第2章 精密切削加工共111页文档
02-精密加工技术-精密切削
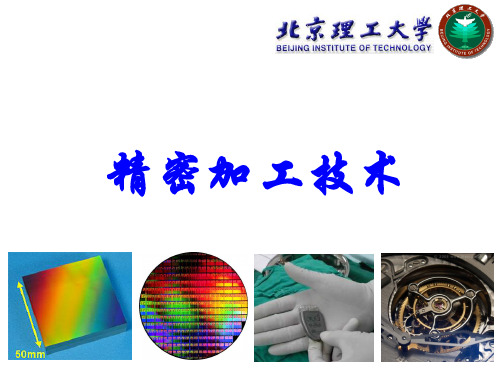
刀刀接口 接口拉钉 7:24定位锥面 中间接杆 刀机接口 基本刀柄 抓刀及扭 矩槽
刀柄拉钉
金属切削基础知识 – 切削变形
刀
具
工
件
金属切削基础知识 – 切削变形
金属切削过程发生剪切和滑移
金属的滑移线和流动轨迹 横向线是金属流动轨迹线 纵向线是金属的剪切滑移线
金属切削基础知识 – 切削变形
精密切削的基本特点
金属切削本质
材料在刀具作用下产生剪切断裂、摩擦挤压和滑移变 形等过程
精密切削机理
采用微量切削方法 切削在晶粒内进行 切削力>原子结合力(剪切应力达13000N/mm2) 刀尖处温度极高,应力极大,普通刀具难以承受 工件变形小,表层高温不会波及工件内层 可获得高精度和好表面质量
精密切削的基本特点
精密切削
刀刃实际切削厚度与名义切削厚度不相同 切削厚度小于一定程度不能正常切削 能稳定切削的最小有效切削厚度称为最小切削厚度 最小切削厚度取决于金刚石刀具的刃口半径
精密切削刀具
精密切削要求刀具能均匀地去除不大于工件加工精度 、厚度极薄的金属层或非金属层 精密切削的刀具,一般指天然单晶金刚石刀具 精密切削必须保证金刚石刀具的刀面和刃口质量
《精密加工技术》研究型课程
精密和超精密加工概述 精密切削 精密磨削和超精密磨削 精密加工的机床设备 精密加工的测量技术 在线检测与误差补偿技术 精密加工的外部支撑环境 精密研磨与抛光 微细加工技术 纳米加工技术
金属切削基础知识 – 切削刀具材料
8000 7000 6000 5000 4000 3000 2000 1000 0
普通切削时主切削力大于径向切削力,精密切削相反 工件材料对精密切削有重要影响:工件表面的不纯物 、结晶的晶界出现阶梯、工件有残留变形和残留应力 、对金刚石刀具的亲和性,产生粘结现象
机械制造技术基础电子课件第2章金属切削原理与刀具

2.2.1 常见刀具类型及刀具的结构
②麻花钻。麻花钻是应用最广泛的孔加工刀具,图 2-11所示为标准高速钢麻花钻的结构。
图2-11 标准高速钢麻花钻的结构
2.2.1 常见刀具类型及刀具的结构
③中心钻。中心钻是 用来加工轴类零件中心孔 的刀具,如图2-12所示。
图2-12 中心钻
2.2.1 常见刀具类型及刀具的结构
图2-17 不带导柱锥面锪钻
图2-18 端面锪钻
2.2.1 常见刀具类型及刀具的结构
⑦铰刀。铰刀常用来对已有孔进行最后精加工,也可对要求 精确的孔进行预加工,如图2-19所示。其加工精度可达IT8~IT6, 表面粗糙度值达1.6~0.2 μm。铰刀可分为手用铰刀和机用铰刀。
图2-19 不同种类的铰刀
③角度铣刀。角度铣刀用于铣削成一定角度的沟槽, 有单角铣刀和双角铣刀两种。
2.2.1 常见刀具类型及刀具的结构
④锯片铣刀。锯片铣刀用于加工深槽和切断工件,其圆周 上有较多的刀齿。为了减少铣切时的摩擦,刀齿两侧有15′~1° 的副偏角。
⑤立铣刀。立铣刀用于加工沟槽和台阶面等,刀齿在圆周 和端面上,工作时不能沿轴向进给。当立铣刀上有通过中心的 端齿时,可轴向进给运动。
机械制造技术基础
第2章 金属切削原理与刀具
2.1 金属切削加工的基础知识 2.2 刀具结构和刀具材料 2.3 金属切削过程 2.4 切削力与切削功率 2.5 切削热与切削温度
第2章 金属切削原理与刀具
2.6 刀具磨损与刀具耐用度 2.7 切削用量和切削液 2.8 金属材料的切削加工性 2.9 高速切削及刀具
切削刃上的选定点相对工件的进给运动的瞬时速度称为进给 速度(vf),单位为mm/s。它与进给量之间的关系为
