第8章 机床夹具的设计原理
机床夹具概述

第一节
机床夹具概述
4)加工中需先试切一段行程,测量尺寸, 根据测量结果再调整铣刀的相对位置, 直至达到要求为止。 5)每加工一个工件均重复上述步骤。 • 这种装夹方法不但费工费时,而且加工 出一批工件的加工误差分散范围较大。
第一节
机床夹具概述
采用夹具装夹方法,不需要进行划线就可把工件 直接放入夹具中去。工件的A面支承在两支承板2 上;B面支承在两齿纹顶 支承钉3上;端面靠在支 承钉4上,这样就确定了 工件在夹具中的位置, 然后旋紧螺母9通过压板 8把工件夹紧,完成了工 件的装夹过程。下一工 件进行加工时,夹具在 机床上的位置不动,只 需松开螺母9进行装卸工 件即可。
第一节
机床夹具概述
3.夹具的两个齿纹顶支承钉3的支承工作面 与两定位键侧面保持平行,也就使支承钉 3的支承工作面与铣 床纵向进给方向平行。 4.由于工件以B面与两 支承钉3的支承工作 面相接触,因而最终 保证了铣出的槽的侧 面与工件B面平行。
第一节
机床夹具概述
对尺寸精度的保证 1.夹具上装有对刀块5,利用对刀塞尺10塞入对刀 块工作面与立铣刀切削刃之间来确定铣刀相对夹 具的位置,此时可相应 横向调整铣床工作台的 位置和垂直升降工作台 来达到刀具相对对刀块 的正确位置。 2.由于对刀块的两个工 作面与相应夹具定位支 承板2和齿纹顶支承钉3 的各自支承面已保证和 尺寸,因而最终保证铣 出槽子的a和b尺寸。
不对应特定的加工对象,适用范 围宽,通过适当的调整或更换夹 通用可调 具上的个别元件,即可用于加工 夹具 形状、尺寸和加工工艺相似的多 种工件。 专为某一组零件的成组加工而设 计,加工对象明确,针对性强。 成组夹具 通过调整可适应多种工艺及加工 形状、尺寸。
第一节
机床夹具概述
举例说机床夹具的工作原理

举例说机床夹具的工作原理
机床夹具的工作原理是通过夹持工件固定在机床上,以确保工件在加工过程中保持稳定。
夹具可以根据工件的形状和尺寸进行设计和制造,其工作原理可以分为以下几种类型:
1. 机械夹具:
机械夹具是通过机械力对工件进行固定的夹具。
例如,机床中常见的机械钳、万能钳等。
夹具通过调节夹紧力和工件夹持位置来保持工件固定,通常使用螺杆、手柄等机械手段来实现调节。
2. 液压夹具:
液压夹具通过液压系统提供的液压力来夹紧工件。
工件放置在夹具中,当液压系统施加压力时,夹具的夹紧手段会对工件进行夹持。
液压夹具通常具有较高的夹紧力和精度,适用于大型工件的夹持。
3. 气动夹具:
气动夹具是通过气动力来夹紧工件。
夹具中装有气动真空吸盘或气动缸等气动元件,当气源施加压力时,气动元件会产生相应的力矩,使工件固定在夹具上。
4. 电磁夹具:
电磁夹具是利用电磁力对工件进行夹持。
夹具中装有电磁装置,工件放置在夹具上时,通电时电磁装置会产生磁力使工件保持固定。
以上只是机床夹具工作原理的一些常见类型,实际应用中还有许多其他不同工作原理的夹具。
不同类型的夹具适用于不同的加工需求,可以根据具体情况选择使用。
机械制造技术基础课件机床夹具设计原理

消除或减少过定位的方法主要有:
(1) 提高工件定位基准之间及定位元件工作表面之间的位置精度,减少过定位对加 工精度的影响,使不可用过定位变为可用过定位;
(2) 改变定位方案,避免过定位。改变定位元件的结构,如圆柱销改为菱形销、长 销改为短销等;或将其重复限制作用的某个支承改为辅助支承(或浮动支承)。
4.过定位
图4.5 连杆大头孔加工时工件在夹具中的定位
如图4.5所示的连杆定位方案,长销限制了
、 4个自由度,支承板
限制了
、 3个自由度,其中 被两个定位元件重复限制,这就产生了过定
