挤出成型和注射成型
peek加工方法
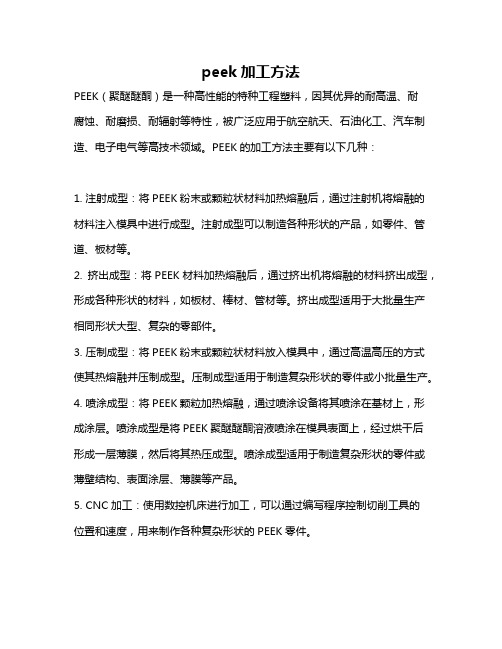
peek加工方法
PEEK(聚醚醚酮)是一种高性能的特种工程塑料,因其优异的耐高温、耐
腐蚀、耐磨损、耐辐射等特性,被广泛应用于航空航天、石油化工、汽车制造、电子电气等高技术领域。
PEEK的加工方法主要有以下几种:
1. 注射成型:将PEEK粉末或颗粒状材料加热熔融后,通过注射机将熔融的材料注入模具中进行成型。
注射成型可以制造各种形状的产品,如零件、管道、板材等。
2. 挤出成型:将PEEK材料加热熔融后,通过挤出机将熔融的材料挤出成型,形成各种形状的材料,如板材、棒材、管材等。
挤出成型适用于大批量生产相同形状大型、复杂的零部件。
3. 压制成型:将PEEK粉末或颗粒状材料放入模具中,通过高温高压的方式使其热熔融并压制成型。
压制成型适用于制造复杂形状的零件或小批量生产。
4. 喷涂成型:将PEEK颗粒加热熔融,通过喷涂设备将其喷涂在基材上,形成涂层。
喷涂成型是将PEEK聚醚醚酮溶液喷涂在模具表面上,经过烘干后形成一层薄膜,然后将其热压成型。
喷涂成型适用于制造复杂形状的零件或薄壁结构、表面涂层、薄膜等产品。
5. CNC加工:使用数控机床进行加工,可以通过编写程序控制切削工具的
位置和速度,用来制作各种复杂形状的PEEK零件。
6. 热压成型:将PEEK材料加热后放入模型中,通过加压使其冷却成型,适用于制作高精度和质量要求较高的PEEK零件。
7. 拉伸成型:通过将PEEK材料加热后悬挂在机械臂上,通过拉伸成型达到所需的形状,适用于制作细长的PEEK零件。
以上是PEEK的主要加工方法,不同的加工方法适用于不同的产品和应用场景,需要根据实际需求选择合适的加工方法。
挤出成型和注塑成型的异同点

挤出成型和注塑成型的异同点挤出成型和注塑成型是两种常见的塑料加工工艺,它们在塑料制品生产中起着重要作用。
虽然它们都属于塑料成型工艺,但在操作原理、应用范围等方面存在一些明显的异同点。
相同点首先,挤出成型和注塑成型都是将塑料原料在一定温度下加工成所需形状的工艺过程。
它们都需要先将塑料颗粒加热熔化,然后通过成型模具得到成品。
在生产效率方面,两者也都能实现批量生产,适用于大规模生产。
其次,挤出成型和注塑成型都能生产多种形状和尺寸的塑料制品,如管材、板材、型材等。
无论是挤出成型还是注塑成型,都可以根据客户需求设计相应的模具,生产出符合要求的塑料制品。
异点1.操作原理不同挤出成型是通过挤压融化的塑料料料挤出成型,其操作原理是利用螺杆在加热的缸体中将熔融的塑料挤出成型。
而注塑成型是将熔化的塑料通过喷嘴注入模具腔内,通过高压使塑料充实模具腔形成成品。
2.适用范围不同挤出成型适用于生产连续性较强的产品,如各种塑料管材、型材等。
注塑成型则更适合生产成型精度要求高、产品结构复杂的塑料制品,如塑料零件、外壳等。
3.生产周期不同一般情况下,注塑成型的生产周期相对较短,适合快速交付需求较紧的订单。
而挤出成型的生产周期较长,主要由于挤出成型需要连续挤压和冷却时间。
4.设备结构不同挤出成型设备主要由挤出机、模具、冷却系统等组成,而注塑成型设备包含注射机、模具、冷却系统等部件。
挤出机专门用于挤出工艺,而注射机则是专门为注塑工艺设计。
总的来说,挤出成型和注塑成型各有其适用的场合和优势,根据具体产品要求和生产需求选择合适的工艺是至关重要的。
通过充分了解挤出成型和注塑成型的异同点,可以更好地进行生产计划和工艺优化,提高生产效率和产品质量。
挤出成型和注塑成型的区别和联系
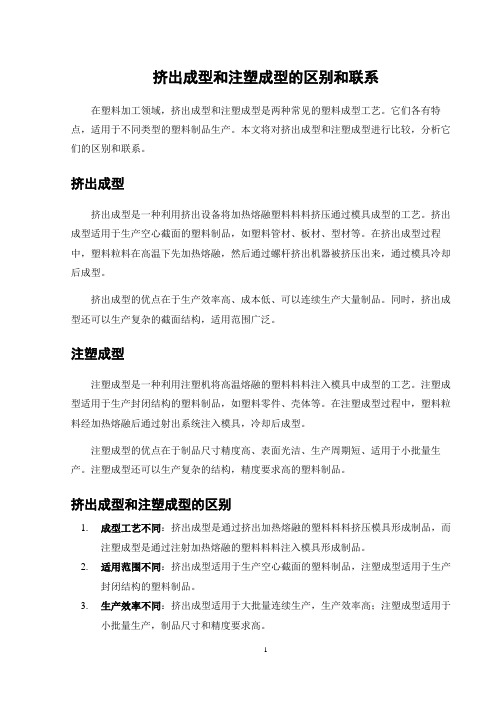
挤出成型和注塑成型的区别和联系在塑料加工领域,挤出成型和注塑成型是两种常见的塑料成型工艺。
它们各有特点,适用于不同类型的塑料制品生产。
本文将对挤出成型和注塑成型进行比较,分析它们的区别和联系。
挤出成型挤出成型是一种利用挤出设备将加热熔融塑料料料挤压通过模具成型的工艺。
挤出成型适用于生产空心截面的塑料制品,如塑料管材、板材、型材等。
在挤出成型过程中,塑料粒料在高温下先加热熔融,然后通过螺杆挤出机器被挤压出来,通过模具冷却后成型。
挤出成型的优点在于生产效率高、成本低、可以连续生产大量制品。
同时,挤出成型还可以生产复杂的截面结构,适用范围广泛。
注塑成型注塑成型是一种利用注塑机将高温熔融的塑料料料注入模具中成型的工艺。
注塑成型适用于生产封闭结构的塑料制品,如塑料零件、壳体等。
在注塑成型过程中,塑料粒料经加热熔融后通过射出系统注入模具,冷却后成型。
注塑成型的优点在于制品尺寸精度高、表面光洁、生产周期短、适用于小批量生产。
注塑成型还可以生产复杂的结构,精度要求高的塑料制品。
挤出成型和注塑成型的区别1.成型工艺不同:挤出成型是通过挤出加热熔融的塑料料料挤压模具形成制品,而注塑成型是通过注射加热熔融的塑料料料注入模具形成制品。
2.适用范围不同:挤出成型适用于生产空心截面的塑料制品,注塑成型适用于生产封闭结构的塑料制品。
3.生产效率不同:挤出成型适用于大批量连续生产,生产效率高;注塑成型适用于小批量生产,制品尺寸和精度要求高。
4.产品特点不同:挤出成型制品常为长条状或截面类,注塑成型制品常为封闭塑件或精密器件。
