对黄金矿山尾矿压滤干式堆存的认识
黄金尾矿干堆技术若干问题探讨
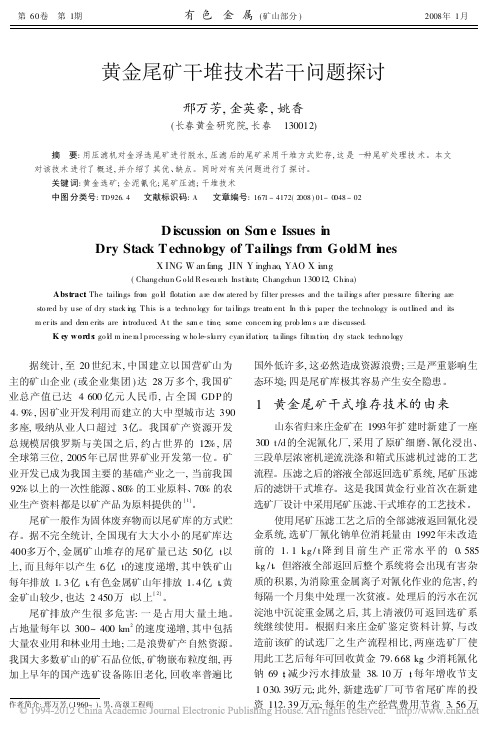
第60卷 第1期有色金属(矿山部分)2008年1月黄金尾矿干堆技术若干问题探讨邢万芳,金英豪,姚香(长春黄金研究院,长春 130012)摘 要:用压滤机对金浮选尾矿进行脱水,压滤后的尾矿采用干堆方式贮存,这是一种尾矿处理技术。
本文对该技术进行了概述,并介绍了其优、缺点。
同时对有关问题进行了探讨。
关键词:黄金选矿;全泥氰化;尾矿压滤;干堆技术中图分类号:TD92614 文献标识码:A 文章编号:1671-4172(2008)01-0048-02D iscussion on So m e Issues i nDry Stack T echnol ogy of Taili ngs fro m GoldM i nesX ING W an fang ,JIN Y inghao ,YAO X i a ng(Chang chun G o ld R esea rch Instit ute ,Changchun 130012,Chi na)Abstract :The taili ngs fro m go l d flotation a re de w atered by filter presses and the ta ili ng s after press ure filter i ng are sto red by use of dry stack i ng .T his is a techno logy for ta ili ngs treat m ent .In th i s paper ,the technology is outli ned and its m er its and dem erits are i ntroduced .A t the sa m e ti m e ,some concern i ng prob le m s a re discussed 1K ey word s :go l d m ine ra l processi ng ;w ho le -sl urry cyan i dati on ;ta ilings filtra ti on ;dry stack techno logy作者简介:邢万芳(1960-),男,高级工程师据统计,至20世纪末,中国建立以国营矿山为主的矿山企业(或企业集团)达28万多个,我国矿业总产值已达4600亿元人民币,占全国GDP 的419%,因矿业开发利用而建立的大中型城市达390多座,吸纳从业人口超过3亿。
尾矿压滤干排堆放工艺在李子金矿的应用

黄铁矿 ( 0% ~3 % ) 黄铜 矿 ( 2 0 、 1% ~ 5% ) 方 铅 、 矿 、 量 毒 砂 ; 金 属 矿 物 主 要 为 石 英 及 碳 酸 盐 少 非
( 0% 一 O% ) 次 为 绢 云母 、 泥石 、 云母 、 石 3 6 , 绿 黑 长
等 。次生 氧化矿 物有褐 铁矿 、 L 孑 雀石 等。矿石结 构主
选矿 厂4k m的李 子村河 口组 马蹄 河 口处 建成 尾 矿 干
7 . 6% ; 0 0 5m /占2 . 4% ~ 4 6 O3 一 . 7 / / 98 3 .3% 。这表 明磨矿 浮选后尾 矿粒度偏粗 , 见表 1 。 表 1 尾 矿粒级构成
粒 级/ m a r
+0 4 .5
送 人尾 矿库 , 自然沉 降后 , 矿渣堆存 库 区 , 水过 经 尾 废 滤后 由溢 流井经库 底 涵 管排 入库 外 几 个 串联 的沉 淀 池 。20 年 8 月 , 0 / 磨 矿 浮 选 车 间 建 成 。 07 40 td
20 0 9年8月底 , 选 矿 厂 院 内建 成 尾 矿 压 滤 干排 车 在 间。现行选矿 工 艺 为 : 矿 分 级 ( 磨 两段 闭路 ) 浮选 一 ( 一粗 三扫 四精 ) 金精 矿 经 压 滤 送 至精 矿 仓 , 矿 一 尾 压滤 干排到 选 矿 厂 临 时储 存 点 。2 1 0 0年 4月 , 在距
将回水池位置由设计中的2台搅拌槽前右端移至压滤车间外的左侧并将设计中4m6m滤液回水铁槽改为5m2mx18m的3个砖砌串联沉淀池排水管由2根直径为159mm的并联管路改为1根直径为250mm的管道取消了设计中的回水泵使回水自流进入河道水池与河道新水混配后再送至选矿厂200m3的高位水池供选矿厂生产使用
金矿尾矿堆积的处理及综合化利用探讨

金矿尾矿堆积的处理及综合化利用探讨摘要:作为我国储备量较为丰富的资源之一,金矿资源是我国重要的战略矿种。
我国金矿尾矿的堆积物随着我国金矿开采程度的加深而成递增趋势,严重威胁周围居民的生活安全。
本文针对金矿尾矿利用现状以及金矿尾矿堆积问题,主要分析金矿尾矿处理方法与综合化利用。
旨在推动金矿尾矿综合化利用的实现,促进资节约型、环境和谐型社会的持续发展。
关键词:金矿;尾矿处理;综合化利用;矿山环境前言世界上最早开采与利用金矿资源的国家包括我国,目前我国探明的金矿资源高达1亿吨[1]。
我国平均每年约发现27个金矿床,增加率为8.6%左右。
但金矿资源需求的日益增加以及金矿开采技术的发展,开采大量金矿资源的同时,堆积了大量的金矿尾矿[2]。
而金矿尾矿中富含大量的有毒、有害元素,危及人类生存环境,矿尾矿的堆积还能引发地质灾害;此外,金矿尾矿也是有价值的资源之一。
近年来,金矿尾矿问题已经成为社会关注的重点话题。
由此,基于整个社会都在关注人类生存环境背景下,研究金矿尾矿堆积的处理及综合化利用有重要现实意义。
1.金矿尾矿利用现状以及堆积问题金矿石选矿后废气固体物为金矿尾矿,Ph值大于10,呈碱性,主要含有SiO2(二氧化硅),此外还含有MgO(氧化镁)、Al2O3(氧化铝)、Fe2O3(氧化铁)等;还有少量的Pb(铅)、Cu(铜)、Ag(银)、Au(金)等。
金矿尾矿成分含量随着金矿资源的不同于提炼工艺技术的不同而不同,变化范围主要主要为,SiO2:65-85%、Fe2O3:5-15%、MgO:0.5-8%、CaO(游离氧化钙):0.5-2%、Na2O(氧化钠):0.5-4%、Au:0.2-0.6%。
金矿尾矿堆积后,造成的主要问题如下:第一、破坏环境。
金矿尾矿需要占用大量的空间,占用植被的土地资源,阻碍植物的生长,从而造成水土流失。
另一方面,多风天气时,金矿尾矿还会产生扬尘,扬尘中含有有毒物质,严重危及矿山周围居民的生存环境与矿山环境。
我国黄金矿山尾矿库概况

