五轴数控加工
数控五轴加工中心编程的方法及步骤
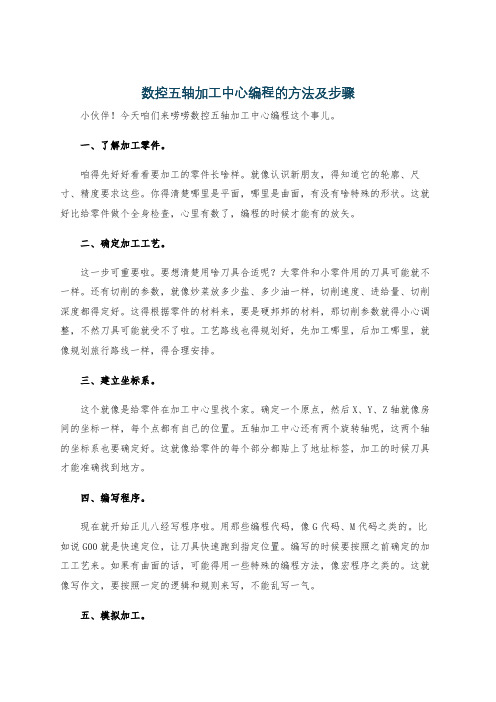
数控五轴加工中心编程的方法及步骤小伙伴!今天咱们来唠唠数控五轴加工中心编程这个事儿。
一、了解加工零件。
咱得先好好看看要加工的零件长啥样。
就像认识新朋友,得知道它的轮廓、尺寸、精度要求这些。
你得清楚哪里是平面,哪里是曲面,有没有啥特殊的形状。
这就好比给零件做个全身检查,心里有数了,编程的时候才能有的放矢。
二、确定加工工艺。
这一步可重要啦。
要想清楚用啥刀具合适呢?大零件和小零件用的刀具可能就不一样。
还有切削的参数,就像炒菜放多少盐、多少油一样,切削速度、进给量、切削深度都得定好。
这得根据零件的材料来,要是硬邦邦的材料,那切削参数就得小心调整,不然刀具可能就受不了啦。
工艺路线也得规划好,先加工哪里,后加工哪里,就像规划旅行路线一样,得合理安排。
三、建立坐标系。
这个就像是给零件在加工中心里找个家。
确定一个原点,然后X、Y、Z轴就像房间的坐标一样,每个点都有自己的位置。
五轴加工中心还有两个旋转轴呢,这两个轴的坐标系也要确定好。
这就像给零件的每个部分都贴上了地址标签,加工的时候刀具才能准确找到地方。
四、编写程序。
现在就开始正儿八经写程序啦。
用那些编程代码,像G代码、M代码之类的。
比如说G00就是快速定位,让刀具快速跑到指定位置。
编写的时候要按照之前确定的加工工艺来。
如果有曲面的话,可能得用一些特殊的编程方法,像宏程序之类的。
这就像写作文,要按照一定的逻辑和规则来写,不能乱写一气。
五、模拟加工。
程序写好可别着急让加工中心干活。
先模拟一下,就像演习一样。
看看刀具的路径对不对,有没有可能撞到零件或者夹具。
要是模拟的时候发现问题,那就赶紧修改程序。
这就像出门前检查一下东西有没有带齐,发现没带钥匙还能及时补上。
六、实际加工。
经过前面的步骤,没问题啦,就可以让加工中心开始干活啦。
不过在加工的时候也不能完全不管,得盯着点。
万一有啥突发情况,像刀具磨损啦,还能及时处理。
数控五轴加工中心编程就是这么个事儿,看起来有点复杂,但是只要一步一步来,多实践,肯定能掌握的。
5轴加工中心

5轴加工中心5轴加工中心是一种先进的数控机床,具有多轴可同时运动的能力,能够进行复杂的零件加工。
它由加工机身、控制系统、刀具库和工作台等组成,通过不同轴的运动来实现多种复杂的加工操作。
首先,5轴加工中心具有更大的加工空间。
传统的3轴加工中心只能在x、y、z轴上进行运动,而5轴加工中心还增加了a轴和c轴的运动能力,使得加工中心的加工范围更广。
这使得5轴加工中心非常适用于加工复杂的曲面和立体零件。
此外,5轴加工中心还具有更高的加工精度。
由于有更多的运动轴,5轴加工中心能够以更多的角度对工件进行加工,从而实现更精细的加工。
这对于一些高精度的行业,如航空航天和医疗器械制造等非常重要。
另外,5轴加工中心还具有更高的加工效率。
它可以在一个夹持定位的情况下完成多个加工步骤,而无需移动工件或更换刀具。
这样可以大大节省加工时间,并提高生产效率。
同时,由于其高精度加工能力,也可以减少加工过程中的废料,进一步提高效率。
此外,5轴加工中心还具有更大的灵活性。
由于具有多轴运动能力,它可以应对各种复杂的加工需求。
无论是进行复杂曲面零件的加工,还是进行螺纹和孔加工,都能轻松应对。
这为制造业提供了更多的可能性,并能够满足市场对高品质和高精度零件的需求。
然而,5轴加工中心也存在一些挑战。
首先,由于其结构更为复杂,维护和保养成本较高。
这需要有专业的技术维护人员定期进行检修和维护。
其次,5轴加工中心的购买成本较高,对于一些中小型企业来说可能存在一定的经济压力。
总的来说,5轴加工中心是一种先进的数控机床,具有更大的加工空间、更高的加工精度、更高的加工效率和更大的灵活性。
它在制造业中的应用越来越广泛,可以满足市场对高品质和高精度零件的需求。
虽然存在一些挑战,但随着技术的不断发展和成本的下降,5轴加工中心的应用前景仍然十分广阔。
五轴数控技术发展有哪些困难和阻力?