2 精密切削2
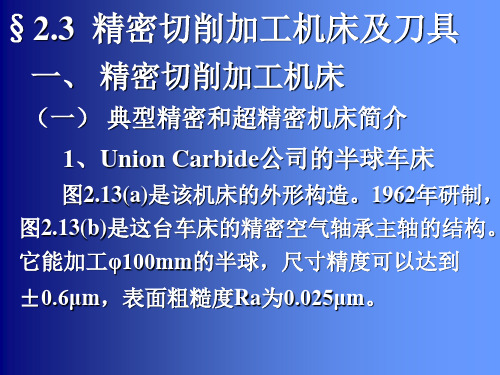
1)不易磨损
2)不易生锈腐蚀
3)热膨胀系数要小
4)材料的稳定性要好
2、主轴的驱动方式
1)电动机通过带传动驱动
2)采用内装式同轴电动机驱动机床主轴
3)电动机通过柔性联轴器驱动机床主轴
(五) 床身和精密导轨部件
1、床身和导轨的材料
目前精密机床主要采用下列材料作为床身和导轨
材料:
1)优质耐磨铸铁,其优点是工艺性好 ;
1)V-平面
2)双V形导轨能为直线运动提供良好的导向
性。 3)压力油润滑导轨 4)导轨偶合面的接触形式
3、导轨类型
导轨类型分三类:滚动导轨 、液体静压导轨、 气浮导轨和空气静压导轨。
4、进给驱动系统
精密进给驱动系统必须由滚珠丝杠副驱动 (见图2.27) 、液体静压和空气静压丝杠副驱
动(见图2.28 )、摩擦驱动(见图2.29 )、微
2)刃口能磨得极其锋锐,刃口半径ρ值极
小.能实现超薄切削厚度。
3)刀刃无缺陷,切削时刃形将复印在加工
表面上,能得到超光滑的镜面。
4)和工件材料的抗粘结性好、化学亲和性 小、摩擦系数低,能得到极好的加工表面完整 性。 由于单晶金刚石现在是无法代替的超精密 切削用刀具材料,故分析研究金刚石的性能是 研究超精密切削的重要基础。
2)花岗岩 。其尺寸稳定性,振动衰减能力,
硬度、耐磨性和抗腐蚀性等方面的性能都优越 ; 3)人造花岗岩。不仅可铸造成形,吸湿性低, 而且加强了振动的衰减能力。
2、导轨的要求和结构形式
常用的机床的导轨结构形式有燕尾形的,有平 面的,有V-平面的,有双V形的。现在液体静压
导轨和空气静压导轨多数采用平面导轨结构。
近期目标2.5nm 近期目标0.001K
精密与特种加工讲解讲课文档

超级光磨的应用也很广泛,如汽车和内燃机 零件、轴承、精密量具等小粗糙度表面的光整加 工。它不仅能加工轴类零件的外圆柱面,而且还 能加工圆锥面、孔、平面和球面等。
28
第28页,共111页。
加工原理
零件旋转,磨具以恒力轻压于零件表面,作轴 向进给的同时作轴向微小振动,从而对零件微观不 平的表面进行光磨。
磨条材料
氧化铝
碳化硅
26
第26页,共111页。
珩磨液
组成
形态
煤
机
溶
水
油
油
液
剂
27
第27页,共111页。
超级光磨
超级光磨是用细磨粒的磨具(油石)对零件施加
很小作方便;(2) 加工余量极小;
(3) 生产率较高;(4) 表面质量好;(5)仅能提高工件
脉冲发生器1的两极分别接在工具电极3 与零件4上,当两极在工作液5中靠近时,极
间电压击穿间隙而产生火花放电。
54
第54页,共111页。
电火花加工装置原理图
1—脉冲发生器 2—自动进给调 节装置 3—工具电极 4—零件 5—工作液
火花放电的同时,在放电通道中瞬时产生大量的
热,达到很高的温度(10000℃以上),使零件和工具 表面局部材料熔化甚至气化而被蚀除下来,形成 一个微小的凹坑。
从应用范围来看,研磨、珩磨、超级光磨和抛光都
可以用来加工各种各样的表面,但珩磨则主要用于孔的
精整加工。
从所用工具和设备来看,抛光最简单,研磨和超级
光磨稍复杂,而珩磨则较为复杂。
43
第43页,共111页。
超精密加工 指加工的尺寸精度以微米计的加工方 法的统称。是指加工精度和表面质量达到 极高精度的加工工艺。
第二章 金刚石刀具精密切削加工

复习晶体结构
晶格模型
面心结构
晶体结构指晶体内部原子规则排列的方式.晶体结构不同, 其性能往往相差很大。为了便于分析研究各种晶体中原子 或分子的排列情况,通常把原子抽象为几何点,并用许多 假想的直线连接起来,这样得到的三维空间几何格架称为 晶格。