我国黄金矿山尾矿库概况黄金矿山尾矿库是指黄金矿山生产过程中产生的废弃物、固体残渣和废水在经处理后产生的固体残渣等,在矿山周边地区进行集中堆积和长期贮存的场所。
本文将对我国黄金矿山尾矿库的概况进行分析和讨论。
一、我国黄金矿山尾矿库的现状目前,我国黄金矿山尾矿库的数量较多,分布广泛。
根据相关统计数据,截至目前,我国共有50多个黄金矿山,其中大部分都建有尾矿库。
黄金矿山尾矿库通常位于矿山附近的山谷、河谷和平原地带,有些甚至建在山脚下。
这种建设方式既方便了尾矿的排放和处理,又减少了运输成本。
尾矿库的规模和容量各异,根据矿山的规模和年产量来决定。
一些大型黄金矿山的尾矿库容量可以达到几百万立方米甚至更多。
然而,尽管容量巨大,很多尾矿库的处理能力却相对较低,导致一些已满的尾矿库面临着溢出和环境风险的问题。
二、我国黄金矿山尾矿库的环境问题1.土壤和水源污染黄金矿山尾矿库中的固体残渣和废水中的化学物质会渗入土壤和水源中,导致土壤和水体的污染。
这对周边生态环境以及人类健康带来了严重的威胁。
污染物如重金属和有害化学物质长期积累,会对植物生长、动物繁衍和人类居住环境造成不可逆转的损害。
2.生态系统破坏黄金矿山尾矿库的建设常常需要破坏大量的土地和植被,导致生态系统的破坏和物种的丧失。
此外,尾矿库周边的矿山开采活动也会产生噪音和空气污染,进一步破坏周边生态环境。
3.安全隐患尾矿库的安全问题一直是关注的焦点。
由于尾矿的松散特性和堆积高度,尾矿库在地震、强降雨等自然灾害发生时容易发生滑坡和溃坝,造成严重的人员伤亡和环境破坏。
三、我国黄金矿山尾矿库的处理与管理为了减少黄金矿山尾矿库对环境的影响,我国采取了一系列的处理与管理措施:1.固体废弃物处理黄金矿山尾矿库中的固体废弃物通常通过浸出、过滤和干燥等工艺进行处理。
其中,浸出过程主要是将含金固体通过化学反应提取黄金,而过滤和干燥则是为了减少废弃物的水分含量和体积,便于长期贮存和管理。
压滤干堆——尾矿处置的新途径

压滤干堆——尾矿处置的新途径
付学忠
【期刊名称】《辽宁城乡环境科技》
【年(卷),期】1998(018)006
【摘要】用压滤干堆的方式进行了尾矿处置,不仅可以控制选矿废水对环境的污染,而且可以节约大量的生产用水和药剂,具有明显的经济效益和环境效益。
【总页数】2页(P72-73)
【作者】付学忠
【作者单位】丹东市环境保护科学研究
【正文语种】中文
【中图分类】X751
【相关文献】
1.金凤公司尾矿压滤干堆技术 [J], 于生昊;尹庆舫;卢军
2.尾矿压滤干堆在凤城地区黄金生产中的应用 [J], 傅学忠
3.天昊黄金选矿厂尾矿压滤干堆的工艺改造及效益分析 [J], 张立征;赵福财;谭琦
4.镍铁尾矿压滤干堆技术特点及实践 [J], 潘料庭;潘国煊;李云峰
5.压滤机在包子铺铁矿尾矿干堆工艺中的应用实践 [J], 张春强;邱崇栋;胡长福因版权原因,仅展示原文概要,查看原文内容请购买。
尾矿干式堆存技术发展现状与方向

尾矿干式堆存技术发展现状与方向吴鹏;胡建军;郭利杰;郑磊【摘要】尾矿干式堆存是近些年发展起来的一种新型尾矿处置技术,可根据尾矿浓度分为尾矿压滤干堆和尾矿膏体堆存。
本文针对尾矿干式堆存技术的特点,综合分析尾矿干式堆存技术的发展现状,提出了尾矿干式堆存技术存在的问题与发展方向。
%Dry-tailings stacking is a new tailings disposal technology developed in recent years ,which can be divided into press filtration stacking and paste stacking .Based on the features of the two forms of this technology ,the status and trends of dry-tailings stacking technology were analyzed .【期刊名称】《中国矿业》【年(卷),期】2014(000)0z1【总页数】4页(P203-206)【关键词】尾矿;干式堆存;尾矿膏体【作者】吴鹏;胡建军;郭利杰;郑磊【作者单位】北京矿冶研究总院,北京100160;北京矿冶研究总院,北京100160;北京矿冶研究总院,北京100160;北京矿冶研究总院,北京100160【正文语种】中文【中图分类】TD926.4长期以来,尾矿通常作为选矿废弃物以尾矿库的方式贮存。
据不完全统计,我国固体矿产长期采选排出的尾矿与废石的堆存量占地面积已达1.87~2.47万km2,全国现有尾矿库达12600多个,金属矿山堆存的尾矿量已经超过50亿t,并且以每年6亿t的速度递增[1]。
这不仅占用大量土地、污染环境,同时造成巨大浪费。
据测算,我国每年因固体废弃物污染造成的经济损失在300亿元人民币左右,其中每年堆存尾矿花费10~15亿元,维护尾矿库花费15~25亿元[2]。
尾矿压滤干堆在凤城地区黄金生产中的应用

黄
金
GoLD
尾 矿 压 滤 干 堆在 凤 城 地 区黄 金 生产 中 的应 用
傅 学忠
( 东市环境科学研究 院) 丹
摘 要 : 尾矿 库 坝体 安 全 、 从 环境 保 护 、 节能 减排 、 济 效 益 角度 , 析 了尾 矿 湿 式 堆存 方 式 存在 经 分 的 问题 , 述 了尾 矿 压 滤干堆技 术在凤 城 地 区黄金 生产 中的应 用及 其效 果 , 论 为黄金 生产 企业尾 矿 处 置及 尾 矿库 改造 提供 借鉴 依据 c n e o e i g g I nd la f o u fd pe i n a e e r h o r c v r n 0 d a e d r m s l e i g l r y fo a i n i o d m i o d o e b t to n a g l ne l
止 新建 排污 口和直接 排入 污水 。
收稿 1 :0 1—1 3期 2 1 2—0 2 作者简介 : 傅学忠 (9 0 ) 男 , 宁丹东人 , 16 一 , 辽 高级工程师 , 从事环境科研及环境 影响评价工 作; 辽宁省丹东 市人民街 3 号 , 东市环境 科学研究 l 丹 院 ,10 2 18 0
展 中的支 柱 产业 之一 。
较大 , 致使坝体 内所 堆存 的尾矿 势能较高。每 年汛 期, 因受凤城地区降雨量较大的影响 , 尾矿库坝体安 全 稳定性 成 为各 矿 山企 业 及 当地 安 全 主管 部 门的关 注焦 点 。另 外 , 为提高 金 的回收 率 , 浮选 、 化等 工艺 氰 磨 矿细度 加 大 , 矿 中 一20 目达 7 尾 0 0% ~ 5% , 易 9 容 造成堆积坝体 的浸润线偏高 , 出现坝外坡渗流 、 管涌 和坝 脚 的沼泽 化 , 尾 矿 库 坝 体 稳 定 性较 差 , 能会 使 可 给坝 下农 田 、 水域及 居 民生 活带来 安全 隐 患 。
尾矿干堆技术探讨

