产品外观检验标准(通用)
五金产品通用外观检验标准
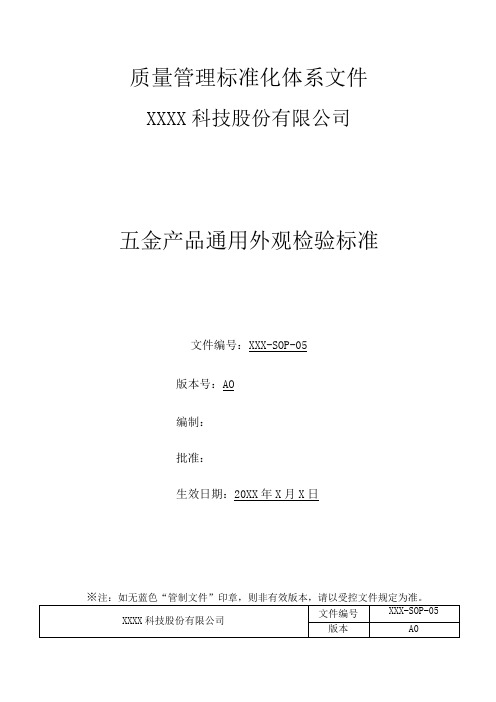
质量管理标准化体系文件
XXXX科技股份有限公司
五金产品通用外观检验标准
文件编号:XXX-SOP-05
版本号:AO
编制:
批准:
生效日期:20XX年X月X日
※注:如无蓝色“管制文件”印章,则非有效版本,请以受控文件规定为准。
1.检验环境
光照条件:正常光源强度为1000土200勒克斯(LUX)。
检验角度:视角为45°或90°。
2.抽样标准
抽样方案依GB2828.1-2012(II)标准,Cr=0,Maj=0.65,Min=1.5。
3.缺陷等级分类
致命缺陷:凡会影响使用者,维护者,或携带者生命安全或有安全隐患之缺陷;
严重缺陷:影响产品的组装或直接影响到产品的使用功能之缺陷;
轻微缺陷:不影响产品的组装或使用功能,只影响到用户视觉或轻微触觉等之缺陷;
4.产品表面等级区分
A面(一级区域):经组装后,位于用户正面之区域;
8面(二级区域):经组装后,位于使用者上面,两侧面与底座上面之区域;
C面(三级区域):经组装后,位于使用者后面与前框、底盘的底面之区域;
D面(四级区域):经组装后,位于正面、上面、后面、两侧下方均无法观测之区域;。
通用外观检验标准
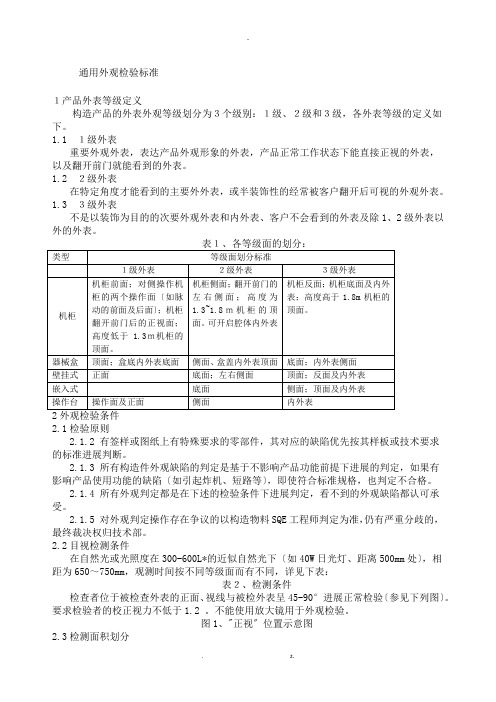
通用外观检验标准1产品外表等级定义构造产品的外表外观等级划分为3个级别:1级、2级和3级,各外表等级的定义如下。
1.1 1级外表重要外观外表,表达产品外观形象的外表,产品正常工作状态下能直接正视的外表,以及翻开前门就能看到的外表。
1.2 2级外表在特定角度才能看到的主要外外表,或半装饰性的经常被客户翻开后可视的外观外表。
1.3 3级外表不是以装饰为目的的次要外观外表和内外表、客户不会看到的外表及除1、2级外表以外的外表。
2.1检验原则2.1.2 有签样或图纸上有特殊要求的零部件,其对应的缺陷优先按其样板或技术要求的标准进展判断。
2.1.3 所有构造件外观缺陷的判定是基于不影响产品功能前提下进展的判定,如果有影响产品使用功能的缺陷〔如引起炸机、短路等〕,即使符合标准规格,也判定不合格。
2.1.4 所有外观判定都是在下述的检验条件下进展判定,看不到的外观缺陷都认可承受。
2.1.5 对外观判定操作存在争议的以构造物料SQE工程师判定为准,仍有严重分歧的,最终裁决权归技术部。
2.2目视检测条件在自然光或光照度在300-600L*的近似自然光下〔如40W日光灯、距离500mm处〕,相距为650~750mm,观测时间按不同等级面而有不同,详见下表:表2、检测条件检查者位于被检查外表的正面、视线与被检外表呈45-90°进展正常检验〔参见下列图〕。
要求检验者的校正视力不低于1.2 。
不能使用放大镜用于外观检验。
图1、"正视〞位置示意图2.3检测面积划分被检外表按其面积或最大外形尺寸划分为不同大小类别,当有两个条件满足时、以大的一类为准。
外表大小划分标准如下表。
〔注:一般情况下,被检外表上的缺陷个数超过2个时,缺陷之间的距离必须大于10 mm,否则视为同一缺陷,尺寸以其总和计。
〕表3、外表大小类别划分3对外观的质量要求3.1总则有签样或图纸上有特殊要求的零部件,其对应的缺陷优先按其样板或技术要求的标准进展判断。
外观通用检验规范
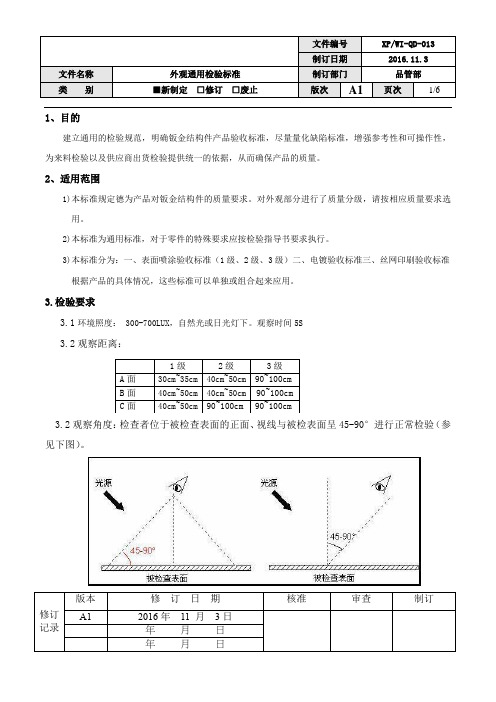
类 别■新制定 □修订 □废止版次A1页次1/6修订记录版本修 订 日 期 核准审查制订A1 2016年 11 月 3日年 月 日 1、目的建立通用的检验规范,明确钣金结构件产品验收标准,尽量量化缺陷标准,增强参考性和可操作性,为来料检验以及供应商出货检验提供统一的依据,从而确保产品的质量。
2、适用范围1)本标准规定德为产品对钣金结构件的质量要求。
对外观部分进行了质量分级,请按相应质量要求选用。
2)本标准为通用标准,对于零件的特殊要求应按检验指导书要求执行。
3)本标准分为:一、表面喷涂验收标准(1级、2级、3级)二、电镀验收标准三、丝网印刷验收标准 根据产品的具体情况,这些标准可以单独或组合起来应用。
3.检验要求3.1环境照度: 300-700LUX ,自然光或日光灯下。
观察时间5S 3.2观察距离:3.2观察角度:检查者位于被检查表面的正面、视线与被检表面呈45-90°进行正常检验(参见下图)。
1级 2级 3级 A 面 30cm~35cm 40cm~50cm 90~100cm B 面 40cm~50cm 40cm~50cm 90~100cm C 面 40cm~50cm 90~100cm 90~100cm类别■新制定□修订□废止版次A1 页次2/6修订记录版本修订日期核准审查制订A12016年11 月3日年月日4.缺陷定义:Note.1 Note.2 Note.3点状缺陷:线状缺陷:当L>2W时按Note.2d=(a+b)/2 W: width, L:length,当L≤2W时按Note.15.字母定义L:长度,W:宽度,d:直径,D:缺陷间的距离,N:缺陷数量,ΔE:色差值。
6.验收标准6.1表面喷涂验收标准序号检验项目检查面1级2级3级工具1 色差A、B、C ΔE≤1.0 ΔE≤1.5 ΔE≤3.0 色板、色差仪2 涂膜光泽、纹理A、B、C 对比色板,无明显差异目视、色板3 附着力A、B、C 百格测试,剥离面积不可有超过总体面积5%以上。
通用外观检验标准
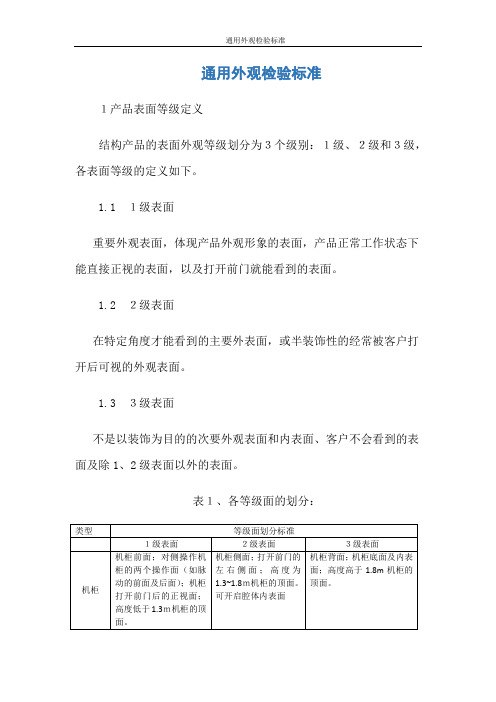
通用外观检验标准1产品表面等级定义结构产品的表面外观等级划分为3个级别:1级、2级和3级,各表面等级的定义如下。
1.1 1级表面重要外观表面,体现产品外观形象的表面,产品正常工作状态下能直接正视的表面,以及打开前门就能看到的表面。
1.2 2级表面在特定角度才能看到的主要外表面,或半装饰性的经常被客户打开后可视的外观表面。
1.3 3级表面不是以装饰为目的的次要外观表面和内表面、客户不会看到的表面及除1、2级表面以外的表面。
表1、各等级面的划分:2外观检验条件2.1检验原则2.1.1产品外观应美观,颜色均匀一致,单独一零/部件的整体视觉效果不能受到破坏,不会给人以劣质产品的印象。
