模具验收标准
模具验收标准

模具验收标准一、模具外观:1铭牌内容是否打印模具编号、模具重量(KG、模具外形尺寸(mm,字符均用1/8英寸的字码打上,字符清晰、排列整齐。
2 铭牌是否固定在模腿上靠近后模板和基准角的地方(离两边各有15mm的距离),用四个柳钉固定,固定可靠,不易剥落。
3 冷却水嘴是否用塑料块插水嘴,C 10管,规格可为G1/8''、G1/4''、G3/8''。
如合同有特殊要求,按合同。
4 冷却水嘴是否伸出模架表面,水嘴头部凹进外表面不超过3mm。
5 冷却水嘴避空孔直径是否为C 25、C 30、C 35mm三种规格,孔外沿有倒角,倒角大于1.5 X 45,倒角一致。
6 冷却水嘴是否有进出标记,进水为IN ,出水为OUT IN、OUT后加顺序号,如IN1、OUT17 标识英文字符和数字是否大写(5/6 ),位置在水嘴正下方10mm处,字迹清晰、美观、整齐、间距均匀。
8 进出油嘴、进出气嘴是否同冷却水嘴,并在IN、OUT前空一个字符加G(气)、0(油)。
9 模具安装方向上的上下侧开设水嘴,是否内置,并开导流槽或下方有支撑柱加以保护。
10 无法内置的油嘴或水嘴下方是否有支撑柱加以保护。
11模架上各模板是否有基准角符号,大写英文DATUM字高5/16 〃,位置在离边10mm处,字迹清晰、美观、整齐、间距均匀。
12 各模板是否有零件编号,编号在基准角符号正下方离底面10mm处,要求同11号。
13 模具配件是否影响模具的吊装和存放, 如安装时下方有外漏的油缸、水嘴、预复位机构等,应有支撑腿保护。
14 支撑腿的安装是否用螺丝穿过支撑腿固定在模架上,或过长的支撑腿车加工外螺纹紧固在模架上。
15 模具顶出孔是否符合指定的注塑机, 除小型模具外, 原则上不能只用一个中心顶出(模具长度或宽度尺寸有一个大于500mm时),顶出孔直径应比顶出杆大5-10mm16 定位圈是否可靠固定(一般用三个M6或M8的内六角螺丝),直径一般为C 100或C 150mm高出顶板10mm如合同有特殊要求,按全同。
模具制作的验收标准
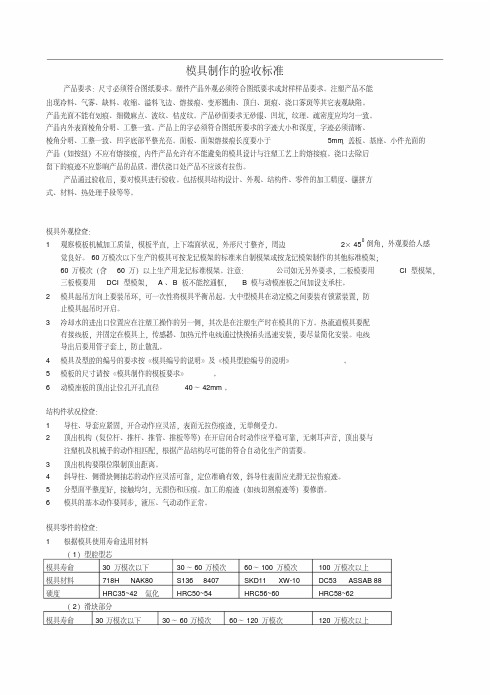
模具制作的验收标准产品要求:尺寸必须符合图纸要求。
塑件产品外观必须符合图纸要求或封样样品要求。
注塑产品不能出现冷料、气雾、缺料、收缩、溢料飞边、熔接痕、变形翘曲、顶白、斑痕、浇口雾斑等其它表观缺陷。
产品光面不能有划痕、细微麻点、波纹、桔皮纹。
产品砂面要求无砂眼、凹坑,纹理、疏密度应均匀一致。
产品内外表面棱角分明、工整一致。
产品上的字必须符合图纸所要求的字迹大小和深度,字迹必须清晰、棱角分明、工整一致、凹字底部平整光亮。
面板、面架熔接痕长度要小于5mm,盖板、基座、小件光面的产品(如按纽)不应有熔接痕,内件产品允许有不能避免的模具设计与注塑工艺上的熔接痕。
浇口去除后留下的痕迹不应影响产品的品质。
潜伏浇口处产品不应该有拉伤。
产品通过验收后,要对模具进行验收。
包括模具结构设计、外观、结构件、零件的加工精度、镶拼方式、材料、热处理手段等等。
模具外观检查:1观察模板机械加工质量,模板平直,上下端面状况,外形尺寸整齐,周边2×450倒角,外观要给人感觉良好。
60万模次以下生产的模具可按龙记模架的标准来自制模架或按龙记模架制作的其他标准模架;60万模次(含60万)以上生产用龙记标准模架。
注意:公司如无另外要求,二板模要用CI型模架,三板模要用DCI型模架,A、B板不能挖通框,B模与动模座板之间加设支承柱。
2模具起吊方向上要装吊环,可一次性将模具平衡吊起。
大中型模具在动定模之间要装有锁紧装置,防止模具起吊时开启。
3冷却水的进出口位置应在注塑工操作的另一侧,其次是在注塑生产时在模具的下方。
热流道模具要配有接线板,并固定在模具上,传感器、加热元件电线通过快换插头迅速安装,要尽量简化安装。
电线导出后要用管子套上,防止散乱。
4模具及型腔的编号的要求按《模具编号的说明》及《模具型腔编号的说明》。
5模板的尺寸请按《模具制作的模板要求》。
6动模座板的顶出让位孔开孔直径40~42mm。
结构件状况检查:1导柱、导套应紧固,开合动作应灵活,表面无拉伤痕迹,无单侧受力。
注塑模(塑料模)模具验收标准
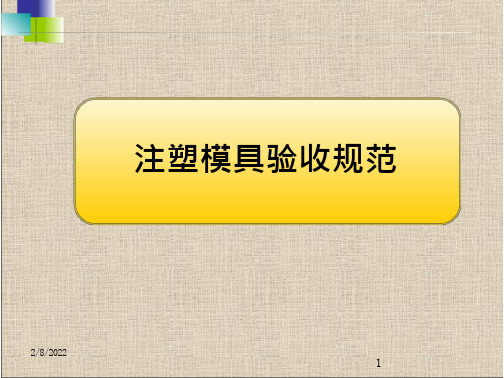
同意烧焊的除外,需注明指出) 6. 流道与入水位必须抛光,不能有作何的刀纹及火花纹。 7. 分模面流道需有排气,是否有? 8. 导套需有排气,是否有?
