工艺控制及防错系统_方案
mes防错料系统方案书

一、背景随着制造业的发展,产品的多样化和生产效率的提高成为企业的追求目标。
然而,在生产过程中,由于操作员的疏忽或材料的混乱,常常会发生料号选错或者给错料的错误,导致生产延误和产品质量问题。
为了解决这一问题,我们提出了MES防错料系统方案,旨在提高生产线的效率和准确性,降低错误率。
二、目标和需求2.1 目标•提高生产线的生产效率•降低错误率•减少废品产生•增加操作员的工作满意度2.2 需求•实时监控物料的选配和供应•检测料号的正确性•告警和纠正错误的能力•记录并汇总错误数据三、系统架构MES防错料系统由以下几个核心模块组成:3.1 物料监控模块该模块用于监控物料的选配和供应过程,通过感应器和扫码设备对物料进行追踪和识别,确保物料的正确性。
3.2 料号检测模块该模块用于检测料号的正确性,通过与数据库中的料号进行对比,确保选用的物料与所需料号匹配。
3.3 告警和纠正模块该模块用于检测错误并及时发出告警,同时提供纠正错误的指导和操作步骤,以减少错误率和生产延误。
3.4 数据记录模块该模块用于记录错误数据并进行汇总分析,生成相关报表和统计数据,为后续优化提供依据。
四、工作流程4.1 操作员流程•操作员进入工作站,通过身份验证登录系统。
•操作员扫描产品条码或输入产品信息。
•系统根据产品信息自动加载相应的工艺参数和物料清单。
•操作员根据工艺参数和物料清单取料并进行组装。
•当操作员选用的物料与所需料号不匹配时,系统立即发出告警。
•操作员按照系统提供的指导纠正错误。
•完成组装后,操作员提交生产报告并退出系统。
4.2 系统流程1.物料监控模块不断监测物料的选配和供应过程。
2.料号检测模块同时检测物料的料号是否正确。
3.若物料选配错误或者料号不正确,则告警和纠正模块发出告警,并提供纠正指导。
4.错误数据被记录到数据记录模块中,并进行汇总分析。
5.数据记录模块生成报表和统计数据,为管理层提供决策参考。
五、预期效果通过引入MES防错料系统,我们预期可以达到以下效果:•生产线的生产效率提高10%•错误率降低50%•废品率减少20%•操作员的工作满意度提高20%六、总结MES防错料系统方案旨在提高生产线的效率和准确性,降低错误率,减少废品产生,增加操作员的工作满意度。
防错技术及其应用

法规规范
02
03
资金支持
制定相关法规和标准,规范防错 技术的研发和应用,保障技术发 展的可持续性。
政府将提供资金支持,推动防错 技术的研发和应用,促进产业升 级。
未来前景展望
个性化定制
随着消费者需求的多样化,防错技术将实现个性化定制,满足不 同需求。
全球化发展
防错技术将走向全球化,推动国际间的技术交流与合作,提升整体 技术水平。
现状
随着科技的不断进步和工业4.0时代的到来,防错技术 正朝着智能化、集成化、网络化的方向发展。一方面, 先进的传感器、机器视觉、人工智能等技术为防错技术 提供了更强大的技术支持;另一方面,工业互联网、大 数据等技术的应用使得防错技术能够实现跨地域、跨行 业的协同和共享。未来,防错技术将在提高产品质量、 降低生产成本、提升企业竞争力等方面发挥更加重要的 作用。
强化技术研发和创新
加强数据安全和隐私保护
加大技术研发和创新力度,提高防错技术 的自主可控能力和核心竞争力。
建立完善的数据安全和隐私保护机制,确 保用户数据的安全性和隐私性。
推动行业合作和标准制定
提高成本效益分析和评估能力
加强行业合作和标准制定工作,促进防错 技术的规范化和标准化发展。
加强成本效益分析和评估能力建设,为防 错技术的投资决策提供科学依据。
绿色环保
防错技术将注重环保理念,推动绿色制造,降低能源消耗和环境污 染。
THANKS
感谢观看
技术兼容性差
不同防错技术之间可能存在兼容 性问题,导致系统整体性能下降 或出现故障。
解决方案
建立技术更新机制,定期评估现 有技术和市场需求,及时进行技 术升级和改造。同时,加强技术 研发和创新能力,提高自主可控 能力。
mes防错料系统方案书

mes防错料系统方案书MES(Manufacturing Execution System)防错料系统方案书一、引言随着制造业的发展和自动化程度的提高,生产过程中的错误和失误成为制约企业效率和品质的重要因素之一。
在制造过程中,防错料是一项关键的任务。
为了提高生产产品的质量和效率,许多企业开始采用MES(Manufacturing Execution System)防错料系统来降低人为错误和材料浪费。
本文将介绍MES防错料系统的方案书,以帮助企业了解和实施该系统。
二、背景MES防错料系统是一种自动化的解决方案,旨在减少生产过程中的错误和材料浪费。
该系统通过跟踪和监控生产环节中的数据和信息,发现潜在的错误并采取相应措施,以减少生产过程中的损失。
三、目标MES防错料系统的目标是提高生产过程的准确性和效率,降低人为错误和材料浪费。
通过引入该系统,企业可以实现以下目标:1. 减少生产过程中的错误率:通过自动化的数据采集和监控,系统可以及时发现潜在的错误,并在生产过程中采取行动,以减少错误发生的可能性。
2. 降低材料浪费:系统可以帮助企业跟踪材料使用情况,并提供及时的警告和建议,以减少材料的浪费和损失。
3. 提高产品品质:通过减少错误和材料浪费,企业可以提高产品的质量和一致性,满足客户的需求。
4. 提高生产效率:系统可以优化生产过程,减少不必要的停机时间和调整时间,提高生产效率和生产能力。
四、系统功能MES防错料系统包括以下主要功能:1. 数据采集和监控:系统可以通过传感器、传输设备和软件工具等手段收集生产过程中的关键数据,并实时监控数据的变化和趋势。
2. 错误检测和预警:系统可以根据设定的规则和标准,对采集到的数据进行分析和比较,发现潜在的错误,并及时发送预警信号。
3. 材料跟踪和管理:系统可以跟踪和管理生产过程中使用的各种材料,包括原材料、半成品和成品等,并提供准确的库存信息和使用记录。
4. 优化生产过程:系统可以根据预设的参数和要求,对生产过程进行动态调整和优化,以提高生产效率和品质。
智能产线装配工艺管控解决方案

