金属铸造成形工艺特点
铸造成形技术-基本知识

(1)流动性 (1)流动性
决定合金流动性的因素主要有: 1、合金的种类:合金的流动性与合金的熔点、 热导率、合金液的粘度等物理性能有关。铸 钢熔点高,在铸型中散热快、凝固快,则流 动性差。
(1)流动性 (1)流动性
2、合金的成分:同种合金中,成分不同的铸造 合金具有不同的结晶特点,对流动性的影响 也不相同。
合金的充型能力及影响因素
1、熔融合金的充型能力: 这里有二个基本概念即充型与充型能力。 ★熔化合金填充铸型的过程,简称充型。 , ★熔融合金充满铸型型腔,获得形状完整,轮廓 清晰铸件的能力,称合金的充型能力。
合金的充型能力及影响因素
2、影响合金充型能力的主要因素有: (1)流动性:流动性指熔融金属的流动能力,它是 影响充型能力的主要因素之一。 (2)浇注条件:指的是浇注温度与充型的压力。 (3)铸型条件:熔融合金充型时,铸型的阻铸型 对合金的冷却作用 都将影响合金的充型能力。
(3)铸型条件 (3)铸型条件
4、铸件结构的壁厚 当铸件壁厚过小,壁厚急剧变化、结构复杂 或有大的水平面时,均会使充型困难。因此 在进行铸件结构设计时,铸件的形状应尽量 简单,壁厚应大于规定的最小壁厚。对于形 状复杂、薄壁、散热面大的铸件,应尽量选 择流动性好的合金或采取其它相应措施。
(3)铸型条件 (3)铸型条件
合金的收缩及影响因素
合金的收缩:
铸件在凝固和冷却过程中,其体积减少的现象称为 收缩。
1)收缩过程及影响因素
收缩可分为液态收缩、凝固收缩和固态收缩,液态 收缩和凝固收缩表现为合金的体积缩小,通常以体积 收缩率表示,它们是铸件产生缩孔、缩松缺陷的基本 原因。 合金的固态收缩,尽管也是体积变化,但它只 引起铸件各部分尺寸的变化。因此,通常用线收缩率 来表示。固态收缩是铸件产生内应力、裂纹和变形等 缺陷的主要原因。
简述铸造成型的特点
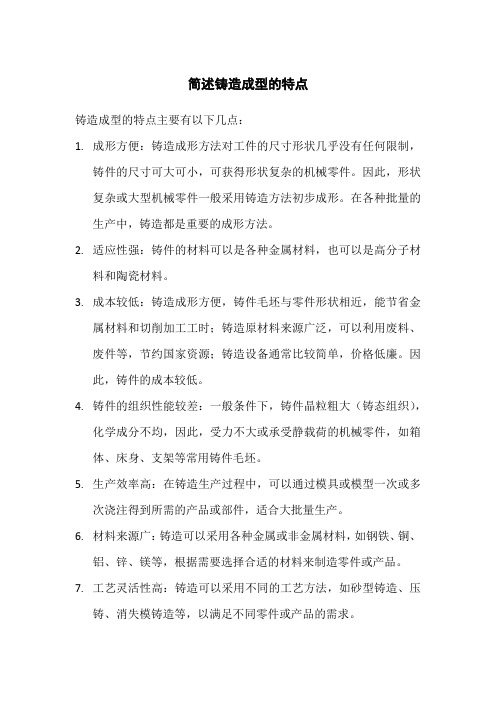
简述铸造成型的特点
铸造成型的特点主要有以下几点:
1.成形方便:铸造成形方法对工件的尺寸形状几乎没有任何限制,
铸件的尺寸可大可小,可获得形状复杂的机械零件。
因此,形状复杂或大型机械零件一般采用铸造方法初步成形。
在各种批量的生产中,铸造都是重要的成形方法。
2.适应性强:铸件的材料可以是各种金属材料,也可以是高分子材
料和陶瓷材料。
3.成本较低:铸造成形方便,铸件毛坯与零件形状相近,能节省金
属材料和切削加工工时;铸造原材料来源广泛,可以利用废料、废件等,节约国家资源;铸造设备通常比较简单,价格低廉。
因此,铸件的成本较低。
4.铸件的组织性能较差:一般条件下,铸件晶粒粗大(铸态组织),
化学成分不均,因此,受力不大或承受静载荷的机械零件,如箱体、床身、支架等常用铸件毛坯。
5.生产效率高:在铸造生产过程中,可以通过模具或模型一次或多
次浇注得到所需的产品或部件,适合大批量生产。
6.材料来源广:铸造可以采用各种金属或非金属材料,如钢铁、铜、
铝、锌、镁等,根据需要选择合适的材料来制造零件或产品。
7.工艺灵活性高:铸造可以采用不同的工艺方法,如砂型铸造、压
铸、消失模铸造等,以满足不同零件或产品的需求。
8.适用范围广:铸造可以生产各种尺寸和重量的零件或产品,从小
型饰品到大型机床和桥梁,都有广泛应用。
总的来说,铸造成型是一种具有广泛应用和重要性的制造工艺。
金属的铸造成形工艺

四、铸造工艺的分类
★按造型材料及工艺特点分为:普通砂型铸造和特种铸造。 普通砂型铸造包括湿砂型、干砂型、化学硬化砂型三类。 特种铸造按造型材料的不同,又可分为两大类:一类以天
然矿产砂石作为主要造型材料,如熔模铸造、壳型铸造、负压 铸造、泥型铸造、实型铸造、陶瓷 型铸造等;一类以金属作 为主要铸型材料,如金属型铸造、离心铸造、连续铸造、压力 铸造、低压铸造等。 ★按金属填充铸型时是否施加外力分为:重力作用下的铸造 成形和外力作用下的铸造成形。
早期的铸件大多是农业生产、宗教、生活等方面的工 具或用具,艺术色彩浓厚。那时的铸造工艺是与制陶工艺 并行发展的,受陶器的影响很大。
司母戊方鼎
曾侯乙尊盘