五轴数控技术发展有哪些困难和阻力?五轴数控加工是数控技术中难度最大、应用最广泛的技术。
它集计算机控制、高性能伺服驱动、精密加工技术于一体,用于复杂曲面的高效、精密、自动化加工。
与三轴CNC加工相比,从工艺和编程的角度来看,复杂曲面的五轴CNC加工具有以下优势:1.提高加工质量和效率2.扩大工艺范围迎接复合材料发展的新方向但是,由于加工空间中刀具的干涉和位置控制,五轴数控加工的数控编程、数控系统、机床结构都比三轴机床复杂得多。
因此,真正实现五轴加工很难,更难操作和使用好。
真假五轴加工说起五轴加工,就不得不说真假五轴加工。
真假五轴加工的主要区别在于是否具有RTCP功能。
RTCP是“旋转工具中心点”的缩写。
只有带RTCP 功能的五轴加工才是真正的五轴加工。
不具备RTCP功能的五轴机床和数控系统必须依靠CAM编程和后处理,提前规划好刀具路径。
对于同一个零件,如果换了机床,或者刀具改变了,必须重新进行CAM编程和后处理,所以只能称为假五轴加工。
简而言之,真五轴加工就是五轴五联动,而假五轴加工可能是五轴三联动,另外两轴只起定位作用。
五轴数控技术发展的难点和阻力虽然我们都知道五轴数控技术的优越性和重要性。
但五轴数控技术的应用还仅限于一些规模比较大的企业,还存在一些未解决的问题。
下面详述了一些困难和阻力。
1、五轴CNC编程抽象,操作难度大这是每一个传统CNC程序员都深感难解的问题。
三轴机床只有直线坐标轴,而五轴数控机床结构多样。
相同的NC代码在不同的三轴数控机床上可以达到同样的加工效果,但五轴机床的NC代码不能适用于所有类型的五轴机床。
CNC编程除了直线运动外,还必须坐标旋转运动的相关计算,如旋转角度行程检查、非线性误差检查、刀具旋转计算等。
处理的信息量非常大,CNC编程极其抽象。
五轴数控加工的操作与编程技巧息息相关。
如果用户在机床上增加特殊功能,编程和操作会更加复杂。
只有反复练习,编程和操作人员才能掌握必要的知识和技能。
五轴加工中心的加工范围
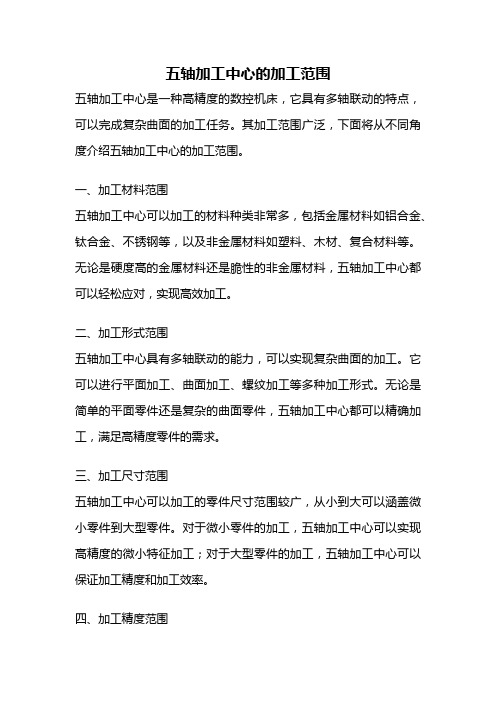
五轴加工中心的加工范围五轴加工中心是一种高精度的数控机床,它具有多轴联动的特点,可以完成复杂曲面的加工任务。
其加工范围广泛,下面将从不同角度介绍五轴加工中心的加工范围。
一、加工材料范围五轴加工中心可以加工的材料种类非常多,包括金属材料如铝合金、钛合金、不锈钢等,以及非金属材料如塑料、木材、复合材料等。
无论是硬度高的金属材料还是脆性的非金属材料,五轴加工中心都可以轻松应对,实现高效加工。
二、加工形式范围五轴加工中心具有多轴联动的能力,可以实现复杂曲面的加工。
它可以进行平面加工、曲面加工、螺纹加工等多种加工形式。
无论是简单的平面零件还是复杂的曲面零件,五轴加工中心都可以精确加工,满足高精度零件的需求。
三、加工尺寸范围五轴加工中心可以加工的零件尺寸范围较广,从小到大可以涵盖微小零件到大型零件。
对于微小零件的加工,五轴加工中心可以实现高精度的微小特征加工;对于大型零件的加工,五轴加工中心可以保证加工精度和加工效率。
四、加工精度范围五轴加工中心是一种高精度的加工设备,其加工精度非常高。
在加工过程中,五轴加工中心可以实现微小误差的控制,保证加工零件的尺寸精度和形状精度。
因此,五轴加工中心广泛应用于精密机械、航空航天等领域。
五、加工效率范围五轴加工中心具有高效率的特点。
它可以通过多轴联动,同时进行多个加工动作,大大提高了加工效率。
此外,五轴加工中心还可以进行自动换刀、自动测量等功能,进一步提高了加工效率。
因此,五轴加工中心在批量生产和加工周期紧张的情况下具有明显的优势。
五轴加工中心具有广泛的加工范围。
无论是材料种类、加工形式、加工尺寸还是加工精度和效率,五轴加工中心都能够满足各种需求。
随着科技的不断发展,五轴加工中心在工业生产中的应用越来越广泛,为制造业的发展做出了重要贡献。
数控五轴加工中心的优势

数控五轴加工中心的优势数控五轴加工中心是一种采用数控技术实现五轴联动加工的高精度加工机床,在工业制造领域中应用广泛。
与传统的三轴加工相比,数控五轴加工中心具有许多优势。
可实现更高的加工精度数控五轴加工中心的加工精度通常可以达到0.005mm以下,远高于传统的三轴加工。
这是因为数控五轴加工中心可以在五个方向进行联动加工,进一步提高了加工精度。
对于一些需要高精度的零部件加工,数控五轴加工中心是非常理想的选择。
可实现更多的加工方向和角度传统的三轴加工通常只能进行三个方向的加工,而数控五轴加工中心可以实现更多的加工方向和角度。
通过控制五个轴进行联动运动,数控五轴加工中心可以实现对于复杂曲面的加工,为制造业带来了更多的灵活性和实现更高效率的机会。
可实现更高效的加工速度数控五轴加工中心在加工速度方面也有很大的优势。
通过合理的计算和设计,数控五轴加工中心可以加速加工速度,从而提高生产效率。
这对于需要大批量生产的企业来说,是非常有利的。
可应用于更广泛的材料由于数控五轴加工中心在进行联动加工时可以实现更多的加工方向和角度,因此可以用于加工更广泛的材料。
无论是金属、塑料、木材或者各种复合材料,数控五轴加工中心都能够进行高效、高精度的加工。
可节省更多的人力和金钱成本数控五轴加工中心的自动化程度非常高,只需要较少的人力投入,就能够完成较大的生产任务。
在生产成本方面,数控五轴加工中心也节省了很多人力和金钱成本,使得企业能够更加高效地运营。
