第五章 胀形与翻边
胀形+翻边+复合成形

6.1.4 胀形在两向拉应力作用下实现的变形,可以成形各种空间曲面的形状。
1)胀形变形特点 (1)胀形变形过程如图6-16,凸模与毛坯接触,凹模圆角处坯料发生弯曲。
同时,凸模底部毛坯产生胀形变形。
坯料屈服后硬化,变形向外扩展。
随后,材料全部进入塑性变形。
胀形变形是弯曲、局部胀形以及由于加工硬化,贴模面积增加,胀形向外扩展的过程。
(2)主要变形区如图6-16所示,在胀形变形过程中,毛坯被带有凸筋的压边圈压紧,变形区被限制在凸筋以内的局部区域内。
与拉深不同,胀形时,变形区是在不断扩大的。
(3)变形区应力、应变状态 如图6-17所示,在变形区内,坯料在双向拉应力作用下,沿切向和径向产生伸长变形,厚度变薄,表面积增大。
生产中的起伏成形、压凸包、压筋、圆柱形空心毛坯的鼓肚成形、波纹管及平板毛坯的张拉成形等都属于胀形成形。
(4)胀形力-行程曲线 与拉深不同,胀形时变形区是在不断扩大的。
因此,胀形变形的力-行程曲线是单调增曲线,产生破裂时,胀形力达到最大值。
胀形破裂也属于强度破裂。
(5)胀形变形规律如图6-15所示,在无凸筋强制压边的条件下,坯料也会产生胀形变形。
此时,胀形变形的性质和胀形在整个工序中所占的比例与毛坯尺寸有关。
当毛坯的外径足够大、内径较小时,拉深与内孔翻边变形阻力大于胀形变形阻力,变形的性质由胀形来决定。
如图6-18所示,当相对法兰直径比d f /d 大于等于2.5时,法兰处进行拉深变形的阻力大于底部胀形变形所需的力,工序性质属于胀形。
与拉深加工相同,除了毛坯几何尺寸外,压边力大小、润滑和摩擦条件、模具的形状与几何尺寸等因素也会在不同程度上影响到工序的变形性质。
2)主要工艺参数胀形工序种类繁多,表示胀形变形程度的参数也不相同。
在生产中,常用工程应变: ε=(l-l 0)*100%/ l 0 (压筋:l 0—原始长度,l —变形后弧长)、 胀形深度:h(压凸包)胀形系数:K=d max /d(圆柱空心件胀形,d max —胀形后最大直径,d —圆筒毛坯直径)等参数来表图6-16 胀形变形过程 图6-17 胀形变形区应力、应变状态 图6-15 拉深变形规律示胀形变形程度。
第5章胀形翻边缩口成型及工艺
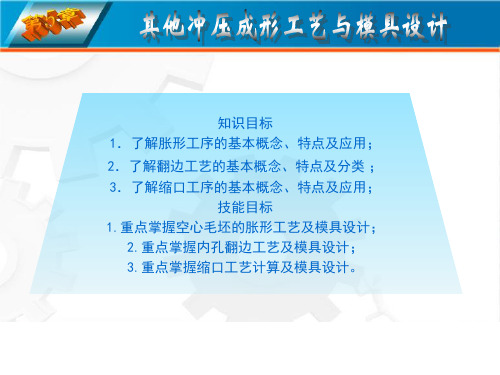
胀形工艺与模具设计
底部起伏 成形计算
侧壁胀形 计算
总胀形力
5.1
5.1.4 胀形模设计实例
胀形工艺与模具设计
1—下模座; 2、11—螺钉; 3—压凹坑凸模; 4—压凹坑凹模; 5—胀形下模; 6—胀形上模; 7—聚氨酯橡胶; 8—拉杆; 9—上固定板; 10—上模; 12—模柄; 13—弹簧; 14—拉杆螺栓; 15—导柱; 16—导套 胀形模模具装配图
不同材料和厚度的平均缩口系数
m0
5.3
缩口成形工艺与模具设计
5.3.1 缩口成形特点与变形程度
不同模具结构的极限缩口系数
mmin
5.3
5.3.2 缩口工艺计算
缩口成形工艺与模具设计
缩口次数的计算公式:
m为缩口系数 m0为平均缩口系数
5.3
5.3.2 缩口工艺计算
缩口成形工艺与模具设计
斜口形式毛坯高度 :
胀形工艺与模具设计
d max k d0
极限胀形系数 Kmax 与工件切向伸长率 A 的关系为:
或
5.1
5.1.3 空心毛坯胀形
胀形工艺与模具设计
2)软模胀形力
1)刚性凸模胀形力
3)胀形毛坯尺寸
毛坯长度 L0:
5.1
5.1.4 胀形模设计实例
胀形工艺与模具设计
胀形零件
5.1
5.1.4 胀形模设计实例
修边余量
拉深的工艺性
基
本
概
念
变薄拉深
变薄拉深主要是在拉深过程中改变拉深件筒壁厚度,而毛坯的直 径变化很小的拉深方法 。
5.1
5.1.1 胀形的变形特点
胀形工艺与模具设计
5.1
5.1.2 平板毛坯的起伏成形
第五章 胀形与翻边解剖
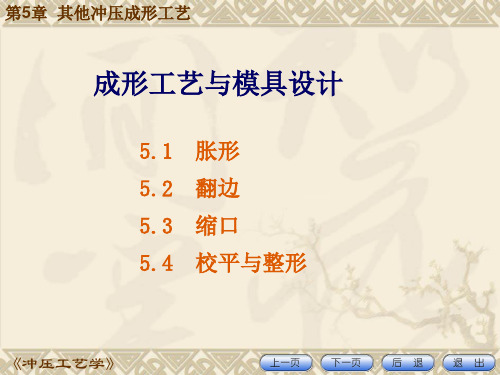
成形工艺与模具设计
5.1 胀形 5.2 翻边 5.3 缩口 5.4 校平与整形
《冲压工艺学》
第5章 其他冲压成形工艺
成形:用不同性质的局部变形来改变毛坯或半成 品形状和尺寸的冲压工序。
伸长类成形:如胀形和内缘翻边,受拉应力而产 生伸长变形,易被拉裂而破坏;
压缩类成形:如缩口和外缘翻边,受压应力而产 生压缩变形,易起皱而破坏。
第5章 其他冲压成形工艺 《冲压工艺学》
第5章 其他冲压成形工艺