位。当连杆小头孔与端面有较大的垂直度误差时,夹紧力F将使长销弯曲或使连杆
变形,见图4.5(b)、(c),造成连杆加工误差,这时为不可用过定位。若采用图4.5
4.1 机床夹具概述
4.1.4 机床夹具的功能
(1)保证工件的加工精度,稳定产品质量。机床夹具的首要任务是 保证加工精度,特别是保证被加工工件的加工面与定位面之间以及被加工 表面相互之间的尺寸精度和位置精度。使用夹具后,这种精度主要靠夹具 和机床来保证,不再依赖于工人的技术水平。
(2)提高劳动生产率、降低成本。使用夹具后可减少划线、找正等 辅助时间,而且易于实现多件、多工位加工。在现代夹具中,广泛采用气 动、液压等机动夹紧等装置,还可使辅助时间进一步减小。因而可以提高 劳动生产率、降低生产成本。
(3)通用可调夹具和成组夹具
(4)组合夹具
(5)随行夹具
4.1 机床夹具概述
4.1.2 机床夹具的分类
2)按使用的机床分类
按所使用的机床不同,夹具可分为车床夹具、铣床夹具、钻床夹 具、镗床夹具、磨床夹具、齿轮机床夹具和其他机床夹具等。
3)按夹紧动力源分类
机床夹具的工作原理

机床夹具的工作原理
机床夹具是一种用于夹持工件以便进行加工的装置。
它通常由夹爪和夹紧机构组成。
工作原理如下:
1. 夹爪:机床夹具的夹爪可以根据工件的形状和尺寸进行设计和调整。
夹爪通常由可移动的夹持手臂组成,可以通过调节机构进行精确定位。
夹爪的设计应根据工件的特点和加工要求来选择。
2. 夹紧机构:夹紧机构用于夹持和固定工件。
它可以是机械式夹紧机构、气动式夹紧机构或液压式夹紧机构等。
夹紧机构可以通过特定的螺杆或液压系统来实现夹紧力的调整和控制。
3. 调整机构:机床夹具通常还配备有调整机构,用于根据工件的尺寸和形状进行调整。
调整机构可以通过手动操作或自动控制来完成。
它可以控制夹爪的位置、张开度和夹紧力等参数,以确保夹具与工件的高精度匹配。
4. 结构刚性:为了确保加工的精度和稳定性,机床夹具通常具有较高的结构刚性。
它应具备足够的刚性和稳定性,以抵抗工件在加工过程中的各种力或动态负荷。
总之,机床夹具的工作原理是通过夹爪和夹紧机构将工件牢固地固定在加工位置上,以便进行各种形状和尺寸的加工操作。
夹具的设计应考虑工件特点和加工要求,同时还要注重夹具的稳定性和精确性。
机床夹具的工作原理是什么
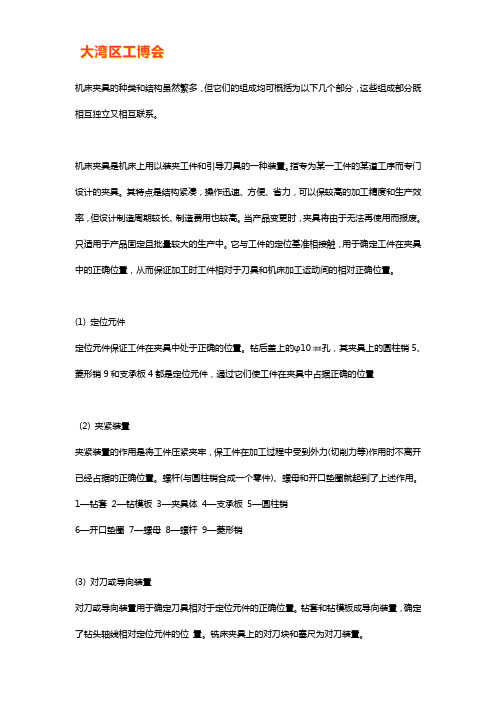
机床夹具的种类和结构虽然繁多,但它们的组成均可概括为以下几个部分,这些组成部分既相互独立又相互联系。
机床夹具是机床上用以装夹工件和引导刀具的一种装置。
指专为某一工件的某道工序而专门设计的夹具。
其特点是结构紧凑,操作迅速、方便、省力,可以保较高的加工精度和生产效率,但设计制造周期较长、制造费用也较高。
当产品变更时,夹具将由于无法再使用而报废。
只适用于产品固定且批量较大的生产中。
它与工件的定位基准相接触,用于确定工件在夹具中的正确位置,从而保证加工时工件相对于刀具和机床加工运动间的相对正确位置。
(1) 定位元件定位元件保证工件在夹具中处于正确的位置。
钻后盖上的φ10㎜孔,其夹具上的圆柱销5、菱形销9和支承板4都是定位元件,通过它们使工件在夹具中占据正确的位置(2) 夹紧装置夹紧装置的作用是将工件压紧夹牢,保工件在加工过程中受到外力(切削力等)作用时不离开已经占据的正确位置。
螺杆(与圆柱销合成一个零件)、螺母和开口垫圈就起到了上述作用。
1—钻套2—钻模板3—夹具体4—支承板5—圆柱销6—开口垫圈7—螺母8—螺杆9—菱形销(3) 对刀或导向装置对刀或导向装置用于确定刀具相对于定位元件的正确位置。
钻套和钻模板成导向装置,确定了钻头轴线相对定位元件的位置。
铣床夹具上的对刀块和塞尺为对刀装置。
