络合铁脱硫技术工艺方案5.13
络合铁脱硫成套技术
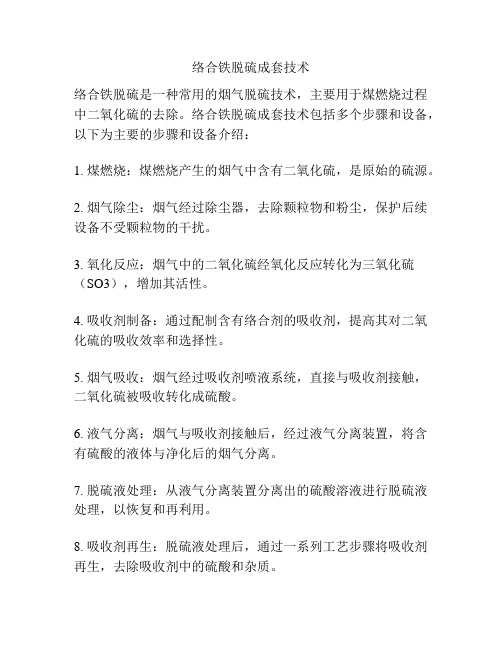
络合铁脱硫成套技术
络合铁脱硫是一种常用的烟气脱硫技术,主要用于煤燃烧过程中二氧化硫的去除。
络合铁脱硫成套技术包括多个步骤和设备,以下为主要的步骤和设备介绍:
1. 煤燃烧:煤燃烧产生的烟气中含有二氧化硫,是原始的硫源。
2. 烟气除尘:烟气经过除尘器,去除颗粒物和粉尘,保护后续设备不受颗粒物的干扰。
3. 氧化反应:烟气中的二氧化硫经氧化反应转化为三氧化硫(SO3),增加其活性。
4. 吸收剂制备:通过配制含有络合剂的吸收剂,提高其对二氧化硫的吸收效率和选择性。
5. 烟气吸收:烟气经过吸收剂喷液系统,直接与吸收剂接触,二氧化硫被吸收转化成硫酸。
6. 液气分离:烟气与吸收剂接触后,经过液气分离装置,将含有硫酸的液体与净化后的烟气分离。
7. 脱硫液处理:从液气分离装置分离出的硫酸溶液进行脱硫液处理,以恢复和再利用。
8. 吸收剂再生:脱硫液处理后,通过一系列工艺步骤将吸收剂再生,去除吸收剂中的硫酸和杂质。
9. 产生石膏:脱硫液处理后的硫酸溶液通过蒸发和结晶等工艺,产生固体硫酸盐(一般为石膏或石膏浆)。
10. 排放净化烟气:经过络合铁脱硫处理后的烟气,其中的二
氧化硫含量大大降低,符合环境排放标准。
这些步骤和设备组成了络合铁脱硫成套技术,可以高效地去除燃煤产生的二氧化硫,减少烟气对环境的污染。
络合铁脱硫法
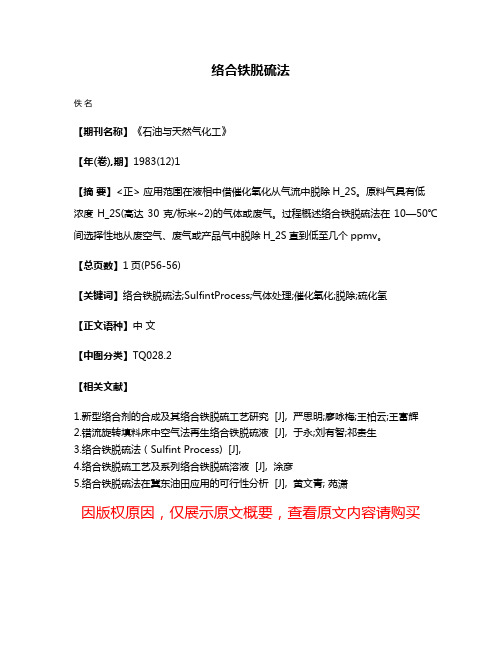
络合铁脱硫法
佚名
【期刊名称】《石油与天然气化工》
【年(卷),期】1983(12)1
【摘要】<正> 应用范围在液相中借催化氧化从气流中脱除H_2S。
原料气具有低浓度H_2S(高达30克/标米~2)的气体或废气。
过程概述络合铁脱硫法在10—50℃间选择性地从废空气、废气或产品气中脱除H_2S直到低至几个ppmv。
【总页数】1页(P56-56)
【关键词】络合铁脱硫法;SulfintProcess;气体处理;催化氧化;脱除;硫化氢
【正文语种】中文
【中图分类】TQ028.2
【相关文献】
1.新型络合剂的合成及其络合铁脱硫工艺研究 [J], 严思明;廖咏梅;王柏云;王富辉
2.错流旋转填料床中空气法再生络合铁脱硫液 [J], 于永;刘有智;祁贵生
3.络合铁脱硫法(Sulfint Process) [J],
4.络合铁脱硫工艺及系列络合铁脱硫溶液 [J], 涂彦
5.络合铁脱硫法在冀东油田应用的可行性分析 [J], 黄文青; 苑潇
因版权原因,仅展示原文概要,查看原文内容请购买。
络合铁法脱硫技术
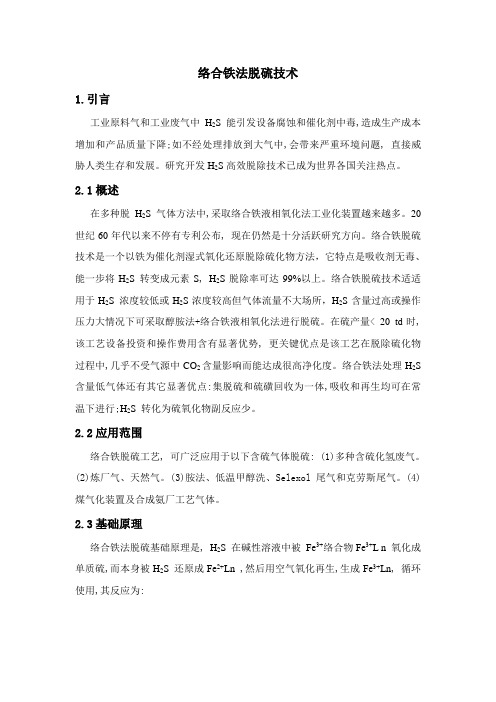
络合铁法脱硫技术1.引言工业原料气和工业废气中H2S能引发设备腐蚀和催化剂中毒,造成生产成本增加和产品质量下降;如不经处理排放到大气中,会带来严重环境问题, 直接威胁人类生存和发展。
研究开发H2S高效脱除技术已成为世界各国关注热点。
2.1概述在多种脱H2S气体方法中,采取络合铁液相氧化法工业化装置越来越多。
20世纪60年代以来不停有专利公布, 现在仍然是十分活跃研究方向。
络合铁脱硫技术是一个以铁为催化剂湿式氧化还原脱除硫化物方法,它特点是吸收剂无毒、能一步将H2S转变成元素S, H2S脱除率可达99%以上。
络合铁脱硫技术适适用于H2S浓度较低或H2S浓度较高但气体流量不大场所,H2S含量过高或操作压力大情况下可采取醇胺法+络合铁液相氧化法进行脱硫。
在硫产量< 20 td时,该工艺设备投资和操作费用含有显著优势, 更关键优点是该工艺在脱除硫化物过程中,几乎不受气源中CO2含量影响而能达成很高净化度。
络合铁法处理H2S 含量低气体还有其它显著优点:集脱硫和硫磺回收为一体,吸收和再生均可在常温下进行;H2S转化为硫氧化物副反应少。
2.2应用范围络合铁脱硫工艺, 可广泛应用于以下含硫气体脱硫: (1)多种含硫化氢废气。
(2)炼厂气、天然气。
(3)胺法、低温甲醇洗、Selexol 尾气和克劳斯尾气。
(4)煤气化装置及合成氨厂工艺气体。
2.3基础原理络合铁法脱硫基础原理是, H2S在碱性溶液中被Fe3+络合物Fe3+L n氧化成单质硫,而本身被H2S还原成Fe2+Ln ,然后用空气氧化再生,生成Fe3+Ln, 循环使用,其反应为:总反应是:依据络合铁法反应原理,因为配体存在, 不仅增加了铁离子溶解性,而且提升了铁离子稳定性。
2.4模拟试验步骤图模拟试验步骤见附图。
