钢材性能柔性化与柔性轧制技术
轧钢生产中应用的新技术新工艺
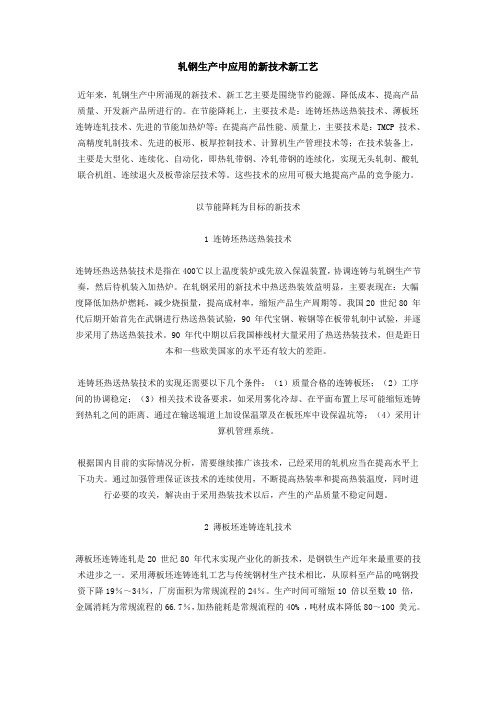
轧钢生产中应用的新技术新工艺近年来,轧钢生产中所涌现的新技术、新工艺主要是围绕节约能源、降低成本、提高产品质量、开发新产品所进行的。
在节能降耗上,主要技术是:连铸坯热送热装技术、薄板坯连铸连轧技术、先进的节能加热炉等;在提高产品性能、质量上,主要技术是:TMCP 技术、高精度轧制技术、先进的板形、板厚控制技术、计算机生产管理技术等;在技术装备上,主要是大型化、连续化、自动化,即热轧带钢、冷轧带钢的连续化,实现无头轧制、酸轧联合机组、连续退火及板带涂层技术等。
这些技术的应用可极大地提高产品的竞争能力。
以节能降耗为目标的新技术1 连铸坯热送热装技术连铸坯热送热装技术是指在400℃以上温度装炉或先放入保温装置,协调连铸与轧钢生产节奏,然后待机装入加热炉。
在轧钢采用的新技术中热送热装效益明显,主要表现在:大幅度降低加热炉燃耗,减少烧损量,提高成材率,缩短产品生产周期等。
我国20 世纪80 年代后期开始首先在武钢进行热送热装试验,90 年代宝钢、鞍钢等在板带轧制中试验,并逐步采用了热送热装技术。
90 年代中期以后我国棒线材大量采用了热送热装技术,但是距日本和一些欧美国家的水平还有较大的差距。
连铸坯热送热装技术的实现还需要以下几个条件:(1)质量合格的连铸板坯;(2)工序间的协调稳定;(3)相关技术设备要求,如采用雾化冷却、在平面布置上尽可能缩短连铸到热轧之间的距离、通过在输送辊道上加设保温罩及在板坯库中设保温坑等;(4)采用计算机管理系统。
根据国内目前的实际情况分析,需要继续推广该技术,己经采用的轧机应当在提高水平上下功夫。
通过加强管理保证该技术的连续使用,不断提高热装率和提高热装温度,同时进行必要的攻关,解决由于采用热装技术以后,产生的产品质量不稳定问题。
2 薄板坯连铸连轧技术薄板坯连铸连轧是20 世纪80 年代末实现产业化的新技术,是钢铁生产近年来最重要的技术进步之一。
采用薄板坯连铸连轧工艺与传统钢材生产技术相比,从原料至产品的吨钢投资下降19%~34%,厂房面积为常规流程的24%。
轧型钢工艺技术

轧型钢工艺技术轧型钢是一种常用的建筑和工程材料,具有强度高、耐腐蚀等特点,被广泛应用于建筑结构、桥梁、车辆制造等领域。
而轧型钢的生产过程则是一个涉及多个工艺环节的复杂过程,我们以下将简要介绍轧型钢的工艺技术。
首先,轧钢是以熔铁而非铁鉱石或铁砂为原材料的。
冶金工艺的基础就是先将生铁中的杂质和过多的碳除掉,对含碳量过高的生铁精炼,得到合适的含碳量的铁水供轧制。
而生铁的融化和熔炼过程中,需要通过高炉等设备,进行喷煤、喷焦、熔炼等操作,最后出铁。
然后,从高炉出铁的生铁通过熔炼后进一步的加工,最终形成钢坯。
钢坯是轧制钢铁产品的初级产品,其形状和尺寸不合乎标准,需要经过一系列加工来获得最终的钢材产品。
其中主要的加工过程包括均热处理、热轧、冷轧等环节。
均热处理是指对钢坯进行恒温保温处理,以消除和减轻内应力,改变晶粒的结构,使钢材获得较好的物化性能。
然后进入热轧环节,热轧是指在高温下将钢坯进行轧制成型的过程。
这个过程中需要通过辊道送入的钢坯在高温下进行塑性变形,根据不同的产品形状和规格要求,通过不同的轧制方式和加工设备来完成。
最后,冷轧是指将经过热轧后的钢材进行冷轧加工处理的过程。
冷轧可以使钢材尺寸和表面质量得到进一步的改善,并增加钢材的强度和韧性。
冷轧还可以通过控制厚度和宽度的方法,制造出不同规格和尺寸的轧型钢产品。
在整个轧型钢的生产过程中,需要涉及到多个工艺技术,例如高炉冶炼、热轧、冷轧、加热、锻造等。
同时,为了确保产品质量,在每个环节中都需要进行严格的质量控制和检测。
例如,在热轧过程中,需要对温度、卷取力、卷厚等参数进行实时监测和调整。
而在冷轧环节中,则需要对冷轧力、冷轧间隙、冷轧温度等进行控制。
总之,轧型钢工艺技术是一个综合性的工艺体系,涉及到多个环节和参数的控制,旨在通过一系列的处理和加工过程,获得满足工程和建筑需求的高质量钢材产品。
随着科技和制造技术的不断进步,轧型钢工艺技术也会不断发展和创新,以满足不同应用领域的需求。
冷轧板超快速退火的组织织构的柔性化控制技术

冷轧板超迅速退火旳组织、织构旳柔性化控制技术微观组织控制:对老式旳冷轧汽车用钢而言,伴随汽车减重、节省燃油和保障安全旳迫切规定,采用减量化成分和紧凑型流程,在保证成形性能旳基础上深入提高材料强度,已经成为新世纪旳研究热点。
高强度深冲用钢(包括IF钢和Al镇静钢等)大多通过添加Mn、P和Si等元素到达固溶强化旳目旳。
这种钢在固溶强化母相旳同步引起晶界强度旳下降,恶化了固有旳晶界脆性问题(IF钢),导致更明显旳二次加工脆性;此外,固溶强化元素Si等旳添加损害深冲性能和涂层旳表面质量,不合用于复杂成形旳外板零件。
晶粒细化是可以同步提高材料强度和韧性旳最有效措施之一。
通过细化晶粒,提高晶界数量和密度,进而Q345B无缝管 bd提高(超)低碳钢旳晶界强度,同步大幅度改善二次加工脆性。
日本某钢铁企业通过大幅提高C 和Nb旳含量,运用细晶强化、NbC析出强化和PFZ无间隙析出区间技术,开发了一种440MPa级别旳细晶高强IF钢,明显提高了试验钢旳抗二次加工脆性。
实际上,除了微合金化手段以外,通过工艺控制同样可以实现晶粒细化。
近十年来这一技术在热轧领域进行了深入旳研究和应用。
总旳来说,重要有两组获得超细晶钢旳技术路线。
一组是剧烈塑性变形措施,如等通道角挤压、叠轧合技术、多向变形和高压扭转等;另一组则包括多种先进旳形变热处理技术,如形变诱导铁素体相变、动态再结晶、两相区轧制以及铁素体区温轧等。
