表面粗糙度值的选用(最新)
表面粗糙度选用标准

表面粗糙度选用-----------------------------------------------------------序号=1Ra值不大于\μm=100表面状况=明显可见的刀痕加工方法=粗车、镗、刨、钻应用举例=粗加工的表面,如粗车、粗刨、切断等表面,用粗镗刀和粗砂轮等加工的表面,一般很少采用-----------------------------------------------------------序号=2Ra值不大于\μm=25、50表面状况=明显可见的刀痕加工方法=粗车、镗、刨、钻应用举例=粗加工后的表面,焊接前的焊缝、粗钻孔壁等-----------------------------------------------------------序号=3Ra值不大于\μm=12.5表面状况=可见刀痕加工方法=粗车、刨、铣、钻应用举例=一般非结合表面,如轴的端面、倒角、齿轮及皮带轮的侧面、键槽的非工作表面,减重孔眼表面-----------------------------------------------------------序号=4Ra值不大于\μm=6.3表面状况=可见加工痕迹加工方法=车、镗、刨、钻、铣、锉、磨、粗铰、铣齿应用举例=不重要零件的配合表面,如支柱、支架、外壳、衬套、轴、盖等的端面。
紧固件的自由表面,紧固件通孔的表面,内、外花键的非定心表面,不作为计量基准的齿轮顶圈圆表面等-----------------------------------------------------------序号=5Ra值不大于\μm=3.2表面状况=微见加工痕迹加工方法=车、镗、刨、铣、刮1~2点/cm^2、拉、磨、锉、滚压、铣齿应用举例=和其他零件连接不形成配合的表面,如箱体、外壳、端盖等零件的端面。
要求有定心及配合特性的固定支承面如定心的轴间,键和键槽的工作表面。
表面粗糙度指标
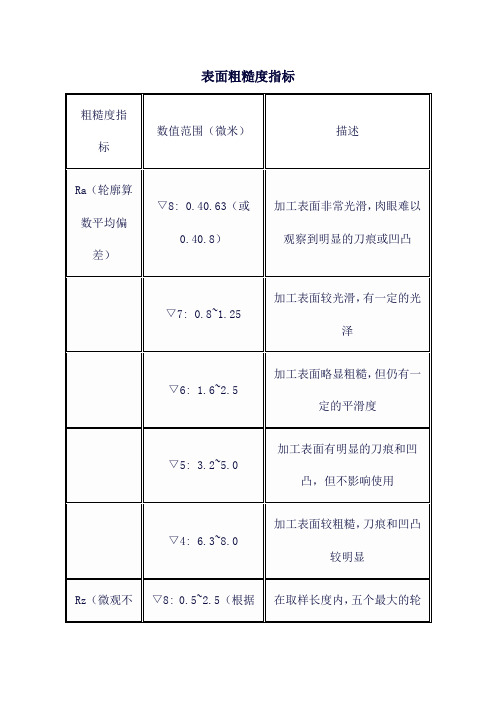
加工表面较粗糙,刀痕和凹凸较明显
Rz(微观不平度十点高度)
▽8: 0.5~2.5(根据Ra值推算,非直接对应)
在取样长度内,五个最大的轮廓峰高的平均值与五个最大的轮廓谷ቤተ መጻሕፍቲ ባይዱ的平均值之和较小
▽7~▽4: 逐渐增加
随着Ra值的增加,Rz值也逐渐增加,表示表面更加粗糙
Ry(轮廓最大高度)
▽8: 0.4~0.8(根据Ra值推算,非直接对应)
在取样长度内,轮廓峰顶线和轮廓谷底线之间的距离较小
▽7~▽4: 逐渐增加
随着Ra值的增加,Ry值也逐渐增加,表示表面轮廓的最大高度差更大
表面粗糙度指标
粗糙度指标
数值范围(微米)
描述
Ra(轮廓算数平均偏差)
▽8: 0.40.63(或0.40.8)
加工表面非常光滑,肉眼难以观察到明显的刀痕或凹凸
▽7: 0.8~1.25
加工表面较光滑,有一定的光泽
▽6: 1.6~2.5
加工表面略显粗糙,但仍有一定的平滑度
▽5: 3.2~5.0
加工表面有明显的刀痕和凹凸,但不影响使用
表面粗糙度与检测(新国标)

3. 中线—指具有几何轮廓形状并划分轮廓的基准线 轮廓算术平均中线:在取样长度内,划分实际轮廓为上、 下两部分面积相等的线
图5.5 轮廓中线
二. 评定参数
1. 幅度参数(高度参数)
(1)轮廓的算术平均偏差Ra
在取样长度lr内,纵坐标值Z(x)的绝对值的算术平均值
Ra1
lr
Z(x)dx
lr 0
表面粗糙度与检测(新国 标)
1概 述
一. 表面粗糙度的含义
微小峰谷的高低程度和间距状况称为表面粗糙度,它是一种微观几何 形状误差,也称微观不平度。
表面粗糙度是指加工后零件表面的微小峰谷(Z)高低程 度和间距(S)状况。
一般按S分:
间距 S
S<1mm 为表面粗糙度;
1≤S≤10mm为 波纹度;
S>10mm为 f形状.。 表面粗糙度的产生:
轮廓单元的平均宽度 RSm:
在取样长度lr
内,轮廓单元宽度Xsi的平均值:
RSm
1 m
m i1
Xsi
3. 混合参数(形状参数) 轮廓的支承长度率Rmr(C) —
在给定的水平位置C上,轮廓的实体材料长度Ml(C)与评定长度ln的比率。
n
bi
Rm(rc) i1 ln
Ml(C)/ln