生产者应认真操作、严格控制产品质量,避免在生产过程中出现对各种表面的损伤。
2.1.2 有签样或图纸上有特殊要求的零部件,其对应的缺陷优先按其样板或技术要求的标准进行判断。
2.1.3 所有结构件外观缺陷的判定是基于不影响产品功能前提下进行的判定,如果有影响产品使用功能的缺陷(如引起炸机、短路等),即使符合标准规格,也判定不合格。
2.1.4 所有外观判定都是在下述的检验条件下进行判定,看不到的外观缺陷都认可接受。
2.1.5 对外观判定操作存在争议的以结构物料SQE工程师判定为准,仍有严重分歧的,最终裁决权归技术部。
2.2目视检测条件在自然光或光照度在300-600LX的近似自然光下(如40W日光灯、距离500mm处),相距为650~750mm,观测时间按不同等级面而有不同,详见下表:表2、检测条件表面等级1级2级3级检视时间5s5s3s检视距离光源650~750mm自然光或光照度在300-600LX检查者位于被检查表面的正面、视线与被检表面呈45-90°进行正常检验(参见下图)。
要求检验者的校正视力不低于1.2 。
不能使用放大镜用于外观检验。
图1、“正视”位置示意图2.3检测面积划分被检表面按其面积或最大外形尺寸划分为不同大小类别,当有两个条件满足时、以大的一类为准。
产品外观检验标准

产品外观检验标准(d o c-8)(总8页)--本页仅作为文档封面,使用时请直接删除即可----内页可以根据需求调整合适字体及大小--产品外观检验标准一、变压器涉及到的有烤漆品、电镀品、塑胶品等样品的外观检查标准有:1、烤漆品外观不良及允收标准:⑴流胶:A面流漆宽度<,长度<15mm, B面不做要求,但不能影响到其它功能⑵沙粒:在不转动零件的情况下:A面沙粒与烤漆同色, 沙粒Φ<,个数应少于8PCS, 且分散;沙粒与烤漆异色, Φ<,个数少于3PC⑶汽泡:零件A面烤漆气泡:检测面内气泡Φ<,不多于3PCS且分散, B面可不作要求⑷针孔:A面针孔:检测面内针孔Φ<,个数少于5PCS,且分散⑸异色:A面异色污染污点:检测面异色污点Φ<,不多于3PCS面⑹划伤:A面不露底色的划伤:检测面内划伤长度<10mm,宽度小于,少于3道;露底色划伤:检测面内划伤长度<5mm, 宽度小于,少于2道. HM软轨烤漆表面有露出胶条底色的划伤不可接收,依长度方向单条划伤超过10cm不可接收,小于10cm的划伤在30cm内不能超过2条,否则不接收。
⑺橘子皮:A面桔子皮无凹凸手感,小于零件检测面的1/4面积,否则属MI,B 面可不作要求⑻脏污:A面不允许有擦拭不掉的污垢、指纹、油污。
B面不作要求⑼抛光痕:A面抛光痕无凹凸手感⑽变形:A面不可有明显的五金变形及摔伤现象,B面不可有影响组装的五金变形2、电镀品外观不良及允收标准:⑴阴阳面:A面1/3面内不允许有阴阳面,B面不作要求⑵镀层脱落:A面(含铁件B面)不可有镀层脱落;压铸件B面允许镀层脱落但不可露底材⑶流漆:A面可有凸手感的流漆(流漆宽度小于,长度小于5mm);B面不作要求⑷沙粒:A面麻点、沙粒φ≤,不超过检验面积的1/3;B面不作要求。
⑸汽泡:铁件A、B表面均不允许有气泡;压铸件,铝件A面不允许有气泡;B面气泡φ≤,且在1cm2面积内不多于3pcs⑹针孔:A面针孔φ≤不多于2个,φ≤的不多于5个, φ≤的不作要求;B面针孔φ≤1mm,1cm2内不多于4pcs⑺异色:在不转动零件的情况下:检验时可见1/2内异色,面积≤1mm2,且不多于3处;B面可不作要求⑻划伤:A面及铁件的B面不允许有露底材划伤; A面允许有不露底色划伤,长度≤10mm,宽度≤不多于2条,且分散;B面划伤不作要求,(反射罩:A面划伤长度≤20mm,且不多于3道,B面划伤长度≤30mm,且不多于5道;)⑼吐酸:A面均不可有吐酸现象;⑽脏污:A面不允许有擦拭不掉的污垢、指纹、油污。
外观质量检查标准(通过观察检验)。

外观质量检查标准(通过观察检验)在现代社会中,产品的外观质量往往是用户选择商品的一个重要标准。
对产品的外观质量进行检查和评估显得尤为重要。
外观质量检查标准通过观察检验产品的外观特征、表面处理、外包装等内容,以确定产品是否符合质量要求。
以下将从不同角度对外观质量检查标准进行详细介绍。
一、外观特征1. 表面平整度产品的表面平整度是衡量外观质量的重要指标。
通过目视检查产品表面是否有凹凸不平、气泡、裂痕等表面缺陷,以及表面光洁度是否符合要求。
2. 颜色和色差颜色是产品外观的一个重要特征,颜色的一致性和准确性直接关系到产品的外观质量。
颜色差异过大会影响产品整体的美观性和一致性。
3. 尺寸和形状产品的尺寸和形状对外观质量也有很大影响。
通过尺寸测量仪器检查产品的尺寸和形状是否符合设计要求,确保产品外观符合标准。
二、表面处理1. 表面涂装涂装是产品表面处理的一种常见方式,目的是提高产品的外观质量和耐久性。
外观质量检查要对产品表面的涂装情况进行全面检查,包括颜色是否均匀、是否存在漏涂、结疤、起皮等情况。
2. 表面镀层对于镀层产品,外观质量检查要检查镀层的均匀性、附着力、亮度和颜色等指标,以确保镀层质量符合要求。
三、外包装1. 包装完整性外包装的完整性决定了产品在运输和使用过程中是否受到保护,因此外观质量检查要对产品的外包装进行全面检查,确保包装完整无损。
2. 标识和标牌产品的外包装需要标识产品的相关信息,外观质量检查要对产品的标识和标牌进行检查,确保标识内容准确完整。
四、检验方法1. 目视检查目视检查是最直接的检验方法之一,通过肉眼观察产品的外观特征、表面处理情况和外包装完整性等内容,进行外观质量的初步评估。
2. 仪器检测对于一些尺寸、颜色和光洁度等指标,需要借助相关的仪器设备进行检测,以确保检测结果的准确性。
五、结论外观质量检查标准通过观察检验产品的外观特征、表面处理、外包装等内容,可以有效评估产品的外观质量,保证产品的外观符合质量要求。
产品外观检验标准

产品外观检验标准(共8页) -本页仅作为预览文档封面,使用时请删除本页-目录目录................................................................ 错误!未定义书签。
