机械可靠性研究方法
机械设计中的安全性与可靠性评估方法探讨
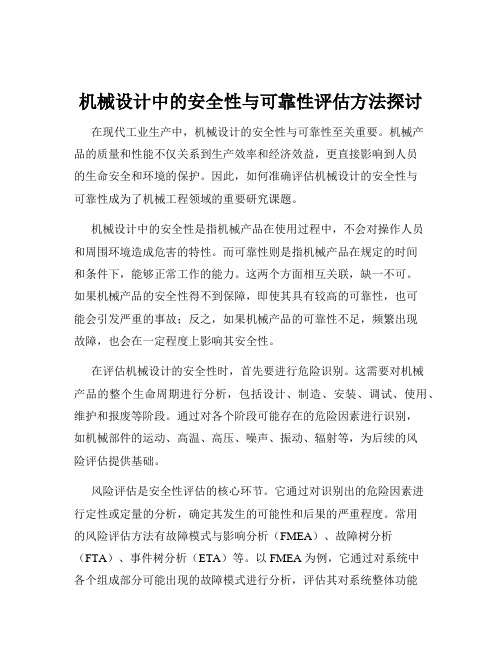
机械设计中的安全性与可靠性评估方法探讨在现代工业生产中,机械设计的安全性与可靠性至关重要。
机械产品的质量和性能不仅关系到生产效率和经济效益,更直接影响到人员的生命安全和环境的保护。
因此,如何准确评估机械设计的安全性与可靠性成为了机械工程领域的重要研究课题。
机械设计中的安全性是指机械产品在使用过程中,不会对操作人员和周围环境造成危害的特性。
而可靠性则是指机械产品在规定的时间和条件下,能够正常工作的能力。
这两个方面相互关联,缺一不可。
如果机械产品的安全性得不到保障,即使其具有较高的可靠性,也可能会引发严重的事故;反之,如果机械产品的可靠性不足,频繁出现故障,也会在一定程度上影响其安全性。
在评估机械设计的安全性时,首先要进行危险识别。
这需要对机械产品的整个生命周期进行分析,包括设计、制造、安装、调试、使用、维护和报废等阶段。
通过对各个阶段可能存在的危险因素进行识别,如机械部件的运动、高温、高压、噪声、振动、辐射等,为后续的风险评估提供基础。
风险评估是安全性评估的核心环节。
它通过对识别出的危险因素进行定性或定量的分析,确定其发生的可能性和后果的严重程度。
常用的风险评估方法有故障模式与影响分析(FMEA)、故障树分析(FTA)、事件树分析(ETA)等。
以 FMEA 为例,它通过对系统中各个组成部分可能出现的故障模式进行分析,评估其对系统整体功能的影响,并根据影响的严重程度、发生的概率和可检测性等因素,确定故障模式的风险优先级。
在机械设计中,为了提高安全性,还需要采取相应的安全防护措施。
这些措施可以分为本质安全设计和附加安全防护装置两类。
本质安全设计是通过改变机械产品的结构、材料、工艺等,从根本上消除或减少危险因素。
例如,采用无锐角的设计、选择强度高的材料、优化工艺流程等。
附加安全防护装置则是在机械产品上安装防护栏、防护罩、联锁装置、紧急制动装置等,以防止操作人员接触到危险因素。
可靠性评估是对机械产品在规定时间内和规定条件下完成规定功能的能力进行评估。
机械设计中的机械强度与可靠性研究

机械设计中的机械强度与可靠性研究在机械设计中,机械强度与可靠性是两个非常关键的研究方向。
机械强度主要关注材料的抗力和机构的承载能力,而可靠性则关注机械系统在工作条件下的稳定性和故障率。
一、机械强度研究机械强度是指机械系统在外部加载或内部受力情况下的稳定性和抗力能力。
机械强度的研究主要包括以下几个方面:1.1 材料力学性能研究机械设计中常使用的材料包括金属、塑料、复合材料等。
对于不同的材料,需要进行力学性能研究,包括拉伸性能、压缩性能、抗弯性能等。
通过对材料性能的研究,可以确定材料的极限强度和变形特性。
1.2 结构承载能力分析在机械设计中,结构的承载能力非常重要。
通过结构力学分析和有限元模拟等方法,可以计算出结构在不同载荷下的应力和变形情况。
这样可以评估结构的稳定性,并确定设计中需要加强或者调整的地方。
1.3 疲劳寿命评估机械系统常常在长时间工作条件下承受循环载荷。
疲劳寿命评估是机械设计中不可或缺的一部分。
通过进行疲劳试验和疲劳寿命预测,可以确定机械系统在不同工况下的使用寿命,并进行必要的优化和改进。
二、可靠性研究可靠性是指机械系统在预定条件下工作的稳定性和故障率。
可靠性的研究主要包括以下几个方面:2.1 故障分析与预测在机械设计中,故障分析和预测是非常重要的一项工作。
通过对机械系统的各个部件进行故障分析,可以确定故障的原因和发生概率。
同时,可以通过故障预测模型,对系统的可靠性进行评估和优化。
2.2 可靠性设计在机械设计中,可靠性设计是一种重要的设计思路。
通过在设计中考虑故障预防、冗余设计和备件设计等措施,可以提高机械系统的可靠性。
同时,可靠性设计也需要结合经济性和实际应用情况进行综合考虑。
2.3 可靠性试验与验证对于机械系统的可靠性研究,可靠性试验和验证是必不可少的。
通过设计合理的试验方案和测试方法,可以验证设计的可靠性,并进行必要的优化和改进。
三、机械强度与可靠性的关系机械强度和可靠性是紧密相关的。
机械装备的可靠性分析与优化设计
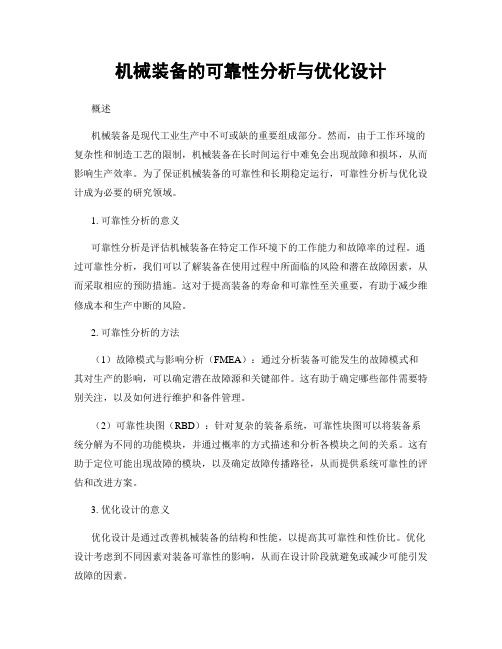
机械装备的可靠性分析与优化设计概述机械装备是现代工业生产中不可或缺的重要组成部分。
然而,由于工作环境的复杂性和制造工艺的限制,机械装备在长时间运行中难免会出现故障和损坏,从而影响生产效率。
为了保证机械装备的可靠性和长期稳定运行,可靠性分析与优化设计成为必要的研究领域。
1. 可靠性分析的意义可靠性分析是评估机械装备在特定工作环境下的工作能力和故障率的过程。
通过可靠性分析,我们可以了解装备在使用过程中所面临的风险和潜在故障因素,从而采取相应的预防措施。
这对于提高装备的寿命和可靠性至关重要,有助于减少维修成本和生产中断的风险。
2. 可靠性分析的方法(1)故障模式与影响分析(FMEA):通过分析装备可能发生的故障模式和其对生产的影响,可以确定潜在故障源和关键部件。
这有助于确定哪些部件需要特别关注,以及如何进行维护和备件管理。
(2)可靠性块图(RBD):针对复杂的装备系统,可靠性块图可以将装备系统分解为不同的功能模块,并通过概率的方式描述和分析各模块之间的关系。
这有助于定位可能出现故障的模块,以及确定故障传播路径,从而提供系统可靠性的评估和改进方案。
3. 优化设计的意义优化设计是通过改善机械装备的结构和性能,以提高其可靠性和性价比。
优化设计考虑到不同因素对装备可靠性的影响,从而在设计阶段就避免或减少可能引发故障的因素。
4. 优化设计的方法(1)强度和刚度分析:通过对装备结构的强度和刚度进行分析,可以确定其在工作环境下的最大负荷和受力情况。
这有助于避免结构在工作过程中的变形和断裂,提高装备的寿命和可靠性。
(2)材料选择和加工工艺优化:选择适合的材料和优化加工工艺可以提高装备的性能和寿命。
例如,使用抗腐蚀性能好的不锈钢材料可以减少装备部件的腐蚀风险,从而提高装备的可靠性。
(3)附件和配件选型:选择合适的附件和配件可以改善装备的整体性能。
例如,选择高质量的轴承和传动装置可以减少运行时的摩擦和能量损耗,提高装备的效率和可靠性。
机械结构的疲劳寿命与可靠性分析