C = Rz %
1. 表面粗糙度的参数数值
表5.1~5.5
表5.2 Ra 的数值
2. 表面粗糙度参数的选用
评定参数选用
幅度参数 Ra、 Rz
优先选Ra :粗糙度参数值在 (0.0256.3) m;
选Rz :粗糙度参数值在
(6.3100)m ,(0.0080.020 ) m;
附加参数---有特殊要求选用RSm , Rmr(c)
专业资料,表面粗糙度的选用

6.3
IT11
3.2
6.3
12.5
IT12
6.3
12.5
2、常用加工方法能达到的表面粗糙度
加工方法 50
表面粗糙度参数Ra/μm
25
12.5
6.3
3.2
1.6
0.8
0.4
0.2
砂铸/热扎
√
√
锻造
√
√
√
电火花加工
√
√
√
冷轧/拉拔
√
√
√
刨/插
√
√
√
√
√
√
钻孔
√
√
√
铣削
√
√
√
√
车/镗
√
√
√
√
√
拉削/铰孔
√
0.4
0.8
3.2
0.4
0.8
1.6
3.2
6.3 3.2-6.3 3.2-6.3
9 1.6
3.2
4、表面粗糙度、形状公差与尺寸公差的关系
尺寸公差等级
形状公差t
IT5-IT7
≈0.60IT
IT8-IT9
≈0.40IT
IT10-IT12
≈0.25IT
>IT12
<0.25IT
Ra ≤0.05IT ≤0.025IT ≤0.012IT ≤0.15t
1、表面粗造度与公差等级的对应关系
基本尺寸/mm
公差等级 >6-10
>10-18 >18-30 >30-50 >50-80 >80-120 >120-180 >180-250
表面粗糙度Ra不大于/μm
表面粗糙度最新国家标注
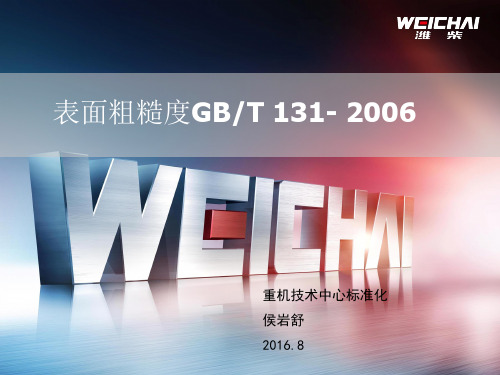
评定长度一般按5个取样长n 度来确定。
3/29/2020
评定表面粗糙度的基准线
评定表面粗糙度的基准线,有以下两种: 轮廓的最小二乘中线m
在取样长度内,使轮廓上各点至一条该线的距离平方和为 最小。
即: n yi2 min i 1
技术产品文件中表面结构要求标注的控制元素
3/29/2020
a 上限或下限符号U或L b 滤波器类型“x”。标准滤波器是高斯滤波器(GB/T 18777)。
以前的标准滤波器是2RC滤波器。将来也可能对其他的滤波器 进行标准化。在转换期间,在图样上标注滤波器类型对某些公 司比较方便。滤波器类型可以标注为“高斯滤波器”或 “2RC"。滤波器名称并没有标准化,但这里所建议的标注名 称是明确的,无争议的。
表面粗糙度GB/T 131- 2006
重机技术中心标准化 侯岩舒 2016.8
新国标 GB/131- 2006《产品几何技术规范( GPS) 技术产品文件中表面结构的表示法》
充分考虑了对零件表面质量影响的多种因素, 除表面粗糙度外还有在机械加工过程中, 由 于机床、工件和刀具系统的振动, 在工件表 面所形成的间距比粗糙度大得多的表面不平 度、即波纹度的影响。所以, 表面粗糙度、 表面波纹度以及表面几何形状误差总是同时 生成并存在同一表面上综合影响零件的表面 轮廓。
3/29/2020
5 表面结构要求在图样中的注法
图1 表面结构要求的注写方向
3/29/2020
标注在轮廓线上或指引线上
表面结构的注写和读取方向与尺寸的注写和读取方向一 致。表面结构要求可标注在轮廓线上, 其符号应从材料 外指向并接触表面, 如图 2 所示。必要时, 表面结构也 可用带箭头或黑点的指引线引出标注, 如图 3 所示。
表面粗糙度最新国家标注

有关检验规范的基本术语
1 取样长度和评定长度
取样长度——测量表面粗糙度轮廓时,测量限制的一
段足够短的长度,以限制或减弱波纹度、排除形状误 差对表面粗糙度轮廓测量的影响。(详见P134表5-1) 评定长度默认为 5 个取样长度, 否则应注明个数。 例如Rz0.4、Ra3 0.8、Rz1 3.2 分别表示评定长度
参数值的选用方法
可用类比法来确定。一般尺寸公差、表面形状公差小 时,表面粗糙度参数值也小,但也不存在确定的函数 关系。 一般情况下,它们之间有一定的对应关系,设形状公 差为t,尺寸公差为IT,它们之间的关系可参照以下对 应关系:
若t≈0.6 IT,则Ra≤0.05 IT; Rz≤ 0.2 IT
极限值判断规则
