8D报告管理程序
8d报告是什么意思

8d报告是什么意思第一篇:8D报告是什么?8D报告是一种管理工具,通常用于跟踪、分析和解决生产和质量问题。
它是美国汽车工业Action Group(AIAG)设定的一种严格的质量管理方法。
8D报告通常用于团队解决问题,利用团队的知识与技能,通过定义问题、分析根本原因、实施短期和长期修正、防止问题再次发生等步骤,解决问题并预防类似问题的再次出现。
8D报告的全称是“8 Discipline Report”,其中的“8 Discipline”代表了8个步骤,这些步骤是解决问题的关键步骤。
这8个步骤分别是:1. 建立问题管理小组;2. 定义问题;3. 制定临时措施;4. 分析根本原因;5. 制订长期解决方案;6. 实施措施;7. 验证效果;8. 预防再次发生。
每个步骤都有特定的目标和要求,以确保问题得到彻底解决,并防止再次出现。
8D报告通常用于工业制造领域,特别是在高产量、复杂产品的制造过程中。
然而,许多公司已经将8D报告及其工具用于解决其他问题,如流程改进、项目管理、售后服务等,以及作为全面质量管理体系的一部分。
总的来说,8D报告是一种有用的质量问题解决方法,是所有企业和组织应该学习和实践的重要管理工具。
第二篇:8D报告的优点有哪些?使用8D报告可以带来许多优点,以下是其中的一些:1. 提高质量:8D报告使用系统化和标准化的方法来解决问题,以确保问题得到根本解决。
它帮助企业识别问题的根本原因,并实施持续的改进措施,以减少质量问题。
2. 提高效率:使用8D报告,可以节省时间和资源。
每个步骤都有特定的任务和时间表,以保证问题能够迅速地解决。
这种方法可以使企业更快地恢复正常生产并提高效率。
3. 提高沟通:8D报告是一种团队合作的方法,强调了沟通和协作的重要性。
它鼓励不同部门和团队之间的合作与协作,以确保问题得以解决。
4. 改进长期解决方案:使用8D报告,企业可以发现并解决根本原因。
这些解决方案将由一个横跨不同部门和团队的小组制定,以确保符合公司整体目标。
SWWP-034 8D报告管理控制程序

1.目的提高解决问题的效率,积累解决问题的经验;提供找出现存的与质量相关问题的框架,杜绝或尽量减少重复问题出现;原则是针对出现的问题,找出问题产生的根本原因,提出短期,中期,和长期对策,并采取相应行动措施。
2.适用范围用于解决各类可能遇到的简单或复杂的问题。
3.定义(1) 8D (8 Disciplines) 方法包含8个解决问题的步骤;它基于使用描述工具、格式化、分析、量化等工具,从而提供彻底解决问题的指引;(2) 问题: 被发现的具体问题,它包括:a、与正常状况相比,属于失常的现象,在这种情况下,需要予以纠正,使其恢复初始正常状况;b、为提高质量的目的而改变目前的状况;(3) 纠正措施:针对现存的不合格项或缺陷所采取的纠正措施,并杜绝或尽量减少重复问题出现;(4) 预防措施:针对潜在的不合格项或缺陷所采取的纠正措施,并杜绝或尽量减少重复问题出现。
4. 在下列情形中须提交8D报告(1)当客户在工厂现场的稽核中发现不合格项或缺陷时,对于严重不良,主要不良及重复发生的次要不良须提交8D报告;(2)出货检验发现严重不良,主要不良及重复发生的次要不良时须提交8D报告;(3)当市场上发现有重复发生的产品缺陷时须提交8D报告;(4)当技术员在测试过程中发现缺陷时须提交8D报告;(5)巡检在同一生产现场连续发现三个位置相同不良现象或三个原因相同不良现象;(6)要对那些需要长期纠正措施来解决的缺陷采取行动时,须提交8D报告;(7)被相关程序文件明确要求提交8D报告时。
5. 提交报告时间要求(1) 在发现问题的24小时内,提交包含所采取的暂时措施描述的8D报告;(2) 在发现问题的72小时内,提交包含问题发生原因的初步分析的8D报告。
6. 结论8D格式用于监控解决问题的过程,它不是一个详尽的报告或复杂的分析,描述工具,而是一个包含了解决问题的每个步骤的集合,因而可从其中找到经提炼的基本信息。
7. 步骤D1-第一步骤: 团队成员小组: 参与解决问题的所有成员所组成的集体;1) 小组中必须有一个负责人, 负责人根据需要,组织合乎要求的人成立临时团队,并负责收集要解决问题的相关数据(技术,定性,定量数据,预算,等);2) 在小组首次会议中,搜集必需的专业意见,定义考核方法(详细的进程计划,其它人员要求,等);D2-第二步骤: 问题描述,问题及其所造成影响的描述1) 描述在具体环境中观察到的现象,或问题造成的危险;2) 定量分析问题的状况;3) 采用适当的图表作为附件来描述(何时、何地、发生了什么事、严重程度、目前状态、如何紧急处理、以及展示照片和收集到的证物;D3-第三步骤:短期临时措施1) 若观察到的问题直接对产品的性能和等级造成影响,立即采取措施(分类,重工,延迟交货,报废)以确保正常生产得以继续进行,直到采取纠正措施将问题解决;2) 检查以确保短期临时措施有效;3) 若短期临时措施有效,则实施;D4-第四步骤: 明确和核实原因1) 从问题描述中寻找最有可能的一些原因,若有可能,做一些测试帮助寻找原因;2) 检查所有考虑到的可能原因, 将它们会带来的结果与观察到的结果比较, 原因/结果矩阵图可帮助选择优先考虑哪个原因;3) 识别问题的种类.(设计,程序,制程,材料,人员技巧);4) 探寻可能的解决方案,列出可行性,效果,实施时间等;5) 建立将要实施的那些措施的检验标准;6) 尽量利用各种图表,如鱼骨图;D5-第五步骤: 选择长期纠正措施1) 对将要执行的长期纠正措施在实施前做进一步的确认,以核对它们是否在实施后能提供一个合乎期望的结果. 目的是解决问题的根源,要防止这些纠正措施带来任何其它的负面影响,在这种情形下,须采取其它的措施消除负面影响;2) 选择或创建一个测量工具,评估在纠正过程中各项工作的功效,如不良率、过程能力;3) 执行长期纠正措施,更新相关文件;4) 长期纠正措施的功效可通过观察问题是否重复出现来评估;D7-第七步骤: 预防问题重复出现措施1) 修正整个质量系统(特别是问题相关的程序,技术说明书,工作说明书 );2) 管理层同意并修正整个质量系统,是该过程的第一步,该过程或立即开始实施,或是一个不断改进的计划;D8-第八步骤: 项目完毕1)关注的问题被解决、确认、核实以及被权威人士审核签名通过并存盘。
客诉根因解决之8D报告

