机械零件结构设计的可靠性分析
机械设计中的产品可靠性分析与评估

机械设计中的产品可靠性分析与评估在当今竞争激烈的市场环境中,机械产品的可靠性已成为企业赢得市场份额和用户信任的关键因素。
可靠性不仅关系到产品的质量和性能,更直接影响着用户的满意度和企业的声誉。
因此,在机械设计过程中,对产品可靠性进行深入的分析与评估具有重要的意义。
一、产品可靠性的概念与重要性产品可靠性,简单来说,是指产品在规定的条件下和规定的时间内,完成规定功能的能力。
这包括了产品在使用过程中的稳定性、耐久性、无故障工作时间等多个方面。
一个可靠的机械产品,能够在各种复杂的工作环境和使用条件下,持续稳定地运行,减少故障和维修的次数,从而为用户提供更好的服务,同时也降低了企业的售后成本。
对于企业而言,产品可靠性的重要性不言而喻。
首先,高可靠性的产品能够提升企业的市场竞争力。
在消费者选择产品时,往往更倾向于那些质量可靠、故障少的品牌。
其次,可靠的产品有助于降低生产成本。
虽然在提高可靠性的过程中可能需要增加前期的研发投入,但由于减少了后期的维修和更换成本,总体成本反而会降低。
再者,良好的可靠性能够增强企业的声誉和品牌形象,促进企业的长期发展。
二、影响产品可靠性的因素在机械设计中,有众多因素会影响产品的可靠性。
设计方面,不合理的结构设计、选用了不合适的材料、零部件之间的匹配度不足等,都可能导致产品在使用过程中出现故障。
制造工艺的优劣也直接关系到产品的质量和可靠性。
例如,加工精度不够、装配不当等都会影响产品的性能和寿命。
此外,使用环境也是一个重要的影响因素。
机械产品在高温、高湿、高压、强腐蚀等恶劣环境下工作,其可靠性会受到极大的挑战。
而用户的操作和维护方式同样不可忽视。
不正确的操作方法、不及时的维护保养,都可能加速产品的损坏。
三、产品可靠性分析方法为了准确评估机械产品的可靠性,需要采用一系列的分析方法。
故障模式与影响分析(FMEA)是一种常用的方法。
它通过对产品可能出现的故障模式进行分析,评估每种故障模式的影响程度和发生概率,从而找出潜在的薄弱环节,并采取相应的改进措施。
机械零件的可靠性设计

3
加强维护
定期维护和保养机械零件,延长其寿命并提高可靠性。
可靠性测试和验证
测试方法
使用可靠性测试方法来验证零件的寿命和性能。
验证过程
验证设计的可靠性,确保其在实际使用中能够达到 预期要求。
案例研究和实践经验
1
汽车发动机设计
通过可靠性改进措施和测试验证,成功提高了发动机的可靠性和性能。
2
航空航天器零件
可靠性评估方法
故障模式与影响分析 (FMEA)
通过识别故障模式和评估其影响,确定潜在故障并采取措施预防。
可靠性指标计算
计算关键零件的故障率、平均寿命等指标,用于评估系统的可靠性水平。
可靠性改进措施
1
优化设计
通过改善设计来减少潜在的故障点,提高分析、可靠性预测等工具来预防和诊断故障。
在航空航天工程中,可靠性设计是确保安全和可靠运行的核心要素。
3
电力设备
在电力行业,可靠性设计是保障稳定供电和电网安全的关键。
机械零件的可靠性设计
在机械工程中,可靠性设计至关重要。本演示将介绍可靠性设计的基本原则, 影响因素和评估方法,以及可靠性改进和测试验证的案例研究和实践经验。
机械零件的可靠性设计的意义
1 保证性能
可靠性设计确保机械零件在使用期间保持良好性能,降低故障率,以满足用户需求。
2 成本节约
通过提前识别和解决潜在问题,可靠性设计可以减少维修和更换零件的成本。
可靠性设计的基本原则
设计简化
简化设计可以减少故障点,提 高系统的可靠性。
材料选择
选择适当的材料可以提高零件 的耐用性和抗腐蚀性。
质量控制
严格控制零件生产过程中的质 量,可以降低缺陷率。
汽车机械制造的可靠性分析与改进

汽车机械制造的可靠性分析与改进在汽车行业,可靠性是一个极其重要的指标。
它是衡量汽车产品质量的重要标准之一,同时也影响着汽车用户的满意度和品牌声誉。
因此,对于汽车机械制造的可靠性进行分析和改进是必不可少的。
本文将对汽车机械制造的可靠性进行深入分析,并提出相应的改进措施。
一、可靠性分析汽车机械制造的可靠性是指在一定的使用条件下,汽车机械系统正常运行所需要的时间,也可以理解为在一定时间内发生故障的概率。
在汽车制造中,可靠性分析通常包括以下几个方面:1. 故障率分析故障率是可靠性分析的重要指标之一,它体现了汽车机械系统的故障情况。
一般来说,故障率可以通过统计一段时间内发生故障的次数来计算。
通过对汽车机械系统的故障率进行分析,可以确定出故障频繁发生的部件,从而有针对性地进行改进和优化。
2. 维修时间分析维修时间也是衡量汽车机械系统可靠性的重要指标。
维修时间包括故障发生后的排除时间和维修时间两个方面。
通过对维修时间的分析,可以评估汽车机械系统的可靠性,找出维修时间较长的部件,进行相应的优化和改进。
3. 失效模式分析失效模式分析是对汽车机械系统故障的分析方法之一。
通过对失效模式的分析,可以确定出造成故障的具体原因,进而针对性地采取措施。
例如,如果发现某个零部件在高温条件下容易失效,那么可以考虑采用耐高温材料替代,以减少故障的发生。
二、改进措施基于对汽车机械制造的可靠性分析,可以提出以下改进措施,以提高汽车机械系统的可靠性:1. 材料优化选用高质量、高可靠性的材料是提高汽车机械系统可靠性的关键。
在材料选择方面,应考虑到材料的强度、耐磨性、耐腐蚀性等因素,并尽量选择具有良好可靠性记录的材料。
2. 工艺改进改进技术工艺是提高汽车机械系统可靠性的重要手段之一。
通过对工艺流程的优化和改进,可以降低汽车机械系统的故障率。
例如,合理安排和控制焊接温度、提高加工精度等都可以有效减少故障的发生。
3. 设计优化在汽车机械系统的设计过程中,应注重可靠性的考虑。
机械零部件 的可靠性设计分析

机械零部件的可靠性设计分析摘要:机械零部件是机械设备的运行基础,其质量、性能等代表着机械设备的工作精度与生命周期。
为此,应定期对机械零部件进行维修养护,通过参数基准检测零部件动态化运行模式,以提升零部件的可靠性。
文章对机械零部件的可靠性进行论述,并对机械零部件的可靠性设计进行研究。
关键词:机械零部件;可靠性设计;分析对于机械零部件的质量来说,它的可靠性是十分重要的,它可以保证机械的使用寿命以及质量,是我国机械加工时应该注意的一项。
1 机械零部件的可靠性概述零部件在机械设备中起到负载、部件联动、动力传输的重要作用,在设备长时间工作状态下,零部件易发生是失效现象,令机械设备产生故障。
