车架设计与汽车的安全性
前副车架设计

前副车架设计1. 引言在汽车工程中,副车架是指承载车身和连接前后悬挂系统的结构组成部分。
其中前副车架作为汽车前部的主要支撑和连接部件,承担着重要的作用。
本文将对前副车架的设计进行详细介绍,包括设计要点、材料选择、结构设计等。
2. 设计要点前副车架设计的目标是实现良好的刚度和强度,同时尽可能减轻重量,以提高汽车的操控性和燃油经济性。
下面是前副车架设计的几个重要要点:1.刚度和强度:前副车架需要具有足够的刚度和强度,以承受前部悬挂系统产生的力和扭矩。
这一点可以通过合理的结构设计和材料选择来实现。
2.重量优化:前副车架的重量对整车的性能有直接影响。
因此,在设计过程中应尽可能采用轻量化的设计方案,包括减少材料使用量、优化结构布局等。
3.安全性:前副车架需要具有良好的安全性能,能够在碰撞事故中吸收和转移能量,保护车辆乘员的生命安全。
3. 材料选择前副车架一般采用高强度钢材作为主要材料,具有良好的强度和刚度特性。
同时,为了实现重量优化,也可以考虑使用铝合金等轻质材料。
具体材料选择应根据车辆的使用环境、预算等因素进行综合考虑。
4. 结构设计前副车架的结构设计是保证刚度、强度和重量优化的关键。
下面是一些常见的结构设计方法:•框架结构:框架结构是一种常见的前副车架设计方案,可以提供较高的刚度和强度。
在设计过程中,可以通过优化框架横截面形状和尺寸,以及增加加强筋等方式来提高结构性能。
•悬挂连接:前副车架需要与前悬挂系统进行连接,以承受悬挂系统产生的力和扭矩。
悬挂连接部分的设计应保证连接强度和刚度,并考虑减少疲劳损伤。
•碰撞安全设计:前副车架在碰撞事故中起到保护车辆乘员的作用。
为了提高碰撞安全性能,可以在前副车架的设计中考虑使用可控变形结构、吸能材料等。
5. 进一步研究和发展方向随着汽车技术的不断发展,前副车架的设计也在不断创新和优化。
以下是一些可能的进一步研究和发展方向:•复合材料应用:复合材料具有高强度、轻量化和抗腐蚀等优点,可以考虑将其应用于前副车架的设计中,以进一步减轻重量。
基于多目标优化的汽车底盘车架设计
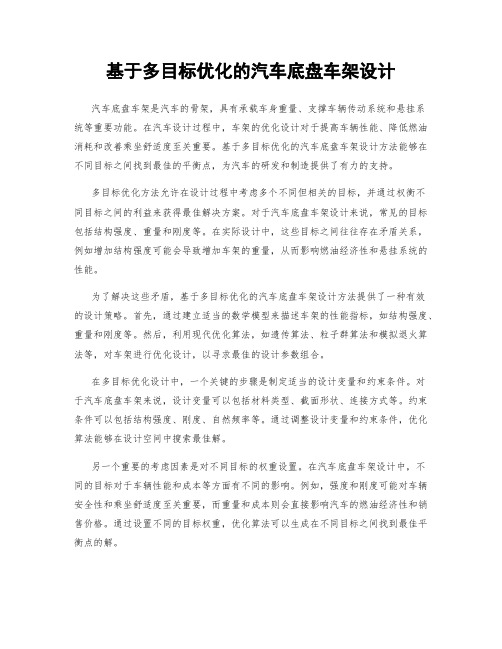
基于多目标优化的汽车底盘车架设计汽车底盘车架是汽车的骨架,具有承载车身重量、支撑车辆传动系统和悬挂系统等重要功能。
在汽车设计过程中,车架的优化设计对于提高车辆性能、降低燃油消耗和改善乘坐舒适度至关重要。
基于多目标优化的汽车底盘车架设计方法能够在不同目标之间找到最佳的平衡点,为汽车的研发和制造提供了有力的支持。
多目标优化方法允许在设计过程中考虑多个不同但相关的目标,并通过权衡不同目标之间的利益来获得最佳解决方案。
对于汽车底盘车架设计来说,常见的目标包括结构强度、重量和刚度等。
在实际设计中,这些目标之间往往存在矛盾关系,例如增加结构强度可能会导致增加车架的重量,从而影响燃油经济性和悬挂系统的性能。
为了解决这些矛盾,基于多目标优化的汽车底盘车架设计方法提供了一种有效的设计策略。
首先,通过建立适当的数学模型来描述车架的性能指标,如结构强度、重量和刚度等。
然后,利用现代优化算法,如遗传算法、粒子群算法和模拟退火算法等,对车架进行优化设计,以寻求最佳的设计参数组合。
在多目标优化设计中,一个关键的步骤是制定适当的设计变量和约束条件。
对于汽车底盘车架来说,设计变量可以包括材料类型、截面形状、连接方式等。
约束条件可以包括结构强度、刚度、自然频率等。
通过调整设计变量和约束条件,优化算法能够在设计空间中搜索最佳解。
另一个重要的考虑因素是对不同目标的权重设置。
在汽车底盘车架设计中,不同的目标对于车辆性能和成本等方面有不同的影响。
例如,强度和刚度可能对车辆安全性和乘坐舒适度至关重要,而重量和成本则会直接影响汽车的燃油经济性和销售价格。
通过设置不同的目标权重,优化算法可以生成在不同目标之间找到最佳平衡点的解。
多目标优化的汽车底盘车架设计方法具有许多优点。
首先,它可以提供多种解决方案,使设计师能够在不同的设计空间中选择最佳方案。
其次,它可以显著提高车辆性能和综合效益。
通过优化设计,可以提高车架的结构强度和刚度,减轻车身重量,降低燃油消耗,提高行驶稳定性和乘坐舒适度。
2024年车架市场发展现状

2024年车架市场发展现状概述车架作为汽车的重要组成部分,承载着汽车的底盘和车身结构,对汽车的安全性和稳定性有着重要影响。
近年来,随着汽车产业的快速发展,车架市场也呈现出不断增长和创新的趋势。
本文将从市场规模、技术创新和市场竞争等方面综述车架市场的发展现状。
市场规模近年来,全球汽车市场持续保持增长态势,推动了车架市场的发展。
2019年,全球车架市场总量达到2540万套,预计到2025年将增至3280万套,年平均增长率约为4.5%。
亚太地区、欧洲和北美地区是全球车架市场的主要消费地区,占全球市场份额的90%以上。
同时,随着新能源汽车的快速普及和推广,新能源车架市场也呈现出快速增长的趋势。
根据市场研究机构的数据,2019年全球新能源汽车产销量约为240万辆,预计到2025年将增至1270万辆。
新能源车架市场规模也将持续扩大,为车架市场提供了新的增长点。
技术创新随着汽车行业的进步和技术的推动,车架市场也在不断进行技术创新,为汽车的性能和安全性提供了更高水平的支持。
制造工艺创新传统的车架制造一般采用钢铁材质,但随着碳纤维复合材料的发展,越来越多的汽车制造商开始采用碳纤维车架。
碳纤维车架相比传统的钢铁车架更轻便、更坚固,能够提高汽车的燃油效率和操控性能。
此外,传统的焊接制造方式也在逐渐被自动化制造技术所取代。
例如,采用铝合金材质的车架常常采用铝合金压铸工艺生产,能够提高车架的精度和质量,减少车架在制造过程中的变形和变色问题。
结构设计创新车架的结构设计对汽车的性能和安全性有着重要影响。
近年来,各汽车制造商在车架结构设计方面进行了一系列创新。
为了提高车辆的抗冲击能力和减轻碰撞对车内乘员的伤害,一些汽车制造商采用了变形吸能结构设计。
该设计可以在车辆碰撞时通过车架的部分变形,吸收撞击能量,减少乘员的伤害。
同时,为了提高汽车的性能和操控性能,一些高端汽车采用了多铝合金材料的复合结构设计。
该设计可以在保证车身强度的同时,减轻车身质量,提高车辆的悬挂性能和操控性能。
简述车身零部件的组成

简述车身零部件的组成《车身零部件的组成》车身零部件是构成汽车外观、保护车内乘客、以及提供结构强度的各个部件的总称。
它们的设计和组装对于汽车的性能、安全性以及外观起着重要的作用。
车身零部件的组成是汽车工业的核心之一,本文将简述车身零部件的主要构成。
1.车架:车架是车身的骨架,负责支撑和承受汽车重量。
它由钢材、铝合金或者复合材料制成,通常包括前后横梁、纵梁和横梁。
车架的设计和材料选择对于汽车的结构强度和刚性起着关键作用。
2.车身板:车身板是构成车身外观的主要部分,包括车顶、车门、车厢侧板和行李厢。
这些车身板通常由钢材制成,也有一些高端汽车采用铝合金或者复合材料来减轻重量。
车身板的设计和加工工艺,决定了汽车外观的美观度和车身的耐久性。
3.车窗:车窗是车身的一部分,负责提供车内的观察视线和通风功能。
车窗一般由钢化玻璃制成,可以避免碎裂,提高安全性。
一些高端车型还采用了隔音玻璃或者防紫外线玻璃,提高了车内乘坐的舒适性。
4.车灯:车灯是车身的重要组成部分,包括前大灯、尾灯、转向灯和雾灯等。
