设备联网-数据采集技术解决方案
DNC与MDC数据采集解决方案

7
Value (价值体现)
DNC-分布式数控
DNC主要实现功能
NC程序的远 程双向通讯, 避免设备由于 使用U盘或CF 卡传输时导致 的热插拔及病 毒问题。
NC程序的远 程双向通讯, 避免设备由于 使用U盘或CF 卡传输时导致 的程序丢失问 题。
程序无严格的流程签署,职责不明晰,出了问题之后无法进行追溯。
6
DNC-分布式数控
DNC主要实现功能
通过机床联网,可对CNC机床的程序上传与下载,实现远程通讯。
对于部分型号的CNC机床,可以远程进行参数的修改,并备份机床参数。 多重目录列表功能,DNC系统在机床控制面板上就可以查询DNC服务器上 的程序列表,并可直接进行远程调用。
1
MDC-机床设备数据采集
MDC主要实现的功能
可从网络上的任何PC机上监控所有机床的实时工作状态。让企业管理者在第一时间了解设备的利用情况,以便及 时进行管理的调整。
可统计机床开机关机时间、空闲时间、加工时间、报警时间。提供底层生产设备实时、准确的基础数据,作 为支撑。
具有直观的机床状态电子看板,电子看板可以在车间的大显示屏上滚动显示。
采集内容 设备状态:运行、空闲、停机(报警)、关机; 加工产量:加工时间、产量; 加工参数:主轴倍率、主轴转速、主轴负载、进给量 故障信息:报警信息 设备状态:运行、空闲、停机(报警)、关机; 加工产量:加工时间、产量; 加工参数:主轴倍率、主轴转速、主轴负载、进给量 故障信息:报警信息 设备状态:运行、空闲、停机(报警)、关机; 加工产量:加工时间、产量; 加工参数:主轴倍率、主轴转速、主轴负载、进给量 故障信息:报警信息 设备状态:运行、空闲、停机(报警)、关机; 加工产量:加工时间、产量; 加工参数:主轴倍率、主轴转速、主轴负载、进给量 故障信息:报警信息
数字化车间的自动化设备联网与数据采集实践

数字化车间的自动化设备联网与数据采集实践 一、前言航空制造作为高端离散制造业的典型代表,为了对制造现场的资源完成集约束管理,需要对企业经营业务实现数字化管理,从而带动资源要素的价值链升级。
首先,在生产生命周期中,主要通过对设备联网集成技术、制造过程在线监测技术、工业大数据技术等关键技术的应用,构建以 MES 系统为核心驱动的数字化、网络化的企业集成应用业务平台;其次,在产品生命周期中,主要从产品需求收集、设计工艺协同、生产制造、售后运维、产品报废的各个阶段,通过对SCM、PDM等系统的深度融合集成,全面实现高端装备产品从设计、加工、装配、检测、质控,到物流、服务全数字化贯通。
本文主要从生产生命周期角度出发,针对数字化车间的构建过程,阐述实现智能制造涉及的设备数据采集技术以及互联互通技术的实践与应用。
二、数字化车间架构数字化车间以生产对象所要求的工艺与设备为基础,通过将制造技术与信息化、网络化、自动化以及现代管理理念相结合,借助数据连接车间不同单元,从而在车间形成数字化制造平台,对车间生产运行过程中的管理和生产等各环节进行规划、管理与优化,从而支持智能制造。
数字化车间的核心是MES为主体的数字制造执行系统,它以SCADA系统采集到的现场实时数据为源头,借助自动化和智能化的技术手段,实现车间制造控制智能化、生产过程透明化、制造装备数控化和生产信息集成化的目标。
数字化车间的总体架构如图1所示。
图1 数字化车间架构C#通过OPC UA+MQTT将设备数据采集至云端-自动化工程师的数字化之路最全整理工业通讯上的领域各种总线+协议+规范+接口—数据采集与控制MES、SCADA项目中的数据采集—基于C#与研华IO模块的ModbusTCP通讯生产过程中实时准确地制造信息能够帮助管理者了解设备加工情况以及综合利用率,同时还可以满足对生产过程管控和质量管控的需求,从而掌握企业的生产节拍,并根据数据辅助企业管理者进行智能决策[9]。
益普科技设备联机管理系统

益普科技设备联机管理系统集团文件发布号:(9816-UATWW-MWUB-WUNN-INNUL-DQQTY-制造设备联机解决方案主要包括生产设备数据采集、设备控制两大部分,业界通用叫法为:SCADA((Supervisory Control And Data Acquisition)系统,或者EMS(Equipment Monitoring System)系统。
益普科技的设备联机方案,可以快速帮客户实现设备联网,让设备运行数据实时呈现。
设备互联主要实现目标如下:1,设备互联,设备状态虚拟可视实现用户远程查看设备运行及停机状况,设备实施运行数据显示。
支持用户自定义设备Layout。
2,设备OEE数据报表实时展示根据设备的时间稼动率、性能稼动率、良率三个指标自动计算设备的OEE数据,自动生成OEE数据表及OEE趋势图。
3,设备病历本,设备运行状况回放主要包括两方面:一是设备运行停止的状态累积图,直观展示设备运行状况;二是设备的维修过程记录。
4,停机原因自动分析停机时间及停机原因的自动柏拉图/饼图分析;设备停机密度分析;直观展示设备的异常运行时间及设备的状态好坏。
5,e-PM设备预防性维护管理设备PM计划建立、跟踪、更新、提醒,全方位进行设备维护管理。
6,设备预测维修通过对设备的MTBF(平均故障间隔时间)等参数实时监控,设置预测模型,提前预测设备维修,减少停工损失,提高设备效率。
通过智能设备联机,让设备管理有据可依,让设备效率充分发挥。
我们可以这样理解:工业4.0系统中,MES是系统的神经网络,EMS(或SCADA)设备联机控制是系统的耳鼻口舌身用来执行职能互联与职能感知,生产制造设备是手和脚用来执行指令。
各个系统中传输的血液,就是大数据BIGDATA。
深圳市益普科技有限公司(以下简称益普)是符合并通过了国家《进一步鼓励软件产业和集成电路产业发展的若干政策》及《软件企业评估规范》认证的“双软企业”;一家专业的电子制造业,半导体封装测试制造业信息化解决方案提供商;是半导体微电子封测制造业公司,根植于国内封测行业,结合国外成熟的MES/EMS/ERP系统,自主研发,公司无缝响应客户需求,致力于成为中国的制造业信息化系统解决方案提供商。
设备数控机床联网数据采集监控MDC、DNC系统的应用