综上所述,数控五轴加工中心具有许多优势,可以满足不同领域的制造需求,帮助企业提升生产效率、降低成本和提高产品质量。
随着科技的进步和制造技术的不断发展,数控五轴加工中心的应用将得到更广泛的发展。
五轴加工实训总结

五轴加工实训总结五轴加工是一种高级的数控加工技术,通过同时控制工件在三个旋转轴和两个线性轴上的运动,可以完成复杂零件的加工。
在本次五轴加工实训中,我深刻体会到了这项技术的重要性和优势。
在实训中,我们学习了如何正确使用五轴数控机床进行加工。
通过调整工件在不同轴上的运动轨迹和切削工具的位置,我们可以实现各种复杂曲面的加工,提高加工效率和精度。
同时,五轴加工还可以减少工件的夹持次数和夹持误差,提高加工的稳定性和一致性。
五轴加工实训让我深刻体会到了团队合作的重要性。
在实训中,每个人都扮演着不同的角色,有的负责编写加工程序,有的负责调试机床参数,有的负责监控加工过程。
只有团队成员密切合作,才能确保加工任务顺利完成。
通过团队合作,我们不仅提高了工作效率,还增强了相互间的沟通和协调能力。
五轴加工实训还让我意识到了安全生产的重要性。
在操作五轴数控机床时,我们必须严格遵守操作规程,佩戴好防护装备,确保人身安全。
同时,还要定期检查机床设备的运行状态,及时发现和排除安全隐患。
只有做好安全生产工作,才能保障工作人员的生命安全和身体健康。
通过这次五轴加工实训,我不仅掌握了五轴加工技术的基本原理和操作方法,还提升了自己的实际操作能力和团队合作意识。
在今后的工作中,我将继续努力学习,不断提高自己的专业技能,为企业的发展贡献自己的力量。
总的来说,五轴加工实训是一次难得的学习机会,让我受益匪浅。
通过实际操作,我深刻理解了五轴加工技术的重要性和应用范围,也认识到了团队合作和安全生产的重要性。
我相信,在不断的学习和实践中,我一定能够成为一名优秀的五轴加工技术人员,为企业的发展做出更大的贡献。
【本文来源网络整理】。
五轴联动数控加工中的刀具轨迹控制算法

五轴联动数控加工中的刀具轨迹控制算法五轴联动数控加工是一种高精度、高效率的加工方式,可以实现对复杂曲面的加工。
在五轴联动数控加工中,刀具轨迹控制算法起着至关重要的作用,决定了加工精度和效率。
本文将介绍几种常见的刀具轨迹控制算法,并对其原理和应用进行详细阐述。
1. 五轴联动数控加工概述五轴联动数控加工是指在数控加工机床上,通过同时控制五个坐标轴的运动,实现对工件的加工。
相比于传统的三轴加工,五轴联动可以更加灵活地加工复杂曲面,提高加工质量和效率。
2. 刀具轨迹控制算法的作用刀具轨迹控制算法是五轴联动数控加工中的关键技术之一。
它可以根据工件的三维模型和加工要求,计算出刀具在加工过程中的运动轨迹,从而实现精确的加工。
刀具轨迹控制算法的好坏直接影响加工精度和效率。
3. 刀具轨迹控制算法的分类刀具轨迹控制算法可以分为两类:离散点算法和曲线插补算法。
离散点算法是指将工件曲面离散化为一系列离散点,然后通过逐点加工来实现曲面加工。
常见的离散点算法有直线连接法、圆心法和切点法等。
这些算法简单直观,适用于加工简单曲面。
曲线插补算法是指根据工件的曲线方程和刀具半径,通过插补计算出刀具的运动轨迹。
常见的曲线插补算法有圆弧插补法、曲线插补法和样条插补法等。
这些算法可以实现对复杂曲面的高精度加工。
4. 圆弧插补算法圆弧插补算法是五轴联动数控加工中最常用的一种刀具轨迹控制算法。
它通过计算刀具半径和工件曲线的切向方向,确定刀具的圆弧插补路径。
圆弧插补算法具有计算简单、加工效率高的优点,适用于多数加工场景。
5. 曲线插补算法曲线插补算法是一种更加精细的刀具轨迹控制算法,可以实现对复杂曲面的高精度加工。
曲线插补算法通过计算刀具在曲线上的切向方向和曲率,确定刀具的插补路径。
与圆弧插补算法相比,曲线插补算法需要更复杂的计算和控制,但可以实现更高的加工精度。
6. 样条插补算法样条插补算法是一种基于数学样条曲线的刀具轨迹控制算法。
它通过计算曲面上的样条曲线,将刀具的运动路径进行插补。
五轴联动是什么
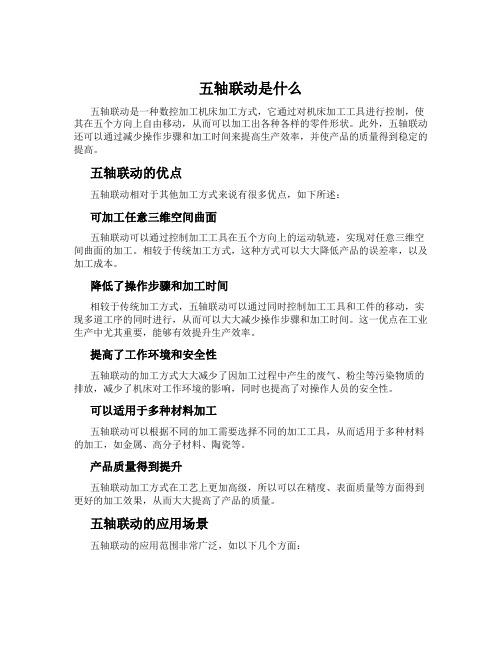
五轴联动是什么五轴联动是一种数控加工机床加工方式,它通过对机床加工工具进行控制,使其在五个方向上自由移动,从而可以加工出各种各样的零件形状。
此外,五轴联动还可以通过减少操作步骤和加工时间来提高生产效率,并使产品的质量得到稳定的提高。
五轴联动的优点五轴联动相对于其他加工方式来说有很多优点,如下所述:可加工任意三维空间曲面五轴联动可以通过控制加工工具在五个方向上的运动轨迹,实现对任意三维空间曲面的加工。
相较于传统加工方式,这种方式可以大大降低产品的误差率,以及加工成本。
降低了操作步骤和加工时间相较于传统加工方式,五轴联动可以通过同时控制加工工具和工件的移动,实现多道工序的同时进行,从而可以大大减少操作步骤和加工时间。
这一优点在工业生产中尤其重要,能够有效提升生产效率。
提高了工作环境和安全性五轴联动的加工方式大大减少了因加工过程中产生的废气、粉尘等污染物质的排放,减少了机床对工作环境的影响,同时也提高了对操作人员的安全性。
可以适用于多种材料加工五轴联动可以根据不同的加工需要选择不同的加工工具,从而适用于多种材料的加工,如金属、高分子材料、陶瓷等。
产品质量得到提升五轴联动加工方式在工艺上更加高级,所以可以在精度、表面质量等方面得到更好的加工效果,从而大大提高了产品的质量。
五轴联动的应用场景五轴联动的应用范围非常广泛,如以下几个方面:航空航天领域航空航天领域对于零件的精度和表面质量要求非常高,而五轴联动可以准确地制造出复杂的零件形状,从而使得其在航空航天领域得到广泛的应用。