它们不仅提供了照明功能,还对车辆的安全性和外观起着重要作用。
现代车灯通常采用LED技术,具有高亮度、低能耗和长寿命的特点。
5.保险杠:保险杠位于车身的前后部分,主要起到保护车辆和行人的作用。
它们通常由塑料或者钢材制成,可以减少碰撞时的冲击力并缓解受损程度。
除了以上部件,车身零部件还包括车顶行李架、车身贴纸、车身护板、车身踏板等。
这些部件不仅仅是为了提供美观和个性化的效果,更重要的是为了保护和提升车辆的功能和驾驶体验。
在汽车工业的发展中,车身零部件的设计和制造技术不断推陈出新。
现代汽车越来越注重车身材料的轻量化、安全性的提升和外观的个性化。
通过不断创新和改进,车身零部件将在未来继续发挥重要作用,为乘客提供更安全、舒适和环保的驾乘体验。
简述车架的功用及对车架的要求
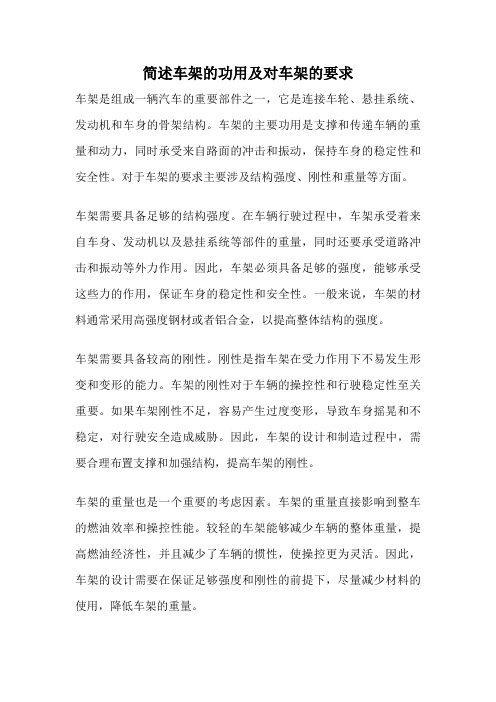
简述车架的功用及对车架的要求车架是组成一辆汽车的重要部件之一,它是连接车轮、悬挂系统、发动机和车身的骨架结构。
车架的主要功用是支撑和传递车辆的重量和动力,同时承受来自路面的冲击和振动,保持车身的稳定性和安全性。
对于车架的要求主要涉及结构强度、刚性和重量等方面。
车架需要具备足够的结构强度。
在车辆行驶过程中,车架承受着来自车身、发动机以及悬挂系统等部件的重量,同时还要承受道路冲击和振动等外力作用。
因此,车架必须具备足够的强度,能够承受这些力的作用,保证车身的稳定性和安全性。
一般来说,车架的材料通常采用高强度钢材或者铝合金,以提高整体结构的强度。
车架需要具备较高的刚性。
刚性是指车架在受力作用下不易发生形变和变形的能力。
车架的刚性对于车辆的操控性和行驶稳定性至关重要。
如果车架刚性不足,容易产生过度变形,导致车身摇晃和不稳定,对行驶安全造成威胁。
因此,车架的设计和制造过程中,需要合理布置支撑和加强结构,提高车架的刚性。
车架的重量也是一个重要的考虑因素。
车架的重量直接影响到整车的燃油效率和操控性能。
较轻的车架能够减少车辆的整体重量,提高燃油经济性,并且减少了车辆的惯性,使操控更为灵活。
因此,车架的设计需要在保证足够强度和刚性的前提下,尽量减少材料的使用,降低车架的重量。
除了上述要求之外,车架还需要考虑其他因素。
例如,车架的设计应该符合车辆的使用环境和需求。
对于越野车或者运输车等重载车型,车架需要更加坚固和耐用,以应对恶劣的路况和重负荷的工作。
而对于轿车和跑车等高性能车型,则需要更加注重车架的轻量化和刚性,以提供更好的操控性能和驾驶体验。
车架作为汽车的骨架结构,具备支撑和传递重量和动力的功能,对于车架的要求主要涉及结构强度、刚性和重量等方面。
车架需要具备足够的强度和刚性,以保证车身的稳定性和安全性。
同时,车架的重量也需要尽量减少,以提高整车的燃油经济性和操控性能。
除此之外,车架的设计还需要考虑车辆的使用环境和需求,以满足不同车型的要求。
车辆安全风险评估报告

引言概述:车辆安全风险评估是对汽车行业进行重要的安全性评价,以提高车辆的安全性能和降低事故风险为目标。
本文将对车辆安全风险评估报告(二)进行详细阐述。
通过对车辆相关的五个主要方面进行分析和评估,包括车辆结构安全、制动系统安全、电气系统安全、被动安全系统和主动安全系统,以进一步提升车辆的整体安全性能。
正文内容:一、车辆结构安全:1. 车身结构和车架的强度评估:通过分析车辆结构材料和连接方式,评估其强度和刚度,以确保在碰撞事件中具备出色的抗冲击能力。
2. 安全气囊和保险杠设计:研究车辆的安全气囊系统和保险杠设计,确保在碰撞事故中能提供充足的保护,降低乘客和行人的伤害风险。
3. 其他车身结构安全措施:包括车门锁定系统、车窗护栏、防滚架等,通过评估其稳定性和可靠性,提高车辆在紧急情况下的安全性能。
二、制动系统安全:1. 制动系统性能评估:对车辆的制动性能进行全面评估,包括刹车距离、制动灵敏度和制动力分配等方面,确保制动系统能够及时准确地响应驾驶员的指令。
2. 制动液和制动器的检测:检测制动液的含水率和制动器的磨损程度,确保制动系统运行的可靠性和稳定性。
3. 制动辅助系统:评估车辆是否配备了ABS、EBD、BA等制动辅助系统,提高车辆在紧急制动时的稳定性和控制性能。
三、电气系统安全:1. 电子控制单元(ECU)的评估:对车辆的ECU进行详细评估,确保其性能稳定可靠,并具备防止黑客攻击的安全防护措施。
2. 线束和连接器的安全性检测:评估车辆电气系统的线束和连接器的接触性和防水性能,降低因电路接触不良或短路而造成的火灾风险。
3. 电池和充电系统的安全评估:检测车辆的电池和充电系统,确保其安全可靠,避免因电池短路或过度充电导致火灾发生。
四、被动安全系统:1. 安全带和头枕的评估:评估车辆的安全带和头枕设计,确保其对乘客的保护性能,在碰撞事故中减少颈部和胸部的受伤风险。
2. 安全座椅和儿童座椅的安全性评估:评估车辆的安全座椅和儿童座椅设计,确保其符合相关安全标准,保护乘客的安全。
汽车卡车车架设计标准是什么
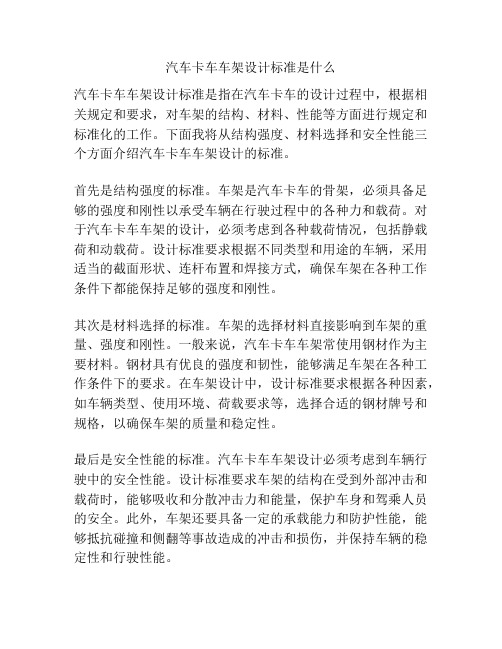
汽车卡车车架设计标准是什么
汽车卡车车架设计标准是指在汽车卡车的设计过程中,根据相关规定和要求,对车架的结构、材料、性能等方面进行规定和标准化的工作。
下面我将从结构强度、材料选择和安全性能三个方面介绍汽车卡车车架设计的标准。
首先是结构强度的标准。
车架是汽车卡车的骨架,必须具备足够的强度和刚性以承受车辆在行驶过程中的各种力和载荷。
对于汽车卡车车架的设计,必须考虑到各种载荷情况,包括静载荷和动载荷。
设计标准要求根据不同类型和用途的车辆,采用适当的截面形状、连杆布置和焊接方式,确保车架在各种工作条件下都能保持足够的强度和刚性。
其次是材料选择的标准。
车架的选择材料直接影响到车架的重量、强度和刚性。
一般来说,汽车卡车车架常使用钢材作为主要材料。
钢材具有优良的强度和韧性,能够满足车架在各种工作条件下的要求。
在车架设计中,设计标准要求根据各种因素,如车辆类型、使用环境、荷载要求等,选择合适的钢材牌号和规格,以确保车架的质量和稳定性。
最后是安全性能的标准。
汽车卡车车架设计必须考虑到车辆行驶中的安全性能。
设计标准要求车架的结构在受到外部冲击和载荷时,能够吸收和分散冲击力和能量,保护车身和驾乘人员的安全。
此外,车架还要具备一定的承载能力和防护性能,能够抵抗碰撞和侧翻等事故造成的冲击和损伤,并保持车辆的稳定性和行驶性能。
总结起来,汽车卡车车架设计的标准主要涉及结构强度、材料选择和安全性能三个方面,以确保车架在各种工作条件下都具备足够的强度、重量和安全性能。
这些标准是保障汽车卡车质量和安全的重要依据,对于汽车卡车制造厂商和设计工程师来说,是设计和生产高质量车辆的基础。
轻型载货汽车车架设计说明书

