高炉炉渣余热回收技术的研究进展_王波
高炉冲渣余热回收的试验研究与利用分析

s l a g w a t e r ,a d e t a i l e d d e t e r mi n a t i o n a n d t h e o r e t i c a l a n a l y s i s a n d c a l c u l a t i o n o f e n e r g y h a s
余热 回收的可行性 , 获得 了第 一手 的试验数据 , 为后期高炉冲渣余热 回收和低品质蒸汽的回收奠定 了基础。
【 关键词】 高炉冲渣; 余热利用 ; 能源诊断; 试验研究 【 中图分类号】 T K l l 5 【 文献标识码】B 【 文章编号] 1 0 0 6 — 6 7 6 4 ( 2 0 1 3 ) 0 7 — 0 0 4 3 — 4 0
b e e n ma d e .T h e s ma l l s c a l e t e s t s h a v e b e e n c o n d u c t e d .T h e c o mp a r i s o n o f t h e t h e o r e t i c a l
me n t a l i n v e s t i g a t i o n
1 引 言
近 几 年 国家倡 导循 环 经 济 和 可 持 续 发 展 的方
性及和冲渣水换热器的结构形式是否能够满足今后 冲渣水取热( 降温 ) 的要求 , 同时解决当前高炉区域 蒸汽外 冒影响环境的现象 ,特进行了小规模 的试验
高炉炼铁过程中废渣资源化利用的技术创新

高炉炼铁过程中废渣资源化利用的技术创新由于工业化的快速发展,高炉炼铁已成为现代钢铁工业中不可或缺的环节。
然而,传统的炼铁过程会产生大量的废渣,给环境带来严重污染。
为了实现可持续发展,推动高炉炼铁过程中废渣资源化利用的技术创新势在必行。
本文将探讨当前废渣资源化利用的现状和趋势,并提出一些创新的技术解决方案。
一、废渣资源化利用的现状高炉炼铁过程中主要产生的废渣主要包括烧结矿、烟气净化渣和炉渣等。
这些废渣通常被视为浪费物料,被丢弃或填埋,给环境带来负面影响。
然而,废渣中含有很多有价值的可回收物质,如铁、钢、矿物等。
因此,将废渣转化为可再利用的资源是一种解决环境问题和实现可持续发展的有效途径。
目前,废渣资源化利用主要通过以下几种方式实现:1. 废渣回收再利用:将废渣中的有价值物质进行分离和提取,重新利用于炼铁过程或其他工业生产中。
例如,烧结矿中的铁含量较高,可以再次用于高炉冶炼过程中。
2. 废渣填充利用:将废渣用于填充坑道、道路建设和土地复垦等工程中。
废渣填充可以减少对自然资源的占用,同时改善了被填充地区的土壤质量。
3. 废渣综合利用:将不同种类的废渣进行混合利用,形成新的产品或材料。
例如,烟气净化渣中的硅酸盐可以与矿产废渣混合制备建筑材料。
尽管废渣资源化利用取得了一定的进展,但仍面临一些挑战。
首先,目前的废渣资源化利用技术还不够成熟,存在成本高、技术路线不清晰等问题。
其次,相关政策法规的缺失和监管体系不健全也制约了废渣资源化利用的发展。
二、废渣资源化利用的技术创新为了推动高炉炼铁过程中废渣资源化利用的发展,需要进行技术创新和研发。
以下是一些可行的技术创新方案:1. 废渣熔融处理技术:通过高炉炼铁过程中炉渣的熔融处理,将废渣转化为玻璃状物质。
这种熔融处理技术可以减少废渣体积,提高废渣中有价值物质的回收率,并且可以将熔融后的产品用于建筑材料或其他工业领域。
2. 废渣碳化技术:利用废渣中的碳含量,将其进行碳化处理,生成高价值的碳材料。
高炉熔渣余热回收技术发展过程及趋势

高炉熔渣余热回收技术发展过程及趋势随着工业化进程的不断发展,高炉熔渣余热回收技术也在不断地发展和完善。
本文将从技术发展的历程和未来趋势两方面来探讨高炉熔渣余热回收技术的发展。