挤出成型和注塑成型的联系尽管挤出成型和注塑成型有着明显的区别,但它们也有一些联系点:1.塑料材料相同:挤出成型和注塑成型都是利用熔融后的塑料原料进行成型,所使用的塑料材料可能是相同的。
2.后处理工艺相似:挤出成型和注塑成型在成型后都需要进行一定的后处理工艺,如切割、去毛刺、打磨等,以满足制品的质量要求。
3.在某些制品上可互相替代:在一些特定情况下,挤出成型和注塑成型也可以相互替代,根据制品的形状、尺寸和数量来选择合适的生产工艺。
挤出和注塑的区别
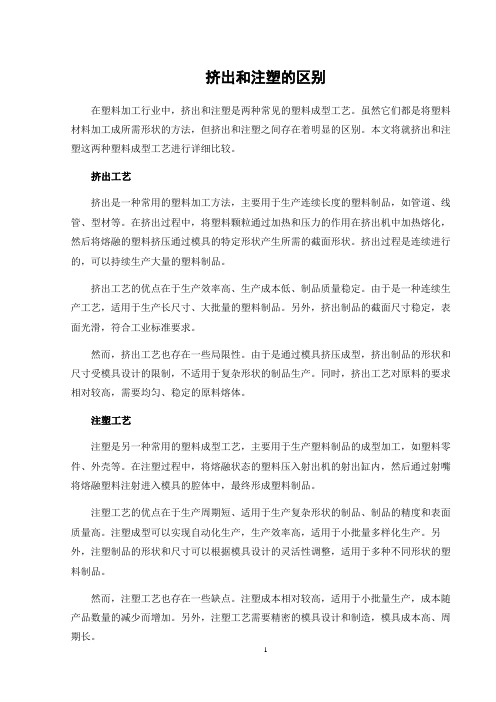
挤出和注塑的区别在塑料加工行业中,挤出和注塑是两种常见的塑料成型工艺。
虽然它们都是将塑料材料加工成所需形状的方法,但挤出和注塑之间存在着明显的区别。
本文将就挤出和注塑这两种塑料成型工艺进行详细比较。
挤出工艺挤出是一种常用的塑料加工方法,主要用于生产连续长度的塑料制品,如管道、线管、型材等。
在挤出过程中,将塑料颗粒通过加热和压力的作用在挤出机中加热熔化,然后将熔融的塑料挤压通过模具的特定形状产生所需的截面形状。
挤出过程是连续进行的,可以持续生产大量的塑料制品。
挤出工艺的优点在于生产效率高、生产成本低、制品质量稳定。
由于是一种连续生产工艺,适用于生产长尺寸、大批量的塑料制品。
另外,挤出制品的截面尺寸稳定,表面光滑,符合工业标准要求。
然而,挤出工艺也存在一些局限性。
由于是通过模具挤压成型,挤出制品的形状和尺寸受模具设计的限制,不适用于复杂形状的制品生产。
同时,挤出工艺对原料的要求相对较高,需要均匀、稳定的原料熔体。
注塑工艺注塑是另一种常用的塑料成型工艺,主要用于生产塑料制品的成型加工,如塑料零件、外壳等。
在注塑过程中,将熔融状态的塑料压入射出机的射出缸内,然后通过射嘴将熔融塑料注射进入模具的腔体中,最终形成塑料制品。
注塑工艺的优点在于生产周期短、适用于生产复杂形状的制品、制品的精度和表面质量高。
注塑成型可以实现自动化生产,生产效率高,适用于小批量多样化生产。
另外,注塑制品的形状和尺寸可以根据模具设计的灵活性调整,适用于多种不同形状的塑料制品。
然而,注塑工艺也存在一些缺点。
注塑成本相对较高,适用于小批量生产,成本随产品数量的减少而增加。
另外,注塑工艺需要精密的模具设计和制造,模具成本高、周期长。
结论综上所述,挤出和注塑是两种不同的塑料成型工艺,各自具有自身的优势和劣势。
挤出适用于生产连续长度的塑料制品,适用于大批量生产,制品尺寸稳定;注塑适用于生产复杂形状的制品,适用于小批量多样化生产,制品精度高。
在实际生产过程中,需要根据所需制品的形状、尺寸、数量等因素选择合适的成型工艺,以实现最佳的生产效果和经济效益。
pfa成型方法
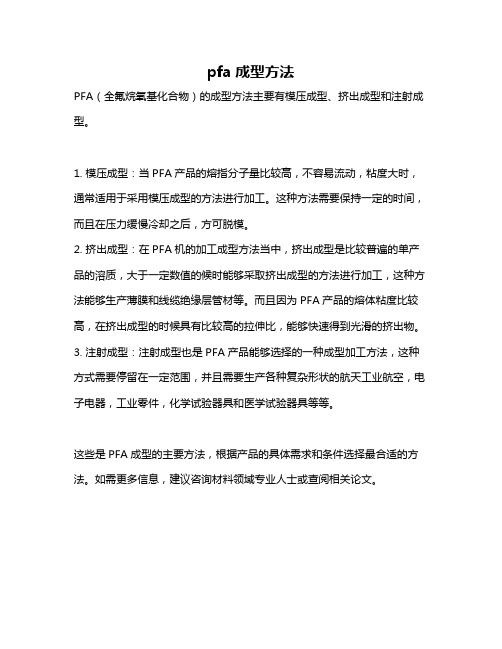
pfa成型方法
PFA(全氟烷氧基化合物)的成型方法主要有模压成型、挤出成型和注射成型。
1. 模压成型:当PFA产品的熔指分子量比较高,不容易流动,粘度大时,通常适用于采用模压成型的方法进行加工。
这种方法需要保持一定的时间,而且在压力缓慢冷却之后,方可脱模。
2. 挤出成型:在PFA机的加工成型方法当中,挤出成型是比较普遍的单产品的溶质,大于一定数值的候时能够采取挤出成型的方法进行加工,这种方法能够生产薄膜和线缆绝缘层管材等。
而且因为PFA产品的熔体粘度比较高,在挤出成型的时候具有比较高的拉伸比,能够快速得到光滑的挤出物。
3. 注射成型:注射成型也是PFA产品能够选择的一种成型加工方法,这种方式需要停留在一定范围,并且需要生产各种复杂形状的航天工业航空,电子电器,工业零件,化学试验器具和医学试验器具等等。
这些是PFA成型的主要方法,根据产品的具体需求和条件选择最合适的方法。
如需更多信息,建议咨询材料领域专业人士或查阅相关论文。
挤出成型和注塑成型的区别在哪

挤出成型和注塑成型的区别在哪在塑料加工行业中,挤出成型和注塑成型是两种常见的方法,它们在生产工艺、设备和产品特性等方面存在显著的区别。
工艺原理挤出成型挤出成型是将塑料通过加热融化后,通过特定形状的挤出口挤出,使其成型后冷却固化的一种成型工艺。
挤出机将塑料料柱加热至熔化状态,然后通过螺杆挤出口挤出,经过模具成型,最后冷却硬化并切割成所需长度。
注塑成型注塑成型是将塑料颗粒加热融化后,由注射机注入模具腔内,冷却后形成所需形状的一种成型工艺。
注射机通过螺杆将塑料颗粒加热融化,然后注射到模具中,通过冷却后得到成型产品。
设备特点挤出成型挤出机通常由进料系统、加热系统、螺杆和机筒、模具头以及成型部分组成。
挤出机更适用于生产连续且较长的产品,如管材、板材、薄膜等。
注塑成型注塑机主要由进料系统、注射系统、压力系统、冷却系统和电气系统组成。
注塑机适合生产成型复杂、结构精细的产品,如塑料零件、壳体等。
产品特性挤出产品挤出成型的产品表面光滑,密度均匀,强度较高,但是尺寸精度较一般。
常见的产品包括各种管材、板材、薄膜、型材等。
注塑产品注塑成型的产品具有较高的尺寸精度和表面质量,可生产出形状复杂且结构精细的塑件。
注塑产品广泛应用于家电、汽车、医疗器械等领域。
生产效率挤出成型由于是一种连续生产工艺,适用于大批量生产,具有较高的生产效率。
而注塑成型虽然可实现自动化生产,但每次注射成型的过程相对禁止,适用于小批量生产。
综上所述,挤出成型和注塑成型在工艺原理、设备特点、产品特性和生产效率等方面存在明显差异。
