JIT精益生产(PPT221页)
合集下载
JIT的精益生产管理PPT课件

• Eliminate waste of all kinds in the production process
• Improve product quality • Identify inefficient processes
Thus, save millions of dollars!!
2
Origin of JIT
Year
13
Globalization contd.
Shippers and receivers expect faster, smaller and reliable transportation
Present scenario Inventory costs are low Transportation distances are far
personnel, or technology Massive software installations for supply chain and inventory
management, with dubious returns
17
Recommendations
At times increased inventory protects producers against unpredictable demand fluctuations and breakdown in the supply chain
16
JIT programs that have exceeded optimum level of inventory reduction may exhibit some
of the following symptoms
Have not resulted in anticipated financial gains, or initial gains have diminished or reversed
• Improve product quality • Identify inefficient processes
Thus, save millions of dollars!!
2
Origin of JIT
Year
13
Globalization contd.
Shippers and receivers expect faster, smaller and reliable transportation
Present scenario Inventory costs are low Transportation distances are far
personnel, or technology Massive software installations for supply chain and inventory
management, with dubious returns
17
Recommendations
At times increased inventory protects producers against unpredictable demand fluctuations and breakdown in the supply chain
16
JIT programs that have exceeded optimum level of inventory reduction may exhibit some
of the following symptoms
Have not resulted in anticipated financial gains, or initial gains have diminished or reversed
精益生产之准时化生产课件

案例二:某电子制造企业的准时化生产改进
总结词
该电子制造企业通过引入准时化生产管理方法,提高了生产效率和产品质量。
详细描述