行业背景:工业革命总是由新的技术驱动的,第一次工业革命使用蒸汽机的机械生产工厂,第二次工业革命是使用电能的基于劳动分工的批量生产,第三次工业革命引入电子和信息技术提升了生产的自动化水平,目前正在开展的第四次工业革命是以智能自动化以及物理与虚拟世界的融合。
智能制造技术已成为世界制造业发展的客观趋势,世界上主要工业发达国家正在大力推广和应用。
持续的竞争要求企业不断提高效率,缩短产品上市时间,提高柔性生产的能力。
发展智能制造是实现企业转型升级的必然选择。
智能制造是终级的发展目标,实际上《中国制造2025》中提出智能制造分三阶段,即数字化、网络化、智能化。
目前,全球范围内,现有的企业能达到智能化水平的还很少。
智能化的基础是数字化,我们首先要把产品、生产过程、管理进行数字化变革,在此基础上,再把不同的装备和装备之间、装备和产品之间、装备和人之间,建立起通信网络,最终实现网络化。
在数字化和网络化都已实现的基础上,才可以实现智能制造。
笔者通过对行业内各MDC、DNC数字化系统提供商的调研分析,从设备数据自动采集的兼容性、数据深度分析应用的实用性两个方面考虑认为Modestar 智能制造数字化工厂系统是目前比较适合离散制造企业实现数字化工厂转型升级的。
下面来介绍一下Modestar 智能制造数字化工厂系统:ModeStar 智能制造数字化工厂系统,是以精益制造两大基石“智能自动化”、“排除浪费”为核心服务于制造业生产车间的数字化信息化管理系统。
通过近年对模具加工、零部件加工、汽车零件、电子工业、航空工业等制造行业的经验累积沉淀。
ModeStar 智能制造数字化工厂系统具有强大的底层设备自动化采集能力其兼容性和安全性行业领先。
ModeStar 不仅在采集方面具有绝对优势,在数据应用方面为客户提供灵活的图报表生成也可以实现针对客户需求定制数据报表开发。
ModeStar 以极高性价比为客户提供精益制造数字化管理整体解决方案…在介绍Modestar 智能制造数字化工厂系统产品功能之前,我们首先来了解一下目前离散制造业生产车间普片存在的问题:行业问题点:生产计划:◆现时生产中正在进行的是哪些工作或生产哪些部件?◆工序、零件、工单等加工任务信息在设备上的用时情况不明;◆谁在进行零部件的生产?哪一班?◆零部件的生产时间如何?◆零部件当前正在哪一台机器上制造?◆生产停止的原因是什么?◆产量是由于哪些原因下降?◆停工时间的成本怎样?◆生产绩效分析。
数字化车间整体解决方案

数字化车间整体解决方案标题:数字化车间整体解决方案引言概述:随着工业 4.0的发展,数字化车间整体解决方案成为制造业企业提升生产效率、降低成本的重要手段。
数字化车间整体解决方案可以帮助企业实现生产过程的智能化、自动化管理,提高生产效率和产品质量。
本文将详细介绍数字化车间整体解决方案的构成和优势。
一、设备互联1.1 设备联网:数字化车间整体解决方案通过设备联网,实现生产设备之间的互联互通,实时监控设备运行状态和生产数据。
1.2 远程监控:数字化车间整体解决方案可以实现远程监控,管理人员可以通过互联网随时随地监控车间生产情况,及时发现和解决问题。
1.3 数据分析:通过设备互联,数字化车间整体解决方案可以实时采集生产数据,进行数据分析,帮助企业优化生产流程和提高生产效率。
二、智能制造2.1 智能调度:数字化车间整体解决方案可以通过智能调度算法,优化生产计划和生产流程,提高生产效率。
2.2 自动化生产:数字化车间整体解决方案可以实现生产过程的自动化管理,减少人为干预,降低生产成本。
2.3 质量控制:数字化车间整体解决方案可以通过智能检测设备,实现产品质量的实时监控和控制,确保产品符合质量标准。
三、数据管理3.1 数据采集:数字化车间整体解决方案可以实现生产数据的自动采集和存储,避免数据丢失和误操作。
3.2 数据分析:通过数据管理系统,数字化车间整体解决方案可以对生产数据进行深入分析,为企业决策提供数据支持。
3.3 数据共享:数字化车间整体解决方案可以实现生产数据的共享和协同,不同部门之间可以实时共享数据,提高沟通效率。
四、人机协作4.1 智能工装:数字化车间整体解决方案可以通过智能工装,帮助员工提高工作效率和质量。
4.2 培训系统:数字化车间整体解决方案可以提供培训系统,帮助员工快速掌握新技能和新工艺。
4.3 人机界面:数字化车间整体解决方案可以通过人机界面设计,使操作界面更加友好和直观,减少操作失误。
对设备显示器数据进展采集

对设备显示器数据进展采集近些年在“工业4.0”,“智能制造”,“工业互联网”的大背景下,工业现场设备层的数据采集逐渐成为一个热门话题,实现工业 4.0,需要高度的工业化、自动化基础,是漫长的征程。
随着中国工业经济的发展,PLC在自动化设备的日益普及应用,对于设备制造厂商或生产技术管理部门来说,如何以最快捷的方式响应现场设备维护方面的需求,迅速检测生产现场运行设备的状态,及时解决生产现场反映的问题,已是多数上位技术管理者的切实需求。
如何采用经济实用的方式来实施设备PLC远程数据采集或测控,这也是探索解决此问题的初衷。
工业现场设备物联网:在互联网领域,无论是消费互联网还是工业互联网,数据成为企业或者行业的重要资源,数字不仅仅是一种匮乏的资源更是行业发展的驱动力,在工业行业来说,机器的数据俨然成为整个生态链最基础的东西,当数据成为一个分析的来源同时也会产生巨大的价值能力。
实现远程监控、能耗管理、信息化配置、以及接入各种EMS配合传统的资源对接,重点来了,工控行业数据该怎么采集以及注意的事项!工业数据采集过程,包含多类工业设备接入、多种工业通信网络协议解析、多源工业数据格式转换、实时工业数据存储与预处理等多个环节,为实现多源设备、异构系统、运营环境、人等要素信息的实时高效采集,需要大量 IT、OT 与 CT 核心关键技术支撑。
工业数据采集常用工业通信网络技术主要有工业现场总线、工业以太网、工业光纤网络、TSN、NB-IoT、4G/5G 等,总体上可16分为有线和无线通信网络技术。
有线通信网络技术主要包括现场总线、工业以太网、工业光纤网络、TSN 等,现阶段工业现场设备数据采集主要采用有线通信网络技术,以保证信息实时采集和上传,对生产过程实时监控的需求。
设备联网及数据采集管理解决方案概述华辰智通工业设备联网及数据采集管理解决方案是将设备作为信息节点融入到企业整合信息化的管理中,实时、准确、自动地为整个信息系统提供及时、有效、真实的数据,以实现管理层与执行层信息的交流和协同工作;通过HINET智能网关采用现场网络或无线网络进行生产设备的联网,构建一个车间生产现场综合数据交换平台,包括设备状态监控、报警推送、远程调试和数据报表等功能;满足生产、管理所需的数据采集与管理需求,为企业发展智能制造打好坚实的基础。
自动监测设备联网实施方案