尾矿干堆技术探讨尾矿干堆技术探讨1 引言金属或非金属矿山开采出的矿石经选矿厂选出有价值的精矿后产生“砂”一样的废渣叫作尾矿。
这些尾矿不仅数量大(每年以亿吨计),有些还含有暂时不能回收的有用成分,如随意排放,不仅会造成资源的流失,更主要的是会增大覆盖良田的面积,淤塞河道,造成严重的环境污染,因此必须对尾矿进行妥善处理。
2 尾矿干堆工艺的实践妥善处理尾矿是摆在矿山生产工作者面前的一个重要问题。
传统的尾矿处理方法是采取尾矿直排技术,建立尾矿库;而近几年新发展的方法是采用尾矿压滤干堆新技术。
辽宁省排山楼金矿在全国黄金矿山串先采用了该项技术。
我矿在有关厂家专门订做了4台1060特大型板框压滤机,选矿排出的尾矿浆,进入搅拌槽缓冲后用渣浆泵送到压滤车间,经压滤机充分挤压成为干片状的尾渣饼,浓度达到80%以上,含水量仅有20%左右,闸皮带传送机运往尾矿于堆场里分层堆放。
为防止粉尘污染,对进入于堆场的尾矿用推土机推平并进行碾压;每逢干旱季节,还在场内喷雾洒水,使其经常保持湿润状态,井在分层干堆形成的坡段上压土盖沙,栽植耐子的沙棘树。
这样,压滤处理后尾渣中含有的微量氰化物等有害物质,已被封闭在干堆场里,避免外渗和扩散,经过长期的露天曝晒和自然降解,已基本消除了对环境的危害,被环保管理部门称之为无排污门的矿山。
3 尾矿干堆工艺的优缺点任何事物都具有相刘性、两面性,同传统直排工艺相比,结合矿山实践经验,总结了尾矿千堆技术的优缺点,详见表1。
4 尾矿干堆工艺与环境保护随着对环境保护力度的不断加大,对尾矿的妥善处瑚工作显得尤为迫切和重要。
对矿山企业来讲,尾矿处理得当与否直接影响环境建设。
通过与传统直排工艺进行比较,尾矿于堆新工艺在环保方面的优势不言而喻,无沦是节约水资源还是避免污染地下水资源,以及避免危害下游居民生产、生活等方面,尾矿于堆新工艺的应用都解决了传统直排工艺所面临的老大难问题。
在国际、国内对环境保护的呼声越来越高的趋势下,矿山企业采取干堆新技术处理尾矿已是迫在眉睫丁。
尾矿干堆工艺技术应用分析及发展前景

尾矿干堆工艺技术应用分析及发展
前景
尾矿干堆是一种资源回收利用的矿渣处理技术,它可以有效地减少废弃物的化学与环境影响,而且在处理高浓度、低体积的尾矿时表现出了高效、节能、环保的优势。
该技术的应用分析与发展前景,体现在以下几个方面。
一、技术应用分析
1. 技术特点
尾矿干堆是将含矿石的残渣分选、干燥、储存,通过感应加压、施压沉降等技术的综合应用,实现了废物碱性的稳定、无毒化、固化并回收利用的目的。
2. 协同作用
采用尾矿干堆技术,还可以配合其他技术一起使用,如光生物技术、复合材料技术等,形成更加完善的尾矿处理流程。
尾矿干堆技术的协同作用,可以进一步提升矿渣堆放的安全性和资源回收的效率。
3. 应用效果
尾矿干堆技术的应用效果非常显著,可以在短期内实现明显的环境效益。
目前,国内许多尾矿处理工程都采用了尾矿干
堆技术,如贵州水城矿区、江西葛坑冶炼厂等,均展现出良好的应用效果。
二、技术发展前景
1. 多技术协同发展
未来,尾矿干堆技术将与其他新型工艺技术协同开发,如发泡混凝土、生活垃圾焚烧技术等,实现对废弃物的高效回收利用,释放更多的资源价值。
2. 优化应用流程
尾矿干堆技术将进一步优化应用流程,降低技术成本,提升技术效率,在固废处理、废弃物资源化利用等方面,将形成更完善、更加成熟的尾矿处理技术体系。
3. 推广应用范围
尾矿干堆技术将进一步推广应用范围,由原来的一些局部应用,逐步演变成为更广泛的应用。
总之,尾矿干堆技术已经成为矿渣处理的重要工艺技术,其应用分析与发展前景也在不断呈现出积极、广阔的态势,在未来的发展中具有广阔的应用前景和极大的潜力。
尾矿干式堆存工艺要点分析及技术优势探讨