从配气罐来试验气体,在常温下进入吸收塔(1)和脱硫液逆流接触,脱除了硫化物净化气经冷却, 分离夹带脱硫液,分析气体组成后放空; 吸收了硫化物富液, 从吸收塔底部流出, 进入再生塔(6) , 和空气并流接触再生,将溶液中Fe2+转变成Fe3+, 再生液经离心机(7)分离硫磺后进入溶液贮槽( 8) ,由贫液泵( 4)加压打入吸收塔中循环吸收。
络合铁脱硫成套技术
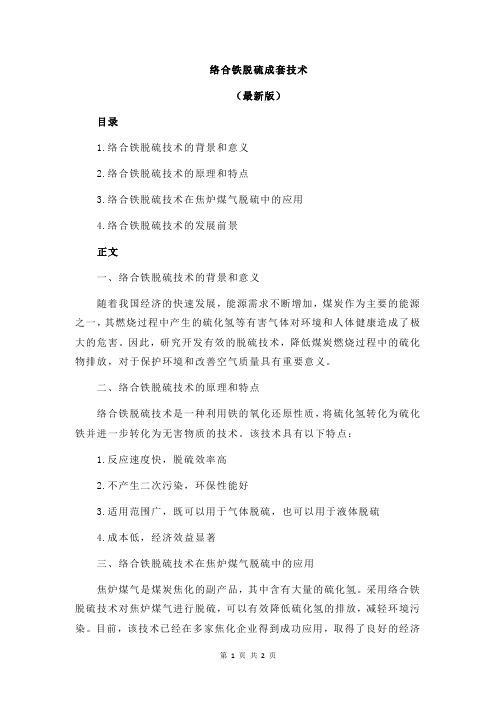
络合铁脱硫成套技术
(最新版)
目录
1.络合铁脱硫技术的背景和意义
2.络合铁脱硫技术的原理和特点
3.络合铁脱硫技术在焦炉煤气脱硫中的应用
4.络合铁脱硫技术的发展前景
正文
一、络合铁脱硫技术的背景和意义
随着我国经济的快速发展,能源需求不断增加,煤炭作为主要的能源之一,其燃烧过程中产生的硫化氢等有害气体对环境和人体健康造成了极大的危害。
因此,研究开发有效的脱硫技术,降低煤炭燃烧过程中的硫化物排放,对于保护环境和改善空气质量具有重要意义。
二、络合铁脱硫技术的原理和特点
络合铁脱硫技术是一种利用铁的氧化还原性质,将硫化氢转化为硫化铁并进一步转化为无害物质的技术。
该技术具有以下特点:
1.反应速度快,脱硫效率高
2.不产生二次污染,环保性能好
3.适用范围广,既可以用于气体脱硫,也可以用于液体脱硫
4.成本低,经济效益显著
三、络合铁脱硫技术在焦炉煤气脱硫中的应用
焦炉煤气是煤炭焦化的副产品,其中含有大量的硫化氢。
采用络合铁脱硫技术对焦炉煤气进行脱硫,可以有效降低硫化氢的排放,减轻环境污染。
目前,该技术已经在多家焦化企业得到成功应用,取得了良好的经济
效益和环保效果。
四、络合铁脱硫技术的发展前景
随着环保法规的日益严格,对于硫化物排放的控制将更加严格。
络合铁脱硫技术作为一种高效、环保、经济的脱硫技术,在未来的应用前景十分广阔。
一种络合铁脱硫及再生工艺方法

专利名称:一种络合铁脱硫及再生工艺方法专利类型:发明专利
发明人:周金国,葛洪强,孟现辉
申请号:CN202010749931.7
申请日:20200730
公开号:CN114053871A
公开日:
20220218
专利内容由知识产权出版社提供
摘要:本发明一种络合铁脱硫及再生工艺方法,包括含有硫化氢的燃气经燃气进口管进入到鼓泡吸收段,经过粗脱硫后的燃气向上进入到喷淋吸收段,经过一层喷淋和二层喷淋的吸收反应,燃气经过一层除雾器和二层除雾器对液滴的捕除,洁净的燃气穿过清洗喷淋经燃气出口管排出,脱硫液在脱硫及再生塔内由上至下经过二层喷淋和一层喷淋进入塔内在喷淋吸收段内吸收硫化氢,继续下行的脱硫液汇集到鼓泡吸收段内继续吸收硫化氢,反应完的脱硫液经下液管流入到水封箱内,最后流回到催化再生段。
申请人:唐山惠川环保科技有限公司
地址:063020 河北省唐山市高新技术开发区软件园四层
国籍:CN
更多信息请下载全文后查看。
络合铁法脱硫技术

络合铁法脱硫技术1.引言工业原料气和工业废气中的H2S能引起设备腐蚀和催化剂中毒,导致生产成本增加和产品质量下降;如不经处理排放到大气中,会带来严重的环境问题,直接威胁人类的生存与发展。
研究开发H2S的高效脱除技术已成为世界各国关注的热点。
2.1概述在各种脱H2S气体的方法中,采用络合铁液相氧化法的工业化装置越来越多。
20世纪60年代以来不断有专利发布,目前仍然是十分活跃的研究方向。
络合铁脱硫技术是一种以铁为催化剂的湿式氧化还原脱除硫化物的方法,它的特点是吸收剂无毒、能一步将H2S转变成元素S, H2S的脱除率可达99%以上。
络合铁脱硫技术适用于H2S浓度较低或H2S浓度较高但气体流量不大的场合,H2S含量过高或者操作压力大的情况下可采用醇胺法+络合铁液相氧化法进行脱硫。
在硫产量< 20 td时,该工艺的设备投资和操作费用具有明显优势,更重要的优点是该工艺在脱除硫化物过程中,几乎不受气源中CO2含量的影响而能达到非常高的净化度。
络合铁法处理H2S含量低的气体还有其它显著的优点:集脱硫与硫磺回收为一体,吸收与再生均可在常温下进行;H2S转化为硫氧化物的副反应少。
2.2应用范围络合铁脱硫工艺,可广泛应用于如下含硫气体的脱硫:(1)各种含硫化氢废气。
(2)炼厂气、天然气。
(3)胺法、低温甲醇洗、Selexol尾气和克劳斯尾气。
(4)煤气化装置及合成氨厂工艺气体。
2.3基本原理络合铁法脱硫的基本原理是,H2S在碱性溶液中被F£+的络合物Fe3+L n氧化成单质硫,而本身被H2S还原成Fe2+Ln ,然后用空气氧化再生,生成Fe3+Ln, 循环使用,其反应为:H:S+ 2 LZ 2 Fe2-L,t+扌乂斗2 H'2 F/T*十ll2O* 2 Fe3* U+ 2总反应是:厂 +図+ HjO i根据络合铁法的反应原理,由于配体的存在,不但增加了铁离子的溶解性,而且提高了铁离子的稳定性。
