影响刀具磨损的几种原因
影响刀具磨损的原因分析及改善措施
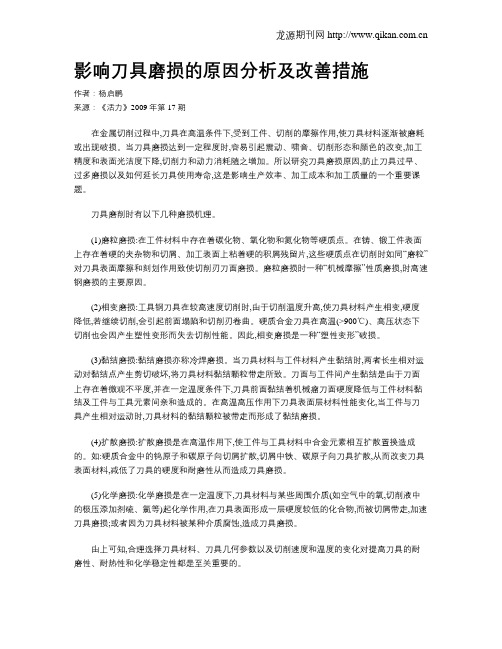
影响刀具磨损的原因分析及改善措施作者:杨启鹏来源:《活力》2009年第17期在金属切削过程中,刀具在高温条件下,受到工件、切削的摩擦作用,使刀具材料逐渐被磨耗或出现破损。
当刀具磨损达到一定程度时,容易引起震动、啸音、切削形态和颜色的改变,加工精度和表面光洁度下降,切削力和动力消耗随之增加。
所以研究刀具磨损原因,防止刀具过早、过多磨损以及如何延长刀具使用寿命,这是影响生产效率、加工成本和加工质量的一个重要课题。
刀具磨削时有以下几种磨损机理。
(1)磨粒磨损:在工件材料中存在着碳化物、氧化物和氮化物等硬质点。
在铸、锻工件表面上存在着硬的夹杂物和切屑、加工表面上粘着硬的积屑残留片,这些硬质点在切削时如同“磨粒”对刀具表面摩擦和刻划作用致使切削刃刀面磨损。
磨粒磨损时一种“机械摩擦”性质磨损,时高速钢磨损的主要原因。
(2)相变磨损:工具钢刀具在较高速度切削时,由于切削温度升高,使刀具材料产生相变,硬度降低,若继续切削,会引起前面塌陷和切削刃卷曲。
硬质合金刀具在高温(>900℃)、高压状态下切削也会因产生塑性变形而失去切削性能。
因此,相变磨损是一种“塑性变形”破损。
(3)黏结磨损:黏结磨损亦称冷焊磨损。
当刀具材料与工件材料产生黏结时,两者长生相对运动对黏结点产生剪切破坏,将刀具材料黏结颗粒带走所致。
刀面与工件间产生黏结是由于刀面上存在着微观不平度,并在一定温度条件下,刀具前面黏结着机械瘤刀面硬度降低与工件材料黏结及工件与工具元素间亲和造成的。
在高温高压作用下刀具表面层材料性能变化,当工件与刀具产生相对运动时,刀具材料的黏结颗粒被带走而形成了黏结磨损。
(4)扩散磨损:扩散磨损是在高温作用下,使工件与工具材料中合金元素相互扩散置换造成的。
如:硬质合金中的钨原子和碳原子向切屑扩散,切屑中铁、碳原子向刀具扩散,从而改变刀具表面材料,减低了刀具的硬度和耐磨性从而造成刀具磨损。
(5)化学磨损:化学磨损是在一定温度下,刀具材料与某些周围介质(如空气中的氧,切削液中的极压添加剂硫、氯等)起化学作用,在刀具表面形成一层硬度较低的化合物,而被切屑带走,加速刀具磨损;或者因为刀具材料被某种介质腐蚀,造成刀具磨损。
刀具磨损的名词解释

刀具磨损的名词解释刀具,作为工业生产和日常生活中广泛使用的工具,其磨损现象是不可避免的。
刀具磨损可以指刀具在使用过程中,由于剪切、切削、研磨等力学作用而导致的表面材料减少、形状变化和性能下降的现象。
刀具磨损主要有以下几种类型。
1.刀刃磨损:刀刃磨损是刀具使用过程中最常见的磨损类型。
当刀具与被加工材料接触和摩擦时,由于受到力学力的作用,刀刃表面的材料会发生磨损和疲劳,导致刀刃的尖端变钝、边缘变钝以及表面光洁度降低。
这种磨损会导致切割质量下降、加工速度减慢、切削力增大等问题。
2.刃口毛刺:在刀具进行切削作业时,如果材料硬度比较高或者切削速度较快,就容易产生刃口毛刺。
刃口毛刺是指刀具的刀刃在磨损过程中,产生的不规则边缘和挂毛现象。
刃口毛刺会导致被加工材料的表面粗糙度增加、加工精度降低,甚至影响材料的机械性能和外观质量。
3.碳化物层磨损:在高温和高压环境下,刀具通常会与被加工材料发生化学反应,导致碳化物层的磨损。
碳化物层磨损通常表现为刀具刀刃表面的光洁度下降、表面出现裂纹、刀刃韧性减弱等现象。
这种磨损对刀具的使用寿命和切削性能都会产生明显的影响。
刀具磨损的原因可能有多种。
首先,刀具与被加工材料之间的摩擦力和剪切力会使刀具表面材料发生疲劳破坏。
其次,刀具在高温和高压环境中与被加工材料之间的化学反应也会导致刀具磨损。
此外,刀具的设计和制造质量、使用条件以及切削参数等也会对刀具的磨损产生影响。
为了减少刀具磨损,可以采取以下几种方法。
首先,选择耐磨性能好的刀具材料,如高速钢、硬质合金、陶瓷等。
其次,合理选择刀具的几何形状和结构,以便提高切削效率和降低刀具磨损。
另外,通过对刀具进行表面处理和涂层,可以增强其硬度、耐磨性和抗腐蚀性能。
此外,在加工过程中,合理选择切削速度、进给量和切削深度,以减少刀具的磨损。
总之,刀具磨损是一种不可避免的现象,但通过合理选择刀具材料、设计和制造,以及优化切削参数等措施可以有效减少刀具磨损,提高切削效率和降低生产成本。
刀具磨损的几种原因
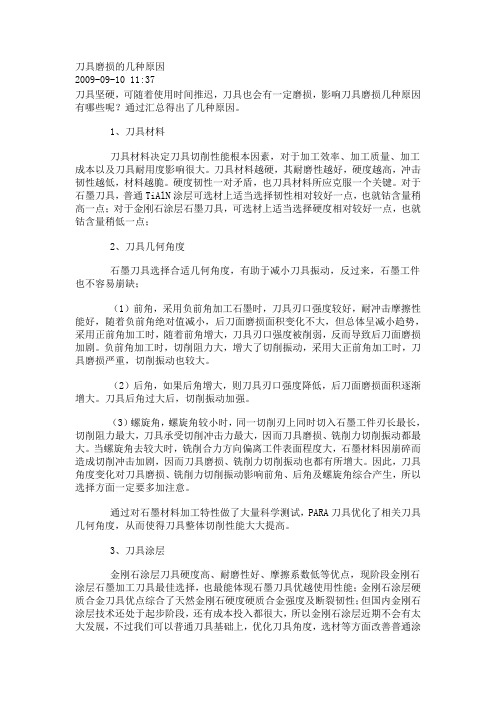
刀具磨损的几种原因2009-09-10 11:37刀具坚硬,可随着使用时间推迟,刀具也会有一定磨损,影响刀具磨损几种原因有哪些呢?通过汇总得出了几种原因。
1、刀具材料刀具材料决定刀具切削性能根本因素,对于加工效率、加工质量、加工成本以及刀具耐用度影响很大。