1
验收检查表
e) 一般CORE面需省光,无明显火花纹及加工刀痕,特殊要求的除
外。
f) 透明胶件或装配后的外观面符合设计要求。
1
注塑成型工艺
1. 模具在一定的注塑工艺条件范围内,应具有啤作的稳定性和工艺参 数调校的可重复性。
2. 模具啤作时注射压力,一般不应超过注塑机额定最大注射压力的 85%。
3. 模具啤作时的注射速度,其四分之三行程的注射速度不低于额定最 大注射速度的10%或超过额定最大注射速度的90%。
b) 顶针机构应保证灵活、可靠、不发生错误动作。 c) 顶针、司筒顶面非平面时,顶针、司筒应定位。
8. 底板上应均匀设置垃圾钉,垃圾钉高度应一致。
1
• 模具应具备结构
9. 4545或以上级大模应加设中托边,一套模中司筒数量达 到或超过16支应增设中托边。
10.流道直径、长度加工应合理,在保证成形质量的前提下 尽量缩短流程,减少断面积以缩短填充及冷却时间,同 时浇注系统损耗的塑料应最少。流道一般应设置冷料井 。
符合要求的标准尺寸? 9. 各顶针、司筒、顶块、斜顶及B板上等是否有打印有装配
对应序号?
1
验收检查表
16.防水“O”形槽及胶圈尺寸是否符合要求? 17防水胶圈尺寸是否正确?有无破损等不良现象? 18水路经过压力测试,是否漏水? 19所有的镙丝头都低于模板面 20所有的螺丝不可以有过加工、切短、等现象。 21模板需打上编号及模号,是否已加工好? 22带热嘴的必须要有接线盒,是否已好? 23水路必须有“IN”“OUT”标识,是否已标? 24所有超过50LBS(约20KG)的配件、模板都需有吊装孔 ,是否有? 25模具上所有的吊模孔需打印上螺纹大小标识,是否已 打印?
模具验收通过判定标准

3)顶杆端部固定台阶为标准尺寸,
不允许有打磨痕,顶杆台阶下部不允
许安装垫圈
顶杆及孔
17
4)顶杆尾部的防转销按标准制作
检查
5)顶杆及顶杆固定板的对应编号规
范、清晰、不混淆
6)顶杆与型腔固定孔的配合长度在 30mm~50mm 之间
7)型腔顶杆固定孔与顶杆的配合尺 寸保证设计要求,保证成型时不漏塑 料
1)导柱、导套同心
4
内滑块检查
利取件
2)内滑块不转动和上下摆动
导柱、导套
5
保证生产过程中导柱、导套不单边和拉伤
检查
冷却水和抽
6
工作时不漏水、不漏油
芯油检查
模具喷嘴检
7
保证成型时不漏塑料
查
脱模性好、不用脱模剂,顶出时制品不自由
8
脱模性检查
下坠
5 件连续成
9
成型正常、不发生异常
型检查
30 件连续成
10
成型正常、不发生异常
25
检查
中不变形
1)使用规定材质,并出具材质报告
模具材质
26 检查
2)模具型腔、型芯必须进行探伤,并
出具探伤报告
标准件检
符合技术要求规定的标准件种类、数
27
查
量
综合判定:
甲方:
乙方:
签字: 日期:
签字: 日期:
2、模具动态验收标准见表 2
工装模具验收报告书 (动态检查)
类别:模具
名称:
序 检查项目
号
2)皮纹无锈蚀、无针眼
芯表观
要求,保证制品脱模时皮纹不拉伤
质量检查
4)无皮纹模具型腔表面粗糙度在 0.2
pc模具验收标准
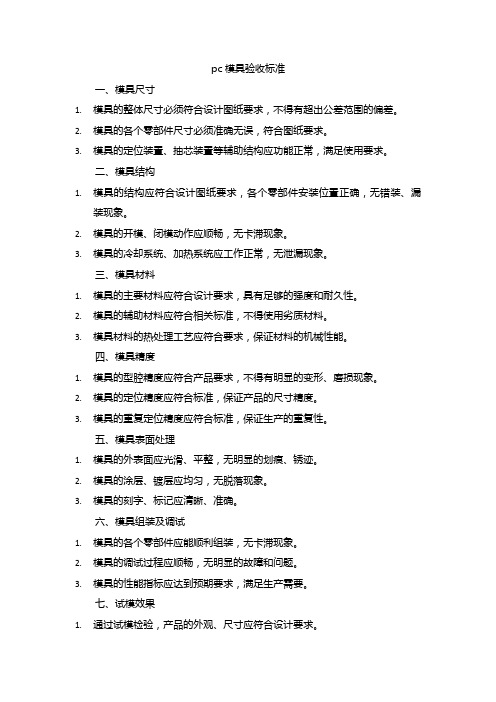
pc模具验收标准
一、模具尺寸
1.模具的整体尺寸必须符合设计图纸要求,不得有超出公差范围的偏差。
2.模具的各个零部件尺寸必须准确无误,符合图纸要求。
3.模具的定位装置、抽芯装置等辅助结构应功能正常,满足使用要求。
二、模具结构
1.模具的结构应符合设计图纸要求,各个零部件安装位置正确,无错装、漏
装现象。
2.模具的开模、闭模动作应顺畅,无卡滞现象。
3.模具的冷却系统、加热系统应工作正常,无泄漏现象。
三、模具材料
1.模具的主要材料应符合设计要求,具有足够的强度和耐久性。
2.模具的辅助材料应符合相关标准,不得使用劣质材料。
3.模具材料的热处理工艺应符合要求,保证材料的机械性能。
四、模具精度
1.模具的型腔精度应符合产品要求,不得有明显的变形、磨损现象。
2.模具的定位精度应符合标准,保证产品的尺寸精度。
3.模具的重复定位精度应符合标准,保证生产的重复性。
五、模具表面处理
1.模具的外表面应光滑、平整,无明显的划痕、锈迹。
2.模具的涂层、镀层应均匀,无脱落现象。
3.模具的刻字、标记应清晰、准确。
六、模具组装及调试
1.模具的各个零部件应能顺利组装,无卡滞现象。
2.模具的调试过程应顺畅,无明显的故障和问题。
3.模具的性能指标应达到预期要求,满足生产需要。
七、试模效果
1.通过试模检验,产品的外观、尺寸应符合设计要求。
2.模具的生产效率应满足生产计划的要求。
模具验收标准
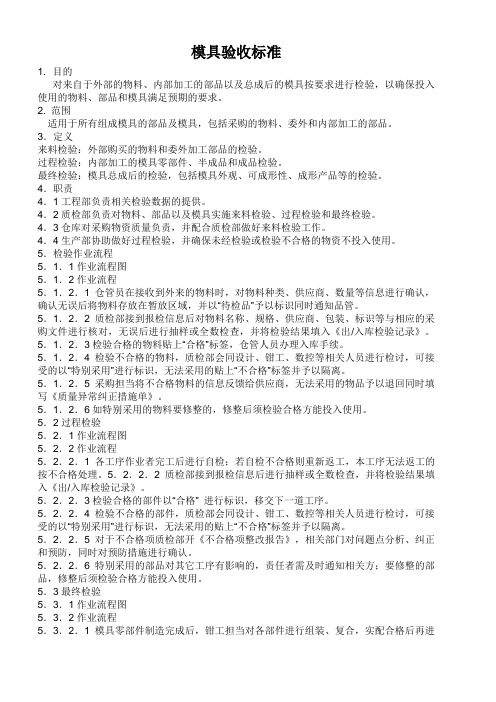
模具验收标准1. 目的对来自于外部的物料、内部加工的部品以及总成后的模具按要求进行检验,以确保投入使用的物料、部品和模具满足预期的要求。
2. 范围适用于所有组成模具的部品及模具,包括采购的物料、委外和内部加工的部品。
3.定义来料检验:外部购买的物料和委外加工部品的检验。
过程检验:内部加工的模具零部件、半成品和成品检验。
最终检验:模具总成后的检验,包括模具外观、可成形性、成形产品等的检验。
4.职责4.1工程部负责相关检验数据的提供。
4.2质检部负责对物料、部品以及模具实施来料检验、过程检验和最终检验。
4.3仓库对采购物资质量负责,并配合质检部做好来料检验工作。
4.4生产部协助做好过程检验,并确保未经检验或检验不合格的物资不投入使用。
5.检验作业流程5.1.1作业流程图5.1.2作业流程5.1.2.1仓管员在接收到外来的物料时,对物料种类、供应商、数量等信息进行确认,确认无误后将物料存放在暂放区域,并以“待检品”予以标识同时通知品管。