机械结构的疲劳寿命与可靠性分析机械结构的疲劳寿命和可靠性分析是机械工程领域中一个重要的课题。
疲劳寿命是指机械结构在长期连续循环载荷下能够正常工作的时间,而可靠性是指机械结构在设计寿命内不失效的概率。
本文将从疲劳寿命与可靠性的概念、影响因素、分析方法以及提高方法等几个方面进行论述。
首先,我们来了解一下疲劳寿命与可靠性的基本概念。
疲劳寿命与可靠性是机械结构设计与评估的重要指标,它们直接影响到机械设备的使用寿命和可靠性。
疲劳寿命是指机械结构在多次循环载荷下,出现疲劳破坏的时间,它是一个统计平均数,并且服从一定的概率分布。
而可靠性是指机械结构在规定的设计寿命内不失效的概率。
疲劳寿命和可靠性是衡量机械结构寿命和可靠性的重要指标。
其次,我们来探讨一下影响机械结构疲劳寿命与可靠性的因素。
首先是载荷条件的影响,载荷是引起结构疲劳破坏的主要原因之一。
不同的载荷条件下,机械结构的疲劳寿命和可靠性会有所不同。
其次是结构材料的影响,材料的强度、韧性和疲劳性能等都会对结构的疲劳寿命和可靠性产生影响。
此外,还有结构形状、焊接质量、温度等因素都会对机械结构的疲劳寿命和可靠性产生影响。
接下来,我们将介绍一些机械结构疲劳寿命与可靠性的分析方法。
首先是数值模拟方法,通过建立适当的数学模型,采用有限元分析等方法,对机械结构的疲劳寿命和可靠性进行预测和评估。
另外一种方法是试验方法,通过对机械结构进行疲劳试验,获取其疲劳寿命曲线和可靠性指标,来评估机械结构的疲劳寿命和可靠性。
而最常用的方法是基于统计学原理的可靠性设计方法,通过收集疲劳试验数据,利用统计分析方法建立概率模型,计算结构的可靠性指标。
最后,我们来探讨一下提高机械结构疲劳寿命与可靠性的方法。
首先是合理的结构设计,通过优化结构形状和尺寸,减少应力集中和历史因素,提高结构的疲劳寿命和可靠性。
其次是选用合适的材料,选择强度高、韧性好、抗疲劳性能优异的材料,可以提高结构的疲劳寿命和可靠性。
机械结构的优化设计与可靠性分析
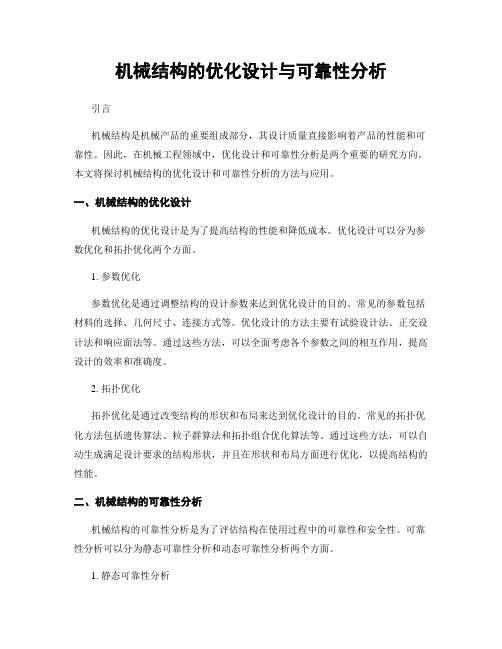
机械结构的优化设计与可靠性分析引言机械结构是机械产品的重要组成部分,其设计质量直接影响着产品的性能和可靠性。
因此,在机械工程领域中,优化设计和可靠性分析是两个重要的研究方向。
本文将探讨机械结构的优化设计和可靠性分析的方法与应用。
一、机械结构的优化设计机械结构的优化设计是为了提高结构的性能和降低成本。
优化设计可以分为参数优化和拓扑优化两个方面。
1. 参数优化参数优化是通过调整结构的设计参数来达到优化设计的目的。
常见的参数包括材料的选择、几何尺寸、连接方式等。
优化设计的方法主要有试验设计法、正交设计法和响应面法等。
通过这些方法,可以全面考虑各个参数之间的相互作用,提高设计的效率和准确度。
2. 拓扑优化拓扑优化是通过改变结构的形状和布局来达到优化设计的目的。
常见的拓扑优化方法包括遗传算法、粒子群算法和拓扑组合优化算法等。
通过这些方法,可以自动生成满足设计要求的结构形状,并且在形状和布局方面进行优化,以提高结构的性能。
二、机械结构的可靠性分析机械结构的可靠性分析是为了评估结构在使用过程中的可靠性和安全性。
可靠性分析可以分为静态可靠性分析和动态可靠性分析两个方面。
1. 静态可靠性分析静态可靠性分析是在给定荷载条件下,评估结构在一定寿命内不发生失效的概率。
静态可靠性分析可以通过概率统计方法、有限元法和可靠性索引方法等进行。
通过这些方法,可以评估结构在设计寿命内的可靠性,并且提供对结构进行改进的建议。
2. 动态可靠性分析动态可靠性分析是在结构受到外界荷载变化时,评估结构在一定时间内不发生失效的概率。
动态可靠性分析可以通过随机振动分析和动力有限元分析等进行。
通过这些方法,可以考虑结构在振动和冲击等动态荷载下的可靠性,并且提供对结构进行抗震和抗冲击改进的建议。
结论机械结构的优化设计和可靠性分析是机械工程领域中的重要研究方向。
通过优化设计,可以提高结构的性能和降低成本;通过可靠性分析,可以评估结构的可靠性和安全性。
机械零部件的寿命分析与可靠性评估研究