目前商业用热轧高强钢旳最小晶粒尺寸在3-5μm,而冷轧退火钢一般在20μm左右。
众所周知,热轧组织参数、冷轧规程和退火工艺旳控制可强烈地影响冷轧产品旳组织和性能,但目前主流旳商业化退火措施,无论是老式旳罩式退火还是较先进旳持续退火,工艺参数单一,可变化范围窄,难以实现对组织性能旳柔性化控制。
这正是数年来制约冷轧-退火材料组织细化旳重要瓶颈,也是冷轧细晶化技术鲜有研究旳重要原因。
为了克服上述问题,RAL研究人员发现,超迅速退火技术因其独特旳加热及冷却方式,Q345B无缝管可实现多阶段复杂途径和灵活多样旳工艺参数控制,有望为冷轧-退火产品提供了更具全新旳组织-织构-性能处理方案。
汽车高强度钢材技术的发展
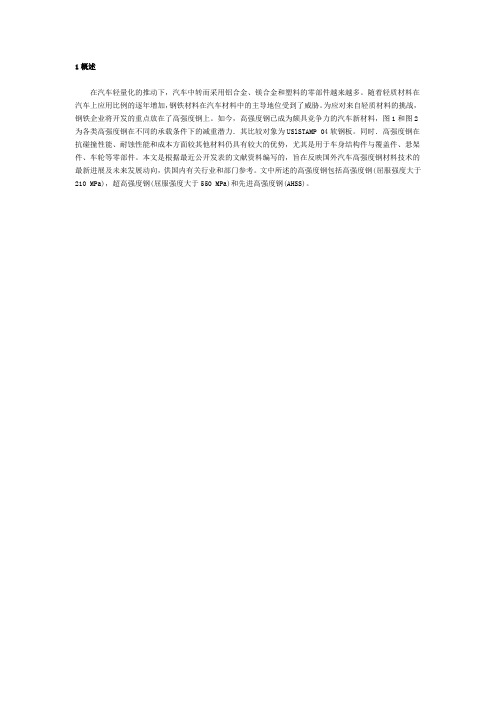
1概述在汽车轻量化的推动下,汽车中转而采用铝合金、镁合金和塑料的零部件越来越多。
随着轻质材料在汽车上应用比例的逐年增加,钢铁材料在汽车材料中的主导地位受到了威胁。
为应对来自轻质材料的挑战,钢铁企业将开发的重点放在了高强度钢上。
如今,高强度钢已成为颇具竞争力的汽车新材料,图1和图2为各类高强度钢在不同的承载条件下的减重潜力.其比较对象为USlSTAMP 04软钢板。
同时.高强度钢在抗碰撞性能、耐蚀性能和成本方面较其他材料仍具有较大的优势,尤其是用于车身结构件与覆盖件、悬架件、车轮等零部件。
本文是根据最近公开发表的文献资料编写的,旨在反映国外汽车高强度钢材料技术的最新进展及未来发展动向,供国内有关行业和部门参考。
文中所述的高强度钢包括高强度钢(屈服强度大于210 MPa),超高强度钢(屈服强度大于550 MPa)和先进高强度钢(AHSS)。
2主要技术进展超轻车身(ULSAB)、超轻覆盖件(ULSAC)、超轻悬架系统(ULSAS)和新概念超轻车身(ULSAB-AVC)等项目的成功实施,验证了高强度钢在减轻汽车自重和改善车辆性能中的有效性。
为了将这些项目所取得的技术成果转化为现实的生产力,近期的高强度钢技术研究,主要集中在支撑技术(Enabling Technologies)上。
2.1若干高强度钢的开发当前正处于新一代高强度钢开发的前夜。
从冶金学的角度看,近几年高强度钢材料的开发,大多只是对原有钢种牌号的补充或性能改善,厚度进一步减薄,材料本身并未取得突破性进展。
开发的难点是要针对不同的零件,力求在产品的强度、塑性和成本之间取得平衡。
SFGHITEN、NANOHITEN、ERW和HISTORY是日本JFE公司最近开发出的几种高强度钢。
其中SFGHITEN为含Nb系列高强度IF钢板,主要应用对象是汽车车身外板,研究用钢的化学成分见表1。
SFGHITEN利用析出的Nb(C,N)微粒和细化晶粒得到强化,其独特之处在于晶界附近存在所谓“无沉淀区”,它降低了材料的屈服强度。
钢铁行业如何实现生产线柔性化
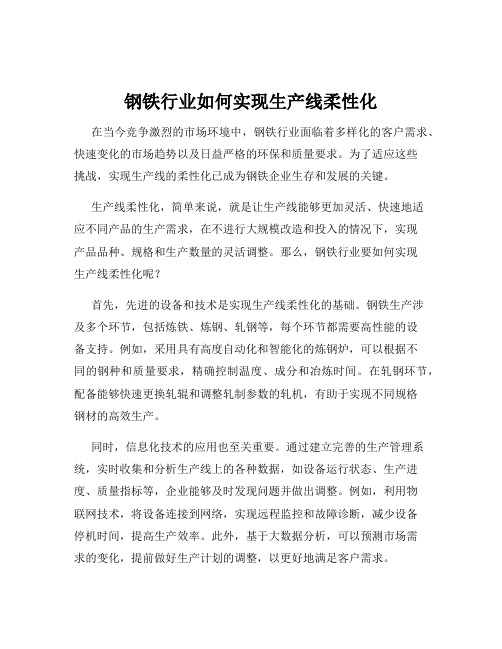
钢铁行业如何实现生产线柔性化在当今竞争激烈的市场环境中,钢铁行业面临着多样化的客户需求、快速变化的市场趋势以及日益严格的环保和质量要求。
为了适应这些挑战,实现生产线的柔性化已成为钢铁企业生存和发展的关键。
生产线柔性化,简单来说,就是让生产线能够更加灵活、快速地适应不同产品的生产需求,在不进行大规模改造和投入的情况下,实现产品品种、规格和生产数量的灵活调整。
那么,钢铁行业要如何实现生产线柔性化呢?首先,先进的设备和技术是实现生产线柔性化的基础。
钢铁生产涉及多个环节,包括炼铁、炼钢、轧钢等,每个环节都需要高性能的设备支持。
例如,采用具有高度自动化和智能化的炼钢炉,可以根据不同的钢种和质量要求,精确控制温度、成分和冶炼时间。
在轧钢环节,配备能够快速更换轧辊和调整轧制参数的轧机,有助于实现不同规格钢材的高效生产。
同时,信息化技术的应用也至关重要。
通过建立完善的生产管理系统,实时收集和分析生产线上的各种数据,如设备运行状态、生产进度、质量指标等,企业能够及时发现问题并做出调整。
例如,利用物联网技术,将设备连接到网络,实现远程监控和故障诊断,减少设备停机时间,提高生产效率。
此外,基于大数据分析,可以预测市场需求的变化,提前做好生产计划的调整,以更好地满足客户需求。
优化生产流程是实现生产线柔性化的重要手段。
传统的钢铁生产流程往往较为固定和僵化,导致生产切换时间长、成本高。
通过对生产流程进行重新设计和优化,可以减少不必要的中间环节,提高生产的连贯性和灵活性。
比如,采用连续铸轧工艺,将炼钢和轧钢过程直接连接起来,减少了钢坯的冷却和再加热过程,不仅节约了能源,还提高了生产效率和产品质量。
另外,培养高素质的员工队伍也是必不可少的。
员工是生产线的直接操作者和管理者,他们的技能水平和应变能力直接影响到生产线的柔性化程度。
企业应加强员工培训,提高他们的操作技能和问题解决能力,使他们能够熟练掌握先进设备和技术的应用,快速适应生产线上的各种变化。
我国轧制技术新进展

总院正在结合首钢、 迁钢和京唐钢铁厂的热轧带 钢生产 线 进 行 组 织 性 能 预 报 技 术 应 用 研 究 。另
柔性轧制技术是通过设计合理的成分和采用 控轧控冷的技术 , 实现“ 一钢多能” 的 目的。目前 该技术 已在邯钢和梅钢得到成熟应用 , 针对钢铁 制品订单的多品种化和小批量生产化 , 有效的提 高了生产效率 , 缩短交货周期 、 降低生产成本。近 年来 , 柔性轧制技术在钢铁轧制工艺领 域中发展
4 0・