前言................................................................ 错误!未定义书签。
1、范围................................................................. 错误!未定义书签。
2、总则................................................................. 错误!未定义书签。
3、加工品质标准 (3)缺点术语和定义 (3)允收标准........................................................... 错误!未定义书签。
检验方法........................................................... 错误!未定义书签。
4、烤漆品质标准 (5)缺点术语和定义 (5)允收标准 (7)烤漆性能测试 (8)5、印刷图文品质标准缺点程定义 (9)充收标准: (9)丝印的测试: (10)6、缺点的测量方法 (10)点状缺点的测量方法 (10)线状缺点测量方法: (11)7、点规图............................................................... 错误!未定义书签。
1、范围适用于生产过程工艺缺点或因加工不当引起的缺点判定;表面处理的外观检验判定;产成品的最终外观检验。
但不包含内部结构尺寸的评判标准。
2、总则原则:产品外观应美观,单独一零/部件的整体视觉效果不能受到破坏,生产者应认真操作、严格控制产品质量,避免在生产过程中出现对各种表面的损伤,如果发现某一缺点具有批量性问题,即便此缺点属于“可接收”范围,也可以对该产品不予验收。
产品外观检验标准(全球通用)

1、目的:
确定通用成品外观标准,为公司品质控制提供标准的依据。
2、适用范围:
适用于我司外观检验的标准判定,另有客户特殊规定除外。
3、职责权限:
3.1品质部:负责本检验标准的制定与审核,产品的鉴定、检验之执行;3.2工程部:负责品质问题的分析和改善活动的推行;
3.3生产部:负责产品的制造、过程检验和过程品质记录。
4、定义:
4.1异色点:产品表面出现的颜色异于周围的点。
4.2缩水:部分区域由于熔体压力不够,在该区域截面形成的凹坑。
4.3批锋:由于工艺或模具原因,在边缘分型面处所产生的废边。
4.3污点:表面形成的可擦除赃污。
4.4无感划伤:用指甲刮过划伤处,无段落感。
4.5有感划伤:用指甲刮过划伤处,有段落感。
4.6脏污:因模具、包装或操作等问题造成,分可擦出及不可擦出。
4.7气泡:因工艺原因内部出现的可见的空气泡。
5、工作程序:
5.1目视检查的条件及位置:
检验条件:距离 30cm~45cm 时间 5 S内,光源检验照明度20-40W
位置:产品与平面呈45°,上下左右转动动在15°之内。
检验时间:一般在5-10秒以内。
条件:不得在反光下检验表面。
5.2 外观区域划分
5.2.1 A区:正常目视第一眼可见面(样品的正面)
5.2.2B区:正常目视第一眼不可见面(左右两侧面,底面,背面,顶面)
5.2.3C区:产品内部,正常目视不可见面
5.3 成品外观检验项目:
5.4产品包装检验项目
5.5面积规格以下图为标准;单位:mm2 请看以下图表。
工厂产品外观检验通用标准

三編
兩編 目視
依客戶要求
單編
東莞市奕聯實業有限公司
類 別
項目
外觀檢驗規范 外觀檢驗判定標准
定義
位置
判定級別
A
B
文件編號: 版 本: 頁 次:
檢驗標准:
圖片 C
尼龍絲或其它材料
編織散亂
在正常形狀下而變 得沒有規律性(凌
亂)
整體
無散亂
無散亂
無散亂
量測 工具
注意事項
目視
編
線頭
線尾接合處多余的 線條
織
網
毛邊
成型后在表面部分 凸出之塑料
B面側面
0.5mm2
0.6mm2
0.7mm2
C面 進料口
0.6mm2
0.8mm2
1.0mm2
C
a
b l
在两处或更多的材料融
合模線 合点有线条(并且终止了 B面側面
结合或流动)
0.05mm
e
0.08mm
0.10mm
外
模
A面正面
L:0.5mm h:0.02mm
L:1.0mm h:0.02mm
量測 工具
注意事項
投影儀
投影儀
不可刮手且不影響 投影儀 裝配,以無手感為
標准
投影儀 不良只允許一處
不影響連接件適 目視 配,且可視圈無滑
牙 不影響連接件適 目視 配,且可視圈無爛
牙
目視 卡尺
不污染產品與使用
目視
者
投影儀
類 別
項目
東莞市奕聯實業有限公司
外觀檢驗規范 外觀檢驗判定標准
定義
位置
判定級別AOD来自均線材粗細不均勻線材面
注塑产品通用外观检查标准

文件控制印章副本发放部门☐营业部☑品证部☑装配☐项管☐行政部☐财务报关☑采购部☑注塑部☑清洁胶☑货仓☐厂机部□SMD☑PMC ☑工程部☑喷油丝印☐工模部☐电脑课☑IMDPATH:G:\DOCCON\TS16949工作指引\KS-QMD-002.DOC如此印章并非蓝色,代表此文件并非合法之版本,并不会受到控制及更新,请使用受控制之文件。
一、目的:明确注塑品一般外判定基准,使作业及检验有据可依。
二、范围:适用于公司所有注塑品的外观判定(若客户有要求时按客户特别要求执行)。
三、内容3.1注塑品常见的外观缺陷:混色、白化、黑点、缺胶、溢胶、缩水、夹水纹、银纹、气纹、伤、油污、表面积灰等;3.2金属部件一般外观判定标准;3.3喷油、丝印、移印、烫印一般外观判定标准;3.4组装件一般外观判定要求及标准;3.5其它类产品一般外观判定要求及标准。
3.6手柄类(BOSCH)外观判定标准3.7工具箱类(BOSCH)外观判定标准3.8 汽车内饰件外观检验标准四、定义:无五、程序内容:常见缺陷及一般外观判定基准5.1注塑产品通用检查标准见附表(1)5.2 金属部件的一般判定基准:5.2.1 金属表面不能有油污,不可有异物附着,用手、目、白抹布及胶纸确认。
5.2.2 金属件生锈断面一般只要少于全周的三分之一可以接受,对螺纹孔生锈只要内径、外径、有效径三项合格可以接收.但部品表面生锈,涂层及表面处理层脱落均不可。