2.4模拟试验流程图模拟试验流程见附图。
络合铁脱硫技术介绍
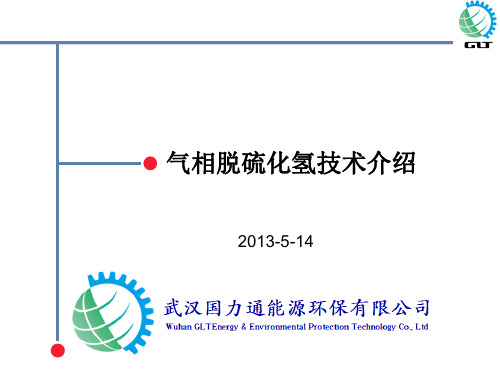
速更新的情况下与气体以极大的相对速度在弯 曲孔道中逆向接触,极大地强化了传质过程。
传质单元高度降低了1~3个数量级,使巨大的
塔器(二三十米以上的高度)降为高度只有 2~3米的超重力机。
13
被
超 重 力机
替代 的脱
硫 塔
14
超重力脱硫技术应用
15
-超重力气体脱硫技术应用
31
GLT超重力-络合铁脱硫技术优势
• 国力通开发的络合铁催化剂GLT-730 ,工作硫容量为国 内外同类产品的10到40倍,显著降低循环液量,设备尺 寸显著缩小,降低投资和操作成本;
• 采用超重力作为气液接触设备,动力消耗降低,延长催 化剂的使用寿命;
• GLT-730的选择性高达99%,而国内湿法脱硫催化剂的选 择性在82-85%,回收硫磺的纯度低,且大量生成了硫酸 盐,严重影响催化剂使用寿命;
(潜硫含量在80Kg/d-30t/d)
26
GLT-Process超重力-络合铁脱硫装置的化学原理
(a) 碱液吸收含硫原料气中的H2S到液相: KOH + H2S → KHS + H2O
(b) 铁离子与HS-离子反应生成单质硫: Fe3L + HS- → Fe2+L + S↓+ H+
(c) 再生中通入空气将Fe2+氧化成Fe3+,脱硫液再生: 4Fe2+L + O2 + 2 H2O → 4Fe3+L + 4OH-
• 炼油厂干气脱硫化氢; • 炼油一体化中合成气的脱硫化氢; • 循环加氢装置中氢气脱硫化氢; • 化肥厂/甲醇厂的水煤气和变换气脱硫化氢; • 油田伴生气脱硫化氢; • 海上石油平台的脱硫化氢; • 煤制化工和煤制油工艺中的脱硫等。 • 煤层气脱硫化氢; • 电厂烟道气脱硫; • 沼气、垃圾填埋场发酵气等生物气脱硫化氢。
络合铁脱硫的操作规程

络合铁脱硫岗位操作规程编制:李建昌审核:李佩斌第一章岗位目的和任务用络合铁法脱除胺法再生气中的硫化氢,脱除后的尾气达到环保排放要求并回收硫磺,同时脱除脱碳来再生气中硫化氢,二氧化碳再生气中H2S<10mg/m3。
第二章设备一览表第三章工艺流程说明工艺流程简述:从变换气脱硫系统来的再生气压力为0.07 Map,总量约7000(Nm3/h)被0.6Mpa络合铁脱硫液自吸进入喷射吸收塔上部,在喷射塔喷射器内气液两相混合,并不断的更新接触面积,气液两相进入喷射塔下部分离器,气相分离液滴后,进入填料塔下部填料,吸收了硫化氢的尾气经放空管排入大气。
来自脱碳系统的再生气压力为0.03 Mpa 气量为8000 Nm3/h,进入填料塔上部填料与络合铁脱硫液逆流接触后经除沫后进入再生分离器,分离液滴后进入老系统。
吸收了硫化氢的络合铁脱硫液进入填料下部,在下部填料继续吸收脱硫再生气中的硫化氢。
络合铁脱硫液富液自喷射塔,填料塔底部汇集进入富液槽,经富液泵打入喷射槽顶部的喷射器,与自吸进入喷射器的空气充分混合,经反应后进入再生槽,在再生槽内进一步氧化再生,再生后的贫液从再生槽上部溢流进入贫液槽,由贫液泵升压送入喷射吸收、填料塔循环吸收。
再生槽内析出的元素硫悬浮与再生槽顶部的环形塔内,并溢流进入硫泡沫槽,再由硫泡沫泵送入熔硫釜回收硫磺。
摘技术方案中。
第四章正常工艺指标1.流量入喷射塔再生气气量 Nm3/h(干基) 7000Nm3/h入喷射塔贫液流量~220m3/h入填料塔下塔贫液流量~220m3/h入填料塔上塔贫液流量~50m3/h2.温度℃入喷射塔再生气温度~40℃入喷射塔贫液温度~36℃入填料塔贫液温度~36℃入再生槽富液温度~36℃3.压力MPa入喷射塔再生气 0.03入喷射塔贫液 0.6入喷射再生器富液 0.64.液位喷射吸收塔 1/3~1/2填料塔 1/3~1/25.分析喷射塔进口H2S ~5 g/m3填料塔下塔出口H2S ~5mg/m3填料塔上塔出口H2S ~5mg/m3溶液碱度~35g/l溶液Fe浓度~1g/l络合剂浓度~12g/l第五章原始开车1 水、气、汽、联动试车:1.1 联动试车的目的:(1)、在单体试车的基础上,继续考核静置设备、动力设备和管道工程的安装质量。
络合铁脱硫工艺
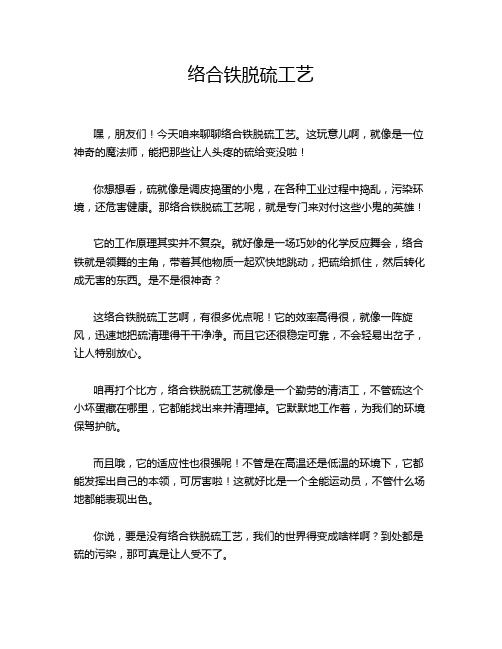
络合铁脱硫工艺
嘿,朋友们!今天咱来聊聊络合铁脱硫工艺。
这玩意儿啊,就像是一位神奇的魔法师,能把那些让人头疼的硫给变没啦!