要, 轧钢装备现代化和国产化工作取得重大突破 , 各项轧钢生产技术经济指标进一步提高 , 轧钢核
心技术 自主创新 出现 了可喜进展 。特别是在无
头、 半 无 头轧制 技术 , 柔性化 轧制 生产与 超快冷技 术, 在 线 与离线 热处 理生 产技术 , 钢材组 织性 能在
线预报与控制技术上 , 我国取得了较大发展 , 部分
的冲击 , 本系统中借助于 P L C实现开 1 3 机速度的 S曲线 变化 。使 用 S曲线 可 以让 开 口机 在 加 、 减
速过程中速度变化平滑, s曲线设计如图4 所示。
能完善 , 运行安全可靠。 b . S曲线速度给定使用电液比例阀能够控制 开 口机平滑运行 , 减少机械冲击 , 大大提高操作人 员的简易性 。触摸屏上显示 了开 口机位置 , 速度 ( 给定速度、 实际速度 ) 、 系统状态等, 方便操作人 员操 作和 观察 。
2 任占海 .冶金液压 设备 及其维轧制 技术 新进 展
近几 年 , 我 国轧 钢生产 技术取 得 了较 大进步 ,
很快 , 使 轧钢 生产具有很 大 的灵活性 。
钢材 品种 结构 调整基 本满 足 了国民经济 发展 的需
轧钢生产中的新技术应用分析

轧钢生产中的新技术应用分析发表时间:2020-12-16T03:13:47.729Z 来源:《防护工程》2020年25期作者:雷志升[导读] 在未来的世界发展中,钢铁材料具有十分重要的地位,没有那种材料能够替代,可以充分的发现其应用的重要性。
而对于轧钢生产工作而言,在生产工艺方面依然存在着滞后的现象。
因此,必须要不断的在轧钢生产期间选取更新的工艺与技术,从而提升我国目前的轧钢生产现状,促使轧钢生产工艺能够将产品的市场竞争力提升,在国际中始终立足于不败的地位。
基于此,本篇文章对轧钢生产中的新技术应用进行分析,以供参考。
雷志升西宁特殊钢股份有限公司青海西宁 810005摘要:在未来的世界发展中,钢铁材料具有十分重要的地位,没有那种材料能够替代,可以充分的发现其应用的重要性。
而对于轧钢生产工作而言,在生产工艺方面依然存在着滞后的现象。
因此,必须要不断的在轧钢生产期间选取更新的工艺与技术,从而提升我国目前的轧钢生产现状,促使轧钢生产工艺能够将产品的市场竞争力提升,在国际中始终立足于不败的地位。
基于此,本篇文章对轧钢生产中的新技术应用进行分析,以供参考。
关键词:轧钢生产;新技术;应用策略引言我国是世界上钢铁产量最大的国家,我国每年钢铁的产量超过了100000余万t,但是和一些发达国家的轧钢技术相比,我国的轧钢技术水平仍然处在比较落后的阶段,对于一些特殊类型的钢材,仍然没有生产出来,需要从国外进口,而这种现象和我国钢材生产大国的称号是不符的,所以应该以科学技术为基础,对轧钢生产工艺和技术进行不断的创新,研发新工艺新技术,从而提升轧钢生产效率,保证轧钢产生质量。
1轧钢工艺技术的发展情况近些年,我国轧钢生产工艺和技术的研发、改造主要是针对轧制控冷新装备和高质量、高性能新产品为主,其中比较突出的是新轧制技术包括6种。
1)半无头轧制技术。
2)超薄规格轧制技术,主要是以热代冷来实现的。
3)长尺钢轨轧制、在线处理生产线技术,可以实现喷风强制冷却轧后高温钢轨。
轧制工艺2
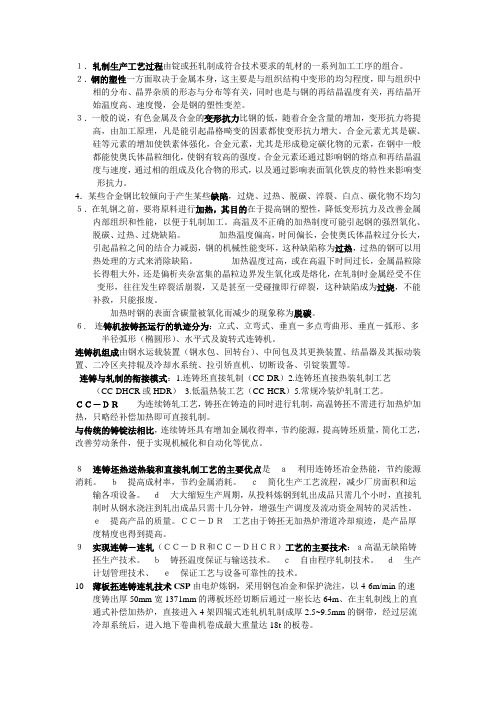
1.轧制生产工艺过程由锭或抷轧制成符合技术要求的轧材的一系列加工工序的组合。
2.钢的塑性一方面取决于金属本身,这主要是与组织结构中变形的均匀程度,即与组织中相的分布、晶界杂质的形态与分布等有关,同时也是与钢的再结晶温度有关,再结晶开始温度高、速度慢,会是钢的塑性变差。
3.一般的说,有色金属及合金的变形抗力比钢的低,随着合金含量的增加,变形抗力将提高,由加工原理,凡是能引起晶格畸变的因素都使变形抗力增大。
合金元素尤其是碳、硅等元素的增加使铁素体强化,合金元素,尤其是形成稳定碳化物的元素,在钢中一般都能使奥氏体晶粒细化,使钢有较高的强度。
合金元素还通过影响钢的熔点和再结晶温度与速度,通过相的组成及化合物的形式,以及通过影响表面氧化铁皮的特性来影响变形抗力。
4.某些合金钢比较倾向于产生某些缺陷,过烧、过热、脱碳、淬裂、白点、碳化物不均匀5.在轧钢之前,要将原料进行加热,其目的在于提高钢的塑性,降低变形抗力及改善金属内部组织和性能,以便于轧制加工。
高温及不正确的加热制度可能引起钢的强烈氧化、脱碳、过热、过烧缺陷。
加热温度偏高,时间偏长,会使奥氏体晶粒过分长大,引起晶粒之间的结合力减弱,钢的机械性能变坏,这种缺陷称为过热,过热的钢可以用热处理的方式来消除缺陷。
加热温度过高,或在高温下时间过长,金属晶粒除长得粗大外,还是偏析夹杂富集的晶粒边界发生氧化或是熔化,在轧制时金属经受不住变形,往往发生碎裂活崩裂,又是甚至一受碰撞即行碎裂,这种缺陷成为过烧,不能补救,只能报废。
加热时钢的表面含碳量被氧化而减少的现象称为脱碳。
6.连铸机按铸抷运行的轨迹分为:立式、立弯式、垂直-多点弯曲形、垂直-弧形、多半径弧形(椭圆形)、水平式及旋转式连铸机。
连铸机组成由钢水运载装置(钢水包、回转台)、中间包及其更换装置、结晶器及其振动装置、二冷区夹持辊及冷却水系统、拉引矫直机、切断设备、引锭装置等。
连铸与轧制的衔接模式:1.连铸坯直接轧制(CC-DR)2.连铸坯直接热装轧制工艺(CC-DHCR或HDR)3.低温热装工艺(CC-HCR)5.常规冷装炉轧制工艺。
轧钢生产中新工艺新技术的应用

轧钢生产中新工艺新技术的应用摘要:改革开放后,我国的经济得到突飞猛进的发展。
而钢铁工业,在国家的发展中起到了至关重要的作用。