该企业针对自身生产线特点,引入了准时化生产管理方法,通过优化生产流程、减少中间环节和降低 库存等方式,提高了生产效率和产品质量。同时,企业还注重引入先进的生产设备和工艺,提高了生 产自动化水平。
起源
准时化生产起源于20世纪50年代的日本丰田汽车公司。当时,丰田公司为了解 决资源短缺和满足市场需求,开始探索一种新的生产方式。经过多年的实践和改 进,最终形成了准时化生产的模式。
推广与发展
随着日本经济的崛起,准时化生产逐渐被其他企业所采用和推广。如今,准时化 生产已经成为全球许多制造业企业所采用的一种先进的生产管理方式。JIT的应用 范围已经不仅仅局限于制造业,还包括服务业、物流业等领域。
改进措施
针对分析结果制定改进措施,持续优化生 产过程。
员工参与
鼓励员工参与改进活动,激发员工的创新 精神和积极性。
跨部门合作
加强跨部门之间的沟通和合作,共同推进 生产过程的持续改进。
03
准时化生产的优势与挑战
准时化生产的优势
提高生产效率
通过减少浪费和过度生产,准时
化生产能够显著提高生产效率,
降低生产成本。
市场需求的变化可能导致生产和供应的不 稳定,影响准时化生产的实施。
设备故障与维护
设备故障可能导致生产中断,影响准时化 生产的连续性。
员工培训与技能
员工需要具备较高的技能水平和管理能力, 以适应准时化生产的需求。
供应链管理
准时化生产需要高效的供应链管理,以确 保原材料和零部件的及时供应。
如何应对挑战
05
JIT生产课件
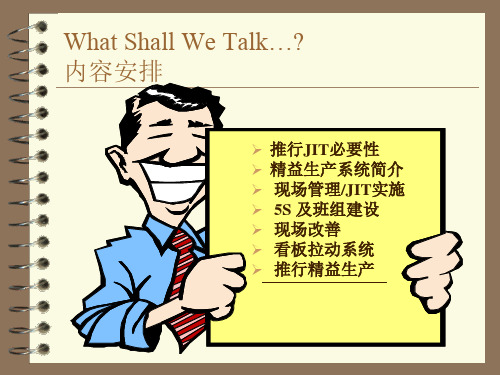
1.「生产过剩」 结果 「工程间在制品的浪费」 「制品仓库的在库浪费」2.「生产过剩」 ① 量方面的生产过剩 ② 先行生产所产生的生产过剩
生产过多过早的浪费
在制
在制
生产过多过早的浪费是因为先行生产或量方面生产过剩
1. 等待 原因 ① 工程编成 ; 1人担当1台机器 ② 流水线平衡 ; 作业分配的问题 ③ 工程困难的发生 ; 准备交替, 缺料, 不良, 故障 等2. 生产现场的 6 大困难 缺产品, 准备交替, 不良, 故障, 削切的工具交换, 承载量的不平衡
精益企业的竞争优势
生产时间减少 90% 库存减少 90% 生产效率提高 60% 到达客户手中的缺陷减少 50% 废品率降低 50% 与工作有关的伤害降低 50% ……否则,要检查一下你在哪里做错了! -《精益思想》, Womack & Jones
精益生产:通过消除企业所有环节上的不增值活动,来达到降低成本、缩短生产周期和改善质量的目的
JIT的基本思想:在必要的时刻、按必要的数量生产必要的产品(或零部件)
JIT起源
准时生产方式(Just In Time简称JIT),是日本丰田汽车公司在20世纪60年代实行的一种生产方式,1973年以后,这种方式对丰田公司渡过第一次能源危机起到了突出的作用,现在这一方式与源自日本的其它生产、流通方式一起被西方企业称为“日本化模式”。 在20世纪后半期,整个汽车市场进入了一个市场需求多样化的新阶段,1953年,日本丰田公司的副总裁大野耐一综合了单件生产和批量生产的特点和优点,创造了一种在多品种小批量混合生产条件下高质量、低消耗的生产方式即准时生产。JIT生产管理方式在70年代末期从日本引入我国,长春第一汽车制造厂最先开始应用看板系统 。90年代,例如第一汽车制造厂、第二汽车制造厂、上海大众汽车有限公司等企业,结合厂情创造性应用JIT,取得丰富的经验,创造了良好的经济效益。
工厂生产车间精益生产方式介绍员工JIT准时制生产培训PPT模板课件

目录
CONTENTS
主要原则
CARDINAL PRINCIPLE
主要原则
主要原则
基本内容
BASIC CONTENT
基本内容
基本内容
基本内容
项目实施
PROJECT IMPLEMENTATION
项目实施
管理实施
MANAGEMENT IMPLEMENTATION
管理实施
管理实施
工厂生产车间培训专用
基本概念
