大型储罐施工方案
大型储罐施工方案

大型储罐施工方案1. 引言大型储罐是用于储存各种液体或气体的容器,在石油化工、化学工业、食品加工等领域有广泛应用。
本文将介绍大型储罐的施工方案,包括施工准备、施工流程、施工工具及安全注意事项等。
2. 施工准备在进行大型储罐的施工前,需要进行充分的准备工作。
2.1 设计评审首先,需要对储罐的施工图纸进行仔细的设计评审。
评审过程主要包括对图纸的合理性、安全性和施工可行性的评估,确保设计方案符合相关标准和规范。
2.2 材料准备根据设计图纸,准备所需的施工材料,包括钢板、焊材、涂料等。
确保材料的质量和数量满足施工要求,并做好材料的保管和清单记录。
2.3 施工人员培训对参与储罐施工的人员进行培训,包括施工工人、安全员等。
培训内容主要包括施工操作规程、安全操作要点以及应急处理等。
3. 施工流程大型储罐的施工流程包括以下几个主要步骤:3.1 地基处理首先,对储罐的施工场地进行地基处理。
这包括平整场地、清除杂物、清洁场地等准备工作。
3.2 钢板准备和预制根据设计要求,对所需的钢板进行准备和预制。
这包括切割、弯曲、焊接等工作,确保钢板的尺寸和质量符合要求。
3.3 钢结构安装在地基处理完成后,开始进行钢结构的安装工作。
这包括立柱、梁、框架等部分的安装。
在安装过程中,需要保证结构的稳定性和安全性。
3.4 焊接工作完成钢结构安装后,开始进行焊接工作。
这包括焊接储罐的壁板、底板以及焊接缝的检测和处理。
在焊接过程中,需要严格按照焊接工艺规范进行操作,确保焊接质量。
3.5 涂装工作储罐焊接完成后,进行涂装工作。
这包括涂装底漆、中间涂层和面漆等工序。
涂装工作需要注意环境温度和湿度,确保涂层的附着力和质量。
3.6 安装附件完成焊接和涂装后,进行储罐的附件安装工作。
这包括进出口管道、液位计、安全阀等附件的安装和连接。
3.7 管道连接和试压完成储罐及其附件安装后,进行管道的连接和试压工作。
在试压过程中,需要检查管道连接的密封性和稳定性,确保系统的正常运行。
大型储罐施工方案1

大型储罐施工方案1大型储罐施工方案1一、前期准备工作1.项目准备:确定大型储罐施工项目的具体要求、规模、工期和技术指标,并与业主进行充分沟通和确认。
2.技术准备:组织相关技术人员进行现场勘察和调研,了解施工地点的地质、气候、环境等情况,以便进行合理设计和施工方案的制定。
3.物资准备:根据项目需求,确定所需的施工材料、设备、机械和工具,并进行采购和安排。
4.人员组织:根据项目规模和施工周期,合理组织施工队伍和人员,并进行必要的技术培训和安全教育。
二、大型储罐的基础施工1.地基处理:根据地质调查结果,采取相应措施对施工地点的地基进行处理,确保地基的稳定和承载力。
2.基础布设:根据设计方案和技术要求,进行大型储罐基础的定位、标高和布置,并确保基础与地基之间的连接牢固。
3.钢筋加工:根据设计要求,对大型储罐的基础进行钢筋加工和安装,确保钢筋的位置准确、间距一致,并与基础牢固连接。
4.混凝土浇筑:按照设计方案和工艺要求,进行混凝土的搅拌、运输和浇筑工作,同时采取必要的措施防止混凝土裂缝和强度不足。
三、大型储罐的主体施工1.储罐制作:按照设计图纸和技术要求,进行储罐的制作和焊接工作,确保制作质量和安全性能。
2.储罐安装:根据现场实际情况和施工方案,进行储罐的吊装、定位和对接工作,确保储罐与基础、管道和附件的连接牢固。
3.密封处理:对储罐进行密封处理,包括对接缝和孔洞的补漏工作,确保储罐的密封性能和防渗功能。
四、大型储罐的附属设备施工1.管道安装:根据设计要求和施工方案,进行储罐周边的管道安装、连接和固定工作,确保管道的通畅和安全性能。
2.防火、防爆设施安装:根据安全规范和技术要求,进行防火、防爆设施的安装和调试,确保储罐的安全运行。
3.控制系统安装:根据设计要求和工艺流程,进行控制系统的安装和调试工作,确保储罐的操控和监测功能正常。
五、大型储罐的验收和交付1.工程验收:在施工完成后,按照相关标准和规范进行工程验收,确保储罐的质量和功能达到设计要求。
储罐施工方案
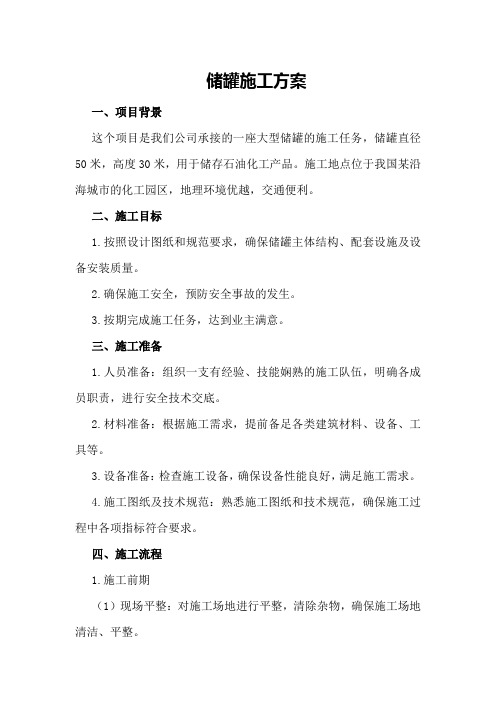
储罐施工方案一、项目背景这个项目是我们公司承接的一座大型储罐的施工任务,储罐直径50米,高度30米,用于储存石油化工产品。
施工地点位于我国某沿海城市的化工园区,地理环境优越,交通便利。
二、施工目标1.按照设计图纸和规范要求,确保储罐主体结构、配套设施及设备安装质量。
2.确保施工安全,预防安全事故的发生。
3.按期完成施工任务,达到业主满意。
三、施工准备1.人员准备:组织一支有经验、技能娴熟的施工队伍,明确各成员职责,进行安全技术交底。
2.材料准备:根据施工需求,提前备足各类建筑材料、设备、工具等。
3.设备准备:检查施工设备,确保设备性能良好,满足施工需求。
4.施工图纸及技术规范:熟悉施工图纸和技术规范,确保施工过程中各项指标符合要求。
四、施工流程1.施工前期(1)现场平整:对施工场地进行平整,清除杂物,确保施工场地清洁、平整。
(2)测量放线:根据设计图纸,进行现场测量,放出储罐基础、罐体、管道等设施的位置线。
2.基础施工(1)基础垫层:按照设计要求,铺设基础垫层,确保基础稳定。
(2)基础模板:根据设计图纸,制作基础模板,保证模板的强度和稳定性。
(3)基础钢筋:按照设计要求,绑扎基础钢筋,确保钢筋间距、长度、直径等符合要求。
(4)基础浇筑:采用商品混凝土,对基础进行浇筑,保证混凝土质量。
3.罐体施工(1)罐壁施工:采用分段施工法,从下至上依次施工罐壁,确保罐壁垂直度、厚度等指标符合要求。
(2)罐顶施工:采用高空作业平台,进行罐顶施工,确保罐顶平整、严密。
(3)罐底施工:采用无缝焊接技术,对罐底进行焊接,保证罐底无泄漏。
4.配套设施及设备安装(1)管道安装:根据设计图纸,进行管道安装,确保管道走向、间距、高度等符合要求。
(2)设备安装:按照设计要求,进行设备安装,确保设备正常运行。