刀具材料越硬,其耐磨性越好,硬度越高,冲击韧性越低,材料越脆。
硬度韧性一对矛盾,也刀具材料所应克服一个关键。
对于石墨刀具,普通TiAlN涂层可选材上适当选择韧性相对较好一点,也就钴含量稍高一点;对于金刚石涂层石墨刀具,可选材上适当选择硬度相对较好一点,也就钴含量稍低一点;2、刀具几何角度石墨刀具选择合适几何角度,有助于减小刀具振动,反过来,石墨工件也不容易崩缺;(1)前角,采用负前角加工石墨时,刀具刃口强度较好,耐冲击摩擦性能好,随着负前角绝对值减小,后刀面磨损面积变化不大,但总体呈减小趋势,采用正前角加工时,随着前角增大,刀具刃口强度被削弱,反而导致后刀面磨损加剧。
负前角加工时,切削阻力大,增大了切削振动,采用大正前角加工时,刀具磨损严重,切削振动也较大。
(2)后角,如果后角增大,则刀具刃口强度降低,后刀面磨损面积逐渐增大。
刀具后角过大后,切削振动加强。
(3)螺旋角,螺旋角较小时,同一切削刃上同时切入石墨工件刃长最长,切削阻力最大,刀具承受切削冲击力最大,因而刀具磨损、铣削力切削振动都最大。
当螺旋角去较大时,铣削合力方向偏离工件表面程度大,石墨材料因崩碎而造成切削冲击加剧,因而刀具磨损、铣削力切削振动也都有所增大。
因此,刀具角度变化对刀具磨损、铣削力切削振动影响前角、后角及螺旋角综合产生,所以选择方面一定要多加注意。
通过对石墨材料加工特性做了大量科学测试,PARA刀具优化了相关刀具几何角度,从而使得刀具整体切削性能大大提高。
3、刀具涂层金刚石涂层刀具硬度高、耐磨性好、摩擦系数低等优点,现阶段金刚石涂层石墨加工刀具最佳选择,也最能体现石墨刀具优越使用性能;金刚石涂层硬质合金刀具优点综合了天然金刚石硬度硬质合金强度及断裂韧性;但国内金刚石涂层技术还处于起步阶段,还有成本投入都很大,所以金刚石涂层近期不会有太大发展,不过我们可以普通刀具基础上,优化刀具角度,选材等方面改善普通涂层结构,某种程度上可以石墨加工当应用。
机械加工中刀具磨损的影响因素及对策
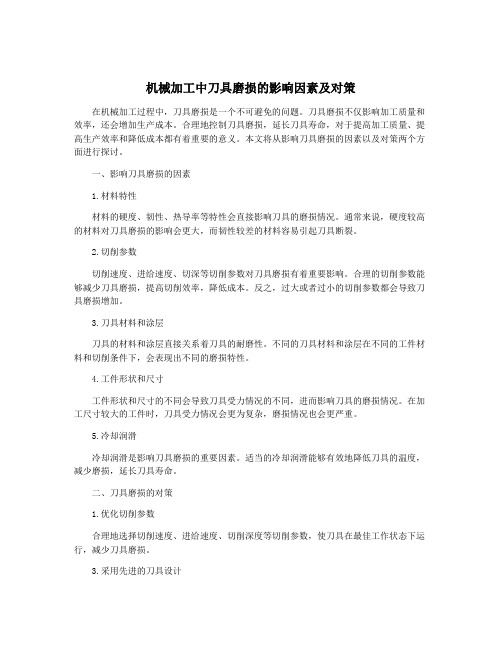
机械加工中刀具磨损的影响因素及对策在机械加工过程中,刀具磨损是一个不可避免的问题。
刀具磨损不仅影响加工质量和效率,还会增加生产成本。
合理地控制刀具磨损,延长刀具寿命,对于提高加工质量、提高生产效率和降低成本都有着重要的意义。
本文将从影响刀具磨损的因素以及对策两个方面进行探讨。
一、影响刀具磨损的因素1.材料特性材料的硬度、韧性、热导率等特性会直接影响刀具的磨损情况。
通常来说,硬度较高的材料对刀具磨损的影响会更大,而韧性较差的材料容易引起刀具断裂。
2.切削参数切削速度、进给速度、切深等切削参数对刀具磨损有着重要影响。
合理的切削参数能够减少刀具磨损,提高切削效率,降低成本。
反之,过大或者过小的切削参数都会导致刀具磨损增加。
3.刀具材料和涂层刀具的材料和涂层直接关系着刀具的耐磨性。
不同的刀具材料和涂层在不同的工件材料和切削条件下,会表现出不同的磨损特性。
4.工件形状和尺寸工件形状和尺寸的不同会导致刀具受力情况的不同,进而影响刀具的磨损情况。
在加工尺寸较大的工件时,刀具受力情况会更为复杂,磨损情况也会更严重。
5.冷却润滑冷却润滑是影响刀具磨损的重要因素。
适当的冷却润滑能够有效地降低刀具的温度,减少磨损,延长刀具寿命。
二、刀具磨损的对策1.优化切削参数合理地选择切削速度、进给速度、切削深度等切削参数,使刀具在最佳工作状态下运行,减少刀具磨损。
3.采用先进的刀具设计采用先进的刀具设计可以改善刀具的受力情况,减少刀具的磨损。
采用合理的刀具几何形状和刀具刃部结构设计,可以减小刀具的摩擦力,降低刀具磨损。
5.及时的刀具维护和更换定期对刀具进行检查、清洁和重新磨削,及时更换磨损严重的刀具,可以延长刀具的使用寿命。
结语在机械加工中,刀具磨损是一个需要引起重视的问题。
通过提高切削条件的合理性、优化刀具材料和涂层选择、加强刀具的冷却润滑、优化刀具设计等方式,可以有效地减少刀具磨损,提高刀具的使用寿命,提高加工质量和效率,降低生产成本。
刀具磨损原因及状况分析

刀具磨损原因及状况分析
(一)俱磨损的原因
于摩擦力的存在,加之金属切削过程中释放热能,被切金属层在刀具的切削刃和前刀面的推挤作用之下会铲生形,如此造成刀具滑移,从而变成切屑。
因刀具前刀面与切屑、具后面与工件已加工表面的摩擦,仍具在切削的过程中产生磨损。
高温同样在一定程度上影响了踌命:刀具在很高的切削温度下进行工作,刀刃材料容易变软,更加剧了俱切削部分的磨损。
当工件材料不同、切削用量不同时,具的磨损形式也不同。
(二)前刀面磨损
在使用刀具切削塑性材料时,刀具前面会因为切削厚度较大而受热量增加,励增大,刀具的前面被磨损,就会形成坑状磨损。
这些坑状磨损在切削过程中,逐渐加深变宽,并向刃方向扩展。
这样便容易导致崩刃。