一、技术发展的历程高炉熔渣余热回收技术是一种利用高炉熔渣余热进行能量回收的技术。
它的发展历程可以分为以下几个阶段:1、初期阶段高炉熔渣余热回收技术最初是在20世纪初期开始出现的。
当时,人们主要采用的是换热器来回收高炉熔渣的余热。
然而,这种技术存在着很多问题,例如换热器的效率低、易受污染等。
2、中期阶段20世纪50年代,人们开始尝试采用“干法”和“湿法”两种方式来回收高炉熔渣的余热。
其中,“干法”主要是采用热风炉或热气轮机等设备来回收余热,而“湿法”则是采用热水或蒸汽等介质来回收余热。
这些技术在当时已经相对成熟,但仍存在着一些问题,如能量回收效率低、设备成本高等。
3、现代阶段进入21世纪后,高炉熔渣余热回收技术得到了更加广泛的应用和推广。
此时,人们开始采用先进的技术手段,如热泵、超临界流体回收等,来提高余热回收效率和设备的可靠性。
同时,人们也开始注重技术的环保性和经济性,力求实现能源的可持续利用。
二、未来趋势未来,高炉熔渣余热回收技术将呈现以下几个趋势:1、高效化随着科技的不断进步,高炉熔渣余热回收技术的效率将会得到进一步提高。
未来,人们将会采用更加先进的技术手段,如超临界流体回收、热泵等,来提高余热回收效率,实现更加高效的能量回收。
2、环保化在未来,高炉熔渣余热回收技术将更加注重环保性。
人们将会采用更加环保的技术手段,如低温余热回收、废热再利用等,来减少对环境的污染,实现绿色能源的利用。
3、智能化未来,高炉熔渣余热回收技术将更加智能化。
人们将会采用先进的智能控制系统,来实现设备的自动化操作和监控。
同时,人们也将会利用大数据和人工智能等技术,对设备的运行状态进行实时监测和分析,以实现设备的优化运行和维护。
总之,高炉熔渣余热回收技术是一项非常重要的能源回收技术。
高炉冲渣水余热回收技术的创新与应用
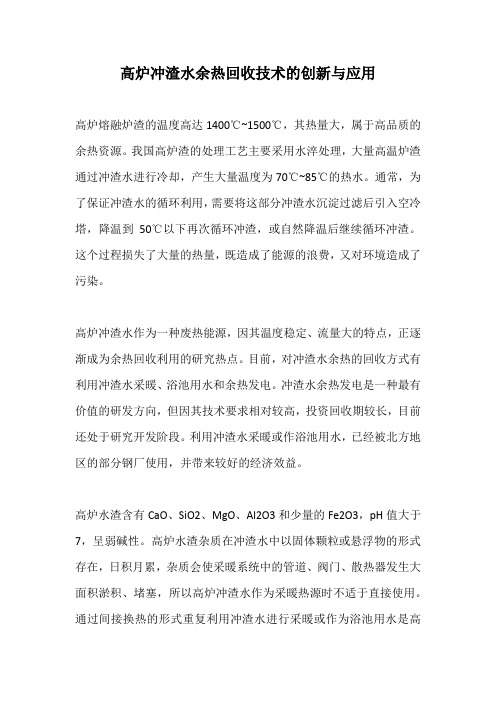
高炉冲渣水余热回收技术的创新与应用高炉熔融炉渣的温度高达1400℃~1500℃,其热量大,属于高品质的余热资源。
我国高炉渣的处理工艺主要采用水淬处理,大量高温炉渣通过冲渣水进行冷却,产生大量温度为70℃~85℃的热水。
通常,为了保证冲渣水的循环利用,需要将这部分冲渣水沉淀过滤后引入空冷塔,降温到50℃以下再次循环冲渣,或自然降温后继续循环冲渣。
这个过程损失了大量的热量,既造成了能源的浪费,又对环境造成了污染。
高炉冲渣水作为一种废热能源,因其温度稳定、流量大的特点,正逐渐成为余热回收利用的研究热点。
目前,对冲渣水余热的回收方式有利用冲渣水采暖、浴池用水和余热发电。
冲渣水余热发电是一种最有价值的研发方向,但因其技术要求相对较高,投资回收期较长,目前还处于研究开发阶段。
利用冲渣水采暖或作浴池用水,已经被北方地区的部分钢厂使用,并带来较好的经济效益。
高炉水渣含有CaO、SiO2、MgO、Al2O3和少量的Fe2O3,pH值大于7,呈弱碱性。
高炉水渣杂质在冲渣水中以固体颗粒或悬浮物的形式存在,日积月累,杂质会使采暖系统中的管道、阀门、散热器发生大面积淤积、堵塞,所以高炉冲渣水作为采暖热源时不适于直接使用。
通过间接换热的形式重复利用冲渣水进行采暖或作为浴池用水是高炉冲渣水利用的技术点,而高炉冲渣水专用换热器适用于换热介质在高悬浮物、高黏度等恶劣工况下的实体应用。
冲渣水余热回收出利器冲渣水专用换热器是由螺旋状扁管换热元件制造而成的新型高效换热器,螺旋扁管的截面为椭圆形,其管内外流道均呈螺旋状,获得国家实用新型专利。
该换热器在使用过程中具有以下特点:压降小。
管壳式换热器在壳程为了减少死区和短路设置了一定数量的折流板,相应地增加了阻力,而螺旋扁管的应用使得壳程中介质的曲折流动变为直接螺旋流动,没有死区,不必设置折流板。
取消折流板降低了阻力,并大大提高了热传递效率。
冲渣水专用换热器和螺旋板式换热器的压降≤30kPa,而板式换热器和固定管板式换热器的压降均为50kPa~100kPa。