(3)电气安装:进行电气线路的铺设和设备接线,确保电气系统安全可靠。
五、施工质量控制1.严格把控施工材料的质量,确保材料符合国家相关标准。
储罐工程焊接施工方案(3篇)

第1篇一、工程概况本工程为XX储罐项目,位于XX地区。
储罐总容量为XX立方米,包括XX座储罐,分别有XX立方米、XX立方米、XX立方米等不同规格。
储罐材质为XX,罐壁厚度为XX毫米,罐底厚度为XX毫米。
本次施工方案针对储罐主体结构进行焊接施工。
二、施工工艺1. 焊接方法:采用手工电弧焊(SAW)进行焊接,焊接方法应符合GB/T 985.1-2015《钢制焊接压力容器》的要求。
2. 焊材选择:根据储罐材质和焊接要求,选用相应的焊条,焊材牌号应符合GB/T 5293-2017《碳钢焊条》的要求。
3. 焊接顺序:按照先底板、后壁板、再顶板的顺序进行焊接。
4. 焊接设备:选用适合的焊接设备,如CO2气体保护焊机、电弧焊机等。
5. 焊接参数:根据焊材和焊接要求,确定焊接电流、电压、焊接速度等参数。
三、施工步骤1. 施工准备:对施工人员进行技术培训,确保其掌握焊接技术;准备施工所需材料、设备、工具等。
2. 罐底板焊接:先进行罐底板的焊接,采用先中心后边缘、先低后高的焊接顺序。
焊接过程中,注意控制焊接热输入,避免出现裂纹、气孔等缺陷。
3. 罐壁板焊接:罐底板焊接完成后,进行罐壁板的焊接。
先焊接罐壁板的中心线,然后逐渐向两侧扩展。
焊接过程中,注意控制焊接顺序、焊接速度和焊接热输入。
4. 罐顶板焊接:罐壁板焊接完成后,进行罐顶板的焊接。
采用先中心后边缘、先低后高的焊接顺序。
焊接过程中,注意控制焊接热输入,避免出现裂纹、气孔等缺陷。
5. 焊缝检查:焊接完成后,对焊缝进行检查,包括外观检查、无损检测等。
发现缺陷及时进行修复。
6. 焊接记录:记录焊接过程,包括焊材牌号、焊接参数、焊接顺序等。
四、质量控制1. 焊接质量应符合GB/T 985.1-2015《钢制焊接压力容器》的要求。
2. 焊接过程中,严格控制焊接热输入,避免出现裂纹、气孔等缺陷。
3. 焊接完成后,对焊缝进行检查,确保焊接质量。
4. 加强焊接过程的管理,确保焊接质量。
十万方大型储罐倒装施工方案

十万方大型储罐倒装施工方案一、施工背景二、施工准备1.确定施工场地,并对场地进行平整、清理,确保没有障碍物和杂物。
2.对施工现场进行测量,确定施工机械的位置和储罐倒装的具体要求。
3.调集所需的施工机械和设备,如起重机、吊车等。
4.安排人员到场施工,包括机械操作人员、安全员等。
三、施工步骤1.检查储罐的结构完整性和表面的光洁度,确保储罐没有任何损坏和污染。
2.准备好大型起重机,并将其稳定固定在施工现场。
3.将储罐放置在起重机下方,并使用吊车将储罐抬升至合适的高度。
4.将储罐倾斜至适当的角度,并进行固定。
5.检查储罐的安全固定,确保不会出现任何移动和倾斜的情况。
6.检查施工现场的安全措施,确保施工人员和机械的安全。
7.完成储罐倒装施工后,进行清理和整理现场,确保没有遗留杂物和施工垃圾。
四、安全措施1.施工现场要设置专门的警示标识,并采取必要的封闭措施,防止外来人员进入。
2.在施工现场设置专门的交通指示牌,指示人员和机械的行进方向,确保施工现场的交通畅通。
3.施工人员要佩戴个人防护用品,包括安全帽、防护服、防护手套等。
4.机械操作人员要经过专门培训,并具备相应的资格证书。
5.施工过程中,要定期检查机械设备的完好性和安全性能,确保其正常运行。
六、施工效果评估通过以上步骤的施工,储罐的倒装工作能够顺利进行,施工现场秩序井然,施工人员和机械的安全得到了保障。
七、总结十万方大型储罐倒装施工方案的制定和实施,为大型储罐倒装施工提供了具体的指导,保障了施工的顺利进行和人员、设备的安全。
但在具体施工过程中,仍需根据实际情况进行具体操作,并严格遵守相关的安全规范和操作规程。
大型储罐施工方案
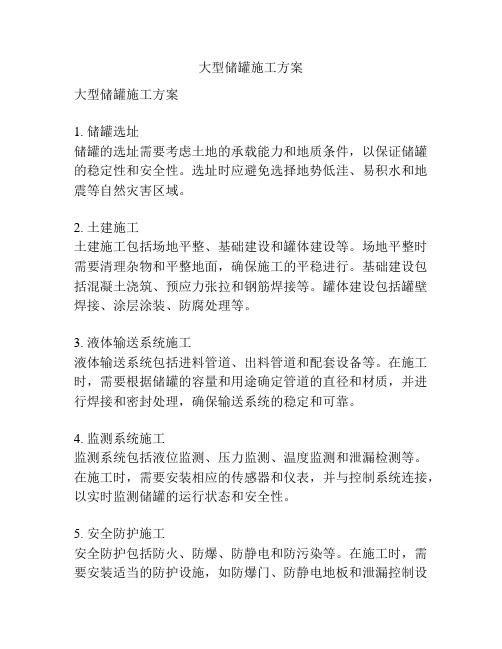
大型储罐施工方案大型储罐施工方案1. 储罐选址储罐的选址需要考虑土地的承载能力和地质条件,以保证储罐的稳定性和安全性。
选址时应避免选择地势低洼、易积水和地震等自然灾害区域。
2. 土建施工土建施工包括场地平整、基础建设和罐体建设等。
场地平整时需要清理杂物和平整地面,确保施工的平稳进行。
基础建设包括混凝土浇筑、预应力张拉和钢筋焊接等。
罐体建设包括罐壁焊接、涂层涂装、防腐处理等。
3. 液体输送系统施工液体输送系统包括进料管道、出料管道和配套设备等。
在施工时,需要根据储罐的容量和用途确定管道的直径和材质,并进行焊接和密封处理,确保输送系统的稳定和可靠。
4. 监测系统施工监测系统包括液位监测、压力监测、温度监测和泄漏检测等。
在施工时,需要安装相应的传感器和仪表,并与控制系统连接,以实时监测储罐的运行状态和安全性。
5. 安全防护施工安全防护包括防火、防爆、防静电和防污染等。
在施工时,需要安装适当的防护设施,如防爆门、防静电地板和泄漏控制设备等,以确保储罐的安全运行。
6. 环境保护施工环境保护包括噪音控制、废水处理和废气处理等。
在施工时,需要采取相应的措施,如安装噪音屏障、建设废水处理设施和使用环保型材料等,确保施工过程对环境的影响最小化。
7. 工期管理在施工过程中,需要制定详细的施工计划和进度安排,确保各项工作按时完成。
同时,需要进行现场管理和监督,解决施工中的问题和协调各方的合作。
8. 质量管理施工过程中,需要严格控制质量,保证施工的合格性和安全性。
可以采取质检和抽查等方式,确保施工质量符合规范和标准要求。
综上所述,大型储罐施工方案需要考虑土地选址、土建施工、液体输送系统施工、监测系统施工、安全防护施工、环境保护施工、工期管理和质量管理等多个方面,以确保施工的安全和可靠。
储罐安装施工方案(3篇)
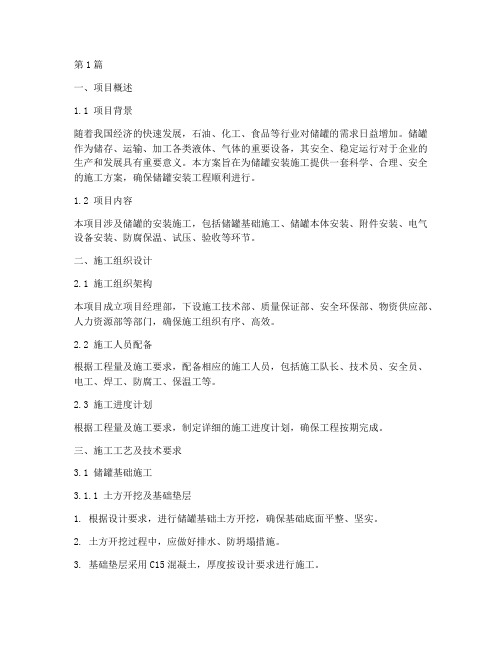
第1篇一、项目概述1.1 项目背景随着我国经济的快速发展,石油、化工、食品等行业对储罐的需求日益增加。