第1章绪论课题背景汽车的使用条件复杂,其受力情况也十分复杂,随着汽车行驶条件车速和路况的变化,车架上的载荷变化也很大,而车架,作为汽车的主要承载工件,它的好坏直接关系着汽车的各方面性能,如操作稳定性、安全性、舒适性、燃油经济性等;有过汽车在使用过程中,车架断裂的情况发生;所以对车架的主要受力件车架纵梁的强度进行校核,有着至关重要的意义;确保车架在各个工况下,车架纵梁的弯曲强度都符合材料的弯曲强度极限要求,如果不符合要求的,找出解决的方案,保证人与财产的安全;另外,随着油价的上涨和国家对汽车尾气排放标准的不断提高,对载货汽车车架进行设计,不管是对其结构参数的优化设计,对其进行轻量化的优化设计,还是对汽车车架进行疲劳寿命预测分析等,都是出于对汽车动力性、安全性、燃油经济性的考虑;是非常有必要的;研究新的车架材料,减轻其质量,可以有效减少其整备质量;车架的发展历程车架”这个名称原本是从法文的“Chassis”衍生而来的,早期汽车所使用的车架,大多都是由笼状的钢骨梁柱所构成的,也就是在两支平行的主梁上,以类似阶梯的方式加上许多左右相连的副梁制造而成;车体建构在车架之上,至于车门、沙板、引擎盖、行李厢盖等钣件,则是另外再包覆于车体之外,因此车体与车架其实是属于两个独立的构造;第2章方案论证参考车型及其参数公告型号CA1092PK26L5E4 公告批次228品牌类型载货汽车额定质量4990 总质量8785整备质量3600 燃料种类排放依据标准轴数 2轴距4560 轴荷3585/5200轮胎规格接近离去角28/12前悬后悬1080/2355 前轮距后轮距识别代号整车长7995 整车宽2260,2445整车高2430 货厢长6180货厢宽2115,2300 货厢高560最高车速95 载质量利用系数备注该车带OBD,防护材料材质:Q235-A,连接方式:螺栓连接,后部防护装置的断面尺寸mm:145×50,离地高度:545mm;汽车车架受力情况2.1.1车架水平菱形扭动力因为车辆在行驶时,每个车轮因为路面和行驶情况的不同,路面的铺设情况、凹凸起伏、障碍物及进出弯角等等每个车轮会承受不同的阻力和牵引力,这可以使车架在水平方向上产生推拉以至变形,这种情况就好像将一个长方形拉扯成一个菱形一样;2.1.2车架非水平扭动力当前后对角车轮遇到道路上的不平而滚动,车架的梁柱便要承受这个纵向扭曲压力,情况就好像要你将一块塑料片扭曲成螺旋形一样;2.1.3车架横向弯曲力所谓横向弯曲,就是汽车在入弯时重量的惯性即离心力会使车身产生向弯外甩的倾向,而轮胎的抓着力会和路面形成反作用力,两股相对的压力将车架横向扭曲;2.1.4车架负载弯曲力从字面上就可以十分容易的理解这个压力,部分汽车的非悬挂重量,是由车架承受的,通过轮轴传到地面;而这个压力,主要会集中在轴距的中心点;因此车架底部的纵梁和横梁member,一般都要求较强的刚度;车架设计要求2.2.1车架必须要有一定的强度保证在各种复杂受力的使用情况下车架不受破坏;要求有足够的疲劳强度,保证在汽车大修里程内,车架不致有严重的疲劳损伤;纵梁受力极为复杂,设计时不仅应注意各种应力,改善其分布情况,还应该注意使各种应力峰值不出现在同一部位上;例如,纵梁中部弯曲应力较大,则应注意降低其扭转应力,减少应力集中并避免失稳;而在前、后端,则应着重控制悬架系统引起的局部扭转;提高纵梁强度常用的措施如下:1提高弯曲强度选定较大的断面尺寸和合理的断面形状槽形梁断面高宽比一般为3:1左右;2提高局部扭转刚度注意偏心载荷的布置,使相近的几个偏心载荷尽量接近纵梁断面的弯曲中心,并使合成量较小;在偏心载荷较大处设置横梁,并根据载荷大小及分散情况确定连接强度和宽度;将悬置点分布在横梁的弯曲中心上;当偏心载荷较大并偏离横梁较远处时候,可以采用K形梁,或者将该段纵梁形成封闭断面;偏心载荷较大且比较分散时候,应该采用封闭断面梁,横梁间距也应缩小;选用较大的断面;限制制造扭曲度,减少装配预应力;3提高整体扭转强度不使纵梁断面过大;翼缘连接的横梁不宜相距太近;4减少应力集中及疲劳敏感尽可能减少翼缘上的孔特别是高应力区,严禁在翼缘上布置大孔;注意外形的变化,避免出现波纹区或者受严重变薄;注意加强端部的形状和连接,避免刚度突变;避免在槽形梁的翼缘边缘处施焊,尤其畏忌短焊缝和“点”焊;5减少失稳受压翼缘宽度和厚度的比值不宜过大常在12左右;在容易出现波纹处限制其平整度;6局部强度加强采用较大的板厚;加大支架紧固面尺寸,增多紧固数量,并尽量使力作用点接近腹板的上、下侧面;2.2.2车架的轻量化由于车架较重,对于钢板的消耗量相当大;因此,车架应按等强度的原则进行设计,以减轻汽车的自重和降低材料的消耗量;在保证强度的条件下,尽量减轻车架的质量;通常要求车架的质量应小于整车整备质量的10%;本设计主要对车架纵梁进行简化的弯曲强度计算,使车架纵梁具有足够的强度,以此来确定车架的断面尺寸;参照材料力学另外,目前钢材价格暴涨,汽油价格上涨,从生产汽车的经济性考虑的话,也应尽量减轻整车的质量;从生产工艺性考虑,横纵梁采用简便可靠的连接方式,不仅能降低工人的工作强度,还能增强车架的强度;车架形式的确定2.3.1边梁式车架这种车架由两根纵梁及连接两根纵梁的若干根横梁组成,用铆接和焊接的方法将纵横梁连接成坚固的刚性构架;纵梁通常用低合金钢板冲压而成,断面一般为槽型,z星或箱型断面;横梁用来连接纵梁,保证车架的抗扭刚度和承载能力,而且还用来支撑汽车上的主要部件; 边梁式车架能给改装变型车提供一个方便的安装骨架,因而在载重汽车和特种车上得到广泛用;其弯曲刚度较大,而当承受扭矩时,各部分同时产生弯曲和扭转;其优点是便于安装车身、车箱和布置其他总成,易于汽车的改装和变形,因此被广泛地用在载货汽车、越野汽车、特种汽车和用货车底盘改装而成的大客车上;在中、轻型客车上也有所采用,轿车则较少采用; 用于载货汽车的边梁式车架由两根相互平行但开口朝内、冲压制成的槽型纵梁及一些冲压制成的开口槽型横梁组合而成;通常,纵梁的上表面沿全长不变或局部降低,而两端的下表面则可以根据应力情况相应地缩小;车架宽度多为全长等宽;2.3.2中梁式车架脊骨式车架其结构只有一根位于中央而贯穿汽车全长的纵梁,亦称为脊骨式车架;中梁的断面可做成管形、槽形或箱形;中梁的前端做成伸出支架,用以固定发动机,而主减速器壳通常固定在中梁的尾端,形成断开式后驱动桥;中梁上的悬伸托架用以支承汽车车身和安装其它机件;若中梁是管形的,传动轴可在管内穿过;优点是有较好的抗扭转刚度和较大的前轮转向角,在结构上容许车乾有较大的跳动空间,便于装用独立悬架,从而提高了汽车的越野性;与同吨位的载货汽车相比,其车架轻,整车质量小,同时质心也较低,故行驶稳定性好;车架的强度和刚度较大;脊梁还能起封闭传动轴的防尘罩作用;缺点是制造工艺复杂,精度要求高,总成安装困难,维护修理也不方便,故目前应用较少;2.3.3综合式车架综合式车架是由边梁式和中梁式车架联合构成的;车架的前段或后段是边梁式结构,用以安装发动机或后驱动桥;而车架的另一段是中梁式结构的支架可以固定车身;传动轴从中梁的中间穿过,使之密封防尘;其中部的抗扭刚度合适,但中部地板凸包较大,且制造工艺较复杂;此种结构一般在轿车上使用; 