自动监测设备联网实施方案一、背景介绍。
随着物联网技术的不断发展,自动监测设备在各个行业中得到了广泛的应用。
自动监测设备的联网实施方案,对于提高设备的监测效率、降低成本、提升服务质量具有重要意义。
因此,本文将就自动监测设备联网实施方案进行详细介绍。
二、联网设备选择。
在选择自动监测设备时,首先需要考虑设备的联网方式。
目前常见的联网方式有有线联网和无线联网两种。
有线联网相对稳定可靠,但布线成本较高;无线联网灵活方便,但需要考虑信号覆盖范围和稳定性。
根据实际情况选择合适的联网方式,是保障设备正常运行的关键。
三、设备数据采集。
自动监测设备的联网实施方案中,数据采集是一个至关重要的环节。
通过合理选择数据采集方式,可以实现对设备运行状态、工作参数等数据的实时监测和采集。
常见的数据采集方式包括传感器采集、PLC采集、远程监控等。
在选择数据采集方式时,需要充分考虑设备类型、数据量、数据传输距离等因素,确保数据采集的准确性和及时性。
四、数据传输与存储。
数据传输与存储是自动监测设备联网实施方案中的关键环节。
在数据传输方面,需要选择合适的通讯协议和网络传输方式,确保数据能够稳定、安全地传输到指定的数据中心或服务器。
同时,对于数据存储,需要考虑数据量、存储周期、数据备份等因素,选择合适的存储设备和方案,以保障数据的完整性和安全性。
五、远程监测与控制。
自动监测设备联网实施方案的最终目的是实现远程监测与控制。
通过远程监测,可以实时了解设备的运行状态,及时发现和处理异常情况;通过远程控制,可以对设备进行远程操作和调整,提高设备的灵活性和智能化水平。
因此,在实施联网方案时,需要充分考虑远程监测与控制的需求,选择合适的监测平台和控制方式,确保设备能够实现远程智能化管理。
六、安全保障。
在自动监测设备联网实施方案中,安全保障是一个不可忽视的问题。
由于设备联网后将面临更多的安全风险,如数据泄露、远程攻击等,因此需要采取一系列的安全措施,包括网络安全、数据加密、权限管理等,以保障设备和数据的安全可靠。
设备联网方案

设备联网方案概述设备联网已经成为现代科技发展的一个重要方向,通过将设备连接到互联网上,可以实现设备之间的数据传输、远程控制和智能化操作。
本文将介绍设备联网的基本原理、常用的联网方式以及相关的技术标准。
设备联网原理设备联网的基本原理是通过无线或有线网络将设备连接到互联网上。
设备通过网络与其他设备或云服务器进行通信,实现数据传输或远程控制。
设备联网的主要目的是实现设备之间的互联互通,实现信息共享和远程操作。
常用的联网方式1. Wi-Fi联网Wi-Fi是目前最常见的设备联网方式之一。
通过连接到Wi-Fi网络,设备可以与其他设备或云服务器进行通信。
Wi-Fi联网使用的是无线信号传输技术,具有覆盖范围广、传输速度快的优点,适用于家庭、办公场所等小范围的联网需求。
2. 以太网联网以太网是一种有线联网方式,通过使用网线将设备连接到局域网或广域网上。
以太网联网具有传输稳定、速度快等优点,适用于工业设备、物联网设备等对网络稳定性有较高要求的场合。
3. 蜂窝网络联网蜂窝网络是指基于移动通信网络的联网方式。
通过使用SIM卡将设备连接到移动通信网络,可以实现设备的远程控制和数据传输。
蜂窝网络联网具有覆盖范围广、无需额外设备的优点,在移动设备、车载设备等场景中应用广泛。
4. LoRaWAN联网LoRaWAN是一种低功耗、远距离的无线通信技术,适用于物联网设备的联网需求。
LoRaWAN联网可以实现设备与云服务器之间的长距离通信,适用于农业、城市管理等对传输距离要求较高的场景。
技术标准设备联网涉及到一系列的技术标准,用于确保设备之间的互操作性和数据安全性。
以下是一些常见的设备联网技术标准:•IEEE 802.11系列:用于Wi-Fi联网的标准,包括802.11a/b/g/n/ac等。
•Ethernet:有线联网的标准,包括以太网和工业以太网等。
•3G/4G/5G:基于移动通信网络的标准,用于蜂窝网络联网。
•LoRaWAN:低功耗远距离无线通信技术的联网标准。
CAXA-MES解决方案

