第八章连铸坯的质量控制
连铸坯质量控制培训课件

连铸坯质量控制培训课件1. 引言连铸坯是金属材料的重要中间产品,在金属加工和制造业中具有重要意义。
为了保证连铸坯的质量,提高生产效率,需要进行严格的质量控制。
本课件将介绍连铸坯质量控制的基本原理和方法,帮助学员全面了解连铸坯质量控制的重要性和具体操作方法。
2. 连铸坯质量控制的重要性连铸坯质量控制对金属材料的加工和制造有着重要的影响。
以下是连铸坯质量控制的重要性的几个方面:2.1 提高材料的机械性能连铸坯的质量直接影响材料的机械性能。
合理控制连铸坯的化学成分和冶炼工艺,可以提高材料的强度、硬度和韧性等机械性能,满足不同应用领域对材料性能的要求。
2.2 降低材料的缺陷率连铸坯的质量控制还能够降低材料的缺陷率。
通过优化连铸装备和操作技术,减少连铸坯中的气孔、夹杂物等缺陷的产生,提高材料的质量和可靠性。
2.3 增加生产效率连铸坯质量的控制还能够提高生产效率。
优质的连铸坯可以减少后续的加工工序,提高生产线的运转效率,降低生产成本。
3. 连铸坯质量控制的基本原理连铸坯质量控制的基本原理包括以下几个方面:3.1 坯料的选择与质量控制合理选择适合连铸工艺要求的坯料对于连铸坯质量的控制至关重要。
坯料的化学成分、净化程度和加热制度等都会直接影响连铸坯的质量。
因此,通过坯料的质量控制,可以保证连铸坯的理化性能符合要求。
连铸操作的控制是保证连铸坯质量的关键环节。
合理控制连铸过程中的操作参数,包括结晶器冷却水量、拉速、浇注流量等,可以减少连铸坯的缺陷,提高连铸坯的尺寸精度和表面质量。
3.3 质量检测方法与设备连铸坯质量的控制还需要依靠科学有效的质量检测方法和设备。
常用的质量检测方法包括化学分析、金相检测、机械性能测试等。
而质量检测设备的选择和使用也直接影响连铸坯质量的控制效果。
4. 连铸坯质量控制的具体操作方法连铸坯质量控制的具体操作方法如下:4.1 坯料质量控制•选择符合连铸工艺要求的坯料,并对坯料进行化学成分、净化程度和加热制度等质量检测。
连铸工艺、设备--09连铸坯质量控制
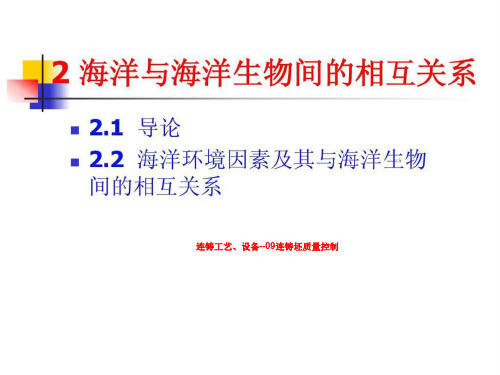
3.影响夹杂物的因素
A.机型对铸坯中夹杂物的影响
在工艺条件一定的情况下,夹杂物在铸坯内 的数量和连铸机铸坯内弧侧的弯曲区,固液界面容 易捕捉上浮的夹杂物,在内弧表面10mm左右 形成Al2O3的聚集,大颗粒夹杂在内弧侧 1∕4~1∕5厚度形成集聚,这是弧形连铸机 的弱点。
2.连铸坯中夹杂物的类型和来源
类型:取决于浇注钢种和脱氧方法。在连铸 坯中较常见的夹杂物有Al2O3和以SiO2为主并 含有MnO和CaO的硅酸盐,以及以Al2O3为主 并含有SiO2、CaO 和CaS等的铝酸盐。此外还 有硫化物如FeS、MnS等。
来源:出钢过程钢液氧化产物占10%,脱氧产 物占15%,熔渣卷入占5%,注流的二次氧化 占40%,耐火材料的冲刷约占20%,中间包渣 约占10%。可见,铸坯中基本上是外来夹杂 物,主要来自于钢液浇注过程中的二次氧化。
即在弯月面区域75mm的铜板内镶入不锈 钢、镀Cr、Ni或碳铬化合物的隔热材料, 使结晶器的热流密度可以减少50~70%, 延缓了坯壳的收缩,减轻了凹陷深度从而 减少了裂纹的发生率。
带不锈钢插件的热顶结晶器 1—镀镍层; 2—不锈钢插件; 3—铜基板
带陶瓷插件的热顶结晶器:
1—浸入式水口; 2—保护渣; 3—陶瓷结晶器; 4—铜结晶器; 5—坯壳
中间包采用大容量、加挡墙和坝等促进夹 杂物上浮的有效措施。还有中 间包吹氩、 使用过滤器、复合渣,以及使用碱性包衬 等,都有利于中间包进一步净化钢液。
5.连铸系统选用耐火度高,融损小,高质量的 耐火材料,以减少钢中外来夹杂物。
6.充分发挥结晶器的钢液净化器和铸坯表面质 量控制器的作用;
7.采用电磁搅拌技术,控制注流的运动。
2.钢中夹杂物分类:
① 超显微夹杂,均匀分布在钢中;
连铸坯质量及控制方法

连铸坯质量及控制方法1、连铸坯质量的含义是什么?最终产品质量决定于所供给的铸坯质量。
从广义来说,所谓连铸坯质量是指得到合格产品所允许的铸坯缺陷的严重程度。
它的含义是:——铸坯纯净度(夹杂物数量、形态、分布、气体等)。
——铸坯表面缺陷(裂纹、夹渣、气孔等)。
——铸坯内部缺陷(裂纹、偏析、夹杂等)。
铸坯纯净度主要决定于钢水进入结晶器之前处理过程。
也就是说要把钢水搞“干净”些,必须在钢水进入结晶器之前各工序下功夫,如冶炼及合金化过程控制、选择合适的炉外精炼、中间包冶金、保护浇注等。
铸坯的表面缺陷主要决定于钢水在结晶器的凝固过程。
它是与结晶器坯壳形成、结晶器液面波动、浸入式水口设计、保护渣性能有关的。
必须控制影响表面质量各参数在目标值以内,以生产无缺陷铸坯,这是热送和直接扎制的前提。