你想想看,硫就像是调皮捣蛋的小鬼,在各种工业过程中捣乱,污染环境,还危害健康。
那络合铁脱硫工艺呢,就是专门来对付这些小鬼的英雄!
它的工作原理其实并不复杂。
就好像是一场巧妙的化学反应舞会,络合铁就是领舞的主角,带着其他物质一起欢快地跳动,把硫给抓住,然后转化成无害的东西。
是不是很神奇?
这络合铁脱硫工艺啊,有很多优点呢!它的效率高得很,就像一阵旋风,迅速地把硫清理得干干净净。
而且它还很稳定可靠,不会轻易出岔子,让人特别放心。
咱再打个比方,络合铁脱硫工艺就像是一个勤劳的清洁工,不管硫这个小坏蛋藏在哪里,它都能找出来并清理掉。
它默默地工作着,为我们的环境保驾护航。
而且哦,它的适应性也很强呢!不管是在高温还是低温的环境下,它都能发挥出自己的本领,可厉害啦!这就好比是一个全能运动员,不管什么场地都能表现出色。
你说,要是没有络合铁脱硫工艺,我们的世界得变成啥样啊?到处都是硫的污染,那可真是让人受不了。
在实际应用中,络合铁脱硫工艺已经在很多领域大显身手啦!化工厂、炼油厂等等,都能看到它的身影。
它就像一个无名英雄,默默地为我们的生活做出贡献。
咱可不能小瞧了这络合铁脱硫工艺啊,它可是解决硫污染问题的一把好手!它让我们的环境变得更美好,让我们能呼吸到更清新的空气。
所以说啊,络合铁脱硫工艺真的是太重要啦!我们应该好好感谢它,让它继续为我们的美好生活努力工作。
难道不是吗?大家一定要多多了解它,支持它呀!。
络合铁脱硫的操作规程

络合铁脱硫岗位操作规程编制:李建昌审核:李佩斌第一章岗位目的和任务用络合铁法脱除胺法再生气中的硫化氢,脱除后的尾气达到环保排放要求并回收硫磺,同时脱除脱碳来再生气中硫化氢,二氧化碳再生气中H2S<10mg/m3。
第二章设备一览表序号名称外形尺寸(mm) 温度℃工作压力(Mpa)容积(m3)介质产地1 贫液槽Φ6000L500040 常压141 络合铁液自制2 再生槽Φ6600*7100L692240 常压154 络合铁液自制3 熔硫釜Φ1000L3733170 0.66 1.87 硫泡沫永济4 富液槽Φ5000L550040 常压107.9 络合铁液自制5 吸收塔Φ2000L3400040 0.03 络合铁液自制6 喷射塔Φ2000*800L1475040 0.06 络合铁液自制7 泡沫槽Φ6000L500040 常压28.96 硫泡沫自制8 沉淀槽Φ6000*4L500040 常压70.4 络合铁液自制第三章工艺流程说明工艺流程简述:从变换气脱硫系统来的再生气压力为0.07 Map,总量约7000(Nm3/h)被0.6Mpa络合铁脱硫液自吸进入喷射吸收塔上部,在喷射塔喷射器内气液两相混合,并不断的更新接触面积,气液两相进入喷射塔下部分离器,气相分离液滴后,进入填料塔下部填料,吸收了硫化氢的尾气经放空管排入大气。
来自脱碳系统的再生气压力为0.03 Mpa 气量为8000 Nm3/h,进入填料塔上部填料和络合铁脱硫液逆流接触后经除沫后进入再生分离器,分离液滴后进入老系统。
吸收了硫化氢的络合铁脱硫液进入填料下部,在下部填料继续吸收脱硫再生气中的硫化氢。
络合铁脱硫液富液自喷射塔,填料塔底部汇集进入富液槽,经富液泵打入喷射槽顶部的喷射器,和自吸进入喷射器的空气充分混合,经反应后进入再生槽,在再生槽内进一步氧化再生,再生后的贫液从再生槽上部溢流进入贫液槽,由贫液泵升压送入喷射吸收、填料塔循环吸收。
再生槽内析出的元素硫悬浮和再生槽顶部的环形塔内,并溢流进入硫泡沫槽,再由硫泡沫泵送入熔硫釜回收硫磺。
络合铁脱硫成套技术

络合铁脱硫成套技术
(实用版)
目录
1.络合铁脱硫技术的概念与原理
2.络合铁脱硫技术的发展历程
3.络合铁脱硫技术的优势与应用场景
4.络合铁脱硫技术在焦炉煤气脱硫中的应用案例
5.络合铁脱硫技术的未来发展趋势
正文
一、络合铁脱硫技术的概念与原理
络合铁脱硫技术是一种利用铁的络合能力,将硫化氢转化为硫化铁并进一步转化为无害物质的技术。
该技术通过添加特定配方的络合铁剂,使硫化氢与铁离子发生反应,生成硫化铁沉淀,从而达到脱硫的目的。
二、络合铁脱硫技术的发展历程
络合铁脱硫技术起源于 20 世纪 70 年代,经过几十年的发展,已经成为一种成熟且广泛应用的脱硫技术。
我国在 20 世纪 80 年代开始研究络合铁脱硫技术,并逐步在各个行业推广应用。
三、络合铁脱硫技术的优势与应用场景
络合铁脱硫技术具有操作简便、脱硫效率高、投资成本低、对设备无腐蚀、无二次污染等优点。
因此,该技术广泛应用于焦炉煤气、燃煤锅炉、石油化工、钢铁冶金等领域的脱硫治理。
四、络合铁脱硫技术在焦炉煤气脱硫中的应用案例
在焦炉煤气脱硫领域,络合铁脱硫技术得到了广泛应用。
例如,山西省化学工业协会在太原组织召开的“GLT 络合铁脱硫化氢技术及其在焦炉
煤气脱硫中多场景应用交流会”,参会的 25 家单位共同探讨了络合铁脱硫技术在焦炉煤气脱硫中的实际应用和效果。
五、络合铁脱硫技术的未来发展趋势
随着环保法规的日益严格,对于硫化物排放的控制将更加严格。
因此,络合铁脱硫技术在未来将面临更广阔的市场需求和发展空间。
天然气络合铁脱硫化氢工艺介绍
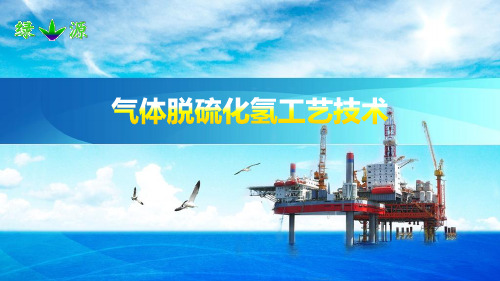
络合铁脱硫技术优势
硫磺回收技术是适合于潜硫含量小于35吨/天的现场。 H2S脱除装置的最佳工艺,最主要体现在投资和运行费用,催化剂可再生。 将H2S直接转化成元素硫,无反应平衡限制,转化率99.99%,处理