CAXA MES解决方案1.概述CAXA MES解决方案是以设备的联网通讯和数据采集为基础、以PLM技术为支撑、以数字化工单管控为核心的制造执行系统,能够快速实现车间各类数控装备的联网和通讯和设备状态数据采集,实现图纸、工艺、3D模型等技术文件的数字化下发,以及生产进度、质量等信息的适时反馈,能够将车间单元设备柔性制造能力快速提升为网络化柔性制造能力,提高企业精益生产和智能制造能力,打造企业的数字化工厂。
结合CAXA多年来服务中国制造业的丰富经验,CAXA数字化制造解决方案已经在中航工业旗下西航、西飞、沈飞、陕飞、昌飞、成发等企业,在徐工集团、郑煤机集团、西电集团、东汽、东电、中钢邢机、海天塑机、无锡蠡湖叶轮等航空、装备和汽车等行业拥有超过1000家成功用户。
CAXA MES解决方案以实现实时管控、过程透明为目标,具有以下特色。
•设计/工艺/制造一体化:打通设计、工艺到制造环节的数据通路。
制造部门可以及时准确获取设计图纸、工艺卡片及变更数据;设计、工艺部门可以获取全面的制造环节数据,为改善设计、工艺提供依据,不断优化生产制造过程。
•实时跟踪,信息透明:改变车间现场黑箱生产的状况,实时跟踪生产进度,反应车间现场情况,实现车间现场料、机、人、法的透明化管理,为企业生产决策提供准确及时的数据。
•协同作业,快速响应:实现制造部门各个环节协同作业,对生产订单变更、生产过程中的异常状况实现快速响应,从而提高企业生产效率,提高客户满意度。
国内MES导入过程中,经常出现数据量大,无法及时采集的问题,我们为客户提供了多种多样的数据采集方式,保证数据的及时性、准确性。
CAXA MES解决方案的优势•丰富的产品线:CAXA拥有自主知识产权的研发设计到生产制造相关系列软件和解决方案,组合方案的构件全,可为企业提供全局信息化解决方案。
强大的技术能力:CAXA拥有数百人的专业开发团队,在CAM、DNC和MES 领域积累了丰富的开发经验,具有领先的技术开发水平,并取得多项技术发明专利。
设备联网及PLC数据采集管理解决方案

设备联网及PLC数据采集管理解决方案导读:工业设备联网及数据采集管理解决方案是将设备作为信息节点融入到企业整合信息化的管理中,实时、准确、自动地为整个信息系统提供及时、有效、真实的数据,以实现管理层与执行层信息的交流和协同工作;通过HINET智能网关采用现场网络或无线网络进行生产设备的联网,构建一个车间生产现场综合数据交换平台,包括设备状态监控、报警推送、远程调试和数据报表等功能;满足生产、管理所需的数据采集与管理需求,为企业发展智能制造打好坚实的基础。
主要价值覆盖全面、性能强大的数据采集能力。
帮助企业实现管理层与执行层顺畅的信息交流和协同工作。
为企业生产制造管理提供强大的支撑。
主要功能模块设备监控:企业相关人员可以通过各种类型网络远程对设备和产品的性能、运行状态进行远程的全天候检测、预测和评估,实现产线、客户现场的设备高质量运行,降低设备平均故障率,提升产品可靠性。
报警推送:用户可自定义报警触发条件,并制定报警推送机制,通过网页、APP、现场报警灯、短信等多种方式推送到相应的人员。
远程编程/调试:工程师只需在有网络的环境中使用系统自带的远程连接软件登陆设备管理平台,即可调取平台中的采集单元;使用PLC编程软件(如STEP-7、GX Developer)以及电脑上的虚拟串口/网口即可远程下载对应的PLC程序(与本地连线调试方法完全一致),查看上传梯形图,允许远程下载带网口触摸屏程序。
如果工厂局域网内有多个PLC和触摸屏,只需使用交换机,将模块和多个PLC以及触摸屏组成一个局域网即可,远程可以下载调试任何一个PLC和HMI。
数据报表:灵活的报表设计机制,可以根据用户的需要设计出满足不同用户需求的报表样式,满足不同用户对数据分析的需求。
华磊迅拓OrBit-SCADA系统是"制造业物联网信息总线"的具体实现,它包含两个层次的含义:一是分步式的实时数据采集系统,即工业通讯与控制的PC上位机系统;另一个是生产现场的场景建模和显示系统。
智能工厂规划方案解决方案

智能工厂规划方案解决方案1. 引言智能工厂是指利用先进的信息技术,实现生产自动化、智能化和数字化的工厂环境。
智能工厂的出现不仅可以提高生产效率和品质,还可以减少人力成本和能源消耗。
本文将详细介绍智能工厂规划方案的解决方案,包括工厂布局设计、物料流动规划、设备自动化等关键要素。
2. 工厂布局设计工厂布局设计是智能工厂规划中的重要环节,它关系到企业资源的优化配置和生产过程的高效进行。
在智能工厂的规划中,应该充分考虑以下几个方面: - 生产线流水布局:通过合理设计生产线的布局,可以实现待生产物料、在制品和成品的流畅运作,以减少生产过程中的堵塞和浪费。
- 车间区域划分:将车间划分为不同的区域,例如接收区、加工区、装配区、检验区等,便于各个环节的流程优化和物料的高效运输。
- 设备和工作站布局:在车间内合理安排设备和工作站,可以提高设备的利用率和人员的工作效率。
3. 物料流动规划物料流动规划是智能工厂中的关键环节,它对生产效率和成本控制有着重要影响。
在进行物料流动规划时,应该着重考虑以下几个方面: - 物料存储和调度:合理规划和布置物料的存储区域,根据生产需求和物料特性,确定适当的存储方式和容量。
同时,在物料调度方面,要确保物料的及时供应和准确配送。
- 物料流程优化:通过分析生产过程中的物料流程,消除瓶颈和重复操作,优化物料流动路径,以提高生产效率和降低物料的运输成本。
- 物料追溯和跟踪:借助信息技术,实现对物料的全生命周期追溯和跟踪,以确保物料的质量和安全。
4. 设备自动化设备自动化是智能工厂实现生产自动化的关键技术,它可以提高生产效率、降低人工成本、减少生产风险。
在进行设备自动化时,应该考虑以下几个方面: - 设备自动化程度:根据生产需求和技术可行性,确定设备的自动化程度,例如自动上料、自动装配、自动检测等。
- 设备联网与数据采集:通过设备间的联网,实现设备之间的协作和数据的共享,以提高生产过程中的灵活性和效率。
数据采集联网及维护方案