8D中的误区
缺乏意识,未有效固化经验。 真正能从系统的角度去考虑和预防问题的发生,总结经验教训,固化经验,
而不是流于形式。
感谢您的聆听
1.8D的基本概念 2.8D的开展步骤 3. 8D的应用误区
8D中的误区
公司任何质量异常均用8D方法予以解决。使得8D在公司上下成为一种形式 对于复杂的、影响严重的问题,才使用8D的方法解决,如:客户投诉、内部
批量质量问题、停线问题等
指定一个人完成一项8D任务 8D是以团队为导向的问题解决方法,即依靠跨部门的横向功能小组来解决问
为了避免此问题或类似问题发生,修改管理系统、实务及流程等标准 (未发生的不发生)
怎么才算合格的8D
通过确认8D报告来决定这些问题是否已经回答:
①对零件的知识进行了充分论证 ②完全确认了根本原因并聚焦于原因 ③遗漏点已经被识别 ④确定与根本相匹配的纠正措施 ⑤纠正措施计划的验证已经被确认(包括了实施纠正措施的时间计划) ⑥有证据显示供方将把纠正措施纳入整个系统
8D报告
8D report
1.8D的基本概念 2.8D的开展步骤 3. 8D的应用误区
什么是8D
8D的原名叫做 8 Disciplines,又称团队导向问题解决方 法、8D问题求解法(8D Problem Solving)是福特公司处理 问题的一种方法,亦适用于制程能力指数低於其应有值时有关问 题的解决,它提供了一套符合逻辑的解决问题的方法,同时对於统 计制程管制与实际的品质提升架起了一座桥梁。现在8D已经成 为许多大公司用这个方便而有效的方法解决品质问题。目前, 8D已经成为一个固定而有共识的标准化问题解决步骤。
为什么推行8D
确定根本问题
认清根本原因
消除根本原因
8D报告管理程序

8D报告管理程序第一步:建立一个团队要解决问题,需要建立一个专门的团队来处理和管理该问题。
这个团队应该由跨部门的成员组成,包括质量控制、工程、生产和供应链等各个部门的代表。
团队成员应该具备良好的沟通和解决问题的能力。
第二步:描述问题在这一步骤中,团队要详细描述问题的性质和发生的具体情况。
这包括问题的类型,涉及的产品或过程以及问题发生的地点和时间等。
通过详细描述问题,团队能够更好地理解问题的本质。
第三步:建立临时控制措施在此步骤中,团队需要快速采取一些临时控制措施来防止问题的进一步扩大。
这可以包括停止生产线、检查设备或产品以及提醒员工注意等。
目标是尽快减少问题带来的影响。
第四步:确定根本原因在这一步骤中,团队将使用不同的分析工具和技术来确定问题的根本原因。
这可能涉及到因果分析、5W1H分析、鱼骨图等。
通过确定问题的根本原因,团队可以制定更有效的解决方案。
第五步:采取长期解决方案在这一步骤中,团队需要根据确定的根本原因制定长期的解决方案。
这可能包括改进产品设计、修改工艺流程、更换设备或培训员工等。
目标是根除问题,确保类似的问题不再发生。
第六步:验证解决方案的有效性在这一步骤中,团队将实施和验证采取的解决方案的有效性。
这可以通过实际操作、统计数据的分析以及检查产品或过程的结果等方式来完成。
目标是确保解决方案可以解决问题并满足预期效果。
第七步:预防措施的推广在这一步骤中,团队将根据验证的解决方案扩大应用范围,并在整个组织中推广使用。
这可能包括培训员工、更新相关文件和程序等。
目标是确保类似的问题不再发生,并在组织中建立起可持续的改进机制。
第八步:表扬和奖励团队成员在解决问题的过程中,团队成员可能需要付出很大努力。
因此,在这一步骤中,团队领导应该表扬和奖励团队成员的工作。
这可以提高团队士气,并激励他们在以后更加积极地参与问题解决。
通过以上八个步骤,8D报告管理程序能够帮助组织有效地识别和解决问题。
这种程序不仅可以提高产品和过程质量,还可以提高组织的绩效和竞争力。
8D报告标准基准(八个步骤)

再发防止对策基准-8D1.0目的为明确产品质量改进的程序和内容,以提高产品质量改进的效率和效果,更好的满足顾客的要求,特制定本办法。
2.0适用范围本办法适用于公司质量改进。
3.0定义3.1现象:通过视觉/嗅觉/听觉/触觉等直觉方式,观察到的不良。
3.2问题:通过品质检查/试验等方法,反馈的与产品或过程基准的偏差。
3.3遏制措施:不良现象反馈的当时当地,采取的紧急措施,防止事态扩大化。
3.4临时措施:针对不良现象采取的措施,防止事态持续化,为永久措施争取时间。
3.5永久措施:针对不良原因采取的措施,预防问题再发生。
3.6体系原因:涉及DFMEA、P-FMEA、图纸、CP(控制计划)、WI(作业指导书)、MP(维护计划)等技术文件的失效/过期/缺失3.7物理原因:产品和产品实现过程所涉及实体的失效/过期/缺失等,包括产品、工装、设备等。
4.0 相关文件《不合格品控制程序》《进料检验控制程序》《信息沟通控制程序》5.0职责5.1品质部:品质工程师负责主导8D报告的填写6.0 作业程序6.1 品质工程师接到下述信息,在PDCA中登录,启动8D。
·客诉(0KM/售后)·1个月后1年内重复出现的过程问题。
6.2按8D的方法及步骤要求,实施行动,并填写对应8D项目,具体填写要求以及工具应用见《8D填写说明+支持资料》)。
6.3向客户提交报告前,必须提交品质部经理确认后提交。
6.4向客户提交报告。
6.5每月底,8D报告作为质量信息登记台帐的附件,提交资料员归档。
6.6 8D编码要求6.6.1规则为车型号+产品分类+年+月+日+流水号 例:R103HSJ201812501①车型号:直接借用客户车型②产品分类:后视镜:HSJ 拉手:LS 灯具:DJ 装饰件:ZSJ 其它:QT③年:4位数字,日历年④月:二位数字,日历月⑤日:二位数字,日历日6.6.28D编码由质量体系管理员统一编码,并登记于《信息跟踪管理台帐》(模版见《不合格品控制程序》附件),与质量信息一起按《信息沟通控制程序》要求传递到相应的品质工程师处,品质工程师在编制8D报告编码时,保持与质量信息登记台帐的8D编码保持一致。
8D报告的流程及关键事项