5.1.2.2质检部接到报检信息后对物料名称、规格、供应商、包装、标识等与相应的采购文件进行核对,无误后进行抽样或全数检查,并将检验结果填入《出/入库检验记录》。
5.1.2.3检验合格的物料贴上“合格”标签,仓管人员办理入库手续。
5.1.2.4检验不合格的物料,质检部会同设计、钳工、数控等相关人员进行检讨,可接受的以“特别采用”进行标识,无法采用的贴上“不合格”标签并予以隔离。
5.1.2.5采购担当将不合格物料的信息反馈给供应商,无法采用的物品予以退回同时填写《质量异常纠正措施单》。
5.1.2.6如特别采用的物料要修整的,修整后须检验合格方能投入使用。
5.2过程检验5.2.1作业流程图5.2.2作业流程5.2.2.1各工序作业者完工后进行自检;若自检不合格则重新返工,本工序无法返工的按不合格处理。
5.2.2.2 质检部接到报检信息后进行抽样或全数检查,并将检验结果填入《出/入库检验记录》。
最全面的注塑模具验收检验标准

最全面的注塑模具验收检验标准一、成型产品外观、尺寸、配合1、产品表面不允许缺陷:缺料、烧焦、顶白、白线、披峰、起泡、拉白(或拉裂、拉断)、烘印、皱纹。
2.、熔接痕:一般圆形穿孔熔接痕长度不大于5mm,异形穿孔熔接痕长度小于15mm,熔接痕强度并能通过功能安全测试。
3、收缩:外观面明显处不允许有收缩,不明显处允许有轻微缩水(手感不到凹痕)。
4、一般小型产品平面不平度小于0.3mm,有装配要求的需保证装配要求。
5、外观明显处不能有气纹、料花,产品一般不能有气泡。
6、产品的几何形状,尺寸大小精度应符合正式有效的开模图纸(或3D文件)要求,产品公差需根据公差原则,轴类尺寸公差为负公差,孔类尺寸公差为正公差,顾客有要求的按要求。
7、产品壁厚:产品壁厚一般要求做到平均壁厚,非平均壁厚应符合图纸要求,公差根据模具特性应做到-0.1mm。
8、产品配合:面壳底壳配合:表面错位小于0.1mm,不能有刮手现象,有配合要求的孔、轴、面要保证配合间隔和使用要求。
二、模具外观1、模具铭牌内容完整,字符清晰,排列整齐。
2、铭牌应固定在模脚上靠近模板和基准角的地方。
铭牌固定可靠、不易剥落。
3、冷却水嘴应选用塑料块插水嘴,顾客另有要求的按要求。
4、冷却水嘴不应伸出模架表面5、冷却水嘴需加工沉孔,沉孔直径为25mm、30mm、35mm三种规格,孔口倒角,倒角应一致6、冷却水嘴应有进出标记7、标记英文字符和数字应大于58、位置在水嘴正下方10mm处,字迹应清晰、美观、整齐、间距均匀。
9、模具配件应不影响模具的吊装和存放。
安装时下方有外露的油缸、水嘴,预复位机构等,应有支撑腿保护。
10、支撑腿的安装应用螺钉穿过支撑腿固定在模架上,过长的支撑腿可用车加工外螺纹柱子紧固在模架上。
11、模具顶出孔尺寸应符合指定的注塑机要求,除小型模具外,不能只用一个中心顶出。
12、定位圈应固定可靠,圈直径为100mm、250mm两种,定位圈高出底板10~20mm。
模具验收标准
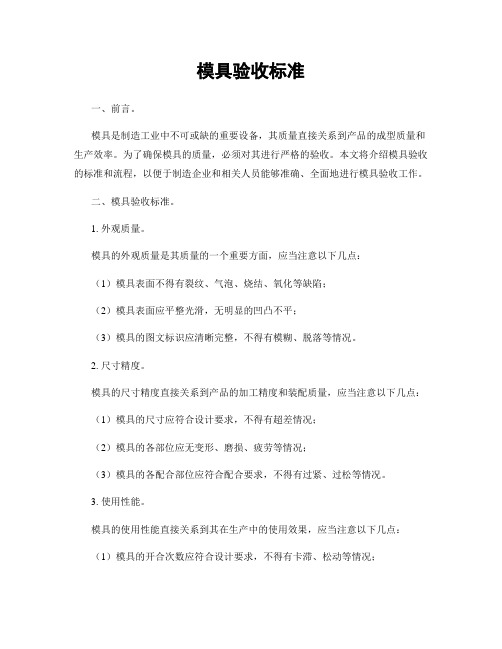
模具验收标准一、前言。
模具是制造工业中不可或缺的重要设备,其质量直接关系到产品的成型质量和生产效率。
为了确保模具的质量,必须对其进行严格的验收。
本文将介绍模具验收的标准和流程,以便于制造企业和相关人员能够准确、全面地进行模具验收工作。
二、模具验收标准。
1. 外观质量。
模具的外观质量是其质量的一个重要方面,应当注意以下几点:(1)模具表面不得有裂纹、气泡、烧结、氧化等缺陷;(2)模具表面应平整光滑,无明显的凹凸不平;(3)模具的图文标识应清晰完整,不得有模糊、脱落等情况。
2. 尺寸精度。
模具的尺寸精度直接关系到产品的加工精度和装配质量,应当注意以下几点:(1)模具的尺寸应符合设计要求,不得有超差情况;(2)模具的各部位应无变形、磨损、疲劳等情况;(3)模具的各配合部位应符合配合要求,不得有过紧、过松等情况。
3. 使用性能。
模具的使用性能直接关系到其在生产中的使用效果,应当注意以下几点:(1)模具的开合次数应符合设计要求,不得有卡滞、松动等情况;(2)模具的冷却、排气、脱模等功能应正常有效;(3)模具的使用过程中应无异常声响、异味等情况。
4. 安全性能。
模具的安全性能是其使用过程中必须重点关注的方面,应当注意以下几点:(1)模具的各部位应无锐利、毛刺等伤人的情况;(2)模具的安全保护装置应齐全有效,不得有缺失、损坏等情况;(3)模具的使用过程中应无漏电、漏油、漏气等危险情况。
三、模具验收流程。
1. 接收模具。
制造企业在接收模具时,应当对其进行全面的外观检查和尺寸测量,确保模具的外观质量和尺寸精度符合要求。
2. 使用性能测试。
制造企业在接收模具后,应当进行模具的使用性能测试,包括开合次数测试、冷却排气测试等,以确保模具的使用性能符合要求。
3. 安全性能检查。
制造企业在接收模具后,应当进行模具的安全性能检查,包括安全保护装置检查、漏电漏油检查等,以确保模具的安全性能符合要求。
四、结语。
模具验收是模具制造过程中的重要环节,其质量直接关系到产品的质量和生产效率。
注塑模具验收标准

执行步骤
一.新模验收,按(塑料模具质量验收鉴定报告)验收,并确认
1.定位圈标准 2.运水标准 3.顶针保护开关标准
1,试模时要以自动生产 状态验证。
4.模号雕刻/铭牌标准
2,试模异常时,注塑技
5.吊环孔标准
术人员需参与提供可量
6.模具防弹片标准 7.模胚要倒角
产解决方案。
8.垃圾钉标准 9.表面油蓝漆
1.模具铭牌上标识模具尺寸, 机台吨位,用料,腔数,产 品编号,产品名称等 2.热流道模具需标识组别,快 速识别.