准时制生产方式(Just In Time简称JIT), 又 称 作 无 库 存 生 产 方 式 ( stockless production),零库存(zero inventories), 一个流(one-piece flow)或者超级市场生 产方式(supermarket production)。
物料需求计划是通过把生产环节与对物料的需求计划紧密地联在 一起,由此来降低需求的不确定性,从而降低库存水平。而准时 制运作强调对全部运作环节进行组织,使得各个运作环节在最恰 当的时间实施运作。看起来,定义是非常简单的,但是运作起来 的确不是一件轻松的事情。要想取得成功,企业需要对其内部的 态度和运作模式完全加以改变,同时还需要经过周密的计划和严 密控制、实施工作才行,这往往需要花费数年的时间。
JIT准时制 生产培训
汇报人:
基本特点
JIT的核心是追求一种无库存的生产系统,或使库 存达到最小的生产系统。为此而开发了包括“看 板””在内的一系列具体方法,并逐渐形成了一 套独具特色的生产经营体系。JIT以准时生产为出 发点,首先暴露出生产过量和其他方面的浪费, 然后对设备、人员等进行淘汰、调整,达到降低 成本、简化计划和提高控制的目的。
丰田公司的准时制采取的是多品种少批量、 短周期的生产方式,实现了消除库存,优化 生产物流,减少浪费目的。JIT生产方式的基 本思想是“只在需要的时候,按需要的量, 生产所需的产品”,也就是追求一种无库存, 或库存达到最小的生产系统。JIT的基本思想 是生产的计划和控制及库存的管理。所以, JIT生产模式又被称为“精益生产”。
精益生产JIT培训材料课件

交流交际
倾听能力
幽默能力
激励能力
精益生产的前世今生
精益生产的八大理念
卓越班组长的角色认知
班组长的管理原则及要点
素质要求
04
(9) 指导员工的能力:传授必要的知识及方法。(10)培养能力:部下的培养是管理人员的重要任务。(11)控制情绪的能力:当你成为一个管理者的时候,你的情绪已经不单单是自己私人的事情了,会影响到你的下属及其他部门的员工;而你的职务越高,影响力越大。
热爱
走动式管理
教育方法
实干作风
问题意识
精益生产的前世今生
指导员工
培养能力
控制情绪
精益生产的前世今生
精益生产的八大理念
卓越班组长的角色认知
班组长的管理原则及要点
素质要求
04
(12)自我约束的能力:了解自己的长处与短处,在有限的时间内有效地活用,努力增进自己的知识、人格、健康的能力。(13)概念化能力:把握事物的本质,发现问题、了解问题时不可缺少的能力。
自我约束
业务素质
职责方面
改善技术
育人技术
组织领导
精益生产的前世今生
精益生产的八大理念
卓越班组长的角色认知
班组长的管理原则及要点
团队
04
精益生产方式强调生产就如同音乐,有旋律(物流)、有节拍(均衡生产)、还有相互之间的和谐(标准作业),而这些是要靠一支训练有素、协调一致的乐队(团队)来保证的。精益生产方式的“团队”理念主要反映在有利于相助的设备布置形式、设立“接棒区”、“自主研究会”、与协作企业的长期合作关系以及追求全体效率等方面。
确保良品
消除不良
明确目的
各尽其职
精益生产的前世今生
JIT精益生产PPT
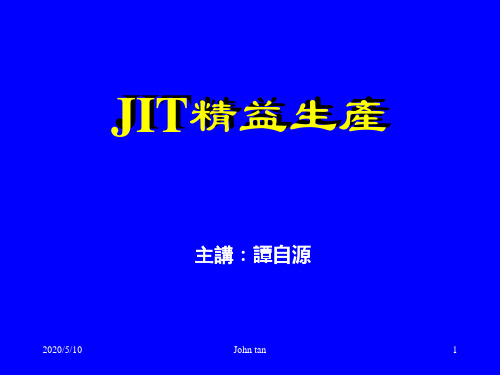
持續全員實踐
2018/7/21
John tan
11
3、精益生產追求的目標
7個“
零
”目標
☆ 零切換浪費 ☆ 零庫存 ☆ 零浪費 ☆ 零不良 ☆ 零故障 ☆ 零停滯 ☆ 零事故
12
2018/7/21
John tan
零目標
目的
現
狀
思考原則與方法
零 切換 浪費
多品種 切換時間長, 對應 切換後不穩定
7個“
JIT精益生產
主講:譚自源
2018/7/21
John tan
1
提要
1960年代開始,以豐田為代表的日本汽車製造 業通過實施JIT生產模式,以低成本、高質量的突出 優勢迅速佔領美國汽車市場,引發了美日之間長達 十年的汽車貿易戰。JIT——因其經營效率極限化被 美國學者讚譽為“精益生產”,並對人類的生產革 命產生了長遠影響。