晶胞
Z
晶胞
c
b Y
a
X
晶格常数 a , b, c
人造单晶金刚石刀具 金刚石刀具 PCD刀具
多晶金刚石刀具
CVD金刚石薄膜涂层刀具
CVD金刚石刀具 金刚石厚度膜焊接刀具
金刚石刀具的性能特点
极高的硬度和耐磨性:硬度达HV10000,是自然界最硬的物质, 具有极高的耐磨性,天然金刚石耐磨性为硬质合金80-120倍,人 造金刚石耐磨性为硬质合金60-80倍。 各向异性能:单晶金刚石晶体不同晶面及晶向的硬度、耐磨性能 、微观强度、研磨加工的难易程度以及与工件材料之间的摩擦系 数等相差很大,因此,设计和制造单晶金刚石刀具时,必须进行 晶体定向。
二、典型机床简介
Pneumo 公司的MSG-325超精密车床
采用T形布局,机床空气主轴的径向圆跳动和轴向 跳动均小于等于0.05μm。床身溜板用花岗岩制造,导 轨为气浮导轨;机床用滚珠丝杠和分辨率为0.01μm的 双坐标精密数控系统驱动,用HP5501A双频激光干涉仪 精密检测位移。
DTM-3大型超精密车床
分为:液体静压和空气静压
供油压力恒定的液体静压轴承
主轴始终悬浮 在高压油膜上
液体静压轴承与气压轴承
1、液体静压轴承主轴
优点
回转稳定性好 刚度高 无振动
缺点
回转运动有温升 回油时有空气进入油源 注:空气静压轴承原理与静
第二章 精密切削加工

一、切削速度、进给量、修光刃和背吃刀量的影响 4、背吃刀量的影响
在刀具刃口半径足够小时,超精密切削范围内,背吃 刀量变化对加工表面粗糙度影响很小。
背吃刀量减少,表面残留应力也减少,但超过某临界 值时,背吃刀量减少反而使加工表面残留应力增加。
2020/1/30
一、刃口锋锐度对加工表面粗糙度的影响
2020/1/30
1、金刚石刀具切削部分的几何形状
金刚石车刀举例
4
3
3
1:主偏角45度
1
1
2
2:前角0度
3:后角5度
4:修光刃0.15mm
2020/1/30
2、金刚石刀具前、后刀面晶面选择
应考虑因素:刀具耐磨性好;刀刃微观强度高,不易产生微 观崩刃;刀具和被加工材料间摩擦系数低,使切削变形小, 加工表面质量高;制造研磨容易。(111)不适合作前后面。
刃口半径为0.6μm、0.3μm
刃口锋锐度对加工表面有一 定的影响,相同条件下(背 吃刀量、进给量),更锋锐 的刀具切出的表面粗糙度更 小;速度的影响不是很大。
2020/1/30
二、刀刃锋锐度对切削变形和切削力的影响
2020/1/30
锋锐车刀切削变形系数明显低于 较钝的车刀。 刀刃锋锐度不同,切削力明显不 同。刃口半径增大,切削力增大, 即切削变形大。背吃刀量很小时, 切削力显著增大。因为背吃刀量很 小时,刃口半径造成的附加切削变 形已占总切削变形的很大比例,刃 口的微小变化将使切削变形产生很 大的变化。所以在背吃刀量很小的 精切时,应采用刃口半径很小的锋 锐金刚石车刀。
2020/1/30
二、金刚石刀具的研磨加工 3、精研
提高研磨质量,使切削刃研制更为锋锐 磨料粒度越小,研磨表面粗糙度越小 研磨盘质量越好,研磨效果越好 研磨方向:逆磨,即沿切削刃口指向刀体内的方向研磨 精抛:研磨时让金刚石作垂直于研磨方向的法向运动,除
机械制造技术PPT课件第二章金属切削基本原理

合理副偏角值的选择
添加标题
一般较小
添加标题
—5°~10°
添加标题
精加工
添加标题
—小,0°
添加标题
加工高强高硬材料或断续切削
添加标题
—小,4°~6°
添加标题
切断刀、锯片、槽铣刀
添加标题
—小,1°~2°
过渡刃的型式
①直线刃
—粗车、强力车 κrε=κr/2
②圆弧刃
—粗糙度值小
冷却作用 清洗与防锈作用