选择合适的成型工艺取决于产品的需求、生产规模以及生产效率要求。
注塑和挤出工艺的区别
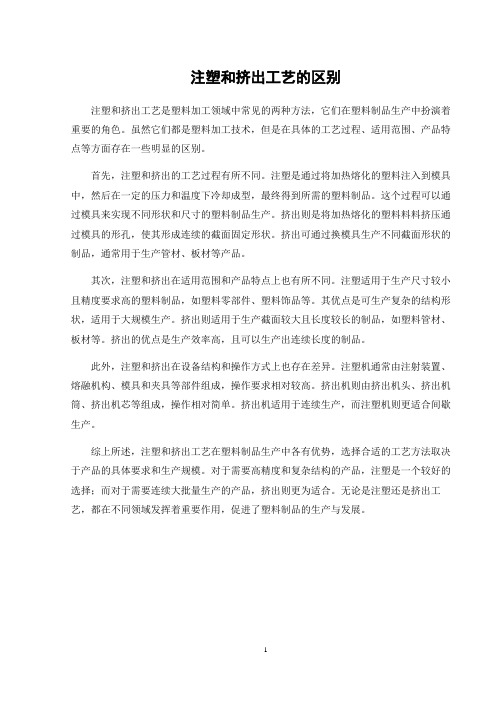
注塑和挤出工艺的区别
注塑和挤出工艺是塑料加工领域中常见的两种方法,它们在塑料制品生产中扮演着重要的角色。
虽然它们都是塑料加工技术,但是在具体的工艺过程、适用范围、产品特点等方面存在一些明显的区别。
首先,注塑和挤出的工艺过程有所不同。
注塑是通过将加热熔化的塑料注入到模具中,然后在一定的压力和温度下冷却成型,最终得到所需的塑料制品。
这个过程可以通过模具来实现不同形状和尺寸的塑料制品生产。
挤出则是将加热熔化的塑料料料挤压通过模具的形孔,使其形成连续的截面固定形状。
挤出可通过换模具生产不同截面形状的制品,通常用于生产管材、板材等产品。
其次,注塑和挤出在适用范围和产品特点上也有所不同。
注塑适用于生产尺寸较小且精度要求高的塑料制品,如塑料零部件、塑料饰品等。
其优点是可生产复杂的结构形状,适用于大规模生产。
挤出则适用于生产截面较大且长度较长的制品,如塑料管材、板材等。
挤出的优点是生产效率高,且可以生产出连续长度的制品。
此外,注塑和挤出在设备结构和操作方式上也存在差异。
注塑机通常由注射装置、熔融机构、模具和夹具等部件组成,操作要求相对较高。
挤出机则由挤出机头、挤出机筒、挤出机芯等组成,操作相对简单。
挤出机适用于连续生产,而注塑机则更适合间歇生产。
综上所述,注塑和挤出工艺在塑料制品生产中各有优势,选择合适的工艺方法取决于产品的具体要求和生产规模。
对于需要高精度和复杂结构的产品,注塑是一个较好的选择;而对于需要连续大批量生产的产品,挤出则更为适合。
无论是注塑还是挤出工艺,都在不同领域发挥着重要作用,促进了塑料制品的生产与发展。
1。
塑料的成型工艺
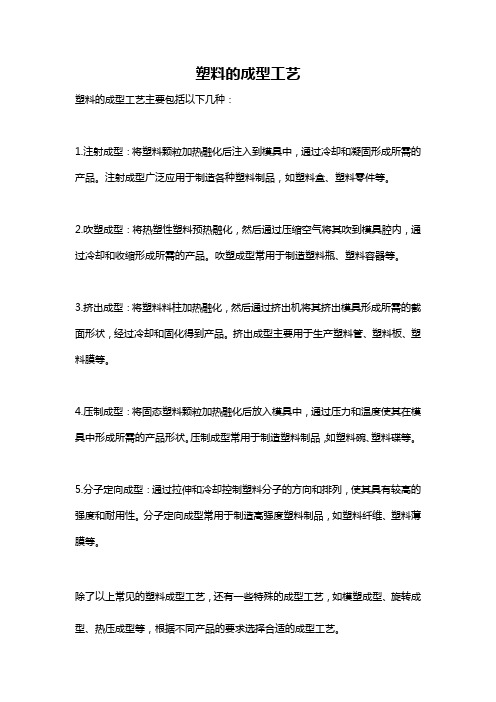
塑料的成型工艺
塑料的成型工艺主要包括以下几种:
1.注射成型:将塑料颗粒加热融化后注入到模具中,通过冷却和凝固形成所需的产品。
注射成型广泛应用于制造各种塑料制品,如塑料盒、塑料零件等。
2.吹塑成型:将热塑性塑料预热融化,然后通过压缩空气将其吹到模具腔内,通过冷却和收缩形成所需的产品。
吹塑成型常用于制造塑料瓶、塑料容器等。
3.挤出成型:将塑料料柱加热融化,然后通过挤出机将其挤出模具形成所需的截面形状,经过冷却和固化得到产品。
挤出成型主要用于生产塑料管、塑料板、塑料膜等。
4.压制成型:将固态塑料颗粒加热融化后放入模具中,通过压力和温度使其在模具中形成所需的产品形状。
压制成型常用于制造塑料制品,如塑料碗、塑料碟等。
5.分子定向成型:通过拉伸和冷却控制塑料分子的方向和排列,使其具有较高的强度和耐用性。
分子定向成型常用于制造高强度塑料制品,如塑料纤维、塑料薄膜等。
除了以上常见的塑料成型工艺,还有一些特殊的成型工艺,如模塑成型、旋转成型、热压成型等,根据不同产品的要求选择合适的成型工艺。
塑料成型的主要方法

2.压 延 成 型
压延成型是热塑性塑料主要成型方法之一。该方法主要是制造薄膜及片状材料。适于压延的热塑性塑料有PVC、PE、PP、ABS、CA、VC/EVA等。
3.注 射 成 型
注射成型又称注射模塑成型,它是一种注射兼模塑的成型方法。注射成型方法其优点是生产速度快、效率高,操作可实现自动化,能成型形状复杂的制件。不利的一面是模具成本高,且清理困难,所以小批量制品就不宜采用此法成型。用这种方法成型的制品有:电视机外壳、半导体收音机外壳、电器上的接插件、旋纽、线圈骨架、齿轮、汽车灯罩、茶杯、饭碗、皂盒、浴缸、凉鞋等等。
泡沫塑料按制品的软硬程度不同分为软质、硬质和半硬质泡沫塑料。
�
我们通常见到的板、棒、管、电线护套、丝、带、某些薄膜等都是用这种方法制成的。国内已能生产细的如渔网丝,粗的如直径为0.2m的大直径塑料管,还能生产建筑上用的异型截面的型材,如塑料门窗。
挤出成型生产效率高,操作简单,产品质量均匀;设备可大可小,可简可精,容易制造,便于投产;可以一机多用或进行综合性生产。另外挤出成型机还可以用于混合、塑化、脱水、造粒、喂料等不同的工艺。
目前,注射成型适用于全部热塑性塑料,其成型周期短,花色品种多,形状可以由简到繁,尺寸可以由大到小,而且制品尺寸精确,产品易更新换代。
4.吹 塑 成 型
吹塑成型包括吹塑薄膜及吹塑中空制品两种。
5.成的内部含有无数微小泡孔的塑料制品,又称为微孔或多孔性塑料。现代技术几乎可以把所有的热塑性和热固性树脂加工成泡沫塑料。目前通常用于制造泡沫塑料的树脂有聚苯乙烯、聚氯乙烯、聚乙烯、聚氨酯、脲甲醛树脂等等。
塑料制品的几种主要成型方法
1.挤 出 成 型
热塑性树脂及各种添加剂混合造粒后加入挤出机。物料在机筒内受到机械剪切力、摩擦热和外加热的作用,使其熔融塑化,同时又在螺杆旋转向前的推挤下,使其成为密实的熔融体。熔融体再经过滤板及不同类型的成型口模,而变为截面形状恒定的型材,经冷却定型得到制品。
塑料挤出和注射成型区别是什么
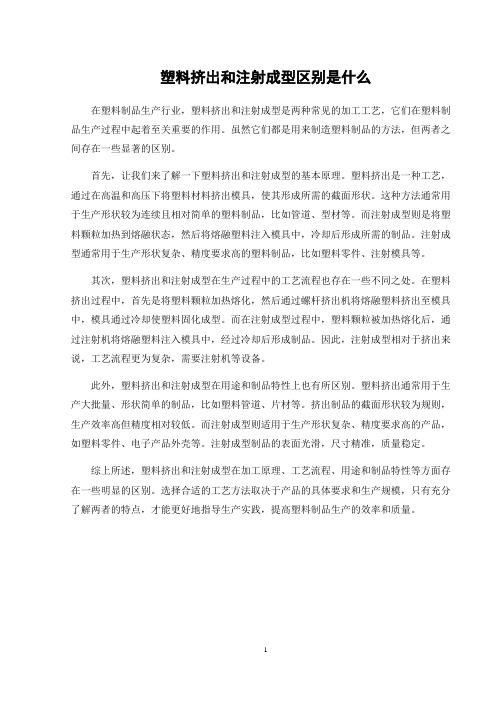
塑料挤出和注射成型区别是什么在塑料制品生产行业,塑料挤出和注射成型是两种常见的加工工艺,它们在塑料制品生产过程中起着至关重要的作用。
