ML 制造流程介绍说课讲解
液体制剂生产设备PPT课件

2)转鼓式超声波洗瓶机
第19页/共54页
其原理如图6—4所示
• 该机的主体部分为卧式转鼓,其进瓶装置及 超声处理部分基本与 YQC8000/10相同, 经超声处理后的瓶子继续下行,经排列和分 离,以定数瓶子为一组,由导向装置缓缓推 入作间歇回转的转鼓针管上。
• 主要依靠对流传热,所以传热速度快,热空气的 温度和流速非常均匀,在整个传送带宽度上,所 有瓶子均处于均匀的热吹风下,热量从瓶子内外 表面向里层传递,均匀升温、确保瓶子灭菌彻底, 同时可避免瓶子产生大的热应力。
• 高温灭菌区的热箱外壳中充填硅酸铝棉以隔热, 确保箱体外壁温升不高于7℃。
第26页/共54页
• ④螺口瓶: 螺口瓶是在直口瓶基础上新发展 的一种很有前景的改进包装,它克服了封盖 不严的隐患,而且结构上取消了撕拉带这种 启封形式,且可制成防盗盖形式,但由于这 种新型瓶制造相对复杂,成本较高,而且制 瓶生产成品率低,所以现在药厂实际采用的 还不很多。
• 螺口瓶之规格尚无行业标准,表8—2为北京 玻璃瓶厂企业标准,其中瓶口高h可根据药厂 要求确定。
• 瓶子在隧道内先后通过预热区(长约600mm)、高 温灭菌区(长约900mm)、冷却区(长约 1500mm)。
第25页/共54页
• 隧道传送带下方装有高效排风机,其出口处装有 调节风门,控制排出的废气量和带走的热量 。
• 高温热空气在热箱内循环运动,充分均匀混合后 经过高效过滤器过滤,获得洁净度100级的平行 流空气,直接对玻璃瓶进行加热灭菌。
第1页/共54页
2、口服液剂制备工艺简 述
行列式制瓶机成型过程讲解
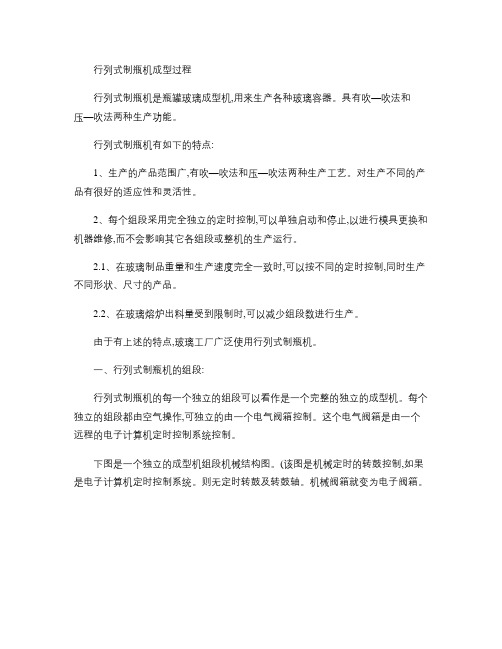
行列式制瓶机成型过程行列式制瓶机是瓶罐玻璃成型机,用来生产各种玻璃容器。
具有吹—吹法和压—吹法两种生产功能。
行列式制瓶机有如下的特点:1、生产的产品范围广,有吹—吹法和压—吹法两种生产工艺。
对生产不同的产品有很好的适应性和灵活性。
2、每个组段采用完全独立的定时控制,可以单独启动和停止,以进行模具更换和机器维修,而不会影响其它各组段或整机的生产运行。
2.1、在玻璃制品重量和生产速度完全一致时,可以按不同的定时控制,同时生产不同形状、尺寸的产品。
2.2、在玻璃熔炉出料量受到限制时,可以减少组段数进行生产。
由于有上述的特点,玻璃工厂广泛使用行列式制瓶机。
一、行列式制瓶机的组段:行列式制瓶机的每一个独立的组段可以看作是一个完整的独立的成型机。
每个独立的组段都由空气操作,可独立的由一个电气阀箱控制。
这个电气阀箱是由一个远程的电子计算机定时控制系统控制。
下图是一个独立的成型机组段机械结构图。
(该图是机械定时的转鼓控制,如果是电子计算机定时控制系统。
则无定时转鼓及转鼓轴。
机械阀箱就变为电子阀箱。
二、吹—吹法吹—吹法作业生产的成型过程为:落料—真空辅助和扑气—倒吹气—翻转—重热—真空成型和内冷却正吹气—钳瓶。
各过程的具体工作原理如下:1、落料玻璃料滴通过分料勺、直料槽、转向槽、漏斗, 落入倒置的初型模中。
一般料滴的直径与初型模的内腔上部要保持约0.8毫米的间隙,这样能获得顺利的准确的落料,使玻璃料滴的擦痕最小。
在初型模内腔上部与落入的料滴之间,有足够大的排气缝隙,以使玻璃料滴下面不需要的空气减至最少。
顺利准确的落料能使玻璃料滴均匀地沉入初型模。
落料前芯子已插入口模内,在扑气之前料滴的头部几乎完全落入瓶子口模部位。
落料过程的要点:为了保证顺利准确的落料,分料器料勺、直料道、转向槽、漏斗及初型模和口模都要调节对好中心。
在料勺、直料道、转向槽上应涂刷必要的润滑涂料。
芯子和套筒及芯子和口模、导向环之间的间隙,应按照I·S制瓶机模具数据手册推荐的数值进行加工。
IML详细工艺介绍和样品展示ppt课件

印刷-晒网
1.网纱涂上感光胶,通过曝光的方法将菲林上的图案转印 到网板上; 2.拥有网板涂布感光胶,曝光和烘烤设施,能够根据客户的 需求快速制作制作出网板;
6
印刷-网印
1.将客户要求外观颜色和图案印刷在片材上; 2.大震印刷设备6台; 3.劲胜的印刷技术: 处于业内先进印刷水平,产品一般印刷
6~7层就能防止油墨在注塑段冲刷的问题; (业内IML产品一般要印刷11层以上,才能防止油墨冲刷)
1.印刷后产品烘烤后,在薄膜的油墨面上附上保护膜,保 护产品在周转过程中(转热压成形制程)不受到 刮伤;
9
成形/冲切-冲孔
1. CCD冲孔机台1台,冲出印刷薄膜上的定位孔,用于热压成 形薄膜在模具中的定位;
10
成形/冲切-成形
1.热压成形, 把薄膜成形出产品的外形形状; 2.热压成形机台7台;
11
耐磨,产品外观图案永不掉 外观图案不耐磨
50
THE END!