常用切削液及其选用 =乳化油+水 切削油 = 矿物油、+动植物油 极压切削油 =切削油+硫、氯和磷极压添加剂 难加工材料的精加工
=水+防锈剂、清洗剂、油性添加剂 磨削、粗加工
①水溶液
01
车削、钻削、攻螺纹 滚齿、插齿、车螺纹、一般精加工
②乳化液
02
刀具磨损与刀具耐用度
4
磨屑形态
带状切屑
直线刃、折线刃、圆弧刃、波形刃
刀具合理几何参数选择应考虑的因素
—化学成分、制造方法、热处理状态 性能,表层情况等
①工件材料
壹
—化学成分、性能,刀具结构形式
②刀具材料及结构
—机床、夹具,系统刚性,功率 切削用量和切削液
③加工条件
叁
贰
各参数间的联系 —综合考虑相互作用与影响
刀具角度的选择
大后角→减小摩擦、提高寿命、改善表面质量 强度降低、散热差、磨损加快
后角的选择原则
工艺系统刚性 刚性差—振动 → 小后角 精度要求高 —重磨 → 小后角
切削层厚度hD小 → 大后角 切削层厚度hD大 → 小后角
强度、硬度高 → 小后角 塑性大 → 大后角
机械制造技术课件第二章金属切削基本原理
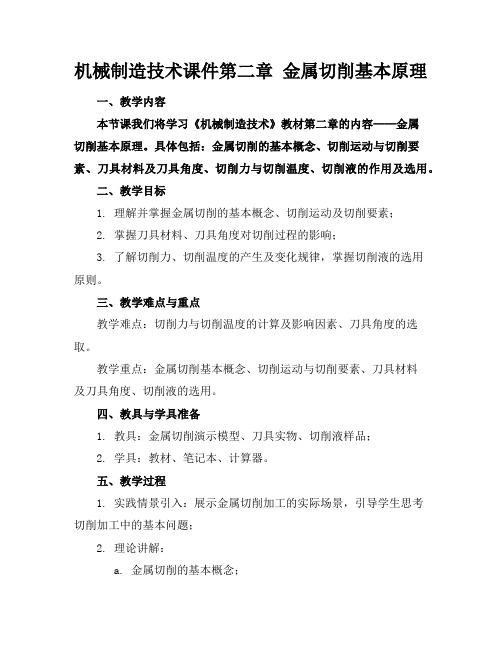
机械制造技术课件第二章金属切削基本原理一、教学内容本节课我们将学习《机械制造技术》教材第二章的内容——金属切削基本原理。
具体包括:金属切削的基本概念、切削运动与切削要素、刀具材料及刀具角度、切削力与切削温度、切削液的作用及选用。
二、教学目标1. 理解并掌握金属切削的基本概念、切削运动及切削要素;2. 掌握刀具材料、刀具角度对切削过程的影响;3. 了解切削力、切削温度的产生及变化规律,掌握切削液的选用原则。
三、教学难点与重点教学难点:切削力与切削温度的计算及影响因素、刀具角度的选取。
教学重点:金属切削基本概念、切削运动与切削要素、刀具材料及刀具角度、切削液的选用。
四、教具与学具准备1. 教具:金属切削演示模型、刀具实物、切削液样品;2. 学具:教材、笔记本、计算器。
五、教学过程1. 实践情景引入:展示金属切削加工的实际场景,引导学生思考切削加工中的基本问题;2. 理论讲解:a. 金属切削的基本概念;b. 切削运动与切削要素;c. 刀具材料及刀具角度;d. 切削力与切削温度;e. 切削液的作用及选用;3. 例题讲解:通过具体例题,讲解切削力与切削温度的计算方法,以及刀具角度的选取原则;4. 随堂练习:布置相关练习题,巩固所学知识;六、板书设计1. 金属切削基本概念;2. 切削运动与切削要素;3. 刀具材料及刀具角度;4. 切削力与切削温度;5. 切削液的选用。
七、作业设计1. 作业题目:a. 解释金属切削的基本概念;b. 列出切削运动及切削要素;c. 分析刀具材料、刀具角度对切削过程的影响;d. 计算给定条件下的切削力与切削温度;e. 论述切削液的选用原则。
2. 答案:a. 略;b. 略;c. 略;d. 略;e. 略。
八、课后反思及拓展延伸1. 反思:本节课学生对金属切削基本原理的理解程度,以及切削力与切削温度的计算掌握情况;2. 拓展延伸:引导学生了解金属切削技术的发展趋势,如高速切削、绿色切削等。
第3次课 第二章 精密切削加工(2)
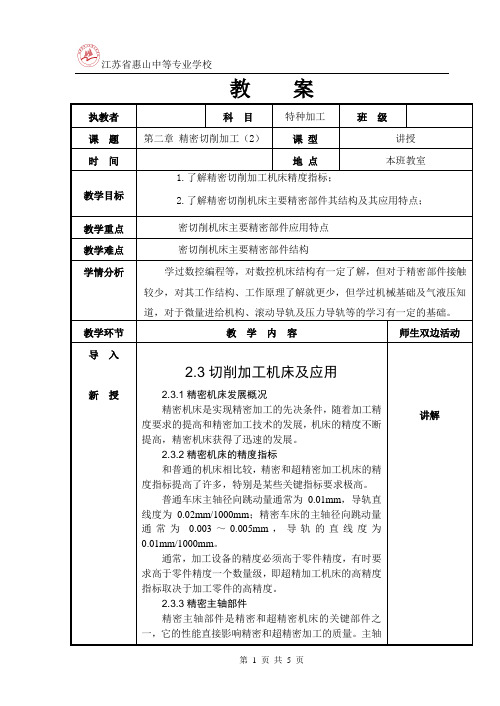
2)液体静压导轨
由于导轨运动速度不高,液体静压导轨的温度升高不严重,而液体静压导轨刚度高,承载能力强直线运动精度高并且平稳,无爬行现象,因此现在不少的超精密机床使用液体静压导轨。
3)气浮导轨和空气静压导轨
气浮导轨和空气静压导轨可以得到很高的直线运动精度,运动平稳,无爬行,摩擦因数几乎为零,不发热,这些特性使得它们在超精密机床中得到较广泛的应用。