青铜尊盘出土于曾侯乙墓。尊盘由尊和盘组成,尊置于盘中。 尊盘的口沿是非常精细的镂空的变形龙纹和龙形雕饰,均可 分辨出每条盘龙上的眼睛。是采用“失蜡法”的铸造方法。 尊和盘均铸有“曾候乙作持用终”铭文。
保持1~2年,设备综合开工率>80%,装备全部 开工率<50%,装备标准化、系列化、商品
标准化、系列化、商品化
化程度很低
注:CT为铸件尺寸公差(Casting Tolerances)的代号,见GB/T6414-1986
★铸件处理 铸件自浇注冷却的铸型中取出后,有浇口、冒
口及金属毛刺披缝,砂型铸造的铸件还粘附着砂子, 因此必须经过清理工序。
铸件清理的设备有抛丸机、浇口、冒口切割机 等。砂型铸件落砂清理是劳动条件较差的一道工序, 所以在选择造型方法时 ,应尽量考虑到为落砂清 理创造方便条件。
有些铸件因特殊要求,还要经铸件后处理,如 热处理、整形、防锈处理、粗加工等。
★铸型准备 不同的铸造方法有不同的铸型准备内容。如砂型铸造:铸
铸造成型技术
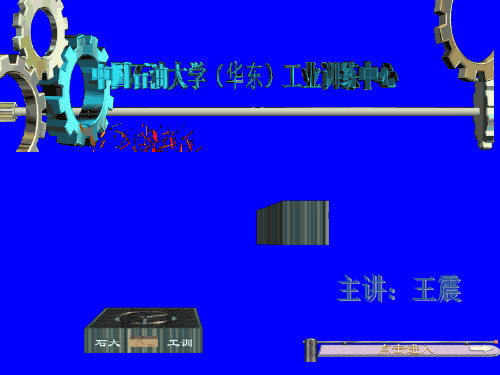
二 铸造的特点
2.1.优点P27 • 毛坯形状(外形至内腔)复杂程度高; • 适应性广(铸件材质、大小、批量); • 材料来源广,成本低(原材料,废料;
形状、尺寸与零件相近,节省材料和加 工费用)。
二 铸造的特点
2.2.缺点P27 • 铸件的力学性能较差(组织粗大,不
均匀); • 质量不容易控制,废品多; • 铸造生产劳动强度大,生产环境差。
• 退让性:铸件凝固后冷却收缩时,型 芯砂是否容易被压缩的性能。
• 可塑性:型砂在外力的作用下成形, 去除外力后能完整的保持所赋予形状 的能力。
五砂 型
他们的关系: 强度 透气性 退让性 可
塑性 耐火性(与原砂中的二氧化硅 的含量有关)
五砂 型
5.2.浇注系统的组成P39
典型的浇注系统一般由外浇口、直浇 道、横浇道和内浇道四部分组成。形状简 单的小型铸件可以省去横浇道。
铸 件
4.2.砂型的组成和作用
名称
作
用
砂 箱 造型时填充型砂的容器,分上、中、下等砂箱。
分型面 各铸型组元间的结合面,每一对铸型间都有一个分型面。
型 腔 用摸样在砂型中形成的,以获得铸件的外形。
型 芯 为获得铸件的内孔或局部外形,用芯砂制成安放在型腔内 部的组元。
浇注系统 在铸型中用来引导金属液流入型腔的通道。
五砂 型
• 外浇口 容纳注入的金属液并缓解液态金属对砂型
的冲击。小型铸件通常为漏斗状,较大型铸件 为盆状。 • 直浇道
连接外浇口与横浇道的垂直通道,通常带 有一定的锥度(上大下小),改变直浇道的高 度可以改变金属液的流动速度从而改变液态金 属的充型能力。
五砂 型
• 横浇道 将直浇道的金属液引入内浇道的水平通道,
铸造成型

模块一 模块二 模块三 模块四
铸造概述 砂型铸造 金属铸造性能 特种铸造简介
模块一 铸造概述
一、铸造成型特点 1、适应性广。各种金属、复杂形状、各种大小。 2、经济性好。废材料利用、设备简单、机加工少。 3、力学性能低。质量不稳、晶粒粗大,缩孔、气孔。 砂型铸造 特种铸造:金属型铸造、 压力铸造、 离心铸造、 熔模铸造等。
特种铸造
一、金属型铸造 一模多铸 1、金属型材料:铸铁或碳钢。 2、金属型铸造的工艺特点 1)金属型预热 预热温度一般不低于150℃。 2)刷耐火涂料 厚0.3-0.4mm,以保护型壁表面。 3、金属型铸造的特点 1)金属型铸件冷却快,组织致密,力学性能高。 2)铸件的精度和表面质量较高 3)金属型成本贵,易产生浇不足。
二、压力铸造
简称压铸
常用压射压力为5-1500MPa,充填速度约5-5m/s, 充填时间很短,约0.01-02s。 压铸过程主要由压铸机来实现。 优点:薄壁、生产率高、细晶、强度较高。 缺点:铸件易产生缩松,制造费用贵。 应用:大批量、薄壁复杂的非铁金属小铸件。
三、离心铸造
优点:力学性能较好;省去芯子和浇注系统。 缺点:内表面质量较差。 应用:空心旋转体、钢套镶铜轴承等。 离心铸造必须在离心铸造机上进行。
铸造应力: 收缩应力、热应力和相变应力 减小铸件变形的措施: 1. 力求使铸件壁厚均匀,形状对称; 2. 合理设计浇冒口等,使铸件冷却均匀; 3. 采用退让性好的型砂和芯砂; 4.