虽然它们都是用来制造塑料制品的方法,但两者之间存在一些显著的区别。
首先,让我们来了解一下塑料挤出和注射成型的基本原理。
塑料挤出是一种工艺,通过在高温和高压下将塑料材料挤出模具,使其形成所需的截面形状。
这种方法通常用于生产形状较为连续且相对简单的塑料制品,比如管道、型材等。
而注射成型则是将塑料颗粒加热到熔融状态,然后将熔融塑料注入模具中,冷却后形成所需的制品。
注射成型通常用于生产形状复杂、精度要求高的塑料制品,比如塑料零件、注射模具等。
其次,塑料挤出和注射成型在生产过程中的工艺流程也存在一些不同之处。
在塑料挤出过程中,首先是将塑料颗粒加热熔化,然后通过螺杆挤出机将熔融塑料挤出至模具中,模具通过冷却使塑料固化成型。
而在注射成型过程中,塑料颗粒被加热熔化后,通过注射机将熔融塑料注入模具中,经过冷却后形成制品。
因此,注射成型相对于挤出来说,工艺流程更为复杂,需要注射机等设备。
此外,塑料挤出和注射成型在用途和制品特性上也有所区别。
塑料挤出通常用于生产大批量、形状简单的制品,比如塑料管道、片材等。
挤出制品的截面形状较为规则,生产效率高但精度相对较低。
而注射成型则适用于生产形状复杂、精度要求高的产品,如塑料零件、电子产品外壳等。
注射成型制品的表面光滑,尺寸精准,质量稳定。
综上所述,塑料挤出和注射成型在加工原理、工艺流程、用途和制品特性等方面存在一些明显的区别。
选择合适的工艺方法取决于产品的具体要求和生产规模,只有充分了解两者的特点,才能更好地指导生产实践,提高塑料制品生产的效率和质量。
1。
粉末材料的主要成型方法

粉末材料的主要成型方法
粉末材料的主要成型方法包括:
1. 烧结成型:将粉末材料加压成形后,在高温下进行烧结,使粉末颗粒粘结和合并,形成坚固的固体。
2. 注射成型:将粉末和粘结剂混合后注射到模具中,然后通过加热或固化使粉末颗粒固化成形。
3. 挤出成型:将粉末和粘结剂混合后挤出成型,通过加热或固化使粉末颗粒固化成形。
4. 粉末冶金成型:通过压制、烧结或热压等方式,将粉末材料制成金属产品或零件。
5. 粘结剂成型:将粉末材料与粘结剂混合后进行成型,其中粘结剂的作用是使粉末颗粒粘结在一起。
6. 激光烧结成型:利用激光束将粉末颗粒局部加热,使其熔化和熔接成形。
7. 真空烧结成型:在真空环境中进行烧结成型,可以减少氧化反应和杂质的产生,提高成品质量。
8. 喷雾成型:将粉末材料喷雾成细小颗粒,在加热或加压条件下使其固化成形。
高分子塑料成型方式
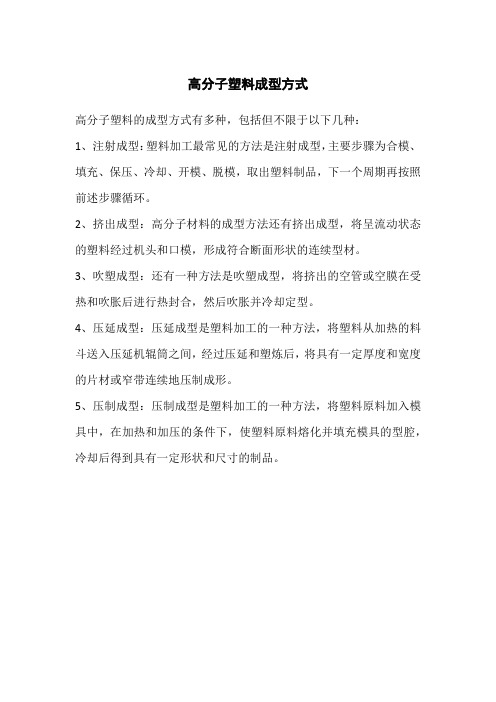
高分子塑料成型方式
高分子塑料的成型方式有多种,包括但不限于以下几种:
1、注射成型:塑料加工最常见的方法是注射成型,主要步骤为合模、填充、保压、冷却、开模、脱模,取出塑料制品,下一个周期再按照前述步骤循环。
2、挤出成型:高分子材料的成型方法还有挤出成型,将呈流动状态的塑料经过机头和口模,形成符合断面形状的连续型材。
3、吹塑成型:还有一种方法是吹塑成型,将挤出的空管或空膜在受热和吹胀后进行热封合,然后吹胀并冷却定型。
4、压延成型:压延成型是塑料加工的一种方法,将塑料从加热的料斗送入压延机辊筒之间,经过压延和塑炼后,将具有一定厚度和宽度的片材或窄带连续地压制成形。
5、压制成型:压制成型是塑料加工的一种方法,将塑料原料加入模具中,在加热和加压的条件下,使塑料原料熔化并填充模具的型腔,冷却后得到具有一定形状和尺寸的制品。
挤出成型和注射成型

4. 成型周期
注射成型周期从几秒钟到几分钟不等。周期的长短取 决于制品的壁厚、大小、形状、注射成型机的类型以 及所采用的塑料品种和工艺条件等。
5. 产品
注射成型可生产各种形状、尺寸、精度满足各种要求 的制品。
注射成型制品的重量从一克到几十公斤不等,视需要 而定。
注塑成型特点
1. 生产周期短、生产效率高; 2. 能成型形状复杂、尺寸精确或带嵌件的制品; 3. 成型塑料品种多; 4. 易于实现自动化。
注射成型是将粒状或粉状塑料从注射成型机的料斗送入 机简内加热熔融塑化后,在柱塞或螺杆加压下,物料被 压缩并向前移动,通过机简前端的喷嘴,以很快的速度 注入温度较低的闭合模具内,经过一定时间的冷却定型 后,开启模具即得制品。这种成型方法是一种间歇式的 操作过程。
3. 原料: 除极少数几种热塑性塑料外,几乎所有的热塑性塑料都 可用此法成型。注射成型也能加工某些热固性塑料,如 酚醛塑料等。
双螺杆挤出原理
双螺杆挤出机的结 构
双螺杆挤出的特点
与单螺杆挤出机相比,双螺杆挤出机具有以下特点 :
1、较高的固体输送能力和挤出产量;
2、自洁能力; 3、混合塑化能力高; 4、较低的塑化温度,减小分解可能; 5、结构复杂,成本高。
(三)螺杆的几种形式
►常用的是等距不等深螺杆
二、熔体输送理论
熔体有四种形式的流动
பைடு நூலகம்
熔体输送能力的分析
► 熔体的输送 Q = Qd - Qp - Ql, 实际的流动形式为:熔 体沿螺槽螺旋前进。类似弹簧缠绕在螺槽内。
► 忽略Ql,经计算熔体输送能力为:
① 机头阻力加大P↑,Q↓产量下降。 ② 转速N↑,Q↑提高。 ③ 螺杆直径增加D↑,Q↑↑产量明显增加。所以要得 到
简述塑料成型的主要方法

简述塑料成型的主要方法塑料成型是将塑料原料转化为制件的过程,通过各种成型方法使塑料原料成为具有所需形状、尺寸和性能的制件。