Aug.2018 工具信息与标准 / 057智能产线装配工艺管控解决方案
● 智能工序设定:
分解拧紧步骤,提前预设工序,可设定工 位拧紧顺序、扭矩值、角度、时间等多个参数;
图示化引导操作者操作,避免错误拧紧,提升混装成功率;
● 自动品管检测,完美防错防漏:
完成工序拧紧后软件自行检测,以色彩、声响、工具锁紧等方式警示不符合项整改完毕后,进入下一工序。
● 触摸屏操作:
固定在相应工位机械臂附近,有效识别数据真实性。
● 智能套筒选择器识别:
通过套筒拿取再次识别拧紧工位扭矩。
拿错或者漏拿套筒后系统提示错误,并进行声光报警。
● ID登录,权限划分:
责任到人,整条产线具有可追溯性
● 大数据管理:
配合以太网及伺服器,衔接MES 系统,从领料到用料、拧紧情况、成品储存到出库、物流,形成数据的统一管理与调阅。
全面实现工业4.0变革。
诺霸立足中国市场,以“互联网+”的思想整合智能产线方案,将智能工具、智能装配工艺软件及MES 系统联动,推出
全新的产线工位智能解决方案。
制造(机械加工)企业生产现场的“防错与改善”措施及方法
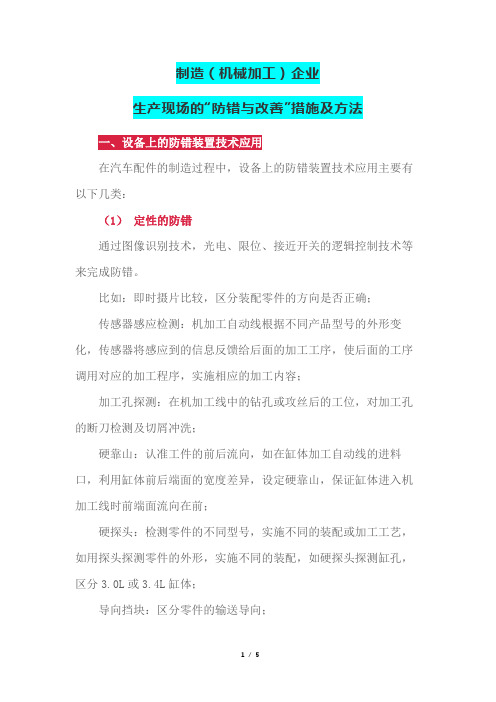
制造(机械加工)企业生产现场的“防错与改善”措施及方法在汽车配件的制造过程中,设备上的防错装置技术应用主要有以下几类:(1)定性的防错通过图像识别技术,光电、限位、接近开关的逻辑控制技术等来完成防错。
比如:即时摄片比较,区分装配零件的方向是否正确;传感器感应检测:机加工自动线根据不同产品型号的外形变化,传感器将感应到的信息反馈给后面的加工工序,使后面的工序调用对应的加工程序,实施相应的加工内容;加工孔探测:在机加工线中的钻孔或攻丝后的工位,对加工孔的断刀检测及切屑冲洗;硬靠山:认准工件的前后流向,如在缸体加工自动线的进料口,利用缸体前后端面的宽度差异,设定硬靠山,保证缸体进入机加工线时前端面流向在前;硬探头:检测零件的不同型号,实施不同的装配或加工工艺,如用探头探测零件的外形,实施不同的装配,如硬探头探测缸孔,区分3.0L或3.4L缸体;导向挡块:区分零件的输送导向;光栅防错:通过光栅的检测控制,达到工件是否摆放到位;夹具防错:控制装配零件在夹具上的摆放是否到位来防错。
(2)定量的防错通过测量探头感应或经过气电转换的测量技术(气体流量转换成电量)来达到防错的目的。
如:探头探测数据反馈:通过探头探测已压装气门座圈的内径来区别零件是3.0L还是3.1L汽车配件的缸盖;刀具长度检测:程序控制加工中心刀具检测可防止错误长度的刀具安装在刀库中,防止加工过程中的断刀现象,减少加工首件或加工过程中的废品出现;定位面气孔压力检测:确认工件正确到位的防错措施;泄漏测试:汽车配件如缸盖、缸体的油道以及水道的在线测试等,控制泄漏件流入下道工序;随线检具直径测量:这在机加工自动线中镗孔及铰孔后的工位应用较广,达到100%控制不合格产品的出现;扭矩控制:汽车配件如很多螺栓固定的拧紧程度均通过扭矩枪来控制。
(3)颤动功能的防错通过颤动机的颤动,使零件随着不断的颤动并输送至判别零件的方向正确与否处,只有零件处于正确的位置方向时,才能进入送料轨道;位置方向错误的零件则掉入零件颤动料箱里,从而达到预防零件的进给方向错误,避免工件报废的目的。
聚合工艺安全控制系统设计指导方案