铸坯的内部缺陷主要决定于在二次冷却区铸坯冷却过程和铸坯支撑系统。
合理的二次冷却水分布、支承辊的对中、防止铸坯鼓肚等是提高铸坯内部质量的前担。
因此,为了获得良好的铸坯质量,可以根据钢种和产品的不同要求,在连铸的不同阶段如钢包、中间包、结晶器和二次冷却区采用不同的工艺技术,对铸坯质量进行有效控制。
2、提高连铸钢种的纯净度有哪些措施?纯净度是指钢中非金属夹杂物的数量、形态和分布。
要根据钢种和产品质量,把钢中夹杂物降到所要求的水平,应从以下五方面着手:——尽可能降低钢中[O]含量;——防止钢水与空气作用;——减少钢水与耐火材料的相互作用;——减少渣子卷入钢水内;——改善钢水流动性促进钢水中夹杂物上浮。
从工艺操作上,应采取以下措施:(1)无渣出钢:转炉采用挡渣球(或挡渣锥),防止钢渣大量下到钢包。
(2)钢包精炼:根据钢种选择合适的精炼方法,以均匀温度、微调成分、降低氧含量、去除气体夹杂物等。
(3)无氧化浇注:钢水经钢包精炼处理后,钢中总氧含量可由130ppm下降到20ppm以下。
如钢包→中间包注流不保护或保护不良,则中间包钢水中总氧量又上升到60~100ppm范围,恢复到接近炉外精炼前的水平,使炉外精炼的效果前功尽弃。
连铸圆坯质量控制

连铸圆坯质量控制连铸坯质量检验及控制一、连铸坯的内部结构(凝固组织)的一般特征及检验。
连铸坯的检验方法连铸坯的内部结构:经过酸浸(酸洗)或硫印的方法在连铸坯横断面或纵断面上用肉眼或低倍放大镜看到内部组织结果。
硫印硫印是用感光相纸显示试样上硫偏析(合金中各组成元素在结晶时分布不均匀的现象称为偏析)的方法,主要用于钢铁行业铸坯质量的检验。
从铸坯上取纵向或横向试样,试验面加工的光洁度不应低于6。
使用反差大的溴化银表面相纸,把与试样大小相同的相纸放入稀硫酸中浸泡1-2分钟后取出,将相纸对准检查面轻轻覆盖好,将试样与相纸间气泡赶净,待接触2-5分钟后取下,将相纸在流水中冲洗,然后定影烘干,即完成一张硫印。
印基本原理:硫酸与试样上的硫化物(FeS、MnS)发生反应,生成硫化氢气体,硫化氢气体再与感光相纸上的溴化银作用,生成硫化银沉淀在相纸相应的位置上,形成黑色或褐色斑点。
用硫印试验,可显示钢锭、连铸坯中心裂纹、偏析线、低倍结构和夹杂分布等。
酸洗用酸液洗去基体表面锈蚀物和轧皮的过程。
用酸浸或硫印法所显示的组织结构属于宏观结构,是连铸坯和金属材料检验中最为常见的检验技术。
连铸坯的内部结构连铸坯自表面至中心都是由边缘等轴晶区(激冷区)、柱状晶区和中心等轴晶,区三部分组成。
温度梯度较大时,固液两相区(图1)小,有利于柱状晶的生长,而凝固速度较快,则易于生成枝晶间距小的铸造组织,所以连铸坯具有较发达的柱状晶组织,并具有较小的枝晶间距。
(图1)枝晶间距是指相邻同次枝晶间的垂直距离,它是树枝晶组织细化程度的表征。
枝晶间距越小,组织就越细密,分布于其间的元素偏析范围也就越小,故越容易通过热处理而均匀化。
通常采用的有一次枝晶(柱状晶主干)间距d1,和二次分枝间距d2两种。
连铸坯宏观组织的好坏可以用等轴晶所占的比例多少来衡量,轴晶结构致密,加工性能能好。
柱状晶具有明显的方向性,加工性能差,容易导致中心偏析,中心疏松和中心裂纹等缺陷。
第八章连铸坯的质量控制课件
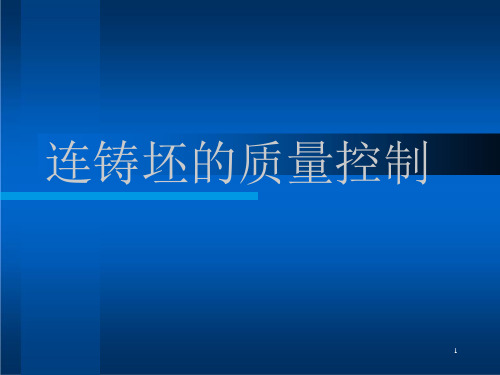
l提高铸坯洁净度的措施: (1)无渣出钢 (2)选择合适的精炼处理方式 (3)采用无氧化浇铸技术 (4)充分发挥中间包冶金净化的作用 (5)选用优质耐火材料 (6)充分发挥结晶器的作用 (7)采用电磁搅拌技术,控制铸流运动 7
三、铸坯表面质量及控制
l控制表面质量的必要性 l表面缺陷的形成 l表面裂纹的主要种类 l液面结壳 l凹坑和重皮
l连铸坯质量控制战略: 铸坯洁净度决定于 钢水进入结晶器之前的各工序;铸坯表面 质量决定于钢水在结晶器的凝固过程;铸 坯内部质量决定于钢水在二冷区的凝固过程。
3
二、铸坯的洁净度
l连铸坯洁净度评价包括: 钢中总氧量; 钢中微观夹杂物量 (<50μm); 钢中大颗粒夹杂物量 (>50μm)。
4
连铸夹杂物形成的显著特征
15
l预防措施: 1 、降低钢水中硫磷含量; 2、适当降低浇铸温度和浇铸速度; 3、控制结晶器的液面波动; 4、检查冷却水; 5 、选择合适黏度的保护渣。
16
3.3.3 表面横向裂纹
l原因:多发生在高碳钢中,当钢坯处于 高温脆性区时对其进行矫直所致。
l影响因素: 1 、结晶器振动不良;
2、辊子偏心;
l
安全放在第一位,防微杜渐。 10月-2310月-2302:21:1002:21:10Octo ber 11, 2023
l
加强自身建设,增强个人的休养。 2023年10月11日2:21 上午10月-2310月-23
l