机械零部件的寿命分析与可靠性评估研究一、引言机械工程中的各种零部件在使用过程中都会经历寿命的限制,这些寿命限制与零部件自身的可靠性密切相关。
因此,对机械零部件的寿命进行分析和可靠性评估能够提高机械系统的性能和可靠性。
二、机械零部件寿命分析方法1. 物理试验方法物理试验方法是一种直接评估零部件寿命的方法。
通过对零部件进行疲劳寿命试验、负载试验等,可以模拟零部件在实际使用过程中所承受的环境和负载条件,从而得出寿命预测结果。
2. 数值仿真方法数值仿真方法利用计算机模拟零部件的受力和变形情况,通过数学建模和有限元分析等技术手段,得出零部件的寿命预测结果。
这种方法具有时间和成本的优势,能够提前评估零部件的可靠性。
三、机械零部件的可靠性评估方法1. 故障率分析方法故障率是评估可靠性的重要指标之一。
通过统计零部件在一定时间内发生故障的频率,可以得出零部件的故障率。
故障率分析方法可以帮助工程师预测零部件的失效概率,进而制定相应的维修和更换策略。
2. 可靠性指标分析方法通过分析零部件的可靠性指标,如平均无故障时间、失效率等,可以评估零部件在特定时间段内正常运行的概率。
可靠性指标分析方法能够帮助工程师了解零部件的可靠性水平,并通过采取相应的措施提高零部件的可靠性。
四、案例分析:汽车发动机飞轮的寿命分析与可靠性评估以汽车发动机飞轮为例,进行寿命分析与可靠性评估研究。
1. 寿命分析通过物理试验方法,模拟实际使用条件下发动机飞轮的受力情况。
根据试验数据,分析飞轮的疲劳寿命和失效模式,预测发动机飞轮的使用寿命。
2. 可靠性评估基于飞轮的失效模式和历史故障数据,采用故障率分析方法得出发动机飞轮的故障率。
同时,通过计算飞轮的可靠性指标,如平均无故障时间和失效率,评估发动机飞轮的可靠性水平。
五、结论与展望通过机械零部件的寿命分析与可靠性评估研究,可以提前发现零部件的潜在问题,预测零部件的使用寿命,并制定相应的维修和更换策略,从而提高机械系统的性能和可靠性。
机械可靠性分析的响应面法研究

机械可靠性分析的响应面法研究一、本文概述《机械可靠性分析的响应面法研究》这篇文章旨在探讨和阐述响应面法在机械可靠性分析中的应用与研究。
机械可靠性分析是机械设计与制造领域的重要研究内容,它涉及到机械系统在各种环境和使用条件下的性能稳定性和可靠性评估。
响应面法作为一种有效的数学优化和统计分析工具,被广泛应用于各种工程领域,特别是在处理复杂系统的优化和不确定性分析方面表现出显著的优势。
本文将首先介绍机械可靠性分析的基本概念和重要性,阐述为何需要对机械系统进行可靠性分析。
接着,将详细介绍响应面法的基本原理和实施步骤,包括如何构建响应面模型、如何选择和设计试验方案、如何进行模型验证和评估等。
然后,将重点讨论响应面法在机械可靠性分析中的具体应用案例,包括如何运用响应面法来解决机械可靠性分析中的实际问题,以及在实际应用中需要注意的问题和挑战。
本文将总结响应面法在机械可靠性分析中的优势和不足,展望未来的研究方向和应用前景。
通过本文的研究,旨在为机械设计与制造领域的工程师和研究人员提供一种新的视角和方法,以更好地理解和解决机械可靠性分析中的复杂问题。
二、机械可靠性分析基础机械可靠性分析是工程领域中的一个重要研究方向,旨在评估机械设备或系统在特定工作条件下完成预定功能的能力。
可靠性分析的核心在于预测和评估设备在受到各种内外部因素影响时,能否保持其性能和功能的稳定。
这对于保障设备的长期运行、减少故障、预防事故、提高产品质量和延长使用寿命具有重要意义。
在进行机械可靠性分析时,需要综合考虑多种因素,包括材料的力学性能、结构的几何特性、工作环境的恶劣程度、制造工艺的精度等。
设备的运行过程中还会受到各种随机因素的影响,如载荷的波动、温度的变化、磨损和腐蚀等。
这些因素可能导致设备的性能退化,甚至引发故障。
为了有效评估这些因素对设备可靠性的影响,需要采用适当的分析方法。
响应面法作为一种有效的数值分析方法,被广泛应用于机械可靠性分析中。
可靠性分析在机械结构设计中的应用研究