所以,在切削塑性材料时,要刀具破损是在刀具的前面。
(三)后刀面磨损
反之,在切削塑性较低的材料时,切削深度较小,速度较低,具前面受的压励和摩擦不大.出现积屑瘤的可能性小。
这时刀具后面屿工件表面的摩擦较大,所以刀具的磨损主要在刀具后面。
切削脆性材料时,前面的温度不高,主要的磨损也在刀具的后面。
(四)前后共同磨损
进给量和切削速度都在中等时,俱会同时遭受前面的坑状磨损和主后面的磨损,共同造成崩刃。
第 1 页共 1 页。
机械加工过程中的刀具磨损与寿命预测

机械加工过程中的刀具磨损与寿命预测引言:机械加工过程中,刀具是至关重要的工具,直接影响到产品的质量和加工效率。
然而,随着加工时间的增加,刀具会不可避免地出现磨损现象,导致加工质量下降和切削力增加。
因此,准确预测刀具的寿命,对于降低生产成本、提高加工效率和优化工艺具有重要意义。
一、刀具磨损类型及原因刀具磨损主要分为磨耗、断裂和切削边脱落三种类型。
其中,磨耗是最常见的刀具磨损形式,其原因可以归结为摩擦、热量和化学反应等因素。
例如,切削区的高温和高压会导致刀具表面发生氧化和软化,从而促使磨粒和切屑与刀具接触并磨损刀具。
此外,不合理的加工参数和材料硬度的不匹配也会导致磨损的加剧。
二、刀具寿命预测方法为了提前判断刀具的寿命,并及时更换,可以使用以下方法进行刀具寿命预测:1. 经验方法经验方法基于加工经验和行业数据,根据刀具使用的时间和加工次数来推测寿命。
例如,在相同材料、相同刀具类型和相同切削参数下,先前加工相同工件所持续的时间可以作为预测刀具寿命的依据。
然而,这种方法的准确性受到很大的限制,因为加工条件的差异会导致寿命的差异。
2. 物理模型物理模型方法基于刀具磨损的物理机制,将刀具磨损过程建模,并通过实验数据进行参数拟合。
例如,基于热力学和力学原理,可以建立刀具磨损与时间、切削力、温度等因素的关系模型。
这种方法能够较为准确地预测刀具寿命,但需要大量实验数据的支持。
3. 人工智能方法人工智能方法利用机器学习和深度学习算法,通过大量的数据训练模型,预测刀具的寿命。
例如,可以通过监测刀具的振动、温度和功率等参数,结合历史数据进行训练,实现对刀具寿命的预测。
这种方法无需事先建立物理模型,适用于复杂的加工过程。
三、刀具寿命预测技术的挑战与发展趋势刀具寿命预测技术面临着以下挑战:1. 数据获取问题刀具寿命预测需要大量的加工数据和历史数据来进行准确的预测,但在实际生产中,获取这些数据并不容易。
因此,如何有效地收集和管理加工数据是一个关键问题。
简述刀具磨损的过程

简述刀具磨损的过程刀具磨损是指刀具在工作时表面出现的磨损和退化现象。
刀具在使用过程中会受到各种因素的影响,例如压力、温度、切削速度和进给量等,这些因素会导致刀具表面的磨损。
刀具磨损的过程可以分为三个阶段:1. 初始磨损:在刀具开始工作后,其表面出现的早期磨损。
这种磨损通常是由于刀具与切削材料之间的摩擦引起的。
随着时间的推移,刀具表面的磨损会越来越厉害,直到达到极限值,形成明显的磨损层。
2. 过渡磨损:在这个阶段,刀具表面的磨损已经比较严重了,但是刀具表面仍然保持着一定的锋利度。
这种磨损通常是由于刀具与切削材料的过度接触引起的。
随着时间的推移,刀具表面的磨损会越来越严重,直到刀具完全失去锋利度,形成平滑的磨损层。
3. 晚期磨损:在这个阶段,刀具表面的磨损已经非常严重,几乎失去了所有的锋利度,并且出现大量的磨损颗粒。
这种磨损通常是由于刀具表面与切削材料的激烈摩擦引起的。
刀具磨损的影响非常广泛,不仅会对刀具的寿命产生影响,还会对加工质量和效率产生影响。
为了减少刀具的磨损,可以通过以下措施进行改善:1. 合理选择刀具材料:刀具材料应该具有良好的耐磨性和韧性,以满足刀具的加工需求。
2. 控制刀具的进给量:进给量过大会导致刀具表面的磨损加剧,而过小的进给量则会降低加工效率。
因此,应该根据实际情况控制刀具的进给量。
3. 进行刀具涂层:刀具涂层可以提高刀具的耐磨性,减少刀具表面的磨损。
常用的刀具涂层包括硬质合金涂层、陶瓷涂层和聚氨酯涂层等。
4. 定期维护和更换刀具:定期维护和更换刀具是减少刀具磨损的有效措施。
应该根据刀具的使用频率和使用寿命,定期更换刀具。
刀具磨损原因及改进方法

在刀尖部分(即图a中的C区)由于强度和散热条件较差,因 此磨损较为剧烈,其最大值为VC 。
在参与切削的切削刃中部(B区),其磨损比较均匀。在B区, 以VB表示平均磨损值,以VBmax表示最大磨损值。
三、扩散磨损
扩散磨损在高温下产生。切削金属时,切屑、工件与 刀具接触过程中,双方的化学元素 在固态下相互扩散, 改变了材料原来的成分与结构,使刀具表层变得脆弱, 从而加剧了刀具的磨损。例如用硬质合金切钢时,从 800℃开始,硬质合金中的钴便迅速地扩散到切屑、工 件中去,WC分解为钨和碳后扩散到钢中.