模具制造模具制造过程中通常会遇到复杂的立体曲面,传统加工方式无法解决这种问题,而五轴联动加工方式可以使得模具的制造变得简单和高效。
医疗设备制造五轴联动可以通过对精细加工的掌握,制造出各种各样的特殊医疗设备,从而为患者提供更加高效的治疗方案。
艺术品制造五轴联动加工方式可以制造出各种各样的艺术品形状,使得艺术品在设计时更加灵活,从而让艺术品制造领域变得更加具有创造性。
五轴加工中心的原理
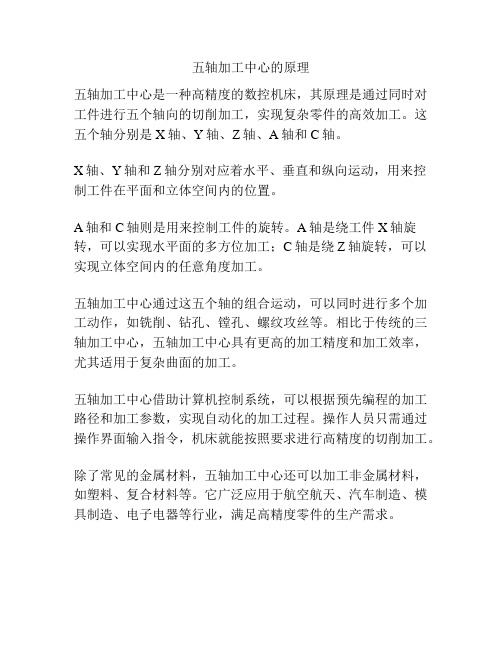
五轴加工中心的原理
五轴加工中心是一种高精度的数控机床,其原理是通过同时对工件进行五个轴向的切削加工,实现复杂零件的高效加工。
这五个轴分别是X轴、Y轴、Z轴、A轴和C轴。
X轴、Y轴和Z轴分别对应着水平、垂直和纵向运动,用来控制工件在平面和立体空间内的位置。
A轴和C轴则是用来控制工件的旋转。
A轴是绕工件X轴旋转,可以实现水平面的多方位加工;C轴是绕Z轴旋转,可以实现立体空间内的任意角度加工。
五轴加工中心通过这五个轴的组合运动,可以同时进行多个加工动作,如铣削、钻孔、镗孔、螺纹攻丝等。
相比于传统的三轴加工中心,五轴加工中心具有更高的加工精度和加工效率,尤其适用于复杂曲面的加工。
五轴加工中心借助计算机控制系统,可以根据预先编程的加工路径和加工参数,实现自动化的加工过程。
操作人员只需通过操作界面输入指令,机床就能按照要求进行高精度的切削加工。
除了常见的金属材料,五轴加工中心还可以加工非金属材料,如塑料、复合材料等。
它广泛应用于航空航天、汽车制造、模具制造、电子电器等行业,满足高精度零件的生产需求。
五轴数控机床加工技术研究
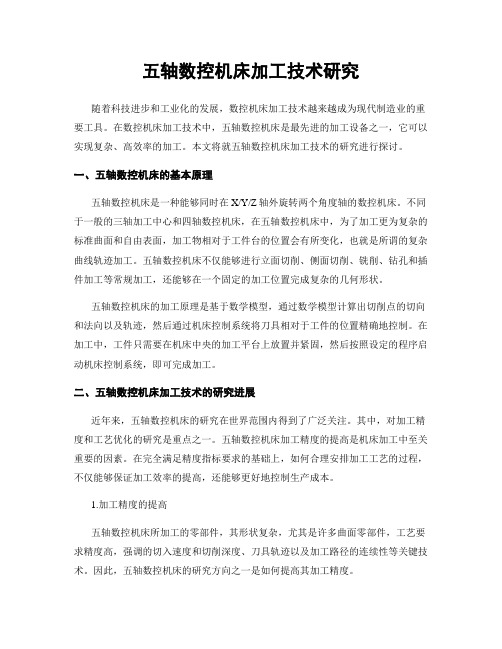
五轴数控机床加工技术研究随着科技进步和工业化的发展,数控机床加工技术越来越成为现代制造业的重要工具。
在数控机床加工技术中,五轴数控机床是最先进的加工设备之一,它可以实现复杂、高效率的加工。
本文将就五轴数控机床加工技术的研究进行探讨。
一、五轴数控机床的基本原理五轴数控机床是一种能够同时在X/Y/Z轴外旋转两个角度轴的数控机床。
不同于一般的三轴加工中心和四轴数控机床,在五轴数控机床中,为了加工更为复杂的标准曲面和自由表面,加工物相对于工件台的位置会有所变化,也就是所谓的复杂曲线轨迹加工。
五轴数控机床不仅能够进行立面切削、侧面切削、铣削、钻孔和插件加工等常规加工,还能够在一个固定的加工位置完成复杂的几何形状。
五轴数控机床的加工原理是基于数学模型,通过数学模型计算出切削点的切向和法向以及轨迹,然后通过机床控制系统将刀具相对于工件的位置精确地控制。
在加工中,工件只需要在机床中央的加工平台上放置并紧固,然后按照设定的程序启动机床控制系统,即可完成加工。
二、五轴数控机床加工技术的研究进展近年来,五轴数控机床的研究在世界范围内得到了广泛关注。
其中,对加工精度和工艺优化的研究是重点之一。
五轴数控机床加工精度的提高是机床加工中至关重要的因素。
在完全满足精度指标要求的基础上,如何合理安排加工工艺的过程,不仅能够保证加工效率的提高,还能够更好地控制生产成本。
1.加工精度的提高五轴数控机床所加工的零部件,其形状复杂,尤其是许多曲面零部件,工艺要求精度高,强调的切入速度和切削深度、刀具轨迹以及加工路径的连续性等关键技术。
因此,五轴数控机床的研究方向之一是如何提高其加工精度。
国内外学者在提高精度的方面,采用的主要策略是将机床材料、结构、系统以及传动等方面的设备进行优化和改进。
例如,采用高刚性的机床组合、新型加工刀具和合理的加工参数,能够显著提高加工精度。
同时,通过改进数控系统和控制模型,可以实现机床运动的更加精确控制。
2.工艺优化工艺优化是五轴数控机床研究的重要方向之一。
五轴加工前景

五轴加工前景五轴加工技术是一种先进的数控加工技术,具有高效、灵活的特点,在当前的机械制造行业中有着广阔的应用前景。
下面从两个方面来阐述五轴加工技术的前景。
首先,五轴加工技术可以实现复杂零件的一次成型。
传统的三轴加工技术只能实现对零件的立体加工,而对于具有复杂曲面的零件,需要进行多次加工,造成加工效率低下和加工精度的下降。
而五轴加工技术可以通过对工件进行多个方向的转动来实现对复杂曲面的加工,只需进行一次加工即可完成零件的加工,提高了加工效率和加工精度。
这在航空航天、汽车、船舶等行业中有着广泛的应用,可以加工出更加复杂、精细的零件。
其次,五轴加工技术可以提高加工的灵活性和适应性。
五轴加工机床具有五个坐标轴的控制能力,可以使工件在多个方向上进行转动和倾斜。
这使得五轴加工机床可以实现对各种形状、角度的零件进行加工,大大提高了加工的灵活性和适应性。
而传统的三轴加工技术对于某些具有复杂形状的零件加工存在一定的局限性,需要进行多次加工和调整,加工效率低下。
而五轴加工技术可以通过对工件进行多个方向的转动和倾斜,可以灵活地调整加工角度和加工路径,提高了加工的灵活性和适应性。
这在各个行业中都有着广泛的应用,可以加工出更加复杂、多样化的零件。
综上所述,五轴加工技术在当前的机械制造行业中有着广阔的应用前景。
它可以实现对复杂零件的一次成型,提高了加工的效率和精度;同时,它还可以提高加工的灵活性和适应性,可以对各种形状、角度的零件进行加工。
这使得五轴加工技术可以应用于航空航天、汽车、船舶等行业,为这些行业的发展提供了有力的支持。
