钢种与保护渣的关系
连铸工艺知识汇总高级工技师题库

河北钢铁杯职工职业技能大赛连铸工试题库(1309题)一、判断题1、钢中含磷高,会引起钢在低温时的韧性大为降低,引起“热脆”。
( )×2、冷却水喷咀的性能,不会影响铸坯质量和拉坯速度。
( )×3、事故冷却水的水量应不小于正常水量的1/5。
( )×4、适当降低过热度的浇注温度,可缩小铸坯中的柱状晶区,扩大等轴晶区。
( ) √5、所谓固相矫直是指铸坯进入矫直区域已全部凝固时进行的矫直。
( )√6、对涂料中间包要求耐热冲击性好,当从室温快速加热到1700℃时不炸裂,不剥落。
( )×7、对于大断面带液芯矫直的铸机,采用多点矫直比采用一点矫直好。
( )√8、二冷区冷却比按每吨铸坯消耗的冷却水体积衡量。
( )√9、钢水由液态变成固态的过程,必须满足一个条件,即一定的过冷度。
( ) √10、钢水在中包内的最佳停留时间为5min。
( )×11、钢液过冷度大,形核速度大于长大速度。
( )√12、连铸结晶器冷却水质要求比二冷水要求高。
( )√13、连铸坯按铸坯断面分类有方坯、板坯、园坯、异型坯。
( )√14、连铸坯常见的表面缺陷有鼓肚、扭曲、菱变。
( )×15、随着保护渣中碳含量的增加,保护渣的熔化速度加快。
( )×16、随着冶炼过程的进行,脱碳速度将越来越快。
( )×17、结晶器的铜板镀Ni是为了提高导热性能。
( )×18、铸坯振痕深度与结晶器振动负滑脱时间有关,负滑脱时间越短,振痕深度越深。
( )19、结晶器冷却水较二冷区冷却水压力低。
( )×20、沸腾钢比镇静钢的表面质量好,但成材率低。
( )×成份的含量不同。
( ) 21、刚玉、高铝和粘土质耐火材料的区别在于SiO2×22、钢包保护套管的作用是改善劳动条件。
( )×23、保护渣水份不会对保护渣的质量造成影响。
保护渣性能概述范文
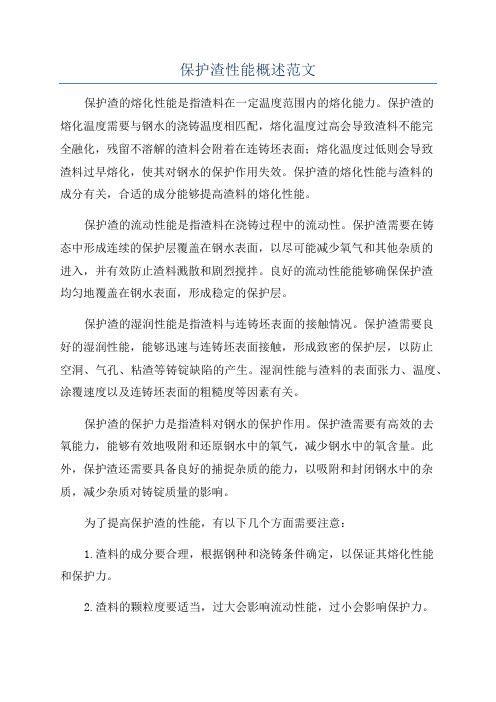
保护渣性能概述范文保护渣的熔化性能是指渣料在一定温度范围内的熔化能力。
保护渣的熔化温度需要与钢水的浇铸温度相匹配,熔化温度过高会导致渣料不能完全融化,残留不溶解的渣料会附着在连铸坯表面;熔化温度过低则会导致渣料过早熔化,使其对钢水的保护作用失效。
保护渣的熔化性能与渣料的成分有关,合适的成分能够提高渣料的熔化性能。
保护渣的流动性能是指渣料在浇铸过程中的流动性。
保护渣需要在铸态中形成连续的保护层覆盖在钢水表面,以尽可能减少氧气和其他杂质的进入,并有效防止渣料溅散和剧烈搅拌。
良好的流动性能能够确保保护渣均匀地覆盖在钢水表面,形成稳定的保护层。
保护渣的湿润性能是指渣料与连铸坯表面的接触情况。
保护渣需要良好的湿润性能,能够迅速与连铸坯表面接触,形成致密的保护层,以防止空洞、气孔、粘渣等铸锭缺陷的产生。
湿润性能与渣料的表面张力、温度、涂覆速度以及连铸坯表面的粗糙度等因素有关。
保护渣的保护力是指渣料对钢水的保护作用。
保护渣需要有高效的去氧能力,能够有效地吸附和还原钢水中的氧气,减少钢水中的氧含量。
此外,保护渣还需要具备良好的捕捉杂质的能力,以吸附和封闭钢水中的杂质,减少杂质对铸锭质量的影响。
为了提高保护渣的性能,有以下几个方面需要注意:1.渣料的成分要合理,根据钢种和浇铸条件确定,以保证其熔化性能和保护力。
2.渣料的颗粒度要适当,过大会影响流动性能,过小会影响保护力。
3.渣料的使用方法需要正确。
渣料要均匀涂覆在钢水表面,并保持一定的厚度,以确保良好的保护效果。
4.渣包维护要及时,定期清理渣包内的渣料残留物,避免二次污染。
综上所述,保护渣性能对于连铸坯质量的影响非常重要。
通过合理选择渣料成分、控制渣料颗粒度、正确使用渣料和及时维护渣包等措施,能够有效提高保护渣的性能,降低二次污染和缺陷率,提高铸锭质量,进而提升钢厂的生产效益。
保护渣简介

保护渣的性能测定一、保护渣的作用1)绝热保温向结晶器液面加固体保护渣覆盖其表面,减少钢液热损失。
由于保护渣的三层结构,钢液通过保护渣的散热量,比裸露状态的散热量要小10倍左右,从而避免了钢液面的冷凝结壳。
尤其是浸入式水口外壁四周覆盖了一层渣膜,减少了相应位置冷钢的聚集。
2)隔绝空气,防止钢液的二次氧化保护渣均匀地覆盖在结晶器钢液表面,阻止了空气与钢液的直接接触,再加上保护渣中碳粉的氧化产物和碳酸盐受热分解溢出的气体,可驱赶弯月面处的空气,有效地避免了钢液的二次氧化。
3)吸收非金属夹杂物,净化钢液加入的保护渣在钢液面上形成一层液渣,具有良好的吸附和溶解从钢液中上浮的夹杂物,达到清洁钢液作用。
4)在铸坯凝固坯壳与结晶器内壁间形成润滑渣膜在结晶器的弯月面处有保护渣的液渣存在,由于结晶器的振动和结晶器壁与坯壳间气隙的毛细管作用。
将液渣吸入,并填充于气隙之中,形成渣膜。
在正常情况下,与坯壳接触的一侧,由于温度高,渣膜仍保持足够的流动性,在结晶器壁与坯壳之间起着良好的润滑作用,防止了铸坯与结晶器壁的粘结;减少了拉坯阻力;渣膜厚度一般在50~200μm5)改善了结晶器与坯壳间的传热在结晶器内,由于钢液凝固形成的凝固收缩,铸坯凝固壳脱离结晶器壁产生了气隙,使热阻增加,影响铸坯的散热。
保护渣的液渣均匀的充满气隙,减小了气隙的热阻。
据实测,气隙中充满空气时导热系数仅为0.09W/m·K,而充满渣膜时的导热系数为1.2W/m·K,由此可见,渣膜的导热系数是充满空气时的13倍。
由于气隙充满渣膜,明显地改善了结晶器的传热,使坯壳得以均匀生长。
二、保护渣的构成1)液渣层当固体粉状或粒状保护渣加入结晶器后与钢液面相接触,由于保护渣的熔点只有1050℃~1100℃,因而靠钢液提供的热量使部分保护渣熔化,形成液渣覆盖层。
这个液渣覆盖层约10~15mm厚,它保护钢液不被氧化,又减缓了沿保护渣厚度方向的传热。
在拉坯过程中,结晶器上下振动。
不同钢种选择保护渣的要求
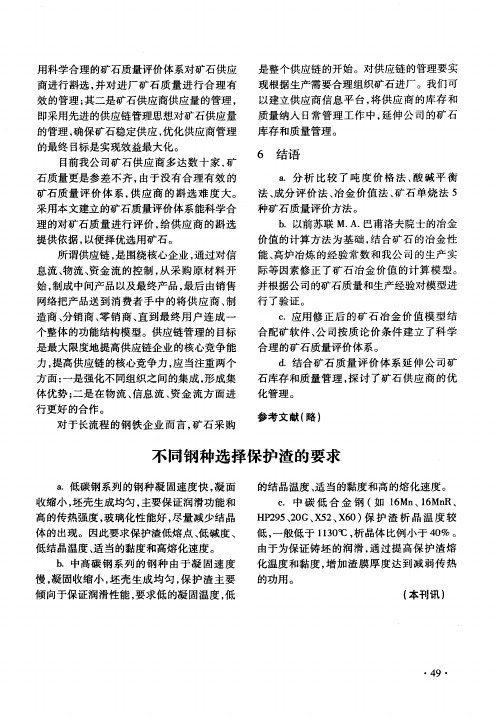
c .应用 修 正 后 的 矿 石 冶 金 价 值 模 型结 合 配矿 软件 、 司按 质 论 价 条件 建 立 了科 学 公 合 理 的矿石质 量评 价体 系 。 d 结 合 矿石 质 量 评 价 体 系 延 伸 公 司矿 . 石 库存 和质量 管理 , 讨 了矿 石 供应 商 的优 探
石 质量 更是 参差 不 齐 , 由于没 有 合 理 有效 的 矿 石质 量 评 价 体 系 , 应 商 的 斟选 难 度 大 。 供 采 用本 文建立 的矿石 质量评 价体 系能科 学合
理 的对矿 石质 量 进行 评 价 , 供 应 商 的斟 选 给
6 结语