聚合工艺安全控制系统设计指导方案聚合工艺安全控制系统是用于确保工艺操作安全的关键设备之一、在聚合工艺中,往往会涉及到高温、高压、易燃易爆等危险因素,因此需要设计一个可靠的安全控制系统来保障工艺操作的安全性。
下面是一个聚合工艺安全控制系统设计的指导方案。
首先,聚合工艺安全控制系统需要具备实时监控和报警功能,以便能够及时发现和处理潜在的安全风险。
可以采用传感器网络来实现对温度、压力、流量等参数的实时监测,并与报警系统相连,一旦出现异常情况,系统能够第一时间发出警报。
其次,安全控制系统需要具备可靠的自动控制功能,以确保工艺操作的稳定性和一致性。
可以采用PLC(可编程逻辑控制器)来实现对工艺参数的自动调节和控制。
PLC可以根据预设的工艺要求,自动调节温度、压力等参数,以保持工艺操作在安全范围内。
同时,安全控制系统还需要具备可靠的紧急停机和事故处理功能。
在发生紧急情况时,系统应能迅速切断供气、断电,并触发事故处理程序。
这可以通过PLC与执行机构(如电磁阀)相连,实现对设备的迅速停机控制。
另外,为了提高安全控制系统的可靠性和故障排除能力,应采用多重保护措施。
可以设置多个独立的传感器和控制装置,以备份和互为备份,避免单点故障。
同时,还可以设置故障诊断功能,及时发现和排除系统故障并进行自动切换。
此外,安全控制系统的设计还需要考虑到操作人员的安全问题。
可以设置安全门、防护罩等装置,确保在操作过程中操作人员不会接触到危险区域。
同时,还需提供安全培训和操作规程,确保操作人员具备相应的安全意识和操作技能。
最后,对于安全控制系统的设计,还需要进行严格的安全评估和验证。
可以进行风险评估分析,确定潜在的安全风险和应对措施。
同时,还需进行模拟实验和现场测试,验证系统的可靠性和稳定性。
总之,聚合工艺安全控制系统是确保工艺操作安全的重要设备,设计时需要考虑实时监控和报警功能、自动控制功能、紧急停机和事故处理功能等。
同时,还需要采取多重保护措施、关注操作人员的安全以及进行安全评估和验证。
工艺流程的监控与预警系统设计
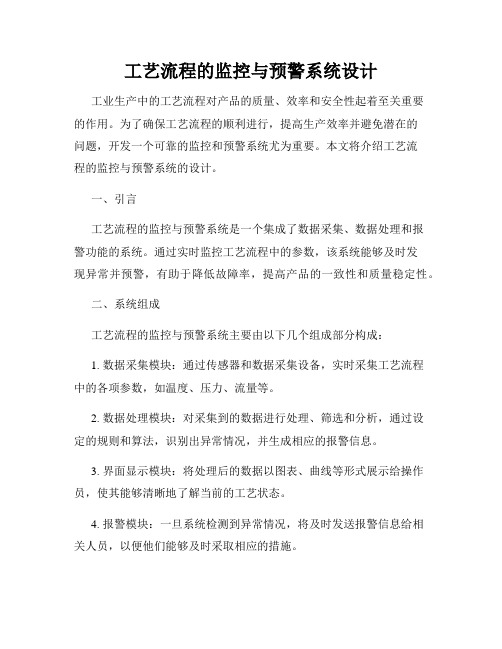
工艺流程的监控与预警系统设计工业生产中的工艺流程对产品的质量、效率和安全性起着至关重要的作用。
为了确保工艺流程的顺利进行,提高生产效率并避免潜在的问题,开发一个可靠的监控和预警系统尤为重要。
本文将介绍工艺流程的监控与预警系统的设计。
一、引言工艺流程的监控与预警系统是一个集成了数据采集、数据处理和报警功能的系统。
通过实时监控工艺流程中的参数,该系统能够及时发现异常并预警,有助于降低故障率,提高产品的一致性和质量稳定性。
二、系统组成工艺流程的监控与预警系统主要由以下几个组成部分构成:1. 数据采集模块:通过传感器和数据采集设备,实时采集工艺流程中的各项参数,如温度、压力、流量等。
2. 数据处理模块:对采集到的数据进行处理、筛选和分析,通过设定的规则和算法,识别出异常情况,并生成相应的报警信息。
3. 界面显示模块:将处理后的数据以图表、曲线等形式展示给操作员,使其能够清晰地了解当前的工艺状态。
4. 报警模块:一旦系统检测到异常情况,将及时发送报警信息给相关人员,以便他们能够及时采取相应的措施。
5. 数据存储模块:将采集到的数据保存在数据库中,供后续分析和回溯使用。
三、系统设计在设计工艺流程的监控与预警系统时,需要考虑以下几个方面:1. 数据采集设备的选择:根据具体的工艺流程需求,选择合适的传感器和数据采集设备,确保采集的数据准确可靠。
2. 数据处理算法的制定:根据工艺流程的特点和问题的可能性,制定适用的数据处理算法,以识别出异常情况并进行预警。
3. 界面显示的设计:设计直观易懂的界面,使操作员能够快速了解工艺状态,并能够及时发现和解决问题。
4. 报警信息的发送方式:选择合适的报警方式,如短信、邮件或声音提示,确保相关人员能够及时获悉异常情况。
5. 数据存储与分析:将采集到的数据存储在数据库中,以便后续的数据分析和回溯,为工艺的改进和优化提供有效依据。
四、系统应用工艺流程的监控与预警系统广泛应用于各个领域的生产过程中,如化工、制药、食品等行业。
工艺过程失效防错方法

工艺过程失效防错方法工艺过程中的失效问题是制造业中常见的难题,失效不仅会导致产品质量问题,还会造成生产效率下降、资源浪费等一系列不良影响。
为了提高工艺过程的可靠性和稳定性,降低失效风险,制定一套科学合理的失效防错方法是非常重要的。
一、失效分析在制定失效防错方法之前,首先需要对工艺过程中可能出现的失效进行分析。
失效分析是通过观察和研究实际生产过程中的失效现象,找出失效的原因和机理,从而制定相应的防错措施。
失效分析可以通过以下几个步骤进行:1. 收集失效数据:收集工艺过程中出现的失效数据,包括失效的时间、地点、原因等信息。
2. 归类整理:将收集到的数据进行归类整理,按照失效的类型、频率等进行分类,以便更好地分析和处理。
3. 原因分析:对每个失效进行深入分析,找出导致失效的原因和机理。
可以采用故障树分析、鱼骨图等方法进行分析。
4. 制定防错措施:根据失效原因和机理,制定相应的防错措施,以预防或减少类似失效的发生。
二、失效预防失效预防是指在工艺过程中采取措施,预防失效的发生。
失效预防可以从以下几个方面入手:1. 设计阶段预防:在产品设计阶段,注重产品的可靠性和稳定性,合理选择材料和工艺,避免潜在的失效问题。
2. 工艺控制预防:严格控制工艺参数,确保工艺过程的稳定性和一致性。
对关键工艺参数进行实时监控和调整,预防失效的发生。
3. 检测手段预防:建立完善的检测手段和流程,对工艺过程中的关键环节进行实时监测,及时发现问题并进行处理。
4. 人员培训预防:加强员工的技能培训和业务知识学习,提高员工的操作水平和技术素质,减少人为失误引起的失效。
三、失效控制除了预防失效外,失效控制也是重要的一环。
失效控制是指在失效发生后,及时采取措施进行控制,防止失效的蔓延和扩大。
失效控制可以从以下几个方面入手:1. 快速反应:对失效进行快速反应,及时停止工艺过程,避免失效的蔓延和扩大。
同时,要对失效进行记录和分析,找出失效的原因,以便后续的防错措施制定。
工艺过程失效防错方法

工艺过程失效防错方法工艺过程失效是指在生产过程中,由于各种原因导致工艺过程无法正常进行或达到预期效果的情况。
为了确保产品质量和生产效率,必须采取一系列措施来预防和纠正工艺过程失效。
本文将介绍几种常用的工艺过程失效防错方法。
一、工艺过程分析工艺过程分析是指对整个工艺过程进行全面细致的分析,确定可能出现的失效点和原因。
通过对工艺流程图、工艺参数、设备性能等进行分析,可以找出可能导致失效的环节,并制定相应的预防措施。
二、工艺参数监控工艺参数监控是指对工艺过程中的关键参数进行实时监控和记录。
通过建立监控系统,及时发现参数偏离预设范围的情况,并采取相应的调整措施,避免失效的发生。
同时,还可以通过对历史数据的分析,找出参数变化的规律,为工艺优化提供依据。
三、设备维护保养设备的正常运行对于工艺过程的稳定性和可靠性至关重要。
定期进行设备的维护保养,预防设备故障和失效,是防止工艺过程失效的重要措施之一。
同时,还应建立设备巡检制度,及时发现和排除潜在的设备问题,确保工艺过程的连续性和稳定性。
四、工艺操作培训工艺操作培训是指对工艺操作人员进行培训,提高其对工艺过程的理解和掌握。
通过培训,操作人员可以更好地理解工艺过程的原理和要求,掌握正确的操作方法,提高对异常情况的判断和处理能力,减少操作失误和工艺过程失效的发生。
五、质量控制体系建立科学完善的质量控制体系是预防工艺过程失效的基础。
通过制定相应的质量标准和检测方法,对工艺过程进行全面监控和控制,及时发现和纠正问题,确保产品质量的稳定性和一致性。
同时,还应建立质量反馈机制,及时收集和分析产品质量数据,为工艺改进提供依据。
六、风险评估和预防措施在工艺过程设计和改进的过程中,应进行风险评估和预防措施的制定。
通过对潜在风险的识别和评估,制定相应的预防措施,降低工艺过程失效的发生概率。
同时,在实施过程中还应进行监控和评估,及时调整和优化措施,确保其有效性和可持续性。
七、故障分析和改进对于已经发生的工艺过程失效,应进行详细的故障分析,找出失效的原因和根源。
工艺流程保证控制保证控制保证措施

