大连理工大学科技成果——复合材料系列工具技术
大连理工大学科技成果——低烟尘镁合金焊接材料制备技术
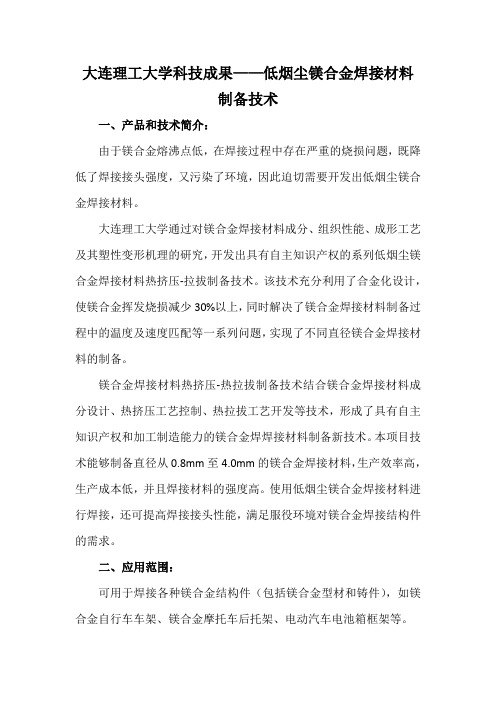
大连理工大学科技成果——低烟尘镁合金焊接材料制备技术一、产品和技术简介:由于镁合金熔沸点低,在焊接过程中存在严重的烧损问题,既降低了焊接接头强度,又污染了环境,因此迫切需要开发出低烟尘镁合金焊接材料。
大连理工大学通过对镁合金焊接材料成分、组织性能、成形工艺及其塑性变形机理的研究,开发出具有自主知识产权的系列低烟尘镁合金焊接材料热挤压-拉拔制备技术。
该技术充分利用了合金化设计,使镁合金挥发烧损减少30%以上,同时解决了镁合金焊接材料制备过程中的温度及速度匹配等一系列问题,实现了不同直径镁合金焊接材料的制备。
镁合金焊接材料热挤压-热拉拔制备技术结合镁合金焊接材料成分设计、热挤压工艺控制、热拉拔工艺开发等技术,形成了具有自主知识产权和加工制造能力的镁合金焊焊接材料制备新技术。
本项目技术能够制备直径从0.8mm至4.0mm的镁合金焊接材料,生产效率高,生产成本低,并且焊接材料的强度高。
使用低烟尘镁合金焊接材料进行焊接,还可提高焊接接头性能,满足服役环境对镁合金焊接结构件的需求。
二、应用范围:可用于焊接各种镁合金结构件(包括镁合金型材和铸件),如镁合金自行车车架、镁合金摩托车后托架、电动汽车电池箱框架等。
三、生产条件:采用本项目技术生产镁合金焊接材料需要3000KN以上压力机1台、拉拔装置1套以及相应辅助设备,包括加热装置、保温装置等。
四、规模与投资:采用镁合金焊接材料热挤压-热拉拔制备技术,能大大提高镁合金焊接材料制备效率,提高质量,减少生产成本。
本技术适合大批量生产,成本预计100万元以内,主要包括压力机、加热炉以及拔丝装置和相关模具制备;生产能力可达月产镁合金焊接材料1-2吨。
五、知识产权情况:具有完全自主知识产权。
六、市场需求与经济效益分析:随着镁合金应用的不断扩大,对镁合金焊接技术需求将日益增长,而镁合金焊接材料是镁合金焊接的技术核心,对镁合金焊接材料的需求将不断增加。
本项目低烟尘镁合金焊丝(特别是直径在φ2.0mm以下)制备技术具有技术含量高、附加值高、经济效益显着(如φ1.2mm 镁合金焊丝目前市场价为80万/吨)的特点,因此本项目技术具有广阔市场前景。
大连理工大学科技成果——激光-氩弧复合热源焊接装备
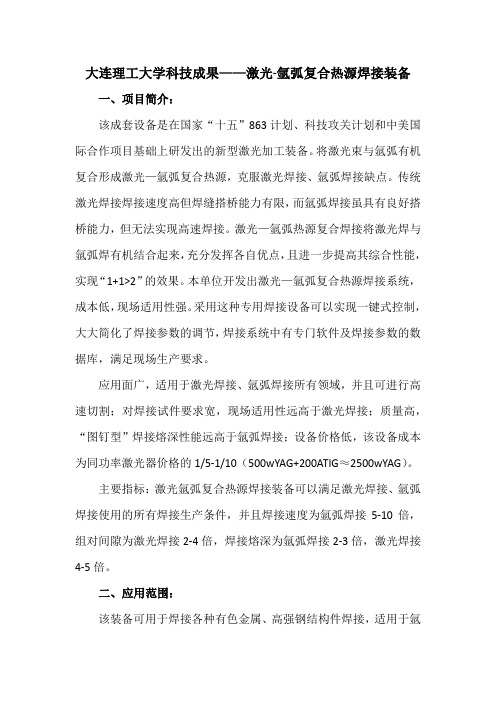
大连理工大学科技成果——激光-氩弧复合热源焊接装备一、项目简介:该成套设备是在国家“十五”863计划、科技攻关计划和中美国际合作项目基础上研发出的新型激光加工装备。
将激光束与氩弧有机复合形成激光—氩弧复合热源,克服激光焊接、氩弧焊接缺点。
传统激光焊接焊接速度高但焊缝搭桥能力有限,而氩弧焊接虽具有良好搭桥能力,但无法实现高速焊接。
激光—氩弧热源复合焊接将激光焊与氩弧焊有机结合起来,充分发挥各自优点,且进一步提高其综合性能,实现“1+1>2”的效果。
本单位开发出激光—氩弧复合热源焊接系统,成本低,现场适用性强。
采用这种专用焊接设备可以实现一键式控制,大大简化了焊接参数的调节,焊接系统中有专门软件及焊接参数的数据库,满足现场生产要求。
应用面广,适用于激光焊接、氩弧焊接所有领域,并且可进行高速切割;对焊接试件要求宽,现场适用性远高于激光焊接;质量高,“图钉型”焊接熔深性能远高于氩弧焊接;设备价格低,该设备成本为同功率激光器价格的1/5-1/10(500wYAG+200ATIG≈2500wYAG)。
主要指标:激光氩弧复合热源焊接装备可以满足激光焊接、氩弧焊接使用的所有焊接生产条件,并且焊接速度为氩弧焊接5-10倍,组对间隙为激光焊接2-4倍,焊接熔深为氩弧焊接2-3倍,激光焊接4-5倍。
二、应用范围:该装备可用于焊接各种有色金属、高强钢结构件焊接,适用于氩弧焊接、激光焊接的所有场合。
三、提供技术的程度和合作方式:激光加工器、氩弧焊机各一台,核心复合技术由我单位提供。
转让中试成果,培训人员操作水平达到技术合同要求。
图激光-氩弧复合热源焊接装备样机图镁合金焊接材料镁合金焊接焊接产品:图摩托车后托架图镁合金自行车。
大连理工大学科技成果——整体式微小复材零件的精密制造技术