当零部件发生损毁现象时,例如老化、堵塞、松脱等,将增加联动部件的运行压力,提升零部件故障检测的难度。
此外,机械设备加工工艺、工作原理存在差异性,在零部件基准参数方面难以进行统一,只有少部分密封件、阀门、泵体等零部件实现通用化、标准化。
为此,在对零部件的可靠性进行设计时,零部件的荷载分布能力、材料强度等则应作为主要突破点。
2 机械零部件的可靠性设计分析2.1 可靠性优化设计可靠性优化设计是以可靠性为前提而开展的更完善的设计工作,不仅可以满足产品在使用过程中的可靠性,还将产品的尺寸、成本、质量、体积与安全性能等得到进一步的改善提高,进而保障结构的预测工作和实际工作性能更契合,能够把可靠性分析理论和数学规划方法合理地融合到一起。
在对各参数开始可靠性优化设计时,首先把机械零部件的可靠度当成优化的目标函数,把零部件的部分标准如成本、质量、体积、尺寸最大限度地缩小,再把强度、刚度、稳定性等设计标准作为约束基础设立可靠性优化设计数学模型,依据模型的规模、性能、复杂程度等确定适宜的优化方式,最后得出最优设计变量。
2.2 可靠性灵敏度设计可靠性灵敏度设计指的是确定机械零部件中的各个参数的变化情况对机械零部件时效的影响程度。
通过灵敏度设计,便于我们找到那些对可靠性设计敏感性较大的参数,后续对这些参数进一步分析并重新设计。
机械设计中的可靠性分析
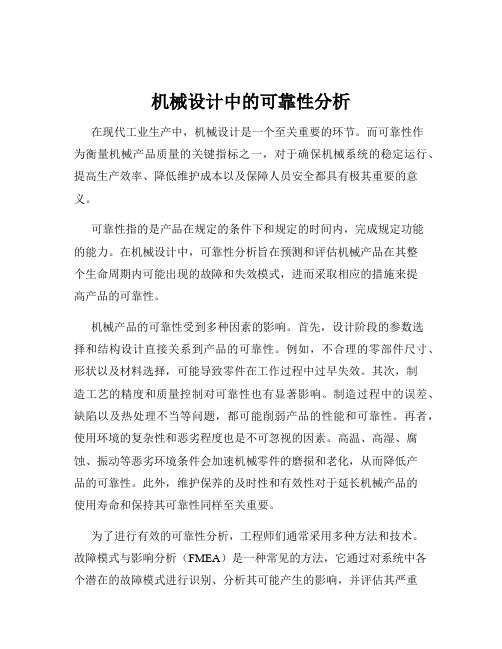
机械设计中的可靠性分析在现代工业生产中,机械设计是一个至关重要的环节。
而可靠性作为衡量机械产品质量的关键指标之一,对于确保机械系统的稳定运行、提高生产效率、降低维护成本以及保障人员安全都具有极其重要的意义。
可靠性指的是产品在规定的条件下和规定的时间内,完成规定功能的能力。
在机械设计中,可靠性分析旨在预测和评估机械产品在其整个生命周期内可能出现的故障和失效模式,进而采取相应的措施来提高产品的可靠性。
机械产品的可靠性受到多种因素的影响。
首先,设计阶段的参数选择和结构设计直接关系到产品的可靠性。
例如,不合理的零部件尺寸、形状以及材料选择,可能导致零件在工作过程中过早失效。
其次,制造工艺的精度和质量控制对可靠性也有显著影响。
制造过程中的误差、缺陷以及热处理不当等问题,都可能削弱产品的性能和可靠性。
再者,使用环境的复杂性和恶劣程度也是不可忽视的因素。
高温、高湿、腐蚀、振动等恶劣环境条件会加速机械零件的磨损和老化,从而降低产品的可靠性。
此外,维护保养的及时性和有效性对于延长机械产品的使用寿命和保持其可靠性同样至关重要。
为了进行有效的可靠性分析,工程师们通常采用多种方法和技术。
故障模式与影响分析(FMEA)是一种常见的方法,它通过对系统中各个潜在的故障模式进行识别、分析其可能产生的影响,并评估其严重程度、发生概率和检测难度,从而为设计改进提供依据。
另一种常用的方法是故障树分析(FTA),它以系统的故障为顶事件,通过逻辑推理逐步找出导致故障发生的各种原因组合,有助于深入了解系统的故障机理和制定针对性的预防措施。
可靠性试验也是可靠性分析的重要手段之一。
通过对机械产品进行模拟实际工作条件的试验,可以直接观察和记录产品的性能变化和故障情况,为可靠性评估提供真实可靠的数据。
此外,基于概率统计的可靠性计算方法,如应力强度干涉模型,可以定量地评估机械零件在给定工作条件下的可靠度。
在机械设计过程中,提高可靠性的措施多种多样。
机械产品的可靠性设计与分析

机械产品的可靠性设计与分析在当今高度工业化的社会中,机械产品在各个领域都发挥着至关重要的作用。
从日常生活中的家用电器到工业生产线上的大型设备,从交通运输工具到航空航天领域的精密仪器,机械产品的可靠性直接影响着人们的生活质量、生产效率以及生命财产安全。
因此,机械产品的可靠性设计与分析成为了机械工程领域中一个极其重要的研究课题。
可靠性设计是指在产品设计阶段,通过采用各种技术和方法,确保产品在规定的条件下和规定的时间内,能够完成规定的功能,并且具有较低的故障率和较长的使用寿命。
可靠性分析则是对产品的可靠性进行评估和预测,找出可能存在的薄弱环节,为改进设计提供依据。
在机械产品的可靠性设计中,首先要进行的是需求分析。
这就需要充分了解产品的使用环境、工作条件、用户要求以及相关的标准和规范。
例如,对于一台用于户外作业的工程机械,需要考虑到恶劣的天气条件、复杂的地形地貌以及高强度的工作负荷等因素;而对于一台家用洗衣机,需要重点关注其洗涤效果、噪声水平和使用寿命等方面的要求。
只有明确了这些需求,才能为后续的设计工作提供正确的方向。
材料的选择是影响机械产品可靠性的重要因素之一。
不同的材料具有不同的物理、化学和机械性能,因此需要根据产品的工作要求和使用环境,选择合适的材料。
例如,在高温、高压和腐蚀环境下工作的零件,需要选用耐高温、耐高压和耐腐蚀的材料;对于承受重载和冲击载荷的零件,则需要选用高强度和高韧性的材料。
同时,还要考虑材料的成本和可加工性等因素,以确保产品在满足可靠性要求的前提下,具有良好的经济性。
结构设计也是可靠性设计的关键环节。
合理的结构设计可以有效地减少应力集中、提高零件的承载能力和抗疲劳性能。
例如,采用圆角过渡可以避免尖锐的棱角引起的应力集中;采用对称结构可以使载荷分布更加均匀;采用加强筋和肋板可以提高结构的刚度和强度。
此外,还需要考虑结构的装配和维修便利性,以便在产品出现故障时能够快速进行维修和更换零件。
机械零件的可靠性设计
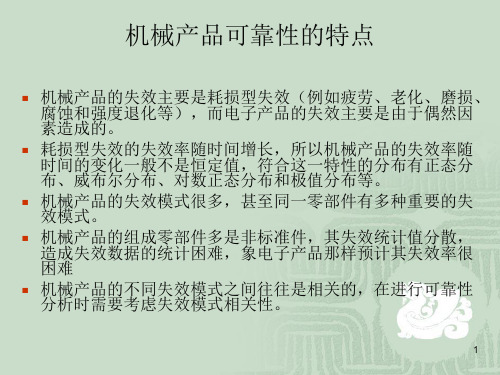
R2 1
X XS
2
2 S
1
350 310 302 102
1 (1.26) 1 0.1038 0.8962
28
(3)“R3σ”可靠性含义下的安全系数:
50000 30000
1.67
R1 1(ZR ) 1
S
2+
2 S
1
50000 30000 10002 30002
1.000
R2 1
S
2+
2 S
1
50000 30000 120002 30002
0.947
27
例2 某汽车零件,其强度和应力均服从正态分布,强度的均
17
例题1
当强度的标准差增大到120MPa时,
z s 850 380 470 3.6968
2
2 S
422 1202 127.1377
查标准正态分布值,得R=0.999 89.
