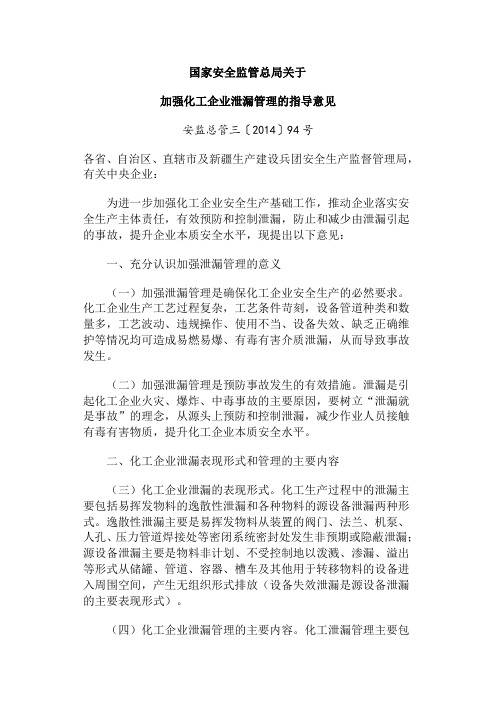
国家安全监管总局关于加强化工企业泄漏管理的指导意见安监总管三〔2014〕94号各省、自治区、直辖市及新疆生产建设兵团安全生产监督管理局,有关中央企业:为进一步加强化工企业安全生产基础工作,推动企业落实安全生产主体责任,有效预防和控制泄漏,防止和减少由泄漏引起的事故,提升企业本质安全水平,现提出以下意见:一、充分认识加强泄漏管理的意义(一)加强泄漏管理是确保化工企业安全生产的必然要求。
化工企业生产工艺过程复杂,工艺条件苛刻,设备管道种类和数量多,工艺波动、违规操作、使用不当、设备失效、缺乏正确维护等情况均可造成易燃易爆、有毒有害介质泄漏,从而导致事故发生。
(二)加强泄漏管理是预防事故发生的有效措施。
泄漏是引起化工企业火灾、爆炸、中毒事故的主要原因,要树立“泄漏就是事故”的理念,从源头上预防和控制泄漏,减少作业人员接触有毒有害物质,提升化工企业本质安全水平。
二、化工企业泄漏表现形式和管理的主要内容(三)化工企业泄漏的表现形式。
化工生产过程中的泄漏主要包括易挥发物料的逸散性泄漏和各种物料的源设备泄漏两种形式。
逸散性泄漏主要是易挥发物料从装置的阀门、法兰、机泵、人孔、压力管道焊接处等密闭系统密封处发生非预期或隐蔽泄漏;源设备泄漏主要是物料非计划、不受控制地以泼溅、渗漏、溢出等形式从储罐、管道、容器、槽车及其他用于转移物料的设备进入周围空间,产生无组织形式排放(设备失效泄漏是源设备泄漏的主要表现形式)。
(四)化工企业泄漏管理的主要内容。
化工泄漏管理主要包括泄漏检测与维修和源设备泄漏管理两个方面。
要通过预防性、周期性的泄漏检测发现早期泄漏并及时处理,避免泄漏发展为事故。
泄漏检测与维修管理工作包括:配备监测仪器、培训监测人员、建立泄漏检测目录、编制泄漏检测与维修计划、验证维修效果等。
源设备泄漏管理工作包括:泄漏根原因的调查和处理、泄漏事件的评定和上报、泄漏率统计、泄漏绩效考核等。
泄漏检测维修工作要实行PDCA循环(戴明环)管理方式。
石油化工装置泄漏检测与修复措施研究

石油化工装置泄漏检测与修复措施研究发布时间:2021-10-28T02:06:52.242Z 来源:《工程管理前沿》2021年6月16期作者:刘立明[导读] 需要生产单位采用科学合理的泄漏检测技术及装置设备修复措施,定期开展检测与修复工作。
刘立明抚顺石化公司烯烃厂聚丙烯车间 113008 摘要:现代化石油化工生产过程涉及危险因素的危险程度大,主要因为生产的连续性、设备的复杂性、介质类型的多样性及输送管道运程较长等,且输送介质具有高温、高压及易燃易爆等特点。
如果在生产过程中石油化工装置发生泄漏,泄漏的主要成分是挥发性有机物质,其危险性极大,可能引起中毒、火灾、爆炸等而造成生命财产的严重损失。
因此,需要生产单位采用科学合理的泄漏检测技术及装置设备修复措施,定期开展检测与修复工作。