利潤 實現
企業的使命實踐
市場 需求 企業 管理 產品 實現 顧客 滿意
2018/7/21
John tan
32
$
2018/7/21
增
值
工作的根本目的是給產品和服務 增加價值。 一切不增加對顧客和企業價值的 活動都是浪費。
John tan
33
3、企業常見的八種浪費
國內企業之大現狀: ☆ 現場混亂,插不進腳 ☆ 員工儀容不整,兩眼無光 ☆ 物料混放,標識不清 ☆ 設備故障不段,苟延殘喘 ☆ 人海戰術,加班加點但還是要待工待料
2018/7/21
John tan
6
不同力量主導的生產方式比較
項 目 生產企業主導 消費者主導
P(品種)
Q(品質)
少品種
JIT精益生产实务课件(PPT 75页)
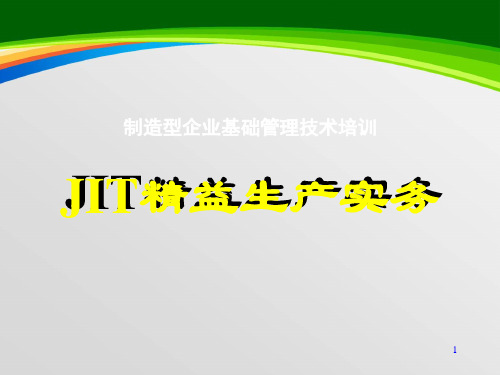
工厂整体布置
一笔画
从提高整体效率的目的出发,将 前后关联的生产线集中布置。
45
工厂整体布置
一笔画
Step4
Step3
整体上呈一笔画布置
Step2
将长屋型改为大通铺式
Step1
采用U字型生产线
由水平布置改为垂直布置
46
1 Step 由水平布置改为垂直布置
AAAAA
B
B
水平布置
(离岛式、鸟笼式
“粗流而慢”)
CCC
垂直布置
(“细流而快”, 满足多样少量)
AAAAA
B
B
B
B
B
CCCCC
47
2 Step 采用U字型生产线
11
成品
14 13 12
10 9
8
7
材料
1
3
4
2
56
(1)以U字型,依逆时针方向按工艺流程排列生产。
(2)入口和出口由同一作业者负责,能够以产距时
间按标准数量进行生产及管理,也便于补充生产。
从浑沌走向成熟的中国市场,价格战此起彼伏, 从产品上市到退出市场,其周期之短、降价之快已 今非昔比,成本能力成为企业的基础竞争能力。
4
提要
1960年代开始,以丰田为代表的日本汽车制造 业通过实施JIT生产模式,以低成本、高质量的突出 优势迅速占领美国汽车市场,引发了美日之间长达 十年的汽车贸易战。JIT——因其经营效率极限化被 美国学者赞誉为“精益生产”,并对人类的生产革 命产生了长远影响。
6、窄面原则 7、三不原则 8、成长带原则
录
15
(一)流线化生产线
1、流线化生产的意义 2、流线生产与批量生产的区别 3、流线化生产的八个条件 4、流线化生产的建立 5、设备布置的三不政策 6、有弹性的生产线布置
一笔画
从提高整体效率的目的出发,将 前后关联的生产线集中布置。
45
工厂整体布置
一笔画
Step4
Step3
整体上呈一笔画布置
Step2
将长屋型改为大通铺式
Step1
采用U字型生产线
由水平布置改为垂直布置
46
1 Step 由水平布置改为垂直布置
AAAAA
B
B
水平布置
(离岛式、鸟笼式
“粗流而慢”)
CCC
垂直布置
(“细流而快”, 满足多样少量)
AAAAA
B
B
B
B
B
CCCCC
47
2 Step 采用U字型生产线
11
成品
14 13 12
10 9
8
7
材料
1
3
4
2
56
(1)以U字型,依逆时针方向按工艺流程排列生产。
(2)入口和出口由同一作业者负责,能够以产距时
间按标准数量进行生产及管理,也便于补充生产。
从浑沌走向成熟的中国市场,价格战此起彼伏, 从产品上市到退出市场,其周期之短、降价之快已 今非昔比,成本能力成为企业的基础竞争能力。
4
提要
1960年代开始,以丰田为代表的日本汽车制造 业通过实施JIT生产模式,以低成本、高质量的突出 优势迅速占领美国汽车市场,引发了美日之间长达 十年的汽车贸易战。JIT——因其经营效率极限化被 美国学者赞誉为“精益生产”,并对人类的生产革 命产生了长远影响。
6、窄面原则 7、三不原则 8、成长带原则
录
15
(一)流线化生产线
1、流线化生产的意义 2、流线生产与批量生产的区别 3、流线化生产的八个条件 4、流线化生产的建立 5、设备布置的三不政策 6、有弹性的生产线布置
