机械系统可靠性论文
机械系统耐久性与可靠性的分析与评估
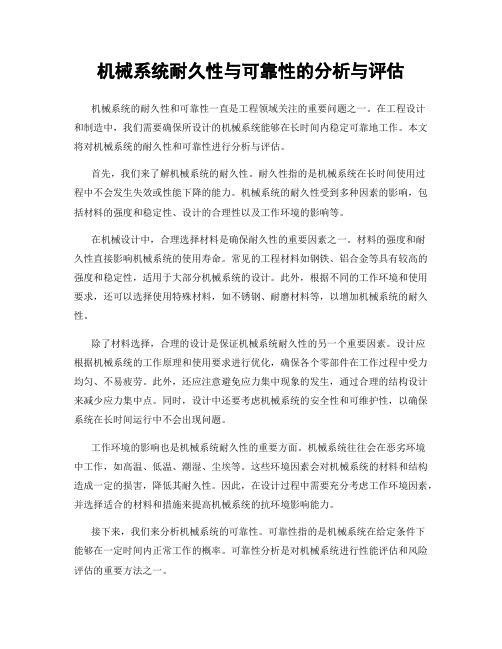
机械系统耐久性与可靠性的分析与评估机械系统的耐久性和可靠性一直是工程领域关注的重要问题之一。
在工程设计和制造中,我们需要确保所设计的机械系统能够在长时间内稳定可靠地工作。
本文将对机械系统的耐久性和可靠性进行分析与评估。
首先,我们来了解机械系统的耐久性。
耐久性指的是机械系统在长时间使用过程中不会发生失效或性能下降的能力。
机械系统的耐久性受到多种因素的影响,包括材料的强度和稳定性、设计的合理性以及工作环境的影响等。
在机械设计中,合理选择材料是确保耐久性的重要因素之一。
材料的强度和耐久性直接影响机械系统的使用寿命。
常见的工程材料如钢铁、铝合金等具有较高的强度和稳定性,适用于大部分机械系统的设计。
此外,根据不同的工作环境和使用要求,还可以选择使用特殊材料,如不锈钢、耐磨材料等,以增加机械系统的耐久性。
除了材料选择,合理的设计是保证机械系统耐久性的另一个重要因素。
设计应根据机械系统的工作原理和使用要求进行优化,确保各个零部件在工作过程中受力均匀、不易疲劳。
此外,还应注意避免应力集中现象的发生,通过合理的结构设计来减少应力集中点。
同时,设计中还要考虑机械系统的安全性和可维护性,以确保系统在长时间运行中不会出现问题。
工作环境的影响也是机械系统耐久性的重要方面。
机械系统往往会在恶劣环境中工作,如高温、低温、潮湿、尘埃等。
这些环境因素会对机械系统的材料和结构造成一定的损害,降低其耐久性。
因此,在设计过程中需要充分考虑工作环境因素,并选择适合的材料和措施来提高机械系统的抗环境影响能力。
接下来,我们来分析机械系统的可靠性。
可靠性指的是机械系统在给定条件下能够在一定时间内正常工作的概率。
可靠性分析是对机械系统进行性能评估和风险评估的重要方法之一。
在可靠性分析中,我们通常使用故障树分析、故障模式与效应分析等方法来评估机械系统的故障概率和故障模式。
这些方法可以帮助我们找出系统中可能导致失效的关键部件以及具体失效原因,并采取相应的措施来提高系统的可靠性。
机械系统的可靠性与寿命评估

机械系统的可靠性与寿命评估引言:机械工程是一门关注机械系统设计、制造和运行的学科。
在现代工业中,机械工程师扮演着至关重要的角色,他们负责确保机械系统的可靠性和寿命评估,以保障设备的正常运行和生产效率的提高。
本文将探讨机械系统的可靠性与寿命评估的重要性以及常用的评估方法。
可靠性评估:机械系统的可靠性评估是指对系统在特定条件下正常运行的能力进行定量化的分析和预测。
可靠性评估的目标是确定系统在一定时间范围内的故障概率,以便采取适当的维护和修复措施。
可靠性评估通常包括故障模式分析、故障树分析、可靠性预测等方法。
故障模式分析是一种常用的可靠性评估方法,它通过对机械系统的各个部件和子系统进行分析,确定可能出现的故障模式和对系统性能的影响。
通过对故障模式进行分析,机械工程师可以识别出潜在的故障点,并采取相应的措施来提高系统的可靠性。
故障树分析是一种定量化的可靠性评估方法,它将系统的故障模式和可能的故障原因表示为一棵树状结构。
通过对故障树进行分析,可以计算出系统在给定时间内发生特定故障的概率。
故障树分析可以帮助机械工程师确定系统中最脆弱的部分,并采取相应的措施来提高系统的可靠性。
可靠性预测是一种通过统计方法来评估机械系统寿命的方法。
通过对历史数据的分析,可以建立系统的可靠性模型,并预测系统在未来一定时间内的寿命。
可靠性预测可以帮助机械工程师制定维护计划和预防性维修策略,以最大限度地延长系统的使用寿命。
寿命评估:机械系统的寿命评估是指对系统的使用寿命进行定量化的分析和预测。
寿命评估的目标是确定系统在特定条件下的寿命,以便制定合理的维护和更新计划。
寿命评估通常包括可靠性测试、寿命模型建立等方法。
可靠性测试是一种常用的寿命评估方法,它通过对机械系统进行实验和测试,确定系统在特定条件下的寿命。
通过可靠性测试,机械工程师可以获取系统的寿命数据,并建立寿命模型,以预测系统在实际运行中的寿命。
寿命模型建立是一种通过统计方法来评估机械系统寿命的方法。
机械系统的安全性与可靠性分析

机械系统的安全性与可靠性分析一、引言机械系统在工程领域扮演着重要的角色,其安全性与可靠性是我们关注的焦点。
本文将就机械系统的安全性与可靠性进行分析,并探讨其重要性和影响因素。
二、安全性的意义与特点机械系统的安全性是指系统在运行中不会对使用者、周围环境以及自身造成危险和损害的能力。
安全性是机械系统设计中最关键的指标之一,能直接影响到人员的生命安全和财产安全。
而其特点主要体现在以下几个方面。
首先,机械系统的安全性包含了多个层面。
不仅需要保证系统在正常工作条件下的安全性,还需要考虑到可能出现的异常情况下的应对措施。
因此,在设计机械系统时,必须全面考虑各种可能的风险和隐患。
其次,机械系统的安全性是一个综合性的概念。
它涉及到多个因素的综合影响,如结构强度、材料性能、控制系统、操作方式等。
只有在各个方面都考虑到安全性要求,才能确保机械系统的整体安全。
最后,机械系统的安全性需要不断进行改进和完善。
随着科技的进步和应用领域的不断拓展,机械系统面临的风险和挑战也在不断增加。
因此,保证机械系统安全性的工作需要持续进行,不断进行安全性的评估和改进。
三、可靠性的意义与评估方法机械系统的可靠性是指系统在一定工作条件下准确、连续且满足需求的能力。
可靠性是评估机械系统能否按照设计目标正常运行的重要指标。
可靠性的意义与特点如下所示。
首先,机械系统的可靠性与系统的稳定性和一致性密切相关。
可靠性不仅仅是指系统在特定工作条件下的正常工作能力,还需要保证系统的运行质量和结果的稳定性。
只有在不同的工作条件下都能达到相同的预期结果,才能说机械系统具备可靠性。
其次,可靠性评估是一个复杂的过程,需要基于大量的实验数据和统计方法进行分析。
可靠性评估通常采用概率统计方法,通过数据分析和模型预测,计算出机械系统的可靠性指标。
这些指标可以帮助工程师了解系统的可靠性水平,并为进一步改进和优化提供依据。
最后,提高机械系统的可靠性需要综合考虑多个因素。
包括设计阶段对系统的建模和分析、材料和工艺的选择、生产和装配过程中的质量控制等。
不确定性机械系统的可靠性与优化设计