51
成形/冲切-冲切
1. 冲切机,把热压成形后的产品冲切出来; 2.机台数量:9台;
12
注塑/检包-清洁片材
1. 注塑成型前对薄膜清洁,降低产品杂质,压点不良;
13
注塑/检包-注塑
1. 把薄膜植入模具中,注塑树脂后得到IML产品; 2.住友注塑成型机台:3台; 东芝注塑机台: 6台;
14
注塑/检包-精雕/检包
35 JS1QCE12021 大理石平台
40*40CM
台
1 使用中 品管课 实验室 唐海年
36 JS1QCF12048 厚薄规
0-1
把
2 使用中 品管课 实验室 唐海年
37 JS1QCF12050
量杯
金属成型新工艺:MIM(金属粉末注射成型)工艺详细介绍

金属成型新工艺:MIM(金属粉末注射成型)工艺详细介绍小编备注:结合国内目前MIM现状补充了一些资料。
转载请注明文章来源:金属注射成型网 1 MIM是一种近净成形金属加工成型工艺MIM (Metal injection Molding )是金属注射成形的简称。
是将金属粉末与其粘结剂的增塑混合料注射于模型中的成形方法。
它是先将所选金属粉末与粘结剂进行混炼,然后将混合料进行制粒再注射成形所需要的形状胚料,然后通过高温烧结,得到具有强度的金属零件。
2 MIM工艺流程步骤MIM流程结合了注塑成型设计的灵活性和精密金属的高强度和整体性,来实现极度复杂几何部件的低成本解决方案。
MIM流程分为四个独特加工步骤(混合、成型、脱脂和烧结)来实现零部件的生产,针对产品特性决定是否需要进一步的机械加工或进行表面处理.混合精细金属粉末和热塑性塑料、石蜡粘结剂按照精确比例进行混合。
混合过程在一个专门的混合设备中进行,加热到一定的温度使粘结剂熔化。
大部分情况使用机械进行混合,直到金属粉末颗粒均匀地涂上粘结剂冷却后,形成颗粒状(称为原料),这些颗粒能够被注入模腔。
CNPIM备注:混炼是MIM工艺中非常重要的一道工序。
目前混炼有几种体系,不同的添加剂,后面对应需要不同的脱脂方法将添加剂去除。
最常用的蜡基和塑基,分别对应热脱脂和催化脱脂。
成型注射成型的设备和技术与注塑成型是相似的。
颗粒状的原料被送入机器加热并在高压下注入模腔。
这个环节形成(green part)冷却后脱模,只有在大约200°c的条件下使粘结剂熔化(与金属粉末充分融合),上述整个过程才能进行,模具可以设计为多腔以提高生产率。
模腔尺寸设计要考虑金属部件烧结过程中产生的收缩。
每种材料的收缩变化是精确的、已知的。
脱脂脱脂是将成型部件中粘结剂去除的过程。
这个过程通常分几个步骤完成。
绝大部分的粘结剂是在烧结前去除的,残留的部分能够支撑部件进入烧结炉。
脱脂可以通过多种方法完成,最常用的是溶剂萃取法。
33ML液体灌装生产线标准操作规程

33ml液体灌装生产线标准操作规程1.目的:建立一个完整的33ml液体灌装生产线标准操作规程标准操作规程,用于规范操作、保证产品质量及设备使用寿命。
2.范围:适用于液体车间33ml液体灌装生产线的标准操作和维护保养。
3.责任:液体车间管理人员、生产线操作人员对本标准的实施负责,动力车间、质量部负责监督。
4.程序:4.1.设备运行前检查4.1.1生产前,检查设备状态标志牌“已清洁”栏中是否注“ √ ”并是否在有效期内,如有,说明机器处于正常状态,将设备状态标志牌“已清洁”栏中的“ 擦拭掉,在“运行”栏中注上“4.1.2检查各连接坚固部件是否牢固,无松动异常现象。
4.1.3通电操作前检查所有开关按钮,使其处于停机状态:检查各电源接线有无破损漏电现象;接电时必须保证电机的正确运行方向。
4.2设备操作过程4.1.1人工在旋盖机的震荡器中放置瓶盖;转动控制盒面板上总电源开关的钥匙至开的状态,则四个停止按钮的指示灯亮,表示机器已正常通电。
按主机点动按钮,使灌装头抬高,处于待灌装状态。
4.1.2打开振荡器开关,把瓶盖预送到导轨出口处;启动输送带,以便把瓶子送到灌装位置。
4.1.3启动旋盖机构,做好旋盖准备。
4. 2.4启动理瓶机,将理瓶机电机拨叉电机及扫瓶电机打开,然后打开提升电机、水平输送链电机,最后把清洁消毒过的塑料扁瓶放入储瓶槽内(加瓶时不要堆满储瓶槽,留有适当空间)。