a 析 比 较 了 吨 度 价 格 法 、 碱 平 衡 .分 酸 法 、 分 评 价 法 、 金 价值 法 、 石单 烧 法 5 成 冶 矿 种矿石 质量评 价方 法 。 b .以前苏联 M. . A 巴甫 洛夫 院士 的冶 金 价值 的计算 方 法为 基 础 , 合矿 石 的 冶 金性 结 能 、 炉冶炼 的经 验 常数 和 我公 司的 生 产 实 高
化温度和黏度 , 增加渣膜厚度达 到减弱传热 的功 用 。
( 刊讯 ) 本
・
4 ・ 9
低 结 晶温度 、 当 的黏度 和高熔化 速度 。 适
b .中高碳 钢 系 列 的 钢 种 由于 凝 固速 度
由于 为保证 铸 坯 的润 滑 , 过 提 高保 护 渣 熔 通
慢 , 固收缩 小 , 壳 生 成 均匀 , 护 渣 主要 凝 坯 保 倾 向于保 证润 滑性能 , 要求 低 的凝 固温 度 , 低
不同连铸工艺及品种的保护渣技术特征2
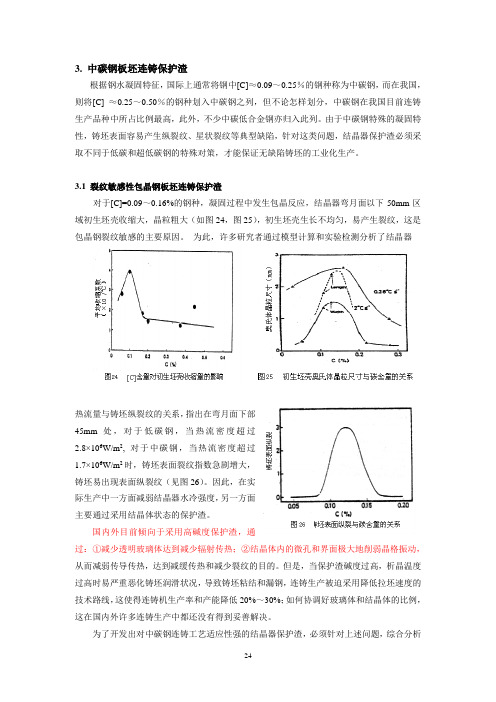
3. 中碳钢板坯连铸保护渣根据钢水凝固特征,国际上通常将钢中[C]≈0.09~0.25%的钢种称为中碳钢,而在我国,则将[C] ≈0.25~0.50%的钢种划入中碳钢之列,但不论怎样划分,中碳钢在我国目前连铸生产品种中所占比例最高,此外,不少中碳低合金钢亦归入此列。
由于中碳钢特殊的凝固特性,铸坯表面容易产生纵裂纹、星状裂纹等典型缺陷,针对这类问题,结晶器保护渣必须采取不同于低碳和超低碳钢的特殊对策,才能保证无缺陷铸坯的工业化生产。
3.1 裂纹敏感性包晶钢板坯连铸保护渣对于[C]=0.09~0.16%的钢种,凝固过程中发生包晶反应,结晶器弯月面以下50mm区域初生坯壳收缩大,晶粒粗大(如图24,图25),初生坯壳生长不均匀,易产生裂纹,这是包晶钢裂纹敏感的主要原因。
为此,许多研究者通过模型计算和实验检测分析了结晶器热流量与铸坯纵裂纹的关系,指出在弯月面下部45mm处,对于低碳钢,当热流密度超过2.8×106W/m2, 对于中碳钢,当热流密度超过1.7×106W/m2时,铸坯表面裂纹指数急剧增大,铸坯易出现表面纵裂纹(见图26)。
因此,在实际生产中一方面减弱结晶器水冷强度,另一方面主要通过采用结晶体状态的保护渣。
国内外目前倾向于采用高碱度保护渣,通过:①减少透明玻璃体达到减少辐射传热;②结晶体内的微孔和界面极大地削弱晶格振动,从而减弱传导传热,达到减缓传热和减少裂纹的目的。
但是,当保护渣碱度过高,析晶温度过高时易严重恶化铸坯润滑状况,导致铸坯粘结和漏钢,连铸生产被迫采用降低拉坯速度的技术路线,这使得连铸机生产率和产能降低20%~30%;如何协调好玻璃体和结晶体的比例,这在国内外许多连铸生产中都还没有得到妥善解决。
为了开发出对中碳钢连铸工艺适应性强的结晶器保护渣,必须针对上述问题,综合分析保护渣主要组份对结晶性能和玻璃化特性的综合影响情况,在此基础上,才能设计保护渣配方。
3.1.1 保护渣组成与结晶性能和玻璃化特性的基本关系为了弄清和明确保护渣组份对其结晶行为的影响规律,本研究首先采用化学纯试剂配制渣样(见表16),采用旋转粘度计测试保护渣在1300℃下的粘度,并在降温条件下测试保护渣粘度--温度曲线关系。
结晶器保护渣
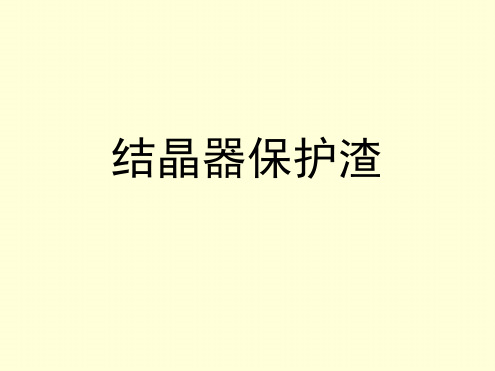
品种钢优特钢连铸保护渣技术
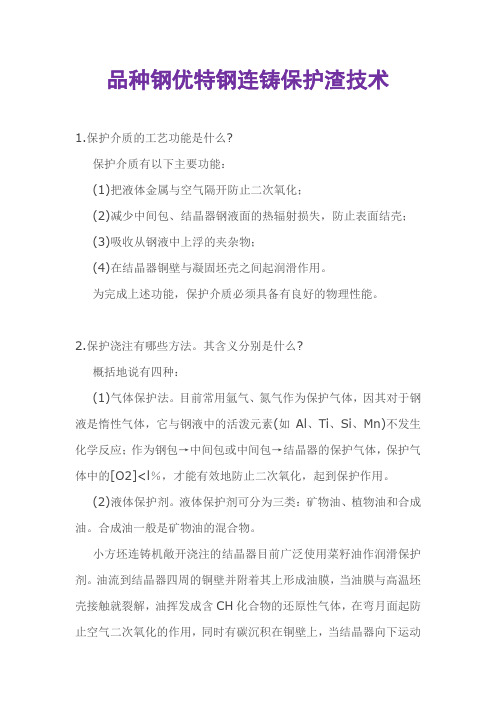
品种钢优特钢连铸保护渣技术1.保护介质的工艺功能是什么?保护介质有以下主要功能:(1)把液体金属与空气隔开防止二次氧化;(2)减少中间包、结晶器钢液面的热辐射损失,防止表面结壳;(3)吸收从钢液中上浮的夹杂物;(4)在结晶器铜壁与凝固坯壳之间起润滑作用。
为完成上述功能,保护介质必须具备有良好的物理性能。
2.保护浇注有哪些方法。
其含义分别是什么?概括地说有四种:(1)气体保护法。
目前常用氩气、氮气作为保护气体,因其对于钢液是惰性气体,它与钢液中的活泼元素(如Al、Ti、Si、Mn)不发生化学反应;作为钢包→中间包或中间包→结晶器的保护气体,保护气体中的[O2]<l%,才能有效地防止二次氧化,起到保护作用。
(2)液体保护剂。
液体保护剂可分为三类:矿物油、植物油和合成油。
合成油一般是矿物油的混合物。
小方坯连铸机敞开浇注的结晶器目前广泛使用菜籽油作润滑保护剂。
油流到结晶器四周的铜壁并附着其上形成油膜,当油膜与高温坯壳接触就裂解,油挥发成含CH化合物的还原性气体,在弯月面起防止空气二次氧化的作用,同时有碳沉积在铜壁上,当结晶器向下运动时,油或碳被挤入到坯壳与结晶器壁之间起润滑作用。
菜籽油用量一般为0.2—0.3L/t钢。
(3)固体保护剂。
中间包钢液面用覆盖剂(如碳化稻壳)或双层结构的覆盖渣,结晶器采用保护渣,均可防止二次氧化。
目前浇注优特钢品种均采用专用结晶器保护渣进行保护浇注。
(4)物理保护法。
连铸生产优特品种钢的过程中,采用较多的物理保护方法是:钢包→中间包采用A1一C质长水口,将长水口插入中间包熔池里100mm左右,机械地把注流与空气隔开,同时避免了注流冲击到中间包熔池面引起的钢水裸露和飞溅造成的二次氧化。
保护的关键是钢包滑动水口与长水口连接部位密封状况,该区域是空气最容易进入的部位。
因长水口内径大未被钢流充满,如同一个抽气泵把空气从接缝处吸入。
为防止在接缝处吸入空气,可采用下述办法解决:1)接缝处使用耐火纤维密封圈;2)接缝处使用金属环并通氩气;3)在接缝处直接通氩气;4)在接缝严密处通人氩气,使长水口顶部区形成正压区。
保护渣性能概述
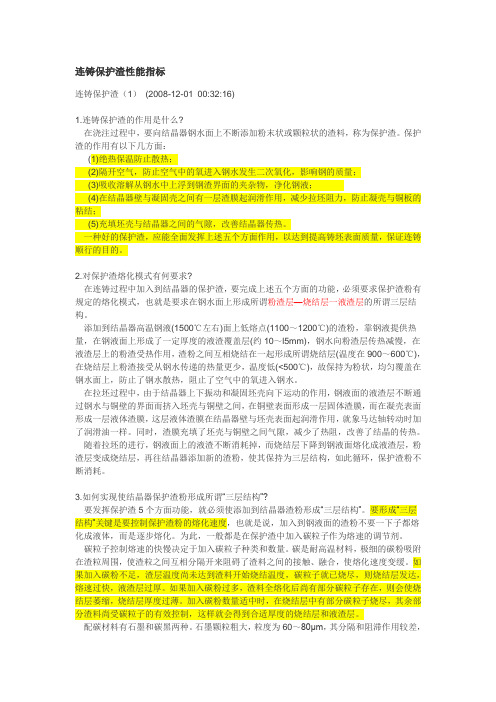
连铸保护渣性能指标连铸保护渣(1)(2008-12-01 00:32:16)1.连铸保护渣的作用是什么?在浇注过程中,要向结晶器钢水面上不断添加粉末状或颗粒状的渣料,称为保护渣。
保护渣的作用有以下几方面:(1)绝热保温防止散热;(2)隔开空气,防止空气中的氧进入钢水发生二次氧化,影响钢的质量;(3)吸收溶解从钢水中上浮到钢渣界面的夹杂物,净化钢液;(4)在结晶器壁与凝固壳之间有一层渣膜起润滑作用,减少拉坯阻力,防止凝壳与铜板的粘结;(5)充填坯壳与结晶器之间的气隙,改善结晶器传热。
一种好的保护渣,应能全面发挥上述五个方面作用,以达到提高铸坯表面质量,保证连铸顺行的目的。
2.对保护渣熔化模式有何要求?在连铸过程中加入到结晶器的保护渣,要完成上述五个方面的功能,必须要求保护渣粉有规定的熔化模式,也就是要求在钢水面上形成所谓粉渣层—烧结层一液渣层的所谓三层结构。
添加到结晶器高温钢液(1500℃左右)面上低熔点(1100~1200℃)的渣粉,靠钢液提供热量,在钢液面上形成了一定厚度的液渣覆盖层(约10~l5mm),钢水向粉渣层传热减慢,在液渣层上的粉渣受热作用,渣粉之间互相烧结在一起形成所谓烧结层(温度在900~600℃),在烧结层上粉渣接受从钢水传递的热量更少,温度低(<500℃),故保持为粉状,均匀覆盖在钢水面上,防止了钢水散热,阻止了空气中的氧进入钢水。