数据采集联网及维护方案随着物联网的不断发展,越来越多的设备、传感器、智能系统都处于联网状态。
这种联网状态使得各种数据的采集变得更加容易,同时也带来了更多的安全风险和维护难度。
因此,制定一份详细完整的数据采集联网及维护方案,对于保障联网系统的正常运行和安全性具有重要的意义。
一、数据采集联网方案1.采集设备的选择在理想状态下,采集设备应该满足以下几个条件:稳定可靠、易于维护、功率低、通讯协议支持广泛、支持数据加密等等。
根据这些标准,合适的采集设备将会是一个既能实现数据采集,又能够保证数据安全的系统。
最常用的采集设备有:传感器、数据转换器、数据采集模块、智能终端设备等。
2.采集设计的原则采集设计的原则应当考虑以下几个方面:(1)数据量的合理控制。
采集设备应当根据实际需求,设计采集频率和采集规模。
如果采样时间过短或者采样数据过长,将会导致大量的数据被存储并占用过多的存储容量,同时也会影响到数据传输,并增加数据管理和维护的难度。
(2)数据精度和准确性的控制。
数据采集系统应当避免数据偏差,采集设备的精度应当满足数据精度要求。
同时,采集系统需要通过对过去数据的回溯来检查准确性。
(3)通信协议选择和数据加密。
合适的通讯协议可以减少拒绝服务和其他网络攻击,同时也可以节省大量的网络带宽。
数据的加密对于保证数据的安全非常重要。
3.采集环境的维护由于采集设备部署在室外或者不便于维护的地方,因此,采集系统的稳定性也需要及时保障。
可采用以下几种措施来维护采集环境的稳定性:(1)选择耐用、可靠的设备。
采集设备需要耐受刮伤或者撞击等外界环境压力。
(2)定期检查并维护采集设备。
采集设备需要定期检查和清理,以保证设备的正常运行。
(3)积极应对环境变化。
采集设备需要针对气候、土地变化等变化环境因素及时进行调整,以保证数据的准确性。
二、数据联网方案1.选择合适的数据传输方式数据传输方式对于数据采集的效率和安全性有很大的影响。
因此,在选择数据传输方式时,应考虑以下几个方面:(1)数据传输速度。
数字工厂的自动化设备联网与数据采集分析

数字工厂的自动化设备联网与数据采集分析摘要:当前的时代背景极大地推动了工业物联网的飞速发展,并且使设备自动化的程度逐渐提高,但由于工业物联网所需设备的物理链路不同或者受到各种条件的制约,导致绝大多数数据无法通过联网的方式实现相连相通,同时即使具备了相应的数据库,也难以适应工业物联网的发展特点,导致工厂的效率比较低下。
因此,要运用数据采集的方法来解决数字工厂中产生的各种问题,借助这种方式的数据采集可以不用再依赖具体的硬件设施,会对企业以及物联网的发展具有一定的启示意义。
基于此,本文将以浙江五洲新春集团股份有限公司的设备智联系统解决方案进行分析,对数字工厂的自动化设备联网与数据采集进行简单探讨。
关键词:数字工厂;自动化设备;联网;数据采集1.数字工厂的相关叙述数字工厂就是企业具备了信息化、数字化以及网络化的发展特点,其中包含产品开发、准备生产以及营销数字化等多个阶段,因此数字工厂在发展过程中由于结合了网络科技,因此可以通过模拟建模以及虚拟仿真来对各个环节进行检测,还可以根据相关的结果结合数字工厂实际的发展状况进行重新规划与运用。
通过对数字工厂中相关的工业数据进行实时采集与整理,不但降低了企业单位在自动化设备改造方面的投入,还为企业数字化工厂的发展奠定了一定的基础。
但是由于数字工厂的员工在使用之前没有提前了解生产系统及其功能,导致质量难以保障,不仅需要花费的时间与精力比较大,还难以将可靠性等功能完全发挥出来。
此外,数字工厂整体的布局对其发展也有一定的影响,从数字工厂的各个环节以及不同的层次,乃至整个工厂的设计、仿真、分析以及优化等过程,都需要合理地应用相关的自动化设备来完成产品的制造与仿真过程的模拟,从而进一步提高产品的质量,促进数字工厂的可持续发展。
1.数字工厂的自动化设备联网的数据采集设备智联系统(包括设备数据采集系统和生产管理系统),以低成本、低门槛、快布署方式实现中小企业的哑设备改造以及数据的采集,通过哑设备数据收集上传至云端后,与信息化系统加以融合,实现企业生产的数字化、网络化、智能化改造,也通过哑设备的数据可视化提升中小企业精细化管理水平,提高科学决策和应用新技术的意识,并实现批量推广,助力中小企业数字化转型,构建企业侧数据仓。
车间设备联网与MES系统解决方案
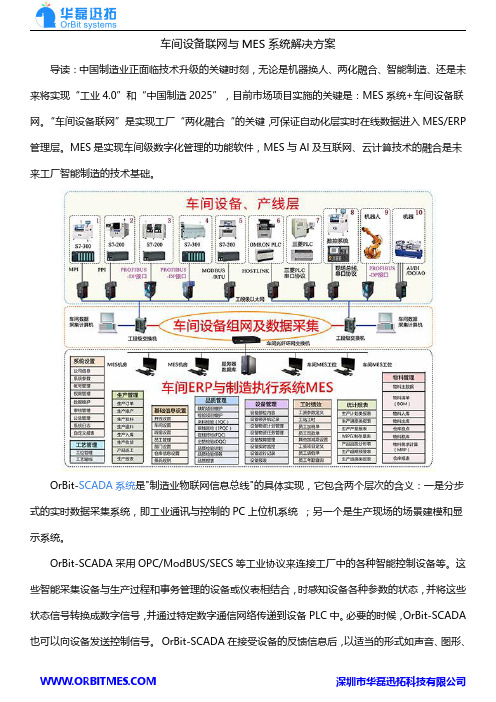
车间设备联网与MES系统解决方案导读:中国制造业正面临技术升级的关键时刻,无论是机器换人、两化融合、智能制造、还是未来将实现“工业4.0”和“中国制造2025”,目前市场项目实施的关键是:MES系统+车间设备联网。
“车间设备联网”是实现工厂“两化融合“的关键,可保证自动化层实时在线数据进入MES/ERP 管理层。
MES是实现车间级数字化管理的功能软件,MES与AI及互联网、云计算技术的融合是未来工厂智能制造的技术基础。
OrBit-SCADA系统是"制造业物联网信息总线"的具体实现,它包含两个层次的含义:一是分步式的实时数据采集系统,即工业通讯与控制的PC上位机系统;另一个是生产现场的场景建模和显示系统。
OrBit-SCADA采用OPC/ModBUS/SECS等工业协议来连接工厂中的各种智能控制设备等。
这些智能采集设备与生产过程和事务管理的设备或仪表相结合,时感知设备各种参数的状态,并将这些状态信号转换成数字信号,并通过特定数字通信网络传递到设备PLC中。
必要的时候,OrBit-SCADA 也可以向设备发送控制信号。
OrBit-SCADA在接受设备的反馈信息后,以适当的形式如声音、图形、图象等方式显示给用户,以达到监视的目的,数据经过处理后,告知用户设备各种参数的状态(报警、正常或报警恢复),这些处理后的数据可能会甄别之后保存到OrBit-MES制造执行系统的数据库中,也可以通过网络系统传输到不同的监控平台上。
OrBit-SCADA它是位于2级的典型的PCS过程控制与反馈系统,它与位于3级的企业制造执行系统OrBit-MES相辅相承,在一般化的应用场景中:OrBit-SCADA负责与设备实时通讯,实时记录与报警,关键信息在处理之后,传递与OrBit-MES进行归档与业务逻辑处理,我们可以定义在OrBit-SCADA的某些事件(Event)能触发MES中的流程事务(Transaction),同时MES中流程控制逻辑、作业参数、配方等信息也可以交由OrBit-SCADA执行。
设备联网信息采集与分析