不确定性机械系统的可靠性与优化设计在现代工程设计中,机械系统的可靠性是一个至关重要的考虑因素。
机械系统的可靠性是指系统在特定的运行条件下实现其功能要求并保持在指定水平的能力。
然而,由于各种内外部因素的影响,机械系统的可靠性往往会受到一定的不确定性的影响。
因此,在设计机械系统时,如何处理不确定性以及如何优化系统设计以提高系统的可靠性成为了一个热门的研究方向。
首先要解决的问题是如何识别机械系统中的不确定性源。
机械系统中的不确定性可以来自多个方面,包括材料的不均匀性、制造过程中的误差、负载的不确定性等。
针对这些不确定性源,我们需要对不确定性进行建模和分析。
主要的不确定性建模方法包括统计模型、随机过程模型和模糊逻辑模型等。
统计模型适用于具有大量数据的情况,可以利用概率统计方法对不确定性进行建模。
而随机过程模型则适用于具有时间相关性的不确定性,可以通过随机过程的理论分析系统的可靠性。
对于那些不易精确描述的不确定性,我们可以采用模糊逻辑模型来表达模糊性,从而更好地描述系统的可靠性。
其次,我们需要在设计过程中考虑不确定性的影响。
在传统的机械设计中,通常通过提高安全系数或使用更强大的材料来抵抗不确定性的影响。
然而,这种方法往往导致了设计的过度保守,从而增加了成本并降低了系统的效率。
因此,如何在不损害系统可靠性的前提下优化设计成为了一个关键的问题。
在此背景下,一种被广泛应用的方法是基于可靠性的设计优化(RBDO)。
RBDO是通过将系统可靠性作为一个约束条件,将系统设计问题转化为一个多目标优化问题。
通过灵活地调整设计变量,RBDO可以在保证系统可靠性的同时最大化系统性能。
RBDO方法通常涉及到较为复杂的数值计算和优化算法。
其中,蒙特卡洛模拟是一种常用的方法。
在蒙特卡洛模拟中,通过对系统进行多次随机抽样,可以得到系统在不同运行条件下的响应。
通过统计分析这些响应数据,可以获得系统的可靠性指标。
另一种常用的方法是基于可信度理论的方法,通过建立系统的可信度模型,可以有效地评估系统的可靠性。
机械系统的可靠性设计与优化

机械系统的可靠性设计与优化机械系统的可靠性设计与优化一直是工程师们最关注的问题之一。
随着科技的进步和需求的日益增加,机械系统的性能和可靠性要求也在不断提高。
本文将从可靠性设计的角度出发,探讨机械系统的优化方法及其应用。
一、可靠性设计的概念与意义可靠性是指系统在规定的时间内正常运行的能力。
机械系统的可靠性设计是为了确保系统在使用寿命内能够正常运行,不发生故障或失效。
可靠性设计不仅可以降低维修成本、提高设备的使用寿命,还可以保障系统的正常运转,提高工作效率。
二、参数设计对可靠性的影响在机械系统的设计与优化过程中,各种参数的选择和控制对系统的可靠性有着直接的影响。
例如,在设计轴承选用时,合理选择轴承的材料、尺寸和润滑方式,可以减小系统因轴承故障而导致的停机时间。
同样,在选择传动装置的设计参数时,如带轮的直径和材料,齿轮的模数和强度等,也会对系统的可靠性产生重要影响。
三、优化方法在可靠性设计中的应用为了提高机械系统的可靠性,优化方法在设计中的应用变得越来越重要。
优化方法可以通过对系统的结构和参数进行调整,使系统在特定条件下具有更高的可靠性。
最常见的优化方法包括传统的试错法、有限元法和可靠性设计的基因算法等。
试错法是最早使用的一种优化方法,在设计过程中通过不断尝试和调整参数,逐步提高系统的可靠性。
然而,试错法需要大量试验和时间,成本较高。
有限元法是一种基于数值计算的优化方法。
它通过分析系统在不同条件下的载荷、应力和变形等参数,来评估系统的可靠性。
然后通过调整设计参数,使系统在特定条件下具有更高的可靠性。
有限元法具有较高的精度和效率,但在处理复杂模型时需要大量计算资源。
基因算法是一种以生物进化理论为基础的优化方法。
通过对设计参数进行随机变异和选择,不断优化设计结果,从而使系统在特定条件下具有较高的可靠性。
基因算法具有较强的全局搜索能力,并能够处理多目标优化问题。
四、案例分析为了进一步说明机械系统的可靠性设计与优化,我们以电动工具的开发为例进行分析。
影响大型机械钢结构系统可靠性因素论文

简析影响大型机械钢结构系统可靠性的因素[摘要] 根据钢结构系统可靠性安全评定原则,立足大型机械钢结构系统研究对象,建立主体失效模式安全余量的方程,来计算失效概率。
做为对风载荷与地震载荷分布进行模拟基础上,通过对大型机械钢结构的算例进行剖析,探讨失效路径长度对大型机械钢结构系统失效标椎及安全可靠性的影响,提出了在结构整体承载能力没出现降低的情况之下,失效路径的长度形成越大越好的结论。
这个结论对大型机械钢结构可靠性的工程应用有重要的指导意义。
本文以结构体系稳定的可靠性做为研究角度对这一领域的研究进行分析评述。
[关键词]大型机械钢结构;可靠性:不确定因素中图分类号:tu391文献标识码: a 文章编号:一、大型机械钢结构体系可靠性研究的成果与问题1、大型机械钢结构体系可靠性研究现状近几十年以来,高强度钢材的使用、施工技术的发展及电子计算机的同步应用,大型机械钢结构体系的大发展和广泛应用形成了极强的趋势。
大型机械钢结构体系的可靠性是国内外学者们一直关注、研究的领域。
经过数十年的研究积累,已经取得丰硕的研究成果。
目前为止,针对大型机械钢结构基本构件理论问题的研究已经很多,在相关数值分析的稳定分析已经较为成熟。
但是对构件整体稳定性与局部稳定相互作用的理论与设计应用还需深入的研究。
由于结构失去稳定是网壳结构破坏的主要原因,因此,网壳结构的稳定是一个不能忽视的问题,正确进行网壳结构稳定性尤其是单层网壳结构稳定性分析、设计是保证网壳的安全的关键所在。
自半个世纪以来,网壳结构的非线性可靠性分析一直是中外学者们关注的焦点。
欧美等发达国家的研究人员进行了全面的理论分析与研究。
创造了如人工弹簧法、能量平衡技术等多种方法,得到结构下降段曲线变为可能。
本国学者在网壳结构稳定性同样进行了大量研究。
文献有国内外研究的基础,通过精确的理论表达方式、合理的路径平衡跟踪以及迭代策略,实现复杂结构体系的几何非线性全面分析,取得了规律性成果。
机械系统的可靠性与误差分析