以下是塑料成型的主要方法:1.注射成型:注射成型是一种常用的塑料成型方法,通过将塑料原料加热至熔融状态,然后注入模具中,冷却后脱模得到所需形状的制件。
注射成型适用于各种热塑性塑料和部分热固性塑料。
2.挤出成型:挤出成型是通过加压方式将塑料原料从模具口挤出,然后在冷却或定型过程中得到所需形状的制件。
挤出成型主要用于生产连续的管材、片材、型材等。
3.压延成型:压延成型是将塑料原料在加热状态下通过一系列轧辊的碾压、拉伸,使其成为薄膜或片材的工艺过程。
压延成型适用于热塑性塑料,如聚乙烯、聚氯乙烯等。
4.吹塑成型:吹塑成型是将塑料原料加热至熔融状态,然后通过模具口吹入空气使其膨胀并贴合模具型腔表面,冷却后得到所需形状的制件。
吹塑成型适用于生产各种中空制件,如瓶子、罐子等。
5.热成型:热成型是将塑料原料加热至软化状态,然后将其覆盖在模具上,通过冷却和定型得到所需形状的制件。
热成型适用于生产大型或复杂的制件,如汽车零部件、家具面板等。
6.旋转成型:旋转成型是通过旋转模具使塑料原料在离心力作用下充满模具型腔,冷却后得到所需形状的制件。
旋转成型主要用于生产圆筒形或旋转体形的制件,如油桶、瓶盖等。
7.激光成型:激光成型是一种高精度、高效率的塑料成型方法,通过激光束照射在塑料原料表面,使其熔融并按照预设形状固化,从而得到制件。
激光成型适用于生产小型、高精度制件,如电子元件、医疗器械等。
8.热压成型:热压成型是将塑料原料加热至软化状态,然后将其覆盖在模具上,再通过加压方式使其贴合模具型腔表面,冷却后得到所需形状的制件。
热压成型适用于生产薄片状或板材制件,如包装材料、建筑材料等。
9.真空成型:真空成型是将塑料原料加热至软化状态,然后在真空作用下使其贴合模具型腔表面,冷却后得到所需形状的制件。
真空成型适用于生产薄片状或管材制件,如食品包装材料、管道等。
ldpe的成型方式
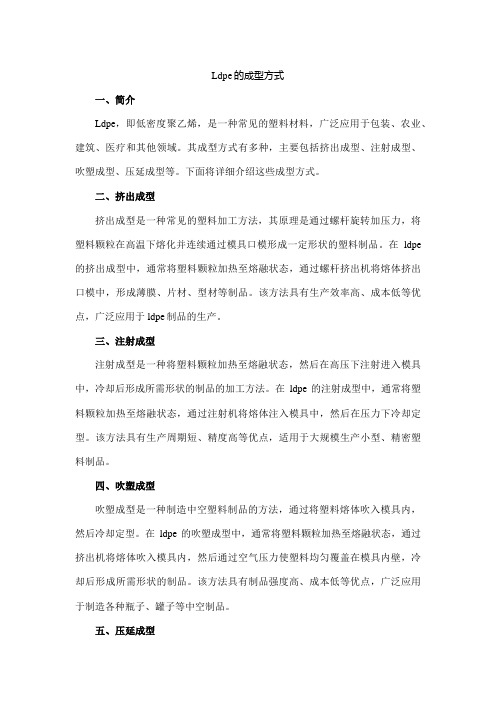
Ldpe的成型方式一、简介Ldpe,即低密度聚乙烯,是一种常见的塑料材料,广泛应用于包装、农业、建筑、医疗和其他领域。
其成型方式有多种,主要包括挤出成型、注射成型、吹塑成型、压延成型等。
下面将详细介绍这些成型方式。
二、挤出成型挤出成型是一种常见的塑料加工方法,其原理是通过螺杆旋转加压力,将塑料颗粒在高温下熔化并连续通过模具口模形成一定形状的塑料制品。
在ldpe 的挤出成型中,通常将塑料颗粒加热至熔融状态,通过螺杆挤出机将熔体挤出口模中,形成薄膜、片材、型材等制品。
该方法具有生产效率高、成本低等优点,广泛应用于ldpe制品的生产。
三、注射成型注射成型是一种将塑料颗粒加热至熔融状态,然后在高压下注射进入模具中,冷却后形成所需形状的制品的加工方法。
在ldpe的注射成型中,通常将塑料颗粒加热至熔融状态,通过注射机将熔体注入模具中,然后在压力下冷却定型。
该方法具有生产周期短、精度高等优点,适用于大规模生产小型、精密塑料制品。
四、吹塑成型吹塑成型是一种制造中空塑料制品的方法,通过将塑料熔体吹入模具内,然后冷却定型。
在ldpe的吹塑成型中,通常将塑料颗粒加热至熔融状态,通过挤出机将熔体吹入模具内,然后通过空气压力使塑料均匀覆盖在模具内壁,冷却后形成所需形状的制品。
该方法具有制品强度高、成本低等优点,广泛应用于制造各种瓶子、罐子等中空制品。
五、压延成型压延成型是一种将热塑性塑料通过两个或多个热辊压延成薄膜或片材的加工方法。
在ldpe的压延成型中,通常将塑料颗粒加热至熔融状态,然后通过压延机将其压延成薄膜或片材。
该方法具有制品厚度均匀、表面光滑等优点,广泛应用于制造薄膜、片材等制品。
六、结论Ldpe的成型方式有多种,每种方式都有其特点和应用范围。
在实际生产中,可以根据产品的要求和生产条件选择合适的成型方式。
随着科技的不断发展,ldpe的成型方式也在不断改进和完善,为塑料制品的生产提供了更多的选择和可能性。
挤出成型工艺过程与注射成型工艺过程最大的区别是
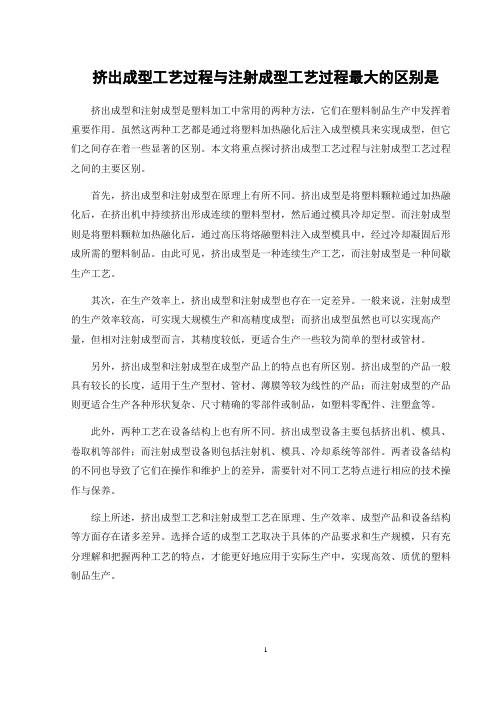
挤出成型工艺过程与注射成型工艺过程最大的区别是挤出成型和注射成型是塑料加工中常用的两种方法,它们在塑料制品生产中发挥着重要作用。
虽然这两种工艺都是通过将塑料加热融化后注入成型模具来实现成型,但它们之间存在着一些显著的区别。
本文将重点探讨挤出成型工艺过程与注射成型工艺过程之间的主要区别。
首先,挤出成型和注射成型在原理上有所不同。
挤出成型是将塑料颗粒通过加热融化后,在挤出机中持续挤出形成连续的塑料型材,然后通过模具冷却定型。
而注射成型则是将塑料颗粒加热融化后,通过高压将熔融塑料注入成型模具中,经过冷却凝固后形成所需的塑料制品。
由此可见,挤出成型是一种连续生产工艺,而注射成型是一种间歇生产工艺。
其次,在生产效率上,挤出成型和注射成型也存在一定差异。
一般来说,注射成型的生产效率较高,可实现大规模生产和高精度成型;而挤出成型虽然也可以实现高产量,但相对注射成型而言,其精度较低,更适合生产一些较为简单的型材或管材。
另外,挤出成型和注射成型在成型产品上的特点也有所区别。
挤出成型的产品一般具有较长的长度,适用于生产型材、管材、薄膜等较为线性的产品;而注射成型的产品则更适合生产各种形状复杂、尺寸精确的零部件或制品,如塑料零配件、注塑盒等。