18
2、概率密度函数联合积分法(一般情况)
g()
f (s)
应力s0处于ds区间内的概率为
f (s0 )
f ( )
f (s)
1 2
y
0 exp[
(
y
y
2
2 y
)2
]dy
y S
y=-S
0
-10
0
10
20
y =-S
y0 y0
30
40
S
50
y=
2
2 S
不可靠度为: F P ( y 0)
1
2 y
0
exp[
(
y
y
机械设计中的可靠性分析
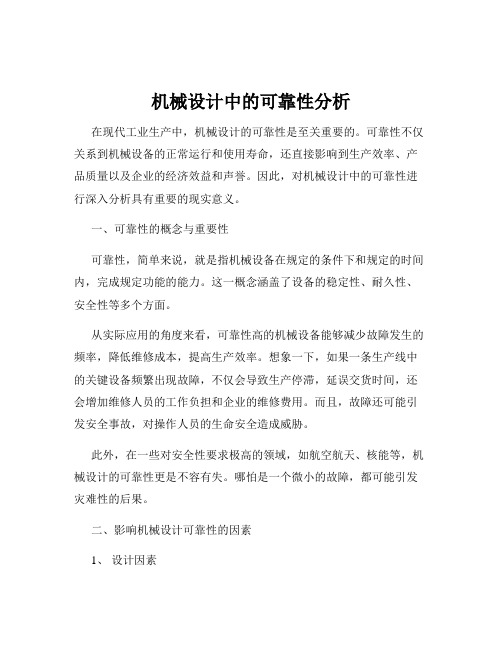
机械设计中的可靠性分析在现代工业生产中,机械设计的可靠性是至关重要的。
可靠性不仅关系到机械设备的正常运行和使用寿命,还直接影响到生产效率、产品质量以及企业的经济效益和声誉。
因此,对机械设计中的可靠性进行深入分析具有重要的现实意义。
一、可靠性的概念与重要性可靠性,简单来说,就是指机械设备在规定的条件下和规定的时间内,完成规定功能的能力。
这一概念涵盖了设备的稳定性、耐久性、安全性等多个方面。
从实际应用的角度来看,可靠性高的机械设备能够减少故障发生的频率,降低维修成本,提高生产效率。
想象一下,如果一条生产线中的关键设备频繁出现故障,不仅会导致生产停滞,延误交货时间,还会增加维修人员的工作负担和企业的维修费用。
而且,故障还可能引发安全事故,对操作人员的生命安全造成威胁。
此外,在一些对安全性要求极高的领域,如航空航天、核能等,机械设计的可靠性更是不容有失。
哪怕是一个微小的故障,都可能引发灾难性的后果。
二、影响机械设计可靠性的因素1、设计因素设计阶段是决定机械设备可靠性的关键环节。
不合理的设计方案,如结构强度不足、零部件选型不当、运动副配合不良等,都可能导致设备在运行过程中出现故障。
例如,在设计一个传动系统时,如果没有充分考虑到负载的变化和冲击,选择的齿轮模数过小,就容易出现齿面磨损甚至断齿的现象。
2、材料因素材料的性能直接影响着机械设备的可靠性。
选用质量低劣、性能不稳定的材料,会使设备在使用过程中容易出现变形、断裂、腐蚀等问题。
比如,在高温、高压的工作环境中,如果选用的金属材料耐高温、高压性能不足,就会很快失效。
3、制造工艺因素制造过程中的加工精度、装配质量等都会对机械的可靠性产生影响。
粗糙的加工表面、过大的装配误差,都可能导致零部件之间的配合不良,从而影响设备的整体性能。
4、使用和维护因素即使机械设备在设计、制造阶段都具备了较高的可靠性,但如果在使用过程中操作不当、维护不及时,也会大大降低其可靠性。
比如,设备长期超负荷运行、润滑不良、未按时进行保养和检修等,都会加速设备的磨损和老化,缩短其使用寿命。
机械结构的失效模式与可靠性分析

机械结构的失效模式与可靠性分析为了确保机械设备的正常运行和安全性,对机械结构的失效模式进行可靠性分析是非常重要的。
机械结构的失效模式主要包括疲劳失效、磨损失效和断裂失效等。
不同的失效模式对机械设备的可靠性有着不同的影响。
首先,疲劳失效是机械结构中最常见的一种失效模式。
由于长期的振动和循环载荷作用,材料中的应力集中会引起裂纹的生成和扩展,最终导致零部件的失效。
为了分析机械结构的疲劳失效,可以进行应力分析和疲劳寿命预测。
通过应力分析可以确定机械结构中的应力分布,从而可以判断零部件是否存在应力集中的情况。
通过疲劳寿命预测可以根据机械结构的工作状态和材料的疲劳性能来估计零部件的寿命。
在实际生产中,可以通过增加材料的强度、改善表面质量和加强润滑等方式来提高机械结构的疲劳强度。
其次,磨损失效也是机械结构中常见的一种失效模式。
由于摩擦和磨损的作用,机械结构中的零部件表面会逐渐磨损,导致间隙的增大和机械性能的下降。
为了分析机械结构的磨损失效,可以进行磨损试验和铁粉分析。
通过磨损试验可以模拟机械结构在实际运行中的磨损过程,从而可以验证磨损速率的预测模型。
通过铁粉分析可以观察机械结构中零部件的磨损情况,从而可以判断机械结构是否存在磨损失效的风险。
在实际生产中,可以通过表面处理、润滑和更换磨损零部件等方式来延长机械结构的使用寿命。
另外,断裂失效也是机械结构中需要关注的一种失效模式。
当机械结构中的零部件由于超过其承载能力而发生破裂时,就会导致断裂失效。
为了分析机械结构的断裂失效,可以进行应力分析和破裂力学分析。
通过应力分析可以确定零部件的最大应力和应力集中的位置,从而可以判断零部件是否存在超载的风险。
通过破裂力学分析可以计算零部件的断裂韧性和临界应力强度因子,从而可以预测零部件的断裂寿命。
在实际生产中,可以通过增加材料的韧性、改善加工工艺和提高结构强度等方式来提高机械结构的抗断裂能力。
综上所述,机械结构的失效模式与可靠性分析对于确保机械设备的正常运行和安全性至关重要。
机械产品结构可靠性设计的十种方法
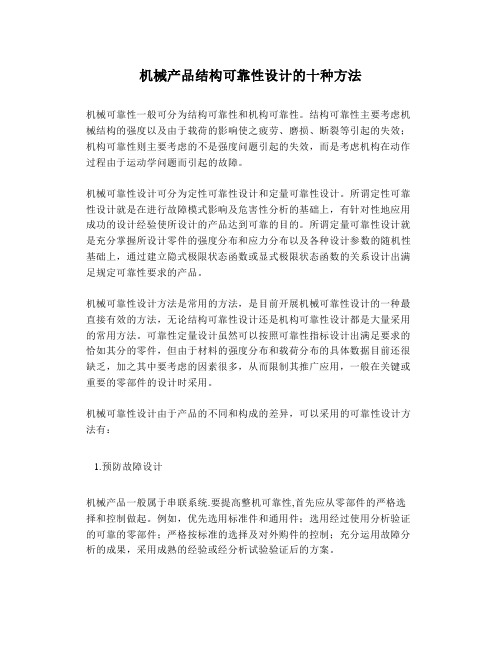
机械产品结构可靠性设计的十种方法机械可靠性一般可分为结构可靠性和机构可靠性。
结构可靠性主要考虑机械结构的强度以及由于载荷的影响使之疲劳、磨损、断裂等引起的失效;机构可靠性则主要考虑的不是强度问题引起的失效,而是考虑机构在动作过程由于运动学问题而引起的故障。
机械可靠性设计可分为定性可靠性设计和定量可靠性设计。
所谓定性可靠性设计就是在进行故障模式影响及危害性分析的基础上,有针对性地应用成功的设计经验使所设计的产品达到可靠的目的。
所谓定量可靠性设计就是充分掌握所设计零件的强度分布和应力分布以及各种设计参数的随机性基础上,通过建立隐式极限状态函数或显式极限状态函数的关系设计出满足规定可靠性要求的产品。
机械可靠性设计方法是常用的方法,是目前开展机械可靠性设计的一种最直接有效的方法,无论结构可靠性设计还是机构可靠性设计都是大量采用的常用方法。