jit准时制和精益生产.pptx

16
一)、JIT的形成与发展
4、精益生产的初期实践 大野耐一开发了冲压中的快速换模技术,
采用了滚子来移动模具配以简单的调整机 构,并由生产工人来承担更换模具的工作。 在西方是用几百台压床来制造汽车的所有 零部件,而大野的这项技术能够用少数几 条冲压线生产整部汽车。
17
一)、JIT的形成与发展
4、精益生产的初期实践 在试验的过程中,大野意外地发现,这样小批量
• JIT概念 • JIT基本思想 • JIT的主要方法 • JIT推进的主要步骤 教学难点 • JIT的主要方法
3
13.1 JIT的基本思想与主 要方法
4
一、生产方式的演变
1、手工生产阶段 福特汽车公司于1902年成立,推出了福特
设计的第一批产品——既实用又便宜的车型, 售价仅为850美元,获得了巨大的成功。 1905年福特公司每季度的销售量达到了 5000辆,成为同行中的佼佼者,至此,福 特汽车的巨大成功仅仅是初露端倪,究竟是 什么样的汽车最符合市场的需要,仍是悬而 未决的问题。
5
一、生产方式的演变
1906年,福特公司推出了8种车型,其中 售价最低为1000美元,最高为2000美元, 这一决策带来了灾难性的结果,销售量猛 然下降,迫使福特公司重新转向薄利多销。 次年,公司降低了售价,销售量魔术一般 地回升,尽管当时全美经济萧条已经开始, 但1906年到1907年间,福特车的顾客之多 是前所未有。
6
一、生产方式的演变
1908年,福特制定了一个划时代的决策,宣 布从此致力于生产标准化,只制造较低廉的 单一品种。
福特开发了新产品——T型车。T型车全身上 下找不到一丝装饰或华而不实之处,百分之 百地实用。它去掉了所有附件,规格一致, 以850美元一辆出售。与当时其他类型的汽 车相比,T型车具有经久耐用、构造精巧和 轻盈便利的优点。
一)、JIT的形成与发展
4、精益生产的初期实践 大野耐一开发了冲压中的快速换模技术,
采用了滚子来移动模具配以简单的调整机 构,并由生产工人来承担更换模具的工作。 在西方是用几百台压床来制造汽车的所有 零部件,而大野的这项技术能够用少数几 条冲压线生产整部汽车。
17
一)、JIT的形成与发展
4、精益生产的初期实践 在试验的过程中,大野意外地发现,这样小批量
• JIT概念 • JIT基本思想 • JIT的主要方法 • JIT推进的主要步骤 教学难点 • JIT的主要方法
3
13.1 JIT的基本思想与主 要方法
4
一、生产方式的演变
1、手工生产阶段 福特汽车公司于1902年成立,推出了福特
设计的第一批产品——既实用又便宜的车型, 售价仅为850美元,获得了巨大的成功。 1905年福特公司每季度的销售量达到了 5000辆,成为同行中的佼佼者,至此,福 特汽车的巨大成功仅仅是初露端倪,究竟是 什么样的汽车最符合市场的需要,仍是悬而 未决的问题。
5
一、生产方式的演变
1906年,福特公司推出了8种车型,其中 售价最低为1000美元,最高为2000美元, 这一决策带来了灾难性的结果,销售量猛 然下降,迫使福特公司重新转向薄利多销。 次年,公司降低了售价,销售量魔术一般 地回升,尽管当时全美经济萧条已经开始, 但1906年到1907年间,福特车的顾客之多 是前所未有。
6
一、生产方式的演变
1908年,福特制定了一个划时代的决策,宣 布从此致力于生产标准化,只制造较低廉的 单一品种。
福特开发了新产品——T型车。T型车全身上 下找不到一丝装饰或华而不实之处,百分之 百地实用。它去掉了所有附件,规格一致, 以850美元一辆出售。与当时其他类型的汽 车相比,T型车具有经久耐用、构造精巧和 轻盈便利的优点。
《精益生产》PPT课件
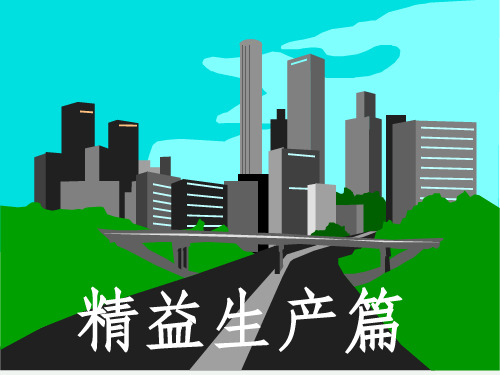
设备现场管理应用
在精益生产方式中,设备故障被视为无效劳动和浪费, 提出设备故障要向零进军,这就要求设备运行过程尽量 不发生故障,少发生故障。
实行全员维修和保养; 实行针对性预防检修; 实行改善性维修;