2 最大规则: 运用本规则时, 被检的整个表 面上测得的参数值一个也不应超过给定的 极限值。 16%规则是所有表面结构要求标注的默认 规则。即图样上不注写其它符号时,均默 认为应用 16%规则( 例如 Ra0.8) 。即当 参数代号后标注写“max”字样时, 则应用 最大规则( 例如 Ramax0.8)
即:F1+F2+…+Fn= G1+G2+…+Gm
F
1
F
2
y=f(x)
Fn
0 G1 G2 L Gm
x
轮廓参数
轮廓参数,与GB/T 3505标准相关的参数 有: —R轮廓(粗糙度参数); —W轮廓(波纹度参数);
—P轮廓(原始轮廓参数)。
评定表面结构常用的参数(三大参数)
轮廓参数( 由 GB/T35052000 定义)
表面加工纹理方向:指表面微观结构的主要方向,由所采 用的加工方法或其它因素形成,必要时才规定。
表面粗糙度参数的选用
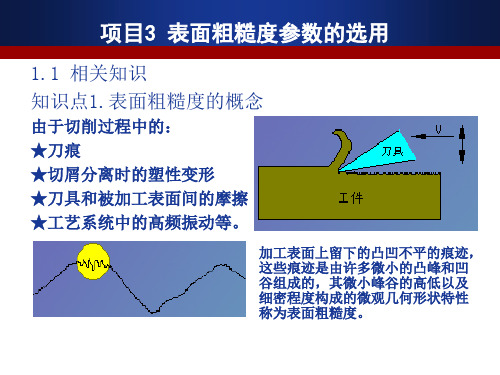
在一个取样长度lr 内,最大轮廓峰高zp 和最பைடு நூலகம்轮廓谷深zv之和的高
度。
用公式表示为 Rz =zp +zv
轮廓的最大高度
项目3 表面粗糙度参数的选用
3)轮廓单元的平均宽度RSm (间距参数) 在一个取样长度lr 内,轮廓单元宽度xs 的平均值。
RSm
1 m
m i 1
Xsi
轮廓单元的宽度
表面粗糙度轮廓单元
项目3 表面粗糙度参数的选用
2.表面粗糙度评定参数
1)评定轮廓的算术平均偏差Ra(幅度参数) 即在一个取样长度lr 内,轮廓上各点至基准线的距离的绝对值
的算术平均值。如图所示。
Ra 1
l
y dx
l0
近似为 Ra 1
n
n i 1
yi
轮廓算术平均偏差
项目3 表面粗糙度参数的选用
算术平均中线 (面积和) i 1 i 1
F1
F2
Fi
F1′
Fi′
F2′
lr
表面粗造度轮的算术平均中线
项目3 表面粗糙度参数的选用
5)轮廓单元:即一个轮廓峰和其相邻的一个轮廓谷的组合。
● 轮廓峰高zp ● 轮廓谷深zv ● 轮廓单元的高度zt ● 轮廓单元的宽度xs
● 高度和间距辨别力:即应计入被评定轮廓的轮廓峰和轮廓谷的最小高 度和最小间距。
匀性差,可选ln>5lr。
取样长度与评定长度
项目3 表面粗糙度参数的选用
lr和ln的数值
Ra /μm
Rz /μm lr /mm ln /mm(ln =5lr )
≥0.008~0.02 >0.02~0.1
≥0.025~ 0.10
表面粗糙度的选用
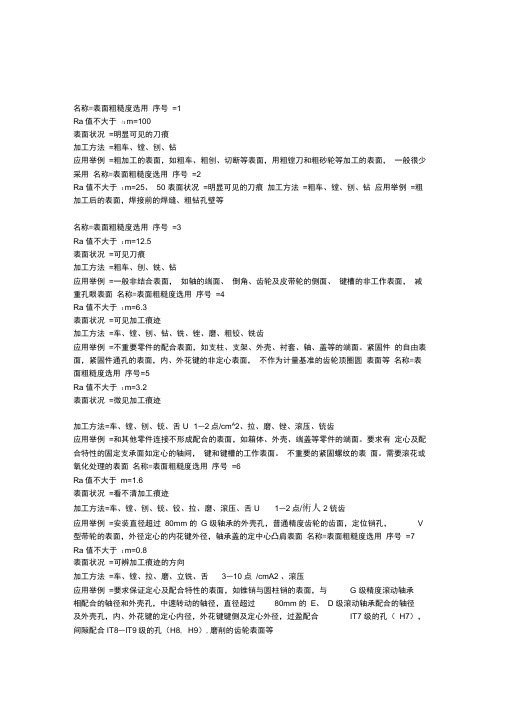
名称=表面粗糙度选用序号=1Ra值不大于(1 m=100表面状况=明显可见的刀痕加工方法=粗车、镗、刨、钻应用举例=粗加工的表面,如粗车、粗刨、切断等表面,用粗镗刀和粗砂轮等加工的表面,一般很少采用名称=表面粗糙度选用序号=2Ra 值不大于 1 m=25、50 表面状况=明显可见的刀痕加工方法=粗车、镗、刨、钻应用举例=粗加工后的表面,焊接前的焊缝、粗钻孔壁等名称=表面粗糙度选用序号=3Ra 值不大于 1 m=12.5表面状况=可见刀痕加工方法=粗车、刨、铣、钻应用举例=一般非结合表面,如轴的端面、倒角、齿轮及皮带轮的侧面、键槽的非工作表面,减重孔眼表面名称=表面粗糙度选用序号=4Ra 值不大于 1 m=6.3表面状况=可见加工痕迹加工方法=车、镗、刨、钻、铣、锉、磨、粗铰、铣齿应用举例=不重要零件的配合表面,如支柱、支架、外壳、衬套、轴、盖等的端面。
紧固件的自由表面,紧固件通孔的表面,内、外花键的非定心表面,不作为计量基准的齿轮顶圈圆表面等名称=表面粗糙度选用序号=5Ra 值不大于 1 m=3.2表面状况=微见加工痕迹加工方法=车、镗、刨、铳、舌U 1〜2点/cm A2、拉、磨、锉、滚压、铳齿应用举例=和其他零件连接不形成配合的表面,如箱体、外壳、端盖等零件的端面。
要求有定心及配合特性的固定支承面如定心的轴间,键和键槽的工作表面。
不重要的紧固螺纹的表面。