2.3.5进给驱动系统
工件的加工精度是由成形运动的精度决定的。成形运动包括主运动和进给运动。进给运动的精度是由进给系统精度决定的,因此精度机床必须具有精密的进给驱动精度。
教学环节
教学内容
师生双边活动
导入
新授
2.3切削加工机床及应用
2.3.1精密机床发展概况
精密机床是实现精密加工的先决条件,随着加工精度要求的提高和精密加工技术的发展,机床的精度不断提高,精密机床获得了迅速的发展。
2.3.2精密机床的精度指标
和普通的机床相比较,精密和超精密加工机床的精度指标提高了许多,特别是某些关键指标要求极高。
精密和超精密加工机床,由于采用了在线检测和误差补偿技术,因此可以加工出精度极高的工件。
现在国外生产的超精密机床,都装有双频激光随机检测系统,检测机床运动部件两个坐标方向的位移位置,和精密数控系统组成反馈控制系统,以保证加工的尺寸精度。精密数控系统现在一般都采用闭环控制,即机床的运动部件的位移用装在机床内部的双频激光干涉测距系统随机精确检测,将数据反馈给精密数控系统,保证位移的高精度。
2.3.4床身和精密导轨部件
床身和导轨是精密机床的基础件,其材料性能对精密机床的整体性能有较大的影响。
精密切削加工讲解
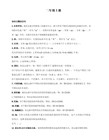
2.1概述 2.2精密切削加工的工艺规律和机理 2.3精密切削加工的机床及应用 2.4功率超声车削
2019/1/6
2.1概述
精密切削是使用精密的单晶天然金刚石刀具加工有色金属 和非金属,可以直接加工出超光滑的加工表面(粗糙度 Ra0.02~0.005µm,加工精度<0.01µm)。 用于加工:陀螺仪、激光反射镜、天文望远镜的反射镜、 红外反射镜和红外透镜、雷达的波导管内腔、计算机磁盘、 激光打印机的多面棱镜、录像机的磁头、复印机的硒鼓、 菲尼尔透镜等。 精密切削也是金属切削的一种,当然也服从金属切削的普 遍规律。 金刚石刀具的精密加工技术主要应用于单件大型超精密零 件的切削加工和大量生产中的中小型超精密零件加工。
一、切削速度、进给量、修光刃和背吃刀量的影响
2、进给量的影响
在进给量f<5μm/r
时,均达到
Rmax<0.05μm的加工 表面粗糙度。
2019/1/6
一、切削速度、进给量、修光刃和背吃刀量的影响
3、修光刃的影响
修光刃长度常取0.05~ 0.20mm。 修光刃的长度过长,对 加工表面粗糙度影响不 大。 修光刃有直线和圆弧两 种,加工时要精确对 刀,使修光刃和进给方 向一致。圆弧刃半径一般 取2~5mm。
2019/1/6
精密加工的关键技术
1.精密加工机床:主轴回转精度、工作台直线运动精度以 及刀具微量进给精度 2.金刚石刀具:金刚石晶面选择、刀具刃口锋利性(刀具 刃口圆弧半径) 3.精密切削机理:微量切削过程的特殊性 4.稳定的加工环境:恒温、防振和空气净化 5.误差补偿:根据规律设定补偿,反馈控制系统 6.精密测量技术
2019/1/6
2 精密切削1
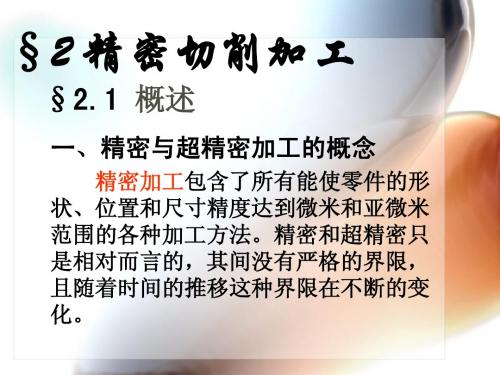
§2.1 概述
一、精密与超精密加工的概念
精密加工包含了所有能使零件的形 状、位置和尺寸精度达到微米和亚微米 范围的各种加工方法。精密和超精密只 是相对而言的,其间没有严格的界限, 且随着时间的推移这种界限在不断的变 化。
1 加工方法、精度及其发展势态:
2 加工范畴的划分:
普通加工 指加工精度低于1μm,表面粗糙度 值大于Ra0.1μm的加工方法。
论,最大剪切应力发生在与切削合力Pi成45°角