可靠性分析在机械结构设计中的应用研究引言:在现代工程设计中,机械结构的可靠性是一个至关重要的指标。
可靠性分析作为一种评估和优化机械结构设计的方法,已经被广泛应用于许多领域。
本文将探讨可靠性分析在机械结构设计中的应用研究,并重点介绍一些常用的可靠性分析方法和工具。
一、可靠性分析方法可靠性分析方法是评估机械系统中部件和系统的可靠性的数学和统计学方法。
其中,最常用的方法包括故障模式与效果分析(FMEA)、故障树分析(FTA)和可靠性增益图(RBD)等。
故障模式与效果分析(FMEA)是一种通过分析系统中各个部件的故障模式和故障对系统的影响程度来评估系统可靠性的方法。
通过FMEA,工程师们可以识别和评估系统中的潜在故障,并采取相应的措施来提高系统的可靠性。
故障树分析(FTA)是一种通过构建树状图来分析和评估系统故障概率的方法。
在FTA中,各个事件(包括故障事件和故障的原因)通过逻辑门(例如与门、或门和非门)相连接,形成树状结构。
通过分析系统中各个事件的故障概率,可以计算系统整体的故障概率,并提出相应的改进方案。
可靠性增益图(RBD)是一种通过图形的方式来表示系统结构和可靠性指标的方法。
在RBD中,每个系统组件由一个方框表示,方框之间通过线段连接。
通过分析RBD中各个组件的可靠性指标,可以评估整个系统的可靠性,并对系统进行优化设计。
二、可靠性分析工具为了支持可靠性分析的实施,工程师们使用了许多可靠性分析工具。
其中,最常用的工具包括故障模式与效果分析软件(如FMEA软件)、故障树分析软件(如FTA软件)和可靠性增益图软件(如RBD软件)等。
故障模式与效果分析软件是一种用于支持FMEA分析的工具。
通过这种软件,工程师们可以方便地识别、评估和管理系统中的潜在故障。
此外,这种软件还可以生成报表和图表,以便更好地分析和优化系统的可靠性。
故障树分析软件是一种用于支持FTA分析的工具。
通过这种软件,工程师们可以方便地构建和分析故障树,从而评估系统的故障概率。
机械系统的可靠性建模与分析方法研究

机械系统的可靠性建模与分析方法研究一、引言在现代工业生产中,机械系统的可靠性是保障生产稳定性和产品质量的重要因素。
可靠性建模与分析方法的研究对于提高机械系统的可靠性、降低故障率具有重要意义。
本文将探讨机械系统可靠性建模与分析方法的研究,为提高机械系统的可靠性提供参考。
二、可靠性建模方法机械系统的可靠性建模是通过将机械系统的组成部分和故障模式抽象为数学模型,来描述机械系统的可靠性特性。
常用的可靠性建模方法有故障树分析法(FTA)、事件序列法(ETA)和Markov模型等。
1. 故障树分析法(FTA)故障树分析法是一种图形化的可靠性分析方法,它通过构建故障树来分析机械系统的可靠性。
故障树的基本组成有事件和门,事件表示系统的故障,门表示事件之间的逻辑关系。
通过对故障树的分析,可以确定机械系统故障的发生概率和影响因素。
2. 事件序列法(ETA)事件序列法是一种基于数学模型的可靠性分析方法,它通过建立系统故障发生的时间序列模型来分析机械系统的可靠性。
事件序列法考虑到了系统的故障发展过程,可以对系统在不同时间段内的可靠性进行评估,并找到故障发生的次序。
3. Markov模型Markov模型是一种基于状态转移的可靠性分析方法,它把机械系统的状态抽象为有限个状态,通过状态转移概率来描述系统状态的变化。
Markov模型可以分析系统在不同状态下的可靠性指标,并计算系统在特定时间段内的失效概率。
三、可靠性分析方法机械系统的可靠性分析是通过收集和分析系统故障数据,来评估系统的可靠性指标和寿命分布。
常用的可靠性分析方法有可靠性增长模型、可靠性剖面分析和失效模式与影响分析等。
1. 可靠性增长模型可靠性增长模型是一种通过逐步增长可靠性数据来评估系统的可靠性改进方法。
它通过记录系统的故障情况,并进行故障分析、故障定位和故障修复,不断提高系统的可靠性。
2. 可靠性剖面分析可靠性剖面分析是一种通过分析系统的故障数据和运行数据,来评估系统的可靠性分布和寿命分布的方法。
机械产品结构可靠性设计的十种方法
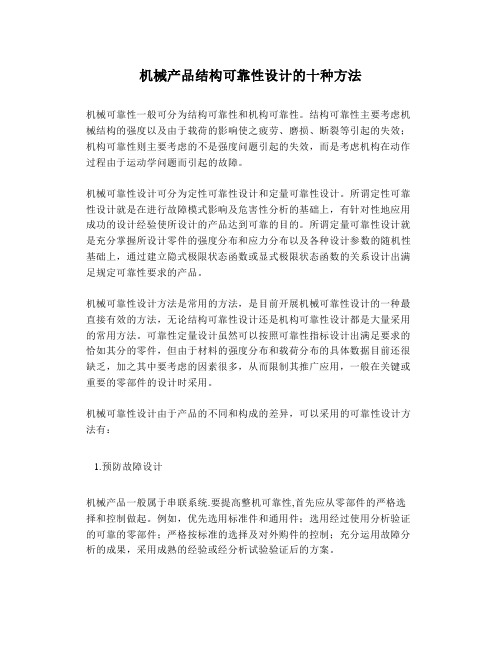
机械产品结构可靠性设计的十种方法机械可靠性一般可分为结构可靠性和机构可靠性。
结构可靠性主要考虑机械结构的强度以及由于载荷的影响使之疲劳、磨损、断裂等引起的失效;机构可靠性则主要考虑的不是强度问题引起的失效,而是考虑机构在动作过程由于运动学问题而引起的故障。
机械可靠性设计可分为定性可靠性设计和定量可靠性设计。
所谓定性可靠性设计就是在进行故障模式影响及危害性分析的基础上,有针对性地应用成功的设计经验使所设计的产品达到可靠的目的。
所谓定量可靠性设计就是充分掌握所设计零件的强度分布和应力分布以及各种设计参数的随机性基础上,通过建立隐式极限状态函数或显式极限状态函数的关系设计出满足规定可靠性要求的产品。
机械可靠性设计方法是常用的方法,是目前开展机械可靠性设计的一种最直接有效的方法,无论结构可靠性设计还是机构可靠性设计都是大量采用的常用方法。
可靠性定量设计虽然可以按照可靠性指标设计出满足要求的恰如其分的零件,但由于材料的强度分布和载荷分布的具体数据目前还很缺乏,加之其中要考虑的因素很多,从而限制其推广应用,一般在关键或重要的零部件的设计时采用。
机械可靠性设计由于产品的不同和构成的差异,可以采用的可靠性设计方法有:1.预防故障设计机械产品一般属于串联系统.要提高整机可靠性,首先应从零部件的严格选择和控制做起。
例如,优先选用标准件和通用件;选用经过使用分析验证的可靠的零部件;严格按标准的选择及对外购件的控制;充分运用故障分析的成果,采用成熟的经验或经分析试验验证后的方案。
2.简化设计在满足预定功能的情况下,机械设计应力求简单、零部件的数量应尽可能减少,越简单越可靠是可靠性设计的一个基本原则,是减少故障提高可靠性的最有效方法。
但不能因为减少零件而使其它零件执行超常功能或在高应力的条件下工作。
否则,简化设计将达不到提高可靠性的目的。
3.降额设计和安全裕度设计降额设计是使零部件的使用应力低于其额定应力的一种设计方法。
机械产品可靠性试验方法