图5.1.6 钢模胀形 1-凹模;2-分瓣凸模;3-锥形芯轴 4-拉簧;5-毛坯;6-顶杆;7-下凹模
《冲压工艺学》
第5章 其他冲压成形工艺 《冲压工艺学》
第5章 其他冲压成形工艺
1-上模 2-轴头 3-下模 4-管坯 加轴向压缩的液体胀形
2) 材料相对厚度t0/d1:材料相对厚度越大,成
《冲压工艺学》
第5章 其他冲压成形工艺 《冲压工艺学》
第5章 其他冲压成形工艺 《冲压工艺学》
第5章 其他冲压成形工艺
5.2 翻边(如图5.2.1)
➢翻边是利用模具把板材上的孔缘或外缘翻成竖边的 冲压加工方法。 ➢按工艺特点,可分为:内孔(圆孔和非圆孔)翻边、 外缘(外曲和内曲)翻边和变薄翻边。 ➢按变形性质,可分为伸长类翻边、压缩类翻边及变 薄翻边。
孔边缘变薄最严重,其值为
t t0 K
可见,翻边系数越小,孔边缘变薄越严重,容易发 生破裂。
孔边缘濒于拉裂时的翻边系数称为极限翻边系数Kl。 可用它反映圆孔翻边成形极限。
《冲压工艺学》
第5章 其他冲压成形工艺
影响极限翻边系数的主要因素: 1) 材料机械性能:应变硬化指数和材料延伸率越
钣金与成型第5章 胀形与翻边
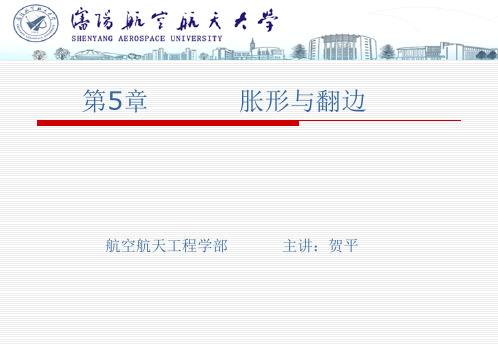
虽然胀形成形极限表示方法不同,但由于胀形区应变
性质相同,且破裂只与变形区应变情况有关,所以影响因 素基本相似。
影响胀形成形极限的材料因素主要是延伸率和应变硬化指
数。一般来讲,延伸率大,破裂前允许的变形程度大,成形极 限也大;应变硬化指数值大,应变硬化能力强,可促使应变分 布趋于均匀化,同时还能提高材料的局部应变能力,故成形极 限也大。
l' l e 2 n l' 0.8
5、 2
翻边
翻边:利用模具将工件的孔边缘翻成竖直
的边。
(图7-1)
一、圆孔翻边 1、圆孔翻边的变形特点(图7-2 ) 变形区应力状态为双向(径向、切向) 受拉的平面应力状态。
变形区的双向应力分布为: 1.155 s
1.155 s (1
极限胀形系数与毛坯切向的许用延 ' 伸率有关,即: dmax d0 p K p 1 d0
(3)张拉成形
特点:曲面变形量很小,破裂不是生产中的主要问题,
零件脱模后的曲面回弹,造成零件出现较大的形 状误差。
措施:工艺上:1)调整压边力;
2)使用拉深筋; 3)增大毛料尺寸等。 选材上:选用屈强比较小的板料成形零件。 张拉成形变形特点及应力应变状态图。
平板张拉成形
……
利用模具把板料上的孔缘或外缘翻成竖边的冲压加工方 法叫翻边。 按工艺特点,翻边分为: 内孔(圆孔或非圆孔)翻边 外缘翻边(内曲翻边、外曲翻边)
变薄翻边
……
按变形性质,翻边分为:
伸长类翻边
压缩类翻边
变薄翻边(属体积成形)
伸长类翻边的特点:
变形区材料切向受拉应力,切向产生伸长变形,导致厚度 减薄,容易发生破裂,如圆孔翻边、外缘的内曲翻边等。 压缩类翻边的特点: 变形区材料切向受压缩应力,切向产生压缩变形,导致厚 度增大,容易起皱,如外缘的外曲翻边。 非圆孔翻边经常是由伸长类翻边、压缩类翻边和弯曲组合 起来的复合成形。
模具设计-冲压工艺与模具设计第五章 精品
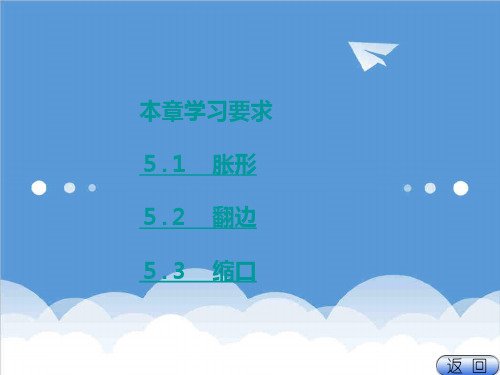
欲提高胀形的极限变形程度,可采用(如图5.1.4)所示两次胀
形法。
1.压加强筋
(1)用刚性凸模压制加强筋的变形力按式 F KLt 计算 :
(2)对在曲柄压力机上用薄料( t<1.5mm)对小工件(面积
(4)翻边力与压边力 在所有凸模中,圆柱形平底凸模的翻边力最大。 其公式为:
F 1.1 (D d 0) b
(2)侧壁胀形计算: K dmax 46.8 1.2
d0 39
侧壁成形力近似按两端不固定形式计算:
F侧胀
Ap
dmax
L
2t d max
b
46.8 40
2 0.5 430N 46.8
54105.89N
胀形前毛坯的原始长度L0由式计算: 可以计算:L0 L[1 (0.3 ~ 0.4) ] Δh
表性。
2.工艺计算 (1)底部压凹坑的计算 查教材表5.1.2得极限胀形深度h=0.15,d=2.25mm,此值大于
工件工件底部凹坑的实际高度,可以一次成形。
压凹所需成形力计算:
F压凹
KAt 2
250
4
152
052
11044.69N
图 5.1.9 罩盖胀形
1—下模板 2—螺栓 3—压凹坑凸模 4—压凹坑凹模 5—胀形下模 6—胀形上模 7—聚氨脂 橡胶 8—拉杆 9—上固定板 10—上模板 11—螺栓 12—模柄 13—弹簧 14—螺母 15—拉杆螺 栓 16—导柱 17—导套