在生产前测试方案,并对方案进行评审以确定所选 的校正措施够解决客户问题,同时对其它过程不 会有不良影响。
重新审视小组成员资格;决策,选择最佳措施;重新评估临时措施,如必要重新 选择;验证;管理层承诺执行永久纠正措施;控制计划 。(永久措施要不产生新 的故障;永久措施经验证能够起效)
保证在永久纠正措施实施前,将问题与内外部顾客 隔离。
用统计工具列出可以用来解释问题起因的所有潜在 原因,将问题说明中提到的造成偏差的一系列事件 或环境或原因相互隔离测试并确定产生问题的根本 原因。
评价紧急响应措施;找出和选择最佳“临时抑制措施”;决策;实施,并作好记 录;验证(DOE、PPM分析、控制图等);临时方案要能够消除对内外部顾客的 影响
成员资格,具备工艺、产品的知识;目标 ;分工 ;程序 ;小组建设
收集和组织所有有关数据以说明问题;问题说明是所描述问题的特别有用的数 据的总结;审核现有数据,识别问题、确定范围;细分问题,将复杂问题细分为 单个问题;问题定义,找到和顾客所确认问题一致的说明,“什么东西出了什 么问题”,而原因又未知风险等级。
8D报告的流程及关键点
8D步骤
目的
关键点
D0:8D程序的准备
D1:组建8D工作团队
D2:问题描述
D3:制定临时措施
D4:定义并验证根本 原因和忽略点 D5:选择并确定永久 措施 D6:执行并验证永久 措施
是一种紧急反应措施。主要是为了判定此类问题是 否需要使用8D来解决。与D3不同,D0是针对问题发 生的反应,而D3是针对产品或服务问题本身的暂时 应对措施。
FMEA、防错、SPC、PPAP
D7:预防问题的重现
8D报告过程以及8D是指的什么讲解
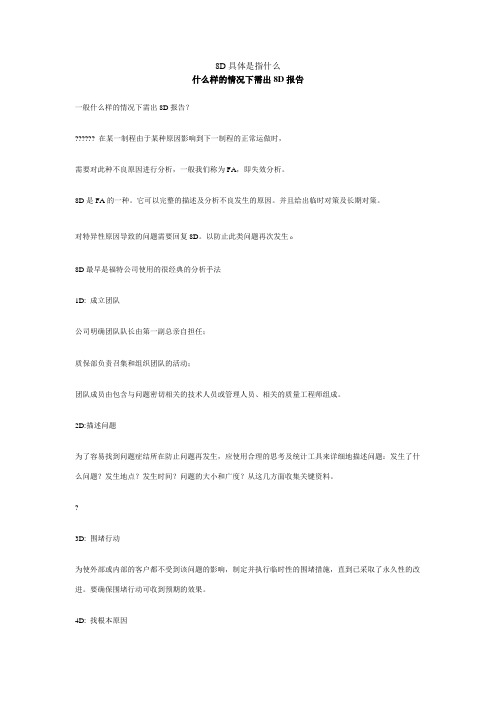
8D具体是指什么什么样的情况下需出8D报告一般什么样的情况下需出8D报告?在某一制程由于某种原因影响到下一制程的正常运做时,需要对此种不良原因进行分析,一般我们称为FA,即失效分析。
8D是FA的一种。
它可以完整的描述及分析不良发生的原因。
并且给出临时对策及长期对策。
对特异性原因导致的问题需要回复8D。
以防止此类问题再次发生。
8D最早是福特公司使用的很经典的分析手法1D: 成立团队公司明确团队队长由第一副总亲自担任;质保部负责召集和组织团队的活动;团队成员由包含与问题密切相关的技术人员或管理人员、相关的质量工程师组成。
2D:描述问题为了容易找到问题症结所在防止问题再发生,应使用合理的思考及统计工具来详细地描述问题:发生了什么问题?发生地点?发生时间?问题的大小和广度?从这几方面收集关键资料。
3D: 围堵行动为使外部或内部的客户都不受到该问题的影响,制定并执行临时性的围堵措施,直到已采取了永久性的改进。
要确保围堵行动可收到预期的效果。
4D: 找根本原因就问题的描述和收集到的资料进行比较分析,分析有何差异和改变,识别可能的原因,测验每一个原因,以找出最可能的原因,予以证实。
5D: 永久性纠正针对已确认的根本原因制订永久性的纠正措施,要确认该措施的执行不会造成其它任何不良影响。
6D: 验证措施执行永久性的纠正措施,并监视其长期效果7D:预防再发生修正必要的系统,包括方针、运作方式、程序,以避免此问题及类似问题的再次发生。
必要时,要提出针对体系本身改善的建议。
8D: 肯定贡献完成团队任务,衷心地肯定团队及个人的贡献,并加以祝贺。
由最高领导者签署8D的流程D1-第一步骤: 建立解决问题小组若问题无法独立解决,通知你认为有关的人员组成团队。
团队的成员必需有能力执行,例如调整机器或懂得改变制程条件,或能指挥作筛选等。
D2-第二步骤: 描述问题向团队说明何时、何地、发生了什么事、严重程度、目前状态、如何紧急处理、以及展示照片和收集到的证物。
质量管理8D报告培训(经典教材)含案例分析