整体式微小复材零件的精密制造技术Precision Manufacturing Technology for Integral Micro Composite Parts背景需求整体式微小复材零件已广泛应用于航空航天领域,如采用薄板聚酰亚胺基体镀铜件作为高速飞行器的关键零部件等。
针对该类整体式微小复材零件的特殊结构,以及保证边缘高质量和不损坏聚酰亚胺基底的加工要求,在现有加工方法及设备无法满足该零件高质量、高效率、低成本的加工要求的条件下,研究搭建针对该类特殊零件的综合加工实验平台,为整体式微小复材零件高精度、高质量和高效率的工业化生产提供技术支持。
研究内容简介平面式微小复材零件整体式微小复材零件根据整体式微小复材零件的结构特点和加工要求,采用“光刻+激光/微铣”的组合工艺方式,实现整体式微小复材零件的精密加工:即对整体式微小复材零件平面微小带宽中心区域采用光刻工艺制造;针对平面其他区域和圆锥部分采用激光/数控微细铣削工艺制造;开发立体视觉定位系统,以实现“光刻+激光/微铣”工艺分段加工精密衔接;研制开发整体式微小复材零件高精度五轴联动激光/微铣加工实验装置,完成平面与圆锥的衔接部分及圆锥螺旋部分的高质量激光/微铣加工,最终获得经过性能检测合格的整体式微小复材零件。
关键技术和主要创新◆整体式微小复材零件光刻与激光/微铣工艺组合的精密加工方法◆“光刻+激光/微铣”组合加工时基于显微视觉的过渡区域精密对正与衔接技术◆整体式微小复材零件平面螺旋与锥面螺旋精确过渡加工策略◆保证整体式微小复材零件线宽及边缘精准的激光/数控微铣削加工工艺1064nm激光加工70μm宽沟槽532nm激光器加工平面螺旋线微细铣削加工沟槽微细铣削加工平面双螺旋线1。
随风扶摇起,直上九万里

随风扶摇起,直上九万里作者:夏莺来源:《求学·新高考版》2023年第18期2023年5月28日,自上海虹桥国际机场起飞的中国东方航空MU9191航班平安降落在北京首都国际机场,标志着国产大飞机C919圆满完成首次商业航班飞行。
C919商业首飞的圆满成功,意味着中国商业航空工业迈上了一个新的台阶,同时也意味着中国民航不再全部依赖国外进口,真正走出了一条自主发展之路。
从“运-10”到C919所谓的“大飞机”就是大型客机,一般指起飞总重超过100吨的运输类飞机,同时包括150座以上的干线客机,这是国际民航的通用机型。
能否自主制造大飞机,决定了各国在民航领域的综合实力,也是国家工业实力的直接体现,如美国的“波音707”、苏联的“图104”及法国的“空中客车A300”,这些都是当时(20世纪70年代)工业强国大型客机的代表型号。
20世纪70年代以前,中国能够生产部分战斗机和运输机,但大飞机还未敢想过。
1970年8月27日,代号“708工程”的“运-10”飞机项目正式立项,军队、中央各部委机构以及全国21个省(区、市)的262个单位被抽调参与研发。
中国航空设计者们在既无经验也无图纸的情况下,通过摸索其他国家客机的结构,用了整整5年的时间,终于完成了“运-10”的全部设计图纸,随后便开始边制造、边试验。
1980年9月26日,首架“运-10”在上海完成飞行试验,且先后在多座城市开展科研试飞,甚至还曾7次飞越喜马拉雅山,为西藏运送急需物资。
不过,“运-10”在试飞时,被发现存在不同程度的问题。
然而,当时孱弱的工业配套设施,使得早产的“运-10”根基不稳,虽经多次试飞,但仍没能解决配套发动机研制周期的问题,再加上翼型、气动研制、参数设置、材料技术上的问题在短时间内难以克服,“运-10”項目不堪重负,最终搁浅。
1985年,整个“运-10”项目被砍。
花费了无数人力物力,历时15年,总投资达5亿元的“运-10”项目自此沉寂于时光之中。
大连理工大学科技成果——大型复杂曲面数字化配对加工设备

大连理工大学科技成果——大型复杂曲面数字化配
对加工设备
一、产品和技术简介:
大连理工大学机械工程学院研制成功的“大型复杂曲面数字化配对加工设备”,综合运用了曲面三维自动跟踪测量、离散数据采集及数学分析处理、数字化加工、机床计算机控制等技术,填补了我国在该领域的空白。
该系统已经成功应用在我国航天制造领域,是目前我国长征系列大型液体燃料运载火箭的某关键部件制造的唯一专用技术装备,该系统亦加工了澳星、铱星、“神舟号”载人飞船等多项重大工程的关键零部件,为我国的航天事业做出了重大贡献。
2001年完成了系统升级。
二、应用范围和生产条件:
航空航天领域的薄壁零件数字化加工、大型复杂曲面零部件的配对加工,其他领域的大型曲面零件配对制造。