a. 一次翻边成形 (如图5.2.4)所示是在平板毛坯上一次翻孔的图。
d0与H 按下式计算:
第五章 胀形与翻边
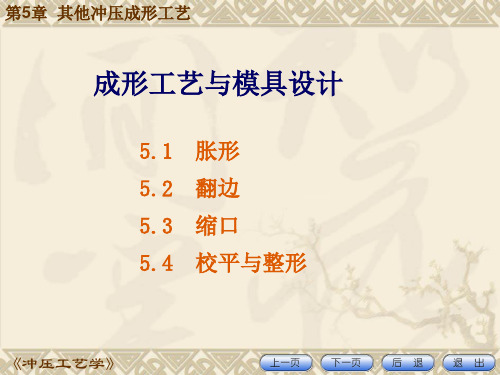
第5章 其他冲压成形工艺
5.1.4 圆柱空心毛坯的胀形
将圆柱形空心毛坯(管状或桶状)向外扩张成曲面 空心零件的冲压加工方法称为圆柱形空心毛坯胀形。高
压气瓶、球形容器、波纹管、自行车三通接头。
1)刚模胀形(如图5.1.4):模具结构复杂,模具与毛 坯间有较大摩擦力,零件精度低 2)软模胀形(如图5.1.5):利用弹性体或流体作为凸 模或凹模。 圆柱形空心毛坯胀形时的应力状态。(如图5.1.6) 1.胀形系数
lmax Kl l0
《冲压工艺学》
第5章 其他冲压成形工艺
《冲压工艺学》
第5章 其他冲压成形工艺
《冲压工艺学》
第5章 其他冲压成形工艺
《冲压工艺学》
第5章 其他冲压成形工艺
《冲压工艺学》
第5章 其他冲压成形工艺
《冲压工艺学》
第5章 其他冲压成形工艺
《冲压工艺学》
第5章 其他冲压成形工艺
《冲压工艺学》
第5章 其他冲压成形工艺
影响极限翻边系数的主要因素: 1) 材料机械性能:应变硬化指数和材料延伸率越
大,Kl越小,成形极限越大。
2) 材料相对厚度t0/d1:材料相对厚度越大,成
形极限越大。
3) 孔边缘状态:孔缘无毛刺和硬化时, Kl小,
成形极限大。
4) 凸模形状(如图5.2.6) :球形、锥形和抛
1、内曲翻边
用模具把毛坯上内凹的边缘,翻成竖边的冲压加工 方法 内曲翻边属于伸长类翻边 内曲外缘翻边的变形程度用翻边系数Es表示:
b ES R b
《冲压工艺学》
第5章 其他冲压成形工艺
2、外曲外缘翻边
用模具把毛坯上外凸的边缘,翻成竖边的冲压方法叫 做外曲翻边
外曲翻边应力应变状况类似于浅拉深,属压缩类翻边。 外曲外缘翻边的变形程度用翻边系数Ec表示:
第5章胀形与翻边

a)翻边过程 ) b)变形区应力 应变状态 )变形区应力,应变状态 图5-12 内孔翻边
2)翻边变形区及变形区的应力应变状态 2)翻边变形区及变形区的应力应变状态 内 孔翻边时, 孔翻边时,变形区被限制在凹模圆角以内的 环状区域内. 环状区域内.与拉深成形通过将板料沿圆周 方向压缩来形成侧壁相反, 方向压缩来形成侧壁相反,内孔翻边是在板 料向凹模圆角弯曲的同时, 料向凹模圆角弯曲的同时,通过将板料沿圆 周方向拉长形成侧壁的过程. 周方向拉长形成侧壁的过程.
如图5 12b所示, 如图5-12b所示,变形区应力状态为双向拉应力 所示 状态, ≥0.孔边缘处, 状态,即σθ>0,σr≥0.孔边缘处,由于径 向材料可以自由变形, 为零而σ 向材料可以自由变形, σr为零而σθ达到最大 由孔边缘向凹模圆角处过渡, 值.由孔边缘向凹模圆角处过渡,径向应力逐 渐增大而切向应力逐渐减小. 渐增大而切向应力逐渐减小.与胀形变形时板 平面的双向伸长变形不同,内孔翻边成形时, 平面的双向伸长变形不同,内孔翻边成形时, 在双向拉应力作用下,板料沿圆周方向伸长, 在双向拉应力作用下,板料沿圆周方向伸长, 径向收缩, εθ>0,径向收缩,εr<0.
3)制件形状和尺寸 3)制件形状和尺寸 就球形凸模和平底凸模而 球形凸模胀形时,应变分布比较均匀, 言,球形凸模胀形时,应变分布比较均匀,能 获得较大的胀形变形程度. 获得较大的胀形变形程度. 4)润滑条件, 4)润滑条件,变形速度及材料厚度 润滑条件
(4)胀形力的计算 (4)胀形力的计算 1)平板毛坯胀形成形力的计算 压制加强筋时, 1)平板毛坯胀形成形力的计算 压制加强筋时,近 似按下式计算. 似按下式计算.
3)翻边变形力 行程曲线 翻边变形力主要由凹 3)翻边变形力—行程曲线 翻边变形力 模圆角处坯料的弯曲力和扩孔, 模圆角处坯料的弯曲力和扩孔,翻边变形阻力 两部分组成.如图5 13所示 在变形过程中, 所示, 两部分组成.如图5-13所示,在变形过程中, 由于变形区域的减小和加工硬化对扩孔, 由于变形区域的减小和加工硬化对扩孔,翻边 力影响的相反效果, 力影响的相反效果,力-行程曲线也呈现出先升 后降的趋势.此外,由图中可见, 后降的趋势.此外,由图中可见,翻边力还受 到凸模底部形状的很大影响, 到凸模底部形状的很大影响,平底凸模成形力 较大,球底凸模的成形力较小. 较大,球底凸模的成形力较小.