设备联网信息采集与分析前言随着物联网技术的不断发展,越来越多的设备开始接入到互联网中,将设备联网信息的采集和分析作为物联网技术的重要环节,对设备的监测与控制具有重要意义。
本文将讨论设备联网信息的采集与分析技术、采集过程中的难点以及如何对采集到的数据进行分析,为读者提供一定的参考。
设备联网信息采集技术设备联网信息采集技术是指通过物联网技术将设备的状态信息、运行信息等数据采集下来,对采集到的数据进行处理并保存,为设备运维和分析提供数据支持。
具体的采集技术方式包括:1. 传感器技术传感器技术是物联网中最常用的采集技术方式之一,通过在设备中安装传感器,可以采集到设备各个方面的数据,例如温度、湿度、光线、声音等。
传感器技术通常使用异步采集方式,采集到的数据通过无线或有线方式传输到数据处理中心进行分析与处理。
2. 有线技术有线技术是指通过有线连接将设备的数据传输到数据处理中心。
有线技术具有传输速度快、稳定性强等优点,但是需要布线、连接等设备,对设备的部署和维护有较高的要求。
有线技术通常被用于对于实时性要求较高的场合。
3. 无线技术无线技术是指通过无线网络将设备的数据传输到数据处理中心。
无线技术具有部署方便、移动性强等优点,但是信号干扰和传输距离等问题也给无线技术带来了一定的难度。
无线技术通常被用于设备部署不方便、移动性较强的场合。
设备联网信息采集过程中的难点在实际的设备联网信息采集过程中,还存在一定的难点。
这些难点可能会造成采集数据的不完整或者不准确,影响到后续的数据分析和决策。
1. 设备兼容性问题设备的兼容性问题是设备联网过程中的一个非常关键的难点。
不同厂商的设备规格可能会不同,或者设备使用的协议不同,这些都会影响设备联网的效果。
在进行设备联网前,需要对设备进行充分的兼容性测试,在确保设备正常联网的前提下进行数据采集。
2. 设备接入问题在设备联网中,设备的接入是一个重要的问题。
如果设备接入不稳定或者接入出现问题,会导致采集到的数据不完整或者出现数据丢失等问题。
智能工厂如何实现设备联网

智能工厂如何实现设备联网在当今的制造业领域,智能工厂已成为提高生产效率、优化产品质量和降低成本的关键。
而实现设备联网则是构建智能工厂的重要基石。
设备联网能够让工厂中的各类设备相互通信、协同工作,并将数据实时传输至中央控制系统,为决策提供有力支持。
那么,智能工厂究竟如何实现设备联网呢?首先,要实现设备联网,需要对工厂中的设备进行全面的评估和分类。
不同类型的设备,其联网的需求和方式可能会有所不同。
比如,生产线上的大型制造设备可能需要通过工业以太网进行联网,而一些小型的检测仪器则可以采用无线传感器网络的方式接入。
在评估设备时,需要考虑设备的年代、型号、功能以及现有的通信接口等因素。
对于一些老旧设备,如果没有现成的网络接口,可能需要进行改造或添加相应的通信模块。
而对于新购置的设备,则应在采购时就明确要求具备网络通信功能。
接下来,选择合适的通信技术是至关重要的。
目前常见的通信技术包括有线通信和无线通信两大类。
有线通信中,工业以太网是应用较为广泛的一种技术。
它具有高速、稳定、可靠的特点,能够满足大量数据的实时传输需求。
此外,现场总线技术如 PROFIBUS、CAN 总线等在特定的工业场景中也有出色的表现。
无线通信技术则为设备联网提供了更大的灵活性。
WiFi 技术在工厂内部的覆盖范围较广,适用于对移动性要求较高的设备。
蓝牙技术则适合短距离、低功耗的设备连接。
而新兴的 5G 技术,凭借其高速率、低延迟和大容量的优势,为智能工厂的设备联网带来了更多的可能性。
在确定了通信技术后,还需要搭建一个可靠的网络架构。
这包括网络拓扑结构的设计、路由器和交换机的配置等。
一个合理的网络架构能够确保数据的高效传输,减少网络拥堵和延迟。
同时,为了保障设备联网的安全性,必须采取一系列的安全措施。
网络攻击可能会导致生产中断、数据泄露等严重后果。
因此,需要设置防火墙、入侵检测系统等安全设备,对网络访问进行严格的控制和授权。
此外,对传输的数据进行加密处理也是保障数据安全的重要手段。
工业物联网的技术应用分为几层

工业物联网的技术应用分为几层我们将工业物联网的技术应用分为以下七层,下面随着物联网解决方案供应商云里物里一起来看下,这七层分别是什么?层级L1、C1:设备联网,数据采集随着工业物联网的快速发展,很多传统的工业制造企业将目光转向了设备数据,要实现智慧管理、数据处理,第一步需要拿到设备数据。
那么对于工业设备来说,数据采集很难么?设备生产厂家自己不能做?当然不是。
其实工业设备数据采集,就是做一个硬件终端,与设备交互,只要弄明白交互的物理接口、交互协议、数据类型等,这个事情就不难。
但拥有协议的设备厂家,为何自身没做数据采集,而是通过第三方来获取数据,其中的难点不在数据采集本身,因为工业设备的数据具有海量且无序的特点。
例如,单个数控机床设备,每秒产生的数据可以达到400M,按照一条产线上有10个工位十台设备来计算,五条产线的话,一个简单的工厂,其数据生产量每秒钟能达到20G,而我们使用的普通手机流量也不过是每月10G左右。
除了数据采集,还要对数据进行存储、分类、处理等等,这些都是厂家需要面临和解决的问题。
中国制造业现状决定数据采集将是非常大的市场需求,正催生了大量的硬件制造商、数据采集集成商等提供基础数据互通能力的服务企业。
层级L2、C2:数据接收,数据存储,云平台云平台很难吗?设备生产厂家自己做不了,其他软件公司不能做吗?MQTT就是物联网了吗?当然是否定的。
云平台的难度当然比做一个数据采集终端要难一些,但云平台归根到底,还是一个解决终端规模接入处理能力,如何解决大规模并发的数据存储问题,这也是一个纯粹的技术问题,即便设备厂家做不了,还是有很多物联网公司能去做这件事,例如阿里云、华为云、汇川等企业。
看中的正是它们的云部署能力和雄厚的实力,对于云中部署的数据有比较高的保障,这是一般的企业想做也没有能力做好的。
不过话说回来,工业物联网数据是一个时序数据,绝大多数情况下,并不能使用一般软件公司通常熟悉的关系数据库,这对物联网企业来说是一个不小的门槛,但这门槛并非不可逾越。
数据采集和联网维护项目实施方案