可靠性定量设计虽然可以按照可靠性指标设计出满足要求的恰如其分的零件,但由于材料的强度分布和载荷分布的具体数据目前还很缺乏,加之其中要考虑的因素很多,从而限制其推广应用,一般在关键或重要的零部件的设计时采用。
机械可靠性设计由于产品的不同和构成的差异,可以采用的可靠性设计方法有:1.预防故障设计机械产品一般属于串联系统.要提高整机可靠性,首先应从零部件的严格选择和控制做起。
例如,优先选用标准件和通用件;选用经过使用分析验证的可靠的零部件;严格按标准的选择及对外购件的控制;充分运用故障分析的成果,采用成熟的经验或经分析试验验证后的方案。
2.简化设计在满足预定功能的情况下,机械设计应力求简单、零部件的数量应尽可能减少,越简单越可靠是可靠性设计的一个基本原则,是减少故障提高可靠性的最有效方法。
但不能因为减少零件而使其它零件执行超常功能或在高应力的条件下工作。
否则,简化设计将达不到提高可靠性的目的。
3.降额设计和安全裕度设计降额设计是使零部件的使用应力低于其额定应力的一种设计方法。
机械设计中的可靠性分析与评估
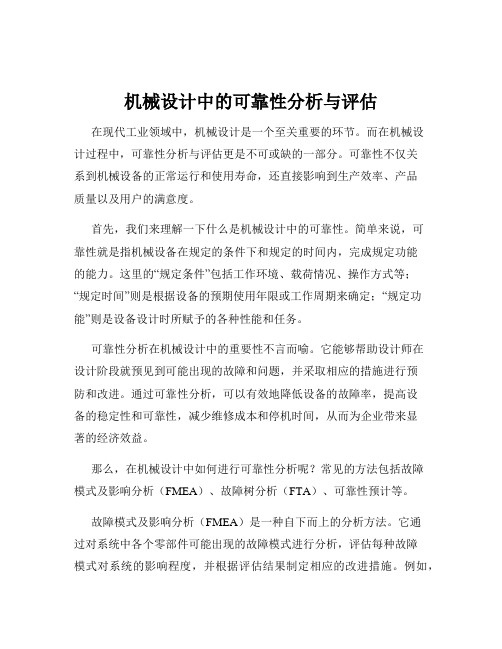
机械设计中的可靠性分析与评估在现代工业领域中,机械设计是一个至关重要的环节。
而在机械设计过程中,可靠性分析与评估更是不可或缺的一部分。
可靠性不仅关系到机械设备的正常运行和使用寿命,还直接影响到生产效率、产品质量以及用户的满意度。
首先,我们来理解一下什么是机械设计中的可靠性。
简单来说,可靠性就是指机械设备在规定的条件下和规定的时间内,完成规定功能的能力。
这里的“规定条件”包括工作环境、载荷情况、操作方式等;“规定时间”则是根据设备的预期使用年限或工作周期来确定;“规定功能”则是设备设计时所赋予的各种性能和任务。
可靠性分析在机械设计中的重要性不言而喻。
它能够帮助设计师在设计阶段就预见到可能出现的故障和问题,并采取相应的措施进行预防和改进。
通过可靠性分析,可以有效地降低设备的故障率,提高设备的稳定性和可靠性,减少维修成本和停机时间,从而为企业带来显著的经济效益。
那么,在机械设计中如何进行可靠性分析呢?常见的方法包括故障模式及影响分析(FMEA)、故障树分析(FTA)、可靠性预计等。
故障模式及影响分析(FMEA)是一种自下而上的分析方法。
它通过对系统中各个零部件可能出现的故障模式进行分析,评估每种故障模式对系统的影响程度,并根据评估结果制定相应的改进措施。
例如,在汽车发动机的设计中,通过 FMEA 可以分析出活塞、连杆、曲轴等零部件可能出现的磨损、断裂等故障模式,以及这些故障对发动机性能的影响,从而在设计阶段就选择合适的材料、优化结构设计,以提高发动机的可靠性。
故障树分析(FTA)则是一种自上而下的分析方法。
它从系统可能出现的故障(顶事件)开始,逐步分析导致故障发生的各种原因(中间事件和底事件),并建立起故障树模型。
通过对故障树的定性和定量分析,可以确定系统的薄弱环节,为提高系统的可靠性提供依据。
比如,对于飞机起落架系统的可靠性分析,可以以起落架无法正常放下这一顶事件为起点,构建故障树,分析诸如液压系统故障、机械结构损坏等原因,从而有针对性地进行改进和优化。
机械工程中的可靠性分析与优化设计

机械工程中的可靠性分析与优化设计在机械工程中,可靠性是一个至关重要的概念。
机械设备的可靠性决定了它们是否能够在设计寿命内正常运行,而可靠性分析与优化设计则是确保机械设备具有高度可靠性的关键。
可靠性分析是通过对机械设备的各种故障形式和失效原因进行分析,以确定可能导致失效的主要因素。
这些因素可以包括材料质量、制造工艺、工作环境等等。
通过对这些因素的分析,可以找出引起故障的根本原因,并采取相应的措施来提高机械设备的可靠性。
一种常用的可靠性分析方法是故障模式和效应分析(Failure Mode and Effects Analysis,简称FMEA)。
FMEA的基本原理是通过分析潜在的失效模式和它们对系统性能的影响,来确定机械设备中的关键零部件和失效途径。
通过对失效途径的分析,可以找出引起故障的原因,并采取相应的措施来预防故障的发生。
而在可靠性优化设计方面,一种常用的方法是可靠性设计优化(Reliability-based Design Optimization,简称RBDO)。
RBDO是一种结合了可靠性分析和优化技术的方法,旨在通过将可靠性约束嵌入到设计优化过程中,以实现对机械设备的可靠性进行优化。
在RBDO中,首先需要对机械设备的可靠性进行分析,确定失效概率和可靠度等指标。
然后,在设计优化过程中,将这些可靠性指标作为约束条件,以保证设计方案具有足够的可靠性。
通过不断优化设计方案,可以得到一个在可靠性和性能方面都达到最优的机械设备。
除了这些传统的可靠性分析与优化方法外,近年来一些新兴的技术也被应用到机械工程中的可靠性分析与优化设计中。
例如,基于故障树分析(Fault Tree Analysis,简称FTA)的可靠性分析方法可以更加直观地描述故障的发生途径;而基于人工智能技术的优化算法如遗传算法、神经网络等能够更高效地搜索最优解。
需要注意的是,机械工程中的可靠性分析与优化设计应该考虑的因素众多。
除了上述提到的材料质量、制造工艺、工作环境等外,还包括设计参数的选择、零部件的可靠性要求、运输和安装过程中的影响等。
机械结构强度与可靠性分析

机械结构强度与可靠性分析机械结构是指由各种零部件组成的机械系统的骨架。
在设计和制造过程中,机械结构的强度和可靠性是非常重要的考虑因素。
强度指材料能够承受的外部力和内部应力的能力,而可靠性则涉及到结构在使用过程中的寿命和稳定性。
本文将探讨机械结构强度与可靠性分析的相关内容。
一、强度分析机械结构的强度分析是指对其受力情况进行计算和评估的过程。
强度分析通常包括材料力学、应力分布分析和结构稳定性等方面。
在材料力学中,我们常常使用应力-应变曲线来描述材料的力学性能。