机械产品可靠性试验方法随着科技的进步和社会的发展,机械产品在我们的生活中扮演着越来越重要的角色。
为了确保机械产品的可靠性和安全性,各行业制定了一系列的规范、规程和标准,用于指导机械产品的可靠性试验方法。
本文将就机械产品可靠性试验方法进行论述。
一、可靠性试验方法的概述可靠性试验是为了评估机械产品在一定时间和工作条件下的可靠性指标,例如寿命、故障率、失效模式等。
可靠性试验方法是为了验证机械产品在实际使用环境中是否能够满足设计要求和用户需求。
二、可靠性试验的分类可靠性试验可以根据不同的目的和试验环境进行分类。
常见的可靠性试验包括环境适应性试验、寿命试验、可靠性增长试验等。
1. 环境适应性试验环境适应性试验是为了测试机械产品在不同的环境条件下的可靠性。
根据具体的使用场景和环境要求,可以进行湿热试验、低温试验、高温试验等。
这些环境适应性试验可以帮助评估机械产品在多样化的环境下的可靠性性能。
2. 寿命试验寿命试验是为了评估机械产品在规定的使用寿命内是否能够达到要求的可靠性指标。
根据不同的产品特性和使用要求,可以进行振动试验、冲击试验、耐久试验等。
寿命试验能够帮助厂家了解机械产品的寿命特性,优化产品设计和选材,并提高产品的可靠性。
3. 可靠性增长试验可靠性增长试验是为了评估机械产品在连续生产过程中的可靠性水平。
通过对多个相同机型产品进行试验,可以了解产品质量的一致性和可靠性水平的波动情况。
可靠性增长试验有助于厂家监测制造过程中的质量控制,并及时采取措施提高产品的可靠性。
三、可靠性试验方法的应用可靠性试验方法在各个行业中都有广泛的应用。
下面将就几个常见的行业进行论述。
1. 汽车行业对于汽车行业而言,机械产品的可靠性试验是尤为重要的。
在汽车领域中,寿命试验是最常见的可靠性试验方法之一。
通过对汽车的发动机、底盘等关键部件进行振动试验、冲击试验和耐久试验,可以评估汽车在各种工况下的可靠性性能。
2. 电子行业电子产品的可靠性试验是保证产品质量的关键环节。
机械系统的可靠性研究

机械系统的可靠性研究引言机械系统的可靠性研究是工程领域的重要课题之一。
可靠性指机械系统在规定的工作环境下,能够正常运行并完成设计功能的能力。
在各个行业中,机械系统的可靠性对于生产效率、安全性和成本控制都有着关键性的影响。
本文将对机械系统的可靠性研究进行探讨,并介绍一些常见的方法和技术。
机械系统可靠性的定义机械系统的可靠性是指在规定的工作条件下,系统在一定时间内完成设计要求的概率能力。
通常用故障率、失效概率、可靠度和平均失效时间等指标来评估系统的可靠性。
故障率是指单位时间内系统发生故障的概率,失效概率是指系统在一定时间内发生失效的概率,可靠度则是指系统在一定时间内正常运行的概率,平均失效时间是指系统正常运行直到发生故障的平均时间。
影响机械系统可靠性的因素设计因素机械系统的设计对其可靠性有着重要的影响。
设计要考虑系统的可维护性、容错性、可靠性和安全性等指标。
在设计阶段,应该选择可靠性高的零部件和材料,并通过合理的结构设计和优化来提高机械系统的可靠性。
工作环境因素机械系统的工作环境也会对可靠性产生影响。
例如,高温、低温、湿度、振动、腐蚀等环境因素都可能导致机械系统的故障和失效。
因此,在设计和使用机械系统时,需要充分考虑工作环境的影响,并采取相应的措施来提高系统的可靠性。
维护因素机械系统的维护也是影响可靠性的重要因素。
定期的检查、维修和保养可以有效地延长机械系统的使用寿命和提高系统的可靠性。
同时,定期更换老化和磨损的零部件,及时处理故障和隐患,也可以减少机械系统的故障率和失效概率。
机械系统可靠性评估方法为了对机械系统的可靠性进行评估,常用的方法包括可靠性试验和可靠性预测。
可靠性试验可靠性试验是通过对机械系统进行长时间的实际运行或模拟测试,来评估系统的可靠性。
通过记录系统的失效情况和运行参数,可以得到系统的故障率、失效概率、可靠度等指标。
可靠性试验可以直接反映机械系统在实际运行中的可靠性水平,但是它需要耗费大量的时间和成本。
机械结构的可靠性分析与改进设计

机械结构的可靠性分析与改进设计引言机械结构作为现代工程的核心组成部分,其可靠性分析和改进设计对于提高产品质量和降低故障率具有重要意义。
随着科技的不断进步和市场的竞争加剧,机械结构的可靠性问题变得越发突出。
本文旨在探讨机械结构的可靠性分析方法和改进设计的关键因素,以及通过优化设计来提高机械结构的可靠性。
机械结构的可靠性分析1. 可靠性概念和评估方法可靠性是指在规定的时间和环境下,机械结构完成给定功能而不发生故障的能力。
可靠性评估通常通过以下两种方法进行:- 实验法:利用实际测试数据进行统计分析,计算故障概率和故障率等指标。
通过对实验数据的建模和分析,可以了解机械结构在不同条件下的可靠性表现。
- 数值模拟法:基于物理原理和数学模型,使用计算机仿真和分析软件进行性能预测和可靠性评估。
通过建立机械结构的有限元模型,可以快速、准确地评估其可靠性。
2. 可靠性指标常用的可靠性指标包括:- 故障概率:表示单位时间或单位使用寿命内机械结构发生故障的概率,通常以百分比或千分比表示。
- 故障率:表示单位时间内机械结构平均每小时或每千小时的故障次数,常用单位为"失效/小时"或"失效/千小时"。
- 平均失效时间:表示机械结构平均连续运行到发生故障的时间,常用单位为小时。
3. 可靠性分析方法可靠性分析方法主要包括故障模式和影响分析(FMEA)、故障树分析(FTA)、可靠性增长测试(RGT)等。
- FMEA是一种通过对系统的每个组成部分进行故障模式和后果分析的方法,以识别潜在故障模式及其影响。
通过FMEA分析可以发现并优化机械结构的弱点,提高其可靠性。
- FTA是一种通过构建逻辑树模型来评估系统中故障事件的可能性和影响的方法。
通过FTA分析可以定位机械结构中可能导致故障的关键部件,进而设计出更可靠的结构。
机械结构的改进设计1. 材料与制造工艺选择材料的选择对机械结构的可靠性具有重要影响。
机械加工工艺可靠性研究