随着科学技术的进步和需求的不断增长,五轴加工技术的应用前景将更加广阔。
五轴加工中心工作原理
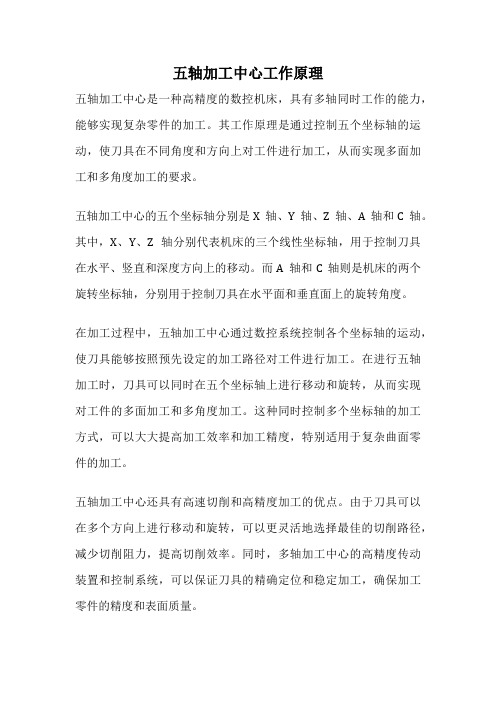
五轴加工中心工作原理
五轴加工中心是一种高精度的数控机床,具有多轴同时工作的能力,能够实现复杂零件的加工。
其工作原理是通过控制五个坐标轴的运动,使刀具在不同角度和方向上对工件进行加工,从而实现多面加工和多角度加工的要求。
五轴加工中心的五个坐标轴分别是X轴、Y轴、Z轴、A轴和C轴。
其中,X、Y、Z轴分别代表机床的三个线性坐标轴,用于控制刀具在水平、竖直和深度方向上的移动。
而A轴和C轴则是机床的两个旋转坐标轴,分别用于控制刀具在水平面和垂直面上的旋转角度。
在加工过程中,五轴加工中心通过数控系统控制各个坐标轴的运动,使刀具能够按照预先设定的加工路径对工件进行加工。
在进行五轴加工时,刀具可以同时在五个坐标轴上进行移动和旋转,从而实现对工件的多面加工和多角度加工。
这种同时控制多个坐标轴的加工方式,可以大大提高加工效率和加工精度,特别适用于复杂曲面零件的加工。
五轴加工中心还具有高速切削和高精度加工的优点。
由于刀具可以在多个方向上进行移动和旋转,可以更灵活地选择最佳的切削路径,减少切削阻力,提高切削效率。
同时,多轴加工中心的高精度传动装置和控制系统,可以保证刀具的精确定位和稳定加工,确保加工零件的精度和表面质量。
总的来说,五轴加工中心通过同时控制多个坐标轴的运动,实现了复杂零件的高效加工。
其工作原理是通过数控系统控制各个坐标轴的运动,使刀具在不同角度和方向上对工件进行加工。
五轴加工中心具有高速切削、高精度加工和多面加工的优点,适用于复杂曲面零件的加工,是现代制造业中不可或缺的重要设备。
五轴数控加工3D刀具补偿及其后置处理方法

五轴数控加工3D刀具补偿及其后置处理方法全文共四篇示例,供读者参考第一篇示例:随着制造业技术的不断进步,数控加工技术已经成为制造业中不可或缺的重要环节。
而在数控加工中,五轴数控加工技术由于其能够完成更为复杂、精密的加工工艺,受到了越来越多制造企业的青睐。
在五轴数控加工中,3D刀具补偿是一个至关重要的环节,它能够帮助提高加工质量和效率。
本文将从五轴数控加工3D刀具补偿的基本原理、常用方法以及后置处理方法等方面进行介绍。
一、五轴数控加工3D刀具补偿的基本原理1.1 3D刀具补偿的概念3D刀具补偿是指在数控加工过程中,通过对刀具轨迹进行补偿,使得实际加工轨迹与设计轨迹保持一致,从而达到精确加工的目的。
在五轴数控加工中,由于加工对象通常是复杂曲面或立体结构,因此需要对刀具轨迹进行三维补偿,以确保加工精度。
1.2 刀具轨迹误差的原因在五轴数控加工中,刀具轨迹误差主要受到机床动态响应、刀具偏心、刀具长度变化等因素的影响。
这些因素会导致实际加工轨迹偏离设计轨迹,从而影响加工精度和表面质量。
在实际加工中,通过对刀具轨迹进行3D补偿,可以对刀具偏差、刀具长度变化等进行校正,从而使实际加工轨迹更加接近设计轨迹。
常用的方法包括刀具半径补偿、刀尖补偿、刀具长度补偿等。
刀具半径补偿是指通过对刀具轨迹进行半径方向的补偿,以校正刀具切削半径偏差。
在五轴数控加工中,刀具通常以不同的姿态进行切削,因此需要根据刀具当前姿态对刀具轨迹进行三维补偿。
刀具半径补偿是常用的3D刀具补偿方法之一。
2.2 刀尖补偿在数控编程中,对刀具补偿的参数进行正确设置是保证加工质量的关键。
根据刀具类型、刀具位置、加工轨迹等因素,正确设置刀具补偿参数,可以有效提高加工精度和效率。
通过对刀具轨迹进行优化,可以减小刀具加工轨迹误差,提高加工精度。
在五轴数控加工中,刀具轨迹优化是一种常用的后置处理方法,通过对刀具轨迹进行优化,可以有效提高加工质量。
3.3 加工参数优化在实际加工中,调整加工参数也可以对刀具补偿效果进行优化。
数控五轴相关的课程
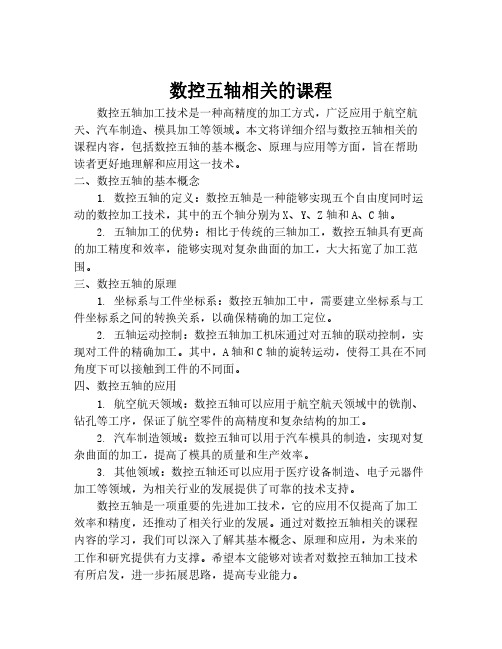
数控五轴相关的课程
数控五轴加工技术是一种高精度的加工方式,广泛应用于航空航天、汽车制造、模具加工等领域。
本文将详细介绍与数控五轴相关的课程内容,包括数控五轴的基本概念、原理与应用等方面,旨在帮助读者更好地理解和应用这一技术。
二、数控五轴的基本概念
1.数控五轴的定义:数控五轴是一种能够实现五个自由度同时运动的数控加工技术,其中的五个轴分别为X、Y、Z轴和A、C轴。
2.五轴加工的优势:相比于传统的三轴加工,数控五轴具有更高的加工精度和效率,能够实现对复杂曲面的加工,大大拓宽了加工范围。
三、数控五轴的原理
1.坐标系与工件坐标系:数控五轴加工中,需要建立坐标系与工件坐标系之间的转换关系,以确保精确的加工定位。
2.五轴运动控制:数控五轴加工机床通过对五轴的联动控制,实现对工件的精确加工。
其中,A轴和C轴的旋转运动,使得工具在不同角度下可以接触到工件的不同面。
四、数控五轴的应用
1.航空航天领域:数控五轴可以应用于航空航天领域中的铣削、钻孔等工序,保证了航空零件的高精度和复杂结构的加工。
2.汽车制造领域:数控五轴可以用于汽车模具的制造,实现对复杂曲面的加工,提高了模具的质量和生产效率。
3.其他领域:数控五轴还可以应用于医疗设备制造、电子元器件加工等领域,为相关行业的发展提供了可靠的技术支持。
数控五轴是一项重要的先进加工技术,它的应用不仅提高了加工效率和精度,还推动了相关行业的发展。