精益求精,追求卓越,因为相信而伟大。 11 十月 20232:21:10上午02:21:1010月-23
13
3.3.2 表面纵向裂纹
l多发生在板坯宽面中央部位。 l原因:初生坯壳厚度不均匀,在坯壳
连铸坯的质量控制
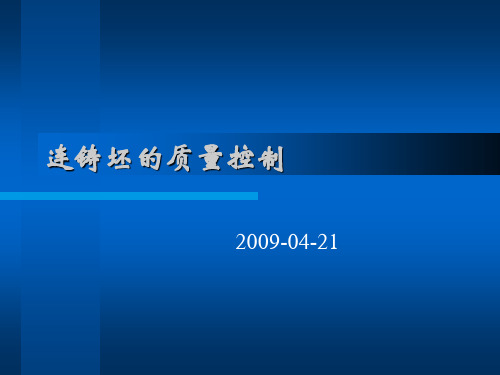
连铸坯的质量控制
2009-04-21
1、液相穴末端采用收缩 、 辊缝; 、 辊缝;2、改善铸坯导向 支撑系统; 、 支撑系统;3、更换弯曲 辊子; 、 辊子;4、调整浇铸温度 和速度; 、 和速度;5、维持正确的 结晶器锥度; 、 结晶器锥度;6、检查喷 水冷却系统; 、 水冷却系统;7、降低钢 水硫含量
夹杂物的控制
控制炼钢炉下渣量 钢包精炼渣的成分控制 保护浇铸 中间包控流装置 中间包覆盖剂 碱性包衬 钢种微细夹杂物去除 防止浇铸过程下渣和卷渣 防止Ar气泡吸附夹杂物 防止 气泡吸附夹杂物 结晶器钢水流动控制
缺
陷
原
因
主要影响因素
预防措施
内部横向裂纹
坯壳变形; 坯壳变形;坯壳受挤压
1、铸坯受弯曲力和矫 、 直力过大; 、 直力过大;2、支承辊 对正不良; 、 对正不良;3、坯壳鼓 肚;4、辊子偏心;5、 、辊子偏心; 、 钢水含硫量过大(> 钢水含硫量过大(> 0.02%) )
1、改善铸坯导向支撑系 、 统;2、更换弯曲辊子; 、更换弯曲辊子; 3、调整浇铸温度与速度; 、调整浇铸温度与速度; 4、降低钢水硫含量;5、 、降低钢水硫含量; 、 降低辊子接触压力
内 容
铸坯表面质量及控制 铸坯内部质量及控制 连铸坯形状缺陷及控制
铸坯表面质量
控制表面质量的必要性 表面缺陷形成原因:较为复杂, 表面缺陷形成原因:较为复杂,但总体 来讲, 来讲,主要是受结晶器内钢液凝固所控 制。
连铸坯质量控制
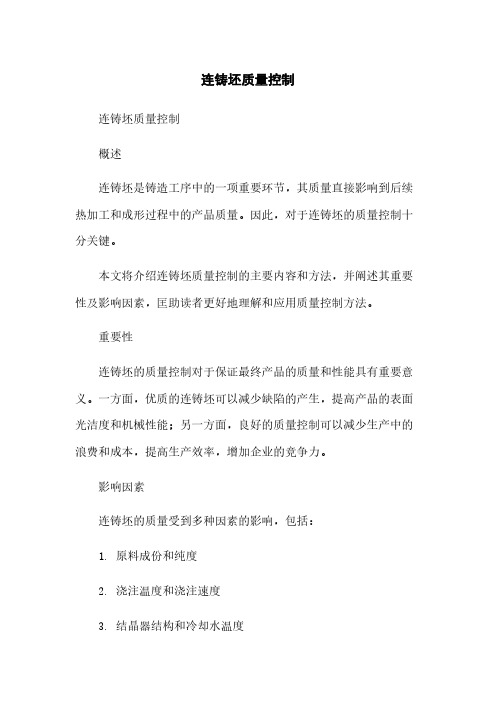
连铸坯质量控制连铸坯质量控制概述连铸坯是铸造工序中的一项重要环节,其质量直接影响到后续热加工和成形过程中的产品质量。
因此,对于连铸坯的质量控制十分关键。
本文将介绍连铸坯质量控制的主要内容和方法,并阐述其重要性及影响因素,匡助读者更好地理解和应用质量控制方法。
重要性连铸坯的质量控制对于保证最终产品的质量和性能具有重要意义。
一方面,优质的连铸坯可以减少缺陷的产生,提高产品的表面光洁度和机械性能;另一方面,良好的质量控制可以减少生产中的浪费和成本,提高生产效率,增加企业的竞争力。
影响因素连铸坯的质量受到多种因素的影响,包括:1. 原料成份和纯度2. 浇注温度和浇注速度3. 结晶器结构和冷却水温度4. 结晶器护盖的材质和形状5. 连铸速度和拉速6. 过度超熔度和段距这些因素的合理控制和调整,可以有效地提高连铸坯的质量。
质量控制方法质量控制步骤连铸坯质量控制主要包括以下几个步骤:1. 原料质量检验:对原料的成份、纯度及其它关键指标进行检验,确保原料的质量符合要求。
2. 浇注质量控制:合理控制浇注温度和速度,以避免过热或者过冷引起的坯体缺陷。
3. 结晶器质量控制:结晶器的结构和冷却水温度对坯体的结晶质量有直接影响,因此需加强结晶器的质量控制。
4. 连铸速度和拉速控制:坯体的连铸速度和拉速会影响坯体的晶粒细化程度和坯体的机械性能,需要进行合理的控制。
5. 坯体表面质量控制:通过加强护盖材料和形状的选取,合理调整过度超熔度和段距,以提高坯体表面的光洁度。
质量控制指标连铸坯的质量控制需要依据具体产品的要求和标准来制定相应的指标。
普通来说,常见的质量控制指标包括:1. 外观质量:包括表面光洁度、无裂纹、无疤痕等;2. 坯体几何尺寸:包括宽度、厚度、长度等;3. 结晶质量:包括坯体的晶粒细化程度、晶界清晰度等;4. 坯体力学性能:包括抗拉强度、屈服强度、延伸率等;以上指标应根据产品要求,通过实验和测试方法进行监控和评估。
连铸坯质量的控制

连铸坯质量的控制
一、引言
连铸是钢铁生产过程中的重要环节,其连铸坯的质量影响着钢质的稳定性、物
理性能和化学成分等方面。
因此,连铸坯质量控制一直是钢铁生产中的关键技术之一。
二、连铸坯质量的影响因素
1.原料质量:包括钢水、氧化渣等的质量;
2.坯型结构和尺寸:坯型结构和尺寸的设计直接影响坯料的冷却效果和
内部应力状态;
3.坯料表面状态:表面缺陷会在浇铸过程中暴露出来,影响坯料的质量;
4.坯料内部缺陷:坯料内部缺陷会影响钢材的使用寿命和物理性能;
5.连铸工艺参数:包括浇注速度、结晶器温度和冷却水流量等。
三、连铸坯质量控制的措施
为了控制连铸坯质量,需要在生产过程中采取以下措施:
1.加强原料质量控制:保证钢水、氧化渣等原料的质量,避免对坯料质
量的不利影响;
2.优化坯型设计:通过设计合理的坯型结构和尺寸,使坯料均匀冷却、
内部应力均匀分布;