储罐作为储存、运输、加工各类液体、气体的重要设备,其安全、稳定运行对于企业的生产和发展具有重要意义。
本方案旨在为储罐安装施工提供一套科学、合理、安全的施工方案,确保储罐安装工程顺利进行。
1.2 项目内容本项目涉及储罐的安装施工,包括储罐基础施工、储罐本体安装、附件安装、电气设备安装、防腐保温、试压、验收等环节。
二、施工组织设计2.1 施工组织架构本项目成立项目经理部,下设施工技术部、质量保证部、安全环保部、物资供应部、人力资源部等部门,确保施工组织有序、高效。
2.2 施工人员配备根据工程量及施工要求,配备相应的施工人员,包括施工队长、技术员、安全员、电工、焊工、防腐工、保温工等。
2.3 施工进度计划根据工程量及施工要求,制定详细的施工进度计划,确保工程按期完成。
三、施工工艺及技术要求3.1 储罐基础施工3.1.1 土方开挖及基础垫层1. 根据设计要求,进行储罐基础土方开挖,确保基础底面平整、坚实。
2. 土方开挖过程中,应做好排水、防坍塌措施。
3. 基础垫层采用C15混凝土,厚度按设计要求进行施工。
3.1.2 基础垫层施工1. 混凝土浇筑前,对基础垫层进行清理,确保表面干净、无杂物。
2. 混凝土浇筑过程中,应严格控制混凝土的配合比及坍落度,确保混凝土质量。
3. 混凝土浇筑后,应及时进行养护,确保强度达到设计要求。
3.2 储罐本体安装3.2.1 储罐本体组装1. 按照设计图纸,将储罐本体分段进行组装,确保组装精度。
2. 组装过程中,严格控制组装间隙,确保储罐本体组装质量。
3.2.2 储罐本体焊接1. 焊接前,对储罐本体进行清理,确保焊接质量。
2. 焊接过程中,采用合理的焊接工艺,确保焊接质量。
3. 焊接完成后,对焊缝进行无损检测,确保焊缝质量。
3.3 附件安装3.3.1 附件选型1. 根据设计要求,选择合适的附件,包括进出口管道、人孔、排污口、液位计、安全阀等。
大型储罐内浮盘安装施工方案
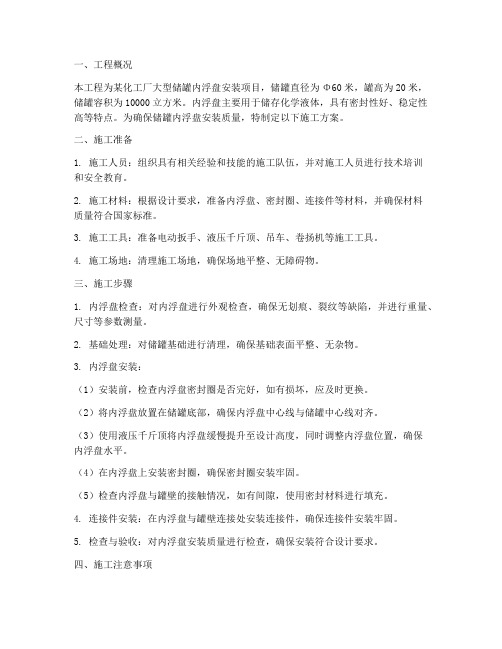
一、工程概况本工程为某化工厂大型储罐内浮盘安装项目,储罐直径为Φ60米,罐高为20米,储罐容积为10000立方米。
内浮盘主要用于储存化学液体,具有密封性好、稳定性高等特点。
为确保储罐内浮盘安装质量,特制定以下施工方案。
二、施工准备1. 施工人员:组织具有相关经验和技能的施工队伍,并对施工人员进行技术培训和安全教育。
2. 施工材料:根据设计要求,准备内浮盘、密封圈、连接件等材料,并确保材料质量符合国家标准。
3. 施工工具:准备电动扳手、液压千斤顶、吊车、卷扬机等施工工具。
4. 施工场地:清理施工场地,确保场地平整、无障碍物。
三、施工步骤1. 内浮盘检查:对内浮盘进行外观检查,确保无划痕、裂纹等缺陷,并进行重量、尺寸等参数测量。
2. 基础处理:对储罐基础进行清理,确保基础表面平整、无杂物。
3. 内浮盘安装:(1)安装前,检查内浮盘密封圈是否完好,如有损坏,应及时更换。
(2)将内浮盘放置在储罐底部,确保内浮盘中心线与储罐中心线对齐。
(3)使用液压千斤顶将内浮盘缓慢提升至设计高度,同时调整内浮盘位置,确保内浮盘水平。
(4)在内浮盘上安装密封圈,确保密封圈安装牢固。
(5)检查内浮盘与罐壁的接触情况,如有间隙,使用密封材料进行填充。
4. 连接件安装:在内浮盘与罐壁连接处安装连接件,确保连接件安装牢固。
5. 检查与验收:对内浮盘安装质量进行检查,确保安装符合设计要求。
四、施工注意事项1. 施工过程中,确保施工人员安全,佩戴必要的安全防护用品。
2. 严格按照设计要求进行施工,确保内浮盘安装质量。
3. 注意内浮盘与罐壁的接触情况,确保密封良好。
4. 施工过程中,注意保护内浮盘和密封圈,避免损坏。
5. 施工完成后,进行验收,确保内浮盘安装质量符合设计要求。
五、施工进度安排1. 施工准备:3天2. 内浮盘安装:5天3. 检查与验收:2天总计:10天六、质量保证措施1. 严格遵循国家相关标准和规范进行施工。
2. 对施工人员进行技术培训和安全教育,提高施工人员的综合素质。
储油罐施工方案(3篇)
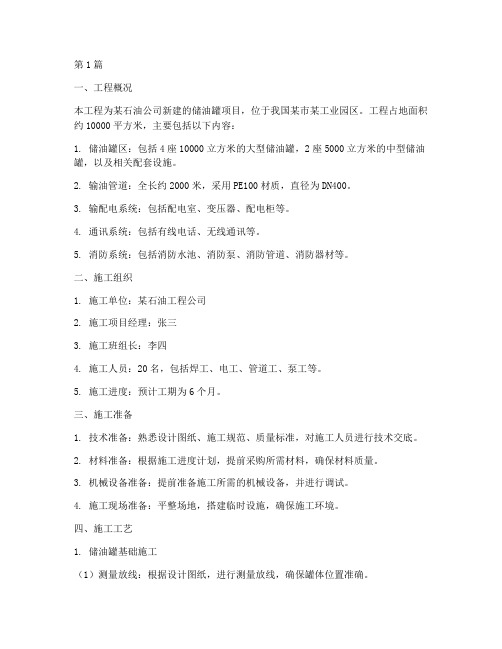
第1篇一、工程概况本工程为某石油公司新建的储油罐项目,位于我国某市某工业园区。
工程占地面积约10000平方米,主要包括以下内容:1. 储油罐区:包括4座10000立方米的大型储油罐,2座5000立方米的中型储油罐,以及相关配套设施。
2. 输油管道:全长约2000米,采用PE100材质,直径为DN400。
3. 输配电系统:包括配电室、变压器、配电柜等。
4. 通讯系统:包括有线电话、无线通讯等。
5. 消防系统:包括消防水池、消防泵、消防管道、消防器材等。
二、施工组织1. 施工单位:某石油工程公司2. 施工项目经理:张三3. 施工班组长:李四4. 施工人员:20名,包括焊工、电工、管道工、泵工等。
5. 施工进度:预计工期为6个月。
三、施工准备1. 技术准备:熟悉设计图纸、施工规范、质量标准,对施工人员进行技术交底。
2. 材料准备:根据施工进度计划,提前采购所需材料,确保材料质量。
3. 机械设备准备:提前准备施工所需的机械设备,并进行调试。
4. 施工现场准备:平整场地,搭建临时设施,确保施工环境。
四、施工工艺1. 储油罐基础施工(1)测量放线:根据设计图纸,进行测量放线,确保罐体位置准确。
(2)挖土方:根据设计要求,挖除基础土方,达到设计标高。
(3)垫层铺设:铺设C15混凝土垫层,厚度为150mm。
(4)基础钢筋绑扎:按照设计要求,绑扎基础钢筋,确保钢筋间距、锚固长度等符合规范。
(5)混凝土浇筑:采用泵送混凝土,确保混凝土质量。
2. 储油罐罐体施工(1)罐体焊接:采用双面埋弧焊,确保焊接质量。
(2)罐底焊接:罐底焊接采用全焊透焊接,确保焊接质量。
(3)罐壁焊接:罐壁焊接采用分段焊接,每段长度不超过6米,焊接顺序为先内后外。
(4)罐顶焊接:罐顶焊接采用分段焊接,每段长度不超过6米,焊接顺序为先内后外。