四. 8D步骤-D7效果确认及标准化
效果确认 实事求是,以事实和数据为依据,对数据用统计工具处 理后得出相应的结论,不应未做对比分析即判定效果。
16.00% 14.00% 12.00% 10.00%
8.00% 6.00% 4.00% 2.00% 0.00%
slot1
slot2
slot3
slot4
slot5
按需要调整 团队成员
四. 8D步骤—D2问题描述
以客户的角度和观点详细描述其所感受到的问题现象, 将所遭遇的问题,以量化的方式,明确出所涉及的人, 事,时,地,为何,如何,多少。
什么是问题???
问期题望
期望 目标
现实
四. 8D步骤—D2问题描述
问题描述方法:5W/2H
WHO WHAT
5W2H 谁
1. 报警按钮未启动三方通话联系到监控中心:NG 2. 事后报警按钮测试(第一次正常,第二次不正常,拆
开后检查发现触点接触不良):NG 3. 警铃不响 电梯只有三方通话功能(国标无强制要求
需警铃鸣响功能) :OK 4. 话筒铃声及功能正常(事后测试):OK
1. 光电感应器位置偏离 导致无信号输出:NG
什么
解释 识别那一个客户(内/外部)在抱怨
问题的症状,无法用文字描述清楚的,借助 于数字或图片将问题表达清楚
WHEN WHERE WHY HOW
何时 何地 为什么 怎么样
记入问题发生的日期 记入问题发生的场所 识别已知的解释 在什么的模式或状态这问题会发生
HOW MUCH
什么程度
问题发生的程度、量
13
三. 何时采用8D
重复发生,一直没有解决的问题 比较重大的制程品质问题 客户要求回复的品质投诉
8D流程
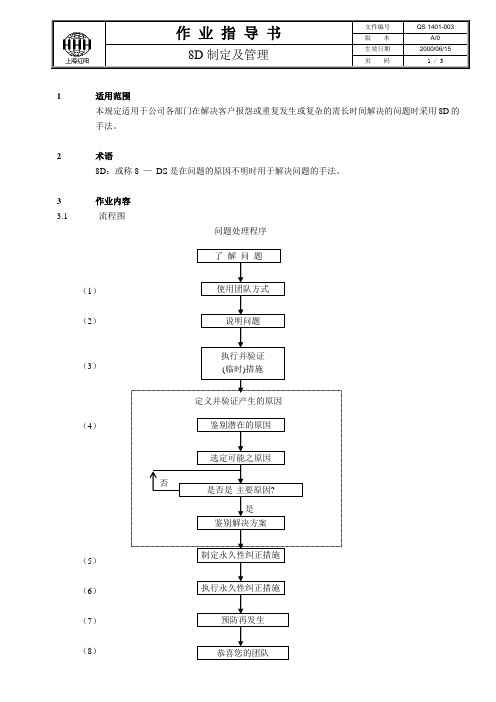
1适用范围本规定适用于公司各部门在解决客户报怨或重复发生或复杂的需长时间解决的问题时采用8D 的手法。
2 术语8D :或称8 — DS 是在问题的原因不明时用于解决问题的手法。
3 作业内容 3.1 流程图问题处理程序(1)(2)(3)(4)(5)(6)(7)(8)3.2职责3.2.1顾客抱怨的解决,由质保部组织成立8D小组,主导实施8D解决问题。
3.2.2各部门负责组织成立8D小组,采用8D解决问题。
3.3方法3.3.18D的实施3.3.1.1先了解问题,确定问题所在3.3.1.2使用团队方式:组建一个了解过程/产品的小组,小组应4至10人,小组成员了解过程/产品,并具有相当的经验和技能。
小组成员应来自于质保部、技术部、生产部、经销部、采购部等,必要时,可邀请顾客参加。
小组应选定一位组长。
组长应能协调市小组成员或各相关部门间的工作,并有一定的决策权。
3.3.1.3问题描述:明确描述问题是否是内部、外部或顾客,具体说明什么事件,何时、何地、那里、为何、如何、多少数量即(5W2H)。
描述问题应作到清楚、准确、以保证理解的一致性。
3.3.1.4临时措施:制订并执行临时措施,减轻问题对顾客的不良影响。
临时措施的执行应持续到实施永久性纠正措施为止。
采取措施如:100%检验、在发货前进行出厂检验、通知顾客等。
临时措施应确定生效日期。
对于临时措施必须验证其有效性,确定是否真正降低了影响。
3.3.1.5主要原因分析:鉴别所有可能导致问题发生的原因,找出根本原因,并验证其是否真正是根本原因。
采用头脑风暴法(各抒已见),围绕着人、机、料、法、环,五大因素进行分析。
对于原因应当确定其影响程度(即占问题的百分比)。
3.3.1.6制订永久性纠正措施:制定永久性纠正措施,并在实施以前评估其有效性,必要时可采用FMEA。
制订永久性纠正措施必须确定实施部门和实施人员以及完成期限。
永久性纠正措施的验证应评估该措施是否能解决问题。
8D报告过程及流程

8D报告过程及流程目录一、8D报告经典的分析手法 (1)1D: 成立团队 (1)2D:描述问题 (1)3D: 围堵行动 (2)4D: 找根本原因 (2)5D: 永久性纠正 (2)6D: 验证措施 (2)7D:预防再发生 (2)8D: 肯定贡献 (2)二、8D报告的流程 (2)D1-第一步骤: 建立解决问题小组 (2)D2-第二步骤: 描述问题 (2)D3-第三步骤: 执行暂时对策 (2)D4-第四步骤: 找出问题真正原因 (3)D5-第五步骤: 选择永久对策 (3)D6-第六步骤: 执行及验证永久对策 (3)D7-第七步骤: 防止再发 (3)D8-第八步骤: 团队激励 (3)什么样的情况下需出8D报告?在某一制程由于某种原因影响到下一制程的正常运做时,需要对此种不良原因进行分析,一般我们称为FA,即失效分析。
8D是FA的一种。
它可以完整的描述及分析不良发生的原因。
并且给出临时对策及长期对策。
对特性原因导致的问题需要回复8D。
以防止此类问题再次发生。
一、8D报告经典的分析手法1D: 成立团队公司明确团队队长由第一副总亲自担任;质保部负责召集和组织团队的活动;团队成员由包含与问题密切相关的技术人员或管理人员、相关的质量工程师组成。
2D:描述问题为了容易找到问题症结所在防止问题再发生,应使用合理的思考及统计工具来详细地描述问题:发生了什么问题?发生地点?发生时间?问题的大小和广度?从这几方面收集关键资料。
3D: 围堵行动为使外部或内部的客户都不受到该问题的影响,制定并执行临时性的围堵措施,直到已采取了永久性的改进。
要确保围堵行动可收到预期的效果。
4D: 找根本原因就问题的描述和收集到的资料进行比较分析,分析有何差异和改变,识别可能的原因,测验每一个原因,以找出最可能的原因,予以证实。
5D: 永久性纠正针对已确认的根本原因制订永久性的纠正措施,要确认该措施的执行不会造成其它任何不良影响。
6D: 验证措施执行永久性的纠正措施,并监视其长期效果7D:预防再发生修正必要的系统,包括方针、运作方式、程序,以避免此问题及类似问题的再次发生。
苹果公司8D报告流程