5.吊环孔标准
吊环孔的位置应方便,安 全,平稳地吊起模具!
孔要倒角好,方便快捷装 吊环。
每块模板都要 做吊装螺丝孔
应在这俩个位 置设吊环孔。
6.防弹片标准
1.所有的模 具必须有防 弹片。 2.防弹片必 须装在模具 正面上方。
7.模胚要倒角
1.所有的模 具边沿要倒 角. 2.模板间要 有撬模角。
8.垃圾钉标准
顶针板后 要按尺寸 大小装相 应的垃圾 钉
9.表面油蓝漆
表面油蓝漆 (码模面不可
油漆)
灌咀,缩短 水口,深入 接近产品!
模具验收标准
其它项目按:(塑 料模具质量验收 鉴定报告) 验收。
XX的前进需要大家共同的努力, XX的发展离不开前端的点滴执行!
注塑模具验收标准
生产模具验收外观标准
1.定位圈标准 2.运水标准 3.顶针保护开关标准 4. 模号雕刻/铭牌标准 5.吊环孔标准 6.模具防弹片标准 7.模胚要倒角 8.垃圾钉标准 9.表面油蓝漆
1.定位圈标准
本厂直径规格: 124.8MM, 159.8MM
1.所有新模具必须有定 位圈。新模量产时,如 没有,不准量产!!
模具验收管理制度
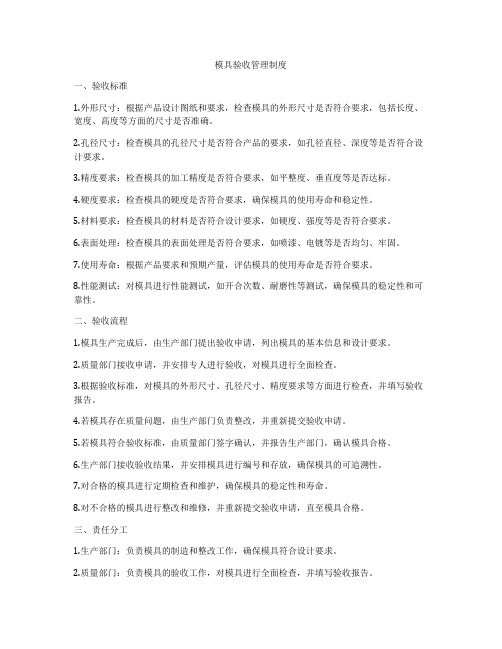
模具验收管理制度一、验收标准1.外形尺寸:根据产品设计图纸和要求,检查模具的外形尺寸是否符合要求,包括长度、宽度、高度等方面的尺寸是否准确。
2.孔径尺寸:检查模具的孔径尺寸是否符合产品的要求,如孔径直径、深度等是否符合设计要求。
3.精度要求:检查模具的加工精度是否符合要求,如平整度、垂直度等是否达标。
4.硬度要求:检查模具的硬度是否符合要求,确保模具的使用寿命和稳定性。
5.材料要求:检查模具的材料是否符合设计要求,如硬度、强度等是否符合要求。
6.表面处理:检查模具的表面处理是否符合要求,如喷漆、电镀等是否均匀、牢固。
7.使用寿命:根据产品要求和预期产量,评估模具的使用寿命是否符合要求。
8.性能测试:对模具进行性能测试,如开合次数、耐磨性等测试,确保模具的稳定性和可靠性。
二、验收流程1.模具生产完成后,由生产部门提出验收申请,列出模具的基本信息和设计要求。
2.质量部门接收申请,并安排专人进行验收,对模具进行全面检查。
3.根据验收标准,对模具的外形尺寸、孔径尺寸、精度要求等方面进行检查,并填写验收报告。
4.若模具存在质量问题,由生产部门负责整改,并重新提交验收申请。
5.若模具符合验收标准,由质量部门签字确认,并报告生产部门,确认模具合格。
6.生产部门接收验收结果,并安排模具进行编号和存放,确保模具的可追溯性。
7.对合格的模具进行定期检查和维护,确保模具的稳定性和寿命。
8.对不合格的模具进行整改和维修,并重新提交验收申请,直至模具合格。
三、责任分工1.生产部门:负责模具的制造和整改工作,确保模具符合设计要求。
2.质量部门:负责模具的验收工作,对模具进行全面检查,并填写验收报告。
3.管理部门:负责制定和完善模具验收管理制度,确保验收流程的有效实施。
4.员工:负责遵守模具验收管理制度,确保模具的质量和稳定性。
四、改进措施1.定期开展模具的培训和技术交流,提高员工的技术水平和质量意识。
2.建立模具质量档案,对每一件模具进行编号和记录,实行全程跟踪管理。
模具验收标准

模具验收标准一、前言。
模具是制造工业中非常重要的一种生产工具,它的质量直接关系到产品的成型质量和生产效率。
因此,模具的验收是非常重要的环节,只有通过严格的验收,才能确保模具的质量达到要求,从而保证产品的质量和生产效率。
本文将介绍模具验收的标准和要求。
二、验收标准。
1. 外观质量。
(1)模具表面应无刮痕、裂纹、气泡、凹凸不平等缺陷,应保持清洁光滑。
(2)模具的尺寸应符合设计要求,无变形、偏差等情况。
(3)模具的各部件应安装牢固,无松动、脱落等现象。
2. 加工精度。
(1)模具的加工精度应符合设计要求,各零件之间的配合间隙应符合标准。
(2)模具的表面粗糙度应符合要求,不得影响产品的表面质量。
3. 使用性能。
(1)模具应能够正常使用,无卡滞、卡死、卡模等现象。
(2)模具的使用寿命应符合设计要求,能够满足生产需求。
4. 安全性能。
(1)模具应符合安全生产的要求,无锋利边缘、突出物等危险因素。
(2)模具的使用应符合相关安全操作规程,能够保障操作人员的安全。
5. 其他要求。
(1)模具的材料应符合设计要求,无掺杂、夹杂等缺陷。
(2)模具的标识应清晰完整,包括生产厂家、生产日期、型号等信息。
三、验收流程。
1. 准备工作。
(1)准备验收所需的工具和设备,包括千分尺、游标卡尺、平行度尺等。
(2)准备验收所需的文件和资料,包括设计图纸、加工工艺文件等。
2. 验收过程。
(1)对模具的外观进行检查,包括表面质量、尺寸等。
(2)对模具的加工精度进行检测,包括尺寸、配合间隙等。
(3)对模具的使用性能进行测试,包括装卸模具、模具运行测试等。
(4)对模具的安全性能进行评估,包括危险因素、安全操作规程等。
(5)对模具的材料和标识进行检查,确保符合要求。
3. 验收结论。
(1)根据验收结果,对模具的质量进行评定,包括合格、不合格等结论。
(2)对不合格的模具,提出整改要求和建议,确保模具质量达标。
四、总结。
模具验收是保证模具质量的重要环节,只有严格按照验收标准进行检验,才能确保模具的质量和使用效果。
模具验收标准

11 各模板在基准边的天侧打有零件编号
12 冷却水嘴用塑料快插水嘴,φ10或φ12管,规格为G1/4"或G3/8"
13 冷却水嘴的安装做沉孔,水嘴头部凹进外表面不超过3MM
14 沉孔的大小一致,直径为φ28,孔外一周倒角,并且倒角一致
15 冷却水嘴标有进出标识IN、OUT,并在标识后加序利号,如:IN1、OUT1
结构 及制 51 一模数腔的制品要有头号
做 52 需与前模碰穿的镶件、镶针要做定向并插入前模里面
53 产品上标识、日期码、材料号、商标按我司要求制做 54 模具型腔喷防锈油 55 所有滑动部件涂黄油 56 浇口套进料口用黄油堵死 57 备件、易损件齐全并附明细 1 模具2维图纸1:1打印,二维和三维全部文件刻碟
28 滑块抽芯用斜导柱时,斜导柱的角度比滑块锁紧面的角度小2到3度
29 滑块的滑动距离大于抽芯距2-3MM,斜顶类似
30 斜导柱装配不能有松动
31 斜边R角要标准,滑块的斜边孔倒角均匀
32 滑块的压条做L形,材料2510,硬度HRC54-56