关键词:石油化工;装置;泄漏检测现代石油化工企业具有生产连续、生产设备复杂、介质类型多、输送管道多,而且输送介质具有高温、高压、有毒、腐蚀以及易燃易爆等特点。
加之在工业生产过程中各类管道和设备都使用了大量的阀门、法兰以及螺纹等连接方式,存在着大量的动、静密封点,一旦这些部位出现泄露,将导致重大的安全事故。
所以,合理利用泄露检测技术以及监测手段,对保证企业的安全生产、职工的身心健康具有十分重要的作用,同时还能够为安全生产及管理运行提供有力的技术支持。
1 石油化工装置泄漏检测与修复流程石油化工行业中将装置的泄漏检测与修复技术实施的全过程进行控制的系统在国外称为“Leak Detection and Repair”,英文缩写是LDAR。
生产企业首次实施LDAR工作流程中的主要环节是项目建立、泄漏检测及泄漏修复等三个重要环节。
项目建立需要进行工艺流程图、管道仪表图、物料平衡表、操作规程、装置平面布置图、设备台账等相关资料的收集,涉及发挥性有机物(VOCs)的物料要对其处理设备进行分析,主要通过检测编码设计、群组信息采集、密封垫信息采集、密封垫台账的建立等步骤的实施经合规审核后建立起LDAR管理项目;进入现场检测阶段需要首先制定检测计划并进行检测仪器、器材等的配备与准备,检测结果数据进行记录与分析后,确定密封点是泄漏点的进行泄漏标识;进入泄漏密封点的修复工作阶段,采取一定的修复措施进行密封处理后要进行复测,复测合格的录入数据库便结束修复工作,复测不合格的在进行延迟性修复或实质性修复后,再次复测,合格则结束修复工作。
1.化工企业生产装置泄漏管理导则--标准编制说明
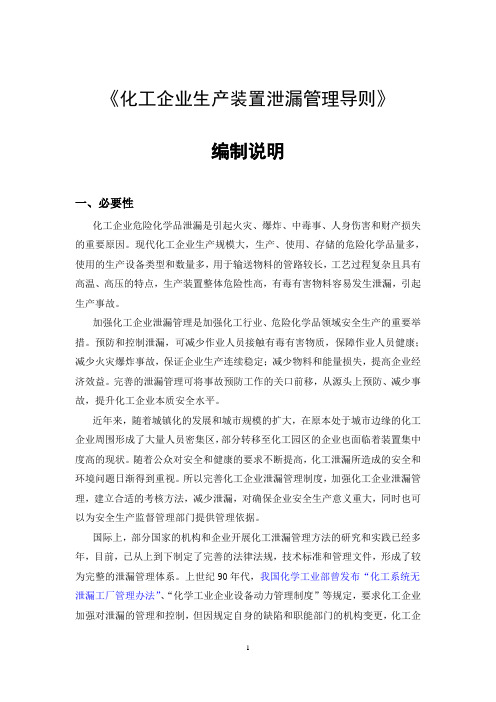
《化工企业生产装置泄漏管理导则》编制说明一、必要性化工企业危险化学品泄漏是引起火灾、爆炸、中毒事、人身伤害和财产损失的重要原因。
现代化工企业生产规模大,生产、使用、存储的危险化学品量多,使用的生产设备类型和数量多,用于输送物料的管路较长,工艺过程复杂且具有高温、高压的特点,生产装置整体危险性高,有毒有害物料容易发生泄漏,引起生产事故。
加强化工企业泄漏管理是加强化工行业、危险化学品领域安全生产的重要举措。
预防和控制泄漏,可减少作业人员接触有毒有害物质,保障作业人员健康;减少火灾爆炸事故,保证企业生产连续稳定;减少物料和能量损失,提高企业经济效益。
完善的泄漏管理可将事故预防工作的关口前移,从源头上预防、减少事故,提升化工企业本质安全水平。
近年来,随着城镇化的发展和城市规模的扩大,在原本处于城市边缘的化工企业周围形成了大量人员密集区,部分转移至化工园区的企业也面临着装置集中度高的现状。
随着公众对安全和健康的要求不断提高,化工泄漏所造成的安全和环境问题日渐得到重视。
所以完善化工企业泄漏管理制度,加强化工企业泄漏管理,建立合适的考核方法,减少泄漏,对确保企业安全生产意义重大,同时也可以为安全生产监督管理部门提供管理依据。