的方向上,即Pyi=Pzi 。 因此,当Pzi>Pyi时,材料质点被推向切削运 动方向,形成切屑;当Pzi<Pyi时,材料质点被 压向零件本体,被加工材料表面形成挤压过程, 无切屑产生;Pzi=Pyi时所对应的切入深度便 是最小切入深度。
△=ρ一h=ρ(1一COSψ)
少刀具与工件材料之间摩擦的效果,从而减小切削
力,减少刀具磨损。另外,抑制积屑瘤的生成,降 低加工区域温度。
大,积屑瘤小时切削力也小,这和普通切削时规
律正好相反。原因是积屑瘤的存在,使刀具的刃 口半径增大;积屑瘤呈鼻形并自刀刃前伸出,这 导致实际切削厚度超过名义值许多;积屑瘤代替 刀具进行切削,积屑瘤、切屑和已加工表面之间
的摩擦比刀具和它们之间的摩擦要严重许多。
(2) 进给量
进给量和切削深度决定着切削面积的大小,因而
精密加工 指加工精度在0.1~1μm之间,粗
糙度值在Ra0.02~0.1μm之间的加工方法 。 超精密加工 指加工精度高于0.1μm,表面粗 糙度值小于Ra0.02μm的加工方法 。 纳米加工 当加工精度高于0.01μm时,被认 为是纳米级的加工 。
二、影响精密与超精密加工的主要
因素
精密与特种加工技术_第二章_精密切削加工 上课用
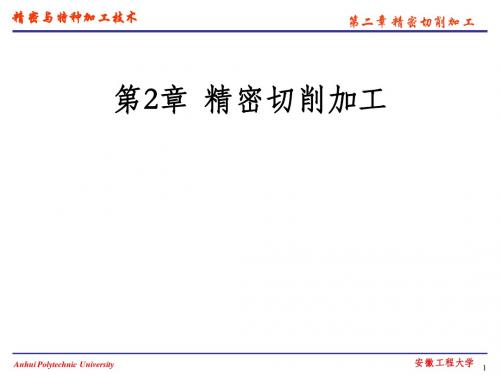
第二章 精密切削加工
第2章 精密切削加工
Anhui Polytechnic University
安徽工程大学
1
精密与特种加工技术
第二章 精密切削加工
2.1 概
述
着科学技术的发展,电子计算机、原子能、 激光、宇航和国防等技术部门对零件的加工精度 和表面质量要求越来越高。精密加工技术的研究 及应用水平已成为衡量一个国家的机械制造业乃 至整个制造业水平的重要依据。各国特别是工业 发达国家对精密加工技术极其重视,投入了大量 的资金对其进行研究,以保证其尖端技术产品处 于国际领先地位,提高其产品在国际上的竞争力。
现象。两摩擦表面的粘结点因相对运动,晶粒或晶粒群受剪或 受拉被对方带走,是造成粘结磨损的原因。 由于刀具材料有组织不均匀、存在内应力、微裂纹及空隙、 局部软点等缺陷,所以刀具表面常发生破裂而被切屑或工件带
走,形成粘结磨损,在前刀面上形成不规则的凹坑。
高速钢、硬质合金、陶瓷刀具、立方氮化硼和金刚石刀具
Anhui Polytechnic University
安徽工程大学
3
精密与特种加工技术
第二章 精密切削加工
精密加工技术是一项涉及内容广泛的综合性技术,实现 精密加工,不仅需要精密的机械设备和工具,也需要稳 定的环境条件,还需运用计算技术进行实时检测和反馈 补偿。只有将各个领域的技术成果集成起来,才有可能 实现和发展精密加工。
Anhui Polytechnic University
安徽工程大学
11
精密与特种加工技术
第二章 精密切削加工
2. 切削力 1) 切削力的来源
切削层金属、切屑和工件表面层金属的弹 性变形、塑性变形所产生的抗力; 刀具与切削同工件表面间的摩擦阻力。
精密加工技术第二讲
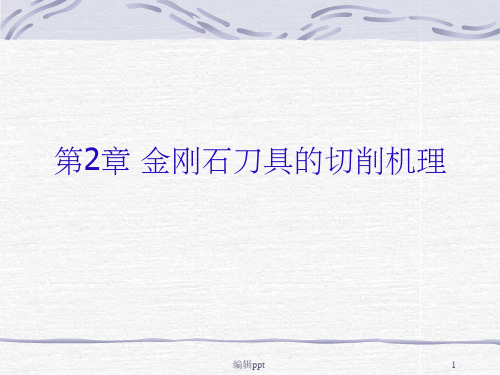
晶体构造
6面体
8面体
12面体
编辑ppt
22
激光反射形成的衍射图象
通过四个对称顶角的面是(100)晶面
编辑ppt
23
八面体的外表面及其平行面(111)晶面
编辑ppt
24
通过两个对称顶角和两个对称边中点的面是(110)晶面
编辑ppt
25
激光反射形成的衍射图象
(110)
编辑ppt
编辑ppt
Байду номын сангаас18
2.3 切削时积屑瘤的生成规律
切削模型分析
实际切削厚度
1)积屑瘤前端R大约 2~3μm,实际切削 力由刃口半径R,切