5.2.3 金属部品变形不可,加工中遗漏不可,断裂不可,螺纹倾斜1°内可接受.5.2.4 金属部品如客户有特别要求,则必须按客户要求执行。
5.2.5 关于五金件和处理保管有其特殊要求,具体可参考祥工016:五金件处理标准。
5.2.6 金属表面若有酒精无法抹去之异色,对内装件可接受。
5.3 喷油、丝印、移印、烫印的一般具体测试及要求可参考<祥品003>的“3A”5.3.1 质检员检查,喷油、丝印、移印、烫印后易显现注塑缺陷。
外观检验通用标准
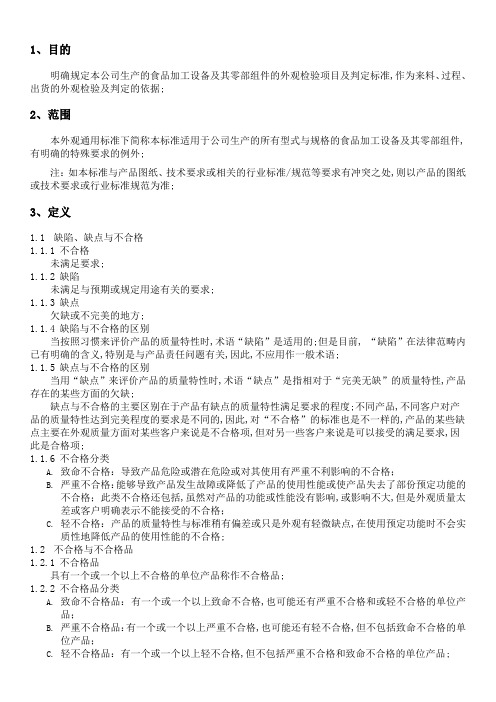
1、目的明确规定本公司生产的食品加工设备及其零部组件的外观检验项目及判定标准,作为来料、过程、出货的外观检验及判定的依据;2、范围本外观通用标准下简称本标准适用于公司生产的所有型式与规格的食品加工设备及其零部组件,有明确的特殊要求的例外;注:如本标准与产品图纸、技术要求或相关的行业标准/规范等要求有冲突之处,则以产品的图纸或技术要求或行业标准规范为准;3、定义1.1缺陷、缺点与不合格1.1.1不合格未满足要求;1.1.2缺陷未满足与预期或规定用途有关的要求;1.1.3缺点欠缺或不完美的地方;1.1.4缺陷与不合格的区别当按照习惯来评价产品的质量特性时,术语“缺陷”是适用的;但是目前, “缺陷”在法律范畴内已有明确的含义,特别是与产品责任问题有关,因此,不应用作一般术语;1.1.5缺点与不合格的区别当用“缺点”来评价产品的质量特性时,术语“缺点”是指相对于“完美无缺”的质量特性,产品存在的某些方面的欠缺;缺点与不合格的主要区别在于产品有缺点的质量特性满足要求的程度;不同产品,不同客户对产品的质量特性达到完美程度的要求是不同的,因此,对“不合格”的标准也是不一样的,产品的某些缺点主要在外观质量方面对某些客户来说是不合格项,但对另一些客户来说是可以接受的满足要求,因此是合格项;1.1.6不合格分类A.致命不合格:导致产品危险或潜在危险或对其使用有严重不利影响的不合格;B.严重不合格:能够导致产品发生故障或降低了产品的使用性能或使产品失去了部份预定功能的不合格;此类不合格还包括,虽然对产品的功能或性能没有影响,或影响不大,但是外观质量太差或客户明确表示不能接受的不合格;C.轻不合格:产品的质量特性与标准稍有偏差或只是外观有轻微缺点,在使用预定功能时不会实质性地降低产品的使用性能的不合格;1.2不合格与不合格品1.2.1不合格品具有一个或一个以上不合格的单位产品称作不合格品;1.2.2不合格品分类A.致命不合格品:有一个或一个以上致命不合格,也可能还有严重不合格和或轻不合格的单位产品;B.严重不合格品:有一个或一个以上严重不合格,也可能还有轻不合格,但不包括致命不合格的单位产品;C.轻不合格品:有一个或一个以上轻不合格,但不包括严重不合格和致命不合格的单位产品;1.3降级为使不合格产品符合不同于原有的要求而对其等级的改变;1.4特采对使用或放行不符合规定要求的产品的许可;特采通常仅限于在商定的时间或数量内,对含有不合格特性的产品的交付;1.5二级品二级品是指有轻不合格主要是外观质量,在使用预定功能时不会实质性地降低其性能的产品;外观质量有缺点但仍在合格范围内的产品,属于合格品;2外观质量检验工作标准2.1外观质量检验工作原则A.外观质量的重要性原则a.产品外观是客户对我公司产品质量好坏的第一印象,也是对公司最直接的感性认识;要努力克服工作中的重视产品性能,不注重外观质量的错误观点,严把产品外观质量关;b.产品出现的外观质量问题往往是因重视不够而犯的低级错误所致,极易纠正但损失很大,故必须引起各级各类人员的高度重视;B.外观质量检验的特殊性原则a.外观质量检验主要是依靠检验员的目测判断,所以,检验标准必须尽量描述详细、准确并尽可能多地制作检验标准限度样板以利于检验工作的顺利进行;b.用目测检验产品的外观质量比用计量器具对产品进行性能检测更方便更快捷,检验人员必须对生产过程中的产品外观质量实行全过程监控,以便防患于未然;C.外观质量检验的符合性原则a.产品外观质量并非越高越好,“严把产品外观质量关”的含义是不让不符合要求的产品通过,并非是不放过任何一个有缺点的产品;b.在产品外观质量检验在标准的判断上发生争议时,品保部应与有关各方进行沟通统一认识,必要时可以与用户沟通,在征得用户同意的情况下特采处理;2.2检验环境外观检验工作原则上应在独立的工作台上进行,检验工作台上方安装有40W日光灯,灯与工作台面的距离为70公分;2.3检验距离一般为30公分;3. 产品外观界定的等级划分原则;3.1 表面外观质量等级标准3.1.1 A级面:在使用过程中总能被客户看见的部分,适用于质量要求高的表面,例:产品的外前部,中低高度设备的顶部,控制面板等表面;3.1.2 B级面:在使用过程中常常被客户看到的部分,例:产品侧面、后面、经常打开的零件内表面等,这些表面允许有轻微不良,但是不致于引起挑剔客户不购买产品;3.1.3 C级面:适用于质量要求一般不作装饰用的表面,在使用过程中很少被客户注意到的表面部分如:设备的底面,底壳或后壳的底面,很高设备的顶面,维修时才看到的部分;此表面的外观缺陷应宽严合理,不至于给客户觉得该产品质量不佳;3.1.4 D级面:在使用过程中几乎不被客户看到部分如:产品的固定内部件表面,标签遮盖的局部区域、被其它部件遮蔽的表面等;此表面的缺陷只要不影响零件使用性能是被允许的;4 .外观检验方式4.1 按百分比抽检抽检10%,抽检数≤100按100,抽检数≥200抽200 ,整批数≤100全检;抽检合格后全检或按具体规定;4.2 全数检验100%检验凡属下列情况之一者应对其外观进行全数检验:A.产品的入库检验;B.样品试制及小批量试生产的成品检验;C.贵重元器件、零部件的进料检验;D.自身价格不高,但可能使装配后的成品部件出现较大损失的元器件、零部件的进料检验;E.