4.2.5根据不同的需瓶速度调节相应的主电机及拨叉电机或提升电机,以达到适应下一步工序设备要求的能力。
4.2.6按电磁感应铝箔封口机箱面板上“ON”(电源)按钮:电源指示灯(绿色)亮,警示灯闪烁水泵、风扇开始运转,控制箱面板上功率显示“00”,冷却指示灯(绿色)亮,表示整机已处在准备状态。
4. 2.7按控制面板上的“START'按钮:警示灯熄灭,功率显示数字在40-70之间的某一数值,表示感应头已经启动,可以开始封口作业。
4. 2. 8清洁消毒过的塑料扁瓶由输送带送至灌装位,调节药液管上的调节阀,调节流量, 达到工艺要求的装量。
啤酒生产技术 麦汁制造(教案).doc

第四章麦汁制造麦汁制造又称糖化,其工艺流程如下:麦芽f粉碎->麦芽粉f麦芽醪(蛋白质分解)\ 酒花\ /热凝固物糖化f过滤f煮沸f热麦汁f回旋沉淀槽大米(辅料)一粉碎一大米粉一米粉醪(糊化)70A图4-1麦汁制备流程图(1)麦芽暫立仓(2)粉碎机(3)糖化锅、糊化锅(4)过滤槽(5)麦汁煮彿锅(6)回旋沉淀槽(刀薄板拎却器(8)过滤机§4-1原料、辅料的粉碎一、粉碎的目的与要求1•粉碎的目的原料、辅料粉碎后,增加了比表瓯积,糖化时可溶性物质容易浸出,有利于酶的作川。
2•粉碎的要求麦芽皮壳应破而不碎。
如果过碎,麦皮屮含有的苦味物质、色素、单宁等会过多地进入麦汁中,使啤酒色泽加深,口味变差;还会造成过滤困难,影响麦汁收得率。
胚乳粉粒则应细而均匀。
辅助原料(如大米)粉碎得越细越好,以增加浸出物的收得率。
二、粉碎方法与设备1・麦芽粉碎方法麦芽粉碎冇干法粉碎、湿法粉碎和冋潮粉碎等三种方法。
干法粉碎是传统的粉碎方法,要求麦芽水分在6%〜8%,其缺点是粉尘校大,麦皮易碎。
湿法粉碎是先将麦芽用50°C水浸泡15〜20min,使麦芽含水质量分数达25%〜30%之示, 再用湿式粉碎机粉碎,并立即加入30〜40°C水调浆,泵入糖化锅。
优点是麦皮较完整,对溶解不良的麦芽,可提高浸出率1%〜2加缺点是动力消耗大。
冋潮粉碎又叫增湿粉碎。
可用0. 05MPa蒸气处理30〜40s,增湿1%左右。
也可用水雾在增湿装置中向麦芽喷雾90〜120s,增湿1%〜2%,可达到麦皮破而不碎的目的。
熬气增湿时,应控制麦芽品温在50C以下,以免引起酶的失活。
2•粉碎设备麦芽粉碎常用辘式及湿式粉碎设备。
辘式设备根据辘的数量乂可分为对辘式、四辘式、和辘式、六辘式等。
锤式粉碎机极少使用。
对辘式粉碎机是最简单的粉碎机,主要由一对平行安装的拉丝辘,以相反转向运转来将麦芽粉碎。
对總式粉碎机存在肴粉碎度较难控制的缺陷。
以对辄式粉碎机为基础发展起来的四辘式、五規式、六觀式等类世的麦芽粉碎机,粉碎性能有了极大的提高,可适用于各种麦芽的粉碎,并可使粉碎度更能符合酿造需要。
MIM粉末注射制造工艺

345
205
20
415
240
25
7.5
65HRb
793
605
4.0
896
731
6
7.5
27HRc
1070
965
4.0
1186
1089
6
7.5
33HRc
42HRc
五、MIM的应用: MIM的应用以涉及到军工、机械、医疗器械、钟表、汽车、IT电子、通讯、航天、体育、 日常用品等多方面领域。
常用MIM材料体系、牌号、及主要应用领域 材料体系 低合金钢 不锈钢 硬质合金 陶瓷 重合金 钛合金 磁性材料 合金牌号、成分 Fe-2Ni、Fe-8Ni 316L、17-4PH WC-Co Al2O3、ZnO2、SiO2 应用领域 汽车、机械等行业的各 种结构件 医疗器械、钟表零件 各种刀具、钟表 IT电子、日常生活用品、 钟表
陶瓷及化合物
氧化铝、氮化铝、铁氧体、羟磷灰石、莫来石
(3Al2O3-2SiO3)、镍铝金属间化合物、氧化硅 、碳化硅、氮化硅、尖晶石、二氧化钛、二氧化钇、 二氧化锆
金属陶瓷及复合材料
3Al2O3-2SiO3、3Al2O3-ZnO2、Mo-Cu、 Nbc-Ni、Ni3Al-Al2O3、Si3N4-SiC、SiO2-Si、 TiC-Ni-Mo、W-Cu、WC-Ni、ZrO2-MgO、ZrO2-Y2O3
特征 角度 相对密度 重量 相对尺寸
一般金属注射成形件的标准公差