机械系统的可靠性与误差分析一、引言机械系统在现代工业生产中起着重要作用。
无论是汽车、航空器还是工厂设备,机械系统都承担着重要的功能。
然而,机械系统存在着一定的可靠性和误差问题。
本文将探讨机械系统的可靠性和误差分析,希望能够增进对于机械系统工作的理解并提高其可靠性。
二、机械系统可靠性的概念机械系统的可靠性是指系统在预定时间内不发生故障的能力。
一个可靠的机械系统应能够在长期使用中保持稳定的性能和功能。
机械系统的可靠性与其设计、制造、安装和维护等环节密切相关。
三、机械系统的误差来源1. 设计误差:机械系统的设计不完善可能会导致系统的误差。
例如,设计中的计算错误、图纸标注错误等。
2. 制造误差:机械系统的制造过程中不可避免会出现误差。
例如,材料的尺寸偏差、加工精度不高、装配误差等。
3. 安装误差:机械系统的安装过程中可能会出现误差。
例如,基础的水平度和平整度不符合要求、连接螺栓的紧固力不均匀等。
4. 维护误差:机械系统的维护不当也可能会导致误差。
例如,润滑不良、零部件磨损忽略等。
四、机械系统可靠性的评估方法1. 故障数据统计分析:通过对机械系统的故障数据进行统计分析,可以评估其可靠性水平。
例如,故障频率分析、故障原因分析等。
2. 可靠性分析方法:可靠性分析通过数学模型和方法对机械系统的可靠性进行量化分析。
例如,故障树分析、失效模式与影响分析等。
3. 可靠性试验方法:通过对机械系统进行可靠性试验,可以评估其在特定条件下的可靠性水平。
例如,寿命试验、加速寿命试验等。
五、机械系统误差的分析与校正方法1. 误差分析:通过对机械系统的误差进行分析,可以找出误差来源和产生原因。
例如,通过测量和测试等手段,分析系统的几何误差、运动误差等。
2. 误差校正方法:根据误差分析结果,采取相应的校正措施,提高机械系统的准确性和精度。
例如,通过调整零部件的位置、改进设计、提高制造工艺等。
六、机械系统的可靠性改进措施1. 设计改进:在机械系统的设计阶段,注重减少误差的产生。
机械系统可靠性分析与优化设计

机械系统可靠性分析与优化设计引言:在现代工业中,机械系统扮演着至关重要的角色。
而机械系统的可靠性则直接决定着产品的性能、生产的稳定性以及企业的竞争力。
因此,机械系统的可靠性分析与优化设计成为了现代工程师不可忽视的重要任务。
本文将探讨机械系统可靠性的分析方法和优化设计策略,为工程师提供一些有益的指导意见。
一、可靠性分析方法1. 故障树分析(FTA)故障树分析是一种常用的可靠性分析方法,通过分析系统的组成部分以及它们之间的关系,来推断导致系统失效的故障事件。
利用故障树分析,工程师可以识别出系统中最重要的故障因素,并针对这些因素进行改进和优化。
通过FTA,工程师可以定量评估系统的可靠性指标,如失效概率和失效率,并进一步识别出系统的薄弱环节。
2. 可靠性块图分析(RBD)可靠性块图分析是另一种常用的可靠性分析方法,通过将系统分解为不可靠性块和可靠性块,并利用布尔代数和概率论的方法,来计算系统的可靠性指标。
通过RBD分析,工程师可以探索系统中各个组件之间的相互作用,找出系统中可能存在的故障模式,并进行适当的改进和调整。
RBD分析可以帮助工程师在优化设计阶段发现并消除系统结构中的潜在问题,提高系统的可靠性水平。
二、可靠性优化设计策略1. 冗余设计冗余设计是提高系统可靠性的常用策略之一。
通过增加系统中的备用部件或系统组件,工程师可以在某些关键节点构建双重或者多重冗余结构,从而提高系统的可用性和可靠性。
冗余设计可以在一个组件失效时提供备用访问路径,并通过及时切换或修复来减少系统故障时间和停机时间。
然而,冗余设计也会增加系统的成本和复杂性,因此需要权衡利弊。
2. 故障预测和预防在系统设计的早期阶段,通过对潜在故障进行预测和预防,可以显著提高系统的可靠性。
工程师可以利用故障数据、历史记录和可靠性模型等方法,来进行故障预测和分析,识别出可能的故障模式和影响因素。
在设计过程中,针对这些故障模式和影响因素进行风险评估和控制,采取相应的措施来消除或减小故障的发生概率和影响程度。
机械系统的可靠性与安全性分析

机械系统的可靠性与安全性分析机械系统在工业领域中扮演着重要角色,承担着各种任务。
然而,由于机械系统的复杂性和长期使用带来的磨损,其可靠性和安全性问题也备受关注。
因此,对机械系统的可靠性和安全性进行分析和评估显得尤为重要。
本文将探讨机械系统的可靠性和安全性分析方法,并提出相应的解决方案。
一、可靠性分析方法1. 可靠性指标可靠性是指机械系统在给定时间内正常工作的能力。
可靠性指标包括可用性、失效率、平均失效间隔时间等。
通过对这些指标的分析,可以评估机械系统的可靠性水平。
2. 故障模式与影响分析(FMEA)FMEA是一种常用的可靠性分析方法,通过对机械系统中各个部件的故障模式和故障后果进行评估,找出可能导致系统失效的潜在故障点,并采取相应的措施进行改进,提高系统的可靠性。
3. 可靠性增长分析(RGA)可靠性增长分析是一种在机械系统设计和运营过程中常用的方法。
通过对系统运行过程中的故障进行统计和分析,了解系统的可靠性增长情况,及时采取措施解决存在的问题,提高系统的可靠性。
二、安全性分析方法1. 风险评估(Hazard Analysis)风险评估是一种常用的安全性分析方法,通过对机械系统可能存在的危险源进行识别和评估,了解其对系统和人员的潜在风险,从而采取相应的措施进行风险管控,确保系统的安全性。
2. 展望性分析(Proactive Analysis)展望性分析是一种通过对机械系统设计和运营过程中的问题进行前瞻性分析的方法。
通过预测和评估可能的安全隐患和故障点,提前采取相应的预防和改进措施,确保系统的安全性。
3. 事故调查与分析(Accident Investigation and Analysis)事故调查与分析是一种对机械系统发生的事故进行深入调查和分析的方法。
通过了解事故的原因和过程,找出潜在的问题和故障点,并采取相应的措施进行改进和预防,提高系统的安全性。
三、解决方案1. 定期维护和检修机械系统的定期维护和检修是确保其可靠性和安全性的重要环节。
航天器机械系统可靠性设计与评估研究