工艺流程保证控制保证控制保证措施工艺流程保证控制措施一、引言工艺流程是指将原材料经过一系列的物理、化学或机械处理,加工转化成最终产品的过程。
在工艺流程中,为了保证产品质量、提高生产效率以及保护员工的安全,必须采取相应的控制措施。
本文将从以下几个方面展开详细阐述工艺流程保证控制措施。
二、设备检查与维护设备的正常运行是工艺流程中保证控制的基础。
定期检查和维护设备是保证工艺流程顺利进行的关键措施。
首先,对设备进行定期巡检,检查设备的运行状态、油温、电压、转速等参数是否正常。
如果发现异常,应立即停机检修,以确保设备的安全运行。
其次,对设备进行定期保养和更换易损件,以免因设备故障导致工艺流程中断或事故发生。
三、工艺参数的监控与调节在工艺流程中,工艺参数的监控和调节是保证产品质量的重要手段。
首先,应通过安装传感器和仪器对关键参数进行实时监测,如温度、压力、流量等。
当参数偏离预设范围时,应及时采取措施进行调节,以确保产品质量的稳定性。
其次,应建立严格的记录和报警机制,对异常参数进行记录和分析,及时发出报警信号,以便及时采取措施避免事故的发生。
四、操作规程与培训操作规程的制定和员工培训是工艺流程保证控制的重要环节。
首先,制定详细的操作规程,明确每个工序的操作步骤、安全注意事项以及危险源的控制方法。
操作规程应易于理解,严格执行,并定期进行更新和修订。
其次,对员工进行系统的培训,包括设备的操作和维护、工艺参数的控制与调节、应急救援措施等。
培训内容应包括理论和实践,强调安全意识和操作技能的培养。
五、应急预案的制定与演练即使在严格执行各项措施的情况下,仍然无法完全排除事故的发生。
因此,制定应急预案,并定期进行演练是工艺流程保证控制的重要环节。
首先,应根据工艺流程中可能发生的事故类型,制定相应的应急预案,明确事故发生时的应对措施、责任人和联系方式。
其次,定期组织应急演练,以检验应急预案的可行性和员工的应对能力,并根据演练结果进行修订和完善。
防止生产错误和差错的措施、原则和方法
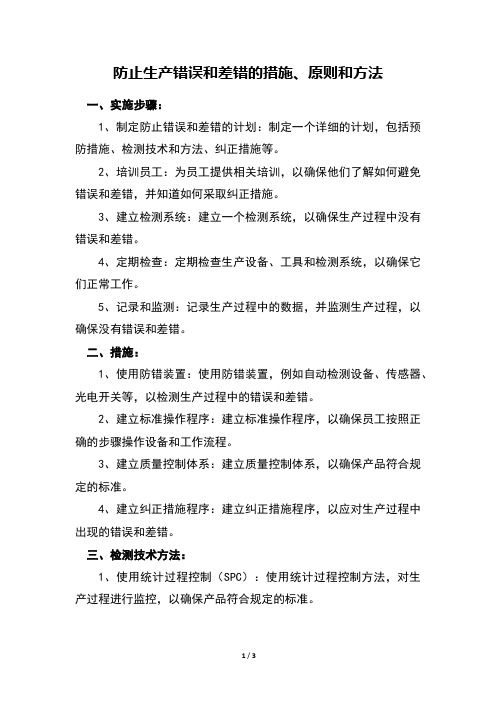
防止生产错误和差错的措施、原则和方法一、实施步骤:1、制定防止错误和差错的计划:制定一个详细的计划,包括预防措施、检测技术和方法、纠正措施等。
2、培训员工:为员工提供相关培训,以确保他们了解如何避免错误和差错,并知道如何采取纠正措施。
3、建立检测系统:建立一个检测系统,以确保生产过程中没有错误和差错。
4、定期检查:定期检查生产设备、工具和检测系统,以确保它们正常工作。
5、记录和监测:记录生产过程中的数据,并监测生产过程,以确保没有错误和差错。
二、措施:1、使用防错装置:使用防错装置,例如自动检测设备、传感器、光电开关等,以检测生产过程中的错误和差错。
2、建立标准操作程序:建立标准操作程序,以确保员工按照正确的步骤操作设备和工作流程。
3、建立质量控制体系:建立质量控制体系,以确保产品符合规定的标准。
4、建立纠正措施程序:建立纠正措施程序,以应对生产过程中出现的错误和差错。
三、检测技术方法:1、使用统计过程控制(SPC):使用统计过程控制方法,对生产过程进行监控,以确保产品符合规定的标准。
2、使用视觉检测技术:使用视觉检测技术,例如图像处理和机器视觉系统,以检测产品的外观缺陷和尺寸偏差。
3、使用无损检测技术:使用无损检测技术,例如超声波检测、射线检测、磁粉检测等,以检测产品的内部缺陷。
四、生产防错的五类方法:1、过程防错:从产品制造过程的角度出发,将防错重点放在工艺设计、产品设计和生产流程设计上,通过消除导致错误的根本原因,防止错误的发生。
2、设备防错:从设备设计和制造的角度出发,将防错重点放在设备的可靠性、可维护性和可检测性上,通过设备自身的防错能力,防止错误的发生。
3、人员防错:从人员培训、技能提升和行为管理的角度出发,通过提高员工的素质和自我控制能力,防止错误的发生。
4、环境防错:从生产环境和工作流程的角度出发,通过优化工作环境和流程,消除错误的根源,防止错误的发生。
5、管理防错:从管理的角度出发,通过完善管理制度和流程,强化监督和检查,及时发现和处理问题,防止错误的发生。
紧固件和工艺孔防错方案
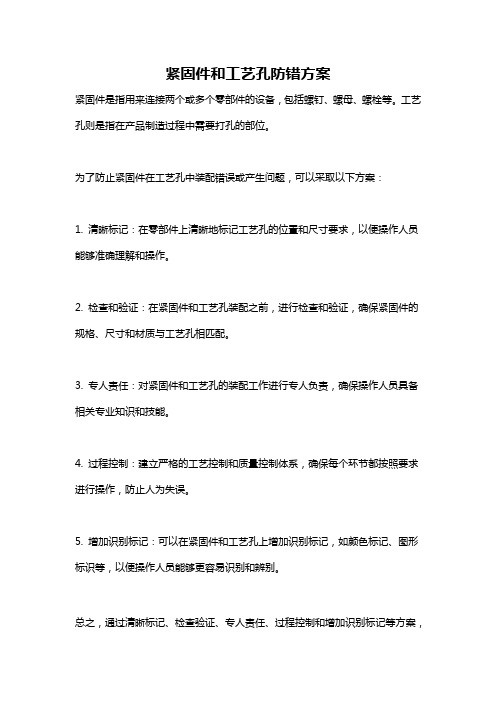
紧固件和工艺孔防错方案
紧固件是指用来连接两个或多个零部件的设备,包括螺钉、螺母、螺栓等。
工艺孔则是指在产品制造过程中需要打孔的部位。
为了防止紧固件在工艺孔中装配错误或产生问题,可以采取以下方案:
1. 清晰标记:在零部件上清晰地标记工艺孔的位置和尺寸要求,以便操作人员能够准确理解和操作。
2. 检查和验证:在紧固件和工艺孔装配之前,进行检查和验证,确保紧固件的规格、尺寸和材质与工艺孔相匹配。
3. 专人责任:对紧固件和工艺孔的装配工作进行专人负责,确保操作人员具备相关专业知识和技能。
4. 过程控制:建立严格的工艺控制和质量控制体系,确保每个环节都按照要求进行操作,防止人为失误。
5. 增加识别标记:可以在紧固件和工艺孔上增加识别标记,如颜色标记、图形标识等,以便操作人员能够更容易识别和辨别。
总之,通过清晰标记、检查验证、专人责任、过程控制和增加识别标记等方案,
可以有效防错紧固件和工艺孔的装配过程,提高产品质量和生产效率。
工艺流程中的质量控制与改进