车架承受着全车的大部分重量,在汽车行驶时,它承受来自装配在其上的各部件传来的力及其相应的力矩的作用;当汽车行驶在崎岖不平的道路上时,车架在载荷作用下会产生扭转变形,使安装在其上的各部件相互位置发生变化;当车轮受到冲击时,车架也会相应受到冲击载荷;因而要求车架具有足够的强度,合适的刚度,同时尽量减轻重量;在良好路面行驶的汽车,车架应布置得离地面近一些,使汽车重心降低,有利于汽车稳定行驶,车架的形状尺寸还应保证前轮转向要求的空间;第3章车架结构车架结构形式的选定3.1.1车架宽度的确定车架宽度是指左右纵梁腹板外侧面之间的宽度;在总体设计中,整车宽度确定后,车架前后部分宽度就可以根据前轮最大转向角、轮距、钢板弹簧片宽、装在车架内侧的发动机外廓宽度及悬置等尺寸确定;从提高整车的横向稳定性以及减小车架纵梁外侧装置件的悬伸长度来看,车架尽量宽些,同时前后部分宽度应相等;本设计取的车架宽860mm;3.1.2车架纵梁形式的确定纵梁是车架的主要承载部件,在汽车行驶中受较大的弯曲应力;车架纵梁根据截面形状分有工字梁和槽形梁;由于槽形梁具有强度高、工艺简单等特点,因此在载货汽车设计中选用槽形梁结构;另外为了满足低速载货汽车使用性能的要求,纵梁采用直线形结构;这样既可降低纵梁的高度,减轻整车自身重量,降低成本,亦可保证强度;材料选用16Mn低合金钢,16Mn低合金钢在强度,塑性,可焊性方面能较好地满足刚结构,是应用最广泛的低合金钢,综合机械性能良好,正火可提高塑性,韧性及冷压成型性能;根据本设计的要求,再考虑纵梁截面的特点,本方案设计的纵梁采用上、下翼面是平直等高的槽形钢;纵梁总长为6815mm;优点:有较好的抗弯强度,便于安装汽车部件;3.1.3车架横梁形式的确定横梁是车架中用来连接左、右纵梁,构成车架的主要构件;横梁本身的抗扭性能的好坏及其分布,直接影响着纵梁的内应力大小及其分布合理设计横梁,可以保证车架具有足够的扭转刚度;从早期通过试验所得出的一些结论可以看出,若加大横梁的扭转刚度,可以提高整个车架的扭转刚度,但与该横梁连接处的纵梁的扭转应力会加大;如果不加大横梁,而是在两根横梁间再增加横梁,其结果是增加了车架的扭转刚度,同时还降低了与横梁连接处的纵梁扭转应力在横梁上往往要安装汽车上的一些主要部件和总成,所以横梁形状以及在纵梁上的位置应满足安装上的需要;横、纵梁的断面形状、横梁的数量以及两者之间的连接方式,对车机架的扭转刚度有大的影响;纵、横梁材料的选用有以下三种:车架A:箱型纵梁、管型横梁,横、纵梁间采用焊接连接,扭转刚度最大;车架B:槽型纵梁、槽型横梁,横、纵梁间采用铆接连接,扭转刚度适中;车架C:槽型纵梁、工字型横梁,横、纵梁间采用铆接连接,扭转刚度最小;从以上三种车架的对比可以看出:轻型载货汽车应该选用车架B;本设计共有八根横梁,有前横梁,发动机前悬置横梁,发动机后悬置横梁,驾驶室后悬置横梁,中横梁,后钢板弹簧前支架横梁,后钢板弹簧后支架横梁,后横梁;纵梁与横梁的连接3.2.1车架纵梁与横梁的连接形式货车多以铆钉连接见下图;铆钉连接具有一定弹性,有利于消除峰值应力,改善应力状况,这对于要求有一定扭转弹性的货车车架有重要意义;车架铆接示意图铆接设计注意事项:a.尽量使铆钉的中心线与构件的端面重心线重合;b.铆接厚度一般不大于5d;c.在同一结构上铆钉种类不益太多;d.尽量减少在同一截面上的铆钉孔数,将铆钉交错排列;[]83.2.2横梁在纵梁上的连接常见有三种型式:横梁和纵梁上下翼缘相连;横梁和纵梁的腹板相连;横梁同时和纵梁的任一翼缘以及腹板相连;其中前后横梁分别采用上下翼缘相连接的方式,可得到较大的连接跨度和连接刚度,使车架扭转刚度增大,纵梁局部扭转改善;第四横梁即车架中部的横梁采用腹板连接的方式,腹板连接结构与翼面连接结构相比,前者比后者可使纵梁的扭转翘曲应力降低;横梁和纵梁腹板及一个翼缘同时相连,则兼有以上两种连接方式的特点,缺点在于作用在纵梁上的力直接传到横梁上;有时使横梁只和纵梁的一个翼缘相连,则极难发挥其刚度作用,因此不常采用;3.2.3车架加强版第4章车架设计计算车架的载荷分析汽车静止时,车架上只承受弹簧以上部分的载荷称为静载荷;汽车在行驶过程中,随行驶条件车速和路面情况的变化,车架将主要承受对称的垂直动载荷和斜对称的动载荷;对称的垂直动载荷是当汽车在平坦道路上以较高车速行驶时产生的,其值取决于作用在车架上的静载荷及其在车架上的分布,还取决于静载荷作用处的垂直加速度之值;这种动载荷会使车架产生弯曲变形;当汽车在不平道路上行驶时,汽车的前后几个车轮可能不在同一平面上,从而使车架连同车身一起歪斜,其值取决于道路不平坦的程度以及车身、车架和悬架的刚度;这种动载荷将会使车架产生扭转变形;由于汽车的结构复杂,使用工况多变,除了上述两种主要载荷的作用外,汽车车架上还承受其他的一些载荷;如汽车加速或制动时会导致车架前后载荷的重新分配;汽车转向时,惯性力将使车架受到侧向力的作用;一般来说,车架主要损坏的疲劳裂纹起源于纵梁和横梁边缘处,然后向垂直于边缘的方向扩展;在纵梁上的裂纹将迅速发展乃至全部断裂,而横梁上出现的裂纹则往往不再继续发展或扩展得很缓慢;根据统计资料可知,车架的使用寿命主要取决于纵梁抗疲劳损伤的强度;因此,在评价车架的载荷性能时,主要应着眼于纵梁;车架纵梁的强度计算车架的应力计算4.3.1支座反力的计算4.3.1纵梁的剪力和弯矩计算要计算车架纵梁的弯矩,先计算车架前支座反作用力,向后轮中心支座处求矩F1——前轮中心支座对任一纵梁左纵梁或右纵梁的反作用力N;F2——后轮中心支座对任一纵梁左纵梁或右纵梁的反作用力N;L——纵梁的总长,7215mm;l——汽车轴距,4560mm;a——前悬,1080mm;b——后悬,2355mm;c——货厢长,6180mm;c1——车厢前端到二轴的距离,4120mm;c2——车厢后端到二轴的距离,2060mm;Ms——空车时的簧载质量,约2400kg;Me——满载时有效装载质量,5190kg;g——重力加速度,s ;代入4-1和4-2可得:==在计算纵梁弯矩时,将纵梁分成两段区域,每一段的均布载荷可简化为作用于区段中点的集中力;纵梁各端面上的弯矩计算采用弯矩差法,可使计算工作量大大减少;弯矩差法认为:纵梁上某一端面上的弯矩为该段面之前所有力对改点的转矩之和;车架材料的选择梁截面系数的计算弯矩应力计算与校核第5章车架制图制图方式传统制图CAD制图5.3.1绘图便利5.3.2保存便利utoCAD在机械零件上的优势。
汽车车架焊接工艺分析及工装设计
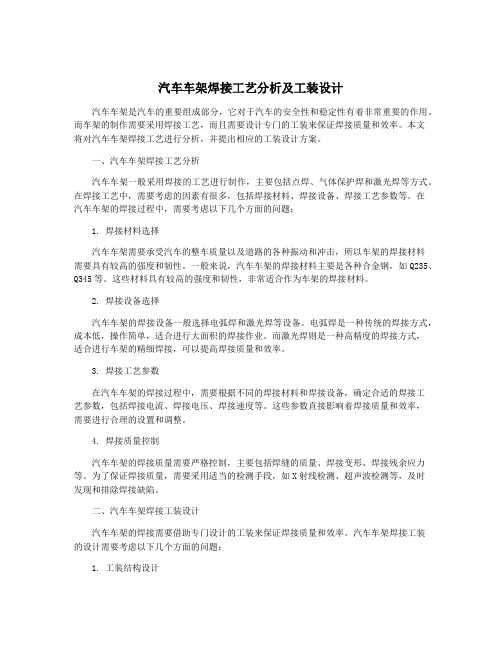
汽车车架焊接工艺分析及工装设计汽车车架是汽车的重要组成部分,它对于汽车的安全性和稳定性有着非常重要的作用。
而车架的制作需要采用焊接工艺,而且需要设计专门的工装来保证焊接质量和效率。
本文将对汽车车架焊接工艺进行分析,并提出相应的工装设计方案。
一、汽车车架焊接工艺分析汽车车架一般采用焊接的工艺进行制作,主要包括点焊、气体保护焊和激光焊等方式。
在焊接工艺中,需要考虑的因素有很多,包括焊接材料、焊接设备、焊接工艺参数等。
在汽车车架的焊接过程中,需要考虑以下几个方面的问题:1. 焊接材料选择汽车车架需要承受汽车的整车质量以及道路的各种振动和冲击,所以车架的焊接材料需要具有较高的强度和韧性。
一般来说,汽车车架的焊接材料主要是各种合金钢,如Q235、Q345等。
这些材料具有较高的强度和韧性,非常适合作为车架的焊接材料。
2. 焊接设备选择汽车车架的焊接设备一般选择电弧焊和激光焊等设备。
电弧焊是一种传统的焊接方式,成本低,操作简单,适合进行大面积的焊接作业。
而激光焊则是一种高精度的焊接方式,适合进行车架的精细焊接,可以提高焊接质量和效率。
3. 焊接工艺参数在汽车车架的焊接过程中,需要根据不同的焊接材料和焊接设备,确定合适的焊接工艺参数,包括焊接电流、焊接电压、焊接速度等。
这些参数直接影响着焊接质量和效率,需要进行合理的设置和调整。
4. 焊接质量控制汽车车架的焊接质量需要严格控制,主要包括焊缝的质量、焊接变形、焊接残余应力等。
为了保证焊接质量,需要采用适当的检测手段,如X射线检测、超声波检测等,及时发现和排除焊接缺陷。