铸件结构的合理性
1、铸件应有合理的壁厚 2、铸件壁厚应力求均匀 3、铸件要有结构斜度 4、应使铸件尽可能不用型芯
模块四
获得外形准确、内部无缺陷铸件的能力。 主要有吸气性、氧化性、流动性和收缩性等。
金属液态成形工艺概述

铸造产品称为: 铸件、铸锭、铸坯、铸带等
一、金属液态成形工艺特点
1. 适应性强
铸件重量:几克 ~ 几百吨 铸件壁厚:0.5 毫米 ~ 1 米 铸件长度:几毫米 ~ 十几米 铸件材质:铁碳合金(鋳铁、鋳钢)、铝合金、铜合金、
镁合金、锌合金、钛合金、复合材料等
速箱体(灰口铸铁)
精密铸造件(不锈钢)
水轮机铸件(铜合金)
箱体(铝合金)
叶轮(钛合金)
一、金属液态成形工艺特点
1. 适应性强
铸件重量:几克 ~ 几百吨 铸件壁厚:0.5 毫米 ~ 1 米 铸件长度:几毫米 ~ 十几米 铸件材质:铁碳合金(鋳铁、鋳钢)、铝合金、铜合金、
镁合金、锌合金、钛合金、复合材料等
铸造方法几乎不受零件大小、形状和结构复杂程度的限制。
轧辊
异型件
装饰件
工艺品
一、金属液态成形工艺特点
2. 尺寸精度高
铸件比锻件、焊接件的尺寸精度高,更接近于零件的尺 寸,可节约大量的金属材料和机械加工工时。
一、金属液态成形工艺特点
2. 尺寸精度高
铸件比锻件、焊接件的尺寸精度高,更接近于零件的尺 寸,可节约大量的金属材料和机械加工工时。
形成的先进铸造技术
精密、优质化
精密成形与加工 近无缺陷成形
数字、网络化
数字造型 虚拟制造
网络制造
精确铸造成形 金属熔体的纯净化、致密化
铸造工艺CAD,铸造模具CAD/CAM一体化 铸造过程宏观模拟及工艺优化 铸件组织微观模拟及性能预测 分散网络化铸造系统
高效、智能化
快速制造 自动化制造系统
智能制造
快速原形及快速制模 铸造过程自动检测与控制,铸造机器人的应用
金属材料成形工艺及控制
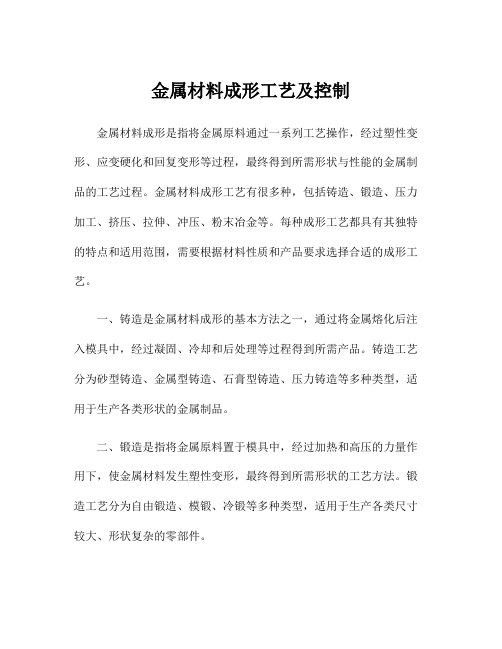
金属材料成形工艺及控制金属材料成形是指将金属原料通过一系列工艺操作,经过塑性变形、应变硬化和回复变形等过程,最终得到所需形状与性能的金属制品的工艺过程。
金属材料成形工艺有很多种,包括铸造、锻造、压力加工、挤压、拉伸、冲压、粉末冶金等。
每种成形工艺都具有其独特的特点和适用范围,需要根据材料性质和产品要求选择合适的成形工艺。
一、铸造是金属材料成形的基本方法之一,通过将金属熔化后注入模具中,经过凝固、冷却和后处理等过程得到所需产品。
铸造工艺分为砂型铸造、金属型铸造、石膏型铸造、压力铸造等多种类型,适用于生产各类形状的金属制品。
二、锻造是指将金属原料置于模具中,经过加热和高压的力量作用下,使金属材料发生塑性变形,最终得到所需形状的工艺方法。
锻造工艺分为自由锻造、模锻、冷锻等多种类型,适用于生产各类尺寸较大、形状复杂的零部件。
三、压力加工是指通过金属材料受到外力压缩、拉伸、弯曲等作用,使其发生塑性变形,并最终得到所需形状的金属成形方法。
压力加工包括挤压、拉伸、剪切、折弯等多种工艺,适用于生产各类薄板、管材、棒材等产品。
四、挤压是指将金属加热至熔点后,在压机的作用下通过模具挤出,得到所需形状的工艺方法。
挤压工艺适用于生产各类型材、异型材、电线电缆、铝箔等产品。
五、拉伸是指通过将金属材料置于拉伸机中,受到拉力的作用下,使其发生塑性变形,最终得到所需形状的金属成形方法。
拉伸工艺适用于生产各类细丝、线材、管子等产品。
六、冲压是指通过冲压机将金属板材置于模具中,经过冲击力的作用下,使其发生塑性变形,最终得到所需形状的金属成形方法。
冲压工艺适用于生产各类薄板金属产品,如汽车车身板、电器外壳等。
七、粉末冶金是指将金属粉末与非金属粉末按一定配比混合,压制成坯料后通过烧结等过程,最终得到具有一定形状和性能的金属制品的工艺方法。
粉末冶金工艺适用于生产各类复杂形状、高精度的金属制品。
以上是金属材料成形工艺的简要介绍,为了保证金属制品质量和实现成形工艺的控制,需要进行相应的工艺控制。
铸造工艺原理和总结

铸造工艺原理和总结一、实质、特点及应用1.铸造定义是指熔炼金属、制造铸型、并将熔融金属浇注入铸型内、凝固后获得一定形状和性能铸件的成形方法。
铸造实质:是利用熔融金属的流动性能实现成形。
铸件:用铸造方法得到的金属零件。
铸型:形成铸件形状的工艺装置。
2.铸造的特点1)成形方便、适应性强•尺寸、形状不受限制长度从几mm-20m;厚度从0.5-500mm;重量从几克-几百吨;•材料的种类和零件形状不受限制。
2)生产成本较低(与锻造比)•设备费用低;•减少加工余量,节省材料;•原材料来源广泛。
3)组织性能较差•晶粒粗大、不均匀;•力学性能差;-工序繁多、易产生铸造缺陷。
4)工作条件差、劳动强度大。
3、铸造的应用1)形状复杂、特别是具有复杂内腔的零件:箱体、缸体和壳体;2)尺寸大、质量大的零件,如床身、重型机械零件;3)力学性能要求不高,或主要承受压应力作用的零件,如底座、支架;4)特殊性能要求的零件,如球磨机的磨球、拖拉机的链轨。
4、铸造成形的基本工序二、金属的铸造性能——是指金属材料铸造成形的难易程度。
评价指标:流动性和收缩性。
(一)流动性——是指熔融金属有流动能力1、表示方法螺旋试样长度L,如L铸钢=20mm,L铸铁=1800mm,铸铁的流动性比铸钢好。