在拉坯过程中,由于结晶器上下振动和凝固坯壳向下运动的作用,钢液面的液渣层不断通过钢水与铜壁的界面而挤入坯壳与铜壁之间,在铜壁表面形成一层固体渣膜,而在凝壳表面形成一层液体渣膜,这层液体渣膜在结晶器壁与坯壳表面起润滑作用,就象马达轴转动时加了润滑油一样。
同时,渣膜充填了坯壳与铜壁之间气隙,减少了热阻,改善了结晶的传热。
随着拉坯的进行,钢液面上的液渣不断消耗掉,而烧结层下降到钢液面熔化成液渣层,粉渣层变成烧结层,再往结晶器添加新的渣粉,使其保持为三层结构,如此循环,保护渣粉不断消耗。
保护渣基础资料
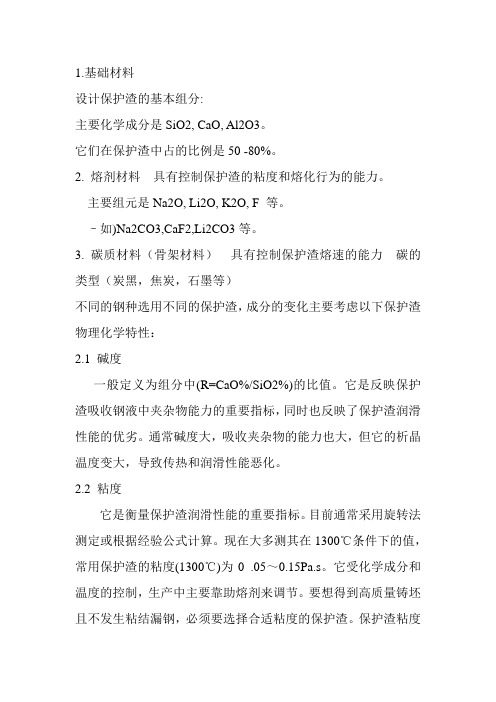
1.基础材料设计保护渣的基本组分:主要化学成分是SiO2, CaO, Al2O3。
它们在保护渣中占的比例是50 -80%。
2. 熔剂材料具有控制保护渣的粘度和熔化行为的能力。
主要组元是Na2O, Li2O, K2O, F 等。
–如)Na2CO3,CaF2,Li2CO3等。
3. 碳质材料(骨架材料)具有控制保护渣熔速的能力碳的类型(炭黑,焦炭,石墨等)不同的钢种选用不同的保护渣,成分的变化主要考虑以下保护渣物理化学特性:2.1 碱度一般定义为组分中(R=CaO%/SiO2%)的比值。
它是反映保护渣吸收钢液中夹杂物能力的重要指标,同时也反映了保护渣润滑性能的优劣。
通常碱度大,吸收夹杂物的能力也大,但它的析晶温度变大,导致传热和润滑性能恶化。
2.2 粘度它是衡量保护渣润滑性能的重要指标。
目前通常采用旋转法测定或根据经验公式计算。
现在大多测其在1300℃条件下的值,常用保护渣的粘度(1300℃)为0 .05~0.15Pa.s。
它受化学成分和温度的控制,生产中主要靠助熔剂来调节。
要想得到高质量铸坯且不发生粘结漏钢,必须要选择合适粘度的保护渣。
保护渣粘度过低,液渣大量流入缝隙,造成渣膜不均匀,局部凝固变缓,导致凝固坯壳变形,引起纵裂和拉漏事故;粘度过大,会使铸坯表面粗糙。
2.3 熔化温度它包括烧结起始温度、软化温度或叫变形温度、半球点温度和流动温度。
实际应用中是将渣料制成锥形3×3 mm的标准试样,在显微镜中测定。
当以一定的升温速度使试样加热到由圆柱形变为半球形时的温度,称为熔化温度。
连铸生产中通常将保护渣的熔化温度控制在1200℃以下。
它主要受保护渣的成分、碱度以及Al2O3含量等因素的影响,熔化温度过高,润滑作用差并且不均匀。
2.4 结晶温度(析晶温度)它是影响凝固坯壳导热的重要参数。
对裂纹敏感性特强的包晶类钢种应使用结晶温度高的保护渣。
它主要受化学成分的影响,尤其是碱度。
通常可以在测保护渣粘度时进行,当保护渣在降温过程中,从粘度-温度曲线上发现熔渣有结晶现象。
板坯连铸机粘结漏钢与结晶器保护渣的关系
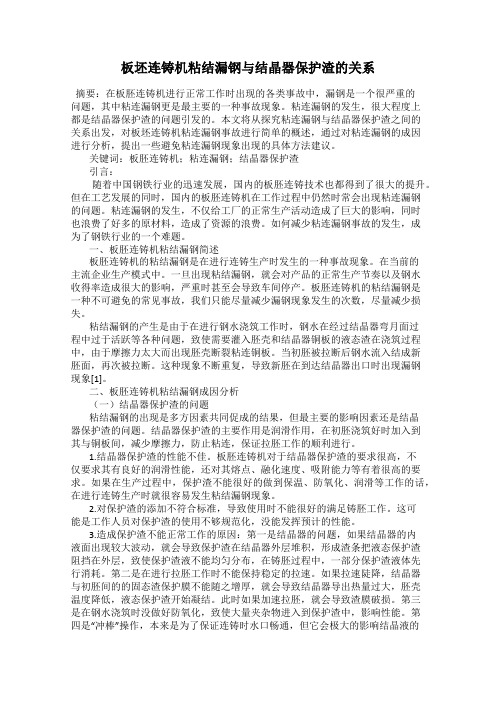
板坯连铸机粘结漏钢与结晶器保护渣的关系摘要:在板胚连铸机进行正常工作时出现的各类事故中,漏钢是一个很严重的问题,其中粘连漏钢更是最主要的一种事故现象。
粘连漏钢的发生,很大程度上都是结晶器保护渣的问题引发的。
本文将从探究粘连漏钢与结晶器保护渣之间的关系出发,对板坯连铸机粘连漏钢事故进行简单的概述,通过对粘连漏钢的成因进行分析,提出一些避免粘连漏钢现象出现的具体方法建议。
关键词:板胚连铸机;粘连漏钢;结晶器保护渣引言:随着中国钢铁行业的迅速发展,国内的板胚连铸技术也都得到了很大的提升。
但在工艺发展的同时,国内的板胚连铸机在工作过程中仍然时常会出现粘连漏钢的问题。
粘连漏钢的发生,不仅给工厂的正常生产活动造成了巨大的影响,同时也浪费了好多的原材料,造成了资源的浪费。
如何减少粘连漏钢事故的发生,成为了钢铁行业的一个难题。
一、板胚连铸机粘结漏钢简述板胚连铸机的粘结漏钢是在进行连铸生产时发生的一种事故现象。
在当前的主流企业生产模式中。
一旦出现粘结漏钢,就会对产品的正常生产节奏以及钢水收得率造成很大的影响,严重时甚至会导致车间停产。
板胚连铸机的粘结漏钢是一种不可避免的常见事故,我们只能尽量减少漏钢现象发生的次数,尽量减少损失。
粘结漏钢的产生是由于在进行钢水浇筑工作时,钢水在经过结晶器弯月面过程中过于活跃等各种问题,致使需要灌入胚壳和结晶器铜板的液态渣在浇筑过程中,由于摩擦力太大而出现胚壳断裂粘连铜板。
当初胚被拉断后钢水流入结成新胚面,再次被拉断。
这种现象不断重复,导致新胚在到达结晶器出口时出现漏钢现象[1]。
二、板胚连铸机粘结漏钢成因分析(一)结晶器保护渣的问题粘结漏钢的出现是多方因素共同促成的结果,但最主要的影响因素还是结晶器保护渣的问题。
结晶器保护渣的主要作用是润滑作用,在初胚浇筑好时加入到其与铜板间,减少摩擦力,防止粘连,保证拉胚工作的顺利进行。
1.结晶器保护渣的性能不佳。
板胚连铸机对于结晶器保护渣的要求很高,不仅要求其有良好的润滑性能,还对其熔点、融化速度、吸附能力等有着很高的要求。
保护渣
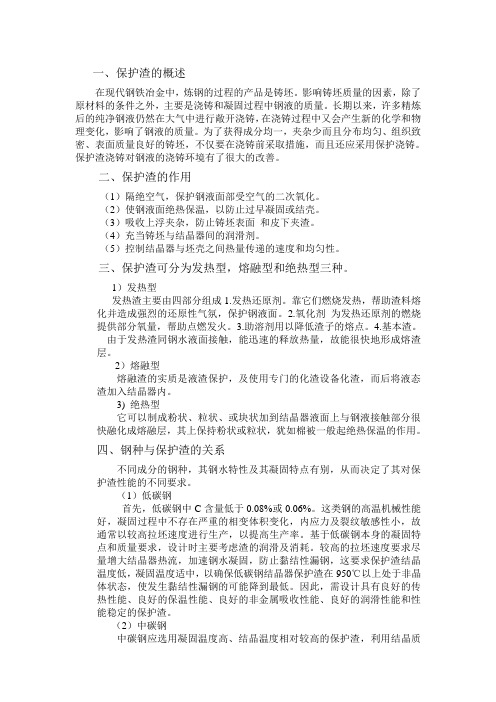
一、保护渣的概述在现代钢铁冶金中,炼钢的过程的产品是铸坯。
影响铸坯质量的因素,除了原材料的条件之外,主要是浇铸和凝固过程中钢液的质量。
长期以来,许多精炼后的纯净钢液仍然在大气中进行敞开浇铸,在浇铸过程中又会产生新的化学和物理变化,影响了钢液的质量。
为了获得成分均一,夹杂少而且分布均匀、组织致密、表面质量良好的铸坯,不仅要在浇铸前采取措施,而且还应采用保护浇铸。
保护渣浇铸对钢液的浇铸环境有了很大的改善。
二、保护渣的作用(1)隔绝空气,保护钢液面部受空气的二次氧化。
(2)使钢液面绝热保温,以防止过早凝固或结壳。
(3)吸收上浮夹杂,防止铸坯表面和皮下夹渣。
(4)充当铸坯与结晶器间的润滑剂。
(5)控制结晶器与坯壳之间热量传递的速度和均匀性。
三、保护渣可分为发热型,熔融型和绝热型三种。
1)发热型发热渣主要由四部分组成1.发热还原剂。
靠它们燃烧发热,帮助渣料熔化并造成强烈的还原性气氛,保护钢液面。
2.氧化剂为发热还原剂的燃烧提供部分氧量,帮助点燃发火。
3.助溶剂用以降低渣子的熔点。
4.基本渣。
由于发热渣同钢水液面接触,能迅速的释放热量,故能很快地形成熔渣层。
2)熔融型熔融渣的实质是液渣保护,及使用专门的化渣设备化渣,而后将液态渣加入结晶器内。
3) 绝热型它可以制成粉状、粒状、或块状加到结晶器液面上与钢液接触部分很快融化成熔融层,其上保持粉状或粒状,犹如棉被一般起绝热保温的作用。