机械加工工艺可靠性研究随着制造业的不断发展,机械加工工艺越来越成为了生产过程中不可或缺的一个环节。
然而,机械加工工艺同样也面临着一系列的可靠性问题,这些问题可能会导致工件质量不稳定、生产效率低下等问题。
因此,对机械加工工艺的可靠性进行研究显得非常重要。
机械加工工艺的可靠性主要包括以下几个方面。
首先,刀具的选择对机械加工工艺的可靠性起着至关重要的作用。
不同的刀具在加工过程中所受的压力和磨损程度不同,因此需要根据不同的加工工件选择不同的刀具以保证加工精度和质量。
此外,应该定期检查刀具的磨损情况并及时更换,以确保刀具的可靠性和稳定性。
其次,加工参数的控制同样对机械加工工艺的可靠性有着至关重要的影响。
例如,切削速度、进给速度、切削深度等参数的选择会直接影响到加工表面的光洁度和精度,如果控制不当,可能会导致工件表面出现划痕、裂纹等缺陷,甚至导致工件失效。
第三,机床的稳定性和精度也是影响加工工艺可靠性的重要因素。
机床的稳定性是指机床在加工过程中不受外部干扰的能力,而机床的精度则是指机床能够达到的加工精度。
如果机床的稳定性和精度不好,就会导致加工精度不稳定,从而影响到工件的生产质量。
最后,模具的质量对机械加工工艺的可靠性也有着重要的影响。
模具是机械加工工艺中不可或缺的一部分,其质量直接影响到工件的加工精度和质量。
如果模具的质量不好,就会直接导致加工表面不光滑、精度不高等问题。
总之,机械加工工艺的可靠性研究非常重要,可以保证工件的加工精度、质量和生产效率。
在进行机械加工工艺时,需要严格控制刀具选择、加工参数、机床稳定性和模具质量等因素,以确保加工工艺的可靠性和稳定性。
机械结构可靠性研究及评估方法

机械结构可靠性研究及评估方法导言:机械结构在现代工程领域中起着举足轻重的作用,对于确保设备的正常运行至关重要。
因此,对于机械结构的可靠性进行研究和评估显得尤为重要。
本文将探讨机械结构可靠性研究的方法和评估的重要性。
1. 可靠性的定义和意义可靠性是指系统在规定的时间和环境条件下,以特定的指标能正常运行的能力。
机械结构可靠性研究旨在通过分析和评估结构的合理性和稳定性,确保其在设计寿命内不发生重大故障,从而提高产品质量和可靠性,减少维修和安全风险。
2. 基于可靠性理论的研究方法2.1 概率论方法概率论方法利用统计学原理和概率分布进行可靠性的分析和预测。
通过对结构中各个关键部件的损坏概率进行建模和分析,可以评估结构的可靠性水平,并制定相应的措施进行改进。
2.2 信度增长方法信度增长是指通过正常使用和维护机械结构,提高其使用寿命和可靠性的能力。
该方法通过对机械结构的维护、更新和改进,以及对使用过程中的故障进行分析和修复,提高结构的可靠性指标,延长其使用寿命。
3. 可靠性评估的重要性3.1 降低成本通过机械结构可靠性评估,可以预测结构的寿命和维护周期,避免因突发故障引发的生产停工和维修损失。
同时,可以根据评估结果合理安排维护计划,减少维修成本,提高设备的利用率。
3.2 提高产品质量机械结构的可靠性评估可以发现结构设计中的弱点和缺陷,及时进行改进和优化,提高产品的质量和可靠性。
通过减少故障和事故的发生,增强用户对产品的信任,提高市场竞争力。
3.3 提升安全性机械结构在一些特殊行业和设备中扮演重要角色,如航空航天、核电厂等。
对于这些系统,可靠性评估尤为重要,能够及早发现潜在的安全风险,采取相应的措施加以处理,确保设备的安全可靠运行。
4. 可靠性评估的应用案例4.1 地铁轨道交通系统地铁轨道交通系统是现代城市交通的重要组成部分。
通过对地铁轨道交通系统的可靠性评估,可以发现列车运行过程中存在的安全隐患,并优化轨道和车辆结构,提高运行的可靠性和安全性。
机械系统中的运动稳定性与可靠性研究

机械系统中的运动稳定性与可靠性研究1. 引言机械系统的运动稳定性与可靠性是工程领域中一个重要的研究方向。
这关系到机械设备的使用寿命、工作效率以及安全性。
本文将就机械系统中的运动稳定性与可靠性进行探讨。
2. 运动稳定性的概念运动稳定性是指机械系统在运动状态下的稳定性能。
一个稳定的机械系统可以在运动过程中保持既定的轨迹和速度,避免出现剧烈的摇晃和抖动。
运动稳定性的研究对于提高机械系统的精度和工作效率至关重要。
3. 运动稳定性的影响因素机械系统的运动稳定性受到很多因素的影响,包括结构设计、材料选择、润滑方式等。
首先,合理的结构设计可以降低系统的振动和摩擦,提高运动的平滑性。
其次,选择适当的材料可以提供足够的刚度和强度,避免变形和失稳。
此外,合适的润滑方式可以减少摩擦和磨损,提高系统的运动稳定性。
4. 运动稳定性的评价方法为了评价机械系统的运动稳定性,可以采用数学模型和仿真分析的方法。
通过建立运动方程和控制方程,可以得到系统的运动规律和稳定性边界。
此外,借助计算机仿真技术,可以对系统进行动态模拟和分析,进一步验证运动稳定性。
5. 可靠性的概念可靠性是指机械系统在给定的工作条件下能够保持正常运行的概率。
一个可靠的机械系统应具备耐久性、抗疲劳性和容错能力。
提高机械系统的可靠性可以减少故障次数和停工时间,提高生产效率和经济效益。
6. 可靠性的影响因素机械系统的可靠性主要受到系统设计、零部件质量和维护方法等因素的影响。
首先,合理的系统设计可以减少零部件之间的耦合和冲击,提高系统的稳定性和可维护性。
其次,选择高质量的零部件可以延长系统的使用寿命和维护周期。
此外,正确的维护方法和保养措施对于保证系统的可靠性也至关重要。
7. 可靠性的评价方法为了评价机械系统的可靠性,可以采用可靠性指标和故障分析的方法。
可靠性指标包括故障率、故障间隔时间和平均修复时间等,可以通过统计分析和概率论方法计算得到。
故障分析则对系统的故障原因进行识别和分析,以制定相应的改进措施和维护策略。
机械工程中的可靠性与维修性分析研究