这条曲线包括弹性阶段、屈服阶段和断裂阶段等不同阶段。
通过强度分析,我们可以确定机械结构在不同的受力情况下是否会发生塑性变形或者破坏。
应力分布分析是通过数值计算或实验方法获得机械结构的应力分布情况。
这可以帮助我们确定结构的应力集中区域和曲率变化等特征。
通过优化设计,我们可以减少应力集中,提高结构的强度和可靠性。
结构稳定性分析是指在外部力作用下,结构的变形能否保持稳定。
结构的稳定性与结构的几何形状和材料的刚度有关。
通常,我们会进行线性弹性稳定和非线性稳定分析,以确定结构的临界负载。
二、可靠性分析可靠性分析是指对机械结构在使用过程中的寿命和失效风险进行评估和管理的过程。
主要包括可靠性设计、失效模式与影响分析和寿命预测等。
可靠性设计是在结构设计过程中考虑到各种不确定性因素,确保结构在使用寿命内不发生失效。
这需要综合考虑材料、设计参数、加载条件等多个因素,并采用一些安全系数和可靠性指标进行设计。
失效模式与影响分析是通过对机械结构失效原因和失效模式进行分析,以及失效对系统正常工作的影响程度来识别潜在的失效风险。
这有助于我们制定正确的维修和保养方案,延长结构的使用寿命。
寿命预测是通过考虑结构的材料损伤和疲劳等性质,预测结构的使用寿命。
这可以通过实验和数值模拟相结合的方法得出,帮助我们制定合理的维修和更换策略。
总之,机械结构的强度与可靠性分析是设计和制造过程中不可或缺的环节。
机械结构的可靠性分析与改进设计

机械结构的可靠性分析与改进设计引言机械结构作为现代工程的核心组成部分,其可靠性分析和改进设计对于提高产品质量和降低故障率具有重要意义。
随着科技的不断进步和市场的竞争加剧,机械结构的可靠性问题变得越发突出。
本文旨在探讨机械结构的可靠性分析方法和改进设计的关键因素,以及通过优化设计来提高机械结构的可靠性。
机械结构的可靠性分析1. 可靠性概念和评估方法可靠性是指在规定的时间和环境下,机械结构完成给定功能而不发生故障的能力。
可靠性评估通常通过以下两种方法进行:- 实验法:利用实际测试数据进行统计分析,计算故障概率和故障率等指标。
通过对实验数据的建模和分析,可以了解机械结构在不同条件下的可靠性表现。
- 数值模拟法:基于物理原理和数学模型,使用计算机仿真和分析软件进行性能预测和可靠性评估。
通过建立机械结构的有限元模型,可以快速、准确地评估其可靠性。
2. 可靠性指标常用的可靠性指标包括:- 故障概率:表示单位时间或单位使用寿命内机械结构发生故障的概率,通常以百分比或千分比表示。
- 故障率:表示单位时间内机械结构平均每小时或每千小时的故障次数,常用单位为"失效/小时"或"失效/千小时"。
- 平均失效时间:表示机械结构平均连续运行到发生故障的时间,常用单位为小时。
3. 可靠性分析方法可靠性分析方法主要包括故障模式和影响分析(FMEA)、故障树分析(FTA)、可靠性增长测试(RGT)等。
- FMEA是一种通过对系统的每个组成部分进行故障模式和后果分析的方法,以识别潜在故障模式及其影响。
通过FMEA分析可以发现并优化机械结构的弱点,提高其可靠性。
- FTA是一种通过构建逻辑树模型来评估系统中故障事件的可能性和影响的方法。
通过FTA分析可以定位机械结构中可能导致故障的关键部件,进而设计出更可靠的结构。
机械结构的改进设计1. 材料与制造工艺选择材料的选择对机械结构的可靠性具有重要影响。
机械设计制造中的可靠性与安全性分析

机械设计制造中的可靠性与安全性分析在机械设计制造的过程中,可靠性与安全性是至关重要的因素。
可靠性指的是机械系统在规定条件下能够长期、稳定地工作的能力,而安全性则是指机械系统在工作过程中不会对操作者或周围环境造成危害的程度。
本文将从理论和实践两个方面,分析机械设计制造中的可靠性与安全性。
首先,从理论角度来看,机械设计中的可靠性与安全性需要考虑以下几个方面。
首先是机械零部件的可靠性。
机械系统由各种零部件组成,每个零部件的可靠性都会影响整个系统的可靠性。
因此,对每个零部件的设计、材料选择以及制造工艺都需要进行深入的分析和评估,以提高其可靠性。
其次是机械系统的结构可靠性。
机械系统的结构设计需要考虑系统的工作原理、受力分析、振动与噪声等因素。
通过结构分析和仿真,可以评估机械系统在不同工况下的可靠性,发现潜在的问题并加以解决。
第三是机械系统的故障诊断与容错设计。
在机械系统运行过程中,故障不可避免。
因此,设计人员需要考虑故障的诊断和修复。
通过引入故障检测设备和容错设计,可以提高系统的可靠性和安全性。
此外,从实践角度来看,机械设计制造中的可靠性与安全性分析需要进行以下几个方面的工作。
首先是原材料的质量控制。
机械系统的可靠性与安全性直接受制于其零部件的质量。
因此,合理选择供应商、制定严格的原材料质量检验标准以及加强供应链管理,都是提高机械系统可靠性与安全性的关键。
其次是制造工艺的控制。
在机械制造过程中,合理的工艺控制是保证产品质量的重要因素。
通过优化工艺参数、引入先进的制造技术以及加强制造工艺的监测和控制,可以提高机械系统的可靠性与安全性。
第三是设备的维护与保养。
定期的设备维护与保养可以有效延长设备的寿命,保证机械系统的可靠性与安全性。
及时更换老化的零部件、进行润滑与清洁以及定期检查设备的性能等都是维护设备的重要措施。
最后是人员培训与操作规程。
机械系统的可靠性与安全性不仅仅依赖于设计与制造,操作者的能力和操作规程也是至关重要的。
某型机械装备的可靠性与维修性分析

某型机械装备的可靠性与维修性分析在现代工业生产中,机械装备是生产力的重要组成部分。
然而,机械装备的可靠性和维修性是影响生产效率和成本的关键因素。
本文将对某型机械装备的可靠性和维修性进行分析,并提出相应的解决方案。
一、可靠性分析可靠性是指机械装备在一定时间内能够正常工作的能力。