四、钢种与保护渣的关系不同成分的钢种,其钢水特性及其凝固特点有别,从而决定了其对保护渣性能的不同要求。
(1)低碳钢首先,低碳钢中C含量低于0.08%或0.06%。
这类钢的高温机械性能好,凝固过程中不存在严重的相变体积变化,内应力及裂纹敏感性小,故通常以较高拉坯速度进行生产,以提高生产率。
基于低碳钢本身的凝固特点和质量要求,设计时主要考虑渣的润滑及消耗。
较高的拉坯速度要求尽量增大结晶器热流,加速钢水凝固,防止黏结性漏钢,这要求保护渣结晶温度低,凝固温度适中,以确保低碳钢结晶器保护渣在950℃以上处于非晶体状态,使发生黏结性漏钢的可能降到最低。
保护渣在连铸机中的应用

保护渣在连铸机中的应用保护渣对连铸生产和铸坯质量有着至关重要的作用,合理选择保护渣不仅能减少铸坯表面纵裂纹、横裂纹、凹坑、表面夹杂等缺陷,而且能优化浇铸工艺,提高拉坯速度,减少粘结漏钢几率。
本文分析了保护渣在连铸机中的应用。
标签:保护渣;连铸机;工艺;应用前言:連铸技术以其简化生产工序、提高金属收得率、节能降耗、提高铸坯质量和改善劳动条件等优点而得到迅速发展。
连铸采用浸入式水口和保护渣浇铸,它对稳定连铸工艺、扩大连铸品种、提高铸坯质量和产量都是一项极为有效的技术。
一、结晶器保护渣结晶器保护渣是人造渣,其主要化学成分为:CaO、SiO2、Al2O3、MgO、K2O、Ba2O3、Na2O、BaO、CaF2、FeO、TiO2碳粒以及有害成分P、S等,通常用于钢水连铸工艺。
保护渣加到结晶器液态钢水的表面,由于钢水的热传导,熔化并流入结晶器壁与坯壳的缝隙中。
保护渣提供结晶器壁和铸坯之问的润滑,减少钢水表面的热损失,保护表面不再氧化,还可以去除钢水中的夹杂物。
连铸保护渣应满足以下冶金功能的要求,具体包括:①对钢水表面起隔热作用;②隔绝钢液与空气接触,防止钢水氧化;③减小坯壳与结晶器壁问的磨擦;①吸收上浮到钢水表面的夹杂物;⑤控制坯壳与结晶器问的热传导。
满足上述要求的保护渣对提高连铸工艺效率和产品表面质量起着非常重要的作用。
二、连铸结晶器保护渣的作用连铸结晶器保护渣在钢水面上形成三层结构,即粉渣层—烧结层—液渣层,这三层结构对连铸坯的表面及内部质量有决定性的影响,是影响连铸机生产效率的一个重要因素.结晶器保护渣在连铸生产中具有如下作用:防止结晶器内钢液的二次氧化;在结晶器内钢液表面形成一绝热层,防止结晶器内钢液表面的凝固;吸收结晶器内钢液中上浮的夹杂物,提高结晶器内钢液的纯净度;在结晶器壁和铸坯凝固壳的间隙形成均匀的润滑层,防止产生粘结性漏钢事故;改善铸坯凝固壳与结晶器壁的传热,减少铸坯的表面缺陷.选择和应用合理的结晶器保护渣,使它们的物理、化学性质和热力学、动力学性能达到最佳,既可减少连铸坯表面的缺陷,又可防止连铸生产过程中的粘结漏钢事故.三、连铸工艺参数对保护渣性能的要求(一)普碳钢保护渣钢厂在选用保护渣时,主要根据钢种的碳含量,不同含碳量的钢种使用保护渣的性能有较大的区别。
不锈钢保护渣

不锈钢连铸保护渣概述摘要:概要介绍了不锈钢的性能特点、主要生产工艺,保护渣的设计原则,围绕提高铸坯表面质量的表面质量,论述了连铸保护渣的优化技术路线,对几个典型生产实例做了介绍。
关键词:不锈钢,连铸坯,表面质量,保护渣1 前言不锈钢是最重要而又普及的金属材料之一,由于其具有许多优良的性能,如耐腐蚀、耐磨损、耐热、耐低温、强度高、易加工等,因此广泛用于工业及民用领域的各个方面。
自1954年加拿大阿特拉斯公司建造了第一台不锈钢板坯连铸机以来,不锈钢连铸技术蓬勃发展,目前不锈钢连铸比已超过95%。
高质量连铸坯生产已成为不锈钢降低成本,提高成材率的关键[1]。
不锈钢中含有大量的Cr、Ni、Ti等合金元素,不同品种具有不同的凝固特性;易氧化元素多,夹杂含量高,在连铸过程中铸坯表面多出现凹陷、裂纹、深振痕及夹渣等缺陷。
这些缺陷增加了铸坯修磨量,严重降低了不锈钢的成材率。
为满足性能要求,不锈钢表面质量要求比普碳钢严格,但其本身却极易产生表面缺陷,因此不锈钢连铸必须选择合适的连铸保护渣并严格控制其理化性能。
2 不锈钢连铸的特点2.1 不锈钢的组成与凝固特点不锈钢主要含镍、铬、钛等合金元素,其主要包括高镍奥氏体、高铬铁素体、对裂纹敏感的马氏体不锈钢及含钛不锈钢。
钢中的合金元素及含量的不同使其具有不同的凝固组织。
铬是稳定铁素体和缩小奥氏体区的元素,足够的铬可以使钢变成单一的铁素体。
镍是稳定、扩大奥氏体和缩小铁素体相区的元素。
钛作为稳定钢中碳元素,优先与碳结合生成TiC,达到防止敏化钛晶界腐蚀的目的。
合金元素及其加入量的不同导致不锈钢的凝固特性相差较大。
有的钢种固液两相区较宽,钢的凝固组织变化较大;有些钢种的热物理性能差别大,裂纹敏感性高,其工艺控制的重点也就不尽相同。
不锈钢的铸坯凝固组织可分3类:1) 钢液凝固形成稳定γ相或δ相,初生的树枝晶和二次晶界完全重合,如0Cr25Ni20为代表的奥氏体及1Cr17为代表的铁素体;2) 钢液凝固先析出γ相,然后发生L+δ+γ,最后凝固成δ+γ,如0Cr17Ni12Mo2;3) 钢液凝固先析出δ相,然后发生L+δ→γ,最后凝固成δ+γ,如1Cr13、2Cr13或0Cr18Ni9。
保护渣对铸坯质量和连铸过程的影响
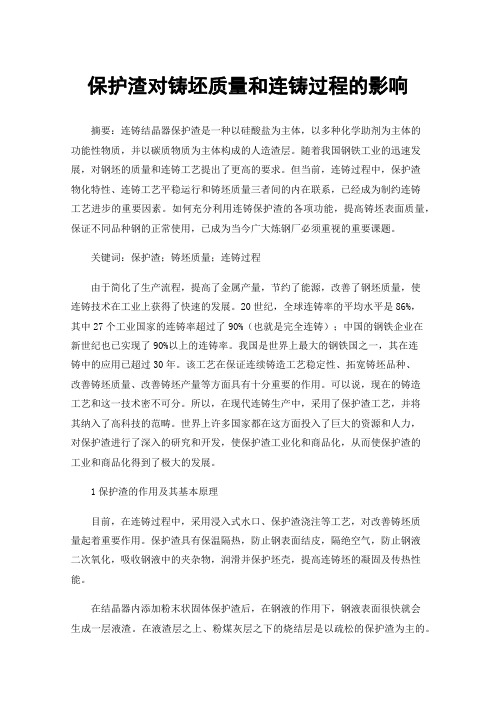
保护渣对铸坯质量和连铸过程的影响摘要:连铸结晶器保护渣是一种以硅酸盐为主体,以多种化学助剂为主体的功能性物质,并以碳质物质为主体构成的人造渣层。
随着我国钢铁工业的迅速发展,对钢坯的质量和连铸工艺提出了更高的要求。
但当前,连铸过程中,保护渣物化特性、连铸工艺平稳运行和铸坯质量三者间的内在联系,已经成为制约连铸工艺进步的重要因素。
如何充分利用连铸保护渣的各项功能,提高铸坯表面质量,保证不同品种钢的正常使用,已成为当今广大炼钢厂必须重视的重要课题。
关键词:保护渣;铸坯质量;连铸过程由于简化了生产流程,提高了金属产量,节约了能源,改善了钢坯质量,使连铸技术在工业上获得了快速的发展。
20世纪,全球连铸率的平均水平是86%,其中27个工业国家的连铸率超过了90%(也就是完全连铸);中国的钢铁企业在新世纪也已实现了90%以上的连铸率。
我国是世界上最大的钢铁国之一,其在连铸中的应用已超过30年。
该工艺在保证连续铸造工艺稳定性、拓宽铸坯品种、改善铸坯质量、改善铸坯产量等方面具有十分重要的作用。
可以说,现在的铸造工艺和这一技术密不可分。
所以,在现代连铸生产中,采用了保护渣工艺,并将其纳入了高科技的范畴。
世界上许多国家都在这方面投入了巨大的资源和人力,对保护渣进行了深入的研究和开发,使保护渣工业化和商品化,从而使保护渣的工业和商品化得到了极大的发展。
1保护渣的作用及其基本原理目前,在连铸过程中,采用浸入式水口、保护渣浇注等工艺,对改善铸坯质量起着重要作用。