国际上,部分国家的机构和企业开展化工泄漏管理方法的研究和实践已经多年,目前,已从上到下制定了完善的法律法规,技术标准和管理文件,形成了较为完整的泄漏管理体系。
上世纪90年代,我国化学工业部曾发布“化工系统无泄漏工厂管理办法”、“化学工业企业设备动力管理制度”等规定,要求化工企业加强对泄漏的管理和控制,但因规定自身的缺陷和职能部门的机构变更,化工企业后续的泄漏管理工作没有得到应有的重视。
目前,我国化工企业整体泄漏控制的水平跟发达国家的化工企业相比差距较大。
首先,相应的标准还比较欠缺,很多企业做防泄漏工作,但是在执行层面方法各异,泄漏治理效果评估缺乏标准依据;其次,管理措施没有系统化,企业的管理方法有一定局限性,不如发达国家对危险化学品泄漏管理措施层次分明、内容全面。
化工装置泄漏应急救援处置预案

化工装置泄漏应急救援处置预案一、概述化工装置泄漏是化工生产过程中不可避免的事故之一,如果不及时采取救援措施,可能会造成严重的人员伤亡和环境污染。
为了有效应对化工装置泄漏事故,保障生产人员和周边环境的安全,制定和实施化工装置泄漏应急救援处置预案是必不可少的。
二、应急救援组织机构及责任人1. 应急指挥中心应急指挥中心是应急救援工作的核心组织机构,由应急指挥中心主任和成员组成。
主要职责包括指挥调度,协调联络,信息收集和信息发布等。
2. 指挥长指挥长负责应急救援工作的总体指挥调度,主要由相关主管领导担任。
3. 现场负责人现场负责人负责实施应急救援工作,组织人员撤离和泄漏物处理等。
三、应急救援流程1. 接到报警当发生化工装置泄漏时,应急指挥中心接到报警后,立即组织人员前往现场,并通知相关单位协助救援工作。
2. 确认泄漏物性质和危害程度现场负责人在到达现场后,首先要确认泄漏物的性质和危害程度,以便采取正确的处置措施。
3. 人员撤离在确认泄漏物性质和危害程度后,现场负责人必须迅速组织周围人员撤离到安全地点,确保人员安全。
4. 封锁现场和区域隔离对于泄漏事故现场,应及时进行封锁和区域隔离,防止泄漏物进一步扩散。
5. 使用个人防护装备在进行泄漏物处置工作时,救援人员必须佩戴相应的个人防护装备,包括防护服、防毒面具、防护手套等。
6. 进行泄漏物处置根据泄漏物的性质和危害程度,选择合适的处置方法和设备,进行泄漏物的清除和处理。
7. 监测环境和空气质量在进行泄漏物处置过程中,要时刻监测环境和空气质量,确保处置过程中无二次污染和安全风险。
8. 恢复生产和环境修复当泄漏物得到有效处置后,要进行生产设备的检修和环境的修复工作,确保生产能够正常恢复,环境没有进一步污染。
9. 事故调查和总结事故发生后,要成立事故调查组,对事故原因进行深入调查,并及时总结救援工作中存在的问题和不足,为未来的应急救援工作提供经验教训。
四、应急救援装备和物资1. 应急救援装备应急救援装备包括个人防护装备、泄漏物清除设备、检测仪器等。
加强化工企业泄漏管理的指导意见
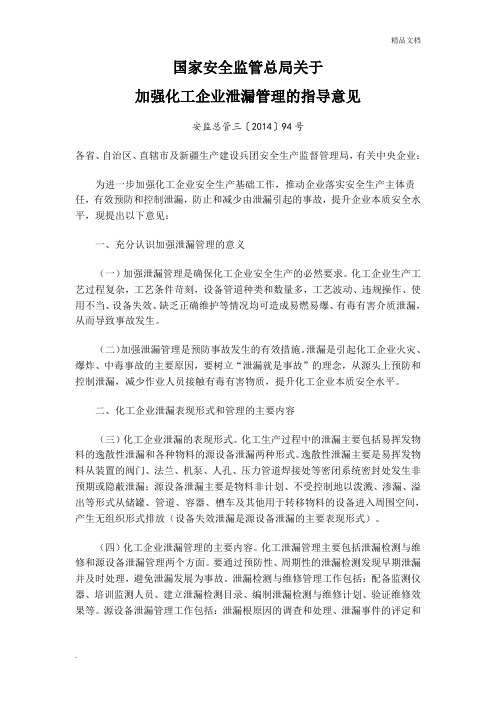