具有较强的机电设备制造和计算机控制系统的研发基础。
三、规模与投资、成本估算:
200万元。
每套控制系统成本约30万元。
四、提供技术的程度和合作方式:
一次性技术转让或共同开发。
大连理工大学科技成果——集成电路设计

大连理工大学科技成果——集成电路设计一、项目简介:设计平台:双核PC 机,Linux 操作系统,Mentor 公司全线集成电路开发工具。
流片:多晶圆项目。
部分芯片设计展示:集成气压传感器芯片:在同一芯片上集成了气压传感器阵列、信号检测电路、温度补偿电路、AD 转换电路、数字接口电路,输入电压5VDC ,输出数字信号;气压检测范围:0.1Pa 至1标准大气压。
0200004000060000800001000003200340036003800400042004400t h e o u t p u t v o l t a g e (m V )gas pressure(Pa) gas pressure risegas pressure dropthe ambient temperature is 30.3℃the bias current is 3.85mAPWM 升压变换器:一款电流型PWM 电源管理芯片。
输入电压范围3~5V ,输出电压稳定在5V ,工作频率170KHz ,典型系统效率大于90%,输出纹波电压小于1%。
稳压器芯片:一款低压差线性稳压芯片,输入电压3.5V -6.5V 时,输出电压稳定在3.3V。
最小压差仅200mV,最高负载电流150mA,输出电压精度±1%。
二、应用范围:低频信号采集、通用运算放大器、模数转换、电源管理芯片。
三、知识产权情况:DUT0726,中国集成电路布图设计专有权,BS.07500252.3;DUT0723,中国集成电路布图设计专有权,BS.07500253.1。
四、规模与投资:产业化程度:实验室阶段五、提供技术的程度和合作方式提供相关的技术图纸,指导生产过程,并负责最终的调试和性能评定,培训售后服务人员。
合作方负责加工和销售环节,利润协商分配。
大连理工大学科技成果——高性能铝合金、铜合金电磁半连铸新技术
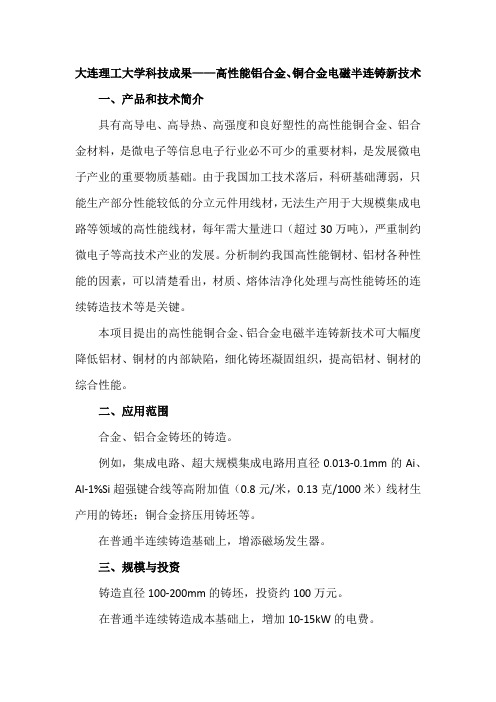
大连理工大学科技成果——高性能铝合金、铜合金电磁半连铸新技术
一、产品和技术简介
具有高导电、高导热、高强度和良好塑性的高性能铜合金、铝合金材料,是微电子等信息电子行业必不可少的重要材料,是发展微电子产业的重要物质基础。
由于我国加工技术落后,科研基础薄弱,只能生产部分性能较低的分立元件用线材,无法生产用于大规模集成电路等领域的高性能线材,每年需大量进口(超过30万吨),严重制约微电子等高技术产业的发展。
分析制约我国高性能铜材、铝材各种性能的因素,可以清楚看出,材质、熔体洁净化处理与高性能铸坯的连续铸造技术等是关键。
本项目提出的高性能铜合金、铝合金电磁半连铸新技术可大幅度降低铝材、铜材的内部缺陷,细化铸坯凝固组织,提高铝材、铜材的综合性能。
二、应用范围
合金、铝合金铸坯的铸造。
例如,集成电路、超大规模集成电路用直径0.013-0.1mm的Ai、Al-1%Si超强键合线等高附加值(0.8元/米,0.13克/1000米)线材生产用的铸坯;铜合金挤压用铸坯等。
在普通半连续铸造基础上,增添磁场发生器。
三、规模与投资
铸造直径100-200mm的铸坯,投资约100万元。
在普通半连续铸造成本基础上,增加10-15kW的电费。
四、提供技术的程度和合作方式成果转让。
大连理工大学科技成果——复合材料加工工具制备技术与应用
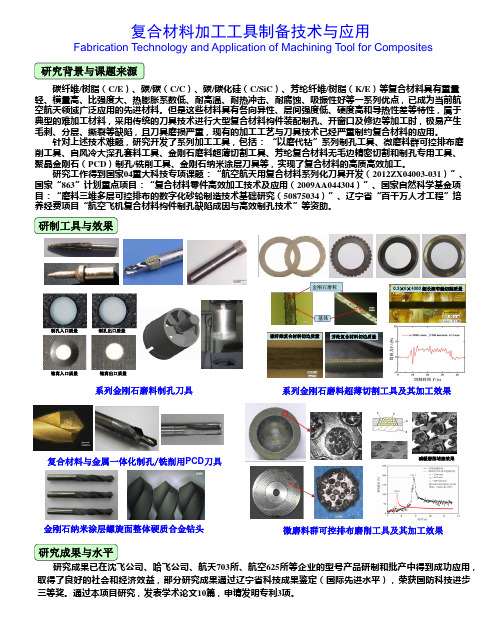
制孔入口质量
制孔出口质量
锪窝入口质量
锪窝出口质量
系列金刚石磨料制孔刀具
0.3×6×1000 超长深窄缝切ຫໍສະໝຸດ 质量碳纤维复合材料切边质量
芳纶复合材料切边质量
系列金刚石磨料超薄切割工具及其加工效果
复合材料与金属一体化制孔/铣削用PCD刀具
减缓磨削堵塞效果
金刚石纳米涂层螺旋面整体硬质合金钻头
微磨料群可控排布磨削工具及其加工效果
研究成果与水平
研究成果已在沈飞公司、哈飞公司、航天703所、航空625所等企业的型号产品研制和批产中得到成功应用, 取得了良好的社会和经济效益,部分研究成果通过辽宁省科技成果鉴定(国际先进水平),荣获国防科技进步 三等奖。通过本项目研究,发表学术论文10篇,申请发明专利3项。