合理磨钝标准
粗加工时,应取磨损过程曲线中正常磨损阶段终点处的磨 损量B点对应的磨损量(VB)作为磨钝标准。
工艺磨钝标准
精加工时,必须保证工件表面粗糙度和尺寸精度,因此要根据表面粗糙度 和精度来制定刀具的磨钝标准。
刀具使用寿命的定义
刃磨后的刀具自开始切削直到磨损量达到磨钝标准为止 的切削时间,称为刀具使用寿命,以T表示。
磨钝标准的选择
车削刚性差的工件时,应控制在VB=0.3mm左右; 而车削刚性好的工件时,磨钝标准可取得大一些。
在切削难加工材料时,一般应选用较小的磨钝标推;加工 一般材料,磨钝标准可以大一些。
加工精度及表面质量要求较高时,应当减小磨钝标准, 以确保加工质量。例如在精车时,应控制VB=0.1— 0.3mm的范围内。
它是指净切削时间,不包括用于对刀、测量、快进、回程 等非切削时间。
也有用达到磨钝标准前的切削路程lm。来定义刀具使用寿 命的。lm等于切削速度Vc和刀具使用寿命(时间)T的乘积, 即
lm=Vc·T
刀具磨损的原因汇总

1、磨料磨损
主要原因是工件材料中的杂质,基体组织中所含的碳化物、氮化物和氧化物等硬质点和积屑瘤的碎片,在刀具表面划出沟纹所造成的机械磨损。
在各种切削速度条件下,都存在磨料磨损,它是低速刀具磨损的主要原因。
减小这种磨损的主要方法,是降低刀具切削部分的表面粗糙度,采用相应的润滑性能好的切削液。
2、粘结磨损
在一定的压力和温度的作用下,刀具切削部分与切屑接触和摩擦,将会产生材料分子间的吸附作用,刀具材料的部分硬质点会被工件和切屑带走,造成粘结磨损。
3、扩散磨损
切削时,在高温的作用下,接触面之间分子活动能量大,产生合金元素相互相置换,如高速刀具在前刀面上形成含Cr、C较高的白色层,不断被切屑带走。
切削钢件温度在800~1000度时,硬质合金中的Co、C、W扩散到切屑中去,钢中的Fe扩散到刀面上,形成硬度低而脆的复合碳化物,加速刀具磨损。
金刚石和立方氮化硼乃具材料也存在扩散磨损。
在硬质合金中,添加TaC、NbC、VC,可提高硬质合金抗扩散温度,减少扩散磨损。
4、化学磨损
空气中的氧在高温条件下,会使硬质合金产生表面氧化膜,形成一层硬度较低的化合物,被切屑带走,造成刀具磨损,称为化学磨损。
机械加工刀具磨损与寿命
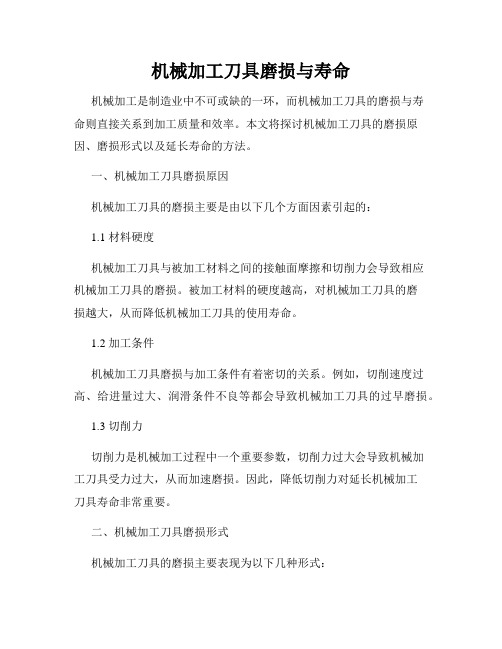
机械加工刀具磨损与寿命机械加工是制造业中不可或缺的一环,而机械加工刀具的磨损与寿命则直接关系到加工质量和效率。
本文将探讨机械加工刀具的磨损原因、磨损形式以及延长寿命的方法。
一、机械加工刀具磨损原因机械加工刀具的磨损主要是由以下几个方面因素引起的:1.1 材料硬度机械加工刀具与被加工材料之间的接触面摩擦和切削力会导致相应机械加工刀具的磨损。
被加工材料的硬度越高,对机械加工刀具的磨损越大,从而降低机械加工刀具的使用寿命。
1.2 加工条件机械加工刀具磨损与加工条件有着密切的关系。
例如,切削速度过高、给进量过大、润滑条件不良等都会导致机械加工刀具的过早磨损。
1.3 切削力切削力是机械加工过程中一个重要参数,切削力过大会导致机械加工刀具受力过大,从而加速磨损。
因此,降低切削力对延长机械加工刀具寿命非常重要。
二、机械加工刀具磨损形式机械加工刀具的磨损主要表现为以下几种形式:2.1 磨损机械加工刀具经过长时间使用后,刀尖会逐渐磨损,切削效果降低。
这是最常见的一种磨损形式。
2.2 刃口断裂在一些高负荷工况下,机械加工刀具的刃口很容易发生断裂,导致刀具报废。
2.3 塑性变形由于材料的软塑性,机械加工刀具可能会在加工过程中出现塑性变形的现象,从而影响加工质量和切削效果。
三、延长机械加工刀具寿命的方法为了延长机械加工刀具的使用寿命,可以采取以下几种方法:3.1 选用合适的材料机械加工刀具的选材十分重要。
选择适合加工材料硬度和加工条件的刀具材料,可以减少磨损。
3.2 控制加工条件合理控制加工条件,包括切削速度、给进量、冷却润滑等参数,可以降低机械加工刀具的磨损。
3.3 频繁刀具检查与维护定期对机械加工刀具进行检查,如果发现有磨损或其他损坏情况,及时更换或维修,可以延长刀具的使用寿命。
3.4 刀具涂层技术刀具涂层技术可以提高刀具的硬度和耐磨性,从而增加刀具的使用寿命。
3.5 刀具刃磨与研磨刀具刃磨和研磨是确保机械加工刀具保持良好切削状态的重要方法。
铰孔加工中的刀具磨损
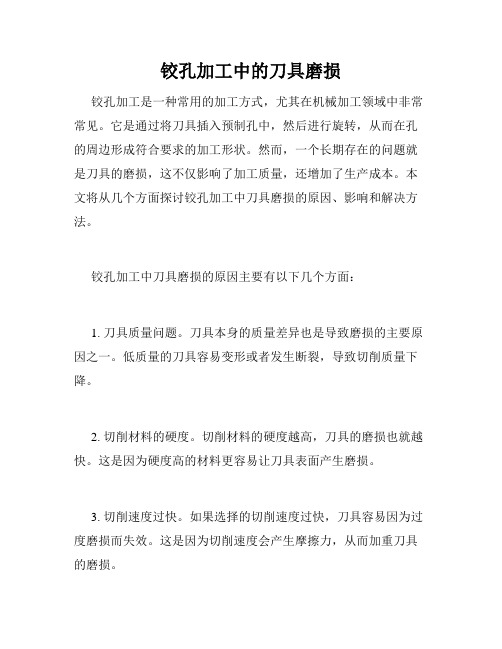
铰孔加工中的刀具磨损铰孔加工是一种常用的加工方式,尤其在机械加工领域中非常常见。
它是通过将刀具插入预制孔中,然后进行旋转,从而在孔的周边形成符合要求的加工形状。
然而,一个长期存在的问题就是刀具的磨损,这不仅影响了加工质量,还增加了生产成本。
本文将从几个方面探讨铰孔加工中刀具磨损的原因、影响和解决方法。
铰孔加工中刀具磨损的原因主要有以下几个方面:1. 刀具质量问题。
刀具本身的质量差异也是导致磨损的主要原因之一。
低质量的刀具容易变形或者发生断裂,导致切削质量下降。
2. 切削材料的硬度。
切削材料的硬度越高,刀具的磨损也就越快。
这是因为硬度高的材料更容易让刀具表面产生磨损。
3. 切削速度过快。
如果选择的切削速度过快,刀具容易因为过度磨损而失效。
这是因为切削速度会产生摩擦力,从而加重刀具的磨损。
4. 刀具使用时间过长。
即使是最好的刀具,如果使用时间太长,也会出现磨损现象。
这是因为刀具的材质并非不可摧不可破,长时间的使用也会让切削边逐渐变钝。
刀具磨损对铰孔加工的影响不仅仅是在加工质量方面,也涉及到生产成本和效率。
磨损的刀具需要更频繁地更换,这增加了人力和成本的开支。
那么,如何解决铰孔加工中的刀具磨损呢?1. 切削液的使用。