机械工程中的可靠性与维修性分析研究引言机械工程作为一门重要的学科领域,旨在研究机械设备的设计、制造和运行等方面。
机械工程的可靠性与维修性是两个关键的概念,对于提高机械设备的性能和延长使用寿命至关重要。
本文将对机械工程中的可靠性与维修性进行深入的研究与分析。
一、定义与概念1. 可靠性可靠性是评估机械设备工作正常的能力。
维修性是评估设备出现故障后维修的便捷程度和速度。
在机械工程中,可靠性是指一个设备在规定条件下,经过规定时间的工作后,不出现故障的能力。
它是一个综合性指标,与设计、制造、运行环境等多个因素相关。
2. 维修性维修性是指在设备故障发生时,对其进行修复和恢复正常工作的便捷程度和速度。
好的维修性能可以减少停机时间和成本,提高生产效率。
二、主要研究内容1. 可靠性分析方法(1)故障树分析法故障树分析法是一种定性与定量相结合的分析方法,通过对系统各个元件的故障进行分类和分析,确定系统故障的原因和发生概率。
(2)失效模式与效果分析法失效模式与效果分析法旨在通过对设备的失效模式进行分析,推测失效原因,并评估对系统产生的影响,以确定设备的可靠性。
2. 维修性分析方法(1)故障树分析法故障树分析法不仅可以用于可靠性分析,也可以用于维修性分析。
通过梳理设备故障树,确定故障发生的原因和对策,以提高维修效率。
(2)维修时间分析法维修时间分析法旨在通过对维修过程中各个环节的时间进行统计和分析,找出影响维修速度的关键因素,从而优化维修流程。
三、应用案例分析1. 常见机械设备的可靠性与维修性研究(1)风力发电机组风力发电机组是一种常见的可再生能源设备,其可靠性与维修性直接影响到发电效率。
研究表明,定期维护和故障预测技术可以显著提高机组的可靠性,并降低维修成本。
(2)汽车发动机汽车发动机是一种需要高度可靠性和快速维修的设备。
研究发现,通过使用先进的故障监测系统和提前维修策略,可以减少故障率和维修时间。
2. 可靠性与维修性参数的优化设计在机械设备的设计过程中,可靠性与维修性参数的选择和优化设计对于设备的性能和寿命有着重要影响。
机械系统的稳定性与可靠性研究

机械系统的稳定性与可靠性研究近年来,随着科技的不断进步和工业化的快速发展,机械系统的稳定性和可靠性研究变得越来越重要。
机械系统是由多个组件和部件组成的复杂系统,其稳定性和可靠性直接关系到生产效率、安全性和资源利用的合理性等诸多方面。
要研究机械系统的稳定性和可靠性,首先需要了解系统的结构和工作原理。
机械系统的设计和制造需要考虑各个部件之间的相互作用和协调,以确保系统的正常运行。
例如,一个自动化生产线由多个机械臂、传送带和控制系统组成。
如果其中任何一个组件出现故障或者不稳定,可能会导致整个生产线无法正常运行。
因此,确保机械系统的各个组件之间的协调和稳定性至关重要。
稳定性的研究对机械系统的性能优化和节能减排方面有着重要意义。
稳定性指的是系统在一定工作条件下保持平衡和运行正常的能力。
机械系统的稳定性受到多种因素的影响,例如系统的结构、负载情况、温度、湿度和振动等。
研究稳定性可以帮助我们了解系统在不同工作环境下的响应和适应能力,从而做出相应的调整和改进。
例如,通过研究和优化机械系统的结构和传动方式,可以降低噪声和振动,提高系统的稳定性和工作效率。
另一方面,可靠性是指机械系统在一定时间和条件下正常运行的能力。
可靠性研究可以帮助我们预测和评估系统的寿命和故障率,从而制定合理的维护和更新计划。
机械系统的可靠性受到多个因素的影响,包括材料的耐久性、部件的磨损和老化、环境因素和不可预测的外部干扰等。
研究可靠性可以帮助我们了解这些因素对系统性能的影响和限制,从而提供有效的解决方案。
例如,通过使用高强度的材料和先进的加工技术,可以提高机械系统的可靠性和寿命。
机械系统的稳定性和可靠性研究也涉及到多个学科的交叉。
例如,材料科学、工程力学、控制工程、可靠性工程等方面都对机械系统的稳定性和可靠性有着重要的影响。
这些学科的研究成果和方法可以相互借鉴和结合,从而为机械系统的稳定性和可靠性提供更全面和有效的解决方案。
总之,机械系统的稳定性和可靠性研究对于实现高效、安全和可持续发展的工业化具有重要意义。
机械系统可靠性与鲁棒性设计的综合方法研究