航天器机械系统可靠性设计与评估研究随着科技的不断进步,航天器机械系统在现代航天探索中扮演着至关重要的角色。
航天器机械系统的可靠性设计与评估是确保航天任务成功完成的关键因素之一。
本文将探讨航天器机械系统可靠性设计与评估的研究。
首先,航天器机械系统的可靠性设计是航天工程中不可或缺的一环。
航天器机械系统需要在恶劣的环境条件下工作,如高温、低温、真空等。
因此,航天器机械系统的设计必须经过严格的可靠性分析和测试,确保其在极端条件下仍能正常工作。
可靠性设计包括但不限于工程材料的选择、结构设计的合理性、功能模块的耐久性等方面的考虑。
只有通过可靠性设计,航天器机械系统才能够在航天任务中发挥出最大的功效。
其次,航天器机械系统的可靠性评估是对设计方案进行验证和验证的过程。
航天工程是一项高风险的工作,任何失误都可能导致严重的后果。
因此,航天器机械系统的可靠性评估至关重要。
可靠性评估需要考虑多种因素,如可靠性指标、故障诊断和恢复能力、故障模式与效应分析等。
通过可靠性评估,工程师可以对设计方案进行修正和改进,以提高航天器机械系统的可靠性和安全性。
除了可靠性设计和评估,航天器机械系统的维修与保养也是一个重要的研究课题。
在航天任务中,航天器机械系统经受了巨大的压力和挑战。
因此,及时的维修和保养对于延长航天器寿命、保证任务顺利进行至关重要。
维修和保养策略的制定需要考虑多个因素,如飞行任务的持续时间、航天器所处的环境条件、航天器机械系统的使用频率等。
通过合理的维修和保养策略,可以减少航天器机械系统的故障率,降低维修成本,提高航天任务的成功率。
此外,航天器机械系统可靠性设计与评估的研究还面临许多挑战。
首先,航天器机械系统的复杂性和巨大性使得其设计和评估工作十分困难。
其次,航天器机械系统的工作环境具有极高的不确定性,如辐射、微重力等。
这些不确定因素给航天器机械系统的设计和评估带来了更大的挑战。
因此,研究人员需要不断创新和改进研究方法,以提高航天器机械系统的可靠性。
机械系统的可靠性优化设计

机械系统的可靠性优化设计随着工业技术的不断进步和发展,机械系统在现代生产中的应用越来越广泛。
然而,机械系统的可靠性一直是设计师和制造商关注的重点问题之一。
因为机械系统在运行过程中,可能会面临各种各样的故障和失效,给生产工艺和维护工作带来了许多困扰。
为了提高机械系统的可靠性,需要进行优化设计。
首先,机械系统的结构合理性对于其可靠性至关重要。
合理的结构设计可以减少各个部件之间的相互作用,降低系统出现故障的概率。
例如,通过合理的布局,可以避免不同部件之间的冲突和摩擦,减少因磨损导致的故障。
此外,还可以采用模块化设计,将系统分成多个独立的部分,这样即使其中一个部分出现故障,也不会影响整个系统的运行。
因此,在机械系统的设计过程中,应当多考虑结构的合理性,避免不必要的风险。
其次,对于机械系统的各个部件,需要选择合适的材料和加工工艺,以保证其可靠性和稳定性。
材料的选择应当与系统所处环境相适应,避免受到温度、湿度等因素的影响。
例如,如果机械系统经常会遇到高温环境,那么就需要选择高温耐受的材料,以保证系统的正常运行。
同时,加工工艺也应当符合部件的要求,避免因加工不当而导致的质量问题。
这些因素都会影响机械系统的可靠性,值得设计师和制造商的重视。
此外,对于机械系统的维护和保养也至关重要。
定期的维护可以及时发现和排除潜在的故障点,保证系统的正常运行。
例如,定期更换润滑油和清洁系统内部的杂质可以减少摩擦和磨损,延长机械系统的使用寿命。
此外,还可以利用故障诊断和预测技术,提前发现可能出现的问题,并采取相应的措施进行修复。
因此,在机械系统的设计和制造过程中,应当注重维护和保养的需求,为系统的可靠性提供有力的支持。
最后,现代技术的应用也可以为机械系统的可靠性优化设计提供新的思路和方法。
例如,借助物联网技术,可以实时监测机械系统运行的各项指标,及时发现异常并采取措施。
通过大数据分析,还可以找出系统中的潜在问题,并提供相应的解决方案。
航空发动机机械系统的可靠性研究与优化设计

航空发动机机械系统的可靠性研究与优化设计航空发动机作为现代飞行器的心脏,其机械系统的可靠性直接关系到航空安全以及飞机性能的表现。
因此,对航空发动机机械系统的可靠性进行研究和优化设计是非常重要的。
本文将探讨航空发动机机械系统可靠性的研究方向和优化设计方法。
一、航空发动机机械系统可靠性的研究方向航空发动机机械系统可靠性的研究方向可以从多个角度入手。
首先是故障原因的分析和排查。
对于航空发动机机械系统的故障,我们需要通过分析和排查,找出具体的故障原因,从而针对性地进行优化和改进。
其次是寿命评估和可靠性预测。
航空发动机机械系统运行时间的长短直接影响到其可靠性,因此需要通过寿命评估和可靠性预测来确定机械系统的使用寿命以及故障发生的概率。
最后是关键零部件的研究和优化。
航空发动机机械系统由许多关键零部件组成,对这些关键零部件进行研究和优化,可以提高整个系统的可靠性。
二、航空发动机机械系统优化设计的方法航空发动机机械系统优化设计是提高可靠性的重要手段。
在优化设计过程中,可以采用多种方法和技术。
首先是先进的材料应用。
选择适当的材料对于提高航空发动机机械系统的可靠性至关重要。
例如,使用高温合金材料可以提高零部件的耐热性能,减少故障的发生。
其次是精密加工和装配技术的应用。
通过提高零部件的精密加工和装配技术,可以减少潜在的故障点和松动问题,提高机械系统的可靠性。
另外,还可以采用冗余设计和安全措施。
冗余设计可以在某些关键部位增加备用零部件,一旦出现故障,可以进行快速更换,从而不影响整个系统的运行。
三、航空发动机机械系统可靠性研究中的挑战与展望航空发动机机械系统可靠性研究虽然具有重要意义,但也面临一些挑战。
首先是相关数据的获取和处理。
由于航空发动机的复杂性和保密性,相关数据的获取和处理是非常困难的。
其次是成本与效益的平衡。
优化设计和提高可靠性需要大量的研究和投入,而这些成本通常会成为制约因素。
在未来,我们可以通过建立更完善的数据收集与处理系统,同时加强学术界与工业界的合作,来解决这些挑战。
机械系统的可靠性与可用性分析