r0=0.2~0.3 μ m 削刃半径增加导致, 切削力增加明显。
2)积屑瘤与切削层和 已加工表面间的摩擦 力增大,切削力增大。
3)实际切削厚度超过 名义值,切削厚度增 加加。hD-hDu,切削力增
瓷轴承
高速精密空 气轴承的电
主轴
编辑ppt
12
2.3 切削时积屑瘤的生成规律
一、积屑瘤的生成现象
切削过程中,会出现一 小块金属牢固地粘附住 所用刀具的前刀面上, 这一小块金属就是积屑 瘤。
积屑瘤是在很大的压力、 强烈摩擦和剧烈的金属 变形的条件下产生的
编辑ppt
13
2.3 切削时积屑瘤的生成规律
说明:表面粗糙度改变之后,表面磨损还是很小!
编辑ppt
9
第2章 金刚石刀具的切削机理
正常磨损的切削刃
剧烈磨损后刀面
说明:刀具剧烈磨损后,后刀面呈层状剥落!
编辑ppt
10
微小崩刃
发生微小振动之后 的微小崩刃现象!
- 1、下载文档前请自行甄别文档内容的完整性,平台不提供额外的编辑、内容补充、找答案等附加服务。
- 2、"仅部分预览"的文档,不可在线预览部分如存在完整性等问题,可反馈申请退款(可完整预览的文档不适用该条件!)。
- 3、如文档侵犯您的权益,请联系客服反馈,我们会尽快为您处理(人工客服工作时间:9:00-18:30)。
24.05.2020
二、积屑瘤对切削力和加工表面粗糙度的影响 1、对切削力的影响
积屑瘤高时切削力也大,积屑瘤小时切削力也小。 与普通切削规律正好相反。
24.05.2020
三、刀刃锋锐度对切削表面层的冷硬和组织位错的影响 1、对加工表面冷硬的影响
➢ LY12铝合金原始材料的显微硬度为105HV。使用p= 0.3μm的金刚石车刀切削,得到的加工表面显微硬度为 167HV;使用p=0.6μm的金刚石车刀切削,得到的加工 表面显微硬度为205HV。
24.05.2020
精密加工的关键技术
➢ 1.精密加工机床:主轴回转精度、工作台直线运动精度以 及刀具微量进给精度
➢ 2.金刚石刀具:金刚石晶面选择、刀具刃口锋利性(刀具 刃口圆弧半径)
➢ 3.精密切削机理:微量切削过程的特殊性 ➢ 4.稳定的加工环境:恒温、防振和空气净化 ➢ 5.误差补偿:根据规律设定补偿,反馈控制系统 ➢ 6.精密测量技术
2.1概述
➢ 精密切削是使用精密的单晶天然金刚石刀具加工有色金属 和非金属,可以直接加工出超光滑的加工表面(粗糙度 Ra0.02~0.005µm,加工精度<0.01µm)。
➢ 用于加工:陀螺仪、激光反射镜、天文望远镜的反射镜、 红外反射镜和红外透镜、雷达的波导管内腔、计算机磁盘、 激光打印机的多面棱镜、录像机的磁头、复印机的硒鼓、 菲尼尔透镜等。
一、切削速度、进给量、修光刃和背吃刀量的影响 2、进给量的影响
在进给量f<5μm/r 时,均达到
Rmax<0.05μm的加工 表面粗糙度。
24.05.2020
一、切削速度、进给量、修光刃和背吃刀量的影响
3、修光刃的影响
修光刃长度常取0.05~ 0.20mm。 修光刃的长度过长,对 加工表面粗糙度影响不 大。 修光刃有直线和圆弧两 种,加工时要精确对 刀,使修光刃和进给方 向一致。圆弧刃半径一般 取2~5mm。
24.05.2020
2.2精密切削加工机理
➢ 切削速度向来是影响刀具耐用度最主要的因素,但 是切削速度的高低对金刚石刀具的磨损大小影响甚 微,刀具的耐用度极高。原因是:金刚石的硬度极 高,耐磨性好,热传导系数高,和有色金属间的摩 擦系数低,因此切削温度低,在加工有色金属时刀 具耐磨度甚高,可用很高的切削速度1000~ 2000m/min,而刀具的磨损甚小。
积屑瘤高度大,表面粗糙度大,积屑瘤小表面粗糙度小。并 且可以看出,切削液减小积屑瘤,减小加工表面粗糙度。