国家安全监管总局关于加强化工企业泄漏管理的指导意见安监总管三〔2014〕94号各省、自治区、直辖市及新疆生产建设兵团安全生产监督管理局,有关中央企业:为进一步加强化工企业安全生产基础工作,推动企业落实安全生产主体责任,有效预防和控制泄漏,防止和减少由泄漏引起的事故,提升企业本质安全水平,现提出以下意见:一、充分认识加强泄漏管理的意义(一)加强泄漏管理是确保化工企业安全生产的必然要求。
化工企业生产工艺过程复杂,工艺条件苛刻,设备管道种类和数量多,工艺波动、违规操作、使用不当、设备失效、缺乏正确维护等情况均可造成易燃易爆、有毒有害介质泄漏,从而导致事故发生。
(二)加强泄漏管理是预防事故发生的有效措施。
泄漏是引起化工企业火灾、爆炸、中毒事故的主要原因,要树立“泄漏就是事故”的理念,从源头上预防和控制泄漏,减少作业人员接触有毒有害物质,提升化工企业本质安全水平。
二、化工企业泄漏表现形式和管理的主要内容(三)化工企业泄漏的表现形式。
化工生产过程中的泄漏主要包括易挥发物料的逸散性泄漏和各种物料的源设备泄漏两种形式。
逸散性泄漏主要是易挥发物料从装置的阀门、法兰、机泵、人孔、压力管道焊接处等密闭系统密封处发生非预期或隐蔽泄漏;源设备泄漏主要是物料非计划、不受控制地以泼溅、渗漏、溢出等形式从储罐、管道、容器、槽车及其他用于转移物料的设备进入周围空间,产生无组织形式排放(设备失效泄漏是源设备泄漏的主要表现形式)。
(四)化工企业泄漏管理的主要内容。
化工泄漏管理主要包括泄漏检测与维修和源设备泄漏管理两个方面。
要通过预防性、周期性的泄漏检测发现早期泄漏并及时处理,避免泄漏发展为事故。
泄漏检测与维修管理工作包括:配备监测仪器、培训监测人员、建立泄漏检测目录、编制泄漏检测与维修计划、验证维修效果等。
源设备泄漏管理工作包括:泄漏根原因的调查和处理、泄漏事件的评定和上报、泄漏率统计、泄漏绩效考核等。
泄漏检测维修工作要实行PDCA循环(戴明环)管理方式。
- 1、下载文档前请自行甄别文档内容的完整性,平台不提供额外的编辑、内容补充、找答案等附加服务。
- 2、"仅部分预览"的文档,不可在线预览部分如存在完整性等问题,可反馈申请退款(可完整预览的文档不适用该条件!)。
- 3、如文档侵犯您的权益,请联系客服反馈,我们会尽快为您处理(人工客服工作时间:9:00-18:30)。
化工企业生产装置泄漏管理
化工企业生产装置的危险化学品泄漏是引起火灾、爆炸、中毒事故的主要原因,加强泄漏管理是落实化工行业、危险化学品领域安全生产的重要举措。
做好泄漏管理可将事故预防工作的关口前移,从源头上预防、减少事故,提升企业本质安全水平;控制生产装置泄漏,可减少作业人员接触有毒有害物质,保障作业人员健康;预防和减少泄漏可以节能降耗,减少物料和能量损失,提高企业经济效益。
泄漏:
包含危险化学品或危险化学品混合物的原料、中间产物、终产物以气体或者液体的形式,通过多种类型的连接点,例如法兰、螺纹连接等,或通过容器、反应器、换热器、塔器、管道、压缩机、机泵、法兰、阀门、管件、仪表和特定类型的工艺设备的缺陷,非计划不受控制的进入外界环境。