针对上述技术难题,研究开发了系列加工工具,包括: “以磨代钻”系列制孔工具、微磨料群可控排布磨 削工具、自风冷大深孔套料工具、金刚石磨料超薄切割工具、芳纶复合材料无毛边精密切割和制孔专用工具、 聚晶金刚石(PCD)制孔/铣削工具、金刚石纳米涂层刀具等,实现了复合材料的高质高效加工。
研究工作得到国家04重大科技专项课题:“航空航天用复合材料系列化刀具开发(2012ZX04003-031)”、 国家“863”计划重点项目:“复合材料零件高效加工技术及应用(2009AA044304)”、国家自然科学基金项 目:“磨料三维多层可控排布的数字化砂轮制造技术基础研究(50875034)”、辽宁省“百千万人才工程”培 养经费项目“航空飞机复合材料构件制孔缺陷成因与高效制孔技术”等资助。
复合材料加工工具制备技术与应用
Fabrication Technology and Application of Machining Tool for Composites
大连理工大学科技成果——高压土工三轴仪

大连理工大学科技成果——高压土工三轴仪一、产品和技术简介:高压三轴仪是测量高围压条件下土的应力应变性质和强度指标的仪器,并可通过数字图像测量系统测量试样变形过程中的全表面场(轴向、径向应变)及追踪剪切带的发展。
该仪器可提供应变控制和应力控制两种控制方式,主要由试验机、高压压力室、测量系统、试样制备工具等四部分组成。
主要功能包括(1)轴向加载:加载速率控制、荷载控制、位移控制;(2)围压加载:恒围压加载、单级围压加载、多级围压加载。
高压三轴仪采用了串联结构小载荷传感器的保护装置。
将高压三轴仪中的轴向大小两个荷载传感器进行串联,借助特殊的机械结构实现保护小载荷传感器的装置。
解决大小两个载荷传感器的串联测试时小量程载荷传感器的保护问题,在不拆卸小量程载荷传感器的前提下实现小量程载荷传感器的隔离保护。
在保持中心加载轴不受影响的情况下,实现在竖直方向自由升降,并且有自锁功能,能够保持加载杆的平衡直至加载到试验要求的最大载荷。
以一组有导向功能并带有梯形螺纹的套筒为主体,利用一对直角圆锥齿轮和具有导向功能套筒将水平传动变为竖直传动,具有较高稳定性和操作灵活性,并且在电动机断电情况下,能够利用自锁功能实现保护。
该单轴小载荷传感器保护装置具有较高的稳定性和操作灵活性,自锁功能保证了在电动机断电情况下稳定加载,并且带梯形螺纹的套筒可成为传力链一环节,对传感器进行保护隔离,实现无须更换传感器的情况下进行高压三轴试验的精确测量。
此外,高围压压力室设有视窗,承受压力可达6MPa,内部装有耐高压平面镜,可实现土样全表面变形测量。
除了常规三轴压缩试验(不固结不排水剪、固结不排水剪、固结排水剪三种)外,尚可进行加荷控制试验、加卸载循环试验、围压控制、空隙水压力控制,同时测量围压、孔隙水压力以及体积变化等。
加载主机的主要技术参数:最大轴向荷载5T;加载速率0.02mm/min-50mm/min;压力室设计使用压力6MPa;试样尺寸可选直径Ф39.1mm,高度H80mm或直径Ф61.8mm,高度H120mm;高压三轴仪配置的土样变形数字图像测量系统的基本参数:分辨率1280×1024测量速度0.5s。
大连理工大学科技成果——镁铝系合金复合细化技术

大连理工大学科技成果——镁铝系合金复合细化技术一、项目简介作为目前工程应用中最轻的金属结构材料,镁合金越来越受到重视,但室温变形能力差、强度有待提高等问题限制了镁合金的推广应用。
晶粒细化技术可以在提高变形能力的同时显著增强合金的强度等性能,因而成为突破镁合金性能和应用瓶颈的重要途径。
然而,对应用较广的镁铝系合金而言,一直缺乏稳定、高效的晶粒细化技术。
本项目利用粉末冶金法制备了一种高效的Al-C中间合金细化剂,并在此基础上与电磁场复合,开发了二元复合细化技术。
Al-C中间合金可以为镁铝系合金熔体提供有效的异质形核颗粒,促进α-Mg晶粒的异质形核,提高形核率;而电磁场不仅可以为熔体施加强制对流,促进温度场与溶质元素均匀化分布,还可以减轻Al-C中间合金中颗粒相的团聚趋势,增加有效形核质点的数量。
两者的复合使用带来了显著的叠加效应,使镁铝系合金的晶粒得到显著细化。
由于Al元素是镁铝系合金中的主要合金元素,Al-C中间合金的引入不会显著改变合金成分。
而且Al-C细化剂和电磁场的施加简单易行,因此具有良好的工业应用前景。