钢的用途非常广泛,尤其是轧钢技术,它在机械生产和设备制造中起到了举足轻重的作用。
基于此,本文以轧钢生产为例,阐述其生产过程中应用新工艺、新技术对我国钢铁行业的重要价值体现,仅供参考。
关键词:轧钢生产;新工艺;新技术;应用分析引言:近几年,钢铁制品的需求不断增长。
在此背景下,我国钢铁工业的发展日益受到重视。
传统的生产工艺和技术已不能适应当前钢铁生产水平和性能的要求。
而新工艺、新技术的涌现,可以很好地弥补这一缺陷。
因此,对各种新工艺、新技术的运用进行分析是十分必要的。
一、节能工艺及技术(一)薄板坯连铸连轧薄板坯连铸连轧是一种典型的新型工艺,在生产高强度钢、超低碳深冲钢、高标号管线钢等领域都有广泛应用。
从该新技术的使用效果来看,采用薄板坯连铸连轧技术在轧钢生产中具有很好的节能效果。
薄板坯连铸连轧技术包括 ISP、CSP等几个常见的工艺类型。
在这些项目中, ISP最初是在意大利某公司建立和投入使用的。
本工艺主要是利用直弧型铸机、平移式二辊轧机等设备来完成。
ISP生产线长度大约180米,采用这种工艺生产的效率大约为30分钟(钢液到卷筒)。
CSP主要是用来制造超低碳钢,碳钢,0.8 mm以下。
(二)高温低氧燃烧在钢铁锻造炉的生产中,常规的生产方法有以下缺点:燃烧时会引起高温(600~700℃),但有关规定的排烟温度应<150℃,说明此工艺存在热量损耗问题。
高温低氧燃烧技术是以降低热耗为目的而发展起来的一项新技术。
该技术的节能机理是:采用喷射方式将燃油与高温、低氧的助燃剂混在一起,促进两者的充分混合。
在燃烧过程中,由于高温、低氧等助燃剂的作用,可以使燃油达到蓄热燃耗,从而使烟气的排放温度下降。
与传统的制程技术相比,本发明具有以下优点:一是节约能源。
在燃烧时,采用高温、低氧的助燃剂,可以使烟道中的余热得到充分的回收,从而降低了热能的损耗。
钢材的轧制工艺及质量控制
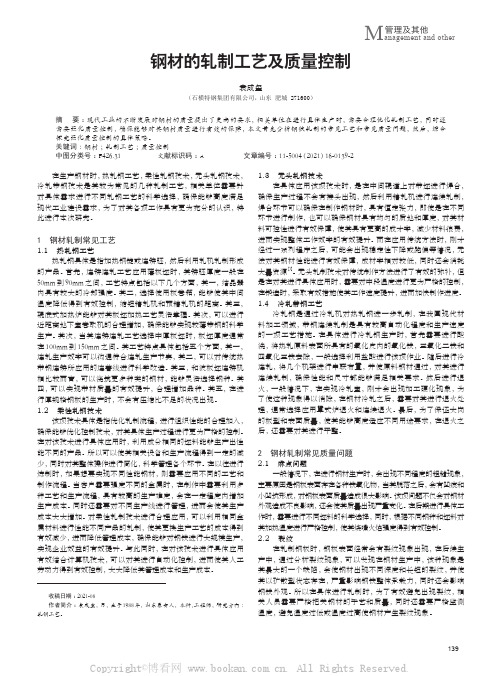
管理及其他M anagement and other在生产钢材时,热轧钢工艺,柔性轧钢技术,无头轧钢技术,冷轧带钢技术是其较为常见的几种轧制工艺,相关单位需要针对具体需求进行不同轧钢工艺的科学选择,确保能够高度满足现代工业建设需求,为了对其各项工作具有更为充分的认识,特此进行本次研究。
1 钢材轧制常见工艺1.1 热轧钢工艺热轧钢具体是指加热钢锭或连铸胚,然后利用轧机轧制形成的产品。
首先,连铸连轧工艺应用薄板坯时,其铸胚厚度一般在50mm到90mm之间,工艺特点包括以下几个方面,其一,结晶器内具有较大的冷却强度。
其二,选择使用板卷箱,能够使其中间温度降低得到有效控制,缩短精轧机和预精轧机的距离。
其三,辊底式加热炉能够对其板坯加热工艺灵活掌握。
其次,可以进行近距离地下室卷取机的合理增加,确保能够实现较薄带钢的科学生产。
其次,当其连铸连轧工艺选择中厚板坯时,板坯厚度通常在100mm到150mm之间。
其工艺特点具体包括五个方面,其一,连轧生产效率可以沟通符合连轧生产节奏,其二,可以对传统热带钢连铸所应用的连着线进行科学改造。
其三,和波板坯连铸机相比较而言,可以浇筑更多种类的钢材,能够灵活选择钢种。
其四,可以实现带材质量的有效提升,合理增加品种。
其五,在进行厚规格钢板的生产时,不会有压缩比不足的状况出现。
1.2 柔性轧钢技术该项技术具体是指优化轧制流程,进行组织性能的合理加入,确保能够优化控制技术,对其具体生产过程进行更为严格的控制。
在对该技术进行具体应用时,利用成分相同的坯料能够生产出性能不同的产品。
所以可以使其相关设备和生产流程得到一定的减少,同时对其整体操作进行简化,科学管理各个环节。
在以往进行炼制时,如果想要实现不同性能钢材,则需要应用不同的工艺和制作流程。
当客户需要强度不同的金属时,在制作中需要利用多种工艺和生产流程,具有较高的生产难度,会在一定程度内增加生产成本。
同时还需要对不同生产线进行管理,进而会使其生产成本大大增加。
材料成型工艺学复习题汇总

1.咬入:依靠回转的轧辊和轧件之间的摩擦力,轧辊将轧件拖入轧辊之间的现象. 改善咬入条件的途径:①降低a: (1)增加轧辊直径D,(2)降低压下量实际生产:(1)小头进钢,(2)强迫咬入; ②提高:(1)改变轧件或轧辊的表面状态,以提高摩擦角;(2)清除炉生氧化铁皮;(3)合理的调节轧制速度,低速咬入,高速轧制.2.宽展:高向压缩下来的金属沿着横向移动引起的轧件宽度的变化成为宽展.3.宽展分类: ①自由宽展: 在横向变形过程中,除受接触摩擦影响外,不受任何其它任何阻碍和限制。
②限制宽展: 在横向变形过程中,除受接触摩擦影响外,还受到孔型侧壁的阻碍作用,破坏了自由流动条件,此时宽展称为限制宽展。
③强迫宽展: 在横向变形过程中,质点横向移动时,不仅不受任何阻碍,还受到强烈的推动作用,使轧件宽展产生附加增长,此时的宽展称为强迫宽展。
4.影响宽展的因素:实质因素:高向移动体积和变形区内轧件变形纵横阻力比;基本因素:变形区形状和轧辊形状。
工艺因素:①相对压下量:相对压下量越大,宽展越大。
②轧制道次:道次越多,宽展越小;单道次较大,宽展大,多道次较小,宽展小;③轧辊直径:轧辊直径增加,宽展增加;摩擦系数;④摩擦系数的增加,宽展增加(轧制温度、轧制速度、轧辊材质和表面状态,轧件的化学成分). ⑤轧件宽度的影响:假设变形区长度 l 一定:随轧件宽度增加,宽展先增加后逐渐减小,最后趋于不变。
5.前滑:轧件出口速度vh 大于轧辊在该处的线速度v,即vh>v的现象称为前滑现象。
后滑:轧件进入轧辊的速度小于轧辊该处线速度的水平分量v的现象。