3.改进坯料清理技术:减少表面缺陷的产生;
4.加强坯料表面处理:处理坯料表面缺陷,消除缺陷部位;
5.控制连铸工艺参数:调整浇注速度和结晶器温度等工艺参数控制坯料
成分,改善坯料品质。
四、
通过加强原料质量控制、优化坯型设计、改进坯料清理技术、加强坯料表面处
理和控制连铸工艺参数等措施,可以有效地控制连铸坯质量。
同时,连铸坯质量控制也是钢铁生产中不可或缺的环节,对于提高钢材质量和降低成本都具有非常重要的意义。
连铸坯质量控制
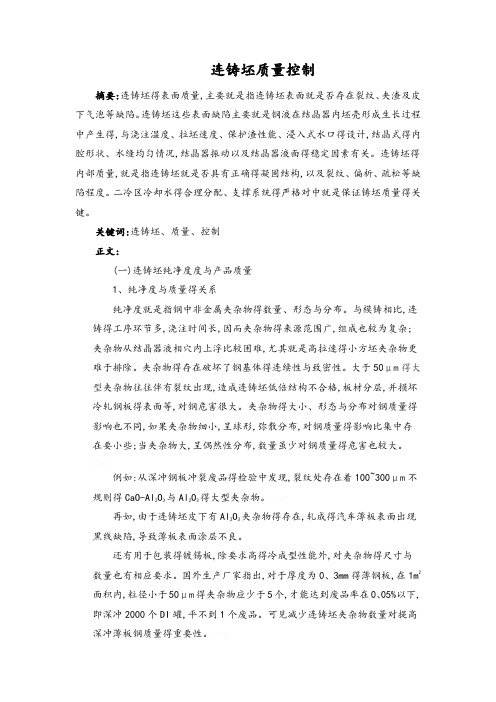
连铸坯质量控制摘要:连铸坯得表面质量,主要就是指连铸坯表面就是否存在裂纹、夹渣及皮下气泡等缺陷。
连铸坯这些表面缺陷主要就是钢液在结晶器内坯壳形成生长过程中产生得,与浇注温度、拉坯速度、保护渣性能、浸入式水口得设计,结晶式得内腔形状、水缝均匀情况,结晶器振动以及结晶器液面得稳定因素有关。
连铸坯得内部质量,就是指连铸坯就是否具有正确得凝固结构,以及裂纹、偏析、疏松等缺陷程度。
二冷区冷却水得合理分配、支撑系统得严格对中就是保证铸坯质量得关键。
关键词:连铸坯、质量、控制正文:(一)连铸坯纯净度度与产品质量1、纯净度与质量得关系纯净度就是指钢中非金属夹杂物得数量、形态与分布。
与模铸相比,连铸得工序环节多,浇注时间长,因而夹杂物得来源范围广,组成也较为复杂;夹杂物从结晶器液相穴内上浮比较困难,尤其就是高拉速得小方坯夹杂物更难于排除。
夹杂物得存在破坏了钢基体得连续性与致密性。
大于50μm得大型夹杂物往往伴有裂纹出现,造成连铸坯低倍结构不合格,板材分层,并损坏冷轧钢板得表面等,对钢危害很大。
夹杂物得大小、形态与分布对钢质量得影响也不同,如果夹杂物细小,呈球形,弥散分布,对钢质量得影响比集中存在要小些;当夹杂物大,呈偶然性分布,数量虽少对钢质量得危害也较大。
例如:从深冲钢板冲裂废品得检验中发现,裂纹处存在着100~300μm不规则得CaO-Al2O3与Al2O3得大型夹杂物。
再如,由于连铸坯皮下有Al2O3夹杂物得存在,轧成得汽车薄板表面出现黑线缺陷,导致薄板表面涂层不良。
还有用于包装得镀锡板,除要求高得冷成型性能外,对夹杂物得尺寸与数量也有相应要求。
国外生产厂家指出,对于厚度为0、3mm得薄钢板,在1m2面积内,粒径小于50μm得夹杂物应少于5个,才能达到废品率在0、05%以下,即深冲2000个DI罐,平不到1个废品。
可见减少连铸坯夹杂物数量对提高深冲薄板钢质量得重要性。
对于极细得钢丝(如直径为0、01~0、25mm得轮胎钢丝)与极薄钢板(如厚度为0、025mm得镀锡板)中,其所含夹杂物尺寸得要求就可想而知了。
连铸坯质量控制

连铸坯质量控制连铸坯质量控制引言连铸坯质量是决定钢铁产品质量的重要因素之一。
在连铸过程中,通过控制连铸坯的凝固结晶形貌、尺寸尺寸以及内部缺陷等,可以保证最终钢铁产品的质量稳定性。
本文将介绍连铸坯质量控制的基本原则和常用技术手段。
1. 连铸坯凝固结晶形貌控制1.1 凝固路径设计连铸坯的凝固路径设计是影响凝固结晶形貌的关键因素。
凝固路径包括主要凝固温度区间、凝固速度以及凝固过程中应有的温度梯度等要点。
通过科学合理地设计凝固路径,可以控制连铸坯的凝固结晶形貌,提高产品的均匀性和致密性。
1.2 凝固浸没深度控制凝固浸没深度是指连铸坯在铸机中浸没的深度。
凝固浸没深度的调整可以通过调整浇注速度、浇注高度和结晶器深度等因素来实现。
恰当地控制凝固浸没深度可以优化凝固结构,减少坯壳厚度和缩孔等缺陷的发生。
2. 连铸坯尺寸控制2.1 坯型设计连铸坯的尺寸控制需要科学合理地设计坯型。
坯型设计要考虑连铸机的性能和工艺条件,以及产品需要达到的尺寸要求。
有效的坯型设计可以保证连铸坯尺寸的精确控制,减少修磨损失并提高铸坯产量。
2.2 坯型换边控制连铸坯在连铸过程中,由于挤压力和引拉力的作用,容易发生坯型换边的情况。
坯型换边会导致铸轧过程中尺寸控制困难,甚至导致产品尺寸不合格。
通过控制连铸机的工艺参数和优化设备结构,可以有效地控制坯型换边,提高铸坯质量。
3. 连铸坯内部缺陷控制3.1 结晶器设计结晶器是连铸过程中控制坯内部缺陷的关键设备。
结晶器的设计应考虑到坯内部的流动状态,并通过合理的传热和传质方式,控制连铸坯内的气体和夹杂物等缺陷。
合理的结晶器设计可以有效减少坯内部夹杂物和气体等缺陷的产生。
3.2 液相线保护措施液相线是连铸过程中凝固结构变化的关键位置。
液相线的形成过早或过晚都会导致内部缺陷的产生。
通过合理的冷却水设定和轧制工艺,可以保证液相线的稳定形成,有效控制坯内部缺陷。
结论连铸坯质量控制是保证钢铁产品质量稳定的关键环节。
连铸坯质量控制