分不 同 、 物理化学特性差 异 、 处理T艺不同以及水 的存在形式 的不 同 , 不 同物 料 形 成 的 膏体 所 表现 出水 力学 指 标 相 差 较 大 。不 是 所 有 的 尾 矿 都 能 形 成 膏 体 , 对 特定 的尾 矿 进 行 必 要 的试 验 。 应 ( ) 体 尾 矿 堆 存方 式 2膏 膏体尾矿的堆存 方式虽也采用管道输送 ,但与传统 的矿浆排放的 堆存 方式有质 的区别 , 矿膏体入库 以后 , 尾 水与 固体之 间 、 固体中的粗 细颗粒之间不产生离析 , 膏体表 面不产生 流动 的水 , 于干法堆存 。加 属 拿大安大略省 Ki re d Cek尾矿堆场 始建于 17 d 3年 , 9 是世界』 第一座采 - 用膏体尾矿堆存方式 的尾矿堆场 , 当前 入场尾矿 1 吨, 2 2 亿 至 0 3年 , 设 汁入场尾矿 13 吨, 汁堆积总高度 2 mt 内蒙古乌奴格土山铜钼矿 .亿 设 9  ̄ ' l 在 国内大型有色金属矿 山中打开了膏体尾矿堆存 的先例 。现常用的膏 体尾矿 的堆存方式主要有 : 自由式堆存 、 j I 谷堆存和筑坝堆存 三种 。 I ① 自由式 堆 存 此种方法适用于开阔地带 , 膏体 自流沉积坡度在 5 7 %~ %左右 。自 f式 堆 存 可 选 择 单管 排 放 , 可 选 择 多管 轮流 前 进 式 排 放 。 l I 也 单管排放的 自f式堆存 : _ } j 此种情况下 , 会形成一个坡度较缓的圆锥 体, 稳定性较高 , 不需筑坝 , 为了防止库 内降雨对环境 的污染 , 建议在库 下游 建 一 个 拦 水 坝 , 雨 水 沉 淀 后 再 外 排 。 将 多 管 轮 流 前 进式 排 放 的 自由式 堆 存 : 法 是 指 采 用 多条 管 道 , 隔 此 问 定 距 离沿 尾 矿 沉 积 坡 度 轮 流 向前 放 矿 ,停 止放 矿 的 尾 矿 表 面 很 快 干 裂, 表面强度增加 , 时在于裂的尾矿堆上继续安装 支架和向前接管 , 此 在 先 前 排 放 的 已 干 裂 的尾 矿 上 面继 续 放 矿 。此 种 方 法 可 以增 大 膏 体 自 流 沉 积 的 角 度 , 而 增 大 尾矿 堆 存 量 , 用 于 降 水 量 少 、 发 量 大 的 地 从 适 蒸
尾矿干式堆存工艺的研究与实践
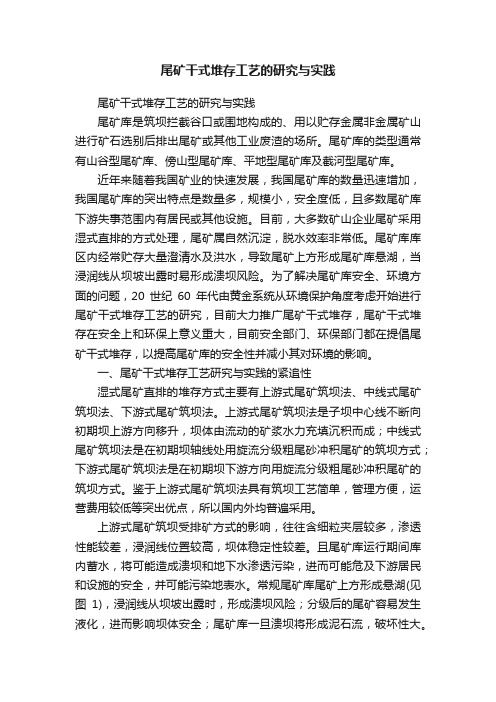
尾矿干式堆存工艺的研究与实践尾矿干式堆存工艺的研究与实践尾矿库是筑坝拦截谷口或围地构成的、用以贮存金属非金属矿山进行矿石选别后排出尾矿或其他工业废渣的场所。
尾矿库的类型通常有山谷型尾矿库、傍山型尾矿库、平地型尾矿库及截河型尾矿库。
近年来随着我国矿业的快速发展,我国尾矿库的数量迅速增加,我国尾矿库的突出特点是数量多,规模小,安全度低,且多数尾矿库下游失事范围内有居民或其他设施。
目前,大多数矿山企业尾矿采用湿式直排的方式处理,尾矿属自然沉淀,脱水效率非常低。
尾矿库库区内经常贮存大量澄清水及洪水,导致尾矿上方形成尾矿库悬湖,当浸润线从坝坡出露时易形成溃坝风险。
为了解决尾矿库安全、环境方面的问题,20世纪60年代由黄金系统从环境保护角度考虑开始进行尾矿干式堆存工艺的研究,目前大力推广尾矿干式堆存,尾矿干式堆存在安全上和环保上意义重大,目前安全部门、环保部门都在提倡尾矿干式堆存,以提高尾矿库的安全性并减小其对环境的影响。
一、尾矿干式堆存工艺研究与实践的紧追性湿式尾矿直排的堆存方式主要有上游式尾矿筑坝法、中线式尾矿筑坝法、下游式尾矿筑坝法。
上游式尾矿筑坝法是子坝中心线不断向初期坝上游方向移升,坝体由流动的矿浆水力充填沉积而成;中线式尾矿筑坝法是在初期坝轴线处用旋流分级粗尾砂冲积尾矿的筑坝方式;下游式尾矿筑坝法是在初期坝下游方向用旋流分级粗尾砂冲积尾矿的筑坝方式。
鉴于上游式尾矿筑坝法具有筑坝工艺简单,管理方便,运营费用较低等突出优点,所以国内外均普遍采用。
上游式尾矿筑坝受排矿方式的影响,往往含细粒夹层较多,渗透性能较差,浸润线位置较高,坝体稳定性较差。
且尾矿库运行期间库内蓄水,将可能造成溃坝和地下水渗透污染,进而可能危及下游居民和设施的安全,并可能污染地表水。
常规尾矿库尾矿上方形成悬湖(见图1),浸润线从坝坡出露时,形成溃坝风险;分级后的尾矿容易发生液化,进而影响坝体安全;尾矿库一旦溃坝将形成泥石流,破坏性大。
对黄金矿山尾矿压滤干式堆存的认识

( 验值 为 9 . l ) 试 9 0 % 。改 造 后 , 由压 滤 产 出 的大 量
含氰化钠尾水作为补充水进入系统 , 回球磨 , 返 增加 了浸出时 间, 浸 出率 比未 改造 时提 高 了 6 ~ 使 % 8 。浸出率提高到 9 % ~ 7 % 6 9 %。并且构成 了三级 逆流洗涤加尾矿压滤效率的联合作业 , 洗涤率提高 到 9 .2 , 7 1% 比未改造时提高了 7 ~ % , % 9 减少了已
一
以归来庄金矿其 中的 1 年报表统计 , 试选厂 回 收金 1.7k , O3 g大选厂回收金 5 . 1k , 8 7 g合计 6 .8 9 O k, g与计算值基本吻合 。 对此 , 我们 按其 生产 月报 表数 据 : 尾矿 滤液 品位
平均为 00 / , .3gL 固体成饼状 留在滤室。从给料 至 排水孔不出滤液时止为压滤完成 , 时停止工作机 此 给料 , 打开下一系列工作机阀门, 开始卸料 。头板返 回, 放松压紧滤板 , 传动系统带动拉板挂钩作往复运 动, 将滤 板一 块块 地相继 拉开 , 滤饼 靠 自重及 滤布 张 力脱落, 并被输送机械运走、 堆存。至此完成一个工
维普资讯
第2 9卷第 2期
20 07年 4月 甘肃冶金
V0 . 9 N0 2 12 . Ap . 2 0 r ,0 7
GANS U METAL LURGY
文 章 编 号 :6 24 6 (07 0 -040 17 - 1 2 0 )204 - 4 3
溶 金 的流失 。
矿在这方面做 的就比较成功。这种工艺与常规湿式 堆存工艺相 比有较大的创新 , 已溶金 的回收率有 明 显地提高 , 充分利用了矿产资源 , 降低了选矿单位成
本 。并对矿山企业在尾矿库难找、 难建 、 投资大的地 区, 不建尾矿库建小型尾矿堆场 , 在洼地或平地干式
干式尾矿排放与堆存安全监管