2、影响流动性的因素1)化学成分:共晶合金最好,纯金属差;2)浇注温度:T浇愈高,保温时间愈长,流动性愈好,但收缩性大和浇毁铸型。
经验:“高温出炉,低温浇注”。
3)铸型类别影响铸型蓄热能力和透气性;如、干砂型〉湿砂型>金属型。
4)铸型结构简单、壁厚的铸型〉复杂、壁薄的铸型。
3、流动性对铸件质量的影响流动性好:铸件形状完整、轮廓清晰;利于气体和夹杂物上浮排出和补偿;流动性不好:产生浇不到和冷隔、气孔和夹杂等缺陷。
4、防止流动性不好缺陷方法调整化学成分、提高浇注温度和改善铸型条件。
(二)收缩性——指浇注后熔融金属逐渐冷却至室温时总伴随着体积和尺寸缩小的特性。
金属型铸造方法

(3)金属型工作温度:取决于浇注合金的种类和牌号、铸 件的结构形状、尺寸大小和壁厚,同时也和合金的浇注温 度有关。过高过低均会产生铸造缺陷。 (4)合金的浇注温度 :受铸件结构、铸型温度、浇注速度 、浇注系统形式和合金种类等因素的影响 。
金属型铸造优点(与砂型铸造比)
(1)由于不需造型,从而节省了型砂的制备和输送以及造型、落砂和 热处理等工序,同样也节省了这些工序所需要的工时及设备。因此, 显著地提高了生产率,改善了劳动条件,减轻了对环境的污染。
图 1一金属型
整体金属型 2一砂芯 8一转轴
图 水平分型金属型 B2。9冠直分型金属型 1一上半型2一砂芯 3—下半型 1一右半型2一左半型3一金属型芯
图 垂直分型金属型 1一右半型 2一左半型 3一金属型芯
金属型的破坏原因
一) 二) 三) 四) 五) 六) 热应力的叠如 热疲劳应力 铸铁生长 氯气侵蚀 金属液的冲剧 铸件的摩擦
二、金属型结构
金属型的结构形式可根据其分型面数、分型面方向和铸型 型体的运动方式等特征,将金属型进行分类。 金属型结构形式的确定取决于:铸件的形状、大小和浇注 位置;分型面的方向和数目;浇注系统和冒口的形式、型 芯的种类和数量;铸造合金种类;铸型中铸件的数量;生 产批量的大小和采用的机械化程度。
三、铸件常见缺陷及防止方法
金属型铸件的常见缺陷有气孔、缩孔及缩松、渣孔、针孔 、裂纹、冷隔等。产生这些缺陷的原因大体上包括金属型 预热温度太低、排气设计不良、涂料本身排气性不佳、金 属液处理不符合要求、金属型设计存在结构或工艺方面的 问题、开模时间或者浇注温度掌握不准确等。应根据出现 的铸件缺陷对症下药,有针对性地解决问题。
第2节 金属型铸造
一、观看金属型铸造机 二、金属型铸 1。金属型铸造原理、特点及热规范的确定 2。金属型结构 3。铸件常见缺陷及防止方法
铸造成形

• “砂型铸造” 时先将下半型放在平板上, 放砂箱、填型砂、紧实刮平,下型造完, 将造好的砂型翻转180度,放上半型,撒 分型剂,放上砂箱,填型砂并紧实、刮 平,将上砂箱翻转180度,分别取出上、 下半型,再将上型翻转180度和下型合好, 砂型造完,等待浇注。这套工艺俗称-“翻砂”。
清 铜螃蟹形
“铸造”俗称“翻砂”的 由来
四、熔模铸造(investment casting)
中国古代三大铸造技术
• 泥范铸造
• 失蜡铸造 • 金属型铸造
古青铜器主要制作法
青铜器的铸造,主要采用泥范铸造和失蜡铸造。 中国的青铜器铸造以泥范为主,并在近代兴起砂型 铸造之前的三千多年时间内,泥范分范合铸一直是 最主要的铸造成形方法,春秋中期以前几乎是唯一 的方法。这和美索不达米亚、埃及等地以失蜡铸造 为主的情况截然不问,是中国独有的技术道路。
接造出曲面分型面,代替挖砂造型,操作较简单。
应用:用于小批或成批生产,分型面不平的铸件。
刮板造型 特点:刮板形状和铸件截面相适应,代替实体模样,
可省去制摸的工序。
应用:单件小批生产,大、中型轮类、管类造型
特点:采用上、下、中三个砂箱,有两个分型面,铸件
的中间截面小,用两个砂箱时取不出模样,必须分模,操 作复杂。 应用:单件小批生产,适合于中间截面小,两端截面大 的铸件。 分型面 上砂箱 中砂箱 下砂箱 分型面
铸件名义尺寸的百分比。
5)铸造圆角 (curving of casting ) 定义:指设计铸件时,在璧间的连接和拐角处,应设
计处圆弧过渡,此圆弧称为铸造圆角。
作用:可避免热节形成;改善应力分布;避免砂型损
坏和产生砂眼。
凝固特性 热节、充型
确定浇铸位置和分型面
铸造成形方法及特点概述
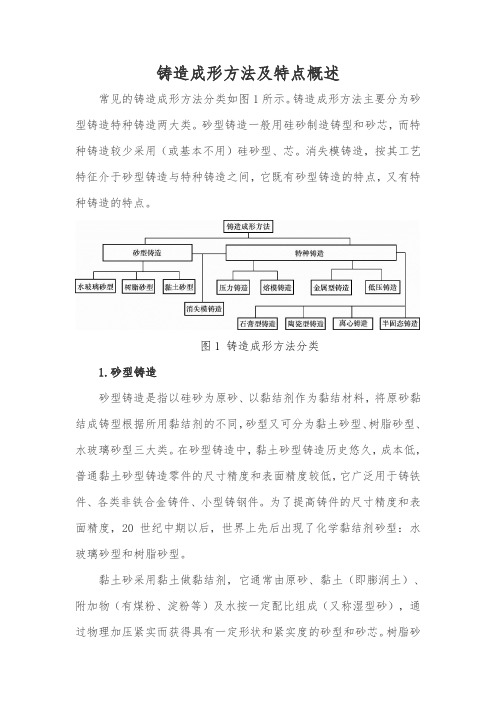
铸造成形方法及特点概述常见的铸造成形方法分类如图1所示。
铸造成形方法主要分为砂型铸造特种铸造两大类。
砂型铸造一般用硅砂制造铸型和砂芯,而特种铸造较少采用(或基本不用)硅砂型、芯。
消失模铸造,按其工艺特征介于砂型铸造与特种铸造之间,它既有砂型铸造的特点,又有特种铸造的特点。
图1 铸造成形方法分类1.砂型铸造砂型铸造是指以硅砂为原砂、以黏结剂作为黏结材料,将原砂黏结成铸型根据所用黏结剂的不同,砂型又可分为黏土砂型、树脂砂型、水玻璃砂型三大类。
在砂型铸造中,黏土砂型铸造历史悠久,成本低,普通黏土砂型铸造零件的尺寸精度和表面精度较低,它广泛用于铸铁件、各类非铁合金铸件、小型铸钢件。
为了提高铸件的尺寸精度和表面精度,20世纪中期以后,世界上先后出现了化学黏结剂砂型:水玻璃砂型和树脂砂型。
黏土砂采用黏土做黏结剂,它通常由原砂、黏土(即膨润土)、附加物(有煤粉、淀粉等)及水按一定配比组成(又称湿型砂),通过物理加压紧实而获得具有一定形状和紧实度的砂型和砂芯。