二、汽车车架焊接工装设计汽车车架的焊接需要借助专门设计的工装来保证焊接质量和效率。
汽车车架焊接工装的设计需要考虑以下几个方面的问题:1. 工装结构设计汽车车架焊接工装的设计需要充分考虑车架的形状和结构,采用合适的夹具和模具来固定和支撑车架,在焊接过程中保证车架的稳定性和一致性。
工装的结构设计还需要考虑操作方便、维修方便等因素。
汽车底盘车架设计的静态与动态分析

汽车底盘车架设计的静态与动态分析汽车底盘车架是整车结构的基础,它承受着车辆整体重量及各种力和扭矩。
因此,在汽车底盘车架设计过程中,静态和动态分析是必不可少的步骤。
静态分析是指在车身静止的情况下,对底盘车架进行受力分析。
首先,我们需要确定车辆的载荷条件,包括车身质量、乘客数量、行李负荷等。
然后,根据这些载荷条件和设计要求,计算车架在静态状态下的应力和变形情况。
在进行静态分析时,需要考虑以下几个方面:1. 材料强度和刚度:选择合适的材料,并确定其强度和刚度参数。
常见的材料包括钢材和铝合金等。
根据材料的特性,计算车架在载荷作用下的应力和变形情况。
2. 荷载条件:准确确定车身的质量分布情况,包括车轮的荷载情况、前后配重比例等。
根据这些荷载条件,计算车架在不同载荷情况下的应力。
3. 过程动力学:考虑车辆行驶过程中的加速、制动、转向等动力学载荷,并进行相应的静态分析。
这些载荷往往是不稳定和非均匀的,需要进行合理的荷载分析和参数计算。
动态分析是指在车身运动的情况下,对底盘车架进行受力分析。
与静态分析相比,动态分析更加复杂,需要考虑更多的因素。
在进行动态分析时,需要注意以下几个方面:1. 荷载分析:根据车辆的动力学特性,确定车架在不同行驶条件下的荷载条件。
包括车辆加速、制动、转向、行驶过程中的颠簸等。
确保车架能够承受这些荷载并保持合适的刚度和强度。
2. 振动分析:考虑车辆行驶时的振动情况,采用有限元分析等方法,计算车架在不同频率下的振动响应。
并结合相关标准和限制条件,设计合适的减振措施。
3. 动态稳定性:确保车架在各种行驶条件下保持稳定和可控。
通过优化设计,提高车辆的操控性和安全性。
综上所述,汽车底盘车架设计的静态与动态分析是保证车辆安全性和可靠性的关键步骤。
在设计过程中,需要考虑车辆的载荷条件、材料强度和刚度、动力学特性、振动响应等因素。
通过合理的分析和优化设计,确保底盘车架能够承受各种力和扭矩,保持良好的稳定性和控制性,为驾驶员提供安全、舒适的行驶体验。
营运车辆运行安全技术条件
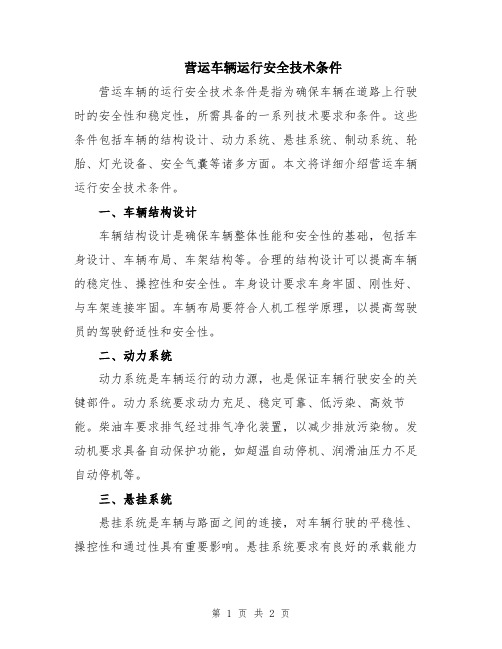
营运车辆运行安全技术条件营运车辆的运行安全技术条件是指为确保车辆在道路上行驶时的安全性和稳定性,所需具备的一系列技术要求和条件。
这些条件包括车辆的结构设计、动力系统、悬挂系统、制动系统、轮胎、灯光设备、安全气囊等诸多方面。
本文将详细介绍营运车辆运行安全技术条件。
一、车辆结构设计车辆结构设计是确保车辆整体性能和安全性的基础,包括车身设计、车辆布局、车架结构等。
合理的结构设计可以提高车辆的稳定性、操控性和安全性。
车身设计要求车身牢固、刚性好、与车架连接牢固。
车辆布局要符合人机工程学原理,以提高驾驶员的驾驶舒适性和安全性。
二、动力系统动力系统是车辆运行的动力源,也是保证车辆行驶安全的关键部件。
动力系统要求动力充足、稳定可靠、低污染、高效节能。
柴油车要求排气经过排气净化装置,以减少排放污染物。
发动机要求具备自动保护功能,如超温自动停机、润滑油压力不足自动停机等。
三、悬挂系统悬挂系统是车辆与路面之间的连接,对车辆行驶的平稳性、操控性和通过性具有重要影响。
悬挂系统要求有良好的承载能力和减震能力,保证车辆通过路面障碍时不发生失控。
悬挂系统的调整要合理,以满足车辆在不同路况下的运行要求。
四、制动系统制动系统是保证车辆行驶安全的重要系统。
制动系统要求制动效果好、制动稳定、制动可靠。
要求车辆能在各种条件下实现良好的制动性能,包括制动距离短、制动稳定、防抱死等功能。
制动系统还要求具备排水性能,以保证在雨天道路上制动效果不受影响。
五、轮胎轮胎是车辆与地面之间的唯一接触面,对车辆的操控性、通过性和行驶安全具有重要影响。
轮胎要求胎面硬度适中,具备良好的抓地力和耐磨性。
轮胎胎纹要求明显,花纹深度不低于1.6mm,以保证在湿滑路面上的抓地性能。
六、灯光设备灯光设备是车辆的\。
汽车碰撞安全设计

汽车碰撞安全设计随着汽车的普及和道路交通的不断增加,交通事故成为了我们面临的一个严重问题。
碰撞事故是其中最常见也是最危险的一种。
为了保障驾乘人员的生命安全,汽车碰撞安全设计成为了整个汽车行业中的一项重要规范。
一、碰撞安全设计的背景与意义车辆的碰撞安全设计旨在降低碰撞事故对人员以及车辆造成的伤害和损失。
这不仅是为了维护人们的生命安全,也是为了遵循道路交通法规、道德伦理和社会责任。
因此,汽车制造商、设计师以及相关政府机构都应该对碰撞安全设计给予高度重视。
二、强化车身结构的碰撞安全能力车身结构是车辆的“躯体”,对于汽车的碰撞安全起着至关重要的作用。
在车身结构的设计中,需要注意以下几个方面:1. 使用高强度材料,例如钢铁、铝合金等,以提高车身结构的抗冲击能力。
2. 采用变形区、吸能结构等设计,将碰撞时的冲击力分散和吸收,减少乘员的受伤程度。
3. 优化车架结构,确保车辆在碰撞时能维持良好的结构完整性,避免发生车身断裂等严重事故。
三、加强安全气囊的设计和应用安全气囊是现代汽车中最具影响力的被动安全装备之一。
正确的安全气囊设计和应用可以大大减轻乘员在碰撞时的伤害。
以下是一些安全气囊设计方面的考虑:1. 为驾驶员和乘客设置多个安全气囊,以覆盖可能发生碰撞的各个方向。
2. 根据碰撞的类型和严重程度,对安全气囊的充气力度和速度进行合理调整,减少因气囊充气过度而导致的二次伤害。
3. 结合传感器和智能控制系统,实现精确的碰撞检测和气囊展开时机的判断,确保安全气囊能在碰撞发生前或发生时迅速展开。
四、提升座椅安全设计除了车身结构和安全气囊,座椅也是汽车碰撞安全的重要组成部分。
以下是一些提升座椅安全设计的关键要点:1. 座椅应具备良好的支撑力和稳定性,能够在碰撞时防止乘员因惯性而发生强烈的前后移动。
2. 采用可调节头枕和腰部支撑器等设计,以提供更好的乘员支撑和减少颈部和腰部的伤害。
3. 结合安全带预紧力限制器等装置,确保座椅和牢固的安全带系统能够最大限度地减少乘员在碰撞时的伤害。
车架的设计方法

车架是汽车的骨架,承担着支撑、连接和保护车辆各部件的重要作用。
车架的设计方法通常包括以下几个方面:
1.结构设计:车架结构需考虑车辆的使用条件、总质量和预期性能,如承载能力、刚度和稳定性。
常见的车架结构包括前置驱动、后置驱动和四驱,可选择框架式、单体式或混合式设计。
2.材料选择:车架的材料选择应考虑强度、刚度、重量和经济性。
常见的材料包括钢材、铝合金和纤维复合材料等。
根据车辆的类型和要求,选择适当的材料组合,并进行合理的加工和焊接工艺。
3.结构优化:通过结构优化方法,如有限元分析和拓扑优化,对车架进行强度和刚度分析,并优化构件的形状和布局,以实现最佳结构性能。
优化还可考虑车辆的空气动力学、减震和降噪等方面。
4.耐久性和安全性:车架设计需要满足车辆的长期使用要求,并在碰撞和事故时提供足够的保护。
通过应用刚度、强度和承载能力测试和模拟碰撞试验,确保车架的耐久性和安全性。
5.制造和装配:车架设计要考虑到制造和装配的可行性和效率。