通过对数控五轴相关的课程内容的学习,我们可以深入了解其基本概念、原理和应用,为未来的工作和研究提供有力支撑。
希望本文能够对读者对数控五轴加工技术有所启发,进一步拓展思路,提高专业能力。
dmg五轴数控加工中心 的加工参数

一、概述随着现代制造业的发展,数控加工中心在加工精度和效率方面具有明显优势,已成为众多制造行业的重要设备。
而数控加工中心的加工参数对于加工效果和成本控制具有重要影响。
本文将针对dmg五轴数控加工中心的加工参数进行深入探讨,希望能够为相关行业的工程师和技术人员提供一些参考和指导。
二、加工速度参数1.1 进给速度进给速度是数控加工中心在加工过程中工件相对于刀具的运动速度,通常以毫米/分钟或英寸/分钟为单位。
对于不同材料的工件以及不同精度要求的加工,进给速度的设定会有所不同。
一般情况下,进给速度越高,加工效率越高,但是也会影响加工表面的光洁度和加工温度,需要根据具体情况进行合理调整。
1.2 主轴转速主轴转速是数控加工中心中刀具旋转的速度,通常以转/分钟为单位。
对于不同直径和材质的刀具,以及不同材料的工件,主轴转速的选择会影响加工效率和加工质量。
在选择主轴转速时,需要考虑刀具的切削速度和进给速度的配合,以及工件的硬度和切削性能。
三、切削参数2.1 切削深度切削深度是指刀具在加工过程中一次切削时所能切削的最大深度,通常以毫米或英寸为单位。
切削深度的选择会影响加工质量和加工效率,过大的切削深度容易造成刀具断裂或加工表面粗糙,而过小的切削深度则会导致加工效率低下。
在设定切削深度时,需要考虑工件的材料和硬度,以及刀具的刚性和切削性能。
2.2 切削速度切削速度是刀具在加工过程中实际切削时的线速度,通常以米/分钟或英寸/分钟为单位。
切削速度的选择与刀具材质、刀具直径和主轴转速密切相关,需要综合考虑切削热量、切削力和切削表面质量等因素。
合理的切削速度可以保证加工表面的光洁度和加工质量,同时也能提高加工效率和延长刀具寿命。
四、冷却参数3.1 冷却液类型在数控加工中心的加工过程中,冷却液的选择对于切削温度和切削表面质量具有重要影响。
不同材料和加工方式的工件,需要选择适当的冷却液类型,以确保切削区域的温度在合理范围内,同时也要注意冷却液对于工件表面的影响,避免出现腐蚀或氧化等负面影响。
五轴典型的加工案例

五轴典型的加工案例
五轴加工是数控加工技术中的一种高级加工方式,可以完成复杂形状
的加工任务。
以下列举了五轴加工的一些典型案例。
1.航空零部件加工:
五轴加工在航空零部件加工中得到了广泛应用。
例如,飞机发动机的
涡轮叶片、涡轮盘等复杂形状部件的加工。
五轴加工可以在一次夹持中完
成多个面的加工,减少零部件的夹持次数,提高加工精度和效率。
2.模具加工:
五轴加工在模具加工领域也有重要应用。
传统的模具加工方式需要多
次夹持和调整工件位置,而五轴加工可以通过工件的旋转和倾斜,使刀具
能够更自由地进入难以到达的角度,从而提高加工精度和效率。
3.医疗器械加工:
五轴加工在医疗器械加工领域也具有广泛的应用。
例如,人工关节的
加工中,五轴加工可以将刀具沿关节表面旋转和倾斜,使得关节表面得到
更好的加工质量和适配性。
4.船舶零部件加工:
五轴加工在船舶零部件加工中有重要作用。
例如,船舶螺旋桨的加工,五轴加工可以通过刀具的旋转和倾斜,使刀具能够更好地机械切削螺旋桨
的复杂表面,并提高螺旋桨的加工质量和效率。
5.汽车零部件加工:
五轴加工在汽车零部件加工中也得到广泛应用。
例如,汽车车身的冲压模具加工,五轴加工可以使刀具在模具表面的各个角度进行切削,使模具内部空腔的加工更加准确和高效。
总之,五轴加工的典型案例涵盖了航空、模具、医疗器械、船舶和汽车等多个领域。
这些案例体现了五轴加工在实际应用中的重要性和优势,通过五轴加工,可以实现复杂形状零部件的高精度、高效率的加工。
什么是五轴机床

什么是五轴机床什么是五轴机床随着国内数控技术的日渐成熟,近年来五轴联动数控加工中心在各领域得到了越来越广泛的应用。
在实际应用中,每当人们碰见异形复杂零件高效、高质量加工难题时,五轴联动技术无疑是解决这类问题的重要手段。
近几年随着我国航空航天、军事工业、汽车零部件和模具制造行业的蓬勃发展,越来越多的厂家倾向于寻找五轴设备来满足高效率、高质量的加工。
但是,你真的足够了解五轴加工吗?五轴加工想要真正的了解五轴加工,首先我们要做的是要读懂什么是五轴机床。
五轴机床(5 Axis Machining),顾名思义,是指在X、Y、Z,三根常见的直线轴上加上两根旋转轴。
A、B、C三轴中的两个旋转轴具有不同的运动方式,以满足各类产品的技术需求。
而在5轴加工中心的机械设计上,机床制造商始终坚持不懈地致力于开发出新的运动模式,以满足各种要求。
综合目前市场上各类五轴机床,虽然其机械结构形式多种多样,但是主要有以下几种形式:两个转动坐标直接控制刀具轴线的方向(双摆头形式)两个坐标轴在刀具顶端,但是旋转轴不与直线轴垂直(俯垂型摆头式)两个转动坐标直接控制空间的旋转(双转台形式)两个坐标轴在工作台上,但是旋转轴不与直线轴垂直(俯垂型工作台式)两个转动坐标一个作用在刀具上,一个作用在工件上(一摆一转形式)术语:如果旋转轴不与直线轴相垂直,则被认为是一根“俯垂型”轴。
看过这些结构的五轴机床,我相信我们应该明白了五轴机床什么在运动,怎样运动。
可是,这么多样化的机床结构,在加工时究竟能展现出哪些特点呢?与传统的三轴机床相比,又有哪些优势呢?接下来就让我们来看看五轴机床有哪些发光点。
5轴机床的特点说起五轴机床的特点,就要和传统的三轴设备来比较。