机械系统的可靠性与可用性分析引言:机械系统在现代工业中起着至关重要的作用,它的可靠性和可用性对于生产效率和安全性具有巨大的影响。
本文将就机械系统的可靠性和可用性进行深入分析,并探讨如何提高机械系统的可靠性和可用性。
一、可靠性分析:可靠性是指在特定条件下,机械系统在一段时间内正常工作的能力。
提高机械系统的可靠性,首先需要进行可靠性分析。
可靠性分析的目的是找出可能导致系统故障的原因,并采取相应的措施预防故障的发生。
1.1 故障模式与失效分析(FMEA):故障模式与失效分析是一种常用的可靠性分析方法。
它通过分析机械系统中可能发生的各种故障模式及其对系统正常工作的影响,来评估系统的可靠性。
故障模式与失效分析主要分为三个步骤:确定故障模式、评估故障后果和制定预防措施。
1.2 可靠度增长与维修策略:在实际运行过程中,机械系统的可靠性可以通过不断进行维修和改进来提高。
可靠度增长与维修策略是一种通过逐步替换系统元件和进行定期检修的方法,来延长机械系统的可靠性。
通过分析系统元件的失效概率和维修资源的分配情况,可以制定出合理的可靠度增长和维修策略。
二、可用性分析:可用性是指机械系统在给定时间内能够正常工作的能力。
提高机械系统的可用性,需要进行可用性分析,并采取相应的措施提高系统的可用性。
2.1 系统可用性计算方法:系统可用性可以通过计算系统的运行时间和故障时间之比来进行评估。
常用的系统可用性计算方法有MTBF(Mean Time Between Failures)和MTTR(Mean Time To Repair)方法。
MTBF指的是故障间隔时间的平均值,MTTR指的是故障修复时间的平均值。
通过不断改进MTBF和缩短MTTR,可以提高机械系统的可用性。
2.2 预防性维护与预防性检修:预防性维护和预防性检修是提高机械系统可用性的重要手段。
预防性维护是指在机械系统正常运行期间对系统进行定期检查和维护,以预防故障的发生;预防性检修是指在系统正常运行期间对系统进行定期检修和更换,以保持系统的正常工作状态。
机械系统的可靠性研究

机械系统的可靠性研究引言机械系统的可靠性研究是工程领域的重要课题之一。
可靠性指机械系统在规定的工作环境下,能够正常运行并完成设计功能的能力。
在各个行业中,机械系统的可靠性对于生产效率、安全性和成本控制都有着关键性的影响。
本文将对机械系统的可靠性研究进行探讨,并介绍一些常见的方法和技术。
机械系统可靠性的定义机械系统的可靠性是指在规定的工作条件下,系统在一定时间内完成设计要求的概率能力。
通常用故障率、失效概率、可靠度和平均失效时间等指标来评估系统的可靠性。
故障率是指单位时间内系统发生故障的概率,失效概率是指系统在一定时间内发生失效的概率,可靠度则是指系统在一定时间内正常运行的概率,平均失效时间是指系统正常运行直到发生故障的平均时间。
影响机械系统可靠性的因素设计因素机械系统的设计对其可靠性有着重要的影响。
设计要考虑系统的可维护性、容错性、可靠性和安全性等指标。
在设计阶段,应该选择可靠性高的零部件和材料,并通过合理的结构设计和优化来提高机械系统的可靠性。
工作环境因素机械系统的工作环境也会对可靠性产生影响。
例如,高温、低温、湿度、振动、腐蚀等环境因素都可能导致机械系统的故障和失效。
因此,在设计和使用机械系统时,需要充分考虑工作环境的影响,并采取相应的措施来提高系统的可靠性。
维护因素机械系统的维护也是影响可靠性的重要因素。
定期的检查、维修和保养可以有效地延长机械系统的使用寿命和提高系统的可靠性。
同时,定期更换老化和磨损的零部件,及时处理故障和隐患,也可以减少机械系统的故障率和失效概率。
机械系统可靠性评估方法为了对机械系统的可靠性进行评估,常用的方法包括可靠性试验和可靠性预测。
可靠性试验可靠性试验是通过对机械系统进行长时间的实际运行或模拟测试,来评估系统的可靠性。
通过记录系统的失效情况和运行参数,可以得到系统的故障率、失效概率、可靠度等指标。
可靠性试验可以直接反映机械系统在实际运行中的可靠性水平,但是它需要耗费大量的时间和成本。
机械系统的安全性与可靠性优化

机械系统的安全性与可靠性优化一、引言机械系统在现代工业中起着重要的作用,然而,安全性与可靠性问题一直是制约机械系统运行效果的关键因素。
本文将探讨如何优化机械系统的安全性与可靠性,以提高工业生产的效率和质量。
二、安全性优化机械系统的安全性是指在运行过程中,系统不会对人员和环境产生危害。
为了优化机械系统的安全性,首先需要对系统的设计和制造过程进行严格的检验和监测。
通过采用高质量材料和先进的制造工艺,可以降低系统故障和事故的风险。
其次,应当加强对机械系统运行过程的监测和维护。
定期对系统进行检查,及时发现和排除潜在的问题,以避免事故的发生。
同时,应建立完善的紧急救援机制,以应对突发事件。
此外,人员的培训和意识提高也是提高机械系统安全性的重要因素。
工作人员应该接受相关培训,了解系统运行原理和维护方法,可以提高其辨识问题和应对突发情况的能力。
三、可靠性优化机械系统的可靠性是指系统在规定时间内能够正确运行的能力。
为了优化机械系统的可靠性,首先需要对系统的结构和零部件进行优化。
采用先进的技术和材料,设计出更加稳定和耐用的部件,可以提高系统的可靠性。
此外,对系统进行充分的试验和验证也是提高可靠性的关键。
通过模拟真实运行环境,对系统进行严格的测试,以确保其能够在不同工况下正常运行。
另外,加强对系统运行过程中的监测和维护也可以提高可靠性。
通过对系统进行定期检查和维护,及时发现和修复问题,可以避免故障的发生。
四、安全性与可靠性的平衡在优化机械系统的安全性和可靠性时,需要注意两者之间的平衡。
提高安全性一方面能够保护人员和环境,减少事故的发生,但也可能导致系统的复杂性增加,增加了出故障的可能性。
相反,过度追求可靠性可能会导致系统成本的增加,限制系统的发展潜力。
因此,在优化机械系统的安全性和可靠性时,应该以综合效益为出发点,根据具体的工作环境和要求,找到最佳的平衡点。
例如,在一些对产品质量要求较高的行业中,可靠性可能更加重要;而在一些人员密集的场所,安全性可能更加重要。
机械系统中的运动稳定性与可靠性研究