二、应用范围:该技术主要针对镁铝系合金,用于实现其铸态晶粒的有效细化。
三、知识产权情况:本团队拥有相关专利和核心技术。
相关专利:一种针对镁合金凝固组织模拟的捕捉和转换规则,发明专利:ZL201110400271.2。
四、规模与投资:本项目针对镁合金的铸造生产,用户可根据合金牌号和具体要求选择相应细化工艺和施加外场装置。
具体投资成本依据研发内容、企业发展定位和当地物价而定。
五、提供技术的程度和合作方式本团队成功开发的含碳细化剂与电磁场复合细化技术,成熟度较高,经试验应用后收到了良好的效果,为该技术的进一步开发拓展奠定了良好的基础。
本团队可提供完整的设备设计、工艺参数,对有需求的单位可进行技术转让等合作。
六、配图:以AZ31为试验对象,对该技术进行测评。
结果显示,Al-C细化剂与螺旋磁场复合获得了显著的细化效果,且优于单独使用细化剂或螺旋磁场。
大连理工大学科技成果——用于气体分离和水深度处理的一种新型炭纤维复合分子筛材料
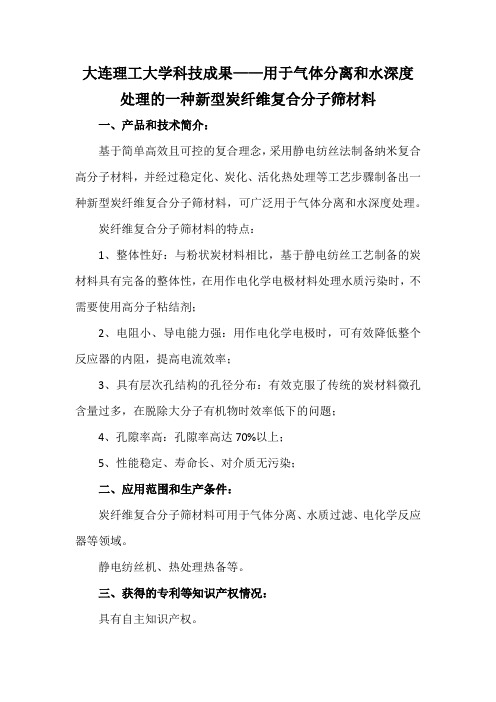
大连理工大学科技成果——用于气体分离和水深度处理的一种新型炭纤维复合分子筛材料
一、产品和技术简介:
基于简单高效且可控的复合理念,采用静电纺丝法制备纳米复合高分子材料,并经过稳定化、炭化、活化热处理等工艺步骤制备出一种新型炭纤维复合分子筛材料,可广泛用于气体分离和水深度处理。
炭纤维复合分子筛材料的特点:
1、整体性好:与粉状炭材料相比,基于静电纺丝工艺制备的炭材料具有完备的整体性,在用作电化学电极材料处理水质污染时,不需要使用高分子粘结剂;
2、电阻小、导电能力强:用作电化学电极时,可有效降低整个反应器的内阻,提高电流效率;
3、具有层次孔结构的孔径分布:有效克服了传统的炭材料微孔含量过多,在脱除大分子有机物时效率低下的问题;
4、孔隙率高:孔隙率高达70%以上;
5、性能稳定、寿命长、对介质无污染;
二、应用范围和生产条件:
炭纤维复合分子筛材料可用于气体分离、水质过滤、电化学反应器等领域。
静电纺丝机、热处理热备等。
三、获得的专利等知识产权情况:
具有自主知识产权。
四、规模与投资、成本估算:
50-200元/m2,取决于使用的原料。
五、提供技术的程度和合作方式:
小试技术。
合作开展中试或工业化生产技术,实现大面积的整体式复合炭分子筛材料的规模化应用。
六、配图:。
大连理工大学科技成果——铜及铜合金板带坯水平电磁连续铸造技术
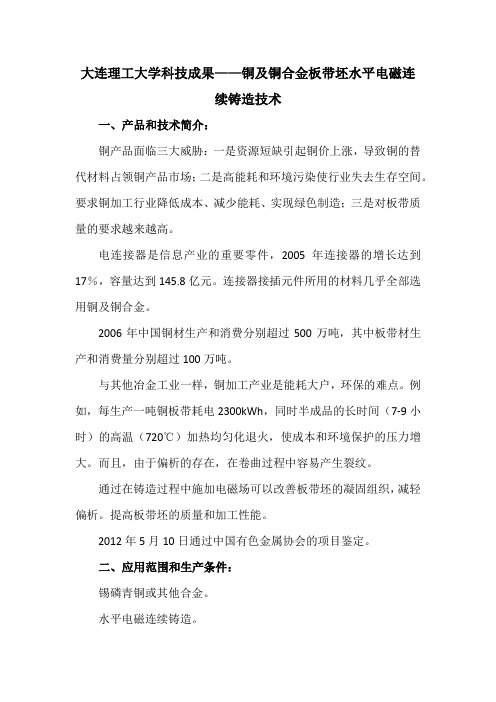
大连理工大学科技成果——铜及铜合金板带坯水平电磁连
续铸造技术
一、产品和技术简介:
铜产品面临三大威胁:一是资源短缺引起铜价上涨,导致铜的替代材料占领铜产品市场;二是高能耗和环境污染使行业失去生存空间。
要求铜加工行业降低成本、减少能耗、实现绿色制造;三是对板带质量的要求越来越高。
电连接器是信息产业的重要零件,2005年连接器的增长达到17%,容量达到145.8亿元。
连接器接插元件所用的材料几乎全部选用铜及铜合金。
2006年中国铜材生产和消费分别超过500万吨,其中板带材生产和消费量分别超过100万吨。
与其他冶金工业一样,铜加工产业是能耗大户,环保的难点。
例如,每生产一吨铜板带耗电2300kWh,同时半成品的长时间(7-9小时)的高温(720℃)加热均匀化退火,使成本和环境保护的压力增大。
而且,由于偏析的存在,在卷曲过程中容易产生裂纹。
通过在铸造过程中施加电磁场可以改善板带坯的凝固组织,减轻偏析。
提高板带坯的质量和加工性能。
2012年5月10日通过中国有色金属协会的项目鉴定。
二、应用范围和生产条件:
锡磷青铜或其他合金。
水平电磁连续铸造。
三、获得的专利等知识产权情况:申报发明专利。
四、规模与投资、成本估算:有连铸机的情况下100万元。
五、提供技术的程度和合作方式:提供技术和装置。
六、配图:
图1 八达铜业铸造现场
图2 板带坯的微观偏析照片
七、产业化程度:产业化阶段
不施加电磁场 施加电磁场。
大连理工大学科技成果——高硬材料密封环复杂曲面超精密加工技术与装备

点接触磨削示意图高硬材料密封环复杂曲面超精密加工技术与装备Ultra precision machining of seal ring complex surfaces in hard materials一、研究方向背景(Background)轴封型核主泵利用流体静压效应或流体动压效应实现非接触式机械密封,其所用的高硬材料密封环端面是由平面、圆锥面、等倾波纹面或斜波纹面构成的高精度复杂曲面,精密制造极其困难,核主泵机械密封是核主泵中唯一尚未实现国产化的部件,目前仍由少数几个国外厂家垄断供应。