工艺流程中的质量控制与改进工业生产中,工艺流程的质量控制与改进扮演着至关重要的角色。
通过对质量的精确控制和不断的改进,企业可以提高产品的质量标准,降低生产成本,并进一步提升市场竞争力。
本文将探讨工艺流程中的质量控制与改进策略。
一、质量控制的基础原则在工艺流程中,质量控制的基础原则是确保每一道工序都能够按照既定的质量标准进行操作。
这种基本原则主要包括以下几个方面:1.标准化:确立统一的质量控制标准,以保证生产过程中的一致性,减少人为误差的发生。
2.检测与监测:引入合适的检测设备和技术,监测产品的生产过程,及时发现和纠正潜在的质量问题。
3.培训与沟通:为工艺流程中的员工提供必要的培训和教育,促进他们对质量控制的理解和重视。
二、质量控制的方法和工具为了确保工艺流程中的质量控制,企业需要采用适当的方法和工具。
下面介绍一些常用的质量控制方法和工具。
1.质量流程图:通过绘制质量流程图,可以清晰地展示工艺流程中的每一个环节,帮助员工理解质量控制的重要性。
2.故障模式和影响分析(FMEA):通过FMEA方法,可以识别和评估每个工艺步骤中的潜在问题,并采取相应的改善措施。
3.统计过程控制(SPC):通过统计过程控制方法,可以实时监测工艺流程中的各项关键指标,及时调整和控制操作,保持质量的稳定性。
4.六西格玛:六西格玛方法着眼于减少质量缺陷和变异性,通过数据驱动的方法实现质量的持续改进。
三、质量改进的策略除了质量控制,质量改进也是工艺流程中不可或缺的一部分。
下面列举一些提升质量的策略。
1.持续改进:通过设置改进目标、定期评估和反馈机制,鼓励员工不断寻找和解决质量问题,并推行持续的流程改进。
2.经验总结与知识管理:建立经验总结和知识分享机制,将从质量问题中得到的教训和解决方案记录下来,以备今后使用。
3.创新技术应用:引入先进的技术设备和自动化系统,提高工艺流程的精确度和生产效率,从而改善产品质量。
4.合理调整生产计划:综合考虑市场需求和生产能力,合理安排生产计划,避免过度生产导致质量问题。
化工配料防错机制

化工配料防错机制
在化工生产中,防错机制是非常重要的,它有助于避免因为错误操作或错误使用配料而引发的安全问题和产品质量问题。
以下是一些化工配料防错机制的常见做法:
1.标签和标识:每种化学品都应该有明确的标签和标识,包括化学名称、CAS号码、危险性符号、安全操作说明等信息。
这有助于工作人员正确辨认和使用化学品。
2.颜色编码:可以使用颜色编码系统,将不同种类的化学品用不同颜色的容器或标签进行标识,帮助人员快速识别。
3.专用容器:将不同的化学品存放在专用容器中,以减少混淆的可能性。
容器上应有清晰的标识和说明。
4.工艺流程控制:在生产过程中,通过控制系统确保配料的正确投放,可以使用自动化系统来减少人为错误。
5.培训和教育:对工作人员进行充分的培训,使其了解各种化学品的性质、用途和安全操作规程,从而降低错误的可能性。
6.工作程序和检查:制定明确的工作程序,包括正确的配料顺序和操作步骤,并设立检查点确保操作的准确性。
7.使用辅助工具:使用辅助工具,例如计量设备、防溢漏装置等,以确保准确投放和防止配料泄漏。
8.双重确认:重要的配料投放步骤可以采用双重确认机制,确保多个工作人员确认操作的准确性。
工艺管理系统方案
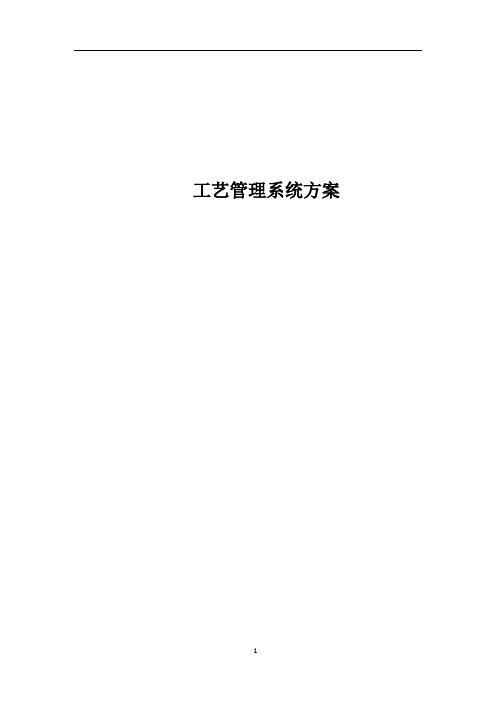
工艺管理系统方案1. 建设目标企业工艺管理是一个分散的管理模式,包括邮件、电子文档、数据报表、纸质文档和流程图等,这种分散的管理导致企业工艺管理部门需要经过不同的途径才得到相应的数据和资料,并且数据和资料文档的历史备份、查找等问题会对企业工艺管理带来一定难度,不利于企业的高效管理,并且一部分数据在其他的业务系统中体现,而且没有接口,对于数据提取和统一管理极其不利的,现将企业工艺管理所涉及的生产、工艺、节能三方面业务建设成一个综合平台,完成日常工艺管理业务工作内容,将工艺技术管理提升到一个新的高度,以适应企业复杂工艺技术不断变化的需求。
具体目标分为以下几个部分:(1)建立工艺技术管理的综合平台,实现对全厂范围内生产、工艺、节能相关内容的综合管理。
(2)建立整个工艺技术管理系统的信息平台,实现企业的工艺技术类信息集成和权限内数据共享。
(3)实现报表的自动生成,装置的技术月报、节能月报可在短时间内自动生成。
(4)开发非正常数据自动剔除或隔离,确保系统界面、报表数据的准确性。
(5)实现系统安全建设,在保证系统自身安全的前提下,根据项目的阶段建设目标,充分利用企业现有信息系统资源,对系统进行安全设计,完成工艺管理系统的安全建设。
2. 建设内容及范围工艺技术管理系统涉及工艺、生产、节能三方面的综合业务,用户通过系统能够管理和维护生产过程中的各种信息内容,全面提升工艺技术管理水平。
2.1建设内容2.1.1 生产计划管理生产计划管理旨在将企业各套装置形成一条条链路,在各条链路上,对应每套装置显示出该装置当前生产加工方案、加工量及主要产品产量,便于各装置明确其自身的加工方案,对工艺参数的调整做到胸有成竹。
2.1.2 生产实时监控对各个装置的物料平衡数据、罐区的罐存及成品数据、公用工程的消耗数据进行动态监控,可监控装置侧线产品流量、罐区油品库存历史变化,装置的侧线产品及罐区油品化验分析同时可进行查询。
2.1.2.1 罐区罐存及成品数据按原油结构对罐区的库存及加工情况进行动态展示,使一次加工装置人员可以实时了解到加工原油的性质及库存情况;对罐区的成品数据进行动态监控,了解各个成品罐的储存情况及储存余量,减少罐区操作人员的工作量。
九大防错设计指南