最好 0.1° 0.2% 0.1% 0.1% 一般 0.2° 1% 0.4% 0.3%
绝对尺寸
孔径 孔位置 平面度 平行度 圆度 垂直度 表面粗糙
0.04mm
0.0% 0.1% 0.1% 0.2% 0.3% 0.1° 0.4μ m
IML注塑工艺
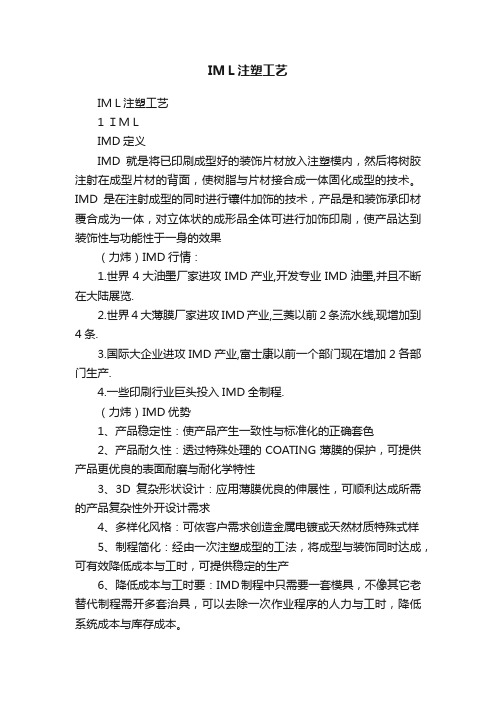
IML注塑工艺IML注塑工艺1 IMLIMD定义IMD就是将已印刷成型好的装饰片材放入注塑模内,然后将树胶注射在成型片材的背面,使树脂与片材接合成一体固化成型的技术。
IMD是在注射成型的同时进行镶件加饰的技术,产品是和装饰承印材覆合成为一体,对立体状的成形品全体可进行加饰印刷,使产品达到装饰性与功能性于一身的效果(力炜)IMD行情:1.世界4大油墨厂家进攻IMD产业,开发专业IMD油墨,并且不断在大陆展览.2.世界4大薄膜厂家进攻IMD产业,三菱以前2条流水线,现增加到4条.3.国际大企业进攻IMD产业,富士康以前一个部门现在增加2各部门生产.4.一些印刷行业巨头投入IMD全制程.(力炜)IMD优势1、产品稳定性:使产品产生一致性与标准化的正确套色2、产品耐久性:透过特殊处理的COATING薄膜的保护,可提供产品更优良的表面耐磨与耐化学特性3、3D复杂形状设计:应用薄膜优良的伸展性,可顺利达成所需的产品复杂性外开设计需求4、多样化风格:可依客户需求创造金属电镀或天然材质特殊式样5、制程简化:经由一次注塑成型的工法,将成型与装饰同时达成,可有效降低成本与工时,可提供稳定的生产6、降低成本与工时要:IMD制程中只需要一套模具,不像其它老替代制程需开多套治具,可以去除一次作业程序的人力与工时,降低系统成本与库存成本。
力炜IMD(IML,IMF)高压气体成型与IMR比较1、IMR是热转印,产品表面并没有一层透明薄膜,不能防止腐蚀和防刮.2、技术在日本方,周期比较长,一打样就是1000米或1000件,批量型.3、只能做平面、轻微弯曲表面装饰,IMF可以做3D装饰。
力炜IMD高压气体成型机与热压成型机比较1、只须要开下模不用开上模(热压是公母模)2、气压成型良率远高于热压成型良率(达90%)。
3、不伤害面材表面(高压没有上模而热压公母模需要接触薄膜表面)4、薄膜厚度变化不用改变成型模(热压是需要修改成型模)5、气压(可达150KG)R角成型质量非常高。
ML-制造流程介绍PPT课件
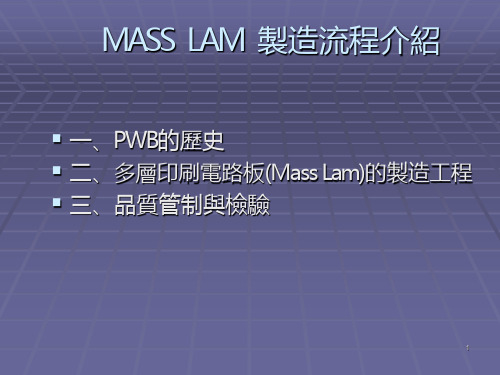
二、多層印刷電路板的製造工程(MASS-LAM)
3-1.基板與黏合片(P/P)原材料
3-1-1.構成要素:銅箔、玻璃纖維布、樹脂..等
3-1-2.製造方法:CCL 、P/P之製造方法
3-2.多層印刷電路板製造流程:見附圖 P5
製前準備:
製
a.客戶使用者 工
前
CAD
作
審
迴路設計
CAM
底
查
CAT
片
準
b-1-2.內層銅面處理:機械研磨粗糙度(厚度28mil以上)不織布校正整平。 化學研磨粗糙度(厚度28mil以下)當槽度,微蝕速度..等 乾燥溫度表面孔內乾燥必要。
b-1-3.內層壓膜:定義:將曝光阻劑貼付在待產基板銅面上並使其加熱產生熱 反應,附著在銅面上 。
控制:壓膜S/P ,T °C ,Pressure ,滾輪清潔度…等。
c-2.有梢套孔疊置( PIN Lamination ) 壓合:
A.壓合機種類:依其作動原理可分為三大類: a.液壓式壓合機
b.艙壓式壓合機( Autoclave ) c.ADARA systemCedal 壓合機( 見附圖 ) B.多層印刷電路配線板的形成方法:參照附圖 C.壓合完成後之解板( Break Down ): 將壓合熱硬化後之疊板依序分離鋼板與壓基板。
b.基板與膠片的經緯方向不可混錯 板彎板扭防止 c.阻抗特性控制的特殊板,膠片及銅箔選擇 皺折防止
d.空白區組合之交錯及鉚釘位置,鋼板選擇 B.環境要求:溫溼度之嚴格控制---溫度22±2°C 、相對溫度 55±5%
無塵室之清潔度控制。 C.對準度之要求方式:c-1.投影燈式及無投影燈方式( Mass Lamination )
1
小容量注射液生产工艺规程