保护渣具有保温隔热,防止钢表面结皮,隔绝空气,防止钢液二次氧化,吸收钢液中的夹杂物,润滑并保护坯壳,提高连铸坯的凝固及传热性能。
在结晶器内添加粉末状固体保护渣后,在钢液的作用下,钢液表面很快就会生成一层液渣。
在液渣层之上、粉煤灰层之下的烧结层是以疏松的保护渣为主的。
在连铸过程中,钢液在连铸过程中逐步形成了一层钢壳层。
在钢液与保护渣界结合的部位,形成了一层钢坯壳,起到了隔绝空气,防止了二次氧化的作用。
保护渣的选用分析
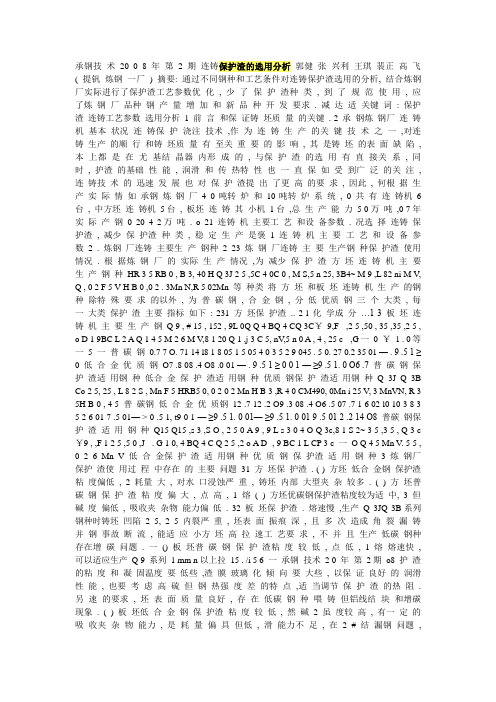
承钢技术20 0 8年第2期连铸保护渣的选用分析郭健张兴利王琪裴正高飞( 提钒炼钢一厂) 摘要: 通过不同钢种和工艺条件对连铸保护渣选用的分析, 结合炼钢厂实际进行了保护渣工艺参数优化, 少了保护渣种类, 到了规范使用, 应了炼钢厂品种钢产量增加和新品种开发要求. 减达适关键词: 保护渣连铸工艺参数选用分析 1 前言和保证铸坯质量的关键. 2 承钢炼钢厂连铸机基本状况连铸保护浇注技术,作为连铸生产的关键技术之一,对连铸生产的顺行和铸坯质量有至关重要的影响, 其是铸坯的表面缺陷, 本上都是在尤基结晶器内形成的, 与保护渣的选用有直接关系, 同时, 护渣的基础性能, 润滑和传热特性也一直保如受到广泛的关注,连铸技术的迅速发展也对保护渣提出了更高的要求, 因此, 何根据生产实际情如承钢炼钢厂4 0吨转炉和10吨转炉系统, 0 共有连铸机6台, 中方坯连铸机5台, 板坯连铸其小机1台,总生产能力5 0万吨,0 7年实际产钢0 20 4 2万吨. o 21 连铸机主要工艺和设备参数. 况选择连铸保护渣, 减少保护渣种类, 稳定生产是褒 1 连铸机主要工艺和设备参数 2 . 炼钢厂连铸主要生产钢种 2 23 炼钢厂连铸主要生产钢种保护渣使用情况. 根据炼钢厂的实际生产情况,为减少保护渣方坯连铸机主要生产钢种HR 3 5 RB 0 , B 3, 40 H Q 3J 2 5 ,5C 4 0C 0 , M S,5 n 25, 3B4~ M 9 ,L 82 ni M V, Q , 0 2 F 5 V H B 0 ,0 2 . 3Mn N,R 5 02Mn 等种类将方坯和板坯连铸机生产的钢种除特殊要求的以外, 为普碳钢, 合金钢, 分低优质钢三个大类, 每一大类保护渣主要指标如下: 231 方坯保护渣.. 2 l 化学成分…1 3 板坯连铸机主要生产钢Q 9 , # 15 , 152 , 9L 0Q Q 4 BQ 4 CQ 3C¥9,F - ,2 5 ,50 , 35 ,35 ,2 5 , o D 1 9BC L 2 A Q 1 4 5 M 2 6 M V,8 1 20 Q 1 ,j 3 C 5, nV,5 n 0 A , 4 , 25 c - ,G一0 ¥1 . 0等一5 一普碳钢0.7 7 O. 71 14 l8 1 8 05 1 5 05 4 0 3 5 2 9 045 . 5 0. 27 0.2 35 01 —. 9 .5 1 ≥ 0 低合金优质钢O7 .8 08 .4 O8 .0 01 —. 9 .5 1 ≥ 0 0 1 —≥9 .5 1. 0 O6 .7 普碳钢保护渣适用钢种低合金保护渣适用钢种优质钢保护渣适用钢种Q 3J Q 3B Co 2 5, 25 , L 8 2 S , Mn F 5 HRB5 0, 0 2 0 2 Mn H B 3 ,R 4 0 CM490, 0Mn i 25 V, 3 MnVN, R 3 5H B 0 , 4 5 普碳钢低合金优质钢12 .7 12 .2 O9 .3 08 .4 O6 .5 07 .7 1 6 02 l0 10 3 8 3 5 2 6 01 7 .5 01— > 0 .5 1, t9 0 1 —≥9 .5 1. 0 01—≥9 .5 1. 0 01 9 .5 01 2 .2 14 O8 普碳钢保护渣适用钢种Q15 Q15 ,s 3 ,S O , 2 5 0 A 9 , 9 L s 3 0 4 O Q 3c,8 1 S 2~ 3 5 ,3 5 , Q 3 c ¥9 , ,F 1 2 5 ,5 0 ,J - . G 1 0, 4 BQ 4 C Q 2 5 ,2 o A D- , 9 BC 1 L CP 3 c 一O Q 4 5 Mn V. 5 5 , 0 2 6 Mn V 低合金保护渣适用钢种优质钢保护渣适用钢种3 炼钢厂保护渣使用过程中存在的主要问题31 方坯保护渣 . ( ) 方坯低合金钢保护渣粘度偏低, 2 耗量大, 对水口浸蚀严重, 铸坯内部大型夹杂较多. ( ) 方坯普碳钢保护渣粘度偏大, 点高, 1 熔( ) 方坯优碳钢保护渣粘度较为适中, 3 但碱度偏低, 吸收夹杂物能力偏低. 32 板坯保护渣. 熔速慢,生产Q 3JQ 3B系列钢种时铸坯凹陷 2 5, 2 5 内裂严重, 坯表面振痕深, 且多次造成角裂漏铸并钢事故断流, 能适应小方坯高拉速工艺要求, 不并且生产低碳钢种存在增碳问题. 一() 板坯普碳钢保护渣粘度较低, 点低, 1 熔熔速快, 可以适应生产Q 9 系列 1 mm n以上拉15 . /i 5 6 一承钢技术2 0 年第2期o8 护渣的粘度和凝固温度要低些,渣膜玻璃化倾向要大些, 以保证良好的润滑性能, 也要考虑高硫但钢热强度差的特点,适当调节保护渣的热阻. 另速的要求, 坯表面质量良好, 存在低碳钢种喂铸但铝线结块和增碳现象. ( ) 板坯低合金钢保护渣粘度较低, 然碱 2 虽度较高, 有一定的吸收夹杂物能力, 是耗量偏具但低, 滑能力不足, 在 2 # 结漏钢问题,润存0粘限制了拉速的进一步提高 . ( ) 板坯优碳钢保护渣粘度低, 热和润滑 3 传外, 由于高碳钢液相线温度低, 铸温度较其它钢浇种要低, 护渣性能设计也要考虑此温度的影响, 保为了防止钢水冻结,高碳钢要使用隔热性能好的保护渣, 体积密度要低. 5 连铸工艺参数对保护渣性能设计要求51 拉速. 效果良好, 以适应 4 坯的生产要求, 是由可5板但于板坯中高碳钢碳含量范围较大, 在统一问题. 存 4 不同钢种对保护渣性能设计要求连铸机的拉坯速度是连铸生产的重要工艺参数之一.随着拉速提高, 护渣耗量减少.保护渣保的消耗量是液渣渗入铸坯与结晶器之间空隙的平均量的一个量度,因此成为一个重要的过程控制不同钢种.其钢水特性及其凝固特点有别, 从而决定了对保护渣性能方面的要求. 41 低碳钢. 低碳钢高温机械性能好,凝固过程中不存在参数, 值一般要求在03 g 其. / 以上.拉坯速度提km 高则保护渣消耗降低,而保护渣的消耗量不足将导致铸坯的润滑和传热状况不良,为此选用高速连铸用保护渣时应提高其熔化速度, 降低其粘度及凝固温度, 以改善液渣的流人特性, 足液渣消满耗的要求. 