精益生产系统的五项原则
质量是 制造出来的
标准化
精益的 制造系统
持续改进
员工参与
短的制造周期
拉动式方法的特点:
坚持一切以后道工序需求出发,宁肯中断生产,也不搞超前超
1 量生产。拉动式生产的核心就是准时化,就是要求在需要的事
后,生产需要的产品和需要的数量,所以又把它称为准时化生 产(Just In Time)。
生产指令不仅仅是生产作业计划,而且还用看板进行为调节。
2 看板成为实施拉动式生产的重要手段。
看板来源于大野耐一从美国超级市场的启示。
拉动式方法 在生产制造过程中的具体运用
1 以市场需求拉动企业生产。
在企业内部,以后道工序拉动前道工序生产,以总装配拉动总
2 成装配,以总成装配拉动零件加工,以零件拉毛坯生产,用以
大幅度压缩在制品储备,消除无效劳动。
U型平面布置的“一个流”生产线; 多工序管理和多机床操作 成批轮番作业的生产线 快速换模技术,实现小批量多批次生产
jit以小批量生产为准则换模工作必须尽快完成消除浪费的方设计流程连接操作平衡工作站能力减小批量规减少安装换模时间2tqm全面质量管理尊重员工qcc小组合理化建议3稳定计划均衡计划不超过生产能力建立冻结区间指计划固定不弯一个时间区段4看板控制由后向前传送指令5与供应商紧密合作缩短提前期增加供货频率交货要及时保证质量可靠性6减少额外存货寻找其他区采用传送带运输机7改进产品设计产品标准化零件标准化及零件数减少改进过程设计产品质量期望jit七个前提条件61传统生产管理中的生产指令生产计划实际生产数量生产顺序表库存工序a工序b工序c库存完成生产指令计划生产数量与实际生产数量不同生产指令生产指令62jit生产计划实际生产数量生产顺序表看板工序a工序b工序c看板完成生产指令计划生产数量与实际生产数量相同63确定看板数量每个容器内数量64防止过量生产生产没有看板不能生产也不能运送目视管理看板必须附在实物上按照取下看板的顺序进行生产改善工具不能把不良品送往下一工序看板机能生产及运送的工作指令65生产系统
《精益生产完整》课件

日本电气公司
日本电气公司通过采用精益生产方法,成功减少了生产中的浪费和成本。
总结
精益生产是一种通过持续改进和消除浪费来提高效率和质量的生产管理方法。
通过建立精益文化、具体实践和借鉴成功案例,可以推动精益生产实施并提 升管理能力。
通过保持工作区域整洁、建立标准化工作流程和培养良好的工作习惯,可以 提高生产效能。
TPM维护 (Total Productive Maintenance)
TPM维护是一种通过持续和预防性的设备维护来保持设备正常运行的方法。 通过优化设备维护计划和提供员工培训,可以减少停机时间和提高设备的可靠性。
SMED单点换模
精益生产的优势
1 提高效率
通过优化流程和消除不必要的步骤,可以大幅提高生产ቤተ መጻሕፍቲ ባይዱ率。
2 降低成本
通过消除浪费,精益生产可以降低成本并提高利润。
3 提高品质
通过持续改进和关注细节,精益生产可以提高产品和服务的质量。
精益生产的历史
1
起源
精益生产起源于日本的丰田生产方式,旨在提高生产效率。
2
应用
随着时间的推移,精益生产的理念得到了广泛应用,跨越了不同行业和国家。
每个单元都专注于特定的任务,并与其他单元协同工作,以确保整个过程的 流畅性。
一次性流程设计
一次性流程设计旨在减少或消除生产过程中的非价值创造步骤,从而提高效 率和质量。
通过优化和简化流程,可以减少时间浪费、材料浪费和人力浪费,从而提高 生产效能。
产出平衡
产出平衡是指在不同工序之间达到良好的平衡,以确保不会出现过剩或短缺的情况。 通过平衡产出,可以最大限度地提高生产效率,并减少资源的浪费。
3
发展
精益生产不断演进和改进,适应了现代企业的需求和挑战。
日本电气公司通过采用精益生产方法,成功减少了生产中的浪费和成本。
总结
精益生产是一种通过持续改进和消除浪费来提高效率和质量的生产管理方法。
通过建立精益文化、具体实践和借鉴成功案例,可以推动精益生产实施并提 升管理能力。