连铸坯质量控制连铸坯质量控制1. 引言2. 连铸坯质量特点连铸坯的质量特点主要包括以下几个方面:2.1 凝固结构连铸坯是通过冷却凝固过程形成的,其凝固过程直接影响到坯体的凝固结构。
凝固结构的好坏会对后续的加工以及材料性能产生重要影响。
2.2 化学成分均匀性连铸坯的化学成分均匀性是其质量的重要指标之一。
成分不均匀容易导致后续钢材性能不稳定,从而影响到产品的质量。
2.3 表面缺陷由于连铸坯制造过程中的一些不可避免的因素,气体夹杂、氧化皮等,会在坯体表面形成一些缺陷。
这些表面缺陷会对后续产品的外观质量产生负面影响。
2.4 尺寸偏差连铸坯的尺寸偏差是指坯体的实际尺寸与标准尺寸之间的差异。
尺寸偏差会影响到钢材的加工工艺和成形质量。
3. 连铸坯质量控制因素及措施连铸坯质量的影响因素众多,包括原料质量、连铸工艺参数、设备状况等。
针对这些影响因素,可以采取以下控制措施来提高连铸坯的质量:3.1 原料质量控制通过严格控制原料的化学成分和物理性能,确保连铸坯的化学成分均匀性和机械性能达到要求。
3.2 连铸工艺参数控制连铸工艺参数的合理设置对坯体的凝固结构和表面质量具有决定性影响。
需要通过优化连铸工艺参数,如冷却水流量、浇注速度等,来控制连铸坯的质量。
3.3 设备维护与改进连铸设备的状态对连铸坯质量也有重要影响。
定期进行设备维护和检修,及时处理设备故障,可以保证设备处于良好状态,进而提高连铸坯的质量。
3.4 检测手段与技术利用先进的检测手段和技术,如超声波检测、磁力检测等,可以对连铸坯进行质量检测,及时发现问题并采取相应措施。
4.连铸坯质量控制是钢铁生产中至关重要的环节。
通过对连铸坯质量特点的分析和影响因素的控制,可以采取相应的措施来提高连铸坯的质量。
这不仅对于保证下游产品质量,还对于提高工业生产效益和降低资源消耗具有重要意义。
开展连铸坯质量控制工作是必不可少的。
连铸坯质量及控制方法

连铸坯质量及控制方法1、连铸坯质量的含义是什么?最终产品质量决定于所供给的铸坯质量。
从广义来说,所谓连铸坯质量是指得到合格产品所允许的铸坯缺陷的严重程度。
它的含义是:——铸坯纯净度(夹杂物数量、形态、分布、气体等)。
——铸坯表面缺陷(裂纹、夹渣、气孔等)。
——铸坯内部缺陷(裂纹、偏析、夹杂等)。
铸坯纯净度主要决定于钢水进入结晶器之前处理过程。
也就是说要把钢水搞“干净”些,必须在钢水进入结晶器之前各工序下功夫,如冶炼及合金化过程控制、选择合适的炉外精炼、中间包冶金、保护浇注等。
铸坯的表面缺陷主要决定于钢水在结晶器的凝固过程。
它是与结晶器坯壳形成、结晶器液面波动、浸入式水口设计、保护渣性能有关的。
必须控制影响表面质量各参数在目标值以内,以生产无缺陷铸坯,这是热送和直接扎制的前提。
铸坯的内部缺陷主要决定于在二次冷却区铸坯冷却过程和铸坯支撑系统。
合理的二次冷却水分布、支承辊的对中、防止铸坯鼓肚等是提高铸坯内部质量的前担。
因此,为了获得良好的铸坯质量,可以根据钢种和产品的不同要求,在连铸的不同阶段如钢包、中间包、结晶器和二次冷却区采用不同的工艺技术,对铸坯质量进行有效控制。
2、提高连铸钢种的纯净度有哪些措施?纯净度是指钢中非金属夹杂物的数量、形态和分布。
要根据钢种和产品质量,把钢中夹杂物降到所要求的水平,应从以下五方面着手:——尽可能降低钢中[O]含量;——防止钢水与空气作用;——减少钢水与耐火材料的相互作用;——减少渣子卷入钢水内;——改善钢水流动性促进钢水中夹杂物上浮。
从工艺操作上,应采取以下措施:(1)无渣出钢:转炉采用挡渣球(或挡渣锥),防止钢渣大量下到钢包。
(2)钢包精炼:根据钢种选择合适的精炼方法,以均匀温度、微调成分、降低氧含量、去除气体夹杂物等。
(3)无氧化浇注:钢水经钢包精炼处理后,钢中总氧含量可由130ppm下降到20ppm以下。
如钢包→中间包注流不保护或保护不良,则中间包钢水中总氧量又上升到60~100ppm范围,恢复到接近炉外精炼前的水平,使炉外精炼的效果前功尽弃。
连铸坯内部质量控制
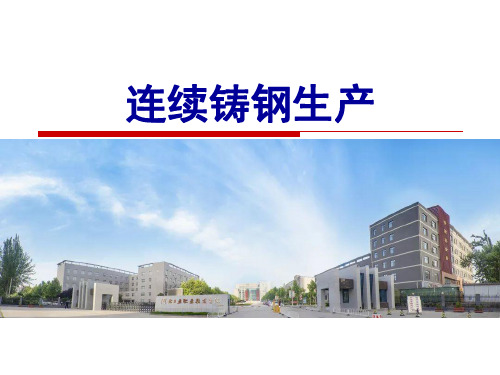
6.4.2中心偏析和疏松
中心偏析是指钢液在凝固过程种,溶质元素在固-液相中 进行再分配时,表现为铸坯中元素分布不均匀,铸坯中心部 位的碳、磷、硫、锰等元素含量明显高于其他部位,中心偏 析往往与中心疏松相伴而生。
6.4.2中心偏析和疏松
在铸坯断面上分布的细微孔隙称为疏松。分布于整个断 面的孔隙称为一般疏松;在树枝晶间的小孔隙称为枝晶疏松 ;铸坯中心部位的疏松称为中心疏松,严重的中心疏松便成 为中心缩孔
富集溶质元素的母液流入裂纹缝隙中,所以此裂纹往往伴有 偏析线,也称“偏析条纹”。热加工过程中不能消除,影响钢 的力学性能,尤其是对横向性能危害最大。
1中间裂纹 中间裂纹发生在铸坯外侧与中心之间,是在柱状晶间产生的 裂纹。内外弧都可能出现中间裂纹.