33
滑块底部做有耐磨块,滑块的锁紧面做耐磨块,耐磨块材料2510,硬度 HRC54-56
26 模板:A、B板间有1MM的间隙
27 导套孔的底部做排气槽
28 顶针板底部停止销(垃圾钉)数量按客户要求
29 三板模的面板与水口板之间要有弹弓或弹弓胶,以辅助开模
30 三板模的水口板滑动顺利,水口板易拉开
1 模具的内模设计合理,没有尖角等不合理的情况
结构 2 模具材料按我司《模具制做规范书》的要求
9 模具材料要有材质证明和热处理证明
10 模具非料位处的利角全部有倒角并且倒角均匀
11 所有螺丝符合图纸要求,没有锯短、没有滑牙
冲压件模具预验收标准(1)

目视 间隙规测量0.03mm以下
目视,手摸 补焊光顺,横向裂纹无,纵向裂纹100 mm内允许3条(只补焊处允许)
目视,直尺 自由状态,贴合间隙小于0.02mm/与基体或背托贴合率大于90%
目视,直尺 有防转措施,冲头固定板与安装面无间隙,至少两处有定位销
目视,角度 尺
刀口尖角不得大于75度,
目视,直尺 必须冲头同时接触
目视 不得多于1片,且必须有螺栓固定
目视 与背托无间隙,与安装面贴合率90%良好;标准件使用率100%。
目视 端头导入R角光顺,大小为R10,滑动面240#以上油石抛光,无刮伤、拉伤。
卷尺 涂红丹着色80%以上,垂直度间隙 符合要求,Leabharlann 目视 大于0.6倍压料板长度
目视,卷尺 必须等高,保证同时吃入,有导柱时,导板必须先吃入15mm
刃口的材质和硬度
29
刃口吃入量
30
接刀缝
31
镶块补焊
32 镶 镶块与安装底面
33
块 与
标准异形冲头
34 刀 刀口形状 口
35 冲 对冲时
36 头 冲孔与整形
37
翻孔与整形
38
定位销
39
定位销
40
标准圆冲头
41
材质和编号刻印
42
起吊装置
43
螺钉与螺钉过孔
镶块、冲头固定座
44
与安装底面
45
清根
46
压边圈
56
安全螺钉
57
限位螺钉
58
侧销
59
侧销
60
工作侧销
61
安全侧销
62
弹簧
63
弹簧
64
新开模具要求与验收标准

新开发模具要求与验收标准一、五金模具开发要求及验收标准1.在开模之前承制厂商应对本公司提供的图纸与要求作一个全面的审核,在审核过程中发现图纸有误或在制造过程中难以达到要求的,承制厂商应向出图方提出并作修改,保证核对无误。
2.模具在制造过程中不能修改图纸上的任何尺寸及说明﹝如有变动需经出图方同意并签名后方可变动﹞。
3.新开模具必须将模具名称,模具编号,制模厂商厂名及制模日期打刻于模具正侧面.容易看到之位置,字体高度不得小于35mm,打刻形式如下:A模具名称B.模具编号C.厂商厂名。
D.制模日期4.新开模具如无工程变更不能有烧焊或补焊现象。
5.模具制造完成后试模出的产品要完全符合图纸尺寸或样品。
6.模具需在厂外试模直到产品合格,并由研发、模房、冲压到厂商处看试模后才能拉回工厂试模,在厂内允许厂商试模三次,超过次数后向厂商收取RMB100元/次/工程试模费7.模具验收合格后,需将产品图,模具图电子图档一并交给本公司(五金模具之模具图必须有每一工程的图纸),电子图档如未提供,《试模报告书》将不予交给制模厂商。
8.制模厂商在送样五金件确认时必须将每一工序的产品送到。
9.产品合格试装报告发行后,工厂可为厂商办理首批60%的请款,在无异常顺利量产3000PCS,算模具合格后,(因订单量不足,则在6个月后,并厂商提供维护保证书后),工厂可为厂商办理第二次请款。
二、五金模具要求及验收标准(一)模具采用标准规格模板,所有模板倒3×45°斜角。
1.上下夹板应保证材料厚度为25mm以上,长度与宽度应与刃口一致,材质为45#钢。
2.上下模座应保证材料厚度为:上35mm,下40mm,长与宽应保证相对之位置,异柱不能靠刀口板太近(最小距离为:15mm)3.刀口模板厚度为30mm以上,长度与宽度保证与刃口最近距离50mm,材质SKD11,热处理硬度58~60HRC。
4.下料及冲孔模上下模板必须采用SKD11,折弯冲头可采用D2,冲头热处理比下模低2~3HRC,为56~58HRC。
塑料注塑模具验收与标准

塑料注塑模具验收标准BP-ZL-006版本号:01目的:为确保模具能生产出合格的产品,正常投入生产,保证模具生产使用寿命,满足产品设计的生产使用要求。
规范从产品质量、模具结构、注塑成型工艺要求等方面认可模具的标准,据此对模具质量进行评估;参照标准:GB/T12554—2006塑料注射模技术条件GB/T4169.1~4169.23—2006注射模零件GB/T12556—2006塑料注射模模架技术条件GB/T14486—2008塑料模塑件尺寸公差一、成型产品外观、尺寸、配合1.产品外观二、模具外观1.模具铭牌内容完整,字符清晰,排列整齐。
2.铭牌应固定在模脚上靠近模板和基准角的地方。
铭牌固定可靠、不易剥落3.冷却水嘴应选用塑料块插水嘴,顾客另有要求的按要求。
4.冷却水嘴不应伸出模架表面。
5.冷却水嘴需加工沉孔,沉孔直径为25mm、30mm、35mm三种规格,孔口倒角,倒角应一致。
6.冷却水嘴应有进出标记。
7.标记英文字符和数字应大于5/6,位置在水嘴正下方10mm处,字迹应清晰、美观、整齐、间距均匀。
8.模具配件应不影响模具的吊装和存放。
安装时下方有外露的油缸、水嘴,预复位机构等,应有支撑腿保护。
9.支撑腿的安装应用螺钉穿过支撑腿固定在模架上,过长的支撑腿可用车加工外螺纹柱子紧固在模架上10.模具顶出孔尺寸应符合指定的注塑机要求,除小型模具外,不能只用一个中心顶出。
11.定位圈应固定可靠,圈直径为100mm、250mm两种,定位圈高出底板10〜20mm。
顾客另有要求的除外。
12.模具外形尺寸应符合指定注塑机的要求。
13.安装有方向要求的模具应在前模板或后模板上用箭头标明安装方向,箭头旁应有"UP”字样,箭头和文字均为黄色,字高为50mm。
14.模架表面不应有凹坑、锈迹、多余的吊环、进出水汽、油孔等以及影响外观的缺陷。
15.模具应便于吊装、运输,吊装时不得拆卸模具零部件,吊环不得与水嘴、油缸、预复位杆等干涉。
- 1、下载文档前请自行甄别文档内容的完整性,平台不提供额外的编辑、内容补充、找答案等附加服务。
- 2、"仅部分预览"的文档,不可在线预览部分如存在完整性等问题,可反馈申请退款(可完整预览的文档不适用该条件!)。