8D报告填写方法作为SQE,审核供应商的8D可以说是家常便饭;作为供应商撰写8D报告也是对客户质量问题的有效合理的回复;那么8D背后又有哪些支持性的工作需要完成才能将8D进行的有理有据呢我们来梳理一下8D;;;D1:小组成立目的:成立一个小组,小组成员具备工艺/产品的知识,有配给的时间并授予了权限,同时应具有所要求的能解决问题和实施纠正措施的技术素质;小组必须有一个指导和小组长;关键要点: 成员资格,具备工艺、产品的知识;目标 ;分工 ;程序 ;小组建设D2:问题说明用量化的术语详细说明与该问题有关的内/外部顾客抱怨,在这里需要客户提供真实有效具体的5W2HWhat happened 到底发生了什么Why is it a problem 为什么这是一个问题When detected 什么时候发现的这个问题Who detected 是谁发现了这个问题Where detected 在那里发现了这个问题How detected 问题是怎么发现的How many bad parts 一共发现了多少件不良品在这里,客户最好能提供好件和坏件,如果不能及时的提供缺陷件最好能提供好件和坏件的同一个视角的对比照片或者视频;供应商拿到相关的量化描述后,首先在内部进行批次信息的追溯,同时对外输出量化的信息,其中一般包括以下的输出信息:What is the difference between good and bad parts 好件和坏件的区别在哪里最好量化;Was part produced in the standard process 追溯问题件是不是在正常的生产过程中生产的When was it manufactured at Supplier 确定不良件的具体生产日期Who manufactured 确定不良件是谁做的;In which other application or processes product is used 确定不良件的生产是否有其他的过程或工艺被应用Are we capturing the defect when rejecting product in normal process 在正常的生产过程中是否可以发现目前的不良Did a similar problem happen previously at customer or internally问题是否在以前出现过关键要点:收集和组织所有有关数据以说明问题;问题说明是所描述问题的特别有用的数据的总结;审核现有数据,识别问题、确定范围;细分问题,将复杂问题细分为单个问题;问题定义,找到和顾客所确认问题一致的说明,“什么东西出了什么问题”,而原因又未知风险等级; D3:实施并验证临时措施保证在永久纠正措施实施前,将问题与内外部顾客隔离;原为唯一可选步骤,但发展至今都需采用方法:FMEA、DOE、PPM关键要点: 评价紧急响应措施;找出和选择最佳“临时抑制措施”;决策 ;实施,并作好记录;验证DOE、PPM分析、控制图等在这里需要明确针对问题的批次进行立即措施进行遏制,需要对客户产线上,库房内,在途,在库内的所有产品进行隔离,防止不良的继续流出,这里最常用的方法是挑选或者换货,如果产品是批量的质量问题,那么换货或者返工是最有效的临时措施,总而言之不能造成客户端的停线;在这里,挑选或者返工必须制定科学合理的方法,如有必要需要设计开发相应的规或者治具,其中挑选或者返工不能产生新的不良;D4:确定并验证根本原因用统计工具列出可以用来解释问题起因的所有潜在原因,将问题说明中提到的造成偏差的一系列事件或环境或原因相互隔离测试并确定产生问题的根本原因;方法:FMEA、PPM、DOE、控制图、5why法、FTA关键要点: 评估可能原因列表中的每一个原因;原因可否使问题排除;验证;控制计划在这里最重要的工作就是找到问题的根本原因,最常用的工具就是FTA,5why .分析分为2大块:产生原因和流出原因,即不合格产品为什么会产生和不合格产品为什么会流出到客户端;其中FTA需要将4M进行详细的分析,选择控制点,控制标准,好件和坏件与标准要求是否一致,最终得出结论:控制标准是否合理/好件和坏件是否符合标准/控制点是否与质量问题的产生有关;针对FTA分析出来的确凿的控制点进行5why 的分析,找到问题的根本原因;针对分析出来的问题根本原因,需要做生产再现来验证控制点的失控的确可以造成不良,这样就可以从问题的再现核实问题的根本原因; D5:选择并验证永久纠正措施重新审视小组成员资格;决策,选择最佳措施;重新评估临时措施,如必要重新选择;验证;管理层承诺执行永久纠正措施;控制计划D6:实施永久纠正措施制定一个实施永久措施的计划,确定过程控制方法并纳入文件,以确保根本原因的消除;在生产中应用该措施时应监督其长期效果;方法:防错、统计控制关键要点: 重新审视小组成员;执行永久纠正措施,废除临时措施;利用故障的可测量性确认故障已经排除;控制计划、工艺文件修改D7:预防再发生目的:修改现有的管理系统、操作系统、工作惯例、设计与规程以防止这一问题与所有类似问题重复发生;这里多数企业会撰写Lessons Learn 并分享到整个工厂,让每一条产线都知晓问题并防止类似问题的重复出现;关键要点:选择预防措施;验证有效性;决策 ;组织、人员、设备、环境、材料、文件重新确定D8:小组祝贺目的:承认小组的集体努力,对小组工作进行总结并祝贺;关键要点: 有选择的保留重要文档;流览小组工作,将心得形成文件;了解小组对解决问题的集体力量,及对解决问题作出的贡献;必要的物质、精神奖励;。
8D管理