1中间裂纹 取100mm宽连铸坯低倍试样,采用1:1的盐酸溶液加热至80℃ 左右浸蚀裂纹试样,得到裂纹试样的低倍组织,观察裂纹截面的 形貌
控制措施: (1)降低钢中易偏析元素的含量。 (2)为液相穴提供和产生等轴晶创造条件:低过热度浇注可以 减小柱状晶的比例,电磁搅拌技术可以消除柱状晶的搭桥,增大 中心等轴晶的区宽度,从而达到减轻中心偏析的作用。 (3)通过补偿铸坯末端的凝固收缩,或防止铸坯鼓肚,抑制凝 固末端吸收富集偏析溶质的钢液:小辊径分节辊,减轻铸坯鼓肚 ;凝固末端轻压下技术,补偿铸坯最后凝固的收缩,抑制富集溶 质元素钢液的流动;凝固末端大压下技术,压下量5~20mm。
感谢观赏
连续铸钢生产
6.4连铸坯内部质量
6.4.1内部裂纹
铸坯从皮下到中心出现的裂纹都是内部裂纹,在凝固过程中 产生的裂纹,也叫凝固裂纹。
带液芯的连铸坯在连铸机内运行过程中,液相穴凝固前沿承 受的应力应变超过钢种所能承受的最大应力应变是产生内部裂 纹的根本原因。
连铸坯质量控制与缺陷控制培训课件
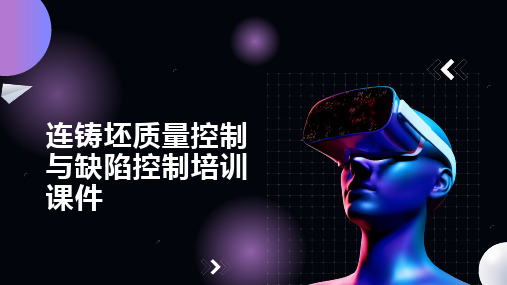
3
夹杂物:表面 或内部出现夹 杂物,影响产
品性能
4
变形:表面或 内部出现变形, 影响产品形状
和尺寸
缺陷原因分析
原材料质量: 如钢水成分、 杂质含量等
01
工艺参数:如 温度、速度、
压力等
02
04
操作人员技能: 如操作不当、 经验不足等
03
设备状况:如 设备磨损、故
障等
缺陷控制方法
优化工艺参数:调整温度、速度、 压力等参数,确保连铸坯质量
02
保证生产效率和质量 冷却控制:控制连铸坯的冷却速
03
度,防止冷却不均匀 结晶控制:控制连铸坯的结晶过
04
程,保证结晶质量
工艺优化方法
优化连铸坯生产 工艺参数,提高 生产稳定性
优化连铸坯生产 工艺流程,提高 生产效率
采用先进的连铸 坯生产设备,提 高产品质量
加强连铸坯生产 工艺管理,提高 生产效率和质量
4
连铸坯质量 管理
质量管理体系
01
质量管理体 系的建立和
实施
02
质量管理体 系的审核和
认证
03
质量管理体 系的持续改
进和优化
04
质量管理体 系的培训和
宣传
质量管理方法
01
制定质量标准:明确连铸坯的质量要 求和检验方法
02
质量检测:对连铸坯进行定期检测, 确保质量符合标准
03
质量控制:对生产过程进行监控,确 保生产工艺和质量符合要求
加强设备维护:定期检查、维护设 备,确保设备正常运行
提高操作技能:加强员工培训,提高 操作技能,减少人为因素导致的缺陷
采用先进技术:采用先进的连铸技 术,提高连铸坯质量,减少缺陷
连铸圆坯凝固传热行为与铸坯质量的控制

连铸圆坯凝固传热行为与铸坯质量的控制一、连铸圆坯凝固传热行为的基础认知连铸圆坯凝固传热这事儿啊,就像是一场热与冷的魔法对决。
你想啊,在连铸的过程中,热量那可是个调皮的小家伙,它到处乱窜呢。
圆坯就像是个小战场,热量从内部想要往外跑,而外部的环境又在努力让它冷却下来。
这时候啊,传热就像是它们之间的交流方式。
圆坯里的热量是有源头的,就好比是热量的小窝,这个源头的热量会逐渐扩散开来。
在这个扩散的过程中,会遇到各种阻碍,就像我们平时走路遇到石头一样。
这些阻碍呢,可能是圆坯内部的结构啊,或者是一些成分的影响。
而且啊,不同的部位传热的速度还不一样呢,就像班级里的同学跑步速度有快有慢。
靠近表面的地方,热量跑得可快了,因为它离外面的冷空气近啊,就像住在海边的人能更快地感受到海风一样。
二、铸坯质量的重要性铸坯质量那可太关键了,这就像是我们盖房子的砖头,要是砖头质量不好,房子能结实吗?对于铸坯来说,如果质量不行,后续加工就会遇到一堆麻烦事儿。
比如说,要是铸坯里面有一些孔洞或者杂质,那在加工成其他产品的时候,就可能会出现裂缝啊,或者是强度不够的情况。
这就好比我们吃的苹果,要是里面有虫子洞,咬一口得多恶心啊。
好的铸坯质量呢,能让我们制造出的产品更加耐用、更加可靠。
就像好的布料能做出漂亮又耐穿的衣服一样。
而且啊,高质量的铸坯还能提高生产效率,减少废品的产生,这可都是实实在在的好处啊。
就像我们考试的时候,答对的题目越多,分数就越高,能节省好多重新做题的时间呢。
三、凝固传热行为对铸坯质量的影响凝固传热行为和铸坯质量那可是紧紧绑在一起的。
如果传热不均匀,铸坯就容易出现质量问题。
比如说,要是某个部位传热太快,可能会导致这个部位冷却过度,就像人在大冬天穿得太少会冻感冒一样。
这样的话,铸坯内部的结构就可能会被破坏,出现一些肉眼看不到的小毛病。
相反,如果传热太慢呢,铸坯可能就不能及时定型,就像蛋糕没有及时烤熟一样,里面还是黏糊糊的。
这时候啊,铸坯的形状可能就不规整了,或者内部会有一些没有凝固好的地方,这对铸坯质量来说,简直就是灾难。