树脂砂型、水玻璃砂型,采用树脂及水玻璃等化学黏结剂,辅之固化剂(树脂砂常用磺酸,水玻璃砂常用CO2和有机酯等)调节砂型的硬化速度,形成强度和精度更高的砂型。
2.特种铸造在铸造行业,砂型铸造以外的铸造方法统称为特种铸造。
特种铸造的种类很多,它包括:精密熔模铸造、压力铸造、金属型铸造、离心铸造、反重力铸造(低压铸造、压差铸造)等。
特种铸造大多采用金属铸型,铸型的精度高表面粗糙度低,透气性差,冷却速度快。
因此,与砂型铸造比较,特种铸造的零件的尺寸精度和表面精度更高,但制造成本也更高;特种铸造,大多为精密铸造的范畴。
大量应用的常见特种铸造方法包括熔模精密铸造、压力铸造、金属型铸造、低压铸造四种。
3.消失模铸造笔者认为,消失模铸造是介于砂型铸造与特种铸造之间的铸造方法,它采用无黏结剂的砂粒作为填充,又采用金属模具发泡成形泡沫塑料模样,浇注及生产过程与砂型铸造过程相似,其铸件的精度和表面质量又与特种铸造相似。
铸造种类和特点

铸造种类和特点铸造是制造工程领域中最常用的成形工艺之一,广泛应用于各个行业,如汽车、航空航天、机械制造等。
它以熔化金属液态材料,通过铸型成形,获得所需形状和尺寸的工件。
根据铸造方法和材料的不同,可以将铸造分为几种不同的类型。
本文将为大家介绍一些常见的铸造种类及其特点。
1. 砂型铸造砂型铸造是最常见和最基本的铸造方法之一。
它使用砂型作为铸造模具,在高温下,将熔化金属注入模具中,冷却后获得所需工件。
砂型铸造具有成本低、灵活性高等特点,适用于大多数金属材料的铸造,尤其适用于复杂形状的工件。
2. 金属型铸造金属型铸造是使用金属型作为模具进行铸造的方法。
金属型通常由铜合金或钢制成,可重复使用多次,具有较高的精度和表面质量。
金属型铸造适用于生产高精度、高表面质量要求的工件,如发动机缸体、汽车零件等。
3. 熔模铸造熔模铸造是一种精密铸造方法,也被称为“失蜡法”。
该方法首先制作模具,然后在模具中注入蜡模,形成整个铸件的空腔结构。
蜡模覆盖有特殊的耐火涂料,形成熔模。
在熔模中倒入熔化金属,蜡模被熔化和燃烧,金属充满模腔后冷却凝固,得到最终的铸件。
熔模铸造具有较高的精度和表面质量,适用于生产复杂形状、高精度的工件。
4. 压铸压铸是一种以高压下将熔化金属注入金属模具中的方法。
它具有高生产效率和较高的表面质量,适用于大批量生产复杂形状的工件。
压铸可用于铝合金、镁合金和锌合金等材料的铸造。
5. 真空铸造真空铸造是在真空环境下进行的一种特殊铸造方法。
在真空中铸造,可有效防止金属氧化和气孔的产生,提高铸件的密度和质量。
真空铸造适用于高温合金、精密合金等材料的铸造,广泛用于航空航天领域。
每种铸造方法都有其适用的范围和特点。
在实际生产中,根据所需工件的形状、尺寸、材料和数量等要求,选择合适的铸造方法非常重要。
总结:铸造作为一种传统工艺,在现代制造业中仍然扮演着重要的角色。
通过不同的铸造方法可以生产出各种形状、材料和尺寸的工件,满足各种行业的需求。
铸造工艺,特点及其应用

铸造(casting)铸造是将金属熔炼成符合一定要求的液体并浇进铸型里,经冷却凝固、清整处理后得到有预定形状、尺寸和性能的铸件的工艺过程。
铸造毛坯因近乎成形,而达到免机械加工或少量加工的目的降低了成本并在一定程度上减少了时间.铸造是现代制造工业的基础工艺之一。
把金属材料做成所需制品的工艺方法很多,如铸造、锻造、挤压、轧制、拉延、冲压、切削、粉末冶金等等。
其中,铸造是最基本、最常用的工艺。
铸造种类很多,按造型方法习惯上分为:①普通砂型铸造,包括湿砂型、干砂型和化学硬化砂型3类。
②特种铸造,按造型材料又可分为以天然矿产砂石为主要造型材料的特种铸造(如熔模铸造、泥型铸造、铸造车间壳型铸造、负压铸造、实型铸造、陶瓷型铸造等)和以金属为主要铸型材料的特种铸造(如金属型铸造、压力铸造、连续铸造、低压铸造、离心铸造等)两类。
铸造可按铸件的材料分为:黑色金属铸造(包括铸铁、铸钢)和有色金属铸造(包括铝合金、铜合金、锌合金、镁合金等)铸造有可按铸型的材料分为:砂型铸造和金属型铸造。
按照金属液的浇注工艺可分为:1、重力铸造:指金属液在地球重力作用下注入铸型的工艺,也称浇铸。
广义的重力铸造包括砂型浇铸、金属型浇铸、熔模铸造、消失模铸造,泥模铸造等;窄义的重力铸造专指金属型浇铸。
2、压力铸造是指金属液在其他外力(不含重力)作用下注入铸型的工艺,按照压力的大小,又分为高压铸造(压铸)和低压铸造。
补充知识:1、精密铸造是相对于传统的铸造工艺而言的一种铸造方法。
它能获得相对准确地形状和较高的铸造精度。
较普遍的做法是:首先做出所需毛坯(可留余量非常小或者不留余量)的电极,然后用电极腐蚀模具体,形成空腔。
再用浇铸的方法铸蜡,获得原始的蜡模。
在蜡模上一层层刷上耐高温的液体砂料。
待获得足够的厚度之后晾干,再加温,使内部的蜡模溶化掉,获得与所需毛坯一致的型腔。
再在型腔里浇铸铁水,固化之后将外壳剥掉,就能获得精密制造的成品2、选择铸造方式时应考虑:a.优先采用砂型铸造 b.铸造方法应和生产批量相适3、 c.造型方法应适合工厂条件 d.要兼顾铸件的精度要求和成4、金属材料的力学性能主要指:强度、刚度、硬度、塑性、韧性等。
金属型铸造工艺流程
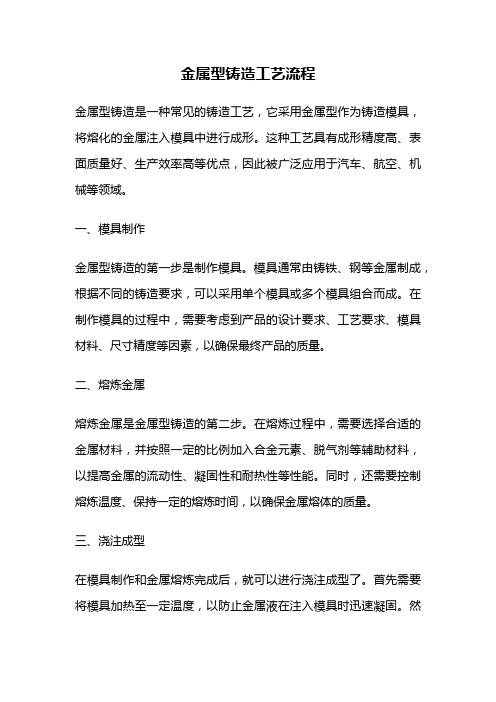