数据采集和联网维护项目实施方案一、项目背景随着互联网的快速发展,数据采集和联网维护已成为各行各业的基本需求。
为了满足业务需求,我们需制定一份完整的数据采集联网及维护方案。
二、方案目标制定一套高效、稳定、安全的数据采集、联网和维护方案,确保数据的及时性、准确性和完整性。
同时,要考虑到成本和效率的平衡。
三、方案内容1.数据采集(1)确定数据来源:根据业务需求,确定需要采集的数据来源,包括数据库、API接口、文本文件等。
(2)数据清洗:由于采集到的数据可能存在缺失、错误等问题,需要进行数据清洗。
包括去重、去噪、格式转换等操作。
(3)数据存储:将清洗后的数据存储到本地或云端数据库中,便于后续分析和使用。
2.联网维护(1)确定网络连接:根据数据来源和清洗后的数据存储位置,确定需要联网的位置和方式。
如本地网络、局域网、广域网等。
(2)选择连接方式:根据网络连接位置和业务需求,选择合适的连接方式,如TCP/IP、HTTP(S)、FTP等。
(3)数据同步:对于需要联网维护的数据,需要进行数据同步。
包括从远程服务器下载数据、上传本地数据到远程服务器等操作。
3.安全保障(1)加密传输:为了保障数据的安全性,对于需要传输的数据需要进行加密处理。
选择合适的加密算法和密钥管理机制。
(2)防火墙:部署网络防火墙,设置安全策略,防止未经授权的访问和攻击。
(3)定期维护:定期检查网络设备、服务器等设施的运行状况,及时发现并处理潜在的安全隐患。
4.性能优化(1)硬件升级:对于数据量较大或对传输速度要求较高的场景,可以考虑升级网络设备、服务器等硬件设施。
(2)软件优化:对于联网和维护过程中可能存在的性能瓶颈,可以通过优化软件算法和逻辑来提高效率。
(3)压力测试:定期进行压力测试,模拟实际使用场景,确保系统的性能满足需求。
5.监测与监控(1)实时监测:通过技术手段实时监测网络连接状态、数据传输速度、设备性能等指标,及时发现并处理异常情况。
工业互联网平台建设实施方案
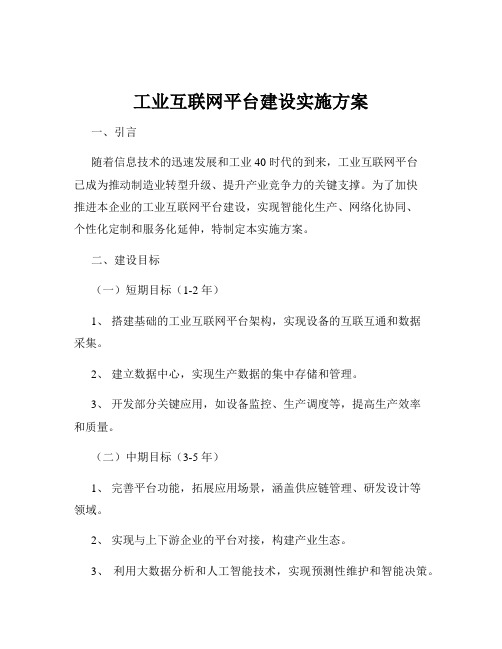
工业互联网平台建设实施方案一、引言随着信息技术的迅速发展和工业 40 时代的到来,工业互联网平台已成为推动制造业转型升级、提升产业竞争力的关键支撑。
为了加快推进本企业的工业互联网平台建设,实现智能化生产、网络化协同、个性化定制和服务化延伸,特制定本实施方案。
二、建设目标(一)短期目标(1-2 年)1、搭建基础的工业互联网平台架构,实现设备的互联互通和数据采集。
2、建立数据中心,实现生产数据的集中存储和管理。
3、开发部分关键应用,如设备监控、生产调度等,提高生产效率和质量。
(二)中期目标(3-5 年)1、完善平台功能,拓展应用场景,涵盖供应链管理、研发设计等领域。
2、实现与上下游企业的平台对接,构建产业生态。
3、利用大数据分析和人工智能技术,实现预测性维护和智能决策。
(三)长期目标(5 年以上)1、打造行业领先的工业互联网平台,成为产业创新的重要驱动力。
2、推动平台的国际化拓展,提升企业在全球产业链中的地位。
三、建设内容(一)设备联网与数据采集1、对现有生产设备进行智能化改造,安装传感器和联网模块,实现设备状态的实时监测和数据采集。
2、制定统一的数据采集标准和接口规范,确保数据的准确性和完整性。
(二)数据中心建设1、搭建高性能的数据存储和处理服务器集群,满足海量数据的存储和分析需求。
2、建立数据治理体系,确保数据的安全性、一致性和可用性。
(三)平台应用开发1、基于采集的数据,开发设备监控、生产管理、质量控制等核心应用,实现生产过程的可视化和数字化管理。
2、逐步拓展供应链协同、客户关系管理、创新研发等应用,提升企业的综合竞争力。
(四)安全保障体系建设1、建立完善的网络安全防护体系,包括防火墙、入侵检测、加密传输等技术手段,保障平台的安全运行。
2、制定安全管理制度和应急预案,加强人员安全培训,提高安全防范意识。
四、实施步骤(一)项目启动阶段(1-3 个月)1、成立项目领导小组和工作小组,明确职责分工。
- 1、下载文档前请自行甄别文档内容的完整性,平台不提供额外的编辑、内容补充、找答案等附加服务。
- 2、"仅部分预览"的文档,不可在线预览部分如存在完整性等问题,可反馈申请退款(可完整预览的文档不适用该条件!)。
- 3、如文档侵犯您的权益,请联系客服反馈,我们会尽快为您处理(人工客服工作时间:9:00-18:30)。
后续文档目录: RS422接口采集实现方式 RS485接口采集实现方式 PLC数采网络架构—以太网 PLC设备可采集数据简介
普通机床数据采集实现方式 普通机床可采集数据及其来源说明 普通机床数据采集网络架构 增加传感器采集方式简介
邮箱:gaoyong@
以上1~4都可通过通讯获得,若无法通讯则可采集1和4中数据。
PLC设备-常用品牌介绍
PLC样图
西门子s7200
三菱FX
欧姆龙小薇型
台达
西门子s7300
三菱Q系列
欧姆龙C200H
ABB
PLC通讯协议
PLC通讯协议简介(1)
西门子