制药有限公司小容量注射液生产工艺规程文件编号:1颁发单位:GMP办公室工艺规程批准程序1. 剂型、规格 (2)2. 生产工艺流程 (2)3. 操作过程及工艺条件 (3)4.质量控制要点 (6)5.设备一览表、主要设备生产能力 (6)6.工艺过程中的SOP (7)7.中间产品的控制 (8)8.验证工作要点 (8)9.工艺验证的具体要求 (9)10.工艺卫生和环境卫生 (9)11.劳动组织及岗位定员 (9)一、制剂类型:最终灭菌小容量注射液,10ml规格,安瓿瓶包装。
二、流程图:小容量注射液生产工艺流程图三、操作过程及工艺条件1 生产前的检查与确认1.1 是否还留有前批生产的产品或物料,是否已清洁并取得“清场合格证”。
1.2 检查确认生产现场的机器设备和器具是否已清洁并准备完毕挂上“合格”标示。
1.3 所使用原辅料是否准备齐全。
是否有质量检验报告单,合格品才能使用。
1.4 检查工艺用水是否新鲜制备,贮存不得超过24小时。
1.5 检查确认与生产品种相适应的批生产指令、配套文件及有关记录是否已准备齐全。
1.6 检查确认生产场所的温度是否在规定范围内(18-26℃,相对湿度在30%-65%)。
2 洗瓶、干燥灭菌2.1理瓶:根据“批生产指令”准备所需的清洁盘、领取必须的安瓶。
在理瓶室将安瓶的合格品摆满瓶盘。
2.2粗洗:把安瓿瓶盘放在不锈钢传送链条上,开动洗瓶机用高压循环纯化水洗安瓿瓶内外壁。
将安瓿瓶盘对称放置,固定在甩水机上,启动甩水机,甩水处理8分钟,至安瓶甩干。
重复上述操作。
2.3 精洗:用水温50--60℃,经孔径0.45um滤膜滤过的澄明度合格的注射用水清洗安瓿瓶内外壁,重复粗洗步骤。
定时检查安瓿的清洁度:目检1000ml注射用水无可见异物,抽50支,毛、块≤2%。
2.4 干燥与灭菌:安瓿盘均匀放入烘干箱内,150℃烘干1小时,或350℃烘干5分钟,消除热原。
2.5 灭菌后的安瓿立即使用或清洁存放,贮存不得超过48小时。
啤酒生产工艺技术教学讲座PPT资料

05
CHAPTER
啤酒生产中的质量控制与安 全
啤酒生产中的质量控制措施
原料质量控制
确保使用优质麦芽、啤酒花、酵母和水等原料, 定期进行质量检测,确保原料质量稳定。
生产过程控制
严格控制生产过程中的温度、压力、时间等参数, 确保发酵、过滤、包装等环节的质量稳定。
成品检验
对成品啤酒进行理化指标和感官质量检测,确保 啤酒符合质量标准。
废水处理
01
对啤酒生产过程中产生的废水进行治理,确保达标排放,减少
对环境的污染。
废气处理
02
对生产过程中产生的废气进行治理,如安装除尘器等设备,减
少大气污染。
废弃物处理
03
对生产过程中产生的废弃物进行分类处理和回收利用,降低对
环境的影响。
06
CHAPTER
新型啤酒生产技术与发展趋 势
新型啤酒生产技术介绍
发酵工艺流程
酵母添加
将适量的酵母添加到麦汁中,开 始发酵过程。
主发酵
在适宜的温度和时间下,酵母将麦 汁中的可发酵糖转化为酒精和二氧 化碳。
成熟与过滤
发酵后的啤酒需要在酒窖中成熟一 段时间,并进行过滤,去除残渣和 酵母。
04
CHAPTER
啤酒的后处理与包装
啤酒的过滤与稳定化
过滤
通过物理方法去除啤酒中的杂质和悬浮 物,提高啤酒的清澈度和口感。常见的 过滤技术包括深层过滤、硅藻土过滤和 膜过滤等。
啤酒生产中的食品安全问题
微生物控制
严格控制生产过程中的微生物污染,定期对设备和环境进行消毒, 确保微生物指标符合标准。
食品添加剂控制
严格按照国家规定使用食品添加剂,确保啤酒中不含有超标或非法 添加剂。
年产亿支ml水针剂生产车间工艺设计

本设计采用安瓿洗、烘、灌、封联动机组,即洗瓶、灌装、封口在同一联动线中,自动化程度高,运行稳定精确。首先将待洗的瓶子放入立式超声波清洗机供瓶网带上,经网带运行带动瓶子进入水槽,采用自来水或离子水经超声波粗洗,瓶子经超声波“空化”作用后,使附着在瓶子上的异物脱落。然后瓶子经不等距螺杆协同提升机构自动上瓶,机械手夹瓶翻转180度,瓶口向下,进行瓶外壁的冲洗,使瓶外壁的异物不进入瓶内,然后进入内壁冲洗工位。针头自动插入瓶子内部,进行水、气压力精洗、吹干,最后由出瓶轮机构将清洗后的瓶子送出立式超声波清洗机,完成瓶子清洗工作。热风循环灭菌烘箱由预热段、高温段、冷却段、网带传动机构、出口输送带、电器控制柜等组成,风速采用变频调速。预热、高温、冷却段全部风流均通过100级耐高温过滤器净化送入网带上西林瓶,确保灭菌质量。热风循环灭菌烘箱配有网带超声波回转清洗装置,对网带进行清洗,并留有验证口及清洁口。对由立式超声波清洗机送来的安瓿瓶进行灭菌、烘干。接着由自动安瓿灌封机对洁净的安瓿瓶进行灌装和封口,至此完成了安瓿瓶的洗、烘、灌、封的全部工序。