通过保持工作区域整洁、建立标准化工作流程和培养良好的工作习惯,可以 提高生产效能。
TPM维护 (Total Productive Maintenance)
TPM维护是一种通过持续和预防性的设备维护来保持设备正常运行的方法。 通过优化设备维护计划和提供员工培训,可以减少停机时间和提高设备的可靠性。
SMED单点换模
精益生产的优势
1 提高效率
通过优化流程和消除不必要的步骤,可以大幅提高生产ቤተ መጻሕፍቲ ባይዱ率。
2 降低成本
通过消除浪费,精益生产可以降低成本并提高利润。
3 提高品质
通过持续改进和关注细节,精益生产可以提高产品和服务的质量。
精益生产的历史
1
起源
精益生产起源于日本的丰田生产方式,旨在提高生产效率。
2
应用
随着时间的推移,精益生产的理念得到了广泛应用,跨越了不同行业和国家。
每个单元都专注于特定的任务,并与其他单元协同工作,以确保整个过程的 流畅性。
一次性流程设计
一次性流程设计旨在减少或消除生产过程中的非价值创造步骤,从而提高效 率和质量。
通过优化和简化流程,可以减少时间浪费、材料浪费和人力浪费,从而提高 生产效能。
产出平衡
产出平衡是指在不同工序之间达到良好的平衡,以确保不会出现过剩或短缺的情况。 通过平衡产出,可以最大限度地提高生产效率,并减少资源的浪费。
3
发展
精益生产不断演进和改进,适应了现代企业的需求和挑战。
- 1、下载文档前请自行甄别文档内容的完整性,平台不提供额外的编辑、内容补充、找答案等附加服务。
- 2、"仅部分预览"的文档,不可在线预览部分如存在完整性等问题,可反馈申请退款(可完整预览的文档不适用该条件!)。
- 3、如文档侵犯您的权益,请联系客服反馈,我们会尽快为您处理(人工客服工作时间:9:00-18:30)。
不同力量主导的生产方式比较
项目 P(品种)
生产企业主导 少品种 多生产一些好
Q(质量) 防止投诉 不良不可避免 抽检为中心
C(成本) 按成本定价 成本+计划利润
D(交货期) 月单位交货 每月集中出货 S(安全) 生产优先 先保证出货, 安全嘛…… F(柔性) 以产定销 只有这个能 力……
消费者主导
2、现代生产组织系统
精益工厂 挑战七零极限目标
柔 性 生 产 系 统
TQM 精 益 质 量 保 证
生 产 与 物 流 规 划
TPM 全 面 设 备 维 护
产 品 开 发 设 计 系 统
现 代
IE 运 用
均 衡 化 同 步 化
全员现场5S活动 ·观念革新 ·全员改善活动
企业有效运营过程:
观念 薪酬 革新 体系
录 目
课程一 精益生产概论 课程二 认识浪费与效率 课程三 JIT技术 · 流线化生产
(一)流线化生产线 (二)流线化设备设计与调整 课程四 JIT技术 · 安定化生产 (一)人员安定化 (二)设备安定化
(三)质量安定化 (四)切换安定化 (五)现场安定化 课程五 JIT技术 · 平稳化生产 课程六 JIT技术 · 适时化生产 课程七 JIT技术 · 自主管理活动
JIT精益生产
主讲
提要
1960年代开始,以丰田为代表的日本汽车制造 业通过实施JIT生产模式,以低成本、高质量的突出 优势迅速占领美国汽车市场,引发了美日之间长达 十年的汽车贸易战。JIT——因其经营效率极限化被 美国学者赞誉为“精益生产”,并对人类的生产革 命产生了长远影响。
获得历史性机遇的中国制造业如何实现由粗放 管理向精细管理的飞跃?当我们还在为混乱的现场、 残缺的数据和蜗牛级的速度而痛苦万分的时候,丰 田的历程给了我们太多的“东方思考”。
4、精益生产实施过程全貌
易
缺
足
难
J I T ust n ime
适品 ·适量 ·适时
流线化 生产
安定化 生产
平稳化 生产
适时化 生产
5、精益生产实施案例
中间在库0,一位停整线停
案例 松下电器大坂收音机工厂组装线
自动插件
插件1 插件2 插件3
焊接
自动
设备
组装1 组装2
检测
包装
1臂间距
极少数自动设备
手工生产方式 完全按顾客要求 通用、灵活、便宜