高炉熔渣干式显热回收技术研究进展

高炉熔渣干式显热回收技术研究进展
高炉熔渣干式显热回收技术研究进展
高炉熔渣含有大量的热,将其回收利用具有极大的经济和社会效益.传统的水淬工艺对熔渣显热基本没有回收,干式显热回收技术得到国内外研究者越来越多的关注.为此,分析了熔渣显热回收的基本问题和技术难点;列举了已研究的各种干式显热回收典型工艺;介绍了旋转杯熔渣粒化技术、水蒸汽-甲烷重整渣热回收技术等最新研究进展,对不同回收工艺进行了综合评价;并展望了熔渣显热回收技术的发展前景.
作者:徐永通丁毅蔡漳平刘青黄晔叶树峰XU Yong-tong DING Yi CAI Zhang-ping LIU Qing HUANG Ye YE Shu-feng 作者单位:徐永通,XU Yong-tong(中国科学院过程工程研究所,北京,100080;中国科学院研究生院,北京,100080)
丁毅,DING Yi(新余钢铁有限责任公司第一炼铁厂,江西,新余,338001)
蔡漳平,CAI Zhang-ping(济南钢铁集团总公司,山东,济南,250000) 刘青,黄晔,LIU Qing,HUANG Ye(北京科技大学冶金与生态工程学院,北京,100083)
叶树峰,YE Shu-feng(中国科学院过程工程研究所,北京,100080) 刊名:中国冶金英文刊名:CHINA METALLURGY 年,卷(期):2007 17(9) 分类号:X706 关键词:高炉熔渣干式粒化热回收旋转杯粒化甲烷-水蒸汽重整。
高炉富氢冶金渣余热回收及综合利用方案(二)

高炉富氢冶金渣余热回收及综合利用方案一、实施背景随着全球对能源和环境问题的关注度不断提高,钢铁工业作为高能耗、高排放的行业,急需进行产业结构改革和绿色发展。
高炉富氢冶金渣余热回收及综合利用是其中的重要环节。
本方案旨在通过开发高效、环保的富氢冶金渣余热回收技术,实现钢铁工业的节能减排和资源循环利用。
二、工作原理高炉富氢冶金渣余热回收及综合利用方案主要采用富氢冶金渣显热回收技术,通过热交换器将冶金渣中的余热转化为高压水蒸气,再利用蒸汽发电或者供热,实现能源的二次利用。
同时,蒸汽还可以用于生产过程中的其他环节,如石灰石分解、矿石焙烧等,进一步提高了能源利用效率。
三、实施计划步骤1. 收集高炉冶金渣:将高炉冶炼产生的冶金渣收集起来,准备下一步处理。
2. 渣水分离:将冶金渣中的水分和渣进行分离,得到富氢冶金渣。
3. 余热回收:将富氢冶金渣中的余热通过热交换器转化为高压水蒸气。
4. 蒸汽利用:将高压水蒸气用于发电、供热或者生产工艺中,实现能源的二次利用。
5. 渣综合利用:将渣进行综合利用,如制备微晶玻璃、生产矿渣水泥等。
四、适用范围本方案适用于钢铁企业中的高炉车间、烧结车间、连铸车间等,能够有效地将冶金渣中的余热回收利用,提高能源利用效率,同时减少环境污染。
五、创新要点1. 开发高效、环保的富氢冶金渣余热回收技术,提高能源回收率;2. 将回收的余热转化为高压水蒸气,再用于发电、供热或生产工艺中,实现能源的二次利用;3. 将冶金渣进行综合利用,制备微晶玻璃、矿渣水泥等高附加值产品;4. 采用先进的自动化控制系统,实现整个工艺流程的智能化控制,提高生产效率和产品质量;5. 针对不同车间的实际情况,提供个性化的解决方案,满足企业的实际需求。
六、预期效果1. 提高能源利用效率:通过回收冶金渣中的余热并二次利用,能够提高能源利用效率20%以上。
2. 减少环境污染:采用本方案能够减少冶金渣的排放量,减轻对环境的污染。
3. 降低生产成本:通过回收和二次利用能源,能够降低企业的生产成本,提高经济效益。
高炉渣余热湿法回收关键过程热质传输机理研究

高炉渣余热湿法回收关键过程热质传输机理探究关键词:高炉渣;余热回收;湿法;热质传输;关键过程。
一、引言高炉渣是钢铁产业过程中的一种重要工业废渣,其中包含的潜在余热资源极其巨大。