3. 输油管道施工(1)管道下沟:根据设计要求,挖掘管道沟槽,确保管道埋深、坡度等符合规范。
(2)管道焊接:采用电弧焊,确保焊接质量。
大型储罐满堂架专项方案

一、编制依据1. 国家相关建筑安全生产法规及标准。
2. 建筑施工模板安全技术规范。
3. 钢结构工程施工质量验收规范。
4. 施工组织设计及施工图纸。
二、工程概况本工程为某大型储罐项目,储罐容积为50000立方米,罐体高度为25米,直径为60米。
储罐基础为钢筋混凝土结构,罐体采用现场组焊的钢制结构。
施工现场位于XX市XX区,占地面积约20000平方米。
三、施工部署1. 组织机构:成立专项施工小组,负责满堂架的搭设、检查、验收及拆除工作。
2. 施工流程:基础验收→材料验收→满堂架搭设→满堂架检查验收→满堂架拆除。
四、满堂架设计1. 满堂架结构形式:采用扣件式钢管满堂架,立杆间距为1.5米,水平杆步距为1.5米,扫地杆间距为1米。
2. 满堂架材料:采用φ48×3.5毫米的钢管和Q235材质的扣件。
3. 满堂架搭设高度:满堂架高度为罐体高度加上0.5米的安全距离,即25.5米。
五、满堂架搭设要求1. 基础处理:对基础进行检查,确保平整、坚实,如有必要,进行基础加固。
2. 材料验收:对钢管、扣件等材料进行检查,确保符合设计要求。
3. 搭设顺序:先搭设立杆,再搭设水平杆,最后搭设扫地杆。
4. 连接要求:钢管与扣件连接牢固,扣件拧紧到位。
5. 加固措施:在满堂架四周设置斜撑,确保满堂架的稳定性。
六、满堂架检查与验收1. 检查内容:满堂架的搭设质量、材料质量、连接质量、加固措施等。
2. 验收标准:符合相关规范及设计要求。
七、满堂架拆除1. 拆除顺序:先拆除斜撑,再拆除扫地杆,最后拆除水平杆和立杆。
2. 拆除注意事项:拆除过程中,注意安全,防止人员受伤和设备损坏。
八、安全技术措施1. 人员培训:对施工人员进行安全教育培训,提高安全意识。
2. 安全防护:施工人员必须佩戴安全帽、安全带等防护用品。
3. 现场监控:设立安全员,对施工现场进行全程监控,确保施工安全。
九、总结本方案旨在确保大型储罐满堂架施工的安全、顺利进行。
大型储罐移位施工方案
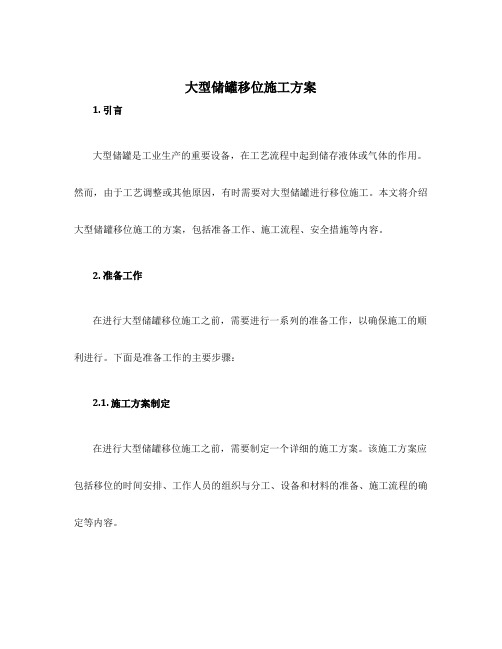
大型储罐移位施工方案1. 引言大型储罐是工业生产的重要设备,在工艺流程中起到储存液体或气体的作用。
然而,由于工艺调整或其他原因,有时需要对大型储罐进行移位施工。
本文将介绍大型储罐移位施工的方案,包括准备工作、施工流程、安全措施等内容。
2. 准备工作在进行大型储罐移位施工之前,需要进行一系列的准备工作,以确保施工的顺利进行。
下面是准备工作的主要步骤:2.1. 施工方案制定在进行大型储罐移位施工之前,需要制定一个详细的施工方案。
该施工方案应包括移位的时间安排、工作人员的组织与分工、设备和材料的准备、施工流程的确定等内容。
2.2. 安全评估大型储罐移位施工是一项高风险的工作,必须进行详细的安全评估。
评估包括对施工现场的环境、设备和人员的安全进行综合评估,以确定潜在的风险和应对措施。
2.3. 材料准备在进行大型储罐移位施工之前,需要准备好所需的材料和设备。
这包括起重设备、支撑材料、防护装置等。
同时,也需检查移动路径,保证路径畅通,能够容纳起重设备和储罐的尺寸。
3. 施工流程大型储罐移位施工的流程分为准备阶段、移动阶段和固定阶段三个主要阶段。
3.1. 准备阶段在准备阶段,需要进行以下工作: - 选派专业人员进行施工,包括指挥人员、技术人员、作业人员等; - 检查工作场所,保证施工现场的整洁和安全; - 组织培训,培训施工人员的专业知识和操作技能; - 准备所需材料和设备,包括起重设备、支撑材料、防护装置等。
3.2. 移动阶段移动阶段是整个施工过程的关键阶段。
在移动阶段,需要进行以下工作: - 使用起重设备将储罐从原位置上起吊,注意保持储罐的平衡和稳定; - 缓慢将储罐移动到新的位置,并确保储罐的准确对位; - 在移动过程中,需要考虑现场的限制条件,如起重设备的尺寸限制、地面承载能力等。
3.3. 固定阶段在移动阶段完成后,需要进行固定阶段的工作: - 使用支撑材料将储罐稳定固定在新位置上,确保储罐不会晃动或倾斜; - 进行连接管道的调整和修复,确保储罐能够正常工作; - 检查施工质量,确保移位施工过程中没有引起其他损坏或问题。
大型储油罐项目混凝土工程施工方案
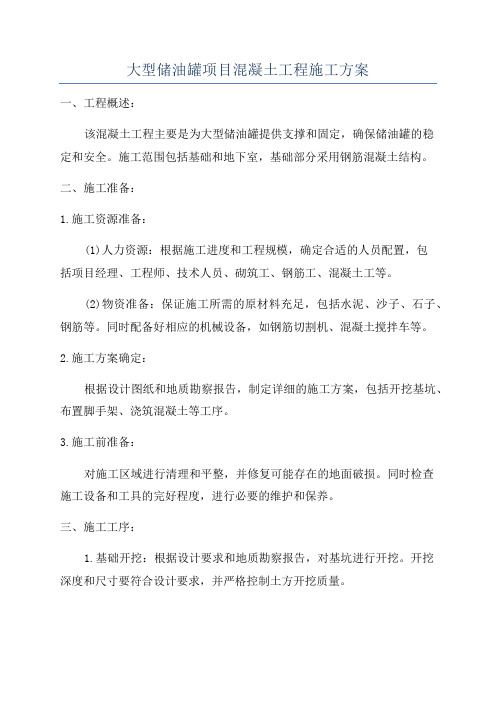
大型储油罐项目混凝土工程施工方案一、工程概述:该混凝土工程主要是为大型储油罐提供支撑和固定,确保储油罐的稳定和安全。
施工范围包括基础和地下室,基础部分采用钢筋混凝土结构。
二、施工准备:1.施工资源准备:(1)人力资源:根据施工进度和工程规模,确定合适的人员配置,包括项目经理、工程师、技术人员、砌筑工、钢筋工、混凝土工等。
(2)物资准备:保证施工所需的原材料充足,包括水泥、沙子、石子、钢筋等。
同时配备好相应的机械设备,如钢筋切割机、混凝土搅拌车等。
2.施工方案确定:根据设计图纸和地质勘察报告,制定详细的施工方案,包括开挖基坑、布置脚手架、浇筑混凝土等工序。
3.施工前准备:对施工区域进行清理和平整,并修复可能存在的地面破损。
同时检查施工设备和工具的完好程度,进行必要的维护和保养。
三、施工工序:1.基础开挖:根据设计要求和地质勘察报告,对基坑进行开挖。
开挖深度和尺寸要符合设计要求,并严格控制土方开挖质量。
2.基础处理:对开挖的基坑进行土方分层处理,确保坑底平整。
对需要加强的土层,采取加固措施,如灌注钢筋混凝土等。
3.基础浇筑:按照工期计划,进行基础钢筋的布置和绑扎。
在钢筋安装完成后,开始进行混凝土浇筑,采用泵送的方式。
4.地下室:(1)地下室施工:根据设计要求,进行地下室墙体和地板的施工。
采用模板结构,配合钢筋的安装,进行混凝土的浇筑。
(2)地下室防水:地下室施工完成后,进行防水层的处理。