设计结构合理,以便于制造工艺,减少成本和浪费。
同时,增加装配精度和可靠性,提高车架的建造质量。
综合利用上述设计方法,可以实现车架设计的性能、经济性和安全性的综合平衡。
同时,符合国家相关安全标准和法规,确保设计和制造的车架符合政策要求,提高车辆的可靠性和行驶安全性。
汽车设计与安全性能的关系分析
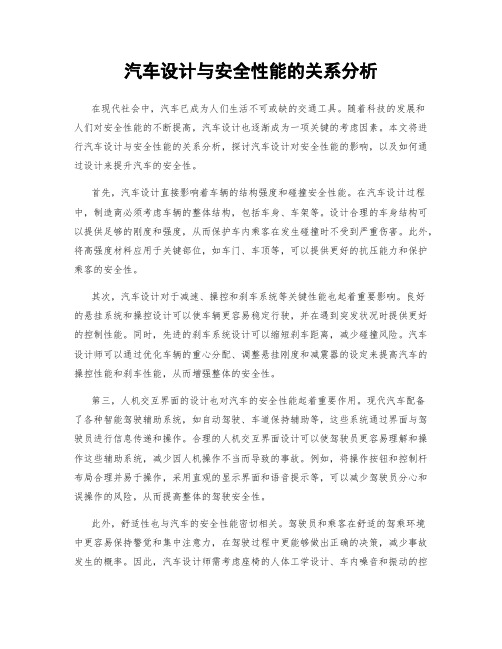
汽车设计与安全性能的关系分析在现代社会中,汽车已成为人们生活不可或缺的交通工具。
随着科技的发展和人们对安全性能的不断提高,汽车设计也逐渐成为一项关键的考虑因素。
本文将进行汽车设计与安全性能的关系分析,探讨汽车设计对安全性能的影响,以及如何通过设计来提升汽车的安全性。
首先,汽车设计直接影响着车辆的结构强度和碰撞安全性能。
在汽车设计过程中,制造商必须考虑车辆的整体结构,包括车身、车架等。
设计合理的车身结构可以提供足够的刚度和强度,从而保护车内乘客在发生碰撞时不受到严重伤害。
此外,将高强度材料应用于关键部位,如车门、车顶等,可以提供更好的抗压能力和保护乘客的安全性。
其次,汽车设计对于减速、操控和刹车系统等关键性能也起着重要影响。
良好的悬挂系统和操控设计可以使车辆更容易稳定行驶,并在遇到突发状况时提供更好的控制性能。
同时,先进的刹车系统设计可以缩短刹车距离,减少碰撞风险。
汽车设计师可以通过优化车辆的重心分配、调整悬挂刚度和减震器的设定来提高汽车的操控性能和刹车性能,从而增强整体的安全性。
第三,人机交互界面的设计也对汽车的安全性能起着重要作用。
现代汽车配备了各种智能驾驶辅助系统,如自动驾驶、车道保持辅助等,这些系统通过界面与驾驶员进行信息传递和操作。
合理的人机交互界面设计可以使驾驶员更容易理解和操作这些辅助系统,减少因人机操作不当而导致的事故。
例如,将操作按钮和控制杆布局合理并易于操作,采用直观的显示界面和语音提示等,可以减少驾驶员分心和误操作的风险,从而提高整体的驾驶安全性。
此外,舒适性也与汽车的安全性能密切相关。
驾驶员和乘客在舒适的驾乘环境中更容易保持警觉和集中注意力,在驾驶过程中更能够做出正确的决策,减少事故发生的概率。
因此,汽车设计师需考虑座椅的人体工学设计、车内噪音和振动的控制,以及空调和通风系统的舒适性等因素。
通过提供良好的舒适性设计,可以降低驾驶员和乘客的疲劳程度,提高驾驶的安全性和舒适性。
汽车底盘系统的结构设计及优化
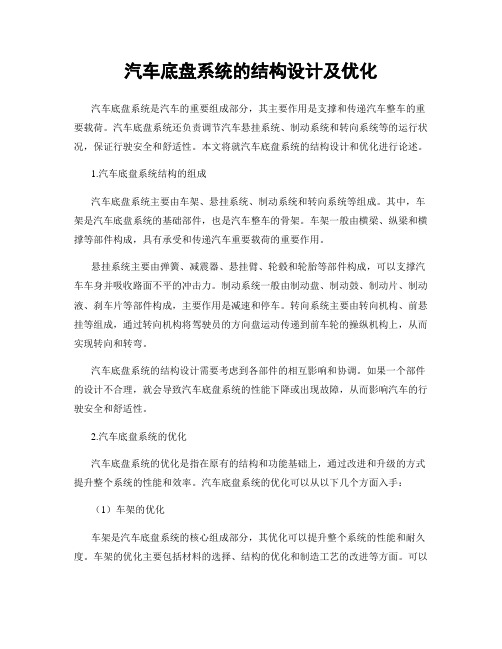
汽车底盘系统的结构设计及优化汽车底盘系统是汽车的重要组成部分,其主要作用是支撑和传递汽车整车的重要载荷。
汽车底盘系统还负责调节汽车悬挂系统、制动系统和转向系统等的运行状况,保证行驶安全和舒适性。
本文将就汽车底盘系统的结构设计和优化进行论述。
1.汽车底盘系统结构的组成汽车底盘系统主要由车架、悬挂系统、制动系统和转向系统等组成。
其中,车架是汽车底盘系统的基础部件,也是汽车整车的骨架。
车架一般由横梁、纵梁和横撑等部件构成,具有承受和传递汽车重要载荷的重要作用。
悬挂系统主要由弹簧、减震器、悬挂臂、轮毂和轮胎等部件构成,可以支撑汽车车身并吸收路面不平的冲击力。
制动系统一般由制动盘、制动鼓、制动片、制动液、刹车片等部件构成,主要作用是减速和停车。
转向系统主要由转向机构、前悬挂等组成,通过转向机构将驾驶员的方向盘运动传递到前车轮的操纵机构上,从而实现转向和转弯。
汽车底盘系统的结构设计需要考虑到各部件的相互影响和协调。
如果一个部件的设计不合理,就会导致汽车底盘系统的性能下降或出现故障,从而影响汽车的行驶安全和舒适性。
2.汽车底盘系统的优化汽车底盘系统的优化是指在原有的结构和功能基础上,通过改进和升级的方式提升整个系统的性能和效率。
汽车底盘系统的优化可以从以下几个方面入手:(1)车架的优化车架是汽车底盘系统的核心组成部分,其优化可以提升整个系统的性能和耐久度。
车架的优化主要包括材料的选择、结构的优化和制造工艺的改进等方面。
可以采用高强度的轻质材料,比如铝合金、碳纤维等来制造车架,从而降低汽车整车的重量。
此外,车架的优化还可以通过模拟分析和试车验证等方法来实现。
(2)悬挂系统的优化悬挂系统是汽车底盘系统的重要部分,其优化可以提高汽车的行驶舒适性和稳定性。
悬挂系统的优化包括弹簧和减震器的调整、悬挂臂的结构优化和轮胎的选择等方面。
可以采用可调节的悬挂系统,根据驾驶需求来调整弹簧和减震器的硬度和软度。
此外,采用适合路面条件的轮胎也可以提高汽车的行驶稳定性和舒适性。
FASE方程式赛车车架设计报告

FASE方程式赛车车架设计报告摘要:本报告基于FASE(Formula Alchemist Speed Engineering)方程式赛车车架设计,对车架结构、材料选择和制造工艺进行了详细探讨。
该设计旨在提高赛车的性能和安全性,并满足赛车比赛规则的要求。
经过分析和测试,本设计成功改进了车架结构,优化了材料选择,并改进了制造工艺。
最终的车架具有良好的刚度、轻量化和耐久性。
1.引言FASE方程式赛车车架设计的关键目标是提高赛车的性能和安全性。
赛车车架是车辆的重要组成部分,它承担着支撑车身、吸收冲击、提供瞄准器和悬挂等功能。
一个优秀的车架设计应该具备良好的刚度、轻量化、耐久性和灵活性。
2.参数规定根据FASE方程式赛车比赛规则,车架设计必须符合一系列参数规定,如最大长度、宽度、高度和重量等。
本设计严格按照这些规定进行设计,并在此基础上进行了优化。
3.车架结构设计车架结构的设计对整个赛车的性能有着重要影响。
本设计采用了单壳式车架结构,由前护舱、驾驶舱、后部结构和底盘组成。
此结构可以提供良好的车身刚度和耐撞击性能,同时减少了重量和气动阻力。
4.材料选择材料的选择在车架设计中至关重要,它直接影响车架的刚度、重量和安全性。
为了满足轻量化和刚度的要求,本设计选择了高强度铝合金作为主要材料。
这种材料具有较高的强度和良好的疲劳性能,在保证车身结构强度的前提下可以减少重量。
5.制造工艺制造工艺是确保车架质量和性能的关键环节。
本设计使用了先进的焊接工艺,采用机器焊接以提高精度和一致性。
此外,对于关键焊接部位,采用了复合焊接工艺来提高强度和耐久性。
6.结果与讨论经过测试和仿真分析,本设计所得到的车架在各项性能指标上均达到了预期目标。
其刚度足够高,能够满足高速赛车的要求;重量轻,有利于提高赛车的加速性能和操控性;同时,车架的耐久性也得到了提高。
7.结论本报告提供了基于FASE方程式赛车的车架设计方案。
通过对车架结构、材料选择和制造工艺的优化,得到了满足比赛规则并具有良好性能的车架。
车架设计 (2)

车架设计简介车架是整个车辆的支撑结构,承载着车辆的重量以及各种力的作用。
一个合理设计的车架能够提供足够的刚性和强度,以确保车辆在各种环境下的平稳行驶和安全性。
本文将介绍车架设计的基本原理、常见的设计要素以及一些优秀的车架设计案例。
基本原理刚性和强度车架的刚性和强度是车架设计的两个最基本的要求。
刚性指的是车架在受力作用下不易变形的能力,而强度则是车架抵抗扭曲和断裂的能力。
一个刚性和强度兼顾的车架设计能够提供稳定的操控性和安全性。
材料选择车架的材料选择直接影响到车架的刚性和强度。
常用的车架材料包括铝合金、碳纤维和钢等。
铝合金车架具有良好的刚性和强度,并且相对较轻,适合一般用途的车辆。