制定干式尾矿排放与堆存安全监管法规,明确监管职责和监管要求
制定干式尾矿排放与堆存安全技术标准,明确排放与堆存技术要求
制定干式尾矿排放与堆存安全监管制度,明确监管流程和监管措施
制定干式尾矿排放与堆存安全应急预案,明确应急处置措施和应急响应流程
01
02
03
04
加强监管力度
制定严格的排放标准和堆存规范
01
建立完善的监管体系,加强监管力度
02
定期对尾矿排放和堆存情况进行检查和评估
03
对违规行为进行严厉处罚,提高企业守法意识
04
提高企业安全意识
03
定期进行安全检查,及时发现并消除安全隐患
02
建立健全安全管理制度,规范企业安全生产行为
01
加强安全教育培训,提高员工安全意识
04
加强应急救援演练,提高企业应对突发事件的能力
企业对安全监管的抵触情绪,影响监管工作的开展
企业对安全监管的投入不足,影响监管效果
企业对安全监管的认识不足,配合度不高
C
B
A
D
4
干式尾矿排放与堆存安全监管的前景
单击此处输入你的正文,文字是您思想的提炼,为了最终演示发布的良好效果,请尽量言简意赅的阐述观点.
技术进步
3
2
4
1
自动化监测技术:提高监测效率,降低人工成本
03
如何利用现代科技手段,提高尾矿排放与堆存的效率和安全性
04
监管难度
STEP4
STEP3
STEP2
STEP1
尾矿排放与堆存点多面广,监管难度大
尾矿排放与堆存涉及多个行业,监管标准不统一
尾矿排放与堆存监管技术手段不足,难以实时监控
在排山楼金矿的成功应用与改造实践
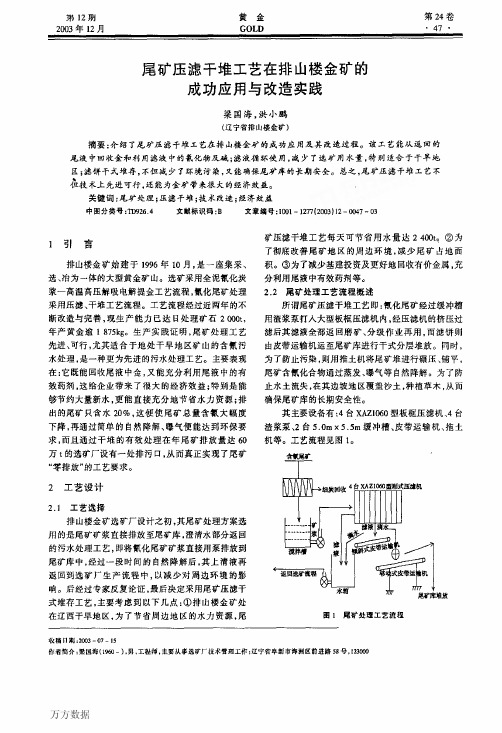
弟12刑黄金第24卷尾矿压滤干堆工艺在排山楼金矿的成功应用与改造实践梁国海,洪小鹏(辽宁省排山楼盎矿)摘要:介绍了尾矿压滤干堆I艺在排山棱金矿的成功应用及其改造过程。
谊工艺能从返回的尾液中回收金和利用滤液中的氰化物及碱;滤液循环使用,减少了选矿用水量,特别适合于干旱地区;滤饼干式堆存,不但减少丁环境污染,又能确保尾矿库的长期安全。
总之,尾矿压滤干堆工艺不但技术上先进可行,还能为金矿带来很大的经济效益。
关键词:尾矿处理;压滤干堆;技术改造;经济效益中图分类号:TD9264文献标识码:B文章编号:1001—1277(2003)12—0047—031引言排山楼金矿始建于1996年10月,是一座集采、选、冶为一体的大型黄金矿山。
选矿采用全泥氰化炭浆一高温高压解吸电解提金工艺流程,氰化尾矿处理采用压滤、干堆工艺流程。
工艺流程经过近两年的不断改造与完善,现生产能力已达日处理矿石2000t,年产黄金逾1875kg。
生产实践证明,尾矿处理工艺先进、可行,尤其适合于地处干旱地区矿山的含氰污水处理,是一种更为先进的污水处理工艺。
主要表现在:它既能回收尾液中金,又能充分利用尾液中的有效药剂,这给企业带来了很大的经济效益;特别是能够节约大萤新水,更能直接充分地节省水力资源;排出的尾矿只含水20%,这便使尾矿总量含氰大幅度下降,再通过简单的自然降解、曝气便能达到环保要求,而且通过干堆的有效处理在年尾矿排放景达60万t的选矿厂设有一处排污口,从而真正实现了尾矿“零排放”的工艺要求。
2工艺设计2.1工艺选择排山楼金矿选矿厂设计之初,其尾矿处理方案选用的是尾矿矿浆直接排放至尾矿库,澄清水部分返回的污水处理工艺,即将氰化尾矿矿浆直接用泵排放到尾矿库中.经过一段时间的自然降解后,其上清液再返回到选矿厂生产流程中,以减少对周边环境的影响。
后经过专家反复论证,最后决定采用尾矿压滤干式堆存工艺,主要考虑到以下几点:①排山楼金矿处在辽西干旱地区,为了节省周边地区的水力资源,尾矿压滤干堆工艺每天可节省用水量达2400t。
尾矿干堆工艺技术应用分析及发展前景
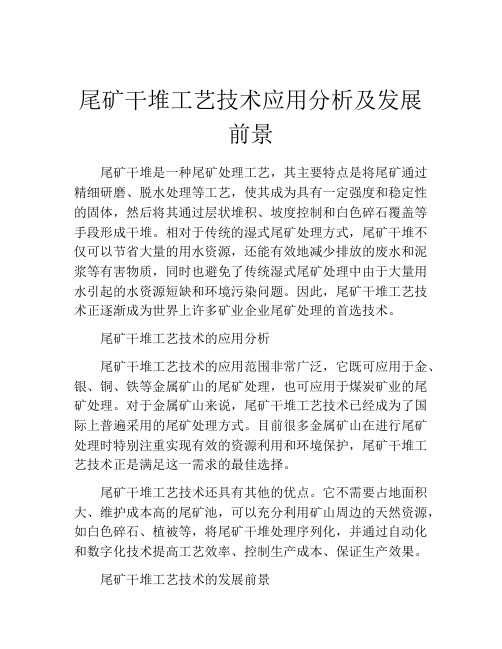
尾矿干堆工艺技术应用分析及发展前景尾矿干堆是一种尾矿处理工艺,其主要特点是将尾矿通过精细研磨、脱水处理等工艺,使其成为具有一定强度和稳定性的固体,然后将其通过层状堆积、坡度控制和白色碎石覆盖等手段形成干堆。
相对于传统的湿式尾矿处理方式,尾矿干堆不仅可以节省大量的用水资源,还能有效地减少排放的废水和泥浆等有害物质,同时也避免了传统湿式尾矿处理中由于大量用水引起的水资源短缺和环境污染问题。
因此,尾矿干堆工艺技术正逐渐成为世界上许多矿业企业尾矿处理的首选技术。
尾矿干堆工艺技术的应用分析尾矿干堆工艺技术的应用范围非常广泛,它既可应用于金、银、铜、铁等金属矿山的尾矿处理,也可应用于煤炭矿业的尾矿处理。
对于金属矿山来说,尾矿干堆工艺技术已经成为了国际上普遍采用的尾矿处理方式。
目前很多金属矿山在进行尾矿处理时特别注重实现有效的资源利用和环境保护,尾矿干堆工艺技术正是满足这一需求的最佳选择。
尾矿干堆工艺技术还具有其他的优点。
它不需要占地面积大、维护成本高的尾矿池,可以充分利用矿山周边的天然资源,如白色碎石、植被等,将尾矿干堆处理序列化,并通过自动化和数字化技术提高工艺效率、控制生产成本、保证生产效果。
尾矿干堆工艺技术的发展前景尾矿干堆工艺技术发展前景看好。
其主要原因有以下几点:1.环保意识提高:随着环保意识的普及,各国政府对于矿山环境保护越来越重视。
通过采用尾矿干堆工艺技术,可以大大减少排放的有害物质,达到环境友好型低成本生产。
2.资源利用效果显著:尾矿干堆可以充分利用矿山周边的天然资源,如白色碎石、植被等,既有利于减少生产成本,也可以实现资源再利用,减少资源浪费。
3.国际市场大:尾矿干堆工艺技术在国际矿业市场上应用较为广泛,国内也在逐步推广应用。
预计未来随着国内外矿业市场的逐步扩大,将有望成为矿山尾矿处理的主流方式。
总之,尾矿干堆工艺技术的应用和发展对于资源利用和环境保护都有着重要的意义,该工艺随着技术的不断提升,将在未来得到更为广泛和深化的应用。
关于干式尾矿排放与堆存安全监管的建议