需要滚花或氧化处理的表面名称=表面粗糙度选用序号=6Ra值不大于m=1.6表面状况=看不清加工痕迹加工方法=车、镗、刨、铳、铰、拉、磨、滚压、舌U 1〜2点/術人2铳齿应用举例=安装直径超过80mm 的G 级轴承的外壳孔,普通精度齿轮的齿面,定位销孔,V 型带轮的表面,外径定心的内花键外径,轴承盖的定中心凸肩表面名称=表面粗糙度选用序号=7 Ra 值不大于 1 m=0.8表面状况=可辨加工痕迹的方向加工方法=车、镗、拉、磨、立铣、舌3〜10 点/cmA2 、滚压应用举例=要求保证定心及配合特性的表面,如锥销与圆柱销的表面,与G 级精度滚动轴承相配合的轴径和外壳孔,中速转动的轴径,直径超过80mm 的E、 D 级滚动轴承配合的轴径及外壳孔,内、外花键的定心内径,外花键键侧及定心外径,过盈配合IT7 级的孔(H7),间隙配合IT8〜IT9级的孔(H8, H9),磨削的齿轮表面等名称=表面粗糙度选用 序号 =8Ra 值不大于 1 m=0.4表面状况 =微辨加工痕迹的方向加工方法 =铰、磨、镗、拉、舌 3〜10 点 /cmA2 、滚压应用举例 =要求长期保持配合性质稳定的配合表面, IT7 级的轴、 孔配合表面, 精度较高的齿 轮表面,受变应力作用的重要零件,与直径小于 80mm 的 E 、 D 级轴承配合的轴径表面、与 橡胶密封件接触的轴的表面,尺寸大于120mm 的IT13〜IT16级孔和轴用量规的测量表面 名称=表面粗糙度选用 序号 =9Ra 值不大于 1 m=0.2表面状况 =不可辨加工痕迹的方向加工方法 =布轮磨、磨、研磨、超级加工应用举例 =工作时受变应力作用的重要零件的表面。
表面粗糙度选用
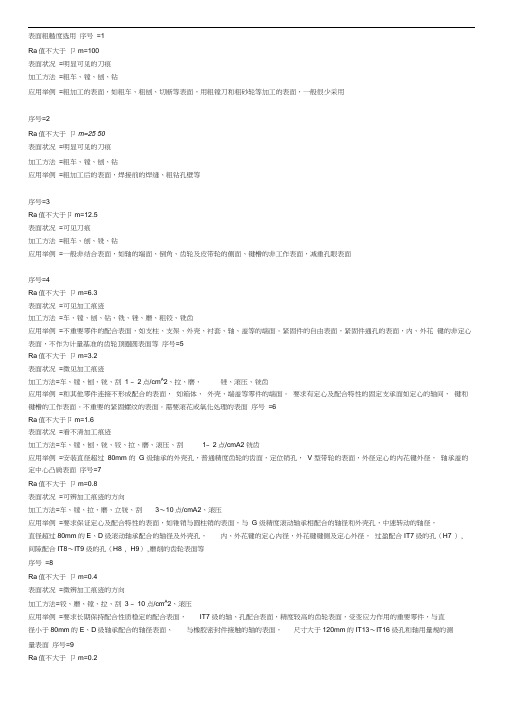
表面粗糙度选用序号=1Ra值不大于卩m=100表面状况=明显可见的刀痕加工方法=粗车、镗、刨、钻应用举例=粗加工的表面,如粗车、粗刨、切断等表面,用粗镗刀和粗砂轮等加工的表面,一般很少采用序号=2Ra值不大于卩m=25 50表面状况=明显可见的刀痕加工方法=粗车、镗、刨、钻应用举例=粗加工后的表面,焊接前的焊缝、粗钻孔壁等序号=3Ra值不大于卩m=12.5表面状况=可见刀痕加工方法=粗车、刨、铣、钻应用举例=一般非结合表面,如轴的端面、倒角、齿轮及皮带轮的侧面、键槽的非工作表面,减重孔眼表面序号=4Ra值不大于卩m=6.3表面状况=可见加工痕迹加工方法=车、镗、刨、钻、铣、锉、磨、粗铰、铣齿应用举例=不重要零件的配合表面,如支柱、支架、外壳、衬套、轴、盖等的端面。
紧固件的自由表面,紧固件通孔的表面,内、外花键的非定心表面,不作为计量基准的齿轮顶圈圆表面等序号=5Ra值不大于卩m=3.2表面状况=微见加工痕迹加工方法=车、镗、刨、铳、刮 1 ~ 2点/cm A2、拉、磨、锉、滚压、铳齿应用举例=和其他零件连接不形成配合的表面,如箱体、外壳、端盖等零件的端面。
要求有定心及配合特性的固定支承面如定心的轴间,键和键槽的工作表面。
不重要的紧固螺纹的表面。
需要滚花或氧化处理的表面序号=6Ra值不大于卩m=1.6表面状况=看不清加工痕迹加工方法=车、镗、刨、铳、铰、拉、磨、滚压、刮1~ 2点/cmA2铳齿应用举例=安装直径超过80mm 的G 级轴承的外壳孔,普通精度齿轮的齿面,定位销孔,V 型带轮的表面,外径定心的内花键外径,轴承盖的定中心凸肩表面序号=7Ra值不大于卩m=0.8表面状况=可辨加工痕迹的方向加工方法=车、镗、拉、磨、立铳、刮3〜10点/cmA2、滚压应用举例=要求保证定心及配合特性的表面,如锥销与圆柱销的表面,与G 级精度滚动轴承相配合的轴径和外壳孔,中速转动的轴径,直径超过80mm的E、D级滚动轴承配合的轴径及外壳孔,内、外花键的定心内径,外花键键侧及定心外径,过盈配合IT7级的孔(H7 ), 间隙配合IT8〜IT9级的孔(H8 , H9),磨削的齿轮表面等序号=8Ra值不大于卩m=0.4表面状况=微辨加工痕迹的方向加工方法=铰、磨、镗、拉、刮 3 ~ 10点/cm A2、滚压应用举例=要求长期保持配合性质稳定的配合表面,IT7 级的轴、孔配合表面,精度较高的齿轮表面,受变应力作用的重要零件,与直径小于80mm的E、D级轴承配合的轴径表面、与橡胶密封件接触的轴的表面,尺寸大于120mm的IT13〜IT16级孔和轴用量规的测量表面序号=9Ra值不大于卩m=0.2表面状况=不可辨加工痕迹的方向加工方法=布轮磨、磨、研磨、超级加工应用举例=工作时受变应力作用的重要零件的表面。
表面粗糙度与检测(新国标)

传输带
补充要求
取样长度 加工工艺
加工余量等。
表面粗糙度要求标注的内容在图中注写的位置,见图 5.10所示。