选用适当的防水材料和施工工艺,确保地下室的防水效果。
5.完工验收:(1)结构完工:待混凝土养护期满后,进行结构的验收。
检查混凝土的强度、外观和尺寸是否符合设计要求。
(2)细部完工:对混凝土结构的细部进行检查和修复,包括缺陷处理、表面涂漆等。
四、质量控制与安全管理:1.质量控制:严格按照设计要求和施工规范进行施工,确保混凝土的强度、密实性和表面平整度等质量指标符合要求。
2.安全管理:根据工程特点和施工环境,制定安全生产计划和施工方案,确保施工过程中人员的安全。
27万立方米储罐施工方案
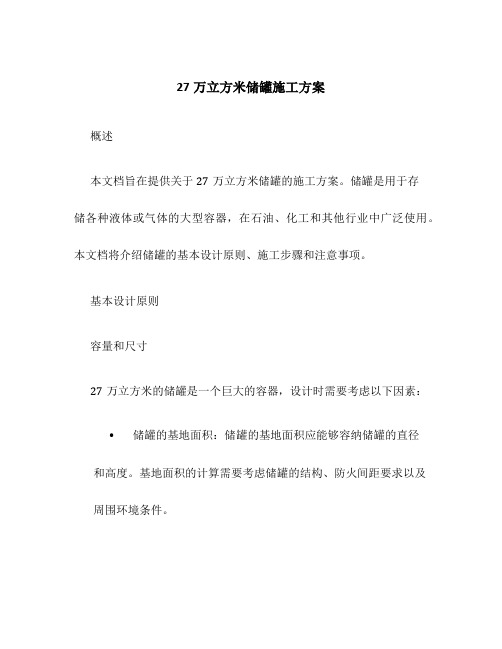
27万立方米储罐施工方案概述本文档旨在提供关于27万立方米储罐的施工方案。
储罐是用于存储各种液体或气体的大型容器,在石油、化工和其他行业中广泛使用。
本文档将介绍储罐的基本设计原则、施工步骤和注意事项。
基本设计原则容量和尺寸27万立方米的储罐是一个巨大的容器,设计时需要考虑以下因素:•储罐的基地面积:储罐的基地面积应能够容纳储罐的直径和高度。
基地面积的计算需要考虑储罐的结构、防火间距要求以及周围环境条件。
•储罐的直径和高度:直径和高度的选择取决于存储物料的特性、容量要求、施工成本和操作可行性。
设计时需要合理平衡这些因素。
结构设计储罐的结构设计主要包括罐壁、罐底和屋顶的设计。
•罐壁:罐壁的设计要满足承受储存物料重量、内部和外部压力、温度变化等要求。
通常采用钢板焊接、铆接或钢筋混凝土等材料。
•罐底:罐底的设计要考虑储存物料的排放和充放载的要求。
常用的罐底结构包括平底、锥底和球底。
•屋顶:屋顶的设计要考虑防止泄漏和减少物料蒸发的要求。
常用的屋顶结构包括浮顶、锥顶和球顶。
安全考虑储罐施工中的安全问题是至关重要的。
以下是一些需要注意的安全考虑事项:•材料选择:选择耐腐蚀、耐高温和耐压的材料以确保储罐的结构稳定性和使用寿命。
•防火设计:储罐的防火设计要满足相关法规和标准的要求,保证防火间距、消防设施等的合理布置。
•环境影响评估:施工前需要进行环境影响评估,确保其不会对周围生态环境造成负面影响。
施工步骤土建施工1.地基处理:在储罐基地上清理土地、平整地表,并进行必要的土方开挖和填筑,确保地基的稳定性和承重能力。
2.基础建设:根据储罐设计要求进行基础的建设,包括打桩、浇筑混凝土等。
3.罐壁施工:根据储罐设计要求进行罐壁的施工,根据使用的材料进行焊接、铆接或浇筑混凝土等工作。
4.罐底施工:根据储罐设计要求进行罐底的施工,包括平底、锥底或球底的建设。
内外表面处理1.表面处理:对罐壁进行除锈、清洗和防腐处理,确保罐壁的平整度和耐腐蚀性。
大型储罐基础工程施工方案
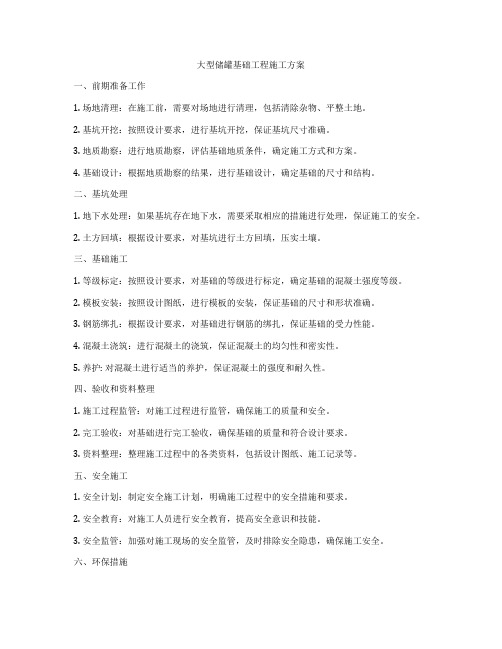
大型储罐基础工程施工方案一、前期准备工作1. 场地清理:在施工前,需要对场地进行清理,包括清除杂物、平整土地。
2. 基坑开挖:按照设计要求,进行基坑开挖,保证基坑尺寸准确。
3. 地质勘察:进行地质勘察,评估基础地质条件,确定施工方式和方案。
4. 基础设计:根据地质勘察的结果,进行基础设计,确定基础的尺寸和结构。
二、基坑处理1. 地下水处理:如果基坑存在地下水,需要采取相应的措施进行处理,保证施工的安全。
2. 土方回填:根据设计要求,对基坑进行土方回填,压实土壤。
三、基础施工1. 等级标定:按照设计要求,对基础的等级进行标定,确定基础的混凝土强度等级。
2. 模板安装:按照设计图纸,进行模板的安装,保证基础的尺寸和形状准确。
3. 钢筋绑扎:根据设计要求,对基础进行钢筋的绑扎,保证基础的受力性能。
4. 混凝土浇筑:进行混凝土的浇筑,保证混凝土的均匀性和密实性。
5. 养护: 对混凝土进行适当的养护,保证混凝土的强度和耐久性。
四、验收和资料整理1. 施工过程监管:对施工过程进行监管,确保施工的质量和安全。
2. 完工验收:对基础进行完工验收,确保基础的质量和符合设计要求。
3. 资料整理:整理施工过程中的各类资料,包括设计图纸、施工记录等。
五、安全施工1. 安全计划:制定安全施工计划,明确施工过程中的安全措施和要求。
2. 安全教育:对施工人员进行安全教育,提高安全意识和技能。
3. 安全监管:加强对施工现场的安全监管,及时排除安全隐患,确保施工安全。
六、环保措施1. 不断进步学习和改进:要提高员工队伍的环保意识,制定出一系列的从业操作规范、控制技术措施和操作方法,组织推广会和环保培训班,使工人对一些常见的污染源给以负责对待。
2. 依法经营:遵守国家各级政府关于污染环境保护方面的法律法规,按照国家的技术、印安态和管理标准进行科学施工,减少废气、废水的排放,预防或减少对环境的积极影响,努力实现国家的污染取控制标准。
大型石油储罐工程施工方案

大型石油储罐工程施工方案一、项目概况在当前石油市场需求高涨的情况下,大型石油储罐工程成为了一个备受瞩目的项目。
石油储罐是用于存储原油及石油产品的重要设施,其建设对于提高石油储备能力以及满足市场需求有着重要作用。
本文旨在对大型石油储罐工程的施工方案进行详细的介绍,包括施工组织设计、工序安排、质量控制、安全管理等方面的内容。
二、施工组织设计1. 部门设置为了保证项目的有序进行,施工方案中需要明确各个部门的设置。
包括工程部、安全生产部、质量管理部、物资部、机电部等。
并设立各部门的职责、人员构成以及工作流程。
2. 人员组织施工中需要各类专业人员,如工程师、技术员、监理工程师、安全员等。
需要根据具体的施工情况,合理安排人员,并对其进行专业培训以及安全教育。
3. 施工队伍在项目启动之初需建立施工队伍,包括土建施工队、设备安装队、电气施工队等。
需要根据工程的进度合理安排各个施工队伍的任务分工。
三、工序安排1. 土建工程土建工程是整个石油储罐工程的基础工程,包括地基处理、基础建设、罐壁施工等。
在施工组织设计中,需要对土建工程的施工顺序、工艺流程、质量要求进行详细规划。
2. 设备安装设备安装是整个工程的重要环节,包括钢构件安装、设备调试等。