2.尾矿干排在国内的发展趋势 目前不完全统计大约20几座矿山采用了尾矿干式排放,主要 集中在黄金和有色矿山,大多数为中小型黄金矿山。原矿处 理规模50~2000t/d左右。 黄金矿山尾矿库的特点: 由于黄金工业生产的特殊性,形成其尾矿库的一些特点。 黄金矿山相对规模较小,所以尾矿库在服务年限内要求的容 积也较小,尾矿库址的选择,为了少占农田,就地就近,多 数地形条件差,山谷峡窄、坡陡、调洪库容小。另外由于选 矿工艺的特点,多采用浮选、氰化或浮选与氰化等联合工艺 提金,并且近年来为提高金的回收率,加大了磨矿细度,其
10 干式堆放场(库)运行管理安全防范的重点 (4) 禁止在尾矿干式堆放场(库)中出现湿、干混排现 象。 (5) 为防止干式尾矿堆场(库)使用期间堆积表面尾矿扬 尘对附近环境产生污染,可采取洒水喷淋或喷洒化学固结剂 等措施,保持表面湿润固结。 化学固结剂的种类:粘结剂(树脂胶黏剂);木质素磺酸 钠、钙、铵;红杉树皮提取液;水泥和石灰;硅酸钾;硅酸 钠、氯化钙(6%)和硅酸钠等。 (6) 尾矿堆放,每个台阶高度不宜超过10~30米,台阶宽 度根据采用设备的不同,控制在合理范围内。终期堆积坝坡 的修整,要逐层碾压到一定的宽度。(建议碾压宽 15~30m)。
干式尾矿排放与堆存
主要内容 1.尾矿干排的定义 2.尾矿干排在国内的发展趋势 3.目前干式尾矿堆场(库)型式及目前运行状况 4.尾矿库湿排与干式排放技术、经济比较 5 尾矿湿排、干排安全性比较 6.干式排放的优缺点 7.干式排放设备的适应性 8.干尾砂的运输方式: 9.排放方式: 10 干式堆放场(库)运行管理安全防范的重点 11.干式尾矿堆放场(库)病害防治 12. 压滤(过滤)设备运行管理 13.安全生产管理职责 14. 干式尾矿堆放场(库)的监测 15. 干式尾矿堆放场(库)植物覆盖
尾矿贮存方式的一种趋势——干堆技术

尾矿贮存方式的一种趋势——干堆技术
宋雪娟
【期刊名称】《新疆有色金属》
【年(卷),期】2007(30)B08
【摘要】无论金属矿山还是非金属矿山,每年都产生大量的尾矿,而传统的尾矿贮存方式为此而建造大量的尾矿库,据统计我国每年需要占用300~400km2的各种农业或林业用地。
黄金矿山尤其使用全泥氯化提金工艺的矿山,为尽量利用氯化废水以及回收氯化物及其已溶金而降低物耗与提高企业的经济效益,所以对尾矿进行压滤,压滤后的尾矿采用干堆方式贮存。
这是尾矿一般贮存方式的一种革命,且前仅在岩金矿山使用,其它矿山或矿业未见有应用的报道。
本文对此技术略作介绍。
【总页数】3页(P73-75)
【作者】宋雪娟
【作者单位】乌鲁木齐有色冶金设计研究院,830000
【正文语种】中文
【中图分类】TD235.4
【相关文献】
1.尾矿库干堆与膏体堆技术
2.铜尾矿的一种新型干堆技术
3.尾矿干排干堆技术在西北某铜选厂的应用
4.CANDU6重水堆乏燃料干式贮存技术优化研究及应用
5.山东
煤机装备集团有限公司“尾矿分级过滤干堆新技术”开创我国绿色无尾矿山新纪元
因版权原因,仅展示原文概要,查看原文内容请购买。
尾矿干堆工艺

尾矿干堆工艺尾矿干堆工艺是一种常用的尾矿处理方法,广泛应用于矿山和冶金行业。
本文将介绍尾矿干堆工艺的原理、优点和应用,并分析其中的挑战和改进方向。
尾矿是矿山开采过程中产生的废弃物,通常含有大量的固体颗粒和水分。
传统的尾矿处理方法主要是采用湿式堆放,即将尾矿通过水力输送到堆放场,并利用水的重力分离作用将尾矿中的固体颗粒沉淀下来,形成堆放层。
然而,湿式堆放存在着水资源浪费、环境污染和安全隐患等问题。
相比之下,尾矿干堆工艺通过去除尾矿中的水分,将其转化为干燥的固体颗粒,然后堆放在特定的场地上。
尾矿干堆工艺的实施过程可以分为几个步骤:首先,使用脱水设备对尾矿进行脱水处理,将尾矿中的水分含量降低到一定程度;然后,将脱水后的尾矿通过输送设备运输到干堆场地;最后,将尾矿均匀地堆放在干堆场地上,形成干堆。
尾矿干堆工艺相比湿式堆放具有多个优点。
首先,尾矿干堆工艺不需要大量的水资源,可以节约水资源的使用。
其次,尾矿干堆工艺不会产生大量的废水,减少了对环境的污染。
此外,尾矿干堆工艺可以降低尾矿的体积,减少了堆放场地的占地面积。
同时,干堆可以更好地保持尾矿的稳定性,减少堆体的滑坡和坍塌风险,提高了安全性。
尽管尾矿干堆工艺具有众多优点,但也存在一些挑战和改进的方向。
首先,尾矿干堆工艺对脱水设备的要求较高,需要选择合适的设备来实现高效的脱水效果。
其次,尾矿干堆工艺对干堆场地的要求也较高,需要选择合适的场地,并采取措施防止风化和侵蚀。
此外,尾矿干堆工艺的实施需要综合考虑经济、环境和安全等因素,进行全面的评估和规划。
尾矿干堆工艺在矿山和冶金行业中得到广泛应用。
例如,在金矿开采中,尾矿干堆工艺可以实现金矿尾矿的高效处理,提高金矿的回收率。
在铁矿开采中,尾矿干堆工艺可以减少尾矿的体积,节约资源。
在铜冶炼中,尾矿干堆工艺可以减少尾矿的含水率,提高资源利用效率。
尾矿干堆工艺是一种高效、环保的尾矿处理方法。
通过脱水处理和干堆堆放,可以降低尾矿的水分含量,减少水资源的使用,减少环境污染。
关于干式尾矿排放与堆存安全监管的建议