图5.10 粗糙度要求的注写的位置
a —第一个表面粗糙度(单一)要求(μm); b — 第二个表面粗糙度要求(μm); c — 加工方法(车,铣); d— 表面纹理和纹理方向; e— 加工余量(mm)。
② 传输带和取样长度 的标注:传输带是指 两个滤波器的截止波 长值之间的波长范围。 长波滤波器的截止波
长值就是取样长度ln。
图5.11 表面粗糙度的单一要求标注示例
传输带的标注时,短波在前,长波在后,并用连字号“—”隔开。 在某些情况下,传输带的标注中,只标一个滤波器,也应保留连字号 “—” ,来区别是短波还是长波。
(4)影响抗腐蚀性;
5.2 表面粗糙度的评定
一. 基本术语 1. 取样长度 lr----基准线长度。至少含5个波峰和波谷 2. 评定长度ln--最小的测量长度。至少包括5个取样长度lr
图5.4 取样长度和评定长度
3. 中线—指具有几何轮廓形状并划分轮廓的基准线 轮廓算术平均中线:在取样长度内,划分实际轮廓为上、 下两部分面积相等的线
3. 表面粗糙度要求在图样上的标注方法
标注方向与 尺寸相同
指引线上标 注
3. 表面粗糙度要求在图样上的标注方法
标注在几 何公差框
格上方
标注在延 长线上
3. 表面粗糙度要求在图样上的标注方法
其余要求标注在标题 栏附近
(给出基本符号)
3. 表面粗糙度要求在图样上的标注方法
全部要求标 注在标题栏
3. 混合参数(形状参数) 轮廓的支承长度率Rmr(C) —
在给定的水平位置C上,轮廓的实体材料长度Ml(C)与评定长度ln的比率。
表面粗糙度的评定参数及其数值的选用

a
c)
tp70%、C50%
a
a
b)
Sm0.05max
d)
tp70%min、C50%
其他各项规定的标注.2
③、加工纹理方向、加工方法的标注
纹理方向符号见表5-9。
铣
a
a
⊥
表5-15 表面加工纹理的标注
二、表面粗糙度要求的图样标注
表面粗糙度符号、代号一般标注在可见轮 廓线、尺寸界线、引出线或其延长线上, 见图5-16、5-17。
符号的尖端必须从材料外指向被注表面。 符号、数字的方向按规定标注。
12.5 12.5
图5-16 表面粗糙度代号注法
3.2 30º 3.2
3.2 30º 3.2
图5-17 表面粗糙度在图样上的标注
3.2 3.2
C×45º
3.2 0.4
φ
1.6 1.6
φ
3.2 M
12.5
φ
12.5
表面粗糙度重复表面的注法
0.8~1.6
0.8
1.6
0.8 0.8~1.6
1.6 1.6~3.2
表5-7 常用表面粗糙度的参数值.2
公差等级
装
配
IT5
按
机 械
IT6至IT7
压
入
IT8
法
热装法
过盈配合的配合表面
基本尺寸/mm
表面
~50
>50~120 >120~500
Ra
轴
0.1~0.2
0.4
0.4
孔
0.2~0.4
0.8
0.8
⑸、配合零件的表面粗糙度应与尺寸公差 及形状公差相协调,一般尺寸公差和形 状公差要求越严, Ra数值越小。
表面粗糙度参数值的选用原则

表面粗糙度参数值的选用原则1. 引言表面粗糙度是指物体表面的凹凸不平程度,对于许多工程应用来说,表面粗糙度是一个重要的质量指标。
通过选择合适的表面粗糙度参数值,可以确保产品的性能、功能和使用寿命。
本文将介绍表面粗糙度参数值的选用原则,包括定义和计算表面粗糙度的方法、常用的表面粗糙度参数以及选用参数值的考虑因素。
2. 表面粗糙度的定义和计算方法表面粗糙度是指物体表面在微观尺寸上存在的凹凸不平程度。
常见的表面粗糙度计算方法包括光学法、机械法和电子扫描法等。
光学法是通过光线反射来测量物体表面的凹凸不平程度,常用的光学仪器有显微镜和投影仪等。
机械法是利用机械探针或测头来测量物体表面的高低起伏,常见的仪器有激光干涉仪和形貌仪等。
电子扫描法是利用电子束或激光束扫描物体表面,通过探测器接收反射或散射的信号来测量表面粗糙度,常见的仪器有原子力显微镜和扫描电子显微镜等。
3. 常用的表面粗糙度参数表面粗糙度参数是用来描述表面粗糙度特征的数值指标。
常用的表面粗糙度参数包括以下几种:3.1 平均粗糙度(Ra)平均粗糙度是指在一定测量长度内,物体表面所有凹凸不平程度的平均值。
Ra是最常用的表面粗糙度参数之一,通常以微米(μm)为单位。