同时, 为了提高熔化速度, 当减少堆应积密度,减少碳含量和增加碳酸盐含量以及选择严重的相变体积变化, 内应力及裂纹敏感性小, 故通常以较高拉坯速度进行生产,基于低碳钢本身的凝固特点和质量要求,主要考虑渣的润滑及消耗.较高拉速要求尽量增大结晶器热流, 速钢水加凝固, 止粘结漏钢, 要求保护渣结晶温度低, 防这凝固温度适中.在高速浇注时, 为使足够的液态保护渣能流人铸流和结晶器内表面之间的区域, 确保良好的润滑和足够的消耗,通常保护渣粘度选合理原料及其物性. 5 铸坯断面形状. 2 方坯与板坯的不同首先在于结晶器内腔的表择较低的范围.另外, 类钢种初生坯壳强度高, 此铸坯振痕较深, 故应使用保温性能较好的保护渣, 提高弯月面初生坯壳温度,有利于减轻振痕过深带来的危害. 因此, 铸低碳钢满足以上各要求, 连就要通过设计具有一定的传热性能, 良好的保温性能, 良好的非金属吸收, 良好的润滑和性能稳定的保护渣来获得. 42 中碳钢. 面积与体积之比即比表面不同.铸坯的比表面增加时, 护渣耗量(gm) 剧减少, 坯的比表面保k/ 2 急板小于方坯. 由于板坯比表面小, 护渣消耗快, 保进而要求较快的熔化速度.另外, 坯对所用保护渣方的粘度不是很敏感,故常使用高粘度渣以减少夹渣和浸入式水口的侵蚀, 由于方坯的比表面大, 要求的渣消耗量(gm) 少, k/ 2 较连铸过程中较容易满足相变, 体积要求. 中碳钢钢水凝固过程中发生8 强烈收缩, 此钢种裂纹敏感性大, 易产生表面裂容纹, 免纵横向裂纹是首要考虑的问题, 避为此, 中其次, 由于板坯连铸时在宽度方向上液面波动较大, 因此要求保护渣熔速较快, 以形成足够的液渣层厚度, 盖整体的钢液表面覆53 结晶器振动特性I 碳钢用保护渣选用的重点应放在控制从铸坯传往结晶器的热流上, 限制结晶器热通量, 望保护渣希具有较大热阻 . 因此, 选用凝固温度高, 晶温应结为了补偿由于拉速的提高等原因导致渣耗的下降, 些钢厂采用非正弦振动取代正弦振动.根有据非正弦振动的位移和速度曲线分析,改用非正弦振动曲线后,负滑脱时间缩短,正滑脱时间延长, 而渣耗增大 .同时, 晶器采用高频率(o 从结3o 次/ i m n以上)小振幅( 3 m) 非正弦振动, 利, +a _r 的有于减少初生凝固壳拉伸应力和减轻振痕, 高铸坯提一度也高的保护渣, 保护渣传热速度减缓, 助于使有减小铸坯在冷却过程中产生的热应力. 4 . 高碳钢 3 此钢种的特点是热强度差;浇铸温度和浇铸速度较低; 同时容易产生粘结漏钢, 高碳钢保护故渣设讨的重点应放在保证润滑上.为此, 设计该保7 一表面质量.因此, 通过改进优化结晶器振动特性, 喂铝线保护渣结块和铸坯增碳问题. 61 将方坯和板坯普碳钢和低合金钢保护渣统.. 2 一可在一定程度上减轻保护渣改善铸坯质量的负荷,结晶器振动特性可在保护渣的设计中作为参考. , 适当提高保护渣碱度, 照适应优碳钢设计, 按同时兼顾普碳钢高拉速要求 . 因此连铸用保护渣性能参数设计应综合多因素考虑, 以实际要求作为出发点, 不同钢种, 应按不同拉速, 同连铸坯断面设计保护渣系列产品, 不以求达到连铸用保护渣合理使用. 6 炼钢厂连铸保护渣工艺优化研究61 增加方坯和板坯优质钢保护渣的碱度, .3 降低熔化在保证润滑和传热效果的条件下提高吸附夹杂能力, 少铸坯内部夹杂. 减62 连铸保护渣工艺优化方案实施效果. 621 方坯和板坯低碳钢保护渣主要物化性能和.. 使用效果61 连铸保护渣工艺优化方案. 611 开发方坯和板坯低碳钢专用保护渣,解决.. 6211 方坯和板坯低碳钢保护渣主要化学成分… 表6 化学成分钢种碱度R 容重gc 3 /I n 熔点℃熔速S 粘度10 ~ P . 3 0C,aS 粒度il rl U 方坯C 0 L8 10 10 5 x 5 21 . 15 . 2 04 .5 O6 .8 + .1 005 + .1 OO 02 . 5 O3 .5 熔化良好, 结块无熔化良好 . 量结块少良好良好板坯0A 10 (9 + 9 ) 8L 8 x 4 5 4 5 一8 一承钢技术20 0 8年第2期6221 方坯和板坯普碳钢保护渣使用效果... 表 1 方坯和板坯普碳钢保护渣使用效果 1 62 .. 方坯和板坯优碳钢保护渣主要物化性能和 3 62 . 方坯和板坯优碳钢保护渣主要物化性能.. 1 3 使用效果表 1 化学成分 2 623 … 方坯和板坯优碳钢保护渣使用效果 2 表 1 方坯和板坯优碳钢保护渣使用效果 4 综上所述, 过保护渣工艺优化, 通减少了保护渣种类,成功解决了低碳钢增碳和喂铝线结块及普碳低合金钢种水口寿命低问题以及板坯 2 钢及板坯连铸机自身的特点, 出了不同钢种对保护找渣性能设计上的要求, 对炼钢厂使用的保护渣并且存在的问题结合连铸机本身的特点进行了分析. 的粘结漏钢问题, 并且提高了方坯4 内部质5钢量, 少了保护渣库存, 到了规范使用, 合炼减达符钢厂品种钢产量增加和新品种开发要求, 益显效著. 7 结论( ) 通过对连铸工艺条件的分析, 2 如拉速提高对渣耗, 流等的影响, 坯与板坯内部及外在热方因素区别的对比,铸坯断面尺寸变化及结晶器振动特性的研究,得出了适用于以上各连铸工艺参数下的保护渣性能设计特点,并且对保护渣工艺参数进行了合理优化, 生产实施, 经取得了良好效果. ( 下转1 3页) 一( ) 通过分析低, , 碳钢等钢种和方坯1 中高9 一承钢技术( i 2= . ( a SO )03 C O) 7 20 0 8年第2期蚀严重停止工作,需进一步研究侧吹自动供气模式研究以提高侧吹砖寿命. 6 结论按公式() 承钢脱氧后终渣计算, 合承钢1 对结终渣实际T e含量,得出承钢终点钢渣Mg F o饱和值在95 . %~ 1 .%之间,比终渣脱氧前平均Mg 0 4 o 饱和值l. 08 %一1.%降低约1 %. 2 4 . 7 44 采用终渣脱氧后溅渣护炉工艺对钢水氧活度. 的影响( ) 承钢半钢炼钢终渣脱氧后进行溅渣护炉 1 工艺能降低渣中T e含量. F ( ) 承钢通过对终渣脱氧降低T e 2 F 含量, 低熔点铁酸盐相比例降低,高熔点相CS Cs相较3+ 2 多, 为 5 %, CS 比例大, 渣的全熔温度平约0 且2相终承钢炼钢转炉出钢前加入焦末对终渣进行脱氧, 验炉次加入焦末1 — . gt , 试. 26 / 钢通过钢水定 5 K 氧试验: 降低钢水ao最大值5 8 p m 降低钢水a ( ) 3. p , 8 ()最小值18 p m o 3. p ,平均降低钢水a () 7 0值 2 71p 7 . m.试验证明焦末在出钢前加入, p 通过对终均提高9 ℃.