(4) 连接元件连接元件是确定夹具在机床上正确位置的元件。
夹具体底面为安装基面,保证了钻套的轴线垂直于钻床工作台以及圆柱销的轴线平行于钻床工作台。
因此,夹具体可兼作连接元件。
车床夹具上的过渡盘、铣床夹具上的定位键都是连接元件。
(5) 夹具体夹具体是机床夹具的基础件,通过它将夹具的所有元件连接成一个整体。
(6) 其它装置或元件它们是指夹具中因特殊需要而设置的装置或元件。
若需加工按一定规律分布的多个表面时,常设置分度装置;为了能方便、准确地定位,常设置预定位装置;对于大型夹具,常设置吊装元件等。
三、机床夹具设计原理

1.造成误差的原因:
造成定位误差的原因有两个。 ⑴定位基准与设计基准不重合,产生基 准不重合误差△B。 ⑵定位基准与限位基准不重合,产生基 准位移误差△Y。
⑴基准不重合误差△B 定位基准与设计基准不重合,产生的基准 不重合误差 △B
基准不重合误差的大小应等于定位基准 与设计基准之间所有尺寸的公差和。在工序 图上寻找这些尺寸的公差。
合成时,若设计基准不在定位基面上 (设计基准与定位基面为两个独立的表 面),即基准不重合误差与基准位移误差无 相关公共变量。
△D=△Y+△B 合成时,若设计基准在定位基面上,即 基准不重合误差与基准位移误差有相关的公 共变量。 △D=△Y±△B
+ - 确定方法: 定位基准与限位基面接触,定位基面直 径由小变大(或由大变小),分析定位基准 变动方向。 定位基准不变,定位基面直径同样变 化,分析设计基准的变动方向。 △Y(或定位基准)与△B(或工序基 准)的变动方向相同时,取“+”号;变动 方向相反时,取“一”号。
(二)常用定位方法与定位元件
例题2 试分析图中各工件,为满足工 件的加工要求需要限制的自由度,选择定位 基准及各定位基准所限制的自由度,为各定 位基准选择相应的定位元件及各定位元件所 限制的自由度。
(三)定位误差的分析与计算
一批工件逐个在夹具上定位时,由于工 件及定位元件存在公差,使各个工件所占据 的位置不完全一致即定位不准确,加工后形 成加工尺寸的不一致,为加工误差。这种只 与工件定位有关的加工误差,称为定位误 差,用△D表示。
▪ 工件的定位平面一般是加工过的精基面,两定位 孔可能是工件上原有的,也可能是专为定位需要 而设置的工艺孔。定位元件是一面两销,即一个 平面、一个圆柱销和一个菱形销。
▪ 一面两孔定位符合基准统一原则,定位简单,夹 紧方便。
机械制造工艺学机床夹具设计原理课件

数字化
利用数字化技术实现产品设计 、工艺规划和生产过程的数字 化管理,提高生产效率和产品 质量。
精密化
采用高精度加工设备和工艺技 术,提高产品精度和表面质量 ,满足高精度和高性能产品的
需求。
02 机床夹具设计原理
机床夹具的分类与特点
通用夹具
专用夹具
适用于一定范围内的各种零件的加工,如 三爪卡盘、四爪卡盘等。特点为结构简单 ,通用性强,但效率较低。
涉及船舶的制造,包括 船体结构、推进系统和
船舶设备的制造。
电子工业
涉及电子产品的制造, 如集成电路、电子元件
和显示器的制造。
机械制造工艺学的发展趋势
智能化
利用人工智能、大数据和云计 算等技术手段,实现机械制造
过程的智能化和自动化。
绿色化
注重环保和可持续发展,采用 清洁能源和绿色制造技术,降 低能耗和减少废弃物排放。
定位误差的产生与计算
定位误差的产生是由于工件在夹具中的定位基准与加工要求不一致所引 起的。
定位误差的计算方法包括极值法和概率法,极值法适用于定位元件为刚 性、无弹性的情况,概率法适用于定位元件有一定弹性、工件尺寸有一
定分散性的情况。
定位误差的大小对加工精度和产品质量有重要影响,因此需要对其进行 控制和补偿。
设计夹具体和零部件