机械系统可靠性与鲁棒性设计的综合方法研究随着机械系统在各个领域应用的广泛发展,人们对于机械系统的可靠性和鲁棒性设计的需求越来越高。
为了保证机械系统的正常运行和长期稳定性,提高其在复杂环境下的适应能力,研究机械系统可靠性与鲁棒性设计的综合方法成为了重要课题。
首先,机械系统可靠性与鲁棒性设计需要建立合理的数学模型和分析方法。
通过对机械系统的结构、工作原理和受力状态等进行深入分析,可以建立起适用于不同机械系统的数学模型。
在模型建立的基础上,运用可靠性、鲁棒性等相关理论和方法,对机械系统的性能指标进行预测和评估。
这些模型和方法不仅可以用于设计阶段的优化和决策,还能够为故障诊断和维护提供科学依据。
其次,机械系统可靠性与鲁棒性设计需要注重系统的全面性和综合性。
机械系统作为一个复杂的系统,其可靠性与鲁棒性不仅取决于各个部件的可靠性,还与系统的结构、工作环境、维护保养等因素密切相关。
因此,在进行可靠性与鲁棒性设计时,需要将系统的各个方面纳入考虑,并进行合理的权衡和折衷。
同时,还需要在设计过程中引入安全性、可维护性、节能性等综合性要求,以确保机械系统在各种工作条件下的稳定可靠运行。
另外,机械系统可靠性与鲁棒性设计需要充分利用信息技术手段。
随着信息技术的不断发展和应用,各种先进的数据采集、处理和分析技术已经在机械系统中得到广泛应用。
通过对机械系统的各个部件进行实时监测和数据分析,可以不仅实时了解系统的运行状态和性能指标,还能够及时发现潜在的故障和异常情况,并采取相应的措施进行处理。
这种基于信息技术的可靠性与鲁棒性设计方法,不仅可以提高机械系统的运行效率和安全性,还可以降低维护成本和人工干预。
最后,机械系统可靠性与鲁棒性设计需要不断完善和优化。
由于机械系统的工作条件和环境复杂多变,很难通过一次设计就能够满足所有要求。
因此,持续的优化和改进是不可避免的。
在实际应用中,可以通过系统的实时监测和数据分析,发现机械系统的问题和不足,并进行相应的改善和调整。
- 1、下载文档前请自行甄别文档内容的完整性,平台不提供额外的编辑、内容补充、找答案等附加服务。
- 2、"仅部分预览"的文档,不可在线预览部分如存在完整性等问题,可反馈申请退款(可完整预览的文档不适用该条件!)。
- 3、如文档侵犯您的权益,请联系客服反馈,我们会尽快为您处理(人工客服工作时间:9:00-18:30)。
概率设计法是以应力一强度干涉理论著基础的,应力一强度干涉理论将应力和强度作为服从一定分布的随机变量处理。本书第3、4章将介绍这方面内容。
9.权衡设计
权衡设计是指在可靠性、维修性、安全性、功能重量、体积、成本等之间进行综合权衡,以求得最佳的结果。
机械可靠性一般可分为结构可靠性和机构可靠性。结构可靠性主要考虑机械结构的强度以及由于载荷的影响使之疲劳、磨损、断裂等引起的失效;机构可靠性则主要考虑的不是强度问题引起的失效,而是考虑机构在动作过程由于运动学问题而引起的故障。
机械可靠性设计可分为定性可靠性设计和定量可靠性设计。所谓定性可靠性设计就是在进行故障模式影响及危害性分析的基础上,有针对性地应用成功的设计经验使所设计的产品达到可靠的目的。所谓定量可靠性设计就是充分掌握所设计零件的强度分布和应力分布以及各种设计参数的随机性基础上,通过建立隐式极限状态函数或显式极限状态函数的关系设计出满足规定可靠性要求的产品。
10.模拟方法设计
随着计算机技术的发展,模拟方法日趋完善,它不但可用于机械零件的可靠性定量设计,也可用于系统级的可靠性定量设计。
当然,机械可靠性设计的方法绝不能离开传统的机械设计和其它的一些优化设计方法,如机械计算机辅助设计、有限元分析等。
作者: 匿名
6.人机工程设计
人机工程设计的目的是为减少使用中人的差错,发挥人和机器各自的特点以提高机械产品的可靠性。当然,人为差错除了人自身的原因外,操纵台、控制及操纵环境等也与人的误操作有密切的关系。因此,人机工程设计是要保证系统向人传达的住处的可靠性。例如,指示系统不仅显示器靠,而且显示的方式、显示器的配置等都使人易于无误地接受;二是控制、操纵系统可靠,不仅仪器及机械有满意的精度,而且适于人的使用习惯,便于识别操作,不易出错,与安全有关的,更应有防误操作设计;三是设计的操作环境尽量适合于人的工作需要,减少引起疲劳、干扰操作的因素,如温度、湿度、气压、光线、色彩、噪声、振动、沙尘、空间等。
7.健壮性设计
健壮性设计最有代表性的方法是日本田口玄一博士创立的田口方法,即所谓的一个产品的设计应由系统设计、参数设计和容差设计的三次设计来完成,这是一种在设计过程中充分考虚影响其可靠性的内外干扰而进行的一种优化设计。这种方法已被美国空军制定的RM2000年中作为一种抗变异设计以及提高可靠性的有效方法。
5.耐环境设计
耐环境设计是在设计时就考虑产品在整个寿命周期内可能遇到的各种环境影响,例如装配、运输时的冲击,振动影响,贮存时的温度、湿度、霉菌等影响,使用时的气候、沙尘振动等影响。因此,必须慎重选择设计方案,采取必要的保护措施,减少或消除有害环境的影响。具体地讲,可以从认识环境、注意产品的工作环境和维修环境,还应了解产品的安装、贮存、运输的环境。在设计和试验过程中必须同时考虑单一环境和组合环境两种环境条件;不应只关心产品所处的自然环境,还要考虑使用过程所诱发出的环境。控制环境指的是:在条件允许时,应在小范围内为所设计的零部件创造一个良好的工作环境条件,或人为地改变对产品可靠性不利的环境因素。适应环境指的是:在无法对所有环境条件进行人为控制时,在设计方案、材料选择、表面处理、涂层防护等方面采取措施,以提高机械零部件本身耐环境的能力。
降额设计是使零部件的使用应力低于其额定应力的一种设计方法。降额设计可以通过降低零件承受的应力或提高零件的强度的办法来实现。工程经验证明,大多数机械零件在低于额定承载应力条件下工作时,其故障率较低,可靠性较高。为了找到最佳降额值,需做大量的试验研究。当机械零部件的载荷应力以及承受这些应力的具体零部件的强度在某一范围内呈不确定分布时,可以采用提高平均强度(如通过大加安全系数实现)、降低平均应力,减少应力变化(如通过对使用条件的限制实现)和减少强度变化(如合理选择工艺方法,严格控制整个加工过程,或通过检验或试验剔除不合格的零件)等方法来提高可靠性。对于涉及安全的重要零部件,还可以采用极限设计方法,以保证其在最恶劣的极限状态下也不会发生故障。
2.简化设计
在满足预定功能的情况下,机械设计应力求简单、零部件的数量应尽可能减少,越简单越可靠是可靠性设计的一个基本原则,是减少故障提高可靠性的最有效方法。但不能因为减少零件而使其它零件执行超常功能或在高应力的条件下工作。否则,简化设计将达不到提高可靠性的目的。
3.降额设计和安全裕度设计
机械可靠性设计方法是常用的方法,是目前开展机械可靠性设计的一种最直接有效的方法,无论结构可靠性设计还是机构可靠性设计都是大量采用的常用方法。可靠性定量设计虽然可以按照可靠性指标设计出满足要求的恰如其分的零件,但由于材料的强度分布和载荷分布的具体数据目前还很缺乏,加之其中要考虑的因素很多,从而限制其推广应用,一般在关键或重要的零部件的设计时采用。
4.余度设计
余度设计是对完成规定功能设置重复的结构、备件等,以备局部发生失效时,整机或系统仍不致于发生丧失规定功能的设计。当某部分可靠性要求很高,但目前的技术水平很难满足,比如采用降额设计、简化设计等可靠性设计方沙土,还不能达到可靠性要求,或者提高零部件可靠性的改进费用比重复配置还高时,余度技术可能成为叭一或较好的一种设计方法,例如采用双泵或双发动机配置的机械系统,但应该注意,余度设计往往使整机的体积、重量、费用均相应增加。余度设计提高了机械系统的任务可靠度,但基本可靠性相应降低了,因此采用余度设计时要慎重。
机械可靠性设计由于产品的不同和构成的差异,可以采用的可靠性设计方法有:
1.预防故障设计
机械产品一般属于串联系统.要提高整机可靠性,首先应从零部件的严格选择和控制做起。例如,优先选用标准件和通用件;选用经过使用分析验证的可靠的零部件;严格按标准的选择及对外购件的控制;充分运用故障分析的成果,采用成熟的经验或经分析试验验证后的方案。