且终渣比脱氧前平均M o饱和值降8 g 低约1 %, 高终渣粘度, 高溅渣护炉效果. . 提7 提( ) 通过对终渣进行脱氧, 变渣钢间氧平 3 改渣进行脱氧, 变渣钢间氧平衡, 降低钢水的自改对由氧活度有作用. 45 采用终渣脱氧后溅渣护炉工艺的护炉效果. 承钢采用终渣脱氧后溅渣护炉工艺后,溅渣衡, 均降低钢水a0值271p 平() 7.pm. ( ) 通过应用终渣脱氧后溅渣护炉工艺, 4 溅渣效果大幅提高. 目前, 承钢4 转炉(0吨) | 4 经济炉龄突破9 0 0 0炉, 原经济炉龄提高 4 0 . 较0 0炉效果较原溅渣护炉工艺有大幅提高,主要表现在如下5方面:①溅渣起渣时间快,在o _ 5 - 1 秒之间. ②溅渣时不需调渣, 直接溅. ③溅渣时间短, 在参考文献9 _ l0 o- 2 秒之间渣基本溅净. ④炉衬挂渣均匀. ⑤溅渣层耐侵蚀情况:下一炉钢出钢时炉衬观察不到砖缝. 5 存在问题【】刘钢.氧气转炉含钒炉渣相图及一些氧化物对 1 C O F0 S0 渣系性能的影响. 京钢铁学院学报,9 3 a — e 一i2 北18— 1 . 【】苏天森. 2 转炉溅渣护炉技术. 北京: 冶金工业出版社, 9 93 l 9 I. 【】杨素波, 3 陈勇等. 钢炼钢条件下的碱渣护炉技半术研究.钢铁钒钛,o 12 ( ) 2 o ,2 3 . () 采用出钢前在终渣中加入焦末脱氧, 1 同时利用出钢时转炉出钢侧侧吹搅拌后进行溅渣护炉工艺,在出钢时炉内反应剧烈,需用压渣剂压渣, 否则影响出钢. 【】Ta H a t g等. 中no 和23 4 si w na n 渣2 o 对转炉溅渣护炉的影响. 钢技术,0 4 5 鞍20 ,. ( ) 转炉侧吹砖的寿命在30 2 00炉左右因侵( 接9页) 上() 从连铸钢种及工艺参数对保护渣性能3 上的要求出发, 设计具有相应性能的保护渣, 此在基础上通过原料的合理组合完成保护渣的设计, 并且进行了保护渣的合理归类,减少了保护渣种类和库存,适应了炼钢厂品种钢产量增加和新品种开发的要求. 参考文献【】史寰兴. 1 实用连铸冶金技术】. 北京: 冶金工业出版社, 0· 25 0 【】陈家祥一2 连续铸钢手册【] M· : 北京冶金工业出版一1 — 3。
保护渣在结晶器内的行为探究

保护渣在结晶器内的行为探究发布时间:2021-06-16T16:31:15.807Z 来源:《科学与技术》2021年第6期作者:廖虔韬[导读] 保护渣的应用是影响连铸工艺高效化程度的关键,对维持连铸的正常生产和改善铸坯表面质量有着重要作用廖虔韬福建三宝钢铁有限公司漳州 363000摘要:保护渣的应用是影响连铸工艺高效化程度的关键,对维持连铸的正常生产和改善铸坯表面质量有着重要作用。
而应对不同钢种的连续浇注,保护渣的种类也变得多样化,但最终的目的都是为了使生产更加顺利地进行和提高铸坯的合格率。
此外,保护渣在结晶器内是以那些形式或者说状态存在,同时又是怎样改善铸坯表面质量。
在此需要对其有更加深人更加全面的认识,所以对保护渣在结晶器内的探究是有必要的。
关键词:保护渣;结晶器;铸坯表面质量一结晶器保护渣1.1保护渣的组成和分类保护渣做为一种复合型材料,其组成成分一般由SiO2-CaO-Al2O3三元系的基料、再添加各种助熔剂以及碳质材料组成。
其中基料的组成一般都是根据SiO2-CaO-Al2O3三元相图中低熔点区所制,根据三元相图能够大致确定其基料的成分范围:CaO为40%-60%,SiO2为40%-60%,而Al2O3一般都低于20%,熔点一般在1300℃-1500℃,但是这个温度是相对较高,而且其组成的黏度较高因此为了降低熔点和黏度,通常需要再加入一些助熔剂,比如冰晶石、硼砂、萤石、氟化物以及纯碱等。
而碳质材料一般都是石墨、炭黑等。
1.2保护渣的分类保护渣的分类一般可分为三种:发热渣、熔融液渣和固体绝热渣。
发热渣的配比一般以硅酸盐加氟化物为主,在加入金属粉和氧化剂,其特点是成渣快,缺点是成本高、起烟大,使用时还会使钢中的夹杂物增多。
熔融液渣也是早期使用的一种保护渣,使用时需要添加熔渣设备,过程比较麻烦,而且成本较高。
固体绝热渣是目前为止使用最为广泛的保护渣,其基料一般都是由硅酸盐为主,加上氟化物、纯碱等低熔点物质做为助熔剂,同时再加入碳质材料做为骨架、隔离和隔热的作用。
结晶器保护渣的性能及研究进展

《连续铸钢》论文论文题目:结晶器保护渣的性能及研究进展作者:李昌齐专业:冶金工程指导教师:刘宇雁教授结晶器保护渣的性能及研究进展李昌齐(材料与冶金学院、08冶金一班、0861107143)摘要:连铸时保护渣对改善连铸坯表面质量具有明显的效果,在设计和选择保护渣时,首先必须了解保护渣的基本性能,来提高连铸效率和质量。
本文综述了保护渣的主要物理性能、化学性能及最新的研究技术成果及应用。
关键词:结晶器;保护渣;物理化学性能;研究进展引言结晶器保护渣是连铸操作过程中使用的多功能冶金辅料,是一项高技术含量的辅料,保护渣对连铸工序生产稳定顺行和铸坯质量的提高有着密切关系[1]。
在连铸过程中,结晶器内钢液面上的保护渣层可绝热保温、隔绝空气防止对钢液的二次氧化、吸收从钢液中到大钢液面的夹杂物。
结晶器与坯壳之间的渣膜具有润滑坯壳、控制坯壳与结晶器间的传热等作用。
保护渣最重要的性能有粘度、熔渣层厚度、熔化温度、熔化速度、、熔化均匀性、玻璃性、吸收和溶解非金属夹杂物等。
这些性能主要与化学成分有关,并且对结晶器内渣膜的传热性有很大的影响。
1 保护渣的物理性能1.1 粘度粘度是决定渣消耗量的均匀渗入的重要性能之一。
它直接关系到溶化后的渣在弯月面区域的行为,对铸坯的表面质量有明显的影响。
如铸坯表面振痕的形状,结晶器铜壁与铸坯坯壳间均匀渣膜的形状,熔渣层吸收和溶解非金属夹杂物以及对浸入式水口的腐蚀等,其中影响最为重要的是对渣膜厚度和均匀性的影响。
为了吸收钢液中上浮的夹杂物,要求保护渣的粘度尽可能低,但是低粘度的保护渣对水口的侵蚀不利,为防止卷渣,在允许的条件下使用高粘度渣。
但粘度不能太高,否则会使保护渣渣耗降低,熔渣流入量减少,渣膜变薄且不均匀,引起摩擦力增大,结果会使坯壳受力,造成纵裂缺陷甚至漏钢。
对于相同的拉速,铸坯的断面增大,渣的单耗量下降,因此,粘度应低一些。
保护渣的粘度,必须与浇注的钢种、连铸机的类型、连铸的工艺参数和保护渣的融化特性相匹配。
保护渣(1)
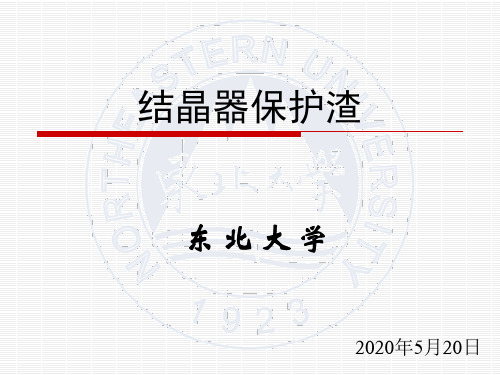
连铸技术
42
连铸技术
下列因素可以增大保护渣溶解吸收 Al2O3 的能 力: (1) 低粘度的保护渣 (2) 氟化物含量的增加(其中 NaF>LiF>CaF2) (3) 用 Li2O 取代 Na2O (4) 提高保护渣碱度 (5) 降低初始 Al2O3含量。