前滑值:轧件出口速度vh与对应点的轧辊圆周速度的线速度之差与轧辊圆周速度的线速度之比值称为前滑值。
后滑值:后滑值是指轧件入口断面轧件的速度与轧辊在该点处圆周速度的水平分量之差同轧辊圆周速度水平分量的比值。
6.影响前滑的因素: ①压下率:前滑随压下率的增加而增加;②轧件厚度:轧后轧件厚度h减小,前滑增加;③轧件宽度:轧件宽度小于40mm时,随宽度增加前滑亦增加;但轧件宽度大于40mm时,宽度再增加时,其前滑值则为一定值;④轧辊直径:前滑值随辊径增加而增加;⑤摩擦系数:摩擦系数f越大,其前滑值越大;⑥张力:前张力增加前滑,后张力减小前滑 .7.轧制生产工艺:由锭或坯轧制成符合技术要求的轧件的一系列加工工序组合。
轧制工艺技术

轧制工艺技术轧制工艺技术,是指通过机械力将金属坯料进行连续轧制、变形和压制,使其从粗糙的坯料变成平整、有形状的金属条、板、管等材料的过程。
轧制工艺技术是金属加工中常用的一种工艺方法,广泛应用于冶金、机械制造、船舶、汽车等领域。
轧制工艺技术主要包括轧制方法、轧制设备和工艺参数三个方面。
轧制方法主要有热轧和冷轧两种。
热轧是将金属加热到一定温度后进行轧制,适用于低碳钢、合金钢等材料的加工。
热轧工艺具有高产量、易控制等优点,但也会引起材料强度下降、变形度不定等缺点。
冷轧是将金属在室温下进行轧制,适用于不锈钢、铝合金等材料的加工。
冷轧工艺具有制品质量好、表面光洁等优点,但也会引起轧制力大、设备损坏等缺点。
轧制设备主要包括轧机和辅助设备。
轧机是轧制过程中最重要的设备之一,它主要由辊子、辊架、传动装置等组成。
根据轧机的结构和原理的不同,可以分为压下式轧机、抓下式轧机和压痕式轧机三种。
辅助设备主要包括卷板机、脱碳炉、退火炉等,它们的作用是为轧机提供原料和对轧制过程进行辅助处理。
工艺参数是指在轧制过程中需要控制的各项参数。
工艺参数的选择直接影响到轧制产品的质量和性能。
常见的工艺参数有轧制温度、轧制力、轧制速度等。
轧制温度是指轧制过程中金属的温度,不同的材料对轧制温度有不同的要求,过高或过低的温度都会影响到轧制产品的质量。
轧制力是指轧制时作用在轧辊上的力,它的大小直接影响到轧制产品的变形度和机械性能。
轧制速度是指轧制辊的线速度,不同的产品对轧制速度有不同的要求,过快或过慢的速度都会影响到轧制产品的表面质量。
轧制工艺技术的应用可以使金属材料获得更好的性能和表面质量,有助于提高产品的竞争力和降低成本。
同时,轧制工艺技术也对轧制设备和工艺参数的要求提出了挑战。
为了更好地应对这些挑战,需要不断改进和创新轧制工艺技术,提高轧制产品的质量和生产效率。
轧制、钢材、热处理

轧制rolling定义:金属(或非金属)材料在旋转轧辊的压力作用下,产生连续塑性变形,获得要求的截面形状并改变其性能的方法。
应用学科:机械工程(一级学科);锻压(二级学科);轧制、拉拔、挤压、镦锻(三级学科)本内容由全国科学技术名词审定委员会审定公布目录编辑本段轧制方向上,从而使钢材在一定程度上不再是各向同性体;浇注时形成的气泡、裂纹和疏松,也可在高温和压力作用下被焊合。
缺点:1.经过热轧之后,钢材内部的非金属夹杂物(主要是硫化物和氧化物,还有硅酸盐)被压成薄片,热轧后的薄板出现分层(夹层)现象。
分层使钢材沿厚度方向受拉的性能大大恶化,并且有可能在焊缝收缩时出现层间撕裂。
焊缝收缩诱发的局部应变时常达到屈服点应变的数倍,比荷载引起的应变大得多; 2.不均匀冷却造成的残余应力。
残余应力是在没有外力作用下内部自相平衡的应力,各种截面的热轧型钢都有这类残余应力,一般型钢截面尺寸越大,残余应力也越大。
残余应力虽然是自相平衡的,但对钢构件在外力作用下的性能还是有一定影响。
如对变形、稳定性、抗疲劳等方面都可能产生不利的作用。
3.热轧的钢材产品,对于厚度和边宽这方面不好控制。
我们熟知热胀冷缩,由于开始的时候热轧出来即使是长度、厚度都达标,最后冷却后还是会出现一定的负差,这种负差边宽越宽,厚度越厚表现的越明显。
所以对于大号的钢材,对于钢材的边宽、厚度、长度,角度,以及边线都没法要求太精确。
冷轧用热轧钢卷为原料,经酸洗去除氧化皮后进行冷连轧,其成品为轧硬卷,由于连续冷变形引起的冷作硬化使轧硬卷的强度、硬度上升、韧塑指标下降,因此冲压性能将恶化,只能用于简单变形的零件。
轧硬卷可作冷轧机器系统为热镀锌厂的原料,因为热镀锌机组均设置有退火线。
轧硬卷重一般在20-40吨,钢卷在常温下,对热轧酸洗卷进行连续轧制。
内径为610mm。
编辑本段产品特点因为没有经过退火处理,其硬度很高(HRB大于90),机械加工性能极差,只能进行简单的有方向性的小于90度的折弯加工(垂直于卷取方向)。
《棒线材轧制的发展方向》课件

2023/12/18
3
连铸坯热装热送或直接轧制
2023/12/18
直接轧制定义:连铸坯不经过再加热而直接 送至成品轧机轧制成材的一种方法;
直接轧制可省掉钢坯冷却和清理仓库存放及 中间加热工序;
前提保证无缺陷钢坯,在线检查和在线清理; 保证轧制温度。
4
柔性轧制技术
对于小批量、多品种的生产,改变规格和品 种时,轧机停机时间增加。
研究表明,在棒线材的轧 制中,2道次低温轧制的面 缩率应控制在24%~31%, 4道次低温轧制的面缩率应 控制在46%~57%。在更 多道次中采用大变形量的 低温轧制,会导致晶粒尺 寸的不均匀。
2023/12/18
低温精轧工艺的温度范围
14
低温轧制的优缺点