二、研究内容(Key technologies)1.高硬密封环材料磨削时材料去除机理2. 高硬材料密封环复杂曲面超精密磨削新原理3. 杯形砂轮线接触磨削密封环复杂曲面关键技术4. 高硬材料密封环复杂曲面超精密磨床研发三、承担的国家项目(Projects )四、研究进展(Progress )1. 提出杯形砂轮线接触磨削核主泵密封环复杂曲面新原理2. 提出二轴联动、三轴联动和四轴联动的核主泵密封环复杂曲面超精密磨床方案3. 申请发明专利10项、发表论文11篇理论磨削生成面形理论磨削生成面形理论磨削生成面形二轴联动超精密磨床方案三轴联动超精密磨床方案三轴联动超精密磨床方案四轴联动超精密磨床方案(a)圆锥面型(b)等倾曲面型(c)斜波纹面型核主泵用密封环1. 国家973计划项目:核主泵制造的关键科学问题,课题六:难加工材料的复杂型面零件高精高效加工原理(2009CB724306)2. 国家自然科学基金:核主泵密封环高硬复杂形面超精密加工理论与技术研究(50875037)轴封型核主泵核主泵机械密封组件面形误差:1.6 nm 面形误差:67 nm 面形误差:108 nm。
大连理工大学科技成果——芳纶复合材料无毛边切割技术
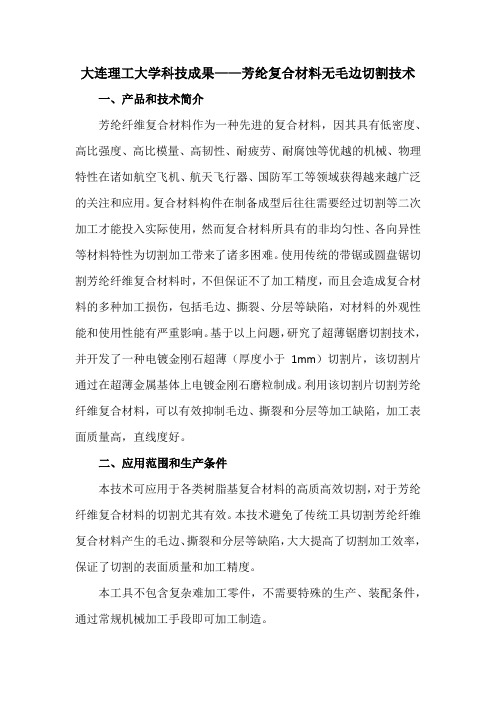
大连理工大学科技成果——芳纶复合材料无毛边切割技术一、产品和技术简介芳纶纤维复合材料作为一种先进的复合材料,因其具有低密度、高比强度、高比模量、高韧性、耐疲劳、耐腐蚀等优越的机械、物理特性在诸如航空飞机、航天飞行器、国防军工等领域获得越来越广泛的关注和应用。
复合材料构件在制备成型后往往需要经过切割等二次加工才能投入实际使用,然而复合材料所具有的非均匀性、各向异性等材料特性为切割加工带来了诸多困难。
使用传统的带锯或圆盘锯切割芳纶纤维复合材料时,不但保证不了加工精度,而且会造成复合材料的多种加工损伤,包括毛边、撕裂、分层等缺陷,对材料的外观性能和使用性能有严重影响。
基于以上问题,研究了超薄锯磨切割技术,并开发了一种电镀金刚石超薄(厚度小于1mm)切割片,该切割片通过在超薄金属基体上电镀金刚石磨粒制成。
利用该切割片切割芳纶纤维复合材料,可以有效抑制毛边、撕裂和分层等加工缺陷,加工表面质量高,直线度好。
二、应用范围和生产条件本技术可应用于各类树脂基复合材料的高质高效切割,对于芳纶纤维复合材料的切割尤其有效。
本技术避免了传统工具切割芳纶纤维复合材料产生的毛边、撕裂和分层等缺陷,大大提高了切割加工效率,保证了切割的表面质量和加工精度。
本工具不包含复杂难加工零件,不需要特殊的生产、装配条件,通过常规机械加工手段即可加工制造。
三、获得的专利等知识产权情况已申请中国发明专利:一种高强纤维树脂基复合材料无毛边高效切割工具;专利申请号:201210060643.6。
四、规模与投资、成本估算根据客户需求确定切割工具的具体尺寸,每片制造成本约为500-800元;使用方仅需要购买切割工具安装在常规设备上即可使用。
五、提供技术的程度和合作方式针对用户定制供货,详情面议。
六、配图(a)使用传统带锯(b)使用电镀金刚石超薄切割片图芳纶纤维复合材料的切割加工表面质量。
大连理工大学科技成果——层状铝合金复合铸坯制备技术
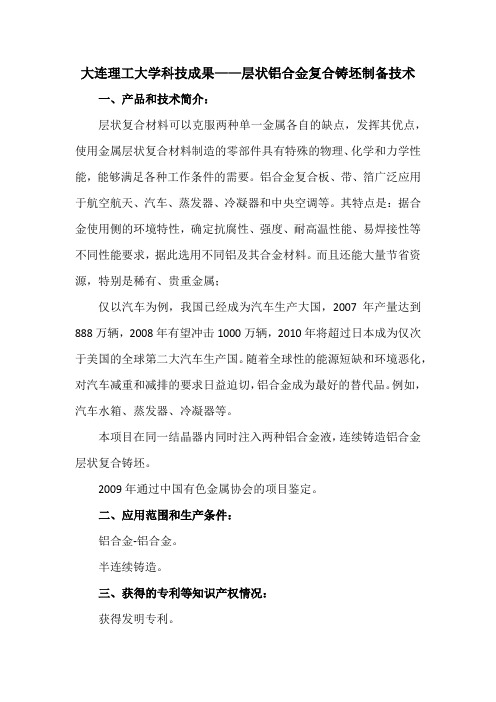
大连理工大学科技成果——层状铝合金复合铸坯制备技术一、产品和技术简介:层状复合材料可以克服两种单一金属各自的缺点,发挥其优点,使用金属层状复合材料制造的零部件具有特殊的物理、化学和力学性能,能够满足各种工作条件的需要。
铝合金复合板、带、箔广泛应用于航空航天、汽车、蒸发器、冷凝器和中央空调等。
其特点是:据合金使用侧的环境特性,确定抗腐性、强度、耐高温性能、易焊接性等不同性能要求,据此选用不同铝及其合金材料。
而且还能大量节省资源,特别是稀有、贵重金属;仅以汽车为例,我国已经成为汽车生产大国,2007年产量达到888万辆,2008年有望冲击1000万辆,2010年将超过日本成为仅次于美国的全球第二大汽车生产国。
随着全球性的能源短缺和环境恶化,对汽车减重和减排的要求日益迫切,铝合金成为最好的替代品。