其他需要进行全数检验的项目;4.3 接受、判退的通用标准4.3.1 致命不合格的接受数永远是0发现一个致命不合格,则整批不接受,只要有可能,还应该停止生产进行彻底检查,努力找出不合格的原因并设法预防再发生;如果认为某些致命不合格不必进行这样的程序,那么应考虑是否将其重新划分为严重不合格; 4.4 影响功能的外观缺点一律不可以降级或特采如攻牙后烂牙影响扭力,加工件有裂纹影响产品的保持力,金属件影响其自身强度的裂纹等; 4.5 整批性外观不良应具体情况具体分析4.5.1 毛刺、锐边所有孔、缝、边和角必须没有因模具或成型工艺原因造成的整批性的毛刺和锐边;4.5.2 色差对于批量生产的注塑件、表面处理件等产品,交货整批的颜色应该均匀一致,并在供需双方签认的颜色限度样板规定的范围以内;4.5.3 对于冲压、压铸件经常发生的,因模具或成型工艺原因造成的整批性外观质量缺点,例如:凹痕、接合线、变形等,应根据产品和客户的实际情况作出接受或判退的明确规定;5、缺点类型与定义5.1 五金钣金切削、冲压类5.1.1 凸:表面局部高于周围向外或向上与图纸或样板不符的突出部分;A.毛刺:金属工件的边缘、孔内或较光滑的面上因某种原因而产生的不光、不平的突出部分;B.铜丝:专指铜材在冲压、裁切加工後端子边缘出现的细小毛刺;C.毛边:专指金属工件的截断面因某种原因而产生的不光、不平的边缘;D.倒角不良:图纸要求倒角的金属工件的边、角等部位锋利、尖锐;5.1.2 凹:表面局部低于周围向内或向下与图纸或样板不符的凹陷部分;A.压、碰伤:金属工件因受其它硬物挤压、磕碰等造成其表面上出现的伤凹痕;B.拉、划伤:金属工件因受其它硬物磨擦拉曳、刻划造成其表面上出现的线性划伤凹痕;5.13 裂:局部表面破裂与图纸或样板不符;A.裂纹:在金属工件表面或折弯处有裂开的痕迹;B.裂缝:在金属工件表面或折弯处有破裂的缝隙;5.14 变形:指金属工件形状发生变化,与图面或样板不符;A.弧形:料带平面向外或向内弯曲,呈现出圆弧形状;B.波浪形:料带平面呈波浪形;C.扭曲:金属工件以扭转的方式变形;D.错位:杯口、卡点部位或折合处出现的错开现象;E.歪pin:板材pin呈倾斜状态;F.高低pin:板材头部或弯曲部位不在同一水平线上,出现高低不平现象;G.缺pin:料带上有掉失;5.15 污迹:金属工件表面有油渍或污垢;色差::金属工件表面颜色不一致或与样板颜色有差别;5.2 机加工后工序类5.2.1 螺纹不良A.滑牙:螺牙不完整或低孔径大而导致的实配不牢固;B.烂牙:螺牙不完整;C.残留金属屑:在加工后的螺牙内卡有金属屑,这会导致通规不通;D.鼓起起泡:攻牙深度没控制好而导致的不通孔背面凸起或穿孔;5.2.2 切边A.缺料:切边模切到产品而致;B.压伤:切边模碰伤产品;C.裂缝:切边时产生微小的裂纹;D.缩孔:铣面后显现出压铸的砂孔;5.2.3 去毛A.锉伤:锉毛刺时锉到产品;B.锉刀痕:锉毛边时产品留下的锉刀痕迹,会影响产品的外观和功能;5.3 电镀类电镀不良主要表现为:镀层起泡气泡、镀层粗糙、底材素材露出、烤焦、镀层剥落、雾状、色差、油污、异斑、氧化、锈斑、刮痕等;5.3.1 规格不符:专指用目测检验方法发现的实物与规范要求的不符之处;A.包装不符:包装方式、方法、标识等不符合图纸或规范要求;B.数量重量不符:实际数量重量与需求数量重量或标识数量重量不符;C.标记错误:工件上刻、印的标记的标示位置、内容、形状等与图纸样板不符;D.混料:有不同规格、尺寸的产品材料、零部件混装在一起;6、我司现有常见不良及检验标准6.1焊接不良主要外观缺陷为假焊、飞溅、焊渣、裂纹、烧穿、缩孔、咬边、焊瘤以及变形;6.2 钣金常见外观不良为材料缺陷、坑包、毛刺、变形、磨痕、划痕等;6.3喷漆常见外观不良主要有起皱、刮花、气泡、流痕、露黑;6.4 机加工常见外观不良主要为变形错位、毛刺、刀纹、台阶、沙孔、生锈;6.5 组装常见的外观不良为表面划伤、磨痕、油污、装配不良;。
通用产品检验标准

通用产品检验标准1. 引言本文档旨在制定一套通用产品检验标准,以确保产品的质量和安全性。
通过统一的检验标准,可以提高产品的一致性和可靠性,满足消费者对产品的期望和需求。
2. 检验要求2.1 外观检验- 产品外观应整洁无损伤,无明显色差或瑕疵。
- 具有可靠的标识、标志和包装。
- 产品尺寸、形状和颜色应与规定相符。
2.2 功能检验- 根据产品的用途,进行功能性能的测试。
- 确保产品的基本功能正常运作。
- 检查产品的操作方式是否易于理解和使用。
2.3 安全性检验- 确保产品符合相关法律法规的安全性要求。
- 检查产品是否存在明显的安全隐患。
- 对产品进行安全性能测试,如电气安全、机械安全等。
2.4 可靠性检验- 对产品进行耐久性测试,检验其使用寿命和可靠性。
- 评估产品的质量控制和生产工艺。
- 检查产品的耐用性和稳定性。
3. 检验方法3.1 样品选择- 样品的选择应具有代表性,并符合产品生产批次的特征。
- 样品数量应满足统计学要求,以提高测试的可靠性。
3.2 检验设备- 使用标准的检测设备和仪器,确保测量结果的准确性和可靠性。
- 检测设备的校准应定期进行,以确保其准确性。
3.3 检验步骤- 根据不同的检验要求,制定相应的检验步骤和操作规范。
- 对每个检验项目进行记录和评估,确保全面和准确的检验结果。
- 对检验结果进行分析,并根据需要采取相应的纠正措施。
4. 结论通过制定并遵守本文档中的通用产品检验标准,可以提高产品的质量和安全性,增强消费者的信任和满意度。
同时,也为生产企业提供了一套简单且可行的检验策略,以保证产品符合市场需求和法律法规的要求。
注:本文档只作为一份参考,具体的检验标准应根据产品特性和相关法规进行调整和制定。
200-300,lux,外观检验规范

竭诚为您提供优质文档/双击可除200-300,lux,外观检验规范篇一:通用外观检验标准通用外观检验标准1产品表面等级定义结构产品的表面外观等级划分为3个级别:1级、2级和3级,各表面等级的定义如下。
1.11级表面重要外观表面,体现产品外观形象的表面,产品正常工作状态下能直接正视的表面,以及打开前门就能看到的表面。
1.22级表面在特定角度才能看到的主要外表面,或半装饰性的经常被客户打开后可视的外观表面。
1.33级表面不是以装饰为目的的次要外观表面和内表面、客户不会看到的表面及除1、2级表面以外的表面。
2.1检验原则2.1.1产品外观应美观,颜色均匀一致,单独一零/部件的整体视觉效果不能受到破坏,不会给人以劣质产品的印象。
生产者应认真操作、严格控制产品质量,避免在生产过程中出现对各种表面的损伤。