九大防错设计指南一、物料防错1. 类似零件的防错:通过在零件上增加凸点、划线、刻字等特征,使其具有唯一性,从而实现防错。
2. 零件方向防错:通过零件的形状、尺寸和装配位置的设计,确保零件只能以正确的方式安装。
3. 零件配对防错:通过将零件设计成互锁或相互卡紧的方式,确保零件的正确配对和装配。
二、识别防错1. 颜色识别:通过不同的颜色标签或标记,区分不同的物料、零件或状态,以便快速识别和分类。
2. 文字说明:在零件或产品上添加文字说明,明确指示操作步骤、注意事项和安全警示等信息。
3. 条形码或RFID标签:利用信息技术,通过条形码或RFID标签进行物料追溯和防错。
三、布局防错1. 区域划分:通过合理规划工作区域和物料摆放位置,减少操作过程中的混淆和错误。
2. 定位销:在固定位置上设置定位销,确保物料和组件的正确放置和装配。
3. 布局优化:调整布局和工装器具的位置,使其更加符合人体工学和操作习惯,减少误操作的可能性。
四、工艺防错1. 自动化设备:利用自动化设备代替手工操作,降低人为因素对产品质量的影响。
2. 关键工艺参数监控:实时监测关键工艺参数,确保工艺过程的稳定性和产品质量的一致性。
3. 工艺流程优化:通过对工艺流程的优化和改进,提高生产效率和产品质量。
五、程序防错1. 操作流程标准化:制定标准操作流程,确保每个员工都能够按照统一的标准进行操作。
2. 操作验证:在操作过程中设置验证环节,确保操作步骤的正确性和有效性。
3. 程序监控:通过程序监控和报警系统,及时发现和纠正生产过程中的异常情况。
六、限度防错1. 数量控制:通过计数器或其他传感器,控制物料数量和生产数量,避免超量或不足的情况发生。
2. 重量检测:通过重量检测设备,实时监测产品重量是否符合标准,避免重量偏差导致的产品质量问题。
3. 尺寸检测:利用测量工具和仪器,检测产品尺寸是否符合设计要求,避免尺寸偏差导致的产品质量问题。
防错技术在汽车制造过程中的应用

防错技术在汽车制造过程中的应用
防错技术是指在生产制造中采取措施避免或减少错误和失误的发生,旨在提高产品的质量和安全性。
在汽车制造过程中,防错技术的应用可以从以下几个方面考虑:
1.质量控制防错技术:在汽车制造生产过程中,应用质量控制防错技术,对制造生产过程进行严格监控,从而确保制造生产的每一个环节都符合质量要求。
例如,在涂装车身外壳时,需要对涂料的涂布厚度和涂布均匀性进行控制,避免出现涂料厚度不均、漏涂等质量问题。
2.工艺控制防错技术:采用工艺控制防错技术,对制造生产过程行为进行严格规范,避免制造生产过程中因为操作不当而发生的失误和错误。
例如,在汽车发动机生产过程中,需要对零部件的配件、加工质量、安装过程等进行严格控制,避免因为工艺问题导致车辆出现故障。
3.故障检测防错技术:在汽车制造生产过程中,应用故障检测防错技术,对制造的汽车进行检测,早期发现可能存在的故障和隐患。
例如,在汽车生产流水线上,采用自动化的车身测量系统检测每个车身的安装和加工质量,避免车身存在变形、歪斜等问题。
总之,防错技术是汽车制造中不可或缺的技术,应用防错技术可以大大提高汽车制造的质量和安全性,避免因为失误和错误产生的质量和安全问题。
防错方法在工艺设计中的应用