例如,汽车水箱、蒸发器、冷凝器等。
本项目在同一结晶器内同时注入两种铝合金液,连续铸造铝合金层状复合铸坯。
2009年通过中国有色金属协会的项目鉴定。
二、应用范围和生产条件:铝合金-铝合金。
半连续铸造。
三、获得的专利等知识产权情况:获得发明专利。
四、规模与投资、成本估算:是规模和现有条件而定。
五、提供技术的程度和合作方式:提供技术和装置。
六、配图:(a)三层铝合金铸坯侧面(b)三层铝合金铸坯横截面图1直接铸造的三层铝合金铸坯,尺寸420×128×5000mm(a)二层铝合金铸坯的横截面(b)二层铝合金铸坯的微观组织图2直接铸造的二层铝合金铸坯,尺寸420×128×5000mm(a)轧制过程(b)轧制后3mm薄板的断面图3直接铸造的二层铝合金铸坯的轧制过程和轧制后3mm薄板的断面五、产业化程度:正在产业化。
大连理工大学科技成果——多孔金属制备技术

大连理工大学科技成果——多孔金属制备技术一、项目简介多孔金属具有超低密度、高比强度、高比刚度、冲击吸能性、低热导率、低磁导率及良好的阻尼特性等优良性能,因而既可作为轻质结构、减振以及填充介质而广泛应用于航空航天、武器装备和汽车等领域,也可作为功能材料应用于高速公路隔音墙、建筑减噪墙面及电子工业等。
多孔金属能将多种优良性能结合在一起,体现出多功能集成性,在结构材料和功能材料领域都能发挥重要的作用,具有广阔的应用前景。
本团队主要采用的如下技术制备多孔金属:熔体发泡法,Gasar 法和渗流铸造法。
熔体发泡法制备泡沫铝的基本原理是将发泡剂均匀分散到具有一定粘度的熔融铝或铝合金中,发泡剂受热分解并释放出气体,气体滞留于粘稠金属熔体中,冷却后得到泡沫铝样品。
Gasar 法即金属-气体共晶定向凝固方法,可以利用该工艺所制备出具有选择性取向孔结构的多孔铝,其特殊性能在航天、汽车等众多领域具有广泛用途。
渗流铸造法是先将制备的预制体放入模具内,然后将金属液渗入到预制块间隙中,最后将预制体溶除,即可得到通孔结构的多孔金属材料,这种方法的优点是结构的设计性和可控性强。
二、应用范围多孔金属作为一种结构功能一体化材料应用广泛,在航空航天、武器装备、交通运输、节能减排、生物医疗、环境保护等各个领域都发挥重要作用。
例如,在交通运输方面,将多孔金属应用在汽车车体或发动机,主要体现在车体减震及减重的效果上,从而达到节约能源,减少大量利用石油能源对环境的污染;由于多孔金属的吸声特性,多孔金属作为一种隔音材料,可作为噪音吸收墙而达到减少环境噪音的目的;利用多孔金属的过滤性能,可对污染的水体、工业生产的废气进行过滤处理,同样可以改善环境污染;利用多孔金属比表面积大这一特点,可以提供给化学催化更好的载体环境,提升化工催化效率;多孔金属可以作为医疗材料,可以对人体损伤的骨骼进行修复和替代;在建筑装修领域,多孔金属同样可以得到应用,同时具备可回收循环利用的优点。
大连理工大学科技成果——碳纤维复合材料加工机理与方法
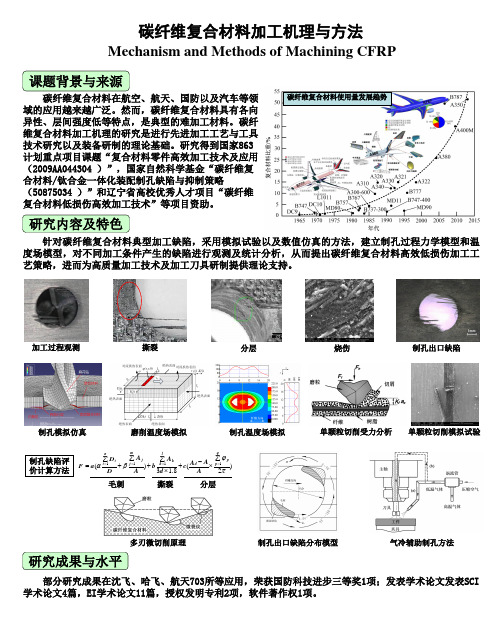
碳纤维复合材料使用量发展趋势
研究内容及特色
针对碳纤维复合材料典型加工缺陷,采用模拟试验以及数值仿真的方法,建立制孔过程力学模型和温 度场模型,对不同加工条件产生的缺陷进行观测及统计分析,从而提出碳纤维复合材料高效低损伤加工工 艺策略,进而为高质量加工技术及加工刀具研制提供理论支持。
加工过程观测
撕裂
分层
碳纤维复合材料加工机理与方法
Mechanism and Methods of Machining CFRP
课题背景与来源
碳纤维复合材料在航空、航天、国防以及汽车等领 域的应用越来越广泛。然而,碳纤维复合材料具有各向 异性、层间强度低等特点,是典型的难加工材料。碳纤 维复合材料加工机理的研究是进行先进加工工艺与工具 技术研究以及装备研制的理论基础。研究得到国家863 计划重点项目课题“复合材料零件高效加工技术及应用 (2009AA044304 )”,国家自然科学基金“碳纤维复 合材料/钛合金一体化装配制孔缺陷与抑制策略 (50875034 )”和辽宁省高校优秀人才项目“碳纤维 复合材料低损伤高效加工技术”等项目资助。
烧伤
制孔出口缺陷
制孔模拟仿真
磨削温度场模拟
制孔温度场模拟
制孔缺陷评 价计算方法nml Nhomakorabeaq
Di Aj
F a( i1 j1 ) b
Ak
k 1
c(
Ad
A
p 1