根据结构方案,设计夹具体的各个零部件 ,并确定其尺寸、材料和热处理要求等。
03 夹具材料的选择与处理
夹具材料的种类与特性
钢材
硬度高、耐磨性好,适用于需要承受较大夹 紧力和切削力的夹具。
铝合金
轻便、易于加工,适用于需要快速装夹和轻 量化的夹具。
铸铁
具有良好的耐磨性和抗冲击性,适用于粗加 工和重型夹具。
机床夹具及应用 单元8 专用夹具的设计方法和步骤
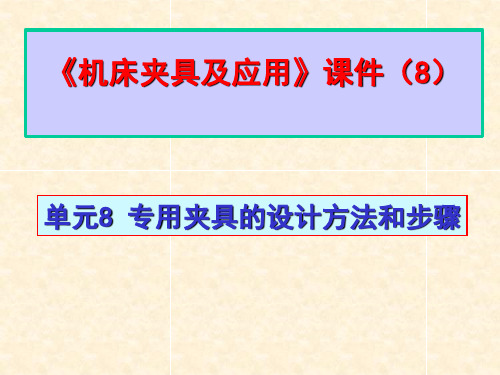
查 研 究 , 收 集 设 计 资 料
明 确 设 计 要 求 , 认 真 调
工件的定位方案
确 定 夹 具 的 结 构 方 案
工件的夹紧方案 变更工位的方案 对刀或导引方案 安装方式及夹具体的结构形式 对结构方案进行精度分析和估算
论证方案的可行性及科学性
对薄弱环节进行修改
绘 制 夹 具 总 图
绘制夹具总图的步骤
夹具总体绘制
夹具总图通常可按定位元件、夹紧 装置以及夹具体等结构顺序绘制。 特别应注意表达清楚定位元件、夹 紧装置等与夹具体的装配关系 夹具总图绘制完毕,还应在夹具设 计说明书中,就夹具的使用、维护 和注意事项等给予简要的说明
车壳体零件
夹具总体设计计算机Βιβλιοθήκη 辅助 夹具设计简介
计算机辅助夹具
设计系统流程图
零部件结构工艺性 要好,应易于制造、 检测、装配和调整 夹具结构应便于维 修和更换零部件 适当考虑提高 夹具的通用性
夹具总图上的尺寸标注
夹具的轮廓尺寸 夹具总 图上标 注的五 类尺寸 定位零件上定位表面的尺寸以及 各定位表面之间的尺寸 定位表面到对刀件或刀具 导引件间的位置尺寸 主要配合尺寸 夹具与机床的联系尺寸 夹具上主要元件之间的位置尺寸公差
其他元件的选择和设计
夹具的设计除了考虑工件的定位和夹 紧之外,还要考虑夹具如何在机床上 定位,以及夹具体的设计等问题 夹具体采用焊接结构,并用两个肋板提 高夹具体的刚度,其结构紧凑、制造周 期短。夹具体主要由盘、板和套等组成 夹具体上设置一个校正套,以便心轴 使夹具与机床主轴对定。夹具采用不 带止口的过渡盘,所以通用性好
了解所使用机床的 主要技术参数等及 与夹具连接部分的 联系尺寸 了解本企业制造和 使用夹具的生产条 件和技术状况 了解所使用量具、 刀具和辅助工具等 的型号、规格
- 1、下载文档前请自行甄别文档内容的完整性,平台不提供额外的编辑、内容补充、找答案等附加服务。
- 2、"仅部分预览"的文档,不可在线预览部分如存在完整性等问题,可反馈申请退款(可完整预览的文档不适用该条件!)。
- 3、如文档侵犯您的权益,请联系客服反馈,我们会尽快为您处理(人工客服工作时间:9:00-18:30)。
• V形块是对中定心元件,
制造无误差时,理论上外 圆中心与V形块中心位置 重合,无基准不重合误差。
j.b 0
• 工件外圆直径有偏差时, 工件轴线在V形块中心线上 下偏移。
j.w(z) A AA' AE AE
d .w( z) A j.w( z) A j.b
D
2sin
D K
2sin
'
0.15 2
1 sin 45
0.106mm
尺寸30变化时,轴心线变化为O’O”=δ”
合成后
''
0.07 2
1 sin 45
0.198mm
0.142 (0.14 0.106)2 0.283mm
2020/6/21
机械工程学院 机械制造基础
δ δ
δ"
30
例:阶梯轴组合定位
• 在阶梯轴轴颈 d的2铣工半序圆尺键寸槽H定 位误差
4
8.2.2 定位现象分析
l 完全定位:限制工件的全部六个自由度。 l 不完全定位:限制工件自由度少于六个,但仍能满足 加工技术要求。
l 欠定位:限制自由度 数少于加工技术要求限制 的最少只有度数。