生产中三轴加工设备比较常见,有立式、卧式及龙门等几种形式。
常见的加工方法有立铣刀端刃加工、侧刃加工。
球头刀的仿形加工等等。
但无论哪种形式和方法都有着一个共同的特点,就是在加工过程中刀轴方向始终保持不变,机床只能通过X、Y、Z三个线性轴的插补来实现刀具在空间直角坐标系中的运动。
- 1、下载文档前请自行甄别文档内容的完整性,平台不提供额外的编辑、内容补充、找答案等附加服务。
- 2、"仅部分预览"的文档,不可在线预览部分如存在完整性等问题,可反馈申请退款(可完整预览的文档不适用该条件!)。
- 3、如文档侵犯您的权益,请联系客服反馈,我们会尽快为您处理(人工客服工作时间:9:00-18:30)。
M08 冷却液开启
67 L X+150.499 Y-56.284 FQ3 。。。 。。。
1223 L Z+38.000 FQ3 1224 L M127 1225 CALL LBL 170 1226 L M128
取消 M126 执行子程序“LBL 170” 用倾斜轴定位时保持刀尖位置(RTCP功能)
1227 L X+32.353 Y-3.083 Z+88.000 A0.000 C0.000 FQ3
: DMU100P-H530
16 ; Output Workplane : 1
17 ;
18 ; TOOL LIST : 3 tools
19 ; No. ID
Diameter Tip Rad Length
20 ; 1 e12
12.000Leabharlann 0.000 60.00021 ; 2 e12
12.000 0.000 60.000
define keys …… azimuth axis = A
elevation axis = C end define …… azimuth centre azimuth axis param …… rotary axis limits
= ( 0.0 0.0 0.0 ) = ( 0.0 0.0 0.0 1.0 0.0 0.0 )
49 CYCL DEF 32.1 T0.100
50 CYCL DEF 32.2 HSC-MODE:0
51 L M03
52 L M129
换刀指令,开转速,长度、半径补偿为 0 Z 轴回机床原点下 5mm Q 参数赋值下切速度 Q 参数赋值切削速度 Q 参数赋值快进抬刀速度 Q 参数赋值快进速度 激活高速高精度自适应循环 ATC 表面光洁度优先 表示工件重量为默认 激活公差循环 定义公差置(轮廓偏差) 定义公差置(更高的轮廓精度)
a) A局部截面示意图
b) B 局部截面示意图 图1 电器面盖模具前模
2、常规三轴数控加工工艺表,如表 1 所示:
行号 刀具和加工内容
加工 时间 (min)
路径轨迹图示
备注
φ12R0.5
1
开粗
61
φ8R0
2
二次开粗
15
φ6R0
3
二次开粗
12
φ3R0
4
二次开粗
10
φ2R0 局部二次
5
开粗
6
参考前一刀具路径作二 次开粗
所有刀具信息
22 ; 3 b10
10.000 5.000 50.000
23 ;
24 ; ESTIMATED CUTTING TIME : 3 TOOLPATHS = 00:12:34 )
理论加工时间
25 ;
26 LBL 170
27 CYCL DEF 7.0 DATUM SHIFT
原点平移
28 CYCL DEF 7.1 X0.000
45 Q3= +10000 ; RAPID SKIM FEEDRATE
46 Q4= +15000 ; RAPID FEEDRATE
47 CYCL DEF 392 ATC ~
Q240=+2 ;Process Mode ~
Q241=+2 ;Default Weight
48 CYCL DEF 32.0 TOLERANCE
φ3R1.5
11 清角
17
按刀具伸出长度和参考 φ8 球刀定义清角范围
φ2R1
12 清角
6
局部清角
合计时间
252 表1 三轴数控加工工艺表
上述三轴加工完成后,图1“B 局部截面示意图”中所示的 R 角位只能使用 R1.5 的球 头刀进行清角,并且局部陡峭位最小只能使用 R4 的球头刀;图1 “A局部截面示意图” 中所示的利角位最小使用R1的球头刀;分形枕位所有角位只能使用 R1.5 的球头刀进行清 角;所剩下的残留余量将留给电火花加工完成。
二、客户原有的模具数控编程加工工艺概况
为了更好的理解五轴加工技术所带来的效益,先对对客户原有的三轴加工工艺和工序状 况稍作介绍。
1、试切机床为德国的“DMG”(DMG-100P)机床;其行程为 1000×1000×1000mm; 控制系统为 heid530;主轴最高转速 24000rpm;使用年限:2007 年 12 月新购,至今将近 3 年;编程所用的 CAM 软件为 PowerMILL;使用的刀具材质为普通硬质合金涂层刀具;试切 工件是一电器面盖注塑模具前模,如图 1 所示:
= ( -125.0 10.0 -99000.0 99000.0 0.01 1 )
b) 增加特定的“ATC 高速高精度自适应功能” 即增加 CYCL DEF 392 ATC 循环指令,具 体修改参数如下:
define block user TOOL_CHANGE_COMMON N ; G1 ; " Z-5 FMAX" ; M1 91 =C
…… N ; " CYCL DEF 392 ATC ~ "
" Q240=+2 ;Process Mode ~ " " Q241=+2 ;Default Weight " end define