此外,两种工艺在设备结构上也有所不同。
挤出成型设备主要包括挤出机、模具、卷取机等部件;而注射成型设备则包括注射机、模具、冷却系统等部件。
两者设备结构的不同也导致了它们在操作和维护上的差异,需要针对不同工艺特点进行相应的技术操作与保养。
综上所述,挤出成型工艺和注射成型工艺在原理、生产效率、成型产品和设备结构等方面存在诸多差异。
选择合适的成型工艺取决于具体的产品要求和生产规模,只有充分理解和把握两种工艺的特点,才能更好地应用于实际生产中,实现高效、质优的塑料制品生产。
1。
注射成形挤出成形和压塑成形的工艺过程有何不同点

注射成形挤出成形和压塑成形的工艺过程有何不同点注射成形、挤出成形和压塑成形是塑料加工领域常用的三种工艺方法,它们各有特点和适用范围。
在实际生产中,厂家根据产品的具体要求和产量选择不同的成形工艺。
下面将分别介绍这三种工艺的特点,以及它们之间的不同点。
注射成形注射成形是利用塑料注射机将熔化状态的塑料材料通过射嘴注入模具腔中,然后在模具中冷却凝固,最终形成所需产品的工艺过程。
注射成形工艺适用于生产大量、精密度要求高的塑料制品。
这种工艺能够生产复杂的结构和形状,并且表面光滑度高,几何尺寸精确,是制造高质量塑料制品的首选方法。
挤出成形挤出成形是通过挤出机将塑料料推入螺杆内,在高温高压下使其熔化,然后通过模具挤出成型的工艺过程。
挤出成形适用于生产连续的塑料型材,比如管材、板材、棒材等,也可以生产一些截面简单的异型材料。
该工艺具有生产效率高、原料利用率高的优点,但对产品的尺寸精度和表面质量要求较低。
压塑成形压塑成形是将塑料料置于开放式模具中,在模具上施加热压力,使塑料熔化并填充到模具腔中,经冷却后得到产品的工艺过程。
压塑成形适用于生产尺寸较大的、结构简单的塑料制品,比如家具、垃圾桶等。
该工艺成本低,但无法生产复杂结构和高精度的产品。
不同点比较1.生产范围不同:注射成形适用于大批量、高精度的产品,挤出成形适用于连续型材的生产,而压塑成形适用于简单结构、尺寸较大的产品生产。
2.产品精度要求不同:注射成形产品的尺寸精度和表面质量要求都极高,挤出成形次之,而压塑成形则要求相对较低。
13.生产效率和原料利用率不同:注射成形的生产效率高,原料利用率高,挤出成形次之,而压塑成形的生产效率和原料利用率都较低。
4.适用产品结构不同:注射成形适用于复杂结构的产品,挤出成形适用于连续型材,压塑成形适用于简单结构的产品。
在选择成形工艺时,除了产品本身的要求,还需要考虑到生产成本、产能和原材料等要素,综合各方面因素做出合理的选择能够有效提高生产效率,降低生产成本,满足市场需求。
塑料挤出成型和注塑成型区别在哪

塑料挤出成型和注塑成型区别在哪
塑料成型技术是制造塑料制品的常用方法,其中挤出成型和注塑成型是两种常见的塑料加工工艺。
虽然它们都用于加工塑料制品,但挤出成型和注塑成型在工艺过程、适用范围和特点上有着明显的区别。
首先,挤出成型是将塑料颗粒通过加热融化后,在挤出机内经过螺杆挤出头挤出成型。
该工艺适用于生产长条状、截面规则的塑料制品,如塑料管材、板材、型材等,具有生产效率高、成本低等特点。
而注塑成型是将塑料颗粒融化后注入模具中,通过高压注射成型而得到成品。
注塑成型适用于制造成型复杂、尺寸精度要求高的塑料制品,如塑料零部件、壳体等。
其次,挤出成型和注塑成型在塑料制品的生产工艺上也存在明显差异。
挤出成型主要通过挤出机将熔化的塑料挤出成型,工艺比较简单,适用于连续生产,但对于成型形状复杂的产品生产效率相对较低。
而注塑成型则需要借助注塑机设备,通过模具的开合和射出系统完成成品的注射成型。
注塑成型的适用范围更广,可以生产各种复杂的立体形状产品。
最后,挤出成型和注塑成型在产品质量和材料利用率上也有所不同。
挤出成型的产品密度相对较低,而注塑成型的产品密度更高,同时注塑成型可以通过多腔模具实现多个产品同时成型,提高生产效率。
另外,由于注塑成型是将塑料材料直接注射到模具腔内,因此可以减少材料浪费,提高材料利用率。
因此,虽然挤出成型和注塑成型都是常见的塑料加工技术,但它们在工艺过程、适用范围和特点上存在明显区别。
选择合适的加工工艺取决于产品的形状、尺寸、材料以及生产要求,合理选用挤出成型或注塑成型将有助于提高生产效率、降低生产成本,并确保产品质量。
1。
【收藏】13种最常用的塑料成型工艺流程
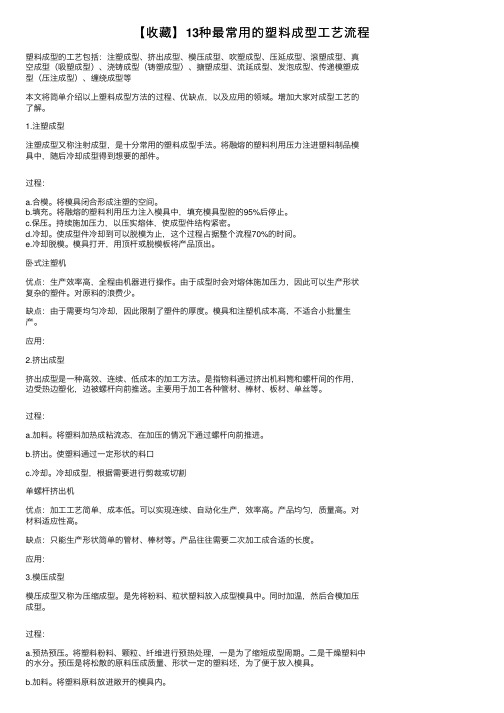
【收藏】13种最常⽤的塑料成型⼯艺流程塑料成型的⼯艺包括:注塑成型、挤出成型、模压成型、吹塑成型、压延成型、滚塑成型、真空成型(吸塑成型)、浇铸成型(铸塑成型)、搪塑成型、流延成型、发泡成型、传递模塑成型(压注成型)、缠绕成型等本⽂将简单介绍以上塑料成型⽅法的过程、优缺点,以及应⽤的领域。
增加⼤家对成型⼯艺的了解。
1.注塑成型注塑成型⼜称注射成型,是⼗分常⽤的塑料成型⼿法。
将融熔的塑料利⽤压⼒注进塑料制品模具中,随后冷却成型得到想要的部件。
过程:a.合模。
将模具闭合形成注塑的空间。
b.填充。
将融熔的塑料利⽤压⼒注⼊模具中,填充模具型腔的95%后停⽌。
c.保压。
持续施加压⼒,以压实熔体,使成型件结构紧密。
d.冷却。
使成型件冷却到可以脱模为⽌,这个过程占据整个流程70%的时间。
e.冷却脱模。