后H2S浓度小于10ppm。 水相介质,条件温和,在常压、常温下即可满足反应条件。 可用来处理任何一种含H2S的气体(包括酸性工艺气、酸性尾气、Claus尾
装置设计及操作 稳定性
投资
络合铁法 管式反应器+高效吸收 塔
1.33-3.31
99%
脱除率大于90%
2170 设计简单、注
鼓泡塔、自循环反 应器
0.2-0.37
吸收设备传质效率高,设备尺寸 和重量更小
络合铁脱硫装置可橇装化,循环 液量低,操作费用低
92%
脱硫剂硫磺回收率更高
在吸收区,溶解的H2S电离为HS-,与Fe3+反应;HS-被氧化为单质S ,与此同时, Fe3+被还原为Fe2+ ;鼓入空气将Fe2+氧化为Fe3+ ,溶液 循环利用。
9
络合铁工艺介绍
MDEA尾气 炼油厂尾气 Claus尾气
沼气 煤制气 油田伴生气
H2S含量 0~100% 0.1~35t/d
络合铁处理 99.99%的脱除率
(3)硫氢根被铁离子氧化生成硫单质
HS 2Fe3 2Fe2 H S
再生部分总反应方程式:
H2S (g) 2Fe3 2Fe2 2H S
(1)O2在配比溶液中被吸收(1:0.049,20℃)
1 2
O2 (g)
H 2O(l)
1 2
O2 (l)
新型络合铁脱硫剂

新型络合铁脱硫剂
新型络合铁脱硫剂是一种高效的燃煤脱硫剂,可以有效地降低烟气中的二氧化硫排放量,对环保具有重要意义。
它采用了新型的配方和生产工艺,通过化学反应将二氧化硫转化为硫酸和硫酸盐,并在反应中释放出大量的热能,实现了同时脱硫和节能的目的。
络合铁脱硫剂的作用原理是利用络合剂将铁离子与硫化物离子
配位结合,形成络合物,从而达到脱除烟气中的二氧化硫的目的。
与传统的脱硫剂相比,它具有脱硫效率高、反应速度快、用量少、不易出现结垢等优点,同时还能够减少烟气中的氮氧化物排放。
由于新型络合铁脱硫剂的研发,使得煤炭等高硫燃料的利用变得更加环保,同时也为燃煤电厂等企业带来了显著的经济效益。
未来,随着环保意识的不断提高,新型络合铁脱硫剂必将得到更加广泛的应用。
- 1 -。
络合铁脱硫的工艺流程
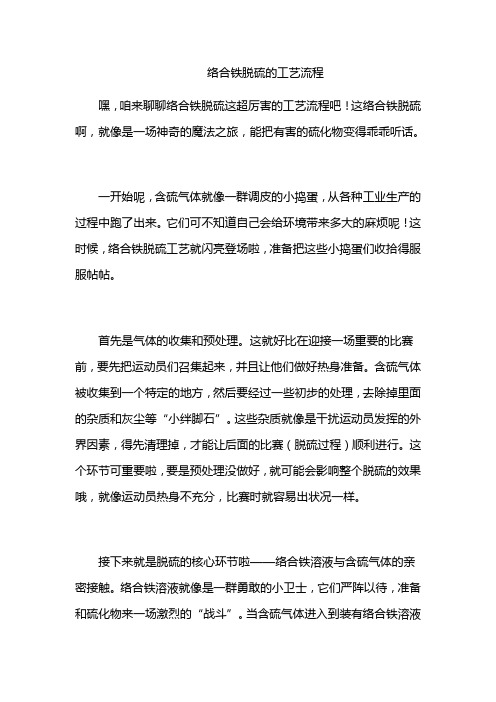
络合铁脱硫的工艺流程嘿,咱来聊聊络合铁脱硫这超厉害的工艺流程吧!这络合铁脱硫啊,就像是一场神奇的魔法之旅,能把有害的硫化物变得乖乖听话。
一开始呢,含硫气体就像一群调皮的小捣蛋,从各种工业生产的过程中跑了出来。
它们可不知道自己会给环境带来多大的麻烦呢!这时候,络合铁脱硫工艺就闪亮登场啦,准备把这些小捣蛋们收拾得服服帖帖。
首先是气体的收集和预处理。
这就好比在迎接一场重要的比赛前,要先把运动员们召集起来,并且让他们做好热身准备。
含硫气体被收集到一个特定的地方,然后要经过一些初步的处理,去除掉里面的杂质和灰尘等“小绊脚石”。
这些杂质就像是干扰运动员发挥的外界因素,得先清理掉,才能让后面的比赛(脱硫过程)顺利进行。
这个环节可重要啦,要是预处理没做好,就可能会影响整个脱硫的效果哦,就像运动员热身不充分,比赛时就容易出状况一样。
接下来就是脱硫的核心环节啦——络合铁溶液与含硫气体的亲密接触。
络合铁溶液就像是一群勇敢的小卫士,它们严阵以待,准备和硫化物来一场激烈的“战斗”。
当含硫气体进入到装有络合铁溶液的容器中时,就像是闯入了一个神奇的魔法世界。
在这里,硫化物会和络合铁发生一系列奇妙的化学反应。
硫化物就像是遇到了克星一样,被络合铁紧紧地“抓住”,然后慢慢地转化成其他无害的物质。
这个过程就像是一场精彩的魔术表演,让人惊叹不已。
你看,科学的力量就是这么神奇,能把有害的东西变得无害,是不是很厉害呢?在这个过程中,还有一个关键的角色,那就是催化剂。
催化剂就像是这场魔法之旅的催化剂(哈哈,名字很贴切吧),它能加快反应的速度,让脱硫的效率大大提高。
就好比给运动员吃了一颗能量豆,让他们跑得更快、更有力。
没有催化剂的帮忙,脱硫的过程可能就会变得慢吞吞的,影响整个生产的进度。
所以,催化剂在络合铁脱硫工艺中可是起着不可或缺的作用哦。
随着反应的进行,被“抓住”的硫化物不断地被转化,络合铁溶液也会慢慢发生变化。
这时候,就需要对络合铁溶液进行再生处理啦。
络合铁法脱硫工艺
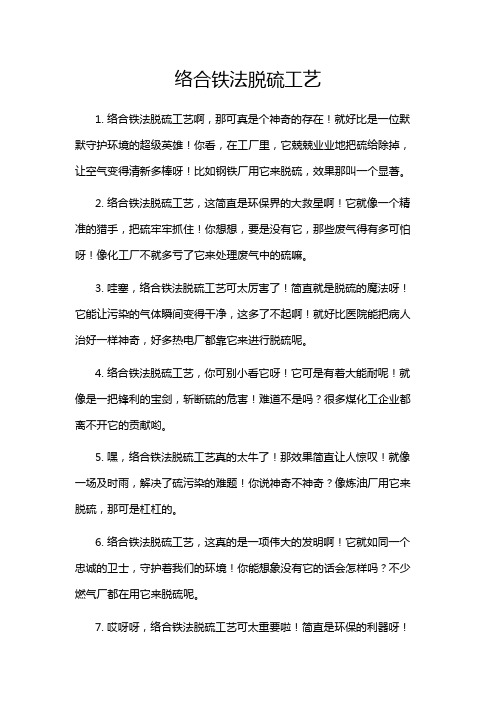
络合铁法脱硫工艺1. 络合铁法脱硫工艺啊,那可真是个神奇的存在!就好比是一位默默守护环境的超级英雄!你看,在工厂里,它兢兢业业地把硫给除掉,让空气变得清新多棒呀!比如钢铁厂用它来脱硫,效果那叫一个显著。
2. 络合铁法脱硫工艺,这简直是环保界的大救星啊!它就像一个精准的猎手,把硫牢牢抓住!你想想,要是没有它,那些废气得有多可怕呀!像化工厂不就多亏了它来处理废气中的硫嘛。
3. 哇塞,络合铁法脱硫工艺可太厉害了!简直就是脱硫的魔法呀!它能让污染的气体瞬间变得干净,这多了不起啊!就好比医院能把病人治好一样神奇,好多热电厂都靠它来进行脱硫呢。
4. 络合铁法脱硫工艺,你可别小看它呀!它可是有着大能耐呢!就像是一把锋利的宝剑,斩断硫的危害!难道不是吗?很多煤化工企业都离不开它的贡献哟。
5. 嘿,络合铁法脱硫工艺真的太牛了!那效果简直让人惊叹!就像一场及时雨,解决了硫污染的难题!你说神奇不神奇?像炼油厂用它来脱硫,那可是杠杠的。