在施工中需要进行专业的测量、安装、校准等工序,以确保设备的正常使用。
3. 电气安装电气安装是整个工程的关键环节,需要对整个石油储罐的电气系统进行布线、连接、调试等工序,确保电气设备的正常运行。
四、质量控制1. 质量检验在整个施工过程中需要进行严格的质量检验,包括原材料的检验、施工工艺的检验、成品的检验等,以确保项目的质量符合标准要求。
2. 质量管理质量管理是施工中一个重要的环节,需要建立质量管理制度,包括质量管理档案、质量问题整改、质量验收等,以确保项目的质量符合规定标准。
3. 质量评定在项目结束时需要进行质量评定,对项目的整体质量进行评估,对其中存在的问题进行整改,并对整个项目的质量进行总结。
大型沥青储罐工程施工方案
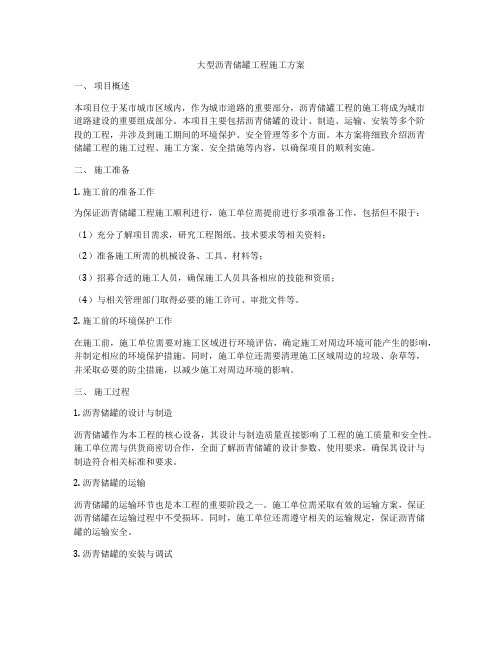
大型沥青储罐工程施工方案一、项目概述本项目位于某市城市区域内,作为城市道路的重要部分,沥青储罐工程的施工将成为城市道路建设的重要组成部分。
本项目主要包括沥青储罐的设计、制造、运输、安装等多个阶段的工程,并涉及到施工期间的环境保护、安全管理等多个方面。
本方案将细致介绍沥青储罐工程的施工过程、施工方案、安全措施等内容,以确保项目的顺利实施。
二、施工准备1. 施工前的准备工作为保证沥青储罐工程施工顺利进行,施工单位需提前进行多项准备工作,包括但不限于:(1)充分了解项目需求,研究工程图纸、技术要求等相关资料;(2)准备施工所需的机械设备、工具、材料等;(3)招募合适的施工人员,确保施工人员具备相应的技能和资质;(4)与相关管理部门取得必要的施工许可、审批文件等。
2. 施工前的环境保护工作在施工前,施工单位需要对施工区域进行环境评估,确定施工对周边环境可能产生的影响,并制定相应的环境保护措施。
同时,施工单位还需要清理施工区域周边的垃圾、杂草等,并采取必要的防尘措施,以减少施工对周边环境的影响。
三、施工过程1. 沥青储罐的设计与制造沥青储罐作为本工程的核心设备,其设计与制造质量直接影响了工程的施工质量和安全性。
施工单位需与供货商密切合作,全面了解沥青储罐的设计参数、使用要求,确保其设计与制造符合相关标准和要求。
2. 沥青储罐的运输沥青储罐的运输环节也是本工程的重要阶段之一。
施工单位需采取有效的运输方案,保证沥青储罐在运输过程中不受损坏。
同时,施工单位还需遵守相关的运输规定,保证沥青储罐的运输安全。
3. 沥青储罐的安装与调试沥青储罐的安装与调试是本工程的重要施工阶段。
施工单位需根据工程图纸和相关规范要求,采取适当的安装方案,确保沥青储罐的安装质量和安全性。
在安装完成后,还需进行必要的调试工作,保证沥青储罐的正常运行。
四、安全管理1. 现场施工安全为保障沥青储罐工程的安全施工,施工单位需加强现场安全管理工作。
大型储罐制作安装施工方案范文

大型储罐制作安装施工方案1. 前言大型储罐是一种重要的工业设备,被广泛应用于石油、化工、食品等行业。
它主要用于储存各种液态物质,如原油、煤油、液化气等。
储罐的制作和安装需要专业化的技术和工程师,本文将介绍大型储罐的制作安装施工方案。
2. 制作2.1 设计制作大型储罐前,首先需要进行设计。
设计过程中需要考虑以下因素:•储存物质的性质和特点•储存物质的数量和密度•储罐的尺寸和型号•储罐的形状和结构•储罐的材料和强度设计完成后,需要进行详细的制作工艺和步骤规划,并制定相关的制作计划。
2.2 材料准备在进行制作前,需准备以下材料:•钢板•焊接材料•螺栓和螺母•导电材料•消防设备2.3 切割和钻孔制作大型储罐需要进行钢板的切割和钻孔。
切割可以采用火焰切割或等离子切割,钻孔则需要使用大功率电钻。
2.4 焊接钢板切割和钻孔完成后,需要进行焊接。
在焊接过程中需要注意以下事项:•焊接位置要清洁,无油污和尘土•焊接材料要符合要求,避免焊接部位出现劣质焊缝•焊接需要按照制定的焊接方案进行2.5 补强和涂装焊接完成后,需要进行储罐的补强和涂装。
补强可以采用在储罐底部和顶部加装钢筋的方式,涂装则需要按照涂装标准进行。
3. 安装3.1 运输和卸载在进行安装前,需要将制作好的储罐通过运输车辆运送到安装现场。
在运输过程中需要注意:•储罐不得受到撞击或碾压•储罐需要有稳定的支撑和固定装置到达安装现场后,需要对储罐进行卸载。
卸载时需要使用专业的卸载设备,保证储罐的稳定性和安全性。
3.2 安装位置储罐的安装位置需要考虑以下因素:•地基稳定性和承载力•储罐与管道的距离和高度•环境安全和保护安装位置确定后,需要对地基进行清理和加固,保证储罐的稳定性。
3.3 接管和连接储罐的接管和连接需要按照设计方案进行。
接管应该采用符合标准的规定尺寸管道,连接时需要进行测试和检查,确保连接紧密和无泄漏。
3.4 消防设施在完成连接后,需要对储罐进行消防设施的安装。
十万方大型储罐倒装施工方案
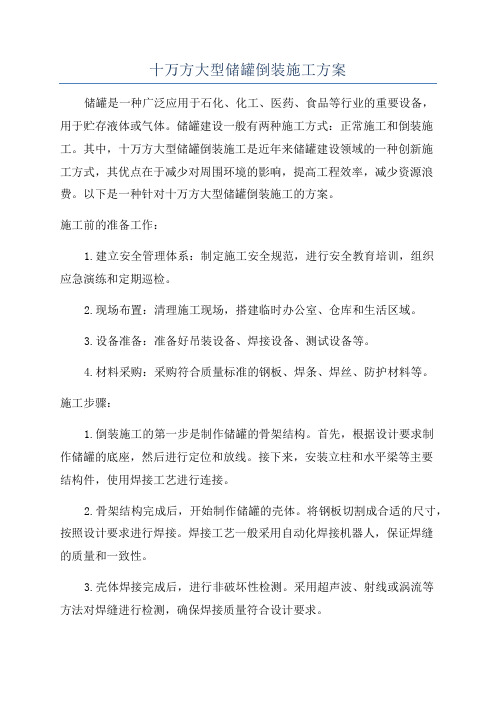
十万方大型储罐倒装施工方案储罐是一种广泛应用于石化、化工、医药、食品等行业的重要设备,用于贮存液体或气体。
储罐建设一般有两种施工方式:正常施工和倒装施工。
其中,十万方大型储罐倒装施工是近年来储罐建设领域的一种创新施工方式,其优点在于减少对周围环境的影响,提高工程效率,减少资源浪费。
以下是一种针对十万方大型储罐倒装施工的方案。
施工前的准备工作:1.建立安全管理体系:制定施工安全规范,进行安全教育培训,组织应急演练和定期巡检。
2.现场布置:清理施工现场,搭建临时办公室、仓库和生活区域。
3.设备准备:准备好吊装设备、焊接设备、测试设备等。
4.材料采购:采购符合质量标准的钢板、焊条、焊丝、防护材料等。
施工步骤:1.倒装施工的第一步是制作储罐的骨架结构。
首先,根据设计要求制作储罐的底座,然后进行定位和放线。
接下来,安装立柱和水平梁等主要结构件,使用焊接工艺进行连接。
2.骨架结构完成后,开始制作储罐的壳体。
将钢板切割成合适的尺寸,按照设计要求进行焊接。
焊接工艺一般采用自动化焊接机器人,保证焊缝的质量和一致性。