2.1.2有签样或图纸上有特殊要求的零部件,其对应的缺陷优先按其样板或技术要求的标准进行判断。
2.1.3所有结构件外观缺陷的判定是基于不影响产品功能前提下进行的判定,如果有影响产品使用功能的缺陷(如引起炸机、短路等),即使符合标准规格,也判定不合格。
2.1.4所有外观判定都是在下述的检验条件下进行判定,看不到的外观缺陷都认可接受。
2.1.5对外观判定操作存在争议的以结构物料sqe工程师判定为准,仍有严重分歧的,最终裁决权归技术部。
2.2目视检测条件在自然光或光照度在300-600lx的近似自然光下(如40w 日光灯、距离500mm处),相距为650~750mm,观测时间按不同等级面而有不同,详见下表:表2、检测条件表面等级检视时间检视距离光源2级3级5s3s650~750mm自然光或光照度在300-600lx1级5s检查者位于被检查表面的正面、视线与被检表面呈45-90°进行正常检验(参见下图)。
要求检验者的校正视力不低于1.2。
不能使用放大镜用于外观检验。
图1、“正视”位置示意图2.3检测面积划分被检表面按其面积或最大外形尺寸划分为不同大小类别,当有两个条件满足时、以大的一类为准。
产品外观通用检验方法及标准

3、定义:A级面:B级面:C级面:零件表面4、接收条件:5、判定规则(出现情况):7、产品跌落测试:①对有跌落测试要求的产品,零部件高度1.3米,整机高度1米②跌落区域及要求:垂直于硬地板,一角三棱六面⑥“缺陷判定表”各项判定标准只作为通用判定区分缺陷的严重性或轻微性,不能作为AQL接受限度标准6、印刷、喷漆、电镀测试方法规定:①必须进行两项以上测试,并且被测试产品达到相关要求和AQL接收限度规定②印刷品一般以3M胶带和酒精测试为测试依据,喷漆一般以百格法和折弯法为测试依据,电镀品一般折弯法、百格法、盐雾试验(无试验机情况下--10克盐:100克水配比浸泡,容器必须密封后做测试)为测试依据,有另外附加测试要求时会在大货生产前另行通知①所有影响产品功能的产品的缺陷判定为“CR”或“MAJ”②所有出现在A级面上不允许或超出范围的缺陷判定为“MAJ”,规定范围内判定为“MIN”③所有出现在B级面上不允许的缺陷判定为“MIN”,不超出规定范围的接受(但批量不良不允许超过10%)④所有出现在C级面上不允许的缺陷判定为“MIN”,允许情况可接受⑤所有加工工艺或加工方法造成的批量缺陷,以签样或得到本公司主管级别人员确认为准(口头形式无效,以邮件或签样为准),否则按“缺陷判定表”内区分产品的缺陷严重性或轻微性所有检验均应在正常照明,并模拟最终使用条件下进行。
检测过程中不使用放大镜,所检验表面和人眼呈45°角。
A级面在检测时应转动,以获得最大反光效果。
①可接受的缺陷不能影响该零件的装配和功能,否则,将被拒收。
④缺陷允收定义了1250平方毫米的区域内各类缺陷的最大允收数量。
对于较大的零件表面,可允收数量和该表面所含1250平方毫米区域数量成正比,但是,两个或两个以上缺陷不能相连。
③所有的等级面应当印刷完好且满足颜色、光泽度、附着力等方面的要求。
②所有的等级面应当喷涂完好且满足颜色、光泽度、厚度、附着力等方面的要求。
通用外观检验标准

1.目的:规定公司产品的表面等级划分及外观质量要求。
2.范围:适用于指导产品的生产、总装及产品结构件的验收,外购件、外加工件的验收及指导。
3.定义:产品表面等级根据重要程度,可划分为A级面、B级面和C级面,具体定义如下:表面等级定义1)如果零件、部件、产品在后续装配、安装过程中被掩盖,则以被掩盖后的表面来定义;如果零件、部件、产品在后续装配、安装过程中有可能被掩盖也有可能不被掩盖,则按照不掩盖的表面来定义。
4.检验条件4.1. 光源要求要求在自然光或光照度为500LX 的近似自然光下检验,如40W的日光灯。
要求光源位于被检查表面正上方45°范围内,且距离被检查表面的直线距离为500mm(图1)。
要求在手电筒光照下检验柜体内部(箱内)。
光源要求示意图4.2. 检验员的要求检验员位于被检查设备的正面,视线与被检查表面呈45°~90°角进行检验(图2),要求检验员的视力或矫正视力应不低于1.0。
检验时不能使用放大镜。
被检查表面与人眼视线的关系4.3. 外观表面大小划分产品外观表面大小分为小、中、大、超大四种,分类原则有两种,一种是按面积大小分类,一种是按最大外形尺寸分类。
按照两种不同的分类原则,得到的表面类别不一致时,以大的一类为准。
比如某一表面按照面积大小划分为“小”,按照最大外形尺寸划分为“中”,则该表面为“中”。
产品外观表面大小划分标准,具体见表 2 。
当缺陷所在面的尺寸超过表 2 中对应的最大一类“超大”时,则将该面划分为若干个“超大”面或其它大小的面处理,且划分方法应保持同一种方式,即始终按面积划分或始终按外形尺寸划分。
产品外观表面大小类别划分标准5.判定总则1)产品外观应美观,单独的零、部件整体视觉效果不能受到破坏,不能给人以劣质产品的印象。
生产者应认真操作,严格控制产品质量,避免在生产过程中出现对各种表面的损伤。
如果发现某一缺陷具有批量性或大面积性或者影响功能,即便此缺陷属于“可接受”范围,也应对该产品不予验收。
产品外观检验标准(通用)

产品外观检验标准(通用)产品外观检验标准(通用)本标准的目的是确定通用成品外观标准,为公司品质控制提供标准的依据。
本标准适用于我司外观检验的标准判定,另有客户特殊规定除外。
职责权限方面,品质部负责本检验标准的制定与审核,产品的鉴定、检验之执行;工程部负责品质问题的分析和改善活动的推行;生产部负责产品的制造、过程检验和过程品质记录。
本标准定义了异色点、缩水、批锋、污点、无感划伤、有感划伤、脏污、气泡等术语。
在工作程序方面,目视检查的外观条件及位置为距离30cm~45cm,时间5 S,光源检验照明度20-40W,位置为产品与平面呈45°,上下左右转动动在15°之内。
检验时间一般在5-10秒以内,不得在反光下检验表面。
外观区域划分为A区、B区、C区,分别代表正常目视第一眼可见面、正常目视第一眼不可见面(左右两侧面、底面、背面、顶面)、产品内部,正常目视不可见面。