6. 络合铁法脱硫工艺,这真的是一项伟大的发明啊!它就如同一个忠诚的卫士,守护着我们的环境!你能想象没有它的话会怎样吗?不少燃气厂都在用它来脱硫呢。
7. 哎呀呀,络合铁法脱硫工艺可太重要啦!简直是环保的利器呀!它能把硫处理得干干净净,这多厉害呀!就好像一个优秀的清洁工,好多水泥厂都靠它来让排放达标呢。
8. 络合铁法脱硫工艺,这绝对是个宝贝呀!它能够神奇地搞定脱硫的任务!这难道不值得我们好好夸赞吗?像焦化厂就深切体会到了它的好。
9. 哇哦,络合铁法脱硫工艺,真的是太让人佩服啦!就像是一个魔法咒语,让硫乖乖消失!你不觉得很神奇吗?许多冶金企业都在依赖它来进行脱硫工作呢。
10. 络合铁法脱硫工艺,这可是环保的大功臣啊!它把硫的问题轻松解决,这是多么伟大的事情呀!不就像一个勇敢的战士打了胜仗嘛!比如火力发电厂就得益于它的强大功效。
络合铁脱硫技术工艺方案

延长石油合成尾气脱硫系统(湿法络合铁脱硫技术)技术文件1概述1.1项目目标本设计方案由唐山绿源环保采用络合铁脱硫技术应用于500kg/d脱硫橇装项目,净化后的H2S降至20ppm以下,并实现每天回收高品质硫磺500kg,在节约投资的前提下达到满足车载橇装需求,便于汽车运输,尾气硫化氢指标合格的目的。
2络合铁脱硫技术介绍2.1络合铁脱硫技术简介络合铁法脱硫技术是一种以络合铁为催化剂的湿式氧化脱除硫化氢的方法,其特点是直接将H2S转变成元素S,吸收H2S以后的含量小于20ppm,一般在5ppm以下,是一种工艺简单、工作硫容高且环保无毒的新型脱硫技术,克服了传统脱硫工艺硫容量低、脱硫工艺复杂、副盐生成率高、环境污染严重等弊端,硫磺回收装置尾气可使硫磺回收率达到99.99%。
络合铁脱硫技术是具有自主知识产权的络合铁脱硫化氢成套技术,相对于其它络合铁脱硫技术,具有硫容量高、可橇装化、脱硫成本低、节能、运行稳定性高、投资低、对COS、硫醇有机硫脱除率高等优点。
2.2络合铁法脱硫技术的工艺原理唐山绿源环保络合铁法脱硫技术是一种以络合铁为催化剂的湿式氧化脱除硫化氢的方法,其特点是直接将气体中的H2S转变成元素S,吸收后气体中H2S的含量小于20ppm,是一种工艺简单、工作硫容高且环保无毒的新型脱硫技术,克服了传统脱硫工艺硫容量低、脱硫工艺复杂、副盐生成率高、环境污染严重等弊端,硫磺回收率达到99.99%,净化后的尾气焚烧后烟气二氧化硫含量降低到20mg/Nm3,可满足不断提升的环保指标。
络合铁脱硫工艺为脱除硫化氢提供了一种恒温、低成本的运行方法。
其化学反应原理是利用空气中的氧气氧化气相中的硫化氢,使硫化氢被氧化为单质硫。
其化学反应方程式如式(1):H2S+1/2O2→H2O+S(1)络合铁脱硫催化剂利用水溶液中络合铁离子的氧化还原性,使含硫化氢气体与含络合铁催化剂的水溶液(简称络合铁吸收剂,下同)进行气液相接触反应。
络合铁法脱硫技术

络合铁法脱硫技术1.引言工业原料气和工业废气中的H2S能引起设备腐蚀和催化剂中毒,导致生产成本增加和产品质量下降;如不经处理排放到大气中,会带来严重的环境问题, 直接威胁人类的生存与发展。
研究开发H2S的高效脱除技术已成为世界各国关注的热点。
2.1概述在各种脱H2S气体的方法中,采用络合铁液相氧化法的工业化装置越来越多。
20世纪60年代以来不断有专利发布, 目前仍然是十分活跃的研究方向。
络合铁脱硫技术是一种以铁为催化剂的湿式氧化还原脱除硫化物的方法,它的特点是吸收剂无毒、能一步将H2S转变成元素S, H2S的脱除率可达99%以上。
络合铁脱硫技术适用于H2S浓度较低或H2S浓度较高但气体流量不大的场合,H2S含量过高或者操作压力大的情况下可采用醇胺法+络合铁液相氧化法进行脱硫。
在硫产量< 20 td时,该工艺的设备投资和操作费用具有明显优势, 更重要的优点是该工艺在脱除硫化物过程中,几乎不受气源中CO2含量的影响而能达到非常高的净化度。
络合铁法处理H2S含量低的气体还有其它显著的优点:集脱硫与硫磺回收为一体,吸收与再生均可在常温下进行;H2S转化为硫氧化物的副反应少。
2.2应用范围络合铁脱硫工艺, 可广泛应用于如下含硫气体的脱硫: (1)各种含硫化氢废气。
(2)炼厂气、天然气。
(3)胺法、低温甲醇洗、Selexol 尾气和克劳斯尾气。
(4)煤气化装置及合成氨厂工艺气体。
2.3基本原理络合铁法脱硫的基本原理是, H2S在碱性溶液中被Fe3+的络合物Fe3+L n氧化成单质硫,而本身被H2S还原成Fe2+Ln ,然后用空气氧化再生,生成Fe3+Ln, 循环使用,其反应为:总反应是:根据络合铁法的反应原理,由于配体的存在, 不但增加了铁离子的溶解性,而且提高了铁离子的稳定性。
2.4模拟试验流程图模拟试验流程见附图。
从配气罐来的试验气体,在常温下进入吸收塔(1)与脱硫液逆流接触,脱除了硫化物的净化气经冷却, 分离夹带的脱硫液,分析气体组成后放空; 吸收了硫化物的富液, 从吸收塔底部流出, 进入再生塔(6) , 与空气并流接触再生,将溶液中的Fe2+转变成Fe3+, 再生液经离心机(7)分离硫磺后进入溶液贮槽( 8) ,由贫液泵( 4)加压打入吸收塔中循环吸收。
- 1、下载文档前请自行甄别文档内容的完整性,平台不提供额外的编辑、内容补充、找答案等附加服务。
- 2、"仅部分预览"的文档,不可在线预览部分如存在完整性等问题,可反馈申请退款(可完整预览的文档不适用该条件!)。