- 3、如文档侵犯您的权益,请联系客服反馈,我们会尽快为您处理(人工客服工作时间:9:00-18:30)。
研发工艺冲压工艺北汽银翔汽车有限公司2014/5/30调试检查程序要点制件品质跟踪单编制要领( Panel Quality Follow Up Sheet 编制要领)1.项目名称,部件名称,制作人,制作日期在最初编制时记入。
2.部件的草图以单件状态做标记并以 ISO View编制为原则。
3 本管理表是真实文件,并其管理内容包括从制作方的调试到生产流水线调试的最终模具移管阶段, 项目结束之后,也应以品质记录依据做维持管理。
4.按品质问题点做分别记录的要领1) 单件 : -外观、尺寸及回弹等问题,需要做记录管理的后工序重要问题。
(单件成绩单中,一般问题用单件质量情况和单件成绩书做管理。
)-冲压品质管理部落实的品质问题。
2) 车身 : - 车身品质跟踪单上记录的问题中,被认定为单件问题的内容。
3) 涂,组: 涂装-组装 品质跟踪单问题,记录中认定为单件问题的内容。
4) 品管 : -品质管理部品质跟踪单上记录的问题中,被认定为单件问题的内容。
5.记录日期与领域无关以最初日期为准编制。
6. 改善日程以最终改善预期日程为准编制。
7.改善现况维持要领TTO 2阶段, PT1,PT2 各分2阶段, 总分为 6个阶段来做改善现况的信息管理。
8 制件品质跟踪单(.Panel Quality Follow Sheet),做为新车开发的综合性质量记录单,应该附加详细的质量内容,做为附件方式管理。
*附件内容可包括如下内容(建议包括所有有关品质记录的内容):单件成绩书、改善工作(结果)报告书、相关的详细内容或测定值、其它部门的质量跟踪单。
模具检查管理明细 ■制件草图冲压线尺寸工作台板调试报告书(A)机床压力(吨)调试压力(吨)后 左总重= 吨NO 问题&原因整改方案冲压设备设置条件模具重量 上 = 吨 下 = 吨NO.意见调试时间吨mm备注压边力kg/cm 2 kg/cm 2编制日期 :编制:落料规格落料材料顶杆数量.后 右前 左个mm气垫行程(C/H)行程(S)气垫压力 前 右 kg/cm 2 kg/cm 2工序数模具尺寸模具闭高编制日期 :产品编号车型制件名供应商C LC LC /HS制件草图12345612345678910111213141516落料重量17NO 调试日期冲压设备负责人组长部长181192203214225236242526272829材料厚度NO问题&原因对策计划意见数量模具尺寸(上/下)工序号模具高度闭合高度气垫高度气垫负载 成型力部件名称工序名称气垫行程模型调试报告书(式样B)落料尺寸模具重量(上/下)材料制作者:制作日:项目 :制件名称 :制件编号:制作方 :时期年月 日地点负责人(乙方)验收人(甲方)主管领导T0T1T2T3[适用范围]检查后模具技能,产品品质,安全方面无问题时便认定合格. ① 模具静动检确认明细适用于 GWM外包或承接的所有模具.② GWM下发给的模具制作方是外厂时,使用此检查明细.但承接模具情况时, 若收到使用者的检查规范,以收到的检查规范为基本,此检查明细作参考用.③ 由模具制作部署或外部制作厂应经常检查模具并将检查明细提供给 GWM 项目的有关负责人[检查时期和检查负责人]项目模具检查时期备注经常检查HT 要求时期模具制作进度现况全工程成型性确认DRAW 成型性成型品质及材料尺寸仅限拉延T1全工序模具制件 产品品质确认全工程T2样品制件生产时模具品质及产品品质全工程T3样品制件生产时模具品质及产品品质全工程(注) 评价调试验证, 和关联部署 GROUP一起在PRESS模具信赖性验证单上实施.[判定记号和内容]记号备注○OK ×NG/无该事项 无需检查CHECK NOT NECESSARY未INCOMPLETE未作业检查负责人 备注确认检查合格不合格英文内容(注)除模具静动检明细之外的另做测定,将测定结果记录在表格里制作方负责人北汽银翔汽车及制作方责任人北汽银翔汽车及制作方责任人北汽银翔汽车及制作方责任人北汽银翔汽车及制作方责任人模具动/静检明细静动检明细(拉延)○,□,×,/,未 标记, 空栏填写测定值自检成型性确认1次立会2次立会■ 适合性1.模具定位(1) 模具闭高是否符合技术协议?(必须确认技术协议)(1)设计值mm测定值mm(2) 模具装配位置及形状是否和图纸一致?(2)(3) U型槽尺寸是否按图纸加工的→A -1(3)(4) 自动快夹固定时,快夹和模具是否有干涉?(4)A B60 +1 Min 120450 750 1050 1350 1650AB①静动检明细(拉延)○,□,×,/,未 标记, 空栏填写测定值自检成型性确认1次立会2次立会■ 适合性(5) 模具固定用键槽是否符合基准?(5)(6) 定位孔位置及尺寸记入(图面值,实际测定值记录)(6)(7)(7) 气垫位置确认及行程的干涉与否确认在机械内部缓慢提升顶杆并确认与模具之间的干涉.(静式检查时再确认干涉与否) (S: mm, C/H : mm)ASEC A-AA 型详图C /HS静动检明细(拉延)○,□,×,/,未 标记, 空栏填写测定值自检成型性确认1次立会2次立会■ 适合性2.导向1) 导向,耐磨板①导向腿的间隙是否在标准之内? 红铅(80%) 或以间隙定料板(0.08mm以下)确认①②导向腿部直角度是否在 0.03/150mm 以内(确认是否红铅80%以上)②③导向板的滑动部位是否有擦伤,拉毛等现象?(擦伤面积在全面积的5%之内& 深度在 1mm 以内)③ ④耐磨板的下端是否设计挡墙?④⑤滑动终端倒角是否做了R5处理?3.顶料器①吊耳规格是否适合(允许重量基准- - 图纸确认)①上模重量下模重量总重量測定値②③ 上/下模的钢丝绳接触部(正常/反转时) 是否加工成R20以上?②③ ④⑤上/下模的钢丝绳路径上(正常/反转时)是否发生因突出形状的干涉?④⑤ ⑥模具悬挂平衡是否良好? (提升时倾斜度要在定位孔部基准50㎜以内)⑥⑦⑦起吊棒是否按标准(环型 &无焊接翻边类,熟知图纸内容)4. 气缸驱动部 (顶料器,排放器,快夹)①提升样是否和图纸一样(行程记录 : mm)① ②气缸和顶料器的连接部位是否设有防止松懈的装置?②③④⑤①( )30静动检明细(拉延)○,□,×,/,未 标记, 空栏填写测定值自检成型性确认1次立会2次立会■ 适合性5.