然而,传统的高炉渣处理方法往往会浪费掉这些可利用的余热。
因此,如何高效地回收高炉渣的余热已经成为了钢铁厂降低能耗和缩减环境污染的重要途径之一。
近年来,高炉渣湿法回收技术备受关注。
这种技术利用水分来降低高炉渣的温度,从而回收热能和有用的材料。
然而,高炉渣湿法回收技术还面临着一些挑战,如效率低下、能源消耗高、产品质量不稳定等问题。
如何进一步提高高炉渣湿法回收的效率和产品质量,成为了当前亟待解决的问题。
二、高炉渣湿法回收关键过程高炉渣湿法回收过程包括原料掺混、加湿、铺平、打硬等关键过程。
这些关键过程直接影响着高炉渣的品质和余热回见效率。
1.原料掺混:高炉渣湿法回收的原料包括高炉炉渣、石灰石、工业废渣等。
不同的原料掺混比例会对高炉渣的湿度、密度和成分产生影响。
因此,在制备高炉渣湿法回收原料时,应依据不同的产品要求和工艺流程,合理设计原料掺混比例。
2.加湿:高炉渣湿法回收需要通过加水来控制高炉渣的温度。
加湿水的温度和湿度将直接影响高炉渣的湿度和热传输效率。
加湿水不能太热或太冷,一般应保持在25℃左右。
同时,加湿应思量匀称性和稳定性,防止在高炉渣中形成水分不均的局部浸润。
3.铺平:铺平是高炉渣湿法回收过程中的一个重要步骤。
铺平过程中需要将高炉渣匀称地分布在回收设备上,同时压实高炉渣,以提高水分浸润的效率和余热回见效率。
铺平过程需要控制高炉渣的厚度和匀称性,防止出现厚薄不一或局部高的现象。
4.打硬:打硬是高炉渣湿法回收过程中的最后一步。
打硬可以缩减高炉渣在转运、堆放和加工过程中的松散度和粉尘产生。
同时,打硬后的高炉渣更有利于水分浸润和余热回见效率的提高。
打硬时需要防止毁伤高炉渣颗粒表面,影响其物理性质和化学活性。
三、影响高炉渣湿法回见效果的热质传输机理探究高炉渣湿法回收的关键在于利用水分来控制高炉渣的温度,并将其转化为可用的热能和材料。
高炉熔渣处理及显热回收工艺的研究进展

一
【 摘要】 介绍 了不 同于传统湿法的高炉熔渣处理及显热回收工艺, 如转杯 ( 转盘) 法、 转杯 化 学复合 法 、 转 筒法 、 风淬 法 、 滚 筒法等 , 并 对各 工 艺进 行 了对 比和评 价 , 以期 为 新. 7 - 艺 的 开发 【 关键词】 高炉熔渣 显热回收工艺 对比 评价
d i f f e r e n t f r o m t h e c o n v e n t i o n a l w e t t r e a t m e n t me t h o d ,s u c h a s r o t a r y c u p( d i s c )m e t h o d ,c o u p l e d
( A n s t e e l T e c h n o l o g y C e n t e r , A n s h a n L i a o n i n g 1 1 4 0 0 9 , C h i n a )
【 A b s t r a c t 】 T h e b l a s t f u r n a c e m o l t e n s l a g t r e a t m e n t a n d s e n s i b l e h e a t r e c o v e r y t e c h n o l o g i e s
d e t a i l e d,a n d t h e c o mp a r i s o n a n d e v a l u a t i o n o f whi c h we r e p e r f o r me d t o p r o v i d e a r e f e r e n e e f o r t h e d e v e l o p me n t a n d a pp l i c a t i o n o f t h e ne w t e c hn o l o g y.