- 3、如文档侵犯您的权益,请联系客服反馈,我们会尽快为您处理(人工客服工作时间:9:00-18:30)。
延长石油合成尾气脱硫系统(湿法络合铁脱硫技术)技术文件1概述1.1项目目标本设计方案由唐山绿源环保采用络合铁脱硫技术应用于500kg/d脱硫橇装项目,净化后的H2S降至20ppm以下,并实现每天回收高品质硫磺500kg,在节约投资的前提下达到满足车载橇装需求,便于汽车运输,尾气硫化氢指标合格的目的。
2络合铁脱硫技术介绍2.1络合铁脱硫技术简介络合铁法脱硫技术是一种以络合铁为催化剂的湿式氧化脱除硫化氢的方法,其特点是直接将H2S转变成元素S,吸收H2S以后的含量小于20ppm,一般在5ppm以下,是一种工艺简单、工作硫容高且环保无毒的新型脱硫技术,克服了传统脱硫工艺硫容量低、脱硫工艺复杂、副盐生成率高、环境污染严重等弊端,硫磺回收装置尾气可使硫磺回收率达到99.99%。
络合铁脱硫技术是具有自主知识产权的络合铁脱硫化氢成套技术,相对于其它络合铁脱硫技术,具有硫容量高、可橇装化、脱硫成本低、节能、运行稳定性高、投资低、对COS、硫醇有机硫脱除率高等优点。
2.2络合铁法脱硫技术的工艺原理唐山绿源环保络合铁法脱硫技术是一种以络合铁为催化剂的湿式氧化脱除硫化氢的方法,其特点是直接将气体中的H2S转变成元素S,吸收后气体中H2S的含量小于20ppm,是一种工艺简单、工作硫容高且环保无毒的新型脱硫技术,克服了传统脱硫工艺硫容量低、脱硫工艺复杂、副盐生成率高、环境污染严重等弊端,硫磺回收率达到99.99%,净化后的尾气焚烧后烟气二氧化硫含量降低到20mg/Nm3,可满足不断提升的环保指标。
络合铁脱硫工艺为脱除硫化氢提供了一种恒温、低成本的运行方法。
其化学反应原理是利用空气中的氧气氧化气相中的硫化氢,使硫化氢被氧化为单质硫。
其化学反应方程式如式(1):H2S+1/2O2→H2O+S(1)络合铁脱硫催化剂利用水溶液中络合铁离子的氧化还原性,使含硫化氢气体与含络合铁催化剂的水溶液(简称络合铁吸收剂,下同)进行气液相接触反应。
该气液相接触反应首先通过水溶液的偏碱性,在气液接触时通过酸碱化学吸收将原料气中的硫化氢吸收进入水溶液;在水溶液中,利用高价络合铁离子的氧化性将硫化氢氧化成单质硫,络合铁离子被还原为低价络合亚铁离子。
络合铁离子水溶液的吸收氧化反应方程式(2)~(5)如下:水溶液吸收H2S气体:H2S(g)+H2O(L)(H2S(L)+H2O(L)(2)式中:(g)——气相,下同;(L)——液相,下同H2S电离:H2S(L)(H+(L)+HS-(L)(3)高铁离子(Fe3+)氧化二价硫:HS-(L)+2Fe3+(L)→2Fe2+(L)+H+(L)+S↓(4)吸收氧化总反应方程式(即方程式(2),(3),(4)叠加)H2S(g)+2Fe3+(L)→2H+(L)+S↓+2Fe2+(L)(5)水溶液中络合亚铁离子容易被氧气氧化,因此,将络合亚铁离子溶液直接与空气进行气液相接触反应,利用空气中的氧气将水溶液中的络合亚铁离子氧化为络合铁离子。
络合亚铁离子水溶液的再生还原反应方程式(6)~(8)如下:络合亚铁离子水溶液吸收氧气:1/2O2(g)+H2O(L)→1/2O2(L)+H2O(L)(6)络合亚铁离子(Fe2+)再生反应:1/2O2(L)+H2O(L)+2Fe2+(L)→2OH-(L)+2Fe3+(L)(7)再生还原总反应方程式(即方程式(6),(7)叠加)1/2O2(g)+H2O(L)+2Fe2+(L)→2OH-(L)+2Fe3+(L)(8)在总反应中,络合铁离子的作用是将吸收反应中产生的电子释放到再生反应中去,由于每一个单质硫的产生需要消耗两个铁原子,所以在反应过程中,至少提供两个铁原子。
由此,铁离子是作为反应物。
不过,在总反应中并不消耗铁离子,铁离子是作为硫化氢和氧气反应的催化剂。
由于这种双重功能,铁离子络合物一般被定义为催化剂。
在络合铁脱硫工艺中,循环水溶液的pH值是一个非常重要的可变操作因素,因为水溶液可吸收H2S气体的总量完全取决于水溶液的pH值(反应方程式(2)、(3))。
pH值是衡量水溶液酸碱度的一种方式,pH值为7代表水溶液是中性的,就是说既不呈酸性也不呈碱性;pH值在1~7代表水溶液是酸性的;pH值7~14代表水溶液是碱性的。
反应方程式(2)和(3)的双向箭头表明反应处于平衡稳定状态,如果增加H+离子的浓度,反应将向左边进行,H2S能被水溶液吸收的总量减少。
如果增加OH-离子的浓度,溶液中的H+将被中和形成水(OH-+H+→H2O),因此反应将向右边进行,H2S能被水溶液吸收的总量增加。
反应方程式(1)表明反应没有H+离子和OH-离子的净产物生成,所以水溶液的pH 值不会产生变化。
但是,副反应会释放H+离子,使得水溶液的pH值降低,最终导致水溶液吸收H2S总量减少。
其中的一个副反应如反应方程式(9)所示,反应产生的硫代硫酸根(S2O32-)对脱硫工艺有益,它使得之前提到的螯合剂变得更加稳定,同时降低螯合剂的分解。
2HS-(L)+2O2(L)→S2O32-(L)+H2O(L)(9)当该反应与电离反应(方程式(3))相结合时,可以看出,随着硫代硫酸根(S2O32-)产生,H+离子生成净产物,使得水溶液的pH值降低。
由于处理的气相中含有二氧化碳(CO2),尤其是在压力较高时,二氧化碳极易溶于水,会形成碳酸氢盐(HCO3-)和碳酸盐(CO32-),随之发生副反应降低水溶液的pH值。