3.2 最大峰高(Ry)最大峰高是指物体表面上最高峰与最低谷之间的距离。
Ry可以用来评估物体表面的极端不平程度,通常以微米(μm)为单位。
3.3 峰谷高差(Rz)峰谷高差是指物体表面上相邻峰和谷之间的距离差异。
Rz可以用来评估物体表面的起伏程度,通常以微米(μm)为单位。
3.4 峰谷平均高差(RzJIS)峰谷平均高差是指在一定测量长度内,物体表面相邻峰和谷之间距离差异的平均值。
RzJIS是日本工业标准(JIS)中定义的表面粗糙度参数,通常以微米(μm)为单位。
3.5 峰值密度(S)峰值密度是指在一定测量长度内,物体表面上峰和谷的数量。
S可以用来评估物体表面的密集程度。
4. 表面粗糙度参数值的选用原则选择合适的表面粗糙度参数值需要考虑多个因素,包括产品功能要求、制造成本、加工工艺和材料特性等。
4.3表面粗糙度数值的选择及检测

三、表面粗糙度轮廓参数允许值的选择原则:
在满足零件表面功能要求的前提下,尽量选取较大的参数值。 (1)同一零件上工作表面粗糙度值,比非工作表面粗糙度值小。
工作表面
非工作表面
(2)摩擦表面粗糙度值比非摩擦表面粗糙度值小; 滚动摩擦表面比滑动摩擦表面的表面粗糙度参数值要小; 运动速度高、压力大的摩擦表面比运动速度低、压力小的摩擦
4-3 R轮廓参数的选用及其检测
一.表面粗糙度轮廓技术要求的内容
1、必须标注参数符号及允许值,同时还应标注传输带、取样长 度、评定长度的数值(若默认采用标准化值,则不标注)、极限 值判断规则(若默认采用16%规则,则不标注)。
2、必要时可以标注补充要求,如表面加工纹理及方向、加工余量、 附加的Rsm等。
表面的粗糙度参数值要小。
(3)受循环载荷的数值要小。
(4)配合要求高的结合表面、配合间隙小的配合表面及要求连接 可靠且受重载的过盈配合表面,均应取较小的粗糙度参数值。
(5)配合性质相同时,一般情况下,零件尺寸越小,则表面粗糙 度参数值应越小;在同一精度等级时,小尺寸比大尺寸,轴比孔 的表面粗糙度参数值要小;尺寸公差,表面形状公差小时,其表 面粗糙度参数值要小。
二.表面粗糙度轮廓参数的选择
1、通常只给出幅度参数符号(Ra或Rz)及极限值,而其他要求则 采用默认的标准化值。
2 、 一般采用Ra 作为评定参数。对于极光滑和粗糙的表面和零件材料 较软时,不能用Ra仪器测量,而采用Rz作为评定参数。
3 、 附加参数Rsm用于密封性要求高的表面,Rmr(c)用于耐磨性 要求高的表面。
(6)防腐性、密封性要求越高,表面粗糙度参数值应越小。
四、表面粗糙度轮廓常用测量方法
比较法 针描法 光切法 显微干涉法
表面粗糙度的选择
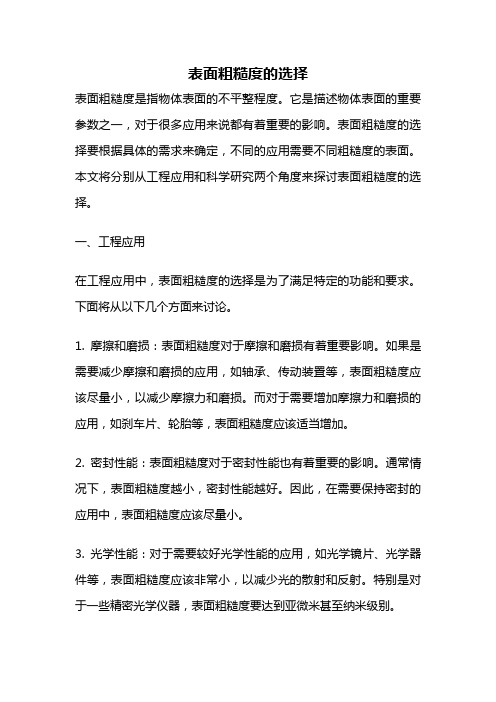
表面粗糙度的选择表面粗糙度是指物体表面的不平整程度。
它是描述物体表面的重要参数之一,对于很多应用来说都有着重要的影响。
表面粗糙度的选择要根据具体的需求来确定,不同的应用需要不同粗糙度的表面。
本文将分别从工程应用和科学研究两个角度来探讨表面粗糙度的选择。
一、工程应用在工程应用中,表面粗糙度的选择是为了满足特定的功能和要求。
下面将从以下几个方面来讨论。
1. 摩擦和磨损:表面粗糙度对于摩擦和磨损有着重要影响。
如果是需要减少摩擦和磨损的应用,如轴承、传动装置等,表面粗糙度应该尽量小,以减少摩擦力和磨损。
而对于需要增加摩擦力和磨损的应用,如刹车片、轮胎等,表面粗糙度应该适当增加。
2. 密封性能:表面粗糙度对于密封性能也有着重要的影响。
通常情况下,表面粗糙度越小,密封性能越好。
因此,在需要保持密封的应用中,表面粗糙度应该尽量小。
3. 光学性能:对于需要较好光学性能的应用,如光学镜片、光学器件等,表面粗糙度应该非常小,以减少光的散射和反射。
特别是对于一些精密光学仪器,表面粗糙度要达到亚微米甚至纳米级别。
4. 粘附性能:表面粗糙度对于粘附性能也有着重要的影响。
通常情况下,表面粗糙度越大,粘附性能越好。
因此,在需要增强粘附性能的应用中,表面粗糙度应该适当增加。
二、科学研究在科学研究中,表面粗糙度的选择往往是为了实现特定的实验目的或研究需求。
下面将从以下几个方面来讨论。
1. 表面特性研究:对于研究物体表面特性的科学研究来说,表面粗糙度的选择要根据具体实验目的来确定。
比如,如果是研究表面形貌的变化规律,需要选择不同粗糙度的表面进行研究。