31
连铸技术
(2)粘度曲线形状的定量描述 结晶器保护渣(S 渣)的粘度曲线。A 点为 1300℃熔渣粘度,通常所指的粘度即为 A 点 粘度, G 点为拐点(粘度突变点),D 点粘度 为 5Pa· 。 s 粘度热稳定性是就 G 点附近的粘度变化情况而 言,而且很少对粘度稳定性进行定量研究。曲 线形状代表粘度的变化规律,曲线的倾斜度意 味着熔渣温度的改变时粘度的变化速率。
34
连铸技术
保护渣 lnη—1/T 曲线
35
连铸技术
3.4 保护渣界面性质
保护渣界面性质指保护渣的表面张力及保护渣与 钢水的界面张力。要使熔融的保护渣溶解吸收 弯月面处的夹杂物如 Al2O3,Cr2O3,TiO2 等,必须使熔渣对这些夹杂物具有良好的润湿 性,即熔渣能很快的捕捉它们,避免或减少这 些夹杂物在弯月面处被卷入凝固壳。
19
连铸技术
20
连铸技术
硅氧离子团结构图
21
连铸技术
氧化物对保护渣熔体网络的作用
22
连铸技术
3 连铸保护渣的物理和化学性质
连铸过程对保护渣的物理及化学性质有一定的要 求。保护渣的熔化温度、粘度及表面张力的大 小取决于渣的化学成分。保护渣的研制和使用 过程要对其密度、熔化温度、粘度、表面张力 和溶解吸收非金属夹杂物能力等基本性质进行 测定。除了上述几个基本性质之外,保护渣的 熔融速度、熔融模型以及导热性也是衡量保护 渣性能的主要指标。
- 1、下载文档前请自行甄别文档内容的完整性,平台不提供额外的编辑、内容补充、找答案等附加服务。
- 2、"仅部分预览"的文档,不可在线预览部分如存在完整性等问题,可反馈申请退款(可完整预览的文档不适用该条件!)。
- 3、如文档侵犯您的权益,请联系客服反馈,我们会尽快为您处理(人工客服工作时间:9:00-18:30)。
钢种与保护渣的关系
钢种与连铸保护渣的关系钢种与连铸保护渣的关系26 连铸保护渣技术,作为连铸生产的关键技术之一,对连铸生产的顺行和铸坯质量有着至关重要的影响,尤其是铸坯表面缺陷,基本上都是在结晶器内形成的,与保护渣有直接关系。
近几年来,该技术在实践中,如空心颗粒渣等的开发和广泛使用,对铸坯质量的改善、连铸生产工艺的稳定起了很大促进作用。
同时渣的基础性能如润滑和传热特性的研究也一直受到人们的重视。
一、不同钢种对保护渣性能设计要求不同成分的钢种.其钢水特性及其凝固特点有别,从而决定了对保护渣性能方面的要求。
1、低碳钢首先钢中w(C)<0.08%或0.06%。
这类钢高温机械性能好,凝固过程中不存在严重的相变体积变化,内应力及裂纹敏感性小,故通常以较高拉坯速度进行生产,以提高生产率。
基于低碳钢本身的凝固特点和质量要求,设计时主要考虑渣的润滑及消耗。
较高拉速要求尽量增大结晶器热流,加速钢水凝固,防止粘结漏钢,这要求保护渣结晶温度低、凝固温度适中,以确保低碳钢结晶器保护渣在950℃以上处于非晶体状态,使发生粘结漏钢的可能性最小。
在高速浇注时,为使足够的液态保护渣能流入铸流和结晶器内表面之间的区域,确保良好的润滑和足够的消耗,通常保护渣粘度选择较低的范围。
另外,此类钢种初生铁素体坯壳中[P]、[S]偏析小,初生坯壳强度高,铸坯振痕较深,故应使用保温性能较好的保护渣,提高弯月面初生坯壳温度,有利于减轻振痕过深带来的危去。
因此,连铸低碳钢满足以
上各要求,就要通过设计具有一定的传热性能、良好的保温性能、良好的非金属吸收、良好的润滑和性能稳定的保护渣来获得。
2、中碳钢中碳钢钢水凝固过程中发生己δ→γ相变,体积强烈收缩,此钢种裂纹敏感性大,容易产生表面裂纹,特别是高拉速时。
避免纵横向裂纹是首要考虑的问题,为此,中碳钢用保护渣设计的重点应放在控制从铸坯传往结晶器的热流上,限制结晶器热通量,希望保护渣具有较大热阻。
因此,应选用凝固温度高、结晶温度也高的保护渣,利用结晶质膜中的“气隙”,使保护渣传热速度减缓,有助于减小铸坯在冷却过程中产生的热应力。
3、高碳钢此钢种的特点是热强度差;浇铸温度和浇铸速度较低;同时容易产生粘结漏钢。
高碳钢容易粘结,这与初始生成的坯壳凝固收缩小有关。
故高碳钢保护渣设计的重点应放在保证润滑上。
为此,设计该保护渣的粘度和凝固温度要低些,渣膜玻璃化倾向要大些,以保证良好的润滑性能,但也要考虑高硫钢热强度差的特点,适当调节保护渣的热阻。
另外,由于高碳钢液相线温度低,浇铸温度较其它钢种要低,保护渣性能设计也要考虑此温度的影响,为了防止钢水冻结,高碳钢要使用隔热性能好的保护渣,体积密度要低,碳的加入量可稍高些甚至可达20%左右。
4、特殊钢特殊钢钢水成分相差较大,这种类型的保护渣配方较为复杂,往往根据钢的用途及易出现缺陷的状况而特殊配制,例如不锈钢,硅钢及含Nb、V、Ti及稀上的钢种等。
二、连铸工艺参数对保护渣性能设计要求
1、拉速连铸机的拉坯速度是连铸生产的重要工艺参数之一。
随着拉速提高,保护渣耗量减少。
保护渣的消耗量是液渣渗入铸坯与结晶器之间空隙的平均量的1个量度,因此成为1个重要的过程控制参数,其值一般要求在0.3kg/m2以上。
拉坯速度提高则保护渣消耗降低,而保护渣的消耗量不足将导致铸坯的润滑和传热状况不良,为此设计高速连铸用保护渣时应提高其熔化速度、降低其粘度及凝固温度,以改善液渣的流入特性,满足液渣消耗的要求。
同时,为了提高熔化速度,应当减少堆积密度,减少碳含量和增加碳酸盐含量以及选择合理原料及其物性。
拉速提高,传往结晶器的热流增大。
这是由于拉速提高,钢水在结晶器中停留时间缩短,坯壳温度增高,凝固坯壳厚度减薄,同样的钢水静压力更容易使坯壳与结晶器壁接触,这样有利于传热,使热流密度随拉速的提高而增大。
因此,对于高速连铸保护渣,应适当降低凝固温度及结晶温度,减小渣膜厚度,保证结晶器传热良好,但也应考虑到各钢种的临界热流值。
2、铸坯断面形状方坯与板坯的不同首先在于结晶器内腔的表面积与体积之比即比表面不同。
板坯220mm×1500mm,从2、3代表薄板坯100mm×1000mm、50mm×1300mm,小方坯160mm×160mm、130mm×130mm,且板坯及小方坯的拉速均为1.5m/min左右的情况总结如下,铸坯的比表面增加时,保护渣耗量(kg/m2)急剧减少,且板坯的比表面小于方坯。
由于板坯比表面小,保护渣消耗快,进而要求较快的熔化速度,因此适于板坯的保护渣熔化速度快于方坯保护渣。
另外,方坯对所用保护渣的粘度不是很敏感,故常使用高粘
度渣以减少夹渣和浸入式水口的侵蚀,这是由于方坯的比表面大,要求的渣消耗量(kg/m2)较少,连铸过程中较容易满足要求。
其次,由于板坯连铸时在宽度方向上液面波动较大,因此要求保护渣熔速较快,以形成足够的液渣层厚度,覆盖整体的钢液表面。
另外,板坯连铸机多用来生产低、中碳钢,而方坯除浇铸中碳钢外,还生产众多的高碳钢。