泄漏检测与修复
使用专用测量仪器,对生产装置的压缩机、泵、搅拌器、阀门、接头、安全阀、管线开口、采样系统、仪表系统及其他设备的泄漏位置进行检测,并根据检测结果对超过排放限值的部位进行修复。
泄漏管理清单
企业建立的,具有泄漏风险的泄漏源的列表,包括泄漏源的名称、位置、类别、类型等信息,企业管理人员根据清单,对泄漏源进行周期性的检查、检测和维护。
预防性检测
按一定周期和频率对设备、管道、部件进行预防性检测。
检测宜包括设备、管道包封容器外壳的退化和破坏检验,设备、管道、管段之间部件的密封效果检验,设备、管道各种开口的排放检测。
对于外壳、密封等的可靠性低和泄漏风险高的相应增加检测的频次,每年应至少进行一次预防性检测。
检验或检测出设备、管道完整性、密封性达不到防止泄漏标准的,应在设备、管道、部件的预测失效时间内组织进行预防性维修。
检测措施包括但不限于:
a) 设备、管道的腐蚀、减薄,壁厚检验;
b) 设备、管道的裂纹、鼓泡、微孔检验;
c) 管道弯头的冲蚀检验;
d) 设备、法兰、阀门、各类管配件以及其它设备的接合部位泄漏检测;
e) 设备动密封的泄漏检测;
f) 各种排放口采样口的泄漏检测。
预防性维修包括但不限于以下内容:
a) 更换压力容器和储罐、校验、更换安全阀;
b) 清理阻火器、更换爆破片、更换动静设备的密封件;
c) 调整法兰的螺栓预紧力,调整填料压紧力;
d) 已发生或经检验将要发生轻微泄漏的管道应打夹具;
e) 监测压缩机、机泵等动设备的振动、温度状况,调节转轴偏心;
f) 测试消防水系统、对可燃/有毒气体报警系统/紧急切断阀/报警和
联锁进行功能测试和更新。
个体防护
较高泄漏风险场所工作的人员进行现场操作、日常巡检、泄漏检查和检测时,应配备满足现场个体安全防护功能要求的防护装备、设备。
根据现场泄漏物类型和泄漏程度的不同,个体防护装备、设备包括但不限于:
a) 呼吸防护;
b) 穿戴类防护;
c) 便携式有毒有害泄漏物检测报警。
紧急响应
制定各种类型泄漏事故的应急响应程序,应急响应措施应包括堵漏、覆盖、收容,稀释、处理、疏散等,泄漏事故的响应宜按照泄漏的程度和范围分级,分级可按如下层次:
a) 设备级:管道、管段、单个容器、单个设备的少量物质泄漏,范围边界限于厂内局部可控区域;
b) 装置级:管道、容器、设备、装置的大量物质泄漏,范围边界限于厂界内可控区域;
c) 厂级:设备、装置大量泄漏,范围超过厂界,企业自身无法控制。
开工前应按照相应技术规程应进行设备单机试车,完成耐压测试、负压测试、气密性测试。
联动试车阶段,管道系统应吹扫、气密、压力试验后方可投入生产运行。
投料试车时,应该使用泄漏检测仪对泄漏风险较高的压缩机、机泵、反应容器、储运容器、工业炉、换热器等主要设备的密封进行全面泄漏测试,对高泄漏风险的管道系统的阀门、法兰等组件的密封件也应进行泄漏测试。
经泄漏测试合格后,可投入生产运行。