检出的不合格产品应及时分类记录,标明品名、规格、代号、批号,置于盛器内移交专人处理。
5、印字包装
安瓿印字包装是水针制剂生产的最后工序,整个过程包括安瓿印字、装盒、加说明书。本设计采用安瓿印字包装联动机,对进入印字包装环节的安瓿一次进行印字包装,工作效率高。将检查、检验合格的水针剂,贴以标签,以示标志。标签的内容应写明品名、浓度、规格、批号、有效期、用法用量、注册商标、批准文号、生产单位。贴签结束后进行包装、装箱,过程中应核对半成品的名称、规格、代号、批号、数量与领用的包装材料、标签是否相符。并应随时检查品名、规格、批号是否正确,内外包装是否相符,包装结束后包装品及时交待验库,检验合格后入库。
MIM金属注射成形工艺讲解
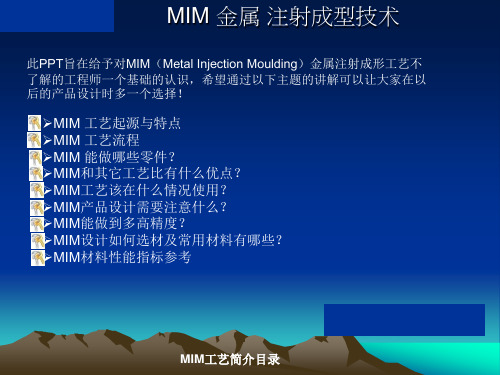
MIM 金属 注射成型技术
MIM 工艺 起源与特点
MIM 工 MIM 能做 MIM和其它工艺 什么情况该 MIM产品设计 MIM能做到 MIM设计如何选材 艺流程 哪些零件? 比有什么优点? 用MIM工艺? 需要注意什么? 多高精度? 及常用材料有哪些?
模具是MIM工艺中最关键的要素之一,
由于MIM金属注射成形工艺和我们常 用的塑胶注射成型工艺类似,所以其 模具设计制造也基本沿用了塑胶模具 的原理。在注射成型过程中金属粉末 不会融化,只是融化后的粘接剂载着 金属粉末进行注射成型。(一般粘接 剂在注射机料筒加热到150摄氏度左 右变为流体) MIM模具制造较塑胶模具而言有更高 的尺寸精度和表面光洁度要求。 毛刺
拔模斜度一般0.5°左右(较早书本要求拔模角较大)。 注:1. 对于较重要的基准面或孔等,也可以将拔模斜度设为0°,
MIM工艺介绍及其应用PPT教案
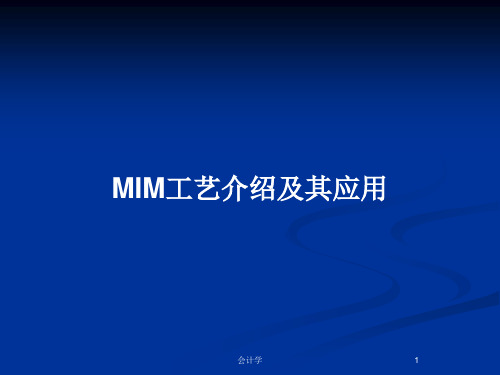
MIM工艺同样适合生产手术器械 长度不是问题
MIM 技术在运动器材中的应用
运动器械
MIM工艺也适用于高强度,耐冲击的材料的生产
MIM 技术在运动器材中的应用
运动器械
MIM工艺也适用于高强度,耐冲击的材料的生产
MIM 技术在航空航天中的应用
航空
MIM工艺也适用于耐高温、耐腐蚀的材料的生产
优点: 1,增加金属质感 2,耐磨,不易掉色
装饰键 材質:316L
优点: 1,金属质感强; 2,光泽度好,耐磨不掉色;
转轴套 材质:Sus 17-4 PH
优点: 1,硬度高(HV300),强度好,韧 性好,抗跌落; 2,耐磨(30万次寿命测试ok) ;
侧键 材质:316L
优点: 1,金属光泽度好,质感强; 3,耐磨; 4,着色付着力好,PVD后效果佳 ;
MIM 技术在汽车产业的应用
涡轮增压器用零件
涡轮增压器转子叶片
MIM 技术在汽车产业的应用
可变截面涡轮增压器用喷嘴环
涡轮增压器调整环
MIM 技术在汽车产业的应用
机械操纵调节用滑块
汽车锁部件
MIM 技术在汽车产业的应用
敞篷车驱动装置中的驱动轮
MIM 技术在汽车产业的应用
活塞冷却喷嘴
变速器部件
0.05 4 Na 17
4
Na Na Na Re
1.5 Na 1 12 1 0.6 0.75 17 0.9 Na 0.5 4
Na 0.35 Na Na Re
Na Na Na Na Re
Na
2
6 Na Re
常用材料性能
MIM技术的应用
MIM工艺在手机应用概述
应用目的:
降低成本,提高性能
2ml安瓶的生产流程
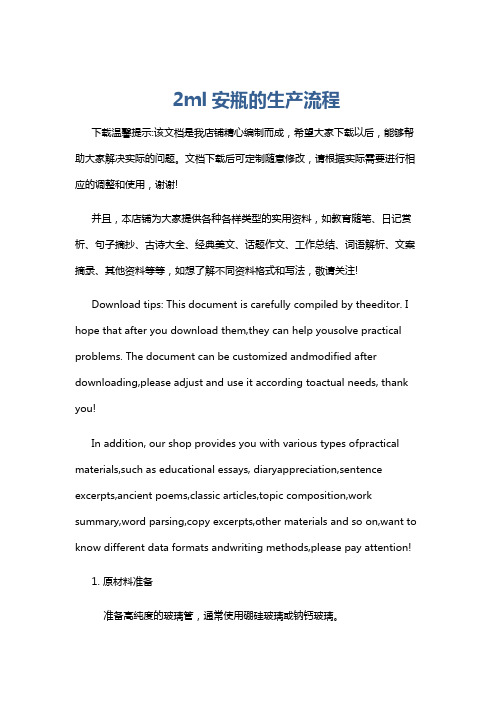
2ml安瓶的生产流程下载温馨提示:该文档是我店铺精心编制而成,希望大家下载以后,能够帮助大家解决实际的问题。