对于某型机械装备来说,可靠性分析应该从以下几个方面进行考虑:1. 设计可靠性:机械装备的设计是否符合工程要求,是否考虑到了各项工作条件和环境因素。
设计可靠性不仅仅包括技术可行性,还包括物料的选择、加工工艺等因素。
2. 零部件的可靠性:机械装备的可靠性与其零部件的可靠性密切相关。
因此,对机械装备的关键零部件进行可靠性分析至关重要。
例如,对某型机械装备的发动机进行故障模式与效果分析,确定常见故障点,并采取相应的措施进行预防。
3. 运行环境的可靠性:机械装备通常在复杂的工作环境中运行,如高温、低温、湿度、振动等。
因此,对机械装备在不同环境下的可靠性进行评估和分析,并对可能出现的故障进行预测。
通过对行业数据的统计和分析,我们可以得出某型机械装备的可靠性指标,并根据这些指标进行改进和优化。
例如,可以通过改进机械装备的设计和关键零部件的选择,提高机械装备的可靠性。
二、维修性分析维修性是指机械装备在发生故障后能够快速修复和恢复正常工作的能力。
对于某型机械装备来说,维修性分析应该从以下几个方面进行考虑:1. 维修过程的复杂度:机械装备维修过程中涉及到的步骤、工具、人力等因素都会影响维修的时间和成本。
因此,对机械装备的维修过程进行分析,并评估其复杂度。
可以通过减少维修步骤、优化维修工具和设备等方式降低维修的难度。
2. 维修资源的可获得性:机械装备维修所需的零部件、人力、技术等资源是否能够及时获得也是维修性的一项重要指标。
因此,建立起完善的备件管理系统和培训体系,确保维修所需的资源能够及时到位。
3. 维修数据的积累和分析:通过对维修记录和统计数据的积累和分析,可以找出机械装备常见的故障模式,并采取相应的措施进行预防。
机械零件的耐久性与可靠性分析

机械零件的耐久性与可靠性分析机械零件的耐久性与可靠性一直是工程领域中的重要研究课题。
通过对机械零件的耐久性和可靠性进行分析,可以有效提升机械设备的使用寿命,降低维修成本,保证设备的正常运行。
一、耐久性分析机械零件的耐久性主要受到材料的选择和加工工艺的影响。
首先,材料的选择需要考虑机械零件所处的工作环境和工作条件。
不同工作环境下对材料的要求不同,如高温环境下需要具备抗热性能的材料,潮湿环境下需要抗腐蚀性能的材料。
其次,加工工艺对于机械零件的耐久性也有着重要影响。
合理的加工工艺能够减少零件的应力集中和缺陷,提高零件的强度和硬度。
除了材料和加工工艺的影响外,机械零件的设计也非常关键。
设计中需要考虑零件的载荷及其分布情况,合理布置结构和增加强度。
此外,还需要进行疲劳寿命分析和有限元分析,以确保机械零件在长时间的使用过程中不会出现断裂和损坏。
二、可靠性分析机械设备的可靠性是指设备在规定的工作条件下,在一定的时间内按要求完成工作的能力。
机械设备的可靠性分析需要考虑多种因素。
首先是负载分析。
负载分析是指对机械设备所受的加载情况进行定性和定量的分析。
通过分析负载情况,可以确定机械零件的承载能力和耐久性。
合理的负载分析可以避免超负荷工作,延长机械设备的寿命。
其次是故障模式分析。
故障模式分析是指对机械设备运行过程中可能出现的故障进行系统性的分析和研究。
通过对故障模式的分析,可以确定潜在的故障点,并采取相应的措施来预防和处理故障,提高机械设备的可靠性。
另外,还需要进行可靠性设计。
可靠性设计是指在设计阶段就考虑并满足用户对机械设备性能稳定性和使用寿命的要求。
通过合理的设计,选择可靠性较高的零部件和工艺,优化结构布局和安全装置,可以提高机械设备的可靠性。
最后,进行可靠性测试和评估。
可靠性测试是指通过实验和检测,验证机械设备设计的可靠性。
评估结果可以为后期的优化和改进提供依据。
综上所述,机械零件的耐久性和可靠性分析是保证机械设备正常运行的重要手段。
机械零件强度与可靠性的分析与优化
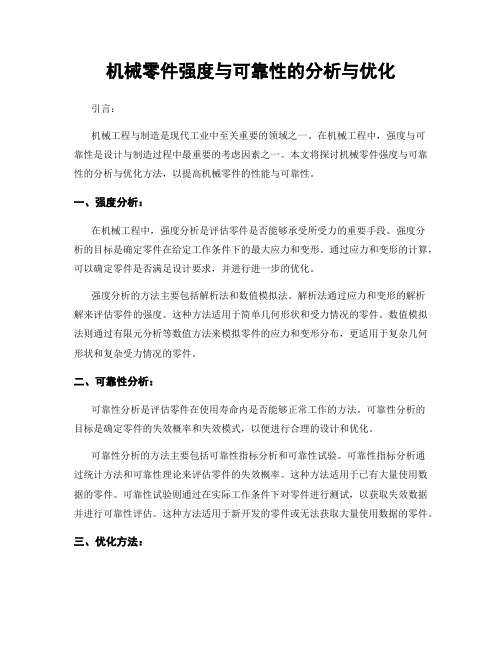
机械零件强度与可靠性的分析与优化引言:机械工程与制造是现代工业中至关重要的领域之一。
在机械工程中,强度与可靠性是设计与制造过程中最重要的考虑因素之一。
本文将探讨机械零件强度与可靠性的分析与优化方法,以提高机械零件的性能与可靠性。
一、强度分析:在机械工程中,强度分析是评估零件是否能够承受所受力的重要手段。
强度分析的目标是确定零件在给定工作条件下的最大应力和变形。
通过应力和变形的计算,可以确定零件是否满足设计要求,并进行进一步的优化。
强度分析的方法主要包括解析法和数值模拟法。
解析法通过应力和变形的解析解来评估零件的强度。
这种方法适用于简单几何形状和受力情况的零件。
数值模拟法则通过有限元分析等数值方法来模拟零件的应力和变形分布,更适用于复杂几何形状和复杂受力情况的零件。
二、可靠性分析:可靠性分析是评估零件在使用寿命内是否能够正常工作的方法。
可靠性分析的目标是确定零件的失效概率和失效模式,以便进行合理的设计和优化。
可靠性分析的方法主要包括可靠性指标分析和可靠性试验。
可靠性指标分析通过统计方法和可靠性理论来评估零件的失效概率。
这种方法适用于已有大量使用数据的零件。
可靠性试验则通过在实际工作条件下对零件进行测试,以获取失效数据并进行可靠性评估。
这种方法适用于新开发的零件或无法获取大量使用数据的零件。
三、优化方法:为了提高机械零件的强度和可靠性,优化方法是必不可少的。
优化方法的目标是在满足给定约束条件下,找到最优的设计参数组合。
常用的优化方法包括试验设计法、遗传算法和人工神经网络。
试验设计法通过设计和分析一系列试验来确定最佳设计参数组合。
遗传算法则通过模拟生物进化过程来搜索最优解。
人工神经网络则通过模拟人脑神经元网络来建立模型,并通过学习和训练来寻找最优解。
结论:机械零件的强度与可靠性是机械工程与制造中不可忽视的重要问题。
通过强度分析和可靠性分析,可以评估零件的性能和可靠性,并进行相应的优化。
优化方法的选择取决于具体的问题和需求。