成品外观检验项目包括金属零件、五金件等,具体包括金属零件表面不可有电镀、生锈或氧化不良现象,断面氧化不可长过3mm,允许有两处间隔≤15mm,批锋不可超过0.04mm,金属零件表面不可有电镀不良现像等。
同时,还需注意外壳刮伤、有感刮伤不可有露底材现像,长≤1.0mm,宽≤0.2mm的无感刮伤等。
五金件方面,需要注意C面凹痕,直径≤3mm,深≤0.2mm(120mm允许3处)等问题。
最后,需检查产品外观是否有擦伤、划伤、缩水、变形、缺料、毛边、披锋、条纹、水纹等问题。
在生产过程中,产品表面出现的缺陷会影响产品的质量,因此需要对这些缺陷进行检查和控制。
下面是一些常见的表面缺陷及其容许范围。
对于A面和B面,刮伤和擦伤的长度不得超过3mm,宽度不得超过0.2mm,并且允许在30mm的距离内有一到两个点。
对于C面,刮伤和擦伤的长度不得超过5mm,宽度不得超过0.2mm,并且允许在30mm的距离内有两个点。
A面的脏污、油污和杂点的直径不得超过0.5mm,允许有一处。
产品通用外观检验标准
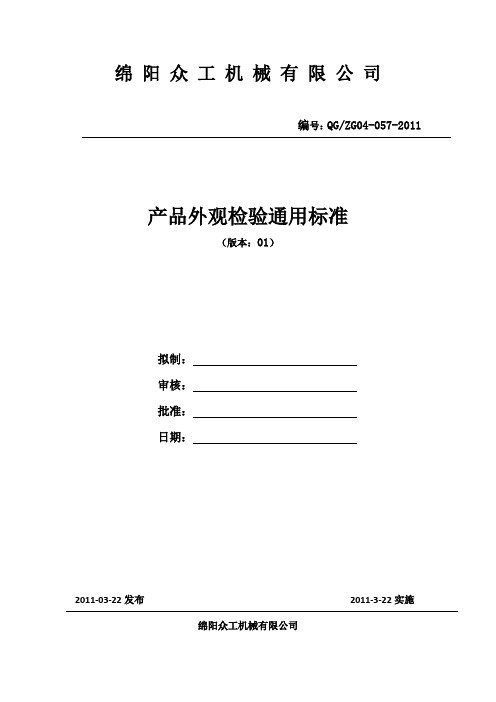
绵阳众工机械有限公司编号:QG/ZG04-057-2011产品外观检验通用标准(版本:01)拟制:审核:批准:日期:2011-03-22发布2011-3-22实施绵阳众工机械有限公司1、定义(Definition)1.1产品:指由我司或者供应商、外协加工单位所生产的产品。
1.2正视:指在检查者站立于被检查表面的正面、视线与被检表面呈45-90°而进行的观察(如图1)。
被检查表面被检查表面图1:“正视”位置示意图1.3A级表面:产品在客户处进行安装调测后能被经常看到的表面。
1.4B级表面:产品在我司正常检验或测试状态下、正视能看到的产品的外表面,A级表面除外。
1.5C级表面:产品在我司正常检验或测试状态下,正视不能看到的外表面。
1.6D级表面:产品内表面。
1.7金属表面:包括电镀、氧化、钝化、以及金属压铸面等非喷涂表面。
1.8拉丝:是一种砂带磨削加工,通过砂带对金属表面进行磨削加工,去除金属表面缺陷,并形成具有一定粗糙度、纹路均匀的装饰表面。
1.9基材花斑:电镀或氧化前因基体材料腐蚀、或者材料中的杂质、或者材料微孔等原因所造成的、与周围材质表面不同光泽或粗糙度的斑块状花纹外观。
1.10镀前划痕:指电镀或氧化之前因操作不当、或对明显缺陷进行粗打磨等人为造成的基体材料上的一般呈细线型划伤或局部摩擦的痕迹。
1.11浅划痕:膜层表面划伤,但未伤至底层(即底层未暴露);对其它无膜层表面则为:目测不明显、手指甲触摸无凹凸感、未伤及材料本体的伤痕。
1.12深划痕:膜层表面划伤,且已伤至底层(即底层已暴露出来);对无膜层表面则为:目测明显、手指甲触摸有凹凸感、伤及材料本体的伤痕。
1.13凹坑:由于基体材料缺陷、或在加工过程中操作不当等原因而在材料表面留下的小坑状痕迹。
1.14凹凸痕:因基材受撞击或校形不良等而呈现出的明显变形、凹凸不平整的现象,手摸时有不平感觉。
1.15抛光区:对基材上的腐蚀、划伤、焊接区、铆接区等部位进行机械打磨抛光后表现出的局部高光泽、光亮区域。
产品外观检验标准(通用)68076

产品外观检验标准(通用)1、目的:确定通用成品外观标准,为公司品质控制提供标准的依据。
2、适用范围:适用于我司外观检验的标准判定,另有客户特殊规定除外。
3、职责权限:3.1品质部:负责本检验标准的制定与审核,产品的鉴定、检验之执行;3.2工程部:负责品质问题的分析和改善活动的推行;3.3生产部:负责产品的制造、过程检验和过程品质记录。
4、定义:4.1异色点:产品表面出现的颜色异于周围的点。
4.2缩水:部分区域由于熔体压力不够,在该区域截面形成的凹坑。
4.3批锋:由于工艺或模具原因,在边缘分型面处所产生的废边。
4.3污点:表面形成的可擦除赃污。
4.4无感划伤:用指甲刮过划伤处,无段落感。
4.5有感划伤:用指甲刮过划伤处,有段落感。
4.6脏污:因模具、包装或操作等问题造成,分可擦出及不可擦出。
4.7气泡:因工艺原因内部出现的可见的空气泡。
5、工作程序5.1目视检查的外观条件及位置:检验条件:距离 30cm~45cm,时间 5 S,光源检验照明度20-40W位置:产品与平面呈45°,上下左右转动动在15°之内。
检验时间:一般在5-10秒以内。
条件:不得在反光下检验表面。
5.2 外观区域划分5.2.1 A区:正常目视第一眼可见面(样品的正面)5.2.2B区:正常目视第一眼不可见面(左右两侧面,底面,背面,顶面)5.2.3C区:产品内部,正常目视不可见面5.3 成品外观检验项目:6、对一些典型缺陷的描述●色点:肉眼观察难以区分长与宽的形状,测量时以其最大直径为其尺寸。
●颗粒:在喷漆件表面上附着的细小颗粒。
●阴影:在喷漆件或塑料件表面出现的颜色较周围暗的区域。
●桔纹:在喷漆件或电镀件表面出现大面积细小的像桔子皮形状的起伏不平。
●透底:在喷漆件表面出现局部的油漆层过薄而露出基体颜色的现象。
●鱼眼:由于溶剂挥发速度不适而造成在喷漆件表面有凹陷或小坑。
●多喷:超出图纸上规定的喷涂区域。
●剥落:产品表面上出现涂层或镀层脱落的现象。
产品等级外观检验标准精选全文完整版

1起泡
擦伤
2脱落
划伤
3烧焦
碰伤
4色差
毛刺
5发白
砂眼6发黄裂纹
7水印
杂质
8麻点焊接痕
9露底材/漏镀变形
镀层表面未镀现象
产品因摔落、运输或挤压等
因素造成
电镀前后因清洗水未及时干燥或干燥不彻底所形成的印迹镀件表面较明显凸状附着物,手感粗糙,因电镀液不纯或镀前产品不清洁(有碎屑,灰尘,油污,结晶物)表面上成片小凸点,大小相当,且很小很光滑,造成此现象的原因为电镀液不干净
或过滤不够焊料过多或未焊接到零件上所致,如果焊料过多,零件上会有结块或隆起,如果焊料不够,零件上会有间隙或
裂缝镀层表面有白色雾状
痕迹
基材表面疏松针孔
镀层表面漏出黄色层电镀件基材表面呈现线状开
裂镀层表面焦黄色,手感略粗糙,多现于边
部
表面因与其他表面较硬物体相撞导致的伤,通常手指甲
触摸有明显凹凸感
产品与色卡有明显差异,或同产品颜色存
在差异
工件已加工部位周围所形成
的刺状物或飞边
因电镀工艺原因引起的镀层与基材之间附着性不强而造成的镀
层隆起现象