切削液可以有效地减轻刀具的磨损,因为它可以将产生的热量带走,同时还能清洁切削面。
2. 切削速度的控制。
应该根据切削材料的硬度和刀具的质量要求适当调整切削速度,这样可以减轻刀具的负担,延长使用寿命。
3. 定期更换刀具。
刀具磨损到一定程度后,应该及时更换,以保证加工质量和工作效率。
4. 刀具的维护和保养。
刀具的维护也非常重要,包括定期清洁、涂抹油脂和检查刃口等,这可以有效地延长刀具的使用寿命。
总之,铰孔加工中的刀具磨损是一个值得关注的问题,它不仅影响到加工质量,还会增加生产成本和浪费时间。
通过合理选择切削液、控制切削速度、定期更换刀具以及维护保养刀具,我们可以有效地解决这个问题。
车削工艺中的刀具磨损与更换

车削工艺中的刀具磨损与更换在车削工艺中,刀具的磨损与更换是一个重要的问题。
刀具的磨损会直接影响车削工艺的质量和效率,因此及时更换磨损的刀具是保证工艺稳定进行的必要措施。
一、刀具磨损的原因与种类刀具的磨损主要是由以下几个方面的因素导致的:材料的切削性、切削速度、切削深度、切削方式、冷却润滑等。
根据刀具磨损的形式和程度,可以将其分为以下几种类型:1. 刀尖磨损:由于刀尖是直接接触被加工材料的部位,所以其磨损最为明显。
在车削过程中,刀尖会逐渐磨损变钝,导致切削力增加,加工表面质量下降。
2. 刀片背面磨损:刀片背面是与刀柄连接的部分,受到切削力的作用,容易产生磨损。
刀片背面的磨损会导致刀片的固定性能下降,影响加工精度。
3. 刀侧磨损:刀侧也是直接接触被加工材料的部位,其磨损主要是由于切屑的剪切作用和磨料颗粒的磨损作用引起的。
刀侧磨损会导致加工表面的光洁度变差。
二、刀具磨损的影响和判断标准刀具的磨损会直接影响车削加工的效果和质量。
刀具磨损过大会导致加工表面粗糙度增加、尺寸误差增大、加工效率下降。
因此,及时判断和更换磨损的刀具至关重要。
1. 观察切屑的形状:在车削过程中观察切屑的形状可以初步判断刀具的磨损情况。
如果切屑形状变化明显,比如从螺旋状变为碎屑状,说明刀具磨损较为严重。
2. 检查加工表面质量:检查加工表面的质量可以更直观地了解刀具磨损的情况。
如果加工表面出现毛刺、痕迹或者光洁度不佳,说明刀具已经磨损严重,需要更换。
3. 测量尺寸误差:通过测量加工零件的尺寸误差可以判断刀具是否需要更换。
如果加工尺寸偏差超过了允许范围,说明刀具已经磨损到需要更换的程度。
三、刀具的更换与维护及时更换磨损的刀具是保证车削工艺质量稳定的重要措施。
在更换刀具时,应该注意以下几点:1. 选择合适的刀具:根据被加工材料的性质、工件的形状和加工要求等因素选择适合的刀具。
不同的刀具有不同的耐磨性和切削特性,选择合适的刀具可以延长刀具的使用寿命。
机械加工中刀具磨损的影响因素及对策
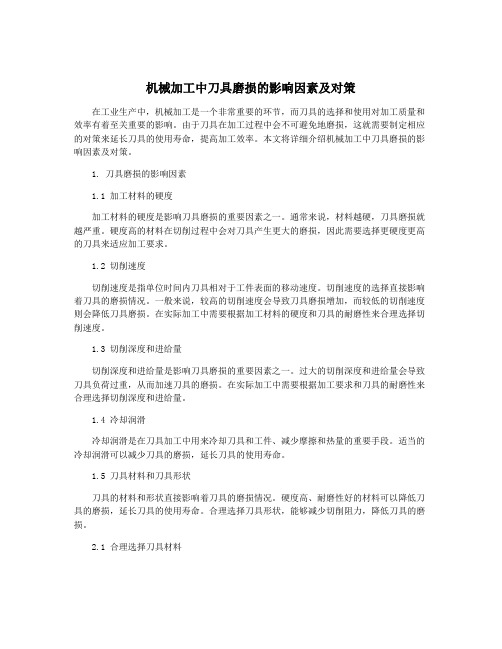
机械加工中刀具磨损的影响因素及对策在工业生产中,机械加工是一个非常重要的环节,而刀具的选择和使用对加工质量和效率有着至关重要的影响。
由于刀具在加工过程中会不可避免地磨损,这就需要制定相应的对策来延长刀具的使用寿命,提高加工效率。
本文将详细介绍机械加工中刀具磨损的影响因素及对策。
1. 刀具磨损的影响因素1.1 加工材料的硬度加工材料的硬度是影响刀具磨损的重要因素之一。
通常来说,材料越硬,刀具磨损就越严重。
硬度高的材料在切削过程中会对刀具产生更大的磨损,因此需要选择更硬度更高的刀具来适应加工要求。
1.2 切削速度切削速度是指单位时间内刀具相对于工件表面的移动速度。
切削速度的选择直接影响着刀具的磨损情况。
一般来说,较高的切削速度会导致刀具磨损增加,而较低的切削速度则会降低刀具磨损。
在实际加工中需要根据加工材料的硬度和刀具的耐磨性来合理选择切削速度。
1.3 切削深度和进给量切削深度和进给量是影响刀具磨损的重要因素之一。
过大的切削深度和进给量会导致刀具负荷过重,从而加速刀具的磨损。
在实际加工中需要根据加工要求和刀具的耐磨性来合理选择切削深度和进给量。
1.4 冷却润滑冷却润滑是在刀具加工中用来冷却刀具和工件、减少摩擦和热量的重要手段。
适当的冷却润滑可以减少刀具的磨损,延长刀具的使用寿命。
1.5 刀具材料和刀具形状刀具的材料和形状直接影响着刀具的磨损情况。
硬度高、耐磨性好的材料可以降低刀具的磨损,延长刀具的使用寿命。
合理选择刀具形状,能够减少切削阻力,降低刀具的磨损。
2.1 合理选择刀具材料刀具的材料对于刀具的使用寿命和加工效果有着至关重要的影响。
对于高硬度的加工材料,需要选择耐磨性好的刀具材料,例如高速钢、硬质合金等。
而对于低硬度的加工材料,可以选择普通碳钢刀具。
2.2 合理选择切削参数在实际加工中,需要根据加工材料的硬度、刀具材料和形状等因素来合理选择切削速度、切削深度和进给量,以减少刀具的磨损。
2.4 定期检查刀具刀具在长时间的使用过程中会出现磨损和损坏的情况,因此需要定期对刀具进行检查,及时更换磨损严重的刀具,以保证加工质量和安全生产。
机械加工中的刀具磨损与开裂分析

机械加工中的刀具磨损与开裂分析机械加工是一项重要的制造技术,它涉及到材料的切削和加工,而刀具则是机械加工中的核心工具。
然而,在机械加工过程中,刀具不可避免地会出现磨损和开裂的问题,这对加工质量和刀具寿命都会产生一定的影响。
因此,对刀具磨损和开裂的分析十分重要。
首先,我们来讨论刀具磨损的问题。
刀具磨损是指刀具表面的材料被磨掉或烧蚀的现象。
机械加工中的切削过程往往会产生大量的摩擦和热量,这就造成了刀具表面材料的磨损。
刀具磨损的主要原因有以下几点。
首先是切削力的影响。
在切削过程中,刀具需要承受巨大的切削力,而这种力会导致刀具表面的材料疲劳和磨损。