减少加热能耗; 减少氧化烧损; 提高轧钢加热炉的加热产量; 延长加热炉的寿命; 减少轧辊的热应力疲劳裂纹以及氧化皮引起的磨损; 降低脱碳层深度; 提高产品的表面质量; 细化晶粒; 改善产品性能。 缺点: 加大了轧材的变形抗力,从而加大了轧制力和轧制功率; 降低了轧制时轧材的塑性,从而影响轧材的咬入。
利用超快速冷却技术,进行TMCP和冷却路径控制,可明显提高线材强度,提高钢材产品利 用率,有十分广阔的应用前景。
利用了线材轧机连续大变形的特点,通过轧后的快速冷却过程抑制线材的再结晶,最后通 过相变过程的控制实现线材的细晶化。
2023/12/18
27
盐浴控冷工艺
线材的在线熔融盐浴直接韧化处理(简称DLP)是新日铁最先开 发的工艺,应用品种主要是桥梁缆索用线材、高级弹簧钢线材、 特殊用途钢丝绳用线材等高档线材。
在生产中采用的方法是低温轧制 实际效果并不好: 1)轧制不方便, 2)质量不稳定
2023/12/18
轧制工艺技术论文

轧制工艺技术论文轧制工艺技术是指利用轧机对金属材料进行加工的一种方法。
轧制工艺技术广泛应用于金属材料的生产加工过程中,对材料的形状和性能进行改善和调整。
本文将介绍轧制工艺技术的概念、工艺过程和应用。
轧制工艺技术是将金属材料通过轧机进行压制和塑性变形的过程,以达到调整材料形状和属性的目的。
轧制工艺技术可以分为热轧和冷轧两种。
热轧是将金属材料加热到高温后,通过轧机进行塑性变形,通常用于大型和厚度较大的材料。
冷轧则是在室温下对金属材料进行加工,通常用于薄板和线材等小型材料。
通过轧制工艺技术,可以调整金属材料的厚度、宽度、长度和形状等尺寸参数,同时还可以提高材料的强度、硬度和耐腐蚀性能。
在轧制工艺技术的过程中,一般分为准备工作、预热工作、轧制工作和后处理工作。
准备工作包括对轧机和材料的准备,确保设备处于良好的运行状态,并调整合适的轧制工艺参数。
预热工作是将金属材料加热到一定温度,以提高材料的塑性,减小轧制压力和能量消耗。
轧制工作是将预热后的金属材料通过轧机进行压制和变形,以获得所需的形状和尺寸。
后处理工作是对轧制后的材料进行调质、修边或其他加工工艺,以达到所需的产品要求。
轧制工艺技术在金属材料的生产加工中有着广泛的应用。
在钢铁行业中,轧制工艺技术被广泛应用于钢材的生产中,如热轧板材、冷轧薄板和热轧带钢等产品的生产。
轧制工艺技术还被应用于铝、铜、锌等有色金属的加工过程中,如冷轧铝箔和轧制铜线等产品的生产。
此外,轧制工艺技术还可以用于金属材料的形状和性能调整,如轧制带钢的拉伸、轧制铝合金板材的固溶处理等。
总之,轧制工艺技术是一种常用的金属材料加工方法,通过对金属材料进行压制和塑性变形,可以调整材料的形状和性能。
轧制工艺技术广泛应用于金属材料的生产加工中,对于提高产品质量和生产效率具有重要意义。
未来,随着科技的发展和工艺技术的改进,轧制工艺技术将会继续推动金属材料加工工业的发展。
轧制工艺技术要求

轧制工艺技术要求轧制是一种重要的金属加工方法,通过不同类型的轧机对金属材料进行压制和变形,从而得到所需形状和尺寸的产品。
然而,轧制过程中存在着一些技术要求,以确保产品的质量和工艺的稳定性。
以下是对轧制工艺技术要求的一些主要内容。
首先,轧制过程中需要控制适当的轧制温度。
温度是影响金属材料的塑性和形变行为的重要因素,过高或过低的温度都会对轧制过程产生不良影响。
因此,在轧制过程中,需通过预热或冷却等方式控制金属材料的温度,以保证其塑性适中,便于变形和成形。
其次,轧制过程中需要控制适当的轧制压力。
压力是实现金属材料变形和破碎的驱动力,过大或过小的轧制压力都会影响成形质量和工艺稳定性。
因此,在轧制过程中,需要根据金属材料的特性和产品的要求,选择合适的轧制压力,以保证金属材料的连续变形和均匀分布。
第三,轧制过程中需要控制合理的轧制速度。
轧制速度与轧制压力、金属材料的塑性等因素密切相关,过大或过小的轧制速度都会导致变形不均匀和产品品质问题。
因此,在轧制过程中,需要根据具体情况调整轧制速度,以保证金属材料的连续变形和均匀分布。
最后,轧制过程中需要保证良好的润滑条件。
润滑是减少金属材料与轧机滚轮间摩擦和磨损的重要手段,同时也有助于金属材料的变形和成形。
因此,在轧制过程中,需要提供充分的润滑剂,以保证轧制工艺的稳定性和产品质量的一致性。
总结起来,轧制工艺技术要求主要包括控制适当的轧制温度、轧制压力、轧制速度和良好的润滑条件。
通过合理地控制这些要求,可以提高轧制工艺的稳定性和产品质量的稳定性。
同时,也可以大大减少因轧制过程中的不良控制而导致的废品率和能源浪费。
因此,轧制工艺技术要求的落实是提高轧制生产效率和产品质量的重要保障。
轻量化工艺分类

不等厚度轧制板
通过轧钢机柔性轧制工艺,生产出厚度连续变化的金属薄板,以适应不同部位的强度需求,实现轻量化。
5
热成形技术
结合热处理和高温成形,使零件获得高强度,适用于对安全性要求高的部位,如防撞杆、A柱等。
6
高压铝合金铸造
利用高压铸造技术生产铝合金部件,实现集成设计复杂薄壁构件的轻量化,减少零部件数量。
轻量化工艺分类
序号
工艺名部分,实现整体结构的轻量化。例如,采用一体化设计、减少零件数量等。
2
材料轻量化
选用轻质高强度的材料,如高强度钢材、铝合金、复合材料等,以替代传统的重质材料,降低整车重量。
3
激光拼焊
将不同厚度、不同材质、不同性能的板坯拼焊在一起,再进行冲压成形,以实现零部件的轻量化。
7
内高压成形(液压成形)
通过向管坯内部充入高压液体,使其胀大至贴靠模具,实现复杂形状零部件的轻量化制造。
- 1、下载文档前请自行甄别文档内容的完整性,平台不提供额外的编辑、内容补充、找答案等附加服务。
- 2、"仅部分预览"的文档,不可在线预览部分如存在完整性等问题,可反馈申请退款(可完整预览的文档不适用该条件!)。