高炉熔渣余热回收技术发展过程及趋势

高炉熔渣余热回收技术发展过程及趋势
随着我国对环境保护及能源利用效率提高的几十年来不断加强,高炉熔渣余热回收技术得到了长足的发展。
20世纪80年代,蒸汽抽取式熔渣余热回收利用技术是最常见的,这种技术将高炉熔渣余热引出用热水罐蒸汽排出。
其中的利用效率通常不高,只有50%-75%。
90年代,随着大型煤气余热锅炉的出现,传统的蒸汽抽取式熔渣余热回收利用技术又得到了发展。
因为把余热采集系统利用效率高于热水蒸汽型,可以提高到75%-85%。
近几年,随着新型煤气余热锅炉、熔渣余热回收循环冷却技术及回收新型低温热能等技术的出现,可以将高炉熔渣余热回收利用效率提高到90%-95%。
目前,各种新型熔渣余热回收技术不断改进,其中热能回收利用效率及经济性均有所提高,有助于各工业企业提升节能减排标准。
未来,高炉熔渣余热回收技术将会发展更多耐用、经济效益高的回收方案,以最大限度的回收余热,实现废热的原汁原味重构,使工业热能效率更高以及对环境更友好。
- 1、下载文档前请自行甄别文档内容的完整性,平台不提供额外的编辑、内容补充、找答案等附加服务。
- 2、"仅部分预览"的文档,不可在线预览部分如存在完整性等问题,可反馈申请退款(可完整预览的文档不适用该条件!)。
- 3、如文档侵犯您的权益,请联系客服反馈,我们会尽快为您处理(人工客服工作时间:9:00-18:30)。
收稿日期: 2013 - 09 - 12; 修订日期: 2013 - 12 - 16 作者简介: 王 波( 1981 - ) ,男,四川珙县人,上海理工大学副教授,博士 .
高炉炉渣中不仅携带了大量余热可资利用,并 且粒化高炉炉渣本身具有水泥材料的性质,因而可 以用于生产水泥。高炉炉渣的主要是由 CaO、MgO、 Al2 O3 和 SiO2 等组成的硅酸盐和铝酸盐,个别含有 TiO2 、V2 O5 等。Al2 O3 和 SiO2 主要来自矿石中的脉石 和焦炭中的灰分,CaO 和 MgO 主要来自熔剂[5]。
1984 年,日本 NKK 也设计了一套双鼓系统[8], 如图 5 所示。
图 5 双鼓法余热回收系统 Fig. 5 Dual roller method-based waste
heat recovery system
这套系统最主要的组成部分是两个反向转动的 转鼓。渣流被泼倒于两鼓之间的渣槽中。高炉渣一 方面由于重力作用在渣槽中往下流动,另一面又因 为转鼓的旋转作用获得向上的运动速度。在这两种 运动的共同作用下,熔渣被初步冷却并粒化。最后, 高温渣粒与位于转鼓之中的低沸点冷却介质进行传 热。所得的冷却剂蒸汽被送进余热锅炉。整个系统 已经在大型化实验中取得成功,其余热回收效率达 到 40% 并且得到了含有 80% 玻璃体的固态渣。但
图 4 转鼓法余热回收系统 Fig. 4 Rotary drum method based waste
heat recovery system
图 3 机械搅拌余热回收系统 ( Sumitomo 金属公司)
Fig. 3 Mechanically-agitated method-based waste heat recovery system( Sumitomo Metal Co. Ltd. )
文章编号: 1001 - 2060( 2014) 02 - 0113 - 08
檪殏
高炉炉渣余热回收技术的研究进展
檪檪檪檪檪檪殏
王 波,王夕晨,袁益超,周秋平
( 上海理工大学 能源与动力工程学院,上海 200093)