模具打开,⽤顶杆或脱模板将产品顶出。
卧式注塑机优点:⽣产效率⾼,全程由机器进⾏操作。
由于成型时会对熔体施加压⼒,因此可以⽣产形状复杂的塑件。
对原料的浪费少。
缺点:由于需要均匀冷却,因此限制了塑件的厚度。
模具和注塑机成本⾼,不适合⼩批量⽣产。
应⽤:2.挤出成型挤出成型是⼀种⾼效、连续、低成本的加⼯⽅法。
是指物料通过挤出机料筒和螺杆间的作⽤,边受热边塑化,边被螺杆向前推送。
主要⽤于加⼯各种管材、棒材、板材、单丝等。
过程:a.加料。
将塑料加热成粘流态,在加压的情况下通过螺杆向前推进。
b.挤出。
使塑料通过⼀定形状的料⼝c.冷却。
冷却成型,根据需要进⾏剪裁或切割单螺杆挤出机优点:加⼯⼯艺简单,成本低。
可以实现连续、⾃动化⽣产,效率⾼。
产品均匀,质量⾼。
对材料适应性⾼。
缺点:只能⽣产形状简单的管材、棒材等。
产品往往需要⼆次加⼯成合适的长度。
应⽤:3.模压成型模压成型⼜称为压缩成型。
是先将粉料、粒状塑料放⼊成型模具中。
同时加温,然后合模加压成型。
过程:a.预热预压。
将塑料粉料、颗粒、纤维进⾏预热处理,⼀是为了缩短成型周期。
⼆是⼲燥塑料中的⽔分。
- 1、下载文档前请自行甄别文档内容的完整性,平台不提供额外的编辑、内容补充、找答案等附加服务。
- 2、"仅部分预览"的文档,不可在线预览部分如存在完整性等问题,可反馈申请退款(可完整预览的文档不适用该条件!)。
- 3、如文档侵犯您的权益,请联系客服反馈,我们会尽快为您处理(人工客服工作时间:9:00-18:30)。
根据排列方式不同分类:卧式、立式、 根据排列方式不同分类:卧式、立式、角式
塑料工艺
注射机的组成
塑料工艺
注射系统
塑料工艺
• 作用:将物料塑化,并在很高的压力和较快的速度下,通 作用:将物料塑化,并在很高的压力和较快的速度下, 过柱塞/螺杆的推挤, 过柱塞/螺杆的推挤,将熔融塑料注射入型腔 • 组成:料斗、加料装置、料筒、螺杆、柱塞和分流梭、喷 组成:料斗、加料装置、料筒、螺杆、柱塞和分流梭、 嘴。
熔体输送能力的分析
塑料工艺
• •
实际的流动形式为: 熔体的输送 Q = Qd - Qp - Ql, 实际的流动形式为:熔 体沿螺槽螺旋前进。类似弹簧缠绕在螺槽内。 体沿螺槽螺旋前进。类似弹簧缠绕在螺槽内。 忽略Ql,经计算熔体输送能力为: 忽略 ,经计算熔体输送能力为:
① ② ③
机头阻力加大P↑, 产量下降 产量下降。 机头阻力加大 ,Q↓产量下降。 转速N↑, 提高 提高。 转速 ,Q↑提高。 螺杆直径增加D↑, 产量明显增加。 螺杆直径增加 ,Q↑↑产量明显增加。所以要得 到 产量明显增加 高的产量,增大螺杆直径是最有效的手段之一。 高的产量,增大螺杆直径是最有效的手段之一。 螺杆长度L↑, ,挤出稳定性增加。 ④ 螺杆长度 ,Q↑,挤出稳定性增加。 螺槽深度h增加 挤出稳定性下降。 增加, ⑤ 螺槽深度 增加,挤出稳定性下降。
塑料工艺
• (一)塑化装置 • 1、料斗、加料计量装置、料筒 、螺杆 与挤出装置大致 料斗、加料计量装置、 相同 • 2、注射螺杆与挤出螺杆的不同: 、注射螺杆与挤出螺杆的不同: – 注射螺杆在旋转的同时有轴向运动,有效长度是变化 注射螺杆在旋转的同时有轴向运动, 的。 – 长径比小,只需塑化,不需稳定。 长径比小,只需塑化,不需稳定。 – 螺槽深以提高生产率。 螺槽深以提高生产率。 – 加料段较长。 加料段较长。 – 螺杆头部多为尖头,有的加止逆环 螺杆头部多为尖头,有的加止逆环。
一、挤出设备
塑料工艺
由: 挤出机 机头 口模 辅机等组成
(一) 挤出设备组成
塑料工艺
单螺杆挤出机的结构
塑料工艺
• 单螺杆挤出机主要 传动系统、 由传动系统、加料 系统、塑化系统、 系统、塑化系统、 加热与冷却系统、 加热与冷却系统、 控制系统等组成。 控制系统等组成。 • 挤出系统是最主要 挤出系统是最主要 的系统,它由料筒、 的系统,它由料筒、 螺杆、多孔板和过 螺杆、 滤网组成。 滤网组成。
螺杆头部结构
三、普通三段式单螺杆存在的问题
塑料工艺
•
目前,一般单螺杆多采用等距不等深螺杆, 目前,一般单螺杆多采用等距不等深螺杆,加料段 常和均化段螺槽深度不变,压缩段螺槽逐渐变浅。 常和均化段螺槽深度不变,压缩段螺槽逐渐变浅。 这种螺杆可以满足一般的挤出成型, 这种螺杆可以满足一般的挤出成型,但存在以下几 方面的问题: 方面的问题: 1. 熔融效率低 熔融段熔体与固体床共同存在于一个螺槽 减小了料筒壁与固体床的接触面积; 中,减小了料筒壁与固体床的接触面积;固体床 随着熔融解体,部分碎片进入熔体中, 随着熔融解体,部分碎片进入熔体中,很难从剪 切获得热量,这样,固体床不能彻底熔融;另外, 切获得热量,这样,固体床不能彻底熔融;另外, 已熔物料与料筒壁接触, 已熔物料与料筒壁接触,从料筒壁和熔膜处获取 热量,温度继续升高过热。 热量,温度继续升高过热。
塑料工艺
塑料工艺
4、混合螺杆 、
• 在熔融段末或均化段增设置混合、混炼、剪切、 在熔融段末或均化段增设置混合、混炼、剪切、 均化等作用的元件,可以提高混合的均匀性、 均化等作用的元件,可以提高混合的均匀性、混 炼效果好,混色均匀,分散性好。 炼效果好,混色均匀,分散性好。
塑料工艺
塑料工艺
注射成型
注塑成型特点
塑料工艺
1. 2. 3. 4.