- 3、如文档侵犯您的权益,请联系客服反馈,我们会尽快为您处理(人工客服工作时间:9:00-18:30)。
第41卷 第11期 2006年11月钢铁Iron and SteelV ol.41,No.11N ovember 2006钢材性能柔性化与柔性轧制技术刘相华, 王国栋, 杜林秀, 刘振宇(东北大学轧制技术及连轧自动化国家重点实验室,辽宁沈阳110004)摘 要:为解决用户个性化需求与企业规模化生产之间的矛盾,提出将组织性能在线优化控制技术应用于柔性轧制,用同一种成分的坯料来生产不同性能的产品,简化炼钢和连铸的操作和管理,利用对钢材性能柔性的控制实现轧制生产的大规模定制。
指出当前2种可行的柔性轧制实例:用普碳钢生产屈服强度为200~400M Pa 的产品,用碳锰钢生产屈服强度为350~600M Pa 的产品。
关键词:柔性轧制;组织性能;在线优化控制;大规模定制中图分类号:T G 30 文献标识码:A 文章编号:0449-749X(2006)11-0032-05Flexible Steels and Flexible Rolling TechnologyLIU Xiang -hua, WANG Guo -dong , DU Lin -xiu, LIU Zhen -y u(T he State Key Labor atory of Ro lling and A utomation,No rtheaster n U niversity,Shenyang 110004,L iaoning,China)Abstract:T he Flexible Rolling T echno lo gy (FR T )fo r o nline optimizing contro l o f micr ostructure and pr operties o f steels is pr oposed to meet the individualized demands.T he key points of such F RT are to produce products w ith dif -fer ent pro per ties fro m the same steel g rade to r ealize mass customizatio n,and simplify operation and manag ement o f steel making and slab casting.T wo examples of the FRT ar e g iv en,including t he steel product s w ith yield str eng th from 200to 400M Pa pro duced fr om plain carbon steel,and y ield strength fr om 350to 600M P a produced fro m C -M n steel.Key words:f lex ible ro lling;micro structur e and pro per ty;online optim izing contro l;mass cust omizatio n基金项目:国家高技术研究发展计划资助项目(2003AA33G010),国家自然科学基金重点项目(50634030)作者简介:刘相华(1953-),男,博士,教授; E -mail :liux h@; 修订日期:2006-02-22随着现代科学技术和经济的发展,用户对钢铁产品需求越来越趋于多样化、个性化和优质化。
而钢铁生产发展的特点是大型化、连续化、集约化。
用户需求与生产技术和组织管理之间产生了矛盾。
这个矛盾由于供需关系由卖方市场转变为买方市场而变得更加突出,且越来越把解决这个矛盾的责任转移到产品生产者一方来。
在研制细晶粒普碳钢时,利用成分与Q195~Q235相同的普碳钢,已成功地生产出屈服强度为400M Pa 的产品[1]。
因此,可以用同一种化学成分的坯料,生产出不同强度级别的产品[2]。
这样可以简化冶炼、连铸的操作和管理,有利于冶炼和连铸工艺的持续稳定,使冶炼、连铸、板坯库、加热炉之间的衔接便捷、管理简化、难度减低[2]。
这种思想的优点是显而易见的,但是必须要有准确的产品组织性能在线预报和控制技术作支撑,才能付诸实施。
需要在坯料化学成分确定的条件下,深入研究并掌握轧制与冷却工艺参数对产品组织和性能影响的定量关系,并能够通过在线控制和调整工艺参数来克服性能指标的偏差,以保证产品的质量要求。
另一方面,柔性轧制的实现为金属产品的大规模定制提供了一条新的途径。
利用钢材性能柔性,可以用一个批号的坯料甚至一炉钢生产不同性能的产品来满足不同的用户需求,以生产技术的柔性化来应对用户需求的多样化,使金属产品的大规模定制得以实现[3,4]。
1 柔性轧制技术柔性轧制技术(FRT ,flexible rolling technolo -gy )是指能够导致轧制过程具有较大灵活性和适应性的轧制技术,一般可分为2种类型:外形尺寸方面的柔性轧制技术和组织性能方面的柔性轧制技术,本文主要涉及后者。
过去为了满足用户对不同强度产品的需求,往往是采用调整化学成分的方法,这样会带来增加生产成本,加快稀缺资源消耗等问题,同时也增加了冶炼工序成分控制难度,使冶炼、连铸、轧制面临频繁更换钢种带来的衔接技术复杂化与管理复杂化。
如果能够通过改变轧制工艺,使用同一种化学成分的原料轧制出不同性能级别的产品,上述问题第11期刘相华等:钢材性能柔性化与柔性轧制技术将迎刃而解。