金属型铸造工艺流程金属型铸造是一种常见的铸造工艺,它采用金属型作为铸造模具,将熔化的金属注入模具中进行成形。
这种工艺具有成形精度高、表面质量好、生产效率高等优点,因此被广泛应用于汽车、航空、机械等领域。
一、模具制作金属型铸造的第一步是制作模具。
模具通常由铸铁、钢等金属制成,根据不同的铸造要求,可以采用单个模具或多个模具组合而成。
在制作模具的过程中,需要考虑到产品的设计要求、工艺要求、模具材料、尺寸精度等因素,以确保最终产品的质量。
二、熔炼金属熔炼金属是金属型铸造的第二步。
在熔炼过程中,需要选择合适的金属材料,并按照一定的比例加入合金元素、脱气剂等辅助材料,以提高金属的流动性、凝固性和耐热性等性能。
同时,还需要控制熔炼温度、保持一定的熔炼时间,以确保金属熔体的质量。
三、浇注成型在模具制作和金属熔炼完成后,就可以进行浇注成型了。
首先需要将模具加热至一定温度,以防止金属液在注入模具时迅速凝固。
然后将熔化的金属液倒入模具中,待金属液凝固后,即可将模具拆卸,取出成品。
四、清理和加工铸造完成后,还需要进行清理和加工。
清理工作主要包括切割、抛光、喷砂等,以去除模具留下的余料和浇注产生的毛刺等杂质。
加工工作则主要包括铣削、钻孔、车削等,以达到最终产品的尺寸精度和外观质量要求。
五、质量检验最后一步是对产品进行质量检验。
质量检验主要包括外观检查、尺寸测量、物理性能测试等,以确保产品符合设计要求和客户要求。
如果发现质量问题,需要及时进行调整和改进,以提高生产效率和产品质量。
金属型铸造工艺是一种精密的制造工艺,需要在每个环节上严格控制,以确保最终产品的质量。
在实际应用中,还需要不断改进和创新,以满足客户日益增长的需求和市场竞争的挑战。
挤压铸造特点及应用

挤压铸造特点及应用挤压铸造是一种能够将金属材料通过压力挤压成型的铸造工艺。
相比于传统的铸造工艺,挤压铸造具有以下特点。
首先,挤压铸造具有高效性能。
挤压铸造的工艺能够在短时间内将金属材料形成所需的结构和形状,生产效率高,并且具有高度的一致性和重复性。
其次,挤压铸造的产品具有优良的机械性能。
挤压过程中,金属材料通过挤压力产生的高压力和高温度,能够使金属内部的结晶粒细化,并且使得材料中的夹杂物和气孔等缺陷得到排除,从而提高了产品的强度、硬度和韧性等机械性能。
再次,挤压铸造可以生产大尺寸和复杂结构的产品。
挤压铸造工艺能够按照模具的形状要求将金属材料挤压成形,因此可以生产出形状复杂、壁厚薄的产品,包括管道、棒材、异型材等。
同时,挤压铸造还具有较高的尺寸精度和表面质量,能够满足高要求的工程需求。
最后,挤压铸造还具有节约能源和环保的优点。
挤压铸造过程中,在减少熔化能耗的同时,还能够最大限度地减少材料的损耗和废弃物的产生,从而降低了资源的浪费和对环境的污染。
挤压铸造在工业生产中有着广泛的应用。
首先,在汽车工业中,挤压铸造被应用于生产汽车零部件,如车身结构件、发动机零部件、悬挂系统等。
挤压铸造能够生产出质量优良、精度高的零部件,提高汽车整体性能。
其次,在航空航天工业中,挤压铸造被广泛应用于生产航空发动机叶片、飞机结构件等关键零部件。
挤压铸造能够保证零部件的高强度和高温性能,提高航空器的安全性和可靠性。
此外,挤压铸造还被应用于制造机械设备的零部件和工具。
比如挤压铸造能够生产出高强度、耐磨损的传动轴、齿轮、螺纹和各种模具等工具件,提高机械设备的使用寿命和性能。
另外,挤压铸造还被广泛应用于建筑、电子、电力等领域。
比如在建筑领域,挤压铸造可以生产出抗震、防火性能优良的铝合金门窗、墙板等建筑材料。
在电子领域,挤压铸造可以生产出散热性能好的铝合金外壳、散热片等电子器件。
在电力领域,挤压铸造可以生产出高导热、高强度的铜导线、铝合金散热器等电力设备。
金属材料成形工艺的种类及特点

金属材料成形工艺的种类及特点金属材料成形方法是零件设计的重要内容,也是制造者们极度关心的问题,金属成形工艺分为八大工艺:铸造、塑性成形、机加工、焊接、粉末冶金、金属注射成型、金属半固态成型、3D打印。
一、铸造液态金属浇注到与零件形状、尺寸相适应的铸型型腔中,待其冷却凝固,以获得毛坯或零件的生产方法,通常称为金属液态成形或铸造。
1、工艺流程:液体金属→充型→凝固收缩→铸件2、工艺特点:1)可生产形状任意复杂的制件,特别是内腔形状复杂的制件。
2)适应性强,合金种类不受限制,铸件大小几乎不受限制。
3)材料来源广,废品可重熔,设备投资低。
4)废品率高、表面质量较低、劳动条件差。
3、铸造分类:(1)砂型铸造砂型铸造:在砂型中生产铸件的铸造方法。
钢、铁和大多数有色合金铸件都可用砂型铸造方法获得。
工艺流程:技术特点:1)适合于制成形状复杂,特别是具有复杂内腔的毛坯;2)适应性广,成本低;3)对于某些塑性很差的材料,如铸铁等,砂型铸造是制造其零件或,毛坯的唯一的成形工艺。
应用:汽车的发动机气缸体、气缸盖、曲轴等铸件(2)熔模铸造熔模铸造:通常是指在易熔材料制成模样,在模样表面包覆若干层耐火材料制成型壳,再将模样熔化排出型壳,从而获得无分型面的铸型,经高温焙烧后即可填砂浇注的铸造方案。
常称为“失蜡铸造”。
工艺流程:优点:1)尺寸精度和几何精度高;2)表面粗糙度高;3)能够铸造外型复杂的铸件,且铸造的合金不受限制。
缺点:工序繁杂,费用较高应用:适用于生产形状复杂、精度要求高、或很难进行其它加工的小型零件,如涡轮发动机的叶片等。