碳纤维车架具有更高的强度和刚度,但也更加昂贵。
钢材车架则具有较高的耐久性和吸震性能。
结构设计车架的结构设计是保证刚性和强度的关键。
常见的车架结构包括平行四边形结构、三角形结构和梯形结构等。
这些结构能够有效地分散受力并提高整体刚性。
另外,还可以通过使用增加支撑杆和加强筋等加强点来进一步提高车架的强度。
设计要素几何形状车架的几何形状直接影响了车辆的外观和性能。
常见的几何形状包括三角形、梯形和曲线等。
三角形结构常被认为是最稳定的结构,具有良好的刚性和强度。
梯形结构则可同时提供强度和舒适性。
曲线形状的车架则更注重外观设计和空气动力学性能。
重量和刚性比重量和刚性之间的平衡是车架设计的重要考虑因素。
过重的车架会增加车辆的油耗和操控难度,而过轻的车架则会牺牲刚性和强度。
设计者需要根据车辆的用途和预期性能选择合适的重量和刚性比。
在某些高性能车辆中,为了追求更高的刚性和强度,会使用更轻的材料来减少整体重量。
吸震性能车架的设计也应该关注车辆的吸震性能。
好的吸震性能能够提供更舒适的乘坐体验,并减少对驾驶员和乘客的不适和疲劳。
一些现代车架设计中使用了可调节的悬挂系统和吸震器来提高吸震性能。
优秀设计案例Porsche 911Porsche 911是一款著名的高性能跑车,其车架设计被广泛认为是行业标杆。
汽车车架实验报告
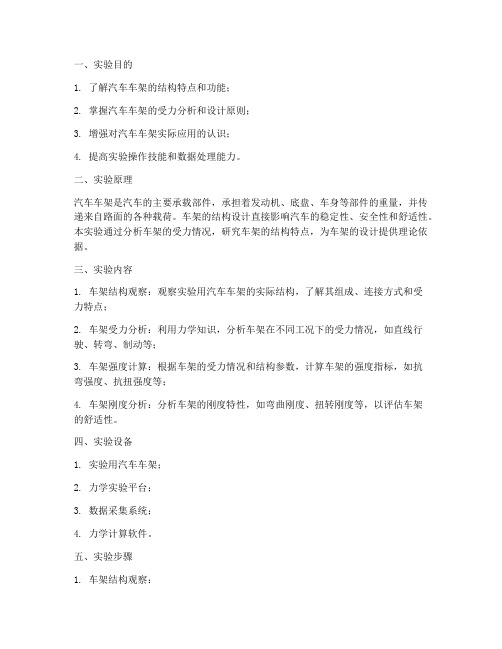
一、实验目的1. 了解汽车车架的结构特点和功能;2. 掌握汽车车架的受力分析和设计原则;3. 增强对汽车车架实际应用的认识;4. 提高实验操作技能和数据处理能力。
二、实验原理汽车车架是汽车的主要承载部件,承担着发动机、底盘、车身等部件的重量,并传递来自路面的各种载荷。
车架的结构设计直接影响汽车的稳定性、安全性和舒适性。
本实验通过分析车架的受力情况,研究车架的结构特点,为车架的设计提供理论依据。
三、实验内容1. 车架结构观察:观察实验用汽车车架的实际结构,了解其组成、连接方式和受力特点;2. 车架受力分析:利用力学知识,分析车架在不同工况下的受力情况,如直线行驶、转弯、制动等;3. 车架强度计算:根据车架的受力情况和结构参数,计算车架的强度指标,如抗弯强度、抗扭强度等;4. 车架刚度分析:分析车架的刚度特性,如弯曲刚度、扭转刚度等,以评估车架的舒适性。
四、实验设备1. 实验用汽车车架;2. 力学实验平台;3. 数据采集系统;4. 力学计算软件。
五、实验步骤1. 车架结构观察:- 观察车架的整体结构,记录其主要部件、连接方式和受力特点;- 拆卸部分零件,观察内部结构,了解车架的细节设计。
2. 车架受力分析:- 在力学实验平台上搭建车架模型,模拟不同工况下的受力情况;- 利用数据采集系统,测量车架在不同工况下的受力数据。
3. 车架强度计算:- 根据受力数据和车架结构参数,利用力学计算软件计算车架的强度指标; - 分析计算结果,评估车架的强度是否满足设计要求。
4. 车架刚度分析:- 在力学实验平台上进行车架刚度测试,测量车架的弯曲刚度和扭转刚度; - 分析测试结果,评估车架的刚度特性。
六、实验结果与分析1. 车架结构特点:- 车架采用梯形结构,具有良好的承载能力和稳定性;- 车架主要采用焊接连接,连接强度高,可靠性好。
2. 车架受力分析:- 在直线行驶工况下,车架主要承受垂直载荷和横向载荷;- 在转弯工况下,车架还承受纵向载荷和侧向载荷;- 在制动工况下,车架主要承受纵向载荷。
车架设计_精品文档
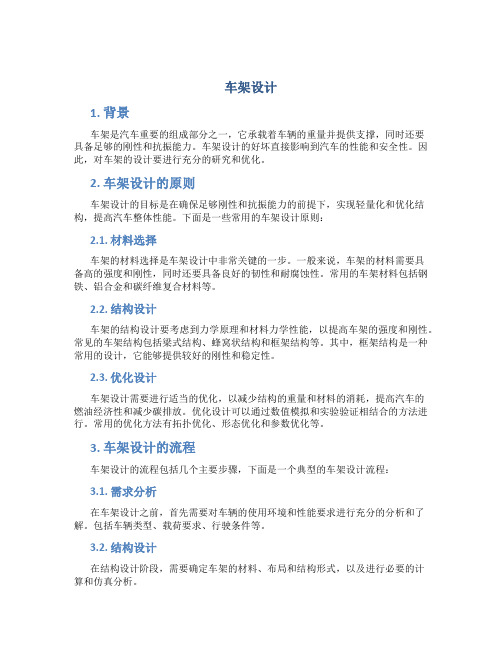
车架设计1. 背景车架是汽车重要的组成部分之一,它承载着车辆的重量并提供支撑,同时还要具备足够的刚性和抗振能力。
车架设计的好坏直接影响到汽车的性能和安全性。
因此,对车架的设计要进行充分的研究和优化。
2. 车架设计的原则车架设计的目标是在确保足够刚性和抗振能力的前提下,实现轻量化和优化结构,提高汽车整体性能。
下面是一些常用的车架设计原则:2.1. 材料选择车架的材料选择是车架设计中非常关键的一步。
一般来说,车架的材料需要具备高的强度和刚性,同时还要具备良好的韧性和耐腐蚀性。
常用的车架材料包括钢铁、铝合金和碳纤维复合材料等。
2.2. 结构设计车架的结构设计要考虑到力学原理和材料力学性能,以提高车架的强度和刚性。
常见的车架结构包括梁式结构、蜂窝状结构和框架结构等。
其中,框架结构是一种常用的设计,它能够提供较好的刚性和稳定性。
2.3. 优化设计车架设计需要进行适当的优化,以减少结构的重量和材料的消耗,提高汽车的燃油经济性和减少碳排放。
优化设计可以通过数值模拟和实验验证相结合的方法进行。
常用的优化方法有拓扑优化、形态优化和参数优化等。
3. 车架设计的流程车架设计的流程包括几个主要步骤,下面是一个典型的车架设计流程:3.1. 需求分析在车架设计之前,首先需要对车辆的使用环境和性能要求进行充分的分析和了解。
包括车辆类型、载荷要求、行驶条件等。
3.2. 结构设计在结构设计阶段,需要确定车架的材料、布局和结构形式,以及进行必要的计算和仿真分析。
3.3. 优化设计在结构设计的基础上,对车架结构进行优化设计,以提高车架的性能和轻量化。
3.4. 材料选型根据结构设计和优化设计的结果,选择合适的材料,并进行材料性能测试和评估。
3.5. 制造与测试最后,根据设计结果制造车架样品,并进行测试和验证。
包括静态试验、动态试验和可靠性试验等。
4. 车架设计的挑战与发展趋势4.1. 轻量化与强度平衡车架设计的一个主要挑战是如何在追求轻量化的同时,保证车架的足够强度和刚性。
- 1、下载文档前请自行甄别文档内容的完整性,平台不提供额外的编辑、内容补充、找答案等附加服务。
- 2、"仅部分预览"的文档,不可在线预览部分如存在完整性等问题,可反馈申请退款(可完整预览的文档不适用该条件!)。
- 3、如文档侵犯您的权益,请联系客服反馈,我们会尽快为您处理(人工客服工作时间:9:00-18:30)。
车架设计与汽车的安全性
2004年11月11日锋线汽车
一部车的性能除了取决于引擎动力的大小,操控也是不容忽视的另一因素,但是要造出优异的操控,悬挂结构的设计就显得相当重要。
除此之外,车架的刚性也是必不可少的先决条件。
早期的车架设计
“车架”这个名称原本是从法文的“Chassis”衍生而来的,早期汽车所使用的车架,大多都是由笼状的钢骨梁柱所构成的,也就是在两支平行的主梁上,以类似阶梯的方式加上许多左右相连的副梁制造而成。
车体建构在车架之上,至于车门、沙板、引擎盖、行李厢盖等钣件,则是另外再包覆于车体之外,因此车体与车架其实是属于两个独立的构造。
这种设计的最大好处,在于轻量化与刚性得以同时兼顾,因此受到了不少跑车制造商的青睐,早期的法拉利与兰博基尼都是采用的这种设计。
由于钢骨设计的车架必须通过许多接点来连结主梁和副梁,加之笼状构造也无法腾出较大的空间,因此除了制造上比较复杂、不利于大量生产之外,也不适合用在强调空间的四门房车上。
随后单体结构的车架在车坛上成为主流,笼状的钢骨车架也逐渐改由这种将车体与车架合二为一的单体车架所取代,这种单体车架一般以“底盘”称之,也就是衍生自英文的“Platform”。
单体式车架
关于单体车架(Monocoque):简单的说就是将引擎室、车厢以及行李厢三个空间合而为一,这样的好处除了便于大量生产,模组化的运用也是其中主要的考虑。