2.NC 程序代码含义 PowerMILL 后处理产生的 NC 程序段代码及含义如下:
0 BEGIN PGM 80_ATC MM
近段时间,珠海某大型电器模具厂采购我司的五轴数控编程软件 PowerMILL,本人接 受公司的任务,为该客户进行五轴技术的培训辅导,并结合实际加工进行模具的试切,实例 指导客户应用五轴加工技术,让客户看到了客观具体的三轴加工与五轴加工两者的效率和质 量对比数据。本文即以此次培训五轴工件试切为例,禅述在电器注塑模具加工当中,五轴数 控加工技术相对于传统的三轴数控加工技术的若干优越性。
60 L A+Q120 C+Q122 FQ4 M126
用TNC 计算的值定位,M126旋转轴旋转轴上的最短
路径移动
62 ; ========= 63 ; TOOLPATH : rou-e12 64 ; WORKPLANE : World
当前刀具路径名 程序编写用户坐标系
65 ; ========= 66 L M08
29 CYCL DEF 7.2 Y0.000
定义子程序“LBL 170”
30 CYCL DEF 7.3 Z0.000
31 PLANE RESET STAY
PLANE 功能复位(倾斜加工面)
32 LBL 0 33 BLK FORM 0.1 Z X-60.009 Y-50.003 Z-25.0
定义毛坯形状
一、五轴数控加工技术简述
1、五轴刀轴和五轴刀轴控制 五轴是由 3 个线性轴(Linear axis) 加上 2 个旋转轴(Rotary axis)组成。 五轴刀轴控制是 CAM 系统五轴技术的核心。五轴 CAM 系统计算出每个切削点刀具的 刀位点(X,Y,Z)和刀轴矢量(I,J,K),五轴后处理器将刀轴矢量(I,J,K)转化为不同机床的旋转轴 所需要转动的角度(A,B,C)其中的两个角度;然后计算出考虑了刀轴旋转之后线性移动的各 轴位移(X,Y,Z)。
参考前一刀具路径作二 次开粗
参考前一刀具路径对刀 具长度允许范围作二次 开粗
参考前一刀具路径对局 部范围作二次开粗
φ8R4
6
中光加工
30
φ8R4
7
精加工
75
φ12R0.5
8
中光加工
6
φ12R0.5
9
精加工
10
φ3R0 光平面和
10 斜度面精加工
4
中光分形面和料位
精加工分形面和料位 带 2 度斜度直纹面中光加 工 带 2 度斜度直纹面精加工 光平面和斜度面精加工
三、五轴加工工件试切
1.根据机床结构和控制系统型号修改后处理文件 试切机床为德国“DMG”(DMU -100P)机;行程 1000×1000×1000mm;heid530 控 制系统,此机床为 Table-Head 型,两个旋转轴分别放置在主轴和工作台上,工作台旋转, 主轴摆动,改变刀轴方向灵活,且为非标 DMU -100P 机床,与一般的标准 DMU -100P 机床 不同之处在于主轴摆动轴是绕 X 轴旋转为 A 轴,摆角为-125 度至 10 度,而不是主轴摆动轴 是绕 Y 轴旋转的 B 轴,摆角为-100 度至 90 度。另外,还需增加特定的“ATC 高速高精度自 适应功能”指令。所以还需对 PowerMILL 标准后处理文件(*.opt)作修改: a) 将摆动轴设置为“azimuth axis = A”,将摆动轴的旋转参照轴改为 X 轴“azimuth axis param = ( 0.0 0.0 0.0 1.0 0.0 0.0 ) ” 将旋转轴的摆动极限修改为-125 度至 10 度 “rotary axis limits = ( -125.0 10.0 -99000.0 99000.0 0.01 1 ) ”具体修改参数如下:
1228 L X-31.465 Y-38.000 Z+67.500 。。。 。。。
1708 L X+111.057 Y+21.866 Z+30.000 FQ3
当前刀具信息
40 ; TOOL DIA. 12.000 LENGTH 60.000
41 TOOL CALL 1 Z S3500 DL+0.0 DR+0.0
42 L Z-5 FMAX M91
43 Q1= +1500
; PLUNGE FEEDRATE
44 Q2= +2200
; CUTTING FEEDRATE
2、五轴机床类型 按两旋转轴的运动位置结构来划分,可分为 Table-Table、Head-Head、Table-Head 三种 类型。 1)Table-Table:此类型机床主轴方向不动,两个旋转轴均分布在工作平台上;工件加 工时旋转轴随工作台旋转,加工时必须考虑装夹承重,可加工的工件尺寸比较小。 2)Head-Head:此类机床工作台不动,两个旋转轴均在主轴上。机床可加工的工件尺 寸比较大。 3)Table-Head:此类机床的两个旋转轴分别处于主轴和工作台上,工作台可以旋转, 可装夹尺寸较大的工件;主轴可摆动,改变刀轴方向灵活。 3、定位五轴与联运五轴 根据刀轴参与的加工方案来划分类型,一般可分为如下两类: 1)定位五轴(3+2 轴) 定位五轴的刀轴矢量可以进行改变,但固定后沿着整个切削路径过程刀轴矢量不变,控 制路径轴 X、Y、Z 参与旋转轴 A(或者 B)、C,既是旋转轴 A(或者 B)、C 定位后保持不变, 只有 X、Y、Z 参与控制机床切削移动。 2)联动五轴 整个切削路径过程刀轴矢量可根据要求进行改变变,控制路径轴 X、Y、Z 控制旋转 A(B)、 C,即是通常所说的五轴联动加工技术。