机械设计中的零件可靠性分析

机械设计中的零件可靠性分析近年来,随着科技的不断进步和工业的快速发展,机械设计在各个领域中扮演着重要的角色。
然而,在实际的机械设计过程中,零件的可靠性问题成为了设计师们必须面对的挑战。
本篇文章将探讨机械设计中零件的可靠性分析,并给出一些解决这一问题的有效方法。
一、可靠性分析的重要性在机械设计中,零件的可靠性直接关系到整体设备的性能和寿命。
一旦某个零件出现故障或失效,不仅会导致设备的停机,还可能引发更为严重的后果。
因此,对零件的可靠性进行充分分析,提高其设计和制造质量,对于确保设备安全可靠运行至关重要。
二、零件可靠性分析的方法1. 统计分析法统计分析法是目前应用较为广泛的一种零件可靠性分析方法。
通过对历史数据的统计和分析,可以得到零件的失效率、失效模式等一系列指标,帮助设计师了解零件的寿命分布和故障机理。
基于统计分析的结果,可以采取针对性的措施,提高零件的可靠性。
2. 失效模式与影响分析法(FMEA)FMEA方法是一种通过系统分析和评估零件的潜在失效模式和影响的方法。
通过识别和排除潜在的失效模式,可以降低零件的失效概率。
此外,FMEA方法还可以帮助设计师确定较为脆弱的零件,从而提前采取相应的措施进行改进。
3. 可靠性成本分析法可靠性成本分析法主要是通过对零件故障和失效给企业造成的经济损失进行评估,从而确定最经济的可靠性设计方案。
该方法考虑到了零件失效引起的维修和停机成本等因素,帮助设计师在实际应用中综合考虑不同的成本因素,以最小的成本达到最大的可靠性。
三、零件可靠性提升的措施1. 材料选择与工艺优化材料的选择和工艺的优化对零件的可靠性至关重要。
通过选择合适的材料,可以提高零件的抗疲劳、抗蚀刻等性能,从而延长零件的使用寿命。
同时,通过对工艺过程的优化,可以减少零件制造过程中的损伤和缺陷,提高零件的质量稳定性。
2. 可靠性试验与验证可靠性试验与验证是对零件进行可靠性检验的重要手段。
通过搭建试验平台和采用适当的试验方法,可以对零件的寿命、稳定性等进行定量分析和评估。
- 1、下载文档前请自行甄别文档内容的完整性,平台不提供额外的编辑、内容补充、找答案等附加服务。
- 2、"仅部分预览"的文档,不可在线预览部分如存在完整性等问题,可反馈申请退款(可完整预览的文档不适用该条件!)。
- 3、如文档侵犯您的权益,请联系客服反馈,我们会尽快为您处理(人工客服工作时间:9:00-18:30)。
(力神动力电池系统有限公司,天津 300384)摘 要:机械零件结构设计的可靠性设计就是可靠性分析,是对机械零部件进行概率设计,其对传统的机械设计进行了改进。
机械零件结构和常规电器元件有所不同,因其自身独有的特性,无法借助实验取得可参考数据,所以只有对机械零件结构进行可靠性分析,才能保证机械零件结构设计的实用性和规范性。
文章对机械零件结构设计特点、设计分析进行了着重说明,为以后机械零件的可靠性设计提供参考。
关键词:机械零件;结构设计;可靠性中图分类号:TH122 文献标志码:A 文章编号:2096-2789(2019)09-0207-02作者简介:张如星(1989—),男,硕士,研究方向:结构设计和焊接技术。
机械零部件可靠性设计是现代机械零部件生产的主要依据,飞机、汽车和船舶等重工业产品和机械类产品内部的重要零部件都是建立在零件可靠性上进行生产的。
另外,我国的核电仪控自动化系统中也离不开零部件的结构设计。
因此,我国相关部门对机械零件结构可靠性设计非常重视。
机械零件结构可靠性设计能力的提升,加速了我国工业水平的发展速度。
1 机械可靠性及其工作的特点1.1 机械可靠性的特点当机械处于正常运行时,必须确保其稳定可靠,如果在使用的过程中出现问题,会造成不必要的损失,所以机械的可靠性尤为重要。
在机械产品运行的过程中,不可避免地会发生摩擦、损耗等情况,导致机械零件破损,以至于不能满足正常使用要求,进而影响工作效率以及质量。
机械是由众多零件组合而成的,在众多的零件当中,非标准零部件所占比例尤为显著,并且这些零部件的失效统计值非常分散,不易统计。
正是因为这个原因,在平时的工作中很难对机械产品的失效数据准确收集、统计。
所以在进行机械的可靠性分析时,并不能对实际情况进行分析,只能针对机械的失效模式进行分析,从而近似得到想要的结果。
1.2 机械可靠性工作的特点要想对机械的可靠性进行分析,要对机械中各部分零件进行可靠性分析,通过失效模式分析以及工作经验,得到相对比较准确的结论,并提供给进行产品研发的有关部门。
进行机械产品的可靠性分析时,为了避免在分析的过程中出现失效现象,首先要做失效模式分析;其次要对机械产品的重要零件和关键零件进行可靠性的设计工作;最后要制定该产品的产品操作要点,并对产品的维修进行说明。
2 机械可靠性设计方法2.1 优化设计分析优化设计分析是在确保零部件的可靠性保持不变的情况下,根据其现在的工作方法、工作环境等多方需求对机械的零部件结构进行调整和优化,以便零部件能够更加高质量、高效率地完成工作。
在对机械可靠性进行优化的过程中,应对机械零件的强度、刚度等性能进行了解,然后运用数学知识构建数学模型,并且进行计算。
2.2 灵敏度设计分析在进行机械可靠性设计时,其中比较重要的是灵敏度设计。
该设计是在可靠性设计基础之上,依据灵敏度参数,计算出对机械产品失效影响的不同数值,找出对机械零件可靠性设计中敏感性影响比较大的变量,根据这些变量造成的工作效果进行新一轮的评估,根据评估结果对相应灵敏度的参数进行调整,以防机械产品在使用过程中因为一些外在因素变差而失去灵敏性。
在灵敏度进行设计的过程中,可以根据灵敏度的计算公式进行计算,以此确定设计参数的灵敏度,根据这些数值进行产品设计,可以提高机械产品的灵敏度,从而减少灵敏度对产品可靠性的影响,使机械零件结构的可靠性得到充分保证。