l 过定位/重复定位: 工件的某一个或几个自由 度被多个定位元件限制。
2020/6/21
机械工程学院 机械制造基础
没有直202接0/6/关21 联时取“+”。机械工程学院 机械制造基础
15
定位误差的结论:
1. 定位误差只产生于采用调整法加工一批工件的情况下,若单件 或批量工件逐个试切加工者不存在定位误差。
2. 定位误差是由于工件定位不准确而产生的加工误差。
表现形式:工序基准相对加工表面可能产生的最大尺寸或位置 的变动范围。
j.w(B) 0
j.w( A) 2Lgtg g
(B) g
2020/6/21
机械工程学院 机械制造基础
26
2. 一面两孔组合定位
• 基准位移误差 j.w(O1) O1'O1" TD1 Td1 1min
j.w(O2 ) O2' O2" TD1 Td1 1min TLg
5
8.2.3 常见定位方式及定位元件
l 工件以平面定位 (1)固定支承:支承钉(限1个)、支承板(限2个) (2)可调支承 (3)自位支承(浮动支承) (4)辅助支承(不限制自由度)
2020/6/21
机械工程学院 机械制造基础
6
l 工件以内圆定位
(1)心轴:短的限两个自由度,长的限四个自由度,锥度多限一 个。
2
动方向与工序基准相对定位基准的
移动方向相同。故
K 1
d.w( z) A j.w( z) A j.b( z)
2
( 2 sin
1)
2
2020/6/21
机械工程学院 机械制造基础
23
(3)设计基准为C点时的定位误差
• 由于定位基准是A, 而设计基准是C,故
j.b( z)
Ld
1 K 2
• 基准位移误差即工 件直径误差造成的A 上下最大变化量
• 安装(装夹):工件在机床上定位和加紧的过程。 8.1.1工件装夹
l 直接装夹
l 划线找正装夹
l 夹具装夹
2020/6/21
机械工程学院 机械制造基础
2
8.1.2 夹具简介 l 夹具的种类
(1)通用夹具 (3)可调夹具 (5)随行夹具
l 夹具的作用
(2)专用夹具 (4)组合夹具
l 夹具的组成
1) 定位元件 3) 引导元件(对刀装置)
2020/6/21
机械工程学院 机械制造基础
25
►组合定位误差分析
1. 内孔与端面组合定位
• 长心轴与窄圆环端面组合
孔与端面的垂直度误差将产生基准位移误差 和角度误差:
j.w(B) dgtg g d jtg j
(B) g
• 短心轴与大端面组合
孔与端面的垂直度误差将产生基准位移误差 和角度误差:
产生原因:基准不重合;工件的定位基准面制造误差、定位元 件制造误差、工件基面与定位元件间的配合间隙及基准不重合 误差。
3. 定位误差由基准不重合误差和基准位移误差两部分组成,但二 者不一定同时存在。
4. 定位误差的计算可以按照定位误差的定义进行计算,也可以按 定位误差的组成注意分析计算。
2020/6/21
➢ 心轴水平放置(重力作用下孔与心轴固定上母线接触)
工件孔尺寸
D TD min0
,心轴尺寸
d0 m a xTd
工件孔中心最大变动量即为基准位移误差:
2020/6/21
j.w O1O2 OO2 OO1
( Dmin TD dmax Td ) ( Dmin dmax )
2
2
22
TD Td 2
u 根据典型表面、元件类型分析各定位元件限制的 自由度;
u 根据加工表面技术要求和实际限制自由度,分析 定位属哪种定位。
2020/6/21
机械工程学院 机械制造基础
9
定位实例分析1
2020/6/21
机械工程学院 机械制造基础
10
定位实例分析 2
夹紧力
2020/6/21
机械工程学院 机械制造基础
11
工件尺寸变化时,定位基准的移
j.w(z) A
AA'
K
2sin
2