- 1、下载文档前请自行甄别文档内容的完整性,平台不提供额外的编辑、内容补充、找答案等附加服务。
- 2、"仅部分预览"的文档,不可在线预览部分如存在完整性等问题,可反馈申请退款(可完整预览的文档不适用该条件!)。
- 3、如文档侵犯您的权益,请联系客服反馈,我们会尽快为您处理(人工客服工作时间:9:00-18:30)。
PPT文档演模板
第八章连铸坯的质量控制
4.3.2 内部纵向裂纹
l 包括中心线裂纹、三角区裂纹和角部裂纹
l 形成原因:液相穴末端板坯鼓肚;
板坯宽面、窄面鼓肚
l 主要影响因素:
1、浇铸速度过快;
2、浇铸温度过高;
3、钢水含硫量过大;
4、结晶器锥度太小;
5、铸流不对正。
PPT文档演模板
第八章连铸坯的质量控制
PPT文档演模板
第八章连铸坯的质量控制
•3.7 表面(皮下)夹渣
l 表面夹渣多为Si-Mn系夹渣,会造成 表面条纹缺陷;皮下夹渣多为Al2O3 系细小夹渣,是深冲薄板钢表面质量 降低的主要原因。
l 主要影响因素:钢水纯净度,保护渣 的化学组成、物理性能及液面波动状 态。
PPT文档演模板
第八章连铸坯的质量控制
第八章连铸坯的质量控制
l 预防措施: 1、液相穴末端采用收缩辊缝; 2、改善铸坯导向支撑系统; 3、更换弯曲辊子; 4、调整浇铸温度和速度; 5、维持正确的结晶器锥度; 6、检查喷水冷却系统; 7、降低钢水硫含量。
PPT文档演模板
第八章连铸坯的质量控制
五、连铸坯形状缺陷及控制
l 菱形变形 l 圆柱坯变形 l 鼓肚变形
PPT文档演模板
第八章连铸坯的质量控制
3.4 液面结壳
l 液面结壳是指在结晶器内钢水表面之上,保 护渣层下边漂浮着浮冰似的钢壳。
结壳厚度与其在液面上的停留时间有关,有 的可达300mm厚。 l 产生原因:液面附近温度低,钢水不活动。
l 可以合理设计浸入式水口侧孔角度改善。
l 判断标准:常用振痕的不规律性,粗大的夹 杂和大孔洞等标志判断。
(3)连铸机下部对弧不准
(4)拉矫辊的夹紧力调整不当,过分压下
PPT文档演模板
第八章连铸坯的质量控制
l 应对圆柱坯变形的措施: (1)及时更换变形的结晶器 (2)连铸机要严格对弧 (3)二冷区均匀冷却 (4)可适当降低拉速
PPT文档演模板
第八章连铸坯的质量控制
5.3 鼓肚变形
l 定义 l 影响鼓肚量大小的因素 l 减少鼓肚的措施
l 铸坯横断面的尺寸与形状 l 钢水静压力大小 l 支撑辊的间距 l 凝固的坯壳厚度 l 钢的高温弹性模数 l 坯壳的温度 l 拉坯速度
PPT文档演模板
第八章连铸坯的质量控制
3rew
演讲完毕,谢谢听讲!
再见,see you again
PPT文档演模板
2020/11/27
第八章连铸坯的质量控制
l 连铸坯质量控制战略:铸坯洁净度决定于 钢水进入结晶器之前的各工序;铸坯表面 质量决定于钢水在结晶器的凝固过程;铸 坯内部质量决定于钢水在二冷区的凝固过 程。
PPT文档演模板
第八章连铸坯的质量控制
二、铸坯的洁净度
l 连铸坯洁净度评价包括: 钢中总氧量; 钢中微观夹杂物量(<50μm); 钢中大颗粒夹杂物量(>50μm)。
PPT文档演模板
第八章连铸坯的质量控制
3.3 表面裂纹的主要种类
l 星状裂纹 l 表面纵、横裂纹 l 角部纵裂纹
PPT文档演模板
第八章连铸坯的质量控制
3.3.1 星状裂纹
l 多发生在板坯上下宽面,深度在1-3mm l 原因:结晶器铜壁内腔的磨损导致低熔
点Cu渗入钢液。
l 预防措施:结晶器内壁镀Cr(不适合做 较厚的镀层)或Ni(适于做较厚的镀 层),能有效的隔绝Cu渗入钢液。
PPT文档演模板
第八章连铸坯的质量控制
l 预防措施: 1、降低钢水中硫磷含量; 2、适当降低浇铸温度和浇铸速度; 3、控制结晶器的液面波动; 4、检查冷却水; 5、选择合适黏度的保护渣。
PPT文档演模板
第八章连铸坯的质量控制
3.3.3 表面横向裂纹
l 原因:多发生在高碳钢中,当钢坯处于 高温脆性区时对其进行矫直所致。
PPT文档演模板
第八章连铸坯的质量控制
•3.5 凹坑和重皮
l 铸坯初始凝固所形成坯壳厚度的不均匀, 坯壳与器壁的摩擦导致铸坯表面形成皱 纹,严重的呈现为山谷状的凹陷,即凹 坑。铁素体钢发生凹坑的几率较大。
l 形成凹坑之处的冷却速度较低,导致组 织粗糙化,易造成显微偏析和裂纹。
l 铸坯拉出的过程中,若横向凹陷处渗漏 出来的钢水能够重新凝固,即形成重皮。 否则导致漏钢事故的发生。
PPT文档演模板
第八章连铸坯的质量控制
连铸夹杂物形成的显著特征
l 连铸凝固速度快,夹杂物长大机会少, 尺寸小,不易上浮;
l 连铸多了中间包,钢液和大气、熔渣、 耐火材料接触时间长,易被污染;
l 模铸钢锭夹杂物多集中在头尾部,通过 切头尾可减轻夹杂物危害,而连铸仅靠 切头尾难以解决问题。