结构技能①型面打磨面是否确保落料面积以上(落料尺寸 + 10 or 15mm)① ②拉延筋不必要时,原有的拉延筋槽是否填平?② ③压边圈的运行是否良好?(不能发生因自重下滑或擦伤等情况)③ ④型面上平衡块的调整薄垫片是否在1个之内,并薄垫片的尺寸是否适当?④ ⑤调整块是否和图纸一样设置?⑤ ⑥顶杆坐面是否有脱离正位置的情况? (要求2/3以上接触)⑥ ⑦铸件上是否有破裂或孔?⑦⑧⑨6. 电气装置① 送料有误检测装置是否按规定适用?①NO.制作方12345②③④⑤电线标准线卡插头部件名限位开关电线连接器OPERATIONLIMITMISS FEED附录4-模具验收标准.xls-静动态检查明细-拉延2(15)② 2个系统以上AIR配管是否区分标记?② ③ AIR软管是否区分输入(MALE)/输出(FEMALE)配管? ④配管是否有弯曲的地方?③⑤AIR软管配管是否按气缸的用途做成同一长度?④⑤⑥3.模具铭牌①②4. 涂装①①涂色是否以色料板为准?是否负荷涂色标准?②颜色定位板,吊耳,缓冲器套,③侧销(固定用 ),防护板挡块,平衡块,侧销红色顶料器,送料/取料装置缸体的输入端,废料滑槽背面防护板,废料排出器操作部位④⑤①装配位置是否符合技术协议? ②是否记载了记录内容?(上模重量,总重量等)5R 4/14黄色2.5R 8/13`色号黄色 2.5Y 8/13③④⑤⑤yellowgreen静动检明细 CHECK LIST(后工序)OP20OP30OP40■ 适合性自检1次2次3次自检1次2次3次自检1次2次3次1.模具固定(1) 模具闭高是否符合技术协议?(必须确认)(1)设计值测定值(2) 模具装配位置及形状是否和图纸一致?(2)(3) U型槽尺寸是否按图纸加工的?A -1(3)(4) 自动夹紧时,快夹和模具是否有干涉?(4)450 750 1050 1350 1650①AB静动检明细 CHECK LIST(后工序)OP20OP30OP40■ 适合性自检1次2次3次自检1次2次3次自检1次2次3次(5) 模具固定用键槽是否符合标准?(5)(6) 定位孔位置及尺寸记录(设计值,实测值记入)(6)(7)(7) 确认气垫位置及行程上的干涉在机械内部缓慢提升顶杆并确认与模具之间的干涉.(静式检查时再确认干涉与否) (S: mm, C/H : mm)AAC /HS修改自检1次2次3次自检1次2次3次自检1次2次3次2.导向1) 导向,耐磨板①导向板的间隙是和图纸一致? 红铅(80%) 或以塞尺(0.08mm以下)确认①②导向腿垂直度是否在 0.03/150mm之内?( 红铅 80% 以上确认)③导向腿的滑动部位是否有擦伤等现象?(擦伤面积在全面积的5%之内& 深度在 1mm 以内)②④耐磨板的下端是否设计托台?(擦伤面积在全面积的5%之内& 深度在 1mm 以内)⑤滑动导入端是否做了R5圆角?③④⑤3.提升①吊耳规格是否适当(允许重量基准)①上模重量下模重量总重量测定值①( )②③ 上/下模的钢丝绳接触部(正常/反转时) 是否加工成R20以上?②③④⑤上/下模的钢丝绳路径上 (正常/反转时)是否发生因突出形状的干涉?④⑤⑥模具悬挂平衡是否良好? (提升时倾斜度要在定位孔部基准50㎜以内)⑥⑦⑦起吊棒是否依照标准(环型 &无焊接翻边类,熟知图纸内容)4. 气缸驱动部①①提升量是否和图纸一致?(行程记录: mm)②②顶料杆和模具之间是否有干涉?③③运行是否良好?④⑤⑥5.构造检查①①镶块间间隙(0.1mm以内),挡墙面之间是否有缝隙? ②②聚氨脂的安全套在下死点和上模之间的缝隙是否2mm以上?③③上模使用定位销时,是否有防止下落措施(例.无头螺栓等)?④④铸件上是否有铸造缺陷?自检1次2次3次自检1次2次3次自检1次2次3次6. 压料芯静式1)(1)侧销和压料芯接触面的中心是否一致? (压料芯打开时肉眼确认)2)(2)压料芯的安全销在下死点上是否确保10mm的间隔?(压料芯打开时确认)3)(3)导向的滑动面上是否有刮伤等发生?4)(4)压料芯卸料螺栓是否松动?5)(5)卸料螺栓与压料芯是否干涉?6)(6)拆装压料芯时如需拆卸镶块,镶块应做顺序标记 (红色漆涂色)7)(7)是否有压料芯强度低的部位?8)(8)压料芯的防滑板螺栓是否有松动情况?9)(9)弹簧导向销是否松动?10)(10)弹簧坐面是否有不足的地方?11)(11)聚氨脂固定螺栓是否松动? 12)(12)聚氨脂压料芯是否设有脱离防止措施? (冲孔)13)(13)氮气弹簧的配管状态是否良好?14)(14)氮气弹簧控制器的位置是否和图纸一致?15)(15)压料芯提升时压料芯的平衡是否良好?动式(1)定料板的高度是否适当,位置是否良好?(导向形状及位置限定形状)(2)定料板的调整状态是否良好?1)(3)定料板是否和斜锲或压料芯有干涉?2)(4)取出时制件是否和模具有干涉部位 ?3)(5)制件的定位是否良好?(确认与形状的贴紧状态)4)(6)成型后制件是否有窜动? (以研合用基准孔确认)5)(7)压料芯管理面宽是否充分,是否有局部模具接触痕迹 ?6)(以红铅确认,管理面要确保充分的研合)7)(8)是否有修边或翻边刃口先行于压料芯的情况?8)(垂直修边, 侧修, 空中剪切部位,废料刀部位)9)(9)修边镶块和压料芯的间隙是否依照图纸? (0.3~0.8mm一般/外板0.3~0.5mm)10)(压料芯轮廓上擦伤等痕迹发生不可有)(10)压料芯的侧销接触同步是否均匀?(在冲压设备上死点用手转回做确认 )7. 电气装置①①是否装配了接近感应器安装支架②②是否装配了自动开关,是否有气缸配线③③各标准是否按图纸?④④电气接线箱是否按要求?⑤⑤是否有配线下垂或与废料,斜锲等有干涉的情况?⑥⑥下模压料芯的感应器配线是否可拆卸?⑦⑦感应器装配位置是否适当?静动检明细 CHECK LIST(后工序)○,□,×,/,未 标记, 空栏填写测定值OP20OP30OP40■ 安全性自检1次2次3次自检1次2次3次自检1次2次3次1. 安全①气缸离驱动部的安全间距是否大于 30mm 或在10mm以内?① ②模具外设置的气缸是否有防护板? ② ③斜锲返回用弹簧是否露出?③ ④用气缸驱动的斜锲限位块部位是否有防护板?④ ⑤重量10kg以上及不好取出的镶块是否设有吊环螺栓用螺纹孔?⑤ ⑥机械加工部位末端的倒角状态是否良好?⑥ ⑦废料滑槽末端是否做了R2~R5圆角?⑦ ⑧吊环螺栓(T型吊耳用螺栓) 用活栓部位是否设置平坦面?