文档下载后可定制随意修改,请根据实际需要进行相应的调整和使用,谢谢!并且,本店铺为大家提供各种各样类型的实用资料,如教育随笔、日记赏析、句子摘抄、古诗大全、经典美文、话题作文、工作总结、词语解析、文案摘录、其他资料等等,如想了解不同资料格式和写法,敬请关注!Download tips: This document is carefully compiled by theeditor. I hope that after you download them,they can help yousolve practical problems. The document can be customized andmodified after downloading,please adjust and use it according toactual needs, thank you!In addition, our shop provides you with various types ofpractical materials,such as educational essays, diaryappreciation,sentence excerpts,ancient poems,classic articles,topic composition,work summary,word parsing,copy excerpts,other materials and so on,want to know different data formats andwriting methods,please pay attention!1. 原材料准备准备高纯度的玻璃管,通常使用硼硅玻璃或钠钙玻璃。
- 1、下载文档前请自行甄别文档内容的完整性,平台不提供额外的编辑、内容补充、找答案等附加服务。
- 2、"仅部分预览"的文档,不可在线预览部分如存在完整性等问题,可反馈申请退款(可完整预览的文档不适用该条件!)。
- 3、如文档侵犯您的权益,请联系客服反馈,我们会尽快为您处理(人工客服工作时间:9:00-18:30)。
乾膜阻劑
Exposure 照光,曝光經由工作底片 工作底片 銅箔絕緣基板
乾膜阻劑
b-1-5.顯影,蝕刻,剝膜(D.E.S) 顯影 :定義:將曝光完成之基板其光阻劑未有UV光硬化之部位以顯影液沖
洗出並徹底洗淨基板表面謂之。 控制:藥液濃度%比率,膜含量控制,S/P ,T °C, 顯影點(break point)
resin中胺類Amine對銅面的影響。
D-2.還原反應: (Post dip ping process),TUC目前為黑化反應並加後予浸方式。
目的:增加氧化層的抗酸性,並剪經絨毛高度到適當水準;以減少絨毛過長
在壓合後及後製程被藥液之攻擊可能性。
D-3.氧化處理之反應式:
Cu ° +Cu O2
Cu2O+ClO3+ Cl-
Cu2O +2CuO2
Cu O+ClO3 + Cl-
Cu2O +H2O
Cu(OH)2+Cu2+
金屬銅與亞氯酸75~納80反°C以應上C先u 生(O成H)中2 間體氧化亞C銅u COu+2HO2,O再進一步反應為
b-1-4.曝光作業:定義:將壓膜完成之基板經由UV光照射使其產生光化學反 應
達到影像轉移到阻劑上(乾膜)謂之曝光 。 控制:曝光能量(m j/cm2) 真空度,對位精準度( film與基板,層
與 層間),同心圓設計,Multi line蝕後沖孔…對位系統考
量。
參照 P8 曝光機構示意圖
UV照光機構示意圖
a-3.製前設計流程: 客戶資料提供
資料審查
著手設計
Process Flow Design 操作參數條件指示
規格定義 製作流程定義 材料使用定義
Too Ling
AOI 檢查 電測設計 生產工程圖
(模治具)
b.內層板線路轉移AOI檢查:
b-1.製作流程注意事項要點:
b-1-1.裁板投料: 發料尺寸確認 基板銅厚確認
CuCl2蝕刻反應式
Cu ° +Cu2+
2Cu+
Cu ° +H2CuCl4+2HCl
2H2CuCl3
Cu ° +H2CuCl4
H2CuCl3+Cu Cl