动方向与工序基准相对定位基准的
移动方向相反。故
d.w(z) A
j.w( z) A j.b( z)
K 2
(
2
1 sin
1)
2
2020/6/21
机械工程学院 机械制造基础
24
例: 有一批直径为d±δd/2的轴类零件,欲加工端面孔,分析 下列方案加工孔与外圆得同轴度误差。
•工件轴线可能发生偏转,转角定位误差为:Δθ=α
2020/6/21
机械工程学院 机械制造基础
20
3. 工件以外圆定位时的定位误差
主要分析工件外圆在V形块上定位情况: 由于工件设计基准不同,可能出现以下三种情况, 即设计基准分别为A、B、C。
2020/6/21
机械工程学院 机械制造基础
21
(1)设计基准为A时的定位误差
• 基准位移误差分两种情况:
1) 工件以粗基准定位:
j.w H
其中ΔH是基面形状误差造成的基面最大变动范围。
2) 工件以精基准定位:
j.w 0
2020/6/21
机械工程学院 机械制造基础
17
2. 工件以圆孔定位时的定位误差
(1)工件圆孔与刚性心轴或销过盈配合
孔与心轴始终同心
j.w 0
(2)工件圆孔与刚性心轴或销间隙配合
定位实例分析 3
2020/6/21
机械工程学院 机械制造基础
12
定位实例分析 4
2020/6/21
机械工程学院 机械制造基础
13
8.2.4 定位误差分析
► 基准的概念及其分类
• 基准:用来确定生产对象上的几何要素之间的几何关系所依据的 那些点、线、面。 •基面:基准不一定具体可见(如孔的中心线等),在零件上通常 是通过有关具体表面表现出来的,这些表面称为基面。
2) 夹紧装置 4) 夹具体
2020/6/21
机械工程学院 机械制造基础
3
8.2 工件在夹具中的定位
8.2.1 定位基本原理
一个空间刚体具有六个自由度
l 六点定位原理:假定工件为空间刚体,正确分布六
各支承点与工件的基准面相接触,限制其空间六个自由 度,确定工件的空间位置。
l 应用六点定位原理时的注意事项:
2
2
d.w(对称) j.w(O) j.b(O) TD Td j min
0.021 0.0013 0.007 0.041mm
2020/6/21
机械工程学院 机械制造基础
29
例:同轴度误差分析
计算一外圆和平面定位加工
内孔时产生的与外圆的同轴 度误差。
外圆φ80变化时,轴心线变 化为OO’=δ’
(2)定位销
l 工件以圆锥孔定位 (1)锥心轴 (2)顶尖
2020/6/21
机械工程学院 机械制造基础
7
l 工件以外圆定位
(1)定心定位: 定位套
(2)支承定位 支承平面
V形块
2020/6/21
机械工程学院 机械制造基础
8
l 定位分析方法与步骤:
u 找与工件表面接触的元件;
u 根据零件表面形状和零件的加工要求分出定位元 件和夹紧元件(一般夹紧元件拿走后,零件定位 状态保持不变,且夹紧元件上有施力机构或作用 力符号);
1) 定位支承点与工件的定位基准面必须始终保持紧贴;
2) 一个定位支承点只能限制工件一个自由度,同时一个自由度原 则上不得有多个支承点重复限制,(支承点数不应超过六个);
3) 工件应限制几个自由度,由工件加工技术条件来确定;
4) 工件的定位不是由夹紧力作用获得的。
2020/6/21
机械工程学院 机械制造基础
2020/6/21
机械工程学院 机械制造基础
27
一面两孔组合定位
•中心线角度误差
(O1O2 )
arctg
j.w(O1 )
j.w(O2 )(c) 2L
j.w(O2 )(c) O2' O2" TD2 Td2 2min
2020/6/21
机械工程学院 机械制造基础
28
例:铣键槽
• 工序要求的位置尺寸L、H 及对称度
2020/6/21
机械工程学院 机械制造基础
14