摘 要: 本文介绍了固体颗粒冲击、机械搅拌、转鼓粒化、离 心粒化和风淬等国外的高炉炉渣余热回收系统,对我国应用 高炉炉渣余热回收处理技术的现状进行了总结。在比较பைடு நூலகம் 内国外同类技术的优缺点后,指出基于离心粒化技术的余热 回收系统具有粒化性能优异、回收效率高等优点,据此认为 有必要进一步研究该系统运行能耗、系统稳定性和控制参数 以及渣粒的处理能力和粒径的均匀性等问题,以尽早实现商 业化应用。
固体颗粒冲击法是用循环固态颗粒对高温熔渣 进行淬碎。该系统最早由瑞典 Merotec 公司开发, 如图 1 所示。
在这个工艺中是利用已固化的循环渣粒将新渣 进行淬碎,所以设计了两个渣粒回收装置,液态渣以 约 1 300 ℃ 的高温从渣罐倒入粒化机中。最终通过 筛子将渣粒分成 > 3 mm 和 0 - 3 mm 两种粒径规 格。前者直接回收在右侧回收装置中,后者作为循 环渣粒进入左侧回收装置,由渣管返回循环渣容器, 与渣罐中 1 300 ℃ 高温液态渣一起送入粒化机进行 粒化,粒化后的新旧渣混合物继续送入流化床换热 器进行余热回收。在流化床中,高炉炉渣与空气通
DOI:10.16146/ki.rndlgc.2014.02.001
檪殏
第 29 卷第 2 期 2014 年 3 月
檪檪檪檪檪檪殏 专题综述
热
能
动
力
工
程
JOURNAL OF ENGINEERING FOR THERMAL ENERGY AND POWER
Vol. 29,No. 2 Mar. ,2014
2. 2. 3 转鼓法 转鼓法是一种基于转鼓离心作用使液态渣冷却
为固态渣 的 技 术。在 20 世 纪 80 年 代 早 期,日 本 Ishikawajimae Harima 重工和 Sumitomo 钢铁公司开 发了第一套基于转鼓技术的余热回收系统,如图 4 所示。
高温熔渣首先被倾倒于转鼓上,在转鼓的直接 作用下破碎。然后,分离的高炉炉渣在转鼓离心力 的作用下,甩入转鼓下容器中的倾斜面,再缓缓进入 余热回 收 室。在 这 套 系 统 中,空 气 可 以 被 加 热 到 500℃ 的高温,并 且 余 热 回 收 效 率 也 接 近 了 60% 。 该炉渣处理方法属于半急冷处理方法,所得产品可 作混凝土骨料。
目前,国内外已有不少机构致力于高炉炉渣的 余热回收系统的研究和开发。常规的高炉渣余热回 收过程中,一般是先将液态高炉炉渣进行初步冷却 粒化,然后将固化的渣粒送入余热回收装置进行热 量的回收。本文介绍了高炉炉渣的基本特性,讨论 了典型高炉炉渣余热回收系统的工作原理、工艺流 程和热量回收效果,为今后高炉炉渣余热回收技术 的进一步发展和实际应用提供参考。
第2 期
王 波,等: 高炉炉渣余热回收技术的研究进展
它的导热热阻,因此余热回收效率不高,也不便于后 续的高炉炉渣综合应用。目前,这两项技术都没有 实现商业化应用。
·115·
图 2 机械搅拌法余热回收系统 ( Kawasaki 钢铁公司)
Fig. 2 Mechanically-agitated method-based waste heat recovery system( Kawasaki Iron and Steel Corporation)
需要特别指出的是,粒化高炉炉渣的活性不仅 取决于 化 学 成 分 而 且 更 重 要 的 是 取 决 于 冷 却 条 件[6]。冷却速度越快,它的性质就越接近于水泥材 料的水硬性和强度。所以在对熔渣进行粒化处理的 过程中,必须保持一定的冷却速度,以促成其形成更 多具有粘结性和水硬性的玻璃体结构,使得它能够 成为高附加值的产品。同时,由于它替代了水泥生 产,从而避免了水泥制造中排放的大量 CO2 温室气 体。综上所述,在进行余热回收的过程中,也要将高 炉炉渣后期的利用品质考虑在内。
高炉熔渣的排放量大,而且排出时的温度一般 超过 1 400 ℃ ,其所含热量较高,具有显著的回收价 值,但传统的湿法处理方式对环境污染比较严重。