p
)
D
A
3d 1.8
A 2
毛刺
撕裂
分层
单颗粒切削受力分析 单颗粒切削模拟试验
多刃微切削原理
研究成果与水平
制孔出口缺陷分布模型
气冷辅助制孔方法
部分研究成果在沈飞、哈飞、航天703所等应用,荣获国防科技进步三等奖1项;发表学术论文发表SCI 学术论文4篇,EI学术论文11篇,授权发明专利2项,软件著作权1项。
复合材料C型框辅助铺叠工具及其使用方法[发明专利]
![复合材料C型框辅助铺叠工具及其使用方法[发明专利]](https://img.taocdn.com/s3/m/745b39d75727a5e9856a61fa.png)
专利名称:复合材料C型框辅助铺叠工具及其使用方法专利类型:发明专利
发明人:马秘辉,姜洪博,关振,刘顺臻
申请号:CN202010823103.3
申请日:20200817
公开号:CN111844809A
公开日:
20201030
专利内容由知识产权出版社提供
摘要:复合材料C型框辅助铺叠工具及其使用方法,属于C型框类复合材料制件领域。
辅助铺叠工具为链状结构,通过圆柱螺栓能够实现类似与关节的转动功能;工具的每个组成单元结构简单,包括夹紧平台和夹钳,实现裁片的夹紧贴合和弯折功能;工具可根据裁片尺寸增加或减少组成单元的数量,灵活度高;辅助铺叠工具通过圆柱螺栓转动,其活动角度覆盖范围广,可适应不同弧度制件的铺叠,通用性强。
申请人:沈阳飞机工业(集团)有限公司
地址:110034 辽宁省沈阳市皇姑区陵北街1号
国籍:CN
代理机构:大连理工大学专利中心
代理人:梅洪玉
更多信息请下载全文后查看。
- 1、下载文档前请自行甄别文档内容的完整性,平台不提供额外的编辑、内容补充、找答案等附加服务。
- 2、"仅部分预览"的文档,不可在线预览部分如存在完整性等问题,可反馈申请退款(可完整预览的文档不适用该条件!)。
- 3、如文档侵犯您的权益,请联系客服反馈,我们会尽快为您处理(人工客服工作时间:9:00-18:30)。
大连理工大学科技成果——复合材料系列工具技术
一、产品和技术简介
航空航天等领域广泛应用的碳纤维/树脂复合材料具有各向异性,层间强度低,且碳纤维的硬度高(HRC=53~65)、强度大、导热性差等特性,导致诸如钻孔、锪窝、开窗口、大孔套料加工、切边、磨削等机械加工过程中,特别是制孔过程中极易产生毛刺、分层、撕裂等缺陷,属于典型的难加工材料。
多年来,航空航天和军工科研与生产企业为确保碳纤维复合材料构件的质量,不得已只能沿用金属加工工具及加工工艺,传统的机械加工方法和现有的手工作业方式不仅效率低下,远远满足不了批量生产的需求,而且极易产生毛刺和撕裂等加工缺陷,国内至今尚无针对C/E复合材料加工的系列专用刀具。
基于以上问题,开展了针对碳纤维/树脂基复合材料工具技术的系列研究,研制开发出系列电镀超硬磨料(金刚石)多刃套料工具及其组合制孔工具、微磨料群可控排布电镀超硬磨料磨削砂轮、超硬磨料超薄切割工具、金刚石纳米涂层螺旋面整体硬质合金制孔刀具、PCD制孔刀具等,并掌握了各种刀具的加工性能和最优工艺参数。
二、应用范围和生产条件
复合材料在军工、航天航空领域应用越来越广泛,而相应的军工企业、研究所都不可避免的面临复合材料加工中出现的各种问题。
复合材料系列工具技术已部分应用与航空和航天企业,例如,中国运载火箭研究院703所、沈阳飞机(集团)有限公司,取得了良好的效果,同时,也为北京航空制造工程研究所的相关科研提供了刀具。
复合材
料系列工具技术对于复合材料应用的航空航天等领域具有广泛的应用前景。
本装置不包含复杂难加工零件,装配简单,不需要特殊的生产、装配条件,通过常规机械加工手段即可加工制造。
三、获得的专利等知识产权情况
已获得中国发明专利:
一种磨粒三维多层可控优化排布电镀工具制作方法;专利公开号:ZL200710010921.6。
一种减缓碳纤维复合材料手工制孔出口速度的方法及其缓冲装置;专利公开号:ZL200910012749.7
四、规模和效益、成本估算
每件工具的结构、尺寸可以根据使用方的特殊加工需求进行调整;每件工具制造成本由具体结构、尺寸确定,根据使用方需求确定投资规模;可以很好的完成常规加工手段无法完成的复合材料加工任务,克服了传统加工中的毛刺撕裂和分层等缺陷,达到了碳纤维等高强纤维树脂基复合材料高效无缺陷加工的目的。
五、提供技术的程度和合作方式
专利技术转让、针对用户定制供货,详情面议。
六、配图。