2.3 稳健性设计分析对机械零部件进行可靠性设计,在最大程度上减少机械外部环境或意外情况的发生而使机械零部件的可靠性发生变化。
在机械设计的过程中,一定做好优化工作,如此机械在使用时即使机械零件发生了意外情况,也影响不到机械的正常运转。
就机械本身而言,在进行设计和投入使用后,一些外在的原因发生会导致机械无法正常工作。
如果对机械进行稳健性设计,就可以抵消这些外在原因对其产生的影响,使机械始终处在相对稳定工作状态,不会因外界因素影响工作,确保机械性能得到最大发挥。
2.4 实验分析当对机械零部件进行可靠性设计后,要对它的可靠性进行试验,保证其在以后使用过程中不会出现各种各样的问题。
在进行试验的过程中,要采集各种零部件在不同工作状态下的运行数据,通过对这些数据的分析,找出产品设计、原材料和加工工艺中的不足之处,进行进一步的调整,使产品进一步完善,从而提高产品成功率,还可以减少维修养护的成本。
为了使机械产品的使用寿命更长,必须提高机械每个零件的产品质量。
如果试验过程中出现故障,要对出现的故障进行认真的分析和研究,针对故障发生的根源,制定有效的处理方案,同时尽可能地在实际应用过程中规避同样的问题。
如果可靠性设计出现更改,就意味着实验工作又要重新开始,不仅会浪费一定的资源,还会浪费较多时间。
因此合理进行模拟实验能够提高可靠性设计的效率,使资源得到合理的利用。
(下转第209页)少拆迁,不占或少占良田,施工、运行管理方便。
新建水厂位置均选择在地势平坦开阔、相对高程较高、周围没有污染源、紧邻公路、交通便利、靠近镇政府以及便于管理的地带。
3 工程设计周口市农村饮水安全工程均采用集中式供水。
(1)管井设计。
根据拟建水源井附近有现有水源井水文地质资料,水源井设计参考附近的现有水源井成井资料。
规划井与参考井处地层岩性、含水层厚度、地下水类型、埋深、水压、出水量、水质相差不大,可参考附近的现有水源井成井资料进行设计。
(2)水源井设计成果。
周口市水源井设计深度大部分为450m,成孔直径均为550mm,单井出水量不小于50m3/h。
(3)水泵选型。
水泵设计流量根据项目区最高日工作时用水量确定,考虑到水厂的中、远期供水目标,使水源井充分发挥效益,水泵设计流量按井的出水量确定。
水泵设计扬程应满足调节水池的最高设计水位要求。
(4)输水工程设计。
输配水管网采用树枝状管网,输水管网设计均在实测资料的基础上进行,按照相关技术要求选择输水线路、布置管道。
(5)配水工程设计。
配水管网采用树枝状管网,管材采用PE管。
(6)水厂工程设计。
水厂设计规模根7)管管网水头损失。
由于在管网水力计算时仅计算到行政村(不是最不利点),以行政村为控制点,所以控制点自由水头取15~20m。
控制点选取时根据水厂供水村平面位置图选定几个距离水厂远、用水量大的供水村为可能的控制点,分别计算出水厂供水压力,选取其中最大的出厂压力所对应的控制点为最不利点,计算出各管段管径和管网水头损失。
4 结束语周口市农村饮水工程不同于城市供水工程,因为其供水区域分散,供水线路长且地形条件复杂,根据供水区的实际情况,创新性地按照“集中连片,适度规模,因地制宜”的原则,确定工程的工程型式为新建水厂供水和管网延伸供水。
水厂根据实际状况选择合适的工艺流程,水厂运行实现全自动化。
管网敷设结合实际地形选择不同的敷设方式和材料。
该工程实施后,均实现供水到户。
经过近些年的实际运行,证明工程取得的效果非常好。
参考文献:[1] SL 310-2004,村镇供水工程技术规范[S].[2] SL 256-2000,机井技术规范[S].[3] GB 50296-99,供水管井技术规范[S].(上接第207页)3 机械零部件可靠性分析方法在对机械零部件的可靠性进行设计时,通常采用概率法。
概率法虽然比较传统,但计算的结果十分精准。
概率方法分三种,即响应面法、蒙卡洛法和一次二阶矩法。
3.1 响应面法响应面法是利用近似函数与对数函数进行相互交替的方法,首先需要确定一个未知零部件,然后通过曲面方式将其表现出来,得到想要的结果。
如果这个结果能够在功能函数中较好地计算,基本上就可以确定通过此方法分析出来的结果是没有问题的。
在运用响应面法进行可靠性设计时,为了保证计算结果的准确性,可以减少函数的待定系数,以便更快地进行计算。
另外,为了计算简便,可以选用一个比较合适的函数公式进行计算。
3.2 蒙卡洛法蒙卡洛法利用计算机进行模拟实验,通过实验结果计算出可靠度的数值。
其计算结果的准确度会随着实验次数的增加而不断提升,此方法较为精准和便捷。
3.3 一次二阶矩法一次二阶矩法相对于前面两种方法简单并且实用。
一次二阶矩法主要用到两个数据,一个是一节变量矩,另一个是二阶矩,通过这两个数据构建一次函数,得到相对准确的可靠性分析结果。
除此之外,在使用一次二阶矩法的过程中,还需要另外两种方法的辅助。
只有通过多种方法相互配合,才能够使分析结果更加精准,得到精准的正态分布形式,以便根据函数的类型或者是线性函数进行相关的计算工作。
4 结束语可靠性对机械产品性能起着重大作用,在进行机械设计时,充分考虑其零件的可靠性有利于机械结构设计更加合理。
目前我国可靠性设计还处于发展阶段,在今后随着可靠性设计理论的逐渐成熟,其势必会应用到不同的领域中,为我国的经济发展发挥重要作用。
参考文献:[1]彭民泰.浅谈机械零部件的动态可靠性灵敏度[J].中国高新区,2017(23):132.[2]王新刚.机械零部件时变可靠性稳健优化设计若干问题的研究[D].沈阳:东北大学,2009.[3]张大基.对机械零件可靠性设计理论与方法分析[J].数码世界,2018(6):258-259.[4]莫才颂,千学明.机械零件强度的模糊可靠性设计分析[J].机械设计与制造,2007(4):33-34.[5]冯昕宇,祝锡晶.机械零件结构设计可靠性分析[J].设备管理与维修,2019(4):43-44.。