关于干式尾矿排放与堆存安全监管的建议1.尾矿干排的定义l 天然状态的土一般由固体,液体和气体三部分组成.若土中的孔隙全部由气体填充时,称干土.l 土的含水率在5%以内为干土;5%-30%为潮湿土;30%以上为湿土。
l 干式尾砂,通常讲采用浓缩或压滤(过滤)设备,将尾矿中的含水率控制23%以内,称为干尾砂。
2.尾矿干排在国内的发展趋势l 目前不完全统计大约20几座矿山采用了尾矿干式排放,主要集中在黄金和有色矿山,大多数为中小型黄金矿山。
原矿处理规模50~2000t/d左右。
l 黄金矿山尾矿库的特点:l 由于黄金工业生产的特殊性,形成其尾矿库的一些特点。
l 黄金矿山相对规模较小,所以尾矿库在服务年限内要求的容积也较小,尾矿库址的选择,为了少占农田,就地就近,多数地形条件差,山谷峡窄、坡陡、调洪库容小。
另外由于选矿工艺的特点,多采用浮选、氰化或浮选与氰化等联合工艺提金,并且近年来为提高金的回收率,加大了磨矿细度,其尾矿粒度为-200目占80%~95%之间居多,给尾矿堆存筑坝带来一定困难,通常用山皮土堆筑子坝,同时给企业管理带来了困难。
l 近几年来,国家加大了对环境治理的力度,为贯彻《中华人民共和国固体废物污染环境防治法》,尤其对一般工业固体废物贮存、处置场的选址、设计、运行管理、关闭与封场、以及污染控制与监测等内容做出了详细规定(GB18599-2001)。
l ⑴第Ⅰ类一般工业固体废物l 按照GB5086规定方法进行浸出试验而获得的浸出液中,任何一种污染物的浓度均未超过GB8978最高允许排放浓度,且PH值在6至9范围之内的一般工业固体废物。
l ⑵第Ⅱ类一般工业固体废物l 按照GB5086规定方法进行浸出试验而获得的浸出液中,有一种或一种以上的污染物浓度超过GB8978最高允许排放浓度,或者是pH值在6至9范围之外的一般工业固体废物。
l 所以在黄金矿山尾矿干式排放发展较快主要源于国家环保方面的规定。
l 发展趋势:目前由国营矿山已发展到地方及私企矿山,尾矿干式排放有向大型矿山发展的趋势。
- 1、下载文档前请自行甄别文档内容的完整性,平台不提供额外的编辑、内容补充、找答案等附加服务。
- 2、"仅部分预览"的文档,不可在线预览部分如存在完整性等问题,可反馈申请退款(可完整预览的文档不适用该条件!)。
- 3、如文档侵犯您的权益,请联系客服反馈,我们会尽快为您处理(人工客服工作时间:9:00-18:30)。
对黄金矿山尾矿压滤干式堆存的认识资讯类型:行业信息加入时间:2009年5月4日17:20对黄金矿山尾矿压滤干式堆存的认识田赞生(兰州有色冶金设计研究院有限公司,甘肃兰州730000)摘要:本文简要介绍板框式压滤机设备在黄金矿山尾矿压滤干式堆存工艺及其选金系统中使用情况。
重点介绍实际运行过程中压滤设备运行的可靠性和经济效益,着重分析了企业在生产过程中获得的经济效益和社会效益及合理应用压滤干式堆存工艺等方面的问题。
关键词:黄金矿山;尾矿压滤干式堆存;板框式压滤机;经济效益;社会效益。
中图分类号:TD926. 4文献标识码:A1前言黄金矿山尾矿压滤干式堆存工艺,很多年前就应用于黄金矿山尾矿的处理工艺上。
山东归来庄金矿在这方面做的就比较成功。
这种工艺与常规湿式堆存工艺相比有较大的创新,已溶金的回收率有明显地提高,充分利用了矿产资源,降低了选矿单位成本。
并对矿山企业在尾矿库难找、难建、投资大的地区,不建尾矿库建小型尾矿堆场,在洼地或平地干式堆存尾矿定期覆土复耕,还地于民等方面开创了一条新路。
同时企业在生产过程中也获得一定的经济效益和社会效益,很值得我们借鉴。
2尾矿压滤干式堆存简介归来庄金矿地处鲁西南丘陵地区,采矿为露天开采。
选矿采用全泥氰化锌粉置换提金工艺。
20世纪90年代初建成日处理120 t规模的试验选矿厂(以下称试选厂),改造尾矿设施变尾矿湿式堆存改为压滤干式堆存。
尾矿堆场距选厂约2 km。
1992年开始设计日处理350 t规模选厂(以下称大选厂)。
在大选厂设计中尾矿处理参照试选厂工业指标及工艺流程采用干式堆存工艺。
1993年建成投产, 1994年大选厂达产。
平均每班处理矿石110~120 t。
试选厂尾矿改造选用了两台240 m²板框式压滤机, 1台工作, 1台备用。
大选厂尾矿压滤选用4台340 m²板框式压滤机, 3台工作, 1台备用。
1994年下半年又扩建一个400 t/d的选厂,同样选用340 m²板框式压滤机4台, 3台工作, 1台备用。
金选矿厂在未改造为尾矿压滤工艺时,浸出率为89. 30% (试验值为95. 28% ),洗涤率为89. 64%(试验值为99. 01% )。
改造后,由压滤产出的大量含氰化钠尾水作为补充水进入系统,返回球磨,增加了浸出时间,使浸出率比未改造时提高了6% ~8%。
浸出率提高到96% ~97%。
并且构成了三级逆流洗涤加尾矿压滤效率的联合作业,洗涤率提高到97. 12%,比未改造时提高了7% ~9%,减少了已溶金的流失。
3尾矿压滤设备及工作流程国内现在压滤机生产企业很多,生产能力都很大,设备使用寿命比20世纪90年代初大有改进,操作自动化程度也提高了,生产的各类型号的压滤机规格也比较完善,有50 m²、60 m²、100 m²、150 m²、240 m²、340 m²、500 m²、700 m²、1 050 m²等规格。
压滤机主要由油缸液压系统主梁传动、头板、尾板、滤板、管路、液压系统、传动系统、电控系统等部分组成。
压滤机工作时首先开启液压系统,活塞杆伸出将滤板推到工作位置并压紧,压紧压力约为13~14MPa,使滤板间构成密封的滤室。
然后给料泵(一般为渣浆泵)将矿浆从止推板的给料孔输入。
进入滤室的矿浆借助给料泵的工作压力使矿浆固液分离。
液体经滤布、滤板排水口流出,滤液中含固体平均为0. 03 g/L,固体成饼状留在滤室。
从给料至排水孔不出滤液时止为压滤完成,此时停止工作机给料,打开下一系列工作机阀门,开始卸料。
头板返回,放松压紧滤板,传动系统带动拉板挂钩作往复运动,将滤板一块块地相继拉开,滤饼靠自重及滤布张力脱落,并被输送机械运走、堆存。
至此完成一个工作单循环。
滤板一般为铸铁或工程塑料材料,滤布一般采用无纺织滤布。