2. 表面改性:对于研究表面改性的科学研究来说,表面粗糙度的选择要根据具体的改性效果来确定。
比如,如果是研究表面涂层对材料性能的影响,需要选择不同粗糙度的表面进行研究。
3. 表面测量:对于表面测量的科学研究来说,表面粗糙度的选择要根据测量仪器的要求来确定。
不同的测量仪器对表面粗糙度的要求不同,需要选择适合的表面粗糙度进行测量。
表面粗糙度参数值选用
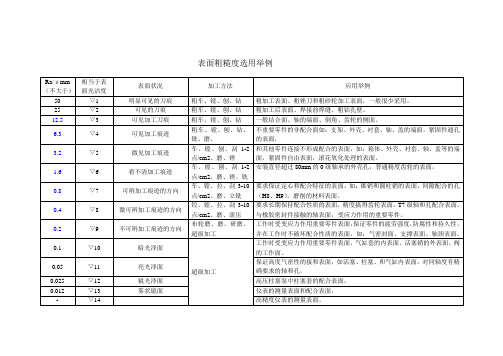
▽4
可见加工痕迹
粗车、镗、刨、钻、铣、磨、
不重要零件的非配合面如:支架、外壳、衬套、轴、盖的端面,紧固件通孔的表面,
3.2
▽5
m2、磨、锉
和其他零件连接不形成配合的表面,如:箱体、外壳、衬套、轴、盖等的端面,紧固件自由表面,滚花氧化处理的表面。
1.6
▽6
看不清加工痕迹
0.1
▽10
暗光泽面
超级加工
工作时受变应力作用重要零件表面,气缸套的内表面、活塞销的外表面、阀的工作面、
0.05
▽11
亮光泽面
保证高度气密性的接和表面,如活塞、柱塞、和气缸内表面,对同轴度有精确要求的轴和孔,
0.025
▽12
镜光泽面
高压柱塞泵中柱塞套的配合表面,
0.012
▽13
雾状镜面
仪表的测量表面和配合表面,
铰、镗、拉、刮3-10点/cm2、磨、滚压
要求长期保持配合性质的表面,精度搞得齿轮表面,T7级轴和孔配合表面,与橡胶密封件接触的轴表面,受应力作用的重要零件。
0.2
▽9
不可辨加工痕迹的方向
布轮磨、磨、研磨、超级加工
工作时受变应力作用重要零件表面,保证零件的疲劳强度,防腐性和持久性,并在工作时不破坏配合性质的表面,如:气密封面、支撑表面、轴颈表面。
Ra/μmm
(不大于)
相当于表面光洁度
表面状况
加工方法
应用举例
50
▽1
明显可见的刀痕
粗车、镗、刨、钻
粗加工表面、粗锉刀和粗砂轮加工表面,一般很少采用。
25
▽2
可见的刀痕
粗车、镗、刨、钻
粗加工后表面、焊接前焊缝、粗钻孔壁。
表面粗糙度数值的选择

3.具体选择参数值时应注意: (1)同一零件上,工作表面粗糙度值小于非工作表面。 (2)摩擦表面粗糙度值小于非摩擦表面。 (3)运动速度高、单位面积压力大,以及受交变应力作用 的钢质零件圆角、沟槽处、应有较小的粗糙度。 (4)配合性质要求高的配合表面,如小间隙的配合表面, 受重载荷作用的过盈配合表面,都应有较小的表面粗糙度。 (5)尺寸精度要求高时,参数值应相应地取得小。 (6)有关标注已对表面粗糙度要求作出规定的,应安相应 标准确定表面粗糙度值。例有关圆柱体结合的表面粗糙度 数值的选用,见教材P100表3-7。
公差配合与测量技术
公差配合与测量技术表面粗糙度 Nhomakorabea值的选择
确定零件表面粗糙度时,既要满足零件表面的功能要求, 又要考虑工艺的可行性和经济性。
表面粗糙度选择包括参数选择和参数值的选择。 1.参数选取的原则
确定表面粗糙度时,可在三项高度特性方面的参数 (Ra、Rz、Ry)中选取,只有当高度参数不能满足表面 的功能要求时,才选取附加参数作为附加项目。 2.高度参数值选择原则 在满足零件表面使用功能前提下,应尽量选用大的参数值。
表面粗糙度的选择方法

表面粗糙度的选择方法表面粗糙度(surface roughness)是指加工表面具有的较小间距和微小峰谷的不平度。
其两波峰或两波谷之间的距离(波距)很小(在1mm以下),它属于微观几何形状误差。
表面粗糙度越小,则表面越光滑。
表面粗糙度一般是由所采用的加工方法和其他因素所形成的,例如加工过程中刀具与零件表面间的摩擦、切屑分离时表面层金属的塑性变形以及工艺系统中的高频振动等。
由于加工方法和工件材料的不同,被加工表面留下痕迹的深浅、疏密、形状和纹理都有差别。
表面粗糙度与机械零件的配合性质、耐磨性、疲劳强度、接触刚度、振动和噪声等有密切关系,对机械产品的使用寿命和可靠性有重要影响。
一般标注采用Ra。
相关的规范有"GB/T 1031-2009《表面结构轮廓法表面粗糙度参数及其数值》"和"GB/T 131-2006 (ISO 1302:2002)《表面结构的表示法》"。
表面粗糙度是反映零件表面微观几何形状误差的一个重要技术指标,是检验零件表面质量的主要依据;它选择的合理与否,直接关系到产品的质量、使用寿命和生产成本。