防错方法在工艺设计中的应用发布时间:2021-07-31T09:57:14.751Z 来源:《电力设备》2021年第3期作者:燕纪钧吴挺成普霞[导读] 或是统一一些标准的工艺编制方法,最大限度的避免整个过程中可能出现的质量问题。
(中国航发西安动力控制有限公司陕西西安 710077)摘要:随着产品的更新换代加速以及市场竞争日趋激烈,导致生产节奏越来越快,工艺编制周期越来越短。
但质量是航空人的生命,如何在紧张的工作节奏中保证产品的质量,尤其是新研产品的质量就显得尤为重要。
怎样在工艺编制中加入防错措施,在满足分厂生任务产周期的同时又能保证产品的质量,是我们在工艺编制时需要考虑的。
关键词:防错措施;生产周期;产品质量一、前言随着分厂生产任务越来越多以及公司对产品质量要求越来越严,更多的压力被放到了工艺员的身上。
由于外部竞争环境激烈,新研工艺的编制周期被大幅压缩,同时对校队人员的压力也非常大。
生产方面,调试工没有多余的时间去消化工艺图纸,从而多方面积累了产品的质量风险。
如何化解这一系列的问题,就需要在工艺编制时多考虑一些防错措施,或是统一一些标准的工艺编制方法,最大限度的避免整个过程中可能出现的质量问题。
二、工序绘图基本要求现行工序绘图随意性较大,有些使用比例缩放功能导致图形尺寸不再是1:1绘制,或者剖切旋转等视图不假思索的按照设计图进行绘图,这些都会给校队者或者加工调试者带来不必要的麻烦,从而成为质量风险点。
最后就是绘图线条有时太近,难以分辨,给加工调试者造成模糊。
因此,在工序绘图时应将一些防错基本要求统一到工艺编制中。
1)工序绘图必须按1:1绘制,在1:1绘制的基础上进行尺寸标注。
如图1所示,禁止编辑基本尺寸及使用文字替代功能。
如果需要缩放图形大小至合适尺寸,可在标注完尺寸后按图2进行比例缩放,缩放时选择尺寸值不变,即可保证所标注的尺寸不会变。
比例不变则代表标注尺寸的大小比例不变,也可选择比例变化,则尺寸大小随图形比例一起变化。
工艺控制及防错系统方案资料

需求 计划生成 3
1
2 计划下达 4
ERP
计划协调
处理并存
贮
18
生产实绩
17
TCP / IP Local network
6
5
生产调度
工单下达 7
8
工单协调
MDS
设备管 理
16 生产报表
WEB监控
14
15
13 数据存储
TCP / IP Local network
车间执行层
控制层
9
10
工单执行 生产控制
数据采集
12 11
生产监控一
OPC-Server
第二部分 总体介绍
系统架构
Config
Monitor
MDS Application
QAD
ERP
Data Interface For ERP
DB
MDS Server
Pack Station
Rework Station
Interface For DI/DO
防错检查-明细功能
主要功能—其他检查
物料检测:检查是否扫描了原材 料批号。 在制品数量检测:检查当前工序 是否堆积了太多的在制品,如果已 经超过最大数量,则进行告警。
客户价值
强化了操作的程序和顺序, 防止由于各种情况下造成的 产品损失、设备损坏、人员 受伤以及缺陷产品的产生。
第三部分 产品解决方案
客户价值
为同一产线少量、多批、 多类型的生产方式提供了良 好的支持,提高了产线灵活 性。 提高产线的设备利用率
第三部分 产品解决方案
1
核心业务流程
2
核心功能一 工序配置
3
质量管控要点防错仪器化和系统预防方案