8D报告步骤分解,你看完就会做了!2017-11-09提到8D,大家会说出哪8个步骤,但是需真正去理解其精髓。
因为在工作中我们需要的是一份能真正对问题解决改善有效果的实质性8D报告,而不是一份文件。
8D起源于福特公司处理质量问题的一种方法。
凡是福特公司的供应商遇到问题必须强制用这种方法。
后来这方法好,其他的非福特公司的供应商也引进这方法处理问题。
就这样家喻户晓,各行业通吃。
而且不仅仅解决工作问题,解决家庭生活问题也很有效。
在这里仅分享下8D在处理质量问题上的应用。
1D0 现象及应急反应活动根据现象评估8D过程是否需要。
如果有必要,采取紧急反应行动(ERA)来保护顾客,并开始8D过程。
8D过程区别了症状和问题。
适用标准的大部分是症状。
没有症状,不会知道有问题。
症状是一个显示存在一个或多个问题的可测量的事件或结果。
这个事件的后果必须被一个或多个顾客经历;问题是指同期望有偏差或任何由未知原因引起的有害的后果;症状是问题的显示。
当收到投诉信息时,质量部门应尽量在客户投诉报告上确认以下信息以便展开调查:·产品编号及品名·客户名称,联系人及地址·缺陷描述,不合格品数量·追溯信息,如LOT NO,发货单编号等·索赔应尽量取得车型等信息如有,应从客户处得到样品,照片,标签及不合格率等必要的信息。
如是芯体泄露或严重投诉,收到投诉的人应立即通知质量经理及总经理。
QE应在收到投诉一个工作日内与客户联系。
应就以下信息与客户沟通:·跨部门小组及联系方式·确认已得到的信息·调查问题所必需的其他信息·应急措施的进展·应急措施及纠正措施的预期完成时间·任何其它的客户要求,如,了解问题进展和期望的交货·所有与客户之间的回复均应记录。
QE根据得到信息,依据三现主义(现场,现物,现象)来确认不良状况;如果是可以目视的不良,尽量取得照片或样品(确认现物);对于不良发生场所状况尽量收集详细的情报(确认现场,现象)。
8D报告过程以及8D是指的什么讲解
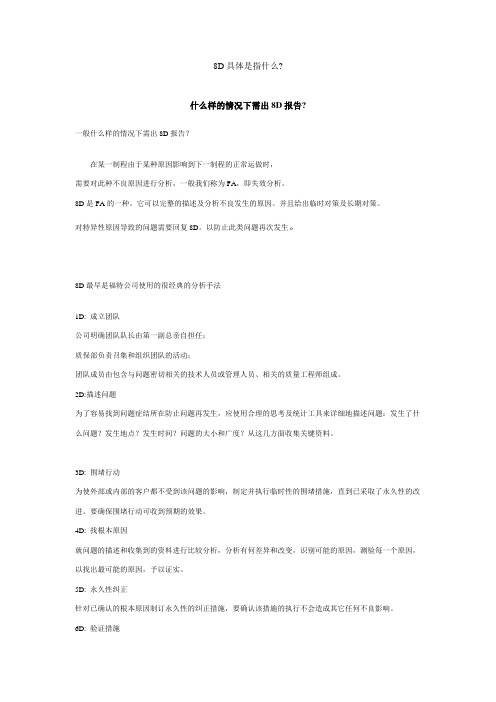
8D具体是指什么?什么样的情况下需出8D报告?一般什么样的情况下需出8D报告?在某一制程由于某种原因影响到下一制程的正常运做时,需要对此种不良原因进行分析,一般我们称为FA,即失效分析。
8D是FA的一种。
它可以完整的描述及分析不良发生的原因。
并且给出临时对策及长期对策。
对特异性原因导致的问题需要回复8D。
以防止此类问题再次发生。
8D最早是福特公司使用的很经典的分析手法1D: 成立团队公司明确团队队长由第一副总亲自担任;质保部负责召集和组织团队的活动;团队成员由包含与问题密切相关的技术人员或管理人员、相关的质量工程师组成。
2D:描述问题为了容易找到问题症结所在防止问题再发生,应使用合理的思考及统计工具来详细地描述问题:发生了什么问题?发生地点?发生时间?问题的大小和广度?从这几方面收集关键资料。
3D: 围堵行动为使外部或内部的客户都不受到该问题的影响,制定并执行临时性的围堵措施,直到已采取了永久性的改进。
要确保围堵行动可收到预期的效果。
4D: 找根本原因就问题的描述和收集到的资料进行比较分析,分析有何差异和改变,识别可能的原因,测验每一个原因,以找出最可能的原因,予以证实。
5D: 永久性纠正针对已确认的根本原因制订永久性的纠正措施,要确认该措施的执行不会造成其它任何不良影响。
6D: 验证措施执行永久性的纠正措施,并监视其长期效果7D:预防再发生修正必要的系统,包括方针、运作方式、程序,以避免此问题及类似问题的再次发生。
必要时,要提出针对体系本身改善的建议。
8D: 肯定贡献完成团队任务,衷心地肯定团队及个人的贡献,并加以祝贺。
由最高领导者签署8D的流程D1-第一步骤: 建立解决问题小组若问题无法独立解决,通知你认为有关的人员组成团队。
团队的成员必需有能力执行,例如调整机器或懂得改变制程条件,或能指挥作筛选等。
D2-第二步骤: 描述问题向团队说明何时、何地、发生了什么事、严重程度、目前状态、如何紧急处理、以及展示照片和收集到的证物。
8D报告解决问题的八个步骤
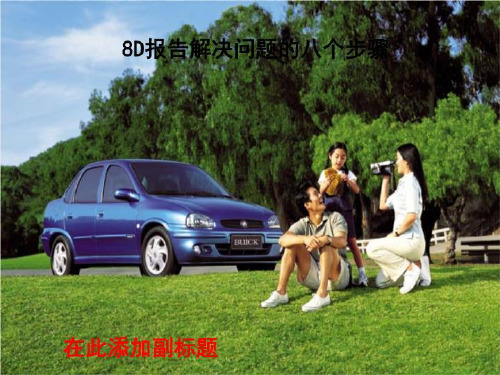
品质控制流程图
品质控制流程图
开始
供应商评审
不合格供应商
采购原材料
特
退供应商要求改善
来料 检验
ok
入库存储
NO 让步
采
发料生产
生产过程分析与改进
调机获 试产
NO
首检
全检重返工返修
工序生产
工序自检
调查分析/落实责任 采取纠正/预防措施
顾客满意 顾客满意度调查
记C 巡检
业务受理 顾客抱怨
品质部(出货报告统一采用我司提供的报告格式),通知我司品 质部进行验货。
出货要求
❖ 1、品质部负责对出货产品的品质进行检验,依据相应图纸、 成品检验指导书,在出货前对所有出货产品进行品质检验, 并记录相关的检验和测量结果,出据书面的《出货检验报 告》。
❖ 2、品质部根据《出货检验报告》的结果对不合格物料按不 合格品处理程序进行返工、全检。返工、全检后再次对物料 做出货检验确认,物料确认合格后将《出货检验报告》(Email电子文档)到客户品质部,然后进行发货给客户。
分析步骤
❖ 第一为P(计划)阶段,其中又分为4个步骤: (1) 分析现状,找出存在的主要质量问题。 (2) 分析产生质量问题的各种影响因素。 (3) 找出影响质量的主要因素。 (4) 针对影响质量的主要因素制订措施,提出
改进计划,定出质量目标。
第二为D(实施)阶段
❖
(5) 按照既定计划目标加以执行。
品质控制要点
❖ c、终检(FQC)
❖ 检验方式(全检、抽检)
❖ 检验标准:图纸、样品、检验指导书 ❖ 检验报告 ❖ 首未件对比
❖ 三、出货检验OQC
❖ 检验标准:图纸、样品、检验指导书、品质控制计划; ❖ 抽样数量:按照(标准MIL-STD-105EⅡ)进行; ❖ 品质异常的处理与跟进(不合格品处理流程) ❖ 检验的方法:检具、试配 ❖ 表面处理要求:热处理、电镀、氧化。。。。。 ❖ 产品出货前一周提供全尺寸的《出货检验报告》给我司(顺荣)
8D报告管理规定

编制:朱松林审核:戴宝泉一、范围:该方法适用于解决各类可能遇到的简单或复杂的问题。
8D方法就是要建立一个体系,让整个团队共享信息,努力达成目标;8D本身不提供成功解决问题的方法或途径,但它是解决问题的一个很有用的工具。
二、目标提高解决问题的效率,积累解决问题的经验;提供找出现存的与质量相关问题的框架,杜绝或尽量减少重复问题出现。
8D格式的原则是针对出现的问题,找出问题产生的根本原因,提出短期,中期,和长期对策,并采取相应行动措施。
还需进一步挖掘深层次的问题(管理原因,组织架构原因等)和横向展开分析对策。
三、定义(1) 8D (8 Disciplines) 方法包含8个解决问题的步骤;它基于使用描述工具、格式化、分析、量化等工具,从而提供彻底解决问题的指引。
(2)问题: 被发现的具体问题,它包括:a、与正常状况相比,属于失常的现象,在这种情况下,需要予以纠正,使其恢复初始正常状况。
b、为提高质量的目的而改变目前的状况。
(3)纠正措施: (按ISO/TS16949:2009标准定义) 组织应采取措施,以消除不合格的原因,防止不合格的再发生。
纠正措施应与所遇到不合格的影响程度相适应。
(4) 预防措施:(按ISO/TS16949:2009标准定义) 组织应确认措施,以消除潜在不合格的原因,防止不合格的发生。
预防措施应与潜在问题的影响程度相适应。
四、在下列情形中须提交8D报告:(1)当客户在工厂现场的稽核中发现不合格项或缺陷时,对于严重不良,主要不良及重复发生的次要不良须提交8D报告。
(2)QC发现严重不良,主要不良及重复发生的次要不良时须提交8D报告。
(3)当市场上发现有重复发生的产品缺陷时须提交8D报告。
(4) QC在同一生产现场连续发现三个位置相同不良现象或三个原因相同不良现象。
(5)要对那些需要长期纠正措施来解决的缺陷采取行动时,须提交8D报告。
(6)被相关程序文件明确要求提交8D报告时。
(7) 8D报告应得到客户的认可,同时后续跟踪验证,填写《品质纠正和预防措施处置表》。
8D报告培训教材(经典)