冲压工艺学6-胀形与翻边

5.1 胀形
利用胀形模具,使板平面或圆柱面内局部 区域坯料在双向拉应力作用下,产生两向伸长 变形,厚度减薄,表面积增大,以获得所需要 几何形状和尺寸制件的冲压工序。生产中起伏 成形、圆柱形空心毛坯的鼓肚成形,波纹管及 平板毛坯张拉成形均属胀形成形。
胀形常与其它方式的成形同时发生。某些汽 车、拖拉机覆盖件和一些复杂形状零件成形 ,常常包含一定程度胀形成分。胀形加工中 ,金属流动量小,因此,使坯料变形均匀以 及控制整个成形工序中胀形变形量是决定成 败及制件质量的关键。
2)胀形变形区及应力应变状态 如图5-1所示, 胀形变形过程中,毛坯被带凸筋的压边圈压 紧,外部材料无法流入,变形被限制在凸筋 或凹模圆角以内的局部区域。
图5-2显示了平板毛坯局部胀形成形时, 变形区内的应力-应变状态。在变形区内,坯 料在双向拉应力作用下,沿切向和径向产生伸 长变形,厚度变薄,表面积增大。
(3)影响胀形成形极限的因素 1)材料性能 加工硬化指数n值对胀形成形极限 影响极大。 n值大,加工硬化能力强,可促使 应变分布趋于均匀化,同时还能提高材料的局 部强度,故成形极限也大。 2)变形均匀程度 胀形破裂发生在板料厚度减薄 最大部位。变形均匀,板料厚度减薄均匀能获 得较大的胀形变形程度。
h1 h h2 max r t
2)翻边力计算 用圆柱形凸模进行翻边,翻边
力按下式计算。
F 1.1t s (d1 d 0 )
凸模形状和凸凹模间隙对翻边力有很大影 响,如用球形凸模或锥形凸模,所需的力略小 于用上式计算的数值。
3)翻边凸、凹模间隙 平头凸模翻边时,侧壁 可能成为曲面,故翻边凸凹模之间的单边间隙 c可控制在0.75t ~0.85t之间,使直壁稍有变 薄,以保证竖边成为直壁。小的圆角半径和高 竖边的翻边,仅仅应用在螺纹底孔或与轴配合 小孔的翻边。此时单边间隙c=0.65t 。 4)翻边凸模的形状及尺寸 图5-20为几种常用 的圆孔翻边凸模形状及主要尺寸。
第五章胀形与翻边
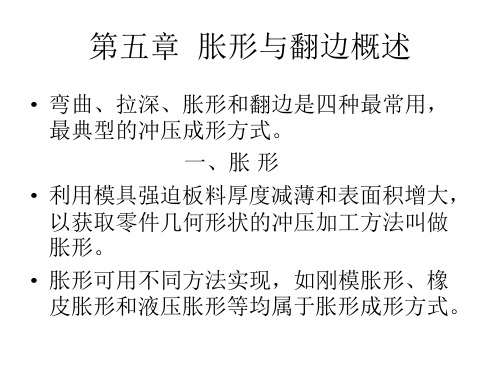
• 在圆孔翻边的中间阶 段,即凸模下面的材 料尚未完全转移到侧 面之前,如果停止变 形,就会得到右图所 示的成形方式,这种 成形方式叫做扩孔, 生产应用也很普遍。
第五章 胀形与翻边概述
• 弯曲、拉深、胀形和翻边是四种最常用, 最典型的冲压成形方式。 一、胀 形 • 利用模具强迫板料厚度减薄和表面积增大, 以获取零件几何形状的冲压加工方法叫做 胀形。 • 胀形可用不同方法实现,如刚模胀形、橡 皮胀形和液压胀形等均属于胀形成形方式。
• 右图是用球头凸模胀形平 板毛坯的示意图,这种胀 形方法可视为纯胀形。纯 胀形时,毛坯被带有拉深 筋的压边圈压死,变形区 限制在拉深筋以内的毛坯 中部,在凸模力作用下, 变形区大部分材料受双向 拉应力作用(忽略板厚方 向的应力),沿切向和径 向产生拉伸应变,使材料 厚度减薄,表面积增大, 并在凹模内形成一个凸包。
二.圆孔翻边
• 利用模具把板料上的孔缘或外缘翻成 竖边的冲压加工方法叫做翻边。 • 右图是圆孔翻边示意图。翻边时带有 圆孔的环形毛坯被压边圈压死,变形 区基本上限制在凹模圆角以内,并在 凸模轮廓的约束下受单向或毛坯中心的圆孔不断胀 大,凸模下面的材料向侧面转移,直 到完全贴靠凹模侧壁,形成直立的竖 边。
• 胀形成形极限以零件是否发生破裂来判别。 • 一般来讲,胀形破裂总是发生在材料厚度 减薄最大的部位,所以变形区的应变分布 是影响胀形成形极限的重要因素。 • 影响胀形成形极限的材料因素主要是延伸 率和应变硬化指数n。一般来讲,延伸率大, 破裂前允许的变形程度大,成形极限也大; n值大,应变硬化能力强,可促使应变分布 趋于均匀化,同时还能提高材料的局部应 变能力,故成形极限也大。
第五章 其它成形方法
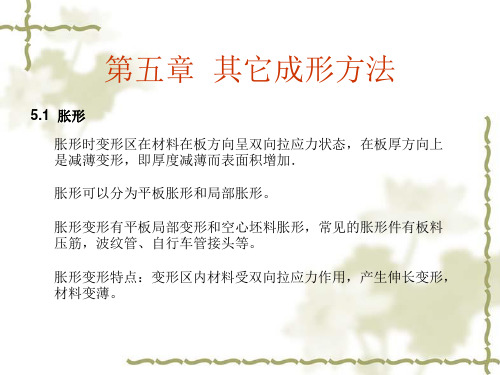
常见的缩口形式如下:
变形程度 缩口变形程度用缩口系数ms来表示,其表达式:
d ms = D
式中 d—缩口后的直径 D—为缩口前的直径
缩口的工艺计算 缩口次数及缩口系数的确定 缩口次数由下式确定:
lg msz n= lg msp
msz 为总缩口系数
msp
为平均缩口系数
msz = d / D
msp ≈ ms min
第五章 其它成形方法
5.1 胀形 胀形时变形区在材料在板方向呈双向拉应力状态,在板厚方向上 是减薄变形,即厚度减薄而表面积增加. 胀形可以分为平板胀形和局部胀形。 胀形变形有平板局部变形和空心坯料胀形,常见的胀形件有板料 压筋,波纹管、自行车管接头等。 胀形变形特点:变形区内材料受双向拉应力作用,产生伸长变形, 材料变薄。
其它圆孔翻边方法: 1 拉深后翻边 2 无预制孔翻边
外缘翻边: 可以分为内曲翻边和外缘翻边,外曲翻边近似于浅拉深,变形 区切向受压,属于压缩变形,内区翻边变形区近似于圆孔翻边,切向受 拉,属于伸长类变形。
内凹外缘翻边的变形程度用翻边系数Es表示:
b ES = R −b
外凸外缘翻边的变形程度用翻边系数Ec表示
圆孔翻边 在板料上沿着冲好的孔翻边,其应力分布如下:
圆孔翻边变形程度以k表示,k = d/D,d为预制孔直径,D为翻 边后直径。 一次翻边成形计算:
d0 = D − 2(H − 0.43r − 0.72t) d0 D D H = (1− ) + 0.43r + 0.72t = (1− m) + 0.43r + 0.72t 2 D 2
δ − −工件的切向延伸率(式5.1.6 )
∆h − −修边余 量,约为 ~ 20mm 5
第5章_局部成形工艺与模具设计
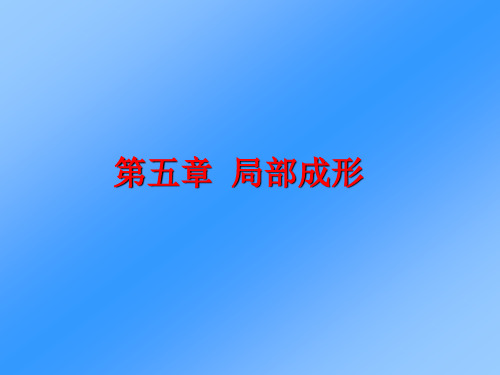
σ
σ
θ
ε
ε
θ
图6-1 胀形变形区
二、胀形的种类 1.平板坯料的起伏成形
起伏成形俗称局部胀形,可以压制加强筋、凸包、凹坑、花 纹图案及标记等。
校平和整形工序的共同特点: (1)只在工序件局部位置使其产生不大的塑性变形; (2)模具的精度比较高;
(3)所用设备最好为精压机。若用机械压力机时,机床应有 较好的刚度,并需要装有过载保护装置。 二、校平 1. 校平变形特点与校平力 校平力 F 用下式 估算:
F AP
平板零件校平 空间零件的校平
Dmin ——胀形最小直径,mm; t ——材料原始厚度,mm。
5.3
翻边:
翻
边
在模具的作用下,将坯料的孔边缘或外边缘冲制成竖立边 的成形方法。 内孔翻边 不变薄翻边 变薄翻边 伸长类翻边 压缩类翻边
外缘翻边
外曲翻边
内曲翻边
内孔与外缘翻边零件
一、内孔翻边 1. 圆孔翻边:是把预先加工在平面上的圆孔周边翻起扩大, 成为 具有一定高度的直壁孔部,是一种拉延类平面翻边。
图6-4
压凸包
表6-2
平板局部冲压凸包的成形极限
2.空心坯料的胀形
空心坯料的胀形:
俗称凸肚,它是使材料沿径向拉伸,将空心工序件或管状坯 料向外扩张,胀出所需的凸起曲面,如壶嘴、皮带轮、波纹管等。 1)几种主要胀形方法 刚性模具胀形 软模胀形 轴向压缩和高压液体联合作用的胀形
图6-5 用刚性凸模的胀形
D P ( D0 0 p )
第五章、翻边与胀形

②软模胀形
利用橡胶,聚氨酯,PVC塑料等作 利用橡胶,聚氨酯,PVC塑料等作 13聚氨酯强度、弹性、 聚氨酯强度 凸模 图5-13聚氨酯强度、弹性、耐 油性方面优于橡胶 得到广泛运用。 橡胶, 油性方面优于橡胶,得到广泛运用。
③液压胀形 P75, P75,
图5-14
图册P68, 图册P68, P68
h1=h-r-to =h-
(1h=1/2Dm(1-K )+ 0.43r+0.75to (1hmax=1/2Dm(1-KL)+0.43r+0.75to
当h>hmax 不能一次成形
(2)可采用拉深后再翻边 (2)可采用拉深后再翻边
或采取预胀形 或拉深后翻边
先确定翻边 h1、 后定 do、 h2 d0有错 196页 有错 页 Dm − do to ∏ to h1 = − (r + ) + (r + ) 2 2 2 2 Dm ≈ (1 − k ) + 0.57 r 2 d o = Dm + 1.14r
δ p = K p −1 θ
得出K 由 δ θp得出Kp 表5-3
5.张拉成形 5.张拉成形
有些大型零件,底部曲率半径很大,曲面部分变 有些大型零件,底部曲率半径很大,曲面部分变 大型零件 形量小,回弹大。 形量小,回弹大。 需胀形的方式增大塑性变形量。 需胀形的方式增大塑性变形量。 增大塑性变形量 两种方法: 两种方法: 采用增大进料阻力工艺措施( 一是采用增大进料阻力工艺措施 调整压边力, 一是采用增大进料阻力工艺措施(调整压边力, 使用拉深筋,增大毛坯尺寸)提高毛坯变形程度。 使用拉深筋,增大毛坯尺寸)提高毛坯变形程度。 可采用δ 较小的板料成形。 可采用δs/δb较小的板料成形。
第5章 胀形与翻边

4、翻边力的计算 采用平底凸模翻边:
F = 1.1π (D − d0 )tσ s
(N)
采用球头凸模翻边:
F = 1.2K0πDtσb
(N)
5、翻边模设计 ⑴、结构类型(图7-8、图7-9) ⑵、翻边凸模和凹模设计(图7-10 )
二、变薄翻边
若零件的翻边高度较大难于一次成形时,可在不影响使用 要求的条件下采用变薄翻边,以提高生产效率并节约材料。 变薄翻边属于体积成形。变薄翻边时,凸模和凹模之间 采用小间隙,凸模下方的材料变形与圆孔翻边相似,但它们成 形为竖边后,将会在凸模和凹模之间的小间隙内受到挤压,进 一步发生较大的塑性变形,使厚度显著减薄,从而提高翻边高 度。由于变薄翻边属于体积成形,所以变薄翻边的变形程度只 取决于竖边的变薄系数:
影响胀形成形极限的材料因素主要是延伸率和应变硬化指 数。一般来讲,延伸率大,破裂前允许的变形程度大,成形极 限也大;应变硬化指数值大,应变硬化能力强,可促使应变分 布趋于均匀化,同时还能提高材料的局部应变能力,故成形极 限也大。 润滑条件和变形速度以及材料厚度对胀形成形极限也有影 响。如用球头凸模胀形时,若毛坯和凸模之间施加良好的润 滑,其应变分布要比干摩擦时均匀,能使胀形高度增大。变形 速度的影响,主要是通过改变摩擦系数来体现的,对球头凸模 来讲,速度大,摩擦系数减小,有利于应变分布均匀化,胀形 高度有所增大。必须指出,用平底凸模胀形时,应尽量增大凸 模底部板料的变形,避免板料在圆角处变形过于集中,否则, 胀形高度就比较小。一般来讲,材料厚度增大,胀形成形极限 有所增大,但料厚与零件尺寸比值较小时,其影响不太显著。