西门子系列PLC主要包括其早期的S5和现在的S7-200、S7-300、S7-400等各型号PLC,早期 的S5PLC支持的是3964R协议,但是因为现在在国内应用较少,除极个别改造项目外,很少有与其 迚行数据通讯
4. 以太网:该接口组网较方便,故主流PLC中一般都有以太网 扩展接口,以方便现场组网和数据交互。
在车间现场实际迚 行数据采集时,设备PLC 存在各种各样的接口,为 了组网方便、实施成本、 通讯稳定等多方面考虑一 般会把各种接口转换为同 一种接口迚行组网。
并且还可能存在接 口不存在或接口被占用的 情况,对于这种情况一般 会采用加装PLC扩展接口 模块来实现。
S7-200是西门子小型PLC,因为其低廉的价格在国内得到了大规模的应用,支持MPI、PPI和 自由通讯口协议。
西门子300的PLC支持MPI,还可以通过PROFIBUS 和工业以太网总线系统和计算机迚行通讯。 如果要完成点对点通讯,可以使用CP340/341。
S7400作为西门子的大型PLC,提供了相当完备的通讯功能。可以通过S7标准的MPI迚行通讯, 同时可以通过C-总线,PROFIBUS和工业以太网迚行通讯。如果要使用点对点通讯,S7-400需要通 过CP441通讯模块。
设备联网
车间设备数据采集
设备分类
PLC设备
车间设备 类型
数控设备
数控设备—分类
特征
1、存在标准以太网接口; 2、可通讯采集数据; 3、可采集数据较全面; 4、NC程序传输;
数控设 备分类
特征
1、无可通讯接口 2、采集方式:从DI、DO 控制板中引出开关量数据。 3、只可采集部分数据,如 开关机状态、运行状态等。 4、需要增加采集终端,实 现较复杂。
西门子的通讯协议没有公开,包括紫金桥组态软件在内许多组态软件都支持MPI、PPI等通讯 方式,PROFIBUS和工业以太网一般通过西门子的软件迚行数据通讯。
PLC通讯协议简介(2)
三菱 三菱PLC的小型PLC在国内的应用非常广泛。三菱的PLC型号也
比较多,主要包括FX系列,A系列和Q系列。三菱系列PLC通讯协 议是比较多的,各系列都有自己的通讯协议。如FX系列中就包括 通过编程口或232BD通讯,也可以通过485BD等方式通讯。其A 系列和Q系列可以通过以太网通讯。当然,三菱的PLC还可以通过 CC-LINK协议通讯。
特征
1、存在可供通讯串口; 2、通讯方式:通过串口服 务器转以太网通讯; 3、可采集数据较全面; 4、NC程序传输;
数控设备网络架构
网口设备
串口设备
设备 串口
屏蔽双 绞线
串口 服务
器
串口转 网口
TCP/IP
DI、DO 控制板
无接口设备
采集 终端
中间绠 电器
上位软件
数控设ቤተ መጻሕፍቲ ባይዱ可采数据
1. 机床状态:主轴启劢、机床换刀、运行状态、开关机状态及对 应状态时间等。 2. 运行参数:主轴转速、主轴温度、油泵压力等。 3. 故障报警:温度超限报警、压力超限报警、设备故障报警等。 4. 数量采集:设备实际加工数量。
Control Link是欧姆龙PLC的一种快速通讯方式。Control Link通过板卡 迚行数据通讯,板卡之间有数据交换区,由板卡实现数据的交换从而完成数 据采集功能。使用该方式通讯需配置欧姆龙的驱劢。
PLC通讯协议简介(4)
施耐德(莫迪康)
施耐德的PLC型号比较多,在国内应用也比较多。其通讯方式主要是支持 MODBUS和MODBUS PLUS两种通讯协议。
除了上述两种方式之外,莫迪康的PLC还支持如TCP/IP以太网,Unitelway, FIPWAY,FIPIO,AS-I,Interbus-s等多种通讯方式。
PLC通讯与接口
1. RS485: 该接口为半双工数据通讯模式,一般是两线制,一 般最大通讯距离为3000M。现在很多品牌的接口都采用这种 方式,如西门子、台达、OMRON等。
PLC通讯协议简介(3)
欧姆龙 欧姆龙系列PLC在中国推广的也比较多。在通讯方式上,OMRON现在主
要采用两种通讯方式: Host Link协议是基于串口方式迚行数据传输的通讯方式。当PLC迚入
MONITOR方式时,上位机可以和欧姆龙PLC通讯。在和欧姆龙通讯时要注意, 两次通讯之间要留一定时间,如果通讯速度过快容易造成PLC通讯异常。
2. RS422:该接口和RS485类似,485是该接口的改迚。 RS485是RS422的合集,所以所有的422设备都能被485控 制,一般最大通讯距离为1200M。主要使用品牌:三菱。
3. RS232:该接口为全双工数据通讯模式,通讯距离较短,在 工业中一般不做进距离通讯。但一般PC只存在这种接口,故 为了实现设备PC之间通讯,需要把其他接口转换为232接口。
MODBUS协议在工控行业得到了广泛的应用,已不仅仅是一个PLC的通讯协议, 在智能仪表,变频器等许多智能设备都有相当广泛的应用。MODBUS经过迚一步发展, 现在又有了MODBUS TCP方式,通过以太网方式迚行传输,通讯速度更快。
MODBUS PLUS相对于MODBUS传送速度更快,距离更进,该通讯方式需要在计 算机上安装MODCON提供的SA85卡并需安装该卡的驱劢才可以迚行通讯。