尤其是在高速切削中,刀具磨损会更加明显。
其次是材料的选择。
不同的材料有不同的硬度和强度,而这些性质对刀具的磨损程度有很大的影响。
合适的刀具材料可以提高其抗磨损性能,延长其使用寿命。
再次是切削条件的合理性。
切削速度、进给量、切削深度等切削条件会直接影响刀具磨损的程度。
如果切削速度过快或者切削深度过大,都会导致刀具的过度磨损。
最后是刀具的使用和维护。
如果使用不当或者缺乏有效的维护,刀具的寿命会大大缩短。
因此,正确的刀具选择和使用方法、以及定期的维护保养是减少刀具磨损的重要策略。
接下来,我们将讨论刀具的开裂问题。
刀具的开裂是指刀具表面出现裂纹或断裂现象。
刀具开裂的主要原因有以下几点。
首先是刀具的强度不足。
刀具在高速和高温的工作环境下要承受巨大的载荷,如果刀具的强度不够,就容易发生开裂。
其次是刀具的设计缺陷。
刀具的设计包括结构和材料的选择,如果设计不合理或者材料不适合,刀具容易出现开裂问题。
再次是切削温度过高。
在高速切削中,摩擦会产生大量的热量,如果不能有效地散热,刀具会因温度过高而出现开裂。
最后是刀具的使用环境。
刀具在工作时会受到不同的工艺条件和外部环境的影响,例如湿度、酸碱性等,这些因素也会导致刀具的开裂。
要解决刀具磨损和开裂问题,我们可以从以下几个方面入手。
首先是选择合适的刀具材料。
机械加工中刀具磨损的影响因素及对策

机械加工中刀具磨损的影响因素及对策刀具磨损是机械加工中的不可避免的现象,经常会导致加工效率的降低和工件质量的下降。
因此,机械加工中刀具的磨损是机械加工过程中需要重点关注和解决的问题之一。
本文将讨论刀具磨损的影响因素及对策。
1. 刀具材料不同材料的刀具磨损程度不同。
硬度较高的刀具抗磨损的能力较强,而硬度较低的刀具容易受到磨损。
对于不同的机械加工任务,需要根据工件材料和加工要求选择合适的刀具材料。
2. 切削条件在机械加工过程中,切削速度、进给量、切削深度等切削条件的设置会直接影响到刀具的磨损程度。
例如,在高速切削时,刀具的磨损速度会更快;在过大的进给量与切削深度下,刀具表面的磨损更严重。
因此,在确定切削条件时,需要合理配置,以减轻刀具的磨损。
3. 冷却润滑在机械加工过程中,冷却润滑也会对刀具磨损产生影响。
如果刀具不得不长时间地接触加工材料时,刀具表面则会产生高温,并快速磨损。
在这种情况下,喷射液可以起到加速冷却、减轻刀具磨损的作用。
4. 加工方式不同的加工方式的刀具磨损程度不同,例如,切削和磨削刀具的耐用程度大不相同。
在选择合适的加工方式之前,应考虑刀具的使用寿命,以提高加工效率和产品质量。
对策1. 优化刀具材料和制造工艺,选择更耐磨损的刀具。
2. 根据不同的加工任务和条件,确定合理的切削条件,如切削速度、进给量、切削深度等,以减轻刀具磨损。
3. 加强冷却润滑措施,使用合适的喷射液,提高刀具的使用寿命。
4. 选择合适的加工方式,避免一些不必要的磨损。
5. 添加服务周期记录,确保定期进行刀具维护与更换,以最大限度地延长刀具寿命,从而提高生产效率和成本效益。
刀片磨损8种常见现象的产生原因和解决办法
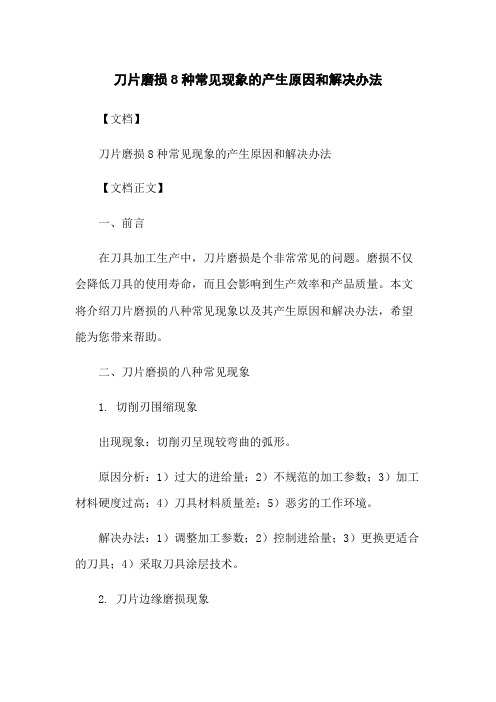
刀片磨损8种常见现象的产生原因和解决办法【文档】刀片磨损8种常见现象的产生原因和解决办法【文档正文】一、前言在刀具加工生产中,刀片磨损是个非常常见的问题。
磨损不仅会降低刀具的使用寿命,而且会影响到生产效率和产品质量。
本文将介绍刀片磨损的八种常见现象以及其产生原因和解决办法,希望能为您带来帮助。
二、刀片磨损的八种常见现象1. 切削刃围缩现象出现现象:切削刃呈现较弯曲的弧形。
原因分析:1)过大的进给量;2)不规范的加工参数;3)加工材料硬度过高;4)刀具材料质量差;5)恶劣的工作环境。
解决办法:1)调整加工参数;2)控制进给量;3)更换更适合的刀具;4)采取刀具涂层技术。
2. 刀片边缘磨损现象出现现象:切削刃变得不够锋利,呈现出磨损现象。
原因分析:1)切削速度过快;2)过大的切削深度;3)加工材料硬度过高;4)不规范的加工材料。
解决办法:1)调整加工参数;2)控制切削深度;3)更换更适合的刀具;4)采取刀具涂层技术。
3. 刀片断裂现象出现现象:刀具出现裂纹或完全断裂。
原因分析:1)制造材料质量差;2)不规范的加工参数;3)切削速度不当;4)过大的进给量。
解决办法:1)更换更适合的刀具;2)严格控制切削参数;3)采用超声波检测技术。
4. 刀具热胀现象出现现象:刀具在加工过程中变得更加膨胀。
原因分析:1)不规范的加工参数;2)加工材料硬度过高;3)恶劣的工作环境。
解决办法:1)控制加工参数;2)采用刀具涂层技术。
5. 刀具表面锈蚀现象出现现象:刀具表面出现腐蚀和锈蚀。
原因分析:1)恶劣的工作环境;2)不规范的存储方式。
解决办法:1)保证工作环境清洁干燥;2)注意保存刀具。
6. 刀具生锈现象出现现象:刀具表面出现锈迹。
原因分析:1)不规范的存储方式;2)恶劣的工作环境。
解决办法:1)注意保存刀具;2)保证工作环境清洁干燥。
7. 刀具热裂现象出现现象:刀具在加工过程中出现热裂。
原因分析:1)切削参数不当;2)制造材料缺陷。
刀具磨损原因
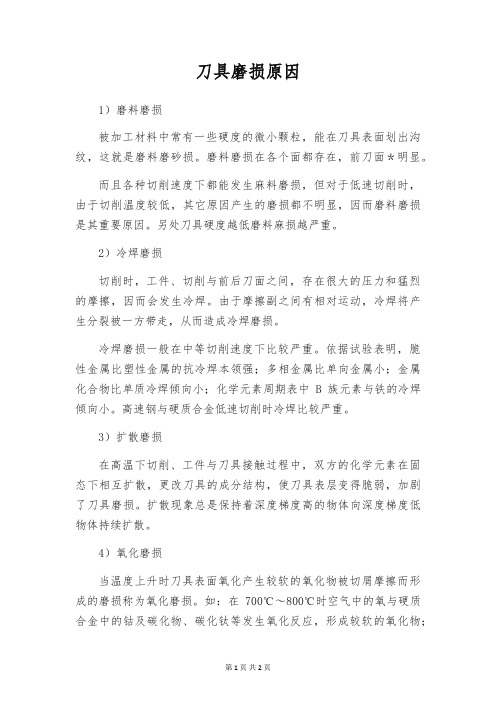
刀具磨损原因
1)磨料磨损
被加工材料中常有一些硬度的微小颗粒,能在刀具表面划出沟纹,这就是磨料磨砂损。
磨料磨损在各个面都存在,前刀面*明显。
而且各种切削速度下都能发生麻料磨损,但对于低速切削时,由于切削温度较低,其它原因产生的磨损都不明显,因而磨料磨损是其重要原因。
另处刀具硬度越低磨料麻损越严重。