通过采取模组化生产的共用策略,车厂可以将同一具车架分别使用在数种不同的车款上,这样也可节省不少研发经费。
例如大众VAG旗下就有多种车款使用相同的车架,通用(GM)的绅宝、富士也有不少车款如法炮制。
除了有利于共用,车体车架也可以通过材料的不同来发挥轻量化的特性,例如本田NSX所使用的铝合金以及法拉利F50、Enzo所使用的碳纤维材料等。
铝合金是80年代末期相当热门的一种工业材料,虽然重量比铁轻,但是强度却较差,因此如果要用铝合金制成单体车架,虽然在重量上比起铁制车架更占优势,但是强度却无法达到和铁制车架同样的水准。
除非增加更多的铝合金材料,利用更多的用量来弥补强度上的不足。
不过这样一来,重量必然会相对增加,而原本出于轻量化考量而采用铝合金材料的动机,当然也就失去了意义。
也正因为这个原因,铝合金车架在车坛上并未成为主流,少数高性能跑车或是使用了强度更高的碳纤维,或是用碳纤维结合蜂巢状夹层铝合金的复合材料取代了铝合金。
但是要用碳纤维制成单体车架,在制作上相当复杂且费时,成本也相对更高,所以至今仍无法普及到一般市售车上,而仅有少数售价高昂的跑车使用。
尽管铝合金车架鲜有车厂使用,不过用钢铁车架搭配铝合金钣件的方式,近年来却受到不少车厂的重视,这样的结构不仅可以保留车架本身的强度,同时也可以通过钣件的铝合金化来取得轻量化效果,在研发成本上自然也不像碳纤维制的单体车架那样昂贵。
关于车架刚性
很多人都知道刚性的良好与否会直接影响到一部车的操控,但是所谓的车架刚性究竟指的是什么?而刚性不足又会带来哪些后果呢?简单的说,车架所要求的刚性其实就建构在车架的抗变形能力上,也就是指车架对于受外力影响而弯曲或扭转的抗力。
一旦车架刚性不足,操控性便会受到影响。
试想前轮因车架变形而导致转向时出现时间差,或是轮胎与路面的接地性不良而影响到循迹性与抓地力等,肯定都会使操纵性无法发挥出原有的水准。
影响车架刚性的外力,通常是来自于路面磨擦力以及加减速或过弯时产生的G值。
早期的汽车由于引擎及底盘设计不像现在发达,轮胎的抓地力也不如今日优异,因此车架刚性的重要性并不容易被关注。
但是近年来市售车所搭载的引擎已有不错的动力,许多车都拥有200km/h以上的极速,而且除了轮胎进化成抓地力更好的辐射层构造,低扁平比薄胎与大直径化的设定也成为了
市场的主流,因此在动力有所提升、轮胎与悬挂所承受的负荷增大并且转移至车架的情况下,车架本身承受的负荷肯定也会大幅提高,而车架刚性的良好与否也就显得更为重要。
车辆重量增加源于安全需要
除此之外,欧美从90年代开始逐渐提高了撞击事故的安全防护标准,这也是凸现出车架刚性重要的另一原因。
许多车厂为了在撞击事故发生时能够确保车内乘员的安全,惟有针对车架以及车体进行全面强化,这也使得除了车架以外的强度有所改善,包括钣件厚度的改变以及各种辅助梁的增设也成为各厂惯用的手法。
不过在这样的情况下,伴随而来的是车重相对增加,这也正是欧美日许多市售车的重量比起10年前、20年前增加不少的主要原因。
关于刚性的确保,大多数车厂在新车的设计阶段,都是利用电脑计算出车架的刚性需求,并以此作为设计依据。
有些车厂在用电脑完成设计雏形后,还会再由专业的试车人员进行实际测试。
不过在前面提到的模组化策略运用下,由于同一车架可能会使用在不同需求的车款上,例如宝马3系列中就有动力最小的1.8升318i和最大的3.2升M3,三菱Lancer车系也有入门级的1.3
升Cedia和2.0Turbo的Lancer EVO,由于不同的车种在动力输出上相差甚远,车架所承受的负荷也截然不同,因此要以相同的车架来对应不同车种,可是有不少学问。
如果要以刚性为首要考虑,最理想的对策当然是以能够承受最大负荷的车架来对应所有引擎,宝马即是采取这样的方式。
尽管318i的最大马力不及M3的一半,但是车架却是使用和M3如出一辙的设计标准。
在车架刚性远胜过引擎动力的条件下,操控品质和整体稳定性具有极高的水准。
不过多数日系车厂却并非采取这样的方式,例如三菱即是以入门型的Cedia车架来对应性能版的Lancer EVO引擎,至于刚性不足的部分,则是再另外通过补强的手法来解决。
这也就是近来包括Lancer EVO或Civic Type R等强调高性能的日系车,在出厂时都已经将引擎室撑杆列为标准配备的主要原因。
关于日本车的安全性
但是无论上述何种方式,其实都很难定论出绝对的优劣性,毕竟德国车和日本车先天就有太多不同的设计理念与使用需求。
德国拥有无限速的Autobahn,在动力允许的情况下,要以超过200km/h的速度巡航对于很多人来说司空见惯,车厂在研发新车之际,当然也会考虑到这种行车速度下的操控与安全性。
但是日本高速道路的速限只有100km/h,而且市售车的极速也必须遵守不得超过180km/h的自主限制,车厂自然不会也没有必要考虑到180km/h之后的操控与安全性。
很多人认为日本车的安全性不如德国车,车体刚性及底盘稳定性也是如此,其实就是由于上述先天不足的设计理念与使用需求所致。
关于车体的安全防护,在过去要确保车内乘员的安全,最有效的办法就是从汽车承受撞击力道的能力来着手,也就是在遭遇撞击时将变形的程度控制到最低。
因此许多车厂在强化车架之余,同时也为车体换上更厚实的钣件,沃尔沃即是其中最具代表性的车厂之一。
不过近年来,这样的安全防护逻辑已经有所转变,因为除了高速状态下的“车对车”撞击事故外,发生在市区街道的“车对人”撞击事故,也是目前许多车厂关注的焦点,道路状况比欧美国家更为拥挤的日本尤为明显。
安全防护观念的扩大
为了将安全防护的范围从车内乘员扩大到车外的行人及骑车者,本田旗下市售车在2000年开始引入了G-CON理念,开始完全打破了过去沃尔沃所强调的安全概念。
本田的G-CON理念,并非利用更厚、更硬的钣件来抑制车体变形的程度,反倒是通过适度的变形或溃缩来将撞击力道予以吸收,这样更有助于减轻行人或骑车者在被直接撞击时所受到的伤害。
但是要如何在车对车的撞击事故发生时,利用最低限度的车厢变形来确保车内乘员的安全,同时又能够在车对人的状况下,通过车体钣件的适度变形来减轻车外行人或骑车者所受到的伤害呢?
诸如此类的两极对立问题,其实在汽车的空气力学上也同样可以见到,例如以往高性能跑车基于操控性的考虑,多半会以牺牲风阻系数来换取更大的下压力。
但是近年来法拉利火爆时都已不再利用车外装设的空力套件来增加下压力。
甚至连尾翼都简化许多,因为加装在车外的扰流装置虽然可以造就更大下压力,但是却会使风阻系数相对增大,对于极速和油耗全然没有帮助。
不过目前包括Enzo、F360或Carrera GT这一类跑车,都已经发展出通过底盘的先进造型来产生地面吸附效应的技术,这样的效果不仅等同于从车外获得下压力,同时也不会因外形上的改变而破坏风阻系数。
今后的课题
要想在车厢空间的确保与车体撞击吸收能力之间取得平衡,或是同时兼顾两者,根本之道就是以高强度的车架来搭配具有溃缩设计的车体。
不过说起来好像很简单,实际上却存在着不少必须克服的困难,例如引擎的体积就直接影响到车头的溃缩范围,引擎越小,当然越有利于吸收撞击力道,但是动力输出势必也会更受限制,而使用在保险杠或其他部位具有缓冲特性的材料,又会与资源再利用的环保理念相违背。
上述因素,甚至包括研发成本的考虑等,都是攸关整体成效的主要因素之一。
当然,这些也正是今后各厂所必须努力的重要课题。
作者:编辑:于妍来源:。