加轴向压缩的液体胀形 1-上模 2-轴头 3-下模 4-管坯
(3)张拉成形
特点:曲面变形量很小,破裂不是生产中的主要问题, 零件脱模后的曲面回弹,造成零件出现较大的形 状误差。 措施:工艺上:1)调整压边力; 2)使用拉深筋; 3)增大毛料尺寸等。 选材上:选用屈强比较小的板料成形零件。 张拉成形变形特点及应力应变状态图。 (教材P135图5-19、5-20)
冲压工艺学6-胀形与翻边讲解
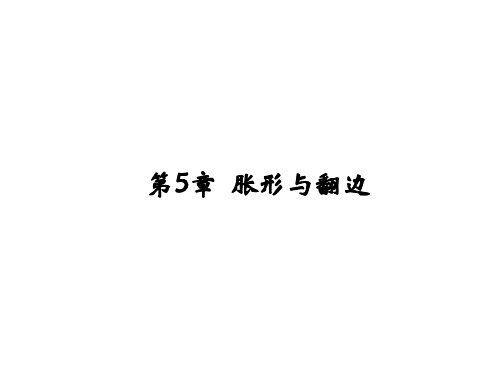
F KAt
2
2)圆柱形空心毛坯胀形力的计算 可按下式 计算。
F p A
胀形单位压力p可按下式计算。
2t p 1.15 z d max
5.2 翻边
利用模具把板料孔缘或外缘翻成竖边,或将 圆柱形空心毛坯口部翻出法兰的冲压工序。 翻边总是与弯曲变形同时发生。如图5-11所示, 根据翻边件形状及变形区应力应变状态的不 同,翻边可分为直线翻边、伸长类翻边、压 缩类翻边和复合翻边四种形式。直线翻边即 弯曲,压缩类翻边的本质与拉深相同。此外, 按翻边材料厚度变化情况,翻边还可分为普 通翻边与变薄翻边两类。
a)径向和厚度方向应变分布 b)切向和径向应变分布 图5-3 胀形件的应变分布和应变状态图
5)胀形变形服从材料的变形规律 当存在多种变形可能性时,实际的变形方式 使得载荷最小。毛坯的外径足够大,内孔较小 时,拉深变形阻力和扩孔、翻边变形阻力大于 胀形变形阻力时,变形性质由胀形决定。
图4-6
毛坯尺寸和工序类型的关系
图5-7 两道工序完成的凸形
(2)圆柱形空心毛坯的胀形 1)胀形方式 a.橡皮(或聚氨酯)凸模 胀形 该胀形方式如图5-8 所示。由于聚氨酯橡胶优 良的物理机械性能,用它 作工作介质的胀形得到愈 来愈广泛的应用。
图5-8 橡皮凸模胀形
b.分块式凸模胀形 如图5-9所示,采用刚性凸模, 凸模必须作成分块式,以便出模时由楔状心块 将其分开。
a)应力状态 b)应变状态 图5-2 变形区应力和应变状态
3)变形力—行程曲线 与拉深不同,胀形时变 形区是在不断扩大的。由于加工硬化,胀形变 形力-行程曲线是单调增曲线,产生破裂时胀 形力达到最大值。
4)应变和板厚的分 布 图5-3是平板毛 坯局部胀形时的应 变分布图。由图中 可见,变形区内径 向应变εr和切向应 变εθ全部大于零, 而厚度方向的应变 小于零,坯料变薄。
同济大学机械第五章胀形与翻边

表1 汽车上部分冲压件与管材液压柔性成形件的重量对比
(2) 减少零件和模具数量,降低模具费用。液压柔性成 形件通常仅需要一套模具,而冲压件大多需要多套模具。 副车架的组成零件由6个减少到1个;散热器支架的组成零 件由17个减少到10个。 (3) 可减少后续机械加工和组装焊接量。以散热器支架为 例,散热面积增加43%,焊点由174 个减少到20 个,装配工 序由13 道减少到6 道,生产率提高66%; (4) 提高强度与刚度,尤其疲劳强度。仍以散热器支架强度 为例,垂直方向提高39%;水平方向提公司对已应用零件统计分析, 管材液压柔性件比冲压件平均降低15~20%,模具费用降低 20~30%。
(6) 成形零件的精度提高。成形零件的尺寸精度从原来的IT14 提高到IT10。管材液压柔性成形适用于制造航空、航天和汽车 领域的各种异形的空心构件,在汽车领域,德国处于世界研究 的最前沿。德国于70 年代末开始管材液压柔性成形基础研究, 并于90 年代初率先开始在工业生产中采用管材液压柔性成形技 术制造汽车轻体构件。德国奔驰汽车公司(DAIMLERBENZ) 于1993 年建立其管材液压柔性成形车间;宝马公司(BMW)已在 其几个车型上应用了管材液压柔性成形的零件。目前在汽车上 应用有:排气系统;底盘构件;车身框架、座椅框架及散热器 支架;凸轮轴等。
图1 有轴向进给的管件内高压成形
图2 无轴向进给的管件液压柔性成形
2、管件液压柔性成形优点及应用范围 用管材液压柔性成形可以一次成形出沿着构件的轴线
截面不同的复杂零件,这是管材液压柔性成形的主要优点。 另外,与传统的冲压焊接工艺相比,管件液压柔性成形的 主要优点还有以下几个方面。 (1) 减轻重量节约材料。对于图3 空心轴类可以减轻 40~50%,节约材料可达75%。汽车上部分采用冲压工艺与 管材液压柔性成形的产品结构重量对比如表1。
- 1、下载文档前请自行甄别文档内容的完整性,平台不提供额外的编辑、内容补充、找答案等附加服务。
- 2、"仅部分预览"的文档,不可在线预览部分如存在完整性等问题,可反馈申请退款(可完整预览的文档不适用该条件!)。
- 3、如文档侵犯您的权益,请联系客服反馈,我们会尽快为您处理(人工客服工作时间:9:00-18:30)。
图1 有轴向进给的管件内高压成形
图2 无轴向进给的管件液压柔性成形
2、管件液压柔性成形优点及应用范围 用管材液压柔性成形可以一次成形出沿着构件的轴线