2)冷焊磨损
切削时,工件、切削与前后刀面之间,存在很大的压力和猛烈的摩擦,因而会发生冷焊。
由于摩擦副之间有相对运动,冷焊将产生分裂被一方带走,从而造成冷焊磨损。
冷焊磨损一般在中等切削速度下比较严重。
依据试验表明,脆性金属比塑性金属的抗冷焊本领强;多相金属比单向金属小;金属化合物比单质冷焊倾向小;化学元素周期表中B族元素与铁的冷焊倾向小。
高速钢与硬质合金低速切削时冷焊比较严重。
3)扩散磨损
在高温下切削、工件与刀具接触过程中,双方的化学元素在固态下相互扩散,更改刀具的成分结构,使刀具表层变得脆弱,加剧了刀具磨损。
扩散现象总是保持着深度梯度高的物体向深度梯度低物体持续扩散。
4)氧化磨损
当温度上升时刀具表面氧化产生较软的氧化物被切屑摩擦而形成的磨损称为氧化磨损。
如:在700℃~800℃时空气中的氧与硬质合金中的钴及碳化物、碳化钛等发生氧化反应,形成较软的氧化物;
在1000℃时PCBN与水蒸气发生化学反应。
刀具磨损的9种形式及应对措施

后刀面磨损原因:切削期间,与工件材料表面的摩擦会导致后刀面的刀具材料损耗。
磨损通常最初在刃线出现,并逐渐向下发展。
应对措施:降低切削速度,并同时增加进给,将可在确保生产率的情况下延长刀具寿命。
月牙洼磨损原因:切屑与刀片(刀具) 前刀面的接触导致出现月牙洼磨损,属于化学反应。
应对措施:降低切削速度,并选择具有正确槽型和更耐磨涂层的刀片(刀具) 将可延长刀具寿命。
塑性变形塑性变形是指切削刃形状永久改变,切削刃出现向内变形(切削刃凹陷) 或向下变形(切削刃下塌)。
原因:切削刃在高切削力和高温下处于应力状态,超出了刀具材料的屈服强度和温度。
应对措施:使用具有较高热硬度的材质可以解决塑性变形问题。
涂层可改进刀片(刀具) 的抗塑性变形能力。
涂层剥落涂层剥落通常发生在加工具有粘结特性的材料时。
原因:粘附负荷会逐渐发展,切削刃要承受拉应力。
这会导致涂层分离,从而露出底层或基体。
应对措施:提高切削速度,以及选择具有较薄涂层的刀片将可减少刀具的涂层剥落。
裂纹裂纹是狭窄裂口,通过破裂而形成新的边界表面。
某些裂纹仅限于涂层,而某些裂纹则会向下扩展至基体。
梳状裂纹大致垂直于刃线,通常是热裂纹。
原因:梳状裂纹是由于温度快速波动而形成。
应对措施:为防止出现这种情况,可以使用韧性更高刀片材质,并且应大量使用冷却液或者完全不用冷却液。
崩刃崩刃包括刃线的轻微损坏。
崩刃与断裂的区别在于刀片崩刃后仍可使用。
原因:有许多磨损状态组合可导致崩刃。
但是,最常见的还是热-机械以及粘附带来的。
应对措施:可以采取不同的预防措施来尽可能减轻崩刃,具体取决于导致其发生的磨损状态。
沟槽磨损沟槽磨损的特点是在最大切深出现过量的局部损坏,但这也可能发生在副切削刃上。
原因:这取决于化学磨损是否在沟槽磨损中占据主导地位,与粘着磨损或热磨损的不规则增长相比,化学磨损的发展更有规律。
对于粘着磨损或热磨损情况,加工硬化和毛刺形成是导致沟槽磨损的重要因素。
应对措施:对于加工硬化材料,选择较小的主偏角,改变切深。
机床加工中的刀具磨损与管理

机床加工中的刀具磨损与管理机床加工中的刀具磨损与管理对于生产效率和产品质量有着重要的影响。
本文将探讨刀具磨损的原因以及有效的刀具管理策略,以提高机床加工效率和降低生产成本。
一、刀具磨损的原因刀具在机床加工中常常会出现磨损现象,主要原因如下:1. 切削力过大:机床加工过程中,刀具承受着巨大的切削力,如果工件材料的硬度高,切削速度过快,切削深度过大等因素都会导致切削力过大,进而引起刀具磨损。
2. 切削温度过高:机床加工中,由于切削速度和切削深度的增加,切削区域的摩擦产生的热量也会增加,切削温度升高会对刀具表面产生热影响区,使刀具表面硬度下降,从而加速刀具磨损。
3. 刀具材料质量不佳:刀具材料的选择直接影响着刀具的使用寿命。
如果刀具材料的硬度、韧性等方面不符合加工要求,那么其使用寿命将大大降低。
二、刀具磨损的类型刀具磨损主要分为三个类型:刀尖磨损、刀片磨损和刀柄磨损。
1. 刀尖磨损:刀尖磨损是机床加工中常见的磨损类型,主要表现为刀尖的磨损和变形,导致切削力不平衡,进而影响加工精度和表面质量。
2. 刀片磨损:刀片磨损是刀具加工过程中常见的现象,主要表现为刀片表面的磨损和破损,导致切削力不稳定,产生振动和噪音,同时还会影响产品的尺寸和表面质量。
3. 刀柄磨损:刀柄磨损是指刀具的刀柄部分出现磨损,主要表现为刀柄的表面磨损和腐蚀,导致刀具与机床的结合不紧密,影响加工精度。
三、刀具管理策略为了延长刀具的使用寿命和提高加工效率,刀具管理至关重要。
以下是一些有效的刀具管理策略:1. 刀具定期检查和更换:定期对刀具进行检查,及时更换磨损严重的刀具,避免在加工过程中因刀具磨损而导致的工件尺寸不合格。
2. 切削参数优化:合理选择切削参数,包括切削速度、切削深度和进给速度等,以减少刀具磨损和提高加工效率。
3. 加工液的选择和使用:选择适合加工材料的加工液,加工液可以降低切削温度,减少刀具磨损。
4. 刀具涂层技术的应用:采用刀具涂层技术可以提高刀具的硬度和耐磨性,延长刀具的使用寿命。
机械加工中刀具磨损的影响因素及对策

机械加工中刀具磨损的影响因素及对策
机械加工中刀具磨损是制约加工质量和生产效率的重要因素之一。
刀具磨损的影响因素包括材料特性、切削条件、冷却润滑条件等,针对不同的情况,可以采取相应的对策来减轻刀具磨损,提高加工效率。
材料特性是影响刀具磨损的重要因素之一。
不同材料的硬度、韧性、切削性能等都会对刀具磨损产生影响。
针对不同材料的特性,可以选择合适的刀具材料和刀具涂层,以提高刀具的耐磨性和切削性能。
在加工过程中控制切削速度和进给量,防止刀具过大负荷工作,减轻刀具磨损。