传统的水力冲渣方式会造成大量水资源的消耗 和热量的浪费,尤其是一些钢铁企业处于缺水地区, 这一因素的制约就显得尤其突出。此外,在对炉渣 进行湿法处理的过程中,还会产生 SOx 和 H2 S 等酸 性气体,从而造成环境污染。若要对湿法处理以后 的高炉炉渣进行进一步利用,还需要消耗相当一部 分的能量对湿渣进行干燥。因此对高炉炉渣的干法 处理技术的开发和应用将成为趋势。
·114·
热能动力工程
2014 年
此设计余热回收装置时应综合考虑回收的热量、装 置的投资和运行成本。如果采取传热管束等间壁式 热交换方式,虽然管内液体的比热和换热系数都相 比气体更大,但可能存在管子磨损等风险。所以,高 炉炉渣的余热回收应选择合适的换热介质种类、流 量和进出口温度等参数,以达到综合效益的最大化。 1. 3 冷渣的利用
关 键 词: 高炉渣; 粒化; 传热; 余热回收
中图分类号: X756
文献标识码: A
引言
钢铁工业是能源密集型产业,其能耗约为中国 总能耗的 10% - 15%[1]。高炉炉渣是钢铁工业中 最主要的废弃物,每生产一吨铁约产生 300 kg 高炉 炉渣,其出炉温度通常在 1 400 ℃ 以上,含有大量的 热量。2010 年中国生铁产量约为 5. 9 亿 t,产生高 炉炉渣约 1. 8 亿 t,水力除渣过程中损失的热量达到 2. 7 × 108 GJ,折合标准煤约 920 万 t。因此回收利用 高炉炉渣的余热对炼钢行业节能减排,提高能源效 率,有着至关重要的作用。
1 高炉炉渣余热回收的制约因素
1. 1 物理性质 高炉炉渣的导热系数较低,这是余热回收的一个
重要制约因素。在 1 400 - 1 500 ℃ 高炉炉渣处于液 态时,导热系数在 0. 1 - 0. 3 W / ( m·K) [2]。当处于 固态时,导热系数在 7 W / ( m·K) 左右。Goto 等通过 红外测量技术测定了 20 - 1 500 ℃ 范围内高炉渣导热 系数的变化规律[3],研究结果表明处于固体状态的高 炉炉渣,其导热系数会随着温度的升高而增加 1 - 2 W / ( m·K) 。然而这一变化规律会在1 200 ℃ 左右炉 渣由固体向液体产生相变的过程中,发生改变。此时 高炉炉渣的导热系数随着温度的上升而减小。所以, 导热系数低使得高炉炉渣的粒化成为了余热回收的 一个限制因素。粒化后的渣粒大小直接影响换热介 质和渣粒的热交换效果。渣粒较小时,可以在较短的 时间内获得较好的传热效果。
图 1 固态渣冲击法余热回收系统 Fig. 1 Solid-state slag impingement method-based
waste heat recovery system
2 国外高炉炉渣余热回收系统的发展现状
高炉炉渣余热回收技术发展至今,粒化始终是 一个必不可少的环节。目前,基于机械碎渣法、风淬 法以及离心粒化法已经衍生出了一系列的余热回收 系统。 2. 1 机械碎渣余热回收系统 2. 1. 1 固体颗粒冲击法
而在另一个由日本 Sumitomo 金属开发的系统 中,如图 3 所示,高温熔渣通过旋转叶片进行击碎粒 化,而热量则以导热和辐射的方式传递给位于轴心 的套管中的水。这 套 系 统 的 排 渣 温 度 大 约 在 900 ℃ ,其余热回收效率达到 50% 。机械搅拌方法的主 要缺点是淬碎后的渣粒粒径相对较大,这就增大了
2. 2. 2 机械搅拌法 在机械搅拌法处理过程中,高温熔渣主要通过
运动中的棍棒 或 刀 片 进 行 搅 拌 和 击 碎。日 本 Kawasaki 钢铁公司开发了一种基于机械搅拌技术的高 炉炉渣余热回收系统,如图 2 所示。