粗略、丰富
懂设计制造 有较高操作技能
高 高 低 极少量需求
大批量生产方式
精益生产方式
标准化,品种单一 品种多样化、系列化
专用、高效、昂贵 柔性高、效率高
细致、简单、重复 不需要专业技能
较粗略、 多技能、丰富
多技能
高
低 高 物资缺乏、供不应 求
低 更低 更高 买方市场
目的 安全 保证
现状
忙于赶货疲于奔命, 忽视安全事故频发, 意识淡薄,人为事故多
思考原则与方法
· 安全第一 · 5S活动 · KYT危险预知训练 · 定期巡查 · 安全教育活动
· 安全改善活动
与传统的大批量生产相比,精益生产只需要一半的 人员、一半的生产场地、一半的投资、一半的生产周期、 一半的产品开发时间和少得多的库存,就能生产质量更 高、品种更多的产品。
《JIT》系列课程之一
精益生产概论
1、何谓精益生产方式 2、现代生产组织系统 3、精益生产追求的目标 4、精益生产实施过程全貌 5、精益生产案例
1、何谓精益生产方式
L P ean roduction 精益生产
1960年代开始,以丰田为代表的日本汽车制造业 通过实施JIT生产模式,以低成本、高质量的突出优势 迅速占领美国汽车市场,引发了美日之间长达十年的 汽车贸易战。
· 均衡化生产 · 设备流水化
零 浪费
降低 成本
“地下工厂”浪 费严重,似乎无 法发现、无法消 除
· 整体能力协调 · 拉式生产彻底暴露问题 · 流程路线图
零目标 目的
现状
思考原则与方法
7个“零”目标 零 不良
质量 保证
低级错误频发, 不良率高企, 批量事故多发, 忙于“救火”
· 三不主义 · 零缺陷运动 · 工作质量 · 全员质量改善活动 · 自主研究活动 · 质量改善工具运用
业务 流程
管理运营
高效 目标 组织 管理
管理 团队 创新 学习
有效 激励
现场 工作 统计 改善 5S 质量 系统 工具
精益生产之“心”、工具 持续全员实践
3、精益生产追求的目标
零 7个“
”目标 ☆ 零切换浪费
☆ 零库存
☆ 零浪费
☆ 零不良
☆ 零故障
☆ 零停滞
JIT——因其经营效率极限化被美国学者赞誉为 “精益生产”,并对人类的生产革命产生了长远影响。
J I T ust n ime
适品 ·适量 ·适时
JIT的基本思想是:只在需要的时候、按需要 的量、 生产所需的产品,故又被称为准时制生产、适时生产 方式、看板生产方式。
JIT的核心是:零库存和快速应对市场变化。 精益生产不断消除所有不增加产品价值的工作, 所以,精益是一种减少浪费的经营哲学。
多数手工作业 面向生产线
2H工位轮换 自主质量改进 (多技能)
案例 组装线员工技能评价表
姓名 张惠妹
插件1 插件2 插件3
△
●
○
自动 插件
●
焊接 组装1 组装2 检测
○
◎
◎
●
包装 ●
徐小凤 ●
☆ 零事故
零目标 目的
现状
思考原则与方法
7个“零”目标 零 切换 浪费
零
多品种 切换时间长, 对应 切换后不稳定
发现 大量库存造成成
· 经济批量 · 物流方式JIT · 生产计划标准化 · 作业管理 · 标准化作业 · 探求必要库存的原因
库存
真正 问题
本高、周转困难, · 库存规模的合理使用
且看不到真正的 问题在哪里
零 故障
生产 效率
故障频繁发生,
加班加点与待工待料一 样多
· 效率管理 · TPM全面设备维护 · 故障分析与故障源对策 · 初期清扫与自主维护
零 停滞
缩短 交货期长、延迟交货多 交货期 顾客投诉多,
加班加点、赶工赶料
· 同步化、均衡化 · 生产布局改善 · 设备小型化、专用化
7个“零”目标 零目标 零 事故
多品种 高质量 低价格
量大固然好,
品种也重要
构建不产生不良 的体系,全检或 零缺陷免检
将“干毛巾拧出 水”,消除浪费
快速交货 JIT
安全第一 安全第一无工伤 符合标准 符合技术法规 快速应变 随时满足
三种生产方式比较
项目 产品特点 设备和工装 作业分工 与作业内容 对操作工人
要求 库存水平 制造成本 产品质量 所适应的 市场时代