机械系统中的运动稳定性与可靠性研究1. 引言机械系统的运动稳定性与可靠性是工程领域中一个重要的研究方向。
这关系到机械设备的使用寿命、工作效率以及安全性。
本文将就机械系统中的运动稳定性与可靠性进行探讨。
2. 运动稳定性的概念运动稳定性是指机械系统在运动状态下的稳定性能。
一个稳定的机械系统可以在运动过程中保持既定的轨迹和速度,避免出现剧烈的摇晃和抖动。
运动稳定性的研究对于提高机械系统的精度和工作效率至关重要。
3. 运动稳定性的影响因素机械系统的运动稳定性受到很多因素的影响,包括结构设计、材料选择、润滑方式等。
首先,合理的结构设计可以降低系统的振动和摩擦,提高运动的平滑性。
其次,选择适当的材料可以提供足够的刚度和强度,避免变形和失稳。
此外,合适的润滑方式可以减少摩擦和磨损,提高系统的运动稳定性。
4. 运动稳定性的评价方法为了评价机械系统的运动稳定性,可以采用数学模型和仿真分析的方法。
通过建立运动方程和控制方程,可以得到系统的运动规律和稳定性边界。
此外,借助计算机仿真技术,可以对系统进行动态模拟和分析,进一步验证运动稳定性。
5. 可靠性的概念可靠性是指机械系统在给定的工作条件下能够保持正常运行的概率。
一个可靠的机械系统应具备耐久性、抗疲劳性和容错能力。
提高机械系统的可靠性可以减少故障次数和停工时间,提高生产效率和经济效益。
6. 可靠性的影响因素机械系统的可靠性主要受到系统设计、零部件质量和维护方法等因素的影响。
首先,合理的系统设计可以减少零部件之间的耦合和冲击,提高系统的稳定性和可维护性。
其次,选择高质量的零部件可以延长系统的使用寿命和维护周期。
此外,正确的维护方法和保养措施对于保证系统的可靠性也至关重要。
7. 可靠性的评价方法为了评价机械系统的可靠性,可以采用可靠性指标和故障分析的方法。
可靠性指标包括故障率、故障间隔时间和平均修复时间等,可以通过统计分析和概率论方法计算得到。
故障分析则对系统的故障原因进行识别和分析,以制定相应的改进措施和维护策略。
机械系统设计中的可靠性问题分析

机械系统设计中的可靠性问题分析机械可靠性的提高是当前机械行业普遍关注的话题,而设计、制造、管理则是提高可靠性的关键要素。
文章对机械可靠性进行了介绍,并在此基础上对机械可靠性的优化设计、稳健设计进行了深入的分析和探讨。
标签:机械可靠性设计;发展沿革;优化设计;稳健设计引言可靠性研究最早开始于四十年代针对电子产品故障的研究,经过多年的积累与发展,电子产品可靠性技术体系已获得完善并逐渐成熟起来。
电子产品的可靠性水平日益提高,并具备丰富的工程经验和巨大的数据资源。
近些年来,可靠性技术也逐渐应用于机械领域,并发挥着重要的作用。
机械系统越来越复杂,对于其可靠性的要求也逐步提高,尤其是在军用装备和航空领域,对于机械可靠性的要求更加严格,并成为系统可靠性中较为薄弱的环节。
为此,非常有必要研究机械的可靠性,从而推动科技的进步与发展。
对于复杂机械产品来说,其可靠性受到多种因素的影响,如使用条件、使用环境、维修方法、人为因素等等,属于可修复的人机系统。
1 机械可靠性设计的概述作为最主要和最重要的技术指标,可靠性是评判产品质量好坏的关键因素,并逐渐成为工程领域普遍关注的焦点。
机械可靠性贯穿于从产品的设计研发到装配调试的各个环节,可靠性是在概率统计的理论基础上发展起来的,加强机械可靠性设计的推广和应用,对于提高产品质量、降低成本有着非常重要的意义。
随着可靠性技术的创新与发展,其设计方式也越来越丰富,呈多样化的趋势发展。
数学模型法是在可靠性设计中应用得较为广泛的一种方式,基于实验所获得的数据,并充分利用了概率统计的原理。
数学模型法可以划分为两部分,其中一部分所涉及的量在时间范畴内具有可靠性质,换句话说,即所涉及的量是遵循一定的规律的,随着时间的变动,其疲劳寿命和损耗也将在一定的范围内产生变动。
另外一部分为偶然因素所引发的事件结果的可靠性,偶然因素所导致的波动是不定期出现的,具有不确定性,一般来说,需要利用概率可靠性来对随机事件进行计算。
机械系统的稳定性与可靠性研究

机械系统的稳定性与可靠性研究近年来,随着科技的不断进步和工业化的快速发展,机械系统的稳定性和可靠性研究变得越来越重要。
机械系统是由多个组件和部件组成的复杂系统,其稳定性和可靠性直接关系到生产效率、安全性和资源利用的合理性等诸多方面。
要研究机械系统的稳定性和可靠性,首先需要了解系统的结构和工作原理。
机械系统的设计和制造需要考虑各个部件之间的相互作用和协调,以确保系统的正常运行。
例如,一个自动化生产线由多个机械臂、传送带和控制系统组成。
如果其中任何一个组件出现故障或者不稳定,可能会导致整个生产线无法正常运行。
因此,确保机械系统的各个组件之间的协调和稳定性至关重要。
稳定性的研究对机械系统的性能优化和节能减排方面有着重要意义。
稳定性指的是系统在一定工作条件下保持平衡和运行正常的能力。
机械系统的稳定性受到多种因素的影响,例如系统的结构、负载情况、温度、湿度和振动等。
研究稳定性可以帮助我们了解系统在不同工作环境下的响应和适应能力,从而做出相应的调整和改进。
例如,通过研究和优化机械系统的结构和传动方式,可以降低噪声和振动,提高系统的稳定性和工作效率。
另一方面,可靠性是指机械系统在一定时间和条件下正常运行的能力。
可靠性研究可以帮助我们预测和评估系统的寿命和故障率,从而制定合理的维护和更新计划。
机械系统的可靠性受到多个因素的影响,包括材料的耐久性、部件的磨损和老化、环境因素和不可预测的外部干扰等。
研究可靠性可以帮助我们了解这些因素对系统性能的影响和限制,从而提供有效的解决方案。
例如,通过使用高强度的材料和先进的加工技术,可以提高机械系统的可靠性和寿命。
机械系统的稳定性和可靠性研究也涉及到多个学科的交叉。
例如,材料科学、工程力学、控制工程、可靠性工程等方面都对机械系统的稳定性和可靠性有着重要的影响。
这些学科的研究成果和方法可以相互借鉴和结合,从而为机械系统的稳定性和可靠性提供更全面和有效的解决方案。
总之,机械系统的稳定性和可靠性研究对于实现高效、安全和可持续发展的工业化具有重要意义。
机械系统中的可靠性与安全性分析