3.壳体焊接完成后,进行非破坏性检测。
采用超声波、射线或涡流等方法对焊缝进行检测,确保焊接质量符合设计要求。
4.进行表面处理和防腐涂层施工。
对焊接缝进行抛丸清理,去除焊渣和氧化物,然后进行底漆、中漆和面漆的施工。
5.安装储罐的附件设备,如进出口管道、排放管道、支撑架等。
进行管道的焊接和连接,确保管道畅通、稳固。
6.进行压力测试和泄漏测试。
使用泄漏检测仪器对储罐的密封性、抗压性进行测试,确保储罐的安全性。
7.进行储罐的竖立和定位。
使用起重机将储罐吊装至指定位置,并进行调整和固定。
8.完成施工后的清理工作。
清理施工现场,回收和妥善处理废弃材料和废水等。
施工注意事项:1.施工过程中,要严格执行安全规范,确保施工人员的人身安全。
2.施工过程中,要根据设计和施工文件进行质量控制和检验,确保施工质量。
3.在储罐竖立和定位时,要确保起重机的稳定性和承载能力,防止因储罐倾倒而导致事故。
- 1、下载文档前请自行甄别文档内容的完整性,平台不提供额外的编辑、内容补充、找答案等附加服务。
- 2、"仅部分预览"的文档,不可在线预览部分如存在完整性等问题,可反馈申请退款(可完整预览的文档不适用该条件!)。
- 3、如文档侵犯您的权益,请联系客服反馈,我们会尽快为您处理(人工客服工作时间:9:00-18:30)。
§1施工方案§1.1 总体施工方案1、液压提升倒装自动焊工艺a、本工程二台20000m3内浮顶罐采用液压提升倒装自动焊工艺进行施工,施工工艺流程图如后图所示。
b、罐底板、罐壁板在本部生产基地进行深度工厂化预制,利用进口的龙门自动切割机,切割下料和坡口加工一次成型。
c、油罐纵缝和环缝外口采用CO2气体保护自动焊,内口采用CO2气体保护半自动焊;油罐底板采用埋弧焊+碎丝焊。
2、液压提升倒装自动焊施工工艺流程图§1.2 油罐预制方案1、罐底预制a、罐底预制主要是弓形边缘板和中幅板的切割。
罐底中幅板、边缘板采用净料预制技术,用龙门自动切割机切割钢板的直边和坡口,罐底边缘板弧线采用半自动火焰切割机切割。
b、罐底板预程序如下:c、底板预制前应绘制排板图,并应符合下列规定●罐底的排板直径,宜按设计直径放大0.1%-0.2%;●边缘板沿罐底半径方向的最小尺寸,不得小于700mm;●弓形边缘板的对接接头,宜采用不等间隙,外侧间隙宜为6-7mm;内侧间隙宜为8-12mm;●中幅板的宽度不得小于1000mm,长度不得小于2000mm;●底板任意相邻焊逢之间的距离不得小于200mm。
d、中幅板的尺寸允许偏差应符合下表的规定2、壁板预制a、壁板预制主要为板料检验、切割下料和滚圆三个过程,进行工厂化施工,壁板预制工艺流程如下:b、壁板预制前,根据设计要求、施工规范及钢板实际到货规格绘制排板图,报设计及监理单位批准,并应符合下列要求:●底圈壁板纵缝,宜向同一方向逐圈错开,其间距不得小于500mm;●底圈壁板纵向焊缝与罐底边缘板的对接缝之间的间距不得小于200mm;●罐壁开孔接管或开孔接管补强板外缘与罐壁纵向焊缝之间的距离,不得小于200 mm;与环向焊缝之间的距离,不得小于100 mm;●包边槽钢对接接头与罐板纵向焊缝之间的距离不得小于200mm;●壁板宽度为1800mm,长度不得小于6000mm。
●壁板尺寸的允许偏差应符合下表:C F D壁板尺寸/测量部位c、壁板预制后用专用胎具进行存放和运输。
d、壁板卷制后,应直立在平台上用样板检查。
垂直方向用直线样板检查,其间隙不得大于1mm;水平方向上用弧形样板检查,其间隙不得大于4mm。
滚制过程中为保证质量,要使用专用引弧胎具,由于立缝自动焊接存在的角变形,所以壁板滚圆时,用样板检查二端弧度时要求预留一定量间隙,保证立缝自动焊完成后,立缝角变形为零。
§1.3 油罐安装方案1、基础验收a、罐底安装施工前首先要完成基础验收工作,主要是对基础的方位、标高、水平度进行复测,重点要保证基础混凝土环梁表面的水平度、环梁径向宽度等,要求沥青砂层表面凹凸度小于规定值,沥青砂层表面应平整夯实,无突出的隆起、凹坑及贯穿裂纹。
b、在底板铺设前,油罐基础应按基础设计施工图及《立式圆筒形钢制焊油罐施工及验收规范(GB128-90)》的规定进行复查验收,有关技术要求为:●基础中心标高允许偏差为±20mm;●圈梁每10m弧长内任意两点的高差不得大于6mm,整个圆周长度内任意两点的高差不得大于12mm;●沥青砂垫层表面应平整密实,无突出的降起、凹陷及贯穿裂纹,其检查方法及技术要求如表所示。
●沥青砂层表面凹凸度按下列方法检查:按图在基础上画出测点分布图,用水准仪测量各点标高,同一圆周上测点的测点标高与计算标高之差不得大于12mm。
2、罐底施工a、罐底施工工序a、按设计直径放大0.1%-0.2%计算所得划线半径划出罐底边缘板外圆线,用油漆作好标记,画出中幅板的中心线及分区长条中幅板的位置,全部核对无误后,进行垫板敷设组焊,再开始铺板。
c 、 铺设中心线长条板时,应把基础上的十字中心线和圆心移至钢板上,作好明显标记,然后铺设罐底中央长条垫板,点固焊接垫板,铺设中幅板,最后铺设扇形中幅板,吊装时用履带吊车将板吊至罐内就位。
d 、 罐底板焊接时,先点焊焊接边缘板外侧,再点焊焊接中幅板短缝,后点焊中幅板长缝,中幅板的点焊由中心向外的顺序对称进行,收缩缝不点焊,按焊接顺序要求分区焊接。
e 、 边缘板剩余对接缝及与中幅板连接的大圈收缩缝(龟甲缝)等壁板与罐底的大角缝焊完后再进行组对焊接。
f 、 边缘板对接焊缝焊接时防变形措如图所示:边缘板防翘曲变形措施垫板卡具g 、 罐底焊接完毕后,须作真空试漏,试验负压值不得低于53Kpa 。
3、 罐顶安装a 、 罐顶组装程序见下图所示。
罐底划线定位定位挡板焊接顶圈壁板组 焊第二圈壁板组焊包边角钢组 焊罐顶人孔、通气孔安装罐顶中心板组焊壁板组焊顶板组装焊接及焊缝检验拱顶伞型支架组装罐顶组装程序图b 、 在罐底板上划出顶圈壁板安装圆,并沿圆周线内侧每隔300mm 处点焊一块尺寸为80×60、δ10定位档板,以保证壁板的椭圆度,见下图①顶圈壁板①②垫板③档板②③④罐底板④顶圈壁板安装示意图c、顶圈壁板按排板图进行组装,组装焊接后,其上口水平和铅垂的允许偏差应符合下表。