质量管控要点防错仪器化和系统预防方案随着现代制造业的发展,质量管控在企业的经营中起着至关重要的作用。
为了提高质量管理水平,许多企业开始引入仪器化的质量管理手段,并采取系统预防的方案来防止错误发生。
本文将探讨质量管控要点防错仪器化和系统预防的相关内容,以帮助企业了解并应用这些方法。
一、质量管控要点防错仪器化1. 引入先进设备和技术在质量管控中,引入先进的仪器设备和技术是关键一步。
这些先进设备和技术可以帮助企业实现自动化、精确化的质量监测和检测,从而大大减少人工干预所带来的错误。
2. 实施过程控制过程控制是质量管控的重要组成部分,可以有效地防止错误的发生。
通过仪器化的监测和控制手段,企业可以及时发现和纠正生产过程中的偏离,从而保证产品的质量稳定性。
3. 数据分析和统计利用仪器化手段收集的数据可以进行深入的分析和统计,帮助企业了解产品的质量状况和生产过程中存在的问题。
通过对数据的全面分析,企业可以找出导致错误发生的根本原因,并采取相应措施进行改进。
二、系统预防方案1. 设立标准操作程序(SOP)标准操作程序是系统预防的基础,它规定了产品生产过程中各个环节的操作标准,并明确了质量控制要求。
通过执行SOP,可以最大程度地减少错误的发生,保证产品符合质量要求。
2. 建立质量管理体系建立完善的质量管理体系是系统预防的关键一步。
质量管理体系包括质量策划、质量控制、质量评估等一系列环节,通过系统化的管理手段,可以提前预防错误的发生,确保产品质量的稳定。
3. 培训和教育培训和教育是保证系统预防方案有效执行的关键环节。
企业应该加强对员工的培训,提高他们的质量意识和质量技能,确保每个员工都能熟练掌握质量管理要点,从而减少因操作错误而导致的质量问题。
结语质量管控要点防错仪器化和系统预防方案是现代企业应用的重要质量管理手段。
通过引入仪器化手段和系统预防方案,企业可以提高质量管理水平,降低错误的发生,确保产品质量稳定,赢得市场竞争的优势。
- 1、下载文档前请自行甄别文档内容的完整性,平台不提供额外的编辑、内容补充、找答案等附加服务。
- 2、"仅部分预览"的文档,不可在线预览部分如存在完整性等问题,可反馈申请退款(可完整预览的文档不适用该条件!)。
- 3、如文档侵犯您的权益,请联系客服反馈,我们会尽快为您处理(人工客服工作时间:9:00-18:30)。
防止由于各种情况下造成的 产品损失、设备损坏、人员 受伤以及缺陷产品的产生。
防错检查-明细功能
主要功能--型号检查
检查工件型号与设备当前
HANSHUN
正在加工的型号是否一致, 如果不一致,则进行告警。 检查工件型号与组装零件 型号是否一致,如果不一致, 则进行告警。
客户价值
为同一产线少量、多批、
多类型的生产方式提供了良 好的支持,提高了产线灵活 性。 提高产线的设备利用率
第三部分 产品解决方案
1 2
核心业务流程
HANSHUN
核心功能一 工序配置
核心功能二 防错检查 核心功能三 防错校准 核心功能四 返工控制 核心功能五 换型支持
核心功能五 换型支持
核心功能六 状态反馈
换型支持-明细功能
主要功能
系统支持同时运行多种产品类型。 不同工站可以同时加工不同的产品类型。 支持根据Load工件的产品类型自动切换机
HANSHUN
器正在加工的产品类型。 在切换产品类型时,可以将该产品类型的 加工参数下发到PLC,也可以让PLC将指定 产品类型的加工参数上传到ACC系统。 可以将产品列表下发到PLC 检查工件类型与系统当期类型是否一致
返工控制-明细功能
主要功能
实现重做,跳站,作废,挂起等操作。 可以用来查询一个工件当前状态,所有加
HANSHUN
工历史,所有使用的物料,所有零件,每次 加工的所有加工工艺参数,测试数据等。 可以根据零件条码或者工件流水号进行查 询,并可以重用零件。 每道工序可以进行的操作可以配置和定义, 并有权限控制。 可以重新打印工件所有相关标签。
客户价值
操作工、线长或其他生产
管理人员可以在不停止生产 的情况下使用返工程序方便 快捷的定位并处理线上的各 种问题。
第三部分 产品解决方案
1 2
核心业务流程
HANSHUN
核心功能一 工序配置
核心功能二 防错检查 核心功能三 防错校准 核心功能四 返工控制
3
4 5 6 7
成功客户
上汽变速器厂、天合零部件、敏实集团等
第二部分 总体介绍
业务范围
需求 计划生成
HANSHUN
3 4 5 6
生产调度 计划协调
ERP
生产实绩
1
2
处理并存 贮
18
计划下达
17
TCP / IP Local network
16
工单下达
7
8
MDS
设备管 理
14
防错检查-明细功能
主要功能--零件有效性检查
检查工件是否合格品 检查组装使用的零件是否合格品 检查工件历史加工状态,如果曾
HANSHUN
经与其他零件一起加工过,则判断 是否经过了重用确认。如果经过了 重用确认,则认为有效;否则进行 告警或阻止操作。
客户价值
生产报表 WEB监控
15
数据存储
13
工单协调
数据采集
TCP / IP Local network
12
9
工单执行
10
生产控制
11
生产监控一
OPC-Server
车间执行层 控制层
第二部分 总体介绍
系统架构
HANSHUN
DB
QAD
ERP
Config
Monitor Data Interface For ERP
HANSHUN LOGO
感谢观看
HANSHUN LOGO
生产线工艺控制及防错系统解决方案
演讲人:
目录
HANSHUN
第一部分 第二部分 第三部分 第四部分
方案简介 总体介绍
方案详细介绍
价值与效益分析
第一部分 方案简介
适用范围
HANSHUN
离散制造业对质量要求较高的大中型工厂
功能特性
生产线的工艺控制及防错
准工作,否则警告或不予运 行;减少了由于操作人员疏 忽或故意漏做校准造成的产 品缺陷及损失。
第三部分 产品解决方案
1 2
核心业务流程
HANSHUN
核心功能一 工序配置
核心功能二 防错检查 核心功能三 防错校准
3
4 5 6 7
核心功能四 返工控制
核心功能五 换型支持 核心功能六 状态反馈
Label Print
PLC DT4000
PC via viewtraka
Wireless Termi务流程
核心功能一 工序配置
核心功能二 防错检查 核心功能三 防错校准 核心功能四 返工控制 核心功能五 换型支持 核心功能六 状态反馈
HANSHUN
3
4 5 6 7
客户价值
强化了操作的程序和顺序,
防止由于各种情况下造成的 产品损失、设备损坏、人员 受伤以及缺陷产品的产生。
防错检查-明细功能
主要功能—其他检查
物料检测:检查是否扫描了原材
HANSHUN
料批号。 在制品数量检测:检查当前工序 是否堆积了太多的在制品,如果已 经超过最大数量,则进行告警。
核心业务流程图
HANSHUN
工艺控制及防错系统
工序配置
防错检查 防错校准 返工控制
换型支持
状态反馈
第三部分 产品解决方案
1 2
核心业务流程
HANSHUN
核心功能一 工序配置
核心功能二 防错检查 核心功能三 防错校准 核心功能四 返工控制 核心功能五 换型支持 核心功能六 状态反馈
3
4 5 6 7
核心功能六 状态反馈
状态反馈-明细功能
主要功能
将工件状态反馈给设备,以
HANSHUN
便设备进行加工。
客户价值
在返工阶段为操作人员提
供指引,提高效率,防止物 料浪费或产品损坏。
例如: 工位加工有轴承装配,壳体油脂润滑, 卡圈装配,开口检测几个操作,第一次 加工时,壳体油脂润滑操作已经完成, 但整个加工失败,需要再次返工,而再 次返工时,是不需要再次进行壳体油脂 润滑的,此时,汉顺系统则会告诉设备, 壳体油脂润滑操作已经完成,设备在接 收到该状态后,跳过壳体油脂润滑操作。
客户价值
强化了操作的程序和顺序,
防止由于各种情况下造成的 产品损失、设备损坏、人员 受伤以及缺陷产品的产生。
第三部分 产品解决方案
1 2
核心业务流程
HANSHUN
核心功能一 工序配置
核心功能二 防错检查
3
4 5 6 7
核心功能三 防错校准
核心功能四 返工控制 核心功能五 换型支持 核心功能六 状态反馈
第三部分 产品解决方案
1 2
核心业务流程
HANSHUN
核心功能一 工序配置
3
4 5 6 7
核心功能二 防错检查
核心功能三 防错校准 核心功能四 返工控制 核心功能五 换型支持 核心功能六 状态反馈
防错检查-明细功能
主要功能--跳站/漏序检查
前序工站未正常加工或前序工站
HANSHUN
加工失败,则系统禁止操作或告警。 若已在本工站加工成功过,则系 统禁止操作或告警。 若在本工站加工失败次数超过预 定的最大值,则系统禁止操作或告 警。
客户价值
强化了操作的程序和顺序,
防止由于各种情况下造成的 产品损失、设备损坏、人员 受伤以及缺陷产品的产生。
防错校准-明细功能
主要功能
边缘样件:系统定义了边缘样件
HANSHUN
(包括好件与坏件),以及运行间 隔时间,达到间隔时间后,必须运 行边缘样件。 Audit:PLC自身进行的校准,ACC 系统达到校准时间后,会提示PLC 进行校准操作 。
客户价值
通过系统强制设备进行校
第四部分 价值与效益分析
HANSHUN
更好的产品品质:在加工过程中实时发现质量问题,并对操作工进 行指引式操作,避免由于操作工操作技术的不熟练而导致设备使用 错误。 更短的交货时间:通过减少通讯时间,缩短平均加工周期,提高了 设备利用率。 更高的运作效率 :将复杂的产品和工艺管理用简单的方式有效管理 起来,让工厂的管理者能够更专注于例外事件的处理和现场决策, 大大减少了产品工程师的工作量,提高作业效率。 更少的在制品 :提供车间管理人员将物料或半成品安排到指定设备 进行作业,大大降低在制品数量。 更低的产品成本 :得益于系统带来的制造资源利用率的提高、在制 品的减少、品质损失的降低,产品的成本将下降。
MDS Server
MDS Application
Interface For DI/DO
Interface For Interface For IPC Wireless Terminal
Interface For PLC
Pack Station
Rework Station
Label Print
3
4 5 6 7
工序配置-明细功能
主要功能
可以对产线产品、半成品进行
HANSHUN
分类管理,并且建立产品制造所 需要的各种基础信息。 能配置每个工站的工艺参数, 运行参数,质检参数,校准参数 等。
客户价值
是系统管理员方便快捷的
配置工具。 对于产品部门及工艺部门, 更方便新增或修改产品路由, 更改零配件类型或版本等。