试车应加强开停车的计划方案审核、泄漏防护和响应。
开车过程中应严格按规程,避免设备承受较大应力。
开工前应按照相应技术规程应进行设备单机试车,完成耐压测试、负压测试、气密性测试。
联动试车阶段,管道系统应吹扫、气密、压力试验后方可投入生产运行。
投料试车时,应该使用泄漏检测仪对泄漏风险较高的压缩机、机泵、反应容器、储运容器、工业炉、换热器等主要设备的密封进行全面泄漏测试,对高泄漏风险的管道系统的阀门、法兰等组件的密封件也应进行泄漏测试。
经泄漏测试合格后,可投入生产运行。
试车应加强开停车的计划方案审核、泄漏防护和响应。
开车过程中应严格按规程,避免设备承受较大应力。
1.1使用
1.1.1压力容器在使用前,应取得设备所在地质量技术监督部门颁发的注册登记证书,并依照有关标准对承压、密封等泄漏相关的性能进行检验并取得检验报告。
部分高泄漏风险的容器可参考压力容器进行管理,定期检验、维护。
1.1.2泄漏风险高的设备投用前应组织进行风险评估,根据评估结果部署防护措施提高设备的防护等级,对于储罐、容器类设备应借助液
位计、压力表、温度表等仪表系统实时监控工艺参数,避免液位超高、压力超压、温度过高等物理因素超标导致设备本体破损或内部物料溢出、喷射,也可通过增加外保护壳、围堰等被动防护措施提升防护等级。
1.1.3压缩机、大型储罐、压力容器等关键设备在日常使用过程中要注意定期检查,可使用包括放射性、红外、磁感、电流、视觉在内的多种无损检测技术手段对设备的完整性和性能进行检测,及早发现设备缺陷,并进行更换和维修。
1.1.4正确执行工艺操作规程,工艺操作的参数和操作步骤应该尽量能保证工艺平稳,避免产生较大工艺波动,保障设备稳定运行,各项安全控制指标不得超过操作设计值。
工艺取样应严格按照取样规范,使用专用采样装置取样。
1.2维护
1.2.1应定期检查和维护设备、管道的密封。
填料密封,应定期检查填料函,并补充或者重新压紧填料。
应定期检查设备管道腐蚀状况,控制腐蚀发生条件,避免阳极腐蚀,建议广泛使用防腐的涂层和防腐金属表层技术。
1.2.2设备管道应严格控制设备载荷,防止应力腐蚀开裂。
设备管道应采取减震措施,增加设备固定点,减少设备的震动,避免震动造成管件自松。
1.2.3动设备的密封应进行高频次的定期监测、维护和保养,维护的周期应远小于静密封设备。
加强动设备运行监控,控制转轴偏心,保
持转动平衡。
严格控制设备转轴的温升,避免密封端面过热,液膜闪蒸,减少密封面磨损。
企业应按AQ/T3034和《危险化学品企业事故隐患排查治理实施导则》的规定进行现场工艺安全管理。
企业应建立制度和规范加强人员对各种渗漏、液滴、结块、污迹、气流、异味等多种泄漏现象的巡检。
发现的泄漏设备、管道或管件应及时挂牌标识。
挂牌标识的设备、管道或管件应在规定的时间内修复,见附录C,不能修复的应经上级主管部门确认。
企业应运行泄漏检测与修复程序,自主独立开展或委托第三方机构实施泄漏检测与修复程序,泄漏检测原始记录表格式可参考附录D。