Cu Cl+2HCBl
H2阻Cu劑Cl3
Etching
Facto控r: 制:蝕銅刻線速路度,T
°C, 比重(銅含量),HCl,H2O2濃度控制
蝕刻因A子 ( e/f值)
d.1953年,日本在PWB實用化。收音機…等民生用品
e.1960年之後,日本開始採用貫孔鍍銅雙面板製造技術電子計算機,週邊佟端機
f.1964年,日本電信電話公社引進美國1960已實用化的ML-PWB製造技術,用於電 子計算機及電子交換機…等。
g.1964年以後至今,除了絕緣材料特性改變外,尺寸穩定性、 耐電蝕性、 銲錫耐熱 性、 防燃性等綜合檢討,最後到目前使用的Glass fiber Copper Clad Laminated boards 。
D.黑氧化處理(Black/Brown Oxide Treatment)
D-1.氧化反應:( 產生Cu O )
目的:a.增加與樹脂接觸的表面積及附著力( Bonding Adhesion)
b.增加銅面對樹脂流動之潤濕性(各死角流入及硬化後抓地力)
c.在裸銅表面產生一層緻密的純化層( Passivation)以阻絕高溫下液態
Gerber file
a-1.行銷員向客戶取得 工單or製作仕樣書
Gerber file
必要時會同工程、品保人員
Check 片
洽談工程製作規範及品質檢驗允收規範。
a-2.工程部製前製作內容資料審查CAM編輯、廠內製作工單、工作底片繪制
轉至生產部門。
CAD/CAM
下料尺寸 Art work NC Drilling Program NC Routing Program
D
D/C示意圖
C
基板
剝膜:俗稱“去膜”亦就是將抗蝕刻之光阻劑在此將其去除掉並同洗淨烘 乾
銅箔表面待下一工程站。 剝膜在PCB製程中有2個 Step會使用: 一是內層或外層酸性蝕刻後之D/F或油墨去除; 另一是外層線路蝕刻前D/F除去(鹼性蝕刻液使用場合)。 使用剝膜液通常為 Na OH或 KOH,以Na OH為最普遍且成本較低。 外層蝕刻剝膜液選擇宜謹慎(酸性蝕刻液)文獻指出K(鉀)會攻擊錫!
維
持 50~70%…等重點。
蝕刻:乾膜光阻劑經顯像後無阻劑部位即被所謂蝕刻液咬蝕去銅,即形成
பைடு நூலகம்所需要之回路謂之。
蝕刻液常見可分為兩種:一是酸性氧化銅( CuCl2)蝕刻液 一是鹼性氨水( NH4Cl)蝕刻液
乾膜(P/F)或油墨作為蝕刻阻劑且具抗酸,一般大部份選擇酸性蝕刻
液。
在外層蝕刻製程,可選擇酸性或鹼性氨水蝕刻液。
ML 制造流程介绍
一、 PWB的歷史
a.1940年代之前,PWB製造技術開始普遍,通信機器或收音機的配線-銅線黏貼於 石蠟上;成了現今PCB的機構雛型。
b.1927年,用印刷方式在玻璃或陶瓷基板上造成電路的構想,之後以絕緣樹脂基板 開發成功後才具體化。
c.1936年,英國的艾斯拉首倡現在這種全面覆蓋著金屬箔的絕緣基板,塗上耐蝕刻 油墨後再將不需要的金屬箔蝕刻去掉減除法,PWB基本製造技術。
外層阻劑為錫鉛共金屬化合物。
C .AOI檢查工程: C-1.檢測前之準備工作: C-1-1.AOI掃描機參數設定 C-1-2.基板掃描固定孔 CCD破靶
C-2.AOI檢查台掃描、VRS人工目視
C-3.直接人工目視
C-4.不良品補修正確認處置
C-5.AOI機台檢測有其極限:細斷路及漏電Leakage很難完全找出。
二、多層印刷電路板的製造工程(MASS-LAM)
3-1.基板與黏合片(P/P)原材料
3-1-1.構成要素:銅箔、玻璃纖維布、樹脂..等
3-1-2.製造方法:CCL 、P/P之製造方法
3-2.多層印刷電路板製造流程:見附圖 P5
製前準備:
製
a.客戶使用者 工
前
CAD
作
審
迴路設計
CAM
底
查
CAT
片
準
備 原始底片
b-1-2.內層銅面處理:機械研磨粗糙度(厚度28mil以上)不織布校正整平。 化學研磨粗糙度(厚度28mil以下)當槽度,微蝕速度..等 乾燥溫度表面孔內乾燥必要。
b-1-3.內層壓膜:定義:將曝光阻劑貼付在待產基板銅面上並使其加熱產生 熱 反應,附著在銅面上 。
控制:壓膜S/P ,T °C ,Pressure ,滾輪清潔度…等。