这种想法是有理论根据的,也已经为新一代钢铁材料开发的实践所证实。
1.1 细晶强化与适度细化H al-l Petch 公式给出了屈服强度与晶粒尺寸间的定量关系:s = 0+k d1/2(1)式中,d 为晶粒的平均直径; 0为其它强化方式作用项;k 为钢种常数。
由式(1)可知,当把晶粒尺寸由15~20 m 控制到3~5 m,材料的屈服强度就能增加1倍左右。
200M Pa 级普碳钢的屈服强度就可能达到400M Pa 级。
如果能在上述范围内控制所希望的晶粒尺寸,就可能在200~400MPa 间控制钢材的性能。
轧制线材时通过对轧制及冷却工艺参数的控制,得到的微观组织实验结果如图1所示,从中可见,屈服强度随着晶粒的细化而逐渐提高,与H al-l Petch 公式基本相符。
既然不改变化学成分也能够在很大范围内改变钢材的性能,图2所示的柔性轧制技术的出现是不难理解的。
这里有以下4点值得注意。
(1)图1(b)中工艺A,B, ,N 之间的差别,既有轧制工艺的差别,也有冷却工艺的差别,且温度制度往往比变形制度更为重要。
(2)晶粒细化是提高屈服强度的有效手段,但是晶粒细化对提高抗拉强度的作用不明显,晶粒过于细化会导致材料的屈强比不合格。
(3)前阶段开发超级钢的经验表明,在当前的钢铁生产条件下,采用适度细化的思路[3]可以得到好的效果,对板带钢平均晶粒为3~5 m,棒线材为5~8 m 。
(4)柔性轧制并不追求晶粒超细化,而是参照H al-l Petch 公式把对晶粒尺寸的控制作为对屈服强度控制的一个手段。
1.2 组织复相化与复合强化双相钢的出现给出了新的启示,如果能够有效地控制钢中硬相(马氏体、贝氏体)与软相(铁素体)的比例,就有可能获得强度与塑性最佳匹配的钢材。
在细晶强化的基础上,利用相变强化和复相组织的强韧化,就有可能避免前面所说的屈强比问题,获得综合性能优良的钢材。
(a)11 m,310M Pa; (b)9.2 m ,370M Pa; (c) 6.8 m,450M Pa; (d)5.6 m,460M Pa图1 轧制线材实验得到的平均晶粒尺寸与屈服强度的关系Fig.1 Relationship between average grain size and yield strength obtained from the test of wirerolling(a)传统生产方式; (b)柔性轧制技术图2 柔性轧制技术生产与传统生产方式比较示意图Fig.2 C omparison between FRT production and traditional one33钢 铁第41卷复相钢开发存在2个难题:如何获得所希望的组织;如何精确控制各相组织的百分比。
在成分确定的条件下,最关键的是轧后冷却过程的控制。
为此开发了高速率冷却装置(H CD,high rate cooling device),在实验室条件下得到了大于400 /s(对3mm 厚板材)的冷却速度,为复相组织的精确控制提供了条件。
利用H CD 冷却装置,对开冷温度、终冷温度、冷却速度和冷却曲线路径4个方面进行控制,采用表1的化学成分得到了表2的实验结果。
可见,马氏体量超过50%,抗拉强度超过了1000MPa;铁素体65%,马氏体35%的情况下,得到的屈强比为0 60。
由上可见,以碳锰钢Q345的化学成分为基础,添加极微量的微合金元素(<0.03%),可以得到屈服强度350~600MPa 的产品,这是利用复相钢的技术思路来实现柔性轧制的又一个有说服力的典型例子。
2 组织性能预报与在线优化柔性轧制为钢铁产品的大规模定制提供了一种技术手段。
要在大生产中实现,还需要有组织性能预报与在线优化控制作为支撑。
2.1 组织性能预报已经有大量的前期理论与实验研究工作,建立了化学成分、加工条件与钢材组织和性能之间的关系[4]。
在此基础上,开发了中厚板的组织性能在线预报系统,并将其嵌入中厚板轧机的过程计算机系统,实现了在线性能预报,取得了良好的效果,如图3所示。
钢材强度指标的预报偏差小于8%。
表1 实验钢的化学成分Table 1 C hemical composition of test steel%w (C)w (M n)w (Si)w (S )w (P)w (Nb)w (Al s )0.141.470.260.0120.0100.0240.012表2 复相钢的实验结果Table 2 Experimental results of complex phase steel%编号R eL /M Pa R m /M Pa A /%R eL /R m 相组成B16791005130.6845%PF+55%M B2528885150.6065%AF+35%M B3499798180.6365%AF+30%GB+5%M B4538790250.6895%GB+5%M D1369522350.7182%PF+18%P D2914109770.8315%PF+85%M D3590898140.6665%PF+35%M D4516795230.6582%PF+18%M图3 中厚板组织性能在线预报系统Fig.3 Online prediction of microstructure and properties during plate rolling34第11期刘相华等:钢材性能柔性化与柔性轧制技术2.2 组织性能的在线优化控制目前实现钢材组织性能的在线直接检测还很困难,但是采用前述的方法,可在已知化学成分的情况下,通过对当前工艺参数的检测,来间接预测组织性能。