生产周期短、生产效率高; 生产周期短、生产效率高; 能成型形状复杂、尺寸精确或带嵌件的制品; 能成型形状复杂、尺寸精确或带嵌件的制品; 成型塑料品种多; 成型塑料品种多; 易于实现自动化。 易于实现自动化。 因此广泛用于各种塑料制品的生产。其成型制 因此广泛用于各种塑料制品的生产。 品占目前全部塑料制品的20~ %。 %。注射成型是一 品占目前全部塑料制品的 ~30%。注射成型是一 种比较先进的成型工艺, 种比较先进的成型工艺,目前正继续向着高速化和 自动化方向发展。 自动化方向发展。
四、新型螺杆
塑料工艺
1、排气式螺杆 用于含水和易产生挥发组分的物料 、 排气原理:物料到排气段时已基本塑化, 排气原理:物料到排气段时已基本塑化,由于该段 螺槽突然加深,压力骤降,气体从熔体中逸处,从 螺槽突然加深,压力骤降,气体从熔体中逸处, 排气口排出。 排气口排出。
塑料工艺
2、分离型(屏障型)螺杆 、分离型(屏障型)
挤出成型
塑料工艺
挤出成型: 挤出成型: 挤出成型是借助螺杆的挤压作用, 挤出成型是借助螺杆的挤压作用,使塑化均匀 的塑料强行通过机头而成为具有恒定截面的 连续制品,如管、 薄膜、 连续制品,如管、板、丝、薄膜、电线电缆 等。挤出成型是塑料成型加工中重要方法之 一。
挤出成型制品举例
塑料工艺
塑料挤出成型工艺流程
• 原理: 原理: – 物料流经过销钉时,销钉将固体料或未彻底熔融的料 物料流经过销钉时, 分成许多细小料流, 分成许多细小料流,这些料流在两排销钉间较宽位置 又汇合,经过多次汇合分离,物料塑化质量得以提高。 又汇合,经过多次汇合分离,物料塑化质量得以提高。 • 销钉设置在熔融区,排列形状有人字形、环形等,销钉形 销钉设置在熔融区,排列形状有人字形、环形等, 状有圆柱形、菱形、方形等。 状有圆柱形、菱形、方形等。
塑料工艺
• 原理:在螺杆熔融段再附加一条螺纹,将原来一 原理:在螺杆熔融段再附加一条螺纹, 个螺纹所形成的螺槽分为两个, 个螺纹所形成的螺槽分为两个,将已熔物料和未 熔物料尽早分离,促进未熔料尽快熔融。 熔物料尽早分离,促进未熔料尽快熔融。
不同类型屏障型螺杆举例
塑料工艺
3、销钉型螺杆 、
塑料工艺
注射成型产品示例
塑料工艺
二、注射成型原理
塑料工艺
注射机的分类
塑料工艺
根据塑化方式不同分为: 根据塑化方式不同分为: 柱塞式注射机 螺杆式注射机
塑料工艺
塞式注射机特点: 柱塞式注射机特点: – 结构简单、但压力损失大、塑化不均匀以, 结构简单、但压力损失大、塑化不均匀以, 不适合热敏性塑料。 不适合热敏性塑料。 • 实际应用: 实际应用: – 目前工厂中广泛使用的是螺杆式注射机, 目前工厂中广泛使用的是螺杆式注射机, 60g以下的小型制件多用柱塞式。 以下的小型制件多用柱塞式。 以下的小型制件多用柱塞式
塑料工艺
双螺杆挤出机的结构
塑料工艺
(二)挤出机的工作过程
塑料工艺
普通单螺杆挤出机的工作过程
双螺杆挤出原理
塑料工艺
双螺杆挤出机的结构
双螺杆挤出的特点
塑料工艺
与单螺杆挤出机相比,双螺杆挤出机具有以下特点: 与单螺杆挤出机相比,双螺杆挤出机具有以下特点: 较高的固体输送能力和挤出产量; 1、较高的固体输送能力和挤出产量; 自洁能力; 2、自洁能力; 混合塑化能力高; 3、混合塑化能力高; 较低的塑化温度,减小分解可能; 4、较低的塑化温度,减小分解可能; 结构复杂,成本高。 5、结构复杂,成本高。
(三)螺杆的几种形式
塑料工艺
• 常用的是等距不等深螺杆
塑料工艺
二、熔体输送理论
塑料工艺
熔体有四种形式的流动 a. 正流: 正流: 正流(拖曳流 拖曳流)Qd(cm3/h)是物料沿螺槽向机头方向 正流 拖曳流 是物料沿螺槽向机头方向 的流动。它是由于螺杆转动, 的流动。它是由于螺杆转动,物料在螺杆根部与 机筒间形成相对运动而形成的流动。 机筒间形成相对运动而形成的流动。正流决定挤 出量大小. 出量大小 b.逆流: 逆流: 逆流 逆流(反流) : 相反的流动。 逆流(反流)Qp:与Qd相反的流动。由机头、 相反的流动 由机头、 多孔板等阻力元件对熔体的反压力造成, 多孔板等阻力元件对熔体的反压力造成,也叫压 力流,随机头压力的升高而增加。 力流,随机头压力的升高而增加。
塑料工艺
c. 环流: 环流: 横流(环流) :由分速度Vbx引起的在螺槽 横流(环流)Qt:由分速度 引起的在螺槽 内与正流垂直的流动。对总挤出量影响不大, 内与正流垂直的流动。对总挤出量影响不大, 可忽略不计,但对熔体的混合、塑化、 可忽略不计,但对熔体的混合、塑化、热交换 起重要作用。 起重要作用。 d. 漏流: 漏流: 漏流Ql: 漏流 :是物料由于机头阻力元件引起的反向 流动。 流动。漏流沿螺杆与料筒间隙向加料口方向流 可降低挤出量。正常情况Ql很小 很小, 动,可降低挤出量。正常情况 很小,为0.1~ ~ 0.6mm,当磨损严重时,Ql的急剧大。 的急剧大。 ,当磨损严重时, 的急剧大
塑料工艺
• 挤出过程: 挤出过程: 加料——在螺杆中熔融塑化 在螺杆中熔融塑化——机头口模挤出 机头口模挤出— 加料 在螺杆中熔融塑化 机头口模挤出 —定型 定型——冷却 冷却——牵引 牵引——切割 定型 冷却 牵引 切割
塑料工艺
• 挤出成型的特点: 挤出成型的特点: 连续化,效率高, ① 连续化,效率高,质量稳定 ② 应用范围广 设备简单,投资少, ③ 设备简单,投资少,见效快 生产环境卫生, ④ 生产环境卫生,劳动强度低 ⑤ 适于大批量生产
塑料工艺
2. 压力、温度和产量波动大 压力、 固体输送时又与螺杆旋转产生较高频率的 波动, 由于熔融过程的不稳定性产生低频波动, 波动, 由于熔融过程的不稳定性产生低频波动, 温控系统的稳定性差或环境因素的变化引起的 波动。 波动。 3. 混合效果差 不能很好适应一些特殊塑料的加工或混炼、 不能很好适应一些特殊塑料的加工或混炼、 着色工艺过程。 着色工艺过程。