冷却润滑条件是影响刀具磨损的另一个重要因素。
良好的冷却润滑条件可以有效降低切削温度,减轻刀具磨损。
在加工过程中,可以采用高压冷却润滑剂来冷却切削区域,降低切削温度,同时也能够将切屑带走,减少切削过程中的摩擦和热量。
还可以通过合理布置冷却润滑系统和增加冷却润滑剂的流量来提高冷却润滑效果,从而减轻刀具磨损。
还可以采取一些其他的对策来减轻刀具磨损。
在加工过程中可以采取合适的切削方式和切削策略,减少刀具在工件上的停留时间和摩擦。
还可以加强对刀具的维护和管理,包括定期对刀具进行检查、修磨以及更换等。
在使用刀具时,也要注意对刀具的正确安装和使用,避免刀具与工件的过度碰撞和振动,减少刀具的磨损。
- 1、下载文档前请自行甄别文档内容的完整性,平台不提供额外的编辑、内容补充、找答案等附加服务。
- 2、"仅部分预览"的文档,不可在线预览部分如存在完整性等问题,可反馈申请退款(可完整预览的文档不适用该条件!)。
- 3、如文档侵犯您的权益,请联系客服反馈,我们会尽快为您处理(人工客服工作时间:9:00-18:30)。
影响刀具磨损的几种原因
刀具坚硬,可随着使用时间的推迟,刀具也会有一定的磨损,影响刀具磨损的几种原因有哪些呢?通过汇总得出了几种原因。
1、刀具材料
刀具材料是决定刀具切削性能的根本因素,对于加工效率、加工质量、加工成本以及刀具耐用度影响很大。
刀具材料越硬,其耐磨性越好,硬度越高,冲击韧性越低,材料越脆。
硬度和韧性是一对矛盾,也是刀具材料所应克服的一个关键。
对于石墨刀具,普通的tialn涂层可在选材上适当选择韧性相对较好一点的,也就是钴含量稍高一点的;对于金刚石涂层石墨刀具,可在选材上适当选择硬度相对较好一点的,也就是钴含量稍低一点的;
2、刀具的几何角度
石墨刀具选择合适的几何角度,有助于减小刀具的振动,反过来,石墨工件也不容易崩缺;
(1)前角,采用负前角加工石墨时,刀具刃口强度较好,耐冲击和摩擦的性能好,随着负前角绝对值的减小,后刀面磨损面积变化不大,但总体呈减小趋势,采用正前角加工时,随着前角的增大,刀具刃口强度被削弱,反而导致后刀面磨损加剧。
负前角加工时,切削阻力大,增大了切削振动,采用大正前角加工时,刀具磨损严重,切削振动也较大。
(2)后角,如果后角的增大,则刀具刃口强度降低,后刀面磨损面积逐渐增大。
刀具后角过大后,切削振动加强。
(3)螺旋角,螺旋角较小时,同一切削刃上同时切入石墨工件的刃长最长,切削阻力最大,刀具承受的切削冲击力最大,因而刀具磨损、铣削力和切削振动都是最大的。
当螺旋角去较大时,铣削合力的方向偏离工件表面的程度大,石墨材料因崩碎而造成的切削冲击加剧,因而刀具磨损、铣削力和切削振动也都有所增大。
因此,刀具角度变化对刀具磨损、铣削力和切削振动的影响是前角、后角及螺旋角综合产生的,所以在选择方面一定要多加注意。
通过对石墨材料的加工特性做了大量的科学测试,para刀具优化了相关刀具的几何角度,从而使得刀具的整体切削性能大大提高。
3、刀具的涂层
金刚石涂层刀具的硬度高、耐磨性好、摩擦系数低等优点,现阶段金刚石涂层是石墨加工刀具的最佳选择,也最能体现石墨刀具优越的使用性能;金刚石涂层的硬质合金刀具的优点是综合了天然金刚石的硬度和硬质合金的强度及断裂韧性;但是在国内金刚石涂层技术还处于起步阶段,还有成本的投入都是
很大的,所以金刚石涂层在近期不会有太大发展,不过我们可以在普通刀具的基础上,优化刀具的角度,选材等方面和改善普通涂层的结构,在某种程度上是可以在石墨加工当中应用的。
金刚石涂层刀具和普通涂层刀具的几何角度有本质的区别,所以在设计金刚石涂层刀具时,由于石墨加工的特殊性,其几何角度可适当放大,容削槽也变大,也不会降低其刀具锋口的耐磨性;对于普通的tialn涂层,虽然比无涂层的刀具其耐磨有显着的提高,但比起金刚石涂层来说,在加工石墨时它的几何角度应适当放小,以增加其耐磨性。
对金刚石涂层来说,目前世界上众多的涂层公司均投入大量的人力和物力来研究开发相关涂层技术,但是至今为止,国外成熟而又经济的涂层公司仅仅限于欧洲;para作为一款优秀的石墨加工刀具,同样采用目前世界最先进的涂层技术对刀具进行表面处理,以确保加工寿命的同时,保证刀具的经济实用。
4、刀具刃口的强化
刀具刃口钝化技术是一个还不被人们普遍重视,而又是十分重要的问题。
金刚石砂轮刃磨后的硬质合金刀具刃口,存在程度不同的微观缺口(即微小崩刃与锯口)。
石墨高速切削加工刀具性能和稳定性提出了更高的要求,特别是金刚石涂层刀具在涂层前必须经过刀口的钝化处理,才能保证涂层的牢固性和使用寿命。
刀具钝化目的就是解决上述刃磨后的刀具刃口微观缺口的缺陷,使其锋值减少或消除,达到圆滑平整,既锋利坚固又耐用的目的。
5、刀具的机械加工条件
选择适当的加工条件对于刀具的寿命有相当大的影响。
(1)切削方式(顺铣和逆铣),顺铣时的切削振动小于逆铣的切削振动。
顺铣时的刀具切入厚度从最大减小到零,刀具切入工件后不会出现因切不下切屑而造成的弹刀现象,工艺系统的刚性好,切削振动小;逆铣时,刀具的切入厚度从零增加到最大,刀具切入初期因切削厚度薄将在工件表面划擦一段路径,此时刃口如果遇到石墨材料中的硬质点或残留在工件表面的切屑颗粒,都将引起刀具的弹刀或颤振,因此逆铣的切削振动大;
(2)吹气(或吸尘)和浸渍电火花液加工,及时清理工件表面的石墨粉尘,有利于减小刀具二次磨损,延长刀具的使用寿命,减少石墨粉尘对机床丝杠和导轨的影响;
(3)选择合适的高转速及相应的大进给量。
综述以上几点,刀具的材料、几何角度、涂层、刃口的强化及机械加工条件,在刀具的使用寿命中扮演者不同的角色,缺一不可,
本文由中国标识网收集整理,更多信息请访问标识商学院。