(3)压力铸造压铸:是利用高压将金属液高速压入一精密金属模具型腔内,金属液在压力作用下冷却凝固而形成铸件。
工艺流程:优点:1)压铸时金属液体承受压力高,流速快2)产品质量好,尺寸稳定,互换性好;3)生产效率高,压铸模使用次数多;4)适合大批大量生产,经济效益好。
缺点:1)铸件容易产生细小的气孔和缩松。
铸造生产的特点和工作流程

铸造生产成本低廉,生产方式灵活
*
01
清理
熔化
02
在砂型铸造中铸造生产的环节包括: 配砂
造型
03
单击此处添加正文
造芯
04
单击此处添加正文
合箱
铸造生产环节
CONTENTS
05
单击此处添加正文
浇注
06
单击此处添加正文
出砂
型砂的组成及性能要求
2-1 铸造生产概论
原砂 ( SiO2 ) 粘结剂:使型砂具有一定的强度 水 添加物:提高型砂容让性,防止铸件粘砂
*
整模造型
2-1 铸造生产概论
工艺特点
模型是一整体,分型面是平面,铸型型腔全部在半个铸型内。造型简单,不会产生错箱缺陷。
应用范围
适用于最大截面靠近毛坯端部且为平面的铸件。 造型方法\整模造型.JPG
*
分模造型
2-1 铸造生产概论
模型沿截面最大处分为两半,分别在上下砂型中,分型面是平面。如果采用整模造型,模型会取不出来。操作简便,分型面整齐。
工艺特点
适用于单件小批生产尺寸较大的等截面或回转体大中型铸件。如带轮、飞轮、齿轮坯等。
应用范围
*
三箱造型
2-1 铸造生产概论
有两个分型面,铸型由上中下三箱构成,中箱高度须与两分型面的高度一致。模型必须分模且只能用于手工造型。操作成本较高。
工艺特点
适用于单件小批生产两端截面大、中部截面小的铸件。
应用范围
*
地坑造型
2-1 铸造生产概论
适用于单件小批生产尺寸较大的大中型铸件或砂箱不足的生产条件。
应用范围
工艺特点
利用地面砂床作为铸型下箱,仅制备上箱即可造型,减少砂箱成本。但技术要求较高。
铸造工艺
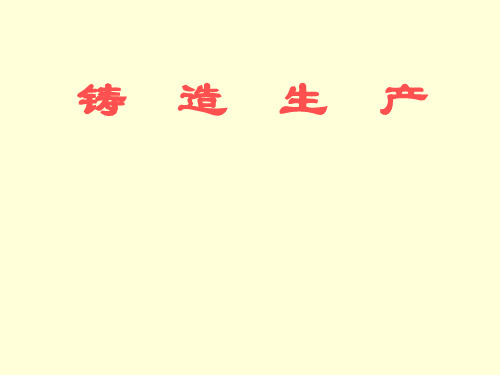
(二)铜合金铸件的生产
1. 铜合金种类 铸造铜合金按其成分不同可分为黄铜和青铜。 铸造铜合金按其成分不同可分为黄铜和青铜。 2. 铜合金的铸造工艺特点 (1)铸造黄铜熔点低、结晶温度窄(30℃-70℃),流 铸造黄铜熔点低、结晶温度窄(30℃-70℃),流 ), 动性好、对型砂耐火度要求不高,可用细砂造型, 动性好、对型砂耐火度要求不高,可用细砂造型,以减小 铸件表面粗糙度值、减小加工余量,并可浇注薄壁铸件。 铸件表面粗糙度值、减小加工余量,并可浇注薄壁铸件。 但其收缩率大、容易产生集中缩孔, 但其收缩率大、容易产生集中缩孔,铸造时应配置较大的 冒口。 冒口。 (2)锡青铜在液态下易氧化,在开设浇道时,应尽力使 锡青铜在液态下易氧化,在开设浇道时, 金属液流动平稳、防止飞溅, 金属液流动平稳、防止飞溅,故常用开放式及底注式浇注 系统。锡青铜的凝固温度宽(150℃-200℃), ),凝固收缩 系统。锡青铜的凝固温度宽(150℃-200℃),凝固收缩 和线收缩率小,虽不易产生大的集中缩孔, 和线收缩率小,虽不易产生大的集中缩孔,但常出现枝晶 偏析与缩松,降低铸件的致密度。 偏析与缩松,降低铸件的致密度。这种缩松便于储存润滑 油,适宜制造滑动轴承。壁厚不大的锡青铜铸件常采用同 适宜制造滑动轴承。
三、 影响合金收缩的因素
不同成分的合金其收缩率一般也不相同。 1. 化学成分 不同成分的合金其收缩率一般也不相同。在 常用铸造合金中铸钢的收缩最大,灰铸铁最小。 常用铸造合金中铸钢的收缩最大,灰铸铁最小。 合金浇注温度越高,过热度越大, 2. 浇注温度 合金浇注温度越高,过热度越大,液体收缩 越大。 越大。
流动性的影响因素: 2. 流动性的影响因素:
不同种类的合金, 1)合金的种类 :不同种类的合金,具有不同的螺旋线 长度,即具有不同的流动性。其中灰铸铁的流动性最好, 长度,即具有不同的流动性。其中灰铸铁的流动性最好, 硅黄铜、铝硅合金次之,而铸钢的流动性最差。 硅黄铜、铝硅合金次之,而铸钢的流动性最差。
- 1、下载文档前请自行甄别文档内容的完整性,平台不提供额外的编辑、内容补充、找答案等附加服务。
- 2、"仅部分预览"的文档,不可在线预览部分如存在完整性等问题,可反馈申请退款(可完整预览的文档不适用该条件!)。
- 3、如文档侵犯您的权益,请联系客服反馈,我们会尽快为您处理(人工客服工作时间:9:00-18:30)。
形状较复杂的铸件,特别广 泛用于有孔或带有型芯的铸 件,如套筒、水管、阀体、 箱体、曲轴、立柱等。
演示
3)三箱造型过程
演示
特点:铸件两端截面尺寸比中间大,采用两箱无法 起模,将铸件放在三个砂箱中组合而成。
注意:中箱高度须与铸件两个分型面的间距相适应。 三箱造型操作费工,且需配有合适的砂箱。
适用于:单件小批生产。具Hale Waihona Puke 两个分型面的铸件。4)挖砂造型
当铸件最大截面在中部,模样又不便分成两半 (如分模后模样太薄或分面是曲面)时,只能将模样做 成整模,造型时挖掉防碍起模的砂子。 特点:模样是整体的,但铸件的分型面是曲面。 造型操作麻烦,生产率低, 要求操作技术水平高。 适用于:单件、小批量生产。
活块造型
铸件上有妨碍起模的小凸台、肋条等。制模时将此部分 作成活块,在主体模样起出后,从侧面取出活块。