截面不同的复杂零件,这是管材液压柔性成形的主要优点。 另外,与传统的冲压焊接工艺相比,管件液压柔性成形的 主要优点还有以下几个方面。 (1) 减轻重量节约材料。对于图3 空心轴类可以减轻 40~50%,节约材料可达75%。汽车上部分采用冲压工艺与 管材液压柔性成形的产品结构重量对比如表1。
图11 利用液压柔性成形胀接工艺生产的凸轮轴
8、结论及应用研究展望
减轻结构重量以节约材料和运行中的能量是现代先进制造 技术发展的趋势之一。液压柔性成形是适应这种趋势提出来的 一种制造空心轻体的新工艺。液压柔性成形件具有诸多的优点, 可以减少模具,降低生产成本,缩短加工周期。可以用于制造 汽车、航空、航天等行业中使用的各类轻体构件。根据美国钢 铁研究院汽车应用委员会的调查结果,在北美制造的典型轿车 中,采用空心轻体件在轿车总重量的比例已从15 年前的10%上 升到16%,而在中型面包车、大吉普和皮卡车的比例还要高。 因此美国有关大学,研究机构和公司十分重视液压柔性成形技 术,已于几年前开始着手研究开发,近年来加大研究开发的力 度。如美国三大汽车公司和十大钢铁公司成立“汽车与钢铁液 力成形工业资源组织 (Auto/SteelPartnershipHydroformingIndustryResourceGroup )”。 据一项调查表明,估计到2010 年北美生产的典型车型中将有 50%零件采用液压柔性成形技术制造
图9 是现今世界汽车行业中应用的最大管材液压柔性成形件: 汽车纵梁,此件是在通用汽车公司开发的专用管材液压柔性成 形机上制造的。该件的原始管坯外径为152.4mm,壁厚为2.0mm, 长度为4876.8mm,而过去采用的方法是采用14个冲压件焊接或 铆接在一起而成的。现采用管材液压柔性成形件降低了造价和 减轻了重量,并且空间结构尺寸愈加紧凑。
图4 用于汽车排气系统的Y 形三通管件(SPS)
图5是汽车上采用的一种接触反应转换器,由一对圆锥体形 成。利用管材液压柔性技术成形后,再从中间剖开,从而形 成两个零件。利用管材液压柔性成形技术可以获得100%的膨胀 量。
图5 一次成形的双锥体零件(SPS)
在汽车排气系统中,还有一类零件,就是符合气体动力学 原理和具有消音功能的复杂的空间构件。传统的生产工艺一 般是先冲压后焊接再一起,这就影响了零件的总体装配精度, 零件的功能也将受到影响。而利用管材液压柔性成形就消除 了这种缺陷的产生,一次生产出合格的零件,如图6所示,为 管材液压柔性成形生产的一种典型的零件。
§5.1 胀形
一、胀形成形特点
胀形的特点是: 1 、胀形时,板料的塑性变形区仅局限于一个固定的变形
范围内,板料不向变形区外转移,也不从变形区外进入变形 区。
2 、胀形时板料在板面方向处于双向受拉的应力状态,所 以胀形时工件一般都是要变薄。因此在考虑胀形工艺时,主 要应防止材料受拉而胀裂。
3 、胀形的极限变形程度,主要取决于材料的塑性。材料 塑性越好,延伸率越大,则胀形的极限变形程度越大。
图3 阶梯轴
表1 汽车上部分冲压件与管材液压柔性成形件的重量对比
(2) 减少零件和模具数量,降低模具费用。液压柔性成 形件通常仅需要一套模具,而冲压件大多需要多套模具。 副车架的组成零件由6个减少到1个;散热器支架的组成零 件由17个减少到10个。 (3) 可减少后续机械加工和组装焊接量。以散热器支架为 例,散热面积增加43%,焊点由174 个减少到20 个,装配工 序由13 道减少到6 道,生产率提高66%; (4) 提高强度与刚度,尤其疲劳强度。仍以散热器支架强度 为例,垂直方向提高39%;水平方向提高50%。
第五章 胀形与翻边
§5.1 胀形 §5.2 圆孔翻边
§5.1 胀形
利用模具强迫板料厚度减薄和表面积增大,以 获取零件几何形状的冲压加工方法叫做胀形。
胀形的方法有: 1 、钢模胀形法 2 、软模胀形法 3 、液压胀形法
冲压生产中的起伏成形、圆柱形空心毛坯的凸胀成形、 波纹管的成形及飞机蒙皮张拉成形等均属于胀形成形。汽 车覆盖件等形状比较复杂的零件成形也常常包含胀形成分。
3、管材液压柔性成形技术在汽车排气系统上的应用
管材液压柔性成形技术过去主要用来研究生产一些简单的 零件如直壁枝杈管等,距今已有30 年的历史。现今汽车的零 件生产主要是一些枝杈管,但与过去生产的直壁枝杈管有所 不同,形状和成形工艺要更为复杂一些。图4 为典型的排气 系统三通管。在管材液压柔性成形过程中可以较精确地控制 零件的尺寸精度,故可以很方便地在后续工序中与其它零件 进行装配。如今,这些工件已在奔驰公司批量生产,用来取 代传统的铸造生产或用两个半壳焊在一起的生产方式。与传 统的生产工艺相比,利用管材液压柔性成形的方式节约了 70%的生产时间,与铸造生产方式相比,大约节约了40%的 重量。
图9 管材液压柔性成形的汽车纵梁(GM)
5、管材液压柔性成形技术在汽车车身框架的应用