反应方程式如(10)~(12):CO2(g)+H2O(L)→H2CO3(L)(10)H2CO3(L)→H+(L)+HCO3-(L)(11)HCO3-(L)→CO32-(L)+H+(L)(12)为了稳定水溶液的pH值,需要在系统中加入氢氧化钾,它与二氧化碳的反应如式(13)~(15):CO2(g)+H2O(L)→H2CO3(L)(13)H2CO3(L)+2KOH(L)→K2CO3(L)+2H2O(L)(14)K2CO3(L)+H2CO3(L)→2KHCO3(L)(15)通常,较高的pH值能够提高反应效能,会促进硫代硫酸盐离子的形成,减少氧气的吸收,但也阻碍单质硫的凝聚;而过低的pH值会阻碍H2S气体的吸收。
所以,控制pH值为8.0-9.0的弱碱性水溶液。
系统采用碱性络合铁催化剂的氧化还原性质,吸收酸性气中的H2S。
H2S被络合铁直接氧化生成单质硫,络合铁转化为络合亚铁,然后在再生沉降槽鼓入空气,以空气氧化碱性吸收剂中的络合亚铁,使吸收剂中的络合亚铁转化为络合铁,再生回用。
同时,在再生沉降槽对硫磺进行沉降分离形成硫磺浆,将硫磺浆送至过滤机中脱水成硫磺饼。
该法的特点是采用高硫容量的络合铁催化剂,不仅适用于高含硫的原料气处理,而且循环液量小,装置尺寸小,并可直接生成单质硫,不存在二次污染问题。
2.3络合铁法脱硫技术的特点(1)络合铁催化剂,工艺处理过程简单,采用一步法处理工艺即可快速将硫化氢直接氧化为硫单质;对各种不同浓度的H2S,其脱硫后的H2S含量可低于20ppm,清除H2S效率高。
(2)系统的抗波动能力强。
对于传统的脱硫装置,原料气中硫化氢含量波动较大时,会造成出口净化气的硫化氢含量波动很大,甚至超标。
络合铁高硫容特性,其脱硫装置完全能自动处理以上波动情况,并不需要人为改变操作且不会影响脱硫率。
(3)运行成本低。
由于在脱硫过程中所使用的各种药剂中的络合铁催化剂可再生循环使用且无副反应发生,只需补充少量的在脱硫过程中损失的络合铁催化剂,产出一吨硫磺运行成本800元。
(4)络合铁催化剂选择性高,副盐产生量低。
在络合铁脱硫中,络合铁离子氧化硫化氢为硫磺,脱硫过程副反应少,药剂使用寿命长。
(5)脱硫工作液硫容量高。
最新开发的络合铁脱硫剂,脱硫剂循环液的硫容量不受二氧化碳的影响,其工作硫容量高达3.3kg硫磺/m3药剂,高于国外同类技术(工作硫容量较好的为0.37kg硫磺/m3药剂)。
故使用络合铁脱硫剂能显著降低循环液量,降低设备尺寸,减少投资和操作成本。
(6)能脱除有机硫COS、硫醇。
(7)设备尺寸小,可有效实现橇装化。
由于工作硫容量高,设备小,可有效实现橇装化,非常适合小项目的橇装化要求。
(8)催化剂的安全性高,系统所采用的催化剂对环境及人体无毒无害,具有良好的环保效益。
(9)已成熟应用于工业化。
目前络合铁脱硫技术在中海油流花油田项目中使用良好。
3设计基础3.1原料气流量及组成原料气:含硫化氢尾气压力:1-2KPa温度:165℃工况流量:200m3/h操作负荷:50%-120%硫化氢含量:98%操作状态:连续3.2装置技术要求(1)净化度要求,要求将原料气中硫化氢脱除至低于20ppm(2)实现装置橇装化,实现车载橇装需求,便于汽车运输。
3.6工艺方案3.6.1工艺流程说明络合铁脱硫系统具体流程。
从界区外来的含硫化氢气体进入换热器对气体进行降温处理随后由增压风机将压力提升至30KPa,尾气由下至上经一级反应器与贫液泵打来的贫液逆向接触,预脱硫后再经二级反应器脱除剩余硫化氢,分离液滴后的气体从二级反应器上部出装置。
两级反应器底部溶液中的三价铁吸收尾气中硫化氢变成二价铁,溶液变成含硫富液自压进入再生槽,与氧化风机鼓入的空气进行氧化。
富液中的二价铁经再生风机鼓入的氧气氧化后变成三价铁的贫液,同时,再生槽中的单质硫经各个隔室逐层长大后和贫液一起经浆液输送泵输送到沉降槽,硫磺颗粒因为重量沉积到沉降槽锥体底部,上层分离了硫磺的贫液经贫液泵输送到两级反应器喷淋进行脱硫。
底部硫磺浆经硫磺浆泵一路送到沉降槽底部进行循环扰动,防止堵塞,当硫磺含量达到15%左右后,另一路打开进入熔硫釜进行硫磺收集,液体回收至系统,硫膏可进行销售。
3.6.2设备选型、安装及布置要求3.6.2.1设备及材质选型说明设备选型原则:满足车载橇装需求,便于汽车运输。
材质要求:在络合铁脱硫工艺设计中,由于络合铁吸收剂具有腐蚀性,凡是与络合铁吸收剂接触的设备、管道必须采用不锈钢。
反应塔:采用前喷淋塔+鼓泡塔形式,反应塔采用双塔串联设计。
再生以及沉降槽:为了保证氧化效果,将再生沉降槽分隔为若干个隔室,络合铁吸收剂富液经折流通过各个隔室以实现梯级氧化,达到最佳的再生效果;因为高度限制,再生槽及沉降槽分开设置,沉降槽采用双体联通双锥体槽设计,沉降槽底部设置夹角的锥体,有利于硫磺沉降并防止堵塞;硫磺浆泵循环管线通入沉降槽锥底部防止硫磺沉积防止堵塞。
泵的选型原则:由于循环液中含有固体硫磺颗粒,因此离心泵的形式选择开式离心泵。
过滤设备:本方案根据硫磺量少以及占地位置小的特点采用熔硫釜分离过滤硫磺浆液。
3.6.2.2设备安装本装置安装的主要非标工艺设备有反应器、再生槽、沉降槽等设备,主要定型工艺设备有泵、风机等设备。
硫磺浆泵布置在沉降槽锥形底封头的正下方;硫磺过滤设备也尽量紧凑布置在一个区域,所有布置以方便操作和减少占地的原则进行;硫磺浆液的管道应尽量减少管道长度和弯头数量,以防止堵塞。