适用于单件、小批生产带有突起部分的铸件
活块用销式 燕尾与模样 的主体连接, 在起模时须 先取出模样 主体,然后 取出活块。
7) 刮板造型
刮板造型
用与铸件截面相适应的刮板代替实体模样造型 的方法。
特点: 刮板造型,可以降低模样成本,缩短生产准备 时间,但要求操作技能高,铸件尺寸精度低,生产 率低,
缺点---生产率低、劳动强度大、铸件质量较 差,所以主要用于单件小批生产。
1.砂箱及造型工具
如图所示。
手工造型的两箱造型图解
排气孔 上箱flask
分型面P/L
型腔 Cavatity
型芯Core
浇注系统 gating system
下箱
2.常见手工造型方法
1) 整模造型
特点: 模样是整体的,铸型的型腔一般只在下箱。造型时,
➢基本术语
模样 由木材、金属或其他材料制成,用来形 成铸型型腔的工艺装备称为模样。
芯盒:制造型芯或其他种类耐火材料芯所用 的装备称为芯盒。 芯盒的内腔与型芯的形状和尺寸相同。
一、砂型铸造
是用模样和型砂制造铸型的一种工艺。
零件图
铸造工艺图
模样图、芯盒图、铸型装配图
混制型砂
制造模样及芯盒 预处理造型材料
混制芯砂
造型
烘干铸型
准备 炉料
熔炼 金属
化验
合型 浇注
落砂、清理
制芯 烘干芯子
检验
热处理
合格铸件
基本工艺过程
砂型铸造
造型材料: 型砂和芯砂 由原砂、粘结剂、水和附 加物
造型方法: 手工造型
整模造型 分模造型 三箱造型 挖砂造型 活块造型 刮板造型等
机器造型
压实式造型 震机压实式造型 微震压实式造型 高压式造型
适用于:单件、小批生产尺寸较大的回转体铸件,如 皮带轮、齿轮等。
8)地坑造型
大型铸件单件生产时,为节省下砂箱,降低铸型 高度,便于浇铸,多采用地坑造型。
造型时先在地坑中填入型砂,制好砂床,再将模 样安卧好,再填砂舂实、刮平,造上箱。
表2-2 常用手工造型方法的特点及应用
造型方法
主要特点
适用范围
空气冲击式造型
射压式造型
抛砂式造型
铸件形体组合-造型方法选定
手工造型hand molding 定义---全部用手工或手动工具完成的造型工
序称为手工造型。
填砂、紧实和起模人工完成
机器造型machine molding
:机器加砂、紧砂与起模(造型机)
(一)手工造型
优点---手工造型操作灵活、工艺装备(模样、 芯盒、砂箱等)简单、生产准备时间短、适 应性强,造型质量一般可满足工艺要求,
整模造型 整体模,平面分型面,型腔在一个 最大截面位于一端并为平 砂箱内;造型简单,铸件精度表面 面的简单铸件的单件、小
质量较好
批生产
分模造型
模样沿最大截面分为两半,型腔位 最大截面在中部,一般为
于上、下两个砂箱,造型简便
对称性铸件,如套、管、
阀类零件单件、小批生产
挖砂造型
模样为整体,但分型面不是平面, 分型面不是平面的铸件的 造型时手工挖去阻碍取模的型砂, 单件、小批生产
挖砂
5) 假箱造型
假箱造型
对于分型面为阶梯面或曲面的铸件,当生产数量较多时, 为了克服挖砂造型的缺点,可用成形底板代替平面底板,并将 模样放置在成形底板上造型,可省去挖砂操作。
成形底板可根据生产数量的不同,分别用金属、 木材制作; 如果件数不多,可用粘土较多的型砂舂紧制成砂 质成形底板
6)活块造型
整个模样能从分型面方便地取出。 整模造型因操作简便,无砂箱错位现象。
适用于:外形轮廓上 有一个平面可作分型 面的简单铸件,如齿 轮坯、轴承、皮带轮 罩等。 整模造型 图示
2) 分模造型
将模样沿最大截面处分为两半,型腔分别位于 上、下两个半型内。
特点:铸件的最大截面不在端部而在中部,因而木 模沿最大截面分成两半。 造型简单,节省工时 。
Clasfication of foundry Methods
砂型铸造
手工造型 机器造型
液态成型工艺
特种铸造
金属型铸造 熔模铸造 压力铸造 低压铸造 陶瓷型铸造 离心铸造
一、砂型铸 造
砂型铸造是传统的铸造方法,由于适应
于各种形状、大小、批量及各种合金铸件
的生产,也是使用最广的一种铸造方法。
一、砂型铸 造
金属的铸造形成工艺
本章学习目的与要求:
掌握各种造型方法的原理、特点与用途; 能根据零件的结构形状、大小 与生产类型 正确选择铸造方法
第一节 重力作用下的铸造成形
靠液态金属自身的重力充填型腔的形成工艺
第二节 外力作用下的铸造成形
靠外力充填型腔的形成工艺
第一节 重力作用下的铸造成形
金属的液态成型工艺的种类
续
造型方法
主要特点
适用范围
刮板造型 用刮板代替模样造型。节约木材, 用于等截面或回转体大中 缩短生产周期,生产率低,技术水 型铸件的单件、小批生产 平高,精度较差
两箱造型
铸型由上型和下型构成,各类模样,最 基 本 的 造 型 方 法 。 各 种
操作方便
铸型,各种批量
三箱造型 脱箱造型
铸件两端截面尺寸比中间大,必须 主要用于手工造型,具有
有两个分型面
两个分型面的铸件的单件、
小批生产
采用活动砂箱造型,合型后脱出砂 用于小铸件的生产。 箱
生产率低,技术水平高
假箱造型
为省却挖砂操作,在造型前特制一 分型面不是平面的铸件的 个底胎,然后在底胎上造下箱;底 成批生产
胎可多次使用,不参与浇注
活块造型 对铸件上妨碍起模的小部分做成活 用于妨碍起模部分的铸件 动部分。起模时先取出主体部分, 的单件、小批生产 再取出活动部分
表2-2 常用手工造型方法的特点及应用