机械零件表面粗糙度的选择方法有3种,即计算法、试验法和类比法。
在机械零件设计工作中,应用最普通的是类比法,此法简便、迅速、有效。
最常用的是与公差等级相适应的表面粗糙度。
在通常情况下,机械零件尺寸公差要求越小,机械零件的表面粗糙度值也越小,但是它们之间又不存在固定的函数关系。
在实际工作中,对于不同类型的机器,其零件在相同尺寸公差的条件下,对表面粗糙度的要求是有差别的。
这就是配合的稳定性问题。
在机械零件的设计和制造过程中,对于不同类型的机器,其零件的配合稳定性和互换性的要求是不同的。
在现有的机械零件设计手册中,反映的主要有以下3种类型:第1类主要用于精密机械,对配合的稳定性要求很高,要求零件在使用过程中或经多次装配后,其零件的磨损极限不超过零件尺寸公差值的10%,这主要应用在精密仪器、仪表、精密量具的表面、极重要零件的摩擦面,如汽缸的内表面、精密机床的主轴颈、坐标镗床的主轴颈等。
模具零件的表面粗糙度要求

使用范围 抛光的转动体表面
粗糙度数值(μ m) GB1031-83(新标准)
0.,0.4
1.压弯、拉深、成形的凸模和凹模工作表面 2.圆柱表面和平面的刃口 3.滑动和精确导向的表面
1.成形的凸模和凹模刃口;凸模凹模镶块的结合面 2.过盈配合和过渡配合的表面——用于热处理零件 3.支承定位和紧固表面——用于热处理零件 4.磨加工的基准面;要求准确的工艺基准表面
模具零件的表面粗 糙度要求
模具零件表面质量的高低用表面粗糙度衡量,通常以 Ra(µm)表示。Ra 数值愈小,表示其表 面质量愈高。 模具零件的工作性能如耐磨性、抗蚀性及强度等,在很大程度上受其表面质量的影响。模具 零件的表面质量越高,其寿命也越长。 但从另一方面看,对模具零件表面质量要求过高,则增加了模具制造成本。 因此,应合理选用模具零件的表面粗糙度。模具零件常用的表面粗糙度要求列于下表,可供 模具设计时参考。
1.内孔表面——在非热处理零件上配合用 2.模座平面
1.不磨加工的支承、定位和紧固表面——用于非热 处理的零件
2.模座平面
不与冲压制件及模具零件接触的表面
0.4,0.8 0.8,1.6 1.6,3.2 3.2,6.3 6.3,12.5
粗糙的不重要表面
12.5,25
不需机械加工的表面
- 1、下载文档前请自行甄别文档内容的完整性,平台不提供额外的编辑、内容补充、找答案等附加服务。
- 2、"仅部分预览"的文档,不可在线预览部分如存在完整性等问题,可反馈申请退款(可完整预览的文档不适用该条件!)。
- 3、如文档侵犯您的权益,请联系客服反馈,我们会尽快为您处理(人工客服工作时间:9:00-18:30)。
特别精密的滚动轴承套圈滚道,钢球及滚子表面;量仪中的中等精度间隙配合零件的工作表面;工作量规的测量表面;摩擦离合器的摩擦表面等
光
微辨
中型机床(普通精度)滑动导轨面,圆柱销,圆锥销和滚动轴承配合的表面;中速转动的轴颈;内、外花键的定心表面等
0.2-0.4
不可辨
夹具定位元件和钻套的主要表面,曲轴和凸轮轴等高速转动的轴颈;工作时受交变应力的重要零件;中型机床(提高精度)滑动导轨面和/P5级滚动轴承配合的表面
0.1-0.2
极光表面
暗光泽面
精密机床主轴锥孔,顶尖圆锥面,高精度齿轮工作表面;和/P4级滚动轴承配合的表面;液压油缸和柱塞的表面;曲轮、凸轮轴的工作表面等
0.05-0.1
亮光泽面
精密机床主轴箱与套筒配合的孔;仪器中承受摩擦的表面,如导轨、槽面等;液压传动用孔的表面,阀的工作表面,汽缸内表面,活塞销的表面
0.025-0.05
表面粗糙度值的选用
表面粗糙度值的选用实例
使用时代TR200粗糙度仪测量时需要选定取样长度,这又牵涉到被测工件本身的粗糙度范围,摘编本表就是希望对此有帮助。
Ra/μm
表面微观特征
应用实例
3.2-6.3
半光表面
微见加工痕迹
半精加工面、支架、轴、衬套端面、带轮、凸轮侧面等非接触的自由表面,所有轴和孔的退刀槽,不重要的铰接配合表面等
1.6-3.2
箱体、箱盖、支架、套筒等和其他零件结合而无配合要求的表面,定心的轴肩,键和键槽,低速工作的滑动轴承和轴颈的工作面,张紧链轮,导向滚轮壳孔与轴的配合表面
0.8、滑动轴承和定位销的压入孔表面,花键的定心表面;带轮槽,一般低速传动的轴颈;电镀前的金属表面
0.4-0.8