压滤机操作条件和生产参数:滤板压紧压力13~14MPa;注浆压力0. 5~0. 8MPa;一次单循环工作时间40~45 min,其中注浆20~30 min(视矿浆重量浓度而定),卸料10~15 min;滤液中固体含量0. 05~0. 03 g/L;滤饼含水量22% ~23%;一次单循环处理干料0. 023~0. 03 t/m²•h。
型号不同,单位处理干料量不同。
4经济效益和社会效益分析4.1企业经济效益以归来庄金矿为例,依据该矿生产的实践和生产过程中积累的大量资料和数据进行了核算和论证,从以下几个方面分析:4. 1. 1已溶金回收率的分析在未改造前,浸出率只有89%左右,三段逆流洗涤率平均只有89. 64%。
改造后,将滤液作为补加水进入球磨时也同时带入了大量剩余氰化钠药剂,从球磨分级段就开始浸出,完成浸出作业后,浸出率一般都在95%以上。
浸出时间的增长保证了较高的浸出效果。
有好的浸出效果,如何提高洗涤效率就成了问题的关键所在。
由于归来庄金矿矿石泥化程度高,磨矿颗粒细,沉降速度慢,浓密机的排矿浓度低等因素造成洗涤效果差。
一部分已溶金溶液随尾矿进入尾矿库,而矿山一般都不重视尾矿库回水的利用,加上库内地表水和大气降水的稀释、渗透等因素,使尾矿水回水率很低,势必造成已溶金的流失。
针对上述问题,根据试选厂改造尾矿压滤工艺工业性试验显示出的优越性,在改造设计中采用了尾矿压滤干式堆存工艺。
由于压滤处理后尾矿中的已溶金溶液充分回收,弥补了洗涤率低的不足,使洗涤率提高了7% ~9%,其总洗涤率达到98% ~99%。
滤液的循环利用解决了上述问题,提高了回收率,使企业经济效益得到提高。
以归来庄金矿其中的1年报表统计,试选厂回收金10. 37 kg,大选厂回收金58. 71 kg,合计69. 08kg,与计算值基本吻合。
对此,我们按其生产月报表数据:尾矿滤液品位试选厂0. 249 g/m³,滤液量41 583. 7 m³;大选厂滤液金品位0. 288 g/m³,滤液量203 817. 32 m³。
如果滤液按90% ~95%回收(进入流程中有一定量的损耗),置换率、冶炼率均按99%用另一种方法推算,Au=年产出滤液(m³)×流程中损耗(% )×置换率(% )×冶炼率(% )×滤液金品位(g/m³),有:试选厂Au=41 583. 7×0. 9×0. 99×0. 99×0.249=9 133. 5 g大选厂Au=203 817. 32×0. 95×0. 99×0. 99×0. 288=54 654. 7 g两厂合计回收金63. 788 kg。
按这种方法计算虽然低于前种方法,但每年也约有63 kg合质金得到回收。
采用尾矿压滤干式堆存工艺给企业带来的经济效益是非常明显的。
4. 1. 2成本分析⑴尾矿压滤作业成本。
依据归来庄金矿生产中统计的指标及材料消耗的成本计算:每完成压滤1 t含水22% ~23%的尾矿渣,发生单位综合作业成本6. 17元(综合成本包括压滤机辅助材料、电费、运费、工资、维修费等),同该矿原有氯碱法处理1 m³污水所发生的成本相当。
假设尾矿排放浓度为40%时,其固液比1: 1. 5,按氯碱法处理1 t尾矿渣,发生单位综合作业成本约为9. 25元,尾矿压滤处理尾矿渣的成本明显低于氯碱法处理尾矿渣的成本。
⑵氰化钠消耗量分析。
采用压滤作业后含有氰化钠的滤液返回了系统,被二次利用,降低了药剂的投入量,减少了剩余药剂有效成分的浪费。
统计数据表明:试验值和未改压滤工艺之前氰化钠单耗均为1~1. 5 kg/t原矿,改造后氰化纳单耗平均为0. 585 kg/t原矿,单耗减少了0. 515~0. 520 kg。
每年光减少购入氰化钠的费用就约50%。
⑶回水的利用。
压滤作业使约80%左右的选金用水返回了选矿工艺流程,节省了大量的补加新水,节省了用水成本,同时减少了生产污水的处理费用和环境污染治理费用,回水利用指标高于国家标准。
缓解了与地方争水的矛盾,保护了水资源的过量开采,保护了环境,利国利民。
4. 1. 3基本建设投资分析在国内现有的冶金矿山的尾矿库基本都是由尾矿坝、排水设施和输送系统3大部分组成。
单就秦岭一带矿山尾矿库而言,排水设施主要都是起排洪作用,其规模之大,投资之高,往往成为一项工程建设的主要投资方面。
如果建设一个500 t/d规模金选矿矿山的尾矿库,服务年限20 a,按现市场价格计算:基建时,用土石方干砌筑坝,库内排水设施的施工,征地等一般需要570~600万元左右。
而干式堆存就可省去大规模的排水设施和必须有一定高度的尾矿坝的建设投资,只需要很少资金建设简单的堆场。
也可在荒坡、洼地等处堆存。
干式堆存的基建费用主要是在购买压滤机和厂房建设方面,一般需要400万元左右。
如果把与堆场间的修路投资、堆场的基建投资加在一起约400~650万元左右。
分析结果表明干式堆存和湿式堆存基础建投资相差不多。
尾渣干堆场也可和废石场综合利用。
另外,干式堆存和湿式堆存的年经营费基本相同。
4.2社会效益采用尾矿压滤干式堆存工艺虽然尾矿压滤后其滤饼(尾渣)仍带有一定含量的氰化钠残液,但对于氧化矿含泥率较高的矿石来说,压滤后因尾矿颗粒细、含泥多、黏性强、滤饼透水性能差,残液难以排出,在堆场中含氰化钠残液尾渣经自然净化,其中的氰化钠(CN-)会发生降解。
在雨季时,受大气降水的淋滤,难免有少量残存的CN-被雨水析出,会对周围环境造成一定的污染。
但与湿式建库堆存比较,尾矿渣中含的CN-量必定是减少了很多,给处理工作节省了大量的资金和工作量,且处理方法也相对简单,只需定期定时在尾矿渣上投撒漂白粉就基本可解决污染问题,这样极大地改善了对环境的污染。
同时,尾矿堆存和排水设施也简化了,排水设施由地下变成了地表的工作和建设,便于监查和维护,消除了尾矿库的事故威胁。
由于充分利用了选矿回水,减少了新水使用量,缓解了与地方争水的矛盾。
干式堆存同时也减少了库区使用范围,保证了少占地、少征地的设计原则,把地表环境破坏降低到最小程度,缓解了与地方争地,降低生产单位基建期投资负担。
总之,采用尾矿干式堆存带来的社会效益也是非常明显的。
5存在问题干式堆存尾矿工艺还存在一定的局限性,并不是什么黄金矿山都能采用,它受地形、规模、矿石性质等一系列条件制约。
⑴规模太大时基建投资比较高,且滤饼的运输也是问题。
如果堆场离选厂较远时,就要修路和增加运输设备,加大了运营成本,使企业效益降低。
⑵地形不理想且大气降水较丰富的地区,同样要投入相当数量的资金建设堆存场地,以防止发生含CN-尾渣流失和污染环境。