析和方案策划。
四. 8D步骤—D1建立小组
建立一个小组来解决问题和执行纠正计划, 小组成员应具有过程和/或产品知识、分配的 时间、权威和需要的技能。
建立小组需要考虑的要素:
小组的领导: 小组的资源: 小组的成员: 人员的数量:
谁来推动? 谁提供支持? 合作及分工? 多少为宜?
备注:广泛用于QS9001/ ISO9001/ TS16949 (变更为
IATF16949/VDR6.3)解决质量问题的8D isciplines。
一.什么是8D
以团队运作导向以事 实为基础,避免个人 主见之介入,使问题 之解决能更具条理。
面对问题应群策群力, 互相帮助、相互提拔、 如此才能彻底解决问题。
• 确定并执行应先采取的临时措施,以遏制外界/内部客 户问题的扩大。
• 临时措施的确定应考虑从供应商零件库存---供应商零 件在途品--内部零件/材料—生产制程—仓库储存—交 付在途品—客户端减少和降低(消除)后果的产生。
• 临时措施一直要持续实施至后续的永久对策的执行有 效后,方可撤消。
• 临时措施实施中,应及时跟踪和验证其效果。
五.8D改善案例
D0.了解问题
2009年11月4日“众盛精密机械厂”投诉,在其包装 车间对“ALT-5检测器”进行包装时,使用公司的MHT 机用膜时一拉就断裂, 并发现使用的机用膜端口破裂 。造成ALT-5检测器包装工作进度延误,顾客要求派 人处理。
五.8D改善案例
D1.成立小组
•按问题涉及范围确定小组成员: •责属单位:生管部、业务部、仓储部、品管部 •责属人员:
五.8D改善案例
D5.长期对策
5.1决定采用长期对策
如何写8D报告什么是8D报告

如何写8D报告,什么是8D报告8D 的原名叫做8 Eight-Disciplines,意思是8 个人人皆知解决问题的固定步骤;也可以称为TOPS(TeamOriented problem solving)即团队导向问题解决方法。
8D主要用于汽车及类似加工行业的问题解决方法。
原始是由Ford 公司,全球化品质管制及改善的特殊必备方法,之后已成为QS9000/ISO TS16949、福特公司的特殊要求。
(一)9个步骤8D是解决问题的8条基本准则或称8个工作步骤,但在实际应用中却有9个步骤:D0:征兆紧急反应措施D1:小组成立D2:问题说明D3:实施并验证临时措施D4:确定并验证根本原因D5:选择和验证永久纠正措施D6:实施永久纠正措施D7:预防再发生D8:小组祝贺(二)3个问题SQE在给供应商做8D报告的培训的时候,必须跟供应商讲清楚,作为供应商在撰写8D报告的时候,务必要保证下面的问题被清楚准确有理有据地回答:D2-问题是什么?D3~D6-问题如何解决?D7-将来该问题如何预防(三)7个问题然而作为SQE在审阅供应商的8D报告的时候,也务必保证以下的问题被如实回答:1.对零件的知识进行了充分的论证2.完全确定了根本原因并聚焦于该原因3.遗漏点已经被识别4.确定与根本相匹配的纠正措施5.纠正措施计划的验证已经被确定6.包括了实施纠正措施的时间计划7.有证据显示供方将把纠正措施纳入整个系统。
(四)质量工具8D的实施过程可能用到的质量工具总结如下:可靠性/设计验证DV/产品和过程确认/潜在失效模式及后果分析FMEA/控制计划CP/PPAP 文件/SPC/DOE/QC7大工具D0:征兆紧急反应措施目的:主要是为了看此类问题是否需要用8D来解决,如果问题太小,或是不适合用8D来解决的问题,例如价格,经费等等,这一步是针对问题发生时候的紧急反应。
关键要点:判断问题的类型、大小、范畴等等。
与D3不同,D0是针对问题发生的反应,而D3是针对产品或服务问题本身的暂时应对措施。
8D报告的管理程序

8D报告的管理程序8D报告管理程序是一种常用的质量管理工具,用于解决问题和改进产品或过程的质量。
以下是一个典型的8D报告管理程序的步骤和流程,以确保问题得到有效解决。
第一步:确定问题在此阶段,团队需要明确识别问题,并确保对于问题的描述准确无误。
必要时,可以使用流程图、鱼骨图等方法进行问题分析和确定。
第二步:组建团队组建一个跨部门的团队,包括专家、质量控制人员、工程师和相关领导,以确保能够全面、全面地解决问题。
确保团队成员具备解决问题所需的技能和知识。
第三步:紧急措施在确定问题后,团队需要立即采取紧急措施来防止问题扩大或进一步影响产品或过程。
这些紧急措施需要在最短时间内实施,以保证质量和客户满意度。
第四步:根本原因分析团队需要使用合适的工具和方法,例如5W1H、5Why、故障模式和影响分析(FMEA)等,来确定问题的根本原因。
这需要广泛的数据收集和分析,以便确定正确的根本原因。
第五步:制定长期解决方案在根本原因分析之后,团队需要制定长期解决方案来解决问题。
这可能包括制定和实施新的工艺、流程或设计变更,以防止问题再次发生。
第六步:验证解决方案在制定长期解决方案后,团队需要验证其有效性。
这可以通过实施试验、数据收集和分析来完成。
验证解决方案的目的是确保其符合预期,能够解决根本原因和问题。
第七步:预防措施在验证解决方案后,团队需要制定预防措施,以确保问题不会再次发生。
这可能涉及到培训员工、改进工艺流程、更新文件和规程等措施。
第八步:庆祝和认可最后一步是庆祝和认可团队的努力和成果。
这有助于激励团队继续提高质量,并鼓励其他团队效仿并使用8D方法来解决类似或其他问题。
总结:通过遵循典型的8D报告管理程序,组织可以有效地解决问题,并改进产品或过程的质量。
这种方法强调团队合作和数据驱动的决策,有助于确保问题的根本原因得到解决,并采取预防措施以防止再次发生。
8D报告的内容及使用说明