24.05.2020
一、切削速度、进给量、修光刃和背吃刀量的影响 1、切削速度的影响
由图2-12知,在有切削液的条件下,切削速度对加工表面粗 糙度的影响很小。 图2-13说明,不同切削速度下均得到表面粗糙度极小的加工 表24.面05.2—020镜面。
24.05.2020
一、切削速度、进给量、修光刃和背吃刀量的影响 4、背吃刀量的影响
在刀具刃口半径足够小时,超精密切削范围内,背吃 刀量变化对加工表面粗糙度影响很小。
背吃刀量减少,表面残留应力也减少,但超过某临界 值时,背吃刀量减少反而使加工表面残留应力增加。
24.05.2020
一、刃口锋锐度对加工表面粗糙度的影响
➢ 超精密切削实际速度的选择根据所使用的超精密机 床的动特性和切削系统的动特性选取,即选择振动 最小的转速。
24.05.2020
总结:天然单晶金刚石刀具只能用在机床主轴转 动非常平稳的高精度车床上,否则由于振动金刚 石刀具将会很快产生刀刃微观崩刃。
24.05.2020
24.05.2020
图2-3:图a是刀刃磨损的正 常情况,图b是剧烈磨损情 况,可以看到磨损后成层状, 即刀具磨损为层状微小剥落。 图2-4:图中所示沿切削速 度方向出现磨损沟槽,由于 金刚石和铁、镍的化学和物 理亲和性而产生的腐蚀沟槽。 图2-5:金刚石切削时,若 有微小振动,就会产生刀刃 微小崩刃。
一、切削参数对积屑瘤生成的影响 1、切 Nhomakorabea速度的影响
24.05.2020
不管在多大的切削速度下都有积屑瘤生 成,切削速度不同,积屑瘤的高度也不 同。当切削速度较低时,积屑瘤高度较 高,当切削速度达到一定值时,积屑瘤 趋于稳定,高度变化不大。
2、进给量f和背吃刀量 p的影响
➢ 由图2-8可以看出在进给量很小时,积屑瘤的高度很大, 在f=5μm/r时,h0值最小,f值再增大时,h0值稍有增 加。
刃口半径为0.6μm、0.3μm
刃口锋锐度对加工表面有一 定的影响,相同条件下(背 吃刀量、进给量),更锋锐 的刀具切出的表面粗糙度更 小;速度的影响不是很大。
24.05.2020
二、刀刃锋锐度对切削变形和切削力的影响
24.05.2020
锋锐车刀切削变形系数明显低于 较钝的车刀。 刀刃锋锐度不同,切削力明显不 同。刃口半径增大,切削力增大, 即切削变形大。背吃刀量很小时, 切削力显著增大。因为背吃刀量很 小时,刃口半径造成的附加切削变 形已占总切削变形的很大比例,刃 口的微小变化将使切削变形产生很 大的变化。所以在背吃刀量很小的 精切时,应采用刃口半径很小的锋 锐金刚石车刀。
➢ 精密切削也是金属切削的一种,当然也服从金属切削的普 遍规律。
➢ 金刚石刀具的精密加工技术主要应用于单件大型超精密零 件的切削加工和大量生产中的中小型超精密零件加工。
24.05.2020
精密加工的加工范畴
按加工精度划分,可将机械加工分为一般加工、精密加工、超 精密加工三个阶段。 精密加工:加工精度在0.1~1µm,加工表面粗糙度在Ra0.02~ 0.1µm之间的加工方法称为精密加工; 超精密加工:加工精度高于0.1µm,加工表面粗糙度小于 Ra0.01µm之间的加工方法称为超精密加工(微细加工、超微细 加工、光整加工、精整加工等 )。
切削模型分析
实际切削厚度
24.05.2020
1)积屑瘤前端R大约 2~3μm,实际切削 力由刃口半径R起 作用,切削力明显 增加 。
2)积屑瘤与切削层和 已加工表面间的摩 擦力增大,切削力 增大。
3)实际切削厚度超过 名义值,切削厚度 增力加 增加hD。-hDu,切削
二、积屑瘤对切削力和加工表面粗糙度的影响 2、对加工表面粗糙度的影响