⑧ ⑨吊环螺栓(T型吊耳用螺栓)是否无干涉完整地装配?⑨2. 气动装置① 缸体和电气箱位置是否按图纸设置?① ②2个系统以上AIR配管是否区分做了标记?② ③空气软管是否区分输入/输出配管? ③ ④配管是否有死弯的地方?④ ⑤AIR软管配管是否按气缸的用途做成同一长度?⑤3.模具铭牌①装配位置是否适当?① ②是否记载了应记入内容?(上模重量,总重量等)②⑦⑧F E E D①①①④静动检明细 CHECK LIST(后工序)○,□,×,/,未 标记, 空栏填写测定值OP20OP30OP40■ 安全性自检1次2次3次自检1次2次3次自检1次2次3次4. 涂装:(1)涂色以北汽银翔涂色标准为准颜色定料板,吊耳,缓冲器套,侧销(固定用 ),防护板挡块,平衡块,侧销红色顶料器,送料/取料装置缸体的输入端,废料滑槽背面防护板,废料排出器操作部位`2.5R 8/13黄色2.5Y 8/13黄色5R 4/14色号部件名称项目A B○X未/OP10OP20OP30OP40OP50OP10OP20OP30OP40OP501键加工状态BAIC标准A 1模具导向间隙BAIC标准A 2闭合高度, 铸造结构筋厚度BAIC标准B 2模具导向间隙参数的有无有A 3定位孔, U-型槽标准书(位置,形状)BAIC标准A 3顶料器的运行正规运行A 4吊耳的适合性BAIC标准A 4制件和凸模的面接触无间隙B 5与自动快夹的干涉BAIC标准A 5斜锲和驱动器面接触各面80%以上B 6顶料器部位(铸件缺陷,尺寸)BAIC标准A 6斜锲的运行A 7标准件是否按规格?(各种零部件等)BAIC标准B 7活动冲头的运行A 8机械类的装配位置(定料板,铭牌,电箱)BAIC标准B 8浮料器的运行(KNOCK OUT)A 9模具平衡BAIC标准A 1拉延模保管时的安全间距A 102顶料器活动式定位板等的安全间距A 1成型安全程度(制件变薄率测定值A)25% 以内A 3上模斜锲的卸料螺钉有无A 2端拾器标准(进入槽,SP柱塞)BAIC标准B 4活动防位器合件部位,安全板的有无A 3柱塞式定位器标准(高度,标准)BAIC标准B 5锐角部位倒角A4顶料器提升位置和平衡(荷载不足)无倾斜度B 5确认板件是否卡住 上下模(连续)模具验证基准B NO验证项目DROP10OP20OP30OP40OP50重要度6废料下落 (连续 10发 信赖性)模具验证基准B 1加工荷载 (吨)7冲孔废料下落( " )模具验证基准B 2闭合高度(mm)8冲孔之后的小型废料是否散乱在工作台上.无(肉眼)C 3定位孔(间距)9废料滑槽标准(形状,技能)BAIC标准B 4模具 重量 上模/下模 (吨)10侧冲弹料 标准BAIC标准B 总重量(包括适配器)(吨)///11加工荷载M/C标准A厂家入库处未作业无该项重要度必须验证可行范围之内解决判定记号适合不适合NO验证项目适合基准判定(工序)分类适合基准判定(工序)适合性模具精度安定性重要度验证项目NO 分类生产性验证结果测定值重要度模具验收检查明细部件名称项目A B○X未/OP10OP20OP30OP40OP50OP10OP20OP30OP40OP50厂家入库处未作业无该项重要度必须验证可行范围之内解决判定记号适合不适合NO 验证项目适合基准判定(工序)分类适合基准判定(工序)重要度验证项目NO 分类重要度模具验收检查明细1/2项目制件名称制件编号工序确认阶段调试-1调试-2调试-3TRY/调试生产线调试-1检查者1 OK NG OK NG OK NG OK NG OK NG 2 OK NG OK NG OK NG OK NG OK NG 3 OK NG OK NG OK NG OK NG OK NG 4 OK NG OK NG OK NG OK NG OK NG 5 OK NG OK NG OK NG OK NG OK NG 6 OK NG OK NG OK NG OK NG OK NG 7 OK NG OK NG OK NG OK NG OK NG 8 OK NG OK NG OK NG OK NG OK NG 9 OK NG OK NG OK NG OK NG OK NG 10 OK NG OK NG OK NG OK NG OK NG 11 OK NG OK NG OK NG OK NG OK NG 12 OK NG OK NG OK NG OK NG OK NG 13 OK NG OK NG OK NG OK NG OK NG 14 OK NG OK NG OK NG OK NG OK NG 15OK NGOK NGOK NGOK NGOK NG废料检查明细1234567891013111215142/2PROJECT/项目制件名称制件编号工序确认阶段调试-1调试-2调试-3TRY/调试生产线调试-1检查者16 OK NG OK NG OK NG OK NG OK NG 17 OK NG OK NG OK NG OK NG OK NG 18 OK NG OK NG OK NG OK NG OK NG 19 OK NG OK NG OK NG OK NG OK NG 20 OK NG OK NG OK NG OK NG OK NG 21 OK NG OK NG OK NG OK NG OK NG 22 OK NG OK NG OK NG OK NG OK NG 23 OK NG OK NG OK NG OK NG OK NG 24 OK NG OK NG OK NG OK NG OK NG 25 OK NG OK NG OK NG OK NG OK NG 26OK NGOK NGOK NGOK NGOK NG废料处理履历管理检查清单1816171920212224262325※ 测定方式为制件切断之后用千分尺(POINT MICROMETER)测定¡à ö´ïÒ ìíí® : '02. 04. 08123456789101211附录4-模具验收标准.xls-变薄率(32)制作方 :项目工序制件名材料123判定材料123判定检查日检查者1 STEEL LAYOUT(UPR) 2镶块布置图(上模)34567891011镶块布置图 (下模)121314151617181920STEEL NO.钢号上 模下 模硬度检查成绩单材料硬度FCD600HRC 55以上GM241HRC 56以上SKD-11HRC 57以上HMD-1HRC 58以上ICD-5HRC 59以上模具厂家。