在汽车工业,结构零件占车身总重的很大一部分,为减 轻车身的重量,可以采用两种途径:一种是采用新型的轻质 材料,另一种就是减少零件的重量。而利用管材液压柔性成 形技术成形开创了一个减重的新领域:结构零件的生产。与 传统的结构部件生产工艺相比,管材液压柔性成形具有以下 优点:高度整体化(即零件数量的减少),复杂空间结构, 零件刚度好,空间利用率高,尺寸精度高。图10 为汽车车 身框架的集成图,其中主要有车顶纵梁,其原始管坯为低碳 钢,管坯的外径为69.9mm,厚度为2.0mm,全部工艺过程 包括弯曲、液压柔性成形、冲裁和切边等,并且为了提高生 产率,左右零件同时用管材液压柔性成形的方法生产,然后 在下道工序中切开。
§5.1 胀形
一、胀形成形特点(续)
应变分布图是冲压成形时零件上各点或局部各点的应变分 布情况图,应变状态图是零件上各点或局部各点的应变在二维 主应变平面上的分布状况图。成形方式、工艺条件和材料性能 的改变,都会引起应变分布图和应变状态图发生变化。利用应 变分布图和应变状态图可以分析冲压变形区的应变情况,寻求 改善板料塑性流动的措施,以解决冲压成形时的各种失稳问题。 将胀形时的应变状态图与板料的成形极限图(FLD)对比,若 零件上某点的应变量超出成形极限图的应变范围,该点就是发 生破裂的危险点,必须采取措施(如改变毛坯或模具的几何条 件、调整压边力、修磨圆角、改变润滑或更换原材料等)降低 该点应变量,以保证不发生破裂。
4 、胀形时,材料处于双向拉应力状态,在一般情况下, 变形区的工件不会产生失稳起皱现象。胀形成形的工件表面 光滑、回弹小,质量好。
§5.1 胀形
一、胀形成形特点(续)
图5-1 纯胀形成形
图5-2 胀形时的应力和应变
§5.1 胀形
一、胀形成形特点(续)
a)
b)
图5-3 胀形时的应变分布与应变状态图 a)应变分布图 b)应变状态图
在汽车零件的加工中,根据有无轴向进给,可以把管件液 压柔性成形分为两类,一类为有轴向进给,如图1 所示,主要 用来成形壁厚均匀或较大成形量的零件;另一类为无轴向进给, 主要用在零件的整形和多个零件的胀接如中空凸轮轴的生产等, 对于轴线为曲线的零件,还需要把管坯预弯成接近零件形状, 然后加压成形, 如图2 所示。
图7 汽车底盘零件(BMW)
图8 汽车副车架(Schuler)
一般来说,在底盘零件上采用的管坯尺寸为直径75~85mm, 壁厚为2~3mm,最终成形零件的长度在1200 到1400mm 之间, 截面的最大膨胀程度在25%到35%之间。生产此类零件时, 要优化所用管坯的原始参数,如外径、壁厚和材料及其性能 参数等,还要确定合适的工艺参数,如果在管材液压柔性成 形时管端部需要较大的膨胀量,则还需要考虑管端部的进给。 如图8 所示为管端部需要较大膨胀量的汽车底盘零件:副车 架,此件所采用管坯外径是69.9mm,壁厚为2.5mm,传统冲 压焊接工艺成形需6 个零件,而内高压成形仅需要一个零件, 重量节省了34%。
图6 具有复杂空间尺寸的汽车排气管件(SPS)
4、管材液压柔性成形技术在汽车底盘上的应用
用管材液压柔性成形技术来生产汽车底盘部件有很多的 优点,如安装空间的充分利用、零件具有复杂的空间结构、 底盘零件的高强度等。利用管材液压柔性成形技术可以获 得刚度很高的轿车结构和高刚性的底盘,这使得操纵汽车 变得更安静、更灵活。生产此类零件,一般有以下几个工 艺步骤:管坯的制造,管坯的预弯以及通过液压柔性成形, 得到零件的最终形状,在必要的情况下,还需进行激光切 割或端部加工等工序。图7为利用管材液压柔性成形的各种 汽车底盘零件的集成。
§5.1 胀形
一、胀形成形特点(续)
变形区各点厚度减薄(εt<0),强 度下降,一旦变形区某点的拉应力 超过该点强度,发生破裂。因强度 不足而引起的破裂叫做α破裂。
(5) 降低生产成本。根据德国某公司对已应用零件统计分析, 管材液压柔性件比冲压件平均降低15~20%,模具费用降低 20~30%。
(6) 成形零件的精度提高。成形零件的尺寸精度从原来的IT14 提高到IT10。管材液压柔性成形适用于制造航空、航天和汽车 领域的各种异形的空心构件,在汽车领域,德国处于世界研究 的最前沿。德国于70 年代末开始管材液压柔性成形基础研究, 并于90 年代初率先开始在工业生产中采用管材液压柔性成形技 术制造汽车轻体构件。德国奔驰汽车公司(DAIMLERBENZ) 于1993 年建立其管材液压柔性成形车间;宝马公司(BMW)已在 其几个车型上应用了管材液压柔性成形的零件。目前在汽车上 应用有:排气系统;底盘构件;车身框架、座椅框架及散热器 支架;凸轮轴等。
图10 管材液压柔性成形的汽车车身框架
6、凸轮轴
利用管材液压柔性成形胀接工艺可以用来实现零件之间的 联接,如图11 为利用此种工艺生产的汽车发动机的凸轮轴。 首先利用粉末冶金的方法生产出单个的凸轮,然后把多个这 样的凸轮预安装在一根管坯上,在管坯内部通以一定的高压 液体,管坯局部经过了塑性变形,在凸轮的两侧超出了凸轮 的宽度,约束了凸轮的轴向位移,并且,由于管坯内压的作 用,凸轮也产生了一定的弹性变形,当内压撤消后,凸轮回 弹,会在凸轮与管坯之间产生一种紧密的结合力,这种结合 力防止了凸轮相对于管坯的转动。与传统凸轮轴生产工艺相 比,由于此种工艺的凸轮与心轴为胀接,可以采用不同的材 料,在相同扭距的情况下,零件总体重量也降低,特别是对 于一些中心需要钻孔的零件更有优势。