机械系统中的可靠性与安全性分析机械系统在现代社会中扮演着重要的角色,涵盖各个行业,包括交通运输、制造业、能源等。
然而,由于机械系统的复杂性和多样性,其可靠性与安全性成为引人注目的议题。
本文将就机械系统中的可靠性与安全性展开论述,旨在探讨其分析方法和关键因素。
一、机械系统中的可靠性分析机械系统的可靠性是指在特定工作条件下,系统在一定时间内正常工作的能力。
可靠性分析通常分为定性分析和定量分析两个层次。
首先,定性分析是在初步认识系统的基础上进行的。
通过观察和了解系统的运行过程,分析系统是否存在潜在的故障点和风险隐患。
定性分析往往结合经验和专业知识,评估系统的结构设计、材料选择、工艺装备等因素是否能够满足预期的要求。
然而,定性分析的结果不能直接得出准确的数字或数据,因此需要进行定量分析。
定量分析是通过搜集系统运行数据并应用数学统计方法来评估系统的可靠性水平。
常用的定量分析方法包括故障树分析、可靠性块图和失效模式与影响分析等。
故障树分析是一种系统性的分析方法,通过图形化表示系统可能发生故障的逻辑关系,识别导致系统故障的根本原因。
该方法可以帮助工程师们定位系统中的故障点,并采取相应的预防措施。
可靠性块图是将整个系统看作是由多个模块组成的,通过概率计算每个模块的可靠性,并综合计算系统的可靠性。
这样可以帮助工程师们判断哪些模块对系统可靠性影响最大,并针对性地进行改进和优化。
失效模式与影响分析方法可以用于分析系统中可能出现的各种失效模式,并评估其对系统功能和安全的影响。
通过模拟不同失效模式的情况,可以制定相应的维护策略以确保系统的可靠性和安全性。
二、机械系统中的安全性分析机械系统的安全性是指在正常工作状态下,系统保证操作人员和周围环境免受伤害的程度。
安全性分析旨在识别潜在的危险源,并确定相应的控制措施以降低风险。
安全性分析的方法主要包括风险评估、安全性评估和可行性研究。
风险评估是确定潜在危险的起源、发生的可能性和危害程度的过程。
高海拔环境下机械系统可靠性研究