镀后在周转、包装过程中碰
花现象
镀层从底层或基材之间剥落起皮现象
产品表面因擦伤而产生的细微线状痕迹,未伤至底层,目测不明显,手指甲触摸无凹凸感,称无感划伤;表面膜层划伤,已伤至底层,手指甲触摸有明显凹凸感,称
有感划伤。
- 1、下载文档前请自行甄别文档内容的完整性,平台不提供额外的编辑、内容补充、找答案等附加服务。
- 2、"仅部分预览"的文档,不可在线预览部分如存在完整性等问题,可反馈申请退款(可完整预览的文档不适用该条件!)。
- 3、如文档侵犯您的权益,请联系客服反馈,我们会尽快为您处理(人工客服工作时间:9:00-18:30)。
产品外观检验标准(通用)
1、目的:
确定通用成品外观标准,为公司品质控制提供标准的依据。
2、适用范围:
适用于我司外观检验的标准判定,另有客户特殊规定除外。
3、职责权限:
3.1品质部:负责本检验标准的制定与审核,产品的鉴定、检验之执行;3.2工程部:负责品质问题的分析和改善活动的推行;
3.3生产部:负责产品的制造、过程检验和过程品质记录。
4、定义:
4.1异色点:产品表面出现的颜色异于周围的点。
4.2缩水:部分区域由于熔体压力不够,在该区域截面形成的凹坑。
4.3批锋:由于工艺或模具原因,在边缘分型面处所产生的废边。
4.3污点:表面形成的可擦除赃污。
4.4无感划伤:用指甲刮过划伤处,无段落感。
4.5有感划伤:用指甲刮过划伤处,有段落感。
4.6脏污:因模具、包装或操作等问题造成,分可擦出及不可擦出。
4.7气泡:因工艺原因内部出现的可见的空气泡。
5、工作程序
5.1目视检查的外观条件及位置:
检验条件:距离 30cm~45cm,时间 5 S,光源检验照明度20-40W
位置:产品与平面呈45°,上下左右转动动在15°之内。
检验时间:一般在5-10秒以内。
条件:不得在反光下检验表面。
5.2 外观区域划分
5.2.1 A区:正常目视第一眼可见面(样品的正面)
5.2.2B区:正常目视第一眼不可见面(左右两侧面,底面,背面,顶面)
5.2.3C区:产品内部,正常目视不可见面
5.3 成品外观检验项目:
6、对一些典型缺陷的描述
色点:肉眼观察难以区分长与宽的形状,测量时以其最大直径为其尺寸。
颗粒:在喷漆件表面上附着的细小颗粒。
阴影:在喷漆件或塑料件表面出现的颜色较周围暗的区域。
桔纹:在喷漆件或电镀件表面出现大面积细小的像桔子皮形状的起伏不平。
透底:在喷漆件表面出现局部的油漆层过薄而露出基体颜色的现象。
鱼眼:由于溶剂挥发速度不适而造成在喷漆件表面有凹陷或小坑。
多喷:超出图纸上规定的喷涂区域。
剥落:产品表面上出现涂层或镀层脱落的现象。
毛絮:油漆内本身带有的,或油漆未干燥时落在油漆表面而形成的纤维状毛絮。
色差:产品表面呈现出与标准样品(客户承认样品)的颜色的差异,称为色差。
光泽不良:产品表面呈现出与标准样品(客户承认样品)光泽不一致的情况。
手印:在产品表面或零件光亮面出现的手指印痕。
异色点:在产品表面出现的颜色异于周围的点。
多胶点:因模具方面的损伤而造成局部细小的塑胶凸起。
缩水:当塑料熔体通过一个较薄的截面后,其压力损失很大,很难继续保持很高的压力来填充在较厚截面而形成的凹坑。
亮斑:对于非光面的塑料件,由于壁厚不均匀,在壁厚突变处产生的局部发亮现象。
硬划痕:由于硬物摩擦而造成产品表面有深度的划痕。
细划痕:没有深度的划痕。
飞边:由于注塑参数或模具的原因,造成在塑料件的边缘或分型面处所产生的塑料废边。
熔接线:塑料熔体在型腔中流动时,遇到阻碍物(型芯等物体)时,熔体在绕过阻碍物后不能很好的融合,于是在塑料件的表面形成一条明显的线,叫做熔接线。
翘曲:塑料件因内应力而造成的平面变形。
顶白/顶凸:由于塑料件的包紧力大,顶杆区域受到强大的顶出力所产生的白印或凸起。
填充不足:因注射压力不足或模腔内排气不良等,使融熔树脂无法到达模腔内的某一角落而造成的射料不足现象。
银条:在塑料件表面沿树脂流动方向所呈现出的银白色条纹。
流纹:产品表面以浇口为中心而呈现出的年轮状条纹。
烧焦:在塑料件表面出现的局部的塑料焦化发黑。
边拖花:因注射压力过大或型腔不平滑,脱模时所造成边缘的擦伤。
破裂:因内应力或机械损伤而造成产品的裂纹或细小开裂。
龟裂:橡胶件由于环境老化而造成在产品表面上有裂纹。
浇口:塑料成型件的浇注系统的末端部分。
搭桥:在导电胶转角位置,出现上面胶是连接着,但下面胶没有连着而出现空洞的现象。
补伤:对导电胶上已损坏的部位进行修补。
油渍:在产品表面所残留的油污。
气泡:由于原料在成型前未充分干燥,水分在高温的树脂中气化而形成气泡。
凹坑:由于模具的损坏等原因,造成在平面上出现的高低不平。
彩虹:指透明区域在反光条件下出现彩色光晕的现象。
透明度差:指透明区出现模糊、透明度不佳的现象。
拉白:成型品脱模时,由于钩料杆拉力大于顶料杆的顶出力,而使某部位所产生的白化。
折痕:在PC薄膜按键的底膜上产生的折叠痕迹。
侧面起皱:在PC薄膜内注入塑料时,由于薄膜受力不均匀在成品上造成皱纹。
漏光:由于PC薄膜上有漏印的部位,造成光线能从背面穿到正面,称为漏光。
顶白:比背景颜色白,常出现于顶针背面。
断裂:材料分离,可依缺料表面的外观检测决定,如表面显示有小颗粒或扭曲,可能是断裂,若表面显示是光滑则可能是短射。
毛边:在塑料零件的边缘或结合线处线性凸起 (通常为成型不良所致)
缺料:由于模具的损坏或其他原因﹐造成成品有射不饱和缺料情形.
硬划伤:硬物或锐器造成零件表面的深度线性伤痕.
碰伤:产品表面或边缘遭硬物撞击而产生的痕迹
油斑:附着在对象表面的油性液体
断差:即错位,各部件组装后的台阶,超过标准。
掉漆:表面涂层的脱落。
气泡:由于原料在成型前未充分干燥,水分在高温的树脂中气化而形成气泡。
缩水:制品表面因成型时,冷却硬化收缩,产生的肉眼可见的凹坑或窝状。
披锋:由于注塑或模具的原因,在塑料件周围多出的塑料废边。
色差:产品表面呈现出与标准样品(客户承认样品)不同的颜色。
碰伤:制品表面的碰伤痕迹。
拖白:制品的侧边,柱孔等位置脱模时产生的发白现象。
参数代码表
代码名称(单位)代码名称(单位)
N 数目(个) D 最大内径(mm)
L 长度(mm)H 深度(mm)
W 宽度(mm)DS 距离(mm)
1。