PPT文档演模板
PPT文档演模板
第八章连铸坯的质量控制
内裂纹形成的三个阶段
l 拉伸力作用到凝固界面 l 造成柱状晶的晶间开裂 l 偏析元素富集的钢液填充到开裂
的空隙中
PPT文档演模板
第八章连铸坯的质量控制
4.3.1 内部横向裂纹
l 形成原因:坯壳受挤压发生变形 l 主要影响因素:
1、铸坯所受弯曲力和矫直力过大; 2、支撑辊对正不良; 3、辊子偏心; 4、钢水含硫量过大。
l 表面质量是影响金属收得率和成 本的重要因素;
l 表面质量是铸坯热送和直接轧制 的前提条件。
PPT文档演模板
第八章连铸坯的质量控制
PPT文档演模板
第八章连铸坯的质量控制
3.2 表面缺陷的形成
l 表面缺陷主要包括:表面裂纹、 表面夹渣、深振痕、表面气泡 和皮下气泡、气孔等。
l 原因:主要是受结晶器内钢液 凝固(即一次冷却)所控制。
第八章连铸坯的质量控制
影响连铸坯洁净度的因素
l 机型。夹杂物在弧形结晶器中易聚集到内弧侧。 可以通过提高钢水净化技术来弥补。
l 连铸操作。正常浇铸时,主要由钢水洁净度决 定夹杂物的多少。非正常浇铸时,夹杂物有所 增加(初期钢水被耐火材料污染较严重;末期涡 流作用会把液面较低的中间包渣吸入结晶器;换 包期间夹杂物易增多)。
PPT文档演模板
第八章连铸坯的质量控制
3.3.4 角部纵向裂纹
l 发生在距角部30-50mm的宽面上,常出 现在方坯中。
l 发生几率随拉速的增加而增加。
l 原因:结晶器窄边锥度与宽边方向上的坯 壳收缩量不一致,进入二冷区后会进一步 扩大。
l 预防措施:增加结晶器窄边锥度,使其与 宽边方向上的坯壳收缩量保持一致。
•3.6 表面气泡(和皮下气泡)
l 形成原因:凝固过程中,钢中氧、氢、氮 和碳等元素在凝固界面富集,当其生成的 CO、H2、N2等气体的总压力大于钢水静 压力和大气压力之和时,即有气泡产生。
l 漏出表面的称为表面气泡;潜伏在表面下 边又靠近表面的称为皮下气泡。
l 为了防止表面气泡的生成,首要条件是控 制钢中的总气体含量。
第八章连铸坯的质量控 制
PPT文档演模板
2020/11/27
第八章连铸坯的质量控制
内容
l 概述 l 铸坯的洁净度 l 铸坯表面质量及控制 l 铸坯内部质量及控制 l 连铸坯形状缺陷及控制
PPT文档演模板
第八章连铸坯的质量控制
一、概述
l 连铸坯的质量概念包括:铸坯洁净度(钢 中非金属夹杂物数量,类型,尺寸,分布, 形态);铸坯表面质量(纵裂纹,横裂纹, 星形裂纹,夹渣,气孔等);铸坯内部质 量(中间裂纹,角部裂纹,偏析等);铸 坯断面形状。
l 耐火材料质量。钢液中的Mn、Al等元素与耐火 材料中的氧化物发生反应形成不能上浮的低熔 点渣层会残留在铸坯中。
PPT文档演模板
第八章连铸坯的质量控制
l 提高铸坯洁净度的措施:
(1)无渣出钢
(2)选择合适的精炼处理方式
(3)采用无氧化浇铸技术
(4)充分发挥中间包冶金净化的作用
(5)选用优质耐火材料
冶金因素影响的形成阶段----①柱状晶的生长; ②由于某些工艺因素的影响使得柱状晶的生 长变得很不稳定; ③优先生长的柱状晶在铸坯中心相遇,形成 “晶桥”; ④“晶桥”形成后上部钢水受阻不能对下部 钢水的凝固收缩进行及时补充。
PPT文档演模板
第八章连铸坯的质量控制
l 机械因素主要是铸坯“鼓肚”。发生 鼓肚时,铸坯中心产生了相当于负压 的抽力作用,此时二相区内被偏析元 素富集的不纯钢液,被吸向心部形成 中心偏析带。
(6)充分发挥结晶器的作用
(7)采用电磁搅拌技术,控制铸流运动
PPT文档演模板
第八章连铸坯的质量控制
三、铸坯表面质量及控制
l 控制表面质量的必要性 l 表面缺陷的形成 l 表面裂纹的主要种类 l 液面结壳 l 凹坑和重皮
PPT文档演模板
第八章连铸坯的质量控制
3.1 控制表面质量的必要性
l 连铸坯表面质量的好坏决定了铸 坯在热加工之前是否需要精整;
PPT文档演模板
第八章连铸坯的质量控制
3.3.2 表面纵向裂纹
l 多发生在板坯宽面中央部位。 l 原因:初生坯壳厚度不均匀,在坯壳
薄的地方应力集中,当应力超过坯壳 的抗拉强度时会产生裂纹。
PPT文档演模板
第八章连铸坯的质量控制
l 影响因素: 1、钢水成分,硫、磷的含量过高; 2、浇铸温度高; 3、浇铸速度大; 4、板坯宽度过大; 5、保护渣粘度不合理; 6、结晶器液面波动过大; 7、铸坯横向冷却不均匀。
减少内部裂纹的措施
l 采用多点矫直技术以弥补单点矫直的 不足
l 二冷区采用合适的夹辊辊距,支撑辊 准确对弧
l 二冷区水量、水压分配适当,保持铸 坯表面温度均匀
l 最好采用液压控制机构控制压下量
PPT文档演模板
第八章连铸坯的质量控制
4.3.3 中心偏析