8D报告的内容及使用说明一、引言。
8D报告是一种用于解决问题和改进过程的工具,它包含了一系列的步骤和方法,用于识别问题、分析原因、制定解决方案以及跟踪改进的进展。
本报告将介绍8D报告的内容及使用说明,以帮助团队更好地理解和应用这一工具。
二、8D报告的内容。
1. D1-建立团队。
在这一步骤中,团队需要确定问题的范围和影响,并组建一个跨职能的团队来处理问题。
团队成员需要具备分析问题和制定解决方案的能力。
2. D2-描述问题。
团队需要详细描述问题的现象和影响,包括问题的发生时间、频率、影响范围等。
同时,需要收集相关的数据和信息,以便后续分析和解决问题。
3. D3-制定临时措施。
在这一步骤中,团队需要制定临时措施来控制问题的影响,以保证生产和客户的利益。
这些措施可能包括暂停生产、更换零部件等。
4. D4-识别根本原因。
团队需要使用适当的工具和方法,如5W1H分析、鱼骨图等,来识别问题的根本原因。
这一步骤非常关键,因为只有找到根本原因,才能制定有效的解决方案。
5. D5-制定永久解决方案。
基于根本原因的分析,团队需要制定永久的解决方案,以避免问题再次发生。
这可能需要改进工艺、修改设计、加强培训等。
6. D6-实施解决方案。
团队需要在生产线上实施解决方案,并监控其效果。
同时,需要培训相关人员,确保他们能够正确执行新的工艺和程序。
7. D7-验证效果。
团队需要验证解决方案的效果,确保问题得到了根本的解决。
这可能需要进行实验、测试和数据分析。
8. D8-预防措施。
最后,团队需要制定预防措施,以避免类似问题再次发生。
这可能包括改进质量管理体系、加强供应链管理等。
三、使用说明。
1. 确保团队成员具备相关的培训和技能,以便他们能够正确地使用8D报告来解决问题。
2. 在每一步骤中,团队需要充分收集数据和信息,以便做出准确的分析和决策。
3. 团队需要严格按照8D报告的步骤和方法来操作,确保问题得到根本的解决。
4. 每一步骤需要有明确的责任人,以便监督和跟踪工作的进展。
- 1、下载文档前请自行甄别文档内容的完整性,平台不提供额外的编辑、内容补充、找答案等附加服务。
- 2、"仅部分预览"的文档,不可在线预览部分如存在完整性等问题,可反馈申请退款(可完整预览的文档不适用该条件!)。
- 3、如文档侵犯您的权益,请联系客服反馈,我们会尽快为您处理(人工客服工作时间:9:00-18:30)。
二、 范围
该方法适用于解决各类可能遇到的简单或复杂的问题。 8D方法就是要建立一个体系,让整个团队共享信息,努力达成目标;8D本身不提供成功解决问题的方法或途径,但它是解决问题的一个很有用的工具。
(3)纠正措施: 针对现存的不合格项或缺陷所采取的纠正措施,并杜绝或尽量减少重复问题出现。
(4) 预防措施:针对潜在的不合格项或缺陷所采取的纠正措施,并杜绝或尽量减少重复问题出现。
四、在下列情形中须提交8D报告:
(1)当客户在工厂现场的稽核中发现不合格项或缺陷时,对于严重不良,主要不良及重复发生的次要不良须提交8D报告。
XX有限公司
编号:QG/ZG04-112-2019
8D报告管理程序
(版本:01)
拟制:
审核:
批准:
日期:
2019-06-21发布2019-06-21实施
XX科技有限公司
名称
8D报告管理规范
文件编号
QG/ZG04-113-2010
版本:
01
生效日期
2019-06-21
页数
1/2
一、目标
为提高解决问题的效率,积累解决问题的经验;提供找出现存的与质量相关问题的框架,杜绝或尽量减少重复问题出现。
(2)成品检验发现严重不良,主要不良及重复发生的次要不良时须提交8D报告。
(3)当市场上发现有重复发生的产品缺陷时须提交8D报告。
(4) 当产品测试或试验过程中发现缺陷时须提交8D报告。
(5)制成检验员在同一生产现场连续发现三个位置相同不良现象或三个原因相同不良现象。
(6)要对那些需要长期纠正措施来解决的缺陷采取行动时,须提交8D报告。
关注的问题被解决、确认、核实以及被权威人士审核签名通过并存盘。
当分析完成,列出您认为最有可能的几项,再逐一动手作些调整改变,并且观察那一些改变可使品质回复正常及影响变异的程度,进而找到问题真正的原因。这就是著名田口式方法最简单而实际的运用。
D5-第五步骤:纠正行动
找到造成问题的主要原因后,即可开始拟出对策的方法。对策的方法也许有好几种,例如修理或更新模具。试试对可能的选择列出其优缺点,要花多少钱?多少人力?能持续多久?再对可能的方法作――最佳的选择,并且确认这样的对策方法不会产生其它副作用。
D2-第二步骤:问题描述
向团队说明何时、何地、发生了什么事、严重程度、目前状态、如何紧急处理、以及展示照片和收集到的证物。将证物、细节描述越清楚,团队解决问题将越快。
D3-第三步骤:临时对策
若真正原因还未找到,暂时用什么方法可以最快地防止问题?如全检、筛选、将自动改为手动、库存清查等。暂时对策决定后,即立刻交由团队成员带回执行。
(7)被相关程序文件明确要求提交8D报告时。
五、提交报告时间要求:
(1)在发现问题的24小时内,提交包含所采取的暂时措施描述的8DБайду номын сангаас告。
(2) 在发现问题的72小时内,提交包含问题发生原因的初步分析的8D报告。
名称
8D报告管理规范
文件编号
QG/ZG04-113-2010
版本:
01
生效日期
2019-06-21
页数
2/2
六、结论:
8D格式用于监控解决问题的过程,它不是一个详尽的报告或复杂的分析,描述工具,而是一个包含了解决问题的每个步骤的集合,因而可从其中找到经提炼的基本信息。
七、8D步骤
D1-第一步骤:团队成员
若问题无法独立解决,通知你认为有关的人员组成团队。团队的成员必需有能力执行,例如调整机器或懂得改变制程条件,或能指挥作筛选等。
D4-第四步骤:根本原因
找问题真正原因时,最好不要盲目地动手改变目前的生产状态,先动动脑。您第一件事是要先观察、分析、比较。列出您所知道的所有生产条件(即鱼骨图),逐一观察,看看是否有些条件走样,还是最近有些什么异动?换了夹具吗?换了作业员?换了供应商?换了运输商?修过电源供应器?流程改过?或比较良品与不良品的检查结果,看看那个数据有很大的差?,尺寸?重量?外观?性能?等等不良的发生,总是有原因,资料分析常常可以看出蛛丝马迹。这样的分析,可以帮助您缩小范围,越来越接近问题核心。
D6-第六步骤:效果验证
当永久对策准备妥当,则可开始执行及停止暂时对策。并且对永久对策作一验证,例如观察不良率已由4000 PPM降为300 PPM等,下工序及客户己能完全接受,不再产生问题。
D7-第七步骤:预防措施
对类似的其它生产,虽然尚未发生问题,亦需作同步改善,防止再发。
D8-第八步骤:结案确认:
三、定义
(1) 8D (8 Disciplines) 方法包含8个解决问题的步骤;它基于使用描述工具、格式化、分析、量化等工具,从而提供彻底解决问题的指引。
(2)问题: 被发现的具体问题,它包括:
a、与正常状况相比,属于失常的现象,在这种情况下, 需要予以纠正,使其恢复初始正常状况。
b、为提高质量的目的而改变目前的状况。