顶圈壁板组焊允许偏差表d、顶圈壁板检查合格后,安装包边角钢。
组装前,应在钢平台上,用弧形样板检查其弧度和翘曲度。
包边角钢的组焊顺序为:角钢对接缝→内部断角焊缝→外部搭接连续角焊缝。
组装焊接后,包边角钢高出壁板的局部允许偏差为±4mm,包边角钢应紧贴壁板,其间隙不应大于2mm。
e、在第十一、第十圈壁板安装后,进行单层双向子午线穹形网壳的施工。
网壳的施工质量应符合《立式圆筒形钢制焊接油罐单层双向午线穹形网壳罐顶施工技术条件》的要求。
f、顶板组装时,在包边角钢和临时支撑架槽钢圈上,划出每块顶板的位置线,并焊上组装定位挡板。
g、上顶板时,按轴线两边对称同时进行。
4、壁板安装a、壁板组装前,应对预制的壁板进行复检,合格后方可组装。
b、组焊第二圈壁板的同时,安装胀圈和液压提升装置。
c、罐顶组装后,在顶圈、第二圈壁板外侧圈第三圈壁板按排版图,在其中的一条纵缝处留活口,并安装拉紧装置,其余纵缝进行焊接。
h、均匀布置液压提升架。
提升架应设置在平实地方,亦应错开焊道,以免影响射线探伤。
液压提升架按需要进行布置。
i、在液压提升架底部铺设一块δ18垫板,且用水平仪或线锤附测量提升架两个方向的垂直度,找正后与罐底板点焊固定,并用∠80×8作斜撑加固。
j、在距罐壁板底边缘300mm处,安装[20#胀圈,用来保证壁板组对的椭圆度及防止罐体提升时发生变形。
胀圈与罐壁用龙门卡具、销子及防滑挡板等连接。
胀圈安装时,应用水平仪找平,防止提升时罐体倾斜。
k、安装液压提升装置及液压控制管路,准备就绪后检查所有机具是否正常,然后准备顶升。
l、启动油压泵进行顶升,当壁板顶升到预定高度后就位,停止提升。
收紧拉紧装置,使当圈壁板与上圈壁板对齐,打好塞块,点焊环缝,使壁板固定,再焊接预留收缩缝,然后进行环缝焊接。
对罐壁找圆。
m、重复上述步骤完成其余数圈壁板的组装。
5、劳动保护及附件安装a、盘梯制安在壁板组装的同时,将已预制的盘梯加强板、侧板、踏步及三角架部件焊接在本体壁板相应位置上,待壁板组装完成后,再安装栏杆及其它连接件。
b、接管安装附件安装前应按设计图纸进行定位划线,并检查其尺寸准确无误后方可开孔。
为减少开孔与焊接产生热应力,罐壁人孔与罐顶透光孔开孔作业前,在上下两侧应焊接加强弧板,减少内应力的产生。
附件接管外伸长度的允许偏差为±5mm,接管中心偏差不得大于10mm,开孔补强板的曲率应与罐体曲率一致。
开孔的补强圈焊完后,应检查焊接的严密性,无渗漏为合格。
c、加强圈安装加强圈组对时,对曲率充分检查一边安装一边调整并考虑到焊接变形,采反变形措施,组对时特要注意防止连接处内凹现象。
6、油罐充水试验a、充水试验应符合下列规定:●充水试验前,所有与严密性试验有关的焊缝,均不得涂漆;●充水试验应用淡水,水温应高于5℃;●充水试验中应加强对基础沉降观侧,在充水试验中,如基础发生不允许的沉降,应停止充水,待处理后,方可继续进行试验;●充水过程中如有异常应立即停止充水,如渗漏则放水至漏水处下缘300mm进行修补,并应重新充水直至合格;●充水和放水过程中,应打开透光孔,且不得使基础浸水;●上水及排水管可用Ф273×7无缝钢管,上水及排水阀门应事先检查合格后再使用。
b、充水试验应检查下列内容:●罐底严密性试验:在充水试验过程中,观察基础四周,无渗漏为合格。
●罐壁强度及严密性试验:充水至最高设计操作液面,保持48小时后焊缝无渗漏,壁板无异常变形为合格。
●基础沉降观测:在罐壁下部(距罐底200mm)沿圆周均匀设置一定数量的观测点(20个点),观测罐体沉降情况。
观测沉降的基准点设在距离油罐基础5m以外某一点。
c、每台油罐进水前先进行一次观测并做好记录;然后进行充水,当水位上升到罐高1/2时,停止进水并进行沉降观测,保持24小时后再进行一次沉降观测,并与上次观测到的数据进行对照,计算出实际的不均匀沉降量;若没有超过允许误差,可继续充水至罐高的3/4,再进行观测;当仍未超过允许的不均匀沉降量,可继续充水到最高液位,保持48小时后进行观测,当沉降量没有超过允许误差且比较稳定即可放水,当沉降量有所显著变化,则应保持最高液位,每天进行定期观测,直至沉降稳定为止。
d、若发生不允许沉降或沉降偏差超过允许偏差值或基础圈梁发生沉降突变、开裂等现象。
应立即停止进水,马上通知建设单位、监理单位和设计单位,待处理后方可继续进行。
§1.4 储罐焊接施工方案1、罐底板的焊接a、罐底板分为罐底中幅板与弓形边缘板两部分。
罐底中幅板的焊接采用气保护半自动焊打底、碎丝埋弧焊填充、盖面焊接工艺;罐底弓形边缘板的焊接采用气保护半自动焊;罐底中幅板与弓形边缘板之间的大收缩缝的焊接,采用气保护半自动焊打底,碎丝埋弧焊填充盖面的焊接工艺。
b、先安装弓形边缘板,并焊接边缘板之间对接缝的外侧300mm,电焊工均匀分布在罐边缘上,同时焊接。
为防止焊接变形,焊前用弧形板加固。
c、整个中幅板由4台(组)焊机对称布置,由中心向四周施焊,为防止焊接变形在大板的两端在焊前加防变形卡具。
在焊接廊板时在大板一侧用槽钢进行加固,并用4块8T配重压于大板一侧。
d、等大角缝焊完后,先焊接边缘板内侧其余部分,再焊接与弓形边缘板之间的大圈收缩缝且在焊接前整个龟甲环缝用I12作背杠加固,2、罐壁板的焊接a、油罐壁板纵缝和环缝的焊接采用CO2气体保护自动横焊和立焊b、油罐壁板应先焊纵缝,后焊环缝,焊工应均匀分布,并沿同一方向施焊。
c、焊接时,应先焊外侧后焊内侧,在施焊内侧前,应清焊根。
d、焊缝全部焊完后,应用木锤排打,纠正焊缝变形,分散和减小焊接时产生的内应力。
e、底圈壁板与罐底板之间的T型角焊缝的焊接,应符合下列要求:●焊条采用碱性低氢焊条;●焊接时,宜采用先焊内侧,后焊外侧,数名焊工均匀分布,沿同一方向分布退步施焊,以减少变形;●减少焊接变形能量也是控制变形量的一个有效手段,因此在10000 m3油罐施焊时,采用多道快速焊进行焊接,焊道分布详见图8。