高海拔环境下机械系统可靠性研究引言:高海拔环境对机械系统的运行稳定性和可靠性提出了严峻的挑战。
在这样的环境下,机械系统面临着气温低、氧含量少、大气压力低等多种影响因素。
因此,对高海拔环境下机械系统可靠性的研究具有重要的意义。
本文将对高海拔环境下机械系统可靠性的影响因素和提升策略进行探讨。
一、高海拔环境下机械系统可靠性的影响因素1. 气温低高海拔地区气温低,会导致机械系统中的润滑剂变得粘稠或凝固,从而影响机械零部件的运行效果。
此外,低温还可能导致机械零部件变脆,增加零部件破裂的风险。
2. 氧含量少高海拔地区的氧含量较低,这对于机械系统的燃烧过程造成了影响。
由于燃烧需要氧气参与,氧含量的减少会导致机械系统的燃烧效率下降,从而影响机械系统的工作效果。
3. 大气压力低高海拔地区的大气压力相对较低,这会导致机械系统在高负荷运作时的散热效果下降。
由于热量无法有效散出,机械零部件温升速度增加,从而影响机械系统的可靠性。
二、提升高海拔环境下机械系统可靠性的策略1. 材料选择在高海拔环境下,材料的选择至关重要。
应选择抗低温和抗腐蚀性能好的材料,以确保机械系统在恶劣环境下的长期运行。
此外,还可以使用一些特殊材料,如陶瓷,来提升机械系统的耐用性。
2. 润滑剂选用针对高海拔环境下润滑剂变稠或凝固的问题,可以选择具有较低凝固点和较好低温流动性的润滑剂。
此外,还可以采用加热手段,确保润滑剂在低温下保持流动性,保护机械零部件不受损。
3. 散热系统设计针对大气压力低导致的散热问题,可以通过合理设计机械系统的散热系统来提升机械系统的可靠性。
例如,增加散热片的面积,增加风扇的数量等措施,以提高散热效果,避免机械零部件过热。
4. 系统维护高海拔地区的机械系统应定期进行维护与保养。
特别是对润滑剂、密封件等易受环境影响的部件应进行定期更换,确保机械系统的可靠性。
同时,对于那些暴露在室外的机械设备,还需要做好防锈和防腐蚀的工作。
结论:高海拔环境对机械系统的可靠性提出了较高的要求,但通过合理的设计和维护,可以提升机械系统在高海拔环境下的可靠性。
- 1、下载文档前请自行甄别文档内容的完整性,平台不提供额外的编辑、内容补充、找答案等附加服务。
- 2、"仅部分预览"的文档,不可在线预览部分如存在完整性等问题,可反馈申请退款(可完整预览的文档不适用该条件!)。
- 3、如文档侵犯您的权益,请联系客服反馈,我们会尽快为您处理(人工客服工作时间:9:00-18:30)。
机械系统可靠性研究
摘要:机械的使用过程,同时也是使用维修方法适应机械结构的过程,而机械的设计过程,又应该是使机械去适应使用与维修条件的过程,两者是相互依存,相互统一的。
机械可靠性虽是设计出来的,制造出来的,管理出来的,但使用对机械可靠性具有巨大的反馈作用。
本文从机械系统的特点分析入手,对机械可靠性的研究中存在的问题及研究的目的和意义进行了详细的分析为机械使用
可靠性的研究奠定了必要的理论基础。
关键词:机械系统可靠性
1 机械系统的特点及对可靠性的要求
可靠性研究最初是从四十年代研究电子产品故障开始的。
经过四十多年的发展,电子产品可靠性技术体系已经比较完善和成熟,工程经验和数据资源比较丰富,电子产品的可靠性水平已有了很大提高。
但随着系统的复杂程度和可靠性要求的日益提高,机械产品的可靠性问题越来越突出,特别是航空产品和军用装备,机械可靠性已成为全系统可靠性的薄弱环节,因此必须对机械可靠性进行研究。
复杂机械产品都属于可修复人机系统,实际应用中其可靠性受环境条件、使用条件、维修方法和人的因素等的影响较大;同时,由于机械系统在故障机理、模式、特性以及装配联接等方面不同于电子产品,导致机械产品可靠性具有以下特点:
1.1 机械产品种类多、功能复杂,各种设备都有其固有的要求,
大多数零部件要分别进行设计,通用性差。
在进行可靠性设计或可靠性预计时,往往没有现成的可靠性数据可以利用,而必须通过试验才能得到。
1.2 机械零件的加工过程多,大多数零件是单件加工,零件的质量因工艺过程、加工设备、操作者的技能等因素的变化而异,这势必给统计零件的故障率带来严重的困难。
缺少“相似”设备,可靠性预计缺乏可借鉴的相似数据。
1.3 在机械产品实际工作过程中,由于产品的载荷、温度、压力和系统的工作条件的经常变化造成其失效模式多种多样,甚至同一种产品用在不同的地方所造成的失效模式也不同。
因此,不能简单地用一种数学模型来处理。
1.4 机械产品,尤其是航空机械产品,其结构复杂,环境条件和工作条件变化范围大,在进行可靠性试验时,很难模拟产品的实际使用情况对产品施加综合应力。
因此,通过场内试验求得的可靠性指标与外场使用可靠性值差别很大。
1.5 机械产品的失效类型多种多样,不能象电子产品那样,一般假定为指数分布,在目前人员水平还比较低的情况下,要把试验、使用数据处理成有用的数据,具有一定的困难。
1.6 变形、腐蚀、老化、磨损与疲劳构成了机械产品主要的失效机理,一般具有耗损特性。
产品的这种失效机理是与产品的结构、材料、加工过程、工作条件和环境条件等综合因素密切相关的,往往不容易采用简单定量方法描述。
1.7 机械产品是由零部件、组件、总成组成的系统,故障不仅与单个零件的失效有关,而且与零件间的装配联接、润滑条件等因素有关。
有些部件的故障属于零件间的动作不协调。
因此,机械产品可靠性的着眼点着重在部件、组件,必须以这些功能模块为研究对象。
1.8 机械产品的设计多采用安全系数法,具有一定的裕度,允许载荷应力在一定范围内波动。
使得机械产品的失效定义与其具体应用场合有关,很难做统一规定。
1.9 通常情况下,只能使用小样对机械产品的可靠性进行试验,此外,需要花费大量的时间才能完成损耗型失效模式的测验,借助于电子产品的可靠性施行试验鉴定的统计方案往往是研制方无法
接受的。
1.10 机械产品的工作环境通常与电子产品不同,对各种环境应力的敏感程度更大。
1.11 机械系统一般为人机系统,影响系统效能和可靠性的因素,除系统的硬件、软件、环境外,还有人的因素。
1.12 机械系统都为复杂的可修复系统,使用中,其技术状态多,技术使用过程复杂,维修对其可靠性影响较大。
2 机械可靠性研究中存在的问题
机械系统是由硬件(设备)、软件(设备说明书和计算机程序等)、环境及操作者(也就是人)等四种因素构成的。
现阶段在研究系统可靠性方面存在许多问题,概括起来主要有下述几点:传统的可靠
性方法与理论主要是研究硬件的,因此人们能够准确地掌握有关系统硬件问题,而且已经形成了较为完善的、系统性较强的一整套的规范标准及技术方法,虽然这些成果是通过对硬件的研究所取得的,并且这些研究成果还存在不完善不健全的地方,但是也已经过了几十年的发展历程,算是相对成熟了。
针对硬件的控制与操作所作的程序与说明就是软件,它有着和硬件根本不同的物理特性。
人们对软件可靠性的研究也只有20多年的历史,从理论到方法都尚未成熟,需要着力深入研究。
人作为系统的智慧主宰,本应有最佳的表现,但由于人在操作时受到本身素质和生理、心理的健康状况的制约,发生错误是难免的。
人机系统的另一个重要因素就是环境,没有哪个系统是可以脱离环境的。
软件的可靠性、硬件的可靠性以及人的可靠性很大程度上都取决于环境。
现阶段,人们已经掌握了系统可靠性与环境的极端值之间的关系,但对于系统可靠性与环境变化率之间关系的研究还尚处于初级阶段,还有待进一步研究。
人对系统可靠性的影响是极为明显的。
我们需要做的是试图将人的可靠性模型科学地描述出来。
机械可靠性包含使用可靠性与固有可靠性两部分的内容。
机械在使用过程中所表现出来的可靠性就是使用可靠性。
机械的设计、使用及维修都离不开使用可靠性的支撑。
现阶段,主要是参考电子产品可靠性的相关方法及理论来开展使用可靠性的研究的。
在具体的研究中,往往将注意力集中在硬件方面,而忽视了人、环境及软件的因素,可靠性评价结果差强人意,所以在今后我们必须深化对
使用可靠性的研究。
通常情况下,我们无法实时监测机械的可靠性指标,因此,我们只能参考同类产品的相关数据及设计者的经验来开展工作。
现阶段,我国的可靠性基础性工作尚未成熟,设计中所使用的指标过于抽象和综合,使机械可靠性和实际情况发生脱节。
为解决这一问题,我们应当强化基础性的管理,充分考虑工程使用因素,走密切联系工程实践的可靠性道路。
3 研究机械使用可靠性的目的与意义
开展针对使用阶段可靠性的研究工作,具有十分重要的意义:第一,虽然在机械的设计、生产阶段就已经形成了机械的结构,但作为设计生产延续的使用阶段才是重点,为提高机械的可靠性,减少故障的发生率,我们必须重视对试用阶段可靠性的研究。
第二,机械的使用、维修条件是与其所处的环境密切相关的,而并非是一成不变的。
我们只有通过对使用阶段可靠性的研究,才能促进维修结构及周期的不断优化。
第三,机械设计中的不足是难以避免的。
为提高机械的可靠性,我们必须重视机械的使用过程,强化对使用阶段可靠性的研究。
对机械使用阶段的可靠性的研究意义深远:首先,有利于科学测定机械使用阶段的可靠性水平,以完成对机械设计可靠性的验证;其次,有利于研究机械可靠性与使用方法与条件的关系,以便制定科学的使用标准;第三,有利于提高机械的利用率,延长机械的使用年限;最后,对机械使用阶段的可靠性研究所获取的数据能
促进机械的改进。
参考文献:
[1]杨志飞,李平等著.以故障为中心的工程可靠性,国防工业出版社,1995.
[2]杨为民主编.可靠性维修性保障性总论,国防工业出版社,1996.
[3]高连华等编.装备系统设计与保障性,国防工业出版社1993.
[4]四川省机械工程学会编译,机器可靠性,四川人民出版社,1983.
[5][英]j莫布雷著,石磊,谷宁昌译,以可靠性为中心的维修,机械工业出版社,1995.
[6]陈学楚主编,维修基础理论,科学出版社,1998.
[7l[英]a.k.s.贾尔丁著,蓝文谨译,维修、更换和可靠性,机械工业出版社,1985.。